
19 minute read
A TEAM-ORIENTED APPROACH TO DRILL, BLAST
from Quarry Feb 2019
by Prime Group
PROMOTING A TEAM-ORIENTED APPROACH TO DRILLING, BLASTING TO THE POWER OF SIX:
Anthony Konya discusses a steady management approach to drill and blast that encourages employee buy-in and a dedication to improved techniques and efficiency. This can assist operators with reducing expenses and achieving better fragmentation.
Acommon problem for quarrying engineers and consultants is the critical challenge of achieving proper blasting.
Many of the problems faced come from operational inefficiencies in the drilling and blasting program. Most operators believe that better blast design will help save costs, improve fragmentation and decrease vibration, and while this is all true, none of it can occur if the design cannot be achieved with reasonable accuracy. By achieving this accuracy, before implementing better blast designs and processes, most quarries save upwards of 15 to 30 per cent on their blasting costs. There are many ways to achieve accuracy, such as designing for inaccuracies, automating jobs and blasting management.
DESIGNING FOR INACCURACIES How does one design for inaccuracies in blasting? This is a common question when inaccuracies are encountered, because engineering out these inaccuracies is one of the easiest options with the least capital cost. However, this approach is extremely costly in the hidden costs of drilling and blasting. One of the first people to study drill deviation on a large scale was Ulf Langefors, who documented his extensive results from dozens of mines in his book The modern technique of rock blasting and discussed ways to “engineer out” drilling inefficiencies. 1 He did this by analysing the average errors in drilling from:
Collaring location – the drill setting up in the wrong place, causing the hole to begin in the wrong location.
Alignment inaccuracies – including drilling improper angles and the deviation inside of the borehole when drilling.
When Langefors studied a multitude of blasts in Sweden, he concluded that, on average, improper collaring locations accounted for 101 millimetres (or four inches) of deviation, and alignment inaccuracies were about one millimetre for every 30 centimetres (or 0.04 inches per foot) in bench blasting. To most, this may seem insignificant, but this is almost ±15cm (or ±6 inches) on a 12m
P10 No deviation 40mm Langefors 101mm Forsyth 51mm
P50 No deviation 302mm Langefors 302mm Forsyth 302mm
P80 No deviation 448mm Langefors 498mm Forsyth 701mm
Table 1. Fragmentation comparison.
P10
No deviation 40mm Langefors 61mm
P50
No deviation 302mm Langefors 190mm
Forsyth Not within accurate modeling
Forsyth 101mm
Table 3. Engineered fragmentation.
P80
No deviation 448mm Langefors 335mm
Forsyth 0.8mm
(40-foot) bench. This means the spacing between the two holes may be reduced by 300mm (one foot) and the burden increased by 152mm (0.5 feet).
1
Forsyth, Deen and Sterk studied this same problem and reported up to three millimetres for every 30cm (0.12 inches per foot) on longer blast holes with a 196mm (7¾ inch) drill bit. 2 As the drill bit is reduced, the drilling errors are larger, based on the stiffness of the drill steel. In this case, both studies were with larger drill bits.
To determine the significance of this, we can look at a fragmentation prediction method called the Kuz-Ram model – a way to predict fragmentation before a blast that has a variable to define the drillhole deviation. 3 To analyse the drill deviation with an example blast in limestone, you would use the following specifications:
• Drillhole diameter – 101mm (4’). • Explosive – ANFO. • Burden – 2.4m (8’). • Spacing – 3.5m (11.5’). • Bench height – 12m (40’). • Sub-drill – 762mm (2.5’). • Stemming – 1.7m (5.6’). From Figure 1, one can observe the actual impact of drill deviation. In this graph, the horizontal axis is the fragmentation (screen size) in inches from the blast, and the vertical axis is the per cent passing that screen size. Table 1 has a summary of these results, with the term P x meaning the screen size that “ x per cent” of the material would pass through. This table shows that, with increasing deviation, the fragmentation oversize significantly increases, which will raise crushing costs as well as secondary breakage costs.
To overcome this drill deviation, Langefors suggested reducing the burden to account for this divergence. He suggested the actual design burden should be the optimal burden subtracted by the deviation per 30cm (or foot). This is what is meant by “engineering out” deviation from drilling. While this can be a good method, it has some drastic ramifications. By engineering out deviation, not only will the burden change, but all blasting parameters have to be modified. To analyse this effect, the Kuz-Ram model will again be used for the design in each of these situations:
A few problems are brought to light instantly when analysing these patterns, even before looking at the fragmentation, ie: 1. The small burden will cause face blowouts, scattering rock across the entire pit. 2. The large powder factors of the “engineered patterns” can cause large air overpressure. 3. The cost will significantly increase (to be analysed later). When analysing the fragmentation in Figure 1 and Table 3, one can see the extreme results this can have. One can observe that, in terms of the fragmentation, Langefors’ method works well with his drill deviation, but with a larger deviation such as Forsyth it becomes impractical and costly, with a large increase in fines and boulders, with relatively little good material.
How much does this “engineering out” method cost a mine? Three sets of figures show the cost for blasting a bench that is 18m (60’) long by 6.7m (22’) wide, based on a drilling cost of $AUD7.00 per 30cm ($US5 per foot for drilling) and $AUD0.42 per 453 grams ($US0.30 per pound) of ANFO:
• No deviation = $AUD1635 ($USD1186). • Langefors = $AUD2812 ($USD2040). • Forsyth = $AUD5969 ($USD4329). One can see that by engineering out the solution, the cost is increased drastically. If better fragmentation is achieved, some of these costs can be offset in reduced crushing and better product. But what if large deviation, like in Forsyth above, is displayed at the quarry? SIX SIGMA BLASTING Large mines are moving to autonomous drilling, with claims of improved accuracy. However, the drills are only as accurate as the GPS and instrumentation available and not error-free. In drilling, a significant portion of the drilling deviation occurs when the steel is in the borehole (see Figure 3 overleaf). These autonomous machines do not control this deviation, and, while they can reduce it, most quarries do not have the capital for the improved drilling set-up location.
To improve its blasting, a quarry must employ management techniques. Even with engineering out a blast, deviations must be minimised to achieve proper breakage. Six Sigma is a management technique used to improve drilling, blasting and fragmentation. Fragmentation (inches) No Drill Deviation Passing Percent Forsyth DeviationLangefors Deviation 0.8 0.6 0.4 0.2 0
0 5 10 15 20 25 30 Figure 1. Drill deviation on fragmentation.
SOLUTION No deviation Langefors Forsyth Drill diameter 101mm 101mm 101mm Explosive used ANFO ANFO ANFO Burden 2.4m 1.8m 1.2m Spacing 3.5m 2.6m 1.8m Bench height 12m 12m 12m Sub-drill 0.7m 0.5m 0.4m Stemming 1.7m 1.3m 0.9m Table 2. Engineered out solution.
Figure 2. Engineered-out fragmentation.
The goals of this program include: • Employee buy-in. • Reduction of drillhole deviation. • Improvements in loading technique. • Improved efficiency in blasting. Without proper employee buy-in, projects generally are unsuccessful and results are not as expected. This is the same with improving a drilling and blasting program, so how can management, engineering and the driller/ blaster all work together and buy in to the project, especially when it has increased workloads for all levels?
According to Maslow’s hierarchy of needs 4 (illustrated in Figure 4), a person is motivated at a higher level by belonging, self-worth, accomplishment and personal growth. In most cases, quarry employees at all levels have safety, a job, insurance, food and water. In general, people are longing for an increased belonging and accomplishment. This is where the Six Sigma effect has large benefits.
Six Sigma functions as a team role, where all levels of management, engineering and the drillers and blasters work together to accomplish these goals. This team is composed of:
• The sponsor (management) – Those who oversee the project at a high level and ensure obstructions from above do not impact the team.
• The leader (any level willing to lead the team) – This person will check in with the entire team, report results and help lead the team in the direction of its goals.
• The black belt (an expert in the field of improvement) – This person will need a deep understanding of drilling and blasting, generally someone who is extremely technical in the area or a consultant.
• The green belt (those knowledgeable in
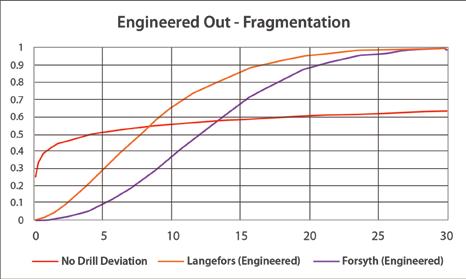
Figure 3. In-hole deviation (photo by T Sinkala).
the field) – Drillers, blasters and engineers to help the team collect data, make interpretations and suggest improvements.
• Team members – This role can range from showing up at monthly/fortnightly meetings to reading the report, or to helping the team in other aspects.
By having all levels involved in the team, all members will feel a belonging and want to improve their work, and that of others, to ensure team success. Little wins for the team will give all members a sense of accomplishment and continue to motivate them towards the goal of improving.
In cases where contract drilling and blasting is done, management should require that the contractor attend these meetings and achieve certain parameters. If these parameters are not met, the contractor should have a financial responsibility for unsatisfactory performance. This will ensure the contractor will listen – although most contractors will have solid knowledge and experience that can assist the quarry, and it would not be in their best interests to cut corners. Good communication between parties is critical and will result in better performance.
This team generally functions under the DMAIC approach (Figure 6), which means the group will:
• Define the objectives of the program. • Measure the inputs and outputs of the blast. • Analyse using statistical means how the inputs are influencing the outputs. • Find ways to improve these inputs. • Ensure these inputs are controlled to within limits for desired outputs.
Figure 4. Maslow’s hierarchy of needs.
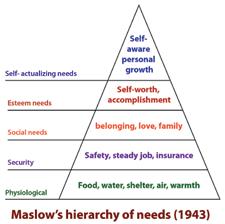
such as: • Reduce all vibration at a nearby neighbour to “ x.xx” millimetres per second (mm/s). • Have a P 80 from blasting of “x” millimetres. • Decrease the cost of blasting (an increased drill and blast efficiency can result in an ability to expand the pattern). Clear goals are needed, and multiple goals can be decided on, with an order of importance. For example, one quarry had the following goals:
• Decrease the cost of blasting by 30 per cent through increased blasting performance. • Have a P 80 of 152mm to 203mm (six to eight inches).
• Increase the speed of drilling and the loading of the bench.
Once the goals are established, the next step is to define key performance indicators (KPI) for the drill and blast program. These are for both the inputs and the outputs of the program. Examples include the following:
SIX SIGMA TEAM
Sponsor Leader Black Belt Green Belt Team members
Figure 5. The make-up of the Six Sigma team.
• Borehole location to intended location. • Borehole path to intended path. • Actual burden to intended burden. • Actual spacing to intended spacing. • Actual sub-drill.
Outputs
• Fragmentation size (P 80 , P 50 , P 10 ). • Air overpressure. • Ground vibration. • Cost to blast. • Time to drill/load. • Muckpile height and throw. • Crusher power output.
MEASURE PHASE The measurement stage of the program is when the driller, blaster, engineer and supervisor will take field measurements for the KPIs. There are many ways to now effectively and quickly measure these KPIs, including: 1. Borehole depth. The simplest way to ensure the proper borehole depth is reached is to get a tape measure that has the length of the borehole +10 per cent and tie a five- to 10-gram lead weight on the end (fishing sinker). This can be let down the hole until the bottom is felt and the depth can be recorded. The depth is important in many places, such as: • Measuring immediately after drilling to determine the depth drilled. • Measuring immediately before loading to determine the slump into the hole. If the depth of the bench is known, this method can be used to analyse the depth of the sub-drill (borehole length – bench height). The sub-drill is often critical in leaving a toe and fragmentation throughout the shot.
2. Flashlight test. The flashlight test is a relatively primitive
Figure 6. The DMAIC approach.
method of determining borehole deviation, but can be useful and provides valuable information for quarries with limited capital. This involves tying a flashlight onto the end of a rope with 152mm to 304mm (½- to one-foot) increments marked. The flashlight is then put into the borehole with the light shining out so one can see it. This is lowered until the light no longer shows (caused by drill deviation) and the depth is recorded.
TAKE A BIGGER PIECE OF THE PIE
The Ranger DX900i is the flagship model of Sandvik’s Ranger DXi family.
Featuring the most powerful rock drill in its class, Sandvik intelligence features, and a counterweight, revolving superstructure enabling ultimate stability, Ranger DX900i characterises our revolutionary generation of Ranger DXi top hammer surface drill rigs.

With an ultimate drilling coverage of 290° (55 m 2 ), it is the most powerful and efficient rig in its class.
3. Burden and spacing (tape measure). The burden (toe burden) and spacing are critical parameters in blasting and need to be field verified to ensure proper placement. This can be done by simply taking a tape measure and measuring the distance from the centre of one hole to the other.
4. Burden and spacing (GPS). For a slightly more accurate, more expensive and quicker way to measure the burden and spacing, a GPS surveyor can be purchased and used to get the exact location of each borehole. These can then be imported into a CAD program and easily measured.
5. Burden and spacing (drone). Another method to very quickly and accurately obtain the co-ordinates of the borehole is to use a drone to capture the locations. This is normally more expensive than other methods, but has a payback in the
Figure 7. Analysis of a muckpile.
time to analyse. This can also be contracted out to another company, and videos of blasts can also be monitored to see what is happening.
6. Borehole tracker (borehole length and deviation). A more accurate method to determine the length and deviation of a borehole is a borehole tracker. These devices are inserted into the borehole and take co-ordinates as
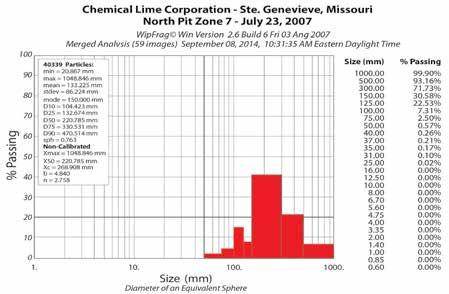
they are lowered. When loaded into a CAD program or other software, one can see the exact path of the borehole, including angles, curves and length.
7. Face profiling system. Many laser and photogrammetric face profiling systems exist, which allow quarries to create a point cloud of the face of their blast. This can be combined with options such as the borehole tracker and drone to
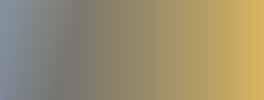
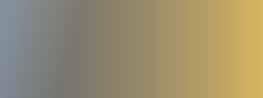
Improve visibility, boost e ciency and control operations costs with Trimble Operations reporting | LOADRITE Payload Management systems | Loadout Management systems | Load & Haul monitoring | Fleet Management | Dredge positioning | Machine Control | Drill Positioning Systems
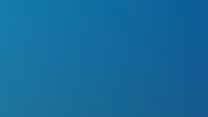
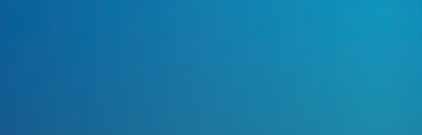
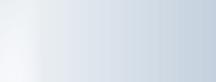
Our rental fleet includes the latest equipment from the world’s leading manufacturers.
create a 3D image and calculate the exact parameters of all variables.
8. Boulder counting. One quick and easy way to measure the fragmentation performance of a blast is to use a boulder count. This is counting the number of boulders over a certain size on the muckpile. To refine this method, the loader operator can count boulders throughout the pile. This method can be deceptive and doesn’t accurately display fragmentation, but will accurately assess the secondary breakage reduction of blasting.
9. Fragmentation analysis (WipFrag, WipWare). If fragmentation is a key output to the quarry (which it normally is), the WipWare systems are a great way to accurately measure the fragmentation (see Figure 7). I have used this at many quarries to help identify fragmentation. This involves taking a picture of the muckpile, in several locations, and using the software to determine the fragmentation of the muckpile. At least nine images at varying locations on the muckpile should be used per muckpile.
10. Fragmentation analysis (reflex system). To simplify this process and achieve more accurate results, WipWare has introduced a reflex system that uses stationary cameras to take pictures of almost the entire muckpile. The camera can be placed on a dump point (crusher), a point all trucks dump, or the front of a loader/shovel.
ANALYSIS The next step is to analyse all inputs and determine which key inputs are relied upon to achieve the desired outputs. This can take many blasts to determine and often the bad blasts are more important than the good blasts for this. By monitoring both, one can determine the changes in different parameters. This, along with pre-blast simulations of performance, can be used to carefully manipulate variables to determine the key inputs.
Important topics to look at in the statistical determination of blasting parameters include: • The mean. • The medium. • Standard deviation. • Normality of data. • Correlation to outputs.
IMPROVEMENTS After the analysis phase is complete and the key inputs are mapped and correlated to the outputs, the improvement phase begins. Improvement is the most difficult step and can be handled in many ways by the quarry.
In certain situations, it is training an employee on proper techniques for drilling or loading. It might be providing employee motivation to achieve measureable goals – or purchasing new equipment or technology to help achieve the goals.
The improvement phase is the area in which the black belt will need to take the lead, using help from the green belts, to determine the exact way the quarry will improve a system. This can come from engineering implementations as well. Like Langefors’ suggestions, if minimal deviations exist, other engineering methods include: 1. Designing holes to be drilled slightly deeper (304mm, or one
Hydraulic Excavators Hitachi and Komatsu 30 to 90 tonnes, Volvo EC480DL
Articulated Dump Trucks Hitachi, Bell 30, 40 & 50 ton capacity & Volvo A45G
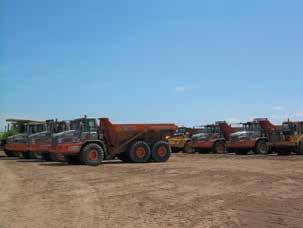
Wheel Loaders Komatsu WA500s & WA600s IT28G, IT62Hs. Volvo L260H & Hitachi ZW370, ZW310
Compactors Caterpillar 815Fs & 825Hs
Dozer Caterpillar D6Rs, D6Ts, D7Rs, D8Ts, D9Ts, D10Ts, Komatsu D375A-5
The Right gear in the Right place at the Right time
Delta Rent Pty. Ltd. 577 Plummer Street Port Melbourne Victoria 3207 FOR MORE INFORMATION PLEASE CALL: Richard Khan, General Manager, Office: 1300 793 071 David Hoyle, Territory Manager East Coast, Mobile: 0423 571 081 Phil Aguis, Territory Manager VIC, Mobile: 0418 753 981 Darren Barlow, Territory Manager SA, Mobile: 0418 800 231 www.deltagroup.com.au
foot) and measured before loading. If slumping has partially filled these holes to the proper loading depth, loading is done. If they are a little deep because no slumping has occurred, the blaster can kick in some drill cuttings to fill the hole to the desired load depth. 2. If burden and spacing are commonly an issue, parameters such as burden setbacks can be used along with timing changes to alter the direction of movement. 3. If drilling is consistently a problem, having the driller fill in the bad hole and drill a new hole can also be used (if a contractor driller, this is done at no additional cost).
CONTROL Finally, the control phase is implemented to ensure the parameters are met. This is normally in the form of quality control charts with maximum acceptable and minimum acceptable limits.
Periodic monitoring should be done (much less than the measure phase) to ensure everything is consistent. In many cases, the outputs can be monitored, creating an easy, successful control plan.
Without the control plan and excellent documentation in place, quarries may implement this process and spend a lot of time on it only to have new people come in and change it. One of the benefits of the Six Sigma team is that an entire team will rarely leave the site at the same time. This ensures knowledge can be passed down, and the quarry’s drilling and blasting can be maintained.
Improper drilling and blasting procedures can result in major blasting costs, which go relatively unnoticed. Design changes and new products will not be beneficial unless proper drilling and blasting management is in place. While some corrections can be made to the design to “engineer out” inaccuracies, a steady management system is one of the only ways to consistently ensure desired performance.
The Six Sigma drilling and blasting approach has proven itself in the trenches. Based on teamwork at all levels, clear goals and measurements of systems, and a control system, it can help quarries achieve excellence in their drill and blast programs. •
Anthony Konya is a project engineer with Precision Blasting Services, Missouri, USA. Email: Anthony@ idc-pbs.com
Article courtesy of Aggregates Manager (US).
REFERENCES & FURTHER READING 1. Langefors U, Kihlström B. The modern technique of rock blasting (3rd edition). Wiley, New York, 1978. 2. Forsyth W, Deen J, Sterk P. Assessment of perimeter blasting at the Homestake Mine. Proceedings of the 23rd conference on explosives and blasting technique. International Society of Explosives Engineers, Las Vegas, NV, 1997: pp 437-445. 3. Cunningham CVB. The Kuz-Ram model for prediction of fragmentation from blasting. In: Holmberg R, Rustan A (eds). Proceedings of the first international symposium on rock fragmentation by blasting. Luleå Tekniska Universitet, Luleå, Sweden, 22–26 August, 1983: pp 439–453. 4. Maslow AH. A theory of human motivation. In: Psychological Review 50 (4), 1943: 370–396. http:// psychclassics.yorku.ca/Maslow/motivation.htm
Quality assured alternative wear parts for all crushing equipment
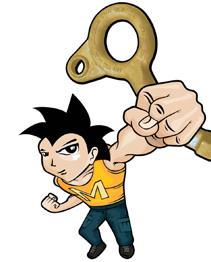

• Manganese & alloy steel wear parts • Bowl, mantle and jaw liners • Concave segments • Blow bars & hammers • Auxillary wear parts • Mining & Quarrying spares • Mill liners • AUD $5 million manganese in stock
lift jaw & cone liners with MANGASAFE ™
Quality Assurance Standard AS/NZS ISO 9001:2008 covered wear parts for all popular crushers in stock Assuring you of our careful attention at all times
MELBOURNE 6 Dib Court Tullamarine VIC 3043 F 03 9338 0680 P 03 9338 0200
PERTH 88 Barberry Way Bibra Lake WA 6163 F 08 9434 5515 P 08 9434 5552
BRISBANE Unit 2/23-31 Meakin Road Meadowbrrok QLD 4131 F 07 3382 0098 P 07 3801 8153
CHILE Santiago