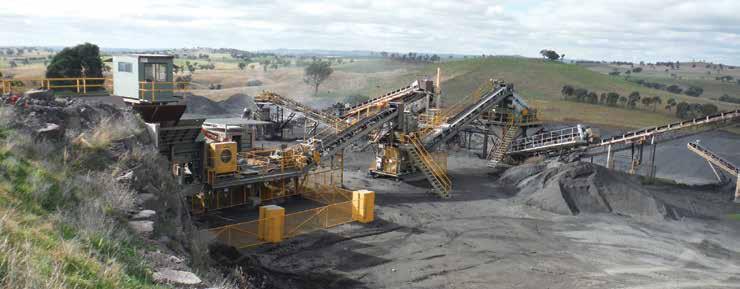
9 minute read
BLOCK UNIT OVERHAUL
Hanson’s Molong Quarry has been in continuous operation for almost 30 years.
BLOCK UNIT OVERHAUL BEATS BEARING, SHAFT FAILURES
A Hanson operation in the central west of New South Wales has turned to solid block housed units to address numerous bearing and shaft failures in its conveyor tail pulleys.
Amaintenance program to replace all conveyor bearings with Timken SRB solid block housed units (previously known in the industry as Blue Brute housed bearings) has meant an end to bearing and shaft failures in the tail pulleys at the Hanson aggregate quarry at Molong in New South Wales’ central west region.
In continuous operation for almost 30 years, Molong Quarry has been an integral part of Hanson Australia since 2005.
One of the leading sites in the group, the quarry produces aggregate for construction and building projects throughout the central west region.
A series of bearing and shaft failures, predominantly in the conveyor tail pulleys, initiated a search for a reliable replacement in the tough working environment.
“By its very nature, a quarry is tough on components such as bearings,” said Molong Quarry’s manager Chris Cooke. “They are generally covered in dust all the time. And each time a bearing or shaft failed meant a couple of days’ lost productivity while the damaged component was removed and the replacement fitted.”
Cooke said the removal and replacement process would affect the site’s run of materials and also occasionally delay deliveries.
Designed to operate in the toughest of environments, the SRB solid block housed units (SBHU) are considered ideal for heavy
An SRB SBHU installation.

duty operating environments. They offer continual extreme load and speed capacity due to the size and number of the two rows of rollers. They are designed to allow for limited shaft and housing misalignment (up to 1.5 degrees from centre) and still work at full capacity. The bearings are distributed nationally through the BSC branch network. “Around the time failures started we were invited to a workshop at the local BSC branch, where they were demonstrating the SRB SBHU product,” Cooke said.
“After having a good look at what they [the SRB SBHUs] had to offer, we didn’t need much convincing. The benefits were easy to see and gave us the solution we needed.”
The Molong Quarry uses the two-bolt pillow block unit, one of seven housing styles available. Four locking styles and seven seal types combine to offer a range of housed bearings to suit virtually any industrial work site and environment. The range will suit shaft sizes from 35mm to 180mm.
To improve maintenance access, Cooke installed greasing lines to the bearings.
“Some of the bearings are hard to get to, so we have installed grease lines to make them accessible from ground level,” he said. “The
bearings have a purge feature so we can’t overfill them and they maintain their integrity and reliability.”
He said the bearings had met all expectations.
“They’re good. They keep working and we are not losing any time due to bearing problems on the conveyors. That’s the type of performance we want. And they last. We pulled one down recently as part of a maintenance program and, aside from a few scratches, it looked just as good as the day it was installed.”
ADAPTABLE TO HARSH CONDITIONS The Timken SRB SBHUs are made from cast steel, giving equal load capacity in any radial direction and allowing simple horizontal mounting, with the inclusion of multiple levels of sealing to protect the bearing in operation. Harsh operating environments often lead to housed unit bearing damage. However, the SRB SBHUs multiply protection with primary and secondary seal options, as well as steel covers in sizes to fit all Timken solid block housed units. Depending on the sealing configuration, up to eight layers of protection can be achieved to protect the bearing, maximising operational life.
Moreover, as most conveyor applications have some amount of structural misalignment, sealing efficiency can be compromised, reducing the life expectancy of most housed units. The SRB SBHUs, however, run efficiently on misaligned shafts up to ±1.5 degrees as a result of the unique design of the spherical roller bearing extended inner ring, where the primary seals run.
The SRB SBHUs are supplied preassembled, so there isn’t any set-up required, which reduces the risk of contamination and precludes feeler gauges during installation, as the SRB’s radial internal clearance is factory set. Moreover each housed unit can be simply adjusted during installation to make it a fixed or floating bearing unit, eliminating the
An SRB solid block housed bearing unit.
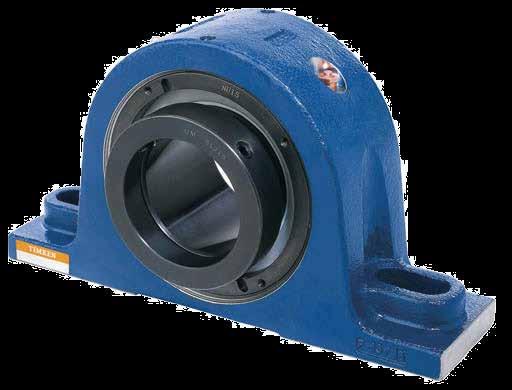
accidental FX/FX issue from oversupply on components.
A range of shaft sizes, from 35mm (1.3”) to 380mm (15”) and mounting options are available.
The housing configuration can also be customised. The SRB SBHU offers interchangeable solutions for common SN, SAF and SD pillow blocks, flange and takeup designs that other manufacturers simply cannot offer. •
Source: Inenco Group
!REYOUGETTINGUNBIASED SCREENINGADVICE
7EWONTDIRECTYOUTOWARDSANYPARTICULAR PRODUCT,OCKEROFFERTHECOMPLETERANGE
7EWANTTOPROVIDETHEBESTSCREENFORYOU
s 7IRE s 2IPPLEAND0OLYRIPPLE s 2UBBER s 0OLYURETHANE s 4UFFLEX s -ODULAROR4ENSIONED3CREENS
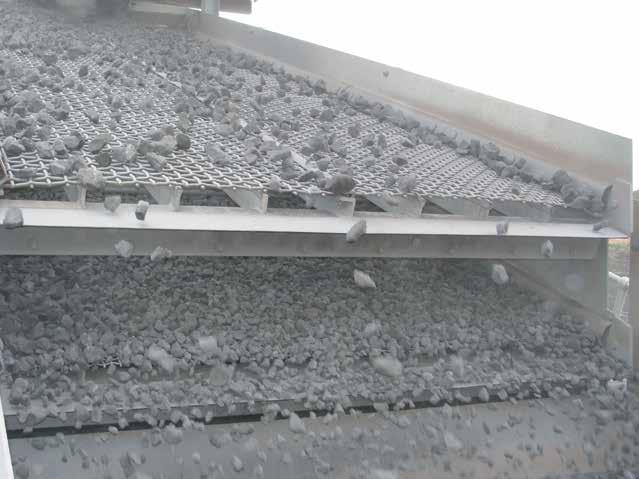
#ONTACTYOURLOCALSCREENINGEXPERT
Original equipment manufacturer (OEM) Haver & Boecker Niagara is offering the mining and aggregates industries rugged primary crushing plants in a wide variety of configurations for pre-crushing, secondary and tertiary crushing. From design to installation, the OEM is using its extensive industry experience and knowledge to provide turnkey systems engineered and built to individual specifications.
Haver & Boecker Niagara – which was established to combine the engineering expertise and product portfolios of its three minerals processing facilities in Brazil, Canada and Germany – will work with any crusher and supplementary component manufacturers to ensure producers receive the best plant matched to their requirements.
Haver & Boecker Niagara highlighted its primary crushing plant systems at bauma 2019 in Munich.
“We’re entrenched in the mining and aggregates industries and are dedicated to each customer’s profitability and success,” Peter Grotjohann, the managing director of Haver & Boecker Niagara’s German facility, said. “We use our industry experience and work closely with each operation to design comprehensive primary crushing plant systems with the highest level of durability, service and flexible design so each customer can find the best plant for their operation.” Haver & Boecker Niagara offers turnkey primary crushing plant solutions through customer-orientated project support, from initial concept to the production phase. In addition to co-ordinating the physical plant, the OEM offers structural building engineering at the start, including verifiable statics calculation. The company can provide transportation management, supervision or the complete package – from assembly and electrical installation to plant start-up and optimisation. Haver & Boecker Niagara also offers project management, on-site services, operating supplies, components or plant control. Operations also benefit from service and spare parts planning and service contracts.
Haver & Boecker Niagara provides crushing plant systems with a variety of components, including impact, jaw, cone or roller crushers, Haver screens or rolling screens, push feeders, apron conveyors and Haver vibrating
The N-class eccentric screen is a mainstay of any customised Haver & Boecker Niagara crushing plant.

Haver & Boecker is offering rugged primary plants in a wide variety of configurations for pre-crushing, secondary and tertiary crushing applications.
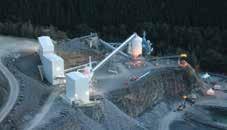
feeders. The plant systems work with all peripheral components such as maintenance cranes, de-dusting systems, compressed air systems, hydraulics and hammers.
Customers choose from two types of systems: basic or master. Basic is the classic pre-crushing plant that incorporates a Haver & Boecker Niagara N-Class eccentric screen to relieve the primary crusher. It includes a feeder, vibrating screen, crusher and several conveyors. If needed, an additional screen deck separates stony earth, either for stockpiling or to be fed to production.
The master system allows customers to get the most production and profitability out of their aggregate deposit. The system offers increased flexibility for primary crushing stages, especially with non-homogeneous natural deposits. For high quality natural deposits, the operations can use the master system to feed extracted material completely to the production. The system can screen stony soil off to a second vibrating screen for moderate natural material deposits. The system can be configured to completely remove stony soil from difficult material deposits.
Both systems work with the Haver & Boecker Niagara N-Class vibrating screen. The screen is perfect for scalping thanks to a smooth operation and heavy-duty design that can screen as much as 5000 tonnes per hour. Haver & Boecker Niagara builds the equipment with an advanced four-bearing design that minimises structural vibration and maintains constant g-force even through fluctuating material feed rates.
The OEM’s primary crushing plant systems feature rugged steel construction and a robust design incorporating a durable, optimum flow, low wear and maintenancefriendly chute system and integrated custom conveyor technology. Accessibility is easy, thanks to engineered work platforms, walkways and stairway systems. Integrated plant control systems and data management also ensure intuitive operation.
Haver & Boecker Niagara also gives extensive consideration to personal safety and environment requirements. It supplies comprehensive plant documentation on CE requirements (European Conformity requirements and equivalent) and a declaration of conforming to New Machinery Directive 2006/42/EC (CE) . Haver & Boecker’s Australian arm is headquartered in Perth, Western Australia. •
RELIABLE MACHINES OUT OF THE USA Tricon Equipment is the exclusive distributor in QLD, NSW, VIC and TAS | Ph: 1300 859 885 LIPPMANN CRUSHERS
SCREENS AT THE TOP OF THEIR CLASS and
CRUSHERS The Lippmann LJ-Series jaw crushers are some of the most versatile crushers on the market, boasting some of the widest jaws in the category, along with innovative designs to deliver maximum throughput and production. The LJ-Series delivers industry leading jaw speed, teamed with enhanced die angles, to bring better reduction and material processing to a variety of applications.
SCREENS Lippmann mobile screeners are high capacity, heavy duty, versatile machines built based on the industry leading ‘High Energy’ screenbox. With the largest screening areas in their class, The LS Series screeners are designed to give customers high output and durability in the most demanding conditions, and deliver high production across industries.
LJ-2745 MOBILE JAW CRUSHER – POA
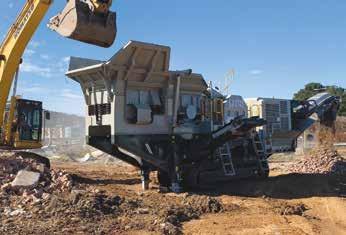
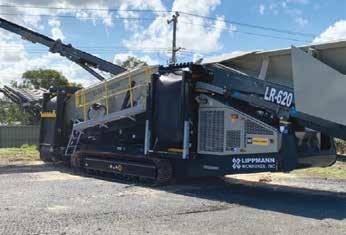
LR-620 MOBILE SCALPING SCREEN – POA
LR-516 MOBILE SCALPING SCREEN – POA
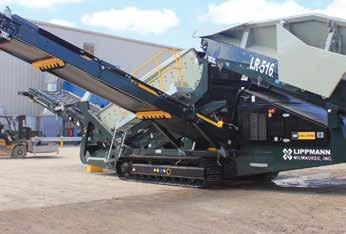
Call: Paul: 0488 012 384 Scott: 0488 288 056 Michael: 0417 281 795 Email: info@triconequipment.com.au Visit: www.triconequipment.com.au
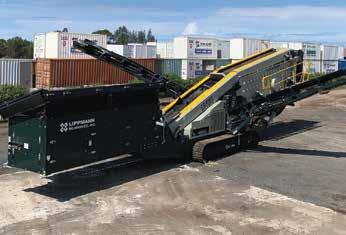
LS-520 MOBILE 3-DECK SCREEN – POA