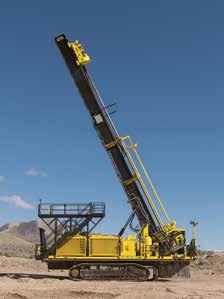
27 minute read
DRILL PROMISES SAFETY
from Quarry Aug 2019
by Prime Group
SURFACE DRILL PROMISES SAFER OPERATION, AUTOMATION FEATURES
Komatsu Mining has released the P&H 77XR surface mining drill rigs, the first of a new line of drills offering safer operation, higher productivity and increased maintainability, as well as including semiautonomous or fully autonomous capabilities. Designed to work in a wide range of applications, from coal to hard rock mining, the 77XR has a bit loading of 35 tonnes, and has been designed for maximum versatility, including the ability to carry out rotary tricone drilling or DTH percussive hammer drilling, in single or multi-pass operations.
According to Mark Petersen, Komatsu’s national product manager for mining, the new rig incorporates several features that are unique to Komatsu P&H drills, including a new automatic bit-changing system and a new boxer-style mast with P&H’s exclusive rack-and-pinion pulldown.
“Auto bit-changing is a major step forward for surface mining rigs, and the 77XR is the first rig on the market to offer this,” Petersen said. “Quite a few manufacturers have tried to achieve this, and we are the first to come up with a solution.
“Our new bit carousel system eliminates the need to change bits manually, speeding up the entire process and minimising the operator’s handling of bits, reducing the risk of strain or injury.
“It’s a major safety and productivity advance, as it takes operators out of the line of fire, and it allows bit changes to be carried out within five minutes.
“The 77XR’s auto bit-changing – in conjunction with other automated features, including auto rod-changing, high precision GPS hole-to-hole navigation, auto drilling, auto levelling and auto mast raise – are key steps towards fully autonomous drill rig operation,” he said.
“This makes a perfect fit with Komatsu’s commitment to autonomous and semiautomated operations across its haul trucks, dozers and excavators.”
Petersen said the new rig’s rack-andpinion pulldown has been a standard – and exclusive – feature on P&H drills for many years; the only difference to the rest of the P&H drill product line is the introduction of the boxer-style mast.
The Komatsu P&H 77XR is designed to work in a range of extractive applications.
P&H 77XR SURFACE DRILL RIG
Bit loading 35,000kg Bit diameters 200-270mm Maximum drill depth - Single pass - Multi-pass - 16.3m - 85m Rotary head power 158kW Torque 14,900Nm@100rpm Engine Cummins QST30 rated at 783kW (6.3kV electric option available)
“The combination of the boxer-style mast and rack-and-pinion pulldown give significant advantages in productivity, reliability, bitloading performance and maintainability. “Our boxer-style masts have only four weld joints running the length of the mast, compared with the multiple weld points of conventional lattice-style masts, making it easier to identify any cracks or other issues, and they are simpler and quicker to repair.
“Again, that strongly aligns with Komatsu’s commitment to ensuring our products have a high degree of maintainability, minimising downtime for service and repairs, and optimising availability and productivity.” He said the rack-and-pinion carriage system delivers the same amount of retract force as pulldown force, to assist operators in the toughest conditions.
“Our optimised single rack design engages the pinion in tandem to improve reliability and maximise bit-loading performance.”
Other improvements on the 77XR include a new, improved lightweight rotary head, allowing the operator to raise and lower the mast with the carriage in the top position and the complete drill string attached.
“This reduces non-productive pipe handling time and streamlines the process of tramming between patterns,” Petersen said. “Our redesigned mast and carriage also enables effective single and multi-pass angled drilling.”
To further add to drilling safety and efficiencies, the 77XR can be fitted with P&H’s high precision automation solution.
“Our auto navigation sensors create a threedimensional grid that calculates size and distance for obstacle detection and collision mitigation,” Petersen said. “Once over the hole location, the drill auto-initiates the drilling process and drills to the proper depth, the first time every time.”
Combined with a HawkEye camera system, the drill control system is alerted to any objects or hazards in the drill’s path and can take appropriate action. “Our drill automation system improves safety and removes variability, leading to increased utilisation and, ultimately, higher drill performance,” he added.
Petersen said the innovations and advances on the new rig helped minimise non-drilling time, translating into more drilling (up to 12 per cent), reduced maintenance costs (by as much as 10 per cent) and increased productivity (by up to five per cent).
“With drilling and blasting at the heart of any surface mining process, the more quickly, precisely and efficiently a mine can execute its drill patterns, the more effective the resulting blasts,” Petersen said. “Our aim with the 77XR has been to better protect mine workers and equipment, while further increasing mine productivity.” •
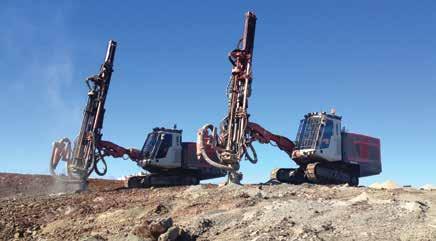
BLAST BUSINESSES UNITE UNDER ONE NAME EAST COAST DRILL AND
Four Australian drill and blast companies with explosives capabilities have merged under one banner after Chinese company Yahua Group bought majority ownership of their organisations.
The Yahua Group is an explosives manufacturer and supplier in Chengdu, China, and is listed on the Shenzhen Stock Exchange. It operates 57 wholly owned subsidiaries and 23 manufacturing bases in the civil explosives business in China, and produces 160,000 tonnes of explosives and 75 million detonators per annum. Yahua also owns The Redbull Powder Company (see page 14) that has two bulk emulsion facilities in New Zealand.
In 2016, the company’s subsidiary Yahua Australia began investing in Australianbased drill and blast companies that were strategically aligned with the quarrying, mining and construction industries: North Star Blasting, Caruana Blasting, Sequel Drill & Blast and Impact Drill & Blast.
Yahua Australia has announced the amalgamation of these companies that will now trade as Impact Drill & Blast. The new company is one of Australia’s largest drill and blast businesses with bulk explosives supply capabilities.
The original owners of Caruana Blasting and Sequel Drill & Blast have retained senior management positions in the new company and will be responsible for daily operations within Yahua Australia.
Impact Drill & Blast has one major hazard facility producing bulk explosives in Darwin, Northern Territory, and has been increasing its capabilities to service all areas of Australia. Redbull and Impact will work as one team to service the Australasia region.
As well as providing its own line of bulk explosives, the company now has one of the largest fleets of drill rigs in Australia, with an experienced team of shotfirers, drillers, maintenance personnel, project managers and blast engineers. Impact Drill & Blast will also focus on providing extractive industry producers with reliable, flexible and costeffective drilling and blasting solutions, and invest in the latest technology to maintain a high level of accuracy and industry compliance. •
Source: Impact Drill & Blast
LEOPARD™ DI650i TIME FOR A NEW LEADER
The Leopard DI650i down-the-hole surface drill rig offers long-term productivity and superior stability with robust and reliable main components seamlessly integrated with state-of-the-art technical solutions.
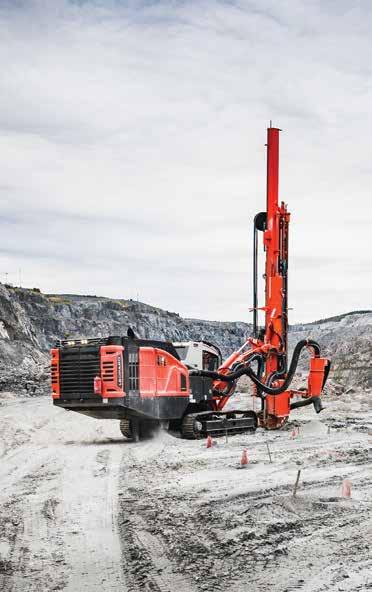
Scalable automation, easy maintenance and outstanding movability are the features that make Leopard DI650i a premium product for both mining and quarrying.
Leave your paw print and enjoy the smooth, efficient ride.
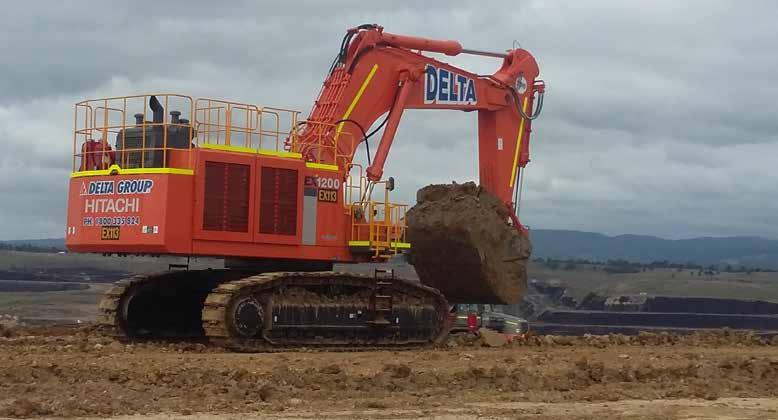
HIRE FLEET PLAYS ONGOING ROLE IN COAL MINE REHABILITATION
Four years ago, Quarry highlighted Delta Rent’s plant and equipment hire service at the Hazelwood power station and open cut mine in Victoria’s Latrobe Valley. Damian Christie re-examines Delta’s role today as the site undergoes extensive rehabilitation.
On 31 March, 2017, the 1542-megawatt power station at the Hazelwood Mine, which had been supplied with brown coal from the adjacent 1165ha open cut pit, officially closed after 52 continuous years of operation. In our last report on Hazelwood Mine, up to 772 million tonnes of coal had been extracted to fuel the power station, leaving three million cubic metres of overburden – clay, gravel and top soil.
At the time, the mine utilised four bucket wheel excavators and giant conveyors to extract and transport the coal from the pit to the bunker to the boiler. The eight conveyor belts combined would transport about 2000 tonnes of coal per hour and the three 8500-tonne slot bunkers would provide reserve coal storage of 18,000 tonnes for about six hours at a time. This meant it was necessary to continually feed the coal directly into the boilers to generate electricity. As a result, there was constant pressure to extract as much coal as the power plant was burning – and this in turn required considerable earthworks around the mine to construct and maintain 142km of roads and create drainage.
Hazelwood Mine turned to Delta Rent, one of Australia’s largest suppliers of rental fleets of specialised earthmoving plant and
Since Hazelwood ceased operation, Delta vehicles have been engaged in remediating the overburden dump.
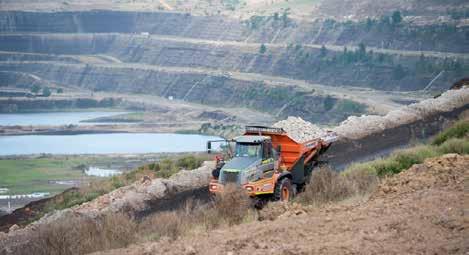
equipment, to administer and maintain the civil earthworks fleet. In 2013, Delta Rent and the mine’s then facilitator GDF SUEZ – today rebranded as ENGIE – agreed that Hazelwood would pay a set monthly fee for each piece of Delta’s plant and equipment, plus an hourly rate for each additional rent beyond the prescribed number of machines. The initial contract was for five years, and Delta Rent would also supply on-site maintenance and servicing of its mobile equipment as part of the contract. In what would be a productive, longstanding relationship, Delta Rent subsequently supplied Hazelwood with up to 100 earthworks machines at any one time, depending on the season, the weather and the scale of required jobs. That partnership has been renewed since the closure of the plant and mine in the first quarter of 2017, and the two parties have maintained a viable, cost-effective rental arrangement.
REHABILITATION PROJECT Since 1 April, 2017, ENGIE has been engaged in decommissioning the infrastructure of the 3550ha power plant and mine site as part of the Hazelwood Rehabilitation Project. The company retains an on-site workforce of 130 (directly employed) and can call on up to 200 more contractors (as required). Its decommissioning activities are being managed in three phases. Phase 1, which involved the de-energising of major plant and equipment and clean-up of pollutants, was completed in June 2017. Phase 2, which has seen the disconnection of all electrical supplies within the site, has occurred since August 2017. Most impressively, part of the decommissioning included the dismantling of the eight conveyors (including the removal of rubber belting a metre wide and 450m long) and the washing down and removal of residual coal from the inert slot bunkers and crushing houses.
This means the power station and the site’s other facilities, including its signature 137m tall chimneys, are awaiting Phase 3 – demolition. In April this year, Delta Group (Delta Rent’s parent company) was awarded the contract for the demolition of the power station. Planning is currently underway for demolition, which will begin in 2020.
Having one eye on the demolition stage has not fazed ENGIE from its work on the rehabilitation project. It is, with community consultation, proposing to convert the 16km mine perimeter into a full pit lake from 2021. The end use of the land external to the mine remediation (eg potentially as parkland) will be decided by state and local government authorities.
There is about another two years of work required to rehabilitate the mine and up to four years of work to remediate the adjacent land, such as the external overburden dump, ash landfills and the Hazelwood cooling pond. To date, 10ha along Hazelwood’s Eastfield eastern batters have been refurbished by excavating the coal batters back to a slope of three to one, then spreading topsoil over the clay and seeding the entire area. Batters in the site’s Knuckle area were also excavated to realign up to 1000m of pipeline and to install a new fire services pipe, using clay from the northern batters (which were rehabilitated before the closure).
In 2018, work was also conducted along the eastern batters to join up with the Eastfield northern batters. Rehabilitation will
There has been as much as 104 plant on-site in peak periods, including dump trucks.
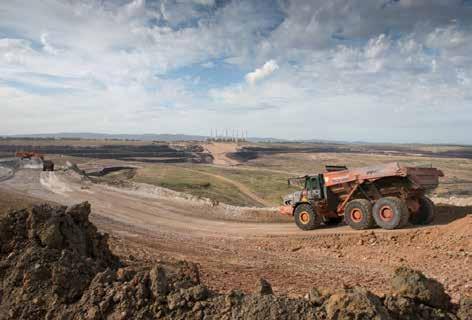
subsequently progress around the perimeter of the South Westfield northern batters and into the Westfield, and then down to the full pit lake level by the start of fill for 2021. The closure of Hazelwood, therefore, means work there is ongoing – and ENGIE continues to employ Delta Rent and contracting service Foundation Civil & Mining to provide the plant and equipment and the operators respectively to achieve the ambitious goals of leaving behind a repurposed space that will benefit the Morwell community in future generations.
‘DRY’ AND ‘WET’ HIRE Jessica Murty is Delta Rent’s site supervisor for its mobile plant and maintenance division at Hazelwood and oversees 12 other Delta personnel with prior experience in logging, agriculture, and open cut and underground mining operations. She oversees the “dry” side of the hire arrangement with ENGIE, supplying and maintaining mobile plant fit for project purposes. There has been as much as 104 plant on-site for the truck and shovel rehabilitation operation in peak periods, comprising primarily earthmoving vehicles. Murty, who has worked in the extractive industry for 11 years, told Quarry that she can source other equipment that ENGIE requires where necessary. “The majority of the plant is used for bulk material haulage to assist ENGIE with their desired end outcome of a successful, world leading, professionally rehabilitated site,” she said.
Delta Rent’s hire machines either come new from the top industry OEMs, such as Caterpillar, Komatsu and Hitachi, or at low hour usage (eg up to 3000 hours). All parts of its fleet, depending on the specific type of machine and application, have an average service life of 12,000 hours. Machines can also be repurposed for less impact work, eg a dump truck can be converted to a water truck. In the past, the most popular vehicles with quarry operators have been 5.5m 3 wheel loaders, articulated dump trucks in the 40- to 50-tonne range and larger excavators from 45 tonnes through to 90 tonnes.
“We have a good mixture of new and older equipment,” Murty said. “Delta are constantly working to improve their fleet and are currently running a brand new Hitachi EX1200 as part of their heavy haulage project. There are also nine new Volvo A45G articulated trucks that have helped ENGIE achieve a very productive bench cubic metre (bcm) rate.”
Delta Rent has long had a large undercover maintenance workshop and storage area called the “Igloo” at Hazelwood Mine to undertake the maintenance and refuelling of its vehicles. Murty said that with the large amount of equipment on-site, Delta Rent has had to “reconfigure more workshop areas that our team can efficiently work in – rain, hail or shine. Refuelling is now carried out by permanent fuel/lube truck operators and offroad fuel/maintenance trucks. This occurs 22 hours a day in peak season”.
Matt Weddell, the earthworks superintendent for Foundation Civil & Mining (FCM), organises the “wet” side of the arrangement – ie the operators to drive Delta’s mobile equipment. He has had two decades of experience in the extractive and earthworks industry.
“My role here is to co-ordinate and supervise labour and plant resources to ensure the projects are delivered safely, to plan and to budget,” he said. “I am in constant communication with Jess to ensure that the mobile plant is available and fit for purpose when required.”
FCM was founded by Rob Dugan, who is also the mine production manager at Hazelwood, and some of the company’s contract workers are former Hazelwood Mine employees, with the rest recruited from throughout the Latrobe Valley region. In peak periods (eg summer), the number of operators on-site can be as high as 90.
“We employ people ranging in age from 20
years old to 60 years young,” Weddell said, “with an emphasis on younger people where we can train them and expand their skills base by pairing them where we can with the older and more experienced operators.
“The training is an ongoing practice where we are constantly looking to improve the experience of the workforce,” he added. “It’s about always ensuring all operators are trained and competent on the machinery and that they use the site’s safe operating procedures at all times.” ASSIGNING THE FLEET Together, Murty and Weddell meet daily to collaborate on the assignment of equipment and operators throughout the Hazelwood Mine.
“Peak season sees Matt, myself and our leading hands constantly working closely together,” Murty said. “Meetings to discuss the day’s targets begin around 6.15am. We then return to our teams to organise and prioritise plant repairs. Throughout the day we are in liaison with each other, considering breakdowns and reinstated plant with the day to day and overall success of the project constantly our target.”
She added that the assignment of the rental fleet is determined not just by the quantity of operators on the ground but also the maintenance schedule, safety, weather and other activities within the rehabilitation site. “We work very closely with Matt, Rob Dugan and their scheduling team to achieve a high rate of utilisation of available plant for the project,” Murty said. “Meetings and communication throughout the day are vital here, especially taking safety and environmental concerns into account. Like any mobile plant supplier there are always days that tasks on-site can change from hour to hour and that really is just the nature of the industry. As part of the greater Delta Group, we can call on other pieces of machinery Australiawide, should there be a need to specialise.”
Weddell said it was a “critical item” for FCM to have the “equipment availability that Jess and the Delta team work very hard to maintain”.
“We have long-, medium- and short-term planning schedules for all projects on-site which allows the group to forecast the tasks and ensure we have the correct availability of plant from Delta,” he said. “This can change on an hour to hour basis depending on a myriad of things like weather, personal leave, plant, etc. We work as a team to overcome whatever hurdles we encounter to keep the job progressing productively.”
Weddell said that FCM assesses the effectiveness of its contract workers through setting daily key performance indicators (KPIs) to each task. “For example, it could be cubic metres per hour productivity on an excavator, the daily volume shifted. We also monitor Delta on the percentage availability of the mobile plant. These KPIs are used as a monitoring tool to assess the productivity and competency of operators. We have daily meetings to discuss operations and modify them if we believe we can achieve more productive outcomes. We also assist our operators with more specific training where we believe this will be beneficial for productivity and safety.”
Both Murty and Weddell said that the feedback from ENGIE about the performance of their plant and people is encouraging.
“ENGIE have been very supportive of Delta Rent on-site and work with us to achieve the desired outcomes,” Murty said. “Like any contract, there are always challenges but having an understanding of the scope of the The EX1200 (above) has recently joined Delta’s heavy haulage project.
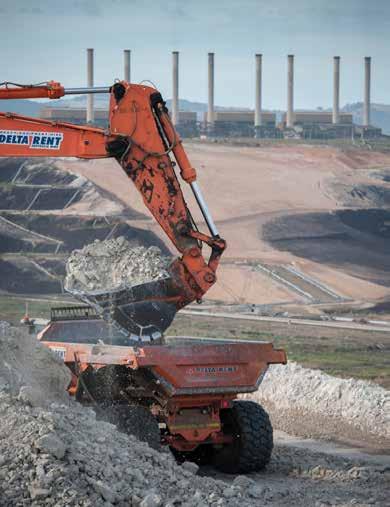
26 Quarry August 2019 work and the required timelines helps both parties work together to achieve the best result.”
“In general, we receive positive feedback as the majority of our operators are conscientious in being safe, productive and caring of the equipment,” Weddell said.
THE FUTURE Weddell said that in the wake of the closure of the power station, the Hazelwood Rehabilitation Project had been invaluable to the Latrobe Valley community. “This is a very important project as it has continued to provide employment and in-direct works for local companies, with the view to achieve an asset that the community will enjoy for many years to come,” he said.
He was also optimistic about the future of the local workforce, including his own contract workers. “While the operators may have finished at the Hazelwood Rehabilitation Project, the experience, training and competencies they will have gained in operating this heavy earthmoving equipment in a very regulated project will hold them in high regard for future employment, both here in the Latrobe Valley and on other major extraction projects within Australia.”
Murty said that for her personally, the opportunity to work on “such a significant project” as the Hazelwood Rehabilitation Project proves that “no matter who you are or how you start off, you can always achieve what you want if you work smart and hard for it. It is also very satisfying to be on a project that will ultimately provide a fantastic resource for the local community for many years to come”.
Murty’s advice for quarrying operators that are considering hiring plant and equipment for their operations is to be “sure on what you want to achieve, be conscious of environmental and community concerns and seek advice from your experienced rental representative when it comes to determining required machine types. Technology is changing on a daily basis and rental companies such as Delta Rent can help any clients access the latest gear”. •
REFERENCES & FURTHER READING 1 Christie D. Hire fleet helps to keep the midnight oil burning. In: Quarry 23(8), August, 2015: 14-19. quarrymagazine.com/Article/6450/Hire-fleet-helpsto-keep-the-midnight-oil-burning
2 ENGIE 2019. Hazelwood: The closure and rehabilitation of the Hazelwood power station and mine. engie.com.au/home/what-we-do/our-assets/ hazelwood
Cost-effective washing solutions with the highest level of after-sales support through our experienced global dealer network. MWS Sandstorm™ now in stock.
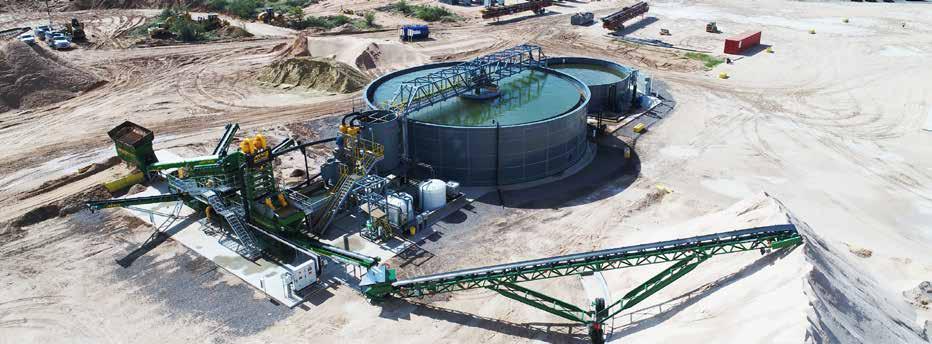
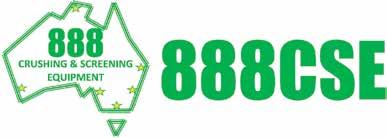
Nationwide distributor www.888cse.com.au Tel: 08 9550 6388
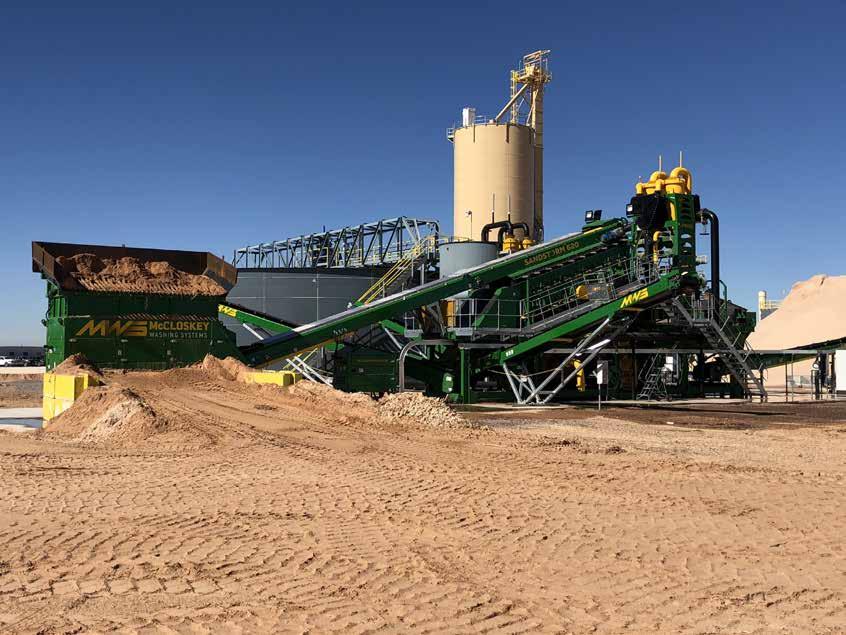
VICTORIAN OPERATION LEADS THE WAY IN INTELLIGENT MOTOR CONTROL
A Boral quarry has successfully updated legacy equipment with the latest motor control technology.
Boral’s Charlton Quarry is off Victoria’s Calder Highway, 240km north-west of the Melbourne CBD and 320km south of Mildura. It is one of the few hard rock quarries in the region that produces notable volumes of different quarry products, which are supplied to infrastructure projects in its vicinity.
As part of its commitment to delivering high quality building and construction solutions, Boral Quarries works to maintain an engaged and reliable workforce and minimise environmental impact. In keeping with this mission, it recently invested in a motor control solution for the Charlton Quarry, to improve uptime and leverage the longevity and compliance provided by the latest motor control technology.
Boral engaged SS Electrics, a Ballarat-based electrical contracting business, to modernise the quarry’s electric equipment.
“We have worked with Boral on projects at their other quarries previously and therefore understood the importance of minimising downtime on-site during commissioning,” SS Electrics director Chris Nunn said. “The Rockwell Automation motor control centres (MCCs) were the most appropriate choice for this application, because it is a fully designed and integrated system that is essentially 75 per cent commissioned upon arrival. This really helped reduce engineering time and meet the tight commissioning timeline for this project.” The Allen-Bradley Centerline 2500 MCCs offer optimal safety, performance and reliability to help quarries meet their production requirements. Modern motor control solutions have to integrate with existing systems and provide advanced diagnostics capabilities. The Centerline 2500 meets these requirements with sound integration and reduced engineering time.
“The quarry required an MCC solution that would meet the highest standards and also one that would be cost-effective, as well as adopting some of the integration benefits,”
28 Quarry August 2019 A bird’s-eye view of Boral’s Charlton Quarry.
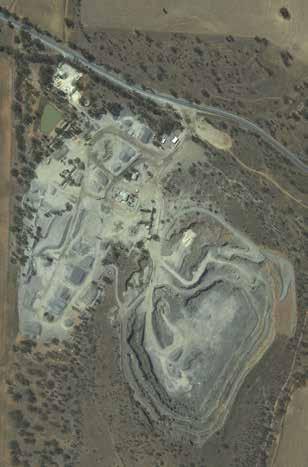
Matthew Treeby, the account manager for Rockwell Automation, said. SS Electrics worked with Rockwell Automation and its distributor NHP Electrical Engineering Products to select the smart components at the heart of the 12-column MCC, including the E300 electronic overloads, the SMC Flex soft starters, the Point I/O modules, Guardmaster safety relays, Stratix switches, ControlLogix control system and PowerFlex 525 variable speed drives for the crushers, conveyors and processing plant. “The MCC provides a reliable solution for motor control in Boral’s Charlton Quarry,” Treeby said. “The MCC is a ‘best of both worlds’ solution because it is not only high quality, fully tested and compliant but the customer was also able to customise the solution to meet their unique requirements, because the design and project management is done locally.”
INTELLIGENT SOFTWARE, SAFETY With a strong commitment to employee safety, Boral chose to include ArcShield Technology in the MCC. ArcShield helps to reduce arc flash hazards and provides increased protection against internal electrical arcing faults.
Offering a scalable safety solution, the MCC’s Guardmaster safety relays address the quarry’s compliance standards and functional safety requirements.
Boral’s MCC also features IntelliCenter technology, which enhances the MCC’s intelligence by using built-in networking to capture information that can be used for predictive maintenance, process monitoring and advanced diagnostics.
Connecting motor control devices over the ethernet allows operators and maintenance to realise the benefits of “the connected enterprise” by monitoring and analysing operations from anywhere at any time.
To reduce engineering time, the MCC was assembled in Rockwell Automation’s Shanghai manufacturing plant. Boral and SS Electrics representatives visited the plant to assess its capabilities before shipping to Australia. The smart motor control solution was programmed with Studio 5000 software and the wiring was connected at SS Electrics’ factory. This provided the opportunity for further testing and programming, therefore reducing the engineering time required for commissioning on-site at Charlton Quarry. By providing consolidated programming, device and system configuration, and operation and maintenance within the Studio 5000 engineering environment, complexity and potential errors can be minimised. In addition,
the requirement for on-site engineering work was reduced significantly, as the MCC had a complete set of electrical drawings, allowing SS Electrics to start the commissioning process from its facility in Ballarat, even before the MCC arrived in Australia.
Upon arrival, commissioning was completed at SS Electrics’ facility, where the MCC was pre-built in a portable room before being shipped to site. This allowed the MCC to be customised to meet site specifications.
IMPROVED UPTIME, COMPLIANCE Boral’s Charlton Quarry is now benefiting from the new smart motor control solution, which provides key diagnostic information that optimises performance, with real time access to operation and performance trends.
As the quarry moves towards being a more connected enterprise, this increased visibility into the system and real time diagnostic data can be transformed into actionable and insightful information.
“A key focus of the Charlton project was
The Centerline 2500 motor control centre under construction at Charlton Quarry.
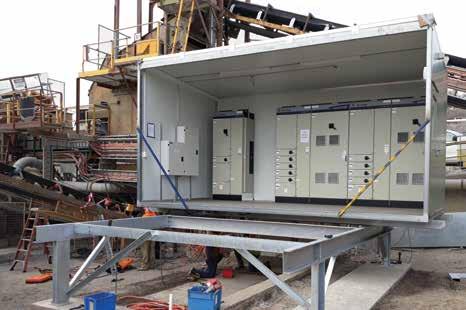
to replace end of life electrical equipment for improved compliance and safety, while minimising any required downtime at the quarry,” Jake McClellan, the mechanical engineer and asset manager at Boral Construction Materials, said.
“This was achieved with the new solution and the help of SS Electrics and Rockwell Automation. It was a very smooth project, and thanks to the increased visibility into the system, fault-finding time has been reduced from hours to minutes, and what was previously a very manually controlled process is now completely automated.
“In addition, the plant manager can now monitor production trends and energy consumption in real time, which assists with plant optimisation.
“With the new MCC, the quarry can confidently service customer demand well into the future. As a result of the success of this project, we have plans to implement similar systems in our other quarries.”
Allen-Bradley, ArcShield, Centerline, ControlLogix, E300, Guardmaster, IntelliCenter, Point I/O, PowerFlex, SMC, Stratix and Studio 5000 are all products of Rockwell Automation. •
Source: Rockwell Automation
sales@precisionscreen.com.au precisionscreen.com.au 1800 727 991 (Free call AUS)
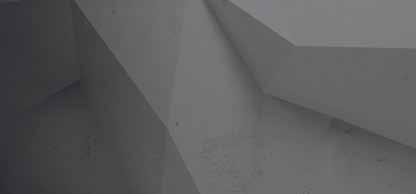
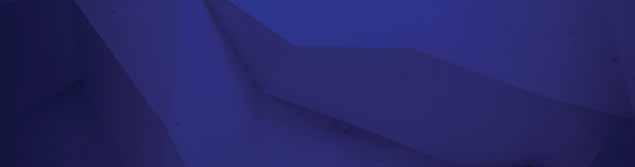
« MOBILE CRUSHERS « MOBILE SCREENS & SCALPERS « CONVEYORS & STOCKPILERS « WASHING PLANTS & PUGMILLS DRY HIRE AVAILABLE PARTS & SERVICE SUPPORT
MIXING SOLUTIONS Precisionscreen Scorpion Pugmill PLC
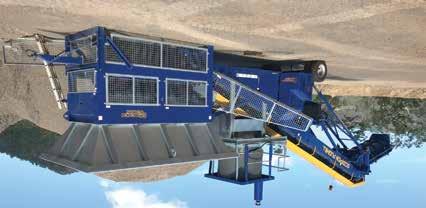
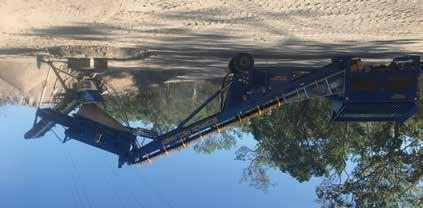
SCREENING SOLUTIONS Precisionscreen Super Reclaimer 10’x5 or 12’x5’ Screen
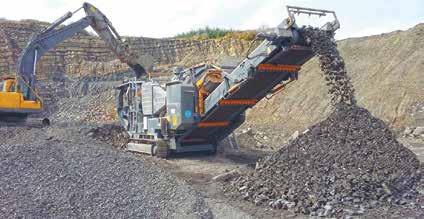
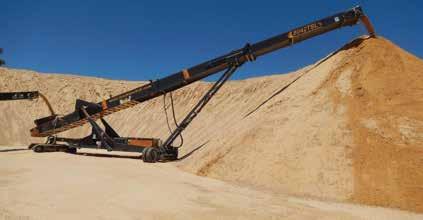
INNOVATIVE ENGINEERING DESIGN FOR PRODUCTIVITY, SAFETY
Mechanical conveyor problems and productivity irregularities are common challenges for today’s materials handling operations, with profitability expectations and continuous productivity deliverables also the norm.
These mechanical problems can be minor but can quickly escalate to frequent unscheduled production downtime if not identified and resolved in a timely manner. In turn, they can pave the way for potential safety hazards and clean-up costs due to material spillage and excessive dust emissions.
The key to on-site productivity, efficiency and safety can often be traced back to correct initial plant planning and design.
In recent years, materials handling components supplier Kinder Australia has invested in conveyor engineering/design software Helix, Solidworks and AutoCAD. By utilising AutoCAD in the production of twodimensional layout drawings or Solidworks in the creation of three-dimensional modelling, Kinder’s team of mechanical engineering specialists can provide quarrying producers with comprehensive recommendations on the correct installation of conveyor components and bulk materials handling accessories and lining materials.
Cameron Portelli, Kinder’s senior mechanical engineer, heads the young and aspiring engineering team. Mechanical engineer Bradley Owen and undergraduate mechanical engineer Jack Cain assist him. Together they focus on advancing producers’ end to end handling processes, with productivity and safety at the core.
“The use of SolidWorks has streamlined our product development process,” Portelli said. “The innovative, detailed and customised conveyor componentry designs generated to solve our customers’ everyday problems can now be fast-tracked with ease and efficiency.” Productivity and safety go hand in hand. With this in mind, the engineering team can use Simulation Finite Element Analysis, an upgrade to the Solidworks basic licence, to more accurately predict and design innovative products and solutions simulating real world scenarios. From there, the team can analyse results and optimise designs for future productivity improvements and gain.
Cameron Portelli is Kinder’s senior mechanical engineer and leads the company’s engineering team.
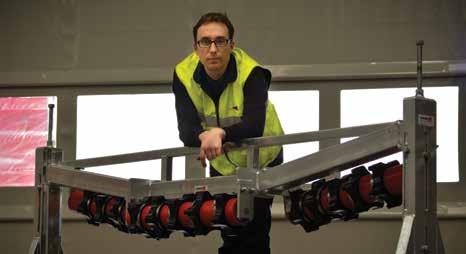
New full-scale conveyor componentry projects and the troubleshooting of existing problems, on the other hand, are best handled with the Helix software, in which the three engineers are fully versed.
With today’s production facilities/operators concerned with increasing their outputs and reducing costs, the engineering team’s expertise in manoeuvring the Helix software helps producers define more accurate specifications and requirements that lead to optimum productivity and profitability outcomes.
For example, if the system is designed, commissioned and installed larger than required or necessary, operations can face high initial and ongoing maintenance costs. On the other hand, if it is underspecified, the resultant system can become overloaded and more likely to underperform, fail and experience production bottlenecks, affecting operational bottom lines.
“Our practical knowledge and installation experience have a global reach, with extensive customer networks at international, national and local locations,” Kinder Australia CEO Neil Kinder said. “For our customer base spanning a multitude of bulk materials handling industries and applications, overall conveyor design and componentry can be checked with Helix software, which ensures the correct product application and design duty is in place.”
With their Helix expertise, Kinder’s engineering team can provide comprehensive mechanical conveyor advice on: • Equipment selection for idlers, pulleys and shafts. • Conveyor pulley and idler shaft dimensions calculations. • Idler bearing life and shaft deflection calculations. • Size requirements pulleys and drives to minimise capital and spares holding cost. “Field experience and direct liaison with our materials handling customers, in particular fixed plant maintenance supervisors, site managers and reliability engineers, provides invaluable insights into the mechanical, maintenance and safety issues experienced on-site,” Portelli said.
This knowledge of on-site intricacies has provided inspiration and ideas for future engineering designs and innovations. Portelli is confident his team will grow and take on highly technical, more customised projects, with the potential to design and install complete conveyor systems solutions for a diverse customer base.
Kinder Australia’s 3000m² warehouse facility in Braeside, Victoria, stores more than 8000 conveyor hardware components and accessories. The company supplies to every state and territory, and earlier this year announced it would begin supplying its products to the Asia-Pacific market. •
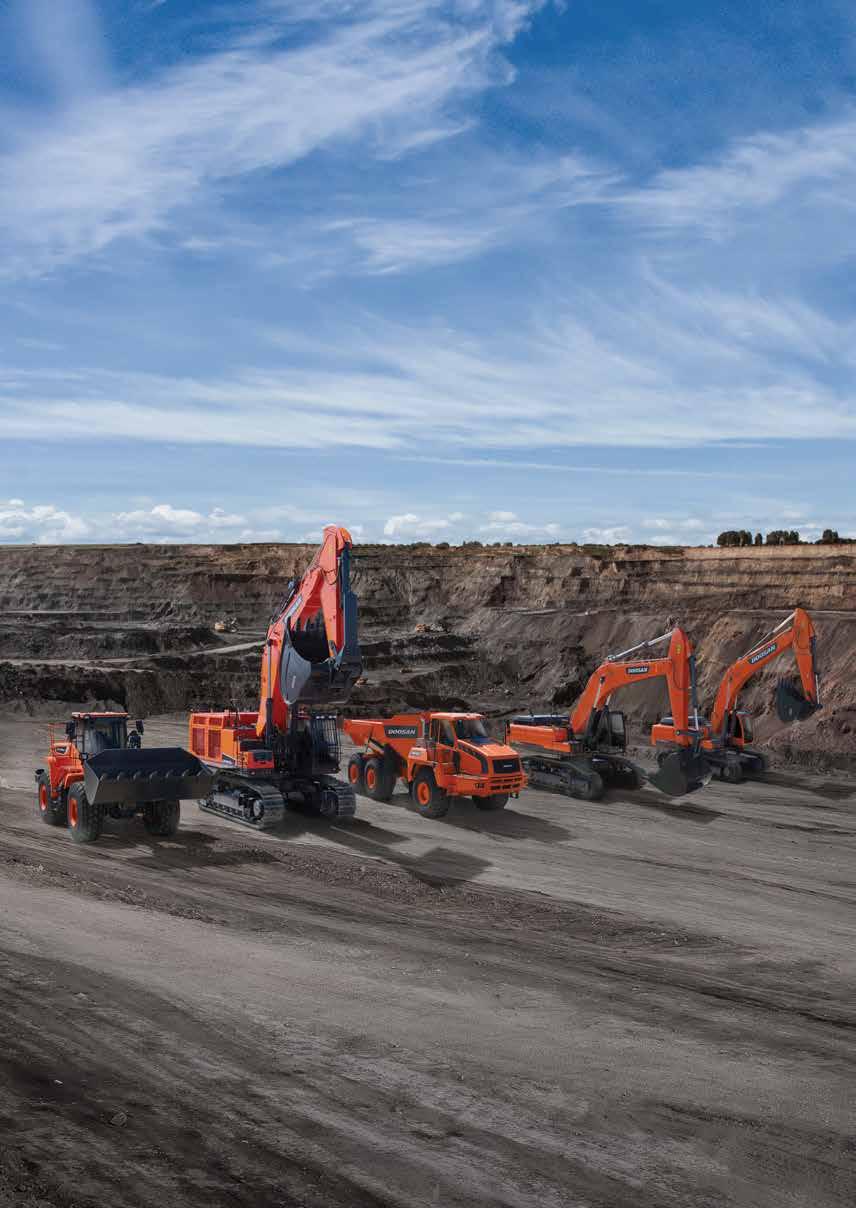