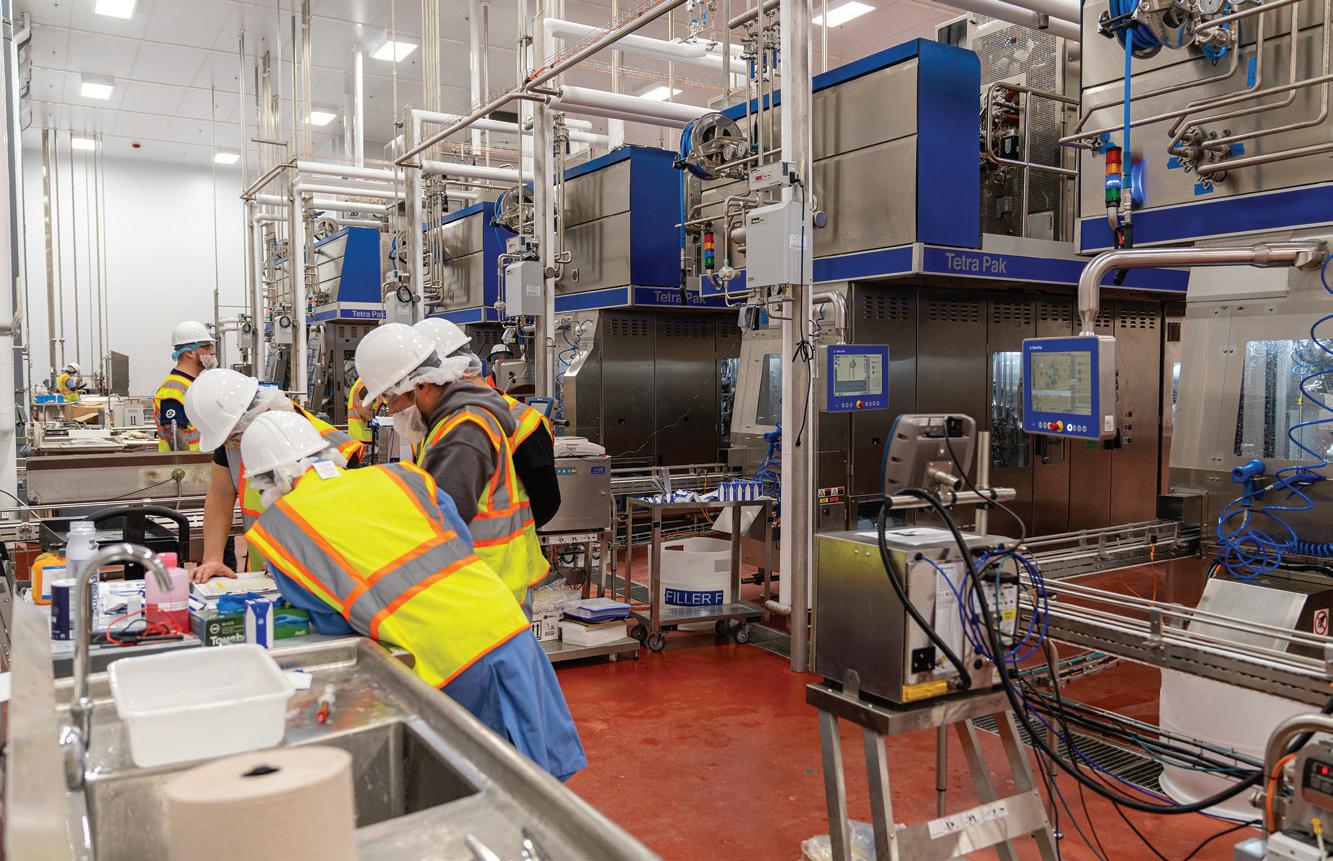
7 minute read
SunOpta Takes Aseptic Processing to New Level
As a greenfield plant, SunOpta has been able to take the best of everything from its three other plants and improve them further—from efficiencies and sustainability to sanitary design and safety.
WHEN SUNOPTA HIT CAPACITY LEVELS at its existing manufacturing facilities, it was time to establish capabilities in a new plant. Despite the company having looked at 180 possible site locations, today it’s hard to see Midlothian, Texas, just outside of Dallas, as anything but a foregone conclusion for the company’s next aseptic manufacturing plant.
“We were super happy with our choice of Midlothian because, not only has the city been great to work with, they have really helped wel- come us into the community. The incentive packages we got were phenomenal,” says Chris Whitehair, vice president of operations. “Our hiring fairs have been super successful, and the caliber of folks we’ve been getting has also been very good.”
Approaching the facility in Midlothian, the town’s growth is apparent, new facilities and residential areas popping up right and left. In fact, Whitehair suspects it would be difficult to get the incentives today that they managed to secure for the site two years ago. SunOpta successfully negotiated with the City of Midlothian and Ellis County for a property tax abatement worth $7.5 million and $500,000 in operation grants contingent upon commencing operations and maintaining full-time jobs.
The plant’s specific location within the U.S. was strategic as well, creating distribution efficiency along with SunOpta’s plants in California, Minnesota, and Pennsylvania. “We’ve got one on the East Coast, one on the West Coast, a third one in the North, and Texas becomes a nice diamond shape,” says Anil Neti, senior plant manager. “Which will help in reducing 15 million miles per year, which equals 59 million pounds of carbon emissions.”
The location also places the co-manufacturer close to important existing and new customers. “One of our largest customers really wanted us to have aseptic manufacturing here,” Whitehair says, referring to a large coffeehouse chain for which SunOpta makes tea. “So that’s really what propelled us to come here and build this plant two years ago.”
Although the broths, teas, and plant-based milks that will be made at the Midlothian plant are many of the same products that are made at its existing plants—and rely on much of the already-trusted Tetra Pak equipment for aseptic production—this greenfield project enabled SunOpta to optimize production, improve the flexibility of its systems, and accommodate new product lines, including 330 mL protein drinks.
That’s where the new customer comes in. The first phase of the buildout is targeted largely at Premier Protein single-serve nutrition drinks, with the capacity to produce about 78 million gallons of product per year. When we visited SunOpta in May, the line dedicated to the drinks had just been running for eight days. Premier Nutrition has one of its largest distribution centers in Arlington, Texas, also in the Dallas area.
The big driver pushing SunOpta to create more plant capacity in the first place, however, came largely from the plant-based milk market. COVID19 created a run on many key household supplies like toilet paper and hand sanitizer. But it also kicked off a boom for many of the more shelf-stable foods in our lives. For SunOpta, this was perhaps most felt in the oat milk market that it served. By spring of 2020, sales of oat milk had skyrocketed 477% over the previous year, according to Nielsen data. Though a particularly significant surge during lockdown, the general trend toward plant-based dairy alternatives was already taking place and is expected to continue. SkyQuest technology foresees a 10.4% rise in the market from 2022 to 2028.
“We’re expanding the current portfolio—whether it’s oat milks, broth, tea, increasing the revenue there—but adding a new 330 mL Premium Nutrition to the bottom line,” Neti says. “That’s a whole new add to SunOpta, which is an incremental revenue to what we’re doing today.” That’s business that SunOpta would not have gotten without moving to this key Texas location.
Innovating through a tight timeline
A key consideration in choosing SunOpta as a Manufacturing Innovation Award winner came in relation to its innovative solutions to some pretty hairy supply chain obstacles while staying on a tight timeline.
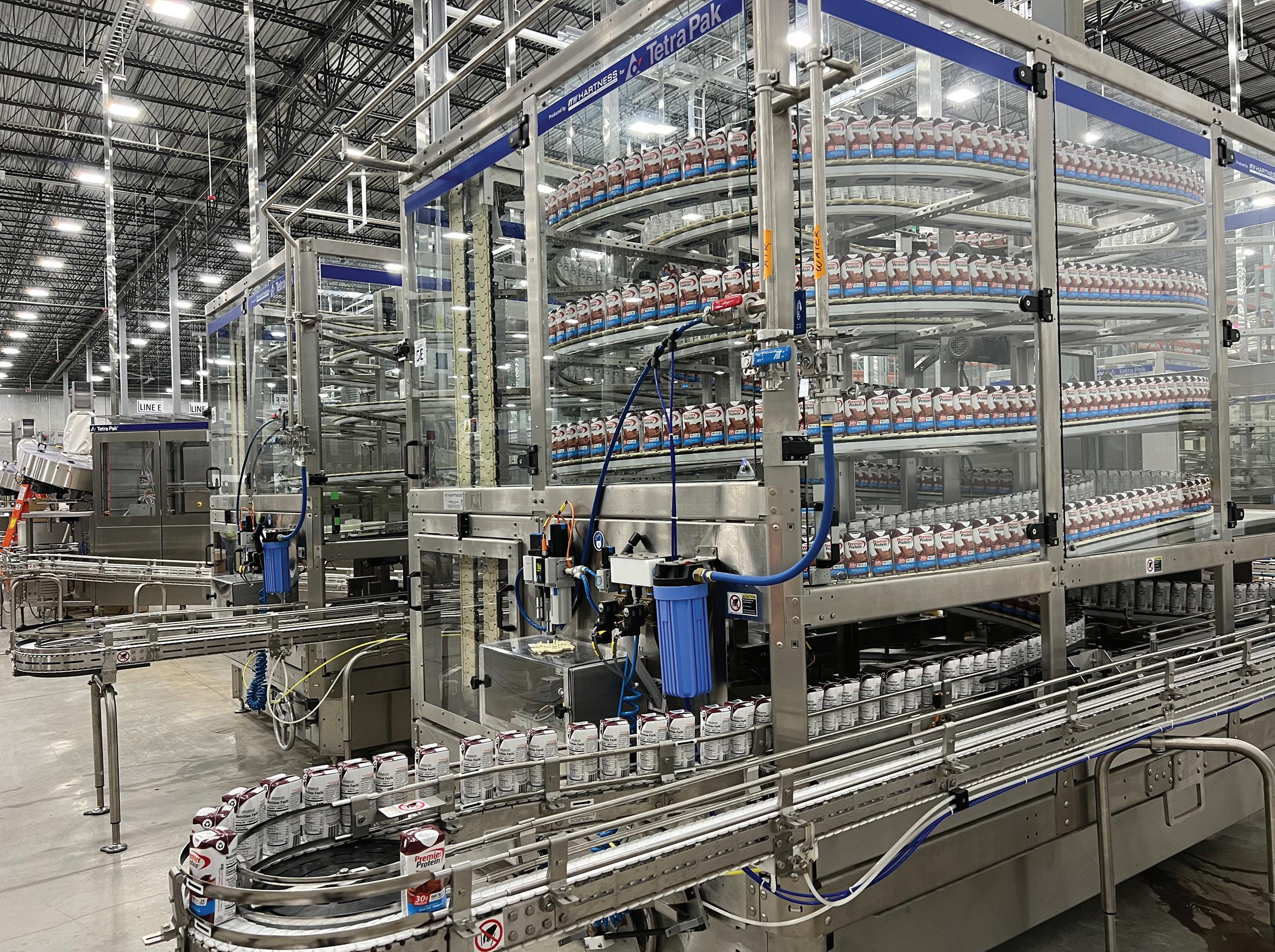
Though staying on schedule—and on budget—is important for any project, SunOpta had a particular need to get this manufacturing plant up and running quickly. To secure the business of its new customer, the co-manufacturer had to be ramped to full production within 18 months of design concept.
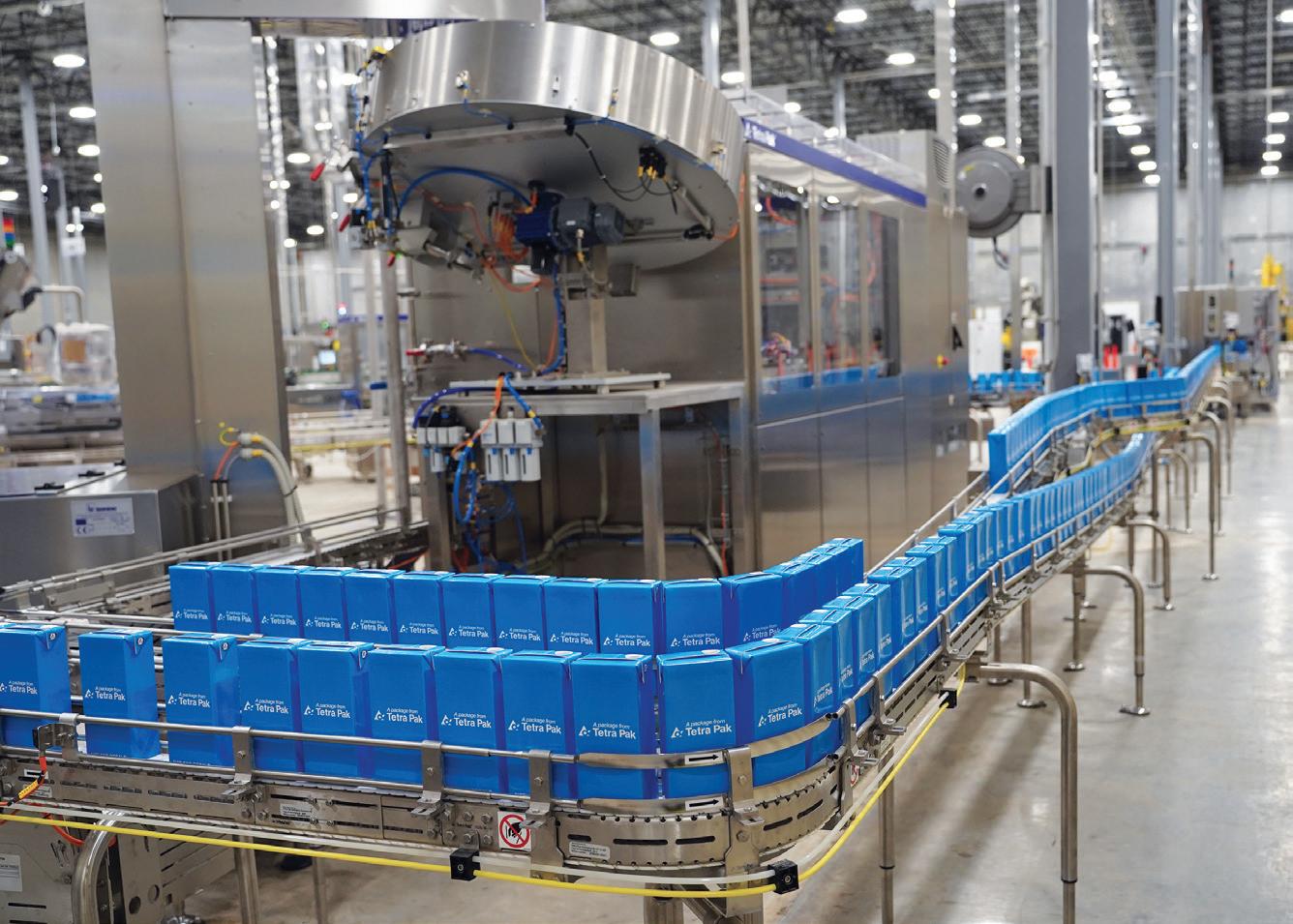
SunOpta had kicked off its search for a site in September 2020, whittling its choices down to six finalists and then ultimately choosing the Midlothian site. By April 2021, the development team had chosen its design concept and presented its business case to SunOpta’s board. Construction began in September 2021.
“And then 16 months later, we actually made first production, which was pretty remarkable,” Whitehair comments.
Having salable product by end of 2022 was no easy feat, and it required fast and creative thinking from the team at SunOpta and long-trusted partners Dennis Group (for design and engineering) and Tetra Pak (for aseptic production systems). Already quite familiar with the kinds of equipment delays that had become all too prevalent since the start of the pandemic, the team made a point of planning ahead.
“One of the things we did smart was we ordered long-lead items like steel and electrical components—anything that we thought was going to be a problem getting delivered coming out of COVID and the supply chain challenges—we got on it and ordered it,” Whitehair says. “That helped a lot.”
They could never have made the 16-month project delivery date without pre-ordering some bigger items in particular, Whitehair says. “We ran into challenges on deliveries every week,” he adds. “There wasn’t a week that went by—from the time we broke ground until the end—that there wasn’t something that we had to work through to get delivered on time.”
The main switchgear for the plant was one of those items, but that pre-planning wasn’t enough— timelines for electrical equipment just continued to grow, and the switchgear’s delivery date was pushed back time and time again. If they were going to have the plant operational by the end of 2022, they would have to pivot and come up with an alternative plan. Finally, they were able to find refurbished switchgear to use instead. Because the bottom conduits wouldn’t line up with what had been planned initially, the team had to quickly—within the span of a week— design and construct a platform for the refurbished switchgear to sit on in order to line up ports.
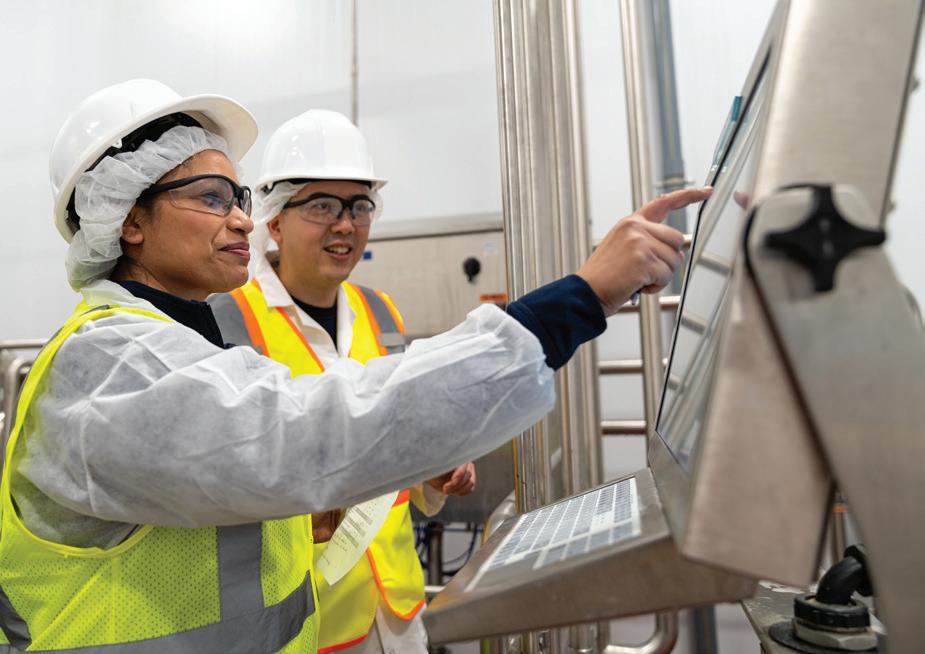
It’s a good thing SunOpta stopped relying on the original switchgear order to arrive. During our visit in May 2023, they were still using the refurbished equipment. The switchgear had recently arrived but was sitting to the side with missing components. “When this showed up, the parts were all missing,” Whitehair says. “Literally, 76% of the parts that were supposed to be in these were missing.”
Commissioning was also accelerated to keep the project on schedule. One solution was to ship the motor control centers while they were only partially constructed and to field install the remainder of the components.
Since power was limited throughout construction, utility systems had to be powered up strategically. Power to equipment was required for I/O checkout and initial function tests. The team would create punch lists and then power the equipment down, moving to the next equipment while completing the punch lists, and finally returning to complete I/O checkout upon completion of the punch list. This process was repeated for all the utilities to drive schedule and allow utility systems to be available to Tetra Pak systems for their checkout and functional tests.
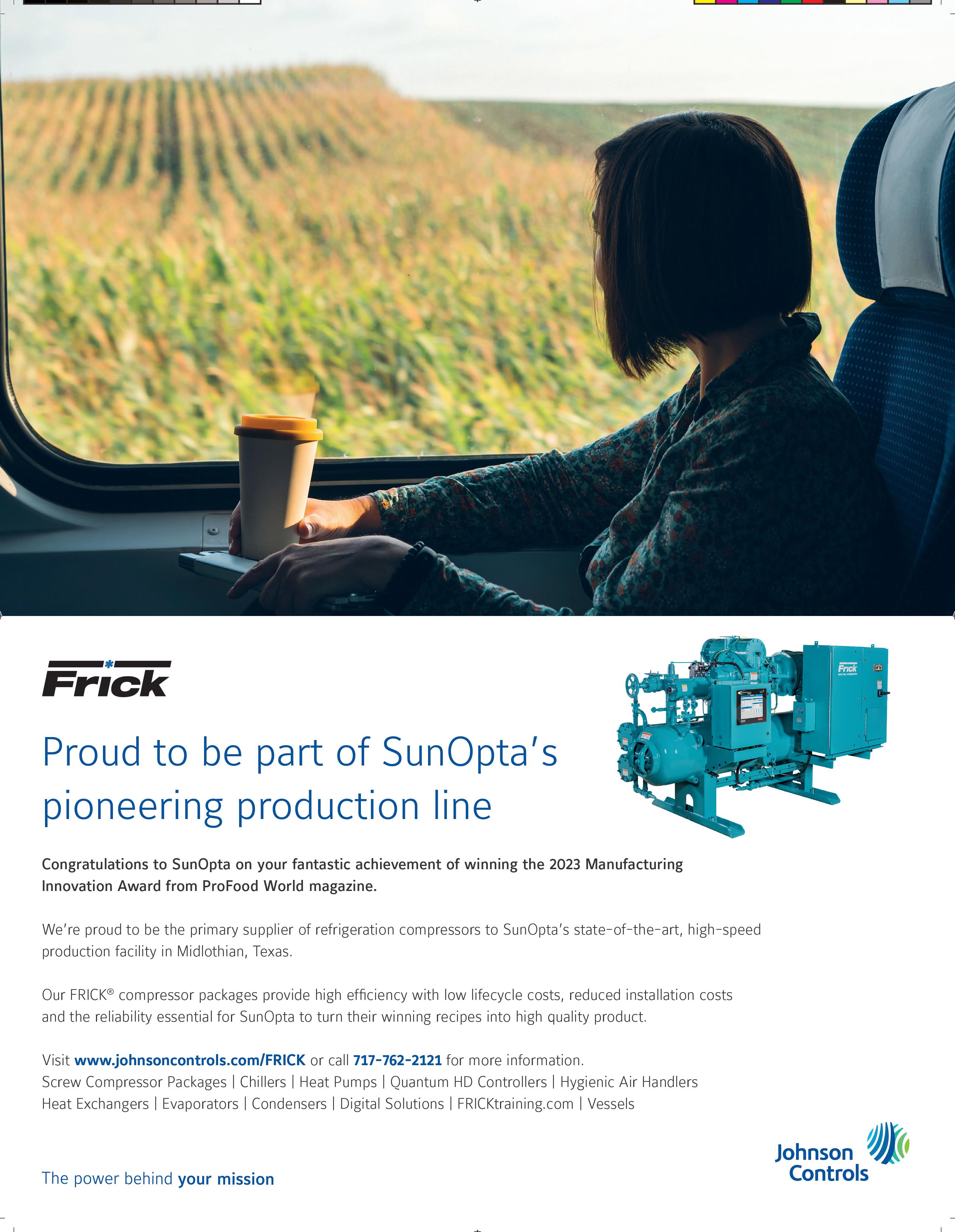
A reverse osmosis system installed for ingredient water is also used to supply feedwater to the steam boilers, reducing blowdown of chemically treated hot water.
On the construction side, delays resulted in the building shell dry-in date being several months later than expected. To keep the project on schedule, all parties committed to doing whatever they could to compensate for the delays, including extended hours, seven days a week. Whitehair says 300+ contractors were on site daily throughout the project.
Neti gives credit to the entire team for the creative solutions along the way. “It is such a great team that thought outside the box,” he says.
“Whether it is the gas, whether it is the power, whether it is the wastewater, you name it—every single one has been a challenge on this project. However, the team did a phenomenal job.”
There were a lot of people looking at answers to questions from every angle and coming up with new solutions to problems. “With SunOpta’s project management, the leadership—all the way from top down—helped in enabling us to be on track,” Neti adds.
Best in class from the ground up
Although the 285,000-sq-ft facility in Midlothian runs many of the same products as its predecessors, it has some advantages. With the new ground-up project, SunOpta was able to assess best practices at its other facilities and make improvements that might not have been possible previously. It also gave SunOpta the opportunity to add new product lines, with the flexibility to expand into new formats in the future.
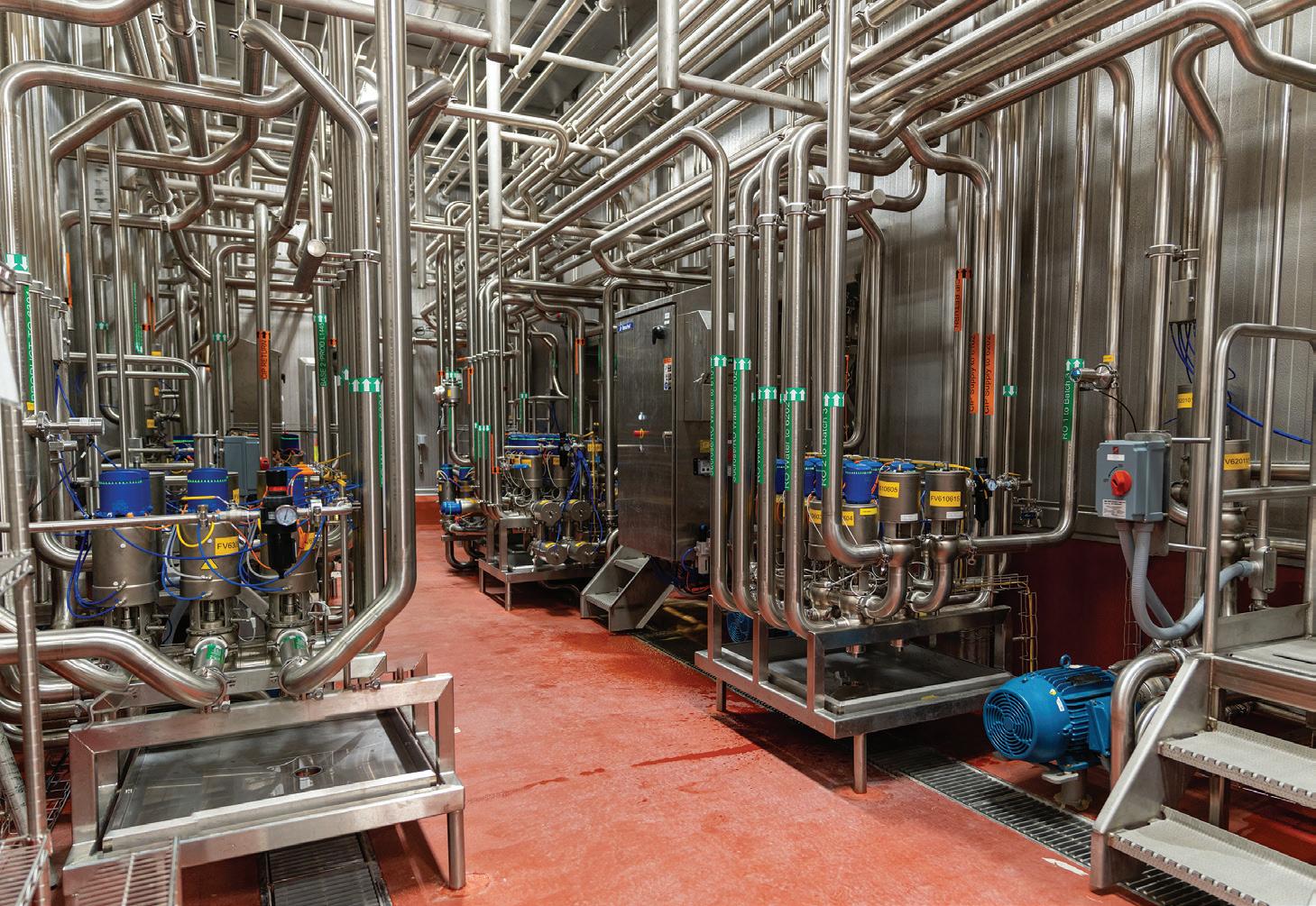
“We spent months in the design phase on how we were going to lay out this plant,” Whitehair says, mentioning extensive work with Tetra Pak and
Dennis Group through several large projects over the past three years. “All of the things that we wanted to improve on got built into Midlothian—whether it’s sanitary design, whether it’s sustainability practices, whether it’s safety of our employees. Everything really got built into the design.”
SunOpta has used Tetra Pak equipment at its other facilities, but a greenfield space enabled the company to make improvements, many in worker comfort and safety. “Along with our sister facilities, feedback was taken from all their floor operators: What would you like to see if we built a new plant? That was incorporated into this design—whether it’s the restroom, whether it’s the mother’s room, whether it’s bigger spaces in the processing area, filling area,” Neti explains. “We’re going towards not just building and running product, but is it employee-friendly? Is there enough room and a comfortable room to make things. Those are all part of the design.”
Upgraded employee amenity areas included a larger locker room footprint to avoid crowding during shift changes, as well as an expansive break room with comfortable seating and a quiet area for phone calls or relaxing, as well as access to a prayer room and mother’s room.
The batching rooms were built larger to allow easier transfer of raw materials via drums or pallets. Equipment layouts provided more space so that operators are positioned further away from steam or chemical residue. Cooling drops were added above the operator stations in high-temperature areas. Additional space was also designed behind the fillers so that multiple operators could remove laminate off