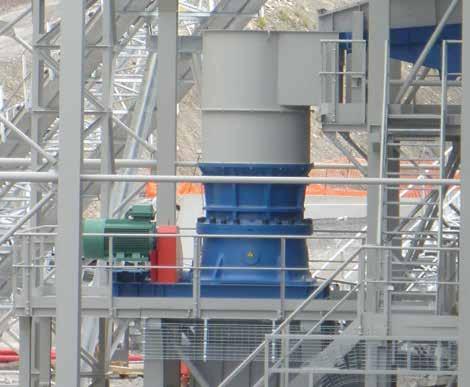
12 minute read
REVAMP FOR THREE
from Quarry Oct 2019
by Prime Group
REVAMP FOR THREE-STAGE HARD ROCK CRUSHING PLANT
A proven performer in hard rock crushing recently underwent substantial technical updates and was standardised to uniform manufacturing standards. Peter Berlitz and Dr Armin Greune explain why the Kubria cone crusher is a competitive option for a quarrying operation.
The Kubria cone crusher from thyssenkrupp has proved effective for many years under the toughest application conditions in the field for hard rock crushing. It is used mainly in the aggregates industry for the secondary and tertiary crushing of granite, basalt, gneiss and other hard rock, and in the mining and cement industries.
The Kubria product line was recently updated to include the latest technical developments and standardised to assure uniform manufacturing standards maintained at thyssenkrupp locations around the world. The result is that the crusher can now be offered very competitively and with significantly lower delivery times.
DESIGN AND FUNCTION The Kubria crusher design has a hydraulically supported main shaft and fixed upper crusher chamber. Crushing takes place between the concaves in the crushing chamber and the mantle-lined crushing cone (Figure 1, overleaf), which is rotated by an eccentric drive in the lower section.
This design allows the gap between the concaves and the crushing cone to be continuously decreased or increased all around the periphery. As the crushing chamber narrows, crushing of the material is achieved by means of increasing pressure on the rock. The geometry of the crushing chamber and the eccentric stroke can be individually adapted to specific crushing requirements as determined by the material characteristics. This is particularly important when the raw material properties or the product requirements change during the service life of the crusher.
The maximum possible feed size for the crusher is determined by the opening width at the top of the crushing chamber. The finished product lump size is determined by the closed side setting (CSS) in the discharge zone.
A G110 Kubria cone crusher in a quarry near Rosetto, France.
The wear material components in the crusher are made of wear-resistant austenitic manganese steel that can be easily replaced. The crushing cone consists of a mantle fit on the cone body that is in turn firmly connected to the main shaft. The crushing ring is fastened in the top shell of the crusher. “G” models for coarse crushing are additionally equipped with annular arranged concaves. The top shell and bottom shell are both made of cast steel.
The “spider” in the upper area of the top shell is used to support the upper shaft bearing. This spider is also made of cast steel and has spider arm liners. As all wear parts and heavy internal removable components parts are accessible from above, the crusher is very easy to maintain. A thrust bearing is used to support the main shaft on a hydraulic cylinder. This cylinder is used to control the crusher setting by raising and lowering the shaft. If tramp material is caught in the crushing chamber, the shaft is lowered automatically, allowing the material to largely pass through the crushing chamber without resulting in damage to the crusher. For run of mine materials that are very hard and tough to crush, the main shaft is equipped with a hydrostatic thrust bearing assembly for operating at high crushing pressures.
The drive and the hydraulic cylinder are housed in the bottom shell of the crusher. The Kubria bevel gear teeth are cut with a specially developed cyclo-palloid process. It provides for smooth, low wear operation,
GLOBAL PRESENCE 2500 PLANTS INSTALLED WORLD WIDE
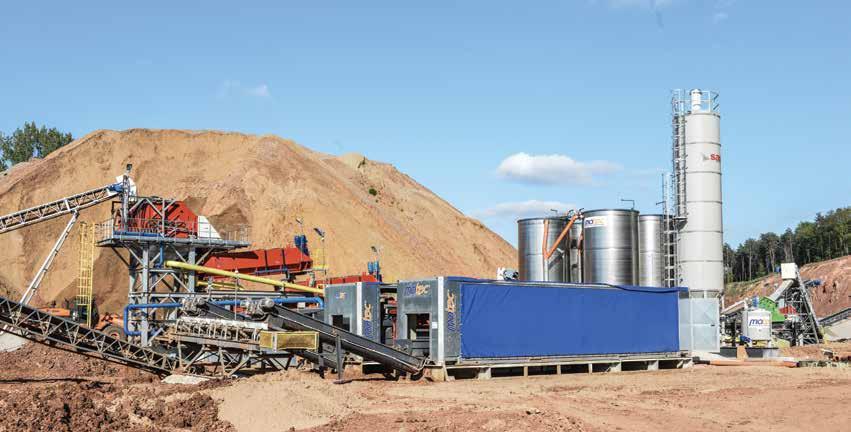
More than 15 years international experience and presence in the mining and quarry industry delivering technical turn key solutions for tailings and residue management
Higher feed pressure Shorter cycle times Higher throughput Less capital equipment
2TE C H NO L O GY FAST OPENING
T E C H N O LO G Y
IQA 2019 CONFERENCE GEELONG - OCTOBER 01-03 COME TO VISIT OUR BOOTH #27
SIEMENS/ ALLEN BRADLEY PLC
100% STAINLESS STEEL HYDROCYCLONE CONES AND TANK
DOUBLE HYDROCYCLONE FOR TWO TYPES OF SAND
• Up to 4 grades of aggregate and 1 or 2 grades of sand • Modular Design, pre-plumbed with Single connection point for easy and fast set-up • Completely pre-wired with simple PLC control panel • Overband magnet on feed conveyor for removal of ferrous metals • Rubber lined pumps, cyclones and transfer points for extended plant life • Transportable as single piece or in different containers
FEEDING PUMPS WITH VFD

100% GALVANIZED STEEL VIBRATING SCREEN FOR THREE TYPES OF AGGREGATES
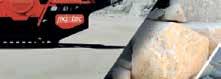
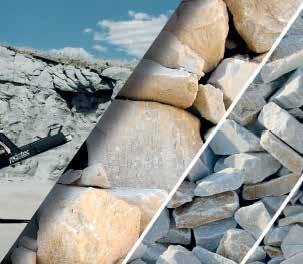
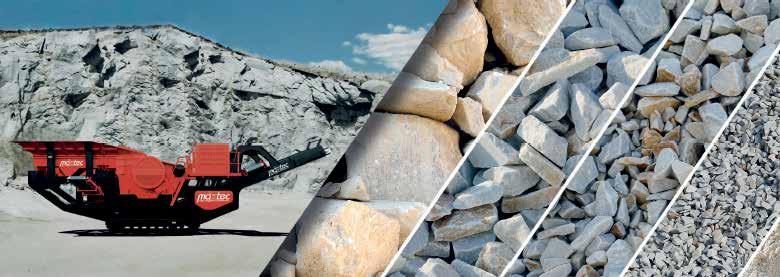
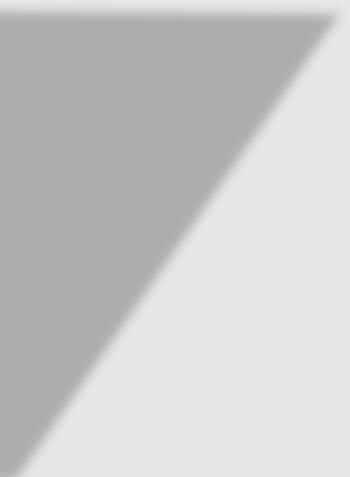
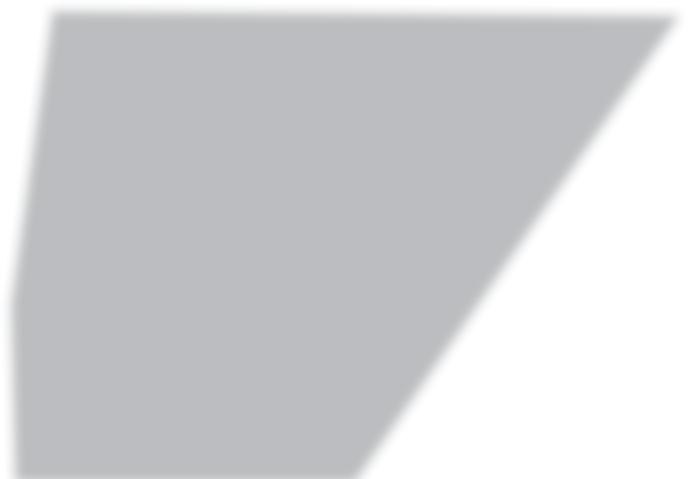
OVERSIZED FEEDING HOPPER WITH VIBRATING SCREEN
Figure 1. Main components of the Kubria cone crusher.
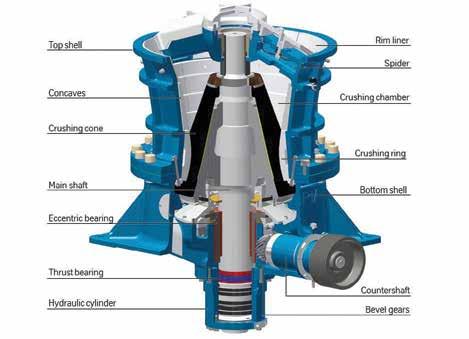
which also allows higher drive powers to be transmitted. The result is that Kubria cone crushers can be equipped with bigger motors. In addition, these crushers are characterised by a long service life and easy accessibility for maintenance work.
The crusher is equipped with a circulating lubrication system to supply oil to the eccentric bush bearing assembly, the axial bearing assembly and the bevel gears, and it is also equipped with an automatic grease lubrication unit for the spider bearing.
Today’s quarrying operations increasingly require automation of plant systems. This also applies to the crushing circuit. The Kubria crusher is typically delivered with the proven Kubriamatic control system, which can be integrated into the control system and the dynamic process display of the overall plant.
With the Kubriamatic control system, the crusher settings can be changed during operation. It is also used to enter and monitor crusher-specific operating data such as
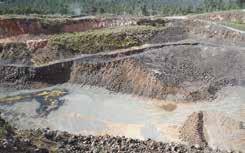
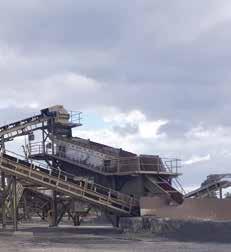
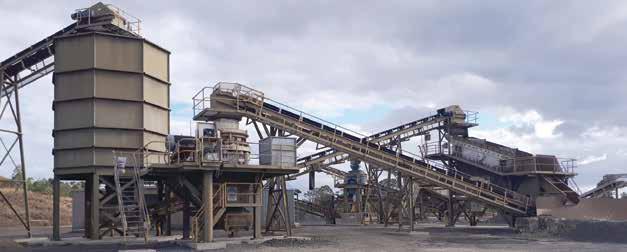
FOR SALE BY EXPRESSIONS OF INTEREST Under Instructions from Boral Construction Materials and Cement GRAHAM MESSER INDUSTRIAL AUCTIONEERS & VALUERS PTY LTD TWO FULLY ESTABLISHED QUEENSLAND QUARRIES
WONDAI FREEHOLD QUARRY • Location: 33klm North West of Kingaroy • Total Area: 514 Hectares • All Extractive Industry Approvals in Place • Crushing & Screening Approvals up to 1M Tonne PA • Resource: Basalt & Granite (High Quality DTMR Approved) • Fixed Crushing & Screening Plant • All Necessary Infrastructure In Place • Weighbridge, Buildings & Associated Plant
AMBY LEASEHOLD QUARRY • Location: 65klm West of Roma • Total Area: 906 Hectares
AMBY Mitchell A2
Roma
• All Extractive Industry Approvals In Place • Crushing & Screening Approvals up to 1M Tonne PA • Resource: Basalt • Fixed Crushing & Screening Plant • Weighbridge & Associated Buildings • Truck Access to Warrego Highway
For further Information contact Marketing Agent: Graham Messer Industrial Auctioneers and Valuers Pty Ltd Graham Messer: Mobile 0417771642 Email: graham@grahammesser.com.au Visit www.grahammesser.com.au for further details EXPRESSIONS OF INTEREST INCLUDING FIRM OFFERS TO PURCHASE ARE INVITED OFFERS CLOSE: THURSDAY 31st OCTOBER 2019
WONDAI
Murgon
Miles
A2
Chinchilla Kingaroy
Nanango
A3
Yarraman
Crows Nest Esk
A2A2
Oakey
A3
Toowoomba
A39
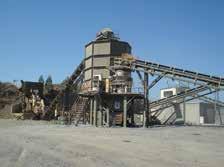
A3 A2
Laidley
CSS, operating power and pressures, plus temperatures and oil flow conditions. Further, important operating data such as operating hours and load and no-load hours, plus the number of pressure and power peaks, can be called up.
The crushing setting is regulated automatically, according to adjustable power and pressure limits. Automatic setting adjustment is carried out to keep the product quality of the crusher constant as the crusher concaves and mantle liners wear.
DESIGN AND APPLICATION For the aggregates industry, Kubria crusher sizes 90, 110 and 130 are commonly used. The number denotes the lower cone diameter. “G” models for coarse crushing and “F/M” models for fine and medium crushing applications are available for each size (Figure 2). The coarse “G” model crusher is equipped with a steeper cone, while the crusher for fine and medium (F/M) crushing has a flatter cone.
The steep cone angle results in higher throughput rates. The use of flatter cone angles in the F/M crusher means a particularly high quality product can be achieved. The design of the bottom shells for either the “G” or “F/M” models is identical.
The coarse crushers are used mainly in the secondary crushing stage. They can process feed sizes of up to 450mm. The fine and medium crushers are used for secondary and tertiary crushing, and can handle feed sizes of up to 230mm.
In all the versions of the Kubria cone crusher, the material has a relatively long retention time in the crushing chamber, with a correspondingly high number of crushing steps. This results in products of high cubicity, which is important for meeting the product standards required for concrete aggregate and other products. The Kubria product name is based on the high-cubicity product it produces.
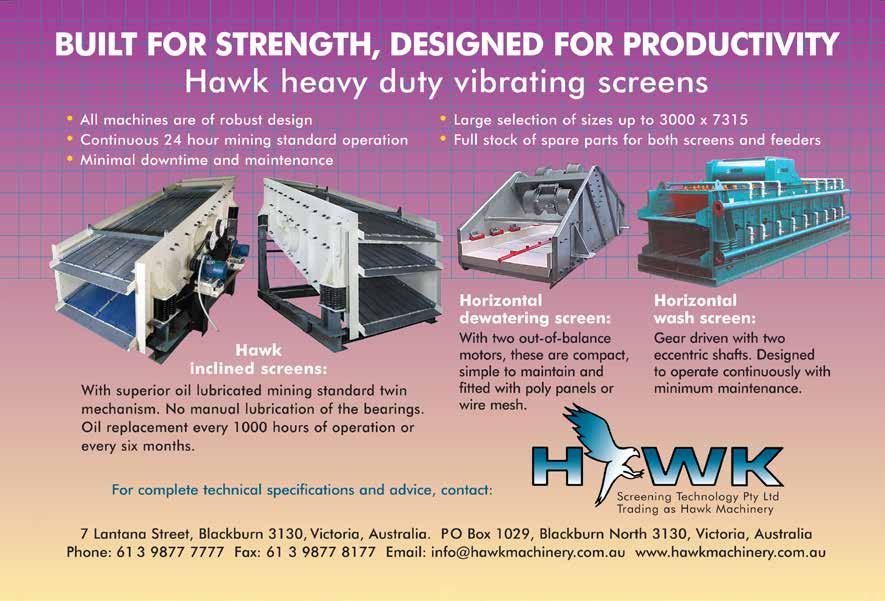
Figure 2. The Kubria ‘G’ type.
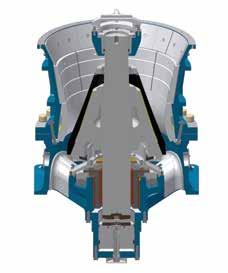
THREE-STAGE PLANT An example of the use of Kubria cone crushers is in a three-stage crushing plant for the production of crushed stone. The flowsheet for this plant, which has a capacity
Figure 3. Flowsheet for a three-stage crushing plant for the crushing of granite.
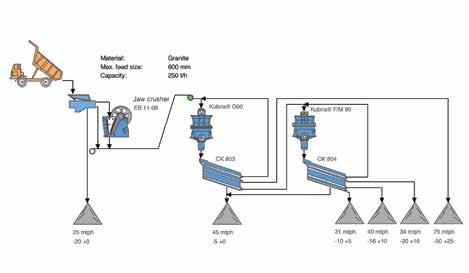
Figure 4. Typical product gradation curves of Kubria cone crushers based on crusher setting.
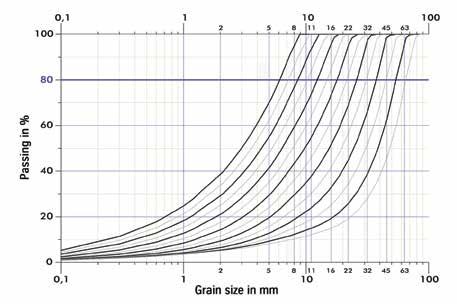
of 250 tonnes per hour (tph), can be seen in Figure 3.
Depending on the requirements of the producer, the plant can be designed as a stationary plant, a semi-mobile crushing plant or a wheel-mounted portable plant in which the crushers and the associated screens are combined into modules.
The 0-600mm run of mine material is discharged from a bin by means of a grizzly feeder where the initial primary screening takes place. Furthermore, a fine screening stage is used to remove natural contaminants such as soil and dust, which are not wanted in the end product.
In the first crushing stage, the material is crushed to 200mm by an EB 11-08 jaw crusher. From there, it is conveyed to a secondary G90 cone crusher where it is crushed to a size of 50mm in closed circuit with a screen. The product from the secondary crusher will already meet product standards, so the 25-50mm fraction can be screened out and sent to product stockpiles for use as railway ballast, drainage systems or other products.
In the tertiary crushing stage, a Kubria F/ M90 is used in a closed circuit to produce the required end product. The product is then split into the various product size ranges by a circular vibrating screen with four decks.
By adjusting the CSS of the secondary and the tertiary crushers, it is possible to produce
64 Quarry October 2019 a final product containing a particularly high portion of the desired fraction. Figure 4 shows some typical product curves for a fine and medium crusher, with different crusher settings.
Thanks to the optimised crushing chamber geometry, the product of the tertiary crusher contains a high portion of the required fraction, which means only about five per cent of the feed volume has to be recirculated. This results in lower wear of the crusher manganese and therefore higher availability for the crusher and reduced operating expenses.
Overall, the use of Kubria cone crushers allows the implementation of a plant concept characterised by efficiency, flexibility and a product that meets the highest quality requirements. With the use of modern control systems, a high degree of automation and user-friendliness can also be achieved.
A plant based on the flowsheet shown in Figure 3 was delivered to Cameroon earlier this year as a wheel-mounted portable plant system. All components were designed and manufactured by thyssenkrupp. The mobile modules, feed bins, surge bins and belt conveyors were taken from the standard range of processing machines. Assembly and commissioning was also conducted by thyssenkrupp, which provided a turnkey plant that was handed over to the producer.
COMPETITIVE GEAR The new Kubria series of cone crushers offers extremely competitive machines for coarse, medium and fine crushing to the quarrying industry. These machines have proven effective under the toughest conditions for crushing granite, basalt, gneiss and other hard rocks in the past few decades. Incorporating the latest technology, these machines provide:
A high cubicity finished product. Low wear and low operating expenses. Rapid crushing setting adjustment. Variable crushing chamber configurations for adaptation to product requirements. Ease of maintenance, with low maintenance downtimes.
A high level of operating reliability and process control with the Kubriamatic control system.
Solutions for mobile, semi-mobile or stationary plant requirements. •

LOW EMISSION ENGINE TRUCKS DESIGNED FOR MAXIMUM PRODUCTIVITY
QARTWORK v3.pdf 1 23/08/2019 3:58:53 PM K omatsu’s 63-tonne capacity HD605-8 rigid dump truck offers low emission Tier 4 engines which reduce fuel usage by up to seven per cent on previous models. Designed for quarrying, construction and smalleR scale mining operations, the truck features the optional Komatsu Traction Control System (KTCS) for optimum traction in all ground conditions, and the exclusive Automatic Retard Speed Control (ARSC) , which maintains control under full load on steep haul roads.
The HD605-8’s engine doesn’t require selective catalytic reduction or diesel exhaust fluid (DEF/AdBlue) to achieve Tier 4 emissions standards, reducing nitrous oxide and particulate matter emissions by 90 per cent on its Tier 3 engine equivalents.
The new engine incorporates an advanced electronic control system that performs high speed processing of all signals from sensors installed in the vehicle, providing total equipment control in all conditions.
Engine condition information is displayed via an on-board network to the cab monitor, providing all necessary data to the operator. In addition, this data can be accessed and managed via the KOMTRAX telematics remote monitoring system, ensuring owners and fleet managers stay abreast of machine health and maintenance requirements.
Like other Komatsu equipment powered by Tier 4 engines, far more detailed data about engine conditions and operation is monitored and transmitted via KOMTRAX, providing unconstrained visibility into equipment health.

According to Richard Feehely, Komatsu Australia’s national business manager for quarries, the HD605-8 is designed to deliver the safest, most productive and cost-efficient operation across a wide range of conditions.
“Operators have unmatched control and safety in the most difficult conditions through our integrated transmission and braking system – which is recognised as the best in the industry,” he said.
This includes Komatsu’s K-Atomics automatic transmission system with “skipshift” function for smoother operation, fully hydraulic wet multiple-disc brakes and retarder (802kW), the KTCS and the ARSC.•
Source: Komatsu Australia
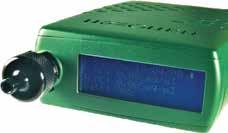