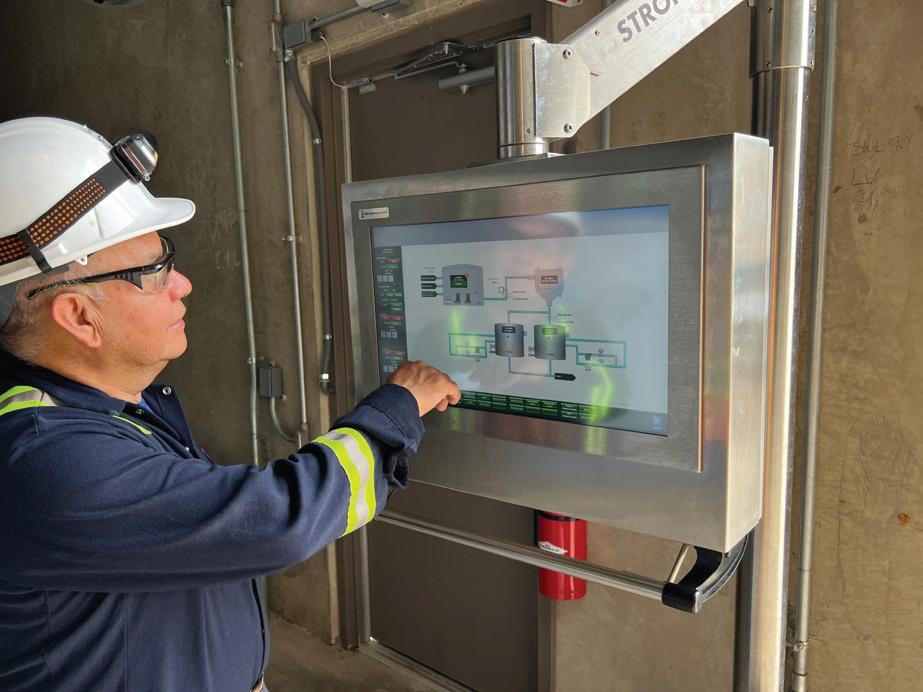
4 minute read
Quality products start with clean equipment

Wastewater capabilities in the area couldn’t handle what the new facility would produce, so SunOpta’s employees are operating the site’s own wastewater treatment plant.
familiar with food sanitation construction, and we leveraged the best practices that they could bring to this design—on floors, walls, ceilings, even how to design a drain properly,” Whitehair says, listing a slew of good sanitation practices.
A lot of investment went into the SunOpta cleanin-place system, Neti notes, including an increased level of automation for several of the tasks. “It’s an automated system to clean the tanks, the lines with the right temperature, right duration, right concentricity, right chemicals in there—a lot of it is automated, so it’s less chance for a mistake to happen.”
Control, communication, traceability
SunOpta has standardized on Tetra Pak equipment on all of its lines at all of its plants, using Tetra Pak controls, and Tetra Pak technicians helping to maintain the lines and train employees on their use. The location of the new plant has also been helpful when it comes to working with Tetra Pak, which has a state-of-the-art factory also in the Dallas metro area, in Denton, Texas.
The production systems use Tetra Pak’s Plant Master control system, so Dennis Group integrated each utility with the proprietary system. Utilities communicate with the Tetra Pak programmable logic controllers (PLCs) so that the system calls for tower water only when needed, which is more energy-efficient. Utilities also have monitoring to alert when there is an issue.
Most of the equipment at the plant is PLCdriven, with the drives, PLCs and supervisory control and data acquisition (SCADA) system all communicating with each other, Neti notes.
SunOpta’s Texas facility is using Redzone software extensively to manage several aspects of information and communication within operations. “It takes some of this information, compiles it, and ensures, for example, what speed are we running a certain line? How many packs did we run? What’s our OEE? What’s our downtime look like? What do our micro-stops looks like? That’s one piece of it,” Neti explains. “The second piece of it is the communication. We don’t necessarily have to go from an operator to a lead to a supervisor to a plant manager to know what’s going on. With the controls automation and the Redzone program that we have, it’s more like Facebook and Instagram combined. An operator can go in and type something in—it’s a high five or it’s a recommendation or it’s a concern. And then they all look at it at the same time.”
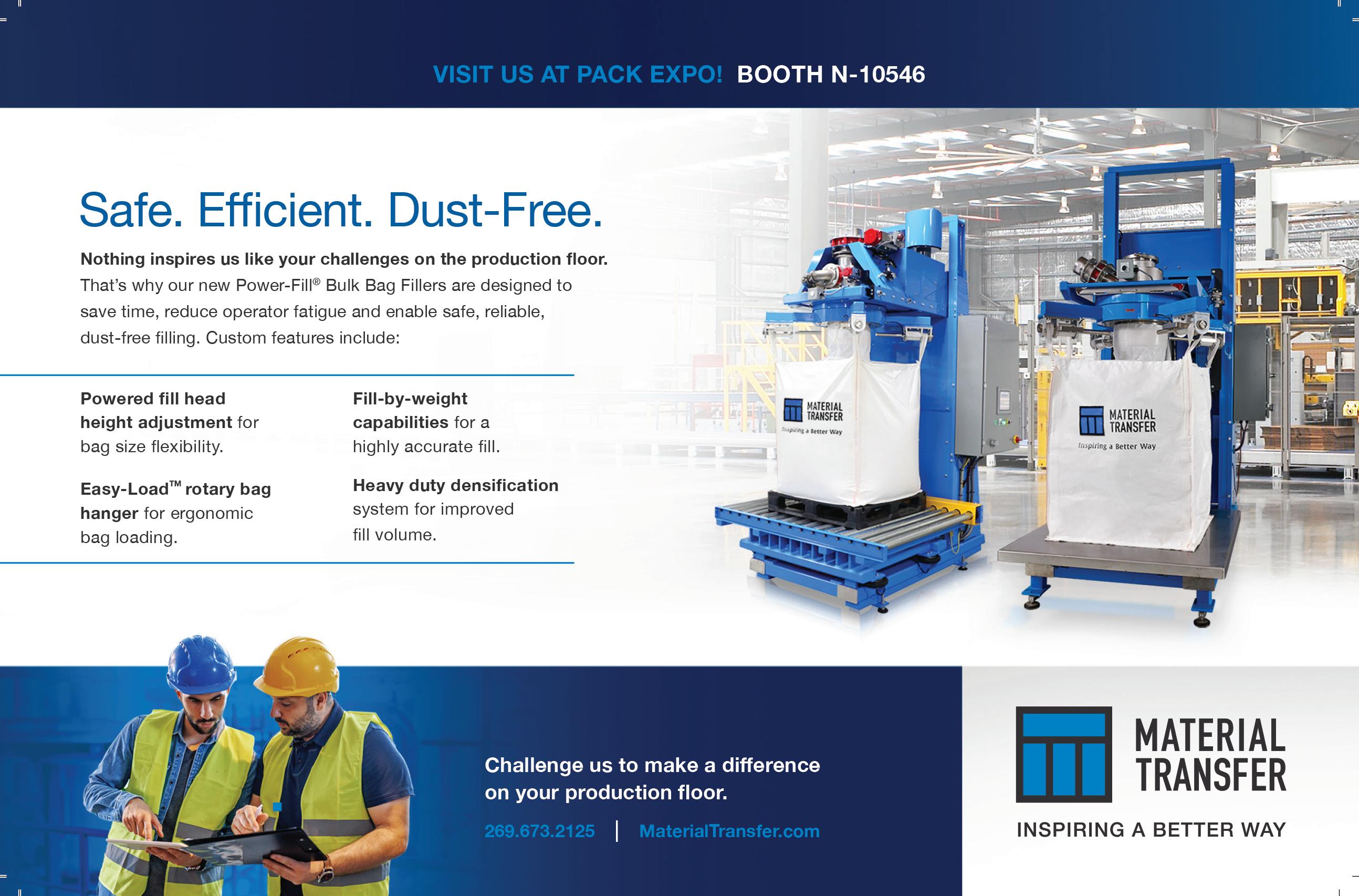
Operator training is an important piece of the Redzone software as well, Whitehair says, commenting about the ability to include short videos in the system, as well as manuals, all of which can be customized to an individual and their comfort level with various types of learning.
“The tool really engages your employees—the daily direction setting, the communication, getting them to feel comfortable because you’ve got these places to go to if you forget something. You can go and watch a short video even on your workstation or
2023 Manufacturing Innovation Awards set for PACK EXPO Las Vegas
The presentation of ProFood World ’s seventh annual Manufacturing Innovation Awards is planned for Tuesday, Sept. 12, during PACK EXPO Las Vegas.
Here are the 2023 winners: n SunOpta—A new facility in Midlothian, Texas, is dedicated primarily to co-manufacturing plant-based milk alternatives, teas, whey-based protein shakes, and other beverages. n Prestage Foods of South Carolina—The 295,000-sq-ft greenfield project in Camden, S.C., is a state-of-theart turkey processing facility that follows a European air-chill processing model. n MyForest Foods—In Green Island, N.Y., the new vertical mycelium farm is the world’s largest of its kind, changing the way food is produced and looking to scale quickly for its MyBacon plant-based bacon. on your handheld tablet,” Whitehair says. Another piece of the software is maintenance, and also quality control. “All of our quality testing, all of that record keeping, will be done within Redzone,” Whitehair says. “It makes the KPIs, the training, the maintenance, and the quality a onestop shop and makes us a virtual shop floor. We built that into the design in the beginning, but we’re already rolling that out in our other plants.
Come hear discussion of all three award-winning projects on the Processing Innovation Stage at PACK EXPO Las Vegas. For more information or to register for the show, visit www.packexpolasvegas.com.
Look for plant profiles about MyForest Foods in the June 2023 issue of ProFood World and Prestage Foods in the upcoming December issue.
The plant’s enterprise resource planning (ERP) is connected to an Oracle system, enabling tracking from farm to fork (or glass). “They’re all traced all the way from the time that we got the raw material and lot numbers, the SKUs, to which piece of equipment it’s going, whether it’s going into a certain tank, certain mixer, certain processor, certain filler line—all the way it’s traced and tracked,” Neti says. “For whatever reason, if things don’t go as well as they should, we would want to know what lot it was, how much did we make, which equipment it was made on. It helps significantly with troubleshooting and during the process.”
Though this traceability has in part to do with regulations around the Food Safety Modernization Act (FSMA), SunOpta aims to push beyond just compliance. “We also continue to try to raise the bar. Our customers are helping us to continue to raise the bar around food safety,” Whitehair says. “We’ll take best practices from an auditor—whether a customer audit or SQF audit or something we learn through the industry—and try to apply it in our plants. With aseptic, you have very little room for error.”
Sustainability designed throughout
SunOpta estimates that its new strategic location in Texas will save the company 15 million freight miles annually and save 59 million pounds of carbon emissions. The plant itself is designed to reduce carbon emissions, conserve water, use power efficiently, and make use of recycled materials.
SunOpta purchased two cooling water skids from Tetra Pak so they could reuse water for cooling instead of disposing of it. When running at full capacity, the water reuse equipment will save close to 20 million gallons per year.
Utility systems throughout the plant were designed to be energy-efficient. A reverse osmosis (RO) system that was installed for ingredient water is also used to supply feedwater to the steam boilers. Using purified RO water for the boilers rather than a soft water system reduces blowdown of chemically treated hot water by about 900,000 gallons annually. The steam boilers have blowers equipped with variable-frequency drives (VFDs), which results in a higher turn down ratio by better matching the load for each individual batch. Both of the two steam boilers have an economizer to recover heat.