
42 minute read
ELECTRIC POTENTIAL: COULD BATTERIES TRUMP DIESEL? Why an OEM is confident its work in battery development can alter the extractive environment
from Quarry Sep 2019
by Prime Group
ELECTRICAL POTENTIAL: COULD BATTERIES REPLACE DIESEL?
Suddenly it seems all pieces of the technological puzzle are falling into place. The battery revolution is under way – and one multinational OEM is convinced it can significantly change the energy landscape of the mining, and by extension the quarrying, industry.
June 2018 was a peak period of activity for Epiroc in Örebro, in central Sweden. An entire new generation of battery-powered mining machinery was to be launched in the following season, and a key person involved in that launch was Erik Svedlund, Epiroc’s marketing manager of vehicle electrification.
Svedlund has been involved in outlining Epiroc’s vision of emission-free mining environments, made possible by battery power. “Electric will replace diesel,” he said. “The machines that we’re developing here already perform equally well or better than diesel machines, except for one thing – running time. But with the rate at which batteries are developing, it won’t be long before that has caught up too.”
According to Epiroc, there has been “an explosion” in the market for electric-powered mining machines because the technology – primarily battery technology – has matured. Previous trials using electricity from cables or rails involved fixed and awkward solutions, and the flexibility required in a mine environment meant the decision traditionally
The Epiroc E2 battery-operated underground drill rig.
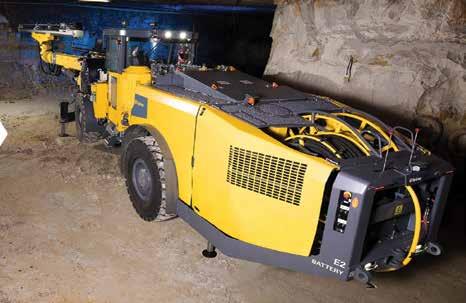
came down in favour of diesel machines. At least, that is, until now.
Svedlund became interested in batterypowered machines in 2010 and started studying the possibilities. “At the time I was head of products and I quickly realised that battery power could not just replace diesel, but could become a profitable business for both us and our customers. I started lobbying internally to start the development of such
Frederik Engman, technician (left), and Anders Lindkvist, project manager, discuss the best placement of powertrain components on an Epiroc Scooptram ST14 battery.
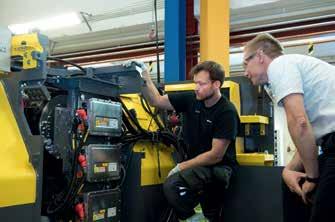
solutions. This went rather slowly until 2013, when we received a request from a customer in Canada. It then took less than a year from prototype to launch of the Scooptram ST7 Battery, and the machine’s performance exceeded expectations.”
The Scooptram ST7 Battery was among the first generation of battery machines launched by Epiroc in 2016. The machines that were subsequently launched in the second half of 2018 were second generation machines and included not just loaders but also mine trucks and drill rigs. “Loaders and mine trucks account for around 80 per cent of fuel consumption in mines,” Svedlund said. “These types of machines are the key – if we don’t come up with these, we won’t solve anything.”
SOUNDLESS ENGINE At Epiroc’s test mine in Kvarntorp outside Örebro, a Scooptram ST7 Battery stands with its bucket full of gravel. If you close your eyes there is nothing to indicate that the loader is running, until it starts to move – and all you hear then is the sound of the gears and axles, and the crunch of tyres on gravel. There is no engine noise. As the loader releases the gravel, the jangling can be clearly heard in the otherwise quiet site.
Anders Lindkvist, Epiroc’s project manager for technological development, and his team learnt a lot while working on the first generation. “For the first generation we basically took existing loaders, removed the engine and fuel tank, and put in an electric motor and battery instead,” he said. “But it worked. We were placing bets in the office on how long the machine could run on a battery, and all the guesses were between one and three hours. But it proved to keep going for five hours.”
The second generation machines were designed for battery operation from the outset; the mine trucks, for example, have motors on each axle. But it is the batteries that are responsible for the biggest change. “Quite early on we started developing a modular battery system that allows the modules to be used in any kind of Epiroc machine,” Lindkvist said.
One advantage of the new battery design is that it can be replaced quickly. In less than 10 minutes a fully charged battery can be in place, so even energy-intensive operations can continue with only a brief interruption.
It has been nearly three years since Epiroc’s management gave the green light to developing the second generation machines, and from
CALL THE EXPERTS IN VIBRATION
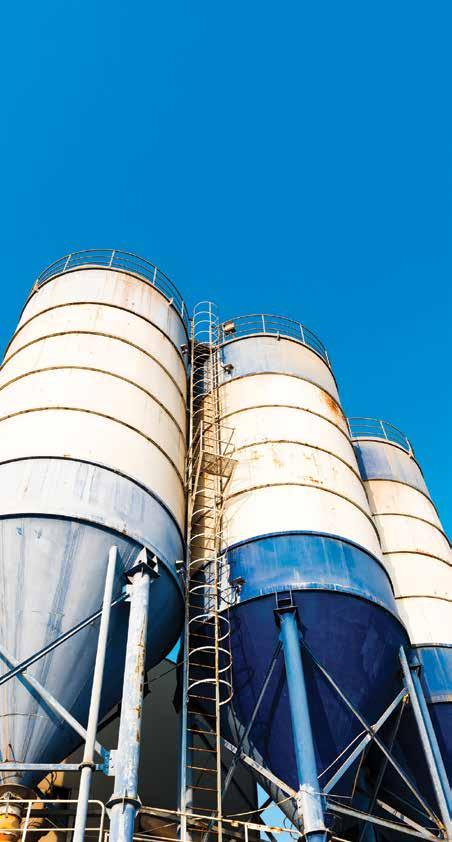
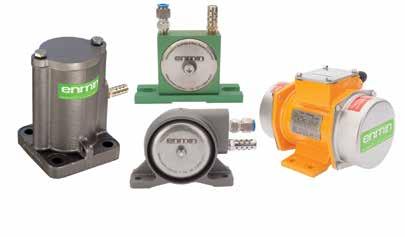
BOLIDEN MINES ENERGY PROGRAM
A test truck travels along a 700m electric trolley route at the Boliden Aitik copper mine, Sweden.
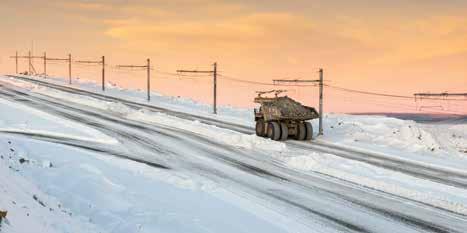
Boliden is a high tech metal company that employs about 5800 people in mine and smelter operations in Sweden, Finland, Norway and Ireland. Its end products include zinc, copper, lead, nickel, gold, silver, sulphuric acid and iron sand. It is also committed to a number of sustainability initiatives, including secondary material recycling and synergies, water management, mine automation and electrification.
In particular, Boliden has been engaged in a pilot project at its Aitik copper mine in northern Sweden, where it has been replacing elements of its transport system with electrified trucks, to move most of the 70 million tonnes of rock extracted at the open pit each year without the assistance of fossil fuels.
As a result it has installed a 700m electric trolley route with overhead wires (much like a tramway route) to power the electrified trucks. This potentially saves up to 830m 3 of diesel fuel per year and reduces up to 80 per cent of greenhouse gas emissions along the electrified routes.
The pilot project, being run over a two-year period, is supported by the Swedish Energy Agency, and it is being implemented with several partners, including ABB and Eitech (electrical infrastructure), and Caterpillar and Pon Equipment (truck conversion).
Jonas Ranggård, manager of the Boliden Mines Energy Program at Aitik, discussed the successes of the program so far. Q: What does your electric future look like? Why is Boliden working on the electrification of vehicles? A: There are a great many advantages to running vehicles on electricity rather than diesel. You can reduce ventilation and maintenance costs, and improve the work environment. From 2023, for example, the EU will be lowering the limit values for NOx in mining environments. Electricity is definitely the best way to deal with these requirements, but such a transition takes time. That’s why we have to start testing the technology now.
Q: How far have you got? A: We are still in the starting blocks. In August [2018] we began an 18-month project [to] test overhead lines and four mine trucks with current collectors in the open pit copper mine in Aitik. We decided to start with open pit mining because we use most diesel aboveground. Once the project has ended, we’ll assess whether the savings meet expectations, how good the availability of the vehicles was and what problems we encountered.
Q: What will be the next step? A: With our switch to autonomous drilling, we’re able to improve upon the rate of production, the accuracy of the holes, and the fragmentation, leading to downstream improvements in our processes as well as improving our safety.
22 Quarry September 2019 that point Lindkvist and his team worked at full throttle.
“This is a new way of working that’s fun and exciting,” Lindkvist said. “It’s tremendously enjoyable to be able to introduce so many new things in such a short time. And on three machines in parallel, too.
“Now we need our suppliers to come up with new solutions at the same rate that we need them.”
Sofia Bratt has been responsible for Epiroc’s project office, which has co-ordinated the work to develop the second generation. “There’s been very close collaboration in the group and with our suppliers,” Bratt said. “It’s been huge fun and has developed all those involved, and I think this type of project will become more common in the future.”
Bratt described a process in which the project office succeeded in breaking new ground. “We’ve looked at areas such as battery cell chemistry, drivelines and control systems, and have been able to evaluate what’s most optimal for our applications. An incredible number of people have been involved, which has made great demands of dialogue and communication. It’s required time and resources from everyone involved, but it’s also been very effective.”
CALM, STEADY PACE In the Epiroc workshop, the first second generation batteries were tested calmly and steadily ahead of their launch at a specially convened event in Örebro in late 2018. These machines included the Scooptram ST14, Boomer E2 and the Minetruck MT42.
According to Epiroc, more customers are starting to demand battery machines. Although diesel machines can reliably do the job, they are not without problems: harmful exhaust emissions, noise, waste heat, high maintenance costs, unplanned stoppages for servicing, rising fuel costs and an increasingly complicated infrastructure.
By comparison, according to Epiroc, batterypowered machines need significantly less maintenance, not least because an electric motor contains a fraction of the number of moving parts in a diesel engine. They give off marginal amounts of waste heat and have no exhaust emissions. If the batteries are charged using renewable electricity, they have no climate impact either.
Safety and sustainability are also an important part of Epiroc’s strategy, and can contribute to its customers’ sustainability work and environmental impact. The company also believes battery-powered machines
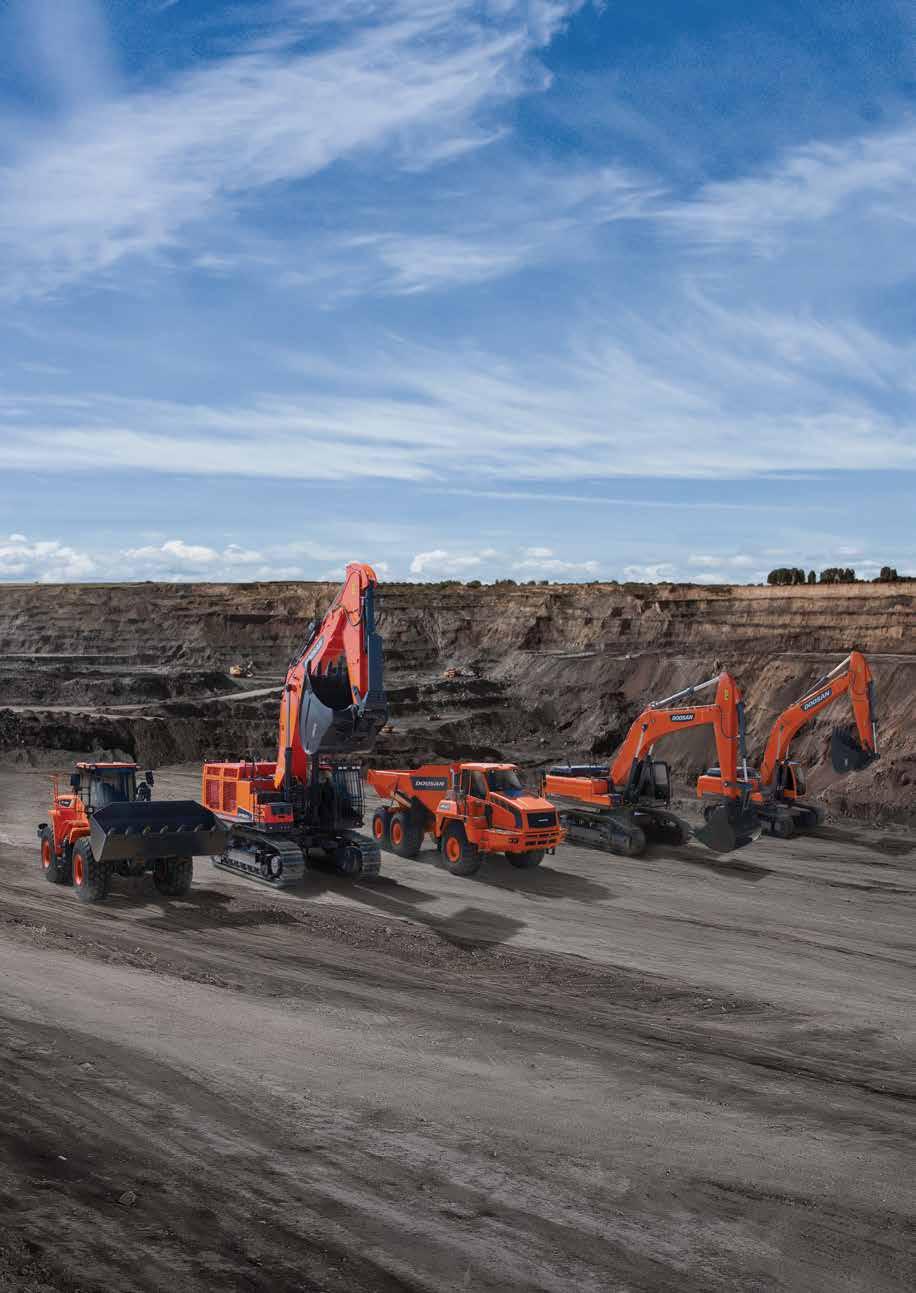
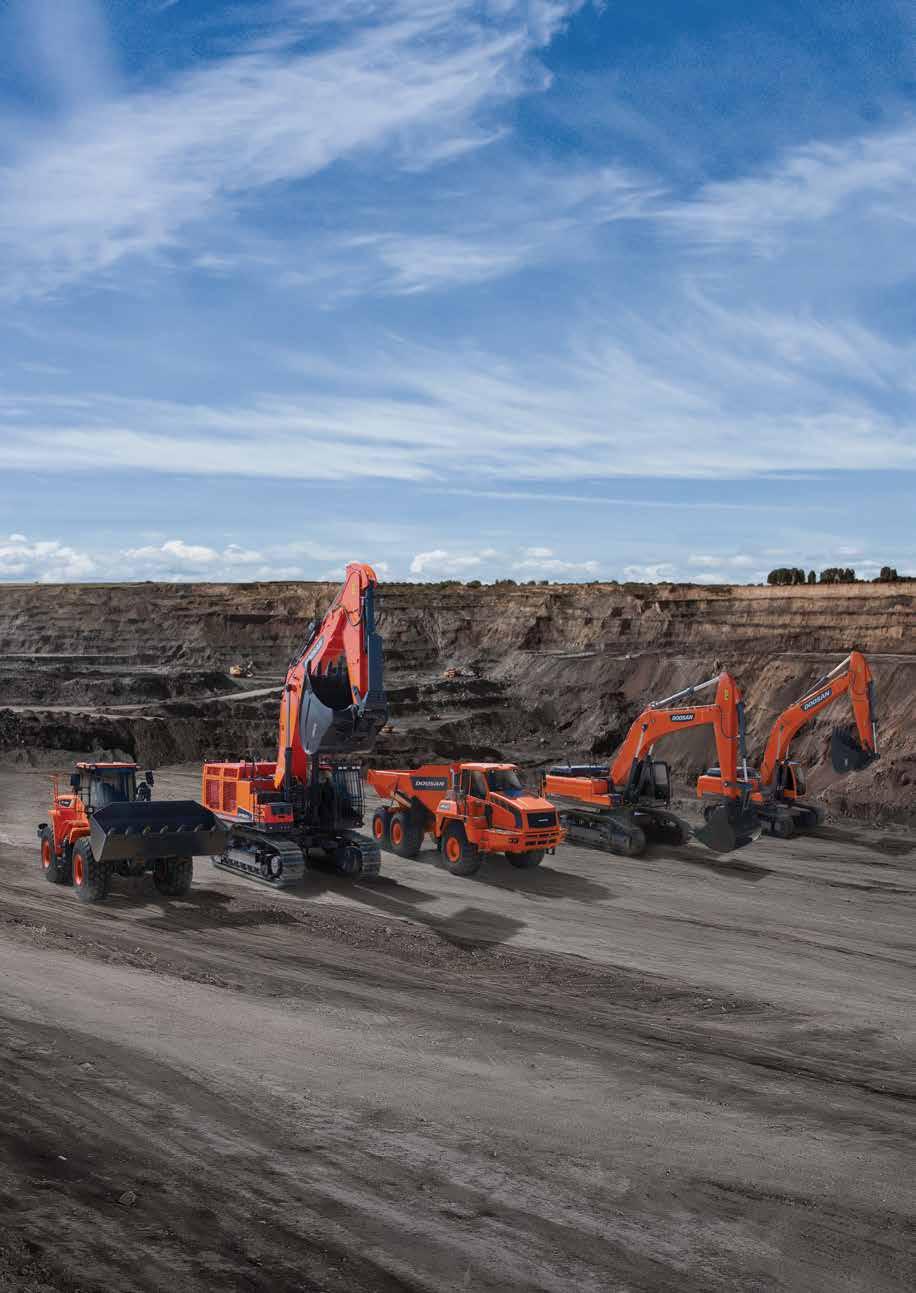

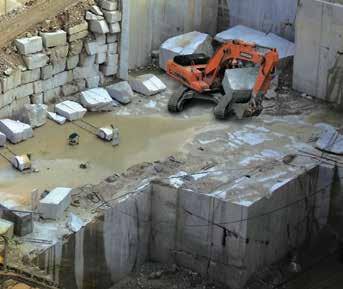
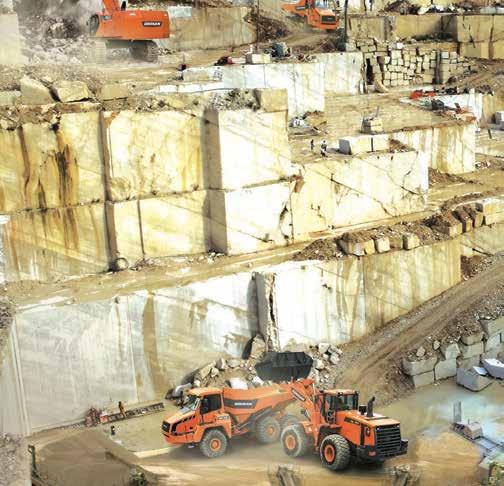
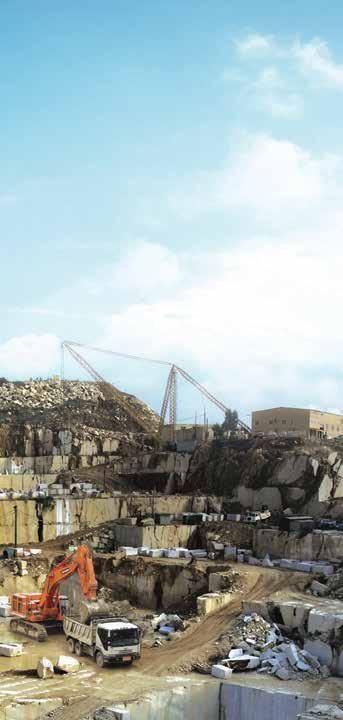

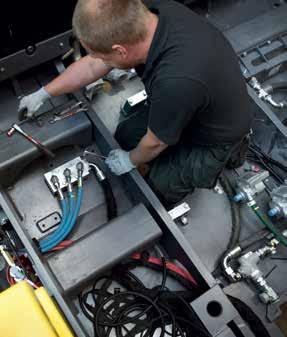
driven by legal requirements and more stringent rules on emissions. Underground, the driving force is instead a desire for a safer work environment – and pure and simple economics. The potential savings are enormous.
A technician works on the battery for Epiroc’s second generation of battery machines.
can help achieve one of the United Nations’ Sustainable Development Goals: access to affordable, reliable, sustainable and modern energy for all.
“Diesel machines are actually poorly suited for use in enclosed spaces underground,” Svedlund said. “A lot of cooling and ventilation are required to deal with the exhaust emissions and heat, and this has become the single largest energy cost in mines.
“If we take away the diesel engine, the situation changes completely. Ventilation costs reduce dramatically and you can go even deeper while still being cost-effective.”
Unlike the shift to electric cars, therefore, the transition in the mining industry is not primarily
AFTERMARKET COMPONENT The person keeping an eye on the aftermarket aspect is Fredrik Martinsson, Epiroc’s marketing manager of service electrification. “Solving the financial model and at the same time strengthening the tie to our customers is a key activity,” he said.
Martinsson’s task is to devise a new business model that will make it as easy as possible for producers to switch to electric operation. The basic idea is that the producer buys the machine, but has a subscription for the batteries. The advantage is the investment is lower, operating costs are predictable and Epiroc takes all the responsibility for the training, maintenance and servicing associated with the batteries. If a customer needs more or less power, the subscription can be adjusted. “We want to dramatically lower the threshold for electrification,” Martinsson said. “We want it to be easy. This is a major change, and it will require hard work by many people over a long period. But everyone – suppliers, customers, the environment and ourselves – will be a winner.”
Source: Epiroc Australia
ZERO EMISSION INITIATIVE
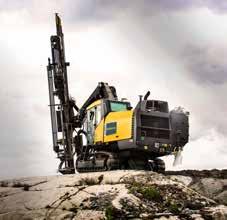
Epiroc’s goal is to offer a zero emission alternative for all its underground mining and tunnelling equipment. The complexity and demands of these kinds of products are high, and, in addition to its own know-how in-house, Epiroc is drawing on external expertise from battery cell and electric drive train manufacturers. ■ The technical solution will vary depending on the type of machine, but everything evolves around the battery electric driveline.
■Customer interaction has always been a key factor in Epiroc’s development work, in addition to increased demands on safety, health, quality and the environment.
■With the zero emission product portfolio, Epiroc is improving health and safety. As a leading OEM, Epiroc considers the mining industry’s carbon footprint and shoulders its responsibility as an industry leader.
SUSTAINABLE INTELLIGENT MINING SYSTEMS
Sustainable Intelligent Mining Systems (SIMS) is a three-year European Unionfinanced project to produce demonstrations of future products for the mining industry. Under the project management of Morgan Rody, the SIMS senior project manager, Epiroc is co-ordinating a collaboration of 13 partners, including manufacturers, mining companies and universities.
Q: What is the EU’s expectation of SIMS? A: Our focus is on “innovation action”. We start from a research project and produce functioning products to demonstrate that the theory works in practice. The EU has high expectations of concrete results. Seventy per cent of our budget – 13 million Euros [more than $AUD21 million] – comes from the European Commission. So we have to deliver. Q: What type of projects are you working on? A: Battery solutions are a big thing and there’s a lot happening in this field. For example, we compared how great the difference is between diesel and batteries. What level of particulates does diesel operation result in? We also have lots of other projects in progress, such as drones, the next wireless mobile standard 5G, better positioning services, thermal imaging and assisted driving systems for diesel-free machines. Also virtual reality, which has become really hot again. We’re aiming to construct a mine in VR so we can demonstrate solutions at events such as trade shows. Many of the projects are concerned with safety, and we’re proud of that. Each person that can be moved out of a dangerous environment is a gain.
Morgan Rody, senior project manager, Epiroc.
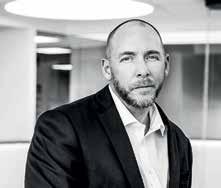
Q: Has the SIMS collaboration worked well? A: Extremely well! It’s useful to meet up properly. And all the partners are aware that what they are doing now will change the mining industry.
Our rental fleet includes the latest equipment from the world’s leading manufacturers.
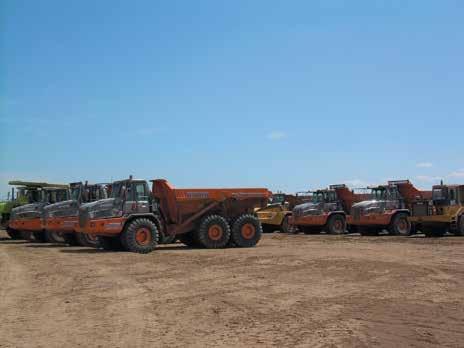
Hydraulic Excavators Hitachi and Komatsu 30 to 90 tonnes, Volvo EC480DL
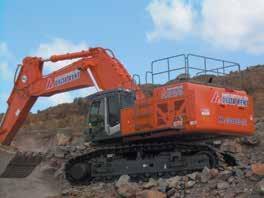
Articulated Dump Trucks Hitachi, Bell 30, 40 & 50 ton capacity & Volvo A45G
The Right gear in the Right place at the Right time Wheel Loaders Komatsu WA500s & WA600s IT28G, IT62Hs. Volvo L260H & Hitachi ZW370, ZW310 Compactors Caterpillar 815Fs & 825Hs
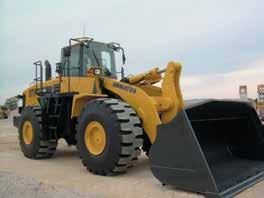
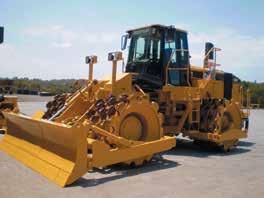
Delta Rent Pty. Ltd. 577 Plummer Street Port Melbourne Victoria 3207 FOR MORE INFORMATION PLEASE CALL: Richard Khan, General Manager, Office: 1300 793 071 David Hoyle, Territory Manager East Coast, Mobile: 0423 571 081 Phil Aguis, Territory Manager VIC, Mobile: 0418 753 981 Darren Barlow, Territory Manager SA, Mobile: 0418 800 231 www.deltagroup.com.au
BIG CHANGES MOOTED BY DEALER FOR EARTHMOVING MARKET
The general sales manager of the new eastern states distributor of John Deere Construction and Forestry Equipment (excepting Western Australia) predicts the brand will make a big impact on the Australian market.
RDO Equipment’s general sales manager Mark Kuhn said that by early 2020, Australian customers will be able to purchase the full line of John Deere products, including quarryspec equipment such as wheel loaders, dozers, backhoes, excavators and articulated dump trucks. The products will be sold and serviced by a strategic dealer network, supported by a new John Deere parts depot and a highly trained team.
Kuhn said even before the launch in May this year, there had been a positive reception for RDO.
“People are looking forward to this change,” he said. “They’re excited about the expanded product range – everyone wants more product – and they’re excited by RDO’s approach to partnering with customers.” He said the RDO customer experience started with getting the basics right. “It’s actually simple stuff that makes good customer relationships. It’s getting back to people, it’s letting them know what’s going on, doing what you say you will do and being accountable.
“We say that the real work for our customers begins after delivery, with our plan to support them. That might involve cross-training their staff or developing parts consignments so they have parts ready the moment they need them. We aim to tailor our service to the customer and have plans in place before our customers have a problem. This is how we build customers for life, another core value for RDO.
“We have put together a strong team here in Australia, including lots of industry veterans with really solid experience, and all of our people are passionate about the business. We’re 100 per cent focused on the John Deere product.”
Kuhn said RDO had big plans for the Australian market, including consolidating and growing its forestry market share over the next three years and bringing the full John Deere construction range to Australian
The Deere ADT 460E will be amongst the new Australian offerings for interested quarrying producers.
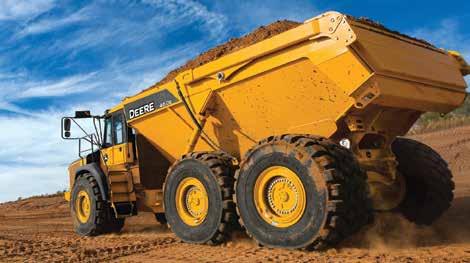
dealerships inside 12 months.
“There’s still a lot of major infrastructure work across Australia so we expect our first year will include a focus on graders and wheel loaders. And we know there’s a lot of excitement in the market about the new products coming in over the months ahead, including the excavator range,” he said.
“The Australian market is very eager for the full line of John Deere equipment. They know that John Deere means quality and reliability – and RDO means an exceptional customer experience.”
Jeff Kraft, the managing director of John Deere Construction and Forestry’s AsiaPacific and Africa division, says the OEM is excited about what the new distribution agreement means for the Australian market. “This is a strategic partnership for us. We see the Australian market as an important part of our Asia-Pacific and indeed our global brand footprint,” Kraft said. “We’ve made strong investments in this market and we’re looking forward to working closely with RDO to expand John Deere Construction & Forestry’s profile in Australia. We foresee a very positive future here.”
RDO will offer Australian John Deere customers an initial eight dealership sites, mostly utilising its existing Vermeer facilities that in the past have supported productionclass machines for the quarrying and aggregate industries. Each is armed with advanced machine monitoring, remote diagnostic capability, and world-class parts availability. Wheel loaders are available from dealers now, with articulated dump trucks and dozers due by the end of the year.
Ron Offutt, a potato farmer in Casselton, North Dakota, established RDO, the world’s largest John Deere dealer, in 1968 when he was 26 years old. More than 50 years later, RDO Equipment has more than 80 locations in the United States, and partnerships in Australia, Africa, Mexico, Russia, and Ukraine.
RDO first came to Australia in 2012 when it acquired a 50 per cent interest in Vanderfield, a 14-store John Deere agricultural equipment dealer based in Toowoomba. In 2015, it made a further investment in Vermeer Australia. RDO is now also the world’s largest Vermeer dealer.
The company became the John Deere Construction and Forestry Equipment distributor for most of Australia on 1 May, 2019 and will support customers from eight branch locations.
The distributor for Deere products in the Western Australian market is AFGRI Equipment. It will service the WA market from five strategically placed branches in Geraldton, Albany, Esperance, Boyup Brook and Perth. •
« MOBILE CRUSHERS « MOBILE SCREENS & SCALPERS « CONVEYORS & STOCKPILERS « WASHING PLANTS & PUGMILLS « PRECOATERS & TROMMELS DRY HIRE AVAILABLE PARTS & SERVICE SUPPORT

PRECISIONSCREEN SCORPION PUGMILL PLC « Versatile machine that can be adapted to work with various applications « PLC control system allows the ability to select different product mixes at the touch of a button « Clam shell pughead for easy access & maintenance « Built in Australia for Australian conditions
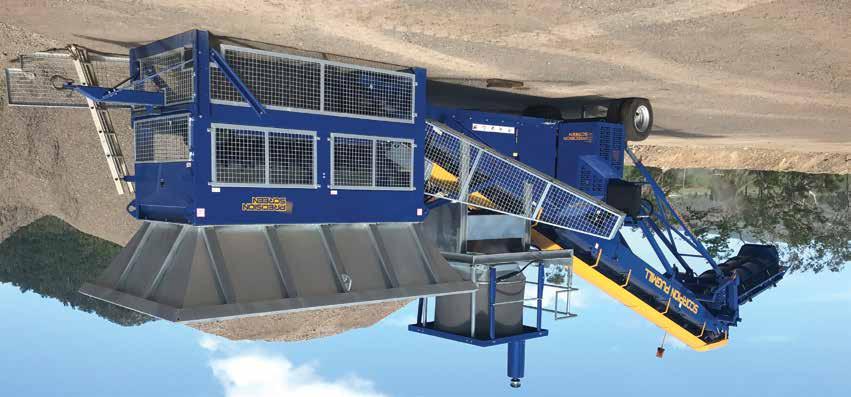

Trackstack 8542TBF 85ft Tracked Belt Feeder Stockpiler
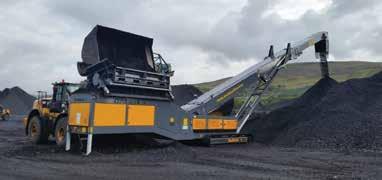
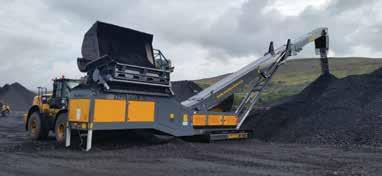
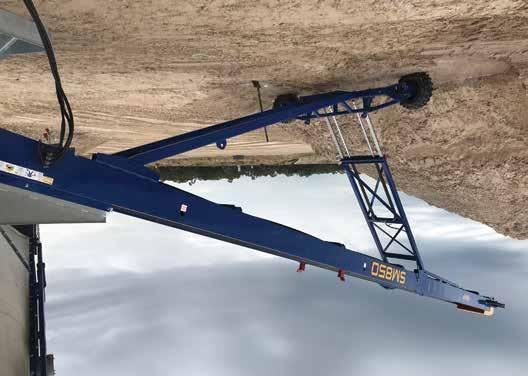
PRECISIONSCREEN SM CONVEYOR RANGE « Australian made wheeled conveyors ranging from 30ft (10m) through to 100ft (30m).

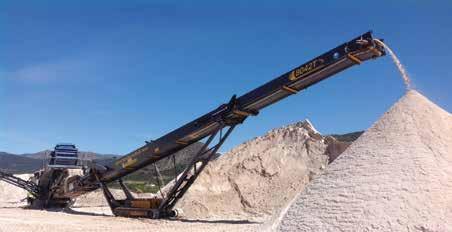
Trackstack 8042T 80ft Tracked Stockpiler
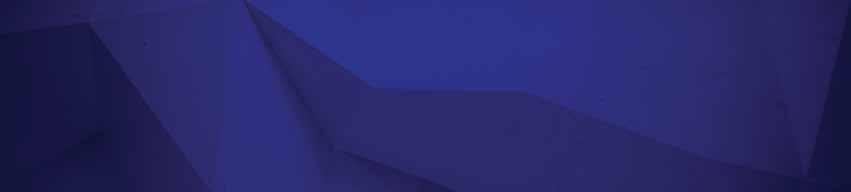
sales@precisionscreen.com.au | www.precisionscreen.com.au 1800 727 991 (Free call AUS)
FAMILY BUSINESSES KEEP FAITH WITH EARTHMOVING EQUIPMENT
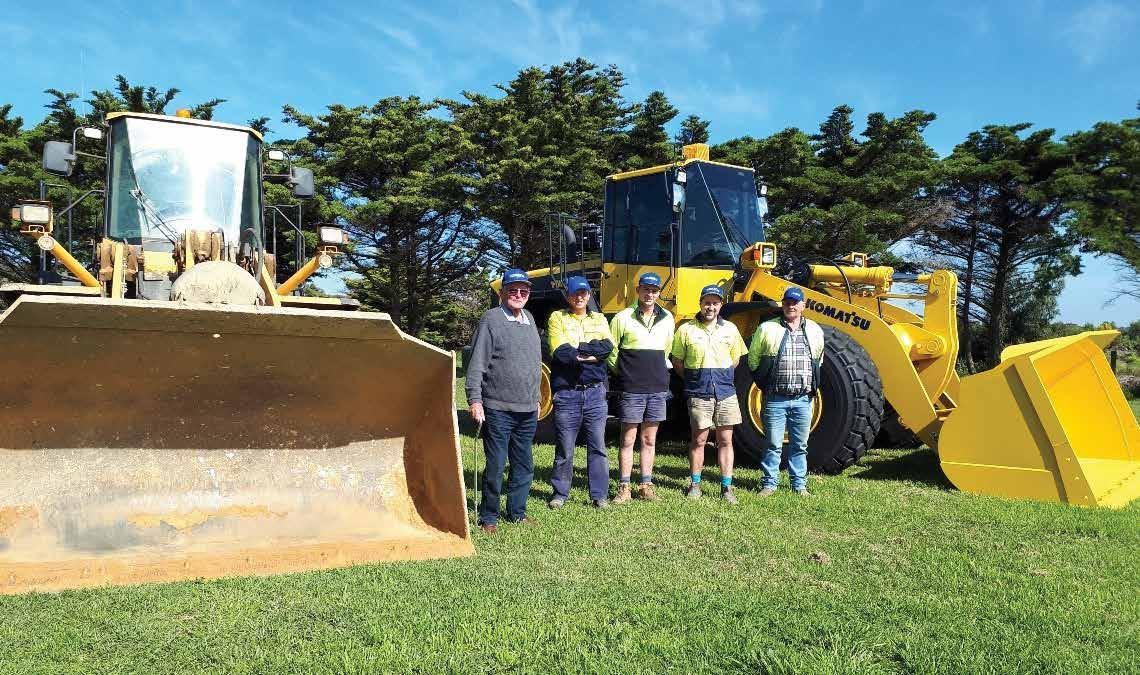
They may be separated by kilometres of coastline but two family companies continue to demonstrate their longevity and durability through decades of service – and their commitment to continuity in their earthmoving fleets.
Menheere Bros has been operating the Ocean Grove Quarry - the last remaining active site on Victoria’s Bellarine Peninsula - for nearly 40 years. The family company’s director Mark Menheere said the family-run business has relied on Komatsu wheel loaders across the generations.
“My father Lofty started the business nearly 60 years ago,” Mark said. “He ran it when I was a boy and I had my go at it as managing director for 30-odd years before stepping down. Now my eldest boy Matt is running the show at our quarry and my other son Ryan runs the earthmoving side of things.
“Dad is a Dutch immigrant who was in the army and also a truck driver,” Mark added of his family history. “He decided he wanted to come and have a go in Australia and started his business.
“I can remember in the early days he had a couple of single-axle trucks, which would be five or six cubic yards by the old imperial measurement [4.5m to 5.4m in today’s metric system]. He didn’t have his own loader then and would sometimes have to load his truck by hand with a shovel, doing so two or three times a day. Now he comes down to the quarry and sees the latest Komatsu
28 Quarry September 2019 WA380-6 wheel loader in action, which goes to show much things have changed just in his lifetime.”
Indeed, the Menheere business has come a long way from shovelling up to three times a day. The manner in which Menheere Bros adopted machinery to work more productively started with Lofty Menheere and continues to this day.
“His first loader was a Fordson and was cable-operated, no hydraulics,” Mark said. “That was a big thing for the business. Then he bought a Hough loader - Hough later being acquired by Komatsu – before switching to Komatsu proper about 30 years ago with his first WA250 wheel loader. We put 13,000 hours on that before selling it. Considering how long we’d had it and the amount of work it had done, we got a really good price for it. That’s one of the reasons we’ve stuck with Komatsu loaders ever since.”
RELIABILITY ACROSS TIME Another key reason for this loyalty is the brand’s reliability across the generations. “We’ve had a great run with our WA380 loaders,” Mark said. “We bought one which now has about 14,500 hours on it and remains in our fleet as a back-up machine to the new one we bought recently.
“They have been really reliable, which is a huge factor. If you’re in the quarry and you can’t load out because of a breakdown or fault, you’re in real trouble.”
Mark doesn’t readily recall too many occasions when his equipment has let him or the business down. “You don’t so much remember the times when things have gone right as much as when they go wrong,” he said. “If you had to recall sometimes that a machine has let you down, well, you do remember those. Luckily, with our Komatsu loaders, 99 per cent of the time they just start up and away you go. We’ve actually come to take that for granted.”
When it came time for a new wheel loader, Mark’s son, Matt Menheere, who has taken on the company’s reins as director, knew exactly what he wanted. “I was confident in another WA380-6 wheel loader because we’d had such a good run with the previous one,” Matt said. “Nothing much went wrong with it, at all, for a good 12 to 13 years - I think there was a little solenoid problem that Komatsu got right to the bottom of and repaired straight away - so there was no need to change.
“We’ve been really happy with the later model. There aren’t huge differences between it and our older model, but it has more power and is more efficient. It rides more smoothly and is more comfortable.”
Matt also requested on-board scales and an auto-grease system for the new WA380. “We had the same on our other 380 and it
makes a difference to our operations,” he said. “The scales allow us to meet changing responsibilities for loading and measuring, both from a sales perspective and for occupational health and safety. And the auto-greaser is handy because it’s timeefficient, providing for weekly rather than daily preventative maintenance.”
With Menheere Bros’ Komatsu loyalty firmly entrenched, Matt could not envisage changing brands. “No, we were happy with our old ones, we’re happy with our latest one and we expect to be happy when rolling over our Komatsu loaders in the future.
“We keep an eye on the market and do some research, but we don’t see value in going to cheaper brands. A reliable machine can save you a lot of money. Conversely, you don’t want to be repairing expensive machinery and facing production loss.
“It’s the old adage: ‘The poor man pays twice’! If you buy a cheap machine that breaks down it very quickly becomes an expensive one.”
Bashford & Sons’ new Komatsu D155A-8 (left), alongside the older D60A-3.
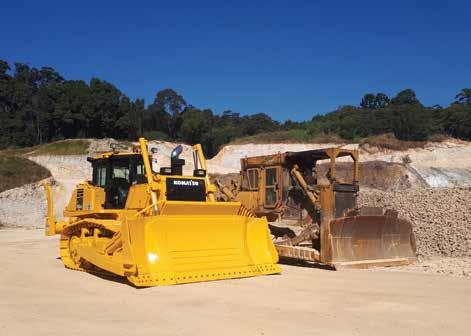
A LIFETIME OF BULLDOZERS Further north, another family company – J&M Bashford & Sons – has acquired a new Komatsu machine for its heavy equipment fleet.
John Bashforth is a fourth generation farmer, quarry and machinery operator in the Byron Bay region of New South Wales, and
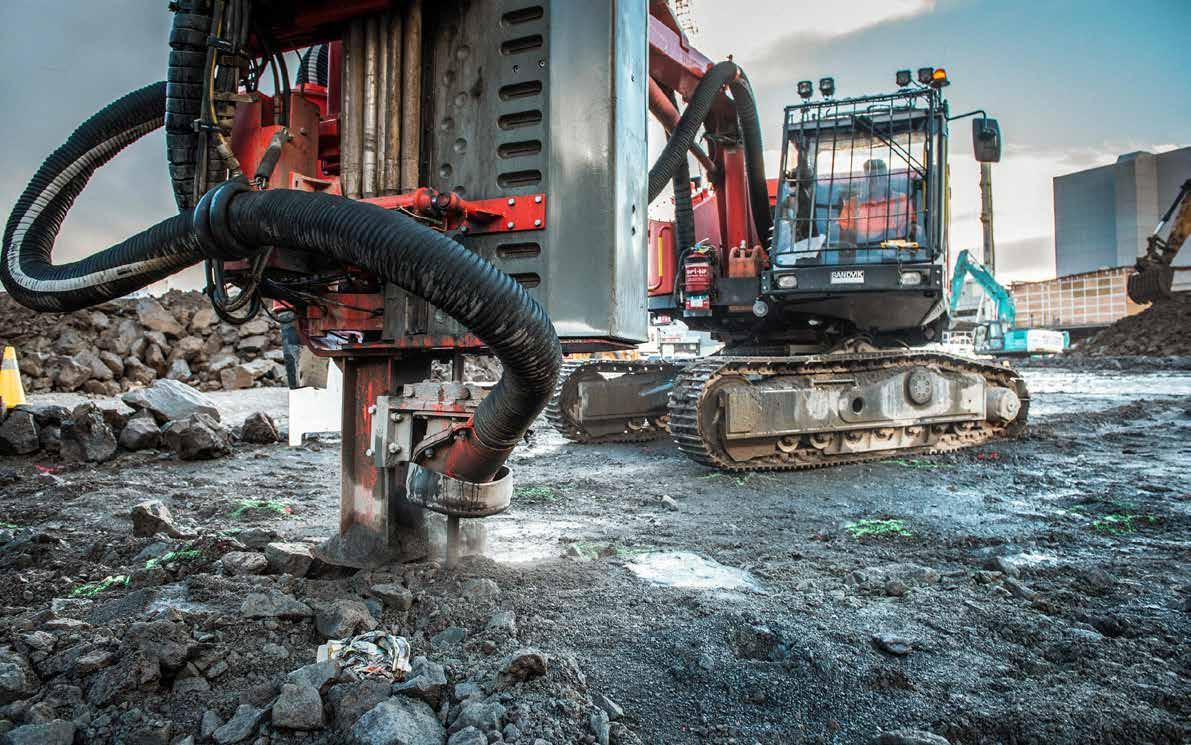
tends not to turn over his heavy equipment often. He is the CEO of J&M Bashforth & Sons, one of the NSW northern coast’s renowned and most prolific operators, with more than 30 machines and a like number of operators working across three primary sectors - quarrying, development and general machinery for local farmers and builders.
John bought his third Komatsu bulldozer
The PC138-US is the latest addition to the Bashford fleet.
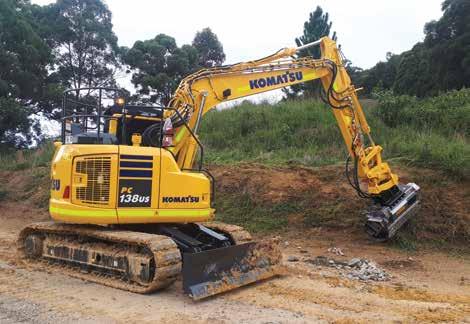
Father and son Mark and Matt Menheere with the Komatsu WA380-6 wheel loader.
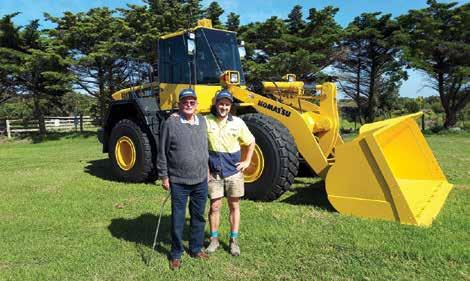
at the end of June, almost half a century after his father Jack purchased the family company’s first. The three machines have seen continuous service.
The original, a D60A-3, which John believes to be only the second Komatsu bulldozer sold in Australia, saw a relatively “brief” 18 years of action on the family’s quarry. The second, a 155A-1, is the long service record holder, with 31 years’ hard work before it was replaced only recently by a high technology Dash 8 version of the same machine.
The core of the family company’s business is its “near to unique” quarry, set just 12 kilometres inland from Australia’s most eastern point – the Byron Bay lighthouse.
John’s father Jack discovered the quarry in the mid-Sixties while clearing for the farmer that owned the property. The quarry’s chert resource – a hard, fine-grained quartz silica with unique self-compacting properties that make it highly prized for base material in building developments and on-roadwork – has long provided certainty to each of the Bashforth company’s divisions.
Jack supplied the first machinery to start the new Ocean Shores Development, and was awarded a contract to produce roadbase from a quarry on-site for the road infrastructure. It was in 1970 that then 16-year-old John, underaged and unlicensed, operated the first Komatsu D60A-3, to win and load material to, back then, one of the state’s largest residential and lifestyle developments, Ocean Shores.
“Fifty years on, we’re working on what could be the last phase of the Ocean Shores development,” John said. “The on-site quarry closed years ago, and returned to nature. The roadbase we use today is produced from the Myocum operation and the same equipment, somewhat upgraded.”
‘MECHANICAL THERAPY’ The Bashforth company today has permission to extract 100,000 tonnes of chert per year from the site and each year it comes within 5000 tonnes of its allowance.
“In fact, for the last two years we’ve been within 1500 tonnes,” John said.
It’s a fine balance made achievable by a number of operational rules that John, and lately his son Luke, have put in place.
“We have our machinery serviced on-site by its supplier to ensure continuity of mechanical knowledge and as much as possible we assign one operator exclusively to a machine,” John said. “The driver on the new
30 Quarry September 2019 Dash 8 was on the Dash 1 before that and he knows how to achieve the best result while treating the machine like he owns it.”
Extracting chert is an exacting process and John says the weight and size of the D155A-8 is well suited to the task. “There’s no need for a larger machine and the hours we need to fulfil our quota are well within the dozer’s capability,” he said.
According to John, the two machines are similarly productive but the Dash 8 does it with substantial improvements in driver comfort, vision and safety.
“I receive Komatsu’s monthly KOMTRAX report which enables me to understand the operating functions, like idle time, and how much time has been spent ripping and dozing, and how it can improve,” John said. “The good news is that it’s pretty much in-line with what my operator is doing.”
John literally grew up with machines, as his father Jack, grandfather Edgar, his brother Norm and great-grandfather Alfred all operated woodcutting, sawmilling and dairy farming operations in the Brunswick Heads region of northern NSW. “I can still recall the old Cletrac 22 tractor that they used to snig the logs to the mill with,” he said.
John was driving machinery well below the legal age and can recall as a 10- or 12-year old working to the mettle on some Saturdays and Sundays. “Bill Simpson, who was a tip truck driver that subcontracted to Dad, would pick me up at 4:00am in the morning, take me out to a farm pit where I would push material all day. There was no need to go to a gym in those days,” he joked. “The stick shift machines and the steering sticks weren’t power assist!”
Today John still enjoys getting on the equipment when business pressures permit. “I call it ‘mechanical therapy’,” he said.
John tried to point his son Luke in a different career direction. “I gave him a ballpoint pen and said: ‘That’s worth $1.50 and it will earn you as much as that excavator over there’,” John said.
However, Luke, with a bachelor degree of civil engineering, went onto work in the extractive industry. After two years with a multinational company, he returned to the family business and enjoys his machine time.
“We’re mirror reverse,” John said of his son. “He’s an engineer who enjoys time operating and I’m an operator performing an engineer’s job.” •
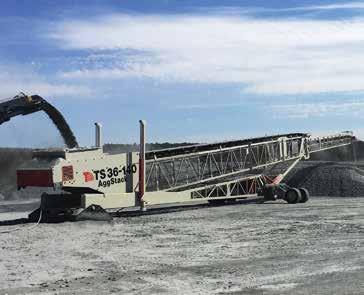
POA
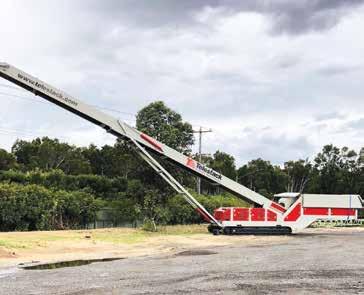
TELESTACK HF-520 HOPPER FEEDER – 800TPH POA
TELESTACK TC-424X 24M STACKER – 400TPH

POA
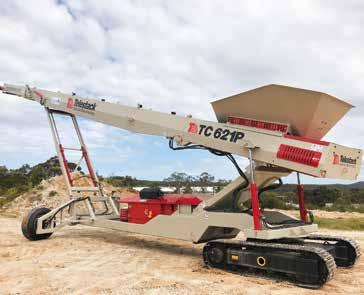
TELESTACK TC-621R RADIAL STACKER – 600TPH POA
Call: Rob: 0488 288 056 Paul: 0488 012 384 Michael: 0417 281 795 Email: info@triconequipment.com.au Visit: www.triconequipment.com.au
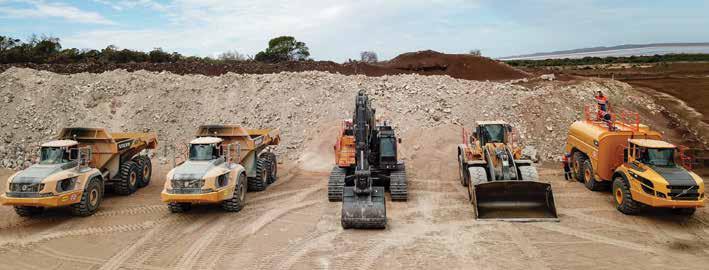
GARNET PRODUCER STAYS TRUE TO ROOTS WITH EXCAVATOR PURCHASE
GMA Garnet Group (GMA) mines, processes, exports and distributes the highest quality garnet globally. Established more than 35 years ago, GMA is now the world’s largest and most advanced garnet mining and processing operation, supplying garnet abrasive to the waterjet cutting and protective coating industries. Garnets are a group of silicate minerals used as gemstones and abrasives. Mined garnet comes in many forms and is utilised for abrasives, cutting and filters. In Western Australia, garnet is a mineral sand and is considered one of the optimum products in the world for industrial applications such as waterjet cutting and sand blasting.
Operating in the midwest region of Australia, GMA was established in the 1980s when it started exploration along a small stretch of coastline in the town of Port Gregory where geologists found small garnet deposits. In 1983 GMA established a dry processing plant in Geraldton, a significant milestone for its operation, where it is still located today. The garnet-bearing sands in Western Australia have a unique geological history of erosion and disposition, resulting in them comprising the highest quality garnet available anywhere. GMA took delivery of its first Volvo machine in 1989 and, more than 30 years on, is still running a fleet of Volvo earthmoving vehicles. Indeed, as the very first business to purchase the Volvo L350F wheel loader in Australia, GMA Garnet is now the first Australian company to own Volvo’s largest excavator – the EC950E.
With a knockout bucket breakout force of 478kN (ISO 6015) and an arm tearout force of 420kN (ISO 6015), the 90-tonne EC950E is considered groundbreaking for its class, offering an enhanced digging force when working with hard and heavy materials. As well as a higher digging force, the crawler excavator offers quick cycle times thanks to an enhanced hydraulics system which increases pump power for a fast and smooth
GMA’s EC950E excavator feeds an A60H articulated hauler at the company’s Geraldton operation.
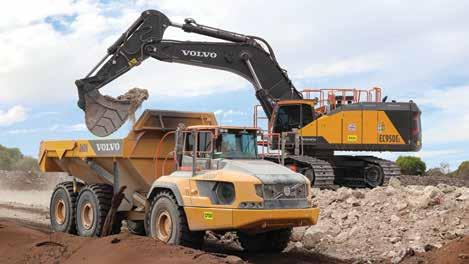
operation. The EC950E is built with protected components, including a heavy-duty boom and arm, and a strong frame structure, and can be relied on for longevity and sustained uptime in demanding applications. It is equipped with a wide track gauge, long track length, retractable undercarriage, and an optimised counterweight that makes it adaptable to challenging environments.
GMA employs a variety of Volvo machines at its operations north of Geraldton. It has A45G and A60H articulated haulers for carting ore from various pits to plant and backloading of waste from plant to pit. The GMA team is convinced the addition of the A60H, Volvo’s largest hauler, has increased productivity due to the extra payload. They also operate Volvo L350H wheel loaders in the processing plant to load ore into hoppers and tailings onto trucks, while its excavators are used on the front line, getting product out of the ground and into the trucks.
To meet the requirement of moving upwards of 10,000 tonnes of materials per day, the ability to maximise operator productivity is essential. GMA’s operators have shared their appreciation of the ergonomic layout of the instruments and controls in the Volvo machines, making for better comfort and reduced fatigue. The new EC950E features a spacious cab, offering a low noise environment and more comfort.
GMA focuses on strong partnerships and an unwavering dedication to its customers. Much like CJD Equipment and Volvo Construction Equipment, the company’s values comprise trust, teamwork and care for people and the environment. These collaborative values, coupled with strong aftermarket service and quality, have built such an enduring relationship between GMA and CJD Equipment over the past 30 years.
The GMA Garnet Group has always led the way in the innovation and development of new products for the global abrasive blasting and waterjet cutting industries. With such an innovative outlook, it is no surprise GMA was the first to acquire the EC950E heavy-duty excavator. •
HEAVYWEIGHT LEADS ‘FORMIDABLE’ EXCAVATOR RANGE
Volvo Construction Equipment’s EC950E crawler excavator may be considered the “Muhammad Ali” of its heavyweight division but it is not the only quarry-spec machine available to producers.
Volvo CE’s line-up also comprises: • The one with the small bum. With powerful, fuel-efficient Volvo engines, a perfectly matched hydraulic system and a robust body, the short-swing radius excavators offer productivity, stability, ease of use and safety in confined or restricted working conditions. Available in both compact (from 1.8 to eight tonnes) and general purpose (from 14 to 30 tonnes) getting around site on these versatile machines is assisted by automatic two-speed travel for optimised traction plus hydraulic travel pedals for easy and accurate track control. • The one with a ‘higher’ purpose. To provide the most versatile machine possible on demolition job sites, the EC480EHR is 28 metres high. It is purpose-built to suit the needs of heavyduty demolition with both high reach/ medium reach and digging capabilities combined as one. It also features a patented modular boom system, which includes an innovative hydraulic modular joint with hydraulic lock mechanism to release digging equipment and change from the high reach demolition boom to a medium reach configuration in a simple and swift operation. • The heavyweight one. With a knockout bucket breakout force of 478kN (ISO 6015) and an arm tearout force of 420kN (ISO 6015), the 90-tonne class EC950E offers enhanced digging force, particularly when working with hard and heavy materials. Constant high
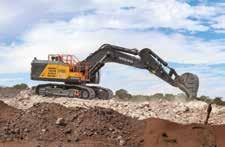
hydraulic pressure delivers power to the machine when needed. Built with protected components, including a heavy-duty boom and arm, and a strong frame structure, the EC950E is reliable for longevity and sustained uptime in demanding applications. Founded in 1974, CJD Equipment is a privately owned Australian company and provider of world-class plant and equipment. Partnering with international manufacturers, CJD offers a diverse range of products from reputed brands, including Volvo CE, SDLG and Kenworth and DAF trucks. CJD has partnered with Volvo CE for more than 25 years, supplying Australia’s construction and earthmoving industries with high quality products, along with national after-market service and support.
CJD’s dealer network encompasses capital cities and regional centres, providing 24/7 sales, parts and service support from more than 500 highly experienced staff. •
Source: CJD Equipment
!REYOUGETTINGUNBIASED SCREENINGADVICE
7EWONTDIRECTYOUTOWARDSANYPARTICULAR PRODUCT,OCKEROFFERTHECOMPLETERANGE
7EWANTTOPROVIDETHEBESTSCREENFORYOU
s 7IRE s 2IPPLEAND0OLYRIPPLE s 2UBBER s 0OLYURETHANE s 4UFFLEX s -ODULAROR4ENSIONED3CREENS
1/2 PAGE HORIZONTAL ADVERTISEMENT
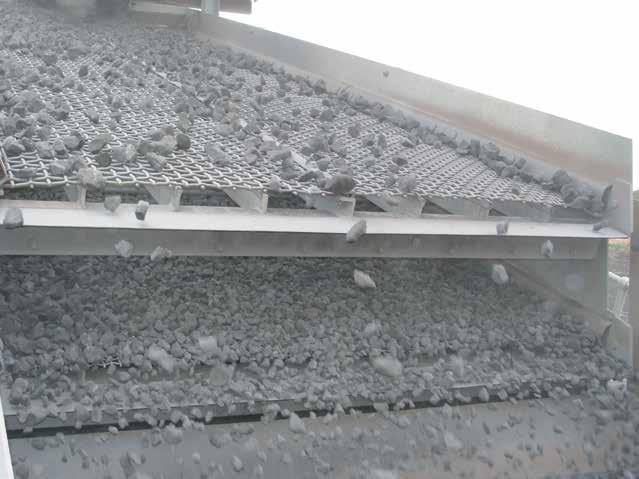
PAGE 33
#ONTACTYOURLOCALSCREENINGEXPERT
EARTHWORKS PROGRAMS PROVIDE ACCURATE GRADES, CONTROL
On opposite sides of the Tasman Sea, a digital product suite is proving invaluable for two construction companies utilising excavators on a range of projects.
United Civil Construction was established more than 40 years ago in New Zealand with the formation of United Carriers Group. When the group separated its construction operation in mid-2006, United Civil was formed. The civil construction company has more than 120 trained and experienced staff who have worked on projects from Auckland up to Cape Reinga, at the northern end of the North Island. With a focus on benefitting its people and the communities in which it serves, United Civil puts health and safety at the core of its operations. It is also committed to building all of its projects in a sustainable manner that does not harm the environment.
With its surveying technology not delivering the desired effect, United Civil sought change. The management team knew technology played a key role in expansion and that as a high growth company, data could be an underused resource in the construction industry. As such, the team began searching for a technology partner that would provide robust, highly useable machines and high quality data that could be used throughout its projects.
After a competitive evaluation process with three leading brands, Mark Daglish, the survey manager at United Civil, said: “We selected Trimble as our technology partner due to its ease of use and the overall quality of the product suite. Trimble also stands out for its commitment to innovation and safety which aligns our two organisations.”
United Civil has deployed the Trimble Earthworks Grade Control Platform (Earthworks) on one of its Hitachi excavators, alongside the Trimble Business Center office software.
Earthworks is the industry’s first integrated 3D aftermarket grade control system with excavator automatics capabilities. The platform includes intuitive, easy to learn software that is extremely customisable and allows each operator to personalise the interface to maximise productivity. Trimble
United Civil has deployed Earthworks on its Hitachi 225US LC excavator.
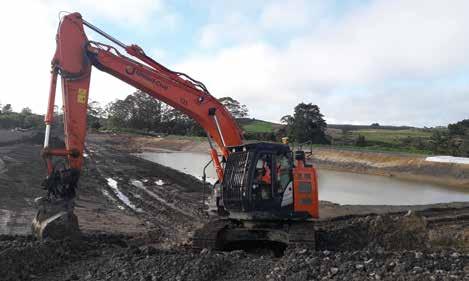
United Civil’s excavator is fitted with the roof-mounted Earthworks platform.
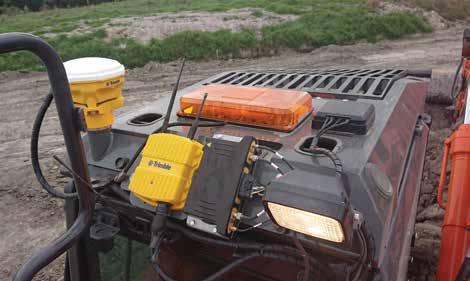
Business Center is an office software tool that can create accurate, integrated 3D constructible models for survey, construction and marine applications.
Together, these solutions enabled United Civil to optimise its decision-making and efficiency in the office and on the job site. The implementation was simple, with little training needed thanks to the familiar interface present across Trimble’s solutions. Daglish said: “The excavator component was easy to get started – it was up and running immediately that day. Sitech NZ was a phenomenal partner too, supplying the team with guidance on
the machines and educating them on how technology will truly make a difference to their work day.”
United Civil reaped several benefits from its deployment of the Trimble packages, including: • Improved health and safety. With a 3D view of the project and grade progress inside the cab, the operator doesn’t have to rely on stakes or a grade checker to dig to correct depths. Daglish said: “It’s going to save survey time and increase the safety of the team working on the site, particularly in the trenches.” • Better data sharing. Users can remotely send and share data across machines. “Trimble is automatically recording data and feeding it back to the site team,” Daglish said. “In addition, it’s able to connect and download updated designs from management which saves us a huge amount of time and reduces human error.” • Faster and more efficient data. With all the data in front of personnel on the machines they work, tasks could be completed in record time. “We’ve doubled productivity thanks to Trimble. We have total confidence with the client that the job will be done to the design, with fewer errors than ever before,” said Daglish. • Better equipment utilisation. United Civil was impressed at the high levels of technology uptake by the team. “The operators have been very impressed with how user-friendly Trimble’s technology is,” Daglish said. “We have a diverse team. Trimble is easy to use, and the benefits of the technology are clear, meaning that driving uptake internally is easy. This is good news for everyone.” Daglish said United Civil’s commitment to the Trimble programs was ongoing. “Our goal is to have a continual investment in the technology that will help us stay ahead of the competition in both price and performance. We are currently planning for additional installations on a grader and excavator along with multiple field GPS units for site engineers. With Trimble this allows us to hit the ground running, making it easy for our staff to adapt and see results.”
JOBSITE TRANSFORMATION The construction industry is known for its slow adoption of technology but southeast Queensland group Bielby Holdings has been challenging this stereotype for the past 15 years, employing technology as its number one tool to transform the jobsite.
Much of the work done with Earthworks at Beilby was entrusted to its Caterpillar 313F excavator.
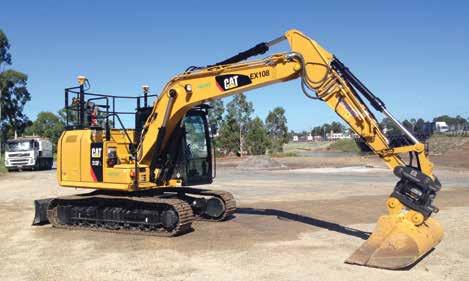
Shannon Watson at the helm of the 313F excavator.
Bielby was established in the 1980s and has successfully delivered more than 150 major transport, earthworks and infrastructure projects along the eastern seaboard of Australia. The organisation has been using Trimble machine control for more than a decade – making the technology mission critical to its operations.
Trimble’s technology was originally deployed by Bielby for a grading project that involved replacing pavement without stopping nearby traffic – the team did not want to use traditional string lines for this job, due to safety reasons. Following the project, the team found it had increased productivity, tightened tolerances and had virtually no reworking. Since then, Trimble’s technology has been used across numerous Bielby jobs as the team realised and enjoyed the enormous advantages gained. After continued use and investment over the years, Bielby now operates no-peg sites, relying on Trimble solutions for accurate grading and control.
In addition, Bielby started using the Earthworks grade control platform and it is now the standard for all Bielby’s projects, providing improved safety, productivity and accuracy.
Much of the work done with Earthworks was entrusted to Shannon Watson and the organisation’s Caterpillar 313F excavator. This was Watson’s first time using machine control
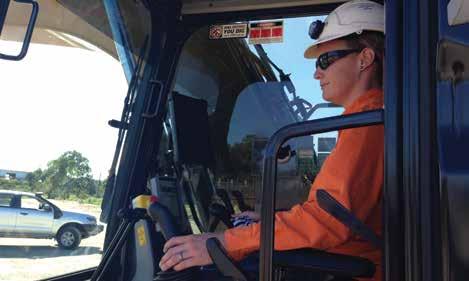
technology after more than a decade spent in the mining and construction industry.
“I love it,” Watson said. “It is mind blowing what you can do with Earthworks. It is making the job easier, as we are able to be more precise and efficient. In addition, it’s also engaging me as an operator.”
Watson explained the simplicity of the Earthworks software, suggesting it is as easy to use as a smartphone. Earthworks has been built on the Android operating system for a positive user experience.
While Watson has spent more than a decade in the industry, she has been an excavator operator for under three years. She said using Earthworks had helped her with the visualisation of jobs. “I’ve found that when I’ve worked on something with Earthworks, if I then jump into the smaller excavator without it, I can ‘see’ the job in my head really clearly and that makes it easier to achieve,” she said.
Sitech Construction Systems worked with Bielby from the beginning.
“Bielby Holdings was an early adopter of Trimble machine control technology and has continued to upgrade and utilise our technology to be a highly competitive and efficient business,” Sitech’s Brent Daniels said. “We’re proud to have helped this company continue to grow and succeed.” •
HEAVY-DUTY HANDLER BOOSTS PRODUCTION IN REHANDLING TASKS
The Caterpillar 990K aggregate handler is designed to handle greater payloads in aggregates yard applications. With as much as a 25 per cent payload increase compared to the standard 990K wheel loader, the handler enables customers to load trucks faster and to move more material in load and haul and stockpile handling tasks.
The 990K has a payload of 20 tonnes and a full turn static tipping load of nearly 44 tonnes. The additional counterweight maintains machine stability, and the robust 990K structure ensures durability in the aggregate handler configuration. The loader makes best use of general purpose and coal buckets for increased volume.
The aggregate handler is available in standard lift configuration with a 4.1m dump clearance, and in high lift configuration with 4.6m dump clearance. The increased capacity and high dump clearance enable customers to load large trucks with a better pass match for faster material handling at lower cost per tonne.
The 990K complements the smaller 986K and 988K aggregate handlers in the Caterpillar large wheel loader line. The aggregate handler, however, is not designed for use in
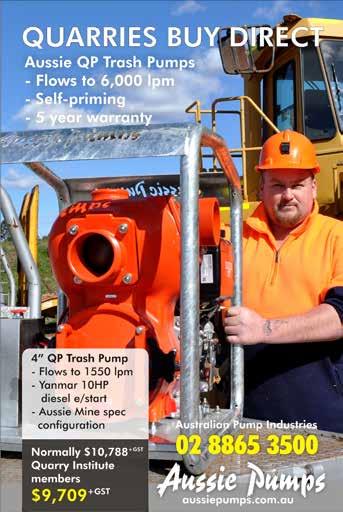
quarry face or other shot rock applications.
The 990K aggregate handler is built on the proven features of the 990K wheel loader. The 990K powertrain offers plenty of “grunt”, with improved fuel efficiency. The Cat C27 engine powers the loader and delivers net power of 521kW. A lower engine speed helps drive economical fuel use. Additional fuel savings can be accrued with the ECO mode (on-demand throttle), engine-idle shutdown system, and engine-idle kickdown/auto-resume system. The Cat exclusive, fieldproven impeller clutch torque converter uses a lock-up clutch, providing direct drive to boost fuel economy, trim cycle times, and reduce heat — especially in load and haul applications. The system allows operators to balance rimpull and hydraulic power for optimum loading efficiency. The positive flow control implement hydraulics use a variable displacement, electronically-controlled pump to precisely apportion oil flow based on operator control inputs.There are a number of drivetrain options available. The integrated axle cooling and ride control options are particularly beneficial in load and haul work.
The operator station features Cat’s Vital Information Management System (VIMS 3G), which provides customisable operator profiles, a cycle timer and an integral payload control system, which provides “on the go” payload weighing. The graphical information display is easy to use and keeps key information in front of the operator. The Cat Comfort III seat provides integrated seat-mounted controls for smooth, comfortable operation. Transmission controls, integral with the STIC steering lever, allow convenient travel control.
The 990K is equipped with the Cat Vision rear-view camera system and an in-cab display to show the operator the area behind the loader. The Cat Detect object detection system, available as an option, builds on the camera system with radars and in-cab software that provide notification to the operator when an object is detected within the radar coverage area. The systems are designed to enhance operator awareness, especially in congested loading areas. •
Source: Caterpillar of Australia
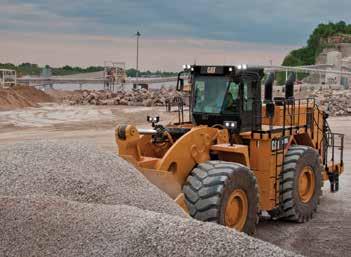