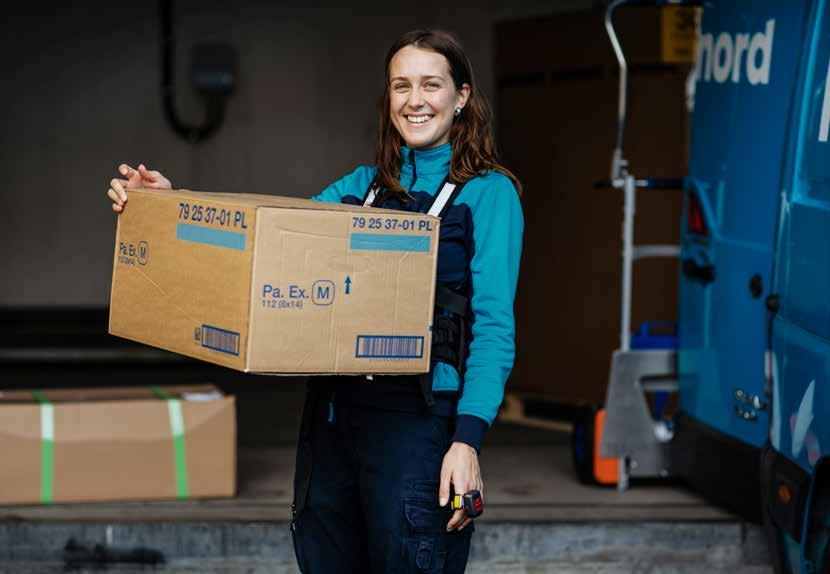
3 minute read
Mathias Krümmel
→ Van driver Vera Nilsson has been working at
PostNord for just over a year. “It’s great to meet so many people, but it’s pretty tough on your body."
WORK ENVIRONMENT RONMENT | I | WORK ENV
POSTNORD TO BECOME INDUSTRY LEADER
“Let's face it – historically we have not done enough to create a good working environment in all areas. That’s about to change. It's not okay for employees to get sick or injured at work. We are making a fresh start in health and safety management. Our focus is not only on the physical working environment, but also about gender equality, diversity and the psychosocial environment – and I want to set the bar high. PostNord will become an industry leader in systematic work environment management.”
MATHIAS KRÜMMEL, HEAD OF POSTNORD SWEDEN, ON THE INVESTMENT IN THE WORKING ENVIRONMENT.
I tested it for a week before giving it my final rating.” Vera and her colleagues assess all tools. There are forms on the terminal on which you can document the good and bad aspects and perhaps suggest improvements.
MAX MALMGREN HAS worked as a van driver since 2011 and is a safety representative at the terminal. He thinks it's great that health and safety is on the agenda, but agrees with Vera that so far no tool has lived up to expectations. One of the tools Max tested was an electric stair climber:
“It makes it easier when you have a big delivery and have to go up some stairs, but it doesn't work at all if you have to go down stairs instead. The stair climbers are also relatively heavy. They are just as difficult to lift in and out of the vehicle as the goods themselves. It might be a good idea to have a couple at the terminal for particular occasions, but not one in every vehicle.”
According to Max, the ultimate tool would be a planning tool. One that shows exactly what has been sorted into the cages and the number of items for each customer. “Then we wouldn't have had to reload and move the parcels around so much”, he says. BY FAR THE coolest device tested at Toftanäs is an exoskeleton that makes the wearer look like something out of a science fiction movie.
“You feel and look like a robot, but unfortunately that's also the only positive thing I have to say about it”, says Anel Hodzic, group leader in the collection area at the terminal. “The exoskeleton is heavy, uncomfortable and hot. And a bit unwieldy, too. Sure, you get help with the lifting, but it's very rare that we lift more than twenty kilos at the collection stage. It simply doesn't suit our activities.”
WHEN ASKED
WHAT the perfect tool looks like, Anel says, “We already got it – it's our body.” He and a couple of colleagues have been trained as lifting instructors. The aim is for all employees to undergo training in lifting techniques before the end of the year.
“Different tools can make the work easier, but the most important thing of all is to think about the technique, train your body and
take care of your shoulders and back”, Anel says. “I think people have got better at doing this lately, maybe because we supervisors keep going on about it.” He describes the atmosphere in the workplace as extremely friendly and positive: “Toftanäs is full of warriors, who try hard to deliver every single parcel and empty the terminal each day.” Terminal Manager Åsa Holmgren agrees. “I’m seeing great commitment, especially on this issue”, she says. “Many people appreciate the fact that they get to be involved in making a Åsa Holmgren, Terminal Manager. difference and that creates a ripple effect.” FOR THE WORK environment initiative to be fully successful, Åsa believes they will have to talk to customers about the conditions, too. Maybe even lower the weight limits: “In the short term, we might lose volume, Max Malmgren, Van Driver. but we’ll regain it in a better working environment. And an image as the sustainable logistics company. “In fact, many customers today combine two parcels to make one heavier one. If we could get them to stop doing that, it would be a major win.”