
23 minute read
Konica Minolta’s New bizhub i Series
digital printing
Konica Minolta’s New bizhub i Series
Advertisement
- to facilitate smarter and safer remote digital printing experience for new-age offi ces.
The new solutions reduce contact with common touch points that can act like potential virus vectors enabling individuals to conduct printing operations remotely using their personal mobile devices.
The Covid-19 crisis has emerged as the black swan event of the 21st century, leaving the work cultures across organisations the world over in a shambles. Against this backdrop, new-age professionals are using the digital ecosystem to bypass the geographical constraints of the lockdown as they scramble to meet their daily deliverables from the safe confines of their homes. It is here that Konica Minolta’s innovative range of digital Multifunctional printers under the New bizhub i Series enters the picture to provide quarantined professionals with smarter and safer office printing and workflow management solutions.
The New bizhub i Series comprises multi-functional printers in the colour and monochrome categories. The former range includes bizhub C250i, bizhub C300i, bizhub C360i, and bizhub C450i colour printers. On the other hand, bizhub 226i, bizhub 266i, bizhub306i, bizhub 225i & bizhub 205i constitute the monochrome line up.
These solutions not only empower modern workplaces to print remotely but also to seamlessly digitize documents and streamline the workflow. In this way, the KM range of digital MFPs can lend a competitive edge to organizations over their peers by enabling them to maintain business continuity in keeping with the social distancing protocols. The following some of the key features enabled by the KM products:
> The New bizhub i Series comprises multi-functional printers in the colour and monochrome categories. > Empowering modern workplaces to print remotely, digitize documents and streamline workflow. > Banner printing function, IC card authentication, Virus Scan and high speed SSD etc.
Key Notes :
Mobile printing As the normalization of disease-curbing social distancing codes has demonstrated, the minimisation of one’s physical contact environment will continue to be the priority for individuals across the globe. In the face of this transformative effect of the pandemic across the global business ecosystem, KM solutions reduce contact with common touch points such as computer screens that can act like potential Covid-19 vectors. Instead, MFPs printers under the New bizhub i Series enable individuals to conduct printing operations remotely using their personal mobile devices.
Banner print function Besides enforcing the social distancing-compliant precautionary measures at the workplace, organisations also need to actively spread awareness to tackle Covid-19. Banners comprise one of the effective awareness-building tools that can be employed at offices now that the work is resuming slowly. Once the economic ball starts rolling again

and business functions across sectors regain their momentum, offices will be required to issue circulars, notices for precautions, advisory, etc. for not just the workforce but visitors as well. And KM MFPs are wellequipped to meet this demand.
IC card authentication In sync with the idea of minimising the physical contact environment, the biometricbased systems will now be replaced by contactless alternatives. The use of IC card authentication (employee ID card) feature comprises one such solution to the problem at hand.The MFPs under New bizhubi Series come equipped with this feature. All a user needs to do is, wave their ID card over a card reader on the machine to print, thereby forgoing the need to touch the MFP Screen.
Xeikon launches SIRIUS technology
Besides being compatible with social distancing codes, the IC card authentication also facilitates robust cyber security measure in an increasingly sophisticated threat landscape. Since only the authorized users can print or scan using IC card
Technology used in brand new Xeikon SX30000 digital press.
Xeikon unveils its ground-breaking new generation dry toner technology for the graphic arts industry. It delivers higher speeds, reduced cost of ownership and further improved quality, and – even better – the first digital press based on this new technology will be launched and commercially available as of June 2020.
By introducing the ‘Power Of Dry Toner’ campaign last year, Xeikon made it absolutely clear that it remains convinced of the unique power that dry toner technology brings to the graphic arts market – pushing its boundaries even further. Today, it proves its case by announcing the next generation Xeikon SX30000 press: an entirely new, robust single pass duplex machine, powered by the new SIRIUS technology, able to run at a printing width of 20 inch (or 508 mm) on a broad range of substrates at 98 ft/min (or 30 meters/minute), 404ppm A4) – boasting an average speed increase of more than 50% throughout the range of 40-350 gsm versus the previous platform.
Setting a new standard in dry toner Xeikon has been allocating major resources since 2017 to set a new standard in dry toner technology and develop a new platform for the graphic arts industry. “The watercooled LDAs, with 1200x3600 dpi technology and the single pass duplex, full rotary concept, have remained unchanged, as well as the 5/5 print station setup. Almost everything else has been re-engineered”, says Dimitri Van Gaever of Xeikon. “One of the things that really sets the SIRIUS technology apart is its ability to print on heavy substrates at high speeds.
Dimitri Van Gaever explains some of the core components that enable SIRIUS to set a new standard. We have been working along 4 major axes: toner development, imaging technology, fusing technology and media conditioning, resulting in more than 400 design changes and developments compared to the previous generation. All these core components have been redesigned and enhanced to deliver superior quality, market leading performance, unequalled sustainability, widest application range and best-in-class TCO.
An important step to bring SIRIUS technology to a new era of productivity is realised thanks to Xeikon’s new EkoFuse technology: a new fuser and a patented new crossflow cooling system add up to achieve superior print quality levels at market leading speeds.”
For our newly developed SIRIUS toner, we have changed the production parameters of the toner and have improved the charging kinetics properties by adapting the outer shell of the toner to cope with the higher engine speed. Our new developer unit ensures superior image quality for high coverage applications.
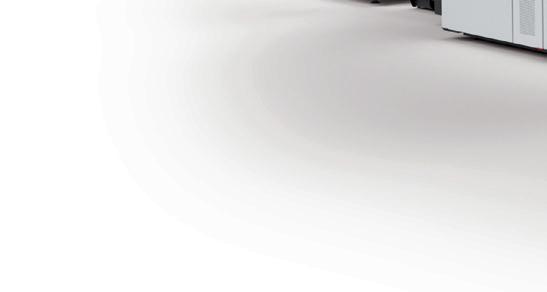
Higher productivity for high value applications
authentication, this feature ensures sensitive documents and business-critical information do not fall into the wrong hands.
In this manner, Konica Minolta underlines its commitment to providing a smart, safe, and secure digital printing experience to new-age offices across India. At the same time, the innovative solutions under the New bizhub i Series further strengthens the company’s position as an innovator in the country’s office printing landscape.
With the SX30000, Xeikon is first and foremost aiming at high value applications, usually featuring high coverage color content on high-quality papers combined with superior quality requirements. “This can be in the book printing segment or high-quality direct mail, but because of the versatility of the technology, it might also be in retail and signage materials, security printing and other general commercial print. Furthermore, we are looking at customers who need higher productivity combined with lower running cost and a compelling overall TCO.”
“We have been the pioneers of dry toner technology, and we continue to see opportunities to further enhance it and improve on it,” says Dimitri Van Gaever. “The technology has been named SIRIUS – after the brightest star in the night sky and in reference to its role in helping people to navigate and set course in various cultures throughout history. We believe this platform will lead the way towards a profitable business for our existing and future customers.”

FUJIFILM ColorPath SYNC now supports X-Rite i1Pro 3 Spectrophotometers
Using the i1Pro 3 Family with ColorPath SYNC allows printers to quickly implement essential colour management solutions that seamlessly integrate with Fujifilm’s XMF Workflow.
X-Rite and Pantone, color science and technology experts, have announced that Fujifilm’s ColorPath SYNC cloud-based colour management tools now support the new i1Pro 3 Family of spectrophotometers. Print providers will be able to quickly and easily create ICC profiles using the i1Pro 3 devices and align production devices to a designated color target using ColorPath SYNC.
“X-Rite’s i1Pro line of measuring devices has always been an integral part of our ColorPath SYNC suite of color management tools,” said Peter Pretzer, ColorPath Solutions Development Manager for FUJIFILM North America, Graphic Systems Division. “We look forward to the gains in productivity both we and our customers will enjoy with the new i1Pro 3 Family in conjunction with ColorPath SYNC.”
The i1Pro 3 Family is ideal for print and graphic arts professionals who require accurate color from their printer, display, and projector. The i1Pro 3 is more accurate, reliable and twice as fast as its predecessor. It simultaneously measures M0, M1, and M2 in a single pass while accounting for optical brighteners. Prepress and print operators can quickly predict how colors printed on optically-brightened substrates will look under different lighting conditions. The i1Pro 3 Plus features a larger 8mm aperture to support additional materials and substrates used in digital printing applications. It also supports transmission scanning for backlit film and materials used in signage. With the addition of the i1iO3, both the i1Pro 3 and i1Pro 3 Plus can be used in automated measurement workflows.
“X-Rite is excited to provide Fujifilm customers with best-in-class solutions to improve their digital printing workflows,” said Ray Cheydleur, Print and Imaging Product Portfolio Manager, X-Rite. “The i1Pro 3 speeds the measurement process with its new single pass scanning workflow for all M conditions. When paired with ColorPath SYNC, print customers can achieve a connected workflow to define printing system settings, create ICC profiles, linearize, validate, and maintain compliance with printing standards.”
The i1Pro 3 is now available. ColorPath SYNC is Fujifilm’s suite of highquality, cloud-based colour management tools that enable users from novice to expert to align multiple output devices quickly, easily, and accurately to industry-standard targets and specifications. ColorPath SYNC creates optimized G7 and ISO alignment curves, high quality optimized device link profiles with integrated validation, and

Fujifilm India extends support to combat Covid-19 pandemic
optimized named colour profiles for fast and accurate brand color libraries — including PANTONE-licensed M0, M1 and M2 simulations — for Fujifilm’s inkjet devices. Please visit Fujifilm’s ColorPath SYNC website for more information.
- Supplies N95 masks and PPE kits to healthcare professionals at PGIMER, Chandigarh.

Fujifilm India, one of the leading names in imaging technologies, has pledged its commitment and contribution towards aid for the unprecedented crisis caused due to the Coronavirus pandemic outbreak.
The company has announced the supply of 200 N95 respiratory & surgical facemasks along with 40 PPE kits to healthcare professionals at Post Graduate Institute of Medical Education & Research, Chandigarh. To combat the spread of the disease, Fujifilm is providing these essential preventive healthcare utility (PPE) kits to doctors, which include Surgeon Gown, Face Mask, Gloves, Preventive Eye wear, Hood Cap and Shoe Cover.
Commenting on this, Mr. Haruto Iwata, Managing Director, Fujifilm India Pvt. Ltd. said, “We all are witnessing an unprecedented and difficult time of our lives due to COVID-19 global pandemic. Committed to work together with the people of India in this hour of difficulty, we have introduced these measures to ensure adequate protective equipment and masks are available for healthcare specialists and associated workforce present on the front lines. At Fujifilm, we believe it’s time for all of us to come together and protect the humanity by acting responsibly and by doing what we can to prevent further spread and avoid disruptions from the COVID-19 virus.”
In addition, the company is installing Computed Radiology, Digital Radiology systems and imagers across isolation wards at hospitals to ensure effective monitoring and controlling the disease outbreaks. These technologies will empower clinicians to improve efficiency and expedite the early diagnosis of the disease.

Bobst reaches milestone with sale of 300th VISIONCUT
The long-standing Bobst customer owning 5 flatbed die cutters, many folder-gluers and a MASTERFLEX-HD adds the 300th VISIONCUT.
Bobst has announced that it has sold its 300th VISIONCUT. The flat-bed die-cutting machine was purchased by Adams, a corrugated packaging manufacturer, based in Poland. The company is a long-standing Bobst customer, already owning five flatbed die-cutters, two of which are VISIONCUT machines and a range of folder-gluers, plus the outstanding MASTERFLEX-HD 5-colour printing press.
Since its launch, VISIONCUT has proven popular with manufacturers around the world looking for first-class die-cutting capabilities, while at the same time delivering true costeffectiveness, flexibility and efficiency.
Able to handle all types of materials and suitable for both long and short runs, VISIONCUT combines robustness, low cost ownership, straightforward handling and optimum performance to meet the needs of today’s converters.
ADAMS supplies a wide range of corrugated packaging to sectors including food and beverage, industrial chemicals, point of sale and display signage, and more recently e-commerce markets.
Adam Skrzyniarz, Founder and President of the management board at ADAMS, commented: “We are operating in a very competitive environment and we are strongly attuned to the needs of the market in order to quickly respond to any new developments and expectations of our customers. It’s important that our equipment and infrastructure enables us to deliver the high-quality standards that both we and our customers demand.
“Thanks to VISIONCUT, our customers can receive high-quality products, precisely tailored to their needs, for the best price. The machine offers a short changeover time, helping us to maximize uptime and productivity, along with an advanced printto-cut register system which delivers the high precision and accuracy that we need. With VISIONCUT, we can improve production planning capabilities and deliver first-time right excellence, every time.”
VISIONCUT was designed to be compact, ideal for companies looking for a machine with a small footprint, and easily integrated into existing production lines. For added value, it also supports a range of peripherals, increasing production output and flexibility further – both features were key selling points for ADAMS when choosing the die-cutter.
Installation was efficient and did not interrupt the production process. Bobst worked closely with ADAMS’ technicians to ensure

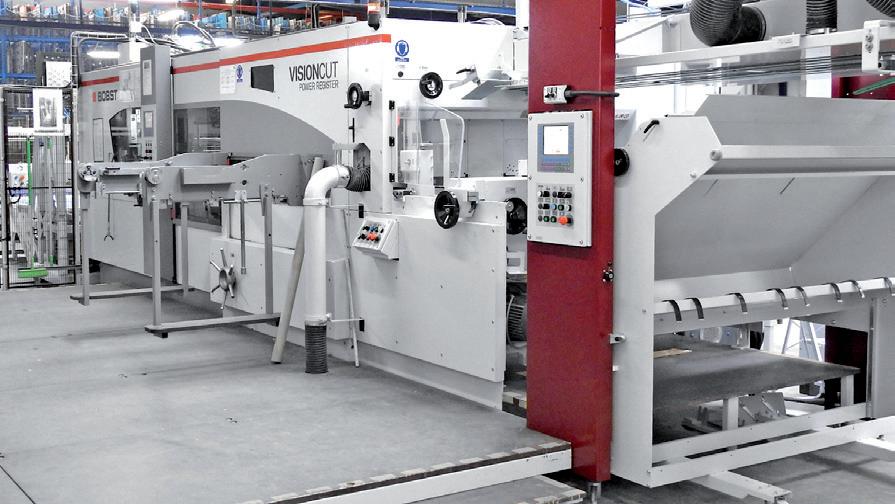
the set up was to their requirements and ran smoothly.
Anna Skrzyniarz, Vice President at ADAMS added: “We regard Bobst as a reliable partner that offers the latest solutions on the market and guarantees after-sales service and availability of spare parts. As a partner, Bobst works with us to customise their products precisely to the needs of ADAMS, which is why we keep investing in new technologies with them.
“As a family-owned company, we value good, long-term relationships with our business partners. It’s why Bobst is a perfect match with our business model. For ADAMS, they are a trusted, reliable partner and work closely with us to customize their range of products to our needs. The support from Bobst is excellent – we can always count on them!”
Anello Meloro, Product Sales Director at Bobst, said: “VISIONCUT is the ideal diecutting solution for our highly-valued client, ADAMS. It ticked the boxes for all their needs in terms of performance, versatility, size and efficiency. We are delighted to have once again been able to supply them with a machine that delivers on all their touchpoints.
“It’s a momentous occasion for Bobst to have sold its 300th VISIONCUT, particularly following so closely to the same milestone for MASTERCUT. It is testament to Bobst in being able to deliver a wide portfolio of machines which meet the needs of customers operating in a variety of markets and at all levels of production.”
Italgrafi ca: It’s never just a Label
For industrial label expert Italgrafi ca, a label is the brand’s business card. It has invested in 3 fully customized OMET Flexy-S 330, 1 XFLEX X6 and a XJET hybrid, with a second XJET fl exo + digital hybrid to be installed in 2020.
The information on the labels changes constantly. To be able to respond effectively to customer requests, Italgrafi ca is investing in this aspect. It distinguishes itself by doing more than the competitors.
Key Notes :
> After the decline of the durable labels in 2008-2009, many companies relocated to Eastern Europe. > Italgrafica, on the other hand, acted against the trend, continuing its activity in Italy > In recent times
Italgrafica has installed several OMET machines suiting its varied needs. “To be successful in a highly competitive and constantly evolving market, it is absolutely necessary to be increasingly flexible, quick and innovative”. These are the guiding principles of Francesco Niorettini, General Manager of Italgrafica Sistemi, one of the leading companies of the industrial label sector.
Italgrafica Sistemi began production in 1992, thanks to the experience gained in the screen printing sector by Francesco Niorettini. “We started from scratch” – quotes the General Manager – taking a path that has led us to a group turnover of around 12 million euros today. We initially concentrated on the industrial sector, with technical labels to be applied on various equipment. This allowed us to develop an in-depth know-how on adhesives and other features of these labels”.
In 2004-2005 Italgrafica started producing in additional sectors such as food, beverage and cosmetics. “We realized that the market was asking technical characteristics that nobody was satisfying, especially in the field of adhesives, where we were highly specialized. For example: a customer in the food sector needed easily removable labels for glass jars, because the end users wanted to reuse the containers. This is why we have developed a specific type of adhesive and, given the excellent results, today we offer this adhesive to other customers”.
Technical skills in the field of adhesives and materials,

associated with extreme flexibility, resulted in an irreplaceable and highly differentiating competitive advantage against the competitors. “Customer, with their needs and products, are always the starting points for us,” adds Francesco Niorettini. “Our proposal and solutions starts from there. For example we can offer very technical premium materials, to our customers in the automotive sector or provide economical and optimal solutions for food manufacturers as per the specific needs of their sector. Our strength is in the ability to understand precisely the need of our customers, by acting as their consultant and presenting them with personalized offerings”.
After the decline of the durable labels (freshmen or labels for household appliances, boilers, industrial machines) in 2008-2009, many companies have relocated to Eastern Europe. Italgrafica, on the other hand, acted against the trend, continuing its activity
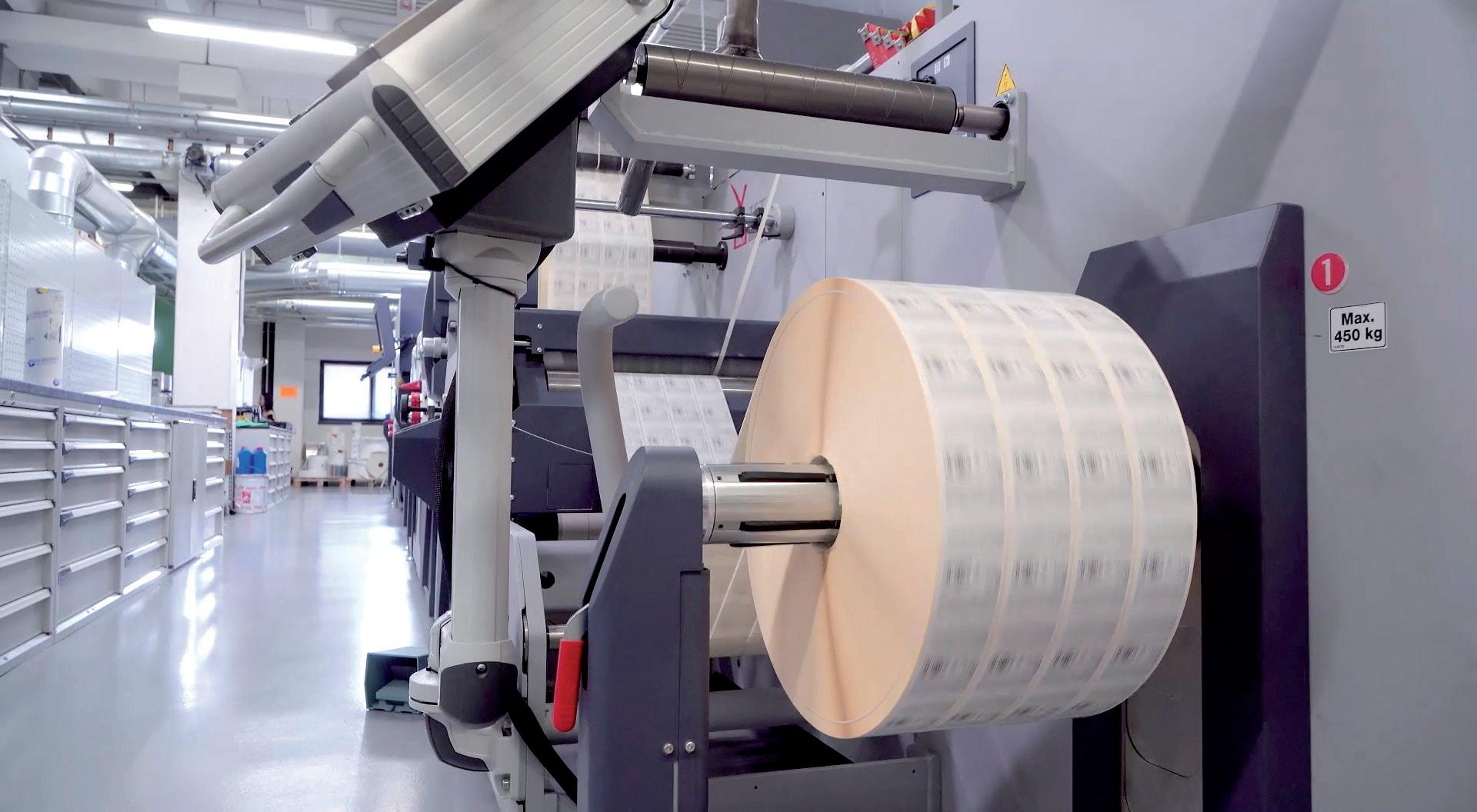
in Italy and focusing on innovation, paying attention to materials, finishes and details. “In those years we distinguished ourselves by doing more than our competitors, who only answer to a customer’s request and fail to provide any advice to help their customers grow,” explains Francesco. “For us it was totally opposite! We advised our customers to produce innovative and compliant labels and helped in optimizing their cost. In addition to this we are constantly looking for innovations in materials by trying to understand in detail their strengths and weaknesses, analyzing and verifying their characteristics and then offering the most suitable ones to our customers.” Unlike many other competitors, Italgrafica doesn’t consider this choice as “expensive”: it is a profitable investment if you can count on a solid organizational structure and internal procedures.
In recent times to enhance its value proposition to the market, Italgrafica has installed several OMET machines, all customized for particular solutions the company has led into (i.e. multilayer labels, foils and special finishes). “When we purchased the first machine – says Francesco Niorettini - we chose OMET because we needed to print a particular format (not for the width but for the print pitch) that other competitors were not capable to offer. OMET, unlike the others, could install cylinders up to 24 inches. Immediately after the first machine we understood that OMET is a performance driven company with the ability to quickly respond to our needs. It’s this trust that we have built with OMET, that we consider it to be a partner rather than a supplier. I can pick up the phone and speak with several people within the company, who are always willing to find solutions to our needs with precision and speed. OMET is structured to develop new and customized projects like the ones we deal with. Although it has grown significantly in recent years, it has not lost its flexibility, which indeed is one of its strengths”.
Hybrid technology was the latest addition to Italgrafica and Niorettini believes it is strategic for the future of the market. “We installed the first hybrid OMET XJet in 2018 - Niorettini says -. We have gained experience and understood that it is the right machine for the type of market we are in. On this press (and on the next one that we are going to soon install) we will plan high quantity print runs, which we traditionally used to print on flexo machines. Although printing is more expensive, the extra cost is offset by saving time in controlling the variables, especially in jobs where the number of variables are high. Considering time is the most expensive resource we have, saving time on job changes makes up for the higher cost of printing, as compared to flexo”.
“Even though, today there are large print runs – continues Francesco Niorettini – but a significant portion of our production is made by orders with limited print runs, often involving numerous variables. Thanks to OMET customizable platform, we have configured the OMET hybrid machines so that the result is excellent even in these cases.”
Will hybrid technology grow in the future? “Definitely yes” – replies Francesco Niorettini – because of the peculiarities of the Italian market, characterized by different print runs which is not common in markets abroad. Not only the quantities, it’s also the frequency
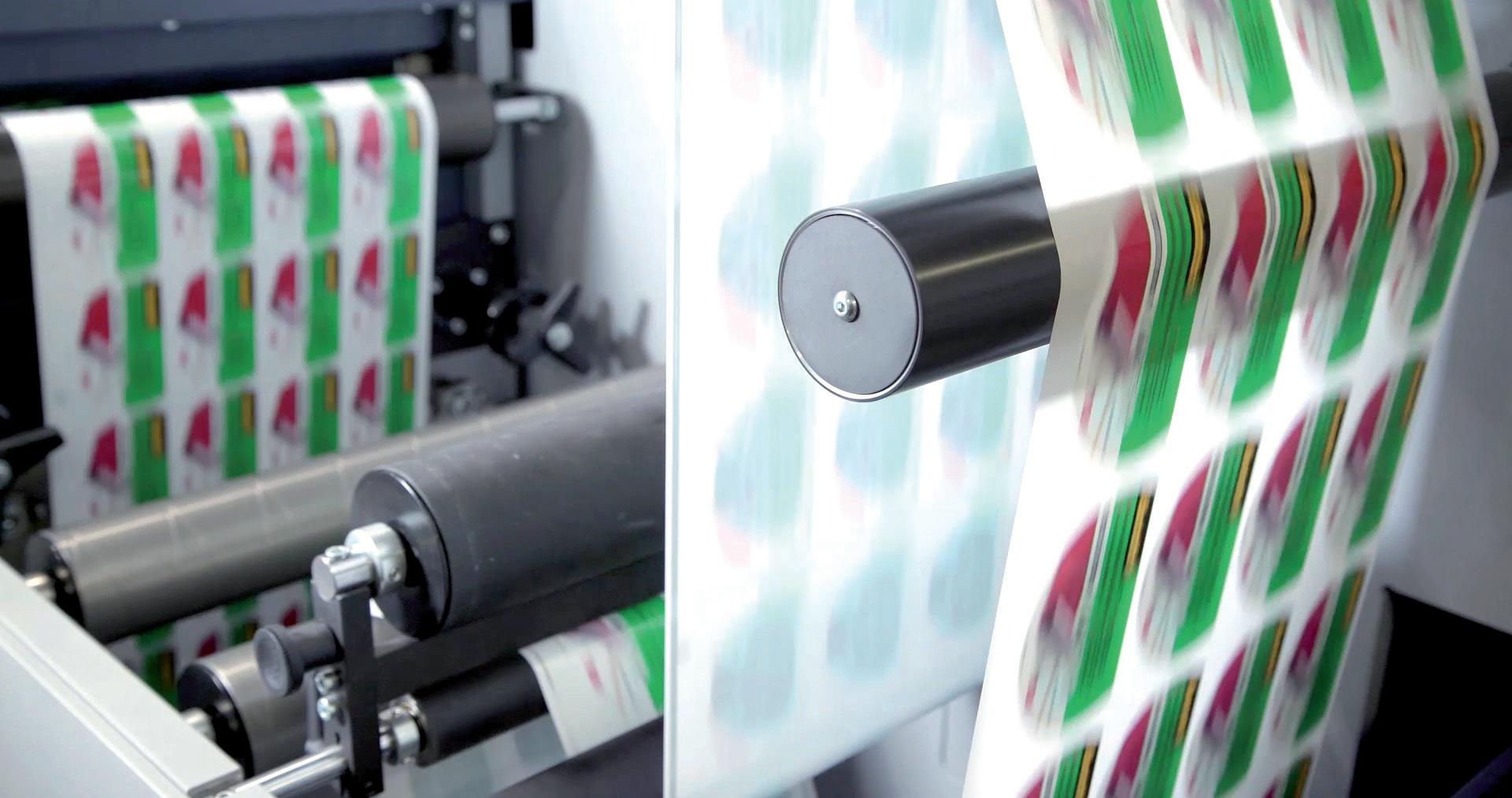
of orders that makes us believe that hybrid technology is here to grow as in our country orders can be placed every fortnight, as compared to markets aboard where its often quarterly.
“Printers need to be increasingly flexible and quick if they want to face the market of the future, which will be more personalized and dynamic,” concludes Francesco Niorettini. “We are constantly reducing our process inventory and manage production with kanban logistic systems where variable data is highly requested. These factors must be considered in the upstream and downstream production phases. Think of the labels with nutritional tables that undergo changes whenever a new legislation comes into force or for export, where the rules change frequently. The information on the labels changes constantly: we will either start to make only labels with brand and QR code, or we will have to be able to respond effectively to customer requests. We are investing in this second aspect, because we know that a label is never just a label, it’s the brand’s business card.”

Xeikon CX300, based on Cheetah 2.0 technology, addresses current market needs in the label market with versatility, productivity and quality.
Xeikon has launched a new digital label press based on next-generation Cheetah 2.0 technology. As demand grows for mass customization, shorter lead times and more product diversification, the new Xeikon CX300 digital label press is an innovative solution that keeps both label converters and their brand owner customers at the forefront of a rapidly evolving industry.
“The Xeikon CX300 delivers exceptional application versatility, designed to achieve the highest possible OEE (Overall Equipment Effectiveness) and is even more productive than the very successful Xeikon CX3 first generation of Cheetah presses,” said Filip Weymans, Vice President of Marketing. “Today’s investments need to deliver results. Printing speed is an important factor, but combining that with a low OEE would not deliver the value printers and label converters are looking for. With Cheetah 2.0 technology, we have focused on combining high production speeds with a high OEE, ultimately resulting in maximum sellable output.”
Cheetah 2.0 technology Cheetah 2.0 technology is based on the proven, scalable Xeikon press architecture that includes five print stations and a full rotary process with a variable repeat length. Also featured:
Printing station Dry toner printing process operating at 30m/ min (98ft/min).
Web width can vary between 220mm (8.6”) and 512mm (20.3”) wide using a LED imaging head operating at 1200x3600 dpi delivering offset/gravure image quality.
The Cheetah developer station, which holds the Cheetah toner, ensures higher color consistency across and along the web, ensuring a higher volume of sellable output with reduced waste.
New generation interfaces The Man-Machine interface has been designed in a way that the operator can assess the status of his press from a distance. The interface also communicates the specific actions the operator needs to perform.
The Machine-Machine interface allows for the integration of pre and post equipment either inline or offline. Throughout this interface, relevant information about the jobs is transferred digitally to the appropriate individual module to eliminate human errors, as the information flows seamlessly through the manufacturing process, which again contributes to the overall OEE.
Cloud connected Built-in technology reporting on performance, availability, etc., in real time, providing data that can be translated into information for fact-based decision making.
Design considerations In designing the Cheetah 2.0 platform, ergonomics for both service engineers and operators were a focus, plus it uses components that simply last long with the objective of reducing maintenance and repair times.
Integrated quality management systems monitor and automatically adjust press operation. This includes the density and tone curve of the process color but also the density of identified brand colors and registration.
Xeikon CX300 The Xeikon CX300 is a 330mm (13”) label press that can offer production capacity of over 50.000 square meters per month in a single shift operation. The full-colour press is equipped with five print stations, including CMYK and single-pass opaque white but can also support color gamut expansion, custom or security colours.
Based on Cheetah 2.0 technology, the Xeikon CX300 can easily operate in a threeshift operation and still deliver high value work. Strong, growing end-use markets such as food, pharmaceuticals and other markets using self-adhesive labels can be supported with the Xeikon CX300. Its dry toner technology surpasses any other digital printing technology with respect to food safety. The Cheetah toner also incorporates the recently announced QB toner technology, making it even more future-proofed against upcoming legislation and regulatory requirements.
Other markets ideally served by the Xeikon CX300 are those that use challenging substrates such as natural structured papers. This includes wine & spirits, craft beer, luxury food, and more. Health & beauty labels also benefit from high-quality full-color printing and single-pass opaque white toner. These are just a few of the end-use market applications that make the Xeikon CX300 a versatile solution that can also be used for the production of heat transfer labels, inmould labelling, wet glue, wraparound labels, and cartons.
Xeikon’s fleXflow process enables the Xeikon CX300 to produce flexible pouches, combining dry toner printing with thermal lamination to deliver a laminated construction with turnaround times never before possible, and increased sustainability driven by the fact that there is no solvent used during either printing or laminating. Xeikon fleXflow is driven by the industry-leading Xeikon X-800 digital front end and includes an innovative inline thermal lamination process.
“The Xeikon CX300 can be the cornerstone of digitizing label manufacturing,” Weymans concluded. “Its built-in technologies enable label converters to address current and future industry demands: connectivity, responsiveness, flexibility and scalability. We believe the Xeikon CX300 can be a valuable addition to any label shop floor and the spark that ignites a digitization process that is unmatched in the industry.”

The Xeikon CX300 has been commercially available since April 2020.