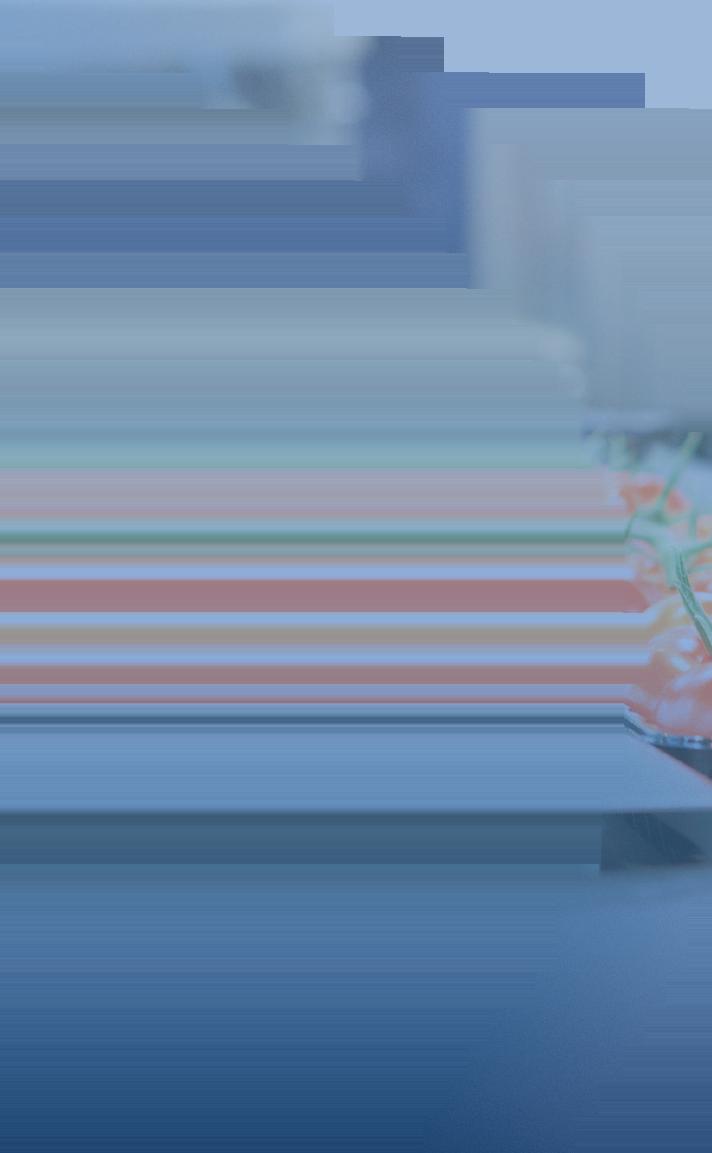
3 minute read
FOOD PROCESSING MAINTENANCE SOLUTIONS
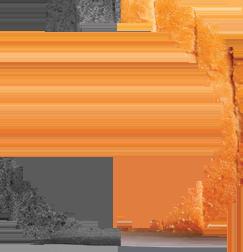
For over 60 years LPS® has earned a reputation for both quality and performance in critical industrial applications. LPS® DETEX® combines that expertise with food safety programs to produce a full line of maintenance solutions specifically formulated for food processing facilities.
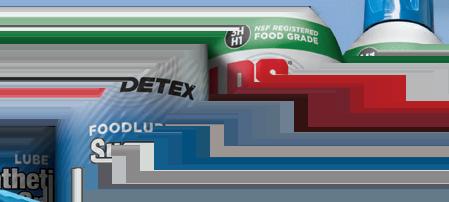
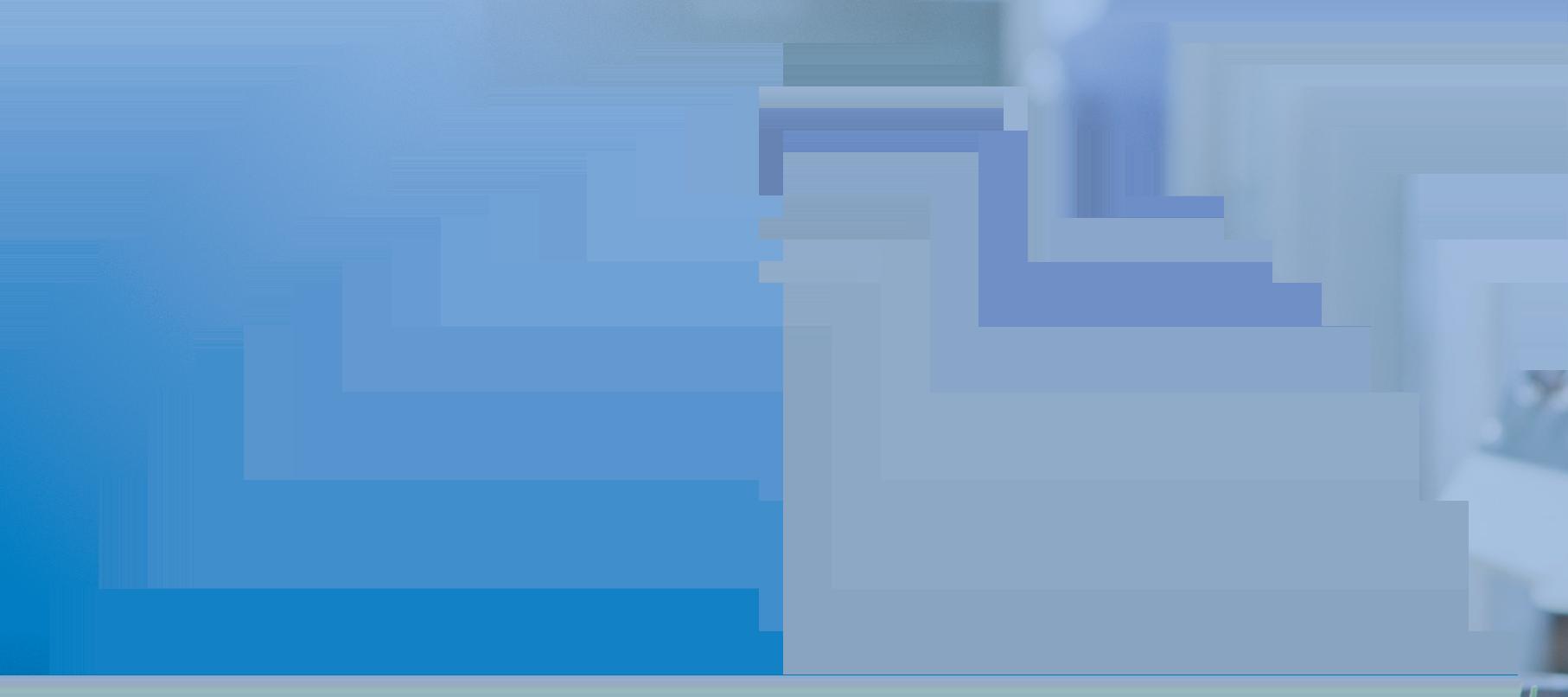
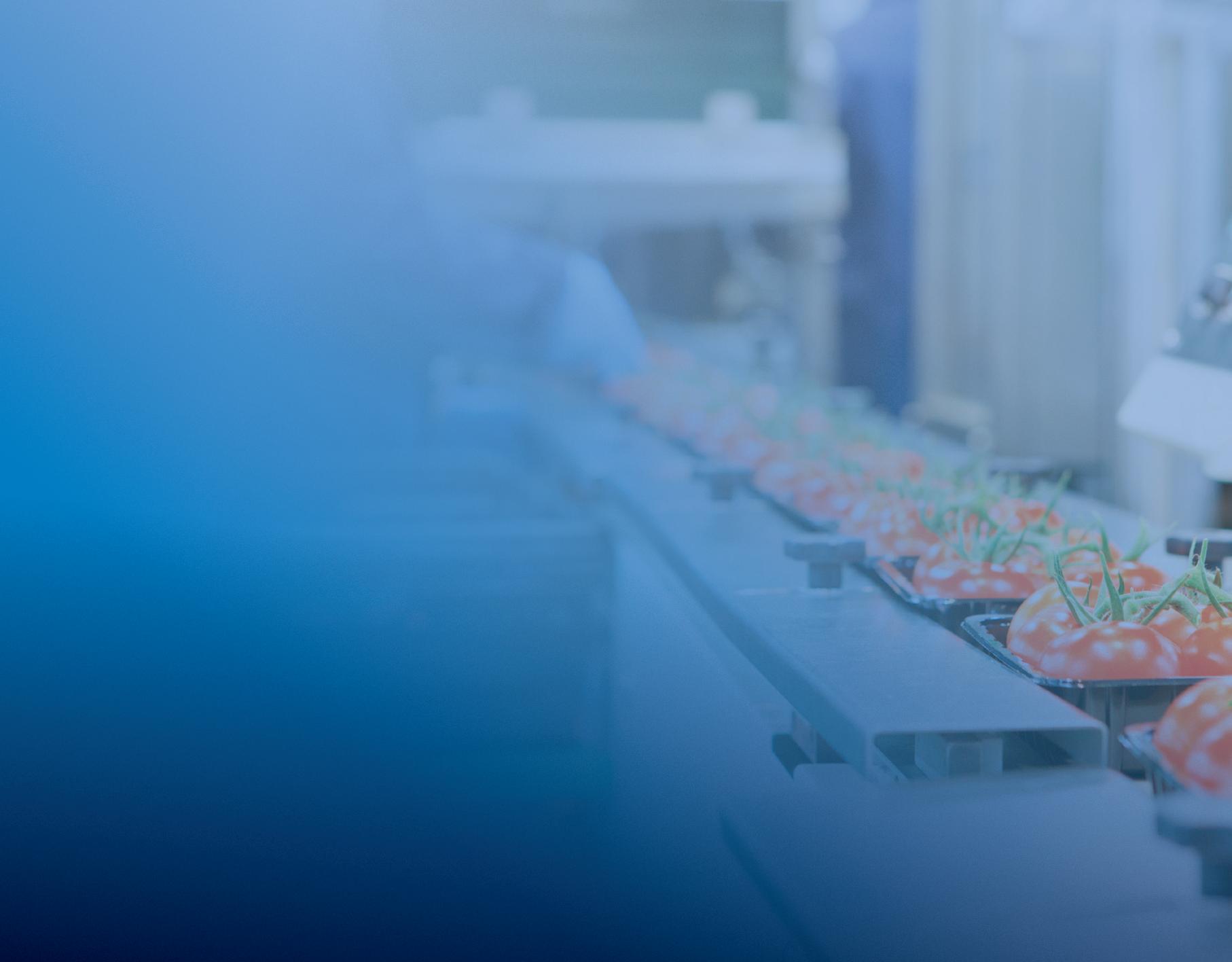
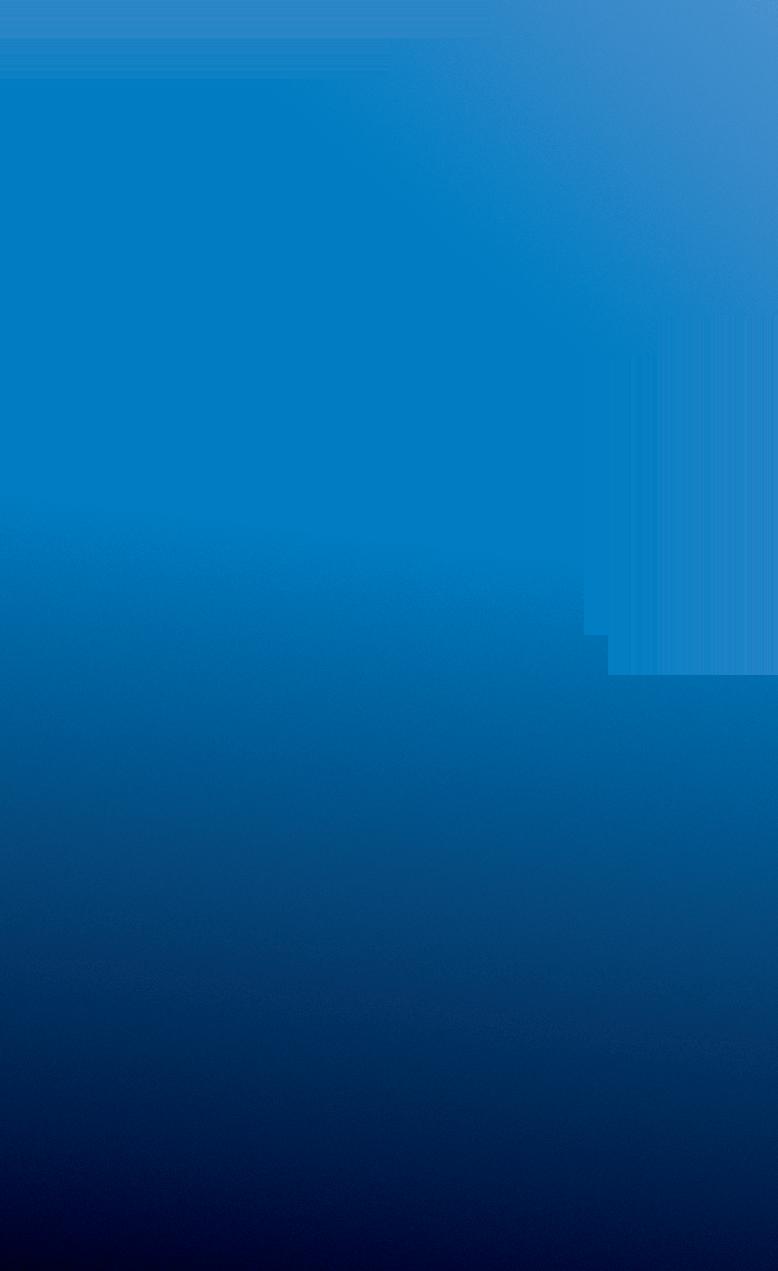
LPS® DETEX® lubricants, penetrants, electronic cleaners, and greases save time and money by extending equipment life, reducing repair time, and lowering frequency of preventative maintenance.
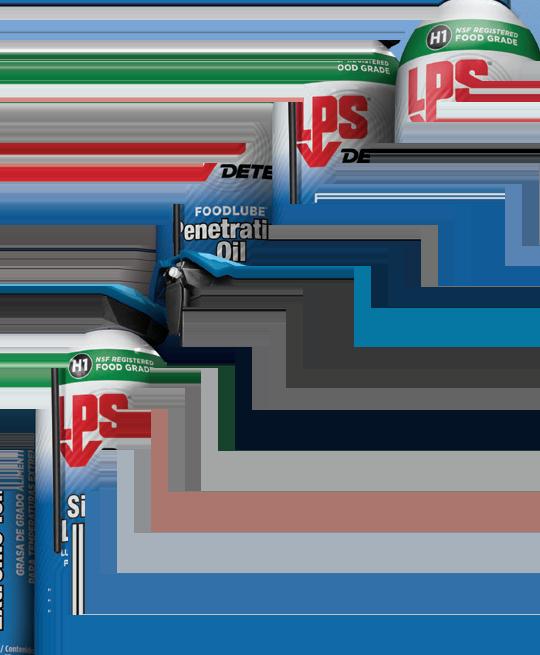
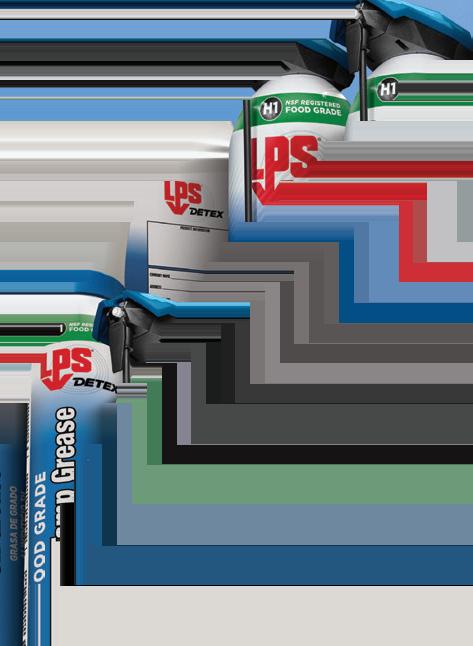
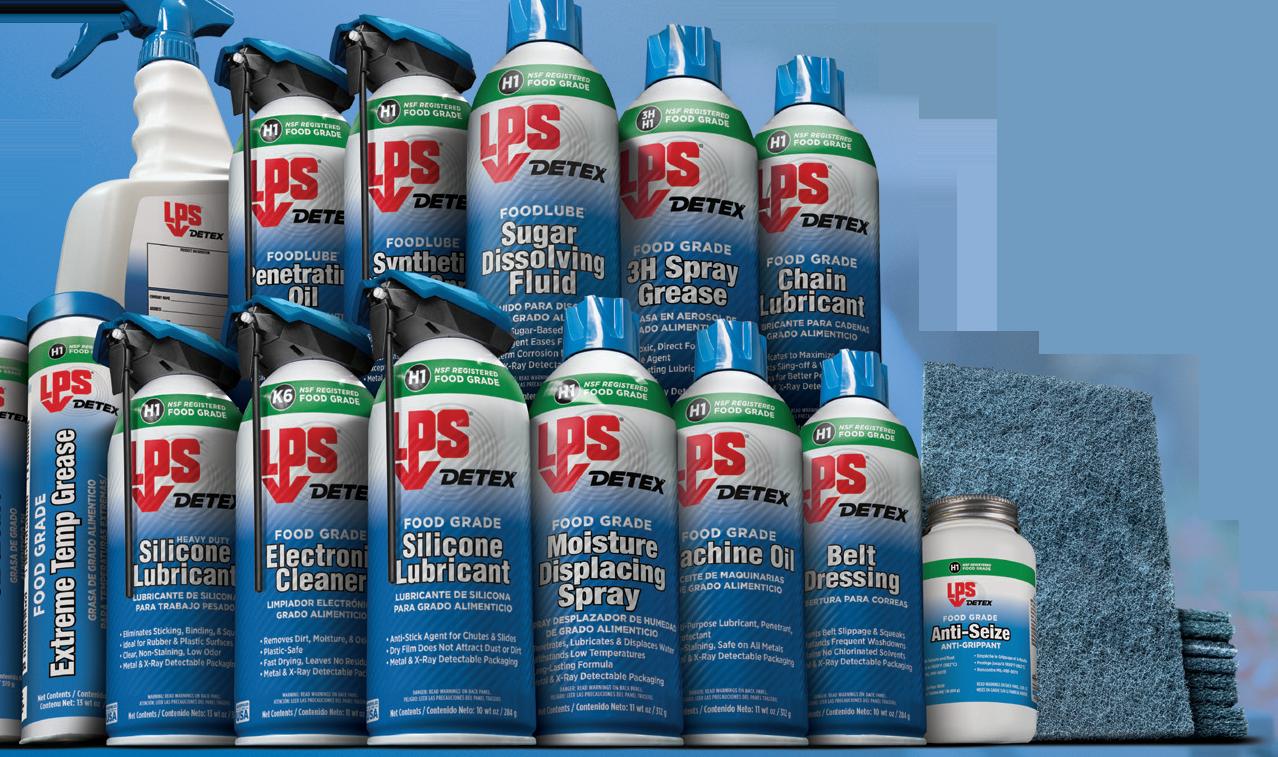
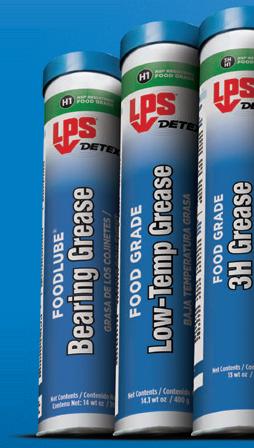
Plastic components used to package LPS® DETEX® products are both metal & X-ray detectable, helping to reduce the risk of foreign object contamination within your facility.
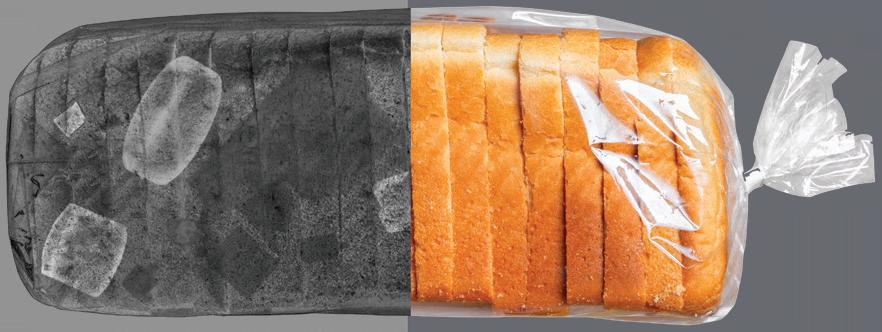
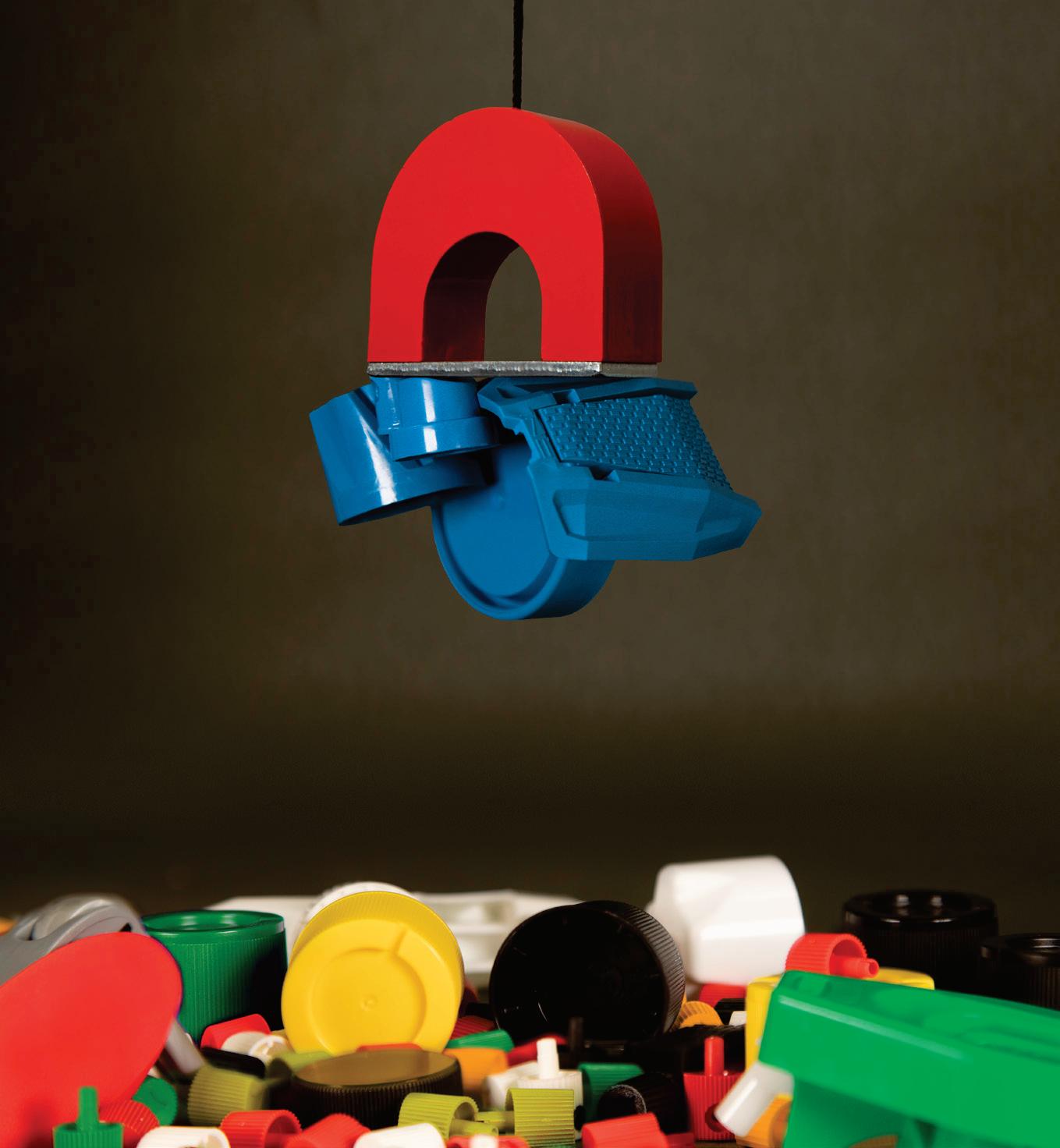
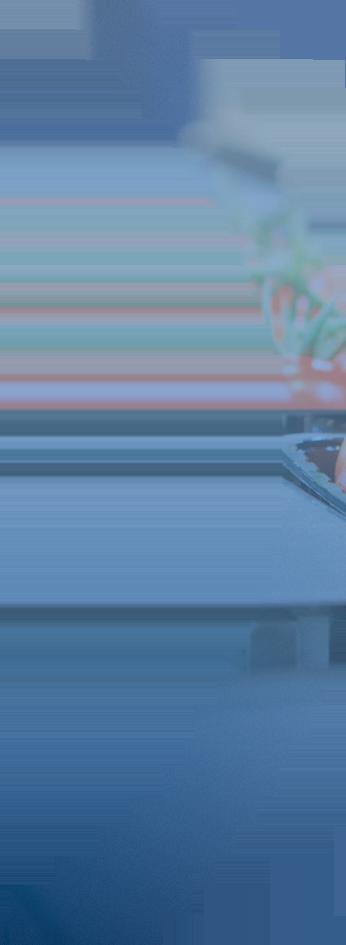
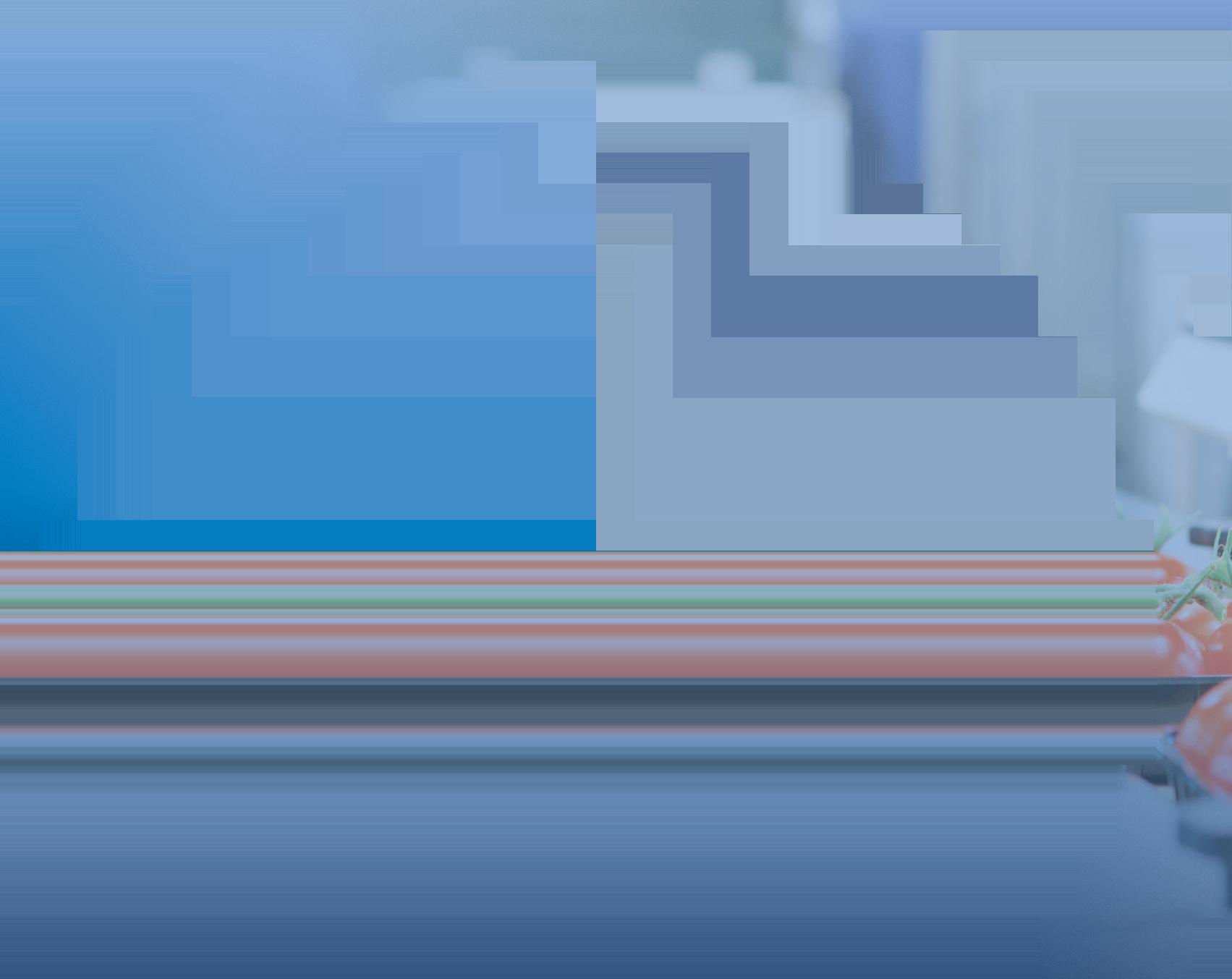
Metal Detectable

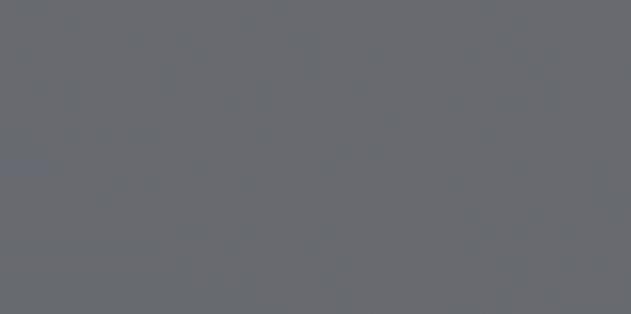
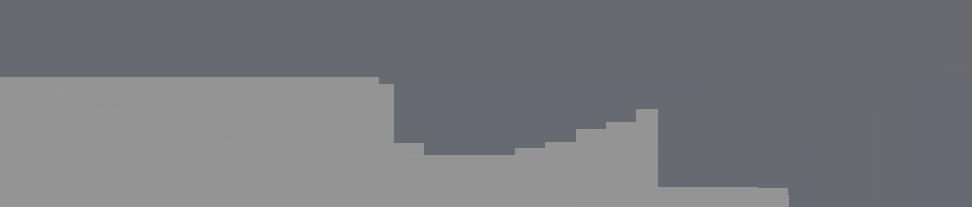
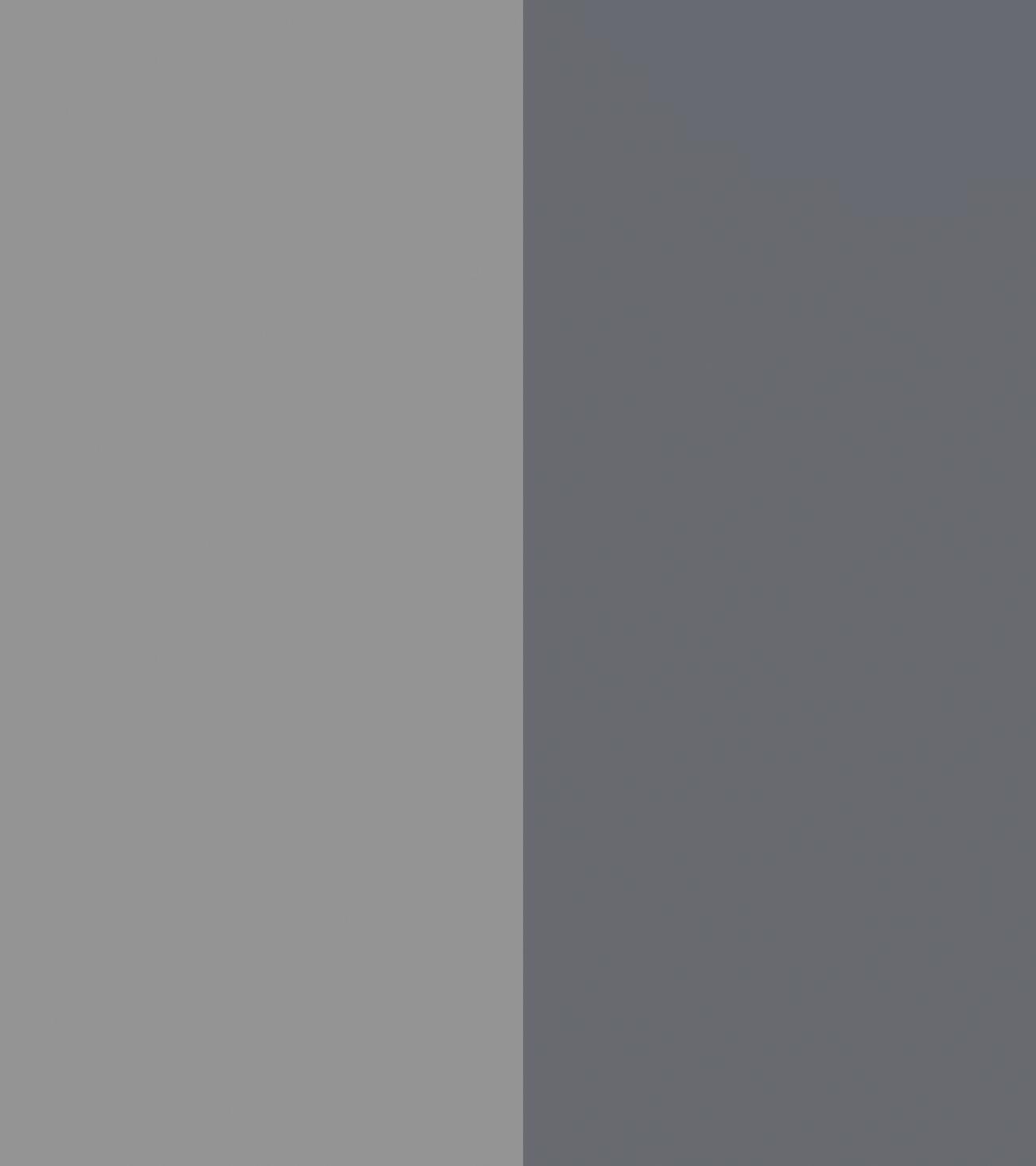
X-RAY DETECTABLE
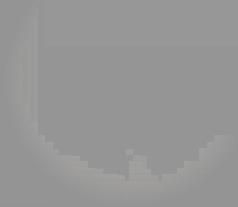
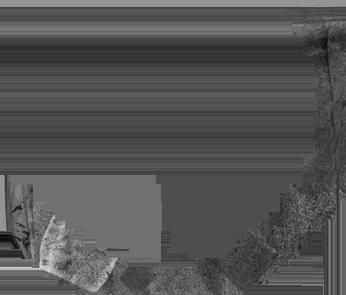
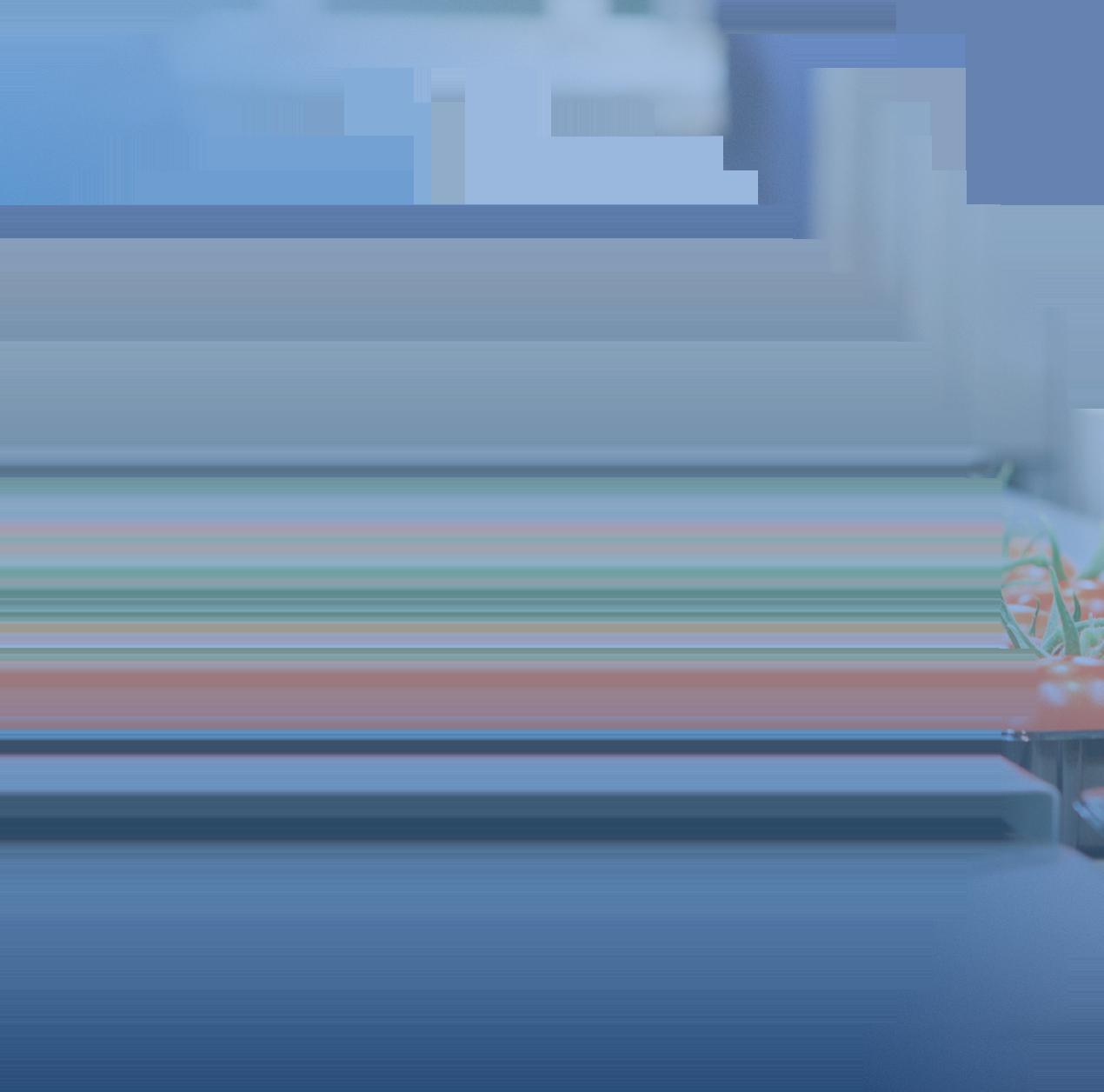
An ammonia-refrigerated cold glycol system was selected for both air handling and process cooling. Using a central ammonia refrigeration plant for building cooling is more energy-efficient than using individual freon-based air handling units. During periods of cooler ambient temperatures, the control system turns off the condenser water circulation pumps and modulates fan speed to save energy based on external conditions such as humidity and temperature. Larger condenser equipment was installed for the ammonia refrigeration system to lower the system head pressure. The speed of the compressors can be varied so the system matches process load for improved efficiency. A fully redundant ammonia compressor was also installed to avoid process downtime.
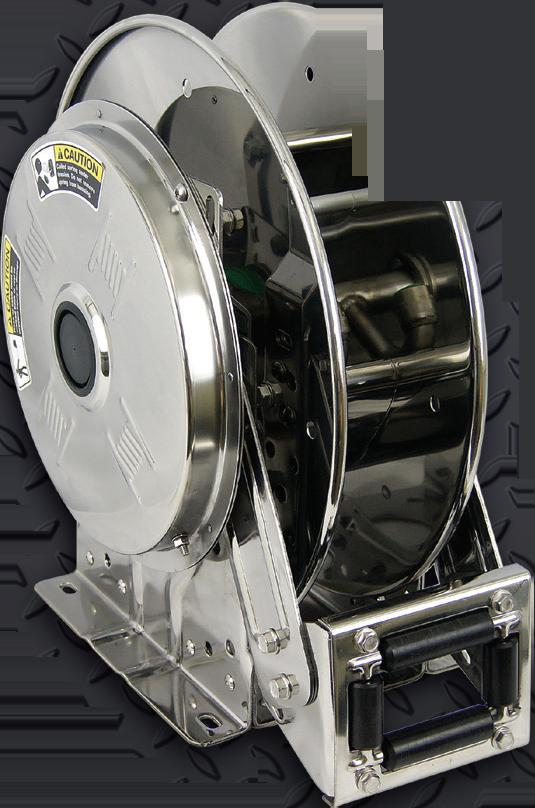
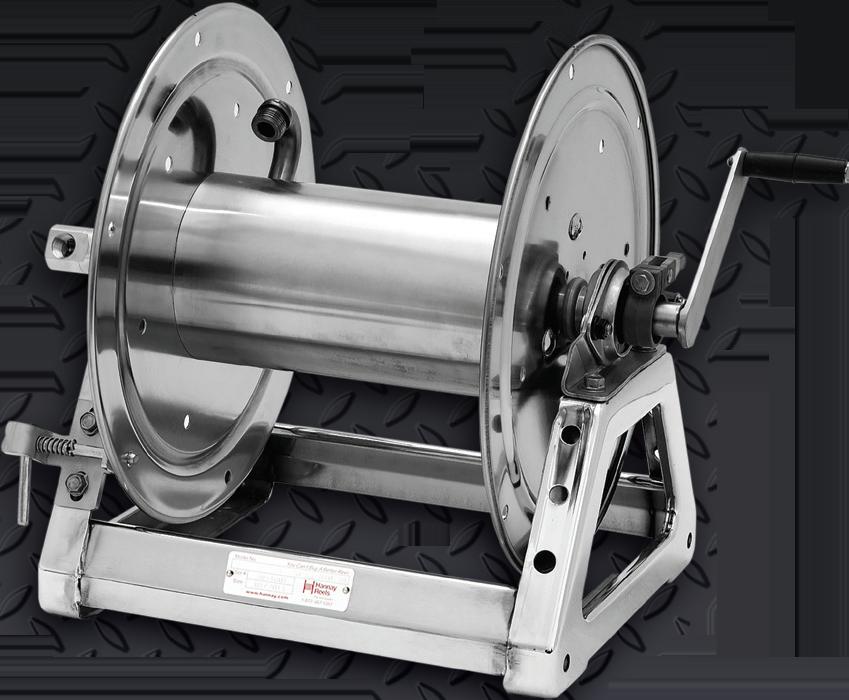
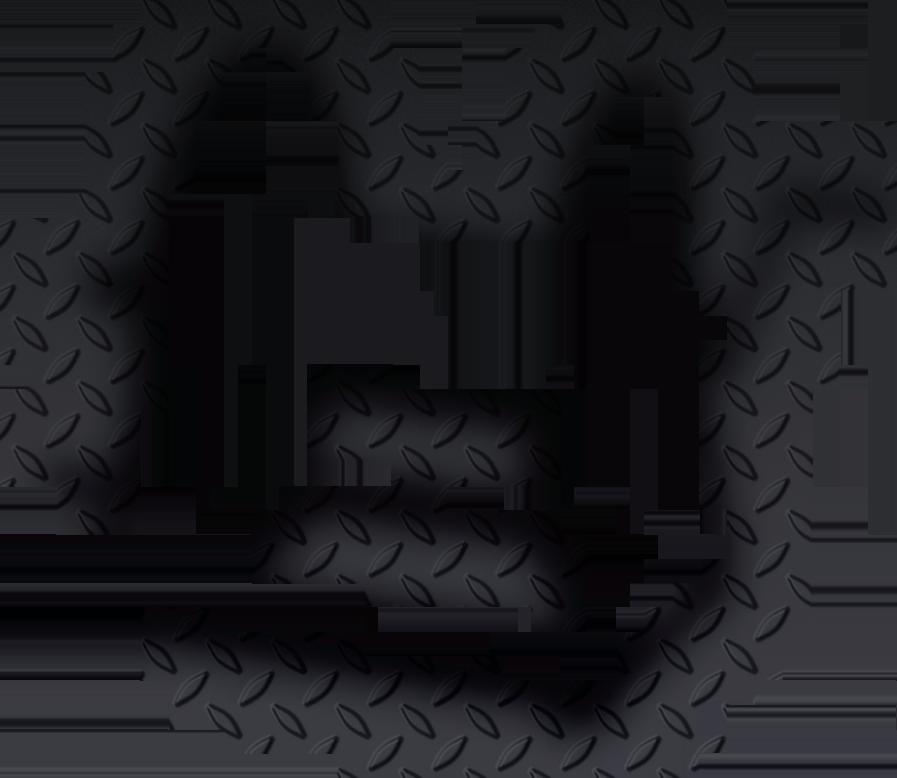
Wastewater treatment on site
With all the new homes and businesses being built in the area, it was important for SunOpta to make sure that the facility had the electrical load, gas, and other utilities available for operation. Wastewater capabilities in the area couldn’t handle what the new facility would produce, so SunOpta spent about $6.5 million dollars on a wastewater treatment plant of its own. “If we hadn’t spent upfront to invest in our own wastewater treatment plant, we would not be running today,” Whitehair says.
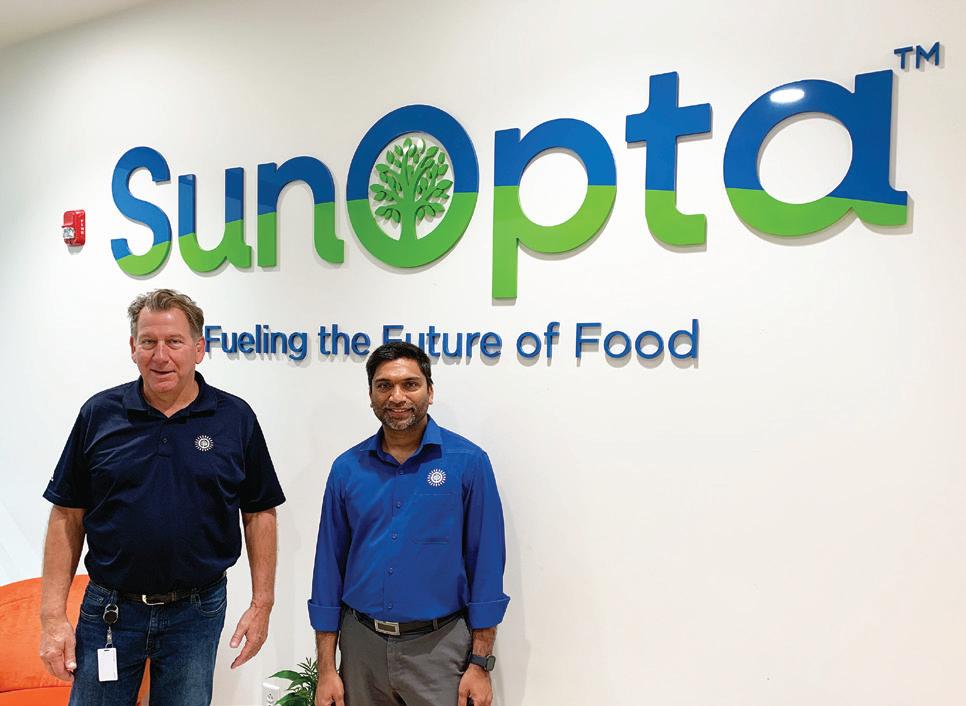
The local water authority, a private entity called Trinity River Authority, had a wastewater treatment capacity of 3 million to 4 million gal/day (MGD) of domestic-strength wastewater at 150 mg/L biochemical oxygen demand (BOD). Since SunOpta’s effluent at 5,000 mg/L BOD was almost equal to the total capacity of the municipality, a full membrane bioreactor (MBR) system was required. The biological system treats down to discharge-quality water, or less than 8 mg BOD per liter. The system, which can handle 240,000 gallons per day, will allow SunOpta to use reclaimed water for various purposes in the plant.

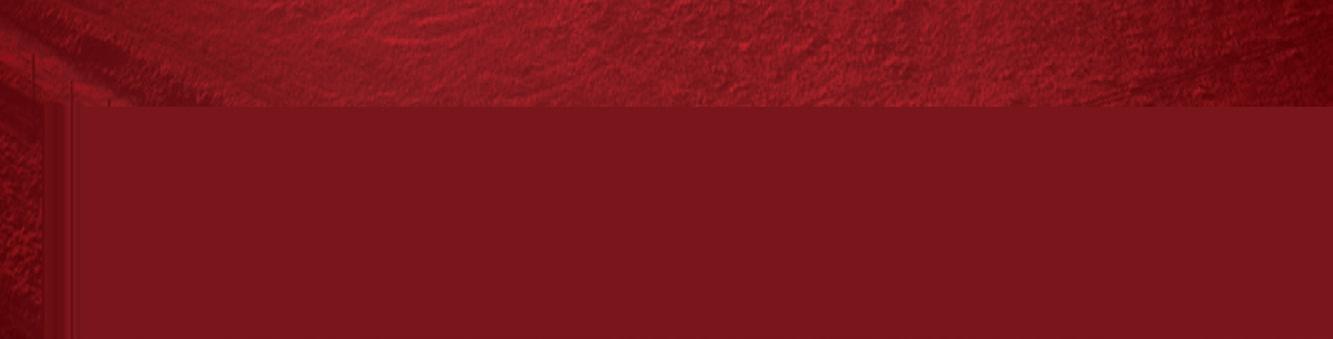
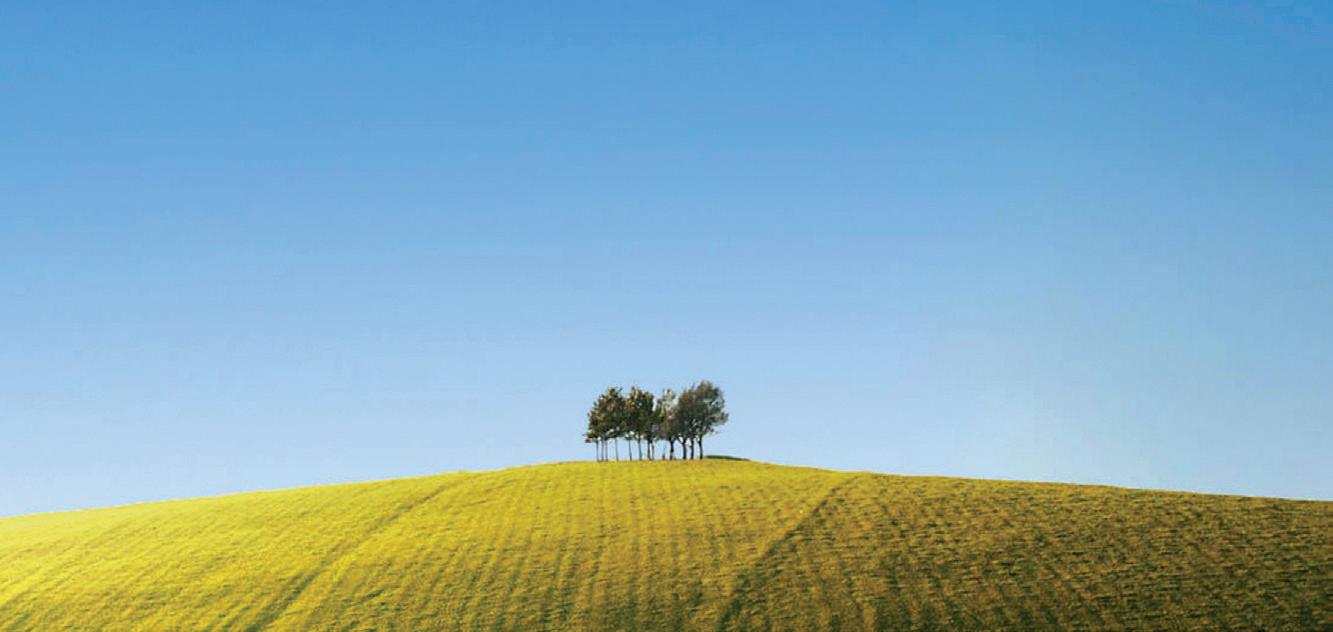
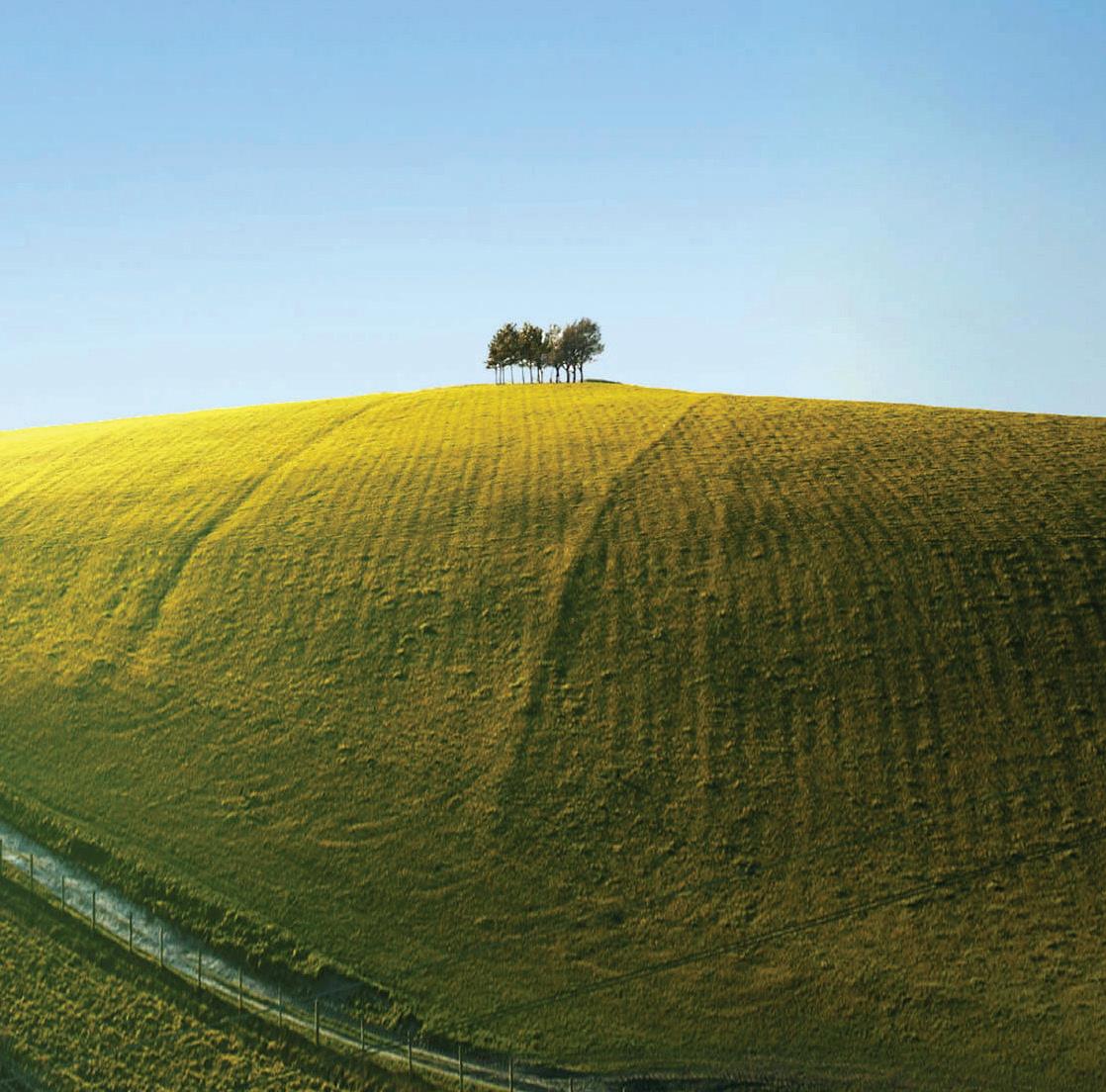
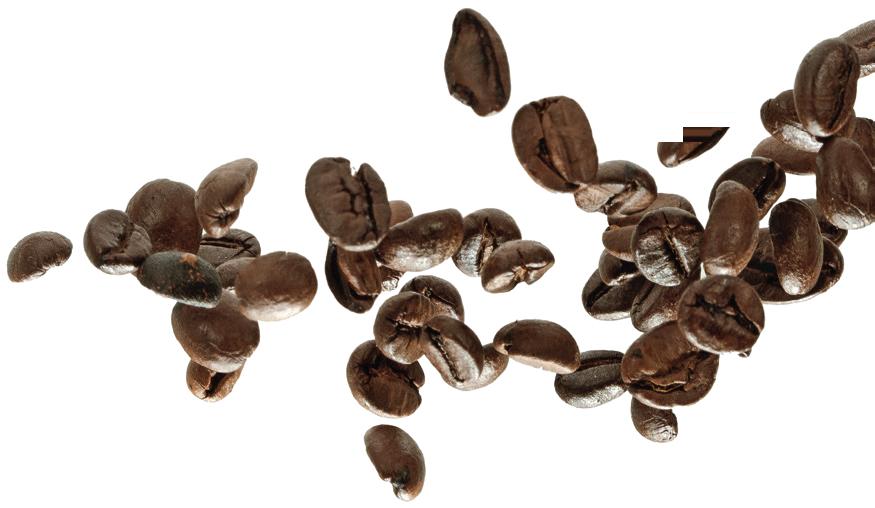
SunOpta also has an option to obtain a surface discharge permit in the future, completely removing any reliance on the limited capacity of the public wastewater system. The system has dissolved air flotation (DAF) for pre-treatment and uses a centrifuge for dewatering, which reduces the sludge to 22% solids. This method reduces hauling costs by about 85%. Bio solids are stored in bins, which further defrays hauling costs by reducing the number of trips.
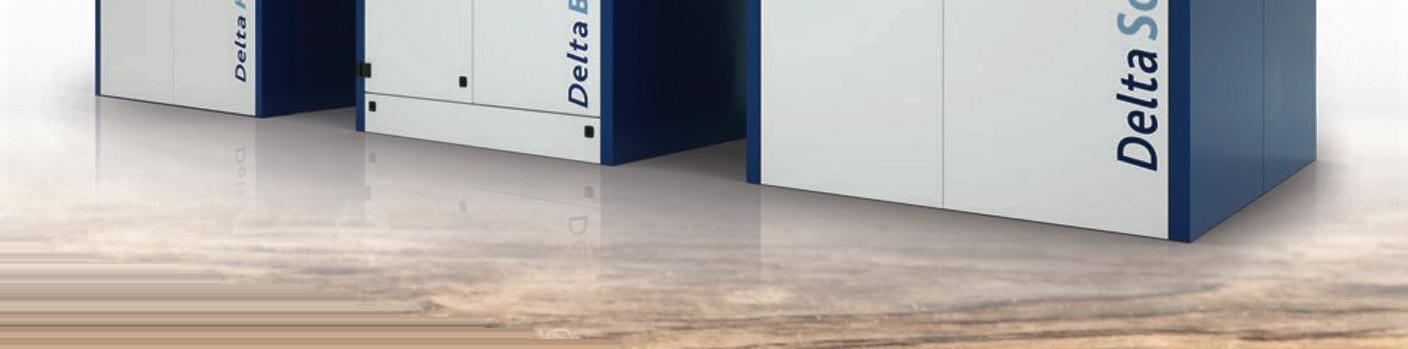
“The investment made is also part of the social responsibility from a sustainability standpoint. The water we discharge today is as good as the water we have coming in, or better at times,” Neti says. “That takes a lot of money to invest to do that. But it fits into our SunOpta sustainability model to make sure we take care of the community, employees, customers, at the same time as the environment”
Built for expansion
SunOpta purchased the 32-acre site in Midlothian with a view toward future expansion. The facility is currently running two lines but can easily double capacity without any building or utility expansions. As part of a longer-term plan, the site is suitable for another 150,000 sq ft of building expansion, and site work—including the placement of fire lanes and the wastewater building—were all designed around that.
At the same time that the new plant gets the advantages of a clean slate, it also has the advantages of corporate resources from existing SunOpta facilities. Whitehair points to the company’s large pilot lab at its headquarters in Eden Prairie, Minn., for example. “A lot of the front-end work can be done there, but we’re also taking the learnings from the other plants,” he says. “SunOpta can learn four times faster because we have four plants operating instead of just one. We’re constantly sharing best practices and learnings, either from our corporate pilot lab or the four other plants. I think that’s really helped us accelerate our improvements.”
The Midlothian plant has had buy-in at every level of the corporate organization. “Early on, when we told our entire company that we were going to spend $125 million on this plant, it was going to be every one of our jobs to make sure that this startup is successful. Having been here a lot for the last couple of years, you truly see it every day—whether it’s the people we can send to a plant to get trained, or the people who have come here to help provide support during startup or training,” Whitehair says. “It’s fun to watch that collaboration and sense of ownership that you get from every level in the company.”
For 100% product purity and safety solutions visit: www.aerzen.com/en-us
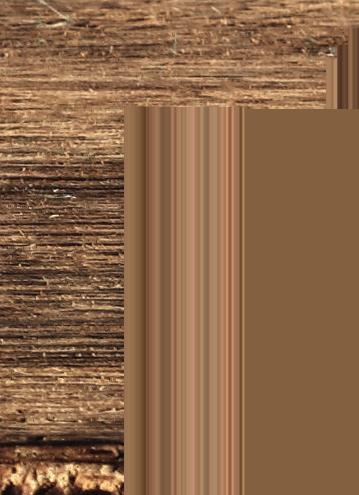
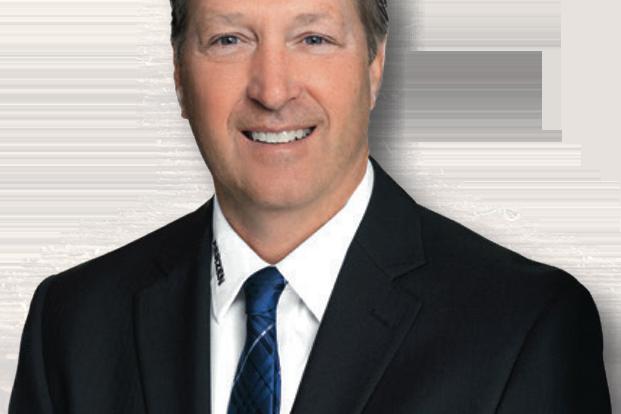
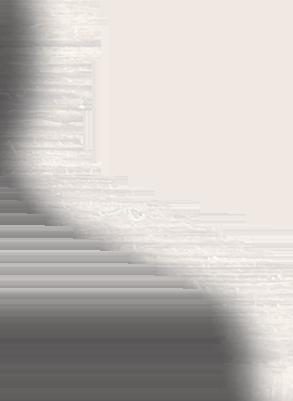

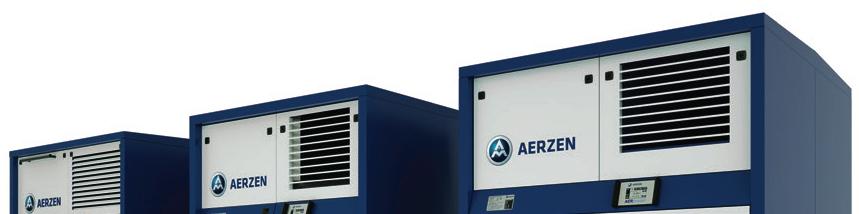


JEANNE SCHWEDER | CONTRIBUTING EDITOR