
27 minute read
COMPLETE PACKAGE RIG EXCEEDS EXPECTATIONS
from Quarry Feb 2019
by Prime Group
Donnelly Blasting Services’ Epiroc SmartROC T40 smart rig, fitted with silenced kit boom, at Fulton Hogan’s Blue Rock Quarry.
A drill rig has set a new in-house record for the manufacturer with the number of metres drilled and litres consumed in one shift. Damian Christie spoke to Daniel Kirwan, of Epiroc, and father and son Jason and Dan Donnelly, of Donnelly Blasting Services, about their SmartROC T40 smart rig.
Donnelly Blasting Services (DBS) is headquartered in Jimboomba, in southeast Queensland. The Australianowned, family-run business conducts work in numerous quarries and construction and dam projects in southeast Queensland and northern New South Wales, with about 80 per cent of its clients being quarries.
The company offers the full rock on ground service. To quote Dan Donnelly, “we do everything in-house – the surveying, markout, boretrack design, shotfiring, monitoring, and drilling”.
His father and company founder Jason added: “We float our rigs, mark our own holes, survey, drill our own holes, load the fire, do all the reporting, all the surveying and all the blast monitoring ourselves. For our explosives, we use Orica as a contractor but we also have our own explosives trucks.” Jason started the business 20 years ago after he spent 10 years as a shotfirer for Orica Mining Services. He wanted to pursue a career as a part-time contract shotfirer but ultimately formed a business that today employs 30 staff, including around 20 drill operators, and keeps him busy full-time.
DBS has a modern fleet of Epiroc smart rigs and specialised rigs that can be configured for special project requirements. Added to that are mobile manufacturing units (or ANFO trucks) with augering and blowloading capabilities, a 25-tonne excavator with rock breaker and a 30-tonne widening tri-axle low loader.
Jason said the company has built its reputation on flexibility, which is “we’re able to do what the customer wants”.
“We have GPS guidance on our rig – a lot of the larger rock on ground services don’t have that,” he said. “We can control the whole outcome because we do the whole job. We put the extra holes in, we control the drilling [with machine guidance] – we understand what’s going on with the drilling. We have the latest technologies in the drills, so we’re saving our customers money. Some other companies can use up to 400 or 500 litres of fuel a day – we’re down to below 200. We work with our customers for a better outcome.”
DBS’s association with drill rig manufacturer and supplier Epiroc covers nearly the whole lifetime of the business.
“We started with Ingersoll-Rand, which was bought by Atlas Copco,” Jason recalled. “It’s been a long association but we’ve probably used Atlas Copco [now Epiroc] for 15 years. We ended up changing to them from another brand for the technology, fuel burn, operator comfort, reliability and product support.”
SOUND OF SILENCE DBS’s 20-strong Epiroc/Atlas Copco drill rig fleet comprises manual-operated PowerROC T35s, as well as numerous smart rigs that operate via machine guidance including ROC D7Cs, ROC D9Cs, and up to six SmartROC T40 rigs. The contractor has also recently
TECHNICAL DATA – EPIROC SMARTROC T40
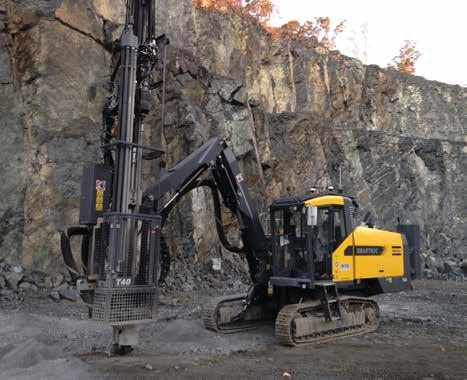
RECOMMENDED HOLE DIAMETER
DRILL ROD/TUBE DIAMETER
HYDRAULIC ROCK DRILL 64-127mm (2.5”-5”)
45mm or 51mm (1.7” or 2”)
COP 2540, COP 2560
ENGINE TYPE/OUTPUT Caterpillar C7.1 ACERT (Tier 3) – 168kW@1800 rpm Caterpillar C7.1 ACERT (Tier 4 Final) – 168kW@1800 rpm
OPERATOR CABIN
CERTIFICATE TRANSPORT LENGTH TRANSPORT HEIGHT WEIGHT OPTIONS Air conditioning, clear laminated glass (10mm front and roof windows and 8mm side windows), clear toughened glass (8mm side windows), rear view mirror, cab heating, electric combined engine inclination and hole length instrument in main computer display.
ROPS and FOPS 11.6m 3.4m (7.4m at feed height) 15 tonnes (15,000kg) Silence conversion kit, HNS, MWD, ROC Manager
taken delivery of some SmartROC C50 COPROD rigs. Some of the DBS rigs are also equipped with sound suppression for environmental drilling restraints (eg noise pollution), reducing the noise factor by about 10 decibels.
“I can be 20 metres away from it and I can pick up my phone and ring you and you’d hear background noise, and that’s all,” Jason said. “The silenced kit takes the ringing, the high frequency out of it – it reduces that steel on steel sound.”
“It doesn’t echo down the valley like a traditional drill rig would,” Dan added. One of these sound-suppressed (or silenced kit rigs) – a ROC D9C – has been working at Fulton Hogan’s Stonemaster Quarry, on the Gold Coast, on an integrated
22 Quarry February 2019 program devised by Cement and Aggregate Consulting Services (CemAgg) to raise the quarry’s productivity by as much as 20 per cent.
DBS has successfully collaborated with CemAgg and Fulton Hogan on a program comprising drone surveillance, quarry design, machine control and site-based GPS surveying to extract Stonemaster Quarry’s remaining reserves. An in-depth explanation of this service has been explained in a previous issue of Quarry. 1 The second silenced kit rig – a SmartROC T40 – has been recently working on a greenstone deposit at Fulton Hogan’s Blue Rock Quarry, at Cedar Creek, also in southeast Queensland. According to CemAgg, Blue Rock has a more challenging geology than Stonemaster Quarry, coupled with new development works that require careful planning so that future production is not constrained by limited supply of higher raw grade feed. 2 The SmartROC T40 is equipped for hole diameters in the 76-127mm range, with maximum hydraulic pressure of 220 bar and a maximum impact rate of 44 to 53 Hz. It features a folding boom system, aluminium profile feed beam, hydraulic cylinder feed beam and a carousel-type rod handling system, with 1 + 7 rods.
The 15-tonne unit is powered by a 168kW, turbo-charged Tier 3 or Tier 4 Caterpillar C7.1 ACERT engine at 2200 revolutions per minute and features an Atlas Copco OIS K-36-C111 GD screw compressor, with a maximum working pressure of 10.5 bar and free air delivery of 153 litres per second. The engine and compressor speed is self-adjusting, according to demand. Three variable hydraulic pumps lower engine speed during non-drilling periods and tramming. Automatic cooler and dust fan controls are standard.
BEST RESULTS Epiroc’s optional machine guidance systems on the T40 comprise the Measure While Drilling (MWD), Hole Navigation System (HNS) and ROC Manager software. The HNS in particular manages hole position, inclination, correct aiming and the required hole length (as defined in the prepared drill plan) via the global navigation satellite system (GNSS). As a result, it can decrease the drill and blast cost per every cubic metre produced.
“We utilise site navigation, so the driller can walk in and utilise the boom as much as possible,” Dan said. “The machine’s not
moving the carrier, it’s moving the boom to the next hole. And with the navigation, we can use the automatic set-up, which means we can get great accuracy.”
It was at Blue Rock Quarry that the silenced kit T40 recorded some of the best results in relation to penetration and fuel usage. Daniel Kirwan, Epiroc’s regional manager for the Brisbane and Mackay regions of Queensland, remotely monitored the performance of the rig and according to that data, the T40 drilled 487m in one shift (of around 11 to 12 hours’ duration) at total drill power and capacity, burning through just 187 litres of fuel – exceeding regular performance expectations. “It’s a pretty good record – to do that many metres in day,” Kirwan explained. “When you start looking at the fuel usage, it pretty much works out as 0.4 litres per metre drilled, which is really good. Normally, the T40s will burn through 0.5 or 0.6 litres per metre. That equates to around 15 litres per hour.”
“It far exceeded our expectations,” Jason said. “Years ago, if we got 200 metres a day,
DRILLING STATISTICS
DAY
1 DAY TOTAL DRILL METERS DRILL METERS PER ENGINE HOUR 487.7 45.8
12/11/2018 487.7 45.8
According to Epiroc's Certiq data, the T40 drilled 487m in one shift - at full drill power and capacity.
FUEL CONSUMPTION STATISTICS
DAY TOTAL LITERS LITERS PER HOUR TOTAL co2 EMISSION
1 DAY 187 17.6 557.3
12/11/2018 187 17.6 557.3
The T40 used up just 187 litres in the one shift - a significant saving on previous drill models.
that was a good day on the previous drill and you would burn 400 litres of diesel. This is how far technology has taken us in such a short period of time.”
“It was amazing,” Dan added, “since the industry average is a litre per metre – the rule of thumb – and there are a lot of machines that are well over a litre per metre.” Kirwan attributed Epiroc’s 64-127mm T51 speed rods at a 3.6m length as a major factor in the metres per litre drilled.
“By having our rod, [DBS was] able to up the impact pressure on the rock drill,” he explained. “Essentially, they’ve been able to increase the impact rate on the drifter to get more metres. And to do that you need to
Load it right
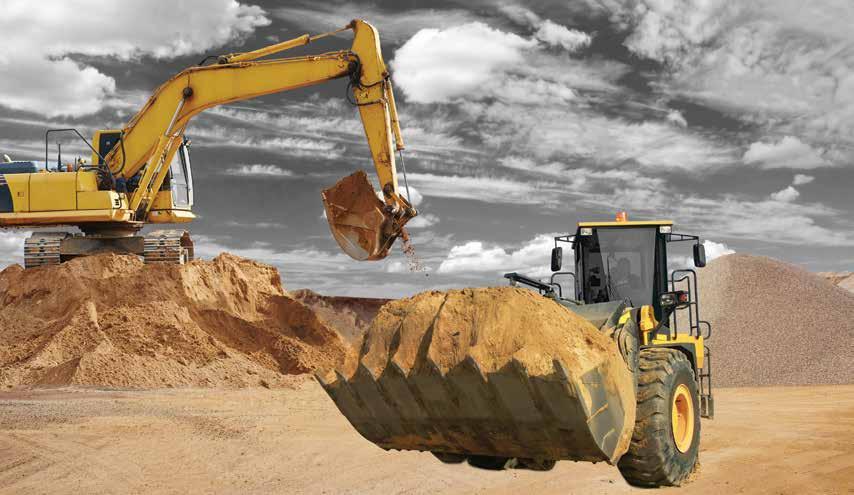
First time. Every time.
TRADE APPROVED
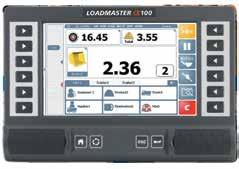
DBS’s ROC D9C smart rig at Fulton Hogan’s Stonemaster Quarry is equipped with a silencer kit on the mast for reduced noise emissions.
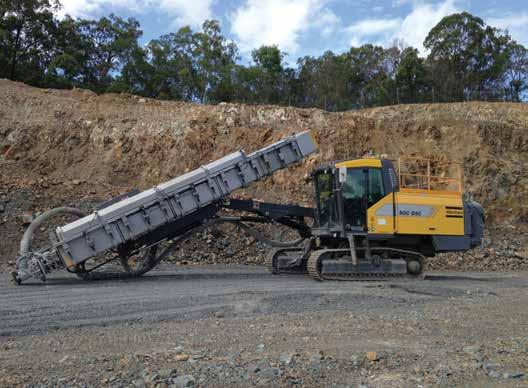
have drill strength capable of standing up to the increased pressure.
“With our shanks and rods there wasn’t breakage and because of the rod quality they could run the drill harder, whereas lesser quality rods would break when you put that much pressure up. So that was definitely a big part of it – being able to increase the performance of the rock drill and have the driller consumables to match it.”
Kirwan said it was a testament of Epiroc’s history and expertise. “Epiroc’s been making rods for the best part of 100 years. It manufactures premium rods at a premium price. What we have is probably the longest lasting, highest quality rod.”
All the parties agree that for these results to be replicated by another rig in another quarry setting, there needs to be a combination of factors.
“As the operator was getting more comfortable with the rig and winding more power into it,” Jason said, “we could see the metres going up and up. That was the thing that was really great about his performance on that shot, it was a good designed shot, good bench preparation, all the stars aligned on it.”
“It’s an example of a customer that’s using all the features of the Epiroc machine,” Kirwan said. “Some customers may just buy the rig for the fuel savings or may just take a silencer kit. But DBS has purchased the whole lot: the silencer kit, the HNS and the fuel burn all working together with the rod package. They’re using the whole Epiroc package to get the best results.”
AT THE LEADING EDGE DBS and Epiroc have reported positive feedback about the performance of the smart rigs. Jason Donnelly said that quarry operators were genuinely surprised by the drilling results.
“When we take the T40 into a quarry, the quarry manager comes around and asks, ‘How many metres did you do today?’ And the operator will say, ‘150, 170’. The manager will go ‘Really?’ and then they’ll go back and check the fuel book and they come back and confirm the next day that it wasn’t a one-off. And they’re like, ‘Wow! I’m glad we’ve got this now!’ They realise that, compared to other drill rigs, 160 metres drilled in a day represents a lot of savings!”
“The bulk of the customers using the T40 are drilling a 89mm hole size and it seems to be the drill of choice, particularly when it comes to penetration rate, fuel burn and then having the technology options on it,” Daniel Kirwan said. “It’s also sort of future-proofed for changes if quarries
24 Quarry February 2019 want to go down the hole navigation path.
“There’s a bigger emphasis in the industry on technology, reducing your fuel burn and having all capabilities built into the machine, so if you go to a site where they want to invest in using hole navigation, you have that capability.
“It comes down to your hole size and capacity, and what you actually want to drill,” Kirwan continued. “The Donnelly guys have set up the T40 and now they’re almost going beyond that to the C50 COPROD to do bigger hole sizes, the 102-115mm holes. If you’re doing the 89-102mm hole size and want to reduce your fuel bill, and potentially look at ways of getting technology into your business, the T40 is definitely a machine to consider.
“We’ve had a lot of success with the T40 on that smaller hole size (89-102mm). We have some newer products like the T45 and the C50, which are the ‘big brothers’ of the T40. Donnelly’s are starting to use some of those machines at the Hanson quarry at Wolffdene to great effect. They are at the leading edge of picking up new technology, trialling new things, which is really good for the market – to challenge the status quo.”
The T40’s positive results at Blue Rock Quarry have prompted DBS to replace the D9C rig with another sound-suppressed T40 at Stonemaster Quarry. The company is gradually replacing the ageing parts of its drill fleet with the smart rigs for its quarry assignments, and its older, more manually operated rigs (such as the PowerROC T35) are being assigned to construction jobs where the need for survey control and estimates has already been determined.
Working with CemAgg and Fulton Hogan on the integrated program at Stonemaster Quarry has also resulted in better machine utilisation for DBS across the board. “The way we conduct our rock on ground is the same but our design is completely different,” Jason said. “We have a path that we take that’s aligned more to pit design. We have a roadmap, we know where we’re headed.”
“We can plan all our maintenance better, we plan our blasting dates further in advance, and we’re not reacting to things in the quarry,” Dan Donnelly added. •
REFERENCE & FURTHER READING 1 Franklin S. The digital quarry: An integrated technical approach. Quarry 26(8); August 2018: 24- 29. quarrymagazine.com/Article/8782/The-DigitalQuarry-An-integrated-technical-approach 2 Ibid.
MODERN CRAWLER RIG TRIALLED ABROAD
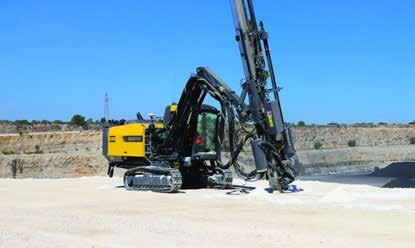
Global explosives producer MAXAM has optimised its drill and blast works in the Polish market through the acquisition of SmartROC T40 drill rigs, equipped with the COP 2560 rock drill, Hole Navigation System (HNS) and remote control function.
In a single year, MAXAM drills about a million metres of blast holes in Poland. It has had as many as 20 Epiroc drill rigs distributed across Poland, providing services to quarries producing granite, dolomite, sandstone, basalt, and melaphyre aggregate, as well as limestone for cement production and other components for construction chemicals manufacture.
In Poland, quarry walls may have a thickness of 12 to 28 metres. Popular hole diameters are 89mm, 95mm and 102mm. In purchasing new rigs, MAXAM was committed to reducing total operating costs. It proceeded to trial a T40 rig at a granite quarry in Rogoznica, in the southwest. The trial comprised two grids of holes spanning 2000m, allowing for a reliable assessment of the drilling costs and the actual tool wear. Until the trial, most blast holes in Poland were designed without consideration of the wall profile or verification of completed hole quality directly after drilling. The use of HNS helped to maintain the depth level of all drilled holes and to avoid uncontrolled excess drilling. The drilling parameters sampled with the MWD system enabled the estimation of quality and possible adjustments (via generation of a table of drilled hole bottom deviations in relation to the planned position) immediately after completion of the grid. In addition, the SmartROC technology indicated that holes could be drilled at nearly half the cost. The results exceeded the MAXAM personnel’s expectations. During the trial, the T40's average drilling progress was 1.1 metres per minute (m/min), compared to 0.8m/min on a ROC F9C. The T40’s fuel consumption was 0.5 litres per metre (lpm) of hole; the ROC F9C varied from 0.9 to 1.1 lpm. The results of the trial convinced MAXAM that the T40 was a worthwhile purchase and there was significant promise of a return on investment in time and fuel savings. The Epiroc technology has further modernised MAXAM’s drill and blast works and presented opportunities for more precise projects with greater quality. It has also reduced total costs by more than 30 per cent (through reduction of the consumption of fuel and explosives, the lack of additional edges and the drop of seismic vibrations during blasting). •
Source: Epiroc
sales@precisionscreen.com.au precisionscreen.com.au 1800 727 991 (Free call AUS)
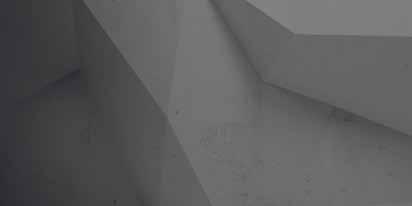
« MOBILE CRUSHERS « MOBILE SCREENS & SCALPERS « CONVEYORS & STOCKPILERS « WASHING PLANTS & PUGMILLS « HAMMERS & ATTACHMENTS DRY HIRE AVAILABLE PARTS & SERVICE SUPPORT

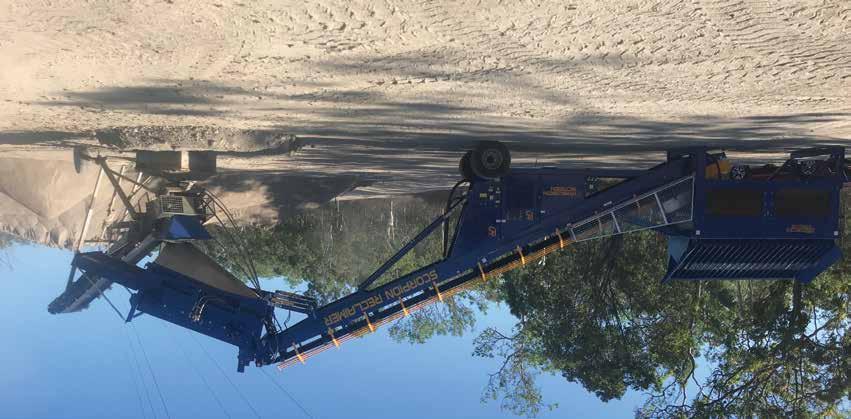
DIGITALLY ENABLED BLASTING PLATFORM SETS OUT TO OPTIMISE OPERATIONS
A next generation software program promises continuous improvement of blasting outcomes through data insights and integration via digitally connected technologies throughout the drill and blast process.
Orica, one of the world’s largest manufacturers of commercial explosives and innovative blasting systems, has released the latest version of its BlastIQ digital blast optimisation platform to the Australian mining market.
It is designed to optimise blasting outcomes by integrating data and insights from digitally connected technologies across the drill and blast process. Solutions enabled by BlastIQ can deliver predictable and sustainable improvements that can reduce the overall cost of drill and blast operations, improve productivity and safety, and facilitate regulatory compliance.
Orica chief commercial officer Angus Melbourne described how Orica’s digital technologies would assist operators. “The downstream impact of variable and poorly controlled blast outcomes today can impact as much as 80 per cent of the total mine processing costs. This presents a significant opportunity for the industry. The new BlastIQ platform enhances blast performance and outcomes for customers by seamlessly connecting data under a single platform,” he said.
“Soon the platform will link geoscientific, blast modelling and design data with measured field operations data, optimised blast delivery and advanced learning for continuous improvement.
“Orica wants to transform how drill and blast unlocks mining value for our customers, utilising digital and automated technologies to create safer, predictable and more productive blast outcomes. BlastIQ enables us to collaborate with customers to realise this transformation.
26 Quarry February 2019 BlastIQ’s information management component provides a secure, centralised online location for users to collate and collaborate on data from across the drill and blast process.
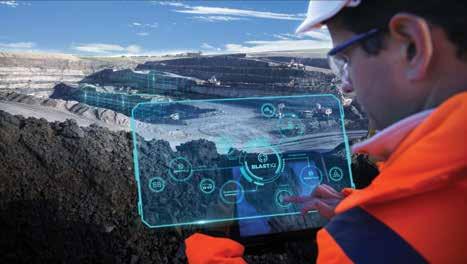
“Building on more than 140 years of experience and innovation in blasting, we have enhanced our ability to deliver value for our customers by adding world-class digital expertise and solutions to our existing suite of market-leading products and services. We believe Orica is uniquely positioned to unlock the value that digitally enabled blasting can deliver.”
SECURE, CENTRAL LOCATION According to Orica, the suite of enhanced technologies in the next generation BlastIQ empowers mine managers and engineers to make better decisions and increase control of blasting outcomes across mining and quarrying operations.
The platform’s information management component provides a secure, centralised online location for users to collate and collaborate on data from across the drill and blast process. This accelerates planning, analysis and auditing of blast data to satisfy regulatory requirements.
Optimised blast designs are developed using Orica’s SHOTPlus 3D design and modelling software. Evolved over 30 years, the advanced design tool has the capability to manage both simple and complex blast designs and initiation sequences.
Orica’s global digital product manager Angelo Labriola outlined the key benefits of the new digital platform.
“Our SHOTPlus design tool improves productivity by integrating seamlessly with the BlastIQ platform,” he said. “This allows blast loading instructions and rules to be communicated in near real-time to field operations, ensuring the right explosive type and quantity is used in the right place and subsequently initiated at the right time, every time.
“Improved in-field blast quality control and assurance is achieved using the new BlastIQ mobile device, enabling the efficient capture of auditable data direct from the bench. Blasthole condition data is captured with the BlastIQ mobile device in near realtime, allowing data to be shared between operations and engineering personnel from anywhere on-site, at any time, empowering rapid decision-making and improved operational efficiencies.”
Labriola said the complete blast control solution, enabled by the BlastIQ Platform, offered a complete integration between the explosives delivery control system, blast design and quality management systems.
“In a world-first, accuracy and efficiency of explosives delivery is significantly enhanced through the new BlastIQ-enabled delivery system, with loading and delivery to design now fully integrated,” Labriola said.
“Orica’s Mobile Manufacturing Unit delivery
Australia’s leading designer and manufacturer of rubber torsion spring motor bases.

systems, in particular the recently released Bulkmaster 7 unit, can be integrated into BlastIQ to wirelessly receive blast designs updated with near real-time blasthole quality data, while on the bench.
“Using this data, Orica’s connected, smart delivery systems load the correct explosive type and quantity according to the original design, adjusted based on blasthole condition measurement data and the automated application of a defined set of rules managed by the drill and blast engineer.
“This unique, direct integration with the delivery control system automates process control, thereby eliminating errors in manual product selection, process control and incorrect logging of loading actuals, as well as, importantly, reducing overall explosives loading times.”
Where a BlastIQ-enabled delivery system is not available, a BlastIQ mobile device can be used to capture and record asloaded data during the delivery process. The system still updates instruction to the delivery system operator based on updated processing of design and in-field blasthole condition measurement that precedes loading.
“The powerful new insights and analytics engine incorporated into the BlastIQ platform presents near real-time, hole by hole, blastrelated data visually to the multiple users across the drill and blast process,” Labriola said.
“Delivering the necessary insights and analytics helps the drill and blast team to easily monitor and manage key blasting KPIs, providing with them an essential tool to optimise blasting outcomes.”
CUSTOMER SUCCESS PROGRAM In addition to the new technologies, functionality and enhanced user experience in the next generation BlastIQ Platform, a comprehensive training, support and customer success program has been introduced.
It is aimed at tailoring each BlastIQ implementation specific to an operator’s needs, increasing the speed of implementation and, importantly, maximising their ability to realise productivity, cost reduction and regulatory compliance benefits.
The new platform has been integrated into several operations around the world, with operators experiencing its benefits and rewards.
Through easy integration into existing operational systems and processes, the BlastIQ Blast Control solution can improve blast quality control through autonomous and seamless data transfer and insights. This results in the elimination of rework, and the reduction of excess drilling and explosives consumption.
Multilingual support was to be introduced to the BlastIQ Platform in late 2018, as well as a new capability to optimise blast fragmentation through integration of drilling data, blast modelling and automated fragmentation measurement. In early 2019 the platform will connect third party mine planning, drilling and predictive modelling to deliver more blast control and optimisation for operators.
The scope for data-driven optimisation in the drill and blast segment of the mining value chain is significant and the next generation BlastIQ will continue to evolve rapidly to meet the growing demands of customers.
Orica will launch the next generation BlastIQ platform to the quarry industry in July 2019. •
Motorbase -Crushers
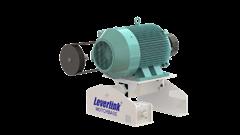
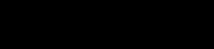
Motorbase -Screens, Feeders
Motorbase -Pumps
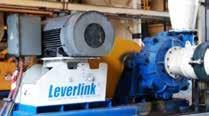
Chain & Belt Tensioners


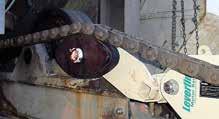
HOW FRAGMENTATION ANALYSIS CAN ASSIST IN BLASTING
The basic aim of all blasting operations is to fragment the rock mass in a suitable granulometric distribution, and obtain a shot pile formation and bulking of the material. The resulting fragmentation can significantly affect later stages of the operation.
In this regard, successfully loading, crushing and milling the material would reduce energy consumption and, in consequence, the total cost of the operation (Figure 1). For this reason, quantifying the resulting fragmentation through photogrammetric techniques combined with predictive models is a fundamental stage in the continuous improvement process for all mining operations.
The energy released when detonating the explosive charge generates a powerful shockwave that is transmitted to the surrounding rock mass, and is continued by a violent gaseous expansion. Although some of the energy released in the detonation is lost in ineffective work, most is concentrated in two distinct phases: (i) dynamic, dominated by the action of the shockwaves; and (ii) semi-static, dominated by the action of the gaseous expansion in the rock mass. The high pressures generated by the detonation of the explosive column are transmitted to the rock through shockwaves during the dynamic phase. These propagate radially through the rock mass by means of concentric compression pulses that attenuate as they move away from the load centre.
The dynamic state the rock was subjected to recovers its almost static state once the shockwaves have passed. The static properties of the rock mass begin to manifest themselves more effectively due to the appearance of a semi-static field of voltages corresponding to the pressure of the gases in the walls of the blast hole.
This is how the combination of both phases brings about a very specific granulometric distribution, bulking and shot pile format.
The assessment of blasting fragmentation is a recent, effective advance. The volume of the samples to be screened, according to industrial sampling rules, would imply that this assessment would be physically
Figure 1. An estimate of the average energy impact in each unit operation.
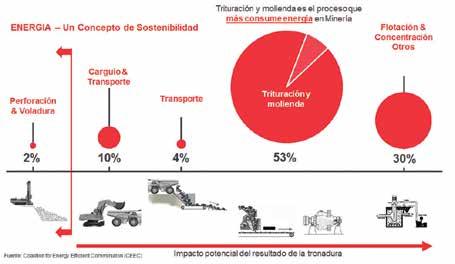
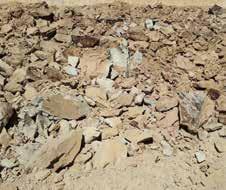
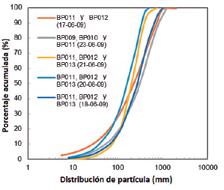
unfeasible due to the financial, human and time costs involved.
However, new photogrammetric techniques are widespread, both in mining and in the ore processing industry, allowing the aforementioned obstacles to be overcome and offering almost immediate results in a convenient, economical manner.
Photometric analysis software can work with images collected using conventional fixed and mobile video cameras, photo cameras or digital files, plus orthophotos obtained with drones. These use automatic algorithms that identify individual blocks by defining contours. Whenever necessary, the images can be manually re-edited to improve the digitisation of each of the blocks.
The flexibility of the series allows several types of reading in accordance with the requirements of each operation, including accumulated distribution charts, histograms and continuous flows, in order to set out any product quality variations quickly in different time periods (see Figure 2).
The need for continuous improvement in all extractive operations makes it necessary to apply measuring models that can, in the design phase, predict the impact of fragmentation on the subsequent phases of the production cycle. It is therefore possible to, after comparing predictions to the actual results, establish the optimal energy configuration in each blast. • Source: MAXAM Australia Figure 2. Fragmentation curves. A shot pile after blasting on the Toowoomba Second Range Crossing project.
INNOVATION AWARDS CELEBRATE SILVER ANNIVERSARY, DRIVE SOLUTIONS
MAXAM, the global technology company specialising in energetic materials in mining, quarries and civil works, recently celebrated the 25th edition of its Santa Barbara Innovation Awards, an initiative in the blast solutions industry that promotes a culture of innovation at all levels of the organisation.
Some of MAXAM’s solutions – such as the RIOBLAST design and simulation software and the RIOSENSOR device – blossomed from these awards.
The awards are aimed at the company’s 6500-plus workforce in 80 industrial facilities and subsidiaries across more than 50 countries on five continents. They are open to any employee who can identify and propose new ideas and solutions that generate a differential value for the company and its customers.
“MAXAM’s professionals in the field face complicated and extremely differing environments such as a mine in Siberia in -40 degrees, underwater blasting machines in Panama, or projects in sub-Saharan Africa in more than 40 degrees of heat,” MAXAM’s chief technology officer Miguel Àngel Flórez said.
“It is they who can quickly detect any new challenge to improve the security and efficiency of operations. Thanks to them, to the non-conformist, innovative spirit of our teams, some significant technological advances have emerged from Santa Barbara that respond to the specific needs of our customers.”
Fernanda Cardama, the company’s global head of people and resources, said: “Innovation is one of our fundamental values as a company and a distinguishing mark of each and every one of MAXAM professionals.
“We have a global, multicultural and diverse team that drives us to innovate every day. Constantly exploring new paths and possibilities is the only way we know to continue creating value for all our stakeholders, while still contributing to the progress of society.”
In its 25-year history, the Santa Barbara Innovation Awards program has been the starting point for some of the company’s
Maxam MSU trucks deliver RIOFLEX bulk watergel to an extractive site. The trucks evolved from mobile assembled explosive units first proposed as part of the Santa Barbara Innovation Awards.
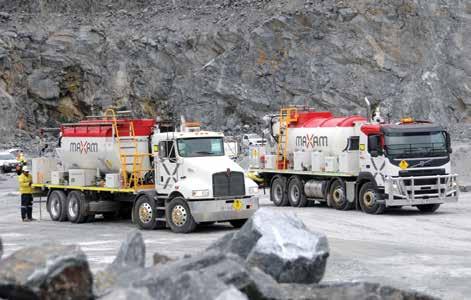
important technological advances. In the past 10 years, the prototypes of innovative developments have featured in the awards, aimed at increasing the efficiency, precision and security of blasting solutions for mining and civil engineering.
For example, technologies such as RIOBLAST and mobile assembled explosive units played key roles in MAXAM’s successful Panama Canal extension project, completed in 2015. Both innovations evolved from the presentations of MAXAM employees at the Santa Barbara Innovation Awards.
Other significant developments arising from winning ideas have included the BER system for the real-time visual inspection of boreholes and the RIOSENSOR device, which contribute to clear security, efficiency and productivity improvements in mining projects.
RIOBLAST is a blast design and simulation software package for managing a one-off blast or complete campaign. It enables the optimisation of explosives and initiation systems, and accurately predicts aspects such as the fragmentation that will be obtained, vibrations in the field and reach, allowing the delimitation of the security perimeter. Additionally, it can be used to analyse results and generate blast reports with details of fragmentation and vibrations. RIOSENSOR is a device designed by the company’s technicians to identify and measure deviations in blastholes before proceeding with the blast. It means corrections can be carried out or the effects of deviations on the final result can be anticipated, therefore improving operational productivity.
BER is a visual and real-time borehole inspection system that can remain inside the borehole while the explosive is loaded, unlike other devices where it is necessary to extract and clean it. In addition, this system transmits real-time images that can be seen from anywhere in the world. Information obtained on every borehole via the BER allows adjustments to be made before executing the blast, contributing to improvement of the end result. During works for extending the Panama Canal, part of MAXAM’s technical team developed a device for packaging the stored explosive on trucks that pump the bulk product into the boreholes. This conversion of trucks into mobile explosive units generates significant economic savings for the customers, and significantly increases the security of an operation. It enables the use of an assembled product in unstable areas or areas with difficult access for pump trucks. •