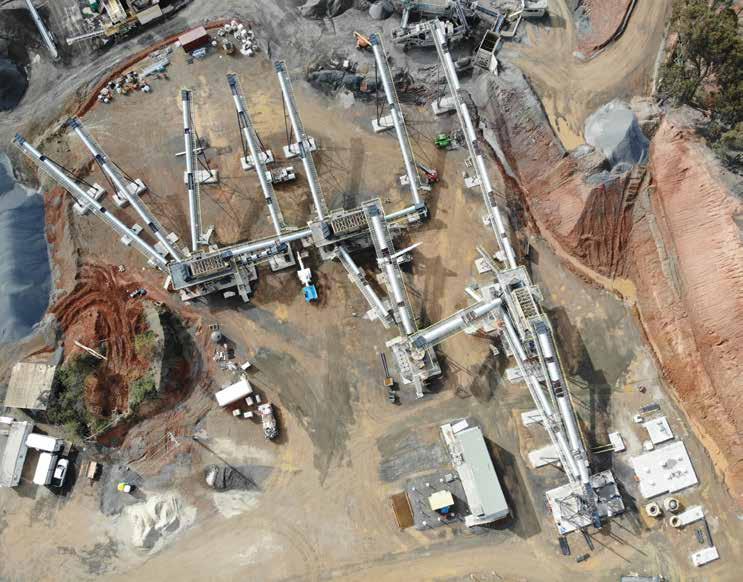
33 minute read
MODERN CRUSHING PLANT BOOSTS OUTPUT A family-owned producer is set to double its capacity with an advanced fixed crushing plant
from Quarry Sep 2019
by Prime Group
MODERN PLANT BOOSTS OUTPUT FOR RURAL FAMILY BUSINESS
A second generation aggregate producer is set to double its production capacity with the opening of a $15 million advanced fixed crushing and screening plant in Victoria’s Benalla region. Myles Hume reports.
Lima South Quarry is a second generation Victorian business, located 200km northeast of Melbourne. Its success rests largely on the extraction, crushing and screening of its in-demand hornfels blue metal aggregates, and the supply of railway ballast in the region.
The quarry first commenced commercial operation in 1998 under the ownership of Geoff and Coral Day. Their son Ashley purchased it from them in 2008 and has since overseen a significant transformation of the operation, including two extensions, taking the total extractive area to 12ha today.
Under his direction, Ashley Day has also expanded the Lima South workforce from a few men to 64 employees, seeing the operation’s annual output increase by 2500 per cent in the past eight years. A third extension application is awaiting imminent approval that would double the quarry’s footprint and extend its life for another century, based on forecasted sales.
Lima South Quarry boasts its own 10-truck transport fleet that is supplemented by about 20 sub-contract drivers who transport Lima South rock as far afield as Melbourne (200km), Mildura (540km), and Albury (150km). In keeping with the quarry’s aim to remain self-sufficient and efficient, Day has also established a NATA-accredited laboratory to test grade specifications on-site, eliminating delays associated with external testing services.
According to the company’s sales and account manager Brendan Tipple, Lima South’s flagship product is its highly sought after hornfels blue metal aggregates, which are predominantly used for asphalt, spray sealing, railway ballast and now concrete applications.
The aggregate is said to have superior properties, including a polished stone value of 60-61 for higher skid resistance, and a Los Angeles abrasion value of eight to 10. The product is only one per cent absorbent, soaking up less bitumen, binders and cement than basalt or other aggregates.
PRE-CAST PRODUCTS In addition to its annual spray sealing contracts, Lima South’s extensive list of projects include the supply of more than 200,000 tonnes of 63mm railway ballast for the Sydney to Melbourne Ballast Rehabilitation Program, as well as the recent provision of specialty leachate aggregates for construction of a new landfill cell for the local authority Benalla Rural City.
Most notably, however, Tipple said the
company has been supplying Downer EDI’s asphalt plants in the region. In recent months it also has begun supplying its products to LS Precast, a related company of Lima South, located 35km north in Benalla.
Established last year, LS Precast employs more than 300 people to produce precast elements. It has secured a major contract with the Victorian Government’s $6.7 billion West Gate Tunnel project, slated for completion by the end of 2022.
“So, in effect, the aggregates from here in Lima South will be in the concrete precast panels for the West Gate tunnel, bridges and overhead roads, as well as all of the precast beams,” Tipple said. “We’ve been supplying LS Precast for the past six months or so and it is beginning to ramp up.”
Concurrently, Lima South is pursuing a contract to provide about 300,000 tonnes of railway ballast for the Australian Government’s $235 million North East Rail Line upgrade, which will see improvements to the entire rail line from Melbourne to Albury/ Wodonga.
As such, this ever-increasing demand for Lima South products has been the catalyst for change.
ADVANCED REPLACEMENT PLANT Until now, the company had relied on significant track-mounted mobile aggregate plant. From this month (September), Lima South Quarry is set to undergo a significant operational transformation as it switches over to a new $15 million fixed crushing plant, which has been installed over two stages this year.
Astec Australia and Nepean Conveyors Roxon Australia, under a unique value based partnering arrangement, have collaborated to design, supply, deliver, install and commission the new fixed plant complete. The turnkey scope of supply has included all structural, mechanical and electrical components for 20 fixed conveyors, as well as the structural steelwork for the crushers, feeders and screening equipment.
For Astec Australia, it is to date the largest supply of the manufacturer’s equipment in an Australian aggregate plant and showcases its range of products.
The resulting plant will double the quarry’s production capabilities, and free up the existing mobile aggregate plant for contract work that can produce between 30,000 and 40,000 tonnes per month.
Initially the plant will produce 7mm, 10mm, 14mm and 20mm aggregates, and ballast,
38 Quarry September 2019 The secondary stage of the modern fixed plant comprises an Astec 8243-38LP horizontal screen (top, against the quarry face) and a Kodiak K400+ cone crusher (bottom right).

The circuit comprises nearly a dozen conveyors, including Roxon HC100 bulk material belts.
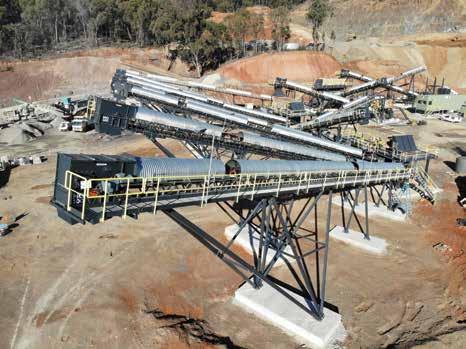
with stage two expected to deliver further varieties of crushed rock.
The new operation, which runs off mains electricity, will considerably reduce the quarry’s diesel consumption, and will be easier to operate than the original mobile plant.
The plant’s key features include two Astec 7.3m x 2.4m (24’ x 8’) 8243-38LP horizontal screens, the first two screens of this size sold outside of the US, and a 1250mm x 3000mm (49” x 118”) Obex pan feeder. The quarry has also invested in a 4500EVTA VSI comprising twin 223kW motors, also the largest and most powerful vertical shaft impactor that Astec has supplied in Australia. Other components include a 15m x 6m (50’ x 20’) primary feeder, secondary and tertiary Kodiak K400+ cone crushers and a third horizontal screen, which is an 8203-38LP model.
Day said that “the quality of the plant, the attention to detail and level of project management and customer engagement was beyond our expectations”.
Astec Australia’s national account manager Adam Gordon said an Astec 90-tonne, tracked-mounted jaw crusher – which had been previously supplied to the quarry – has been relocated to the pit where it will now conduct in-pit primary crushing, before the material is loaded on to dump trucks and driven 300m to 400m to the new plant. On arrival, he said the rock is tipped into the dump hopper and brake control-fed into the plant. The material passes through a secondary crusher before being processed on the first of the 8243-38LP horizontal screens.
From the screen, oversized material then heads for further reduction to the tertiary 298kW cone crusher, which operates in closed circuit with the second 8243-38LP
screen. Sized products are sent into various directions for further processing or sent directly to product stockpiles.
“For further processing Lima South Quarry has gone a step further and introduced the 447kW VSI and that works in closed circuit with a secondary screen,” Gordon said.
“Any surplus material, whether it be 14mm or 20mm aggregate or whatever, they can selectively and proportionately return it to the VSI for further reduction, which means the plant has the flexibility to make what they need to sell and is effectively made ready to order.”
COMPREHENSIVE PARTNERSHIP This approach, Gordon said, means if the plant generates throughput of 5000 tonnes on any given day, then almost 5000 tonnes of usable material will leave the gate the next day. “This reduces the presence of surplus stockpiles, which incrementally increase in size, and it also minimises their dead stock,” he said.
The phase one installation of the Astec fixed
The two Astec 8243-38LP screens are the first of their size to be installed outside of the US. A 8203-38LP horizontal screen rounds out the circuit.
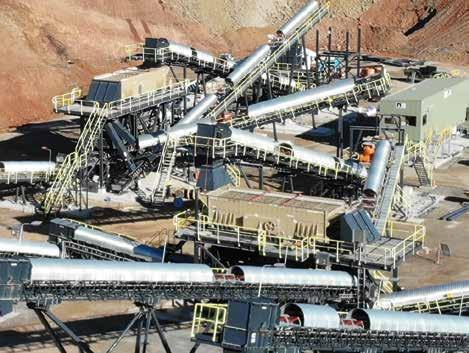
plant at Lima South Quarry is the culmination of a collaborative and comprehensive process between the equipment manufacturers and the quarry operator. In the coming years, as the quarry develops and extends, Gordon said Lima South planned to eliminate the need for dump trucks and had factored in the capability of extending the conveyor circuit closer to the pit. Gordon said he had worked closely with Day, which involved visits to quarries in Tasmania, New South Wales and study trips to the US. He said Lima South had taken the components of other best practice operations and adapted them to suit its own requirements, which had resulted in an advanced version of the typical Australian crushing plant. •
HEINEHARD
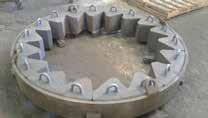
Wear parts for impactors, jaws & cones. Modified designs for longer wear life. Tailored chemistry and heat treatment for extra wear life. Buy back for credit on chrome iron scrap. Australian made AS3901/ISO9001.


The John Heine foundry in Sydney casts white irons and manganese steels wear parts for the mining and quarrying industries. These Australian made parts can be tailored to your requirements by designing extra pads of material in high wear areas. We have a selection of developed proprietary grades of chrome iron alloys to suit your particular application and improve wear life. As part of our service, we offer a buy back scheme for credit on your worn white iron components, as we can melt down and re-cycle into new parts. We stock a large range of castings such as hammers, anvils, impact plates and blow bars now including chrome, martensitic steel and manganese ceramic alloys. Our range can cover Canica, Kleemann, Nordberg, RubbleMaster, Jacques, Trio, Sandvik, Cedarapids, Extec, Hazemag, Pegson, Striker and Teesab. We also manufacture chute protection liner castings and a range of pug mill and Fisher Air Separator parts. We import a range of jaws, mantles and concaves for many brands of machines.
WHY NOT CALL RAY BOGG ON 0458 111 503 AND START SAVING NOW?
John Heine & Son Pty Ltd 273 Edgar Street Condell Park 2200 Phone 02 9772 5000 sales@johnheine.com.au • www.johnheine.com.au “Molten Engineering”
HEALTH, SAFETY BREACHES IN THE WORKPLACE ARE NEVER ‘TRIVIAL’ MATTERS
It might at the time seem like a ‘bit of fun’ but two recent workplace incidents highlight why employers and employees – especially in the extractive industry – should be mindful about safety. Shane Koelmeyer outlines the circumstances and why the employees were judged to be at fault.
According to the Fair Work Commission’s (FWC) most recent annual report, unfair dismissal applications are by far the most common type of application lodged with the FWC. In the 2017-18 reporting period, more than 13,000 unfair dismissal applications were lodged by employees across Australia.
Clearly, unfair dismissal continues to be one of the main areas of dispute between employers and employees.
The Fair Work Act 2009 (Cth) sets out the matters that must be considered by the FWC when determining whether a dismissal was in fact unfair. One of the most important matters for consideration is whether there was a “valid reason” for the employee’s dismissal.
Over the years, case law has established that a valid reason must be sound, defensible and well founded, and should not be capricious, fanciful, spiteful or prejudiced. It is often on this question of whether there was a valid reason for dismissal that employers and employees clash. Employers may view an employee’s conduct, performance or safety breaches as extremely serious but the employee views those same things as minor infractions not warranting attention, let alone the kind that results in loss of employment.
A ‘COOL AS HELL’ PHOTO Two recent cases from the FWC highlight this kind of discrepancy in the characterisation of events.
An employee at a mine site was dismissed
An example of some booster charges – not recommended for ‘show and tell’ indoors.
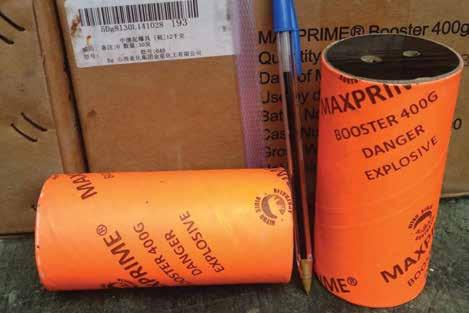
after he posed for a photo standing on top of a piece of heavy machinery that was parked, but still running. In the photo (that was posted on Facebook) the employee was pictured standing on the machine with one foot on top of the cab while holding a large metal roof bolt in his right hand.
The employer considered the employee’s actions a serious breach of its safety policies and rules, as well as conduct that was capable of causing harm to the employer’s reputation and business.
Upon discovering the photo, the employer informed the employee of the seriousness with which it was treating his conduct and asked him to show cause as to why his employment should not be terminated.
The employee responded with a somewhat sarcastic email in which he said he posed for the photo because he thought “it’d just look cool as hell”.
The employer subsequently terminated his employment.
In determining the employee’s unfair dismissal claim, the FWC considered all the relevant policies and procedures of the
employer related to safety, including those concerning the isolation of machinery. The FWC also considered recent developments at the mine site where the main operator of the site had contacted the employer about a spate of injuries, insisting that the employer do more to prevent safety incidents.
The FWC found the employer had a range of safety policies, rules and procedures in place and the employee had been trained appropriately in these. On this basis, he should have known that climbing on top of a piece of heavy machinery that was still running was a breach of the employer’s safety policies, procedures and rules.
Further, the FWC accepted there were valid reasons for dismissal, in that the employee’s actions were not only risky in terms of safety, but also risked the employer’s reputation and business interests because one of its biggest partners had recently warned it about its safety record.
At the hearing of the matter, the employee accepted that his conduct was out of line and was a silly thing to do, but he did not accept that he could have fallen off the machine or that his conduct amounted to a breach of the employer’s policies or procedures. The FWC commented: “These refusals, together with the contents of his response to the ‘show cause’ request demonstrate [the employee’s] lack of genuine remorse and acceptance of accountability for his conduct.”
The FWC found there was nothing unfair about the employee’s termination and his application was dismissed.
DISMISSAL AT 20 PACES Everyone has different hobbies, activities or interests they want to share with their friends and colleagues at work. However, not all interests are appropriate for the workplace. In Rodger v ACT Government – Transport Canberra and City Services T/A ACTION [2018] FWC 6970, the FWC held that an employee’s conduct in bringing ornamental duelling pistols and inert booster charges in to work to show his colleagues created a risk to safety and constituted misconduct.
In June 2017 the employee’s service was terminated after an investigation by his employer found that in January 2017 he brought two explosive booster charges to work and, on a previous occasion, had brought two duelling pistols to work.
The employee lodged an unfair dismissal application submitting that his dismissal was unfair given his unblemished 17-year work record, and that his
A matched pair of engraved, gilded muzzle-loading percussion-lock duelling pistols from the Philadelphia Museum of Art. Again, not an ideal exhibit for workplace engagement!

misconduct did not warrant dismissal.
The employer argued there was a valid reason for dismissal as the employee’s conduct in bringing the items to work created a health and safety risk to employees and others in the workplace. The employer submitted that the employee’s behaviour constituted misconduct under the applicable enterprise agreement and had the potential to bring the employer into disrepute.
While the employee agreed that he brought the items into work to show his colleagues, he argued the items were not active and as such were not a genuine risk to health and safety. The employee said he explained to his colleagues that the items were not active and at no time did his colleagues raise any concern about a risk to their health and safety. The employee also submitted that he brought the booster charges into work to make an effort to talk to his colleagues. Although it was in dispute whether the items were operational or not, the FWC was satisfied that by bringing the booster charges and duelling pistols in to work the employee nevertheless created a risk to health and safety. The deputy president remarked that:
While it is clear from their statements that none of the employees who saw the charges/guns felt intimidated or concerned about them being in the workplace, this is in my view due to good fortune rather than the absence of any risk to safety. Other employees may have reacted very differently in the circumstances and may have legitimately been fearful for their safety.
The FWC also found that the employee’s conduct in bringing the items into work had the potential to bring the employer into disrepute. For the FWC, it was irrelevant whether the items were operational or not, as the employee had no legitimate reason to bring them into work.
Accordingly, it was held that the employee’s behaviour was misconduct, which was a valid reason for the termination of his employment. The FWC dismissed the employee’s submissions that the dismissal was unfair given his unblemished record, noting his misconduct outweighed this consideration. The FWC found the dismissal was not harsh, unjust or unreasonable and rejected the unfair dismissal application.
LESSONS FOR EMPLOYERS Employers have obligations to ensure the health and safety of all employees. This obligation requires employers to minimise or eliminate both physical and psychological risks to health and safety. This duty was recognised by the FWC in this matter where it was agreed that the employee created a risk to health and safety by bringing the booster charges and firearms into work – or, in the first case, by posing on a piece of running machinery.
Employers are entitled to expect high standards of conduct from their employees. This includes expecting that employees will not act in a manner that negatively impacts on the reputation of the employer. Where an employee engages in inappropriate conduct, an employer is within its rights to treat that conduct as serious in nature, even if the employee considers it trivial or not their fault.
These cases demonstrate that, even if an employee doesn’t think their conduct is grave enough to warrant dismissal, the FWC will treat serious matters seriously and valid reasons as valid, despite an employee’s characterisation to the contrary. •
2019 IQA EVENTS2019 IQA EVENTS
ACT BRANCH 15 Nov Dinner meeting
NSW BRANCH 23 Oct Sixth Annual Quarries and Concrete Seminar
NSW ILLAWARRA SUB-BRANCH 30 Nov Races day/Christmas function (Venue TBA)
QUEENSLAND BRANCH 24 Sept Breakfast meeting, Brisbane 15 Nov Lunch meeting, Brisbane
NORTH QUEENSLAND BRANCH 13 Sept Annual golf day, Townsville 8 Oct Technical and dinner meeting, Townsville 30 Oct Technical and dinner meeting, Cairns 15 Nov Christmas Party, Townsville
SOUTH AUSTRALIAN BRANCH 8 Nov Dinner meeting, Adelaide
VICTORIAN SUB-BRANCH 12 Sept Dinner meeting, Ballarat 21 Nov Dinner meeting, Bendigo
CENTRAL QUEENSLAND SUB-BRANCH 23 Oct Safety and Health Seminar, Rockhampton
WESTERN AUSTRALIAN BRANCH 3 Sept AGM and dinner meeting, Imperial Court Restaurant 22 Nov Annual golf day, Joondalup Resort
All dates and venues for the above branches are correct at time of press. Not all branches had confirmed their activities/ dates. For further information about IQA branch activities, contact your local branch representative (see IQA branch contacts on page 47) or visit quarry.com.au
PDP WORKSHOPS & EVENTS
To register for the courses below and for further information, visit: quarry.com.au/Education/ProfessionalDevelopmentProgramsCalendar.aspx

IQA 62ND ANNUAL CONFERENCE Geelong Football Club, Kardinia Park Geelong, Victoria 1-3 October (Tuesday to Thursday), 2019
“The Future of Quarrying” will be the theme of the IQA’s annual conference at the home of the Geelong Cats AFL Football Club. The conference program will focus on numerous topics, including: the maximisation of limited natural resources through technology; the benefits of effective management of workplace diversity; new developments in emerging fixed and mobile plant technology; environmental and economic trends impacting on the industry; and much more. In a first, the conference program will be hosted on a Tuesday, Wednesday and Thursday. For more information, visit conference.quarry.com.au
EFFECTIVE RISK MANAGEMENT WPDP 2 September, 2019
The IQA and the quarrying industry at large recognise the importance of managing safety risks. Effective risk management processes are vital in realising significant gains in safety performance. This webinar will assist operators in ensuring their risk management processes are effective. It will consider why such processes fail, identify risk profiles, provide advice on effective risk management processes and cover some incident investigations. Participants will be given practical examples of how small-scale quarries have achieved significant safety improvement through managing risk. The webinar is recommended for managers, supervisors and key support personnel.
HAZARD AND RISK IDENTIFICATION PRINCIPLES WPDP 9 September, 2019
Hazard and risk source identification are key steps in risk management. This webinar will outline definitions and interpretations, benefits of comprehensive hazard and risk source identification, potential consequences of inadequate hazard and risk source identification, common hazard and risk source identification methodologies, and an introduction to alternate hazard and risk source identification methodologies.
IQM CONEX 2019 Palm Garden Hotel Malaysia 15-16 October, 2019
The theme of the Institute of Quarrying Malaysia’s (IQM) annual conference and exhibition is “Innovative Quarrying Technology – Industry 4.0”. It recognises the quantum leap into the era of Industry 4.0 (cyber-physical systems) will require the quarrying industry worldwide to stay competitive and evolve quickly through cutting-edge knowledge, skills and innovative practices. The role of Industry 4.0 in quarrying will be explored and discussed across a range of presentations, including smart equipment manufacturing, the latest trends in rock fragmentation/blasting, smart and autonomous features in transportation, and cyber-security risks and safety precautions in data management. For more information, contact the IQM secretariat, tel 60 3 8062 4194, mobile 60 12 219 7519, email nirmala@iqm.com.my or visit iqm.com.my/news&events.htm
The Institute of Quarrying Australia
FROM THE CEO
SAFETY RESET TO SHARPEN ATTENTION ON WORKERS’ HEALTH, SAFETY
The Queensland Department of Natural Resources, Mines & Energy (DNRME) recently initiated a “safety reset” from the end of August for all mines and quarries across the state. The IQA fully supports the safety reset initiative and encourages all members to review their risk management procedures. For more information about the Queensland safety reset, visit the DNRME website: dnrme.qld.gov.au/miningresources/initiatives/safety-reset
The safety reset is a crucial first step in refocusing the industry’s attention on what should be everyone’s number one priority – the health and safety of workers. This is a timely reminder of the importance of safety and the IQA can support sites with training required on a broad range of topics to improve safety outcomes. Any sites needing to update aspects of training for their staff from accredited courses to areas such as slope stability, electrical awareness or risk can contact the IQA via email: education@ quarry.com.au

With the new financial year well under way, it is important for us to keep our eyes firmly on “The Future of Quarrying” in Australia today. As such, membership to the IQA has many benefits. Primarily, Institute membership is a formal recognition of an individual’s professional achievement, development and competency. By becoming a member, career prospects may be enhanced.
In the past 12 months the IQA Board has worked diligently to execute its vision of “educating and connecting our extractive industry,” with the upcoming 12-month period to 30 June, 2019 set to deliver tailored training programs, specific to the extractive industry, that are required to attain CPD accreditations and certification on many specialist topics.
The IQA conference in Geelong, from 1 to 3 October, 2019, further focuses on “The Future of Quarrying” up to 2024, with several highly successful and experienced speakers talking to critical topics for 2020 and beyond. These include keynote speakers Robert Mellor (BIS Oxford Economics) and Sean Taylor (Komatsu Australia), whose vast experience and expertise is discussed in more detail in “The Future of Quarrying” editorial on pages 14-15. We look forward to seeing you at the IQA conference in Geelong next month. To register for the conference, visit conference.quarry.com.au
To renew your membership or join the IQA, visit quarry.com.au KYLIE FAHEY Chief Executive Officer Institute of Quarrying Australia
IQA NEW MEMBERS
GRADE NAME BRANCH Associate Amanda Love WA Associate Andrew William Troughton NSW Associate Brendan Green QLD Associate Daniel William Cleary NSW Associate Chris John Bannister NSW Associate Andrew Johnstone QLD Associate Ben Smith QLD Associate Cameron Mansell VIC Associate Emma Jayne Darling VIC Associate Michael Griffin QLD Associate Allan Walton VIC Associate Warrick Prowse NSW Associate Paul Mitchell NSW Associate David Camilleri VIC Associate Michael Willmott VIC Associate Jonathan Kristopher Milligan QLD Associate Corrie Beythien SA GRADE NAME BRANCH Associate Boris Jurak VIC Associate Colin Somerton VIC Associate Peter Addison VIC Fellow Reece Naylor NQLD Member Alison Young NSW Member David William Saville NSW Member David George Gregson QLD Member Adam Wilkinson VIC Member Andrew Hauser VIC Member Sean Lynch VIC Member Ziggy Gregory WA Member Stephen McNair VIC Member Darren Bass QLD Member Luke Tavener QLD Member Jason Barrett VIC T/Member Mark Provost QLD
IQA BRANCH CONTACTS
ACT Peter Hewson: 0429 001 476 NSW Gemma Thursfield: 0402 431 090 Northern Gemma Thursfield: 0402 431 090 Hunter Gemma Thursfield: 0402 431 090 Illawarra Dylan Treadwell: 0418 632 057 Central West Mitchell Bland: 0428 462 987 NT Darren McKenna: 08 8988 4520 QLD Jennifer Milward: 0419 782 688 Gladstone Jennifer Milward: 0419 782 688 Townsville Jennifer Milward: 0419 782 688 Cairns Chris Wilson: 0438 134 752 SA Marie Cunningham: 08 8243 2505 Tasmania Nicholas Palmer: 0418 126 253 Victoria Eli Carbone: 03 8637 4723 Vic Sub-branch Craig Staggard: 0407 509 424 WA Celia Pavri: 0417 027 928
IQA NEWS
The South Australian WIQ hosted its third annual conference at Adelaide Pavilion in July.
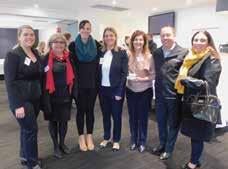
Michelle Connelly and Annie Harvey enjoy the opportunity for networking.

SOUTH AUSTRALIAN BRANCH NEWS The IQA held its third Women in Quarrying (WIQ) conference in South Australia, at the Adelaide Pavilion on 12 July. The conference attracted more than 90 delegates from a number of quarries, suppliers and the SA Department for Energy & Mining (DEM).
“The WIQ initiative promotes networking among members of the quarrying industry and encourages and creates opportunities for personal and professional development,” WIQ SA co-ordinator Sarah Bellman said. “The conference saw a number of delegates attending their first conference and welcomed attendance from diverse sectors of the industry which provided the opportunity for anyone in the industry to connect, network and share experiences.
“We are seeing through conferences like this the industry is creating new ways to encourage conversations on diversity and inclusivity. These are conversations that ultimately improve our workforce capability.” The conference had a strong focus on leadership, with keynote presentations from Alex Blood (the executive director of Mineral Resources Division, DEM), Mary Thompson (managing director of McLeod Rail) and Dayle Stevens (the general manager for technology at AGL Energy).
Delegates also had the opportunity to learn
44 Quarry September 2019 from a number of technical presentations on native vegetation, progressive rehabilitation, blasting technology and ways to reduce energy costs.
“These IQA events are important to encourage people to connect, network with industry leaders and ultimately to develop themselves in their careers,” Bellman said. By Kylie Fahey
NEW SOUTH WALES BRANCH NEWS Registrations are now available for the Sixth Annual Quarries & Concrete Safety Seminar, which will be held at Rydges Campbelltown on Wednesday, 23 October. The seminar, featuring a full day program of expert and industry speakers, is co-hosted by the CCAA and the IQA.
Dr Sean Brady, a forensic structural engineer who specialises in identifying the cause of defects and failures in construction and engineering, is the keynote speaker. Dr Brady is currently undertaking a review into mining and quarrying incidents in Queensland. His presentation will examine how the automation of industry systems, whether by computers or by robots, can have very unexpected, comical or even destructive effects.
The seminar theme is “Understanding and managing critical risk” and will include sessions covering: • Critical control management in the quarry industry. • The use of drone technology to collect and process aerial observational data. • Case studies from Boral Construction Materials and Hitachi Construction Machinery. • Respirable crystalline silica. • The NSW Regulator’s report on competencies. • The IQA’s report on professional development and training. • Mental health, a panel discussion facilitated by Scott Tipping (Hanson). The seminar is sponsored by the New South Wales Government (Department of Planning, Industry and Environment – NSW Resources Regulator). Hitachi Construction Machinery is the gold sponsor of the seminar. A trade exhibition will be held in conjunction with the seminar. At the time of printing, trade exhibit sites and sponsorship packages are still available. To register for the seminar, visit the IQA website: quarry.com.au/IQA/events For more information, contact the seminar secretariat, tel 0419 782 688 or email qldadmin@quarry.com.au
CENTRAL QUEENSLAND SUB-BRANCH NEWS The Central Queensland sub-branch hosted its annual golf day on 19 July. About 43 players enjoyed a day on the green at the Rockhampton Golf Club.
The golf day sponsors were Orica, REO Heavy Equipment Repairs, Inline Drilling (Qld), Komatsu, The Caves Quarry, UKW Spares and The Achieve Group.
The sub-branch’s next meeting will be a safety and health seminar in Rockhampton on 23 October.
Central Queensland sub-branch chairman Darren Wardle thanks golf day sponsors The Achieve Group (left) and Inline Drilling for their support.
NORTH QUEENSLAND BRANCH NEWS The Cairns sub-branch of the North Queensland branch hosted its annual golf day in Cairns on 26 July. The event was well attended by local members and well supported by sponsors which included NQ Equipment, TUFF Tyres, Pioneer North Queensland (PNQ), Apex Drill & Blast, UKW Spares, King Bars, Brown & Hurley, Construction Sciences, RPS Group, Hitachi Construction Machinery, BSC Bearing & Power Transmission, Orica, Hastings Deering, Cobbe Contracting, Komatsu and Impact Drill & Blast.
The winning teams on the day were Team Moody Kiddell & Partners (first place), Team 1 PNQ (second place), Team 1 Orica (third place). Hitachi & Applied IT finished as the NAGA/last place.
The branch’s next meeting will be its annual golf day in Townsville on 13 September, followed by further technical and dinner meetings in Townsville on 8 October and Cairns on 30 October.
KEN MAWSON: A RARE TALENT BEYOND ROCKS AND NUMBERS
Ken Mawson, one of the industry’s oldest and most esteemed leaders, has passed away peacefully, aged 97, after a long, healthy and productive life. John Mawson reports.
Ken was born in Cohuna, the oldest of EB (Barney) and Annie Mawson’s five children. Growing up in a small country town at the edge of the Redgum Forest and irrigated dairy farms along the Murray River, Ken enjoyed what he described as a “lucky” childhood. The Great Depression had engulfed Australia and times were difficult but the Mawson family was frugal and resourceful, making ends meet through Barney’s hard work and business acumen. Eventually prosperity returned to the Australian community. Ken, having successfully completed all the schooling Cohuna could offer, was enrolled in an electrical apprenticeship program at the local butter factory. Ken excelled at school in Cohuna and had a great thirst for knowledge which his aunt Rehna, Annie’s sister, recognised. Rehna’s son was the same age as Ken and she offered Ken the opportunity to join them in Melbourne and continue his education.
Attending Box Hill and Melbourne high schools and Burnley College, Ken thrived on the opportunity his extended family provided. After school, he went to Melbourne Teachers’ College and earned a scholarship to the University of Melbourne, where he studied commerce. Following university and after being rejected from military service because of his “poor skin”, Ken took up a teaching position at Melbourne High School.
During one of his regular visits home after the war, Ken saw that his father’s employees were earning more driving trucks than he was as a teacher. The lure of the country was strong and the opportunity was great so Ken made the move back to Cohuna. In 1947, Ken married Olive Stanton. Olive, a talented musician and teacher, grew up in Rutherglen and had met Ken at teachers’ college. They formed a strong team and were very happily married for 72 years until Ken’s passing. Upon his return to Cohuna, Ken started work with his father and brother Bernie driving trucks and building timber bridges. The civil construction, cartage, woodcutting and farming business Barney had begun with
Ken Mawson (left) and his brother Bernie (right) presented Jack Price (centre), a contemporary of their father Barney, with a souvenir clock in 2000.

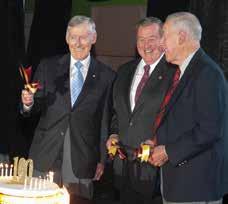
From left to right: Ken Mawson and brothers Lloyd and Bernie cut the Mawsons’ centenary cake in 2012.
his father and brother about 35 years earlier was sound and steadily expanding. Ken recognised that for the company to grow and prosper, more structure and sophistication was needed for the enterprise. And so it was that Ken’s formal commerce training came to the fore, as he began his career as a modern manager at a little desk in the corner of his parents’ dining room at 139 King George Street, Cohuna.
Laying the administrative foundations that facilitated Mawsons’ orderly growth and efficient management, Ken, along with Barney, Bernie and younger brother Lloyd (who joined the company in 1955), formed EB Mawson & Sons in 1960. By then the need for quarry products to provide material for civil construction and work for the Mawson tip trucks had been well recognised and the new company was operating four quarries and several sand pits. Ken’s experience overseeing these businesses enabled him to develop a full, intimate understanding of hard rock, gravel and sand operations. That expertise placed him in an excellent position to guide others and lead the Australian division of the Institute of Quarrying in years to come.
Life for Ken was not all crushed rock and numbers though; he was a devoted father, keen sportsman and a proud community leader. Ken was president of the Cohuna Tennis Club, an elder of the Uniting Church, a founder of the Cohuna Chaplaincy Foundation and served on the Cohuna and District Hospital Management Board for more than 30 years. He was head of the Masonic Lodge in Victoria and the Australian and International President of the Institute of Quarrying (from 1989 to 1990).
Ken served for many years on the Victorian Government’s Extractive Industries Advisory Board and as a trustee for the Institute of Quarrying Education Foundation. The Kennett Government also appointed him a commissioner for the newly-formed Gannawarra Shire. In 2006 his exceptional service to the community and the quarrying industry was recognised with an Order of Australia Medal.
In 2007, after 61 years of diligent, selfless, hard work, Ken sold his share of EB Mawson & Sons to Adelaide Brighton. Ken and Olive moved to a peaceful retirement in Torquay and, while he remained vitally interested in the continued progress of the Mawson business, he relished the time he spent with his grandchildren and great-grandchildren by the sea. •
GEOLOGY TALK
SO, WHAT’S IN YOUR SMARTPHONE?
For every 0.014g of gold in a smartphone, the amount of high grade ore needed is about 1.6kg.
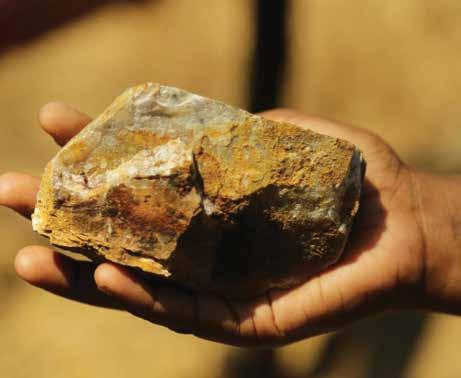
ELEMENT (GRAMS) PRIMARY USES
Aluminium (31.14g) Case Silicon (8.14g) Glass screen
Copper (7.84g) Electrical conductor
Cobalt (6.59g) Rechargeable batteries
Chrome (4.94g) Rechargeable batteries
Nickel (2.72g) Electrical connections, capacitors and batteries
Lithium (0.87g) Rechargeable batteries
Tin (0.66g) Solder for electrical connections Magnesium (0.65g) Alloy with aluminium
Tungsten (0.02g) Heat sink and the mass for phone vibration
Gallium (Ga) (0.01g) GaAs (gallium combined with arsenic) is used to make light-emitting diodes (LED) Arsenic (As) (0.01g) Gold (0.014g) Circuit board
Table 1. Twelve typical elements in a smartphone.
‘Honey, I’ll put you on hold!’ Bill Langer takes a moment away from his ‘mineral-laden’ smartphone to explain how many fractions of minerals are present in the average unit and contribute to its functions …
Back in the mid-1980s my wife Pam and I were working with a realtor to look at houses. The fellow had a newfangled device called a mobile phone. It was about the size of a shoebox, and had a handset like that on a traditional household phone of the time (if you can remember what that looked like). We were really impressed that he could call the office from his car.
Since that time mobile phones have evolved from simple communication devices into multi-function smartphones. As the phones became more complex, the list of elements needed to create them grew. There were about 25 to 30 elements that went into the 1980s device. Today about 75 different elements (almost threequarters of the periodic table) are needed to meet all the special functions of our smartphones.
Twelve of the elements in a smartphone, the amount of the element in the phone and their primary uses are shown in Table 1.
These elements are refined from minerals extracted all across the globe. You might wonder how much material is mined to make one smartphone.
Let’s start by looking at how much gold ore is mined to produce the 0.014 grams of gold used in a smartphone. For this exercise we will assume that a mine is capable of producing high grade ore, which is about eight to 10 grams of gold per tonne of ore (eight to 10 parts per million), and that the recovery of gold from processing the ore is 90 per cent.
First, there is no such thing as an average gold mine or average “any type of mine”. Similarly, the amount of gold or other metal recovered during processing also varies depending on the type of ore and the method of processing. So, the values I give above are very generalised.
The 0.014 grams of gold used in a smartphone is about the size of a grain of sand. The amount of high grade ore needed to obtain that amount of gold is about 1.6 kilograms. For lower grade ore the sample might be twice that size.
Of course, mining other elements can be much more efficient. For example, silica sand is used to make the screen of a smartphone. Most commercially worked silica sand deposits are at least 90 per cent pure, and very little of the material is lost during processing. So the tablespoon (15cm 3 or so) of silica sand used in a smartphone might require mining a heaping tablespoon of sand.
Add to those two samples all the other types of ore that have to be mined to get the remaining 73 elements and you have a pile of rock that weighs somewhere around 34kg – just to make one 130g cell phone!
I gotta go! Pam just sent me a text message on my mineral-laden smartphone! •
Bill Langer is a consultant geologist. Email bill_langer@hotmail.com or visit researchgeologist.com
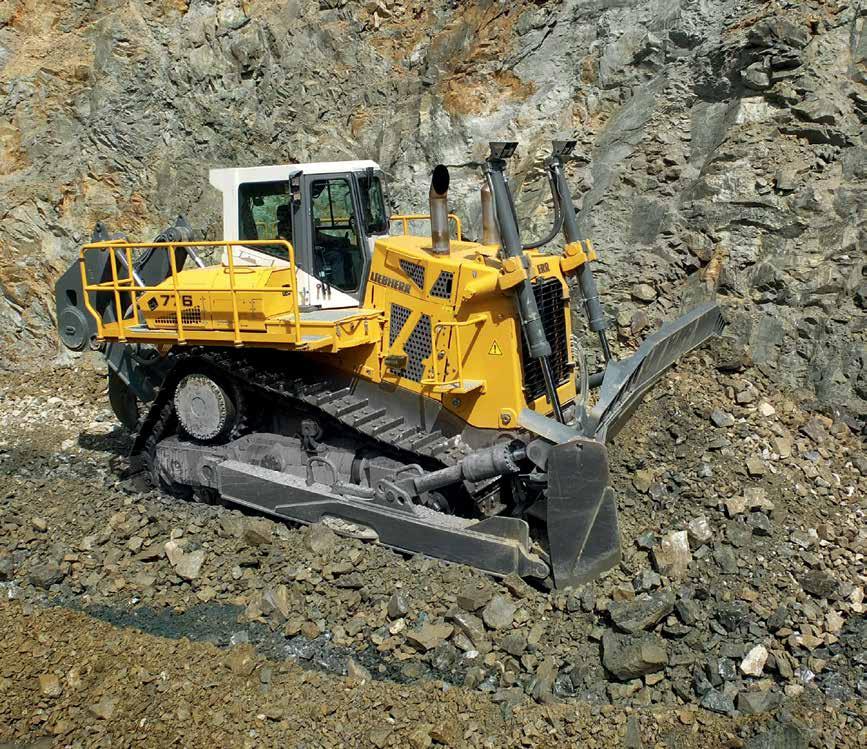
Find your Liebherr-contact
Liebherr crawler tractors are distinguished by:
Powerful engine and stepless hydrostatic transmission Fuel efficiency due to constant engine speed and Eco-Mode Perfect operator comfort for productive work
Visit us at: IQA Conference 2019 1-3 October, GMHBA Stadium, South Geelong, Victoria Stand: 16
PEOPLE POWEREDTECHNOLOGY KOMATSU QUARRY SOLUTIONS
Availability
Efficiency
