
10 minute read
Automatisierung des Werkzeugwechsel-Vorgangs.
Automatisierung des Werkzeugwechsel-Vorgangs
Mit der immer stärker zunehmenden Konkurrenz in der Fertigungsindustrie suchen Metall verarbeitende Firmen nach neuen Wegen, die Geschwindigkeit und Leistungsfähigkeit der Produktion zu verbessern. Während moderne abkantpressen mit höherer Geschwindigkeit sowie mit größerer Leistungsfähigkeit und Präzision arbeiten als Maschinen von vor 10 Jahren, so behindern Engpässe beim Einrichten und der Auslegung der Werkzeuge weiterhin den Ausstoß und die Produktivität.
In vielen Werkstätten, die mehrmals am Tag neu einrichten müssen, kann eventuell ein erheblicher Anteil von Produktionszeit zwischen Biegearbeitsgängen verloren gehen, und zwar auf Grund der Zeit, die für die Bediener erforderlich sein kann, die Werkzeuge auf der Gesenkbiegepresse manuell abzubauen, den nächsten Werkzeugsatz zu finden und an der Maschine anzubringen, sowie zusätzlich die Werkzeuge in der Maschine zu montieren und auszurichten, ehe der nächste Arbeitsgang beginnen kann. Hinzu kommt, dass ein potenzielles Risiko für den Bediener besteht, sich bei der Handhabung der schweren Werkzeuge zu verletzen, sowie auch das Risiko, teure Werkzeuge durch unsachgemäße Handhabung oder fehlerhaftes Einrichten zu beschädigen.
Die für jeden Werkzeugwechsel erforderliche Zeit kann auf Grund mehrerer Faktoren stark variieren; dazu gehören die Erfahrung und Schnelligkeit des Bedieners, die Menge an Werkzeugen, die zu entfernen und zu montieren sind, Zurückbringen der Werkzeuge ins Lager, Finden und Montieren des nächsten Werkzeug satzes und die Kompliziertheit der neuen Werkzeugeinrichtung.
Effektive Werkzeuglagerung und –verwaltung stellt in den meisten Werkstätten eine Herausforderung dar. Sehr oft ergeben sich Produktionsverzögerungen durch die zusätzlich erforderliche Zeit für das Auffinden der Werkzeuge für einen Biegearbeitsgang. In vielen Fällen sind die Ober- und Unterwerkzeuge der Abkantpressen auf Regalen und Gestellen in der Werkstatt gelagert, und sie werden von zwei oder mehreren Maschinen benutzt. Eine effiziente Produktionsstätte verlässt sich dabei auf gewissenhafte Bediener, welche die Lagerung und den Einsatz von Werkzeugen manuell bewältigen; dies ist aber nicht immer der Fall.
Man bedenke, wie viel Produktionszeit in der jetzigen Situation verlorengeht, wenn Bediener Zeit aufwenden, Werkzeuge und vielleicht auch nur ein letztes Teil zu suchen, um die Einrichtung zu komplettieren. Vielleicht sind die benötigten Werkzeuge schon auf einer anderen Maschine im Einsatz. Für Produktionsstätten, die an einem Tag viele verschiedene Teile bei einem straffen Produktionsablauf fertigen, ist es unbedingt nötig, dass für jede Maschine alle Werkzeuge vorhanden und stets greifbar sind. Hersteller von Abkantpressen haben zur Lösung dieser Probleme intelligente mechanische Systeme entwickelt, die den Werkzeugwechsel völlig automatisieren.
Verglichen mit dem manuellen Werkzeugwechsel-Ablauf machen Abkantpressen mit Automatic Tool Changer (kurz ATC) das Maschinen-Setup und den Werkzeugwechsel schneller, verlässlicher und viel effizienter. Diese Systeme stellen dem Bediener auch mehr Zeit zur Verfügung, um andere Aufgaben auszuführen oder um Rohmaterial zum Biegen zu beschaffen, so dass die Produktion beginnen kann, sobald der Werkzeugwechsel-Ablauf abgeschlossen ist.
Von den Biegepresseherstellern als Sonderzubehör angeboten, ist ein ACT entweder schon in der Konstruktion der Maschine enthalten oder als separates, integriertes Modul erhältlich. Obwohl die Konstruktionen und ihre Funktionalität variieren und es sich um Spezialausführungen der einzelnen Hersteller handelt, enthalten die ACT Abkantpressen allgemein dieselben Grundelemente. Das beginnt mit dem Werkzeug-Lagerbereich, der sich entweder innerhalb der Maschinengrundfläche befindet oder extern angebracht ist, einem motorisierten System, das die Werkzeuge zwischen dem Lagerbereich und der Werkzeugaufnahme an der Maschine transferiert, und schließlich einem Mechanismus, der die Positionen und Abstände der Werkzeuge entlang der Länge der Maschine bestimmt.
Der automatische Werkzeugwechsel-Ablauf wird vom CNC System in Verbindung mit dem Biegeprogramm gesteuert. Der ATC entfernt zunächst alle Ober- und Unterwerkzeuge, die nicht für das nächste Setup benötigt werden, und führt sie in den Lagerbereich zurück. Dann identifiziert der ATC den nächsten Werkzeugsatz, der im Biegeprogramm vorgegeben ist, und holt sich die erforderlichen Oberund Unterwerkzeuge vom Lagerbereich und führt sie in die Werkzeugaufnahme ein, was gewöhnlich ein hydraulisches oder pneumatisches Werkzeugspannsystem beinhaltet. Die horizontale Positionierung der Oberund Unterwerkzeuge entlang der Länge der Maschine wird eingestellt, einschließlich aller erforderlichen Abstände zwischen den Werkzeugen, die für die Teilefertigung nötig sind, wie z.B. bei Kastenbiegen, wobei die genauen Werkzeuglücken benötigt werden, um partielle Seitenflansche unterzubringen.
Auch in Fällen, bei denen mehrstufiges Biegen erforderlich ist, können diese intelligenten Systeme komplexe Setups bewältigen, auch mit verschiedenen Werkzeugprofilen.
TRUMPF, LVD, Prima Power, Salvagnini und Warcom gehören zu einer Reihe von Abkantpressen-Herstellern, die ihre eigenen Speziallösungen entwickelt haben, um den Werkzeugwechsel-Ablauf zu automatisieren und zu optimieren.
TRUMPF ToolMaster
Der ToolMaster von TRUMPF wechselt Biegewerkzeuge automatisch und erhöht so die Produktivität. Die neue Generation des Werkzeugwechslers kann drei Mal so viele Meter an Biegewerkzeugen speichern wie sein Vorgänger und wechselt sie binnen Sekunden. Nutzer können neben Standardwerkzeugen auch ACB-Sensorwerkzeuge und kundenspezifische Sonderwerkzeuge lagern und vollautomatisch rüsten.
Im Inneren des Werkzeugmagazins lagern die Ober- und Unterwerkzeuge auf unterschiedlichen Regalfächern. Die durchschnittliche Speicherkapazität beträgt 85 Meter an Biegewerkzeugen (abhängig von den ausgewählten Werkzeugen), die dort gut gegen Korrosion geschützt sind.
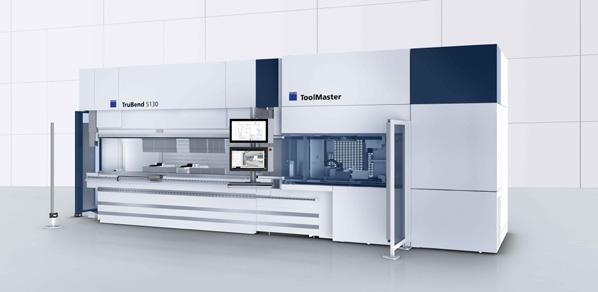
TRUMPF ToolMaster
TRUMPF hat eine Lösung entwickelt, die in nur drei Schritten einen effizienten und schnellen Werkzeugwechsel ermöglicht.
Den ersten Schritt übernehmen zwei unabhängige Be- und Entladearme, einer für die Ober- und einer für die Unterwerkzeuge. Jeder dieser Arme ist mit mehreren Achsen ausgestattet, die sich horizontal und vertikal zu den unterschiedlichen Regalfächern bewegen, und mit einem Greifer, der die Werkzeuge aus den Fächern nimmt.
Nach der Entnahme platzieren die Be- und Entladearme die Werkzeuge auf zwei separaten Drehscheiben, einer für die Ober- und einer für die Unterwerkzeuge. Diese Drehschreiben bewegen sich unabhängig voneinander um 90 Grad und bringen die Werkzeuge damit auf die Flucht der Ober- und Unterwerkzeugklemmung der Maschine. Die Drehscheibe für die Oberwerkzeuge kann sich auch in die andere Richtung bewegen, sodass sich gekröpfte Werkzeuge gedreht einsetzen lassen.
Im letzten Schritt bringen zwei Transportschlitten die Ober- und Unterwerkzeuge auf ihre entsprechende Position in der Maschine.
Zusätzliche Werkzeuge lassen sich einfach einlagern. Der Bediener setzt die neuen Werkzeuge von Hand in die Ober- und Unterwerkzeugklemmung ein. Mithilfe eines 2D-Code Scanner liest er den Data Matrix Code auf der Vorderseite der TRUMPF Werkzeuge ab. Nach dem Scanvorgang muss der Bediener die Eingabe auf der Steuerung bestätigen und der ToolMaster lagert diese Werkzeuge automatisch ein. >>

Salvagnini B3.AU-TO
Die Salvagnini B3.AU-TO Biegepresse lagert Ober- und Unterwerkzeuge in einem abgedeckten Werkzeugmagazin, das sich auf der Hinterseite der Biegepresse befindet und bis zu 24 m an Biegewerkzeugen einlagern kann.
Das patentierte AU-TO System ermöglicht den Transfer von Werkzeugen zwischen dem Werkzeugmagazin und den Werkzeugaufnahmen. Sobald die Werkzeuge platziert sind, macht das B3 von zwei zusätzlichen Automatisierungsstufen Gebrauch, indem es die ATA und ATA.L Geräte benutzt, um die Ober- und Unterwerkzeuglänge und die Abstände einzustellen.
Das ATA (Automatic Tool Adjuster) Gerät wird dazu benutzt, die Länge des Oberwerkzeugs automatisch zu wechseln und einzustellen, wobei
Zeit eingespart und die Produktionseffizienz erhöht wird. Der Wechsel ist schnell, er dauert nur ein paar Sekunden, und Programmieren ist einfach und intuitiv.
Das ATA.L Gerät für die Unterwerkzeuge ist die ideale Lösung für Kit-Produktion, da es das aufeinanderfolgende Biegen von Teilen verschiedener Stärke ermöglicht.
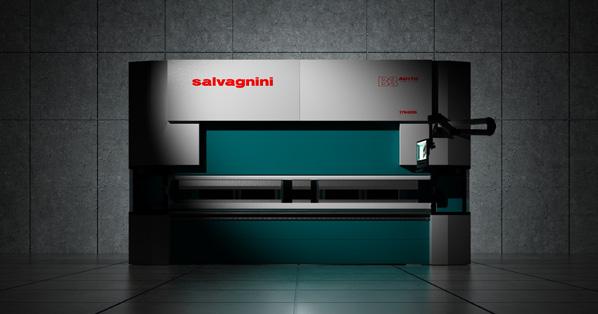
Salvagnini B3:AU-TO
LVD ToolCell
LVD ist stolz darauf, nahe am Kunden und den Anforderungen moderner Fertigungstechnik zu bleiben. In den letzten 10 bis 15 Jahren hat die Firma einen dramatischen Trend hin zum Fertigungstyp “Kleine Stückzahlen – Kurze Vorlaufzeiten“ erlebt. Zusätzlich reduzieren viele Hersteller ihre
Lagerhaltung (zum besseren Einsatz von Arbeitskapital) und setzen dabei die Lieferkette unter Druck. Also gab es für LVD einen eindeutigen Bedarf für eine dramatische Erhöhung des Ausstoßes beim Fertigen von Teilen in kleinen Stückzahlen.
Als Reaktion auf diese Anforderungen an die Fertigung wurde LVD ein frühzeitiger Anwender eines Automatic Tool Change Ablaufs durch die Einführung ihrer ToolCell Biegepresse, und die Firma war der erste Hersteller, der ein Werkzeugmagazin innerhalb der bestehenden Maschinengrundfläche integrierte.
ToolCell ersetzt das Herumsuchen nach Werkzeugen mit einer Speziallagerung in einem stadionartigen Raum für Ober- und Unterwerkzeuge, der sich unter dem Hinteranschlag der Maschine befindet, wobei man von vorhandenem Raum Gebrauch macht. Das Werkzeugstadion fasst bis zu zwei komplette Längen von Oberwerkzeugen und fünf komplette Längen von Unterwerkzeugen für Flexibilität und Platzersparnis, und alles in einer kompakten Konstruktion. Das ToolCell
Lagersystem bietet eine flexible Werkzeugkonfiguration, die sich für spezielle Anwendungsfälle eignet.
Innovative Greifer, die in die Hinteranschlag-Finger der Maschine eingebaut sind, dienen als Werkzeugwechsel-Mechanismus zum Transferieren der Ober- und Unterwerkzeuge. Während der Bediener die Teile für die nächste Serie vorbereitet, entfernt die Maschine das vorherige Werkzeug-Setup und platziert das nächste Setup, und alles findet ohne manuelles Eingreifen statt.
ToolCell ist mit LVD’s patentiertem Easy-Form® Laser (EFL) ausgerüstet, einem adaptiven Biegesystem. EFL gewährleistet, dass der erste Biegevorgang jedes Mal genau ist. Das EFL System überträgt die digitale Information in Echtzeit an das CNC Steuergerät, wo sie verarbeitet wird und das die Position des Oberwerkzeugs sofort nachstellt, um den richtigen Winkel zu erhalten. Der Biegevorgang wird nicht unterbrochen und keine Produktionszeit geht dabei verloren.
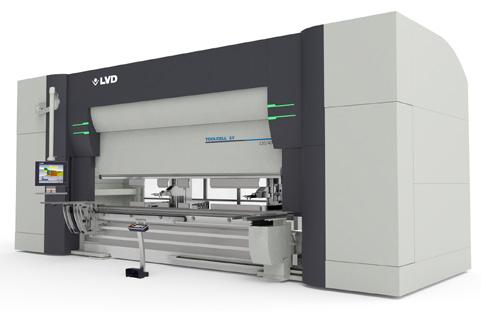
LVD ToolCell XT
LVD bietet auch ToolCell XT an, die neueste Generation ihrer ToolCell-Biegepresse mit automatischem Werkzeugwechsel, die eine erweiterte Kapazität aufweist und 50% mehr Werkzeuge als die ursprüngliche Konstruktion aufnehmen kann.
Die große Kapazität von Werkzeugen, die innerhalb der Biegepresse untergebracht werden können, bietet die Flexibilität, eine größere Folge von Biegeaufträge zu bewältigen, einschließlich komplexer Layouts. Mit seiner erweiterten Werkzeugkapazität bietet ToolCell XT die Vielseitigkeit an, verschiedene Materialtypen zu bearbeiten, Werkzeuge nach Materialtypen zu organisieren, leicht von Edelstahlauf Baustahlanwendungen umzuschalten. >>
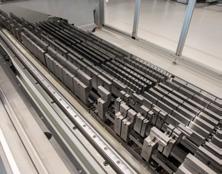

Prima Power eP Genius
Prima Power eP Genius Eine weltweite Premiere auf der Blechexpo feiert die neue Biegelösung von Prima Power, die eP Genius 1030. Dabei handelt es sich um eine servoelektrische Abkantpresse eP 1030 mit automatischem Werkzeugwechsler und lager.
Das Werkzeuglager ist die wichtigste Innovation dieses Produkts. Es kann insgesamt 32 m an Werkzeugen aufnehmen, die auf 8 Werkzeughaltersupports gesetzt werden, die entlang 3 Achsen verfahrbar sind. Es erlaubt die Handhabung von Werkzeugen (WILA-Ausführung) mit einer Mindestlänge von 20 mm bis zu maximal 515 mm. Darüber hinaus dreht ein rotierender Werkzeugteller die Werkzeuge, die dem Lager entnommen werden, so dass mehrere Bearbeitungsmöglichkeiten zur Verfügung stehen. Die Bedienerschnittstelle der neuesten Generation erlaubt die einfache und intuitive Programmierung von Teilen, sowohl an der Maschine als auch offline, sowie das automatische Management des Maschinen-Setups.
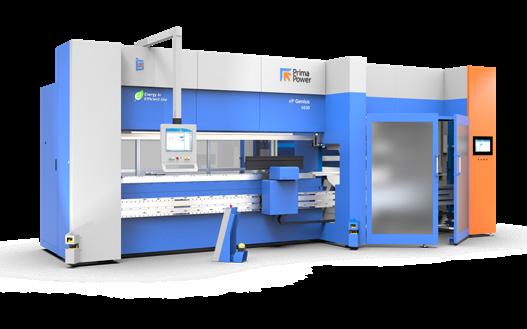
Prima Power eP Genius
Warcom BEND-MASTER
Der italienische Abkantpressenhersteller Warcom hat den BEND-MASTER entwickelt, ein automatisches Werkzeugwechsel-System, das sein gesamtes Biegesystem im Hinblick auf größere Flexibilität, Schnelligkeit und Zuverlässigkeit vervollständigt.
BEND-MASTER weist ein sechsachsiges Antriebssystem auf, das ein zweiachsiges Gestellsystem, eine einachsige Drehbrücke und ein dreiachsiges Shuttle zum Be- und Entladen beinhaltet. Das Werkzeuglager beinhaltet die Option von 32 m oder 52 m Werkzeugkapazität, die eine Reihe von ausgewählten PROMECAM und WILA Ober- und Unterwerkzeugen aufnehmen kann. Der Lagerraum kann sowohl auf der rechten als auch der linken Seite der Biegepresse aufgestellt werden und umfasst eine Reihe von Gestellen und Schubladen, die bis zu 4,5 m an Werkzeugen pro Regal aufnehmen können.
Wahlweise können zwei Abkantpressen von demselben BEND-MASTER bedient werden.
Während des automatischen Werkzeugwechsels bewegt sich das Regal, welches die im Biegeprogramm vorgegebenen Werkzeuge enthält, zur Vorderseite des Lagerraums. Das Shuttle verschiebt sich zum Lagerraum und schiebt die benötigten Ober- oder Unterwerkzeuge heraus und fährt das Werkzeug zur richtigen Stelle in den oberen oder unteren Werkzeugaufnahmen. Während dieser Vorgang abläuft, bewegt der Lagerraum das Werkzeuggestell nach oben und unten oder bringt ein anderes Werkzeuggestell nach vorne, so dass das nächste Ober- oder Unterwerkzeug einsatzbereit ist. Das spart Zeit, da das Shuttle nie untätig bleibt, während es darauf wartet, bis das nächste Werkzeug an der Reihe ist.
Wenn ein Stempel in der umgekehrten Position installiert werden soll (z.B. bei einem umgekehrten gekröpften Werkzeug), setzt das System eine Drehbrücke ein, die sich zwischen den Werkzeuggestellen und dem Maschinenbett befindet. Das Shuttle schiebt den Stempel vom Werkzeuggestell hinüber zur Drehbrücke, und die Drehbrücke dreht den Stempel um 180 Grad, so dass er in die entgegengesetzte Richtung zeigt. Dann fährt das Shuttle damit fort, den Stempel auf der Biegepresse in Position zu bringen.
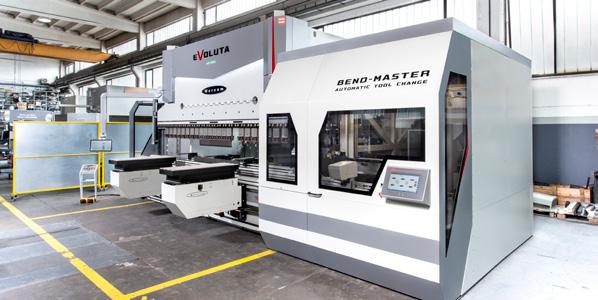
Warcom BEND-MASTER
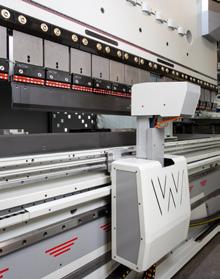
Automated workflow
Automatisierte Arbeitsabläufe spielen auch eine wichtige Rolle beim Optimieren von Produktionsprozessen mit vernetzten Maschinen, die effektiver vom Büro aus gemanagt werden können, wobei die Bediener in der Werkstatt um weitere Aufgaben entlastet werden. Eine komplette Arbeitsschicht geplanter Biegeprogramme und Werkzeug-Setups kann über Fernbedienung im Voraus an die Maschinen übertragen werden, so dass der nächste automatische Werkzeugwechsel beginnen kann, sobald der vorherige Auftrag erledigt ist.
Abkantpressen-Benutzer sehen im automatischen Werkzeugwechsel auch eine Lösung zum Reduzieren von Ermüdung der Bediener und Verbesserung der Sicherheit, um das Risiko von kurz oder lang anhaltenden Verletzungen zu vermindern. Viele Maschinen benutzen schwere Werkzeuge, die entweder manuelles Heben vom Bediener oder Hebezeuge wie z.B. einen Kran erfordern, um die Werkzeuge von und zur Maschine zu transportieren. Verletzungen können sich ergeben durch Überlastung beim Heben oder dadurch, dass Werkzeuge herunterfallen, wobei möglicherweise im Laufe vieler Jahre langfristige
Gesundheitsschäden durch wiederholtes Heben schwerer Werkzeugen auftreten. Dank dieser modernen automatischen Systeme werden Werkzeugwechsel schneller, sicherer und sehr viel effizienter. ATC Abkantpressen sind die ideale Lösung zum Managen einer Vielzahl von täglichen Werkzeugwechseln, komplizierten Setups von Ober- und Unterwerkzeugen sowie der effektiven und geschützten Lagerung von Werkzeugen.