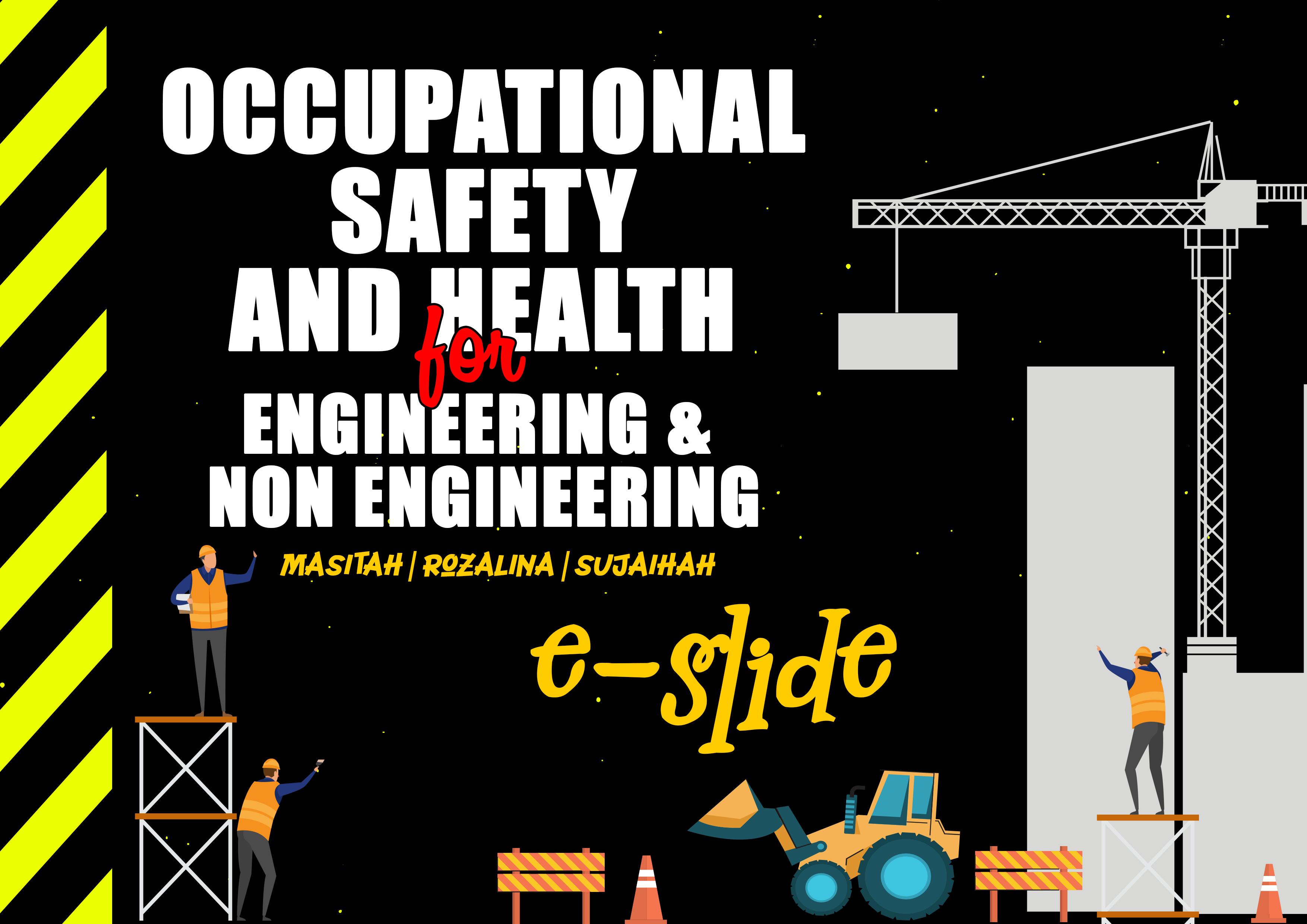
Masita Binti Hassan
Rozalina Binti Ab Rashid
Sujaihah Binti Razali
OCCUPATIONAL SAFETY AND HEALTH FOR ENGINEERING & NONENGINEERING
Rozalina Binti Ab Rashid
OCCUPATIONAL SAFETY AND HEALTH FOR ENGINEERING & NONENGINEERING
Politeknik Sultan Haji Ahmad Shah, 25350 Kuantan, Pahang
All right reserved. No part of the publication may be reproduced or distributed in any form or by any means, or stored in a database or retrieval system, without prior written permission of the solely private publisher as stated above.
This E-Book was created in collaboration with three authors: Masitah Hassan, Rozalina Rashid and Sujaihah Razali. First and foremost, thank to God the Almighty, we were able to successfully complete the task of producing the Safety and Health for engineering and Non-Engineering E-Book. With this opportunity, we would like to express our special thank and gratitude to the Head of the Civil Engineering Department, who has given us this golden opportunity to produce this
E-Book. The completion of this book would not have been possible without the assistance of the Civil Engineering Department’s E-Learning coordinator, Mr Saiful
Hazman bin Mokhtar for whom we are extremely grateful. Last but not least, to our loving, devoted and encouraging family members, we sincerely appreciate you. Your inspiration when thing got difficult are greatly appreciated and appropriately noted.
Occupational Safety and Health for Engineers teaches self-regulation concepts and provisions under the Occupational Safety and Health Act of 1994. This book is intended as additional reading material for polytechnic engineering and nonengineering students. The contents of this book are relevant to the most recent syllabus for all engineering and non-engineering programmes. This book focuses on responsibilities. Employers and employees are both responsible for implementing and adhering to workplace safety procedures. The book provides an overview of the Occupational Safety and Health Management System, Incident Prevention, Hazard Identification, Risk Assessment, and Risk Control (HIRARC). The book also includes information on fire safety, workplace environment, and ergonomics, with the goal of guiding students to a better understanding Occupational Health and Safety.
An Act to make further provisions for securing the safety, health and welfare of persons at work, for protecting others against risks to safety or health in connection with the activities of persons at work, to establish the National Council for Occupational Safety and Health, and for matters connected therewith. (25th February 1994)
Enacted by DYMM Seri Paduka Baginda Yg Dipertuan Agong with advice and consent of Dewan Negara and Dewan Rakyat.
Guideline used by public or private companies in preparing and promoting safety and health policies in the workplace
Cultivates safety and health awareness among employers and employees by giving the guidelines to promote , prompt and encourage a high standard of OSH at the workplace.
Helps to ensure that everyone , especially employers and employees become more responsible in creating a safe working environment.
Provides general duties for the employer, a self-employed person, the designer , the manufacturer and the supplier, the provisions of appointing officers and establishment of National Council, policy development and the preparation of OSH measures, enforcement, the role of investigators and the liabilities of the offense.
It protects employees and the employer from death or injury.
It teaches workers how to work in a safe environment.
It prevents companies from lawsuits.
It keeps everyone feel safe and happy. It teach
It teaches the workers to pay attention to their surroundings.
LEGAL
The Act: General rules which are dependent upon Parliament’s approval and the King’s consent.
The Regulation : Detail of an act and endorsed by Minister
Industry Code Of Practice (ICOP): Any code, standard, rule and specification to support the Acts and regulations. It serves as a guideline for the general requirement and enables legislation to be kept up-to-date through content revision.
Guidelines: Documents that present opinions on good practice which have no legal force.
To secure the safety, health and welfare of persons at work against risks to safety or health arising out of the activities of persons at work.
To protect persons at a place of work other than persons at work against risks to safety & health arising out of the activities of persons at work.
To promote an occupational environment for persons at work; which is adapted to their physiological and psychological needs.
To provide means whereby the associated Occupational Safety and health legislation may be progressively replaced by system of regulations and approved industry codes of practice operating in combination with provisions of the Act designed to maintain or improve the standards of safety and health.
General duties of employers and selfemployed persons to persons other than their employees.
Section 16 Duty to formulate safety and health policy.
duties of employers and self-employed persons to their employees.
15.2.(e) facilities for their welfare at work
15.(1) Safety, health and welfare at work of all his employees
15.2.(a) the provision and maintenance of plant and systems of work that are, so far as is practicable, safe and without risks to health
15.2.(c) the provision of such information, instruction, training and supervision as is necessary to ensure, so far as is practicable, the safety and health at work of his employees
15.2.(d) access to and egress from it that are safe and without such risks
15.2.(b) operation, handling, storage and transport of plant and substances;
be liable to a FINE not exceeding fifty thousand ringgit or
to IMPRISONMENT for a term not exceeding two years
or
Himself & other person while at work
24.1.(b) Co-operate with the employer or any other person in the discharge of any duty
24.1.(c) Wear & use PPE/safety equipment provided for preventing risks
24.1.(d) comply any instruction or measure on OSH instituted by the employer
Nom trade union shall take any action on any of its members who, being an employee at a place of work.
No employer shall dismiss an employee, injure him in his employment or alter his position if the employee:
Traditional approaches which stressed upon enforcement to prevent occurrence of occupational accident and disease at the workplace.
The objective of the Factories and Machinery Act (FMA) 1967 is to :
1. To provide for control of factories with respect to matters relating to safety , healthy and welfare of persons.
The registration and inspection of machinery
For matters connected therewith
Department of Safety and Health (DOSH)
National Institute of Occupational Safety and Health (NIOSH)
Department) under Ministry of Labour April 1994 – DOSH under Ministry of Human Resources
Main roles:
• To ensure the S&H&W of people at work from arising hazards in all activities at workplace
• To investigate all accidents, poisonous or dangerous occurrences in the workplace
• To administered and enforce the legislation related to OSH of the country
• To study and review the legislation and OSHA 1994 policies whenever necessary
• To provide advisory service and information to all agencies about the management and technical aspects of OSH
Established as a Company Limited by Guarantee under the Malaysian Companies Act 1965.
• Provide training and consultation services, to disseminate information and to conduct research in the field of OSH.
•
To provide social security protection by social insurance , including medical and cash benefits
• To give provisions of artificial aids and rehabilitation to employees in order to reduce suffering
• To provide financial guarantee and protection to the workers family
An Act relating to the prevention, abatement, control of pollution and enhancement of the environment, and for purposes connected therewith.
It also deals with the administration of the environment and towards the achievement of the national environmental policy.
The Act provides specific provisions with respect to licences, prohibition and control of pollution, appeal, delegation of powers and to make regulations for with respect to any matters to the environment.
The regulations are to provide a clearer picture and smooth implementation of the main Act. It helps the enforcement mechanism of the Act in terms of its rules, regulations and orders are subjected to interpretation, the capabilities of enforcement officers, their expertise and human factors.
Therefore, the awareness and fully understanding of the existing subsidiary legislation as provided by the Act is crucial for implementation and enforcement purposes.
Top management involvement and work organization
Consulting employees Assigning representatives to provide health and safety assistance
Giving adequate supervision and
Providing information ,
and training
and reviewing
for best practices
The development of systems to prevent accidents, injuries, and other adverse occurrences in an institutional setting.
The concept includes prevention or reduction of adverse events or incidents involving employees, patients, or facilities.
Examples include plans to reduce injuries from falls or plans for fire safety to promote a safe institutional environment. (12 Dec 1998)
Review of system of continue improvement of OSH performance
Monitor and measure programme against the OSH policy, objectives, legal and other equipment.
Involve setting of OSH policy, allocation of resources, provision of skills & organizations, hazard identification and risk assessment.
Actual implementation and operation of OSH programme.
Identify
Management must have a written OSH policy
Management must commit themselves to:-
Promoting health and preventing accidents, diseases and other work-related health effects in the workplace
Complying with OSH legal requirements and other requirements
Workers and their representatives are consulted when making workplace rules and regulations
Providing the necessary resources to ensure that work and the workplace is safe
Management as a whole is responsible for OSHEnsuring that management and workers are competent to carry out their tasks, especially the hazardous ones
Employees are informed of hazards they are working in and procedures are established to ensure their safety and health
Management must promote safety and health espects
There must be procedures for purchasing and contracting to ensure safety and health requirements are incorporated in purchased materials and equipment as well as in contracting activities.
OSH management activities must be planned, and performance targets set
• Identifying and analyzing the root causes of any nonconformities with relevant OSH regulations or management arrangements
• Initiating , planning , implementing, checking the effectiveness of corrective and preventive action including changes to the OSH management itself.
(2) The composition of a safety and health committee established under subsection (1), the election or appointment of persons to the committee, the powers of the members of the committee and any other matter relating to the establishment or procedure of the committee shall be as prescribed.
(3) Every employer shall consult the safety and health committee with a view to the making and maintenance of arrangements which will enable him and his employees to co-operate effectively in promoting and developing measures to ensure the safety and health at the place of work of the employees, and in checking the effectiveness of such measures.
A broad range of safety and health expertise and experience is available for solving problems
All employees have a way to express concerns and have them addressed
Safety and health awareness is improved
Cooperation
rates
• Employer or Authorized Manager shall be chairman
• Schedules monthly meetings, arranges time, date and place
• Develops safety and health agendas
• Conduct monthly meetings
• Help members to arrive at consensus on the solution
• Ensures all members are involved, everyone has the opportunity to share facts and ideas
• Person employed as Safety & Health Officer or appointed by the chairman or appointed among the members.
• Records meeting minutes
• Distributes minutes to representatives
• Posts minutes for all employees to review
• Maintains and manages the safety and health committee file
• Points out items that require discussion and follow up by the committee
• Keeps minutes and agendas for at least three years
• Report employees’s safety and health concerns to the committee
• Report collection of accidents, near miss incidents and unsafe workplace environment to the committee
• Suggest items to include in the monthly meeting agenda
• Encourage employees to report workplace hazards
• Establish procedures for conducting workplace inspections and give recommendations to management to control hazard
• Help management evaluate the company’s safety and health programme and suggest improvement activities
• Establish better investigation procedures for any causes of accidents and near miss incidents in the workplace.
relating
Management Chart should show lines of responsibilities and accountability such as:
Responsibility of Directors and Senior Management
Responsibility of the Safety Specialist
Responsibility of Supervisors and Foreman
Responsibility of Employee
Allocating adequate resources (financial, assets, and human training) for the best possible functioning of the OSH programme.
Building up a good management team or organizational representatives to support OSH development in the company.
Assigning a senior management representative to be responsible for OSH administration and agent to be in charge of any OSH occasion.
According to section 16 of the Occupational Safety and Health Act 1994 (“OSHA 1994”), it is a duty of the employer (or a self-employed person) to prepare a safety and health policy.
Aside from preparing such a policy, they must also update it as often as necessary.
Ensuring the policy, standards and safety guidelines in the workplace must be suitable for all levels of employees
Keeping each format to reach all levels of employees
Preparing readable, clear and easy to understand procedures, standards or safety guidelines
It must be realistic, credible, achievable and measurable.
Design and delivery of goods and services
- Assess the skills to carry out the task safely
- Provide the means to ensure that all workers, and management are adequately instructed and trained
- Ensure that workers doing dangerous work have adequate training, experience and other qualities to carry out the work safely
- Access for advice and help
- Restructuring or reorganization to ensure the competence of those taking on new OSH responsibilities
people responsible for particular health and safety jobs
especially where special expertise is called for, e.g. doing risk assessment, driving fork-lift trucks
that managers, supervisors and team leaders understand their responsibilities and have time and resources to carry them out.
knows what they must do
how they will be held accountable
set
-
- Involve staff in planning and reviewing performance, writing
and
and co-operate with those
who work on
Standards must be realistic, achievable and measurable
in which
injury or illness actually
at work
related events in which an injury or ill health or fatality occurred
or could have occured
MISS-
incident where no injury or illness occurs
• NEAR MISS- an event that, while not causing harm, has the potential to cause injury or ill health
• UNDESIRED CIRCUMSTANCE- a set of conditions or circumstance that have the potential to cause injury or ill health
An incident, in the context of occupational health and safety, is an unintended event that disturbs normal operations.
OSHA defines an incident as "an unplanned, undesired event that adversely affects completion of a task.“
Incidents range in severity from near misses to fatal accidents.
incident, in the context of occupational health and safety, is an undesired & unplanned events.
may result in:
physical harm ( injury, ill health or disease) to individual.
damage or loss to property
damage to environment
COMBINATION of any or all of these potential outcomes.
An event which did not result in injury or damage to property but had the potential to do so.
Share the same root cause as an accident. It is only the chance that harm or damage to be occurred.
Needs similar attention as an accident
SLIP AND FALL CAUSING INJURY ON THE ARMS AND ELBOW
WET AND SLIPPERY SURFACE CORRIDOR LIGHTING
SLIP WHILE WALKING UP STAIRS (NEAR MISS)
WORN OUT SHOE SOLES
HOLD STAIR RAILING
DUE TO THE DIM LIGHTS, PEDESTRIAN UNABLE TO SEE WET AND SLIPPERY SURFACE
DUE TO WORN OUT SHOE
SOLES, WORKER SLIPS AND MISSES ONE OF THE STEPS BUT MANAGES TO HOLD TO STAIR RAILING TO AVOID FALLING
SLIPPERY BOTTLE SURFACE DUE TO RESIDUE WRONG SIDE OF THE BOTTLE (COVERING LABEL)
DUE TO THE SLIPPERY SURFACE OF THE BOTTLE, BOTTLE SLIPS AND FALLS ON THE FLOOR
NONE
WHILE DRILLING A HOLE, WOOD CHIP FILES UPWARS BUT MISSES HANDLER
NONE NONE
Develop to assist safety officer to investigate and identify the causes of the occupational accident effectively
Understanding and identification of the types of failures or errors that cause accidents could be done
• Heinrich says, "The occurrence of a preventable injury is the natural culmination of a series of events or circumstances which invariably occur in a fixed and logical order." He defines accidents as, "events such as falls of persons, striking of persons by flying objects are typical accidents that cause injury.“
• Injury results from accidents, and some types of injuries Heinrich specifies in his "Explanation of Factors" are cuts and broken bones.
The domino theory developed by H. W. Heinrich, a safety engineer and pioneer in the field of industrial accident safety.
After a study of 75,000 industrial accidents, Heinrich concluded that:-
• 88% of accidents result from unsafe acts of individuals
• 10% of accidents result from dangerous physical or mechanical conditions.
• 2% of accidents result from unknown.
This first domino in the sequence deals with worker personality.
Heinrich explains that undesirable personality traits, such as stubbornness, greed, and recklessness can be "passed along through inheritance" or develop from a person's social environment, and that both inheritance and environment (what we usually refer to now as "nature" and "nurture") contribute to Faults of Person.
The second domino also deals with worker personality traits.
Heinrich explains that inborn or obtained character flaws such as bad temper, inconsiderateness, ignorance, and recklessness contribute at one remove to accident causation.
According to Heinrich, natural or environmental flaws in the worker's family or life cause these secondary personal defects, which are themselves contributors to Unsafe Acts, or and the existence of Unsafe Conditions.
The third domino deals with Heinrich's direct cause of incidents.
As mentioned above, Heinrich defines these factors as things like "starting machinery without warning ... and absence of rail guards. " Heinrich felt that unsafe acts and unsafe conditions were the central factor in preventing incidents, and the easiest causation factor to remedy, a process which he likened to lifting one of the dominoes out of the line. These combining factors (1, 2, and 3) cause accidents.
• Loss Causation Model is a way of linking actual loss to root causes and underlying management system failings in a domino type model.
• The Loss Causation Model was identified by Bird (in the 1970’s and has been used as the basis for a number of incident investigation techniques.
• Lack of knowledge,skill, inability to handle pressures of the job
• Inadequate training, inappropriate and inadequate equipment and tools, worn equipment and tools.
According to Bird and Germaine (1996), when the amount of energy absorbed or received by a person or object is below the safe energy absorption level, the person or property escapes without harm.
However, when the amount of safety values injury or damage is a result of the exceeded absorption
The model above is a simplified reflection of the real-life situation but powerful for communication purpose
It relates the management system to the event and the results thereof, either good or bad, depending on the quality of the system.
An activity conducts in a manner that may threaten the health and/or safety of workers.
- Use of tools for other than their intended purpose.
- Bypass or removal of safety devices.
A condition in the workplace that is likely to cause injury or structural/property damage
- Congestion in the workplace.
- Inadequate guards and warning systems.
- Unnoticed or disregarded hazardous releases or spills of hydrocarbons having the potential to create fire od explosions upon ignition.
- Poor ventilation
Cost is important for incident prevention as without any allocation , most incident prevention plans cannot be launched. It is hard to determine the actual cost needed to implement prevention programmes , but determining a projected cost is vital.
Cost that are used to develop prevention equipment for accident/incident in workplace.
The designs based on HIRARC reports, Job analysis reports, need analysis reports and accident investigation reports.
a. install machine guard
warning Sign
Cost that are used to aware workers on Safety and health in workplace
Incident prevention programme include safety training, new safety practice information, open day OSH to create awareness of safety in the workplace.
OSH training Cost
PPE Cost
Cost that are used to make sure safety in workplace
Accident intervention –lowers the costs of injuries, illness, loss of property and time.