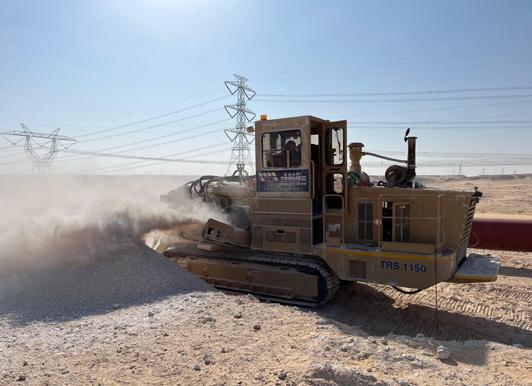
4 minute read
Strategic Excavation
by Pedemex BV
Tesmec’s Pioneering Methods for Underground Utility Detection
Flavio Villa, CTO, Tesmec BU Trenchers & Surface Miners
A recent pipeline installation project in Saudi Arabia highlights Tesmec’s extensive capabilities within the pipeline sector.
This ambitious endeavor involved the installation of a 40-inch (1016 mm) pipeline across challenging terrain, including hard limestone rock, marl, and sand, while simultaneously navigating a complex network of existing utilities and infrastructure. Tesmec’s advanced technology and comprehensive service model enabled precise and safe excavation in this intricate environment.
Tesmec ensures the success of pipeline projects through thorough terrain assessments and feasibility studies, utilising advanced technologies like ground-penetrating radar (GPR) and drones to identify obstacles and streamline planning. By offering comprehensive support throughout every project stage and maintaining a global presence, Tesmec positions itself as a reliable partner in the pipeline sector.
Project Challenges and Unique Terrain Conditions
The project faced a remarkably high density of utility crossings, which included 62 above-ground pipes, 156 underground pipes, and 41 underground cables, in addition to multiple roadways such as a highway, five asphalt roads, and thirty-three marl roads. In total, the pipeline corridor comprised an impressive 379 crossings along the pipeline route. Given this complexity, traditional excavation methods, such as drilling and blasting, were prohibited due to the proximity of existing infrastructure. As a result, Tesmec’s specialized chainsaw trenchers, designed to minimize vibrations, emerged as the ideal solution, allowing for safe operation near existing utilities without the risk of damage.
Advanced GPR Mapping and Utility Detection
To effectively navigate this intricate utility network, Tesmec employed advanced ground-penetrating radar (GPR) in conjunction with differential GPS technology. While maps of known crossings were available, realtime utility detection was essential to prevent costly errors during excavation. The GPR surveys, enhanced by post-processing software, produced high-resolution, three-dimensional maps of the subsurface environment, enabling the Tesmec team to accurately locate utilities with impressive precision.
The GPR technology utilised featured utility detection capabilities operating at frequencies of 600-1000 MHz, achieving penetration depths of up to 4 metres. For geological analysis, high-penetration radar at 80 MHz was employed, reaching depths of up to 5 metres. This dual approach allowed for the identification of geological layers critical for planning trench dimensions, while GPS integration provided exact coordinates for utility mapping and trenching. As a result, Tesmec was able to generate AutoCAD drawings with accurate utility coordinates, which proved essential for adjusting excavation plans when deviations in utility placement were discovered, including instances where some utilities were located up to 7 metres away from their mapped positions.

Efficient Trenching with the Double-Cut Technique
To meet the project’s unique demands, Tesmec implemented its innovative double-cut trenching method in the rocky sections of the pipeline route. This systematic approach involved initially excavating a trench, backfilling it with the excavated material, and then creating a parallel trench, followed by the removal of the central ribbon with an excavator. The pipeline specifications required trench widths of 1420 mm
x 2110 mm in sandy areas and 1620 mm x 1267 mm in rocky conditions. To comply with the client’s request for low ground pressure, Tesmec utilised smaller trenchers, which necessitated the double-cut technique to achieve the required trench width in multiple passes. In less challenging sections, conventional excavators were employed to enhance efficiency.
Performance and Results
Despite facing strict regulatory controls and a challenging landscape, Tesmec’s trenchers achieved remarkable production rates. In sandy and marl areas, the team managed to complete an impressive 210 metres per day, while in rocky areas, the production rate was 82 metres per day. The project adhered to a rigorous timeline, with trenching operations commencing on 15 October 2022, and concluding on 29 January 2023, while maintaining stringent quality and productivity targets. Although work permits and regulatory compliance limited daily excavation hours, Tesmec’s team demonstrated adaptability, ensuring consistent project momentum.
Tesmec’s Advantage as a Pipeline Partner
This case study of the Saudi Arabian pipeline project underscores Tesmec’s leadership in delivering comprehensive pipeline solutions. Through innovative utility detection, precise trenching methodologies, and a commitment to end-to-end support, Tesmec maximises safety, productivity, and cost-efficiency. With its global reach and local expertise, Tesmec stands as a trusted partner for clients navigating the complexities of pipeline infrastructure projects worldwide, solidifying its position as a leader in the industry.