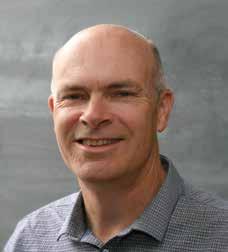
21 minute read
THE IMPACT OF NEW
from Quarry Oct 2019
by Prime Group
NEW TRENDS IN MANAGING MINING LIABILITY
Some jurisdictions have introduced reforms to manage the liability of resource projects in the remediation phase – but there are concerns these reforms may unduly impact quarries with traditionally lower risk profiles than mines. Michael Cramer discusses his work in this field.
Michael Cramer is director of Accent Environmental, a Melbournebased consultancy that provides environmental and social impact assessment and management services and strategic advice to the resources, industrial, water and waste sectors. He has more than 25 years’ professional experience working with private clients and government agencies in the resource sector, and specialises in closure planning of sites.
Cramer is currently advising on reforms to Queensland’s financial assurance system for resource development projects. His presentation will outline some of the new approaches across Australia towards the management of liability for resource projects in the remediation phase.
What is your key message for the industry? There are several new approaches towards the management of liability for mining projects that are either being adopted or considered by regulatory authorities. There are likely to be flow-on effects to the quarrying industry – some good, some not so good – that need to be anticipated and managed. These approaches include consideration of post-relinquishment liabilities, changes to liability cost calculation methods (including incorporation of risk components), further movement towards pooled rehabilitation funds, and more prescriptive requirements to drive progressive rehabilitation.
What advice does Accent Environmental offer about site closures and repurposing? Effective closure and repurposing can achieve a positive outcome for an operator, community and industry. There are opportunities that did not exist a decade ago – eg the use of sites as part of integrated renewable energy projects, or with the potential to support pumped hydro. My advice would be to consult widely, particularly at the early planning stage.
Accent Environmental director Michael Cramer.
Where are mines and quarries expected to contribute to pooled rehabilitation funds? Queensland is leading the way on reforms to the management of mine rehabilitation and financial assurance. Regulators in jurisdictions such as Victoria, New South Wales and the Northern Territory are watching them. The Queensland reform program includes the introduction of a pooled fund for lower risk operations to cover rehabilitation liability. Interestingly, the program will also require payment as part of final site surrender to cover any ongoing liability for the state, including exposure to residual risks. Accent is developing a cost calculation tool for the Queensland Department of Environment and Science to estimate site surrender costs. The reforms cover the mining and petroleum and gas sectors, but not the extractive industry.
What are the pros and cons of pooled funds? Do they work as effectively as envisaged? I am strongly in favour of pooled rehabilitation funds for mining, but less in favour for quarrying. If set up correctly, they provide the state with funds to cover rehabilitation default without having to trouble the taxpayer – whereas if the funds are tied to a specific tenement, the taxpayer has to step in if the financial assurance is inadequate. I think they suit mining better because the risk profile of mining projects is generally greater than quarrying projects – ie the potential for a risk event to occur that drains the estimated surety for a site is much greater.
The implementation of the mining rehabilitation fund in Western Australia has not gone as smoothly as hoped. It will be interesting to see how the Queensland scheme – which had the advantage of learning from the WA scheme - progresses. For quarry operators, a pooled fund may put them under greater financial pressure, depending on the level of the fund levy compared with the fee for maintaining a bank guarantee and the associated cost of capital.
What makes the risk profiles of quarrying operations different from mining operations? Rehabilitation risks associated with quarrying operations are generally well understood and amenable to standard risk mitigation practices. For example, geotechnical, hydrological and hydrogeological risks can be quantified and managed. In contrast, many mining operations have rehabilitation risks that are more difficult to manage, with large, even order-of-magnitude implications. This is true in the area of water quality, where issues like acid and metalliferous drainage can be intractable at many mining operations. In addition, mines typically have much higher capital and operating costs than quarries, and are often remote from settlement, making them less able to survive poor market conditions. Rehabilitation reforms aimed at addressing mining risks may inadvertently overcook quarry risks, if applied without adequate thought.
stable and non-polluting site are nonnegotiable and progressive rehabilitation goals need to zero in on this outcome. The area that is questionable is the nature of postclosure land use – to what extent can the rehabilitated site support ongoing productive and sustainable land use, and is that land use acceptable to the community and other stakeholders? It is in the interests of the quarry operator to maximise the commercial value of the land for on-selling but this may conflict with local community aspirations. The earlier in the life of a quarry that end land use can be agreed the better for rehabilitation planning, although it is often only as closure approaches that agreement can be reached.
Should regulators expect proponents to outline mine closure plans at an early stage? It is not unreasonable to have a well developed concept to form a basis for rehabilitation planning and to enable a realistic estimation of financial assurance. It is important though for regulators to realise the plan at the start of a long-lived operation will almost certainly be different from the plan at the end of the operation, as quarries need to adapt to many different factors such as improved resource definition, changing market conditions, changes in surrounding land use, new regulatory requirements and evolving community expectations.
Are rehabilitation liability calculation tools available for quarries to use? Rehabilitation liability calculation tools are typically developed for mining, not quarrying. The Victorian rehabilitation bond calculator is used for mining and quarrying as the same legislation covers both sectors, but it is arguably better suited to mining. Calculation tools incorporating risk-based cost factors are being considered but introduce a higher level of complexity – both for the user of the calculator and for the regulator reviewing the output. Current calculation tools generally handle uncertainty through a percentage contingency that is applied to the total cost estimation. Given the lower risk nature of most quarrying operations, risk-based calculation is probably overkill, but it has its place for high risk mining operations.
What sort of residual liabilities can remain for an operation once a site is remediated? The work that Accent is undertaking for the Queensland Government has identified two broad categories of residual liability at mine sites, even after successful rehabilitation and closure. These are a “residual risk cost” associated with the potential for unplanned events to occur (ie slumping of an embankment) and a “maintenance and monitoring cost” (ie where a drainage structure needs annual maintenance). At many sites, residual liabilities may be minimal or effectively zero. As quarries are generally lower risk than mines, residual liabilities would typically be lower. •
Michael Cramer will deliver his presentation at the IQA’s annual conference at GMHBA Stadium, Geelong, on Thursday, 3 October.
HEINEHARD
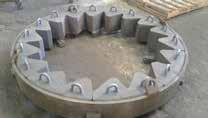
Wear parts for impactors, jaws & cones. Modified designs for longer wear life. Tailored chemistry and heat treatment for extra wear life. Buy back for credit on chrome iron scrap. Australian made AS3901/ISO9001.
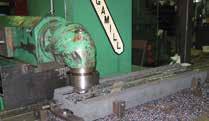

The John Heine foundry in Sydney casts white irons and manganese steels wear parts for the mining and quarrying industries. These Australian made parts can be tailored to your requirements by designing extra pads of material in high wear areas. We have a selection of developed proprietary grades of chrome iron alloys to suit your particular application and improve wear life. As part of our service, we offer a buy back scheme for credit on your worn white iron components, as we can melt down and re-cycle into new parts. We stock a large range of castings such as hammers, anvils, impact plates and blow bars now including chrome, martensitic steel and manganese ceramic alloys. Our range can cover Canica, Kleemann, Nordberg, RubbleMaster, Jacques, Trio, Sandvik, Cedarapids, Extec, Hazemag, Pegson, Striker and Teesab. We also manufacture chute protection liner castings and a range of pug mill and Fisher Air Separator parts. We import a range of jaws, mantles and concaves for many brands of machines.
WHY NOT CALL RAY BOGG ON 0458 111 503 AND START SAVING NOW?
John Heine & Son Pty Ltd 273 Edgar Street Condell Park 2200 Phone 02 9772 5000 sales@johnheine.com.au • www.johnheine.com.au “Molten Engineering”
GEELONG FAMILY COMPANY CONSOLIDATES ITS PARTNERSHIPS
With its head office at Moolap, a suburb of Geelong, Newcomb Sand and Soil is a family-owned company, started by Doug and Joy Dunoon in 1973. Joy continues as CEO today, with sons Chris and David as the operations manager and general manager respectively, and daughter Joanne as administration manager.
The company prides itself on being a “one stop shop” for the Geelong and southwestern Victoria region, and the state as a whole. Newcomb offers recycling services, retail garden supplies and fine sand supplies, along with plant hire and subcontracting.
Its recycling operations cover asphalt, concrete, brick and soils, while it operates four fine sand pits at Portalington and Inverleigh, along with two retail garden outlets in Newcomb and Torquay.
Newcomb provides hourly plant hire and subcontracting services for local councils and contractors, with a complete fleet of equipment covering excavators, graders, scrapers, wheel loaders, dump trucks, trucks and trailers, mobile crushers and screens, and other ancillary equipment. The business is also a significant contributor to the Geelong, Bellarine and Surf Coast areas, donating garden supply prizes for raffles and fundraisers for community groups. It sponsors junior teams at the Newcomb Football Club; indeed, the football ground has been renamed Newcomb Sand and Soil Oval. It also offers work experience opportunities for school students through a joint program with the Newcomb Secondary College and the Victorian Department of Education.
Newcomb Sand and Soil has also been a long-time supporter of the Torquay Surf Life Saving Club, purchasing a trailer on the club’s behalf that assists the life savers in transporting their surf boat. It also sponsors court number one at the Moolap Tennis Club, where members of the Dunoon family have been long-time members.
When it comes to long-term relationships, Newcomb Sand and Soil has been buying Komatsu earthmoving equipment for the past 10 years, due to equipment
The new PC220-8 in the Newcomb Sand and Soil Supplies yard, with operations manager Chris Dunoon (left), Simon Bird (middle) and general manager David Dunoon (right).
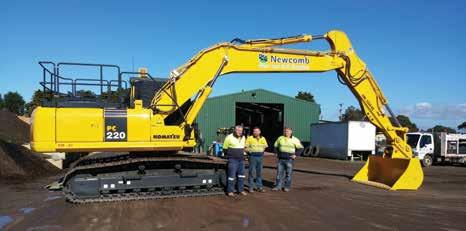
reliability, machine performance and a strong relationship with Komatsu’s local representative.
Currently the business owns three Komatsu excavators: a five-tonne PC50MR-8, a 21-tonne PC200-8 and a 25-tonne PC220-8, which was purchased in July. The company also recently retired a WA380-3 wheel loader that it had owned for 20 years.
According to Chris Dunoon, Newcomb Sand and Soil’s long-term partnership with Komatsu began in 2007, when it bought a PC50MRX-2 excavator from local representative Geoff Killury.
“We went for Komatsu because I liked their reliability and service, plus the local knowledge from the likes of Geoff, his communications with us and focus on relationship. They’ve all lived up to expectations,” he said. “So far, the service and support we’ve received has been excellent.”
Newcomb’s excavators carry out a range of tasks, including general plant hire work, loading screens at crushing sites, shifting soil from site to site, and loading dump trucks at its sand pits.
“We find the excavators ideal in our sand pits,” Chris said. “Being fine sand, we have to move it in layers.”
The latest Komatsu PC220-8 replaced a 20-tonne unit of another make. “That machine was well worn, and we needed to replace it,” he said. “We find the Komatsu
Chris Dunoon in the cab of the new machine.

is better in fuel economy, diagnostics and reliability, plus we know we have that relationship with Geoff and knowing he’ll help us if we have any issues. Basically we prefer to go with Komatsu in our excavator fleet.
“Since the PC220-8 was delivered, we’ve found a huge difference in performance between our previous 20-tonne machine and this 25-tonner. It’s more stable in our sandpit operations, and the all-new electronics make it very efficient.”
Chris said all of Newcomb’s Komatsu machines utilised the KOMTRAX remote monitoring system. “It’s always good to get that report every month, showing us fuel economy, engine hours, idling times and so on. And if a machine is ever stolen, we have that extra peace of mind that it can be tracked.” •
Komatsu’s Smart Solutions team in Australia operates out of the Rutherford Centre in the NSW Hunter Valley.
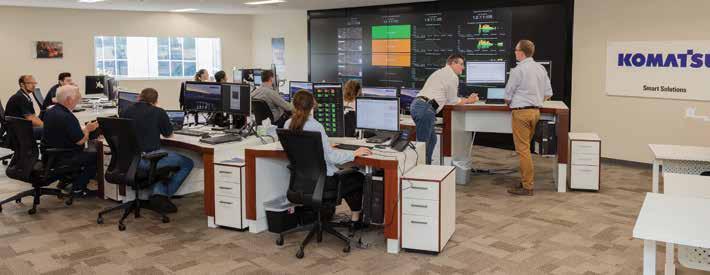
A ‘GAME-CHANGING’ APPROACH TO MACHINE DATA ANALYTICS
Komatsu Smart Solutions is an industry-leading approach to harnessing machine data for analytics and analysis, using data that is continuously streamed from machines on jobsites. It will be progressively rolled out to all Komatsu customers across all industry sectors.
“Our ability to transmit and receive this very detailed data on a continuous basis is allowing us to apply advanced analytics and trends analysis to Komatsu mining equipment,” said Mick Hewitt, technology development manager at Komatsu’s Rutherford facility in the New South Wales Hunter Valley.
“Smart Solutions has been available on [Komatsu’s] Joy and P&H mining equipment for some years, and our team is now working on integrating Komatsu’s ‘traditional’ mining equipment product line – dump trucks, excavators and shovels, mining loaders, dozers, etc – into this offering.”
The data derives from a wide range of sources: the Modular Mining and MineWare product suites, KOMTRAX Plus remote monitoring, and other on-board remote monitoring systems.
“Through Smart Solutions, we can now take mining equipment and mine site performance, productivity and safety to the next level,” Hewitt said. “Our ability to receive a constant data flow off our machines greatly enhances the insights we receive from equipment on-site.
“This powers our advanced data-based decision-making processes, which are essential to today’s modern mining operation. Then, by using our ‘big data’ capabilities, we can apply trends knowledge to the data we are capturing.
“This means that, rather than receiving alarms and alerts as an issue arises, we are getting predictive information – ensuring that we know about a potential failure or machine issue well in advance of it happening.” Komatsu’s Smart Solutions teams collaborate with mine management and on-site personnel to determine the best mix of equipment, services, training, technology, monitoring and data analytics options to create value for customers.
Each Smart Solutions offering is customised to an individual customer’s specific needs and is designed to deliver the lowest cost per tonne in alignment with a customer’s financial and operating goals. Smart Solutions was developed as an overarching philosophy for applying machine data for analytics and analysis. In Australia it is widely used with Komatsu’s P&H electric rope shovels and P&H wheel loaders. It is also being used for Komatsu’s Joy underground mining equipment, both on hard rock and soft rock.
As Komatsu’s product lines become increasingly integrated, Hewitt predicted the KOMTRAX Plus offering for Komatsu mining equipment would form a subset of Smart Solutions, with the two ultimately becoming part of a single offering.
“Once this occurs, KOMTRAX Plus data will feed into a database accessible by Komatsu’s analytics team, which develops algorithms that can detect any issues with machines across our entire range,” he said. “Once KOMTRAX Plus is integrated with Smart Solutions, we will offer many additional advantages for customers and mine operators, right across the ‘four pillars’ that we aim to deliver for all our machine owners – HSE [health safety and environment], reliability, productivity, and owning and operating cost.”
Hewitt said the first stages of this have already been implemented. However, it will be an evolving product, so it will undergo many stages of development.
The Smart Solutions/KOMTRAX Plus integration program is being undertaken in Australia and in Komatsu’s Milwaukee (US) offices.
“Komatsu Milwaukee is responsible for the management of all of the databases, while Komatsu Australia is assisting in ensuring all of the ancillary technologies and information are compatible and will work together,” Hewitt said.
“This will deliver benefits not only to our customers here in Australia, but also throughout the world. The technology used in Smart Solutions will eventually also have applications in Komatsu’s construction products. We are currently working on a completely new offering that will overlap both mining and construction. Known as KOMTRAX Plus Air Relay, it is being completely developed in Australia. Details of this will be made available in due course.” •
ELECTRIC DRIVE LOADER CULMINATION OF FIVE DECADES OF DEVELOPMENT
Introduced in 1963, the Caterpillar 988 wheel loader has been an industry mainstay for more than 50 years. It has been renowned for its reliability, performance, safety, operator comfort, serviceability and productivity. The new electric drive version of this machine platform – the 988K XE – offers improved sustainability and maximised efficiency.
The new 988K XE is the first wheel loader offered by Caterpillar with a high efficiency electric drive system. This new large loader joins industry stalwarts in the 988K and 986K wheel loaders to provide quarrying producers with the most cost-effective loader for each application. The XE has 90 per cent commonality with the 988K, with the same C18 ACERT engine, lower powertrain and cab. The new loader features switched reluctance technology and leverages more than 15 years of Cat electric drive experience and more than four years of stringent testing in a range of applications for proven reliability in the field. The 988K XE provides overall efficiency of 25 per cent, and up to 49 per cent in face-loading applications, as compared to the 988K loader. While the electric drive transmission replacement on the XE allows for a significant increase in efficiency, the axles and the driveline are the same as on the proven 988K mechanical drive. The C18 ACERT engine is built and tested to meet demanding applications while complying with the Tier 4 Final/Stage V emission standard. Oil change intervals have been doubled from 1000 hours with the 988K to 2000 hours with the XE, resulting in 40 per cent less powertrain oil being used. In addition, the oil filter interval has been extended fourfold from 500 hours to 2000 hours to match the oil change interval, promising more savings in maintenance costs. The electric drive powertrain means there is no need for a transmission or clutch, only a single speed range, so the machine efficiently operates without gear shifting. New virtual gears help control machine ground speed and deliver those smooth, quick directional shifts, forward or reverse. The efficient electric drive design increases engine life by up to 3500 hours, extending time between powertrain rebuilds.
The standard Cat Product Link software
The new 988K XE is Caterpillar’s first wheel loader with a high efficiency electric drive system.

offers remote data monitoring through VisionLink, so key personnel can stay informed of critical machine operating data. Fuel usage, payload summaries, scheduled service reminders, fault code alerts and various productivity reports are available to help improve machine management. In addition, the on-board Vital Information Management System (VIMS) provides operating data via an interactive touch screen display.
The new Cat 988K XE loader is equipped with a host of technology solutions to increase operating efficiency and machine uptime. Cat Production Measurement (CPM) brings payload weighing to the cab, so operators can work more productively and deliver accurate loads with confidence. CPM offers advanced weighing modes, which assist with payload accuracy and increase loading cycle speed. The Optional Tyre Pressure Monitoring System is a fully integrated Cat feature, which enables operators to monitor tyre inflation. Available through the VIMS display, the operator can quickly view each tyre’s pressure and take action when needed to reduce wear and increase service life. The 988K XE offers a range of bucket capacities from 4.7m 3 to 13m 3 . The loader’s rated standard and high lift payload can reach 11.3 tonnes when working with face material and 14.5 tonnes with loose material. SPECS – CATERPILLAR 988K XE WHEEL LOADER Engine Cat C18 ACERT Gross power (SAE J1995) 439kW Operating weight (standard) 53 tonnes Operating weight (high lift) 54 tonnes Rated payload: Standard (face material) 11.3 tonnes Standard (loose material) 14.5 tonnes High lift (face material) 11.3 tonnes High lift (loose material) 14.5 tonnes
The Advansys Series Ground Engaging Tools protect bucket components and reduce operating costs, thereby maximising machine performance.
The standard 988K XE is performancematched to offer efficient three-pass loading of the 39-tonne Cat 770G off-highway truck and four-pass loading of the 46-tonne Cat 772 truck. Its high lift configuration delivers five-pass loading of the 55-tonne Cat 773G and six-pass loading of the 64-tonne Cat 775G. •
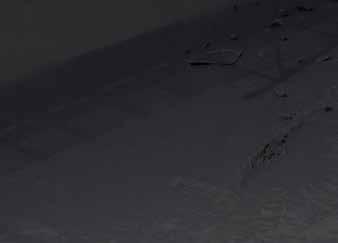
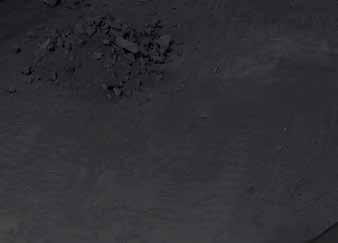

That’s how we make the big di erence, the Metso Way.
The Metso MX™ cone crusher is based on the patented Multi-Action crushing technology, which combines the piston and rotating bowl into a single crusher. The new crusher provides a giant leap in pro tability, cutting operational costs by 10% and enabling 10% more uptime compared to traditional cone crushers.
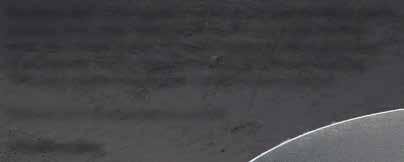
Find out more at www.metso.com/mx
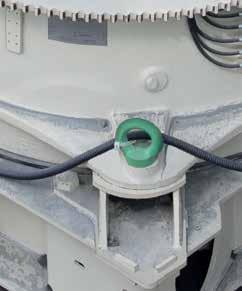
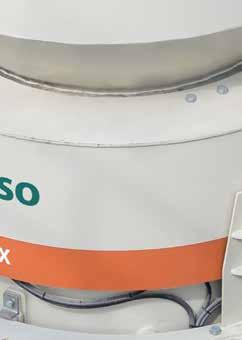


#TheMetsoWay
CERTIFIED BREAKER, ATTACHMENT RANGE BOOSTED BY PARTNERSHIP
The Rammer range of rock breaker and demolition attachments has a new home. Sandvik Mining and Rock Technology, which owns and manufactures Rammer, recently formed a new partnership with renowned Queensland supplier QLD Rock Breakers (QRB), based in Rocklea, Brisbane.
Sandvik and QRB regard the partnership, formalised in July this year, as a positive step and the next phase of business growth. QRB, which is a subsidiary of the RDW Machinery group, has been the leading rock breaker supplier in Queensland for more than 20 years. The company has grown from humble beginnings to be a premium equipment supplier, capable of offering not only genuine certified Rammer products but also backing this up with the only Rammercertified service centre in Queensland. This will also see QRB service Papua New Guinea and the South Pacific Islands (excluding New Zealand) for Rammer products.
“We see the partnership with Sandvik/ Rammer as a positive fit for our business,” said Fred Carlsson, the general manager for the RDW and QRB businesses. “We have been in business for over 30 years and during those years taken pride in being able to not only supply premium products to the market but more importantly, being able to support these products on time and with great service and technical support.
“Our business has been built on taking care of customers’ needs and offering solutions that add value to our customers’ business,” Carlsson said.
For more than 40 years Sandvik’s Rammer division has manufactured premium product out of its Finland base. Recently Sandvik/ Rammer introduced the renewed “Excellence Line” of hydraulic rock breakers with integrated smart technology. In addition to a new and improved focus on safety, Rammer is the first on the market to introduce the RD3 monitoring device, together with the My Fleet platform, to make it easier for producers to monitor their rock breaker fleet remotely.
“RD3 uses the My Fleet telematics service to track and monitor fleet equipment usage without needing to go to the site to collect the data,” Carlsson said. “It’s ideal for dealers,
The Rammer E-line is fitted with RD3 monitoring, making it easier for producers to monitor breaker performance.
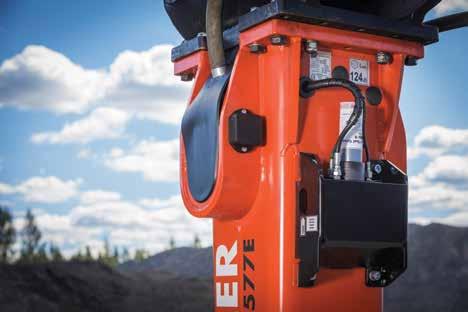
The Rammer 2577 breaker is part of the renewed ‘Excellence Line’, with integrated smart technology.
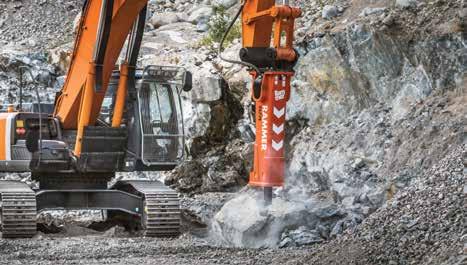
rental companies and operators. This cloudbased system enables the rock breakers to be viewed and monitored via Google maps.” David Scurr, Rammer’s territory sales manager for the Asia-Pacific, Middle East, Indian and Commonwealth of Independent States, said recently launched RD3 capabilities, coupled with a new dealer in QRB, make Sandvik/Rammer the strongest rock breaker supplier in Australia. “We have recently carried out factory technical training to all of our Australian dealer technical staff and I see us now moving to another level in the industry,” Scurr said. “All of our dealers have invested heavily in stock of both breakers and parts, which enable them to offer a premium service.” •
All the features you need for efficient onsite crushing and screening...
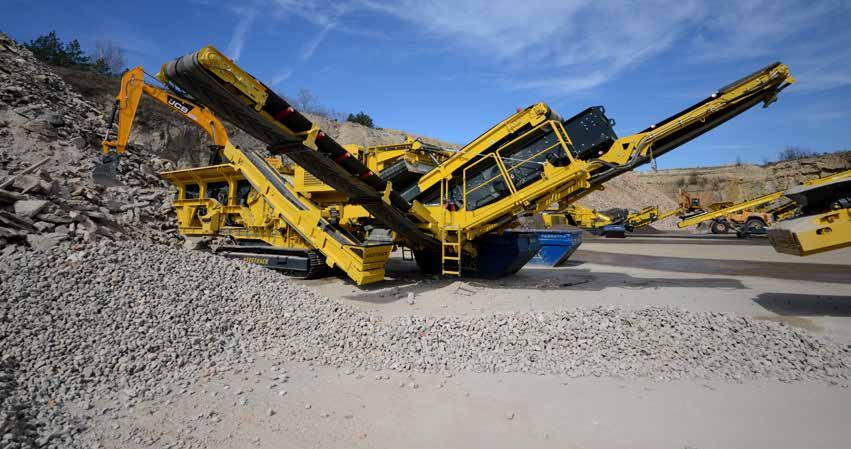

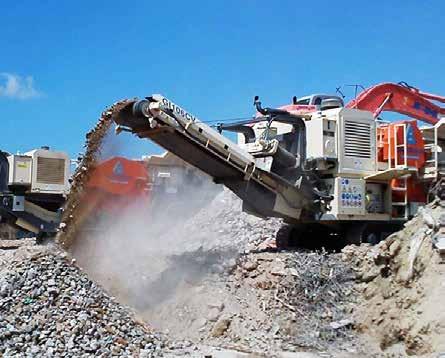
PORTAFILL SERIES Available Australia wide Quality, compact, reliable and robust Crushers and Sreens.
KEESTRACK SERIES Available SA & WA Innovative, high performance, cost efficient, quality Crushers and Screens.
GASPARIN SERIES Available Australia wide European quality, ready to perform in the most demanding conditions.
STOCK RUNOUT * USED
Call 1800 267 847 www.bostgroup.com.au Let us find a solution that will reduce costs & meet your operational requirements! Enquire today!