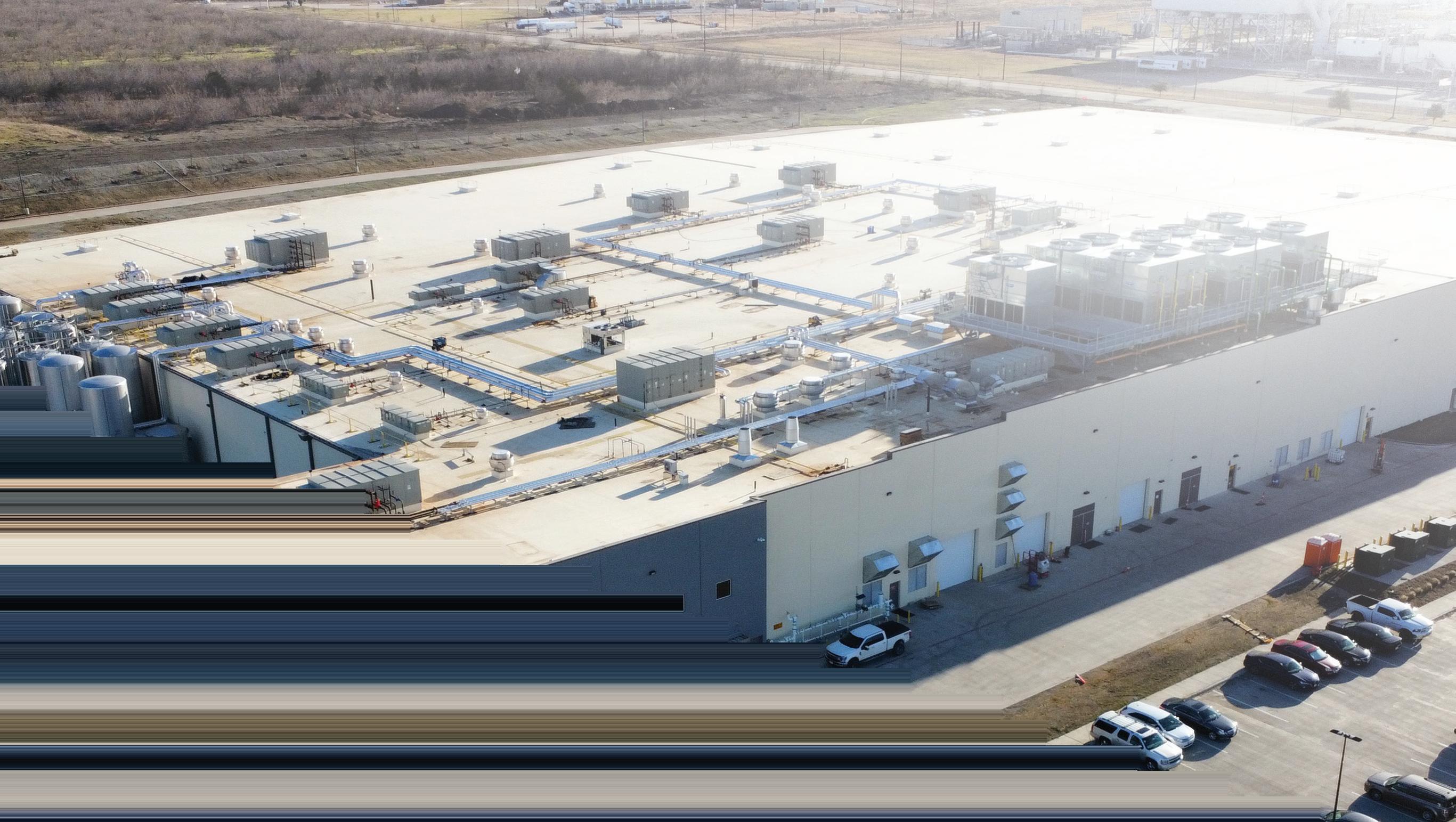
2 minute read
FEATHER IN THEIR CAP A FAST-TRACKED
Congratulations dennisgroup.com info@dennisgroup.com
When sales of oat milk surged during the pandemic, long-time sustainable food & beverage leader SunOpta stepped up to the plate with an innovative new facility to sustainably increase plant-based milk production. But this facility won’t just produce oat milk – the energy efficient design brought to life by Dennis Group will help reduce 59,000,000 pounds of carbon per year. It’s a winner in more ways than one.

Congratulations to the project teams on their success!
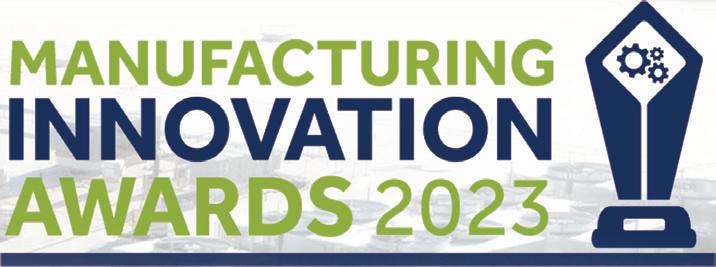
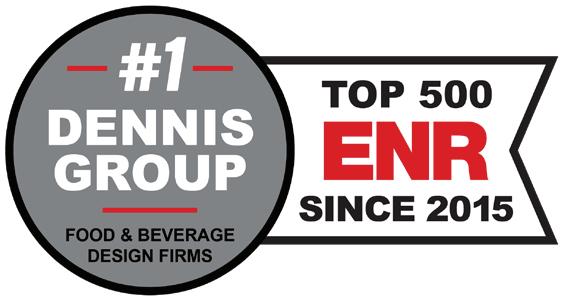
+1.888.514.7270
United States
● Canada
● Brazil
● Portugal pallets without interfering with each other.
SunOpta also improved the location of its control rooms. The new plant has three separate control rooms—one for mix, one for processing, and one for filling. “They’re very close so the employees can go into the control room, do their work, and then only operate the equipment when they need to, and they can come back to the control room,” Neti says.
“We tried to make it as user-friendly as we could just by laying out the plan properly. We even have small satellite labs, even for our truck bay, where we receive materials. They have a lab out there, so they don’t have to walk 200 yards to another lab to test the products before we accept them,” Whitehair adds. “The flow of the plant—from ingredients coming in on the east side, finished goods going out on the west side, and all the mixing, processing, and filling that goes on in between—it’s just a very natural flow of the plant from east to west. For this facility, we were able to do that because we were starting with a blank sheet of paper.”
The Texas facility has a two-lane bay where various liquid product bases are received, sampled, tested, and then transferred to refrigerated silos with agitators. Liquid sweetener is also received and transferred to a heated jacketed silo with an agitator. Exterior air into the tank passes through HEPA filters and a UV disinfection chamber to avoid contaminants or bacteria from being introduced.
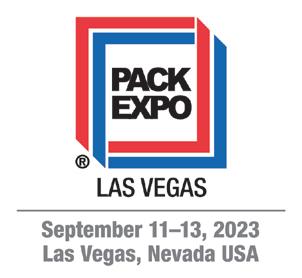
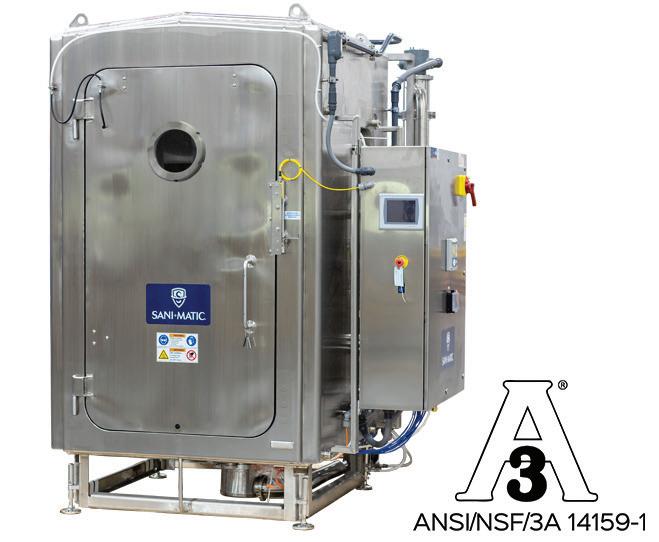
These silos feed two Tetra Pak high-speed aseptic production lines that are flexible enough to produce more than 100 SKUs for SunOpta’s diverse customer base. Batch systems are completely automated for bulk ingredients, while minor ingredients are added manually. Once batched, the product is thermally processed with direct or indirect steam. Depending on the product, the packaging formats include slim liters, edge liters, and 330 mL single-serve beverages. Robotic palletizing is used before product is transferred to the finished goods warehouse, which typically holds five weeks of inventory.
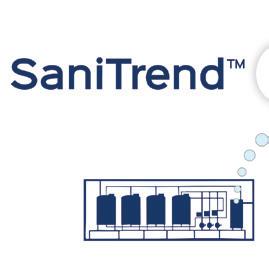
Hygienic finishes are used throughout the production space, particularly in high-care areas, including a walk-on ceiling, insulated metal panel (IMP) walls, stainless-steel finishes, and sloped drainage. Mix-proof valves enable SunOpta to take any system down for sanitation or service, while other systems remain online.
“We leveraged the Dennis Group, who are very
