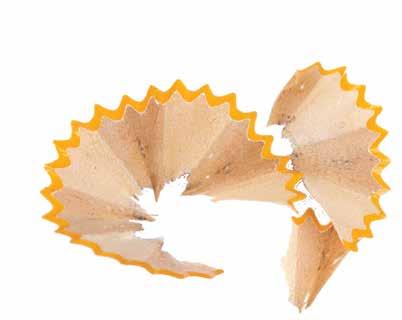
3 minute read
Energy Efficiency: A Clarion Call for the Industry
well-sharpened to respond
to industry needs...
Advertisement
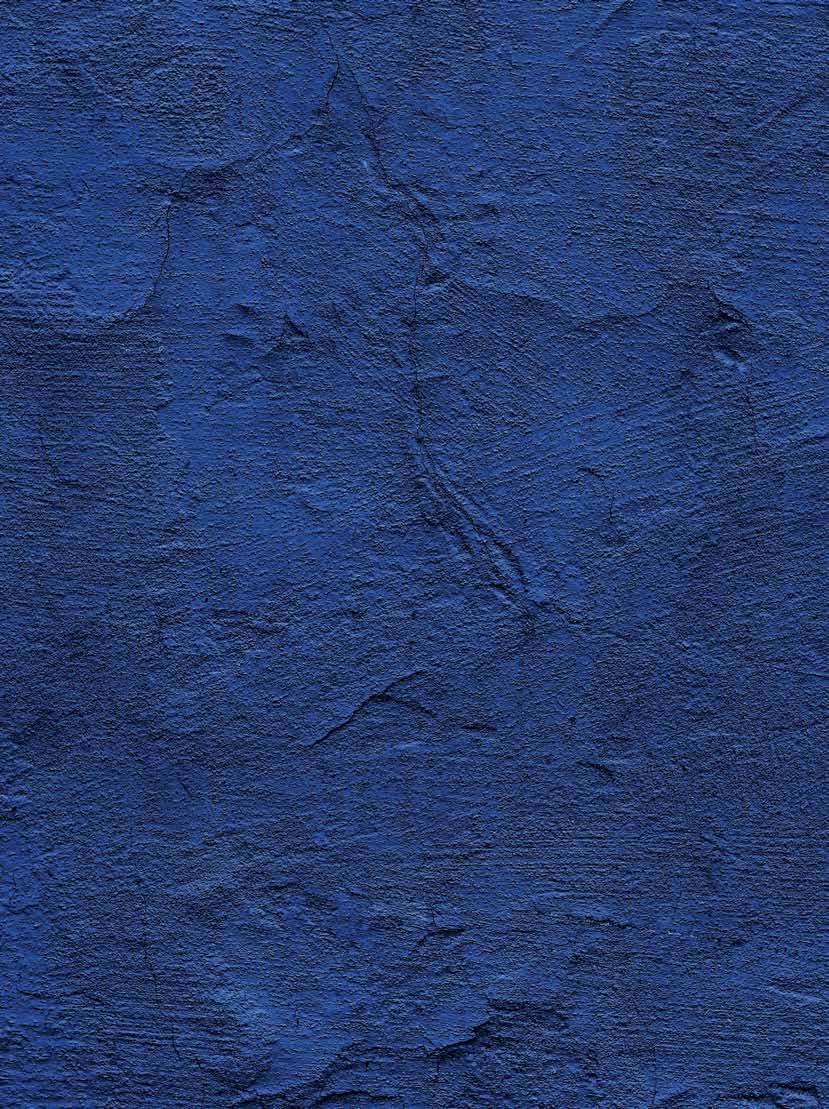
Luxurious print edition
Global digital edition
+91- 8879050327 info@polymerscommunique.com
Weekly
e-bulletin
On-the-go MyPC mobile app
Scan and download the MyPC app

Varun Ramsisaria,
Director, Viva Petrochemical LLP, Tamil Nadu “India is a price-sensitive market and the changes in technology were accepted at a slower pace; things are changing rapidly now as the industry is becoming more tech-savvy. With younger and more tech-aware entrepreneurs entering the market, we are witnessing a slow, but steady shift in the mindset and that is sure to make a huge difference,” opines Varun Ramsisaria, in dialogue with POLYMERS Communiqué.
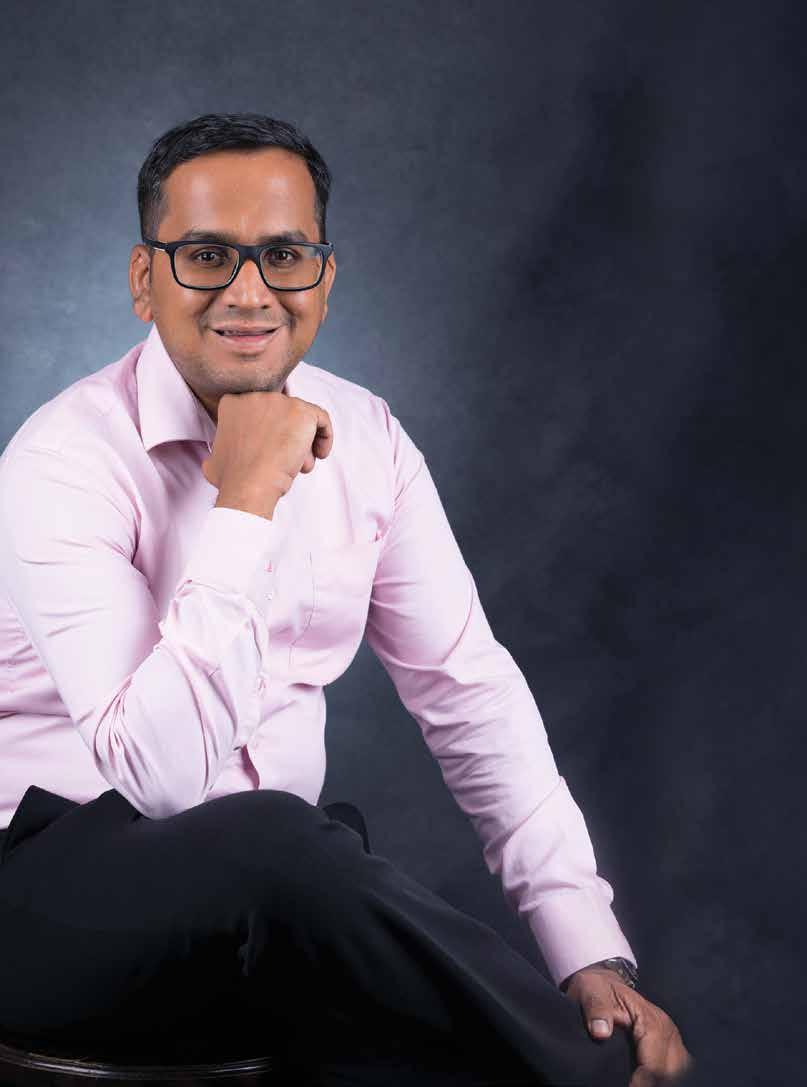
Q. The organisation was founded by experts from the polymer industry. Please state the most important and impactful milestones in the progress of the company this far.
To start with, there are two products that we manufacture. One is under Virgo Polymer India Ltd. (VPIL) which produces FIBC (jumbo bags) and the second is Viva Tech which provides eco-solutions. As far as Viva Tech and its eco-solutions are concerned, it’s still at a very nascent stage with energy solutions coming in the form of infrared heaters and IE5 motors. It started with the idea of providing energy-saving products to the polymer industry that was earlier using only ceramic heaters in the heating process of the extrusion barrel. These ceramic heaters required stronger insulation and still, there was a huge amount of energy loss in the process. So, when you heat the barrel with a ceramic heater, it takes a much longer time to heat it as compared to an infrared heater. We are amongst the first ones to introduce infrared heaters that are completely insulated from the inside.
Energy Efficiency
A Clarion Call for the Industry
Although these heaters are far more effective and energy-efficient, the shift from ceramic to infrared has been rather slow because of the pricing. We also introduced the IE5 motors in the market that was predominantly using IE3 motors at that time. This was a huge milestone for us as these motors are quite efficient and ensure better productivity. Despite the fact that this shift has been a slow-moving process, we have got approvals from several companies. We also have future polymer solutions where we act as a bridge between small-time plastic material processing units and our clients to provide the required materials.
Virgo Polymer, on the other hand, is an old and established company that started almost three decades ago from a small shed. From such humble beginnings to now manufacturing almost 6,000 tonnes per annum of FIBC is something that we take pride in. Since our inception, we have emphasised on producing the best quality products and that has been our most consistent trait. To ensure that we continuously get better, we have established an in-house R&D centre, complete with the latest test laboratory equipment. And being based in Chennai, the port city of India, enables us to provide quick and timely deliveries. These are some of the salient features of our company that give us a competitive edge over our contemporaries.

As regards FIBC, India is the largest manufacturer. However, in terms of operational efficiency, Turkey is far ahead of us because of the various processes they follow.
Q. Efficiency is the name of the game today. Share with us a case study in the polymer industry wherein efficiency improvement was the cornerstone of business success.
We have conducted many successful trials in the polymer and engineering industries. I would like to highlight 2 cases of our trials.
One such application was replacing IE2 induction motors with IE5 motors on Lohia looms. Operating this loom for 24 hours had given a saving of 8% on electricity consumed, which was reduced from 99.04 units in 24 hours to 90.85 units in the equal number of running hours.
To know more, please subscribe to PolymErS Communiqué at subscriptions@polymerscommunique.com