
3 minute read
Leading the industry in yearbook production with a completely digital workflow
Leading the industry in yearbook production with a completely digital workfl ow
Balfour and Meccanotecnica experience the third round of investment with new digital print finishing solutions for the production of yearbooks.
Advertisement
Balfour, formerly known as Taylor Publishing Company, was founded in 1939 by Herbert, Edgar, and Bill Taylor. Their vision to simplify the book creation process through innovation and technology has allowed the company to not just keep pace with the industry but set it.
While the company entered the industry during the era of photoengraving and copper plates, today Balfour’s 325,000 square-foot, state-of-the-art production facility is equipped with the latest printing and bookbinding technology. Most importantly, Balfour continues to employ the skilled and experienced personnel necessary to produce high quality, hard- and soft-bound books efficiently.
Balfour is one of only a few US printing/binding operations with significant cover making capabilities. They offer numerous case-bound (hardcover) production options, including cloth-based or printed. With the use of foils, inks, embossing, die-cutting, and laminating, the company offers thousands of options for book cover customization. In addition to case-bound cover capabilities, Balfour produces printed covers for softcover books that can be bound in a variety of ways including saddle stitch, perfect binding, thread-sewing and more. Balfour operates one of the largest Komori sheet-fed offset pressrooms in North America. They regularly produce print runs of 300 to 10,000 copies or more, but also have several digital printing machines dedicated for shorter print runs.
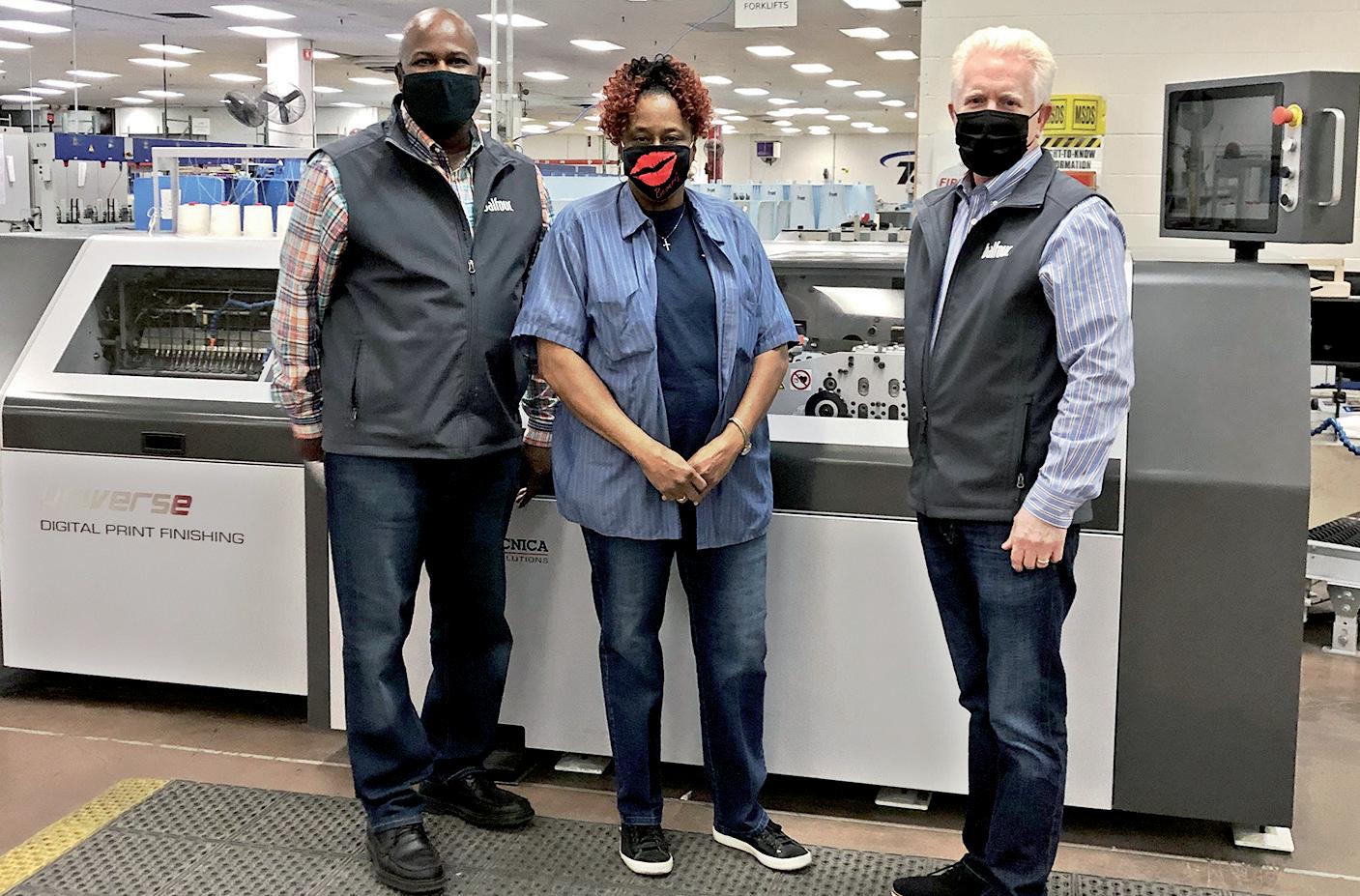
From the left Mr. Terry Allen (Bindery manager), Mrs. Beverly Edwards (Sewing lead) and Mr. Gary Thompson (V.P. of Operations).
Balfour was the first company in the US to implement online publishing, produce all-color yearbooks, and move to a completely digital workflow. “We lead the industry in yearbook software technology, offering the most robust set of technology and educational tools for our customers to manage their yearbook creation journey”, says Mr. Gary Thompson, V.P. of Operations at Balfour.
All publishing production is done in Dallas. However, Balfour’s parent company, American Achievement Corporation, has facilities across North America for the production of its achievement products such as caps and gowns, graduation announcements, letter jackets, school photography, and class jewelry.
“Meccanotecnica has been supplying book finishing machines to Balfour since 1976, starting with the first automatic tippers in achieve (500 sheets/minute as a constant feed speed, Ed.) were decisive in the choice”. - Mr. Gary Thompson
RESULTS
“We have just installed our second Universe™ line, increasing our efficiency, and reducing cost”, says Mr. Gary Thompson. “We thread-sew all of our case-bound yearbooks for quality reasons. We believe it is the strongest form of production enabling the books to last for decades, holding up for milestone celebrations like 5, 10, 20-year reunions. When we pull a book off the shelf, it will still be in good shape due to threadsewing and hardcover production.”
KEY FIGURES
Balfour produces millions of books of which about 85% are thread-sewn and hard covered. They service thousands of schools in the K-12 and College market.
“Digital finishing is very cost-effective for us. By printing digitally, we have faster turn time and less waste. Digital printing has no loss of time for drying as in offset (8 hours), so we gain that time back and can begin sewing immediately after printing. We are also able to tip the end sheets inline without a separate operation, this is very efficient,” concludes Mr. Gary Thompson.
FOCUS ON THE PROCESS
After sewing, the integrated spine-nipping press automatically presses the book blocks reducing the thickness of the spine build-up. This improves the quality and efficiency of downstream processes.
The end-sheet tipper is also integrated and connected in line with the nipping press, significantly enhancing the efficiency of the book block preparation for hardcover application. The module automatically glues the end-sheets to the first and last page of the book block by using cold glue.
