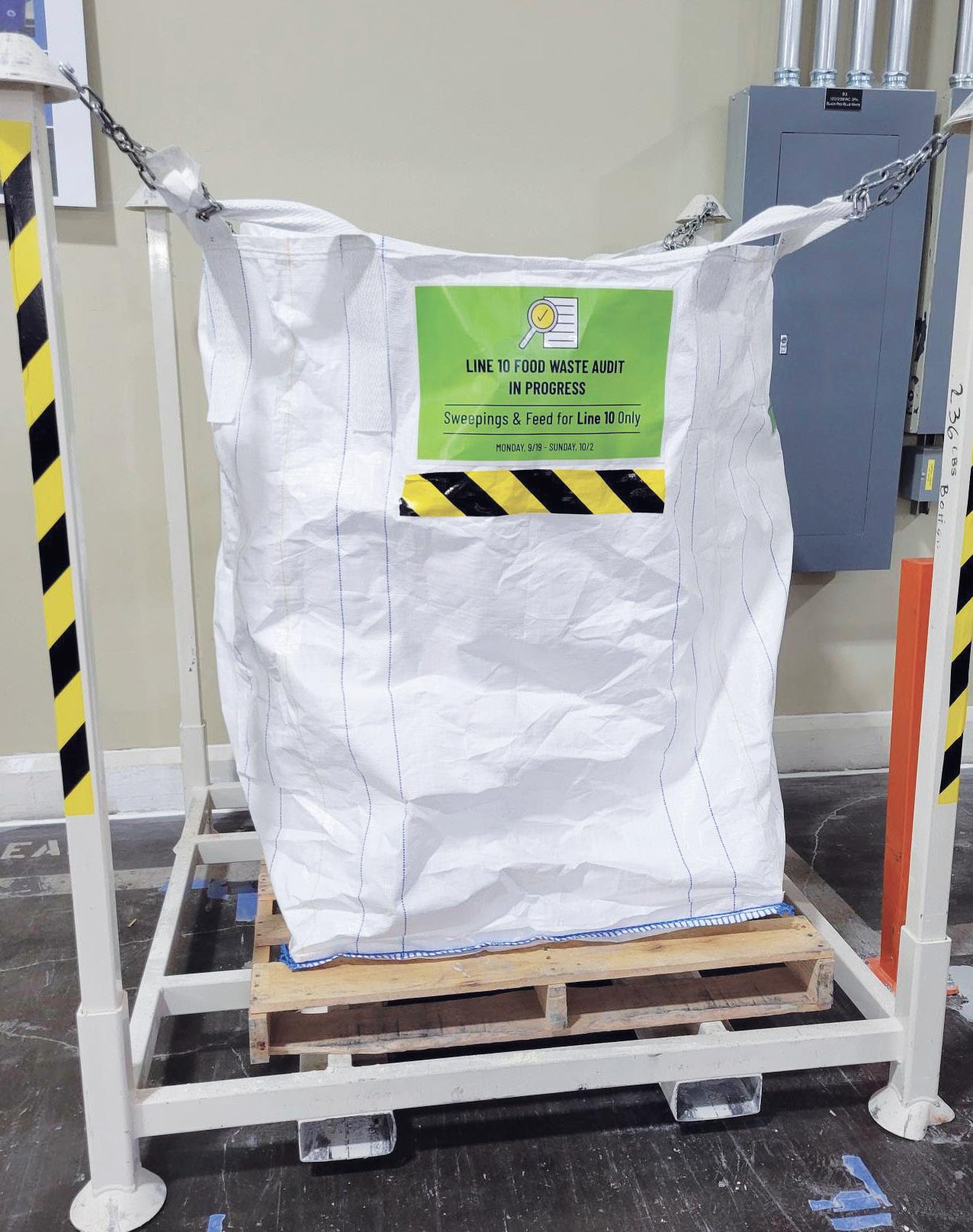
1 minute read
EXCELLENCE MANUFACTURING AWARDS
Food waste was collected in a dedicated tote, enabling the company to measure the improvement.
The post-implementation food waste audit showed an average 71% reduction in food waste per pound and 78% reduction per case for each product produced on the line. For granola products, it was 15 lb of product saved per pallet produced, and for pulse/whole grain products, the change saved 110 lb of product per pallet produced.
With a relatively simple change needed—requiring just a few hours of maintenance time, with a total cost of about $500—the ROI was almost immediate, Person says.
“The pilot shows how one simple employee idea can translate into impactful environmental savings,” Person says. “Food waste savings translate to avoided carbon emissions as food is able to make it into the hands of customers, rather than being wasted.”
The PCFWC supported the pilot, and a key outcome of the project was to share results with other manufacturers—through both a published case study (pfwgo.to/bobs) and a presentation at the PCFWC Manufacturer Summit.