
16 minute read
Monotech installs 1st JETSCI
Monotech installs country’s first JETSCI at Bhavik Publication
The first print-on-demand JETSCI Monochrome Inkjet web press is already in production for over 3 months at the Ahmedabad facility.
Advertisement
Monotech Systems has installed India’s first fully integrated high speed print-on-demand Inkjet web press at Bhavik Publications located at Ahmedabad. Machine is already in production for over 3 months and is installed with inline servo driven variable cut sheeting device.
This Web press has been manufactured with the joint efforts of JETSCI (Monotech Systems) which supplied the complete application and inkjet printing solution and Pressline that supported the web control system with inline sheeter.
Apart from Print-on-Demand book printing applications, the machine can be fully utilized in more demanding transactional and security printing applications.
Mr. Dipak N. Patel, Owner, Bhavik Publications, says, “We were looking for the digital press for our Print-on-Demand short run jobs in publishing and security printing for over 2 years but could not find the right solution which has speed, quality, the local support availability and reasonable requirement of investment. The JETSCI fits to all our requirements very well. We are really happy with quality and productivity on the machine.”
“We are now able to deliver our jobs in the shortest turnaround time with this web press, which can deliver high quality at resolutions up to 600dpi and speed of up to 150m/ min, the programmable variable cut sheeter ensures us the perfect delivery in the sizes we need having quick setup times. We will gradually move our all short and medium run jobs on this press and will offer the great value addition to our customers of digital printing like variable data and security printing along with the regular jobs,” he added.
Mr Dinesh Thakur, DGM Sales-IPS, Monotech Systems says, “Digital Printing has grown exponentially in all the fields of printing industry like labels, packaging, books, printon-demand, and security applications. After the Covid-19 situation, we are sure about the surge in the demand for digital printing
Dinesh Kumar Thakur, DGM - Sales, Monotech Systems, Dipak N. Patel, Owner, Bhavik Publications
and it will definitely help the printers to grow faster and respond to the market demands quickly.”
Bhavik Publication began operations in the year 1981 by putting up printing presses in different locations of Ahmedabad city. Turning point came in the year 1995 with the shift of focus towards educational Publication business. Starting with Preparing Lesson Dairy for students, in the following year they launched 2 books – Gujarati and Maths for Junior and Senior Kg Students. There is no looking back since then and today the company has expanded into businesses in Print & Multimedia dimensions – Printers, Publishers, Manufacturers & Sellers of Educational Materials. They are known for their high quality products in the region.
Business continues despite COVID-19
The COVID-19 remains a rapidly developing and unforeseen global health crisis. As a reaction, Nilpeter carefully follows the directions and recommendations of local authorities.
All Nilpeter facilities around the world are still operating with ongoing production, observing local government and health services guidelines. Spare parts handling is fully active in normal opening hours, and Customer Care is performing 24/7 remote support and trouble-shooting from all global Call Centers.
All inquiries for visits in Nilperter’s Technology Centers in Denmark, USA, Thailand, Brazil, and India are welcomed and handled in compliance with local travel regulations. The company’s focus is to achieve “business as usual” with the health and well-being of employees and partners safe and secure under current conditions in all markets.
For inquires customers may contact local Nilpeter Partner.

Rise in Alcohol prices creates fi nancial impact for Packaging companies
By Dr. Dieter Niederstadt, Technical Marketing Manager, Asahi Photoproducts.

For flexographic companies using solventbased platemaking processes, the sharp rise in alcohol prices we are seeing in several EU countries increases the cost of flexographic plates by as much as 3 EUR per square meter.
To get to this number, we did the following calculations: • In several European markets, the cost of alcoholhas doubled, from 1 to 2 EUR per liter. • It typically requires 15 liters of washout solvent per square meter of plate. • 20% of that 15 liters is typically alcohol used to remove the black mask layer, meaning an average consumption of 3 liters of alcohol per square meter of plate material. • The result is an increase in cost of 3 EUR per square meter of plate material in the solvent wash process.
At the same time, it is true that if a flexographic platemaking operation has a recycling unit on site, it can recover up to 85% of the solvents. This would still mean an extra cost of 45 cents per square meter.
While this impact may still be moderate for flexoplate maker, packaging printers who are currently using solvent-based inking systems have a much bigger burden to carry. Most large industrial ink suppliers currently implement a price surcharge for solventbased packaging inks around the globe. In addition, it should be mentioned that they cannot guarantee supply if governments decide to redirect products for medical purposes. Whereas flexographic printing can operate with several different inking systems like UV, EB, water and solvent, packaging suppliers such as rotogravure printers are faced with limited choices.
The packaging industry is a competitive market, and, especially in the light of the global pandemic disruption, we see discussions taking place and starting to shape the “new normal” in the times ahead.
At Asahi Photoproducts, we brought our water-washable AWP plate technology to market 10 years ago. Thanks to these 10 years of experience, we know that AWP produces even better quality than typical solvent-wash plates, while at the same time creating an operation that is more in harmony

with the environment.
Our experts are available to discuss these subjects with you, or any other issues you may have around flexographic platemaking. Just send an email to Asahi photoproducts or contact your local Asahi Photoproducts representative.
Asahi Photoproducts was founded in 1971 and is a subsidiary of the Asahi Kasei Corporation. Asahi Photoproducts is a leading pioneer in the development of photopolymer flexo printing plates. By creating high quality flexographic solutions and through continued innovation, the company aims at driving print forward in harmony with the environment.

hubergroup strengthens its profile with a new brand image
Website with a freshlook; new company logo symbolizes a strong appearance as a global player.

hubergroup is a traditional family business. With over 255 years of company history, it is rich in experience and know-how. In order to position itself even better for the future, the printing ink manufacturer has taken a number of measures such as a relaunch of its website and further development of the logo. These are now visible and tangible for the customer.
New website with a personal touch hubergroup has a new online presence. The site is based on a revised corporate design, which is significantly streamlined in its look and thus gives the website a fresher and more modern look.
The dominant colour is reflex blue. As hubergroup is the last big manufacturer of the pigment alkaline blue, the printing ink specialist has given it more weight in the course of the redesigns.
Customers will benefit from the new website, as the newly designed product finder will help them find solutions even more quickly and clearly.
The website now features individual contact persons for each country, so that customers worldwide can contact the appropriate competent local advisors directly with their specific requirements. With the new website, the printing ink manufacturer presents itself in a much more approachable way. The visual language has become more personal and emotional, with hubergroup relying exclusively on its own employee portraits in the design, emphasizing authenticity.
To reflect the global nature, the content is available in a large number of national languages of the hubergroup locations and has been optimised for mobile use in line with today’s standards.
Global orientation in the logo As hubergroup, with over 30 locations worldwide, continues to grow in an integrated manner across its global footprint, this is also reflected in the new logo. hubergroup is a company that offers its customers around the world consistently high product quality and service standards. The group functions as a unit, which is now also visually represented in the new logo. With 255 years of experience, hubergroup is one of the leading international specialists for solutions and technologies relating to printing inks and printing aids for packaging and commercial printing. The company produces a large part of the key raw materials, such as pigments, binding agents and additives, in their own production facilities in India.
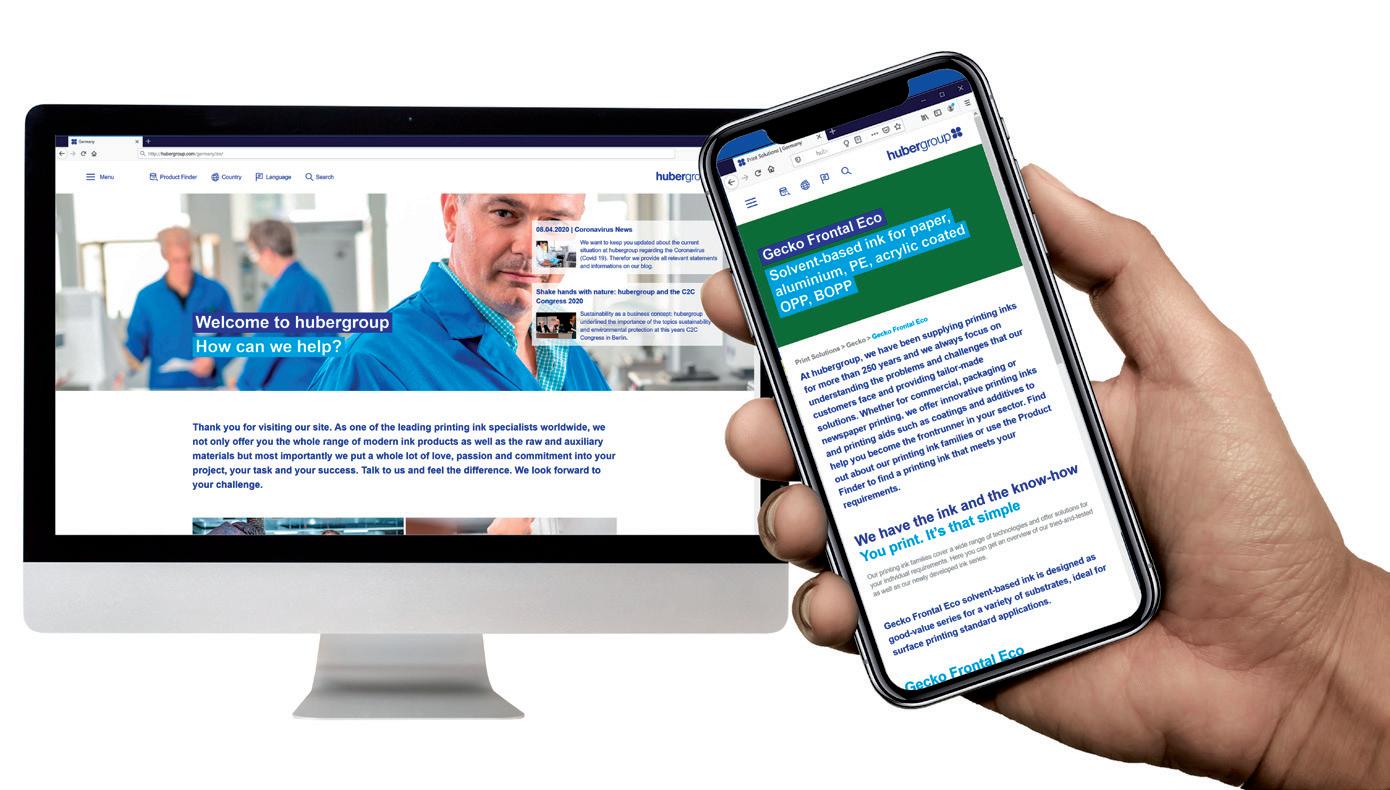
Tarsus Group has postponed its upcoming edition of Labelexpo Southeast Asia 2020 (due to take place at Bangkok’s International Trade and Exhibition Center (BITEC) from 7 – 9 May 2020) in light of concerns over coronavirus/COVID-19. The show will now take place on 10 – 12 September 2020.
Lisa Milburn, managing director of Labelexpo Global Series, said: “We have taken the difficult decision to postpone Labelexpo Southeast Asia 2020 in May due to coronavirus/COVID-19. This is an unprecedented situation, and given the vast amount of preparation that goes into our shows, not a decision we have taken lightly. However, the health and safety of our exhibitors, visitors and staff is our top priority, and working on the advice of our local partners and BITEC, we feel the best course of action is to postpone the show until September.

We have been continuously monitoring the situation in Thailand and the wider Southeast Asia region, and are following all local government advice, as well as that of the World Health Organization.
We thank all our exhibitors and partners for their understanding at this difficult time, and look forward to working with them on the rescheduled show. All other Labelexpo shows in 2020 are currently scheduled to go ahead as planned.”
Xeikon committed to providing ongoing critical support to customers during Corona crisis
Sufficient stocks on hand of consumables required for production operations.

Xeikon, provider of equipment, services and consumables for digitally printed labels and packaging, reconfirmed its dedication to continuing to make critical consumables available for its presses. This enables customers to produce the documentation, labels and packaging required to get food, health and pharmaceutical products to market during the Corona crisis. As widely covered by the media, the coronavirus has impacted the health and well-being of many people in various countries around the world. Many businesses worldwide are impacted by production disturbances, supply and delivery interruptions, and Xeikon is committed to minimising these for its customers.
“Many of our customers, particularly converters, are producing essential print such as documentation, labels and packaging for critical items like pharmaceutical products, food for supermarkets, labels for disinfectant bottles, to name but a few, and rely on our solutions to ensure that essential supplies are made available to sick, vulnerable and isolated people,” says Benoit Chatelard, Xeikon’s President &CEO. “In order for them to keep up with production demands during this crisis, they need reliable access to consumables, parts and services from Xeikon, and our entire team is committed to doing its best to ensure a consistent flow of these items. Xeikon has sufficient stock and a stable supply in consumables and spares to support our customers globally. However, as many flights worldwide have been cancelled and as countries enact more restrictions on traffic, we could expect some shipments to take longer than before to be delivered. That being said, we will keep our customers informed of the status of all shipments and requests for service so they know exactly what to expect.”
Chatelard notes that the company’s first priority is to safeguard the health of its employees per World Health Organization and government guidelines, closely followed by implementation of measures to guarantee the continuity of its supply chain and safeguard business continuity for customers. “While some cases may require on-site visits from a technician,” he says, “there is a can do with remote diagnostics and technical support. All our machines are connected and, to a large extent, self-diagnostic. For interactive discussions with customers and prospects, we are investing in tools that allow us to produce virtual demonstrations and testing for customers. We are also closely monitoring the economic impact of the Corona emergency, both to the overall printing industry and for Xeikon’s business.”
In addition, in light of the postponement of drupa 2020 to April 2021, Xeikon is revisiting its go-to-market strategy and preparing to be fully ready to deal with both the current crisis and drupa 2021 by continuing to bring to market the innovation that the industry has come to expect from the company. “We will be bringing some new products to market prior to drupa,” Chatelard states, “in order to make the latest technology available to our
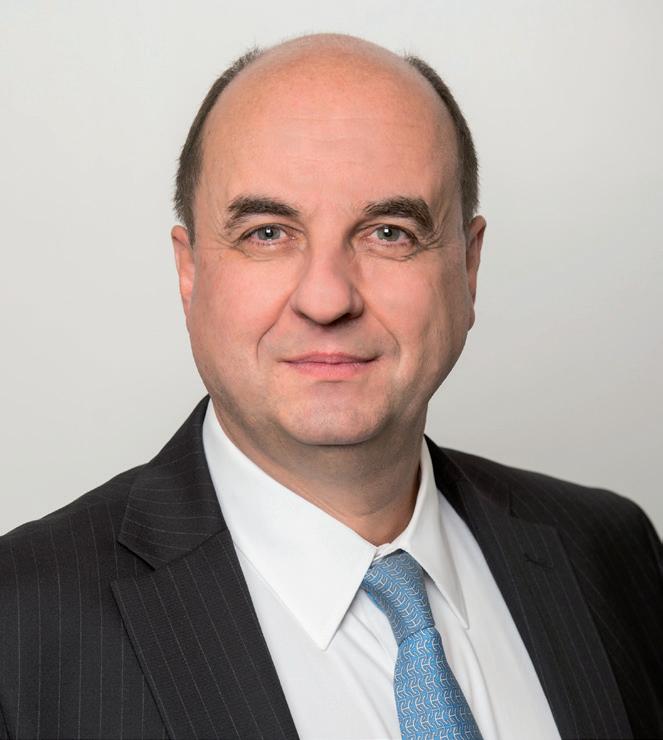
NiceLabel, global developer of label design software and label management systems, is offering free subscriptions of its cloud-based labeling solution and technical consulting services to organizations that have joined the fight against COVID-19.
NiceLabel has launched the non-commercial and non-profit-based initiative in order to help these organizations get much needed deliveries of medical equipment and supplies; respirators, disinfectants, masks or other critical supplies to those in need as quickly as possible.
Having the cloud-based labeling solution in place will enable these organizations to produce new labels quickly and rapidly add them to the packaging used on their new product lines to ensure that equipment and materials arrive on the front line without delay. Label Cloud is a cloud-based version of the NiceLabel Label Management System. Organizations likely to qualify include manufacturers re-focusing on the production of critical healthcare supplies; farms and other food producers who must meet new labeling requirements to supply critical food to supermarkets; hospitals and other organizations involved in fighting COVID-19.
NiceLabel to provide free label cloud software
customers. And by drupa 2021, we expect to have even more innovation available to announce and exhibit so customers can be well-prepared for the recovery that is sure to come.”
Last but certainly not least, let’s thank all the Xeikon employees for their engagement and contribution to allow Xeikon to continue its operations in these critical times.

Label Products finds ‘complete package’ with Durst and Wifac
Label Products has invested in a Tau 330 RSC E inkjet press from Durst and Wifac to continue organic expansion.
“The deal with Durst and Wifac, its distribution and service partner across BENELUX, is a complete package,” says Matthias Dhondt who, together with Stephan and Maarten Dhondt, forms the future of Label Products. “Our investment in the Tau 330 RSC E plays a key role. With our spread of markets and a strong commercial presence in Belgium, the Netherlands and France we are going to benefit from that growth,” adds Mr. Dhondt.
“The Durst Tau 330 RSC E immediately caught our attention, but we needed to undertake a thorough investigation of the market,” he said. “We visited companies in Switzerland, Austria, Poland, Italy and other countries. We analyzed the operation of the various heads, the quality of the work, the speed of the machines, the price of ink and substrates. At the end we opted for the Tau 330 RSC E because of its impressive print quality and productivity and have never looked back. It’s a complete package. Ultimately, it’s about the total cost of ownership. At first, we wondered whether we would have enough volume on the press, but that hasn’t been a problem. More and more variable and tailor-made labels are being provided for various customers. So, a digital press is better than flexo printing.”
Another important factor for choosing Durst was the support and service provided through Wifac. “You can’t afford downtime and we have two service technicians on standby,” said Mr. Dhondt. But since the installation in the middle of 2019, not once have we needed to use them. The relatively simple operation of the press is another positive element for the business, particularly when skilled operators are hard to find due to skill shortages. We are a real family business with an open mind to helping our employees. In our finishing department, we were able to provide one employee with the chance to work as an operator on the Durst Tau 330 RSC E. She seized that opportunity with both hands.”
Continuing controlled growth is the aim for Label Products this year, as well as certifying itself for the British Retail Consortium. The BRC’s Standard for Food covers hygiene and safety requirements for food processing companies supplying the retail sector. From special clothing and hygiene regulations to visitor registration, the BRC works well throughout the whole company. “We have a focus on food sectors, but don’t lose sight of other markets,” Mr. Dhondt. “The strength of BRC is that this approach takes Label Products to a much higher level of quality.”
The family-owned company employing 36 people, which was founded by Pieter and Marc Dhondt in 1986, produces labels and tags on four flexo and digital production machines. Originally started as an offset print business, it has expanded into new areas, including label markets.
Helmuth Munter, Durst’s Segment Manager, Labels and Package Printing, said: “Our Tau RSC platform is setting new benchmarks in growing numbers of markets for companies such as Label Products. We offer a total package to all our customers in terms of highquality, the best possible service and resulting production reliability. Across BENELUX, this is with our partner Wifac. It’s a win-win combination.”

Sustainability in Packaging Asia 2020, Singapore
Smithers are bringing Sustainability in Packaging to Asia, Singapore from 22-24 September 2020.

On 22 September, Smithers will focus on Sustainable E-commerce Packaging. Visitors will have the exclusive opportunity to hear from expert speakers who will present on a range of topics including global market trends, innovations and developments in e-commerce packaging.
Already confirmed to attend the conference as Advisory Board Members and speakers include DHL, DELL, P&G, Amcor, EFI, JD Logistics, China Post, Johnson & Johnson, KCL, CaiNiao (part of Alibaba), Kezzler, Sealed Air, Tetra Pak, BetterPackaging and more.
Sustainability in Packaging conference will be held from 23-24 September. This 2-day conference will feature presentations exploring the latest technologies, emerging applications, relevant opportunities and challenges surrounding recycling, sustainability and the environment of the sustainable packaging industry. Companies already confirmed to attend include Nestle, Unilever, Mondelez, Coca-Cola, WWF,

BioPak, Borouge, GA Circular, LUSH, GSK, Avery Dennison, WestRock, UPM, Johnson & Johnson, Colgate-Palmolive, Associated British Foods, Food Industry Asia, CPRRA, UPM RAFLATAC, SABIC, Veolia and many more.

By joining Smithers at Sustainability in Packaging Asia 2020, visitors will hear the latest insights, trends and solutions of the packaging supply chain from key decision makers and influencers.
