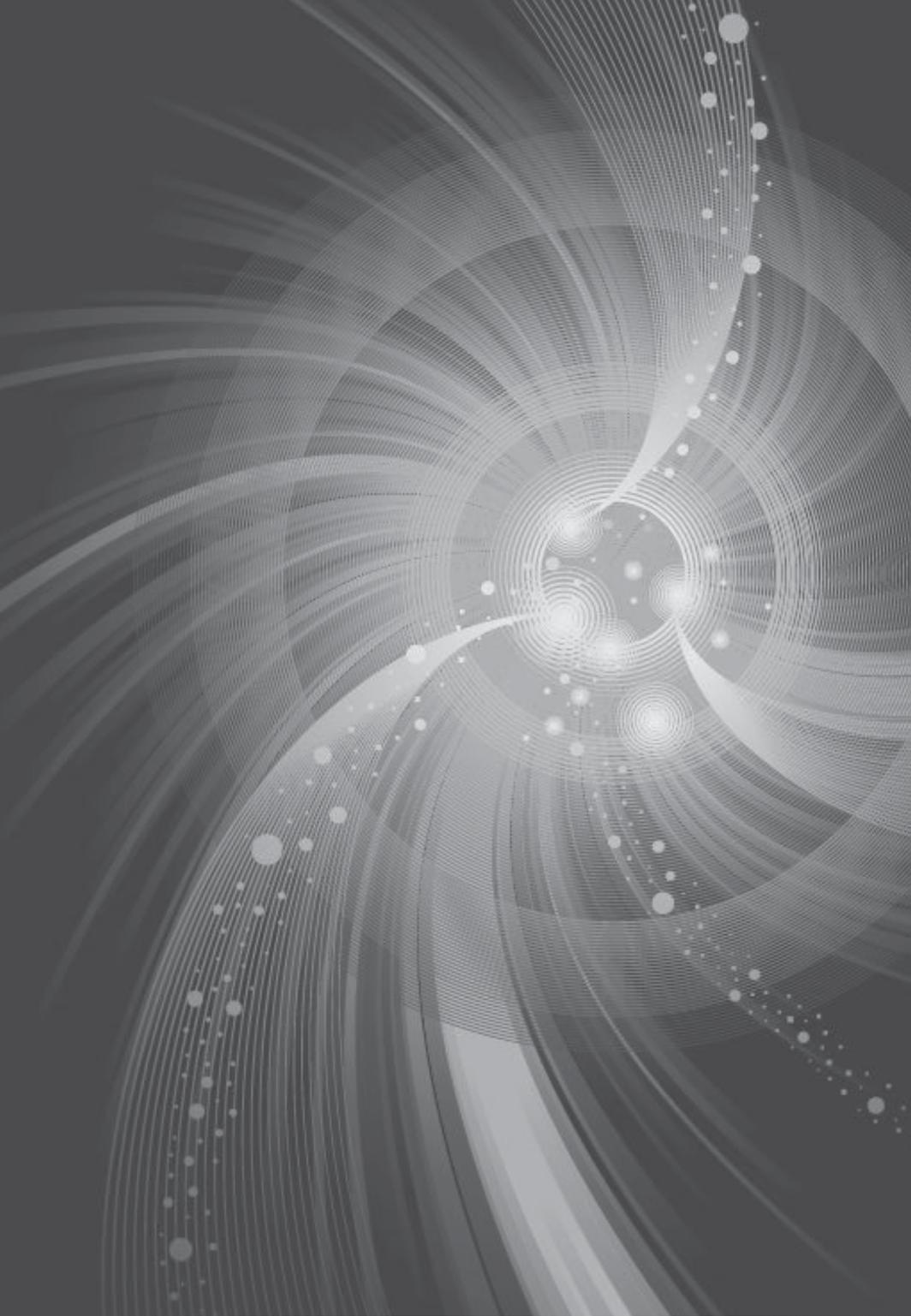
8 minute read
Exciting Times Ahead: Toys, Renewal Energy, Automotive Healthcare to Present Growth Opportunities
Table 1: 3-layer PE Film Formulation (Figures in %)
Polymer O M I LLDPE 70 78 40
Advertisement
LDPE 30 20 30
mLLDPE 0 0 30
MB 0 2 0 Table 2: 5-layer POD Formulation
(Figures in %)
Polymer O 2nd M 4th I LLDPE 80 90 78 90 50
LDPE 20 10 20 10 20
mLLDPE 0 0 0 0 30
MB 0 0 2 0 0
4% 2% 3% 2%
4%
3%
82% material being delivered to the die head. This can indeed do wonders.
If processing limitations are taken care of, there is a lot more possible with reduction of the cost of material which has been of great interest in the flexible packaging industry - to work on input raw material cost. The reason is very simple that depending on the location, polymers account for more than 82% of the total product cost (Refer Figure 3).
Hence, processors always find it more rewarding to work on reduction of raw material costs. If we see a typical formulation in Tables 1 and 2, savings on raw material can be upto INR 3,200 per tonne (i.e. USD 40 per tonne). In case of barrier films, this savings is substantially higher as the barrier layers should be processed as per required barrier properties (mostly as thin as possible) and the polymers are much more expensive.
Cost saving can be extremely rewarding when someone is using expensive functional polymers and are focused on downgauging with properties kept intact. Using recycled material or less expensive polymers is an option that is increasingly becoming very interesting. For special purpose films, reducing use of special additives can save when you use it judiciously by splitting functional layers and body layers. Instances where specific polymers or compounds are
Raw Material Labour Depreciation Energy Distribution Wastage Finance Cost
Figure 3: Production costs.
Implementing SCD, the unique advantage is to upgrade the line from 5 to 7 to 9 layers just by adding die stacks and extruders. This is going to be a major benefit for the industry at much lower additional investments, compared to multilayer blown film lines that use conventional dies. A big boon for the processor should be with changing market scenarios, the line will not go redundant.
essential for processing it on specific equipment is a completely different scenario. So, a lot more is needed than just a mathematical calculation on cost saving when you want to process your magical film formulations.
That is the key point and SCD is the way to go!
The Mamata Impact
Mamata Machinery Pvt. Ltd. (Mamata) is a globally leading manufacturer and Exporter of extrusion blown film lines, converting machines and end-of-line packaging machines. With an installed base of nearly 5,000+ machines in more than 88+ countries, Mamata enjoys close customer relationships across the globe. Mamata operates from Ahmedabad, India with a facility spread over 4,50,000 sq. ft. area with in-house electronics department, a fully equipped paint shop, in-house demonstration centre and installed capacity to make over 250 machines a year. In the USA, Mamata operates from two locations and caters to the needs of both, converting and packaging industries. Our Montgomery, IL facility is a pre-sales and after-sales service centre for converting machines. Our Bradenton, FL facility focuses on the design and manufacture of state-ofthe-art horizontal form, fill and seal pouching machines and multilane sachet packaging machines. Both the facilities are also showrooms of Mamata Machines for North, Central and South America.
For more details, write to rajesh.sonar@mamata.com
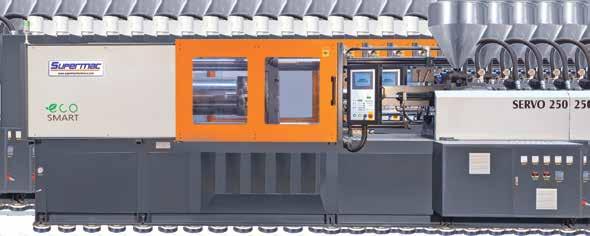
1995

Prakash kumar khemani
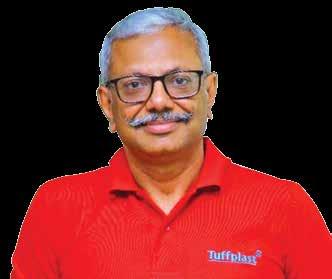
CEO, Suraj Logistix Pvt. Ltd.
It was in 1995 that Prakash made his foray into business and today leads the Suraj Group with over 5,000 team members. The retro picture also highlights the ‘straight in the eye’ look!

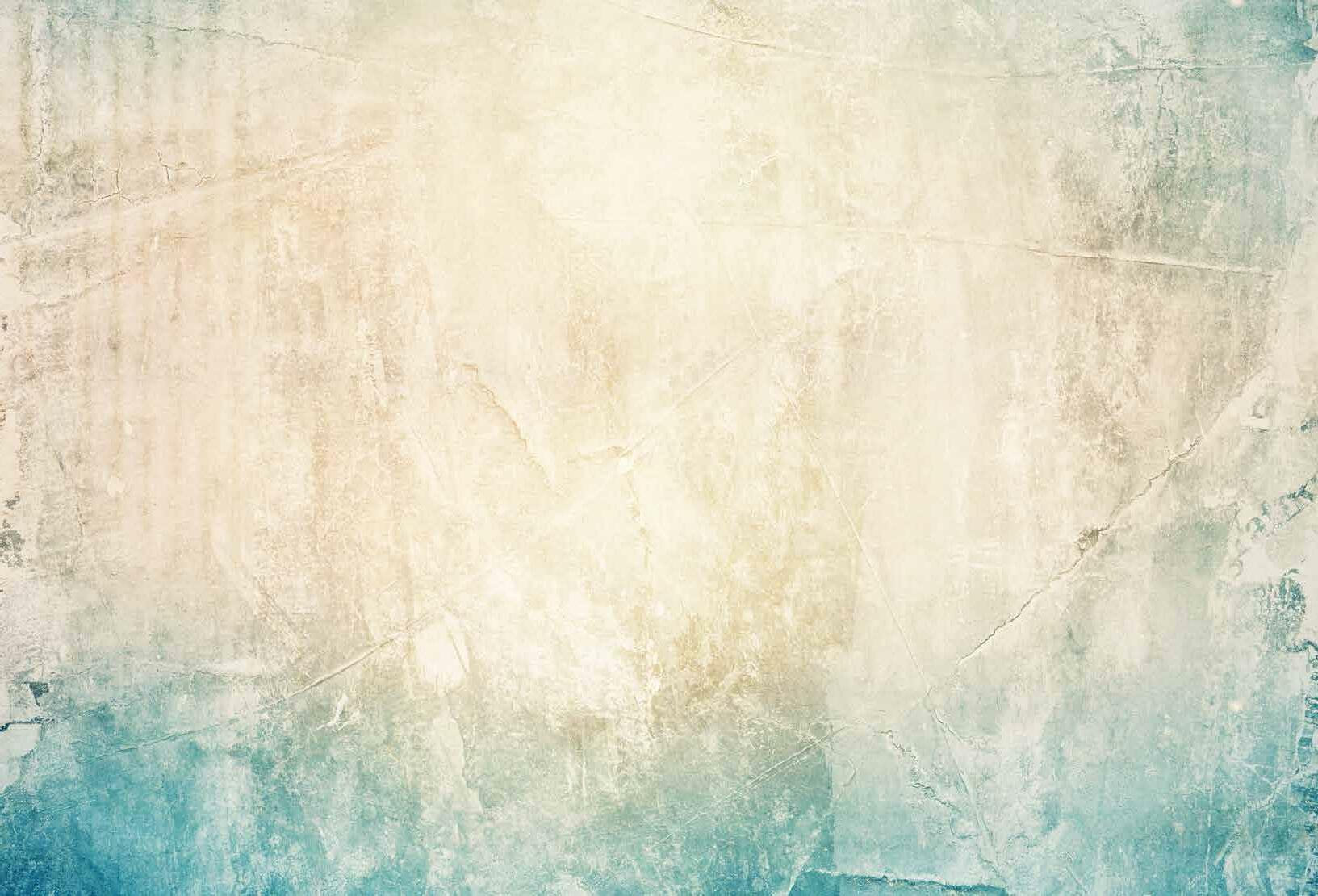
Change being the only constant, we thought it would be wonderful to capture this and freeze ‘time’. We associate with the ‘current look’ of our industry colleagues and would it not be exciting to know of their persona, decades ago. That’s what we did, had them dig deep into their archives and share this just for your ‘read’... or should we say ‘see’! A visual delight!
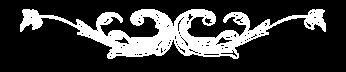
1995
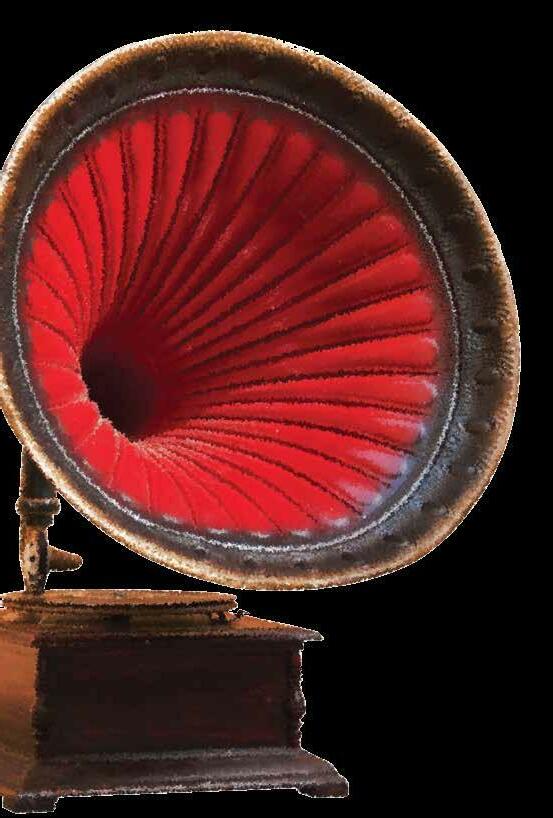
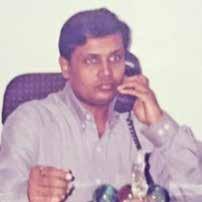

haresh Gudhka
Partner, Total Packaging Services
An uncanny resemblance then and now, Haresh, today a Partner at Total Packaging Services loves to travel and explore new places.
1984 1998

shriPal raj lodha
Managing Director, Uma Group of Companies
With an astute vision that both his pictures clearly indicate, Shripal started Uma Group in 1988 with a desire to make it (Uma Polymers) amongst the top 3 flexible packaging companies in India.
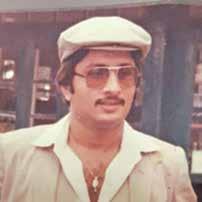

PradiP nayyar
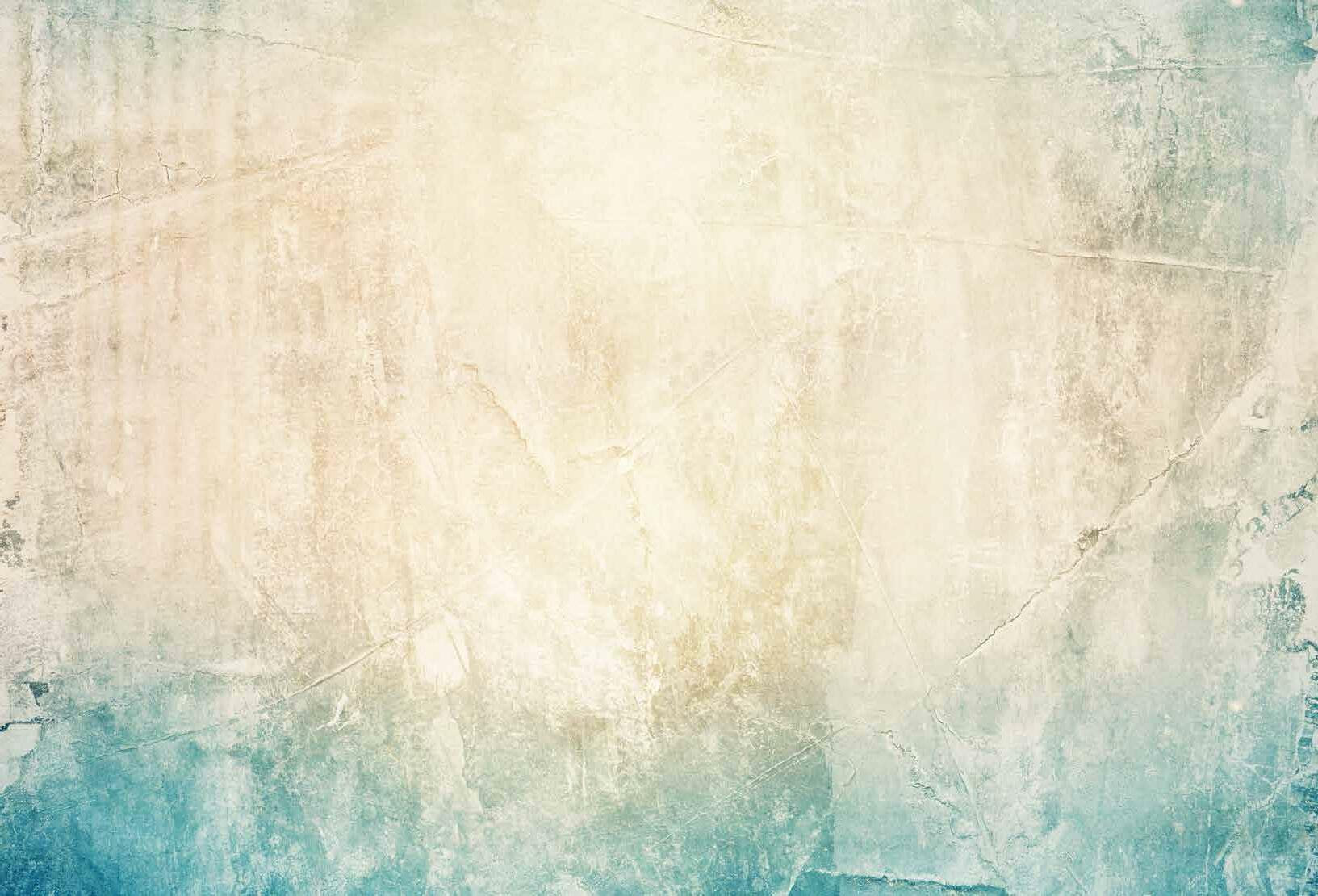
Partner, Kumar Engineering Works
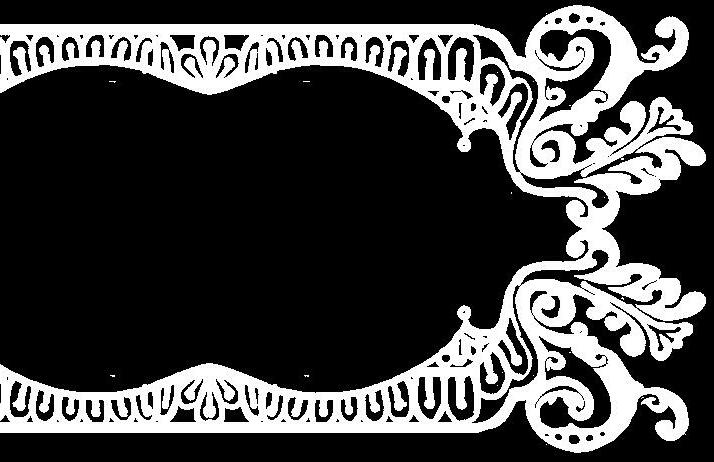
Truly retro, the 1984 picture at Shimla clearly carries the ‘Pradip look’ which is evident in his persona even today. Today, he is responsible for the business at Kumar and has contributed immensely to the growth of the plastics industry.
1989
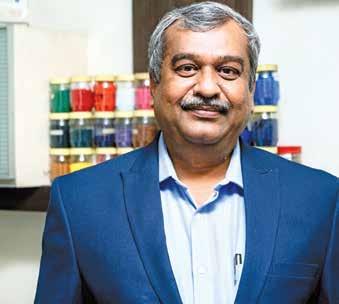
ParaG Parikh
Founder and CEO, Universal Masterbatch
Graduating in 1987, Parag started his own business in the even then-growing plastics and rubber industry. He has come a long way (a satisfied look which his picture clearly highlights) from his initial manufacturing of a unique polymerless masterbatch that was compatible with any plastic or rubber product.
Exciting Times Ahead
Toys, Renewal Energy, Automotive, Healthcare to Present Growth Opportunities
“The last few years have been great for the Indian manufacturing economy, which has seen tremendous yearon-year growth, thanks to initiatives like ‘AatmaNirbhar Bharat’, ‘Make in India’ and many more by the Indian government. Such schemes have encouraged the Indian players not only to manufacture products locally (rather than importing them from foreign markets), but also to boost Indian exports to various countries globally,” opines Amit V. Pendse, in dialogue with POLYMERS Communiqué.
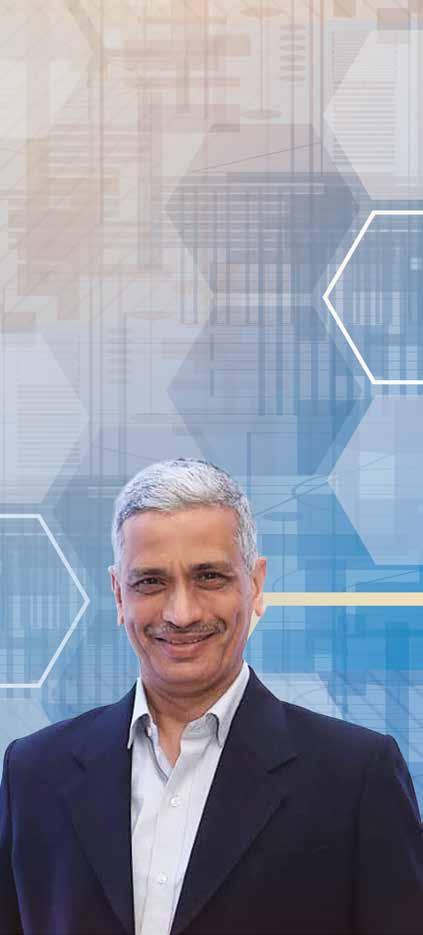
Amit V. Pendse
President, Electronica Plastic Machines Ltd., Pune Q. Highlights of this journey from ‘moulds to moulding’...
Electronica Group has been in the business of making metal cutting machines for the last more than 50 years and it has been an extremely rewarding journey. Many customers were engaged then and are still engaged in mould manufacturing for the plastic injection moulding process. As an obvious step, Electronica Group then diverted into manufacturing plastic injection moulding machines way back in 1992-93. We faced several challenges in the beginning in our pursuit to develop and manufacture quality machines and we were able to overcome them with our dedication, grit and determination.
Like most beginnings, we also had a slow start. Our real journey and progress began after 1997-98. It was at this stage that we actually started establishing ourselves. We made a lot of changes in our machine designs and the best part is that everything was done indigenously.
We made it a practice of upgrading and innovating our machines regularly. Since then, we have kept on introducing a range and type of new machine series and models over the years. We started with the toggle-type machines, which we continue to manufacture to date. Later, we introduced the ram-type machines and, a few years back, we introduced the latest generation twoplaten injection moulding machines as well.
Q. Please share some more insights into the features of the 5-point toggle-type machines and the advantages they will bring to the users?
The 5-point toggle-type machines are very energy-efficient by virtue of their design itself and produce high-quality, consistent products. When we started, there was only one company making plastic injection moulding machines, but those were ram-type machines and nobody else was manufacturing toggle-type machines. However, toggletype machines, especially the 5-point toggle-type, that we started with, provide a 16 - 17 per cent energy savings over the ram-type machines. What makes toggle-type machines a dominant player in the market is their ability to exert uniform and positive clamping force over the entire mould area and provide ideal mould movement dynamics during mould opening and closing functions.
Q. With your range of injection moulding machines, is there a sub-sector that really excites you as regards the growth potential in the coming years?
The last few years have been great for the Indian manufacturing economy, which has seen tremendous yearon-year growth. Thanks to the great initiatives like ‘AatmaNirbhar Bharat’, ‘Make in India’ and many more by the Indian government. Such schemes have encouraged the Indian players not only to manufacture products locally (rather than importing them from foreign markets), but also to boost Indian exports to various countries globally.
One of the prime examples of this change is the Indian toy industry. Earlier, a major portion of the toys sold in India was imported, which is now changing very fast as a lot of conventional jobwork moulding operations are getting into specialised toy manufacturing. Newer manufacturing hubs are being set-up and developed and we are getting good response and support from this industry.
To know more, please subscribe to Polymers Communiqué at subscriptions@polymerscommunique.com
MAKING MARCOM
CORPORATE COMMUNICATION SERVICES CONTENT DEVELOPMENT SERVICES EDITORIAL CO-ORDINATION MEDIA DISSEMINATION SERVICES ONLINE MARKET SURVEYS CUSTOMER INTERACTION REPORTS CREATIVE STUDIO
Custage Marketing Solutions LLP 406, Vikas Centre, Dr. C. G. Road, Chembur, Mumbai 400 074, India. T: +91-22-2520 4436; M: +91-88790 50327; E: info@custage.com