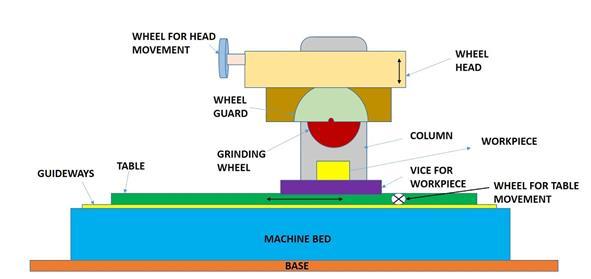
2 minute read
Surface Grinding
Surface Grinding
Surface grinding process is generally the most common grinding techniques. The term surface grinding
Advertisement
assign that any process which accurately processes or grinds a surface. Surface grinding methods are
included horizontal spindle, vertical spindle, vertical spindle rotary grinding, vertical spindle single disk
and vertical head grinding. Parts or workpieces may require a grinding process if there is a need to
produce a flat surface with accurate thickness tolerance. Surface grinding also able to provide a part
with specified and very smooth surface roughness. Surface grinding can be used for cutting tool
sharpening. Surface grinding is used primarily for grinding and to obtain a desired flat surface finish or
smoothness, precise angularity, perpendicularity and flatness tolerances. Surface grinding machines and processes where first developed to manufacture and removed material from very hard metals.
A surface grinding machine normally consists of a magnetic chuck, which resembles a table,
the grinding wheel that is attached to a rotating spindle, and a few handwheels for manually
operated. A straight wheel is mounted on the horizontal spindle of the grinder. Transverse grinding
occurs as the table reciprocates longitudinally and feeds laterally after each stroke. Surface grinding
machine and all parts includes is illustrates in a diagram of Figure 9. The grinding wheel used is
depends on the component being ground. Different grinding wheel compound for different type of
material to be ground.
Figure 9. Parts of surface grinding machine, 2020, Retrieved from https://www.youtube.com/watch?v=mGR7oszv9SE/
On the surface grinding machine, the workpiece is placed on a magnetic chuck attached to a worktable
of the grinder. The chuck is activated either by a switch or lever. When the chuck is activated, the part
will then hold firmly to the magnetic chuck. Non-magnetic workpieces are held by vices or fixtures.
The workpiece mounted on either a reciprocating or a rotary table is brought into contact with the
grinding wheel. The workpiece will be feed in horizontal direction, below the grinding wheel, with the
help of fed table. The abrasive grinding wheel rotates on a spindle and runs generally above the
workpiece. This produces the desired surface finish along with the ability to grind to extremely high tolerances, with typically + /-0 .0001” or + / – 0 .002 mm. Once the grinding wheel is touching the
workpiece surface, the worktable is set to move side to side and front to back until the entire surface
of the part is ground. The movement of worktable is repeat with the grinding wheel brought close to
touch the workpiece surface until the desired dimension is accomplished. The illustration of workpiece
attached on the worktable and how the grinding wheel is positioned above the workpiece is shown in
Figure 10 below. Figure 11 shows the actual setup of workpiece material on a surface grinding
machine with grinding wheel located above to workpiece to be ground. There are sparks generate just
after the grinding wheel rotated in high speed and touched surface of workpiece.
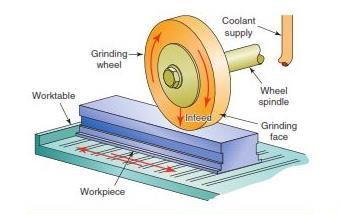
Figure 10.Position of workpiece on the worktable and grinding wheel is above the workpiece, 2015, Retrieved from https://cadcamengineering.net/types-of-grinding-machines/
Figure 11.Surface grinding operation produce sparks on the surface of workpiece, 2018, Retrieved from https://www.mech4study.com/2018/12/grinding-machining-process-complete-notes.html/
