VOLUME 117/3 | APRIL 2025
PROCESSING PIONEERS
EDUCATION A NEW FRONTIER OF EFFICIENCY
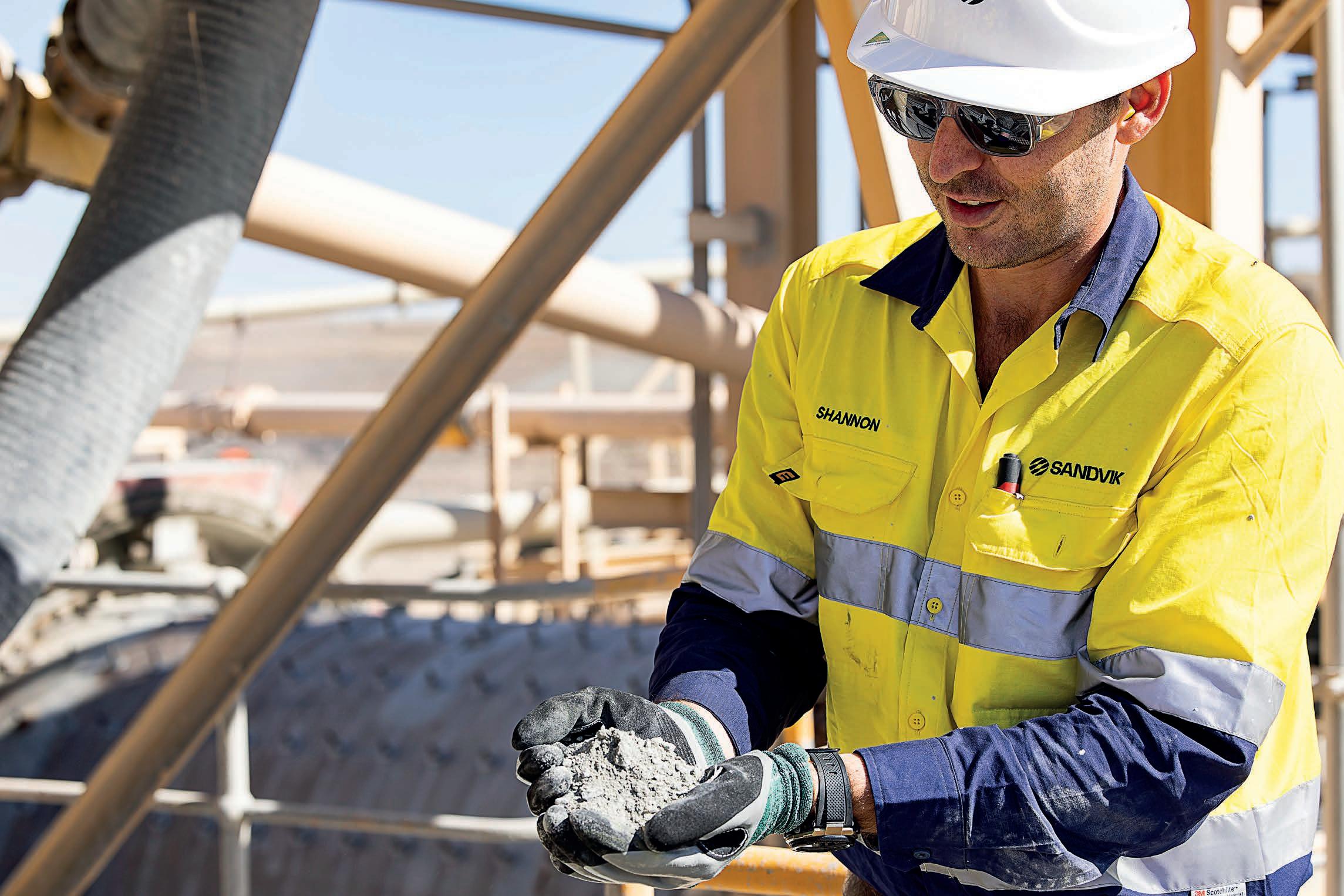

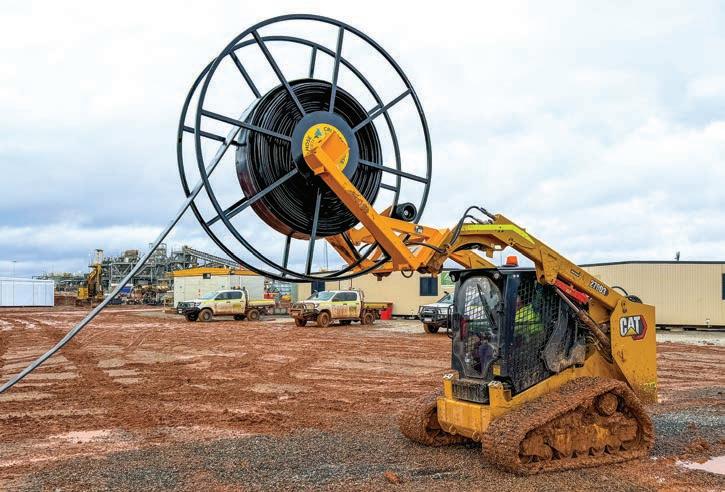
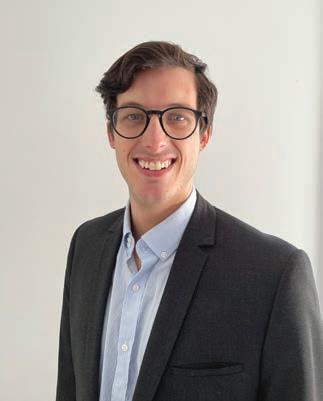
THE CORNERSTONE OF EFFICIENCY
WHILE MINERAL PROCESSING MAKES UP A SIGNIFICANT PORTION OF THE INDUSTRY’S ENERGY OUTPUT, OEMS AND TECHNOLOGY PROVIDERS ARE LOOKING TO CHANGE THIS.
There’s no doubting greater efficiencies could be achieved in mineral processing – a sector that consumes a significant amount of water and energy to refine materials into higher-value products.
According to Sandvik, which graces this month’s cover, the mining industry consumes 6–7 per cent of the world’s total energy usage, and almost half of that is consumed in the comminution process – crushing, screening, feeding and milling. There are opportunities for efficiencies, and original equipment manufacturers (OEM) are thinking outside the box to refine mineral processing operations through innovative solutions.
The likes of Sandvik, FLS, Sefar, Thejo, ifm, Metso and McLanahan are just some of the companies leading the way, with this edition taking the opportunity to showcase their products and methodologies.
Sandvik discusses its recently launched DeckMapp platform, which is set to transform screen deck maintenance by capturing, storing and sharing real-time data to present a single source of truth for all activities within the screen media lifecycle.
The OEM also spotlights its 800i cone crusher which, when combined with the new ACS-c 5 automation system, combines robust mechanical design with powerful, user-friendly automation to support diverse operational needs.
Since its introduction, FLS’ Reflux Flotation Cell has delivered drastic efficiency improvements for the mineral processing industry.
CHIEF EXECUTIVE OFFICER
JOHN MURPHY
CHIEF OPERATING OFFICER
CHRISTINE CLANCY
MANAGING EDITOR PAUL HAYES
EDITOR
TOM PARKER
Email: tom.parker@primecreative.com.au
ASSISTANT EDITOR
ALEXANDRA EASTWOOD
Email: alexandra.eastwood@primecreative.com.au
JOURNALISTS
OLIVIA THOMSON
Email: olivia.thomson@primecreative.com.au
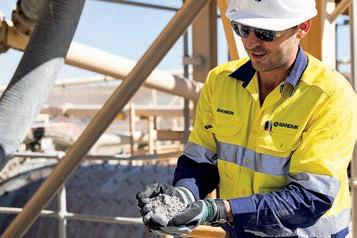
FRONT COVER
FLS global product line manager Lance Christodoulou spoke to Australian Mining about how the RFC eliminates the need for froth, enabling operators to separate minerals more effectively.
Elsewhere in this edition, we break down the Federal Government’s $22.7 billion Future Made in Australia policy and explore what it means for the local mining sector.
We also take the opportunity to analyse the global geopolitical landscape, investigating how the increased role of technology and automation and shifting environmental, social and governance (ESG) priorities have created a rapidly evolving landscape for mining companies. Global law firm White & Case offers its expertise on the matter.
Schlam introduces its new Hercules Ultra truck bed – the latest step in the company’s commitment to evolving and enhancing mining truck solutions.
Asia-Pacific’s International Mining Exhibition (AIMEX) is also in the spotlight as it prepares for its first instalment in Adelaide in September, while we also chat to a key sponsor of the upcoming WA Mining Conference and Exhibition in October.
Happy reading.
Tom Parker Editor
DYLAN BROWN
Email: dylan.brown@primecreative.com.au
CLIENT SUCCESS MANAGER
JANINE CLEMENTS
Tel: (02) 9439 7227
Email: janine.clements@primecreative.com.au
SALES MANAGER
JONATHAN DUCKETT
Mob: 0498 091 027
Email: jonathan.duckett@primecreative.com.au
BUSINESS DEVELOPMENT MANAGERS
JAMES PHIPPS
Mob: 0466 005 715
Email: james.phipps@primecreative.com.au
ROB O’BRYAN
Mob: 0411 067 795
Email: robert.obryan@primecreative.com.au
ART DIRECTOR MICHELLE WESTON michelle.weston@primecreative.com.au
SUBSCRIPTION RATES Australia (surface mail) $120.00 (incl GST) Overseas A$149.00
For subscriptions enquiries please contact (03) 9690 8766 subscriptions@primecreative.com.au
Tier 1 engineering company Sandvik leverages digitalisation as a cornerstone of its cutting-edge technologies to enhance the efficiency and sustainability of mineral processing. The Sandvik 800i cone crusher series reflects a commitment to the continuous evolution of design, materials and technology, with the new ACS-c 5 automation system taking this machine to new heights. Sandvik has also launched its new DeckMapp platform, which provides comprehensive tools to view deck history, share deck plans, visualise panel wear patterns and capture feedback. Through its range of product verticals, Sandvik is assisting miners unlock greater operational efficiencies, driving down costs and improve sustainability outcomes.
Cover image: Sandvik
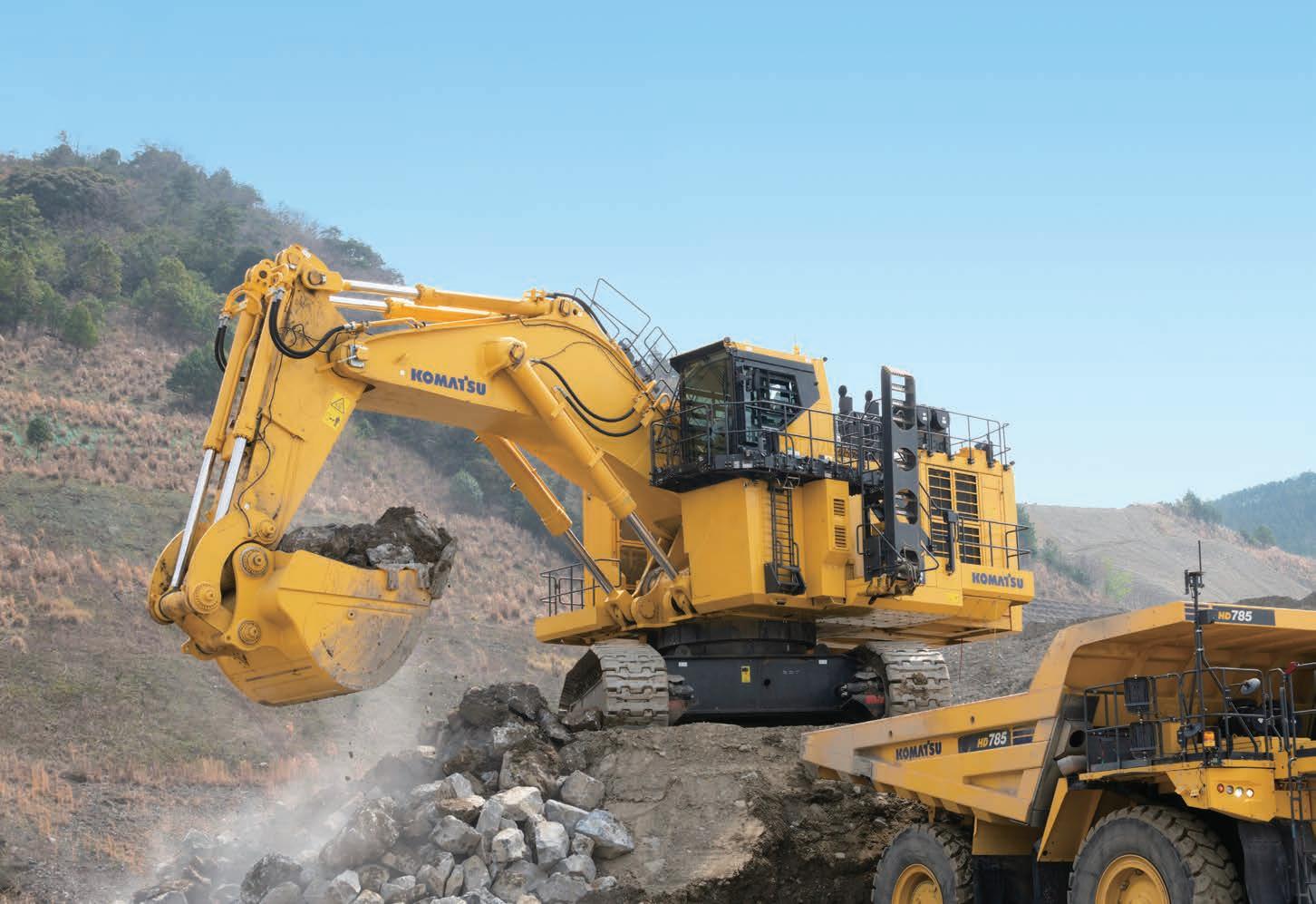
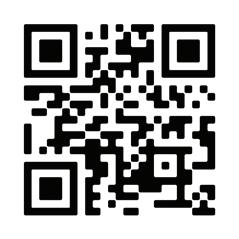
Introducing the PC3400-11 Excavator – engineered for peak performance with a 31% boost in productivity and 22% improved fuel efficiency. Featuring class-leading engine power, the longest reach, and the highest digging forces, it delivers a fast digging cycle to maximise your output. Optimised bucket sizes of 18m³ to 24m³ ensure perfect truck matching for 90t to 190t class mining trucks, making it the ultimate choice for efficient mining operations. Get more done, faster, and more efficiently!
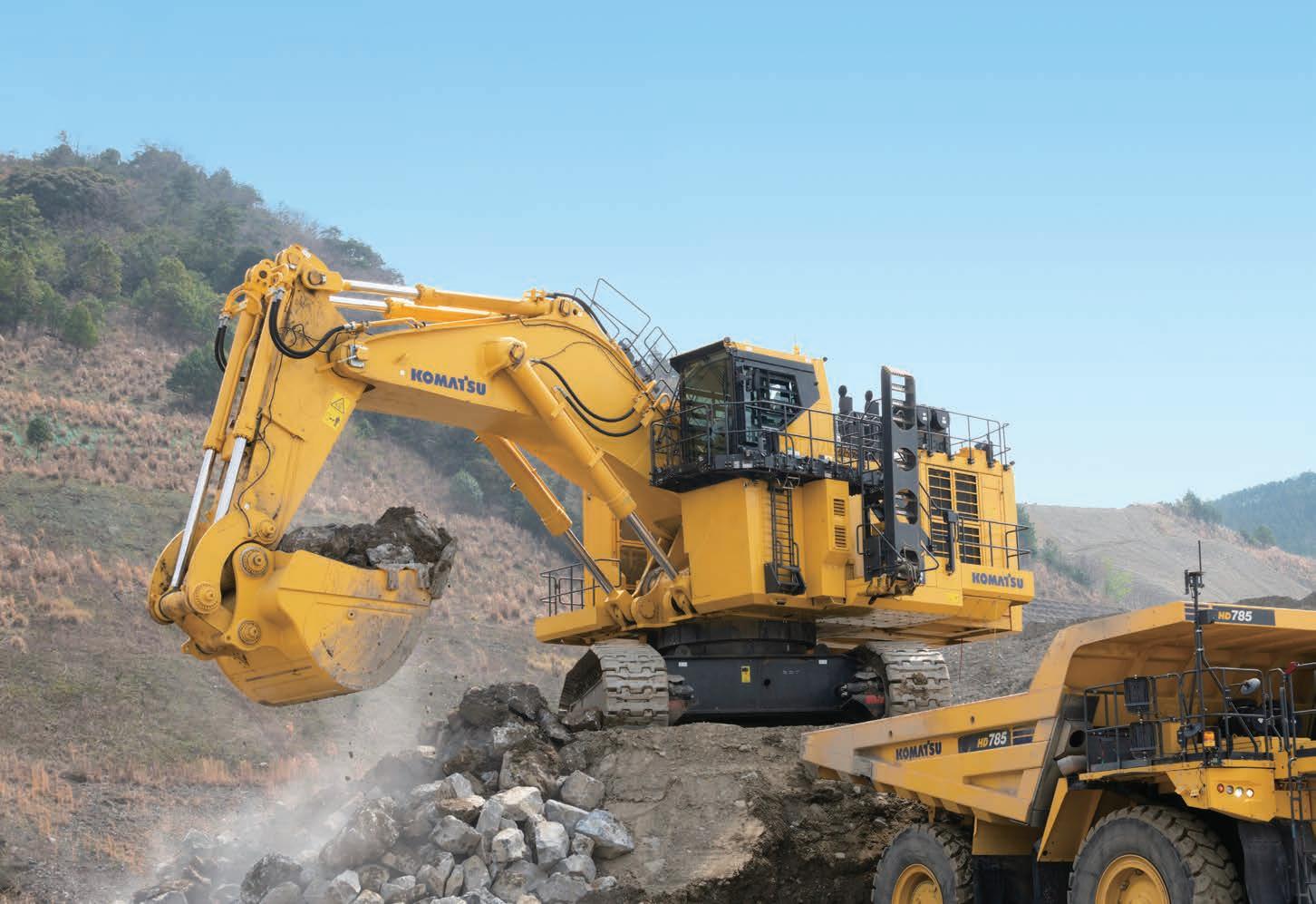
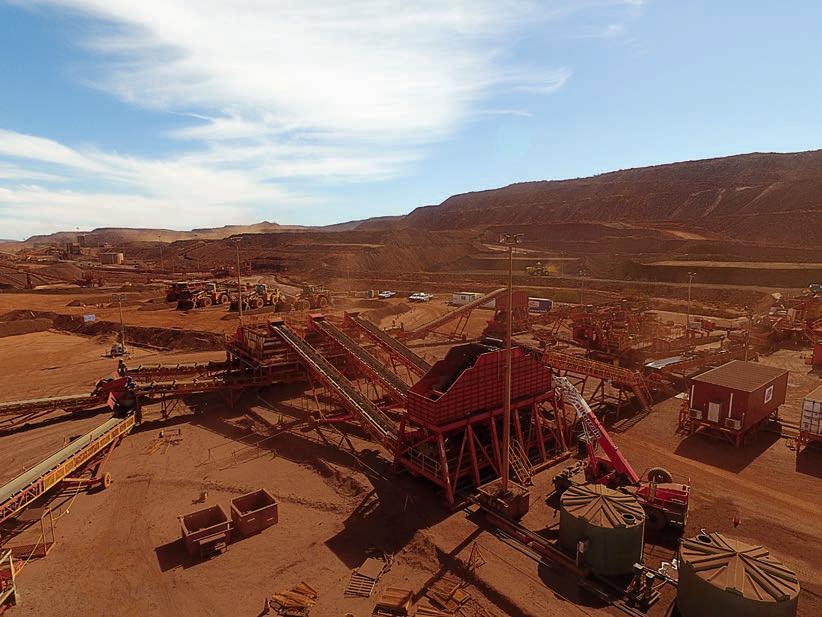
INSIGHT
Creating a renewable energy superpower Australian Mining breaks down the Federal Government’s Future Made in Australia legislation, and how the resources sector fits in as “the heart” of the policy.
16 MINERAL PROCESSING
The future of flotation FLS has developed an inspired flotation solution for the mining industry, delivering drastic improvements across all key metrics.
20 MINERAL PROCESSING
24 MINERAL PROCESSING
Driving data-driven operations

Minitab has developed comprehensive, easy-to-use statistical software that boosts productivity and saves costs on mine sites.
42 COMPANY PROFILE
Building blocks of the future VHM chief executive officer Ron Douglas sheds light on how the company plans to bring its flagship project online to meet growing rare earths demand.
46 COMPANY PROFILE
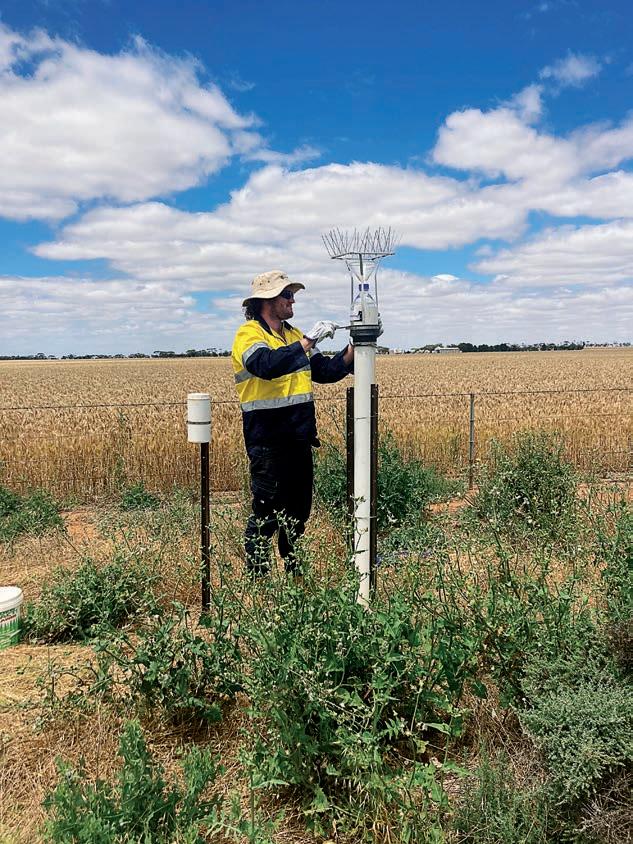
ore than the ‘powerlines guys’ ustralian Mining sat down with Genus managing director David Riches to discuss the company’s rapid growth trajectory.
54 EFFICIENCY AND OPTIMISATION
Triggering a chain reaction
Treotham discusses how its easy-to-install energy chain solutions can improve the functionality of mining operations.
62 SUSTAINABILITY
Leading the energy transition
Mining has a large part to play in the world’s transition towards net-zero.
72 SUSTAINABILITY
Safe, secure and environmentally friendly
Komatsu’s dedication to providing safe and environmentally friendly sites was recently bolstered by two new certifications.
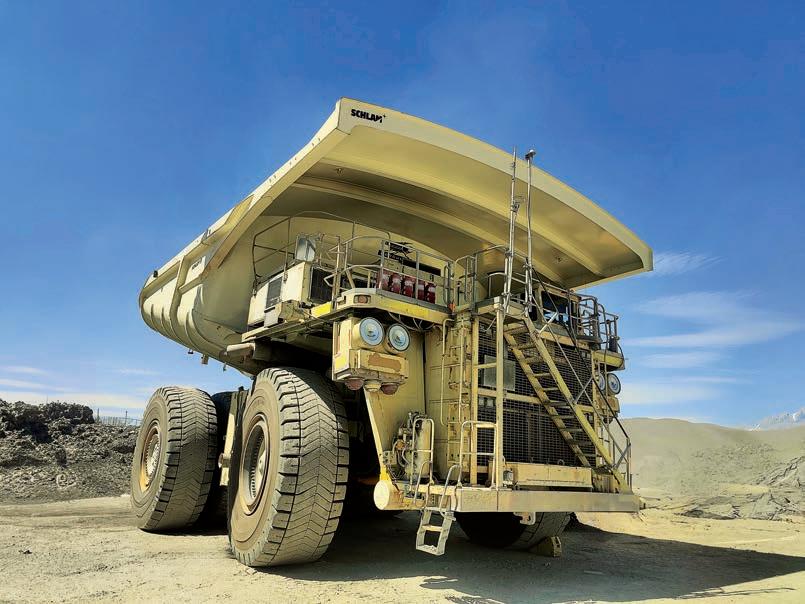
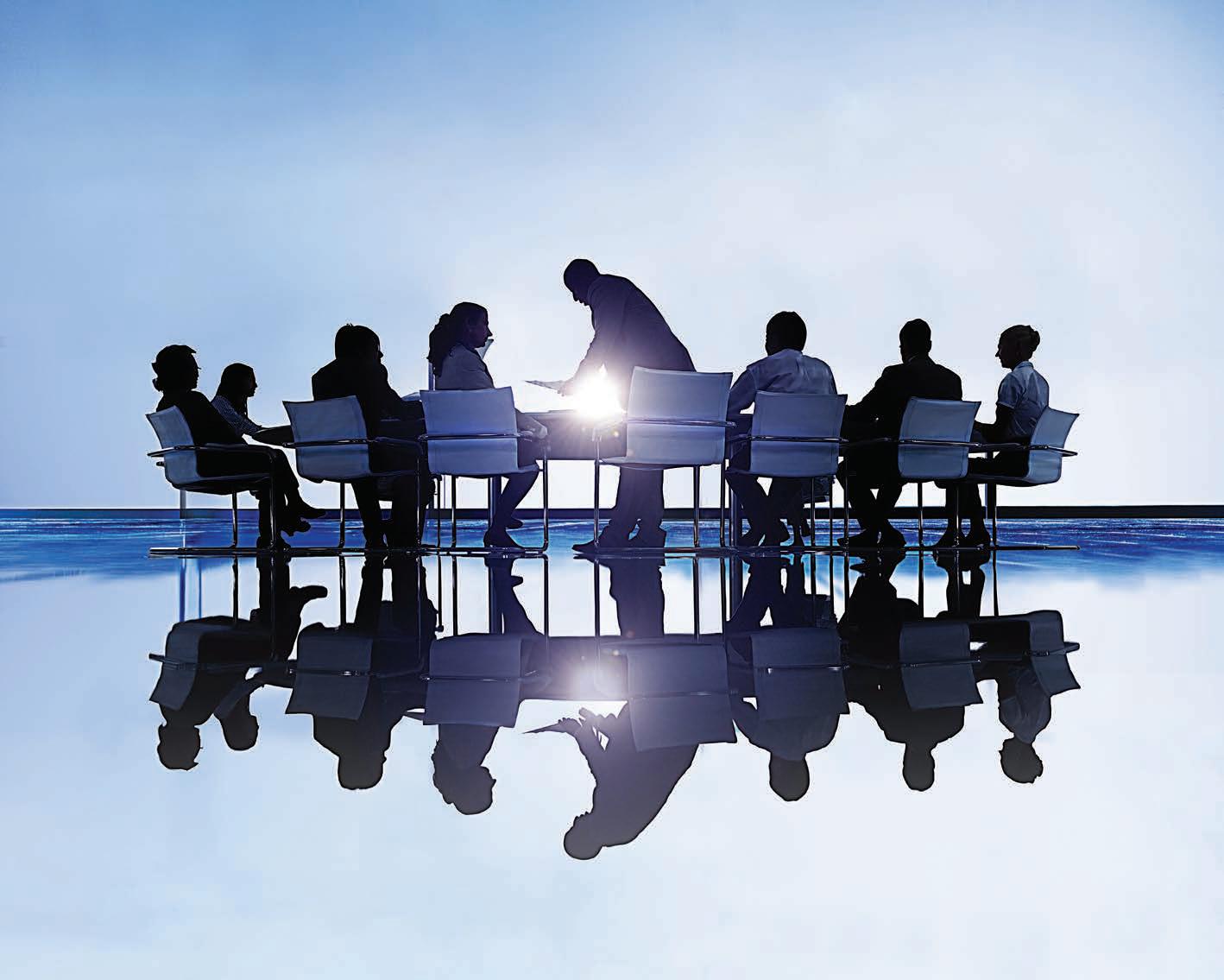
FOLLOW THE LEADERS: THE LATEST EXECUTIVE APPOINTMENTS
KEEP UP WITH THE LATEST EXECUTIVE MOVEMENTS ACROSS SIBANYE-STILLWATER, BHP AND FORTESCUE.
Sibanye-Stillwater confirmed that its current regional officer for southern Africa
Richard Stewart began his transition into the chief executive officer (CEO) role from March 1.
Stewart, who brings extensive experience in resources operations with more than 24 years in South Africa’s geological and mining industries, is a fellow of the Geological Society of South Africa and a registered natural scientist.
Stewart joined Sibanye in 2014 and has since contributed significantly to a successful and value-accretive acquisition and growth strategy.
The appointment comes as current Sibanye CEO Neal Froneman prepares to retire on September 30.
“Neal has led the Sibanye-Stillwater group since 2013, guiding the initial turnaround of the three mature, challenging gold mines that the group inherited from Gold Fields,” SibanyeStillwater chair Vincent Maphai said.
“From the significantly more profitable and stable base that was established, he subsequently drove the strategic growth and diversification of the group into what it is today – a multinational mining and metals processing company with a diverse portfolio of operations, projects and investments across five continents.”
Maphai thanked Froneman for his strategic leadership and commitment.
“I am sure that these sentiments are echoed throughout Sibanye-Stillwater, where Neal’s inspirational and values-
based leadership in the role he defined as ‘chief enabling officer’ will be sorely missed,” Maphai said.
“Neal leaves a business which is in good health, financially and operationally, with a clear and consistent strategy.”
Maphai said he and Froneman are immensely proud of Sibanye’s extraordinary achievements over the past decade.
“As Neal expressed to me, while he has the same enthusiasm for what he does and has lost none of his drive, he now wishes to spend more of his time with his family and loved ones and on his many interests,” Maphai said.
“Neal’s legacy extends far beyond his role at Sibanye-Stillwater and he is highly regarded as a thought leader globally.
“His prominent roles as chairman of the World Gold Council and coleading the Crime and Corruption workstream for business in South Africa, amongst other high-level engagements, suggest that he will contribute to the advancement of the global minerals industry in various ways in future.”
BHP chair Ken MacKenzie retired from the board on March 31, after more than eight years at the Big Australian.
MacKenzie joined the BHP board in September 2016 and served as chair from September 2017.
During his tenure, MacKenzie oversaw the strategic transformation of BHP’s portfolio towards future-facing commodities such as copper.
“It has been a privilege to serve as the chair of BHP for the last eight years and as a director for nine years,
and I am proud of what the board and management has achieved during that time,” MacKenzie said.
“BHP is a simpler, more productive and more resilient company and this has been a result of a talented and committed team focused on creating sustainable long-term value for our shareholders, our supply chain, partners and our communities.”
Succeeding MacKenzie is Ross McEwan, who has been an independent non-executive director of BHP since April 2024.
McEwan has over 30 years’ global executive experience, with specific expertise in capital allocation, risk management and value creation in complex regulatory environments.
Before joining BHP, McEwan was the National Australia Bank CEO for five years.
“It is an honour and privilege to succeed Ken MacKenzie as chair of BHP,” McEwan said.
“Under his leadership, the company is simpler, more agile and well positioned for the future. Ken will be remembered for his strategic decision-making, active institutional and retail shareholder engagement and outstanding capacity to see value, whether that’s in strategy, portfolio, operational excellence or capital allocation.
“As incoming chair, I am committed to generating long-term value for all our shareholders and will work tirelessly with the board and management to achieve this. I look forward to continuing to take this great company forward.”
In February, Noel Quinn, the former HSBC Holdings CEO, joined the Fortescue board as a nonexecutive director.
As HSBC CEO, Quinn was involved in several initiatives to facilitate public and private sector financing solutions for large infrastructure projects.
He is now bringing his 37 years of banking experience across a broad range of financial services to Fortescue.
Quinn’s appointment comes as Fortescue works to eliminate Scope 1 and 2 emissions at its Pilbara iron ore operations by 2030 without voluntary carbon offsets and carbon capture and storage, an initiative the company calls ‘real zero’.
“I am honoured to be joining the Fortescue board at a time when the company is pursuing its ambitious ‘real-zero’ journey, leading the way for industry to decarbonise and transition to a fossil-fuel-free future,” Quinn said.
“I look forward to bringing my experience in global banking to assist the company in achieving its long-term growth objectives and continuing to deliver on shareholder value.”
Fortescue executive chairman Andrew Forrest welcomed Quinn to the board.
“Noel is a highly respected leader who brings a wealth of international expertise and experience in finance and capital markets,” Forrest said.
“His deep understanding of the complexities of the global financial landscape will be invaluable as Fortescue continues to diversify into new markets and grow as a green technology, energy and metals group.” AM
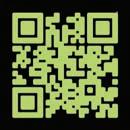
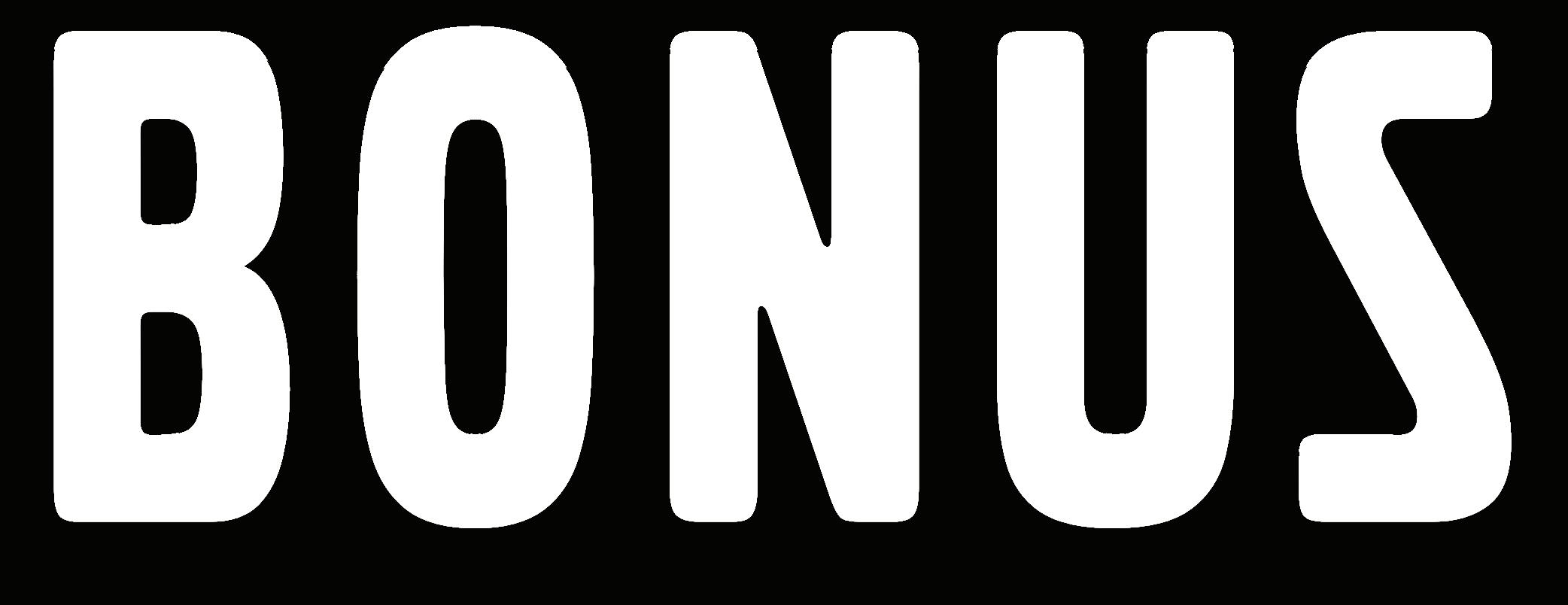

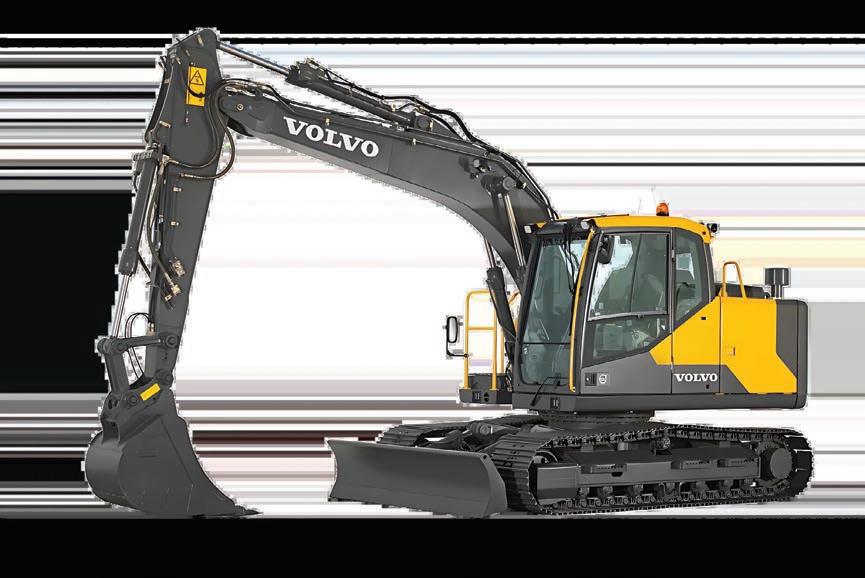



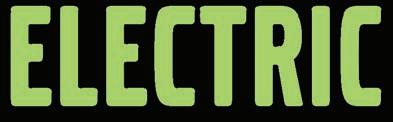
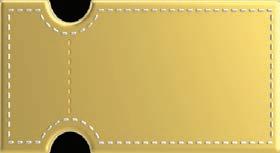

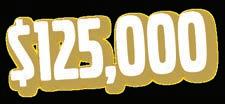
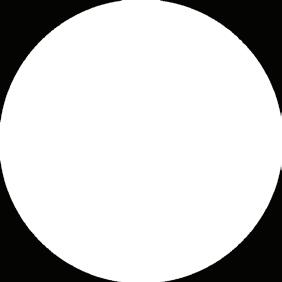





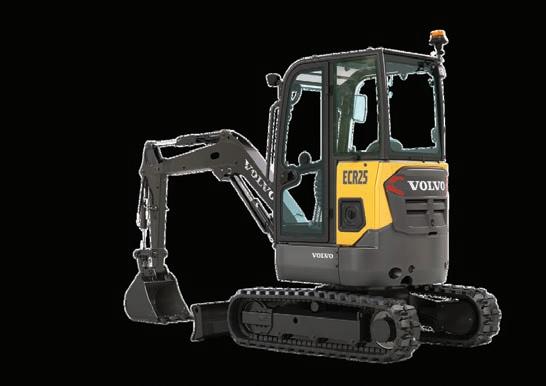

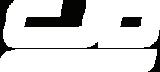
CREATING A RENEWABLE ENERGY SUPERPOWER
AUSTRALIAN MINING BREAKS DOWN THE FEDERAL GOVERNMENT’S FUTURE MADE IN AUSTRALIA LEGISLATION, AND HOW THE RESOURCES SECTOR FITS IN AS “THE HEART” OF THE POLICY.
With a plethora of critical minerals needed for decarbonisation beneath its surface, Australia is positioned to play a crucial role in the ongoing global energy transition.
In recognising this, the Federal Government announced its ‘Future Made in Australia’ plan in April 2024.
When unveiling the plan for the first time at the Queensland Media Club, Prime Minister Anthony Albanese said the Federal Government is committed to enticing more investment in renewable energy and critical industries.
“In this time of transformative opportunity, (the Federal) Government will not be an observer or a spectator –we will be a participant, a partner, an investor and enabler,” Albanese said.
“We will be guided by three principles. First, we need to act and invest at scale. Second, we need to be more assertive in capitalising on our comparative advantages and building sovereign capability in areas of national interest.
“Thirdly, we will continue to strengthen and invest in the foundations of economic success.”
But what does ‘Future Made in Australia’ mean, and how has the nation’s resources sectors reacted to the plan?
The agenda
The Future Made in Australia policy is essentially Australia’s response to the US’ Inflation Reduction Act (IRA), considered to be the largest climate investment in US history.
The IRA encourages innovation by giving firms various demand- and supply-side incentives to invest in developing and deploying clean energy technologies. It includes a $US30 billion manufacturing production tax credit that subsidises the downstream processing of critical minerals.
The Future Made in Australia Act 2024, which was granted royal assent on December 10, 2024, acts in a similar manner, establishing a National Interest Framework to guide the identification of priority industries and investments in the national interest.
Priority industries are identified under two streams. The ‘net-zero transformation’ stream will identify industries that can significantly contribute to achieving net-zero, as well as where Australia can increase comparative advantage. Renewable hydrogen, green metals and low-carbon liquid fuels fall under this stream.
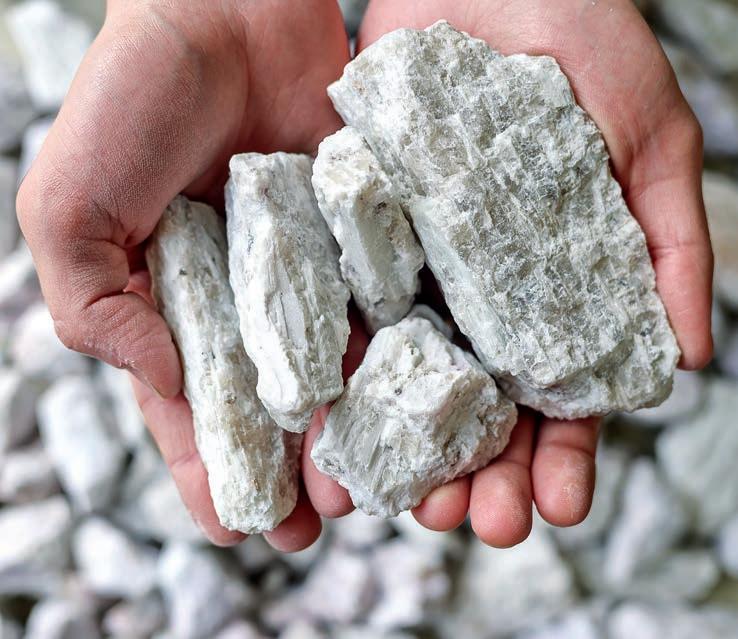
Critical minerals processing and clean energy manufacturing are part of this stream.
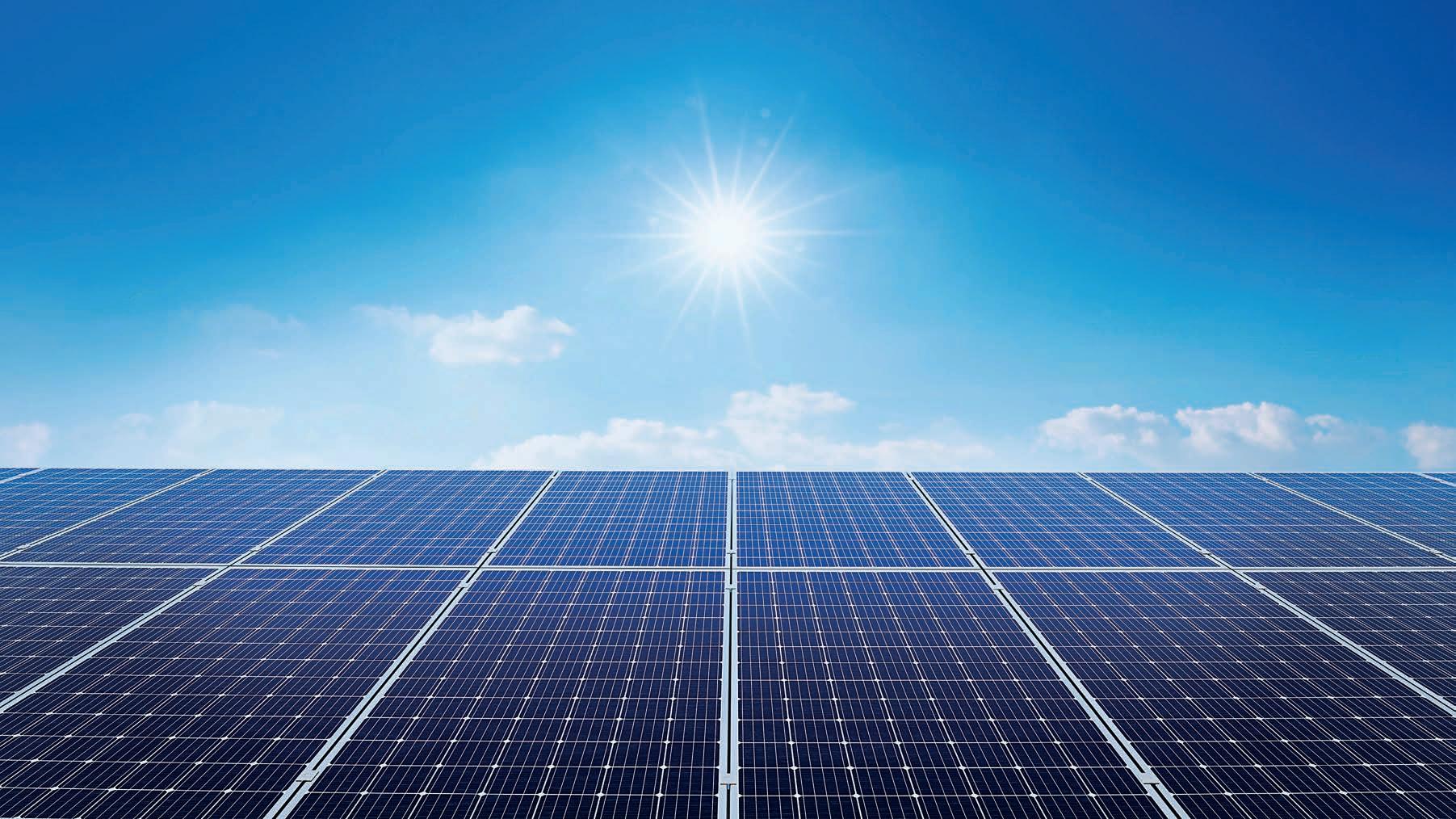
CRITICAL MINERALS ARE CRUCIAL TO BUILDING SOLAR PANELS AND BATTERY ENERGY STORAGE SYSTEMS.
The ‘economic security and resilience’ stream will identify sectors critical to Australia’s resilience that are vulnerable to supply disruptions, requiring support to unlock sufficient private investment.
The Federal Government’s 2024–25 Budget said the Future Made in Australia policy aims to maximise the economic and industrial benefits of the net-zero transition and secure Australia’s place in a changing global economic and strategic landscape.
The Budget allocated $22.7 billion to be invested in five key areas over the next decade. These include skills and training to build Australia’s future workforce, renewable energy, supporting national investment, utilising natural resources and critical minerals, and industrial innovation and technology. Key funding for the resources sector includes:
THE FEDERAL GOVERNMENT BELIEVES A STRONG RESOURCES SECTOR MEANS A STRONG AUSTRALIA.
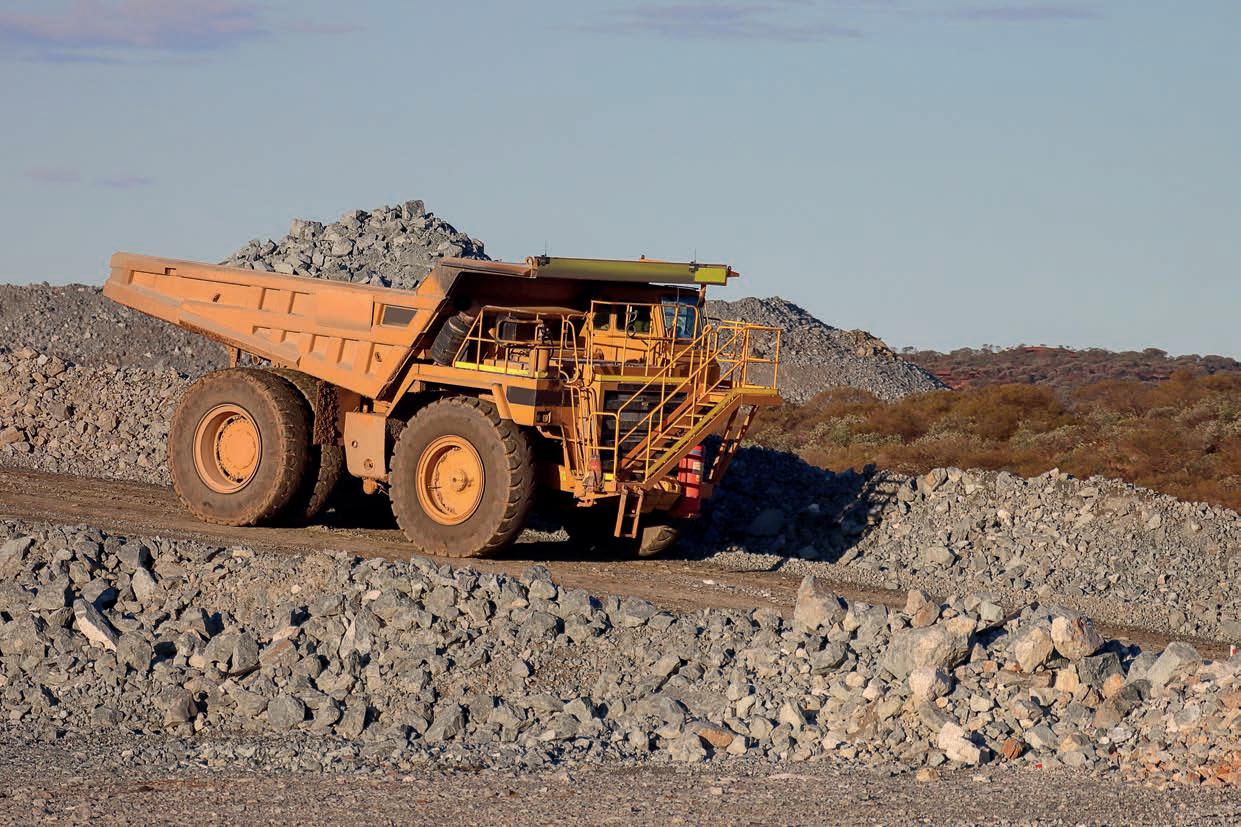
• $3.2 billion in investment to support the commercialisation of technologies critical to achieving net-zero
• $1.7 billion Future Made in Australia Innovation Fund to deploy innovative technologies and facilities linked to priority industries
• $556 million in investment over a ten-year period to support Geoscience Australia in mapping the nation’s endowments of critical minerals
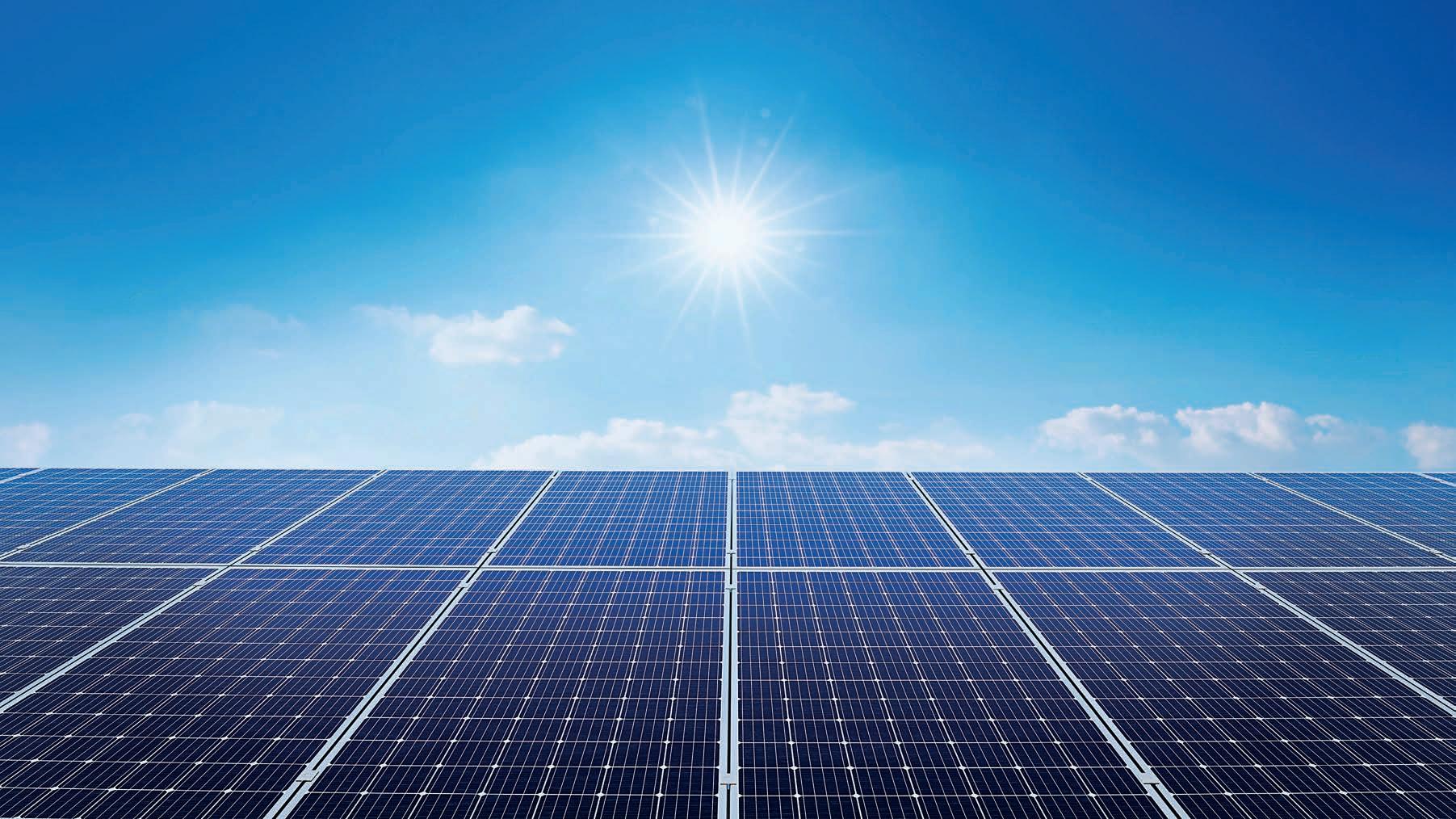
• $13.7 billion in production tax incentives for processed critical minerals and renewable hydrogen.
The Future Made in Australia (Production Tax Credit and Other Measures) Bill 2024, which was granted royal assent on February 14, will implement the production tax incentives to unlock private sector investment and aim to build a stronger and more diversified economy.
The Critical Minerals Production Tax Incentive will provide eligible recipients with a refundable tax offset of 10 per cent for the costs of processing some or all of the 31 critical minerals currently listed in Australia, and the Hydrogen Production Tax Incentive will provide a $2 incentive per kilogram of renewable hydrogen produced.
Both credits will be available for a maximum of 10 years between July 1, 2027, and June 30, 2040.
Industry response
Several industry bodies have welcomed the Future Made in Australia plan.
In February 2024, a report commissioned by the Association of Mining and Exploration Companies (AMEC) suggested that Australia should also introduce its own production tax credit if its mining and downstream industries are to remain globally competitive.
When the Future Made in Australia plan was first announced, AMEC chief executive officer (CEO) Warren Pearce said the policy was “very encouraging”.
“By leveraging our unique position with natural resources and expanding investment opportunities by developing new industries right here in Australia, our country can benefit from this once in a lifetime energy transition,” Pearce said in April 2024.
Chamber of Minerals and Energy of Western Australia CEO Rebecca Tomkinson said the $566 million investment in critical minerals mapping was “an intelligent way to leverage geoscientific data”.
“Exploration is the foundation of the resource development pipeline and the development of those resources is imperative to the industry’s ongoing contribution to the state and federal economies, employment, services, and social infrastructure,” Tomkinson said in May 2024.
Minerals Council of Australia (MCA) CEO Tania Constable echoed similar sentiments.
“Enabling public access to a richer set of nationally consistent pre-competitive data offers a detailed investment prospectus for mining companies but also paves the way for more precise and productive exploration efforts,” Constable said in May 2024.
Pearce and Tomkinson have supported the production tax incentives for critical minerals and hydrogen. According to the Federal Government, MCA also gave evidence supporting the Critical Minerals Production Tax Incentive.
Looking ahead
In March, the Federal Government lifted the lid on its plans for the $1.7 billion Future Made in Australia Innovation Fund, with $750 million of funding allocated to various projects.
The Federal Government earmarked funding for a range of initiatives, including the Green Aluminium Production Credit, the Green Iron Investment Fund, the Whyalla steelworks, critical minerals projects, and further funding in Geoscience Australia.
“Demand for green metals is expected to account for a third of the global metals market in coming years, this is an opportunity we cannot afford to miss,” Federal Industry and Science Minister Ed Husic said. “For a century, metalmaking has been the spine of Australian industry, and this investment is there so it continues to underpin our economic and national security resilience for decades to come.”
The funding will be administered by the Australian Renewable Energy Agency. AM
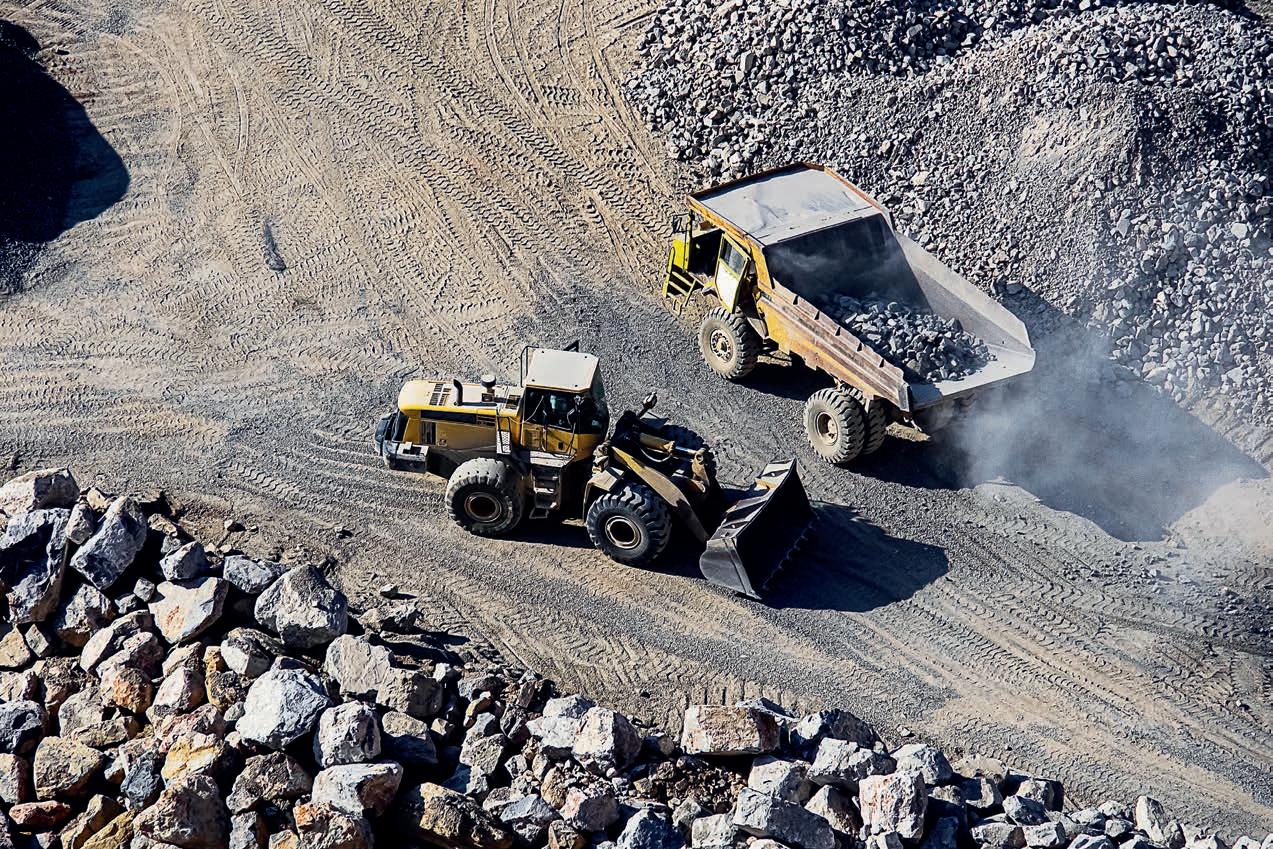
A RAPIDLY EVOLVING LANDSCAPE
ESG AND THE CURRENT GEOPOLITICAL LANDSCAPE HAVE THE POTENTIAL TO SIGNIFICANTLY IMPACT THE MINING SECTOR.
The Australian mining sector is no stranger to unpredictability, but 2025 presents a unique convergence of challenges and opportunities.
From geopolitical division and shifting environmental, social and governance (ESG) priorities, to the increasing role of technology and automation, mining companies must navigate a rapidly evolving landscape.
According to White & Case partner John Tivey, these factors will significantly impact investment, dealmaking and operational strategies into the future, with Australia’s position as a leading exporter of critical minerals placing it at the centre of global trade tensions.
The geopolitical landscape is reshaping how mining projects are financed, with increasing capital costs and cautious lending from traditional banks.
“In jurisdictions such as Latin America, we’re seeing a gradual comeback of export credit agency- and development finance institutionbacked project financing,” Tivey told Australian Mining.
“Supply chain realignment and regionalised financing are likely to make cross-border deals more complex, while interest rate and market volatility may slow investment.”
For Australian miners, securing diversified funding will be critical, particularly for projects in emerging markets or regions affected by trade restrictions.
The country’s critical minerals sector is also under heightened scrutiny, as Western investors prioritise sustainability while others focus on resource nationalism.
“Companies will need diversified financing sources and adaptive risk management strategies to navigate these challenges,” Tivey said.
Managing deal-making barriers
Cross-border transactions are becoming more complex as governments tighten regulations on foreign investments and push for greater domestic beneficiation of critical minerals.
This trend is particularly relevant to Australia, given its position as a major supplier of lithium, rare earths and other essential materials for clean energy technologies.
On December 6, 2024, the Federal Government announced grants to emerging critical minerals projects.
The five grants will be distributed through the International Partners in Critical Minerals program, providing critical minerals companies with up to $20 million in funding to grow supply chains with international partners.
Tivey believes the changing political landscape may slow deals.
“Nationalism and government policies are creating additional hurdles for international dealmakers,” he said.
“Inflationary pressures and supply chain disruptions are also driving up development costs, making it more difficult to achieve returns that justify major capital investments.”
For Australian miners looking to expand operations overseas or attract foreign investment, these dynamics mean deal-making will require greater strategic risk management and alignment with ESG priorities.
Additionally, engagement with local communities and Indigenous groups remains crucial, particularly in regions with strict regulatory frameworks.
“In this evolving and challenging environment, successful deal-making will require strategic risk management, ESG alignment, and the ability to navigate shifting regulatory landscapes,” Tivey said.
While decarbonisation remains a core objective for the Australian mining industry, companies are increasingly prioritising social license issues such as
community engagement, Indigenous rights and labour standards.
“We have seen these issues take precedence over decarbonisation efforts as companies face growing pressure from local stakeholders and governments,” Tivey said.
“While climate goals and decarbonisation remain important, they are currently secondary to the immediate need to address social and community concerns that are crucial for maintaining operations and securing governmental support.
“However, that doesn’t mean that decarbonisation has fallen off the radar, especially for investors in the sector. Even in a less stringent regulatory climate, the global push towards climate action and sustainability will continue to drive corporate strategies.”
Conversely, global political shifts could influence ESG priorities and changes to the US Government could result in a more relaxed regulatory environment, reducing short-term pressure for aggressive decarbonisation strategies.
For Australian miners, this means striking a balance between community expectations and long-term sustainability goals.
Investors remain focused on climate-conscious investing, meaning decarbonisation will remain a critical factor for maintaining access to capital.
Technology as an advantage In an increasingly fragmented market, Australian mining companies must turn to technology to drive efficiency and
SECURING FINANCING WILL REQUIRE A MIX OF TRADITIONAL AND ALTERNATIVE FUNDINGSOURCES.
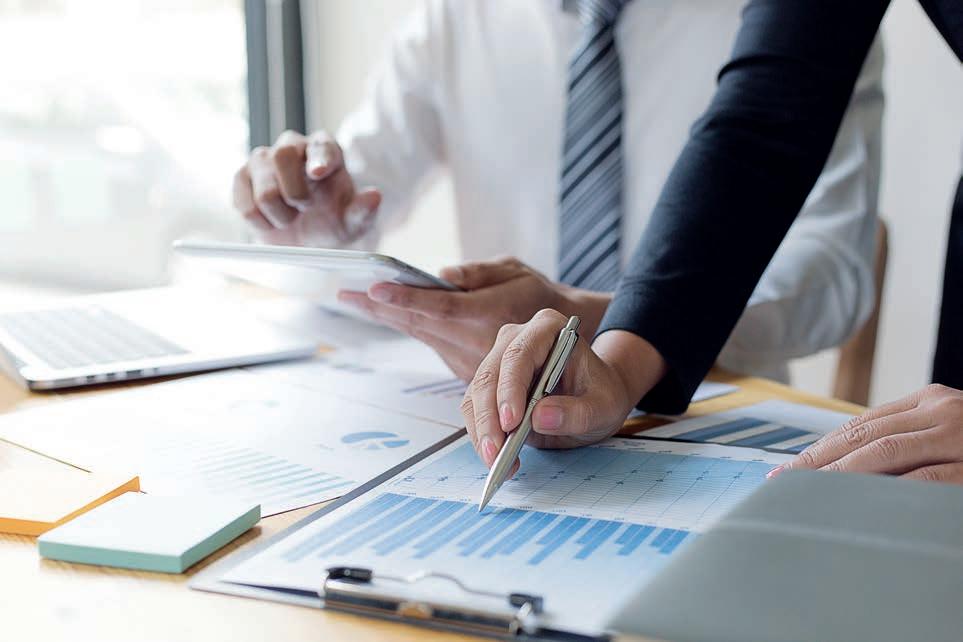
management, reducing costs and enhancing safety.
“The mining sector is still viewed as an ‘old-fashioned’ industry, but we are seeing a mindset shift as the advantages of new technologies become clearer,” he said. “As the industry faces geopolitical uncertainties, supply chain disruptions, and evolving regulatory environments, technological innovation offers a path to
Australia is already at the forefront of mining technology, with major miners such as BHP and Rio Tinto investing in autonomous haulage systems, AIdriven exploration, and digital twins for optimising operations.
Beyond operational efficiency, technology also plays a role in strengthening ESG credentials.
AI-powered monitoring systems,
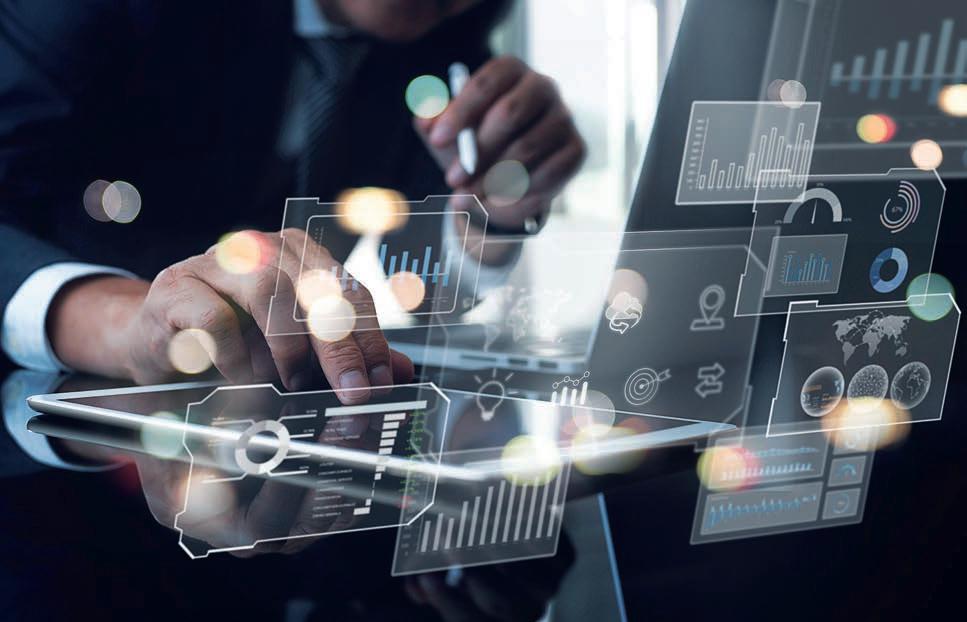
What lies ahead for Australian mining?
As geopolitical fragmentation, ESG shifts, and technological transformation reshape the mining sector, Australian miners must take a proactive approach.
Securing financing will require a mix of traditional and alternative funding sources, while deal-making will depend on careful risk assessment and regulatory compliance. At the same time, ESG strategies must align with both investor expectations and local community priorities.
While decarbonisation remains a key issue, social license concerns are taking precedence in many jurisdictions, requiring companies to engage more deeply with stakeholders.
Technology will be a defining factor in how Australian miners adapt to these challenges.
“The mining industry is at a crossroads, and those who strategically manage risk, embrace ESG priorities and leverage technology will be best placed to succeed,” Tivey said.
“Companies that invest in tech solutions will be better positioned to navigate market volatility and increase operational efficiency.
“Tech-savvy companies can access new markets, improve resource extraction in challenging environments, and strengthen their social license by meeting ESG expectations, all of which contribute to maintaining a competitive edge.”
MAKING MORE WITH LESS
SANDVIK’S BOUNDARY-PUSHING SOLUTIONS ARE INSPIRING A MORE EFFICIENT MINERAL PROCESSING INDUSTRY.
The mining sector has been a cornerstone of the world’s development for hundreds, if not thousands, of years.
As the world’s population continues to grow and we move towards carbon neutrality, society’s need for minerals, especially those critical to decarbonisation, is growing rapidly.
The mining industry is highly energy intensive. According to Sandvik, the industry’s direct consumption represents between six and seven per cent of the world’s total energy usage. Almost half of this energy is consumed in the comminution process – crushing, screening, feeding and milling.
The combination of a growing demand for minerals and falling ore grades is driving the industry to
comminution and the increasing energy per tonne of final product produced, the need for process efficiency has never been more important.
Innovative technology
Sandvik leverages digitalisation as a cornerstone of its innovation and cutting-edge technologies, which can significantly enhance the efficiency and sustainability of mineral processing operations.
“Not only is our latest equipment easy to operate, manage, maintain and service, but it also contributes to our industry’s need to reduce its environmental impact,” Sandvik Rock Processing Solutions president Richard Harris said.
“Through our close partnerships with customers and our unwavering focus
GRINDING ACCOUNTS FOR 40 PER CENT OF THE MINING INDUSTRY’S TOTAL ENERGY USAGE.
Advanced crushing solutions
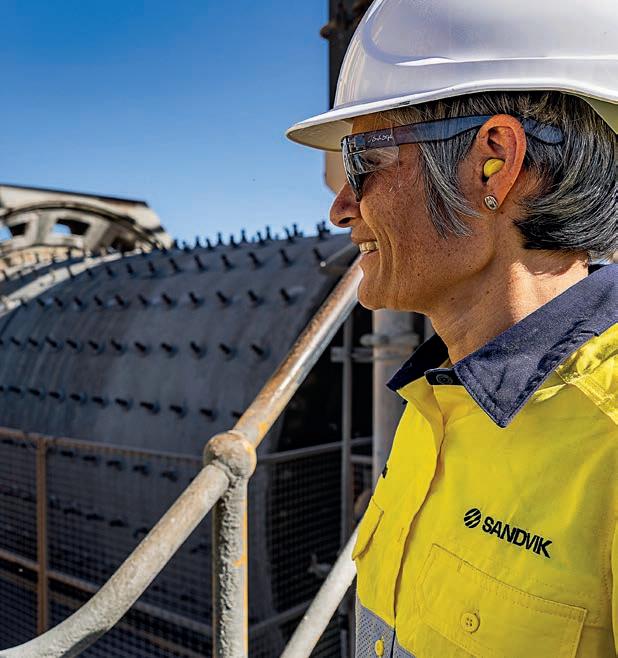
According to Sandvik experts, about 40 per cent of the mining industry’s total energy consumption can be attributed to the grinding process.
more and providing a finer feed to the milling circuit, significant efficiency gains can be made in the overall comminution process.
The Sandvik 800i cone crusher series

SANDVIK LEVERAGES DIGITALISATION AS A CORNERSTONE OF ITS INNOVATION AND CUTTING-EDGE TECHNOLOGIES.
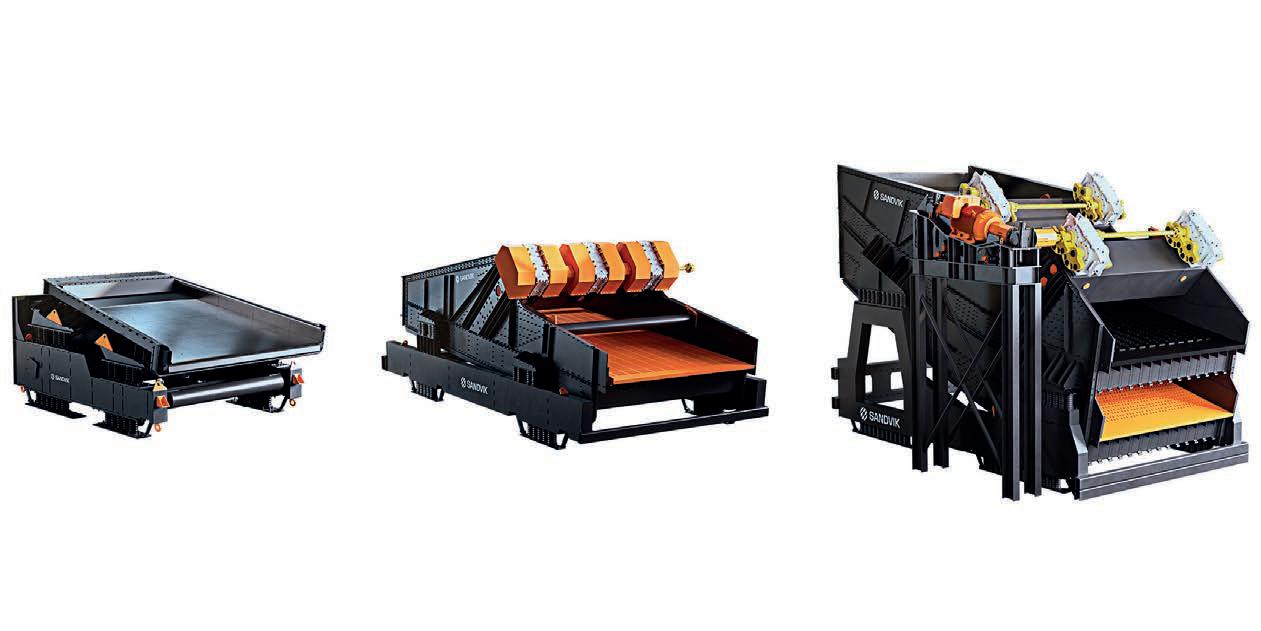
The latest models, integrated with the new ACS-c 5 automation system, combine robust mechanical design with powerful, user-friendly automation, supporting diverse operational needs.
These machines can be tuned to produce a very fine product, significantly reducing the load on the downstream grinding process.
Leading gold producer Gold Fields was able to take advantage of this with its new crushing and screening plant at the Agnew gold mine in Western Australia.
According to Gold Fields senior management, the finer feed from their new crushing and screening circuit has improved downstream mill performance, increasing the maximum throughput rate from 155 to 170 tonnes per hour (tph).
A comminution crushing and grinding survey demonstrated that the new circuit is around 18 per cent more energy efficient than the previous installation.
Maximising screening efficiency
Screening also plays a critical role in mineral processing. Operating in extremely harsh environments, vibrating screens and feeders accelerate large loads of highly abrasive materials with forces of up to 5G.
Thanks to recent acquisitions, Sandvik now offers an expanded lineup of heavy-duty vibrating screens, feeders and screening media which are well-adapted to the world’s toughest mineral processing applications, with machines capable of throughputs up to 8000tph.
Optimal screening efficiency is subject to pairing the right machine with the right screening media.
Choosing the best time to replace screening media is also critical to process efficiency – replacing too early can be a waste of money but waiting too long can lead to process inefficiencies.
The worst-case scenario is panel failure which can catastrophically impact operational efficiency. Screening media maintenance and replacing screening media at just the right time has always come down to the experience
and judgement of plant maintenance personnel – something of a ‘dark art’.
Leading digitisation
Sandvik has recently launched DeckMapp, a groundbreaking new digital platform for screen deck maintenance. The company believes that this highly innovative, cloud-based software solution is set to transform screen deck maintenance and drive substantial improvements in the efficiency and operational performance of mineral processing plants.
Accessible via laptop, tablet or mobile phone, DeckMapp captures, stores and shares real-time data to present a reliable, single source of truth for all activities within the screen media lifecycle.
According to Matt Cutbush, Sandvik Rock Processing Solutions’ digital solutions product manager, DeckMapp provides screening teams with comprehensive tools to view deck history, share deck plans, visualise panel wear patterns and capture feedback, as well as access maintenance plans and activity reports.
“By guiding operators through maintenance updates and wear assessments, DeckMapp ensures consistent data entry across the board, resulting in robust, reliable historical wear data for every screen in your operation,” Cutbush said.
“DeckMapp enhances data quality and formalises maintenance processes, thereby eliminating information inconsistencies that can adversely affect production and profitability due to rework and extended task durations.
“DeckMapp delivers real-time updates to ensure all team members are aligned, further reducing the risk of miscommunication and operational inefficiencies.”
A key feature of DeckMapp is the optional add-on WearApp, an innovative wear assessment system powered by artificial intelligence.
Users simply capture images of worn screening media panels with a smartphone or a tablet. WearApp then applies artificial intelligence (AI) to
automatically assess each aperture and calculates the amount of wear, panel efficiency and remaining wear life.
Cutbush said this revolutionary application not only saves substantial time but also delivers far greater accuracy over traditional manual wear assessment methods.
With DeckMapp and WearApp, plant operators can leverage data-driven insights to make smarter, more efficient maintenance decisions, and significantly reduce cost overruns associated with screen deck maintenance.
According to Cutbush, these enhanced capabilities allow processing plant operators to make more informed decisions regarding their screening media maintenance strategies, such as determining optimal replacement times based on actual open area rather than individual aperture wear.
The Sandvik range of screens and feeders has been enhanced by a new condition monitoring system called ACS-s, which allows operators to keep an eye on the condition of their machines 24–7.
Errors in maintenance and operations can lead to component damage. Early detection and diagnosis is vital in the
prevention of catastrophic machine failure and protracted plant downtime. ACS-s is designed to alert plant personnel to small problems before they can become big ones, which is critical to maximising plant uptime and efficiency.
Connected solutions for operational excellence
ACS-c 5 and ACS-s can be seamlessly integrated with SAM by Sandvik, a cloud-based digital assistant designed to support operational excellence in crushing and screening plants.
SAM captures data from all connected Sandvik equipment, offering a comprehensive overview of the entire operation. Plant operators can monitor equipment status, communicate across teams, receive alerts and notifications, and proactively order spare parts, all from one, centralised platform.
Commitment to environmental responsibility
Sandvik’s solutions are engineered to reduce energy consumption, minimise waste and optimise operational efficiency, assisting companies to improve their environmental footprint while delivering outstanding performance. AM
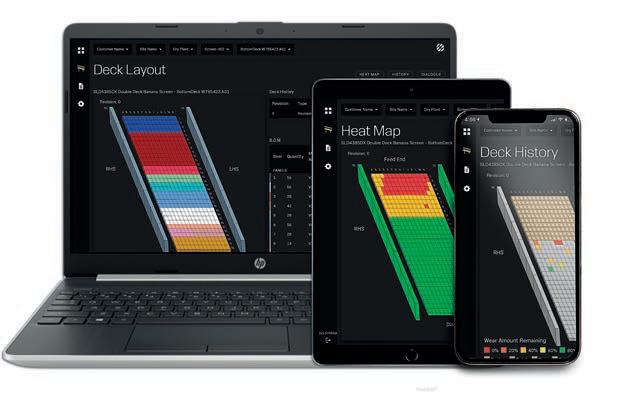
A DREAM PARTNERSHIP
PROACTIVE AND TRANSPARENT PARTNERSHIPS ARE DRIVING THE AUSTRALIAN MINING INDUSTRY INTO A NEW ERA OF EFFICIENCY AND SUSTAINABILITY.
MAX Plant and MACA have shared a long-standing partnership that has seen the deployment of more than 150 pieces of equipment over the years. It’s a relationship steeped in trust, with MAX Plant proving itself as a reliable original equipment manufacturer (OEM) capable of supplying Tier 1-spec machinery and solutions.
Having worked with MAX Plant for decades, MACA operations manager –crushing Asmir Kursumovic thoroughly understands the company’s recipe for success.
“We’ve partnered with MAX Plant since the early 2000s because they’re flexible, versatile and design-driven,” Kursumovic told they review that scope, and they give us a quality solution that is both reliable and cost-effective.
such as BHP, Fortescue, Atlas Iron and Rio Tinto but also provide solutions for
Tier 2 and 3 customers as well, whether the plant has a throughput of 1.5 million tonnes per annum, 15 million tonnes per annum (Mtpa), or anything in between.”
Kursumovic said MAX Plant has a “wealth of knowledge” to handle any mineral processing request, with company founder Craig Pedley and his team able to quickly coordinate the design and development of a solution.
“As a contractor, part of our success comes from the quick responses, the quick mobilisations and the quick plant designs which need to be shared with our mining clients,” he said.
“MAX Plant has all the necessary capabilities in-house, meaning they can quickly draft up designs and drawings aligned to MACA and (parent company)
of Tier 1 mining companies. This is reflective of the strong MACA–MAX Plant partnership.
“MAX Plant wants to understand the MACA and Thiess design and manufacturing standards, as well as our strategy and plan as a business,” Kursumovic said. “In practice, this means MAX Plant can design machines to the correct specification right from the outset.
“For example, if I need a JM1310 jaw crusher, MAX Plant already has full understanding of the required kit and specification. This is based on previous communication, previous projects and previous expectations of our equipment. This enables MAX Plant to turn around their solutions quickly by leveraging the relationship and understanding we have
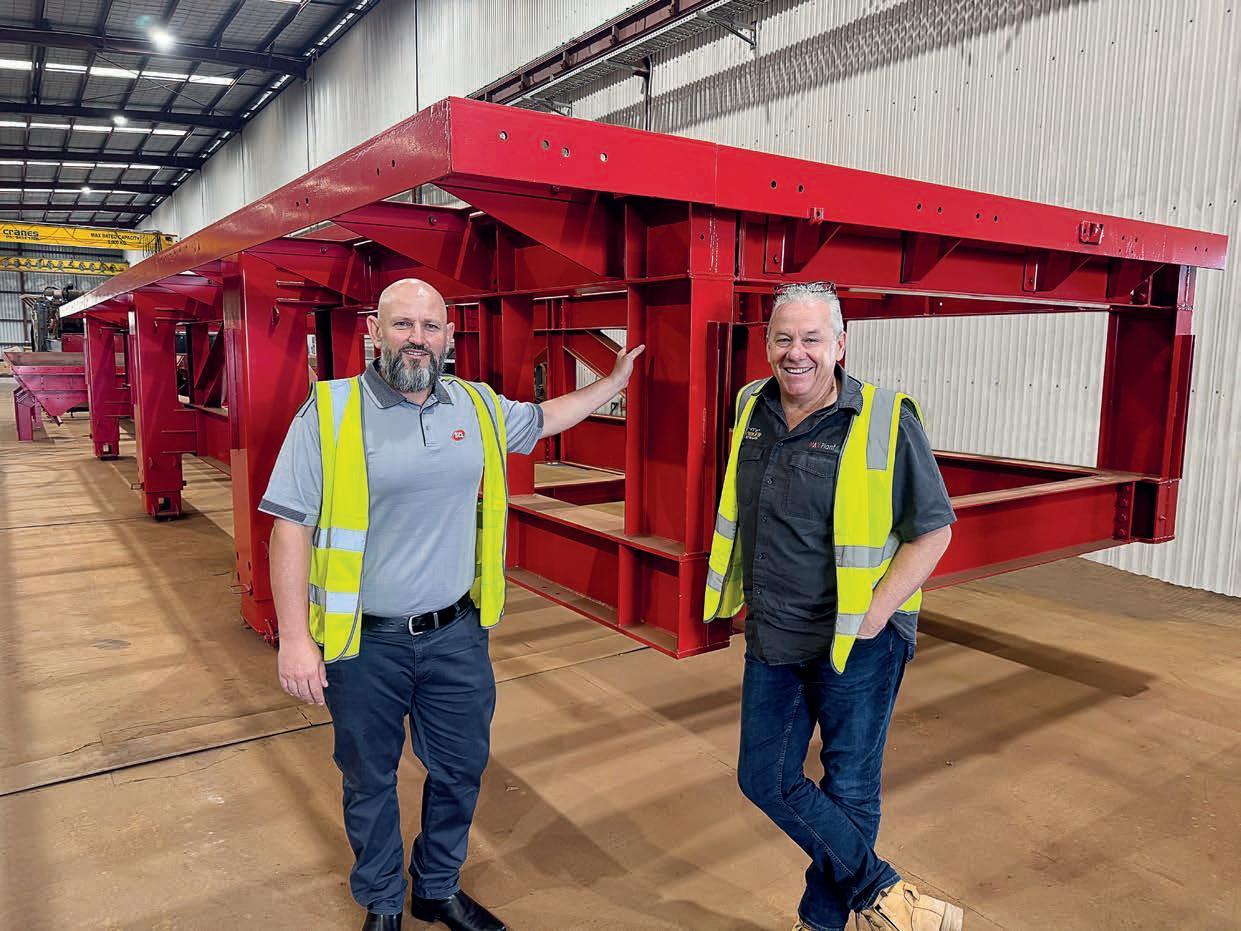

MAX PLANT AND MACA HAVE WORKED TOGETHER ON SOME OF AUSTRALIA’S BIGGEST MINING PROJECTS.

they are engaging with me or other MACA staff – everyone receives the same communication and treatment.”
As MACA and Thiess coordinate new projects and contracts, MAX Plant is in the engine room, designing and manufacturing bespoke solutions to the right specifications.
Kursumovic said some of MAX Plant’s solutions are “mind-blowing”.
“We’re in a process now where MAX Plant is refurbishing and redesigning some of our equipment for a new project we’re looking to mobilise in the next few months,” he said. “MAX Plant is regularly rebuilding equipment and
changing structures to suit different projects, because every project asks for something unique, whether it’s the size of the plant or the specific operating conditions.
“MAX Plant is an outside-the-box designer and manufacturer which proactively considers the operational outcomes of their solutions ahead of time. This means their solutions can hit the ground running right from the beginning of a project.”
It’s not just about providing a solution for new projects but also ensuring the continuous improvement of existing projects.
“MAX Plant is always engaging with our operational team to see how they can help,” Kursumovic said. “When we’re after a plant adjustment, we engage with MAX Plant, as the OEM, to come up with a solution.
“I’ll provide the operational scope for that adjustment and MAX Plant will go away and do the calculations and design and, 99.9 per cent of the time, they’ll come out with a solution that adds immense value.
“For one project, we had three or four different continuous improvements in a year, which involved adding extra features such as walkways, platforms, access points and egress points.”
As much as it prioritises operational improvements, MAX Plant also prioritises safety in its adaptations.
“We’re always looking at how we can eliminate confined spaces and working at heights,” Kursumovic said. “Craig and his team are always quick to adopt these considerations and implement them in their designs and future builds.
“This adds huge value to a solution that has already been optimised from an operational standpoint.”
MAX Plant and MACA’s partnership was on full display when they were tasked with supplying equipment to a Tier 1 client’s iron ore operation. The partners delivered a 12Mtpa plant with a spring capacity of up to 15Mtpa “in record time”.
“The infrastructure involved with this project was huge,” Kursumovic said. “MAX Plant welcomed me to their manufacturing facilities, where I was intimately involved in the verification process to see how the plant was built.
“I was able to meet the engineering and fabrication team and see how they go about their work. I needed to ensure the plant was meeting the client’s exact specifications, so having that visibility was important for the success of this project.”
Kursumovic said MAX Plant and MACA are currently working on two other projects to supply equipment to separate WA iron ore operations, suggesting the companies “would be flat out” in the next year or two, further proof – if any were needed – that this partnership is firing on all cylinders. AM
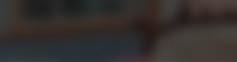
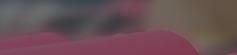
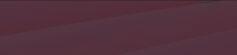


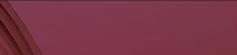

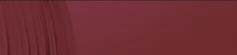
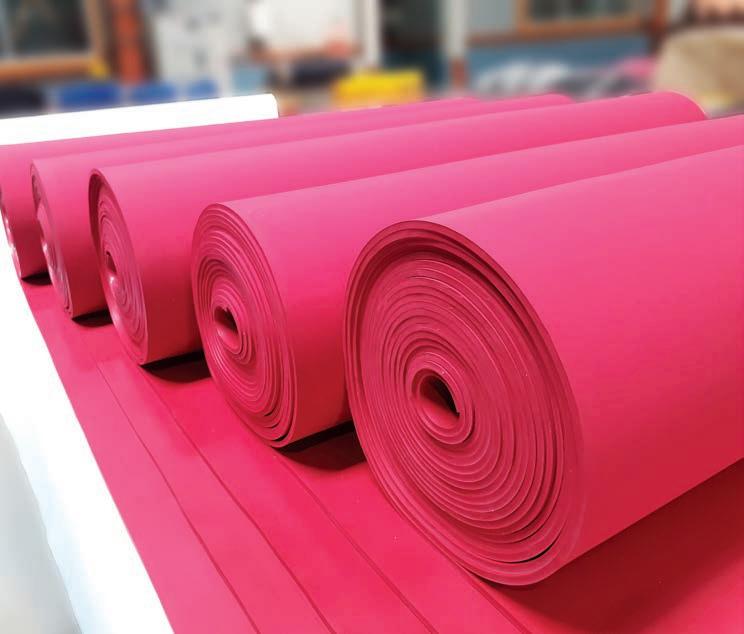
THE FUTURE OF FLOTATION
FLSMIDTH HAS DEVELOPED AN INSPIRED FLOTATION SOLUTION FOR THE MINING INDUSTRY, DELIVERING DRASTIC IMPROVEMENTS ACROSS ALL KEY METRICS.
The REFLUX Flotation Cell (RFC) is reshaping flotation technology as we know it, offering substantial improvements in recovery rates, energy efficiency, and water savings.
The innovative flotation machine, developed by global mineral processing pioneer FLSmidth (FLS), operates in a frothless environment, delivering significant efficiency and sustainability benefits for mining companies.
Lance Christodoulou, FLS global product line director – REFLUX Technologies, spoke to Australian Mining about the RFC’s cutting-edge design, its advantages over traditional flotation methods and the impact it is having on mining operations across the world.
Unlike conventional flotation tanks that rely on a froth layer to separate valuable minerals from waste, the RFC eliminates the need for froth, instead using a high-volume bubbly mixture. This enables operators to separate minerals more effectively.
“The REFLUX Flotation Cell is a high-intensity flotation machine,” Christodoulou said. “It delivers staged flotation in a frothless environment, so there’s no discernible froth pulp interface.
“The machine contains inclined channels in the separator to help segregate the bubbles from the liquid – a novel approach that mitigates common issues with traditional flotation cells, such as froth breakage, drop-back losses, and stagnant zones that hinder recovery.
“All open tank flotation machines have a froth layer and a pulp layer.
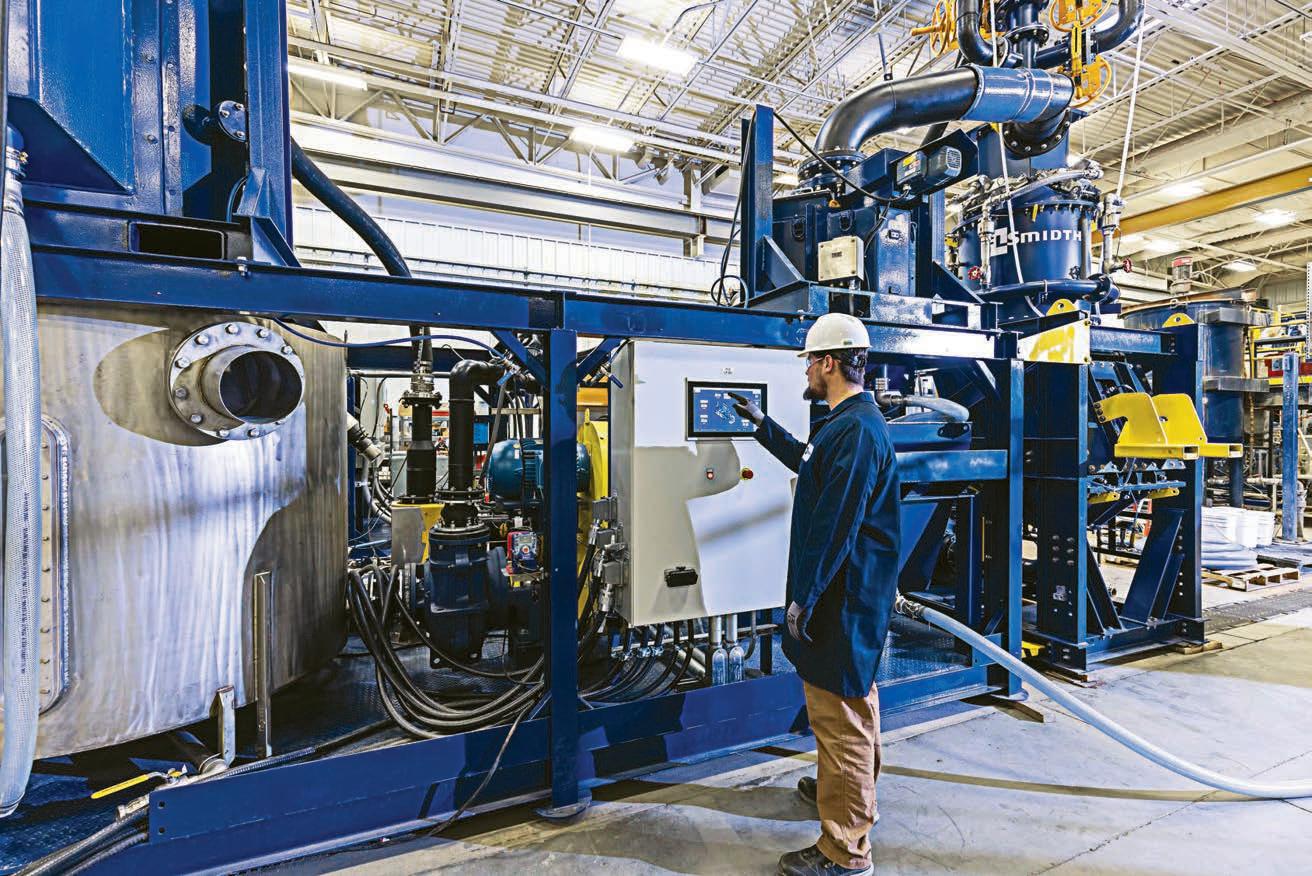
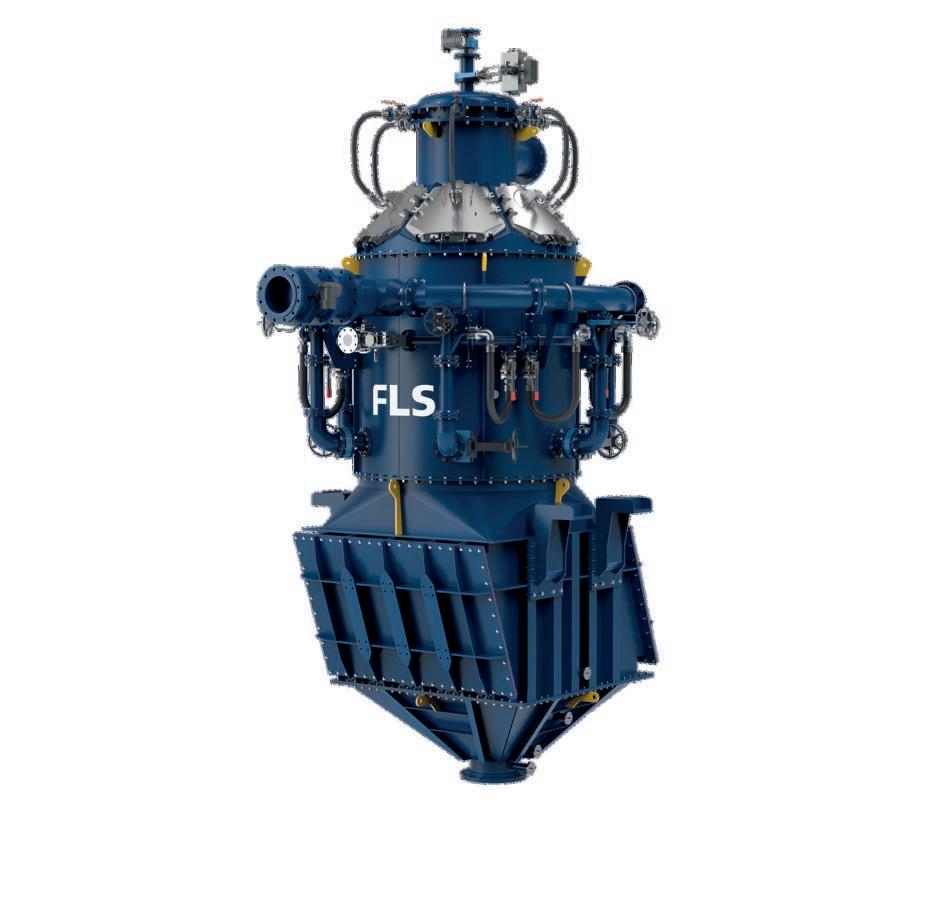
significantly increasing recovery rates.
“We’ve seen applications where it’s up to 10 times faster in terms of kinetics. If you need 10 minutes of residence time in a traditional flotation setup, you only need one minute with the RFC.”
This increase in processing speed means mining companies can achieve the same output with a significantly smaller flotation footprint, reducing capital and operational costs.
The RFC has demonstrated success across a range of mineral applications, including copper, gold, lead, zinc, nickel, potash, graphite and coal.
The technology is not only limited to specific ore types, but also excels in various flotation applications, such as scavenger, rougher and cleaner circuits.
“In scavenger applications, we see a major footprint reduction,” Christodoulou said. “The RFC shifts the grade–recovery curve, which means we can process more material using significantly less space.
“In rougher applications, we can produce a much higher-grade concentrate, which reduces the need for multiple cleaning stages.”
By reducing the number of cleaning stages, the RFC simplifies the flotation process, lowering costs while maintaining – or even improving – product quality.
With the mining industry under increasing pressure to reduce energy consumption and improve water efficiency, the RFC is delivering substantial savings in both areas.
“The high kinetics of the RFC means material moves through the system much faster, so we require a much smaller footprint,” Christodoulou said.
“We don’t have a direct mechanical mechanism driving the flotation process – it’s all hydraulic – so energy consumption is reduced by 30 to 60 per cent compared to traditional flotation systems.
“The water savings are also significant. If you look at a conventional column flotation cell, you need a large amount of wash water to maintain efficient product cleaning.
“With the RFC, because we reduce the flotation cross-sectional area, we can achieve up to 70 per cent savings in air and water supply.”
The RFC has already delivered impressive results in mining operations. One notable case study involves a copper concentrator, where FLS conducted extensive testing on the rougher, scavenger and cleaner circuits.
“The copper plant required about 30 minutes of retention time, but we were able to achieve the same results in just three minutes,” Christodoulou said.
“The client was so happy with the results that we’re now working with them to implement a full-scale RFC at their operations.”
Such outcomes highlight the realworld impact of the RFC, demonstrating its potential to transform mineral processing operations.
FLS works closely with its clients to install and optimise the RFC for specific mineral processing environments, including after-market service.
“We provide full support from commissioning to overseeing installation,” Christodoulou said. “We also have a team of site service personnel available to assist, and I personally stay involved to ensure a smooth transition for all RFC installations.”
As the RFC makes waves in the mining industry, FLS continues to refine and improve its design.
“We’ve already made some mechanical design adjustments based on industry feedback, and as the product matures, we’ll continue to optimise it,” Christodoulou said. “But I don’t see a fundamental change in the product’s approach because it’s quite unique and novel in the flotation industry.”
Christodoulou also sees a broader shift in the mining sector, with companies becoming more receptive to new flotation methods.
“There are multiple new flotation technologies emerging, and all of them are gaining traction,” he said. “It’s great to see the industry moving forward and
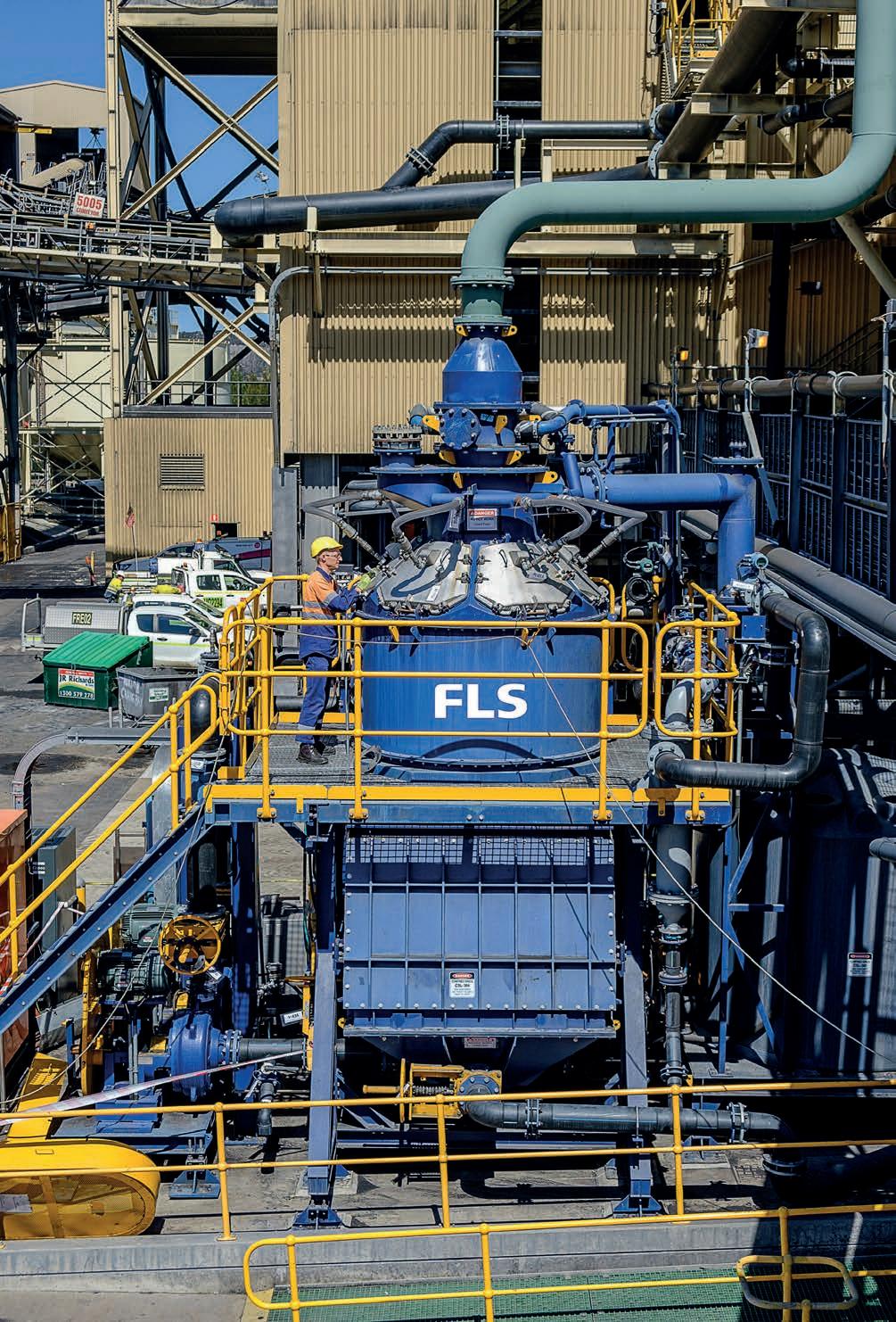
exploring better alternatives to what’s been done for the last 100 years.”
Beyond efficiency gains, the RFC plays a key role in improving sustainability outcomes. By extracting more valuable material from ore, it reduces waste and improves overall resource efficiency.
“The flotation technology is very efficient, so we’re getting much more out
of what we put in,” Christodoulou said. “With higher recoveries, we’re ensuring that valuable material isn’t lost and wasted.”
With its groundbreaking approach, high efficiency, and sustainability benefits, the RFC represents a significant advancement in flotation technology.
As mining companies worldwide continue to seek smarter, more
cost-effective solutions, the RFC is proving to be a key innovation that meets both economic and environmental demands.
Backed by FLS’ commitment to support and continuous improvement, the RFC is well-positioned to drive the future of flotation technology and help mining companies optimise their operations for years to come. AM
AN INGENIOUS FILTRATION SOLUTION
SEFAR’S PREMIUM FILTRATION SOLUTIONS ENABLE MINERAL PROCESSING OPERATIONS TO BOOST PERFORMANCE AND ENHANCE SUSTAINABILITY.
The global mineral processing industry is under the pump to sustainably produce highquality minerals.
With companies facing profitability challenges due to fluctuating market prices, rising operational costs and strict environmental regulations, it’s never been more important for those on the frontline of mineral production to optimise operational efficiency.
Addressing these issues requires a focus on process optimisation, technology investments, and strategic resource management.
Sefar, which controls every step of its manufacturing process, combines extensive application expertise with a leading fabric portfolio to deliver customised filtration solutions that tackle these core challenges.
By focusing on the continuous improvement of filtration processes, Sefar aims to reduce clients’ total cost of ownership, enabling them to achieve a sustainable and profitable future.
Forming the right partnerships
Establishing partnerships with suppliers is crucial to optimising filtration processes and achieving the best production results. These partnerships ensure access to the latest technologies, materials, and expertise, boosting performance, reducing costs, and enhancing sustainability.
This is where Sefar comes to the fore.
Through its supplier relationships, Sefar has established a product portfolio to combat insufficient filtration retention and accelerate separation for increased capacity and highmaintenance demands.
Sefar clients are finding they can quickly identify the root causes of their issues, pinpointing key areas of concern and implementing tailored solutions.
This includes a prominent alumina producer, which saved $300,000 in filter cloth expenses by adopting Sefar’s solutions.
By rigorously analysing the client’s processes, Sefar developed a specialised cloth for the alumina industry, one that not only vastly outperforms previous materials but also promotes enhanced flow throughout its operational lifespan.
Alumina production
Matching the correct fabric with the filtration process specifications is key to achieving higher flow rate, filtrate quality, cloth longevity, cake release, and cleaning efficiency of alumina.
Sefar’s fabric demonstrated exceptional recovery from overflocculation events, showing significantly improved durability after caustic washing. The previous fabric typically lasted 1800 hours, while the new Sefar fabric lasted 3000 hours on average, marking a substantial increase in performance.
Once the new filter cloth was implemented and the much-improved filtration process was in place, additional steps were taken to see how downtime and maintenance could be lowered.
When fitting, cloth closure was more difficult due to the fabric being thicker and more slippery. It was therefore more difficult to install filter media.
In response, Sefar introduced a zipper closure for the alumina industry’s commonly used Kelly filter, eliminating
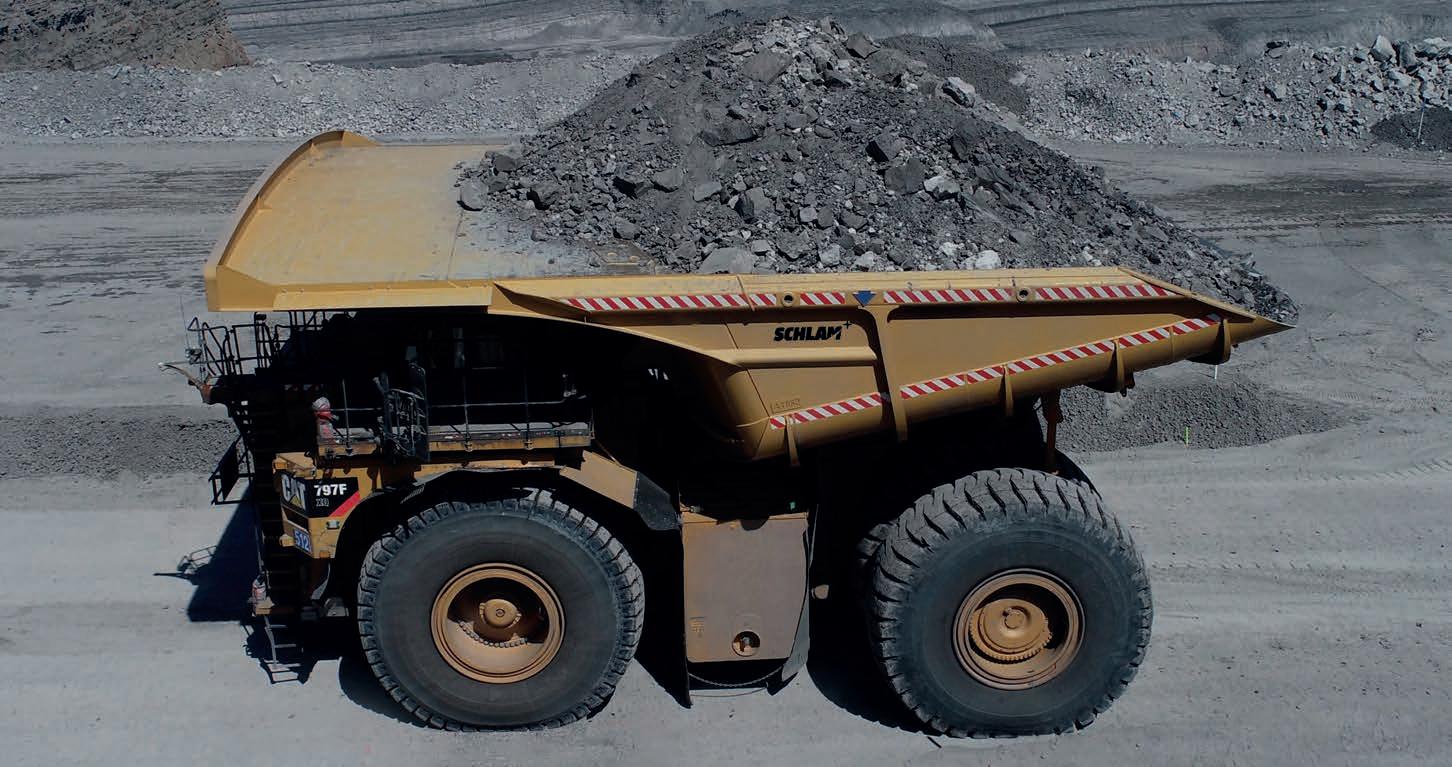
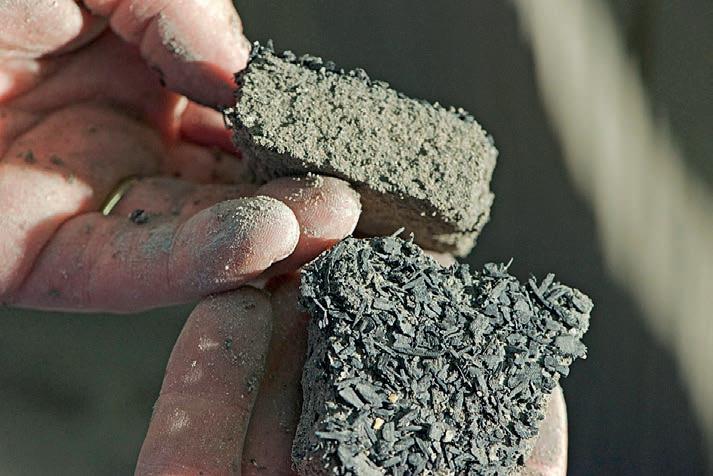
The zipper closure delivers more closure consistency of the filter media, achieving improved tightness and conformity. It also saves time, removing the need to apply thousands of staples to filter media, improving workplace sustainability in the process.
With close-fitting zipper lugs, the zipper closure doesn’t require a cloth flap to prevent solids from passing through the zip itself, saving on materials while preventing operational headaches.
Combine Sefar’s patented fabric with the zipper closure and alumina producers have access to a solution that will save them time and significant capital and operational expenditure.

The innovative cloth from Sefar might be slightly more expensive due to its extra thickness and quality, but it has significantly lowered the total cost of ownership, resulting in a marked reduction in overall filtration expenditure.
Understanding specific filtration needs
Whether you’re a technician installing filter media or a chemical or metallurgical engineer supervising the entire mineral production process, a comprehensive understanding of your operation is crucial.
According to Sefar Oceania managing director Max Wijasuriya, it’s not enough to simply solely focus on the filter cloth’s performance; achieving optimal separation of your final product requires a keen awareness of how every element of your process interacts.
“We work closely with our customers, applying a holistic
approach to enhancing the efficiency and effectiveness of their processes,” Wijasuriya said.
“It’s the people at Sefar that sets us apart. Our domain expertise and commitment to finding innovative solutions has seen us work with some of the biggest players in mineral processing. Many people don’t realise that Sefar is nearly 200 years old and comes with a pedigree of knowledge and capability that is second to none.”
In developing its products, Sefar controls every step in the manufacturing process, whether the company is selecting polymer for yarn production, weaving, finishing and fabricating the final filtration product, or anything in-between.
This provides Sefar complete traceability of all critical parts, meaning the company has full oversight of product quality and can certify performance and reliability.
Sefar’s solution
By applying its holistic approach, Sefar is helping mining companies all across the world improve their processes, with its fabric excelling in a range of filtration processes, including copper, lead, zinc, gold, titanium dioxide, and lithium applications, to name a few. Whether a company is producing alumina using Kelly leaf filters, extracting lithium from spodumene with vacuum filters, or dewatering tailings for dry stacking, among other applications, Sefar has the solutions to support a more efficient, costeffective and sustainable mineral processing operation.
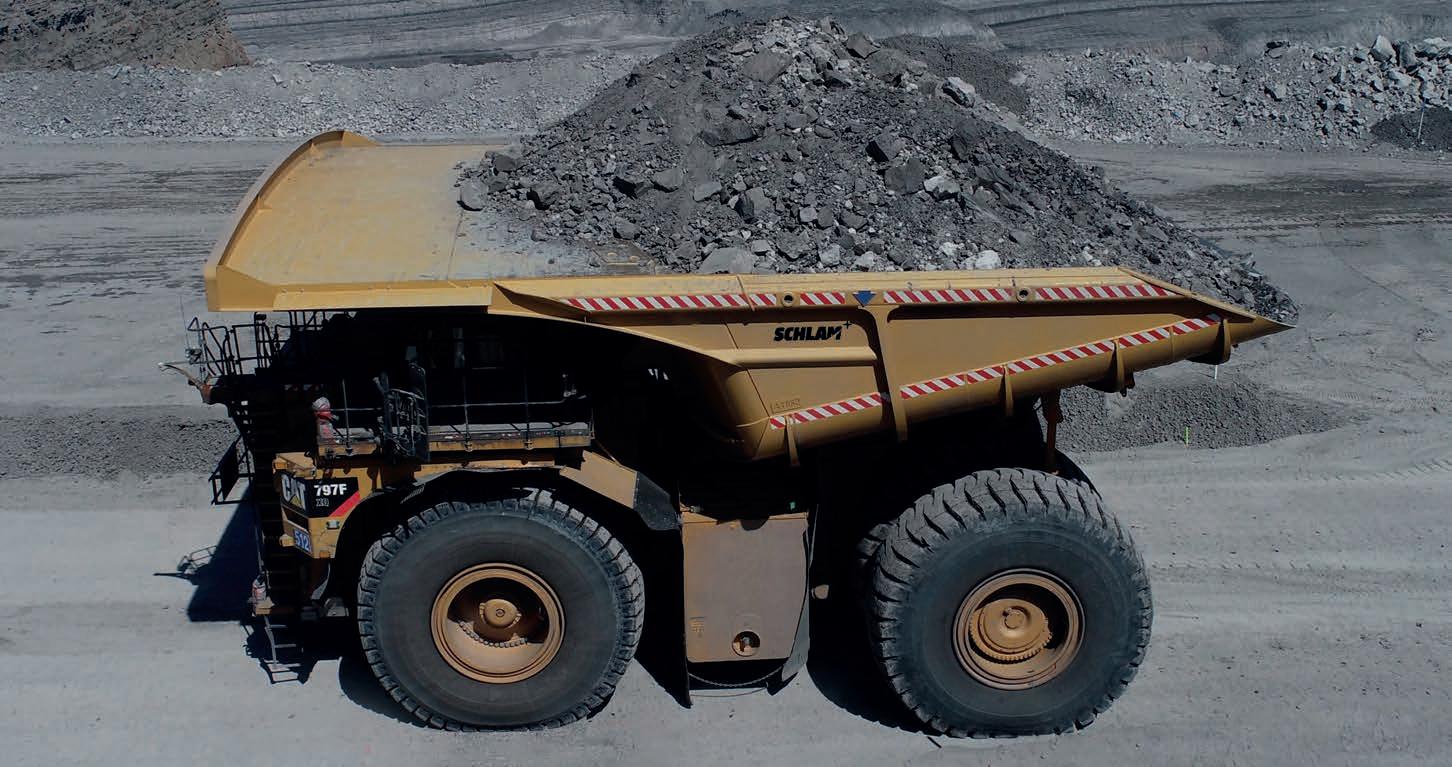
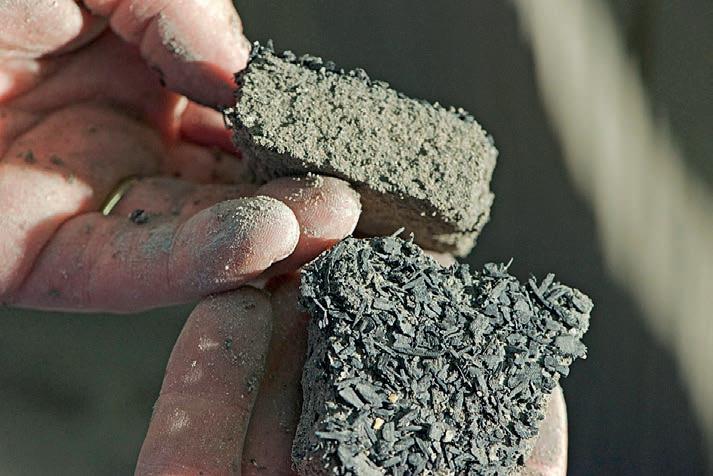
HERCULES ULTRA
ULTRA STRONG. ULTRA LIGHT ULTRA PERFORMANCE
Hercules Ultra – The Next Evolution in Load and Haul Efficiency
Schlam is redefining ultra-class mining with the Hercules Ultra - our most advanced mining truck bed yet.
Built to be stronger, lighter, and more efficient, it delivers up to 10% more payload while reducing maintenance costs. Designed to operate for 25,000 hours maintenance free, the Hercules Ultra is engineered to keep your ultraclass fleet moving longer.
The latest innovation from the global leader in load and haul attachments, the Hercules Ultra can be custom-built to match your site’s unique demands.
Maximise the payload productivity of your ultra-class mining truck fleet with the new Schlam Hercules Ultra.
METSO: A KARRATHA MAINSTAY
METSO’S KARRATHA SERVICE CENTRE IS CELEBRATING ITS FIRST ANNIVERSARY.
In March 2024, Metso opened its largest service centre globally in Karratha, Western Australia.
Boasting state-of-the-art facilities and an investment of $52 million, the 35,000m2 facility is delivering top-tier service to local customers.
A pioneering move, the Karratha Service Centre’s location was strategically chosen to best position Metso to help its WA mining customers.
Now, one year on, the centre is a bustling hub of activity as some of Australia’s largest miners turn to Metso for its world-class service.
“It’s been an incredible journey,” Metso president Asia Pacific Stuart Sneyd told Australian Mining. “The progressive ramp up of the business in the last year has been a highlight to watch.”
Like all of Metso’s service centres, the Karratha hub works with the same bestin-class processes, tools and methods as all of Metso’s 140 service locations.
“This proven approach helps us guarantee our services and repairs to the same demanding standards around the globe,” Sneyd said.
The centre is also focused on providing top-tier response time in Karratha, significantly improving lead times on customer servicing, maintenance and repairs.
“One customer had a component break down in December and was able to put it straight on an urgent transport truck to the Karratha Service Centre,” Metso senior sales manager Chris Brouwer told Australian Mining.
“They waited while the team worked on the component and six hours later, they were back on the road. To put that into perspective, the truck wouldn’t have even reached Perth in that time if they chose to send it elsewhere.”
The Karratha Service Centre is a fullservice 24–7 centre, meaning it can meet all customers’ needs, whether scheduled or emergency services, services exchange, availability of spares and wares or even on-site repairs from field experts.
“Our customers really appreciate having a state-of-the-art local facility,” Sneyd said. “Karratha has advanced amenities including high-capacity cranes, CNC machines, a heat treatment furnace and heavy fabrication and welding facilities.
“We can handle pretty much whatever our customers need – from, for example, repairs on filter plate packs

through to complex heavy equipment, including crushers, screens, mills, and car dumpers.”
The time saved in trucking equipment to Karratha translates to production and sustainability gains for Metso customers.
“A significantly quicker journey, with lower emissions, translates to improved sustainability outcomes for our customers,” Brouwer said.
A boost in safety has been an added bonus for Karratha customers.
“Doing local repairs in the centre provides a more controlled environment,” Sneyd said. “On-site repairs can pose a higher risk because you’re not able to control what’s going on around you.
“But at the Karratha Service Centre, we have an end-to-end process, from sandblast and clean through to welding, machining, heat treatment and so on. We can control every step of the process at Karratha.”
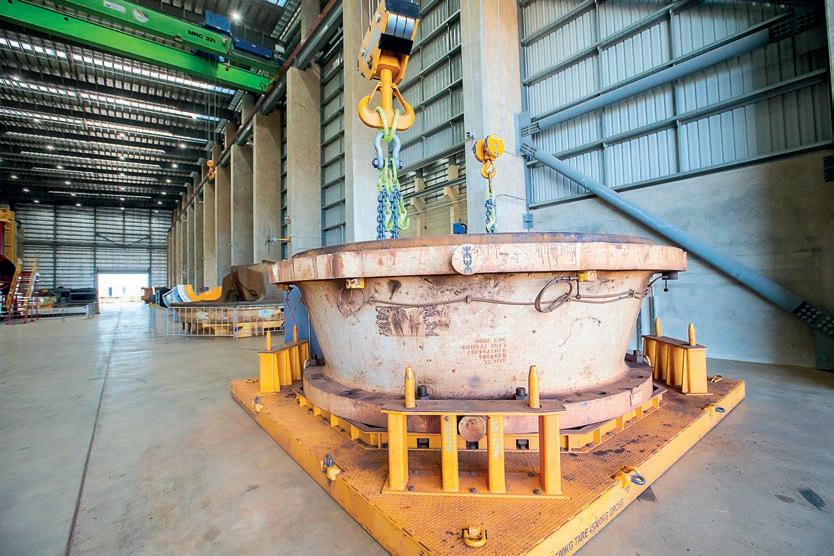
With the expertise of the centre’s dedicated local workforce and the sheer number of advanced machinery the centre houses, Metso’s customers have been quick to jump aboard the Karratha train.
“Our customers really appreciate having this capability right at their doorstep,” Brouwer said. “Our ability to handle everything in-house, 24–7, from Metso to other supplier equipment, truly makes our customers’ lives much easier.
“If equipment comes in for servicing, either Metso’s or another supplier’s, we have the state-of-theart facilities and expertise to handle it at Karratha
“We also have a workforce made up of about 70 per cent Karratha locals and we’ve even had some of our Perthbased FIFO team transfer to Karratha. Metso is becoming a real local business in Karratha, and we’re proud of that.”
As the team looks to the future, it’s acutely aware of how beneficial the move has been.
“This is a long-term and significant commitment to the Pilbara region,” Sneyd said.
“One of our core focuses is to be close to the customer and to be where they need us.
“We have some big things in the works for 2025 and beyond, but above all, we really appreciate how customers have embraced our centre and services.
“We are incredibly proud of our Karratha team and the services they offer. We are excited to call this area home for years to come.” AM
Building Australia’s future of digital connectivity
Through our expertise, brilliant network, and unique customer focus, we make brilliant digital solutions simple.
Fibre network purpose built to connect the Pilbara
Vocus Satellite - Starlink connecting remote locations
24x7 network monitoring with local support
LTE network connectivity built for the mining industry
Backed by a team of leading network experts, solution architects, dedicated account teams and strategic partners, our reliable and secure network provides connectivity across Australia and into Asia Pacific. Visit vocus.com.au
TAILINGS OPTIMISED WITH THICKENER TECH
BALANCING ENVIRONMENTAL RESPONSIBILITY WITH OPERATIONAL EFFICIENCY IS A GROWING CONCERN FOR MINING OPERATIONS WORLDWIDE, WITH TAILINGS MANAGEMENT A KEY ASPECT.
Tailings management is a growing concern for mining operations around the world, balancing environmental responsibility with operational efficiency.
As a leader in mineral processing, McLanahan provides insight into how different thickener technologies can optimise tailings management, improve water recovery, and enhance site sustainability.
Thickeners are essential for liquid–solid separation in mining operations, reducing the volume of slurry material sent to the settling pond or tailings storage facilities (TSFs) while recovering valuable process water.
The right thickener can help mines reduce pond size or eliminate the need for ponds or TSFs altogether, thereby reducing their environmental footprint, streamlining operations, and lowering permitting challenges.
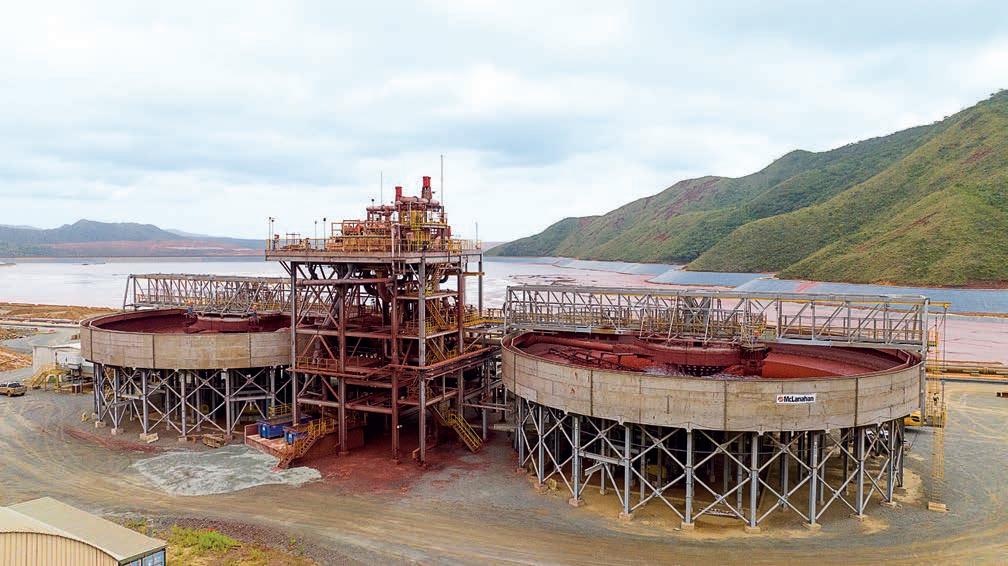
Understanding thickener types
Most thickener types operate by using a chemical polymer, such as a flocculant, to agglomerate solid particles in the slurry, allowing them to settle and discharge while the clear liquid overflows and is collected in a storage tank.
There are variations in thickener design and performance to achieve different process goals. McLanahan outlines the primary thickener types and their applications.
High-rate thickeners
High-rate thickeners are commonly used in mining operations to achieve moderate underflow density and high liquid recovery with relatively low chemical usage.
These units feature a sloped floor and a rotating rake mechanism to assist with compacting the mud bed.
They are a cost-effective choice for operations looking to improve tailings management while maintaining reasonable capital and operational expenditures.
Ultra rakeless thickeners
Ultra rakeless thickeners eliminate moving parts, relying instead on a deep tank and steeply sloped floor for solids settling.
THICKENERS ARE ESSENTIAL FOR LIQUID–SOLID SEPARATION IN MINING OPERATIONS.
While this reduces maintenance, it increases reliance on chemical additives and requires longer residence times – the duration solids remain in the thickener before discharge. This allows for better settling and compaction but can slow production rates.
Ultra rakeless thickeners are an attractive option for operations looking to minimise mechanical complexity, but it’s important to factor in throughput requirements and the cost of chemicals when assessing long-term viability.
High-density thickeners
High-density thickeners offer improved underflow density and water recovery compared to high-rate thickeners.
Their design features include taller tanks, steeper floor slopes and, in some cases, vertical pickets on the rake mechanism to enhance compaction.
These thickeners are ideal for operations wanting to reduce tailings storage requirements while maximising process water recovery.
Paste thickeners
Paste thickeners provide the highest possible solids concentration using gravity alone, often producing an underflow with a paste-like consistency.
Their tall tank design, steep floor slope, and extended bed residence times allow for maximum liquid recovery, making them well-suited to waterconstrained sites.
Paste thickeners can significantly reduce water loss in tailings disposal, particularly in areas where water is scarce. This makes them a strategic investment for long-term sustainability.
Other thickener variants
In addition to primary options, various other thickener designs exist, each with unique operational benefits:
• Bridge thickeners – feature a mechanism suspended off a bridge spanning the tank’s diameter
• Clarifiers – prioritise overflow clarity rather than underflow density
• Column thickeners – incorporate a centre pier to support the bridge structure.
• Conventional thickeners – largediameter, low-aspect-ratio tanks that often operate without chemical flocculants
• Elevated thickeners – raised tanks that offer improved access to underflow pumps
• On-ground thickeners – built directly on the ground, reducing construction costs
These designs can sometimes be combined. For example, a high-rate thickener can also function as a bridge thickener or an elevated thickener, depending on site-specific requirements.
Selecting the right thickener
Determining the most suitable thickener for a given application requires
consideration of factors such as material characteristics, process parameters, and operational goals.
Conducting material testing can help operators identify the optimal type and size of thickener needed. Tailings management is not a one-sizefits-all approach.
By understanding the strengths and limitations of different thickener designs, operations can make informed decisions that enhance efficiency, reduce costs and promote environmental sustainability.
The future of tailings management
With increasing pressure on the mining industry to reduce its environmental impact, the role of thickeners in tailings management is becoming even more critical.
As technology advances, new thickener solutions are helping operations recover more water, minimise waste and improve overall efficiency.
Investing in the right thickener not only improves water recovery and reduces reliance on TSFs but also contributes to a more responsible and efficient mining operation.
By leveraging the right thickener technology, mining operations can enhance their sustainability efforts while ensuring long-term operational efficiency. McLanahan’s solutions offer proven reliability backed by decades of innovation and industry leadership. AM
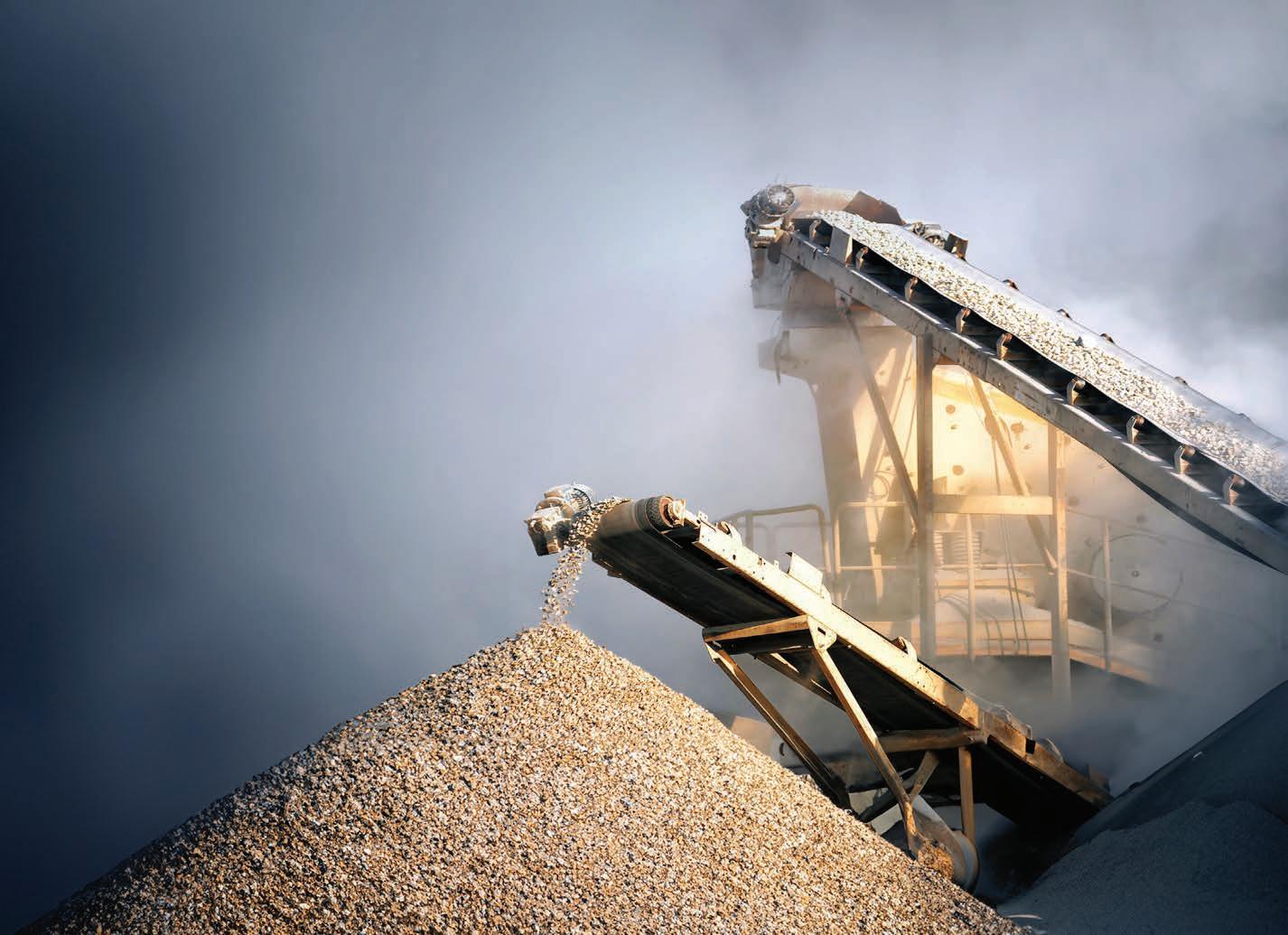

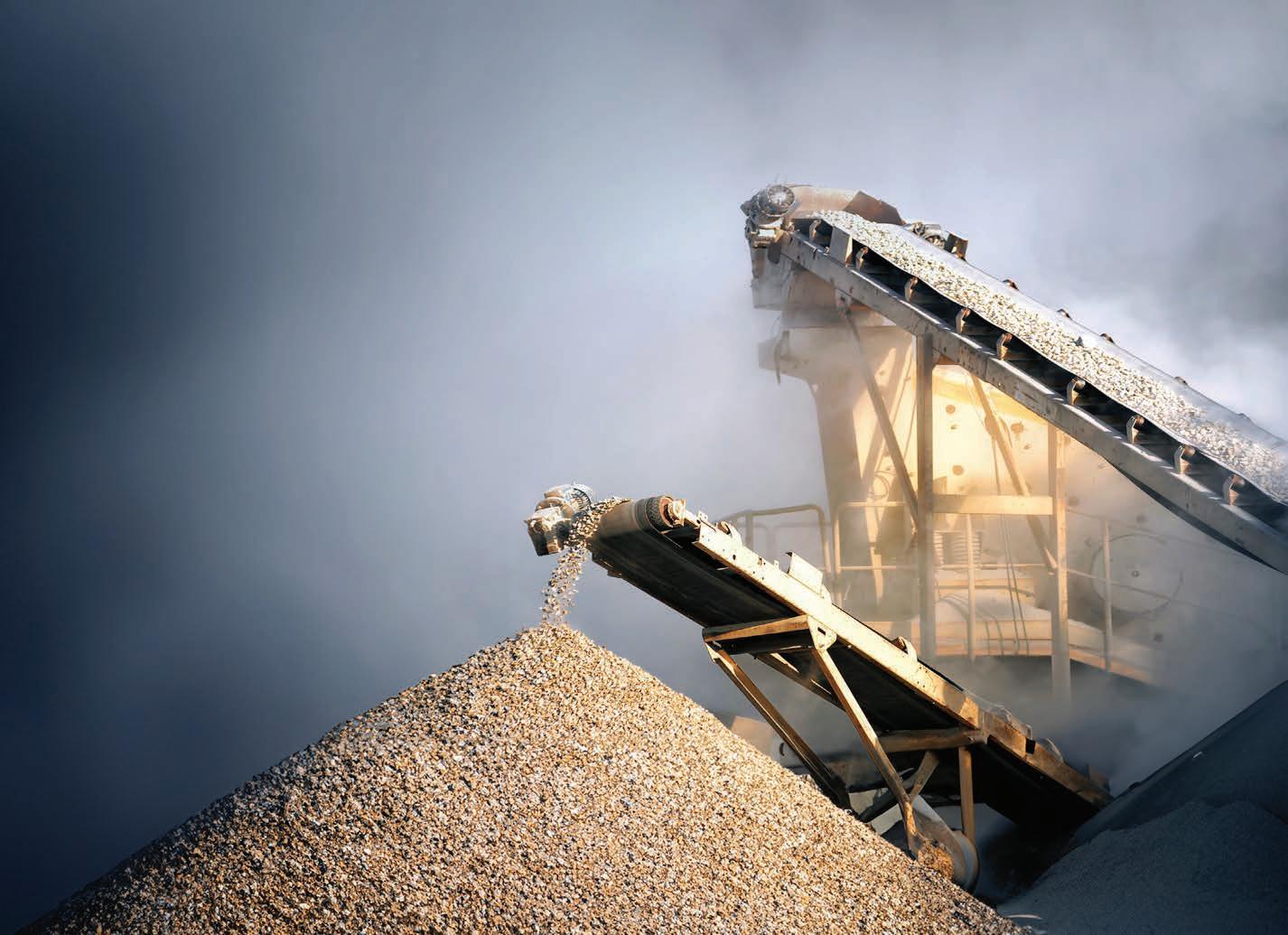
Mining is unforgiving – dust, grime, and debris can cripple standard sensors. The R1D Radar Distance and Speed Sensor is purpose-built to handle these extremes.
Whether it’s detecting large rocks on a conveyor, monitoring blockages in chutes, or preventing collisions on mobile equipment, the R1D delivers reliable, maintenance-free performance.
With non-contact measurement and multiple applications in a single device, it’s the sensor that keeps mining operations moving safely and efficiently.
Applications
Conveyor monitoring
Distance control and height measurement Monitoring surroundings and collision avoidance
Vehicle positioning
Smart access control
DRIVING DATA-DRIVEN OPERATIONS
MINITAB HAS DEVELOPED COMPREHENSIVE, EASY-TO-USE STATISTICAL SOFTWARE THAT BOOSTS PRODUCTIVITY AND SAVES COSTS ON MINE SITES.
Mining companies are increasingly leveraging Minitab Statistical Software to optimise operations, improve resource recovery, and reduce costs.
The solution helps operators make informed decisions by analysing large datasets from sensors, equipment logs, and geological surveys, organising “noisy data” and giving miners greater oversight of their operations.
“Harsh conditions can lead to incomplete or noisy data, making it difficult to build reliable models,” Minitab analytics solutions design manager Bass Masri told Australian Mining
“Minitab helps overcome these challenges by cleaning and organising data for meaningful insights.”
Beyond resource recovery, Minitab Statistical Software plays a vital role in safety and environmental monitoring. The software can analyse historical safety data to identify common incident causes, such as equipment failures or human error.
Through real-time statistical process control (RTSPC), Minitab can also monitor pollutants like heavy metals and particulate matter to detect anomalies and confirm the effectiveness of environmental mitigation measures.
“Using the predictive analytics module (PAM) and machine learning techniques, Minitab enables mining
companies to create predictive models for safety and environmental metrics, helping them take proactive measures to reduce risks,” Masri said.
The Fresnillo case study highlights Minitab’s use of design of experiments (DOE) to optimise silver recovery at the Saucito mine in Mexico.
By investigating variables such as raw materials, water, and chemical reagents, Fresnillo identified the impact of reagents such as zinc sulfate, frothers and Aerofloat 7310 Promoter on silver recovery.
Using Minitab’s Response Optimizer, Fresnillo achieved maximum silver recovery and hit a target grade of 13,500 grams per tonne.
Regression analysis also played a key role at Fresnillo’s Saucito mine, where operator-dependent variability affected recovery rates.
Minitab identified inconsistencies in how operators adjusted reagent settings, prompting the company to standardise decision-making and reduce humaninduced variation at Saucito.
“Fresnillo is a great example of how Minitab can standardise operator decisions and promote consistent outcomes, reducing human-induced variability,” Masri said.
Minitab has also helped Fresnillo achieve a 12 per cent reduction in reagent usage, while increasing recovery rates using statistical modelling.
“The team used predictive models and response optimisation to determine

MINERS ARE LEVERAGING MINITAB STATISTICAL SOFTWARE TO OPTIMISE OPERATIONS AND IMPROVE RESOURCE RECOVERY.
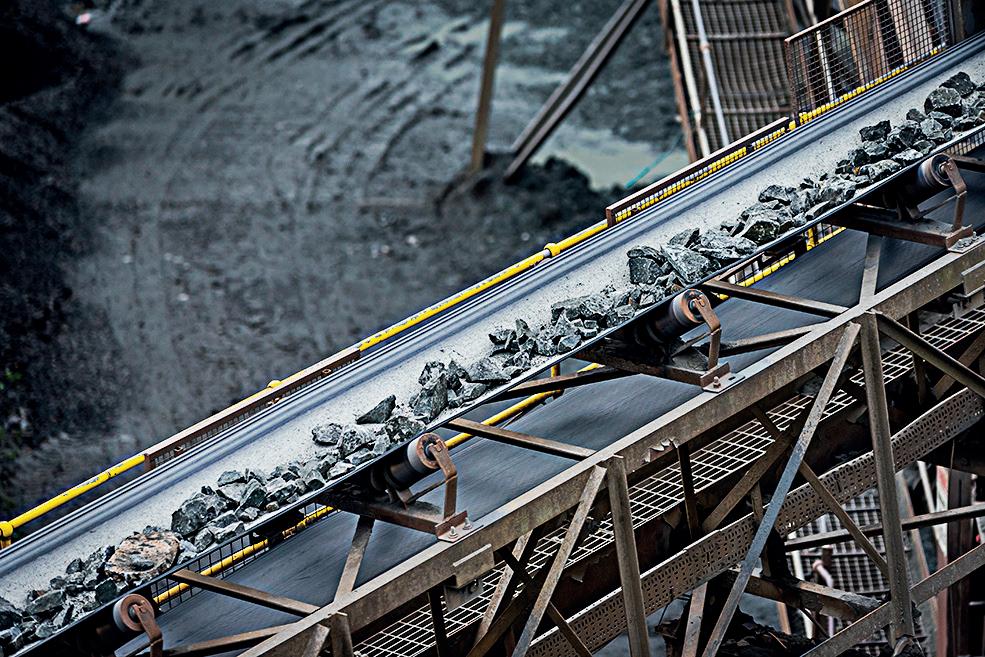
the minimum effective reagent dosage that still optimised silver recovery, avoiding unnecessary overuse,” Masri said. “The team optimised both reagent costs and silver recovery, proving that efficiency gains don’t always require increased spending.”
One of Australia’s largest gold producers came to Minitab with a problem, where its fleet of large-haul trucks descend a narrow ramp.
On-site truck speed varies, with slower trucks delaying other vehicles resulting in a significant loss of productivity.
The gold miner implemented Minitab Statistical Software, with its easy-to-understand graphics and platform, to reduce bottlenecks in its operation.
Using Minitab to plan and design experiments and analyse data at each step, the mining company identified that reducing the grade of the haul ramp from 10.22 to 9.9 per cent in the test section resulted in a 2.6 per cent increase in truck speeds, and reduced variation in truck speed by 7 per cent.
These insights prompted the miner to overhaul the entire haul ramp by reducing all ramp grades to under 10 per cent, an adjustment set to save at least 8.3 seconds per uphill trip.
Minitab analysis also revealed that 10 per cent of the miner’s trucks weren’t operating at their peak.
Faulty fuel injectors were identified and replaced, improving truck cycle times by 5.6 per cent per truck. This is the equivalent of one extra trip per truck per day.
By implementing Minitab’s changes, the gold miner anticipates it will save over $835,000 in just the first year.
As AI and automation reshape the mining landscape, Minitab Connect is evolving to integrate real-time data analysis and predictive maintenance.
Minitab’s predictive analytics module uses machine learning techniques to develop, test and select the best models.
“In predictive maintenance, vibration sensors on pumps or conveyors can feed data directly into Minitab,” Masri said.
“The software can analyse this data to forecast equipment failure before it happens, reducing downtime and optimising maintenance schedules.
“For process optimisation, operators can access a dashboard showing real-time data alongside predictive insights, enabling them to understand when equipment is likely to require maintenance or when certain process adjustments will result in optimal recovery.”
The Fresnillo case study demonstrated how data-driven process improvements not only enhanced financial performance but also delivered significant environmental benefits.
By leveraging Minitab’s robust datadriven statistical solutions (Minitab Statistical Software) and process improvement platforms (Workspace and Engage), mining companies can achieve operational excellence, improve recovery rates, drive sustainability initiatives, and foster a culture of continuous improvement, ensuring they stay competitive in a dynamic industry.
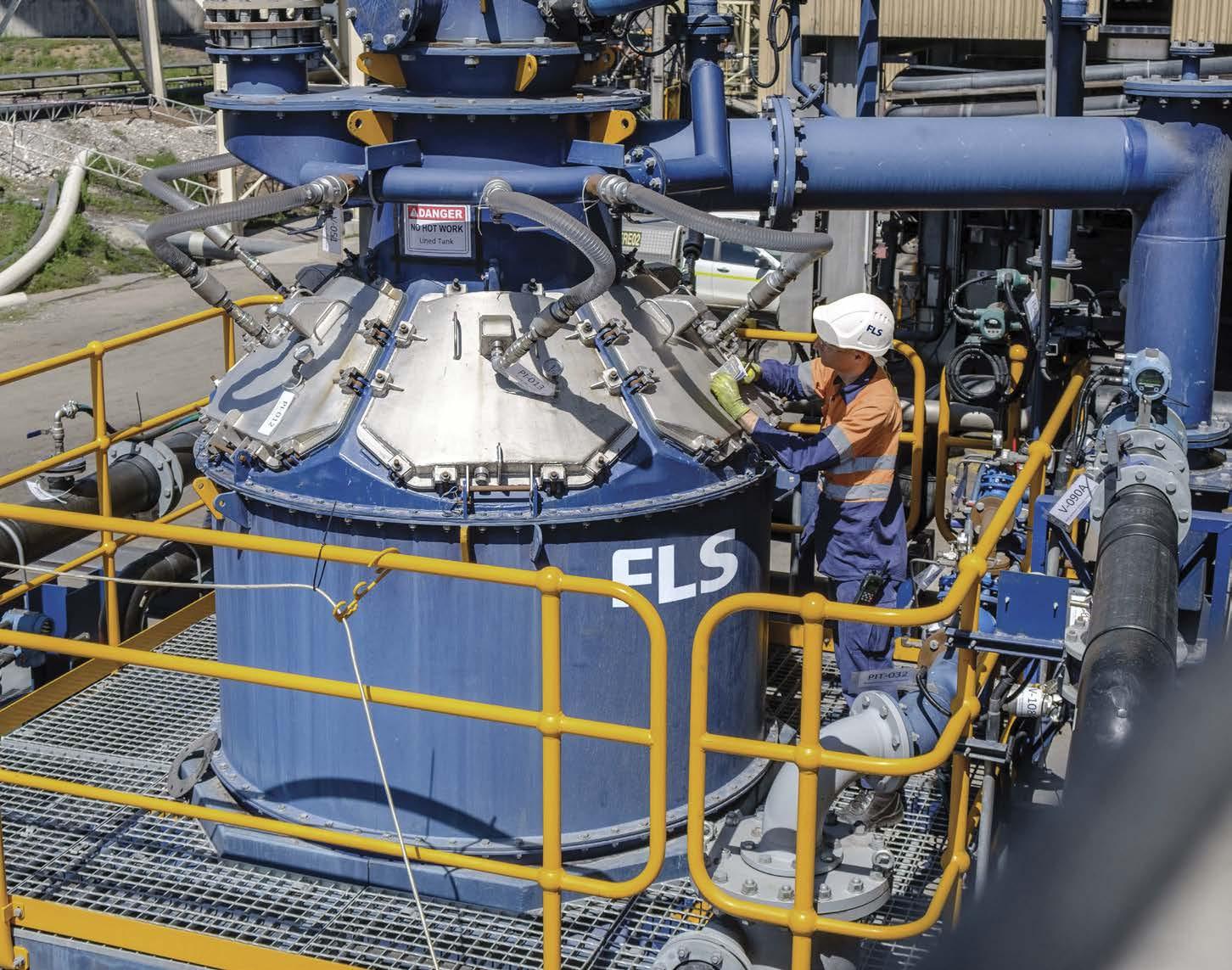
REFLUX™ Flotation Cell (RFC)
Expanding the bounds of flotation

Increased throughput
Up to 10x higher than traditional open-tank flotation cells
Enhanced grade and recovery
Higher separation efficiency enhances gangue rejection
Smaller footprint
Faster flotation kinetics reduces required installation footprint
Energy efficient
No moving parts and lower utility demand provide a more sustainable operation
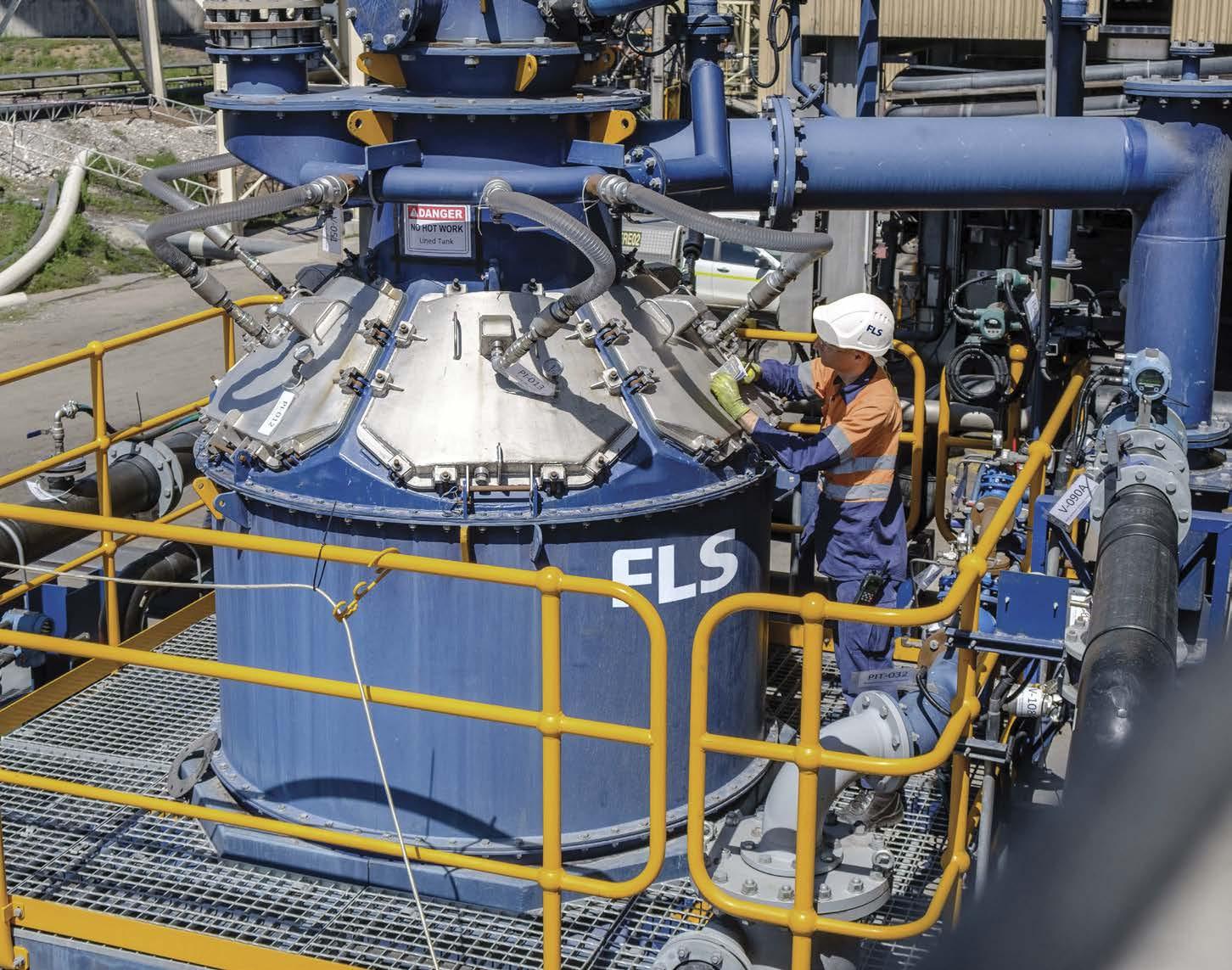
BOOSTING EFFICIENCY AND REDUCING DOWNTIME
IFM IS REDEFINING MINERAL PROCESSING TECHNOLOGY THROUGH ITS VIBRATION AND RADAR SENSORS.
In an industry where efficiency and uptime are paramount, mining operations are increasingly turning to advanced conditionmonitoring technologies to enhance productivity.
A leading provider of automation and sensing solutions, ifm is at the forefront of this movement with its latest innovative vibration and radar sensors. These solutions offer real-time insights into equipment health, helping miners prevent costly breakdowns and optimise performance.
Australian Mining spoke with ifm about the company’s latest advancements in sensor technology and how they are transforming the way mining operations approach condition monitoring.
ifm’s understanding that mining thrives on efficiency, with even minor equipment failures potentially resulting in millions of dollars in lost production, was a driver in the company developing a range of sensors designed to detect early warning signs of mechanical issues before they escalate.
“Our key focus in mining is on process instrumentation and enhanced condition monitoring,” ifm mining specialist Sam Rupasinghe told Australian Mining
“We supply everything from pressure, level, flow and temperature instrumentation to advanced solutions that minimise downtime in critical assets like conveyors, crushers, mills and mobile machinery.”
Condition monitoring plays a crucial role in this effort, ensuring key equipment remains operational, reducing the risk of unplanned shutdowns.
ifm’s latest innovations in radar and vibration sensors provide miners with an edge in predictive maintenance.
While radar technology has long been used in mining for level monitoring, ifm’s newly developed sensor takes functionality to the next level by integrating multiple applications into a single device.
“Radar is a well-established technology in mining because it can operate effectively in dusty environments,” Rupasinghe said. “But what makes our radar sensor unique is that it combines level monitoring, blockage detection, speed measurement and area monitoring applications in a single product range.”
One of the key applications of this technology is in mining chutes through
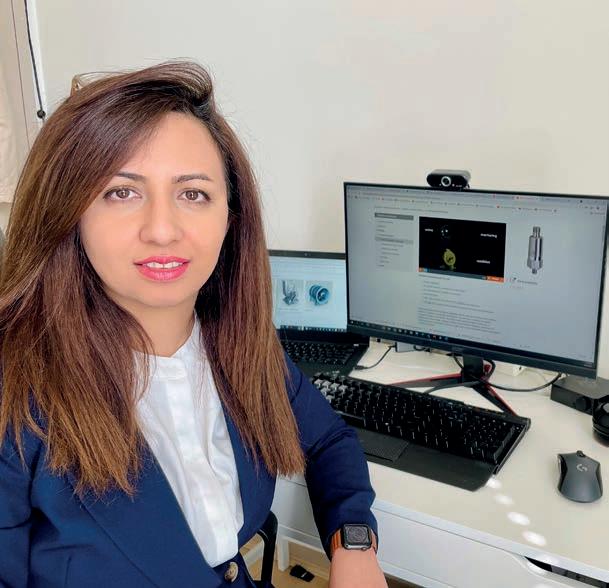
which bulk material, such as ore and waste rock, is transferred.
Blockages in these chutes can cause major disruptions, but ifm’s radar sensor detects build-up in real-time, allowing operators to intervene before production is affected. The detection area of the radar beam can be adjusted depending on the size of the chute.
“The same principle applies to crushers and screens,” Rupasinghe said. “Blockages in these areas can cause significant damage, leading to costly repairs.
“Our radar sensor can identify these issues early, ensuring that maintenance teams can act before a critical failure occurs.”
The sensor also provides realtime speed monitoring, a feature not commonly available in industrial radar systems.
“By tracking the speed of ore across screens, operators can identify slowdowns that may indicate a developing problem,” Rupasinghe said. “This helps miners address issues proactively rather than reactively.”
Beyond fixed plant applications, ifm’s radar sensor also enhances safety in mobile machinery via collision avoidance. The sensor can be mounted on large mining vehicles, such as haul trucks and dozers, to detect objects in their vicinity.
“Mining trucks operate in challenging environments where visibility can be limited,” Rupasinghe said. “Our radar sensor provides distance-based alerts, helping operators avoid collisions and improve site safety.”
The sensor can be programmed to create multiple detection zones, triggering different levels of alerts according to an object’s proximity to the vehicle.
ifm has also developed a controller area network (CAN)-enabled version that integrates directly into mobile equipment control systems, further enhancing its usability in mining fleets.
While radar technology is invaluable for blockage and level monitoring, vibration analysis remains one of the most effective methods for detecting early signs of mechanical failure in rotating equipment.
ifm’s new VVB3 vibration sensor brings enhanced functionality to this
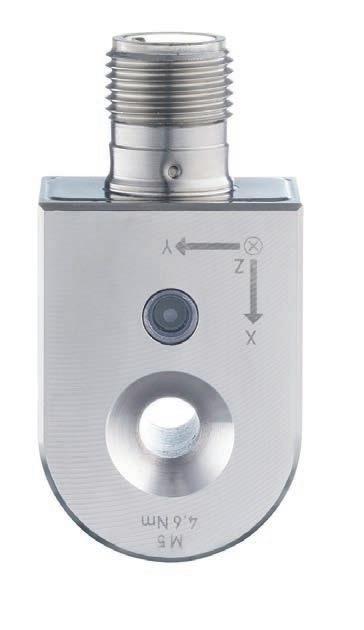
space, providing detailed insights into machine health.
“Vibration monitoring is one of the most commonly used techniques of condition monitoring,” ifm vibration expert Zeinab Khaksar told Australian Mining. “Condition monitoring in the mining industry benefits from vibration analysis because it provides a clear picture of equipment health, particularly for motors, pumps, and other rotating machinery.”
What sets ifm’s VVB3 sensor apart is its ability to perform raw vibration data and bearing analysis within the hardware itself. ifm has termed this ‘Bearing Scout’. The sensor can do this across three axes – X, Y and Z – providing a comprehensive view of machine condition.
The sensor also includes an in-built surface temperature monitor, adding another layer of condition monitoring.
“Every machine has a vibration signature,” Khaksar said. “By continuously monitoring changes in that signature, we can detect anomalies that indicate potential failures.”
One of the standout features of ifm’s VVB3 sensor is its Bearing Scout technology, which allows operators to program specific bearing parameters of an asset into the sensor. This enables early detection of bearing wear, which is one of the most common failure points in rotating machinery.
“Bearings are critical components,” Khaksar said. “If a bearing fails, it
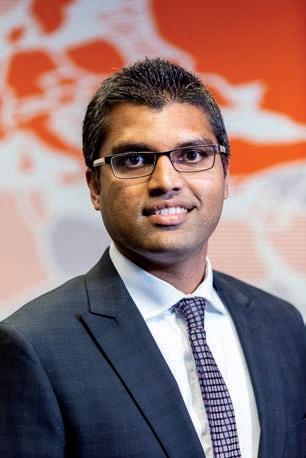
can cause secondary and catastrophic damages to the machine.
“Our bearing scout feature monitors the health of bearings in real-time, allowing maintenance teams to intervene before a failure occurs.”
Another key feature is the unbalance detector.
“Unbalance is one of the main causes of high vibration that leads to excessive stress on bearings,” Khaksar said. “By detecting this issue early through the unbalance detector, operators can take corrective action before it leads to serious damage.”
The VVB3 sensor is also equipped with built-in memory, allowing it to store up to nine days of historical vibration data. This provides maintenance teams with a valuable record of machine performance and enables more accurate trend analysis.
Ease of integration is another key advantage of ifm’s condition monitoring solutions, with the radar and vibration sensors designed to work seamlessly with existing mining infrastructure.
“The radar sensor outputs standard industry signals such as analogue 4–20 milliampere (mA), simple switch and IOLink, making it easy to connect to existing control systems,” Rupasinghe said. “For mobile applications, the CANenabled version allows direct integration into vehicle operating systems.”
Similarly, the VVB3 vibration sensor uses IO-Link technology, which helps to simplify configuration and data transfer.
“IO-Link makes it easier to set up the sensor and integrate it via existing communication protocols such as Ethernet IP, Profinet and Modbus,” Khaksar said. “It also provides selfdiagnostics, so operators can quickly identify if a sensor is malfunctioning.”
As many aspects of mining operations become increasingly automated, condition monitoring technologies like ifm’s radar and vibration sensors will play an ever-increasing role in improving efficiency and safety.
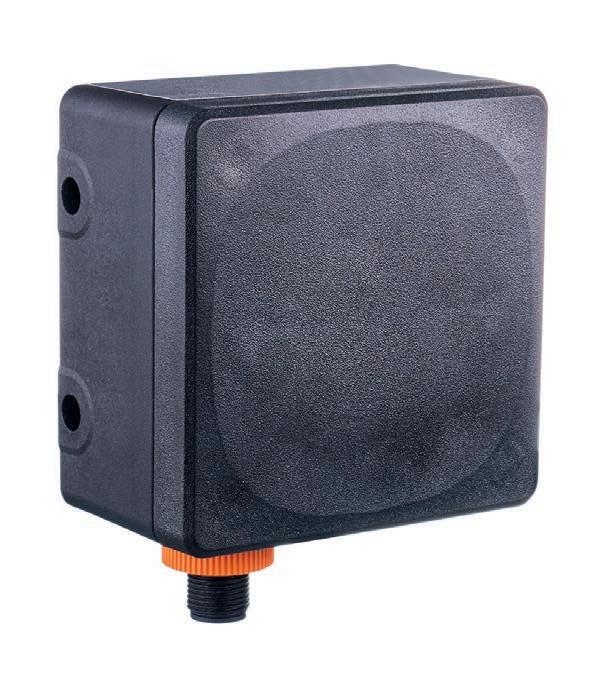
“In mining, time is money,” Rupasinghe said. “Minimising downtime is crucial and our sensors provide the real-time insights needed to keep operations running smoothly.”
By combining advanced monitoring capabilities with seamless integration and user-friendly features, ifm’s latest solutions are helping miners take a more proactive approach to equipment maintenance – by reducing
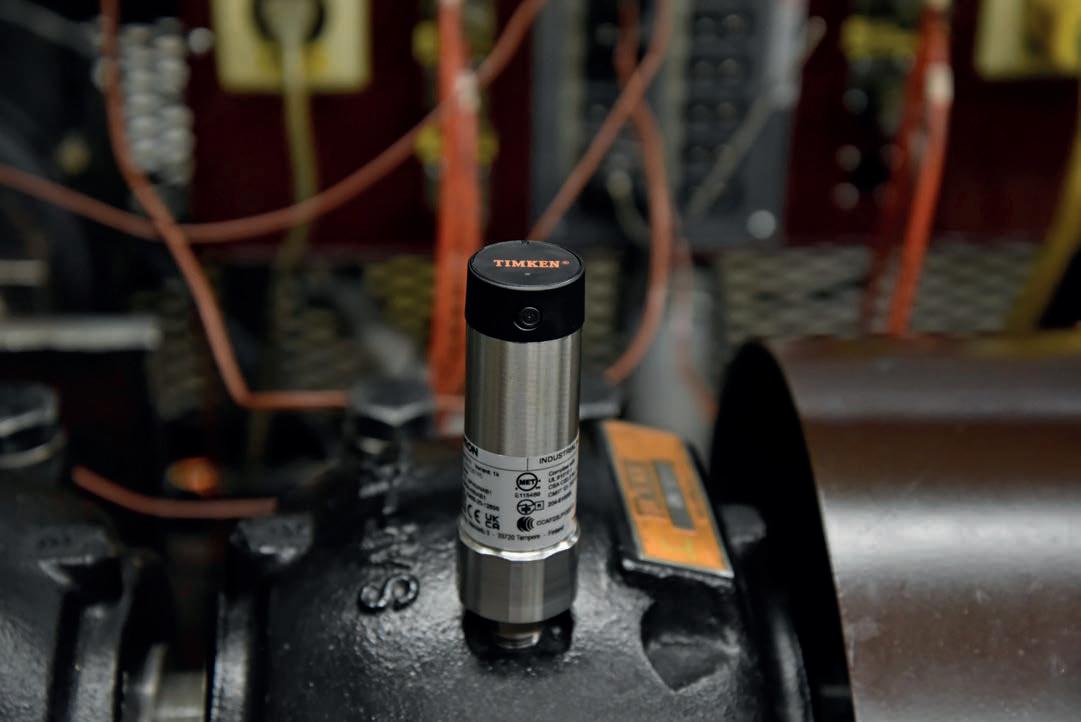
costs, improving safety and ensuring continuous production.
With local support available in Australia, ifm is well-positioned to help mining companies implement these technologies and maximise their operational efficiency.
As the industry moves towards a more data-driven future, solutions like these will be essential in driving the next generation of smart mining. AM
Timken Wireless Sensors
» Vibration and Temperature Monitoring
» Data stored on gateway (on site) without ongoing fees
» Mesh technology (sensor connectivity and expandable range)
» DIY setup
» Ethernet
» WiFi
» Mobile or PC dashboard
» Can be used standalone
» Data can be added into existing CM
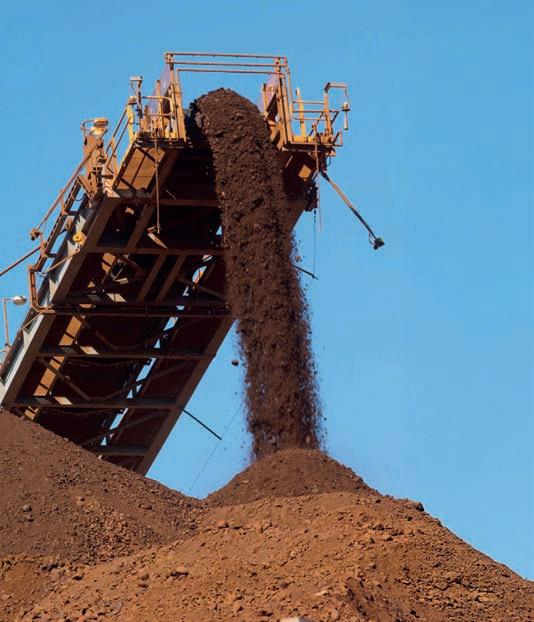
For more information: www.timken.com/product mark.davies@timken.com
SMALL DROPS, LARGE IMPACT
TECPRO AUSTRALIA IS ENHANCING PRODUCTIVITY AND SAFETY THROUGH ITS DIVERSE RANGE OF DUST SUPPRESSION AND CONTROL SOLUTIONS.
The first step in mineral processing is crushing and grinding ore to reduce particle sizes and support processing applications down the line.
While this stage is critical to extracting the desired crude material, it generates a large amount of dust, which can have harmful impacts on workers.
To mitigate these risks, Tecpro Australia offers a trusted range of dust suppression and control solutions designed to meet specific customer needs.
Formed in 1982, Tecpro was conceived as a company that solves engineering challenges associated with spraying water.
“Early on, we formed a partnership with PNR Italia and started offering their range of spray nozzles to Australia,” Tecpro Australia director Patrick Cooper told Australian Mining
“We also moved into complete fogging systems, such as misting systems, used for dust suppression, before becoming one of the first companies in Australia to
and automation dust control software to Australia, as well as the world’s first electric dust control vehicle that doesn’t omit emissions.
“We like being at the forefront of evolving technology.”
When it comes to dust suppression, Tecpro believes there’s no such thing as a ‘one-size-fits-all’ solution, which is why the company offers complete solutions specifically tailored to an application.
“We’ve been helping customers solve dust issues and keeping employees safe for over 40 years,” Cooper said. “This experience and knowledge enables us to solve even the most challenging dust issues as they arise.
“Every application we work on must be customised in some way as they’re all unique. Customers can’t just buy products from our website. We speak with customers to discuss their required application and work out what solution will be the best fit for them.”
Spray nozzles
Ranging from low-pressure to highpressure options, Tecpro’s spray
By converting liquid pressure into kinetic energy, Tecpro’s spray nozzles disperse liquid into droplets of varying sizes and patterns.
Each Tecpro spray nozzle, manufactured with quality material from Europe, is designed to withstand harsh industrial environments common in the Australian mining industry, reducing corrosion and extending wear life.
“Spray nozzles can be used to dampen product on moving conveyor belts, suppressing dust in the process,” Cooper said.
“They can also create a barrier. For example, if a truck dumps material into a bin, spray nozzles can create a curtain of water, so when dust tries to exit the bin, it hits the curtain of water and drops back down.
“Spray nozzles can also be used for airborne dust. By spraying water at the dust, the droplets make contact with the dust particles and carry it down to the ground.”
Tecpro recently supplied air atomising nozzles to an Australian mine site, which will be attached to an
“At another site, air atomising nozzles were installed on a conveyor discharge chute, producing a very fine ring of droplets where the ore was falling onto the stockpile to capture any dust as it landed.”
Tecpro helps customers select the best spray nozzle option based on factors such as dust type and particle size, water supply, how dust is generated, the desired location of the spray nozzles, and associated infrastructure.
Autonomous dust control
As leaders in innovation, Tecpro offers a range of autonomous dust control solutions.
Autonomous technology offers several benefits to users, including enhanced safety of personnel, increased optimisation and sustainability, and reduced downtime and human error.
Tecpro can customise its autonomous dust control systems to meet the conditions of a mine site at any given time.
“(The system) can be automated by a virtually controllable map on a central
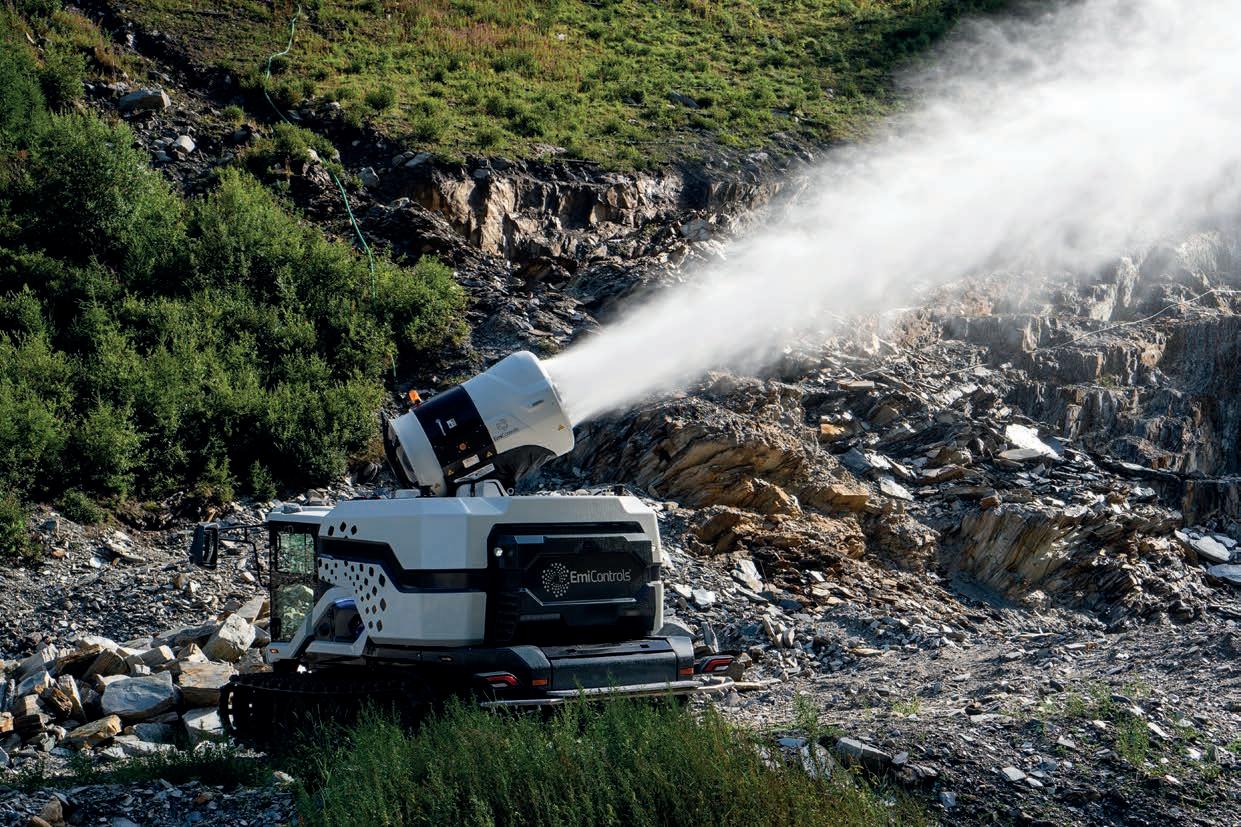
TECPRO AUSTRALIA IS THE AUSTRALIAN DISTRIBUTOR FOR SEVERAL BRANDS, INCLUDING EMICONTROLS AND PNR ITALIA.
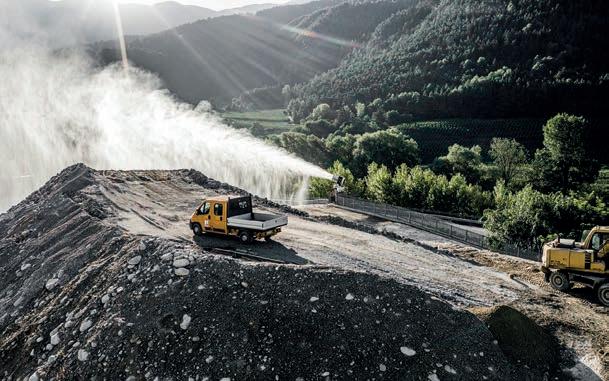
identify that dust levels are increasing, triggering the sprays to begin operating.
“This means you’re only using energy to control the pumps and the water in the sprays when necessary, reducing operating costs.”
A staple offering from Tecpro is the CURTPro intelligent dust management system, which oversees all dust controllers and associated components of a plant and controls them in real-time. The solution can also be used for odour control and wastewater evaporation.
CURTPro’s key features include its user-friendly dashboard, and the ability to customise configurations, allowing the system to automatically react to linked sensors.
CURTPro’s dust monitors pick up when dust levels increase above the pre-set levels, activating fogging sprays on the crusher and its transfer points,” Cooper said.
“If dust has the risk of reaching a nearby town due to wind, say over 10 knots, the weather monitor can activate the sprays when the wind reaches eight knots, proactively controlling the dust before it becomes an issue.”
Above all, Tecpro strives to build long-lasting relationships with its clients.
“We’ll work with them to come up with the solution that exceeds their expectations,” Cooper said.
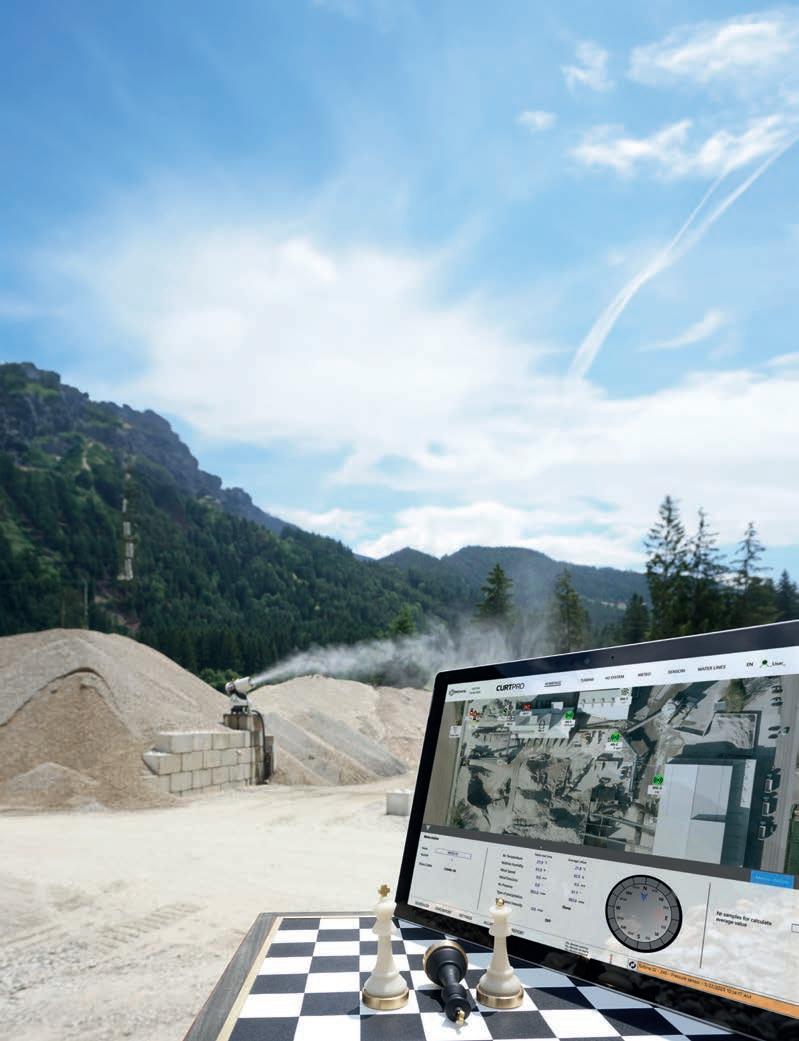
CURTPRO SOFTWARE
KEEP YOUR KOMATSU FLEET MOVING
Products manufactured and stocked to suit:
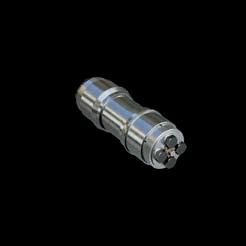

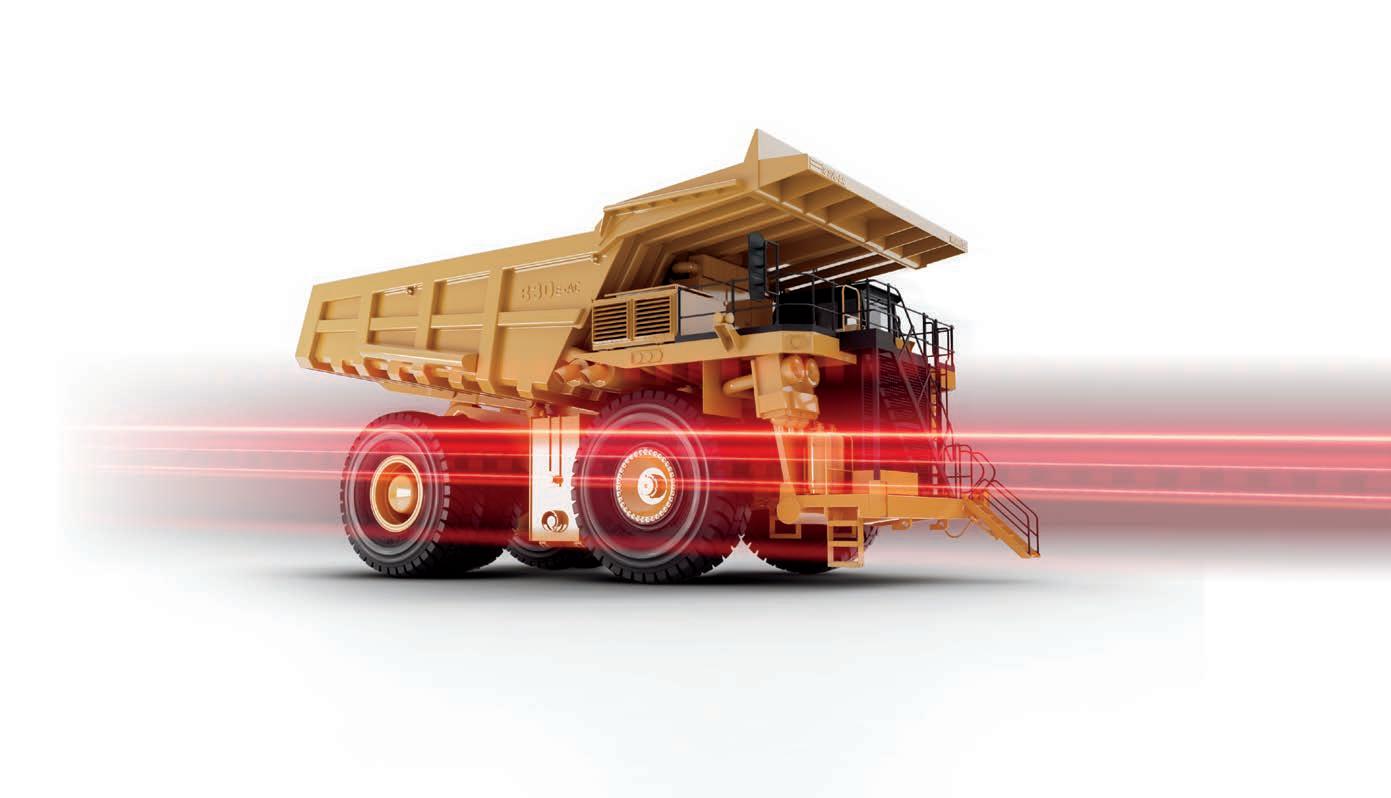
FROM ROCKS TO RICHES
ERIEZ HAS COME UP WITH A SIMPLE SOLUTION TO BALL MILL PERFORMANCE EFFICIENCY WOES.
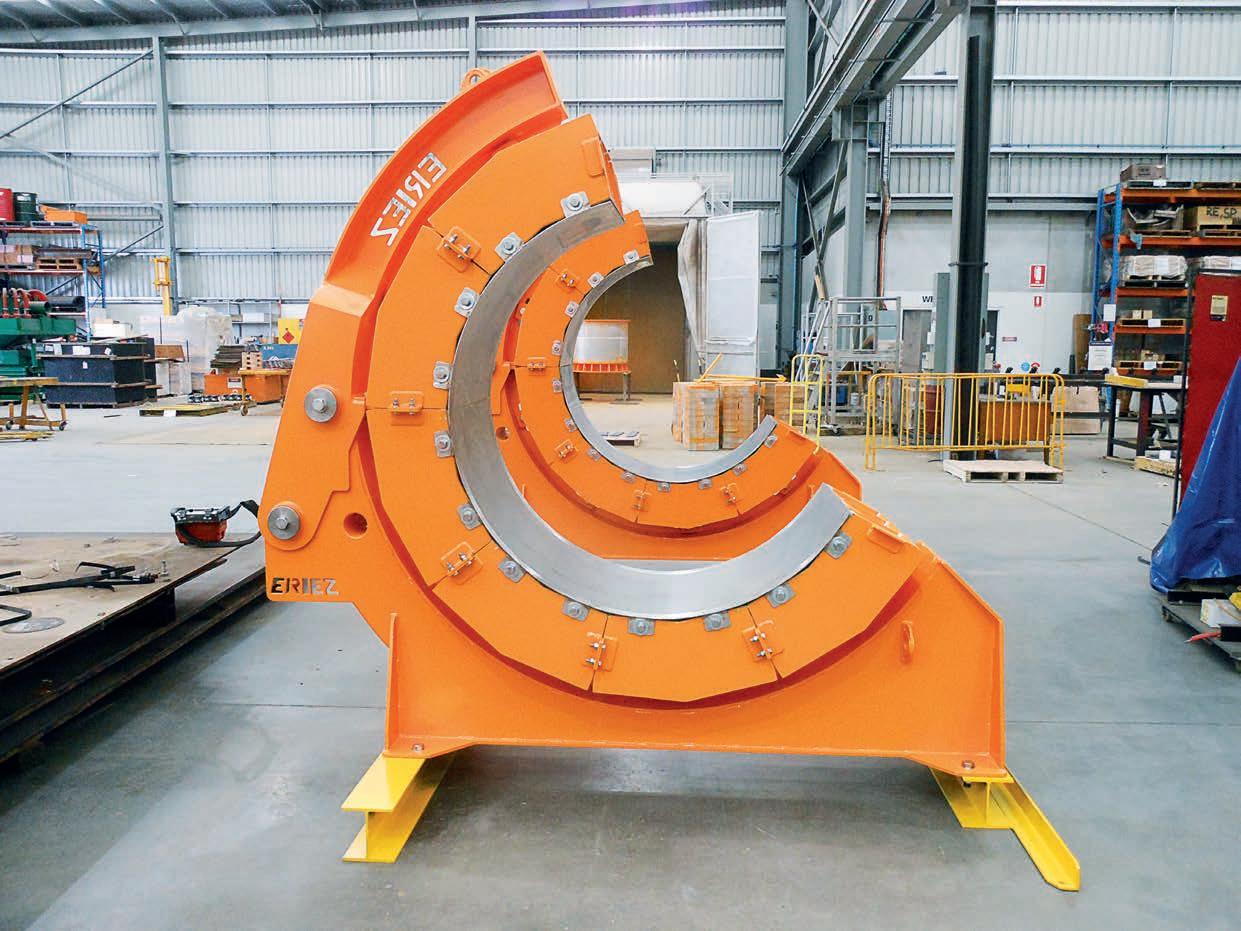
Bcomminution stage of mineral processing, the mill is filled with grinding media such as steel balls. As the mill rotates, the balls collide with the ore to break it down into smaller pieces. While the process might sound relatively simple, the humble ball mill can cause some major problems for miners. The balls are susceptible to the same wear and tear as many other machine parts, and over time some chips or fragments may come loose and recirculate through the mill. These chips occupy space that could otherwise be used for added ore.
Seeing these problems, Eriez Australia knew there was a simple solution it could present to the market: the trunnion magnet system. The system bolts directly to the ball mill discharge flange and provides continuous magnetic
with some substantial safety and productivity benefits.
“Many miners use trommel screens to separate ball chips, but these screens are heavy and require a lot of maintenance,” Eriez business development manager – mining Omkar Bokil told Australian Mining
“The trunnion magnet system is a permanent magnet circuit so it doesn’t require constant installing and dismantling.”
Bokil highlighted the potential electricity savings as one of the system’s key features.
“We have seen a nominal eight per cent reduction in mill power consumption,” Bokil said. “That in itself slashes a big ongoing cost that most mines have to contend with.”
There are four basic components to the trunnion magnet system: stainless steel barrel; magnet circuit; support
several benefits of removing grinding ball fragments, including a 250 per cent increase in the lifespan of pumps and hydrocyclones, a nominal five per cent increase in mill throughput and a more efficient grinding process, leading to an approximate 10 per cent reduction in the mill work index,” Bokil said.
Eriez also supplies exemplary beforeand after-sales support to ensure its customers are buoyed by an expert hand.
“We start with our ‘lunch and learns’,” Bokil said. “This involves us going out to the customer’s site to understand their problems and any budgetary constraints.
“Once we understand that, we propose a site-specific solution to solve their problem. We know mines work 24–7 so we are available seven days a week in case our customers need us after a solution has been installed.”
Customer feedback on the trunnion magnet system has been far-reaching
“Cost estimates of a typical 18-feet diameter mill indicate savings of up to $100,000 per year,” Bokil said.
“By installing our trunnion magnet system, mines are saving on the cost of trommels and maintenance.
“The magnet doesn’t come in direct contact with the media, so it doesn’t wear out. This means mines aren’t paying for maintenance and replacements.”
Looking to the future, Eriez is excited to work with the wider mining industry to implement its trunnion magnet system at more mines.
“We’ve had a lot of interest from the major ball mill manufacturers, so we’re exploring how we can work with them in the future,” Bokil said.
“Working with them would create a win–win–win scenario: a win for the manufacturer, a win for us and, most importantly, a win for the customer.” AM
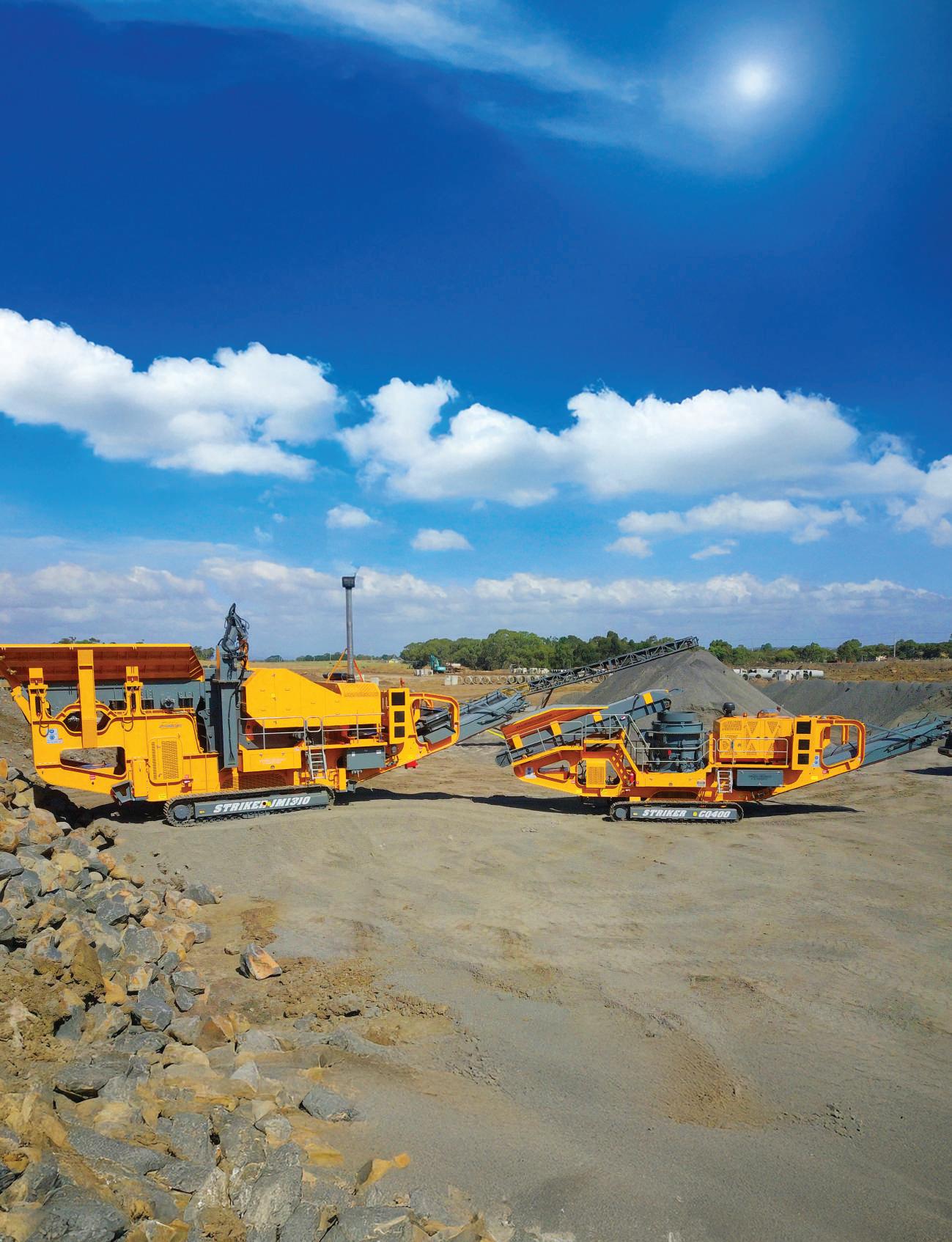
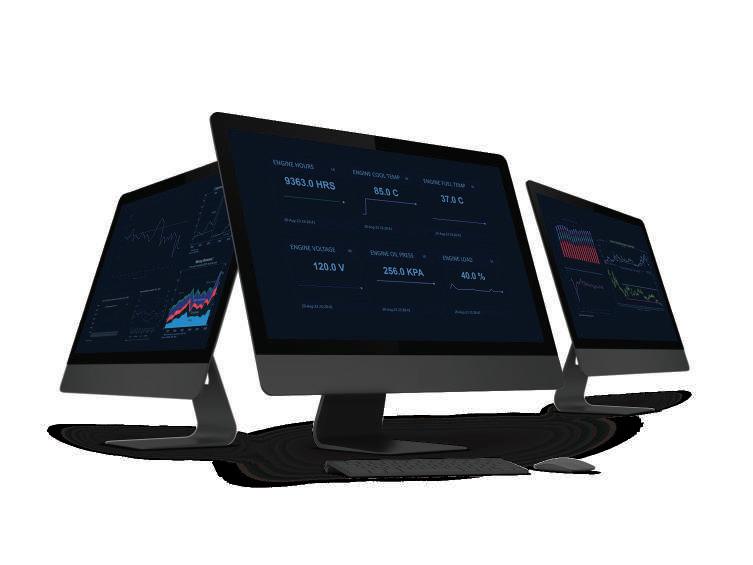

MINING REIMAGINED WITH 3DEXPERIENCE
DASSAULT SYSTÈMES PROVIDES THE BUILDING BLOCKS FOR A SUSTAINABLE MINE OF THE FUTURE BY MITIGATING RISKS, MINIMISING ENVIRONMENTAL IMPACT, AND MAXIMISING EFFICIENCY.
Technology is reshaping the world, and the mining industry is no exception, with virtual twin technology at the forefront.
As the industry faces challenges such as declining ore grades, rising costs, and stricter environmental regulations, technology like Dassault Systèmes’ 3DEXPERIENCE platform is critical.
“Our platform connects all the data points across mining operations, ensuring that when something changes in one area all other relevant processes are updated accordingly,” Dassault Systèmes’ global sales director Ralph Smith told Australian Mining
“This provides auditability, repeatability, traceability and visibility, underpinned by governance tools to digitise the mining value chain.”
In mineral processing, virtual twins can be used to model equipment maintenance, simulate plant performance, and integrate data across the mining value chain.
“Whether it’s testing different processing parameters or predicting potential bottlenecks, the technology enables mining companies to make proactive decisions rather than
DASSAULT SYSTÈMES IS INTREGRATING AI INTO ITS VIRTUAL TWIN PLATFORM, FURTHER ENHANCING PREDICTIVE CAPABILITIES.
reactive ones,” Smith said. “We can model and simulate something before physically implementing it. For example, we can plan and simulate the mining production cycle and the beneficiation process.
“By connecting multiple disciplines, we can better understand our decisions to maximise value, extract more for less, and drive our sustainability and productivity ambitions.”
By simulating entire mining operations in a virtual environment, companies can optimise layouts, reduce waste, and minimise environmental impact before a single shovel breaks ground.
More significantly, virtual twins allow mines to align key performance indicators (KPIs) across different operational areas.
“What tends to happen is that geoscience, mine planning, and processing teams often work in silos, leading to inefficiencies,” Smith said.
“There can be confusion at the end of the month regarding KPIs and who did what.
“A virtual twin connects these disciplines so that when someone makes a change, you can see the impact down
At the core of Dassault Systèmes’ virtual twin technology is data –accurate, real-time information that enhances decision-making.
Mining companies can integrate real-time data from sensors placed throughout their operations.
“For example, sensors in a copper deposit can scan material in a bucket as it’s being loaded, providing real-time analysis of its quality,” Smith said.
“That information is then integrated into the virtual twin, allowing operators to anticipate what’s going to the mill or stockpile.”
By feeding real-time data into the virtual twin, mining companies can better predict processing requirements, whether it’s adjusting crushing and grinding parameters or modifying reagent mixes for optimal recovery.
One of the biggest challenges in mining is ensuring alignment between blasting, material movement, and processing efficiency.
“A blasting engineer’s KPI is often to reduce costs, not necessarily to increase plant productivity,” Smith said.
“But if you spend 20 per cent more on blasting and get a one percent improvement in plant throughput, the
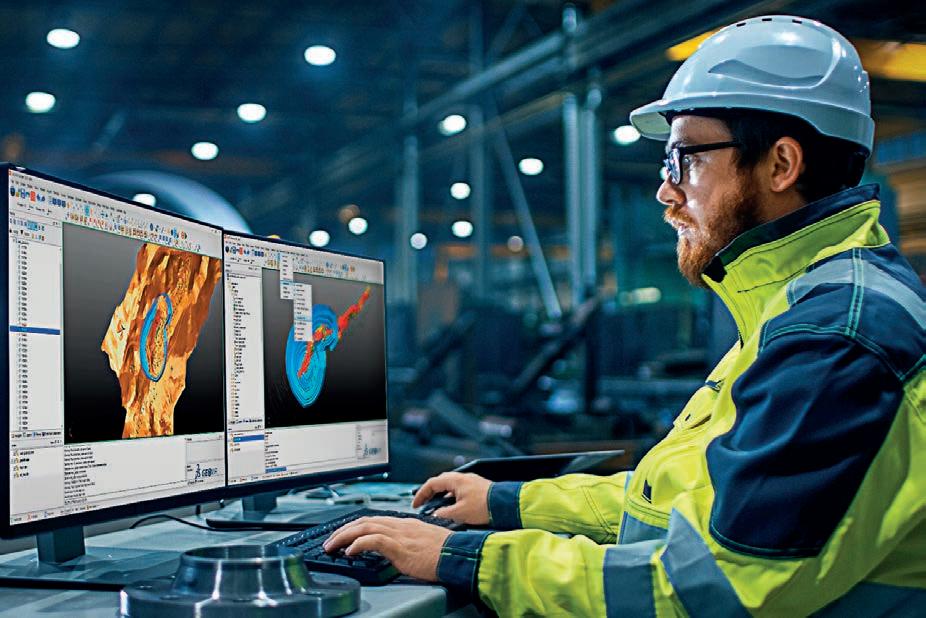
Dassault Systèmes’ virtual twin technology helps mine operators bridge these gaps, optimising every step from ore extraction to final processing.
“We can simulate how material moves through the processing plant, identifying bottlenecks before they happen,” Smith said. “It’s about connecting the dots across disciplines rather than optimising individual silos.”
Dassault Systèmes has also explored the reprocessing of old waste dumps and tailings, helping miners extract residual value while mitigating long-term environmental risks.
“There are more projects revisiting old tailings because what wasn’t valuable 20 years ago is now economic at today’s commodity prices,” Smith said.
“It’s not just about recovering more material; it’s also about reducing environmental liabilities.”
Dassault Systèmes is also integrating artificial intelligence (AI) into its virtual twin platform, further enhancing predictive capabilities.
Aura, an AI-powered virtual copilot, was unveiled by the company at the 3DEXPERIENCE World event in Houston, Texas, in February.
“It’s an intelligent conversational chatbot for mining operations, where you can ask questions, and it provides responses based on the available data,” Smith said.
“It can summarise information quickly and allows you to dive deep into data across the entire operation by learning, teaching, and performing tasks for you.”
By embedding AI into the system, Dassault Systèmes enables mining companies to continuously learn from past performance, refining their processes over time.
“The advantage of AI is that it can analyse vast amounts of data quickly, summarizing key insights while providing links to source information for deeper analysis,” Smith said.
Dassault Systèmes’ Virtual Twin Experience offers innovative solutions for the mining industry, enabling companies to rethink models, processes, and business strategies to drive sustainable innovation. These cuttingedge tools allow users to develop and maintain cross-disciplinary virtual twins, transforming the future footprint of mining operations.
By integrating virtual twin technology, the mining industry can achieve greater efficiency, sustainability and strategic foresight, setting new standards for operational excellence and environmental responsibility. AM
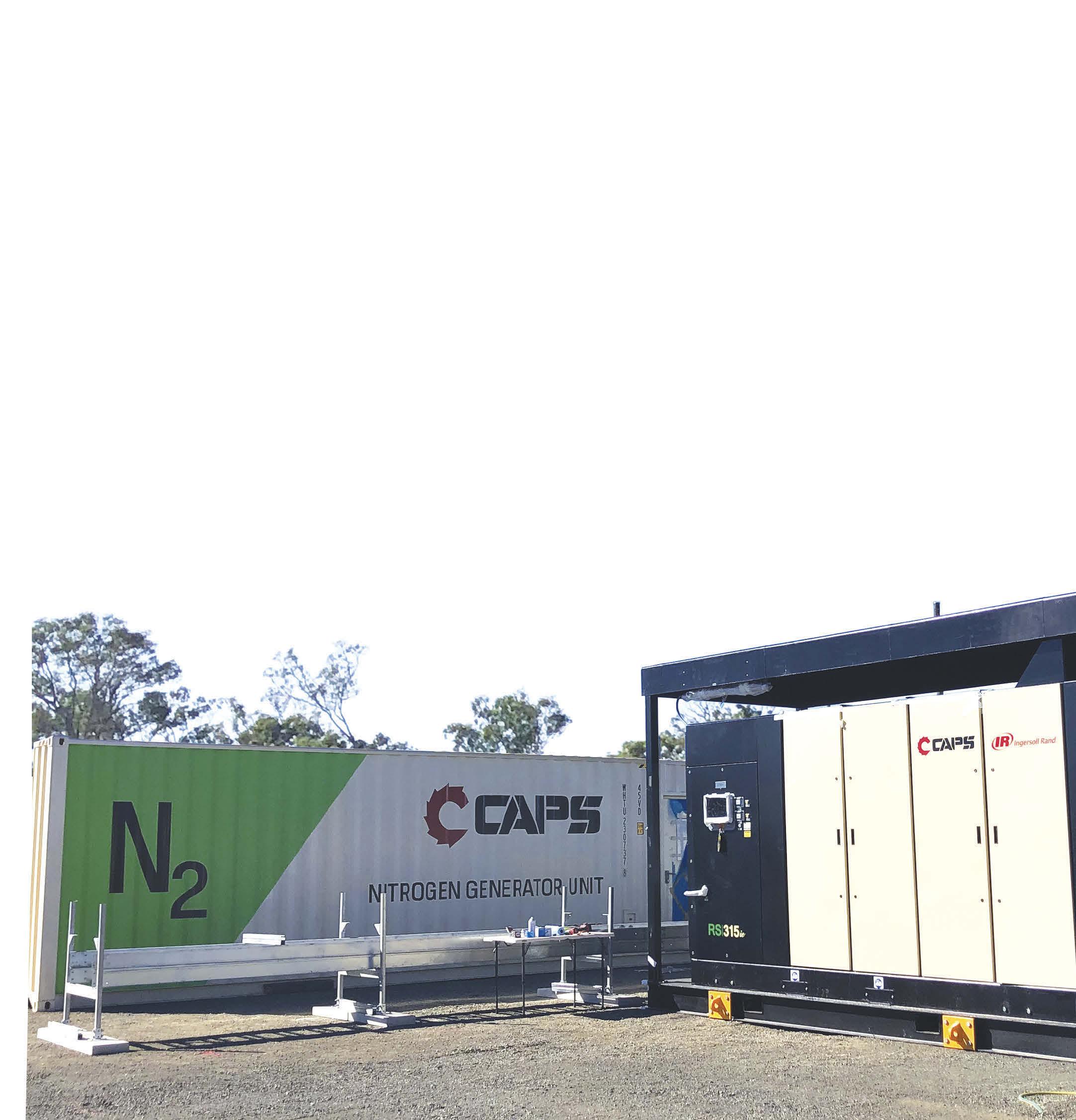
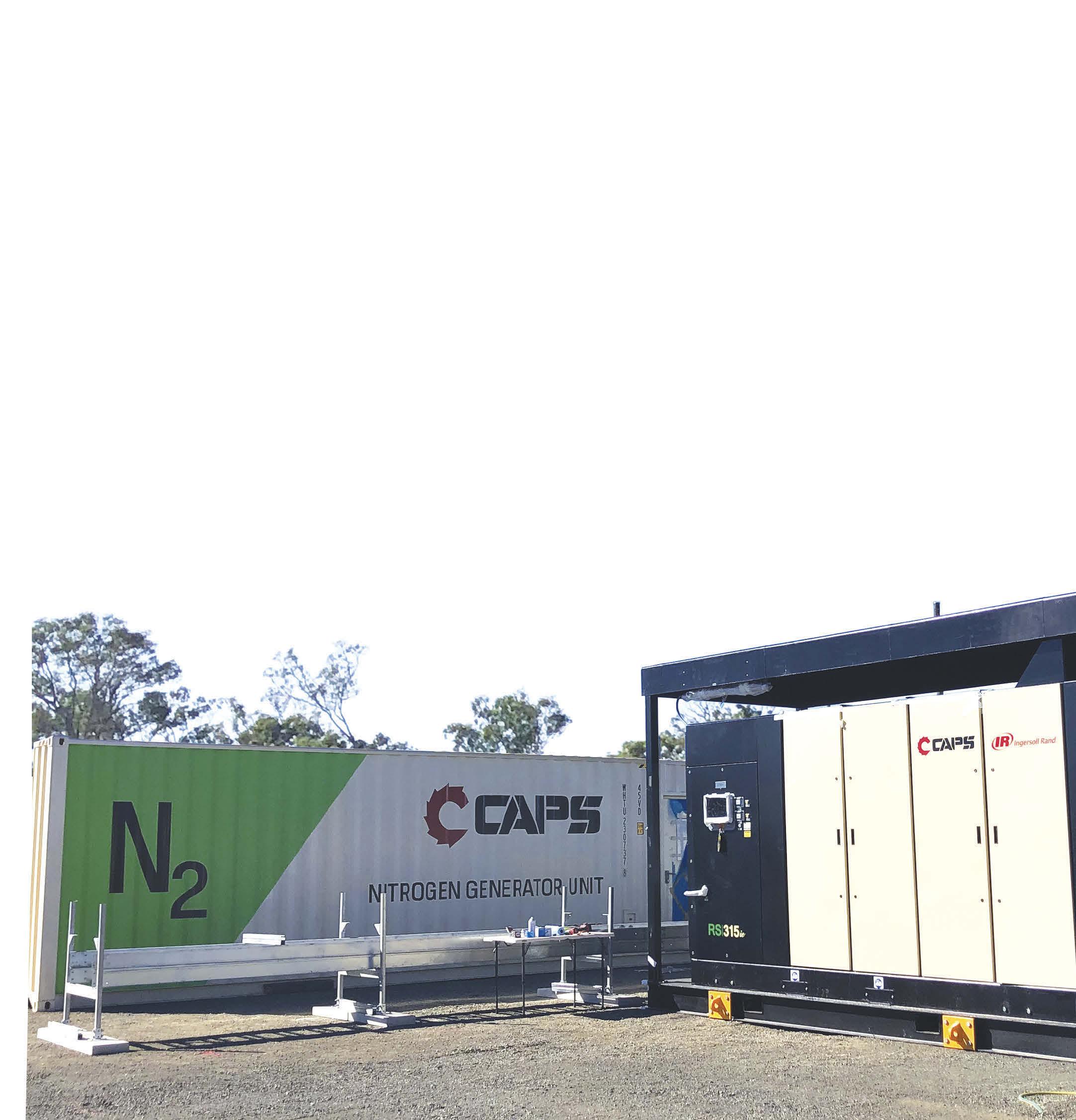
Global technology for Australian conditions backed by local support
A 360-DEGREE APPROACH
THEJO HAS BEEN PIONEERING MINERAL PROCESSING SOLUTIONS FOR OVER TWO DECADES.
As the mining and mineral processing industries continue to evolve, companies need partners who can provide not just products but complete solutions that drive operational efficiency, sustainability, and continuous process improvement.
Thejo Engineering’s commitment to innovation and excellence is reflected in the premium services the company offers through its subsidiary, Thejo Australia.
With a dedicated team based in Perth and across Western Australia, Thejo Australia has been supplying the mineral processing sector with high-quality engineering solutions for over a decade.
A legacy of excellence
Thejo Australia has been directly serving the Australian mineral processing market since 2013, offering an extensive range of products and services for the sector.
Thejo Australia leverages the expertise of its international parent company, which has a presence in India, Saudi Arabia, the United Arab Emirates, Brazil and Chile, bringing cutting-edge technology to the local market.
The company offers dedicated sales, service and customer support from its Perth headquarters, with workshops and a service centre catering to the needs of the local mining and mineral processing communities.
The facility, located in the Perth suburb of Bibra Lake, is accompanied by a servicing crew deployed at various locations across Western Australia, supporting mine sites with their product and maintenance queries.
“Thejo is committed to serving the Australian mining industry by offering complete solutions that not only meet but exceed expectations,” Thejo head of sales and marketing, mineral processing division Jomon Mathew said.
Proven
performance across the globe
Thejo Engineering is proud to offer a range of proven products that have been adopted by leading players in the mining industries in India, Australia, South America, Africa and Europe.
One such product is the THOR mill liner, available in rubber and composite versions for use in SAG (semiautogenous grinding) mills, rod mills, ball mills, scrubbers, and ceramic mills.
These liners have become the reliable choice for Thejo clients due to their high-level performance and durability.
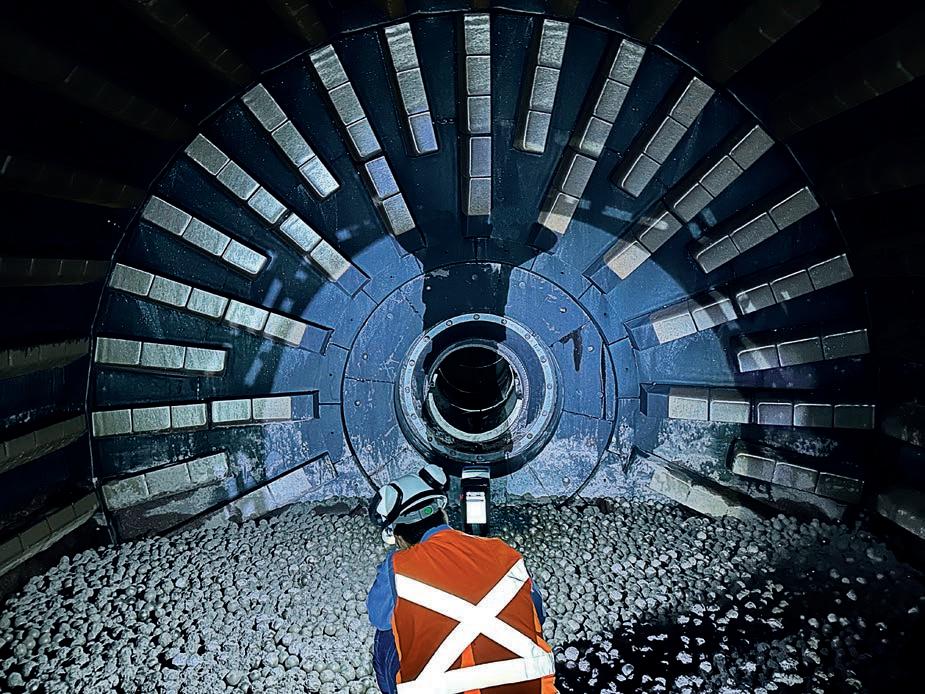
mill liners to be their first choice due to their unparalleled performance backed by our customer-centric approach,”
Thejo product head of mill liners Rishinath Udayan said.
“Another product our clients rave about is the GRATOR trommel solution, which is engineered to optimise mineral processing operations.”
By understanding the specific needs of each mineral processing unit, Thejo offers designs that can handle more slurry volume and reduce shutdown schedules.
In fact, the company has helped clients extend trommel operation periods more than 2.5 times from the standard 12 weeks, and close to four times from the standard 13 weeks in different applications, demonstrating its ability to provide robust engineering solutions that boost productivity.
End-to-end mineral processing solutions
Thejo recognises that mineral processing is a complex and demanding field. That’s why the company offers a range of engineering solutions that are designed to address every aspect of mineral processing – from bulk material handling and screening to slurry handling, flotation and filtration. Its solutions include products like RHINO wear panels in rubber,
WARDOG, a wet abrasion-resistant rubber sheet; and CERALINE, a rubber-backed ceramic lining panel.
These are just some of the materials Thejo offers clients, with these materials also used in Thejo-manufactured equipment such as slurry pipelines, sump boxes, launders, cyclone underpans, transfer chutes and tanks.
Thejo’s HIPO filtration solutions, a popular alternative for original equipment manufacturer (OEM) spares in the filtration industry, are a premium offering. The company provides spares for pressure filter presses, including rubber membranes, filter plates, pinch valve sleeves, and more.
The company also provides retrofitting, re-engineering, and operational and maintenance services to extend the lifecycle of filtration systems belonging to leading international brands such as Metso, Larox, Diemme and Andritz.
Leading the way in bulk material handling
Alongside its mineral processing solutions, Thejo has been at the forefront of developing innovative solutions to enhance conveyor system efficiency.
The company’s transfer-point solutions are designed to reduce spillage, mitigate dust emissions, and ensure the smooth flow of materials.
market share by providing technical services such as conveyor belt splicing, pulley lagging, and belt laying, ensuring clients’ conveyor systems are always operating at peak performance.
A holistic approach
Something that sets Thejo apart is its commitment to offering sustainable synergetic solutions (SSS).
These solutions encompass everything from the initial design and manufacturing of products to the ongoing supply and on-site services that help to ensure continuous process improvement for clients.
With SSS, Thejo takes a 360-degree approach to tackling mining challenges, offering not just individual products but comprehensive solutions that optimise every aspect of an operation.
The future of mineral processing
As the mining industry continues to grow and evolve, Thejo remains committed to providing innovative, sustainable solutions that help clients unlock the true potential of their operations.
By engaging Thejo, mining companies can be assured of more than just a supplier – they are rather engaging a partner dedicated to their long-term success. AM
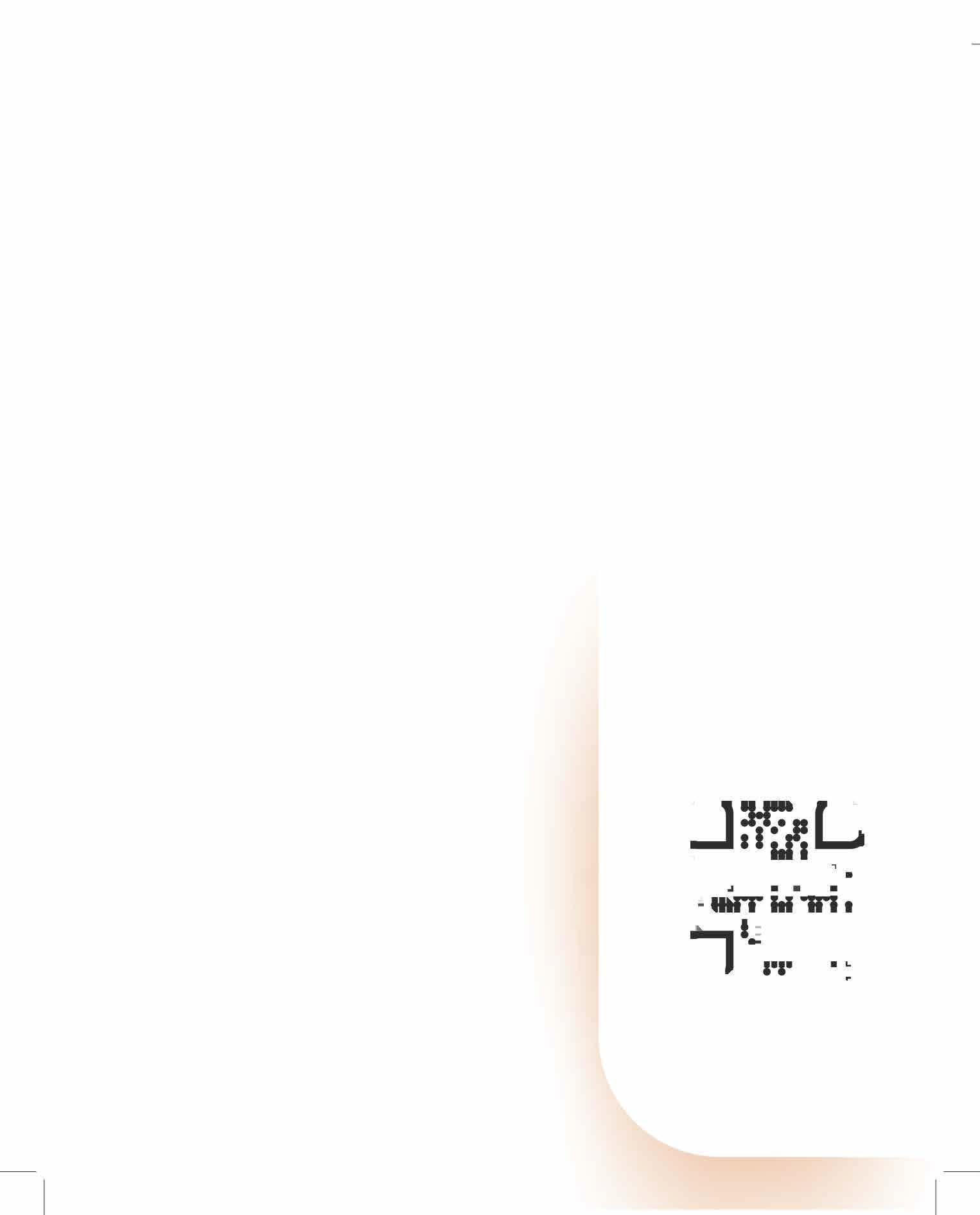
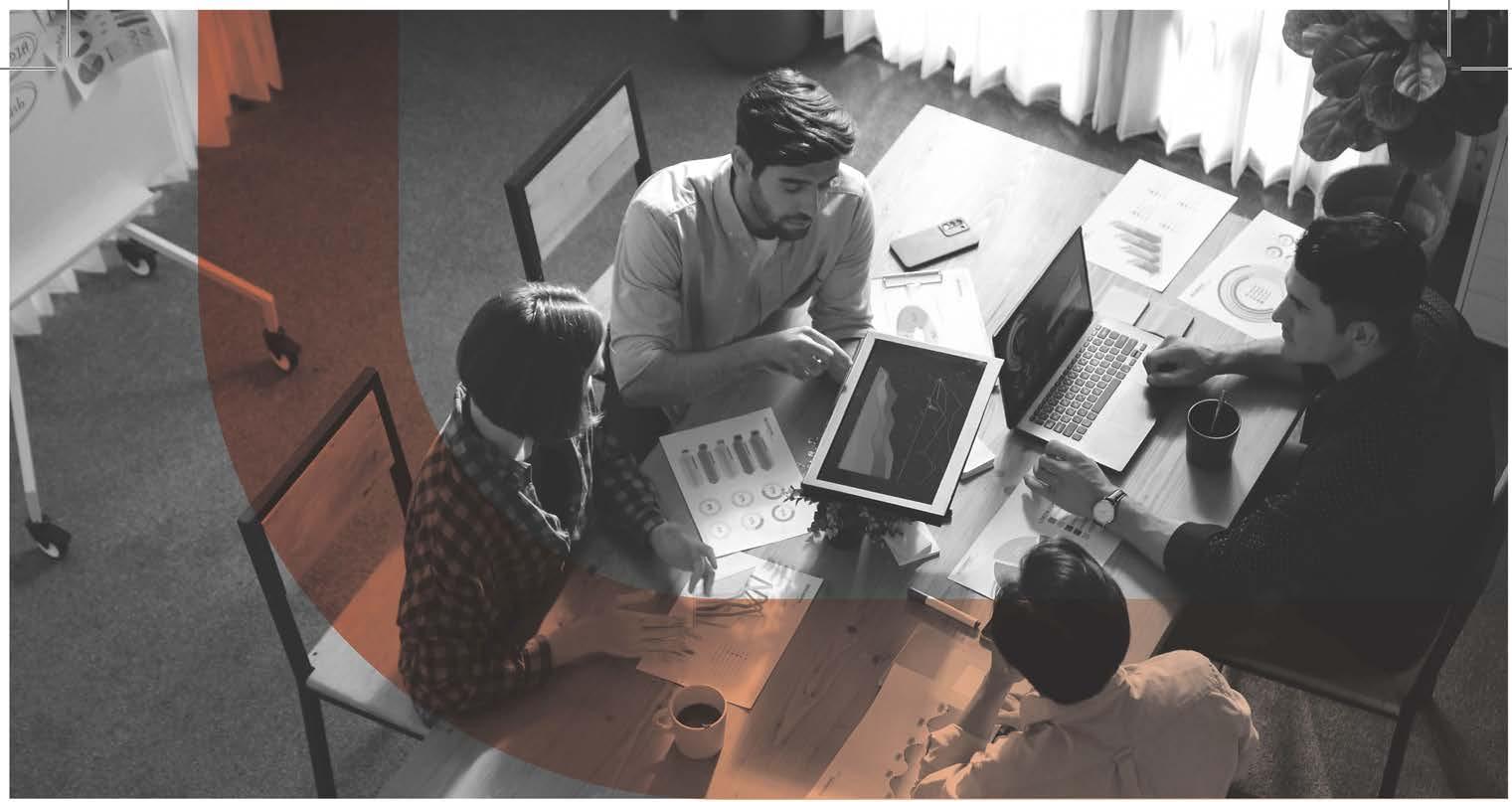
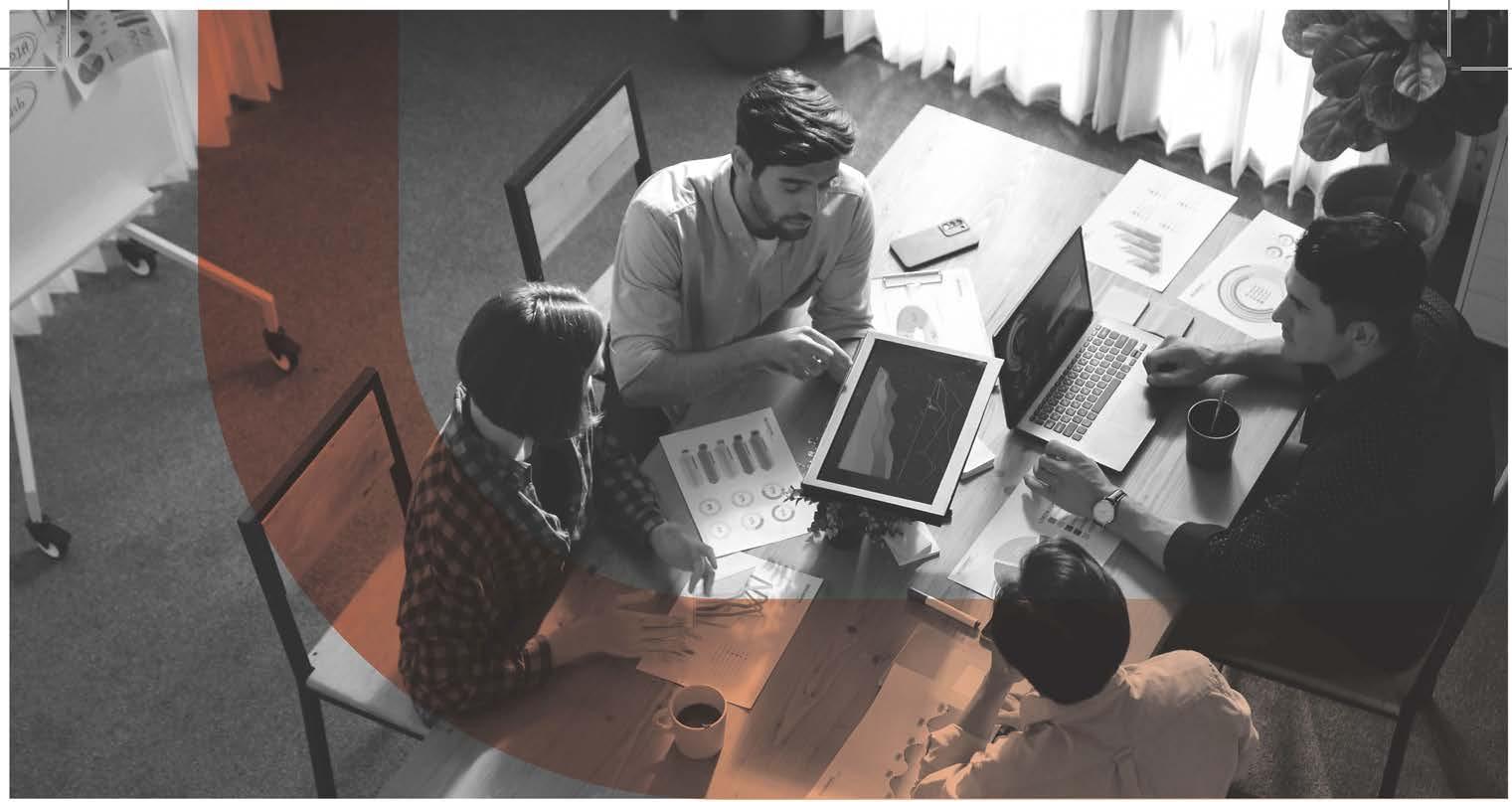
Technology that delivers. Performance that lasts.
Full-spectrum solutions engineered for real-world impact.
Efficiency, stability, and safety aren't just goals for mining operators. They're imperatives. And consistently unearthing IT and OT value demands a technology partner that doesn't just know your systems but understands the people and pressures that shape your operation.
At Brennan, we connect technology to real business outcomes. With a national presence, 27+ years of experience, and pressure-tested sector expertise, our strategic thinking, proven know-how, and full-spectrum solutions work hand-in-glove across IT and OT footprints.
And our True Performance System ensures we work closer, think sharper, and drive stronger results to help you unlock new levels of productivity, profitability, and security, and across networks, infrastructure, applications, telecoms, and beyond. Because we're all about technology that works, not technology you're sold.
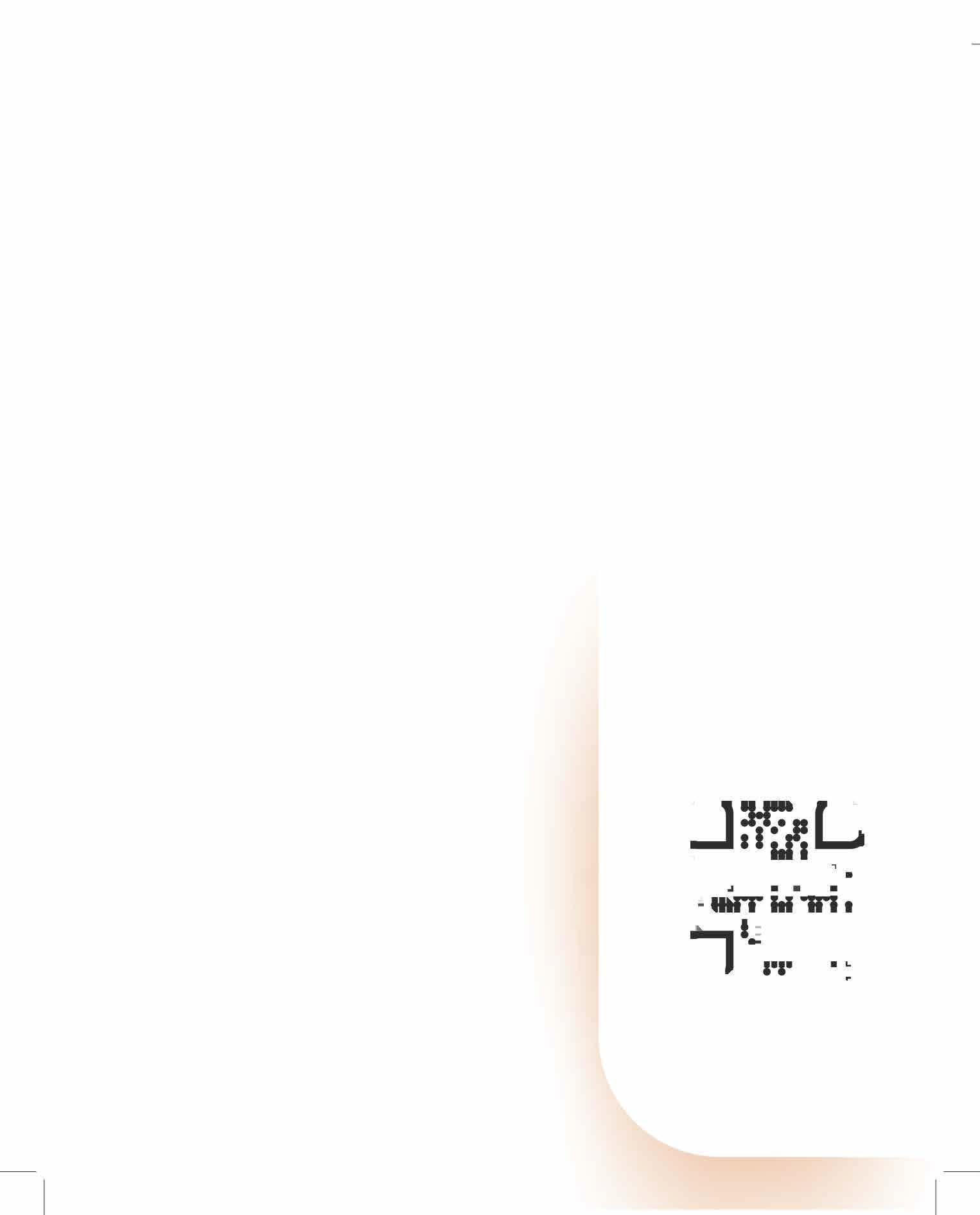
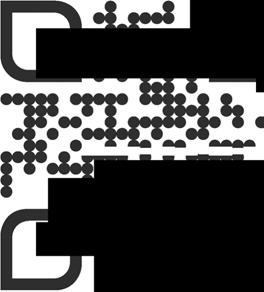


PIONEERING FLOTATION MACHINE MANUFACTURING
BACKED BY 70 YEARS OF EXPERIENCE, TÜFEKÇIOĞLU PROVIDES TURNKEY FLOTATION FACILITIES TO A RANGE OF INDUSTRIES.
Tüfekçioğlu (TK) has experience in rubber spare part manufacturing, particularly mill liners and manufacturing machineries for flotation plants, flotation cells, hydrocyclones, slurry and froth pumps.
Having been manufacturing rubber mill liners since the 1980s, custom design for all sizes and types of mill liners are a specialty for TK.
According to TK, the most important item in its manufacturing portfolio is the tank-type flotation cells. The company started research and development for the product in 2008, with the aim of creating its own design for these types of cells and, once the patent was gained in 2010, TK commenced manufacturing.
The uniqueness of TK’s flotation cells is derived from its mixing mechanism and froth output methods. The rotor/ stator features a patented shape for providing optimum parameters at the mixing zone.
The circular launders connected with radial launders can discharge froth as soon as it’s floated to ensure the highest froth recoveries.
The design of TK’s flotation cells is made by utilising computational fluid dynamics (CFD) programs. Several design candidates are evaluated and the optimum design is chosen to be prototyped.
This prototype tank cell is then used for measuring of flotation parameters such as bubble size distribution, sauter mean diameter (d32), superficial gas velocity (Jg), and air surface area flux (Sb). Then, with finalised parameters, manufacturing begins with unit volume sizes from 1.5–300m³. In parallel, manufacturing of conventional flotation
TK’s flotation cells use froth crowders, designed in-house, which facilitate pulplevel control, especially in scavenger cells. The crowders can be easily installed in existing flotation cells.
TK flotation cells have their own froth launder design, which contain donut and radial froth launders to help increase recovery.
Pulp level is controlled by a combination of ultrasonic level sensors and dart valves. The number of dart valves, which can be internal and external, vary depending on the cell size and the throughput. Special control software provides precise pulp-level control with main control area connectivity.
Polyurethane on steel is used in rotor/ stator manufacturing. Rotors can be turned bi-directionally, which helps to increase durability and therefore extend the warranty period.
TK uses its own rubber lining method for inner lining of flotation cells, ‘metal supported rubber lining’ (MSRL).
The lower sections of the cells exposed to intense abrasion are lined with MSRL, eliminating problems such as peeling, swelling, and breakage of the lining.
The system applied against abrasion and corrosion in TK’s flotation cells consists of three sections:
• MSRL is used for aggressive mixing zone
• MSRL also covers bottom and lower parts of the tanks
• Polyurethane lining is used for rotor and stator.
Advantages of TK tank type flotation cells
The top-down pulp flow around the rotor enhances the efficiency of bubble–
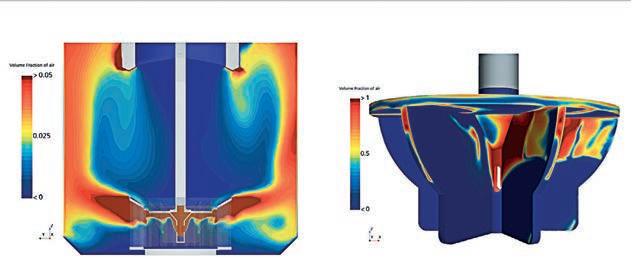
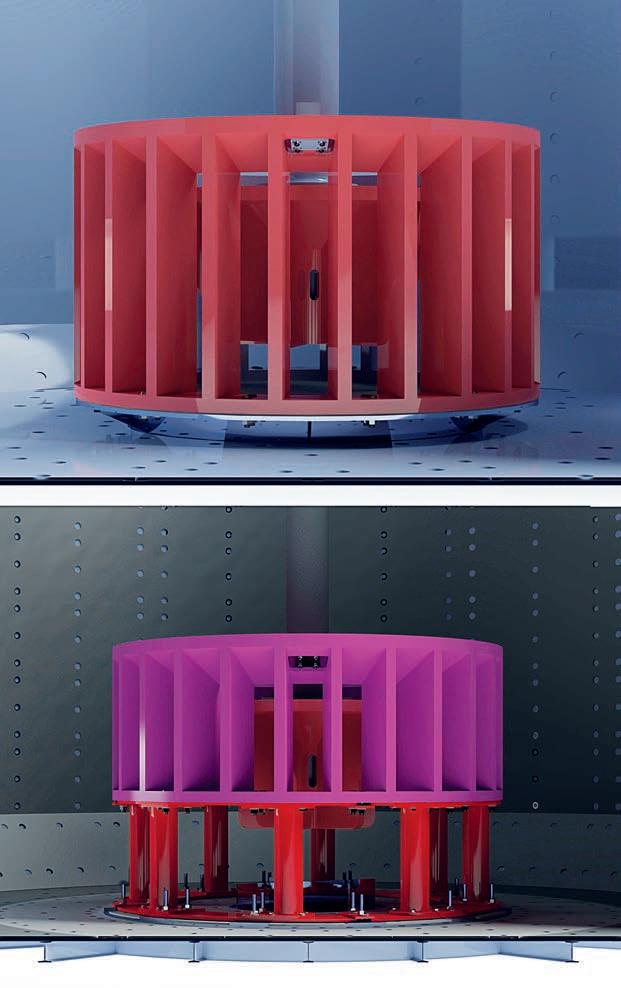
The distinctive rotor/stator configuration of these cells generates a vortex dispersion that diminishes progressively from the bottom to the top, permitting the formation of a quiescent zone.
The internal design of the tank bottom minimises dead zones inside.
The unique design and manufacturing stages ensure several values:
• M inimal vibration values (amax 0.5m/s2, >0.6mm)
• M inimum noise values (65–80 dB[A])
TÜFEKÇIOĞLU’S FLOTATION CELLS ARE MADE BY UTILISING COMPUTATIONAL FLUID DYNAMICS PROGRAMS.
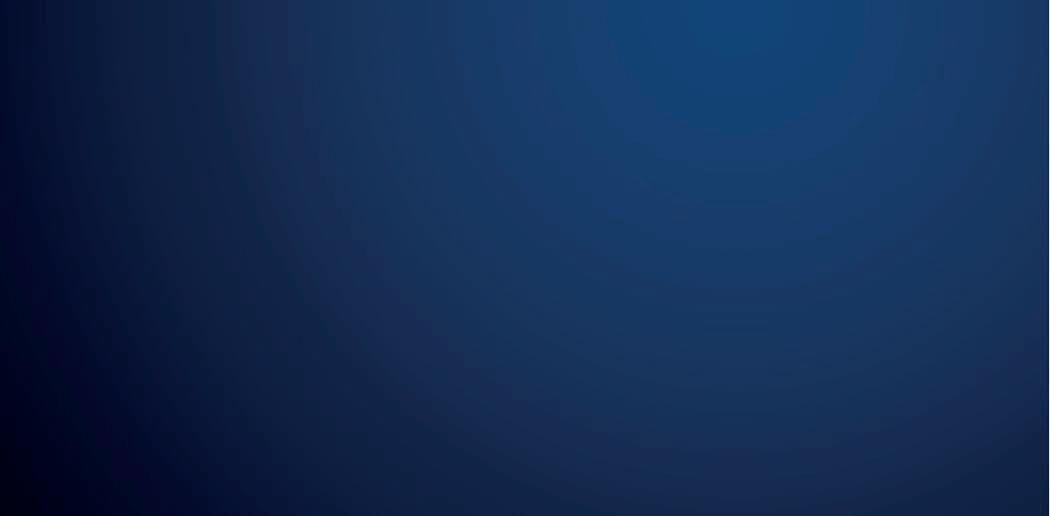
• Bearings experience minimal heating (maximum 55°C).
Separated rotor and stator is designed for easy maintenance, while optimised residence time distribution in the tank cell means bypass is reduced, and optimising design of the rotor, stator and tank with CFD leads to reduced energy consumption.
The unique rotor design also means less power consumption without any adverse effect on efficiency. The cells also feature better flotation performance for finer particles (<20 µm). AM
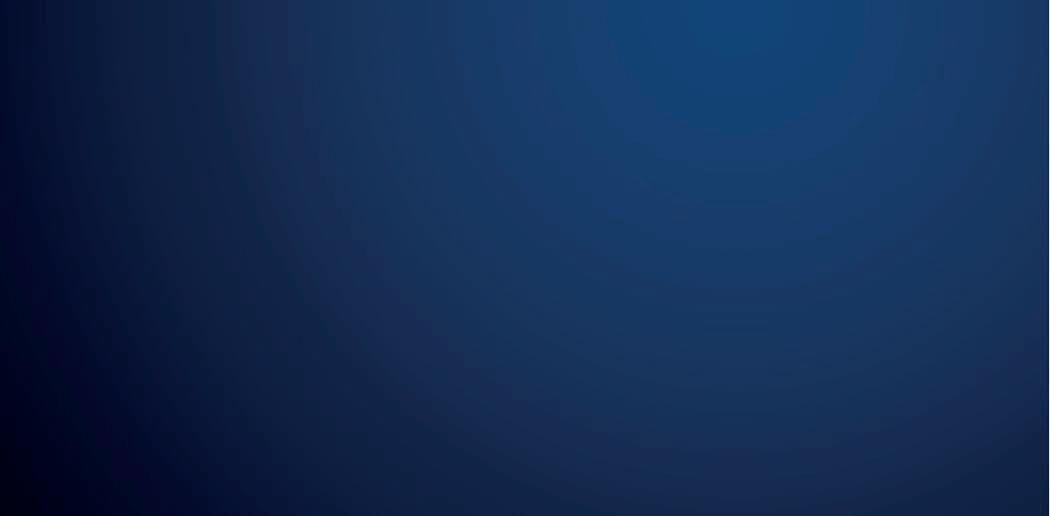

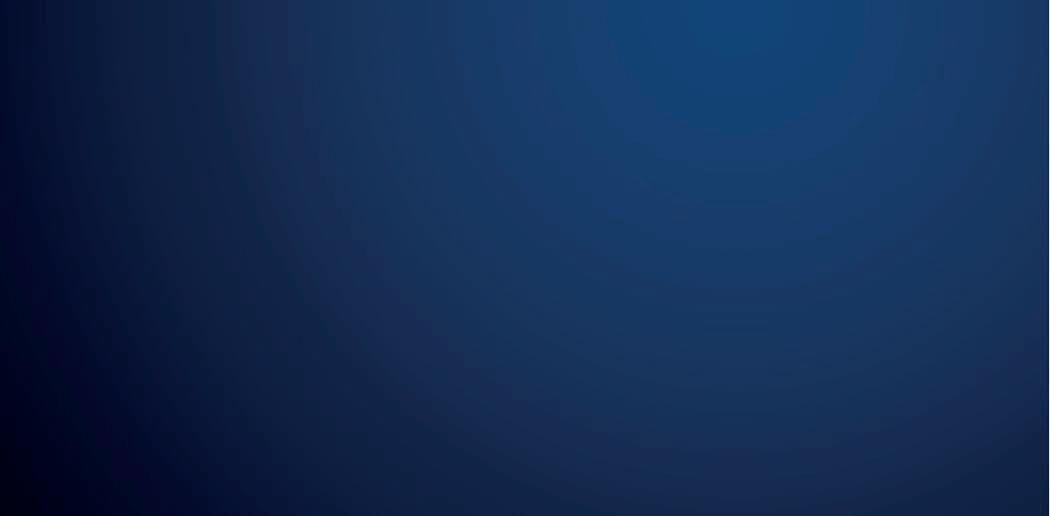
Master Drilling Australia sets the industry standard with world-class boring technology for vertical and horizontal underground production and development.
Drawing upon our 35-years experience and drive for innovation, MDA is committed to spearheading essential projects across Australia.
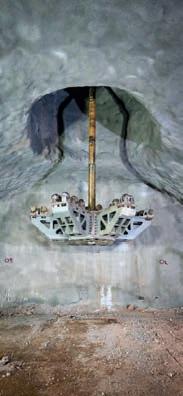
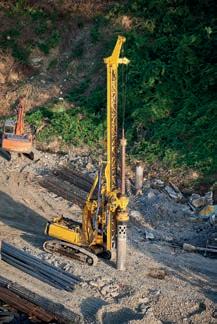
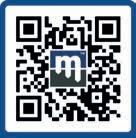
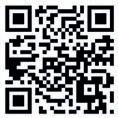
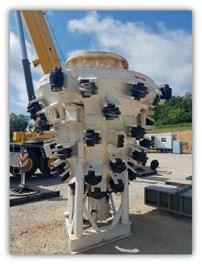
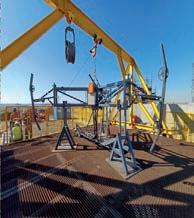
As an Original Equipment Manufacturer (OEM), we develop cutting-edge technologies that drive precision, efficiency, and safety in our services across industries. Our expertise, combined with a proactive approach, is shaping a new era in the Australian market.
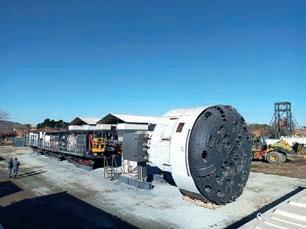

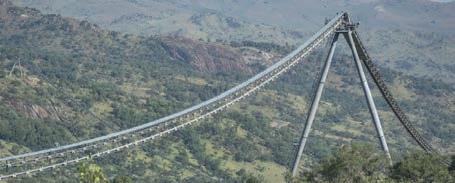

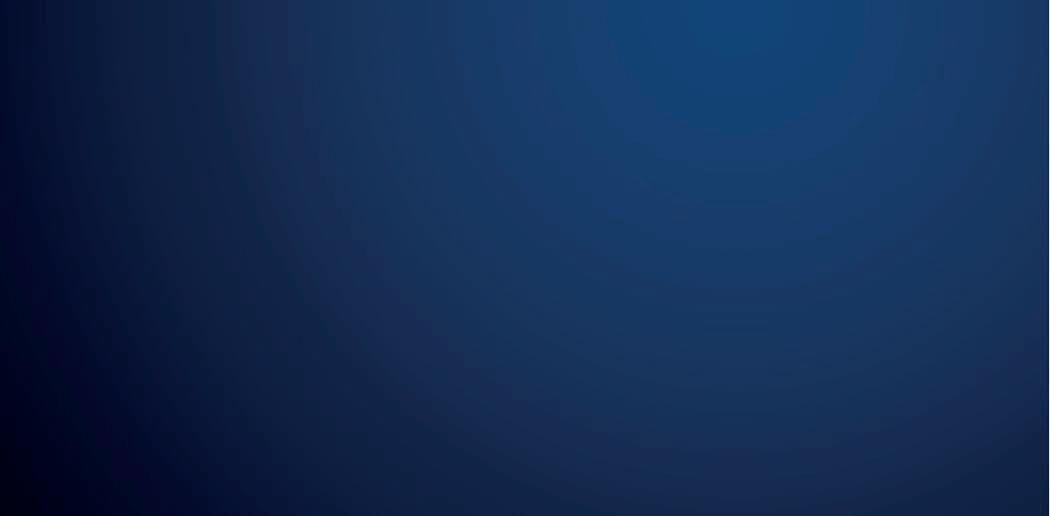
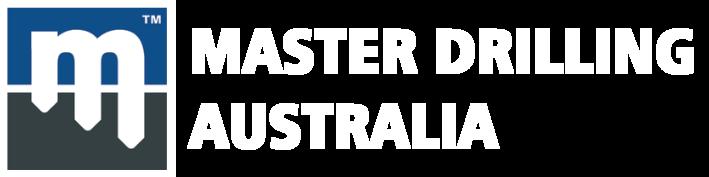
MINERAL PROCESSING STANDOUTS AT GRX25
GRX25 IS AN EVENT DESIGNED “BY INDUSTRY FOR INDUSTRY” THAT WILL CHAMPION INNOVATION AND COLLABORATION.
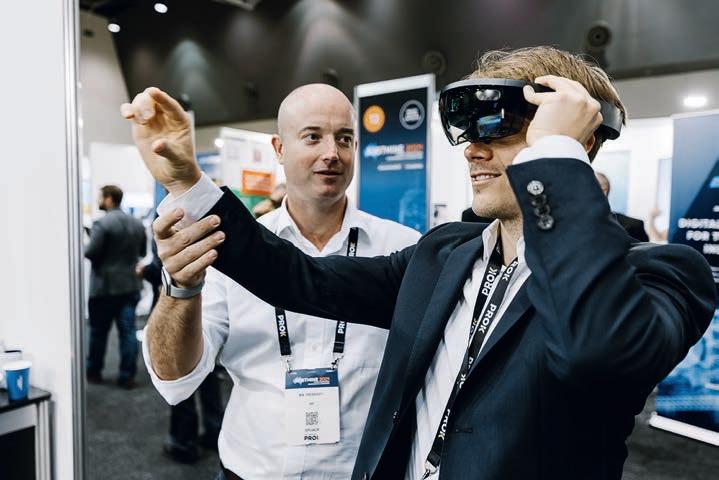
TInnovation Expo (GRX25), hosted by Austmine in partnership with AusIMM, represents a platform for showcasing cutting-edge advancements in the mining sector, and this year’s Accenture Innovation Zone is a prime example. Accenture managing director Eric Croeser believes the mining industry is on the cusp of a transformative era powered by artificial intelligence (AI) and other emerging technologies.
“In an environment ripe for reinvention, it’s critical for miners to embrace technology to remain futurefocused and stay globally competitive in the critical minerals and bulk commodities extraction sector,” he said.
GRX25, to be held in Brisbane from May 20–22, will enable Accenture to showcase its breadth of capabilities and services to assist mining clients in Australia and around the world.
“We are excited to share how our clients are utilising technology to remain ahead of the curve, optimise operations and enhance decision-making processes,” Croeser said.
Innovation is a core strategy for Accenture, which is committed to being at the forefront of technological change, driving a culture of continuous learning and innovation for its people and clients.
“We see the Accenture Innovation Zone as an exciting opportunity to support others with this mindset,” Croeser said. “Working with AusIMM and Austmine, we aim to give researchers, start-ups, entrepreneurs and tertiary
institutions exposure to foster new connections and a global platform to showcase cutting-edge tech solutions.”
Croeser will be presenting at GRX25, discussing significant growth in demand for critical minerals, driven by a shift to low-carbon tech. He will also discuss the challenges faced by mining companies operating in this sector, including how they can achieve net-zero via sustainable and responsible production practices.
Croeser will outline the technology interventions identified in Accenture research that can accelerate decarbonisation, as well as identify the pain points that can delay value creation.
Two companies in particular, Loop Hydrometallurgy and Optrix, are leading the way with technologies in mineral processing and digital integration, and are set to redefine the future of mining operations.
Ever-growing demand for critical minerals, especially copper, means the mining industry faces a growing supply shortage. Loop Hydrometallurgy has introduced the Halion Loop technology, a new hydrometallurgical process that enables mines to produce high-purity copper on-site, reducing reliance on traditional smelting. This innovative process is built on a saltwater-based extraction method that minimises costs, water usage, power consumption, and carbon emissions.
Unlike conventional technologies that require high temperatures, high pressures, and complex refining processes, the Halion Loop simplifies copper recovery while making it economically viable to
process low-grade, polymetallic, and arsenic-contaminated ores.
A key feature of the technology is its next-generation electrowinning cell, which reduces power consumption for copper recovery by up to 70 per cent, giving it the lowest carbon footprint of any copper extraction method globally.
Trials in 2024 demonstrated the capabilities of the Halion Loop. According to Loop Hydrometallurgy, the process achieved 99 per cent copper extraction from ores with as little as eight per cent copper content and from particles as large as 1080 microns.
Optrix has developed ARDI, a DataOps platform designed to consolidate, analyse and visualise operational data from mining machines and processes. ARDI acts as a centralised data integration tool, bringing together multiple data sources into a single accessible interface.
The technology has already demonstrated its value in several key areas, including remote monitoring, where it provides real-time visualisation of mining activities. It has also been instrumental in data-driven decisionmaking, helping companies identify inefficiencies and optimise performance.
Machine learning capabilities within ARDI further enhance its impact, allowing for predictive maintenance enhanced performance.
By analysing operator behaviour and machine performance, the platform can highlight areas for improvement, leading to increased productivity and reduced equipment downtime.
In mineral processing, ARDI has been used to fine-tune plant operations,
improving throughput while minimising energy consumption.
Currently in its growth stage, Optrix is expanding its presence in the mining sector by providing a comprehensive solution for digital integration.
With the ability to create a single source of truth for mining operations, ARDI is helping companies bridge the gap between raw data and actionable insights, making digital mining operations more efficient, cost-effective and sustainable.
A new era of innovation
The Accenture Innovation Zone at GRX25 highlights the transformative power of emerging technologies in the mining sector.
In addition to Loop Hydrometallurgy and Optrix, the Accenture Innovation Zone will house a further 14 innovators, including the University of Adelaide’s Stimula Strategic Consulting, Theia Simulation, Stratum AI, Metalogenia Australia, Greyman Ops, Swing Invent Holdings, and more.
As the resources sector strives to increase efficiency, reduce environmental impact and secure a stable supply of critical minerals, these innovations offer practical solutions that can drive longterm sustainability and profitability.
The Innovation Zone provides an ideal platform for the researchers, innovators and entrepreneurs to have a unique space to present their work to a global audience. AM
GRX25 will be held at the Brisbane Convention and Exhibition Centre from May 20–22. Register now at grx.au

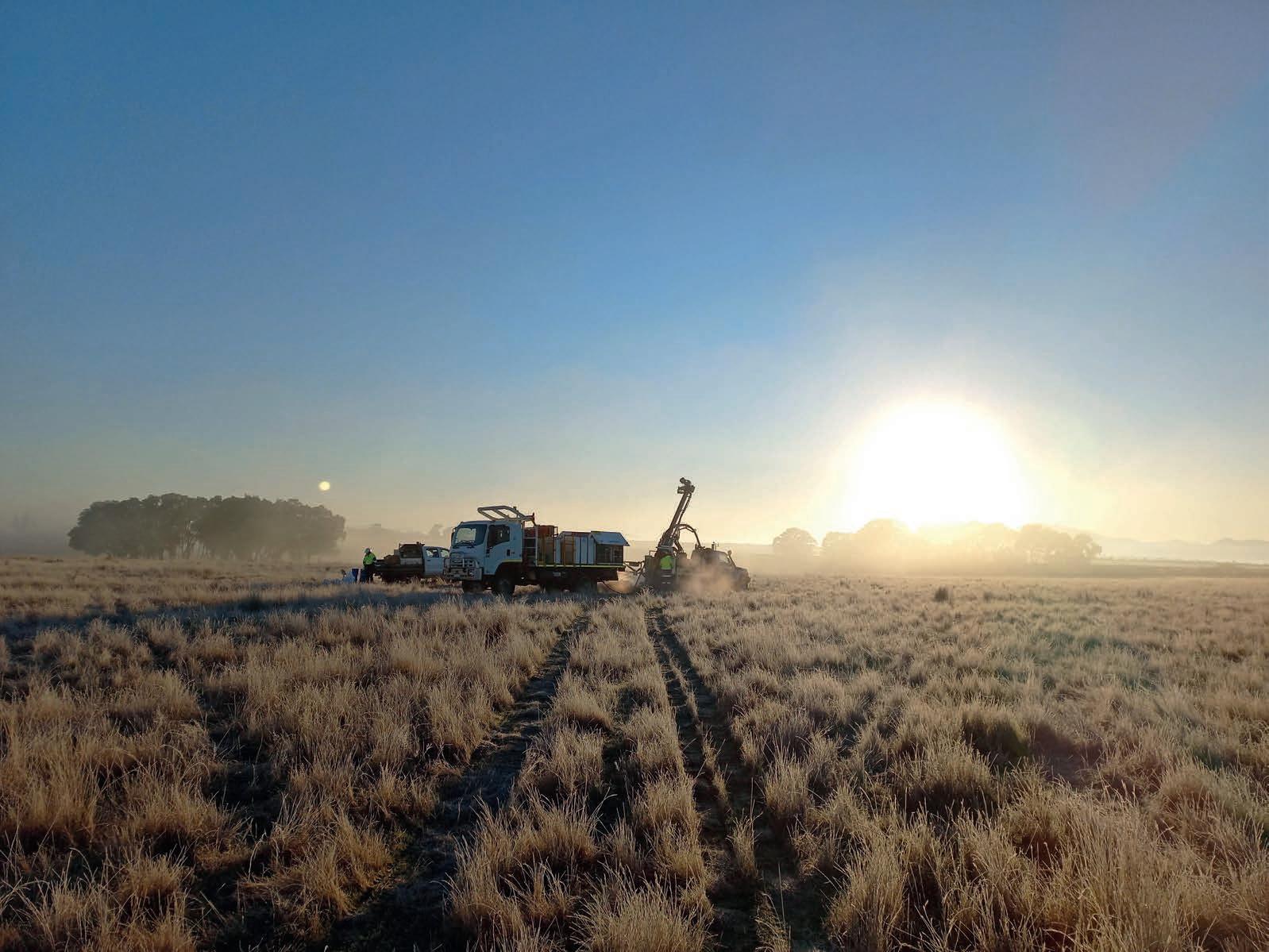
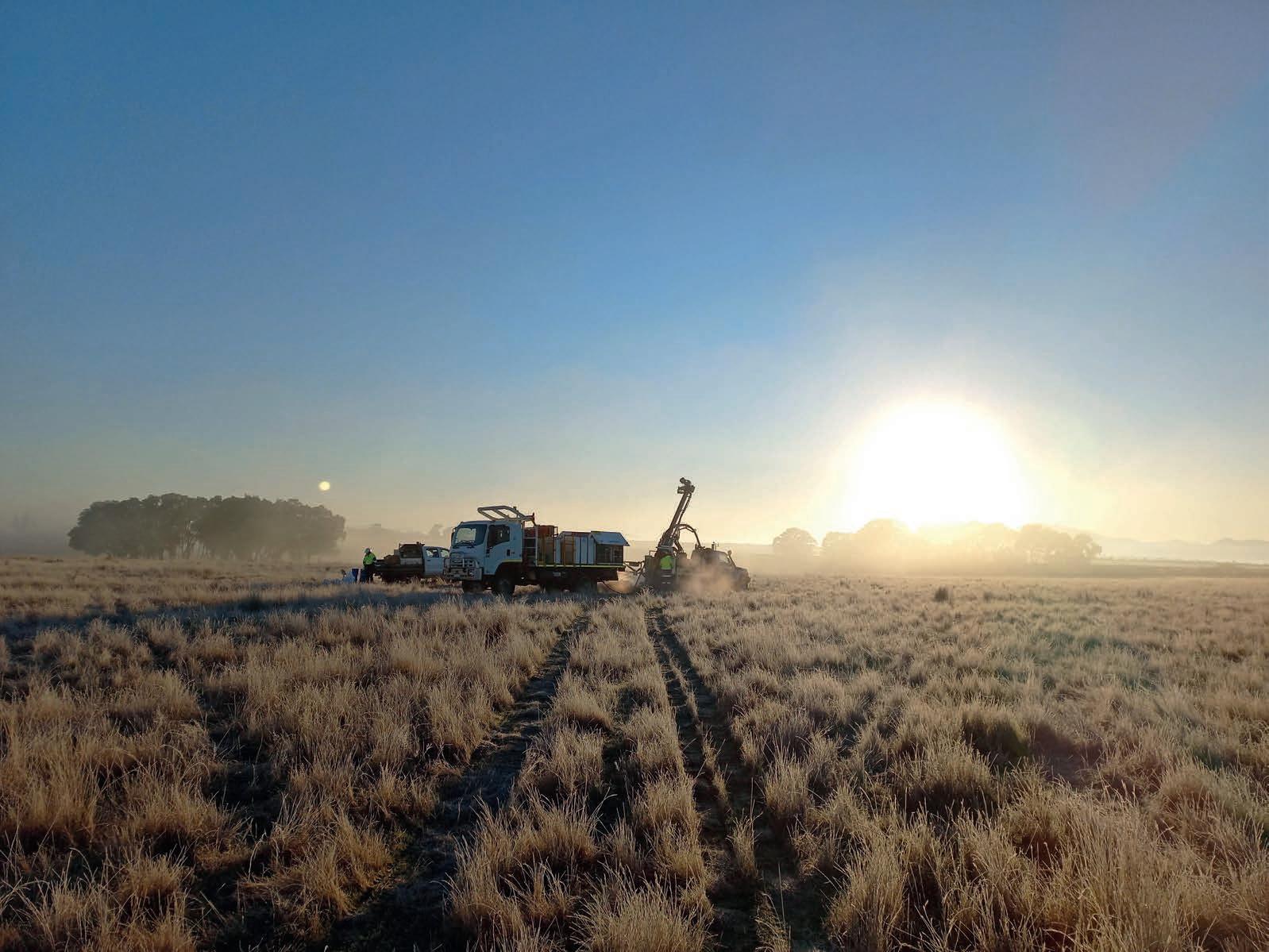
With a renewed vision and a fast-moving exploration strategy, Aureka is advancing some of the most promising gold projects in Victoria’s richest districts.
Extensive gold resource base: The most advanced undeveloped mineral resource in Victoria. Fast-tracked exploration: Two active drilling campaigns underway, targeting resource growth and new discoveries.
Strategic value creation: Committed to delivering exceptional returns for shareholders while strengthening local communities and industry partnerships.
Aureka is building momentum and positioning itself at the forefront of Victoria’s next gold era. Join us in this legendary adventure E info@aureka.com.au P +61 3 9692 7222
MINERAL PROCESSING IN THE SPOTLIGHT
PROUDLY HOSTED BY AUSTMINE IN PARTNERSHIP WITH AUSIMM, GRX25 IS SET TO SHOWCASE THE BEST OF MINERAL PROCESSING INNOVATION.
Mineral processing is a vital step in the mining sector Without it, valuable minerals and metals cannot be efficiently separated from their ores.
However, robust solutions built to withstand the various fluids involved in the processing are essential.
Enter the 2025 Global Resources Innovation Expo (GRX25), an expo “by industry, for industry”, to be held in Brisbane from May 20–22.
With a theme of ‘embracing a new era’, GRX25 will bring together people working across the global resources sector to network, drive important conversations about the latest trends, and showcase cutting-edge innovation.
With 150 exhibitors locked in and a plethora of networking opportunities, GRX25 will be a mining event not to forget. Australian Mining spotlights two mineral processing companies set to exhibit their solutions at the event, and what attendees can expect from each stall.
MMD Australia
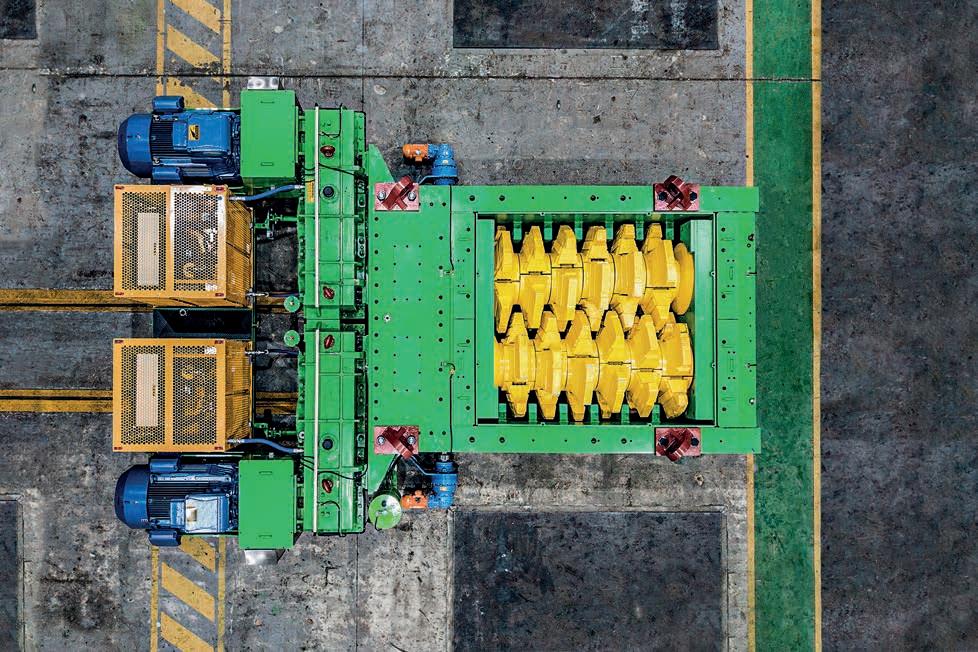
Backed by more than 45 years of experience, MMD Australia follows a ‘not-one-size-fits-all’ approach in designing mineral processing solutions that meet specific customer needs while delivering greater longevity.
This philosophy will be front and centre for MMD at GRX25.
“MMD retains the belief, which some might see as old fashioned, of
– it’s the best of both worlds,” MMD told Australian Mining. “GRX25 aligns perfectly with MMD’s core values of supporting the mining community through innovative, tailored solutions.
“MMD often works with clients who already have a concept in mind, but by engaging in forums hosted by associations the company gains deeper insights into challenges, refines ideas and develops new product protocols –ultimately driving value and innovation in the mining and metals industry.”
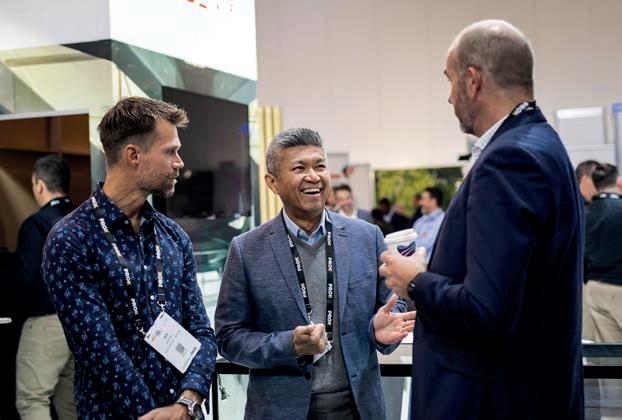
for their efficiency in crushing and processing a variety of materials, as well as its fully mobile surge loaders, which are integral for optimising material flow and improving operational efficiency.
Through its solutions, MMD offers benefits such as control over design and fabrication, a commitment to stocking critical spare parts, and expert maintenance support.
“One standout example of MMD’s equipment in action is a highperformance sizer that has been operating at a processing plant in Tasmania for nearly 30 years,” the company said.
“This particular machine has demonstrated remarkable longevity and reliability, continuing to play a vital role in the processing plant’s operations to this day. Over the decades, the sizer has proven to be an essential piece of equipment, efficiently handling the ore and contributing significantly to the plant’s throughput. The machine’s ability to maintain high performance, even after such a long period of service, speaks to the robustness and durability of MMD’s technology.”
MMD also views GRX25 as an opportunity to engage with attendees about the real challenges they face in their mineral processing operations.
MMD AUSTRALIA WILL EXHIBIT ITS HIGH-PERFORMANCE SIZERS, DESIGNED TO HANDLE VARIOUS MATERIALS AND THROUGHPUT CAPACITIES.
specific processing issues with us –whether related to efficiency, capacity or material handling,” MMD said.
“Our team is eager to listen, understand the unique challenges in processing, and discuss how our solutions can be tailored to meet their needs.”
Weir Group
Supported by an extensive portfolio of mineral processing solutions, technologies and equipment, Weir is ready to take GRX25 by storm.
Weir general manager – original equipment projects, minerals division Peter Alexander said the GRX25 theme of ‘embracing a new era’ aligns with the company’s commitment to innovation, collaboration, environmental stewardship and technological advancement.
“GRX25 offers valuable networking opportunities with industry leaders and experts, helping us strengthen our market presence and drive the industry forward,” Alexander told Australian Mining.
“We will be exhibiting our ENDURON high-pressure grinding rolls and vertical stirred mills and the CAVEX DE cyclone, both designed to enhance efficiency and reduce
energy consumption, and our NEXT Intelligent Solutions platform, which leverages digital twin technology to provide real-time monitoring and predictive maintenance, optimising equipment performance, process efficiency and decision-making.
“We will also feature Motion Metrics AI (artificial intelligence)-enabled sensing technology and ESCO bucket and tooth systems, demonstrating our comprehensive approach to advancing mining technology.”
Key trends on display at GRX25 will be AI and machine learning, two technological advancements designed to increase productivity and safety.
“By integrating advanced AI and machine learning into our offerings, we provide unparalleled process optimisation and predictive maintenance capabilities,” Alexander said.
“This digital transformation allows us to deliver real-time insights and recommendations, enhancing operational efficiency and reducing downtime.
“Deep customer insights and world-class material science and engineering expertise enable us to develop tailored solutions that address the unique challenges of each mining operation.”
Delivering integrated technology solutions, Weir will also showcase
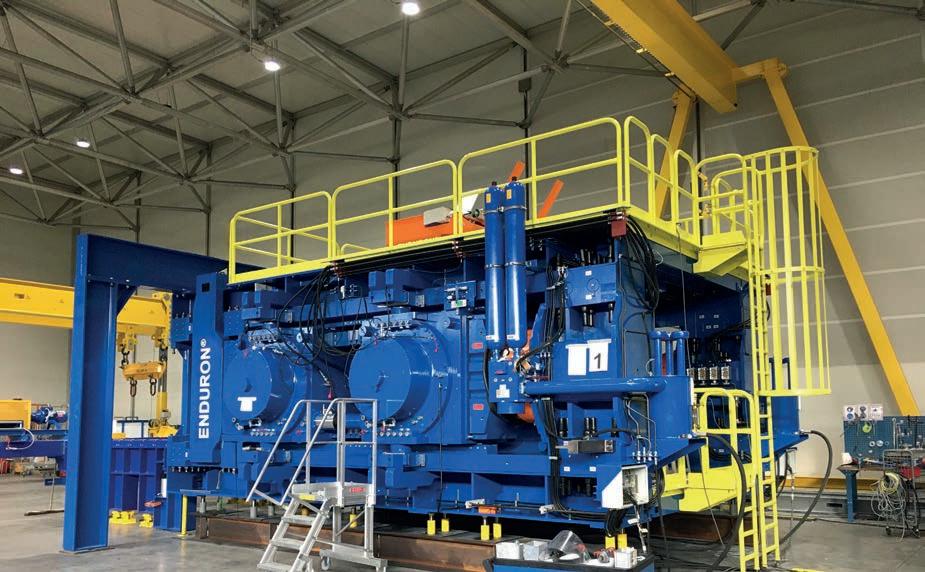
signature brands such as WARMAN, GEHO, LINATEX and MULTIFLO, among others.
Weir representatives will be on the exhibitor floor at stand C20, ready to showcase its portfolio of innovative technologies while it answers questions from attendees.
“No one serves more mines than Weir,” Alexander said.
“Working in close partnership with our customers, we help them to
move less rock, use less energy, use water wisely and create less waste –accelerating the path to smart, efficient and sustainable mining.”
Alexander said Weir is excited to show industry leaders and other experts how the company’s cuttingedge solutions can drive the future of mining.
“By integrating the capabilities of our leading brands, we deliver comprehensive solutions that
address the full spectrum of challenges faced by today’s mining industry,” he said.
“Our focus on continuous innovation and our close partnerships with customers worldwide enable us to drive progress in an industry that is constantly evolving.” AM
GRX25 will be held at the Brisbane Convention and Exhibition Centre from May 20–22.
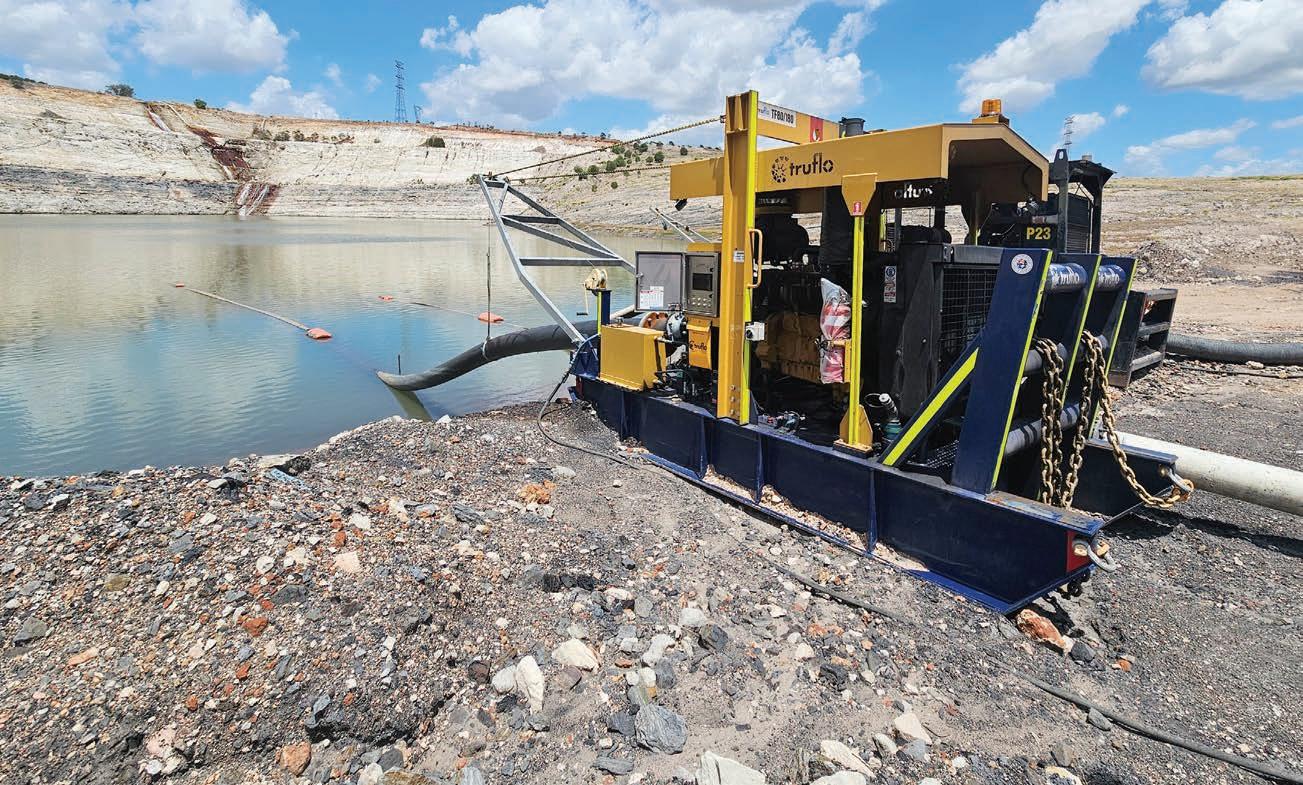
Truflo Pumps’ dewatering solutions have kept mining operations running smoothly in the harshest conditions imaginable — right around the world. Built to outlast, engineered to outperform We understand that in your business, downtime isn’t just inconvenient — it’s costly.
BUILDING BLOCKS OF THE FUTURE
VHM CHIEF EXECUTIVE OFFICER
RON DOUGLAS ON HOW THE COMPANY PLANS TO BRING ITS FLAGSHIP PROJECT ONLINE TO MEET GROWING RARE EARTHS DEMAND.
According to the International Energy Agency’s ‘Global Critical Minerals Outlook 2024’, demand for magnet rare earths nearly doubled between 2015 and 2023.
The same report found that demand for rare earths has the potential to double again by 2050 due to the increased adoption of clean energy solutions such as battery storage and solar farms.
As the global energy transition sees the world shift away from fossil fuels and embrace future-facing commodities, Australia is keen to play a part in providing the rare earths needed to meet the growing demand.
China has long held the title as the world’s largest rare earths producer, followed by countries such as Brazil, Vietnam and Russia.
Australia currently makes up four per cent of the world’s rare earths resources and five per cent of the world’s total rare earths production, stemming solely from Lynas Rare Earths’ Mt Weld operation in WA.
A company keen to supply rare earths is VHM, an Australian-based miner that started trading on the ASX in January 2023 through a $30 million initial public offering (IPO).
VHM’s flagship asset is the Goschen rare earths and mineral sands project in the Loddon Mallee region of Victoria,
which is on track to achieve first production in the coming years.
VHM closed 2024 on a high by securing its environment effects statement (EES) from the Victorian Government, marking the first time a greenfield mineral sands mine has been greenlit since 2008.
“It was quite a significant event,” VHM chief executive officer Ron Douglas told Australian Mining
“Concurrently, the Victorian Government released its critical minerals roadmap, sending a clear message to the market that Victoria is back in the mining business.”
Victoria’s critical minerals roadmap highlights the state’s vast mineral reserves and opportunities for growth, with an eye to developing critical mineral processing and battery production industries in the future.
The roadmap also includes the creation of critical minerals priority development zones, providing certainty for players like VHM and local communities in mining locations.
“The city of Melbourne was built off the back of gold mining,” Douglas said. “It was the gold rush at Bendigo and Ballarat that actually (made) Melbourne the richest capital in the world (in the 1880s).
“Victoria then drifted away from mining, but now the state is heading back into it.
“The Murray–Darling Basin holds sands rich with rare earths mineralisation, which can be leveraged to create a new rare earth industry in Victoria.”
Rare earths are listed on the Australian critical minerals list. This basket of minerals includes neodymium, praseodymium, dysprosium and terbium – magnet rare earths with a key role to play in a clean energy future.
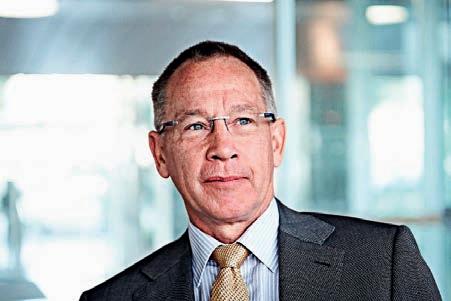
In VHM’s case, these rare earths are contained in Goschen’s deposits within minerals such as monazite and xenotime.
“If you go back through the millennia of time, inland seas eroded the granite structures where our orebody is, depositing our mineralisation – both the rare earths and the heavy minerals –into a sand setting as the seas retreated,” Douglas said.
“Our mining is essentially just digging up sand, taking the rocks out, and using gravity spirals to separate the heavy minerals. The rare earths are then separated from that product.
“Many of our competitors are in hard-rock environments, meaning they have to drill, blast, mine, crush and grind ore before they even get to our starting point.”
VHM plans to develop Goschen through a staged approach.
Stage one (years 1–3 of production) will deliver 1.5 million tonnes per annum (Mtpa) of throughput
for 4300 tonnes per annum (tpa) of rare earth mineral concentrate (REMC) production and 69,000tpa of zircon-titania heavy mineral concentrate (HMC).
With construction commencing in the fourth quarter of 2025, stageone production is set to commence in the fourth quarter of 2026. This process will cost $160 million to get up and running.
The combined production of REMC and HMC will then help fund stage-two construction, which is set to commence after the first three years of operations.
This will cost an additional $85–90 million and support 5Mtpa of throughput for 9000tpa of REMC production and 134,000tpa of HMC production. Stage two will support an additional 19 years of mine life.

Douglas said this phased approach, which was developed with Yellow Iron Fleet, de-risks and simplifies Goschen.
“Our benefit is we can, from the cash flow, self-finance to the approved 5Mtpa project,” Douglas said.

banks,” Douglas said. “The Federal Government is supporting critical minerals development, so we are in discussions with government agencies to see how they can participate.
“We are also seeing how our offtake partners can contribute, with the potential to secure debt and equity.”
Goschen’s Major Project Status was recently extended for three years by the Federal Government, signalling the asset’s importance to meeting the growing rare earths demand.

technologies.
“We reached an all-time rare earths price high in 2022, and if you look at the last few months, the commodity is ticking up. As long as the market grows, rare earths are a worthwhile investment.”
VHM has established a dual commodity stream to bolster its bottom line in the years to come. With regulatory approvals moving at pace, the company’s Goschen project is becoming a key cog in Australia’s critical minerals aspirations. AM
ATLAS COPCO

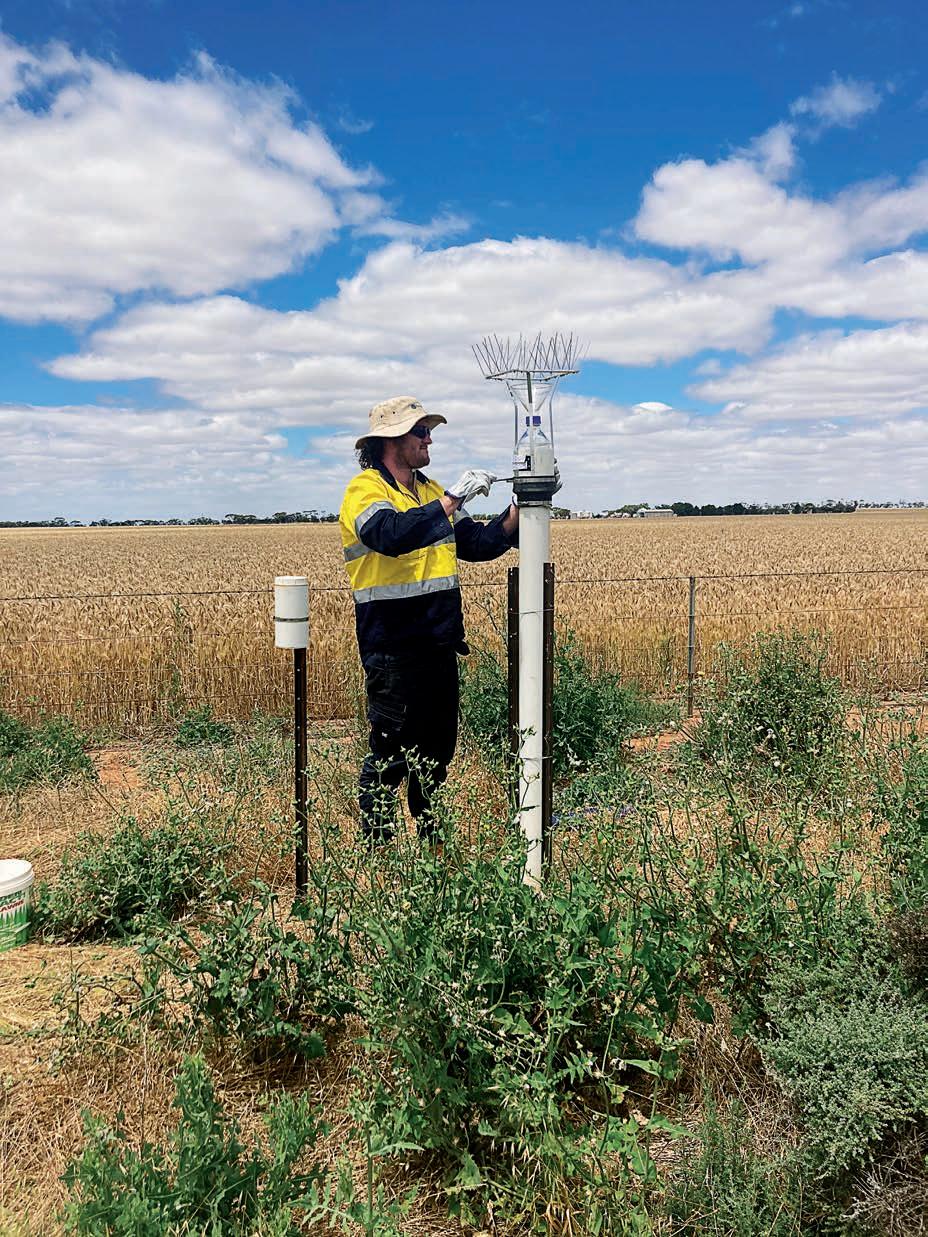
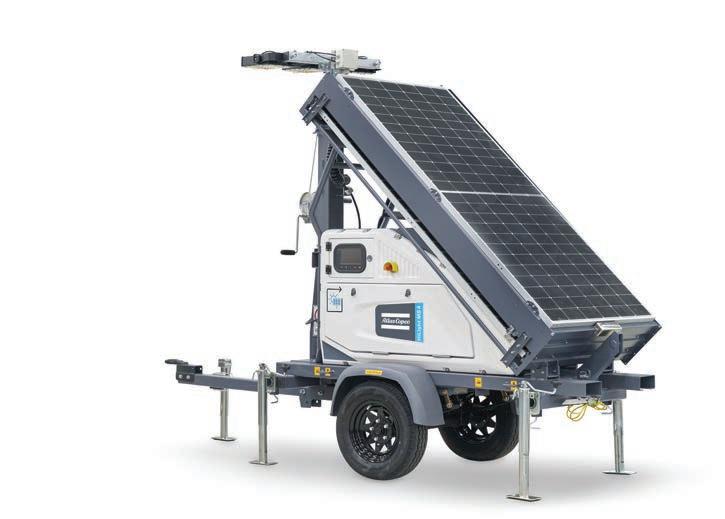
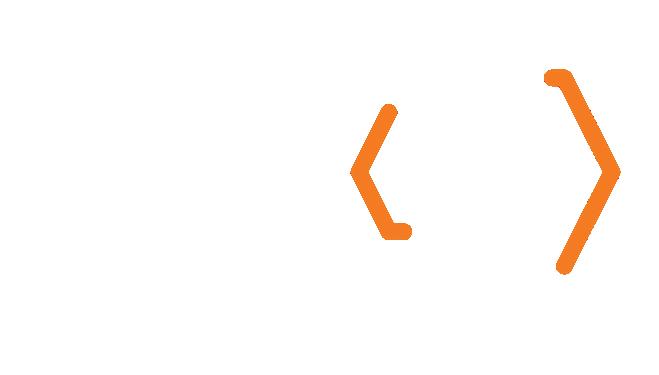
A GOLDEN RENAISSANCE
AUREKA IS AIMING TO UNLOCK A GOLDEN TREASURE CHEST LYING BENEATH VICTORIA’S SURFACE.
Victoria has become a hive of exploration in recent years, as junior miners look to discover the next Swan Zone – one of the world’s highest-grade gold deposits.
Aureka is one such company, with a suite of gold projects that could enter production in the coming years.
A name change from Navarre Minerals in late 2024 signalled a new direction for a company that has been focused on Victorian gold for years. The new moniker combines ‘Au’, the chemical symbol for gold, and ‘Eureka’, a common expression when a discovery was made during the Victorian gold rush in the 1800s.
“Through the name change, we really wanted to acknowledge that while a lot of small companies pivot to the next best thing, whether it be a different commodity or jurisdiction, we haven’t done that,” Aureka managing director James Gurry told Australian Mining.
“Having accumulated several projects across the state, we’re committed to bringing Victoria’s gold to life, because there’s far more gold to be found. ‘Aureka’ captures that sense of discovery.”
Aureka is represented by its Irvine, Tandarra, St Arnaud and Jubilee gold projects in Victoria, each of which is proximate to known goldfields. And these are not early-stage projects.
“We’ve inherited a lot of existing discoveries made by the previous team,” Gurry said.
“The accounts show that $30 million of work has been done on these discoveries, with $20 million spent on the Irvine project.”
A notable discovery made by the previous team is the Resolution lode within the Irvine project, with Resolution boasting an inferred JORC resource (announced in March 2021) of 264,000 ounces (oz) at 2.61 grams per tonne (g/t) gold. Aureka commenced drilling at its Irvine project in January, followed by drilling at Tandarra in February.
With little drilling completed at Irvine since Navarre released the project’s March 2021 resource estimate, Aureka is eager to maximise past successes.
“We identified last year during planning that the southern shoots at the Resolution lode have real potential, and we want to test how good the grades get at depth,” Gurry said.
Aureka is focused on an Irvine exploration target containing 280,000–420,000oz at 2–3g/t gold, with the hope of bringing some of these projected mineralisation into the existing JORC resource.
“We want to grow the size of Irvine project and see if the project’s two lodes, Resolution and Adventure, link up,” Gurry said.
The Tandarra project is located near Bendigo in the same region as the Fosterville mine, a more “recently famous” area of gold mining that has produced 22 million ounces of in the past.
“Tandarra has relatively shallow cover, meaning there’s not much topsoil and dirt to drill through before you hit fresh rock and potential mineralisation,” Gurry said.
“The project adjoins the wellknown Four Eagles discovery, made by Catalyst Metals and Gina Rinehart’s Hancock Prospecting. They’ve already defined 160,000 ounces at eight grams per tonne, and within that there’s a subset of 70,000 ounces at a super high grade of 26 grams per tonne.
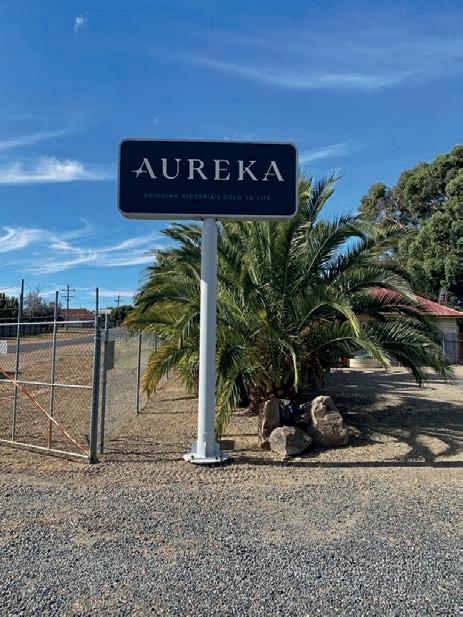
“We’ll be testing some of the northern reaches of the Tandarra tenement to see if it links up to some of the Four Eagles mineralisation. We’ve already identified, through the
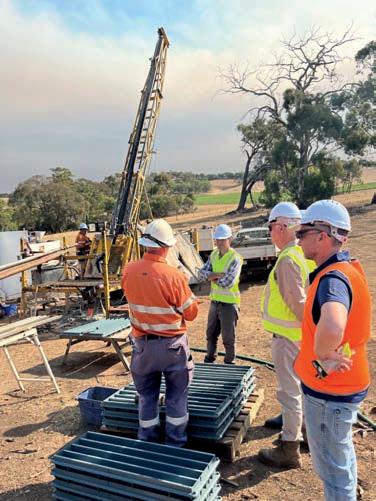
the company has one diamond drill rig operating at all times.
“We’ve got 7000 metres of diamond drilling occurring over the coming 12 months, and on top of that we’ve got around 6000 metres of aircore drilling, so it’s a huge amount
of drilling that we’ve got planned and underway,” he said. “The key thing for us is to continually update the market on the work we’re doing, and hopefully by the second half of the year we have enough Irvine drilling and results under our belt to update the March 2021 JORC resource.
“Ultimately, I want the company to be looking at one million ounces of JORC resources across our projects within 12 months.” AM
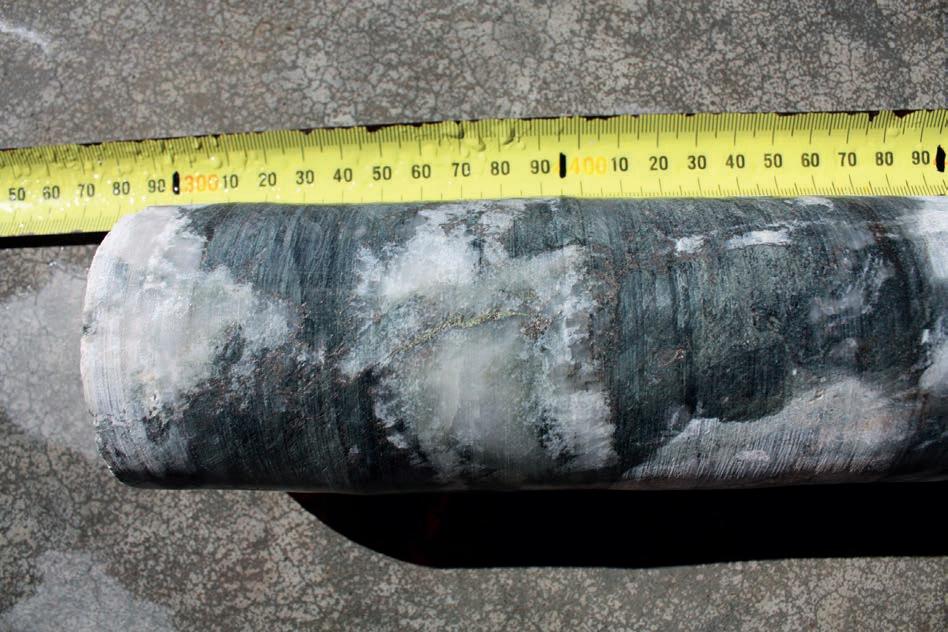


MORE THAN THE ‘POWERLINES GUYS’
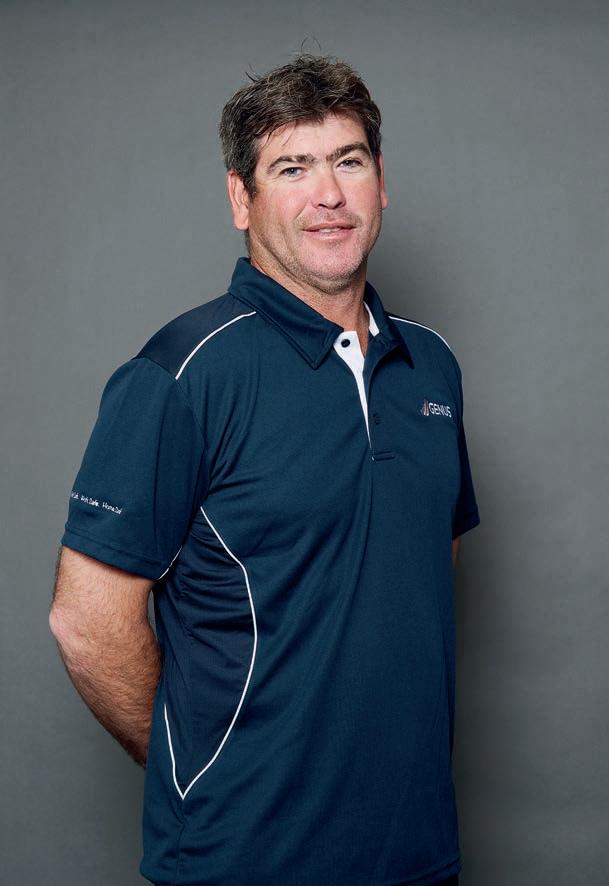
AUSTRALIAN MINING SAT DOWN WITH GENUS MANAGING DIRECTOR DAVID RICHES TO DISCUSS THE COMPANY’S RAPID GROWTH TRAJECTORY.
Aspecialist power and communications solutions provider is taking on and beating the industry’s biggest names to secure landmark national projects, having carved out a niche in the market through its authentic and personable approach.
While Genus has worked with the likes of Rio Tinto, Fortescue, Roy Hill, BHP and Northern Star Resources to design, construct and maintain the crucial infrastructure that keeps their mine sites running, the company isn’t getting ahead of itself.
“We’ve come a long way from being the ‘powerlines guys’, and I’m proud of where we find ourselves,” Genus managing director David Riches told Australian Mining “We’ve rapidly diversified and scaled our offering and now operate across three divisions covering everything from transmission lines and substations to communications solutions and renewable energy. But there’s always room for improvement, which is what
drives us each day to become Australia’s contractor of choice.
“As we grow, it’s really important for us to maintain our culture, continue that can-do attitude and ensure that we don’t stop until we finish our jobs – something we’ve always prided ourselves on.”
Unlike competitors that outsource extensively, Genus has nearly 1400 directly employed professionals ensuring quality and consistency across every job from start to finish.
Riches said Genus employees are experts at what they do.
“When it comes to renewables, power lines, substations or anything to do with energy and engineering of energy facilities or assets, we’re not confused in any way, shape or form,” he said.
“We’re doers rather than talkers, and our clients understand that we deliver projects as promised. If a client’s got a problem, we work through that issue quickly – we always prioritise transparency and communication.”
This approach enables Genus to pull through when the going gets tough.
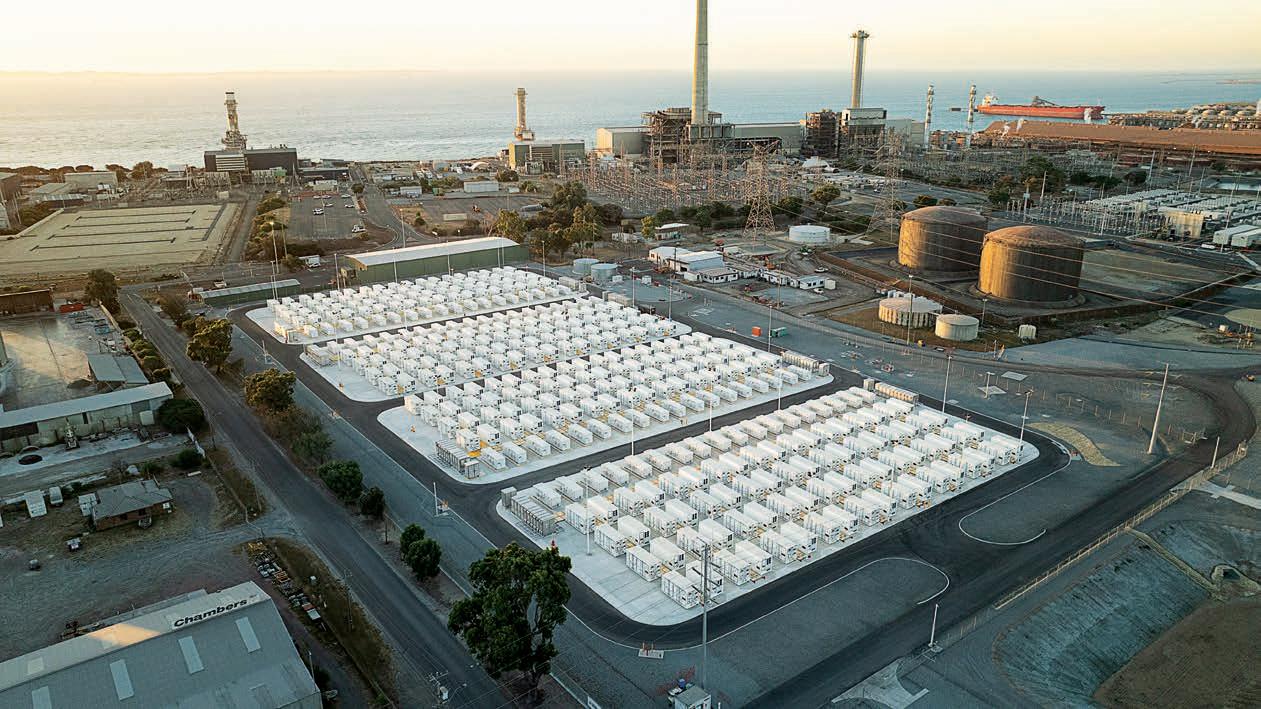
“Whether it’s a difficult, remote project or navigating COVID or whatever gets thrown at us, we’ll find a way to get the job done,” Riches said. “We’ll find a way of innovating that project and making it happen.
“We’ve built a culture of mateship, so we understand we’ve got to help each other on both the good days and bad days. There are days where it’s challenging to deliver the desired outcome, meaning we’ve got to work together and think outside the box.
“This comes from me as well. I’m certainly a managing director that doesn’t mind getting his hands dirty and assisting projects and our management team where required so we can all achieve our goals.”
By investing time into its employees, Genus has become an attractive workplace destination for professionals in power, communications and, by connection, mining industries.
This allows Genus to not only lure talent but also retain talent, creating a culture of excellence and establishing the company as a leader in its field.
“Some of our general managers (GMs) are the first GMs of their respective units and have remained in these roles as the company has grown,” Riches said. “We also have a strong retention rate in our blue-collar roles, which is really important for us to maintain our standards across the business.”
Genus commenced working with Rio Tinto in 2010.
“We started on a small job for Rio Tinto in Tom Price, and we’ve effectively never left,” Riches said. “We’ve always done regular work for the iron ore miners since then.
“But we don’t discriminate on size. Alongside our Tier 1 client base, we’ve also worked with a lot of Tier 2 and 3 miners across Australia in a range of commodities, including mineral sands, gold and copper.”
Complementing Genus’ longstanding relationship with Rio Tinto, delivering Fortescue’s Pilbara Generation Project was a landmark achievement for the company.
“Fortescue contracted us to build four substations and a 220-kilometrelong power grid at 220 kilovolts as part of stage one of the Pilbara Generation Project,” he said. “A few other utilities and miners would have been looking to see how we were going to go with this big project.
“We delivered this project through COVID and our order book has ballooned ever since.”
In addition to WA, Genus has established a national footprint with a strong presence in the Queensland mining industry, while the company plans to grow into New South Wales by leveraging the success of energy infrastructure projects such as HumeLink East for TransGrid and its partnership with AusGrid on EnergyCo’s Hunter–Central Coast Renewable Energy Zone.
Contract after contract, Genus is solidifying its status as a Tier 1 power and communications solutions provider, with renewable energy becoming another key growth area for the company.
“While we have our core capabilities, we’re also trying new things all the time,” Riches said. “This might involve an acquisition or rebuilding a company out of administration.
“We’re always learning new skill sets as well, which is how our renewables arm came into play. We acquired electrical business EC&M and created it into a multi-function renewables business, doing batteries, solar, and now even looking at wind.
“We’ve already built two major solar farms – one for Rio and one for Fortescue – so we’re starting to really establish ourselves in the renewables space.”
As Genus expands through organic growth and acquisitions, backed by a strong balance sheet and recordbreaking half-year revenue, the company isn’t losing sight of its DNA and what got the business to where it is today.
“When you start a company, and it’s a tiny little tree in a pot plant and then you grow the company into a big tree, it’s critical you don’t lose your identity,” Riches said.
“To preserve this, we’re focused on building internal relationships within the business, between both our senior leadership and project management levels, as well as with our bluecollar roles.
“We’re also focused on promoting from within. We’ve established a great mix of people who want to work for an ambitious, growth-minded company.” AM
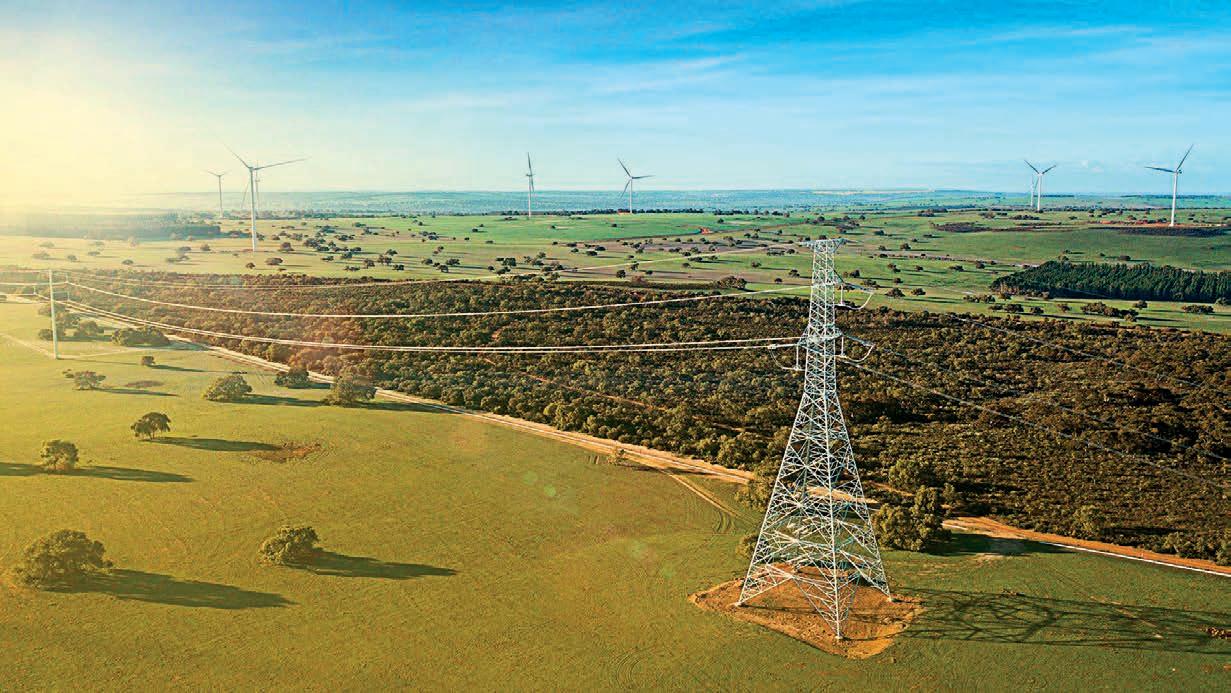
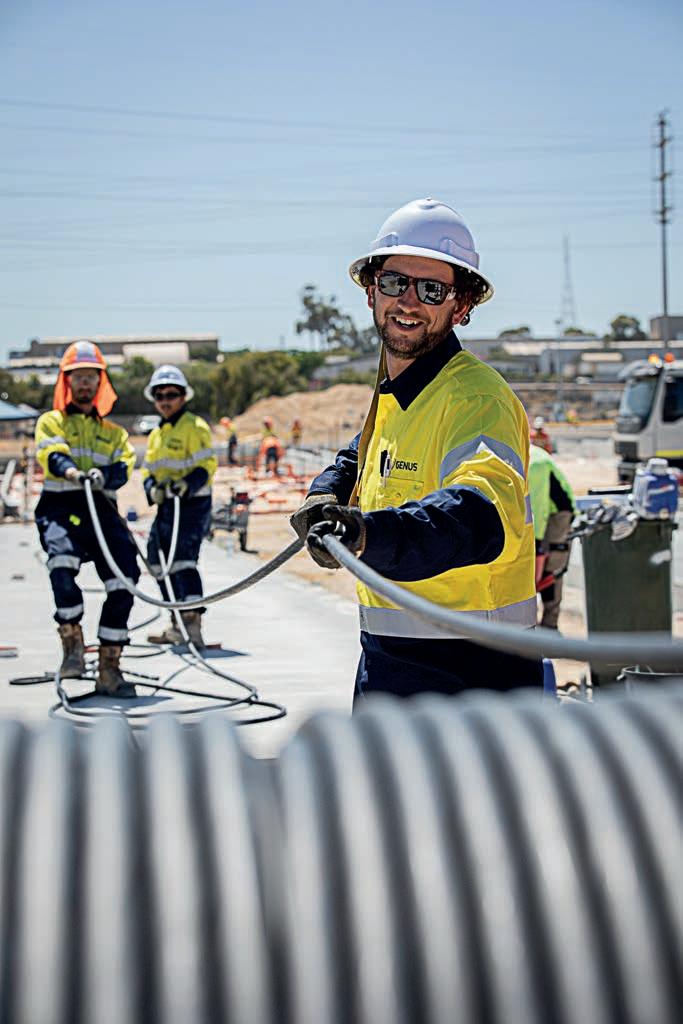
MANAGING LITHIUM-ION RISKS
FM’S LOSS-PREVENTION DATA SHEET FOR BATTERY ENERGY STORAGE SYSTEMS IS DESIGNED TO EDUCATE MINING OPERATORS ON THE RISKS ASSOCIATED WITH LITHIUM-ION BATTERIES.
Battery energy storage systems (BESS) have become a core component of the Australian resources industry as miners increasingly implement renewable energy to power their sites.
While these systems offer a more sustainable and cost-effective alternative to traditional diesel generators, especially in remote locations, they don’t come without their risks.
The lithium-ion batteries that make up a BESS pose fire and explosion hazards due to their flammable materials. This has prompted commercial property insurer FM to release a loss-prevention data sheet exploring the risks associated with a BESS, with specific guidance that can be adopted by the mining industry.
FM operations chief engineer Mike Hunneyball explained the inspiration behind the data sheet.
“While their adoption has increased rapidly in recent years, lithium-ion batteries have been used in electrical devices since the 1990s, so they’ve been around for quite some time,” Hunneyball told Australian Mining. “FM has been doing research on lithium-ion batteries for over 10 years, helping clients
understand the risks stemming from the flammable electrolytes that make up these batteries.”
Hunneyball said FM has supported clients in understanding that lithium-ion batteries “are different”.
“They’re more challenging when it comes to a fire due to the additional risk of thermal runaway, where a battery can’t dissipate the heat from the chemical reaction fast enough, causing off-gassing and subsequent fires to sustain and even intensify,” he said.
“As clients have adopted lithiumion batteries, we’ve worked alongside them to understand the risks and what needs to be considered to deal with those risks.”
One of the key considerations for a mining company when implementing a BESS is its location.
“You want to install these systems outside and away from critical pieces of equipment so there isn’t additional damage created from a fire or explosion,” Hunneyball said.
“It’s important to consider how close the installed containers are from each other. If there’s a fire in one container, is that going to easily propagate to the next container and the next container?”
Hunneyball advised against installing a BESS indoors. If this is the desired
option, however, a fire protection system should be implemented.
“A fire protection system, such as a sprinkler system, is key to stopping a fire propagating,” he said.
“Space separation is also a key consideration, because the closer batteries are to each other, the more likely this will cause a fire in adjacent batteries to go into thermal runaway, which is when the worst fires occur.”
Understanding the important role renewable energy will play in a net-zero future, Hunneyball said these risks shouldn’t discourage mining companies from implementing a BESS.
AN FM TEST STUDYING THE FIRE CHARACTERISTICS OF BULKSTORED LITHIUM-ION BATTERIES.
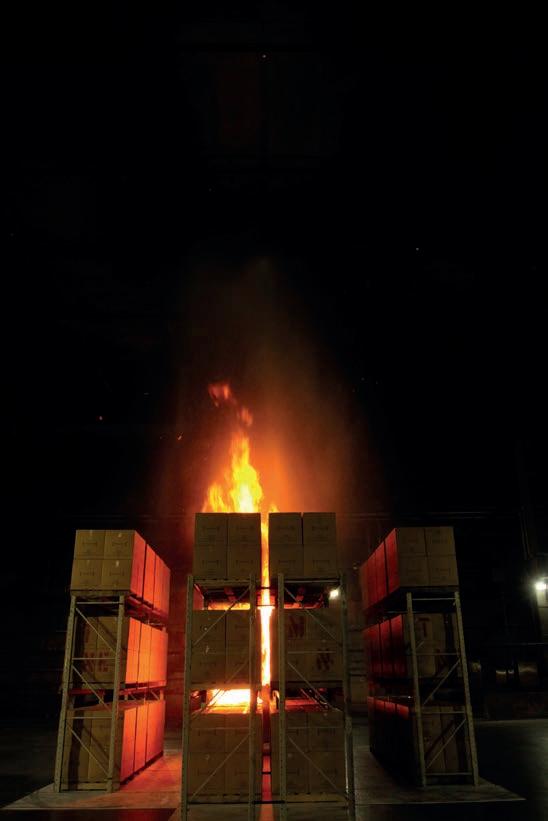
But miners need to be strategic.
“It’s important to understand that you could be changing the risk profile of a business, building or piece of equipment if you incorporate lithium-ion batteries,” Hunneyball said.
“Explosions can occur, and these fires can be long-duration fires, so you need to have an emergency response team at the ready. If it’s a remote mine and there isn’t a fire brigade nearby, you might have to rely on your own people to fight these fires, so it’s important to also consider that.”
While mining companies must have emergency plans in place for the possibility of a lithium-ion
“Battery management systems (BMS) and condition monitoring are critical to understanding the real-time stressors being placed on lithium-ion batteries,” Hunneyball said.
“These can detect thermal runaway early on, enabling the system to trip before a fire occurs.
In addition, FM’s research on early intervention thermal runaway prevention has shown devices that detect high cell temperatures or off-gas detection are a good way to increase the likelihood of detecting and isolating thermal runaway events.
Hunneyball said mining companies should also ensure they replace lithium-ion batteries within their recommended lifecycle, as ageing batteries could be at greater risk of causing fires and explosions.

FM’s loss-prevention data sheet for a BESS incorporates nearly 200 years of accumulated property loss experience, research and engineering results to analyse the risks associated with implementing lithium-ion batteries.
These standards support mining companies in reducing the chance of property loss due to lithium-ion battery fires, enabling operators to future-proof their mine sites.
FM’s data sheets also cover lithiumion battery manufacturing, storage and data centres, along with other mining applications such as conveyors, rotary kilns and dryers, and metal cleaning.
“Our data sheets are some of the best pieces of guidance out there globally,” Hunneyball said.
“A lot of manufacturers and clients have adopted our guidance to improve their operations.
“We conduct testing every year to ensure our guidance is up to date, so clients can be rest assured that our data sheets are always current and reflect existing technology.” AM
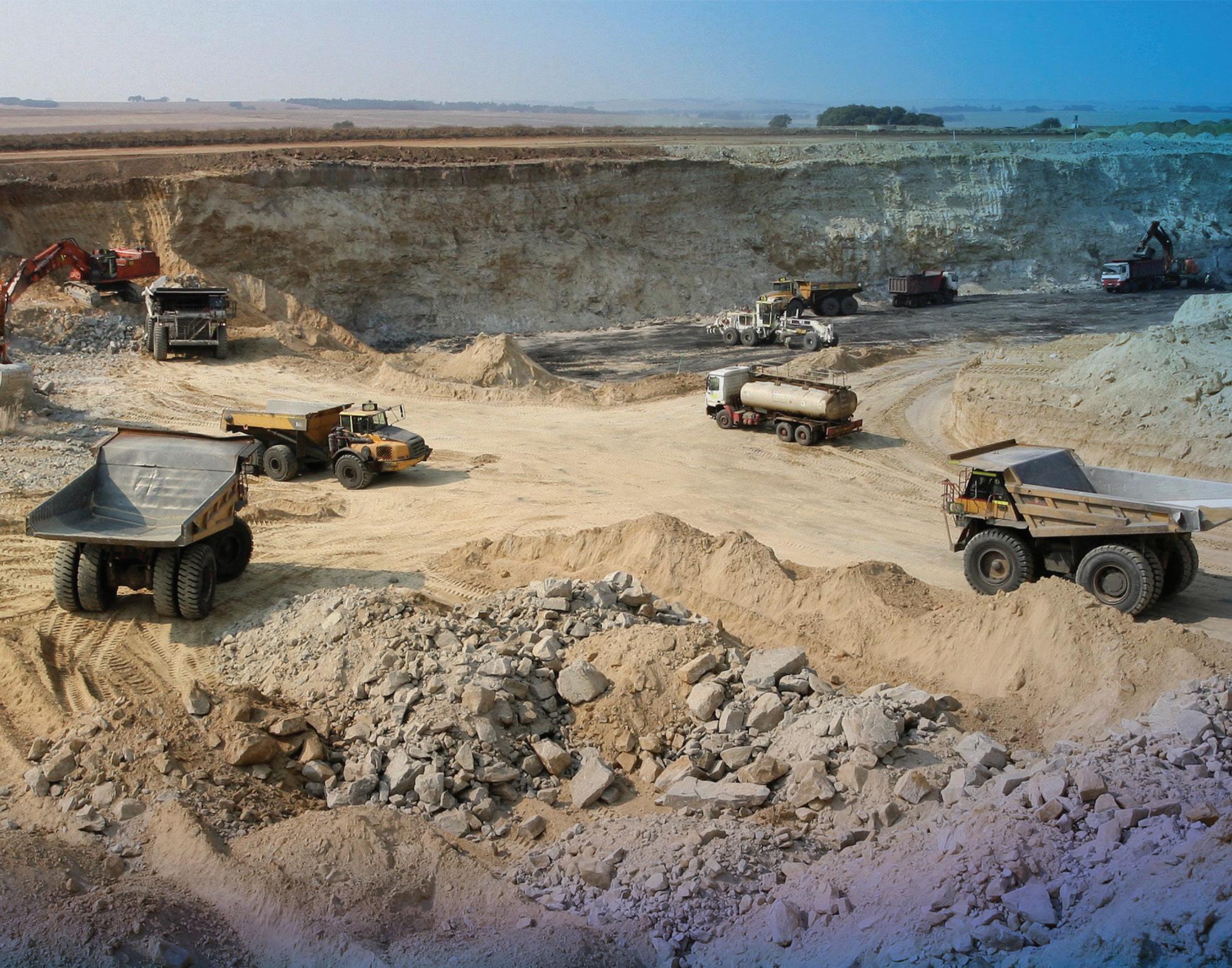
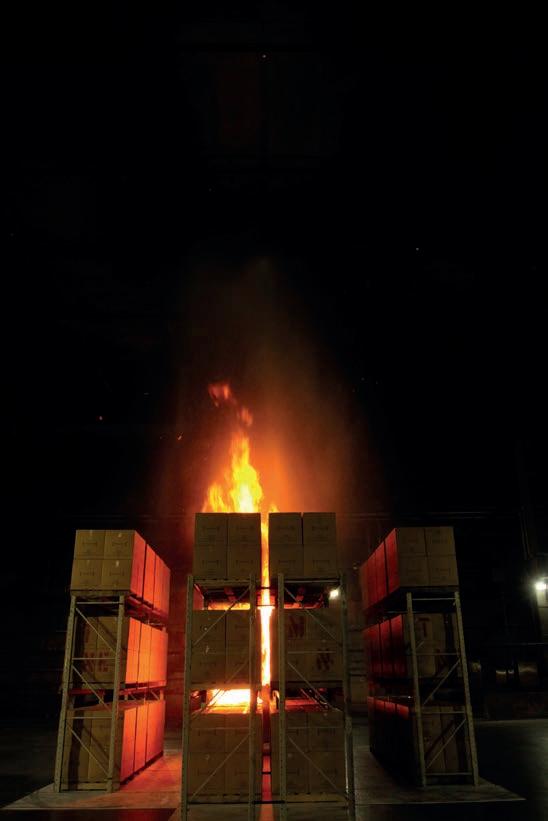
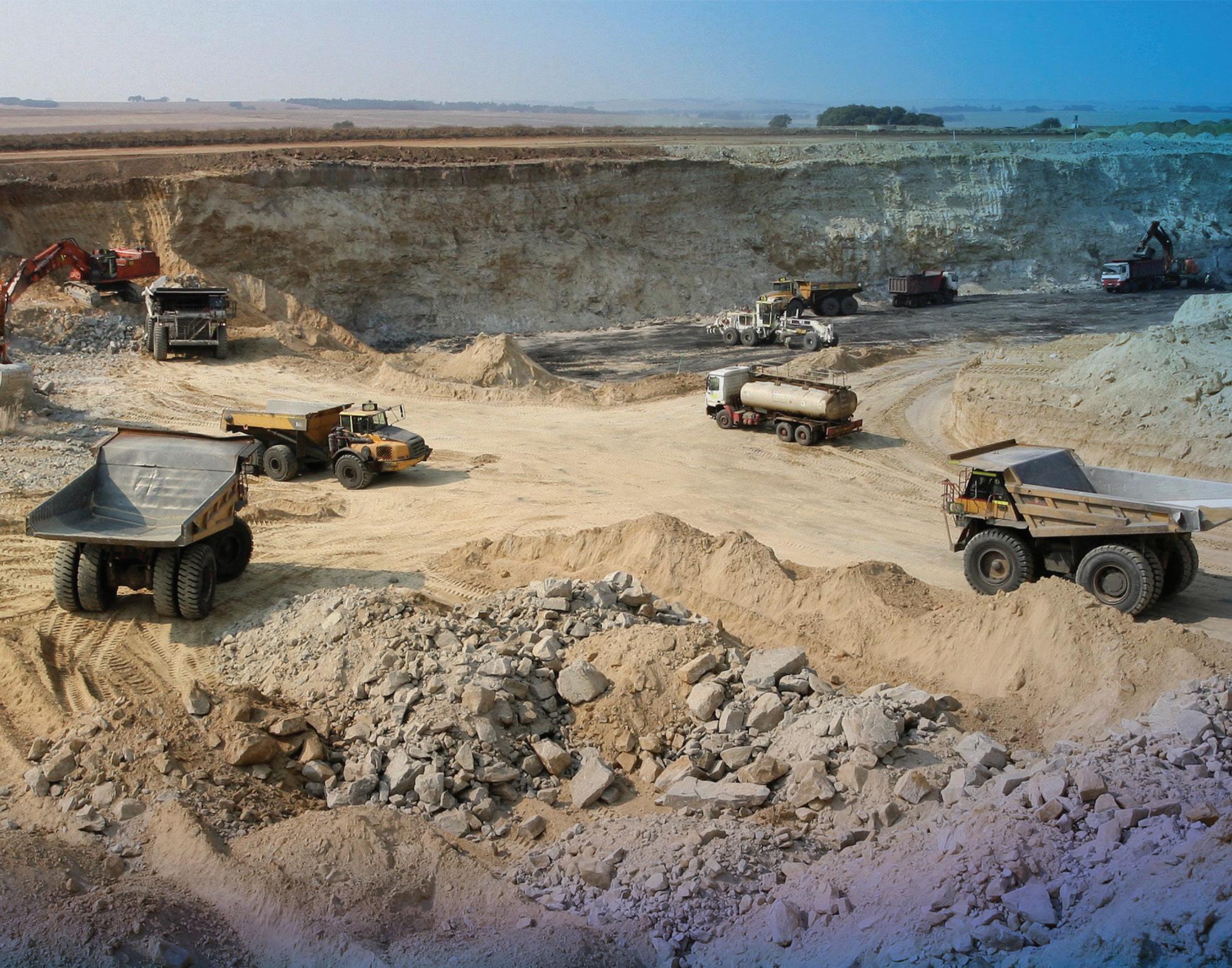
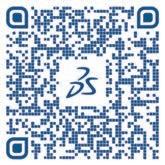
ALL ABOARD FOR CLEANER TRANSPORTATION
FROM ELECTRIFICATION TO ROUTE OPTIMISATION, MINING OPERATORS – ALONGSIDE PARTNERS LIKE VDI AUSTRALIA –
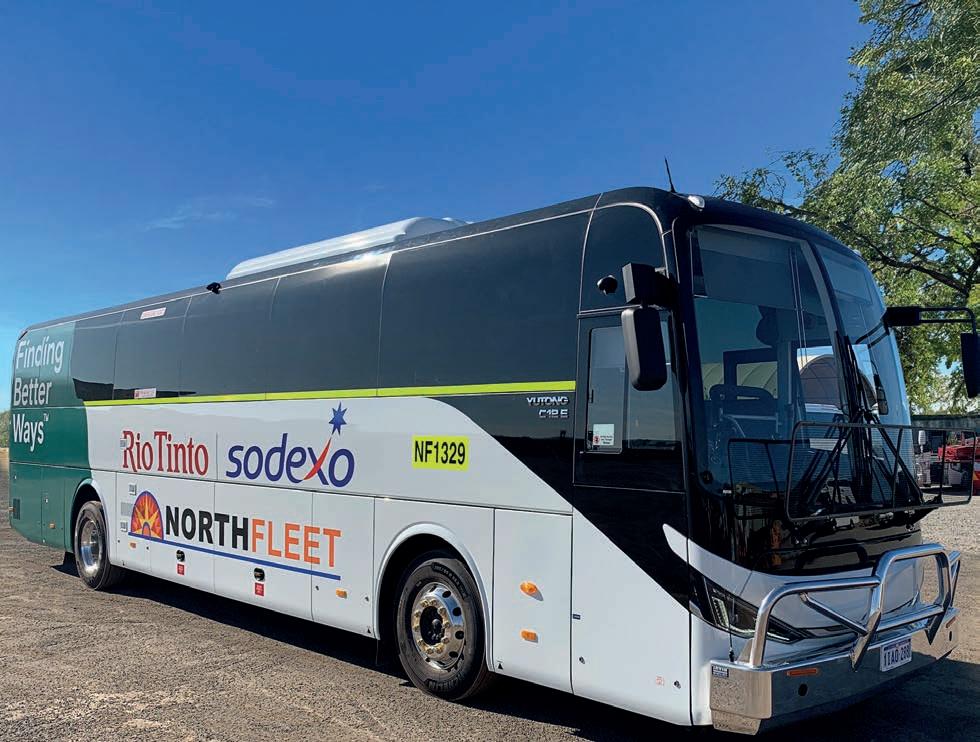
Electrification is more than just an industry buzzword.
With mining operators increasingly looking to find new ways to make transportation more sustainable – whether through electrification, route optimisation or smarter fleet management – the push for electric vehicles (EVs) has never been stronger.
While much of the industry’s focus has been on cutting emissions from haulage fleets, workforce transport presents an immediate opportunity to enhance sustainability goals, reduce costs, and improve efficiency.
Battery-electric buses are emerging as a strong option for workforce transportation, offering mining operators a cost-effective way to decrease emissions while maintaining operational efficiency.
While many in the industry are still using traditional diesel coaches to ferry their workers to and from an operation, the momentum to shift to cleaner, greener methods is building with companies already looking at the myriad ways electric transportation can be added to their repertoires.
As mining operators explore these options, VDI Australia, the national distributor of Yutong buses, is at the forefront of supporting the transition, providing proven zero-emission solutions through its partnership with Yutong.
“We’re seeing more mining operators take real steps towards electrification, not just discussing it as a future possibility,” Yutong Bus Centre WA general manager Mike Kennedy told Australian Mining. “With the right technology and support, batteryelectric buses are already proving to be a practical and scalable solution for workforce transport in mining.”
But every mine is unique, with different operational needs. This is something mines must consider when pursuing EV solutions.
“The transition to electric workforce transport in mining isn’t a one-size-fitsall solution – it’s about matching the right technology to operational needs,” Northfleet managing director Toby Hagen told Australian Mining
“For sites with shorter daily travel distances, EV coaches are proving to be a strong alternative, and we’re already seeing promising uptake from Tier 1 clients.”
transportation
be weighed with the ability to address practical challenges like comfort and reliability.
“While we always aim to reduce operational costs, enhance employee safety, lower carbon emissions and improve overall efficiency, customer comfort is just as important,” Hagen said.
“The temperature in the Pilbara regularly reaches over 40°C, so the need for reliable air-conditioning is paramount. We also don’t want to miss any runs and leave the team waiting for transportation, so reliability is another major consideration.”
Northfleet has been working with VDI to action a shift into EV coaches. VDI has found that the mining industry is actively evaluating electric workforce transport as a key consideration for the here and now, not just the future, and having the right features is vital.
Safety features like lane-departure warnings and fatigue-monitoring systems are becoming non-negotiables for miners – and they come standard in Yutong’s battery-electric buses.
Kennedy agrees that reliability and safety are just as important as
sustainability when mining operators consider electrification.
“Beyond emissions reductions, reliability is a top priority for mining operators considering EV transport,” Kennedy said.
“With Yutong’s Vehicle+ (V+) telematics system, operators can track vehicle performance remotely and receive instant alerts if an issue arises. This helps prevent unexpected downtime and ensures workforce transport runs efficiently – critical factors for the demanding conditions of mining operations.”
It’s not just Northfleet that has taken up the call to switch to EVs. Major companies like Rio Tinto and its services partner Sodexo are also on board.
“Introducing the Pilbara’s first electric bus through a joint investment with Rio Tinto Iron Ore was a bold step towards a more sustainable mining sector,” Sodexo managing director Keith Weston told Australian Mining
“After 18 months of testing and learning, we are now exploring opportunities to expand our EV fleet, further driving innovation in support of Sodexo and Rio Tinto’s sustainable business goals.”
With majors like Rio Tinto at the helm, it’s becoming increasingly clear that EVs are the future of mine site transportation. And while barriers still exist to getting all miners to rely 100 per cent on EVs, companies like Northfleet and industry partners such as VDI Australia are actively working to make the transition both viable and scalable.
“Electric transportation is the future, and we take it very seriously,” Hagen said. “The world is moving to a net-zero milestone and as a consumer of diesel we need to move with the social, environmental and community expectations around net-zero.
Kennedy agrees that industry momentum is growing, with an increasing number of mining operators seeing electrification as more than just an experiment.
“As mining companies accelerate their transition to cleaner transport solutions, VDI Australia is committed to ensuring they have the right technology and support to make it work,” he said. “With growing interest from major operators, we see electric workforce transport as a defining shift for the industry. The time to act is now.” AM
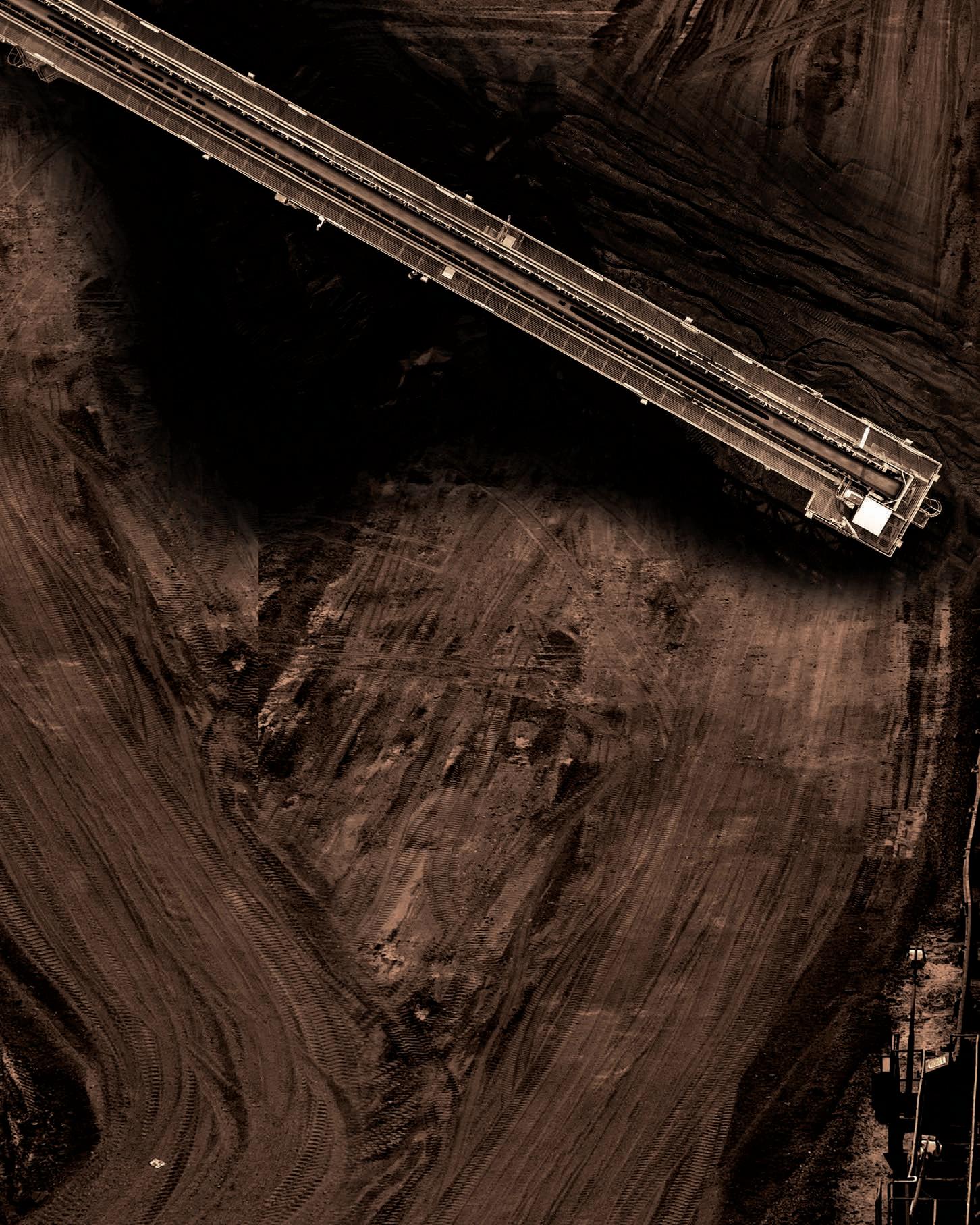
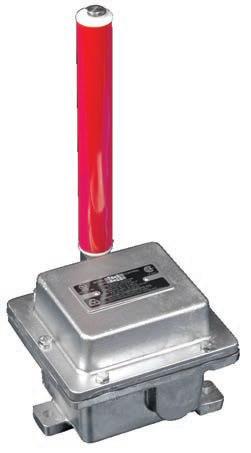
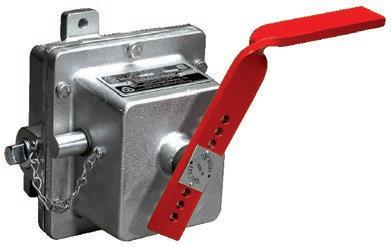
MODELRS
MODELDB
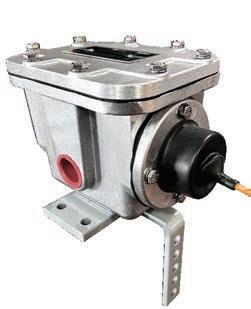
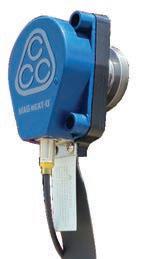
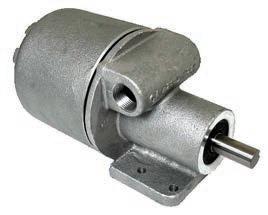
INTRODUCING AN EASY WAY TO PROTECT YOUR WORKERS AS WELL AS PROTECT YOUR INVESTMENT INTO YOUR EQUIPMENT.
THE CONVEYOR SAFETY SYSTEM™ IS AN EASY, COST EFFICIENT WAY TO GET PEACE OF MIND AND PROTECTION FOR CONVEYOR EQUIPMENT. BY BUNDLING OUR MODEL RS SAFETY STOP SWITCH WITH OUR MODEL TA BELT ALIGNMENT SWITCH, MODEL DB DAMAGED BELT DETECTOR WE HAVE YOUR WORKERS AND EQUIPMENT COVERED. COUPLE THAT WITH ADDING ONE OF OUR MOTION SWITCHES (MAG-NEAT-O™ OR MODEL CMS), YOU CAN FEEL CONFIDENT KNOWING THAT YOUR SYSTEM AND WORKERS ARE PROTECTED FOR A FRACTION OF THE COST OF DOWNTIME, REPAIRS AND REPLACEMENT EQUIPMENT.
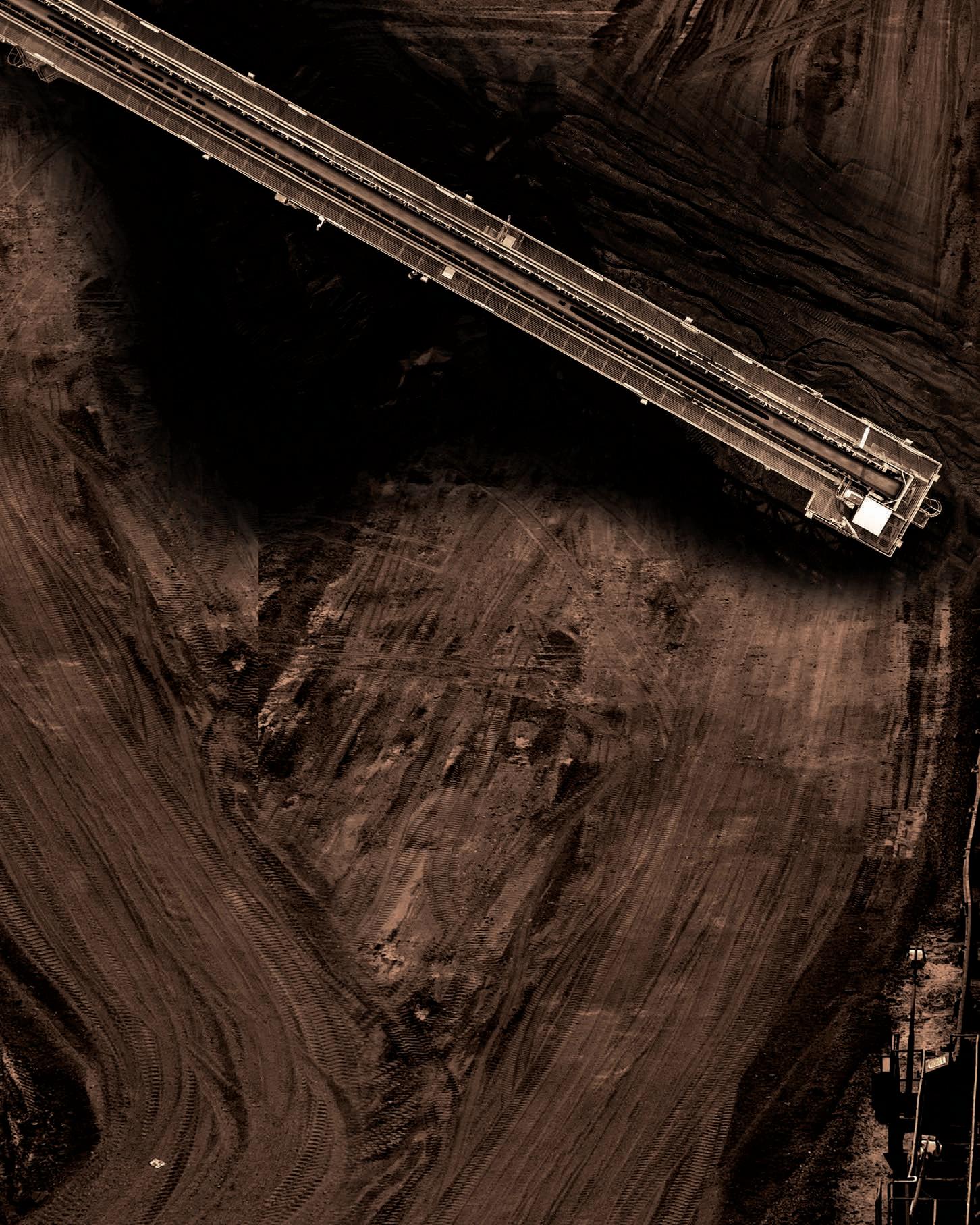

Filter Media Solutions for the Minerals Industry
Sefar is a global leader in technical filtration media for diverse minerals applications. We leverage our extensive application expertise with a leading fabric portfolio to provide customized filtration solutions that meet our customers‘ specific needs. Our commitment to continuous process improvement aims to lower your total cost of ownership while supporting a sustainable and profitable future.

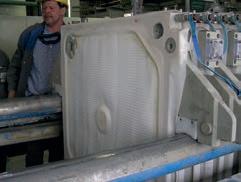
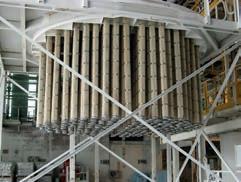
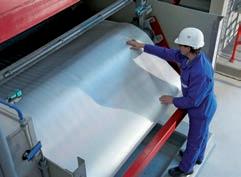

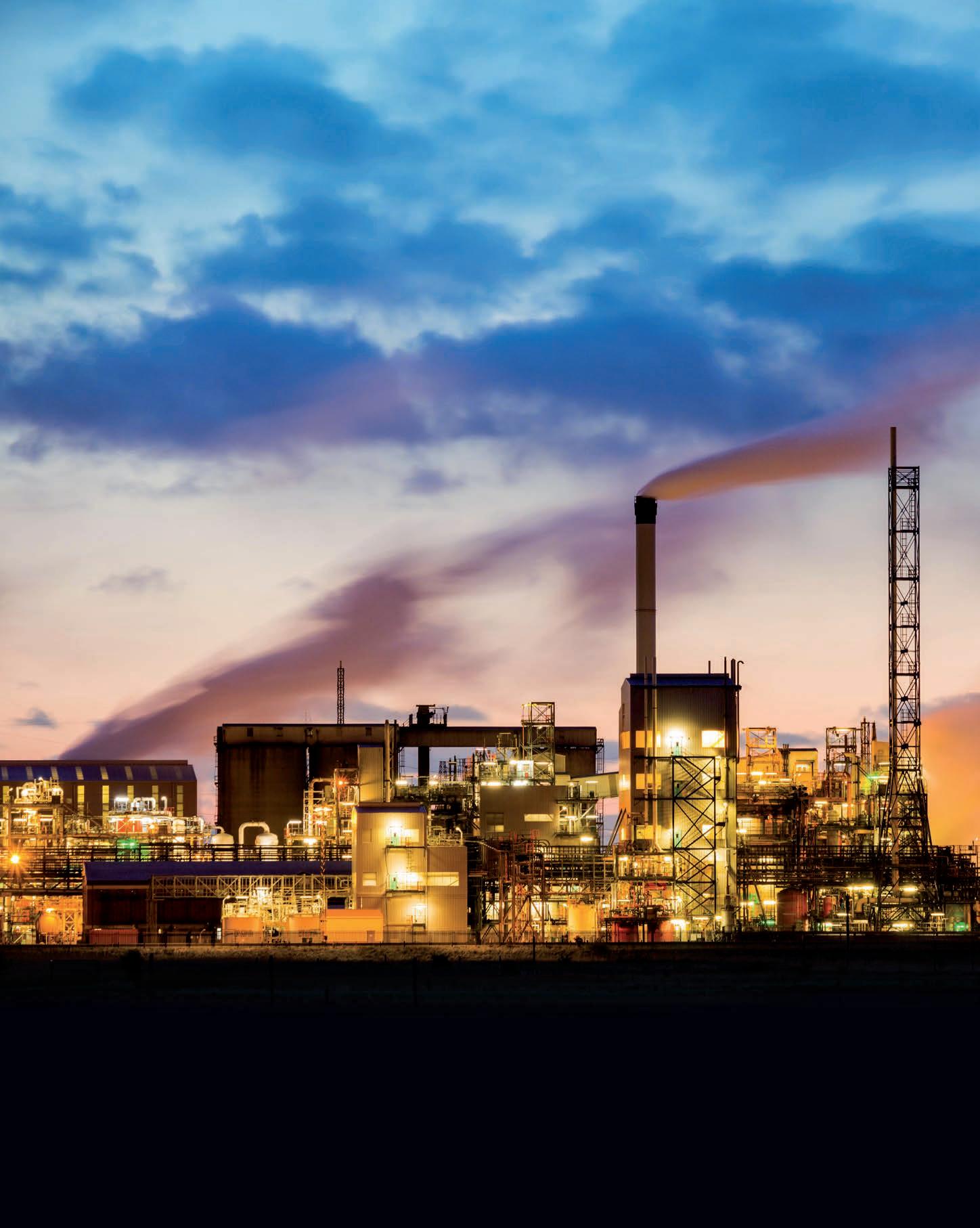
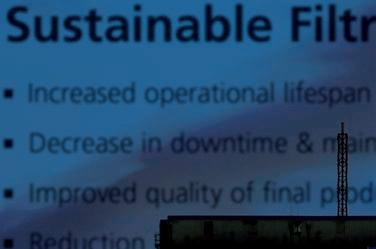
Sustainable Filtration Excellence
Increased operational lifespan
Decrease in downtime & maintenance
Improved quality of final product
Reduction in total cost of ownership
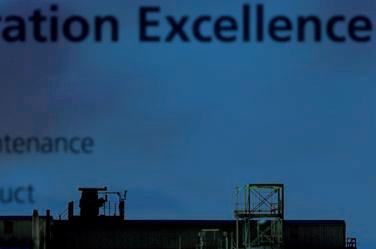
Diminishing your environmental footprint
Sefar Oceania
19-21 Huntingwood Drive, Huntingwood NSW 2148
phone 1300 306 661 oceaniasales@sefar.com www.sefar.com.au

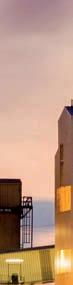
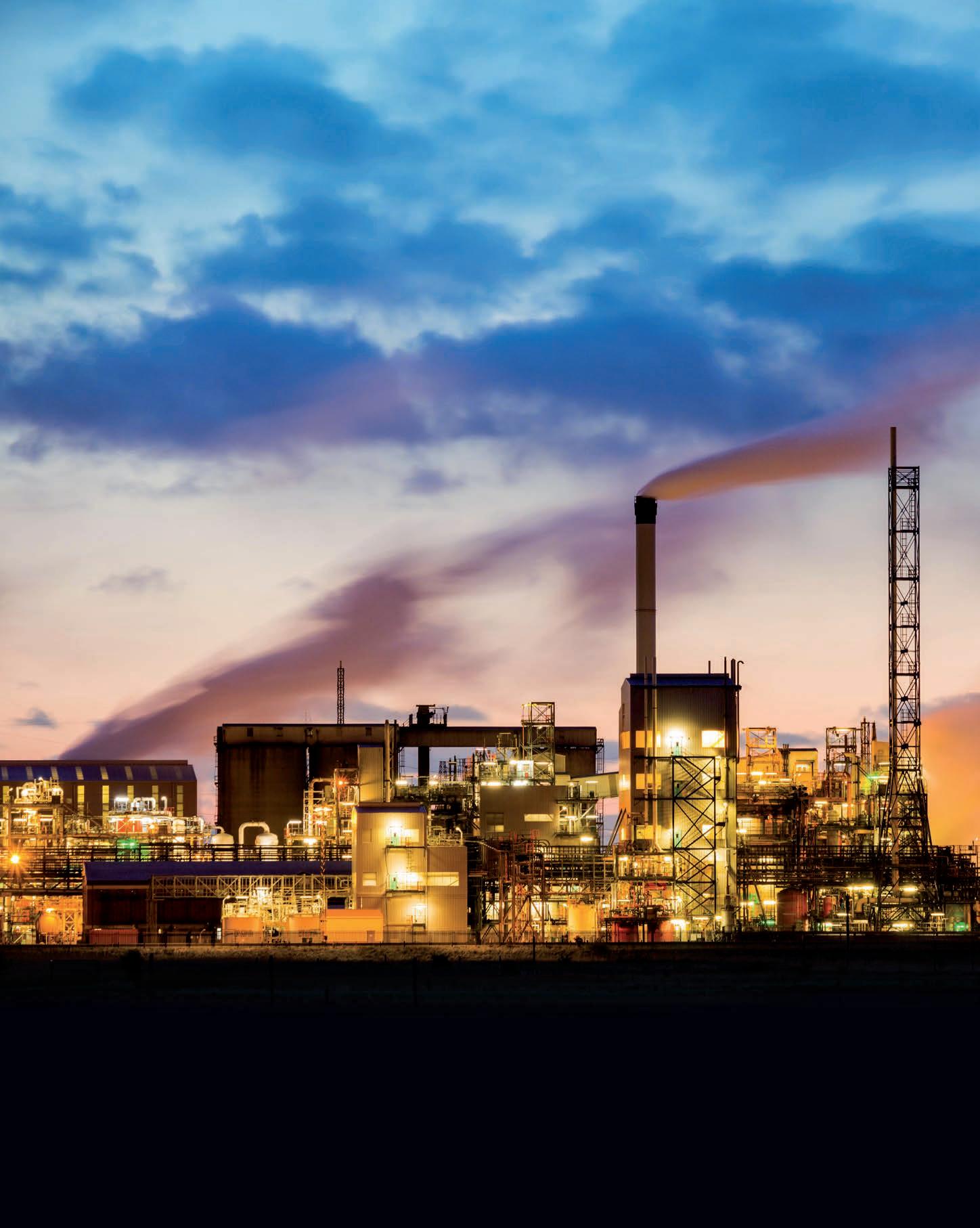
CONNECTING WORKERS TO HYDRATION
THE CONNECTED HYDRATION MONITORING SYSTEM FROM EPICORE BIOSYSTEMS IS NOW AVAILABLE IN AUSTRALIA THROUGH ALLIANCE SAFETY EQUIPMENT.
Whether they are in an open-pit or underground operation, processing plant, or remote site, Australian mine workers are used to working in humid conditions. But extreme heat often comes with adverse effects, including cognitive decline, fatigue and physiological dysfunction, and decreased physical performance.
This is where hydration is critical.
Alliance Safety Equipment has long been a supplier of advanced solutions to the mining industry, with a strong technical focus on gas detection, height safety, and respiratory protection.
“Building on this expertise, we have increased our focus on hydration safety, ensuring we provide technical expertise in hydration alongside our core specialisations,” Alliance Safety general manager Jonathan Pearson told Australian Mining. “Through our partnership with Epicore Biosystems, we have introduced Connected Hydration, a real-time monitoring solution that helps mining companies proactively manage worker wellbeing, reduce risk and improve productivity.”
Connected Hydration was launched in April 2024 after having been in development since 2019.
Alliance Safety Equipment looked to distribute Connected Hydration to the Australian market to fill the gap in education surrounding hydration in demanding industries like mining.
The monitoring system comprises a lightweight flexible patch users wear on their arm, a mobile application, and a cloud engine.
“The patch worn on the bicep fills up with sweat,” Epicore vice president of strategy Matt Marrapode told Australian Mining
“Through the sweat collected inside the patch, it measures total body fluid loss and electrolyte concentration and loss to generate rehydration recommendations for the user.
“The mobile app allows the user to see their personal biometrics, while the cloud helps health and safety teams improve site safety.”
Unlike generic hydration devices or reactive measures, Connected Hydration generates real-time dehydration information based on the direct measurement of fluid and electrolyte loss.
The system’s data dashboard tracks daily and longitudinal changes across work sites, providing users with early warning signals through alerts, alarms, and risk trends to enhance decisionmaking around the prevention of dehydration and fatigue incidents.
Built with an extended battery life of over 1000 hours, Connected Hydration is certified Class 1, Division 2 for hazardous environments, as well as for Groups A, B, C, D and T6. The system’s cloud security is also SOC2 Type 2-compliant, demonstrating user data protection and confidentiality.
“By providing data-driven insights, the technology helps site managers proactively manage hydration, reducing the risk of heat-related incidents and improving workforce performance,”
Pearson said. “The impact has been immediate. Workers report behavioural changes after wearing the device for the first time, becoming more aware of their hydration levels and ensuring they replace fluids lost and start shifts properly hydrated.
“From a management perspective, case studies have driven positive process changes, with sites recognising the long-term value of a tailored hydration solution.
“We now have clients committed to integrating Connected Hydration into their safety programs to proactively manage worker wellbeing and reduce heat-related risks.”
As Connected Hydration enters the Australian market, Alliance Safety is on
hand to ensure the system is seamlessly integrated into existing safety processes.
“We offer ongoing technical support, including regular system updates, maintenance and troubleshooting, to ensure the technology remains fully operational,” Pearson said.
“We provide on-site training to ensure that staff are confident in using the system effectively and are well-versed in interpreting the data. Our team also works closely with clients to monitor performance, offer insights and provide tailored recommendations to enhance hydration management and overall safety.
“This ongoing support helps clients maximise the value of our products, ensuring they continue to meet evolving safety requirements.” AM
CONNECTED HYDRATION PRODUCES REAL-TIME DEHYDRATION INFORMATION BASED ON FLUID MEASUREMENT AND ELECTROLYTE LOSS.
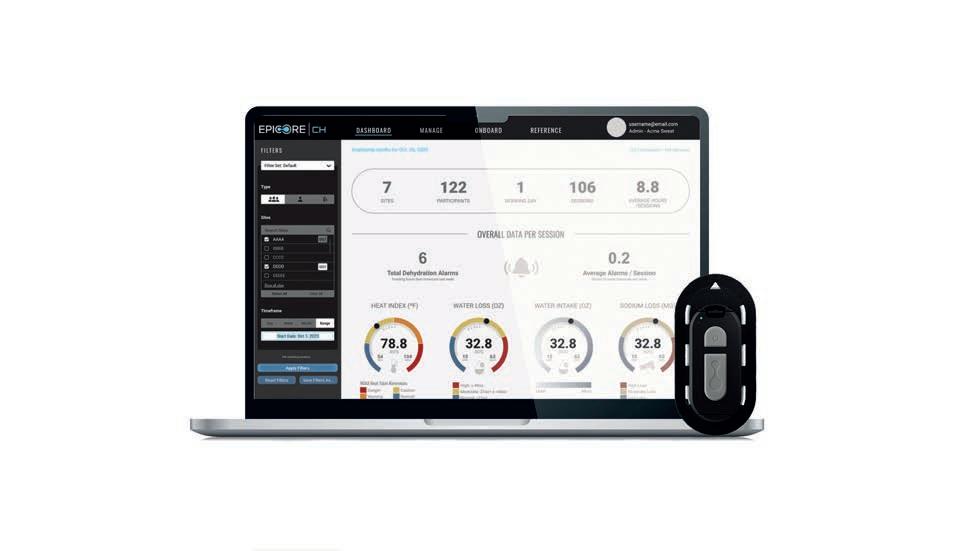
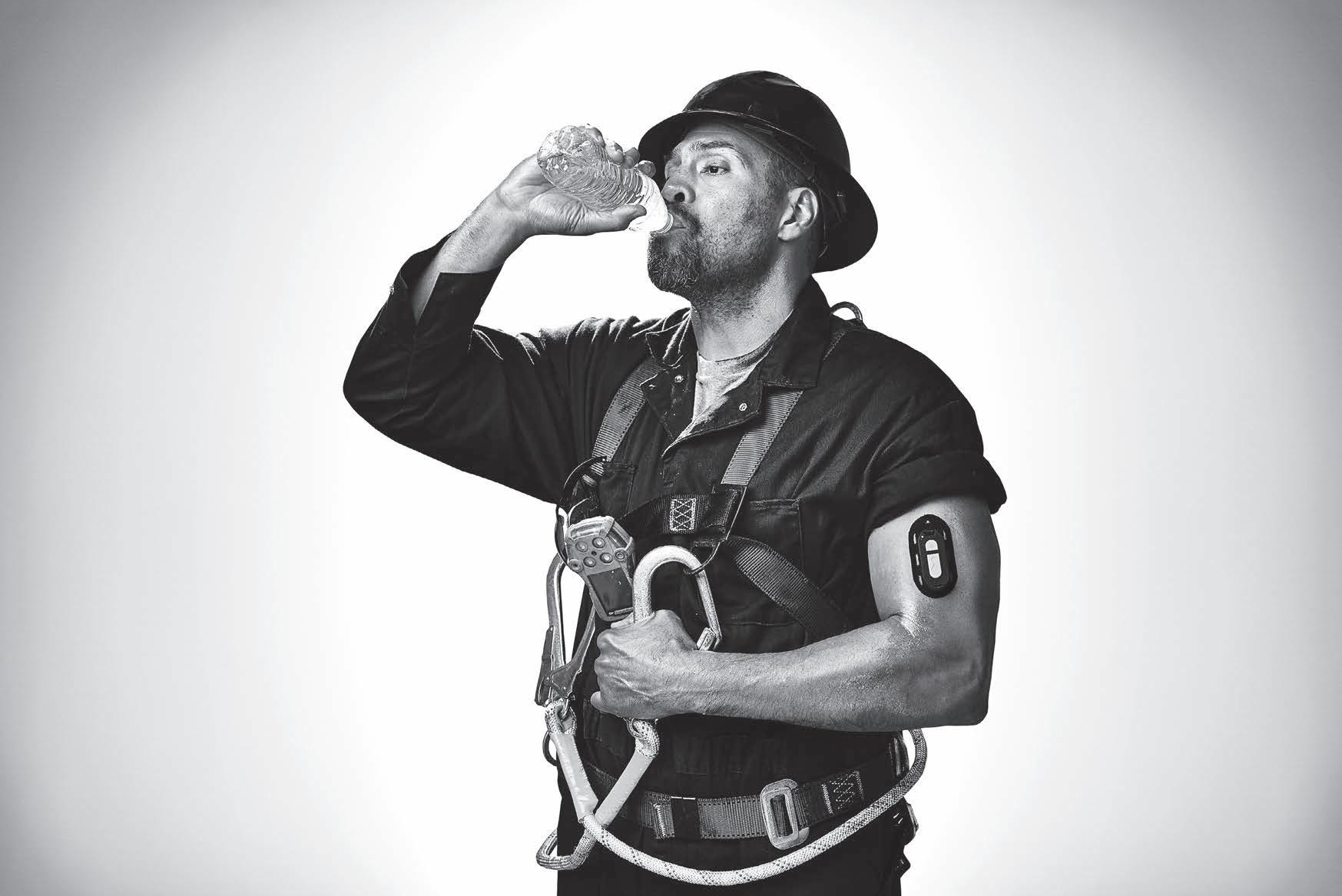
TRIGGERING A CHAIN REACTION
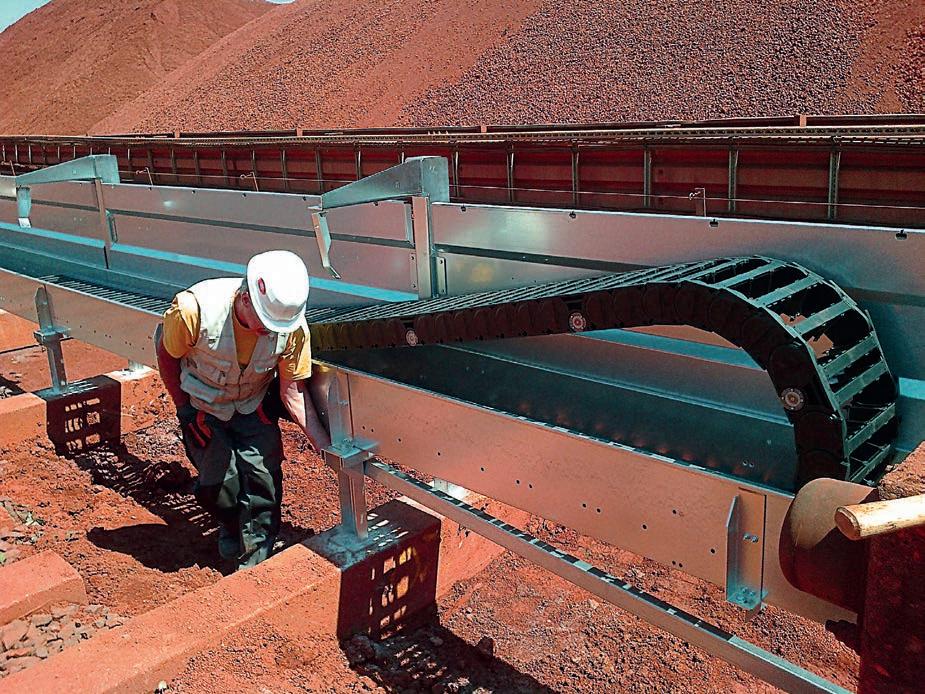
Ecritical mining operations adopt technologies that enhance durability and streamline processes.
A leader in industrial automation and energy chain solutions, Treotham is helping mining companies with cutting-edge systems designed to replace outdated equipment and improve operational efficiency.
The company’s energy chain systems have already proven their effectiveness in various bulk handling industries, including shipping, rail and manufacturing.
A recent refit project at a train manufacturing facility highlighted how replacing outdated festoon systems with energy chains has several advantages and can save operators money by avoiding unscheduled maintenance downtime. The transition from a festoon system to an energy chain significantly improved functionality, reducing instances where chilled water lines would freeze and damage equipment.
The train refit project demonstrated the importance of integrating flexible and adaptable systems that cater to demanding conditions, an approach well-suited to the dynamic nature of mining and port operations.
A key advantage of Treotham’s process is the ability to replace ageing, inefficient systems with modern solutions that require less maintenance.
Treotham national sales manager John Sharp emphasised that mining operations often face challenges when integrating new technology due to preexisting infrastructure constraints.
point,” Sharp told Australian Mining
“A lot of salespeople don’t have the big-picture experience. They know the product, but when it comes to integrating it into existing infrastructure, that’s often the key to success.”
By working closely with clients, Treotham ensures installation of its energy chain solutions is efficient and cost-effective.
Rather than requiring extensive new support structures, the company leverages existing frameworks, significantly reducing installation costs and time.
“Customers often have existing structures to support our energy chain solution, which can save costly installations of new structures,” Sharp said.
Beyond improving operational efficiency and limiting downtime, Treotham’s energy chains also deliver safety outcomes.
Traditional festoon and cable reeler systems can present risks that include excessive wear, entanglement, or obstruction.
Energy chains help to eliminate these issues by providing a secure, enclosed system for cables, hoses and other critical components.
Sharp said functionality is among the key reasons customers turn to Treotham’s cable management solutions.
“If a ship loader is located next to a town, for example, dust suppression is essential,” he said.
“You might need a cable reeler for power, but adding a water line to it isn’t always straightforward.
system, supporting a contained dust suppression solution.”
This all-in-one approach enables mining companies to enhance operations without the need for costly secondary installations.
Strategic placement of energy chains further enhances system resilience.
Instead of installing chains in areas that are prone to ore spillage or high-pressure washdowns, Treotham suggests minor modifications like adding protective barriers to improve durability.
“Simple solutions include adding a sheet of metal above the system to shield it from falling material or raising it off the floor to prevent water damage,” Sharp said.
“Small adjustments like these make a huge difference in extending the lifespan of the system.”
The integration of smart technology into mining operations is becoming increasingly important.
Treotham’s energy chain systems can be equipped with advanced sensors and data tracking capabilities to provide real-time monitoring and predictive maintenance insights.
Sharp discussed one instance in which a ship loader was saved by an automatic shutdown system.
“When an operator accidentally left a ladder in the machine’s path, the system triggered a stop, preventing extensive damage,” he said. “A simple detection system prevented what could have been a catastrophic failure.”
As mining operations look for ways to enhance efficiency, reduce costs and improve safety, Treotham’s cable management systems offer a proven solution.
With customisable designs, seamless integration and long-term reliability, these systems provide a strategic advantage for mining companies looking to future-proof their operations.
“We’re educating the mining industry that our cable management systems can be easily integrated with existing infrastructure,” Sharp said.
“Once miners understand how much they can save in installation and long-term maintenance, the benefits become clear.”
Treotham is playing a crucial role in transforming mining operations across Australia, bridging the gap between innovation and practicality. AM FUNCTIONALITY IS A KEY REASON CUSTOMERS TURN



RAZOR SHARP DECISION-MAKING
RAZOR LABS’ DATAMIND AI TRANSFORMS MINING OPERATIONS BY PREDICTING FAILURES BEFORE THEY HAPPEN.
Prevention, as they say, is better than cure. This is especially true on a mine site, where predictive maintenance is among the most effective approaches to ensuring operations run smoothly.
While preventive maintenance offers benefits such as reduced risk of equipment breakdowns and decreased downtime, it can be more labourintensive, resulting in increased staffing and operating costs.
This is why more and more mining companies are turning to predictive maintenance solutions.
Predictive maintenance analyses realtime sensor data to detect failure risks early, enabling proactive repairs before breakdowns occur.
Razor Labs is a pioneer in AIdriven predictive maintenance. Its fully automated system has optimised asset reliability for leading mining companies since 2016.
Described as a ‘single out-of-thebox solution’, Razor Labs’ DataMind AI predictive maintenance system is designed to eliminate unplanned downtime, increase productivity, and enhance safety.
DataMind AI integrates sensor data from mining equipment, using neural networks to detect hidden failure patterns. This enables operators to predict and prevent costly breakdowns with precision.
“We first partnered with a Tier 1 miner in Australia to develop AI-driven failure prediction models using timeseries data and other insights from its existing systems,” Razor Labs chief business officer Tomer Srulevich told Australian Mining
“We start by analysing key maintenance KPIs (key performance indicators), particularly the planned versus unplanned maintenance ratio, to pinpoint where reliability can be improved.
“We assess whether the main constraint is in the mine or the plant, identifying critical bottlenecks that restrict throughput. By mapping single points of failure, we help sites reduce downtime, streamline maintenance, and eliminate production constraints for maximum efficiency.
“If the client has existing sensors, we can easily integrate them into DataMind AI. If not, we map optimal placements for full asset coverage, ensuring seamless data collection.”
Built to withstand tough environmental conditions, DataMind AI’s platform integrates sensors for
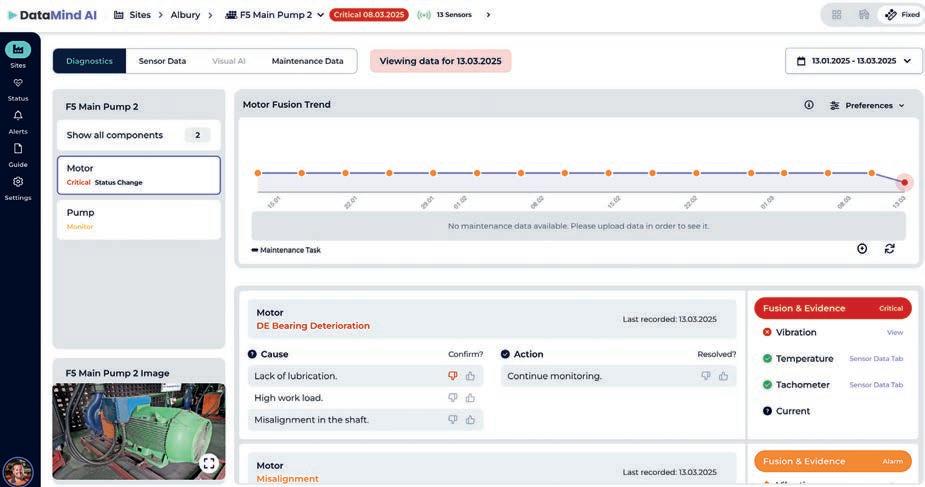
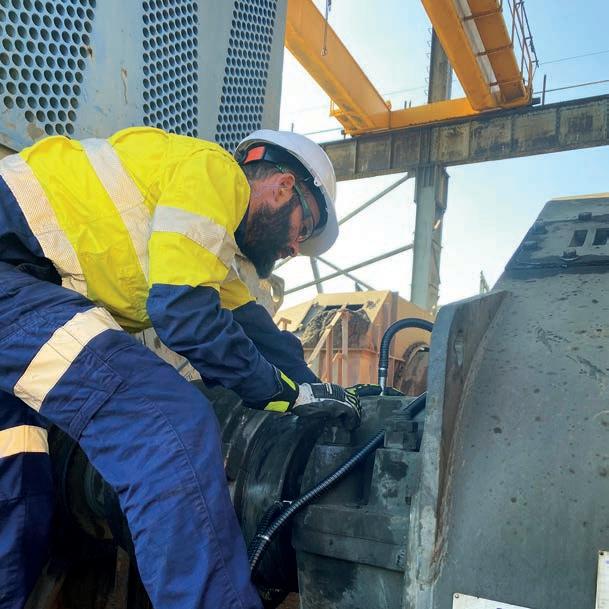
time equipment monitoring.
The platform also includes a camera for vision-based analysis, enabling material monitoring and belt drift detection, ensuring 24–7 visibility with no sensor gaps.
“DataMind AI’s sensor fusion technology pinpoints failure root causes and delivers AI-driven prescriptive actions to prevent breakdowns,”
Srulevich said. “Integrating data from multiple sources and various sensor types is one of the biggest challenges in mining. Fragmented systems, handheld devices, and isolated sensors often miss
“Unlike traditional monitoring systems, DataMind AI’s sensor fusion combines vibration, temperature, pressure and oil analysis – offering a multi-layered diagnostic advantage.”
DataMind AI is deployed by a preapproved and inducted site integrator, eliminating the need for new vendors. With minimal training, the integrator can execute the installation efficiently, ensuring rapid deployment without complex model calibration.
“Once it’s up and running, the system immediately begins generating predictive insights,” Srulevich said.
“Some of the equipment installations can even be done while the machine is operating. We continuously sharpen our process to make sure the implementation is as short and efficient as possible.
“DataMind AI has already helped mining operations across Australia, identifying critical failures in both iron ore and coal sites.”
At the iron ore mine, DataMind AI detected rapid deterioration of a critical pump bearing overlooked by manual inspections.
Envelope demodulation acceleration increased six to nine times compared to baseline, with AI sensor fusion compensating for operational deviations. The system flagged the issue as ‘critical’, enabling timely bearing replacement during scheduled downtime and preventing costly secondary damage.
At the coal mine, DataMind AI identified fluting in a conveyor motor bearing caused by electrical currents passing through bearings, reducing their lifespan and increasing maintenance costs. Early detection allowed proactive maintenance, avoiding unplanned stoppages and extending equipment life.
“These outcomes underscore DataMind AI’s real-world impact across diverse mining environments and commodities in Australia,” Srulevich said.
“Our ability to aggregate vast data sets and transform them into actionable insights is unmatched in the industry.
“We continue to push the boundaries of AI-driven predictive maintenance, setting new standards in mining efficiency.” AM


PROUDLY POWERING WHAT MATTERS
At Genus, we’re not just building power and communications infrastructure; we’re shaping Australia’s future. From transmission lines and substations to communications solutions and renewable energy, we design, construct, and maintain the systems that keep the country moving forward.
We’ve become one of Australia’s fastest-growing infrastructure companies, winning landmark projects and setting new industry standards.
Our difference? A challenger mindset, hands-on approach, and commitment to our people. That’s The Genus Way; and it’s driving our mission to be Australia’s contractor of choice.
WWW.GENUS.COM.AU
UNDER PRESSURE
COLLABORATIVE RESEARCH AND DEVELOPMENT OF TOOLS, PRACTICES AND SYSTEMS ARE NEEDED TO REDUCE RISK FOR THOSE WORKING CLOSEST TO MINING’S BIGGEST TYRES.
The mining industry is no stranger to the risks associated with servicing mining tyres.
The weight and size of the tyres, combined with operating temperatures and pressures, make even the most basic task something that must be undertaken with the utmost care and precision.
While steps have been taken in the last 20–30 years to improve tyre servicing safety, rapid development in truck types and sizes, as well as increased production targets, means that many miners are pushing plant equipment and tools to their operating limits.
When combined with a shortage of skilled workers, these factors can contribute to tyre technicians working under increasing pressure, leading to a higher number of service-related safety incidents. This is something Kal Tire wants to change.
Lightening the load
With mining tyres regularly standing up to 4m tall and weighing up to five tonnes each, handling them can lead to muscle and back strain, and finger pinches and crushes.
Advances in mechanisation and tooling have provided important safety improvements over the years; however,

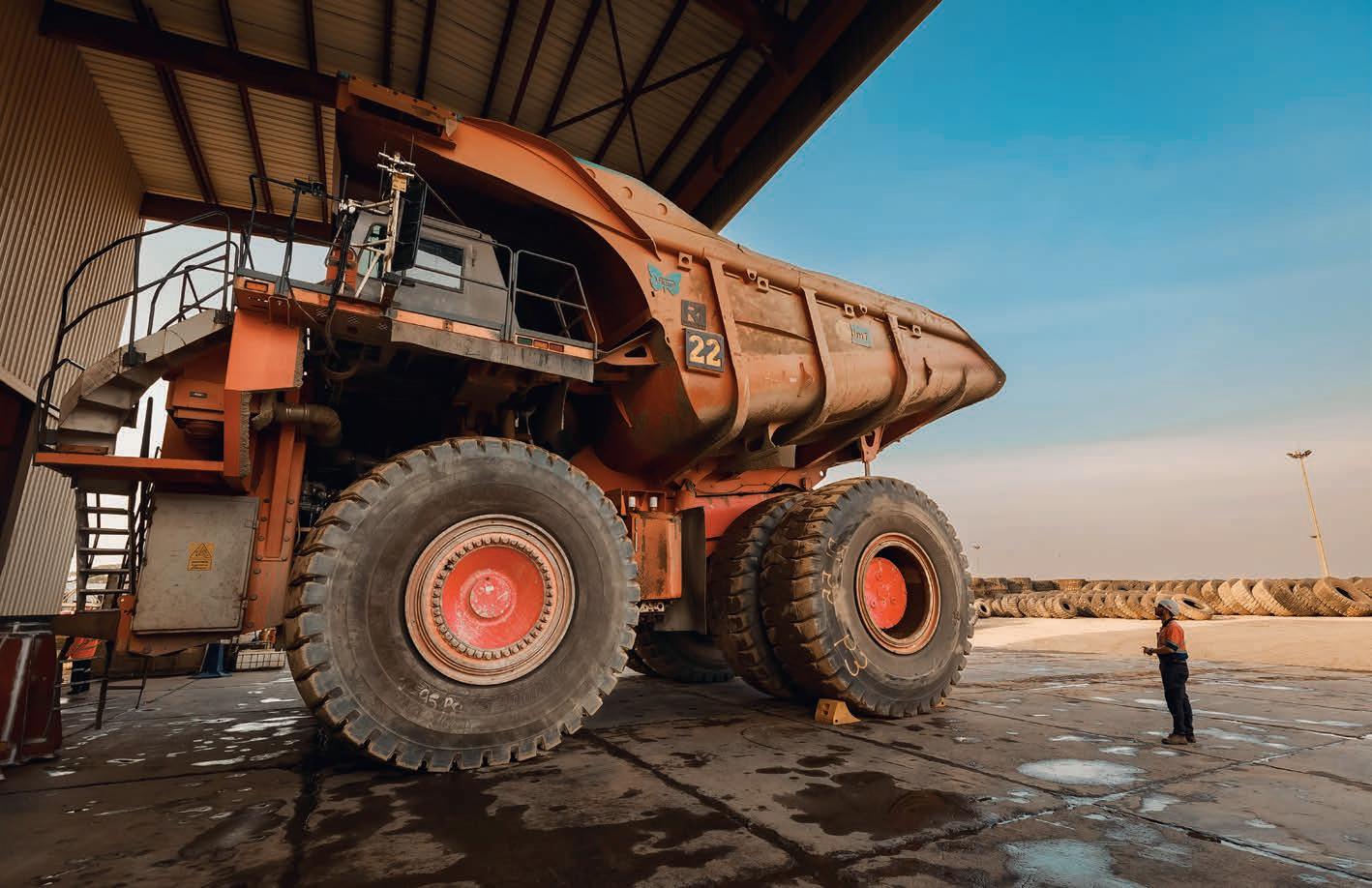
many of these tools have changed little since they were introduced 30 years ago and must continue to be properly applied, inspected and maintained.
Additionally, some tools require training for safe use and can be heavy beasts themselves, with torque guns, for example, often weighing in at 36kg.
Since time is money in the mining industry, there can be pressure on technicians to get machines back into service quickly. This can lead to a potential conflict between doing the job quickly and doing it safely.
And while technologies, tools and training each have a key part to play in keeping technicians safe, they must be implemented and focused on in the manner of a hierarchy to be truly effective.
“Implementing high-level controls tends to be more effective than those at the lower end of the control hierarchy,” Kal Tire Mining Tire Group senior vice president Dan Allan said.
“Frequently in mining, rules or personal protective equipment (PPE) are used for mitigating hazards, but these aren’t enough.
“It’s time to think about eliminating hazards through new processes or using engineering control like innovative tooling to guard against hazards more effectively.”
While PPE will always have a role in safe working environments, the onus is on technicians to apply it consistently. Reinventing work – while more challenging – is likely to be more effective and permanent.
Collaborative tooling innovation
Allan believes that ongoing investment in innovation will be critical in eliminating potential tyre servicing hazards.
“That’s why Kal Tire established its Innovation Center in 2015; to get to the heart of the underlying issues to make our work around the wheel as safe as possible,” he said.
Kal Tire’s GATR (Gravity Assist Tooling Rig) is a prime example of this investment.
Developed via feedback from the company’s technicians, GATR eases the physical burden on technicians by supporting the weight of heavy tools, such as the 36kg torque gun.
“They’re essential in reducing finger pinches, fatigue and strain when mounting tyres, especially ultra-class models,” Allan said.
Leveraging data for the future
Kal Tire hopes insights generated by tyre data management systems will be used to optimise the
planning and execution of tyre servicing in the future.
The company pointed to a recent example in British Columbia, Canada, where one of its customers conducted a trial focusing on automating tyre pressure data collection into Kal Tire’s Tire and Operations Management System (TOMS).
Trial insights showed a reduced inspection time, reducing technician exposure by 40 per cent.
Robotics and automation also have a part to play in increasing safe practices. With most manual work in buffing, building and grooving already eliminated, automation could see these risk mitigated further if robotics were to take over the remaining tasks.
“As automated systems become more economical and feasible, there are so many opportunities to use automation in the tyre service space to eliminate hazards and risk,” Allan said.
“The only limit to the application of these automated systems is our own imagination.
“To achieve safer tyre servicing, mining companies need to work closely with their teams, service providers, original equipment manufacturers, training bodies, and more. We’ll get there faster and more effectively if we work together.” AM

THE PROCESS in Mineral Processing
Our innovative flotation technologies are changing the way mineral processing plants are designed. Our vision is to make processing minerals more efficient and less impactful on the environment. Leap Forward with Eriez. The patented HydroFloat® Coarse Particle Flotation (CPF) technology is proven to increase mill throughput and net metal production while unlocking transformational tailings disposal techniques.
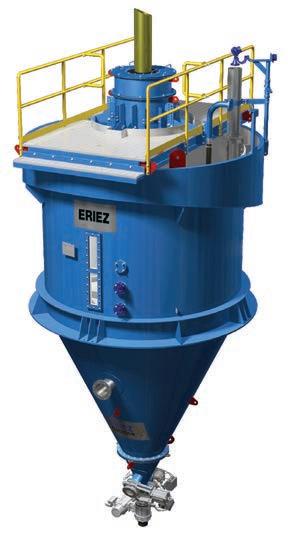
A REFRESHED BRAND IDENTITY
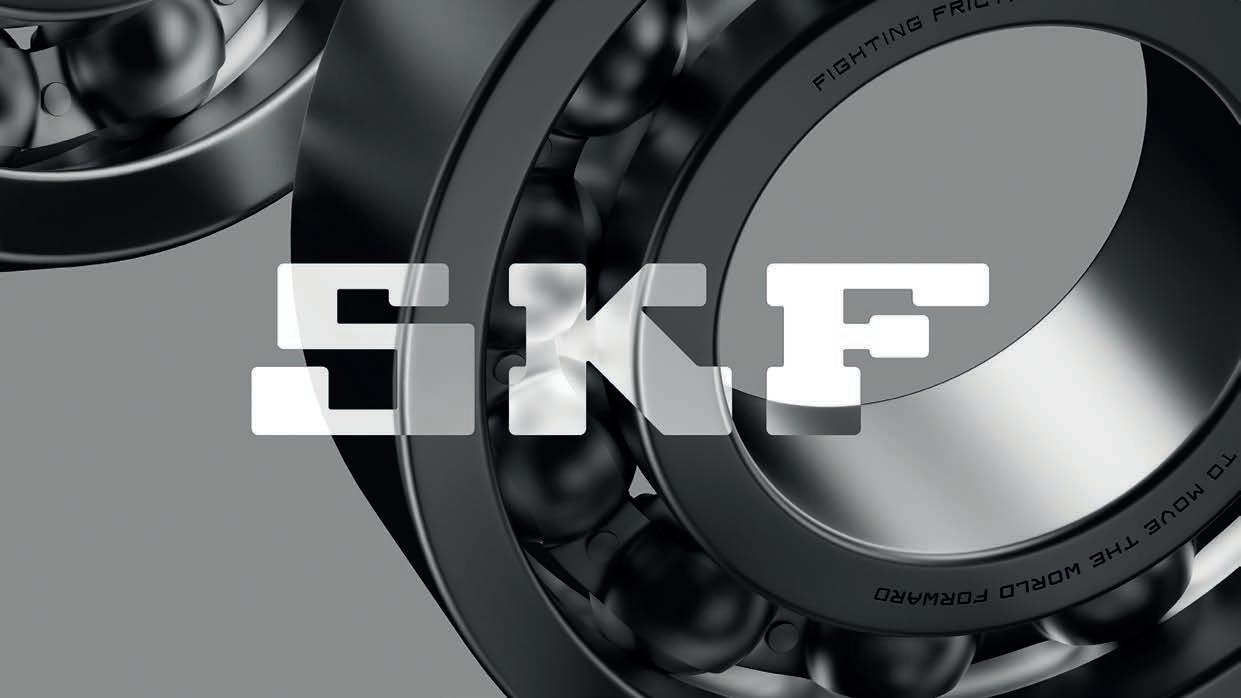
Sand solutions that reduce friction for over 100 years.
Now, the company is stepping up its efforts as it actively fights to move the world forward. SKF aims to make industry smarter, more competitive, and more energy-efficient, ultimately contributing to a more sustainable society where more can be done with less.
To align its brand with today’s offering and values, SKF is making subtle but significant changes to its brand, which reflects the business SKF has become, helping the group to further stand out in the industry, attract more customers, and drive profitable growth.
people, reputation, communication and our desired future state,” SKF president and chief executive officer Rickard Gustafson said.
“From a business perspective, we are building favourability among current and potential customers, employees, investors, partners, and beyond. It’s a way of earning our place in the world while staying true to our values and purpose.”
The new brand strategy builds on SKF’s historical, current and future strengths, refining communication to tell a bigger story. This new direction aims to bridge the gap between SKF’s extensive impact on the world and public perception, which means highlighting
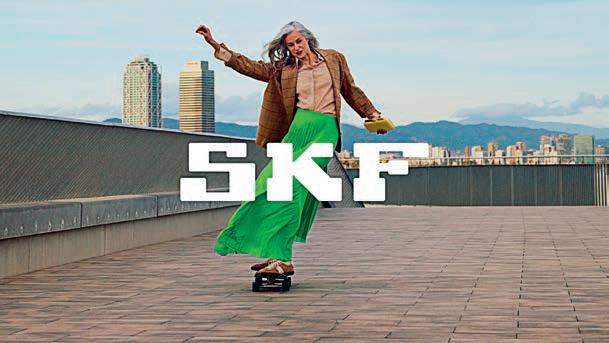
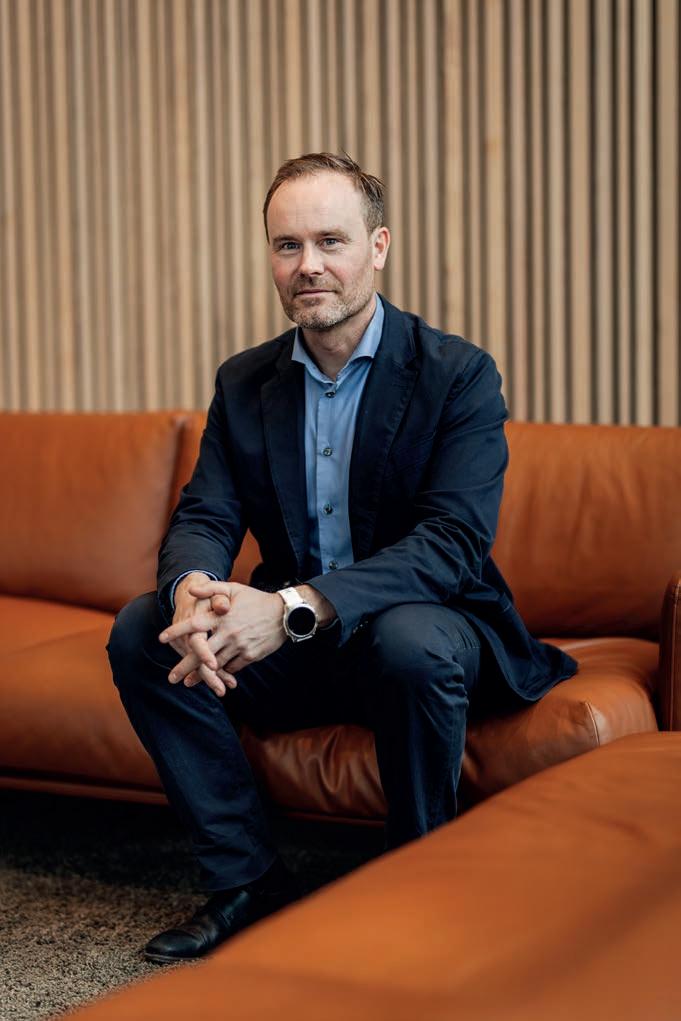
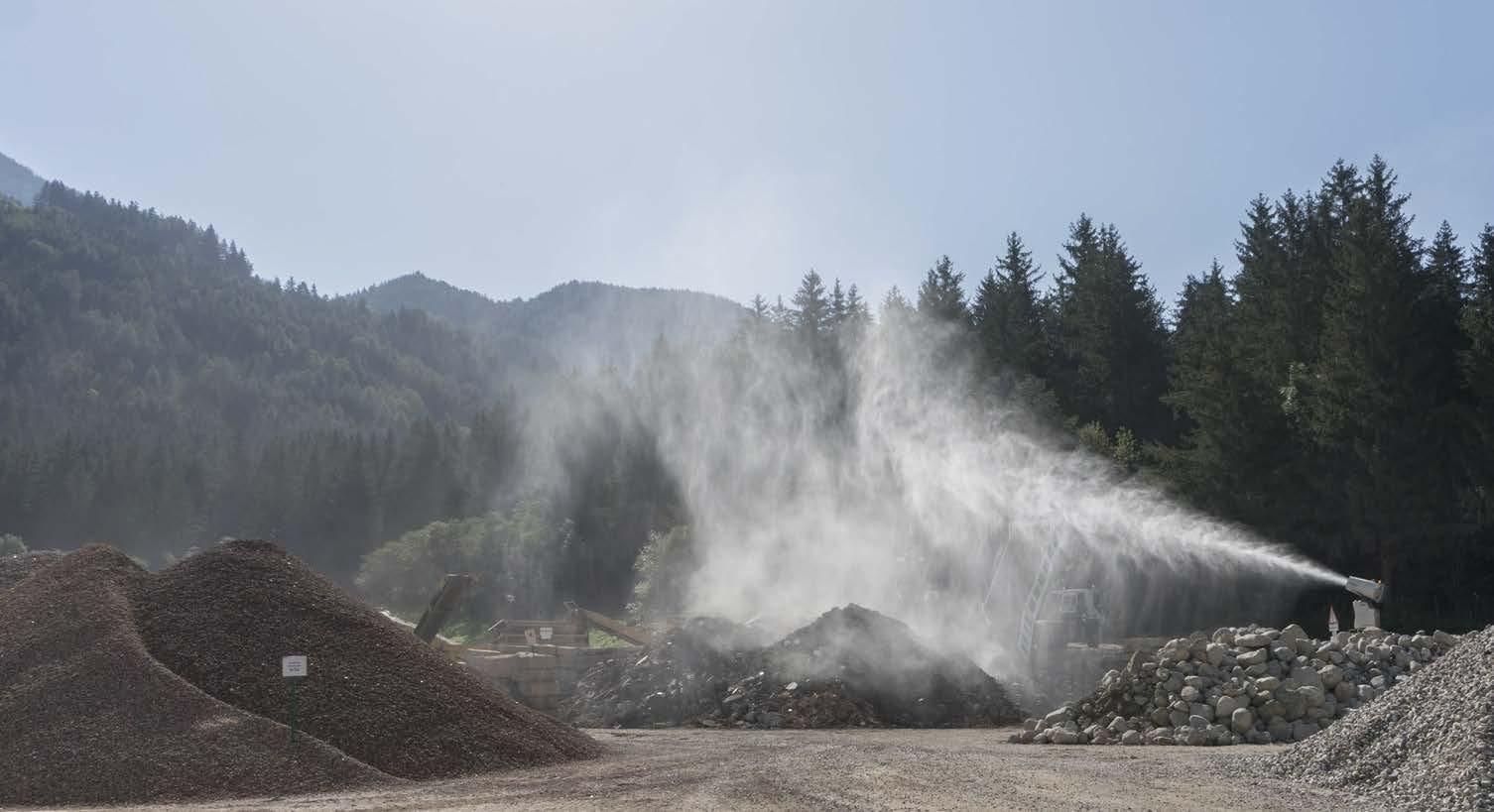
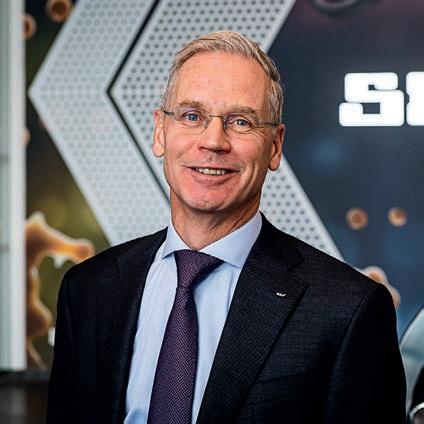
will also provide better marketing support for distributors, including a redesigned distributor identity that is simpler, more consistent, and easier
“In almost 120 years of innovation, we’ve developed products and solutions that reduce friction,” Gustafson said. “Now we’re stepping that up. Not just reducing friction but actively fighting friction to move the world forward and telling the story about the difference
These updates will be rolled out over the coming year across new marketing and communications materials, a refreshed website, and other
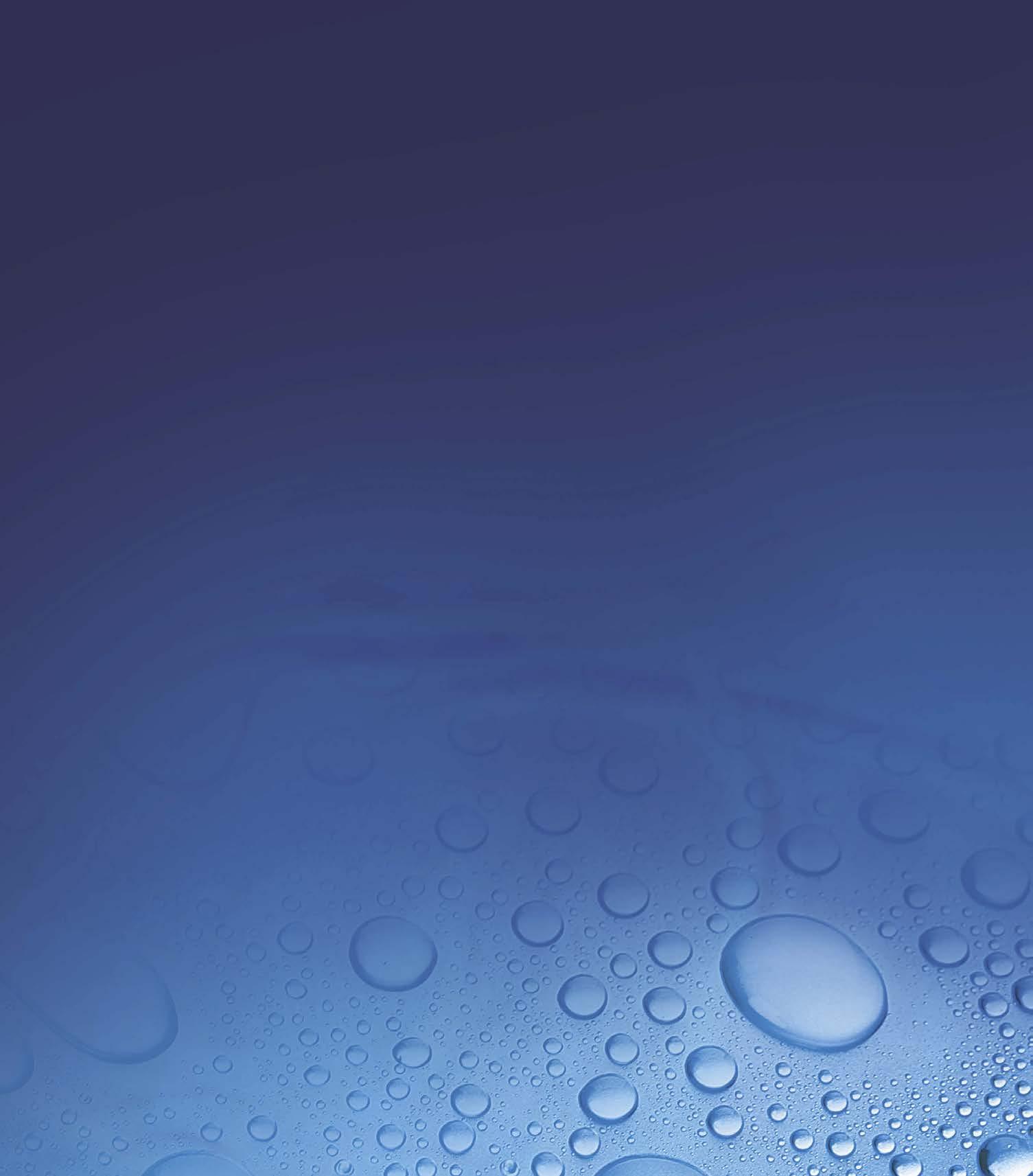
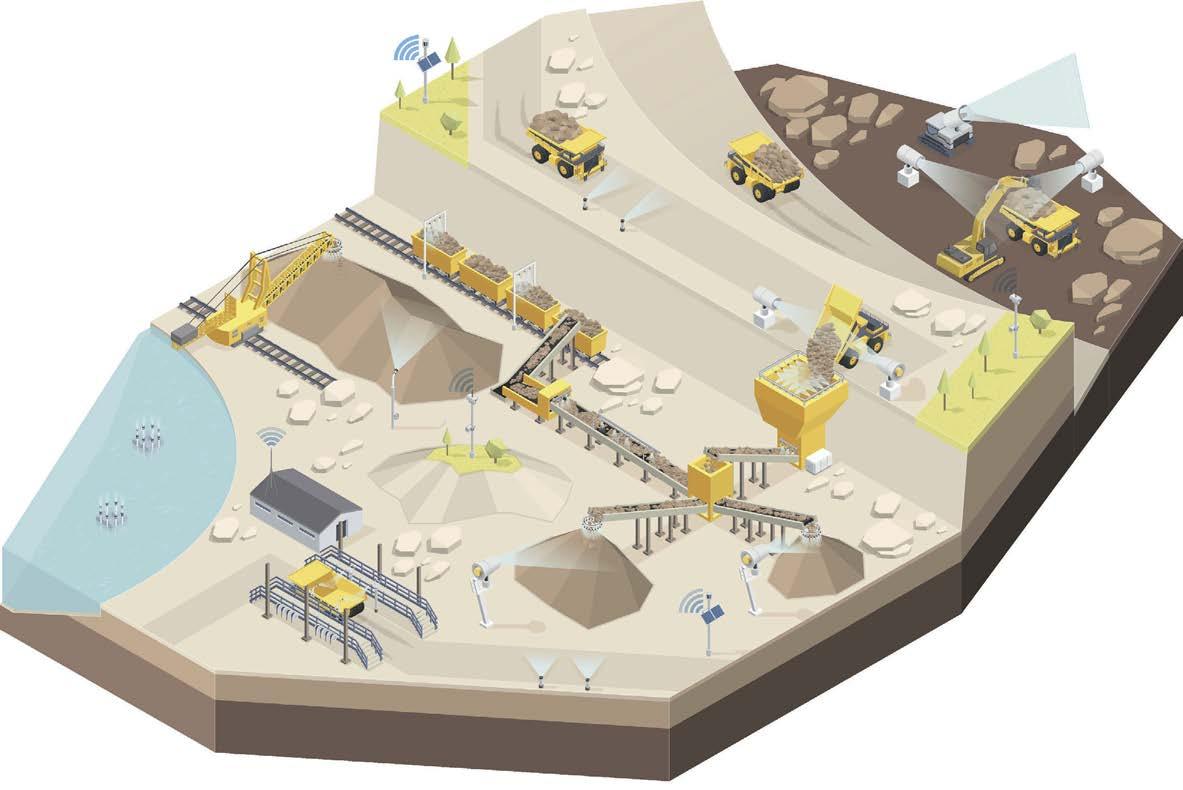
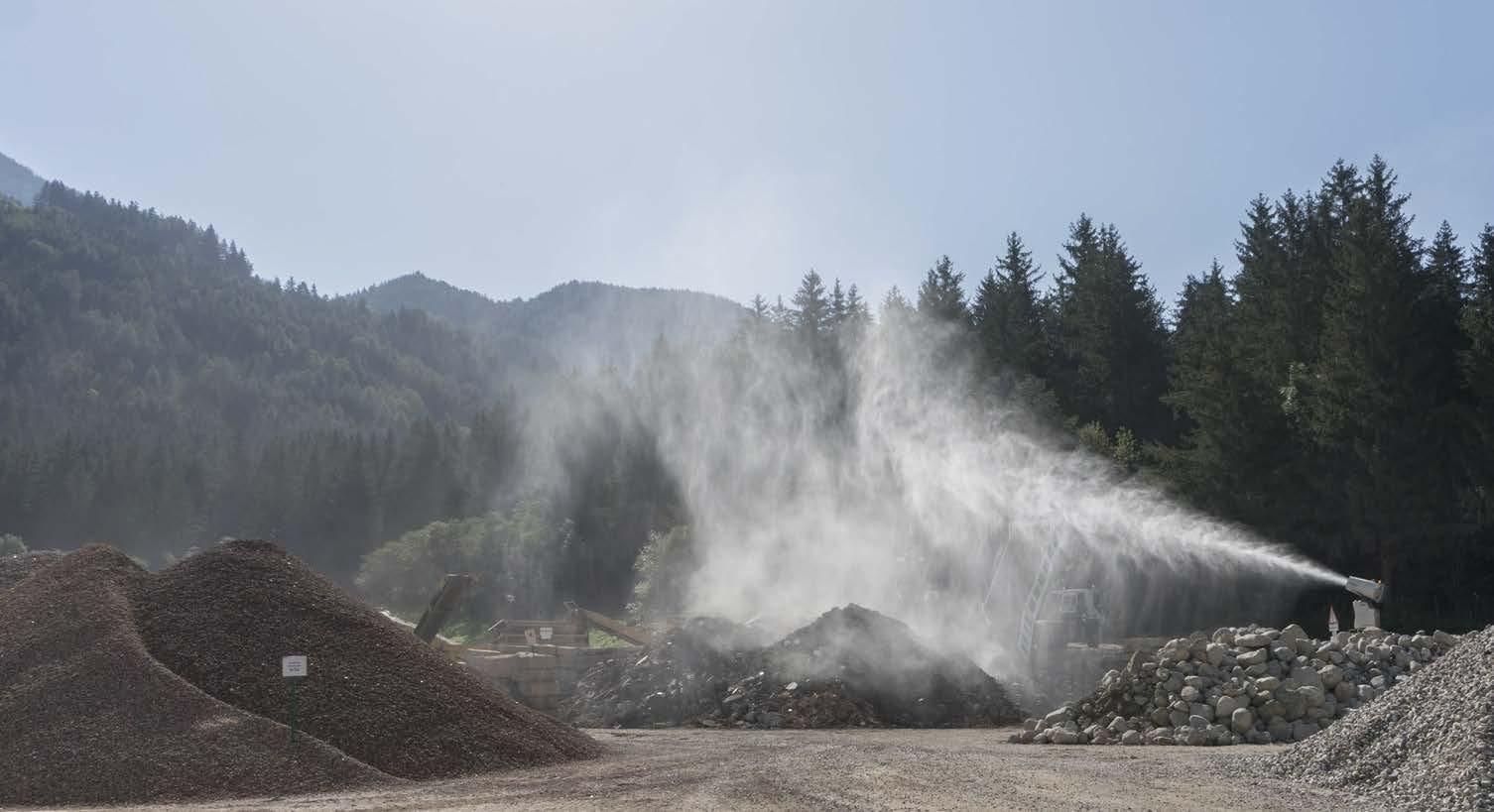
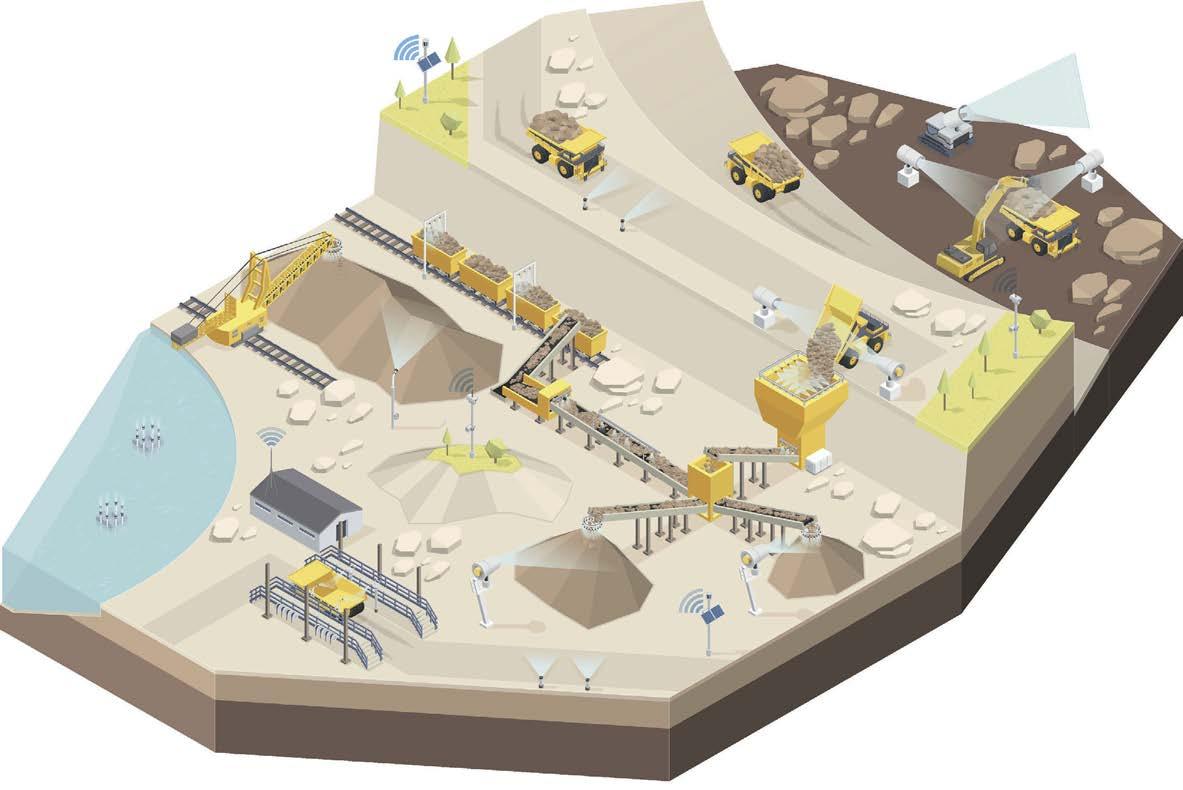
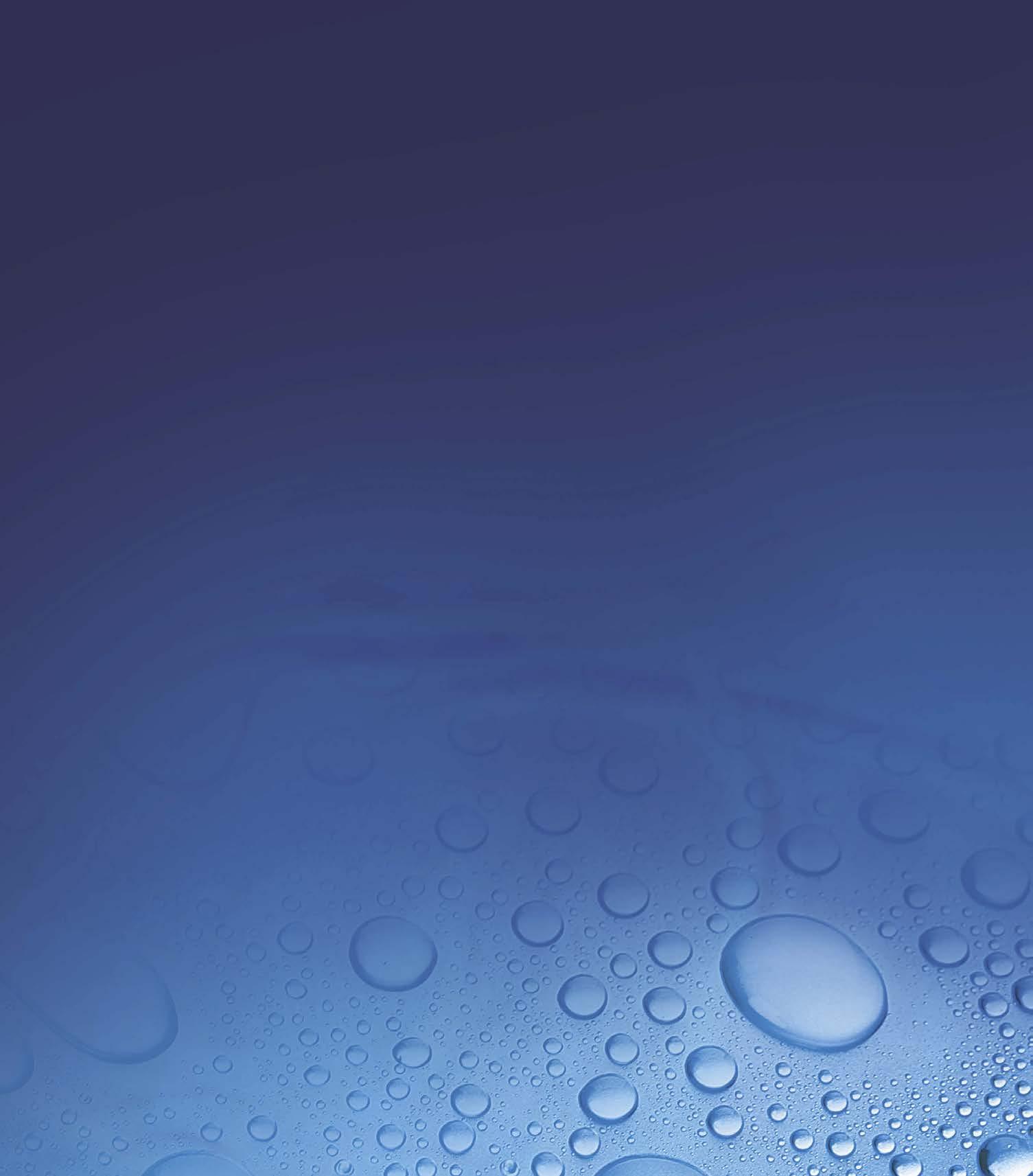
LEADING THE ENERGY TRANSITION
MINING HAS A LARGE PART TO PLAY IN THE WORLD’S TRANSITION TOWARDS NET-ZERO.
The mining industry stands at a crossroads as global economies push towards netzero emissions.
Accenture managing director Eric Croeser sat down with Australian Mining to outline the challenges and opportunities miners face in the decarbonisation journey, stressing that the transition is already well underway.
“There’s been significant movement forward,” Croeser said. “More than 50 per cent (of mining companies) are actually implementing things, and within those 50 per cent, they have a wide array of levers that they are pulling in all ways and forms.”
The three pillars of decarbonisation
According to Croeser, mining companies need to focus on three key areas to drive the transition: investment, operations and policy.
The first area, investment, is where miners are putting their money as they look to what assets they acquire and develop.
“If you have a look at all of the acquisitions that are being made, any of the mergers that are happening, it’s across either copper, high-grade iron ore, or lithium deposits,” Croeser said.
“These are the commodities needed for renewable energy infrastructure, battery storage and electric vehicles.”
The second area, operations, encompasses technology adoption within existing operations.
“Are we seeing miners actually transitioning and bringing in some of these new technologies? The jury is out, it’s sort of a 50–50 split at the moment,” Croeser said.
“While many companies have detailed decarbonisation plans, only about half are actively executing them.”
The third area, policy, relates to process development to ensure long-term decarbonisation efforts remain a priority.
Croeser said mining’s ability to attract new talent will increasingly depend on its environmental credentials.
“Mining is not the sexiest business in the world, we know it hasn’t been,” he said. “But the fact that we are at the cusp of the energy transition, and miners have such a big part to play, makes it an exciting industry to be in.”
Lithium’s long-term outlook
Lithium remains at the heart of Australia’s mining future, but recent price fluctuations have caused uncertainty. Croeser recognised the volatility but stressed that the long-term fundamentals remain strong.
“There’s definitely a recognition that battery metals are required,” he said. “The short-term depression in some of those prices is potentially due to quite a bit of an oversupply.
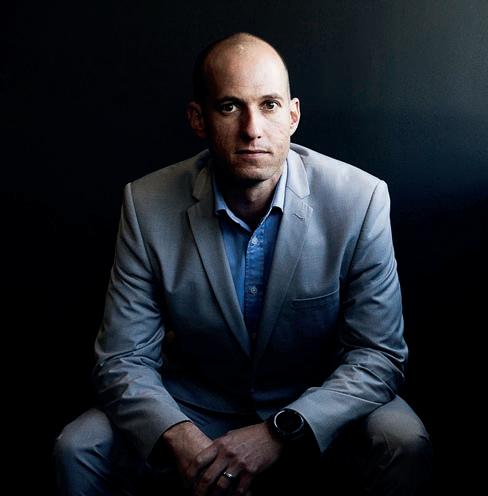
Challenges for mid-tier miners
“Diesel and fossil fuel consumption still account for upwards of 60 per cent of operational expenditure,” he said. “If you can improve efficiency and introduce an energy mix, you lower your cost of production, extend mine life and make marginal projects viable.”
AI and automation
The rise of artificial intelligence (AI) and automation is revolutionising mining operations, not just in efficiency but also in workforce attraction.
“We’re in a race to attract the industry experience and technical expertise needed to meet future demand,” Croeser said. “The skillset required in mining has shifted to a much more tech-led, decision-driven model. Companies that integrate AI and automation into their operations will have a significant advantage in talent attraction.”
Mining’s role in the energy transition
“However, if you look at the large miners, their investments are in lithium, which means they see a 10-, 15-, or 20year timeframe on the horizon.”
Croeser highlighted the need for attractive policy settings to help ensure Australia maintains its competitive edge in lithium.
“It’s not rocket science: we need policy to ensure that investment is channelled into Australia,” he said.
“We need to think about the fully integrated value chain – not just mining and processing but the entire end-to-end operation.”
While major mining companies have the capital to invest in decarbonisation, those closer to the middle can face greater challenges.
Croeser suggested they focus on three strategies: fast adoption of proven technologies, prioritisation of cost-saving initiatives, and industry collaboration.
“Mining in general has always been a relatively fast adopter,” he said.
“Mid-tier miners tend to be very quick adopters once the big five have figured it out.”
Croeser also pointed out that electrification can drive significant cost savings, particularly in dieseldependent operations.
Despite its challenges, mining is fundamental to achieving net-zero.
“If it doesn’t flow or it doesn’t grow, you have to mine it,” Croeser said.
“The great thing from the data is that we can see mining companies driving efficiency, staying cost-competitive, and securing investment.”
Croeser said it’s tempting for companies to only look at a 12-month cycle, but these are long term investments, particularly with adopting sustainable tech.
“The time for investment and decision-making needs to be longer,” he said. “The balance between getting material out of the ground effectively and sustainably is critical.” AM
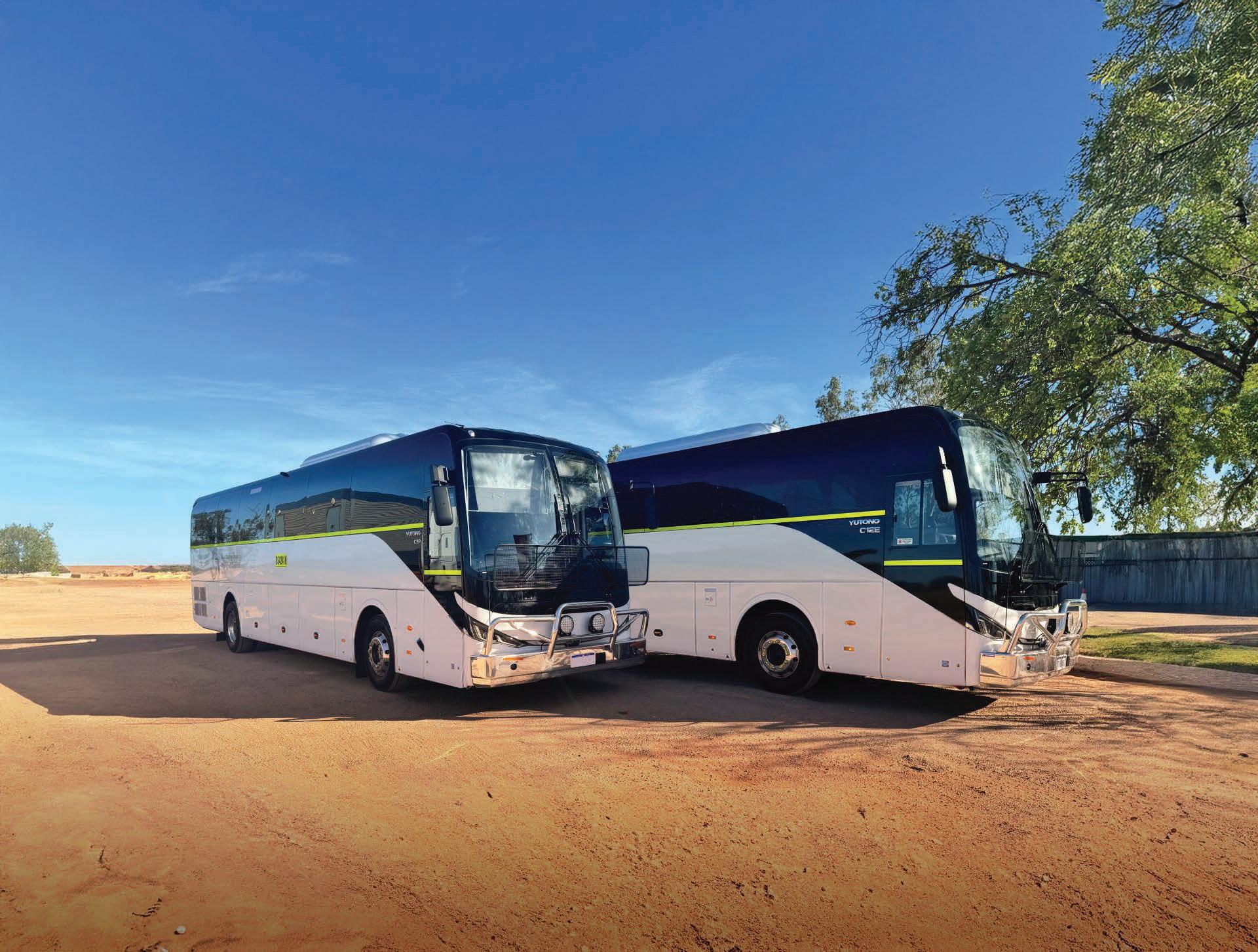
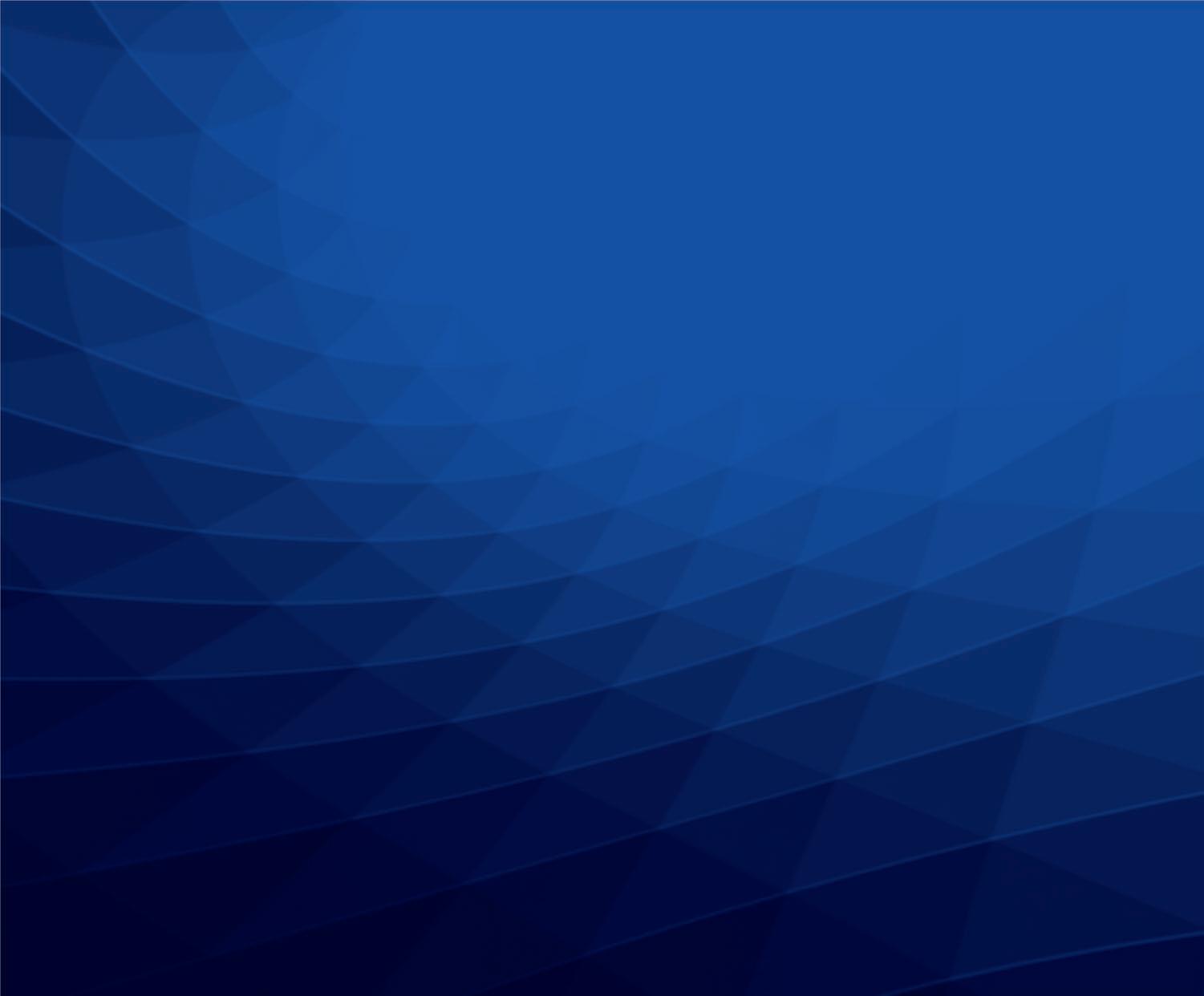
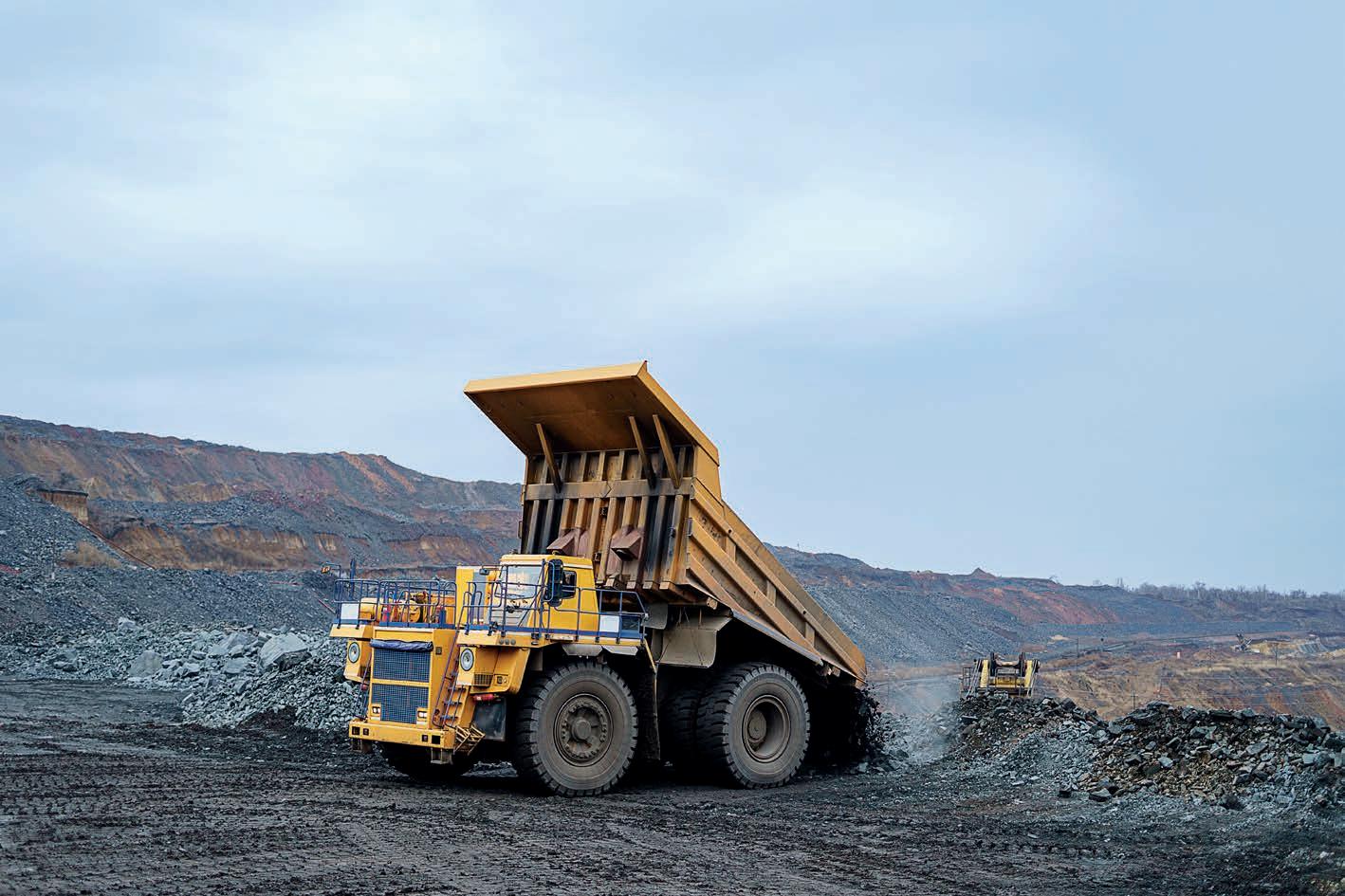
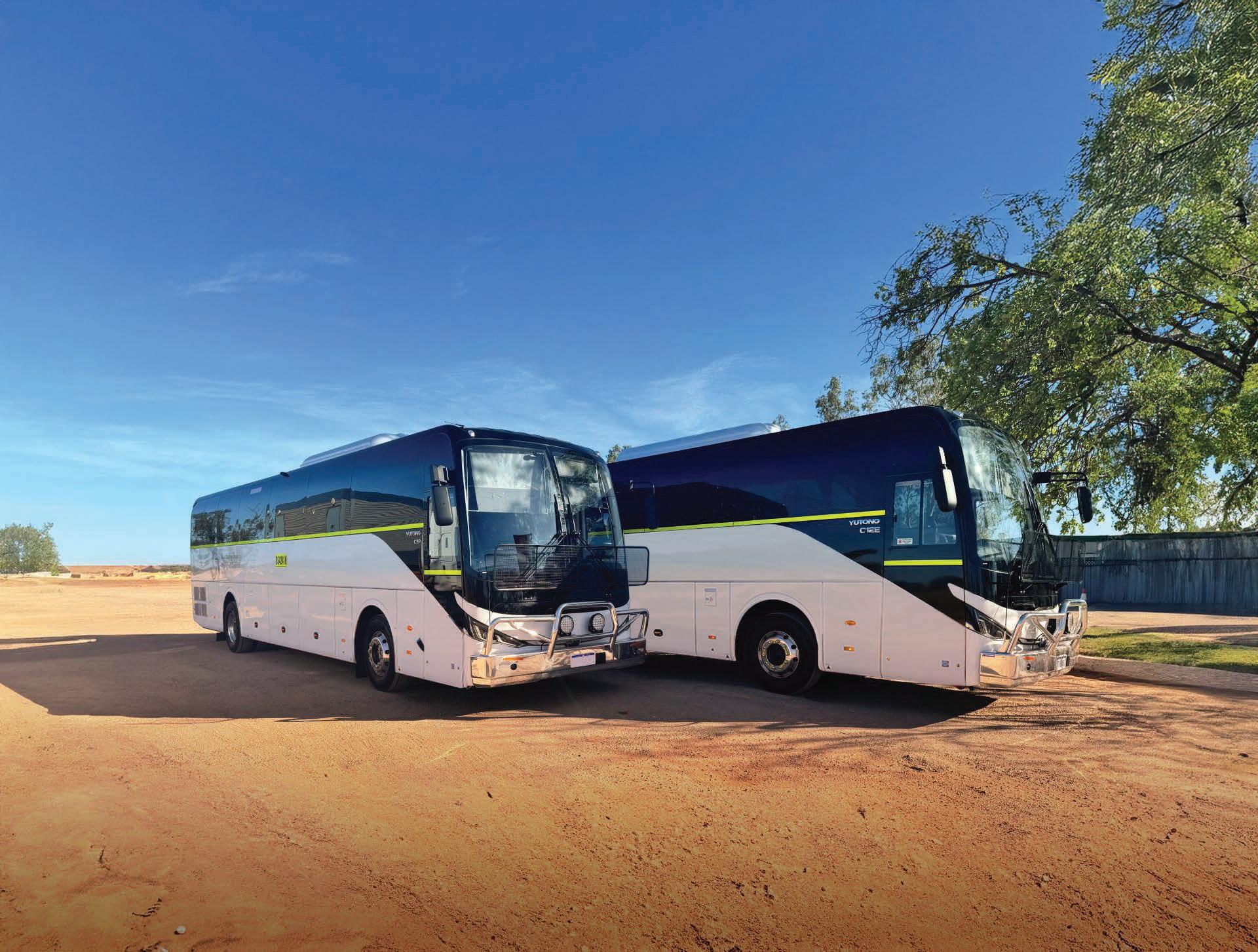



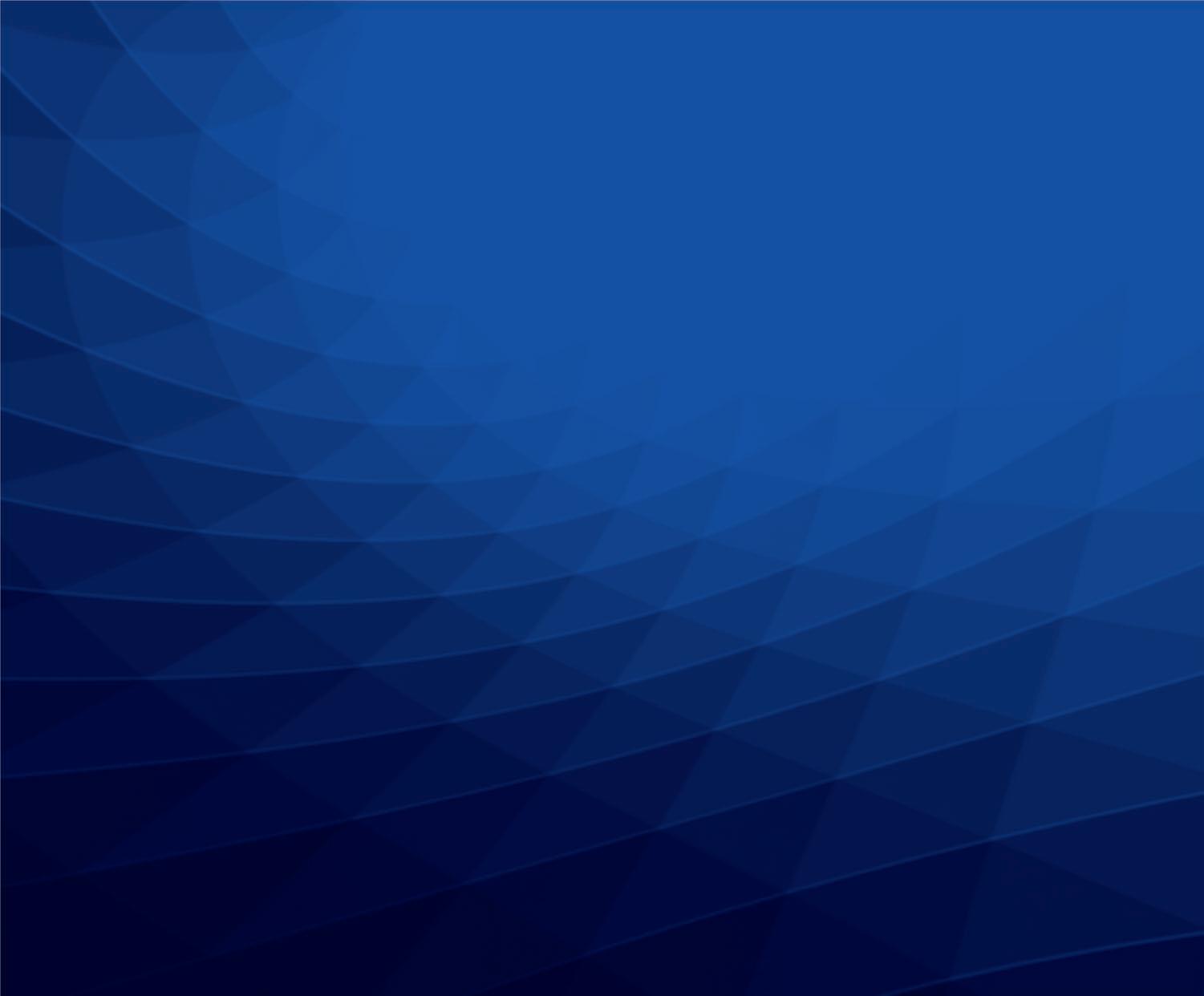

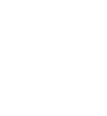
GLENCORE GIVES GRADUATES THE OPPORTUNITY TO LEARN ON THE JOB.
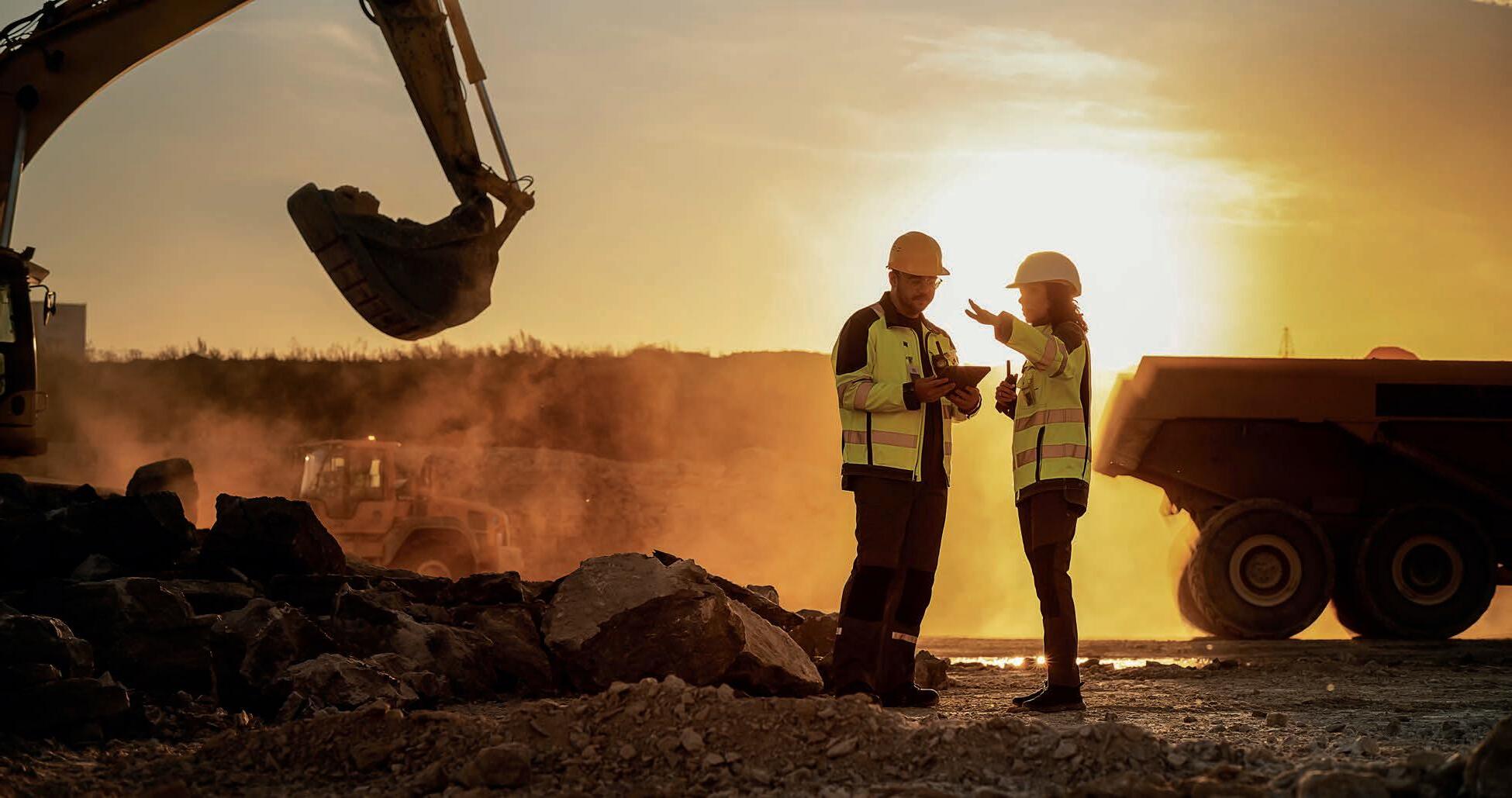
GOLDEN GRADUATES
GLENCORE’S GRADUATE PROGRAM PUTS CAREER GROWTH FIRMLY IN THE PATH OF FUTURE MINING PROFESSIONALS.
Glencore knows the future of the Australian mining sector lies in the next generation. With that firmly in mind, the Tier 1 miner has been cultivating its graduate program, welcoming more than 600 aspiring mining professionals new into its coal, zinc and coppers operations across the country.
The two-year program gives the graduates opportunity to learn on the job with Glencore, embracing new skills and relationships as they learn the ins and outs of the industry.
As Glencore readies itself to welcome its 2026 cohort, Australian Mining sat down with two current graduates to discover how the program has changed their lives and careers.
“Getting the chance to work with an experienced crew and learn from people on the ground has been a highlight for me,” Glencore coal graduate Amy Scott said. “I’ve now been working at Oaky Creek in Queensland for a year and I’ve learnt so many practical skills.
“What we do each day varies, so I’m never bored. Everyone has been so supportive and genuinely wanting the graduates to succeed.”
Metals graduate Sascha Bentley is also one year into the program. Working as a graduate environmental advisor at Mount Isa in Queensland, Bentley said the professional development from the program has been invaluable.
“I’ve been able to work across air-, water- and soil-quality spaces with a friendly team,” she said.
“While I’m developing professionally, I’m also developing key relationships with other graduates and the senior leaders to push me further.”
Glencore coal human resources (HR) manager Michelle Montgomery has been with the team since well before the graduate program began in 2020. She remembers when Glencore had just six graduates, a number that can now reach up to 70 a year in the coal business alone.
“The networking opportunities are one of my favourite aspects of the program,” Montgomery told Australian Mining
“The graduates are able to meet each other from day one, and we have our senior management team speak to them that day, too. Since they’re sharing the same journey, graduates naturally form a tight-knit group where they can learn from each other. They’re also learning from subject-matter experts on the field, so they can tap into years of experience.”
Glencore zinc pathway program coordinator Stephanie Jabbour explained more about how the program works.
“We run on a structured 70, 20, 10 model,” she told Australian Mining. “That’s 70 per cent hands-on learning, 20 per cent peer learning and mentorship, and the last 10 per cent is run through an HR-led program.
“The zinc graduate cohort goes up to Mount Isa four times a year during the program to make sure they’re getting the best possible mentorship and support. First-years can use this opportunity to ask second-years questions and create some further connections.”
Jabbour and Montgomery agree that the Glencore graduate program is an essential part of the wider business.
“We have people who started their careers at Glencore on the graduate program who are now ambassadors and mentors,” Montgomery said.
“I’m proud to work for a company that is so supportive of graduates, and one that always has a place for them.”
Scott and Bentley are each hoping to stay on as Glencore employees once their graduate years are finished.
“The program has given me the opportunity to live independently while also cultivating close social bonds,” Scott said.
“The program has given me a wellrounded understanding of what the expectations of my role are and how I fit into the bigger picture of the coal handling and preparation plant.”
Bentley has found the experience to be a truly unique one.
“One of my favourite parts has been the wet season,” she said.
“Getting out into the more remote areas around town, four-wheel driving, and water sampling in the middle of the bush is far from a hard day in the office.” AM
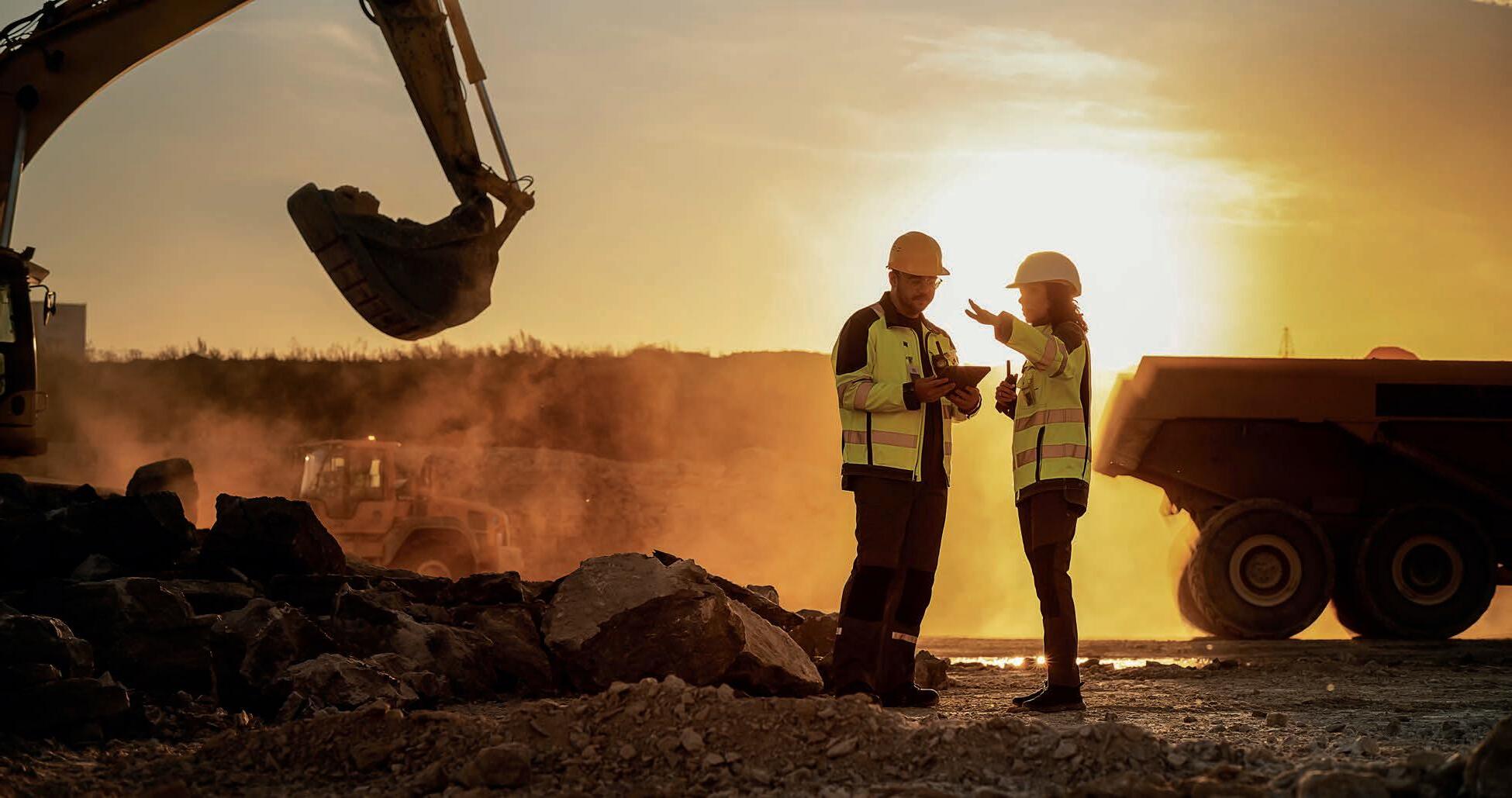

Unlock the Full Power of Predictive Maintenance with AI Sensor Fusion Technolo
Optimize Planned vs. Unplanned Maintenance for peak efficiency
Reduce unplanned maintenance hours and disruptions
Lower total maintenance expenses
Enhance annual plant output and operational performance
Save significantly on repair and maintenance costs
Extend the equipment lifespan with smarter, AI-driven maintenance strategies
Join the revolution in AI-driven predictive maintenan Get in touch today.
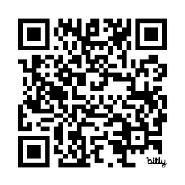
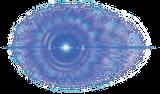
Scan the QR code to contact us
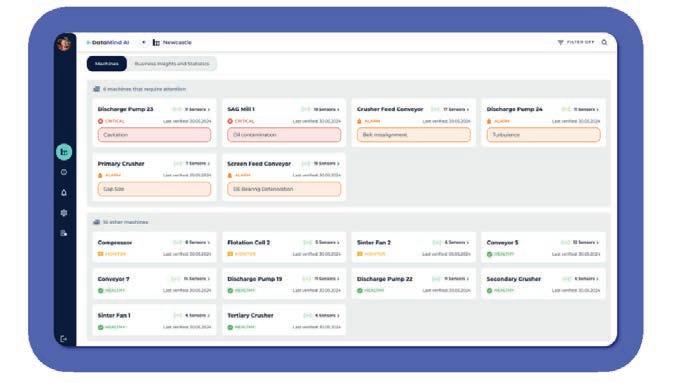
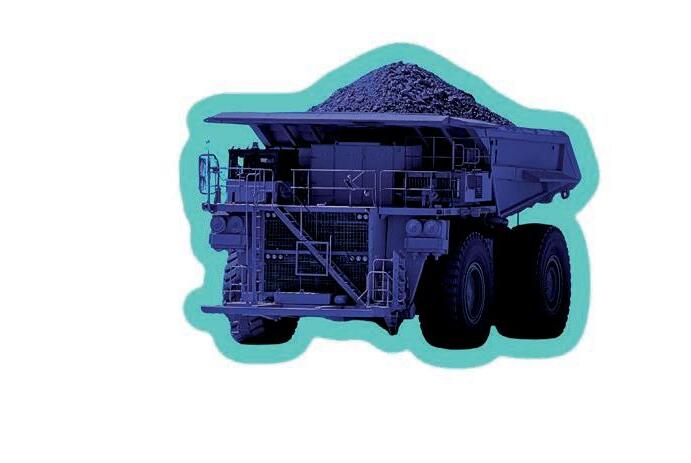
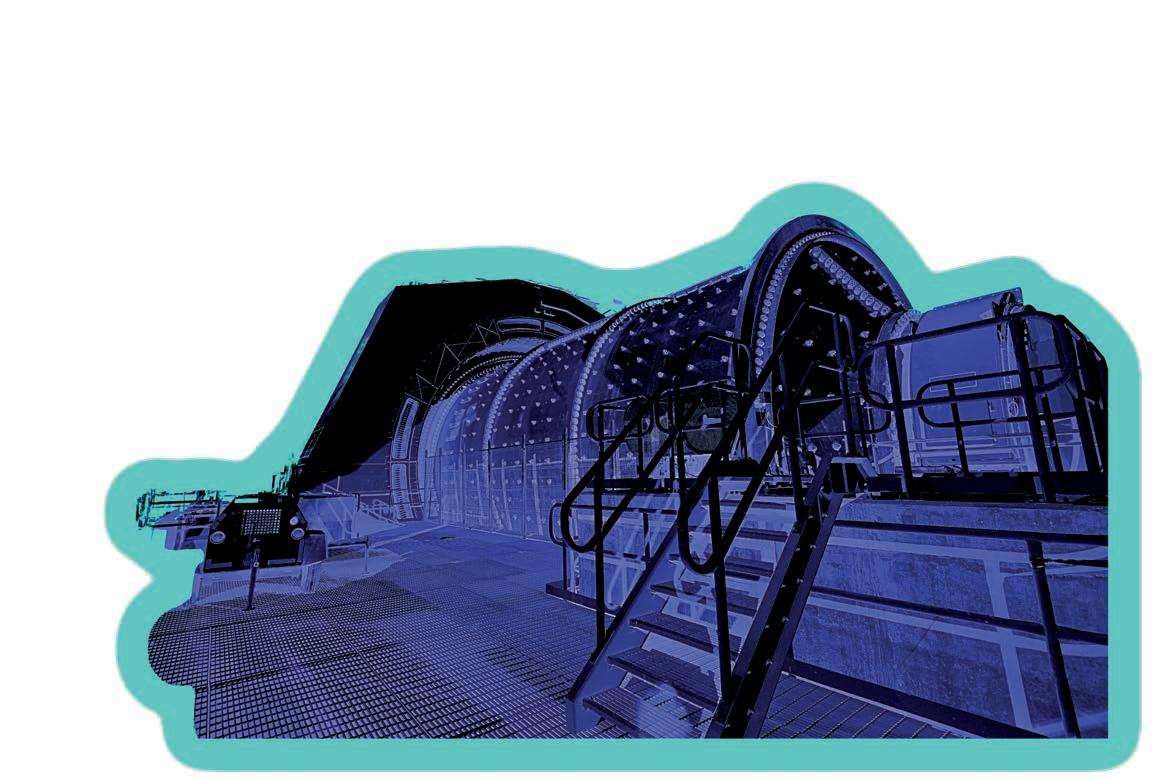
SCHLAM LAUNCHES THE HERCULES ULTRA
SCHLAM IS DRIVING A NEW ERA OF ULTRA-CLASS MINING TRUCK INNOVATION.
As the demand for greater efficiency and productivity in mining operations escalates, Schlam continues to lead the charge in designing and delivering innovative solutions for the mining industry.
The introduction of the Hercules Ultra, an advanced truck bed designed for ultra-class mining trucks, marks the latest milestone in Schlam’s evolution as a global leader in load and haul attachments.
Schlam’s commitment to innovation, customer collaboration and strong engineering principles has resulted in a product that is set to redefine industry standards.
A legacy of innovation
Schlam’s Hercules range has built a strong reputation for delivering performance improvements across the mining industry.
Mining operators across the world have seen payload productivity
improvements of up to 22 per cent, significant maintenance cost reductions, and enhanced fatigue life and asset longevity.
The introduction of the Hercules Ultra is the latest step in Schlam’s commitment to evolving and enhancing mining truck solutions, bringing these same benefits to the next generation of ultra-class mining trucks.
The evolution of the Hercules range
The Hercules range has seen continuous improvements since its inception, driven by Schlam’s focus on innovation and listening to the needs of its clients.
Schlam works closely with its clients to understand their challenges and uses strong engineering principles to develop products that provide lasting solutions. This customer-centric approach has made Schlam a leading supplier of mining truck beds in Australia and a key supplier to autonomous mining truck fleets worldwide.

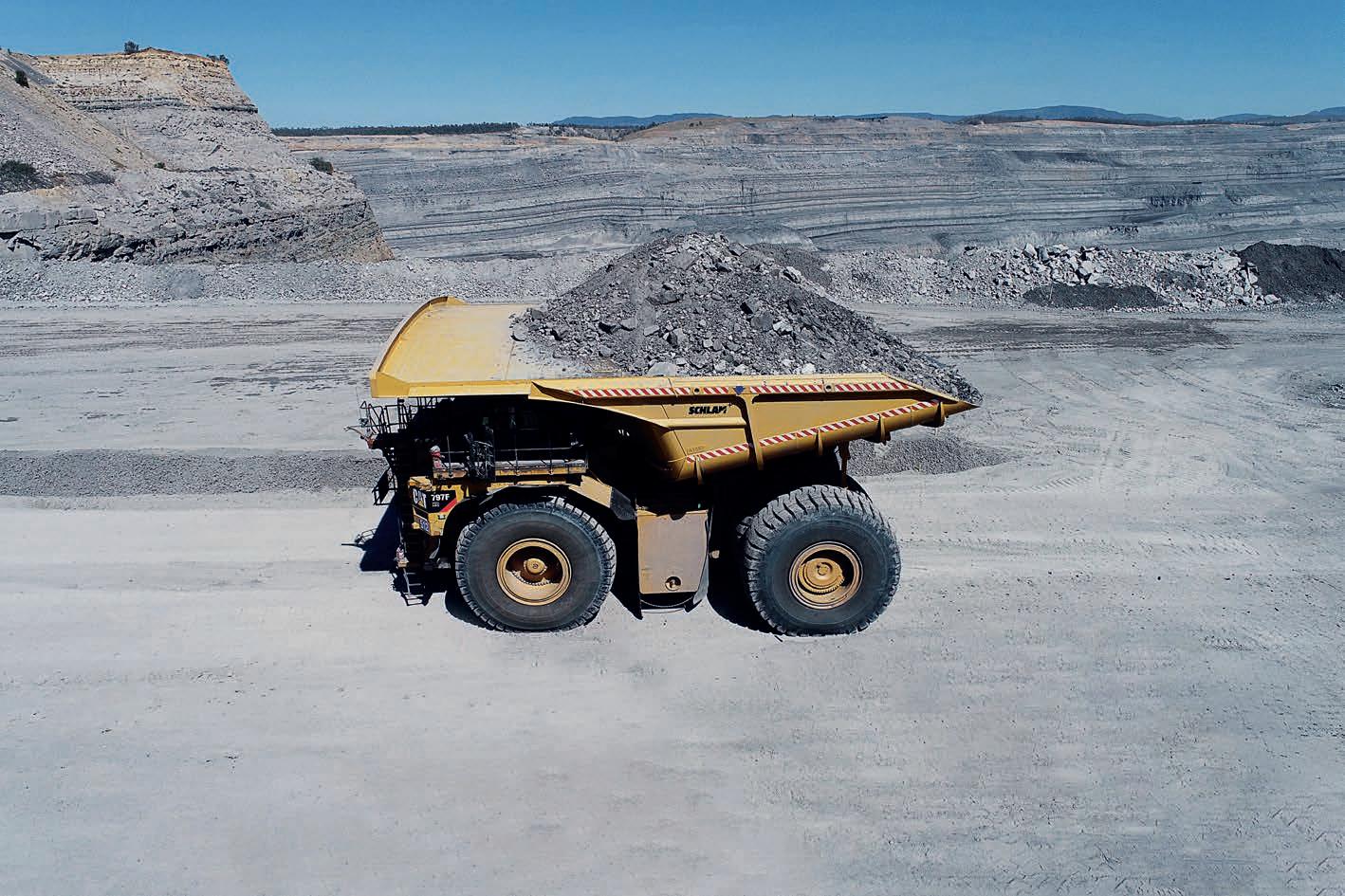

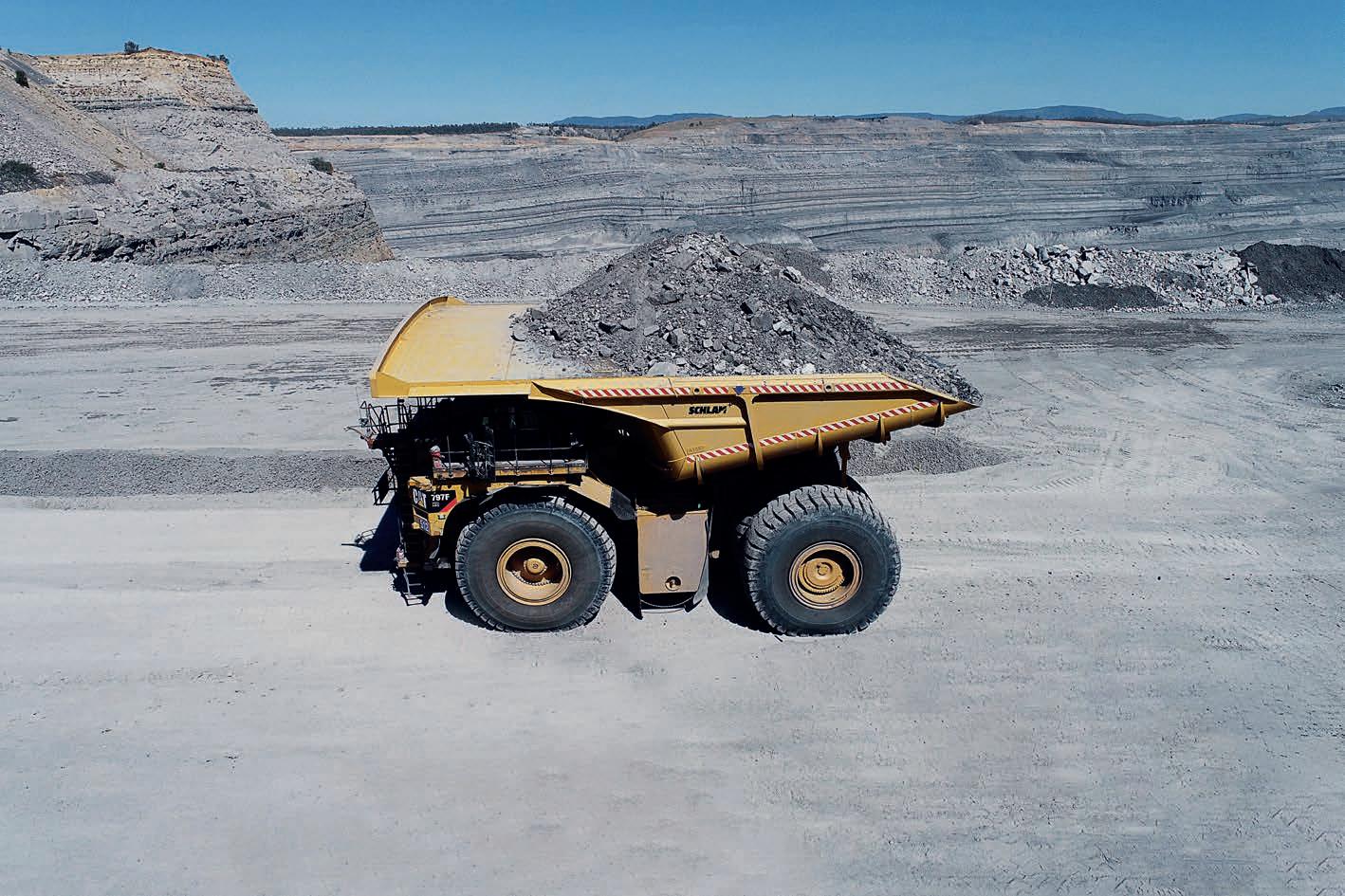
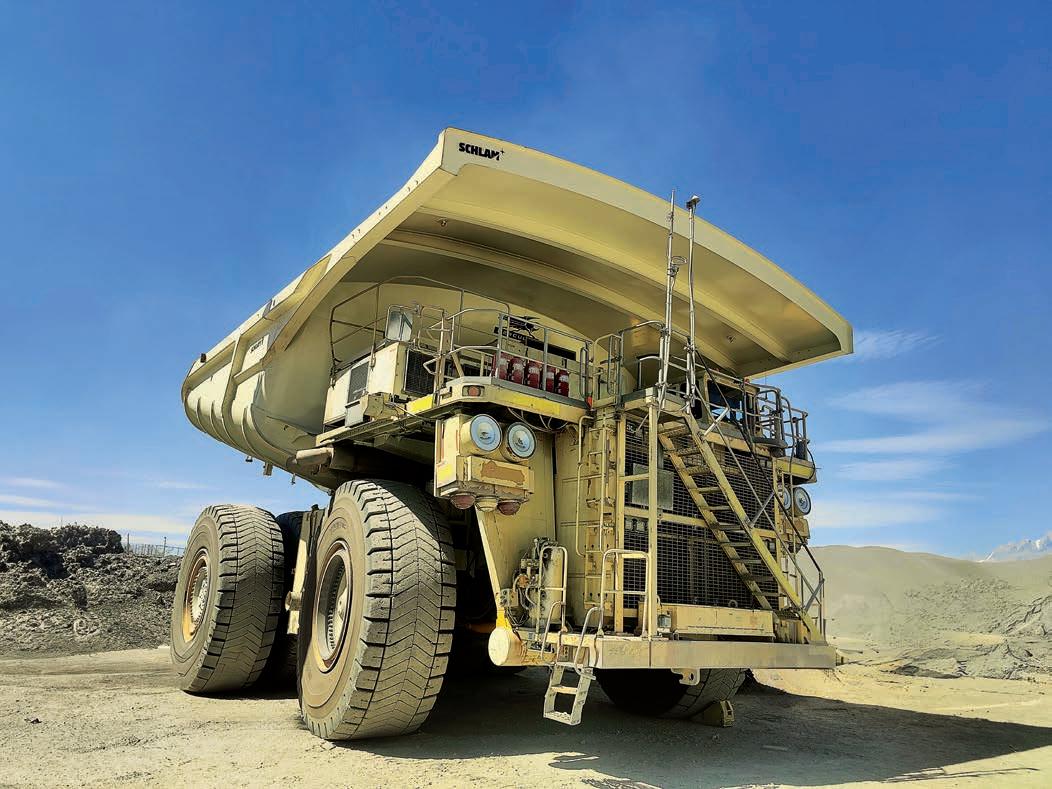
terms of payload capacity, durability, and performance.
Ultra-class mining trucks are the workhorses of mining, and as such, the demand for solutions that can further optimise their performance is critical.
The introduction of the Hercules Ultra comes at a time when mining companies are pushing for more efficient, higher-performing solutions to meet the demands of modern mining operations.
With the mining industry’s growing adoption of automation and fleet management technologies, ultra-class trucks are becoming increasingly sophisticated, making the need for equally advanced accessories like truck beds even more important.
Evolution in action
The development of the Hercules Ultra was driven by an increasing need for stronger, lighter, and more efficient dump beds for ultra-class trucks.
Schlam understood that as payloads increase and larger truck models are introduced to the market, the need for stronger, lighter, and more efficient truck beds was essential.
This led the company to develop the Hercules Ultra, the next step in the evolution of the Hercules range, representing a major leap forward in
Combined with Schlam’s extensive experience in developing solutions for large-scale mining operations, the Hercules Ultra builds on the DNA of the Hercules EXO.
“The Hercules Ultra demonstrates our commitment to continuous improvement,” Schlam global product manager Tom Smith said. “We utilised our extensive product knowledge and engineering capability to solve the unique challenges these high-payload trucks face.”
The Hercules Ultra maintains all of the lightweight product benefits of the Hercules bed, but with structural upgrades to withstand the fatigue challenges associated with the increased payloads of ultra-class trucks. Engineered to operate for 25,000 hours maintenance free, with the goal of extending that to 30,000 hours, mining operators can rely on the Hercules Ultra for long-term performance.
The Ultra advantage
One of the defining features of the Hercules Ultra is its ability to combine strength and weight reduction.
Schlam achieved this balance by reinforcing high-stress areas to maintain structural integrity while eliminating unnecessary components to
MORE EFFICIENT, HIGHER-PERFORMING SOLUTIONS IN THE MINING INDUSTRY.
reduce weight, resulting in a stronger and lighter truck bed that offers increased payload capacity without compromising durability.
The Hercules Ultra’s design represents the next generation of mining truck beds, tailored to meet the evolving demands of the ultra-class haul truck segment. Whether it’s maximising payload, improving fatigue life, or reducing maintenance costs, the Hercules Ultra delivers a comprehensive solution for mining operators looking to optimise their fleets.
Glencore partnership
The development of the Hercules Ultra was supported by Schlam’s ongoing relationship with Glencore Coal. Extensive field trials were conducted at Glencore’s Ravensworth operation in New South Wales, providing valuable insights that helped refine the final product.
“We are truly grateful to Glencore Coal for assisting with our trial,” Smith said. “Their input was invaluable in helping us refine a product that meets the specific needs of the ultra-class truck market.”
A spokesperson for Glencore Coal’s Ravensworth open cut mine said the Hercules Ultra has already proven its worth in increasing production capabilities.
“We wanted a Hercules product that delivered increased production capabilities while maintaining the same features and benefits as the original range,” he said. “The trial showed that the Hercules Ultra could deliver on that requirement.
“We’ve recommended expanding its use across our other operations and regard it as a product that contributes to our commitment of sustainable and responsible resource extraction.”
A bright future
The Hercules Ultra represents Schlam’s unwavering commitment to pushing the boundaries of innovation. As the global leader in load and haul attachments, Schlam’s latest offering is set to transform the ultra-class haul truck segment, providing miners with the tools they need to drive productivity, enhance operational efficiency, and meet the growing demands of the industry.
Hercules Ultra truck beds are currently operating across the globe in large-scale mining operations.
With the Hercules Ultra already proving its value in operations around the world, it’s clear that Schlam is driving the next generation of mining truck solutions.
The future of ultra-class haul trucks is here, and with it, the future of mining productivity – powered by Schlam. AM
FROM THE COALFACE TO INNOVATION
TRUFLO PUMPS IS DRIVEN BY A SOLUTIONS-FOCUSED APPROACH THAT’S ABOUT “BUILDING LONG-TERM RELATIONSHIPS, NOT JUST TRANSACTIONS”.
In an industry where reliability, efficiency and cost-effectiveness are paramount, Truflo Pumping Systems is leading the way with a focus on expertise, innovation and providing the best solutions.
For Truflo Pumps national sales manager Martin Richardson, the journey from hands-on industry experience to sales leadership has been instrumental in shaping the company’s approach to pump solutions. His story is one of deep industry knowledge, earned through years spent travelling out to various mine sites rather sitting behind a desk.
That type of practical approach is fundamental to Truflo Pumps’ commitment to problem-solving over salesmanship.
“We aren’t looking for a quick sale. We are solutions-focused, and if that means telling a customer they already have a pump on-site that can do the job, we’ll do that,” Richardson told Australian Mining “It’s about building long-term relationships, not just transactions.”
This willingness to always do what’s best for the customer, even at the
incorrectly in what pump to purchase,” Richardson said. “You have to ensure it’s the right fit, even if it takes longer or it costs more upfront.”
With over 30 years of experience, the company understands that no two sites are the same, and each presents unique challenges that require customised system design.
The future of pump protection
One of Truflo Pumps’ most significant innovations is the AquaBoss asset protection system, an advanced pump control solution developed alongside hydraulic engineers, pump maintenance teams and mine site crews.
“AquaBoss isn’t just another control panel – it’s a game-changer for mining operations,” Richardson said. “We designed it based on customer pain points that existing solutions didn’t address.”
The system continuously monitors operational parameters, ensuring pumps operate within their designed performance range. It helps to extend equipment lifespan by offering dual
to proactive, using predictive analytics to identify potential issues before they become costly problems.
“By maintaining pumps within their ideal operating parameters, it significantly reduces failures and extends equipment life,” Richardson said. “That means huge savings in replacement and repair costs.”
One of the most user-friendly AquaBoss features is its traffic light system, where green indicates optimal operation, orange signals the pump is approaching its limits, and red triggers a shutdown to prevent damage.
“Even someone with no mechanical experience can operate it in minutes,” Richardson said. “It’s that simple.”
Truflo Pumps is continuing to develop AquaBoss, with plans to introduce smart pump technology that will allow the system to automatically adjust engine RPMs to maintain peak efficiency.
“It’s a complex project, but we have the right team in place to make it happen,” Richardson added.
Proudly Australian
“I think we’re pretty well the last of
higher here, but we have full control over our quality and production, and that makes a huge difference.”
Manufacturing locally allows Truflo to quickly respond to customer needs, a key advantage over relying on overseas suppliers with long lead times.
“We’re here in Australia and that means we can deliver parts quickly and support our customers directly,” Richardson said. “That’s something you don’t get when you’re waiting for overseas shipments.”
Truflo’s dedication to quality and innovation has driven interest from around the globe, with the company expanding its reach into Africa, Indonesia and the Philippines.
“We’ve got agents all over the world,” Richardson said. “In fact, we just had an order from Zambia come through this morning; that’s a testament to the reputation we’ve built.”
Expertise and trust
Beyond its products and services, Truflo Pumps fosters a company culture that values experience, innovation and customer relationships. Unlike traditional sales teams, Truflo Pumps’ business development managers (BDMs) come from engineering and mechanical backgrounds, providing them first-hand knowledge of the challenges faced by mine operators.
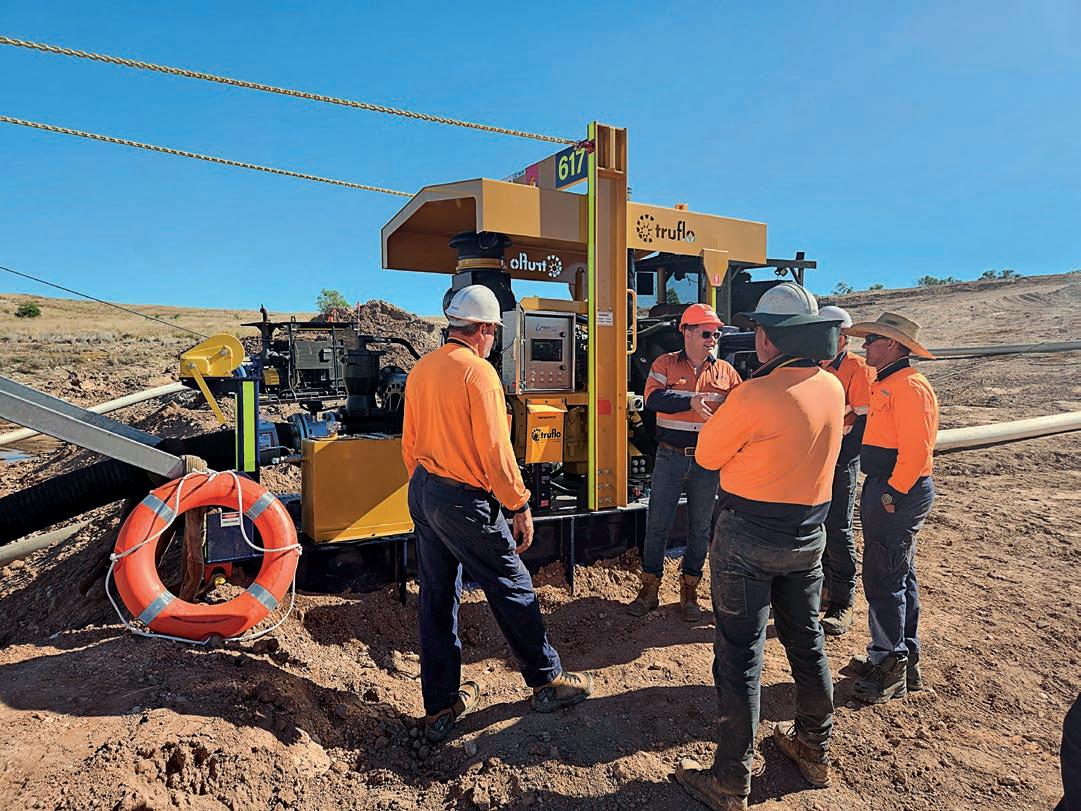
“Our BDMs aren’t just selling pumps,” Richardson said. “They’ve worked underground, repaired equipment and understand the realworld challenges of mining operations.
“That means they can speak the same language as our clients, offering expert advice rather than just reading from a sales brochure.”
Truflo also takes pride in its low rate of staff turnover.
“Many of our team members have been with us for over a decade,” Truflo marketing and sales assistant Martin Hygemann said.
“One of our guys told me the other day that he wants to stay here until he retires, which is almost unheard of
Looking to the future, the company is actively developing new technologies, refining its bespoke design approach, and expanding into international markets.
“Mining is evolving, and we’re evolving with it,” Richardson said.
“Our focus on quality, innovation and tailored solutions ensures that we remain a trusted partner for mining operations worldwide.” AM
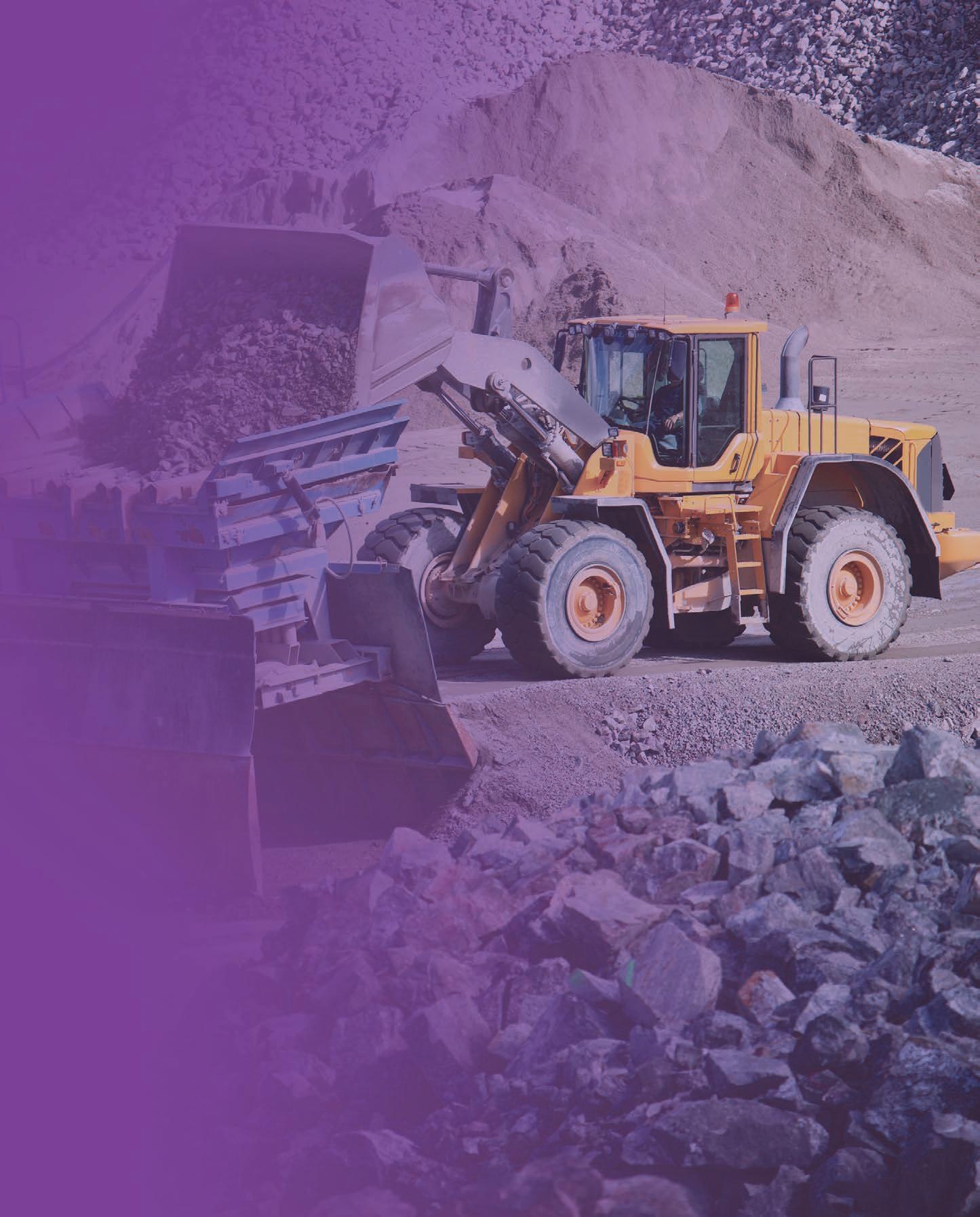
Dig Deeper into Your Data
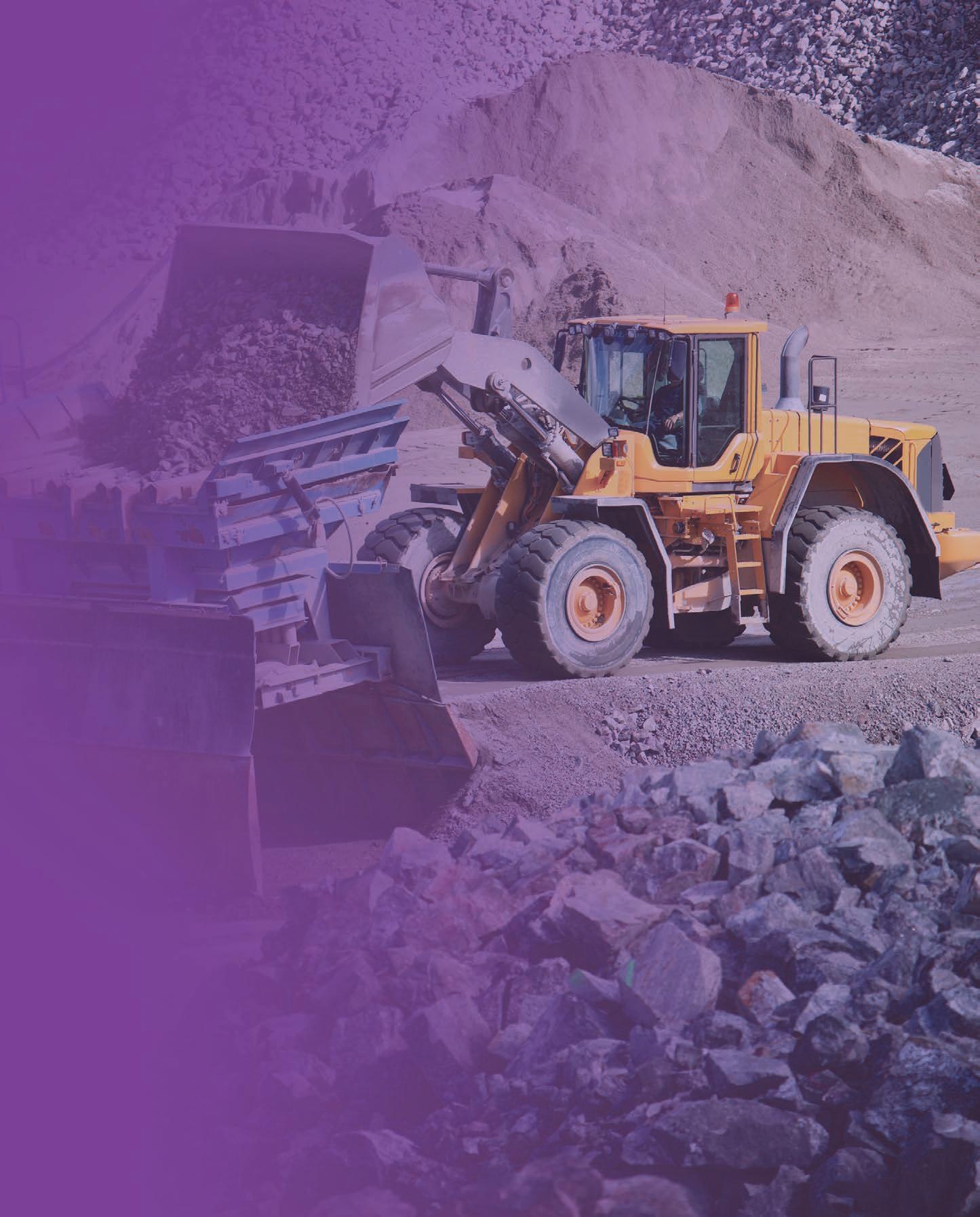
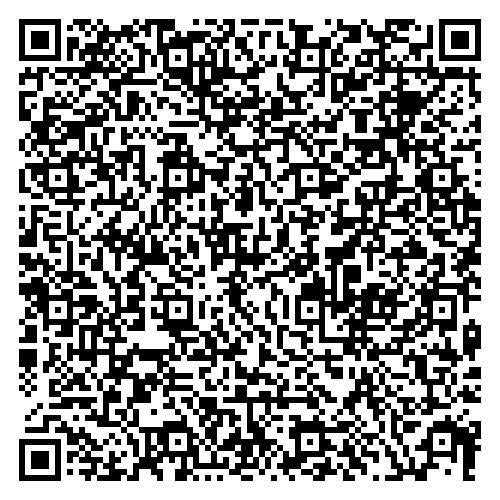
EXPANDING A 60-YEAR LEGACY
CONVEYOR COMPONENTS COMPANY IS MARKING ITS 60TH ANNIVERSARY BY EXPANDING ITS FOOTPRINT IN THE AUSTRALIAN MINING INDUSTRY.
Australian miners face high stakes every day as they navigate safety concerns and the risk of unplanned downtime.
This is particularly true in the conveying industry, where commodities are transported at rapid speeds, putting constant pressure on machine integrity and worker safety.
Enter Conveyor Components Company (CCC), an esteemed original equipment manufacturer (OEM) offering conveyor safety solutions that align with the industry’s unique operational needs.
“Expanding into Australia was the natural next step for us,” CCC business development support Austin Scheid told Australian Mining
“We’ve always prioritised customer relationships, and in the Australian market it’s about understanding what customers need to keep their operations running efficiently and safely.
“As we invest in growing our people and machinery, we’re trying to educate new markets of what we’re able to do.”
CCC’s customer-first approach is central to its success. Scheid discussed the importance of listening to customers and building connections based on trust and understanding.
“We sell on customer relationships, by getting to know the customers and their needs,” Scheid said.
“Whether it’s a big project or a small order, we treat everyone the same and
look at how our units can help them achieve their goals.”
By establishing open communication channels, CCC ensures customers feel supported, even across time zones.
“We make ourselves available when needed,” Scheid said. “We’re organised and ready to go so that customers are never waiting on us.”
At the heart of CCC’s offerings is the company’s patented Conveyor Safety System, which plays a pivotal role in reducing downtime and improving worker safety. The system includes emergency rope safety switches, belt misalignment controls, damage belt detection units, and a speed control switch to ensure operators remain in control of their conveyor.
The system’s robust construction and advanced sensing technology are designed to enable miners to detect potential hazards, such as belt misalignment or sudden speed variations, before they escalate into critical failures. This helps ensure compliance with industry standards and promotes a safer working environment for conveyor personnel.
While some overseas suppliers cannot guarantee the time of product delivery, CCC has ramped up its stocking capacity to enable same-day shipping.
“We’ve increased our stocking capacity to reduce downtime concerns for our customers,” Scheid said.
This quick turnaround helps CCC remain competitive and reliable, even when operating internationally.
The company has long embraced a customer-driven approach to innovation, incorporating feedback into its research and development (R&D) process.
This approach recently saw CCC make improvements to its magnetically coupled motion switch (MCM) called the MAG-NEAT-O, now a key component of its conveyor safety system.
The MAG-NEAT-O, which can be easily attached to the roller shaft of a conveyor, is a speed switch that can be programmed as an over-speed, underspeed or zero-speed device. A proximity sensor communicates pulses into an MSD controller, relaying signals to up to two different circuits.
CCC developed the MAG-NEAT-O based on customer feedback.
“If one customer has an idea, more than likely another customer is thinking it, too,” Scheid said.
“Listening to our customers has helped us refine our offerings and better meet the needs of miners.”
As sustainability becomes an increasingly important topic for miners, CCC is investing in new technologies to support these goals.
The company recently acquired a new CNC (computer numerical control) machine, which will double its manufacturing capacity and shorten lead times for urgent orders.
This investment not only supports faster production but also helps CCC operate more sustainably by optimising its manufacturing processes.
Looking back on CCC’s success over the past 60 years, Scheid emphasised teamwork as a key factor in the company’s longevity.
“It takes a lot more than just one person to make everything work,” Scheid said.
“Everyone shares the same goal of helping customers as quickly and efficiently as possible.
“We’ve got a lot of experience and a great team that’s passionate about growing the company and serving our customers.”
As CCC continues its Australian expansion, the company is optimistic about building stronger relationships and gaining a deeper understanding of the needs of the market.
Its focus on reliability, innovation, and quick service positions CCC well to become a key player in the Australian mining industry.
“Our expansion into Australia is about more than just entering a new market; it’s about bringing our decades of experience to help miners keep operations running smoothly,” Scheid said.
“We’re investing in our people, machinery, and customers to ensure long-term success.”
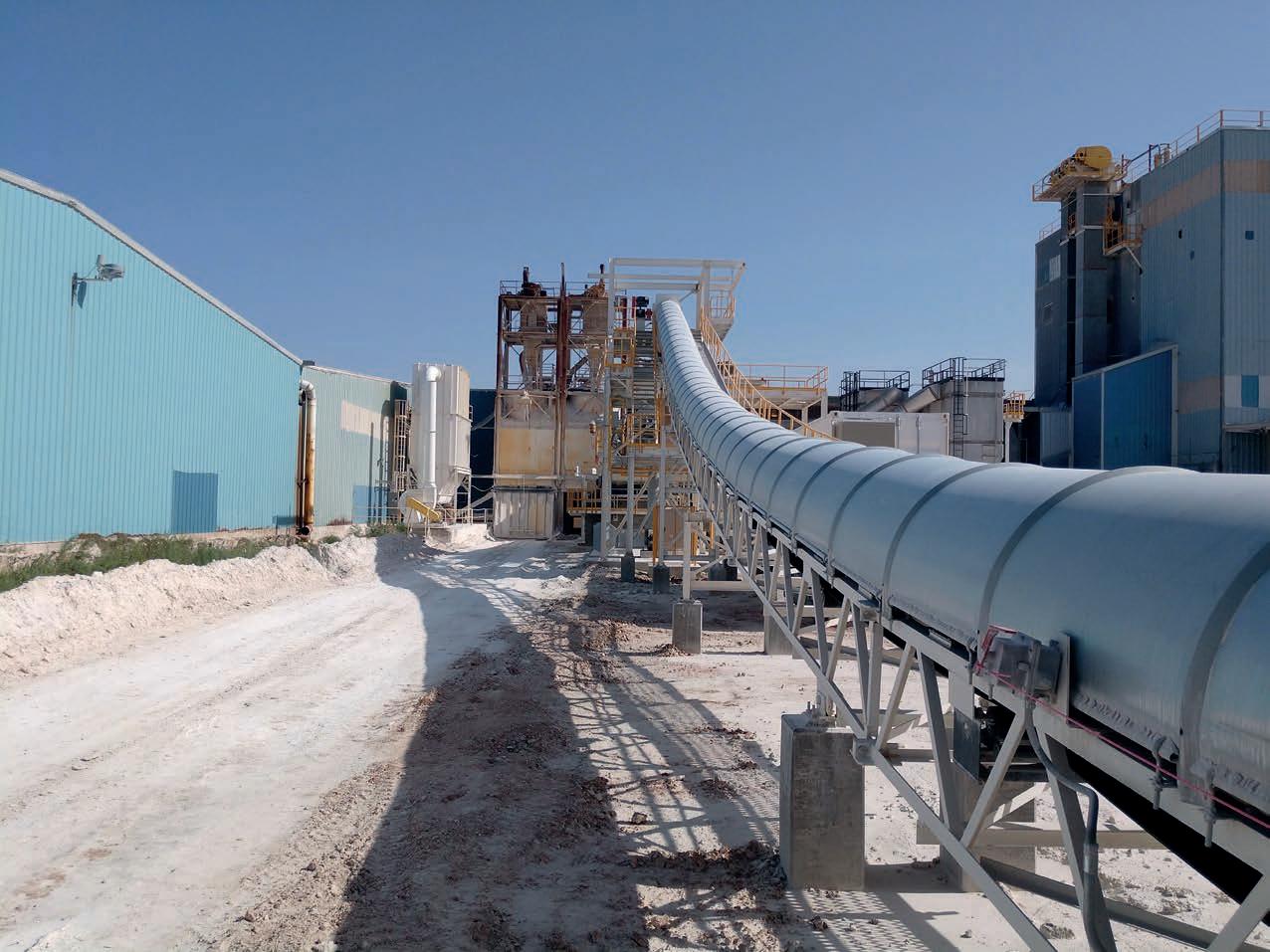
As it celebrates its 60th anniversary, CCC is well-prepared to meet the evolving demands of Australian miners and continue its legacy of innovation and service for decades to come. AM


Less Friction more progress
SAFE, SECURE AND ENVIRONMENTALLY FRIENDLY
KOMATSU’S DEDICATION TO PROVIDING SAFE AND ENVIRONMENTALLY FRIENDLY SITES WAS RECENTLY BOLSTERED BY TWO NEW CERTIFICATIONS.
Komatsu Australia has long been a staunch supporter of safety and environmental management.
The original equipment manufacturing (OEM) giant recently took this dedication a step further, achieving ISO 45001 and ISO 14001 certification, the internationally recognised standards for occupational health, safety and environmental management.
Komatsu executive general manager –safety and sustainability Henrietta Jukes said the rigorous standards have been designed to improve employee safety, reduce workplace risks and create better environmental outcomes.
“Komatsu Australia’s certification underscores its dedication to integrating best-practice management across its operations,” Jukes said.
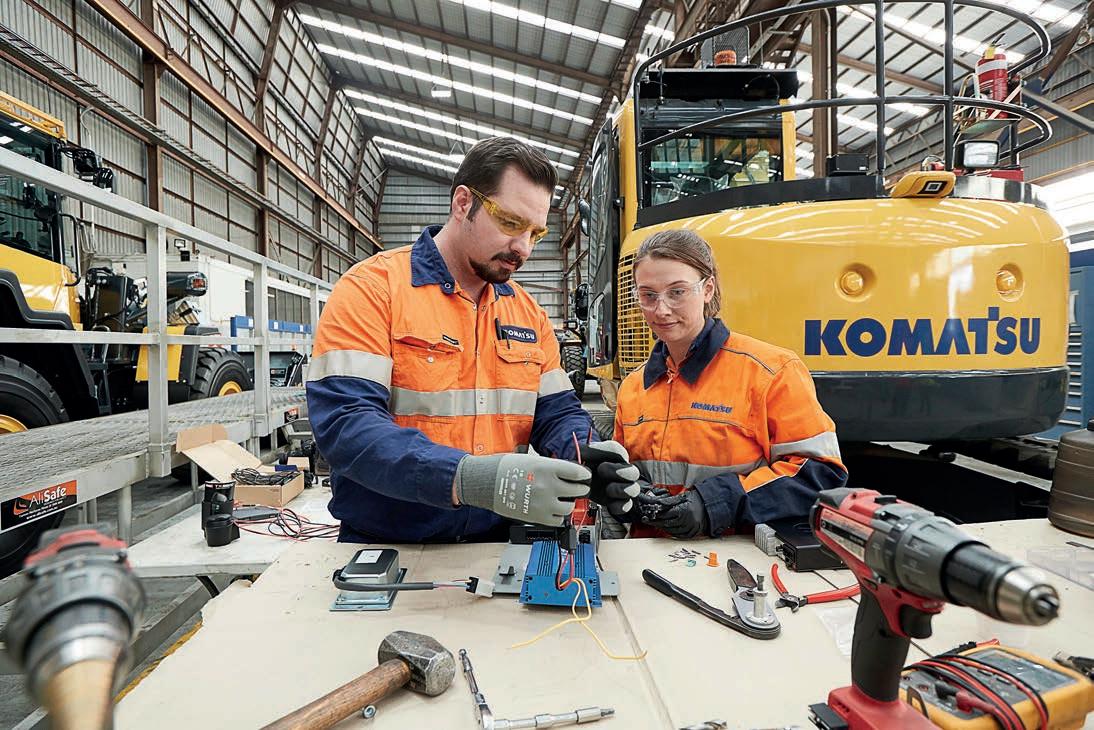
“This certification says to our staff and our communities that we are looking after your safety and the environment. And to our customers it says we are a business that is absolutely committed to best practice in every part of our operations.”
The certification process was an extensive one, involving audits across multiple Komatsu Oceania sites, including in Australia, New Zealand and New Caledonia.
The audits assessed the effectiveness of each site’s safety and environmental management systems, policies and procedures. A total of 22 sites were audited over a six-week period that saw independent assessors evaluate Komatsu’s commitment to identifying hazards, mitigating risks and fostering a culture of continuous improvement.
The auditing confirmed that Komatsu was already well aligned with the requirement of ISO 45001 prior to certification, highlighting the robustness of the company’s existing safety management framework.
“At Komatsu, safety is at the heart of everything we do,” Juke said. “Achieving both these accreditations is a testament to our team’s unwavering
commitment to continuous improvement in workplace health and safety and environmental management.
“This milestone reflects our proactive approach to identifying and mitigating risks while fostering a culture of safety and sound environmental practices across all levels of our organisation.”
Jukes said that while the management systems already in place adhered to the standards’ principles, actually achieving the certification represents a major highlight for Komatsu.
“We appointed a national health, safety, security, and environmental (HSSE) assurance and systems manager to oversee the process; the organisation made a real commitment to doing this,” Jukes said.
“We did a gap analysis first, then we reviewed all our policies, our procedures and went through a process of updating 180 or so procedures to align them to legislation, align them to state requirements, and then also align them to best practice, most importantly.”
The environmental audit was conducted by different auditors, in parallel with the safety audits.
“We have very few environmental incidents but there’s a lot of new initiatives that we’re starting from a sustainability perspective, especially
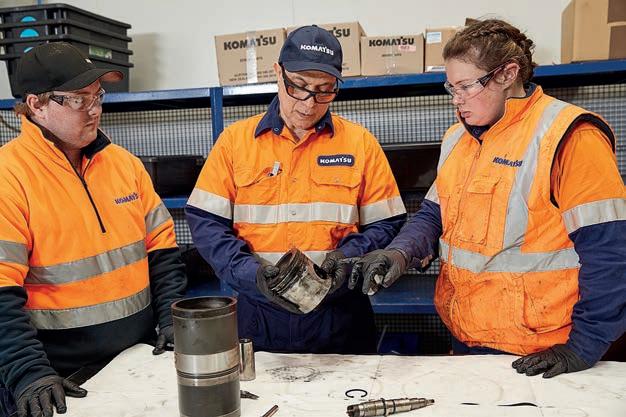
AUDITING CONFIRMED THAT KOMATSU WAS ALREADY ALIGNED WITH THE REQUIREMENT OF ISO 45001 PRIOR TO CERTIFICATION.
around waste, because of this very rigorous management system,” Jukes said.
Helen Goudy, the manager who drove the process, said the achievement of certification is the result of dedicated collaboration across the business.
“The audit process was incredibly thorough, with assessors closely examining our procedures, risk assessments and employee engagement in initiatives,” Goudy said. “We had the option just to go for head office
certification, but we didn’t do that. We wanted certifications for all of our branches.
“Feedback from the audit confirmed that our systems not only meet but exceed the standard requirements.
“We are very proud of this milestone, which reinforces our responsibility to provide a safe and supportive workplace for all, with a firm focus on sustainability and environmental responsibility.” AM
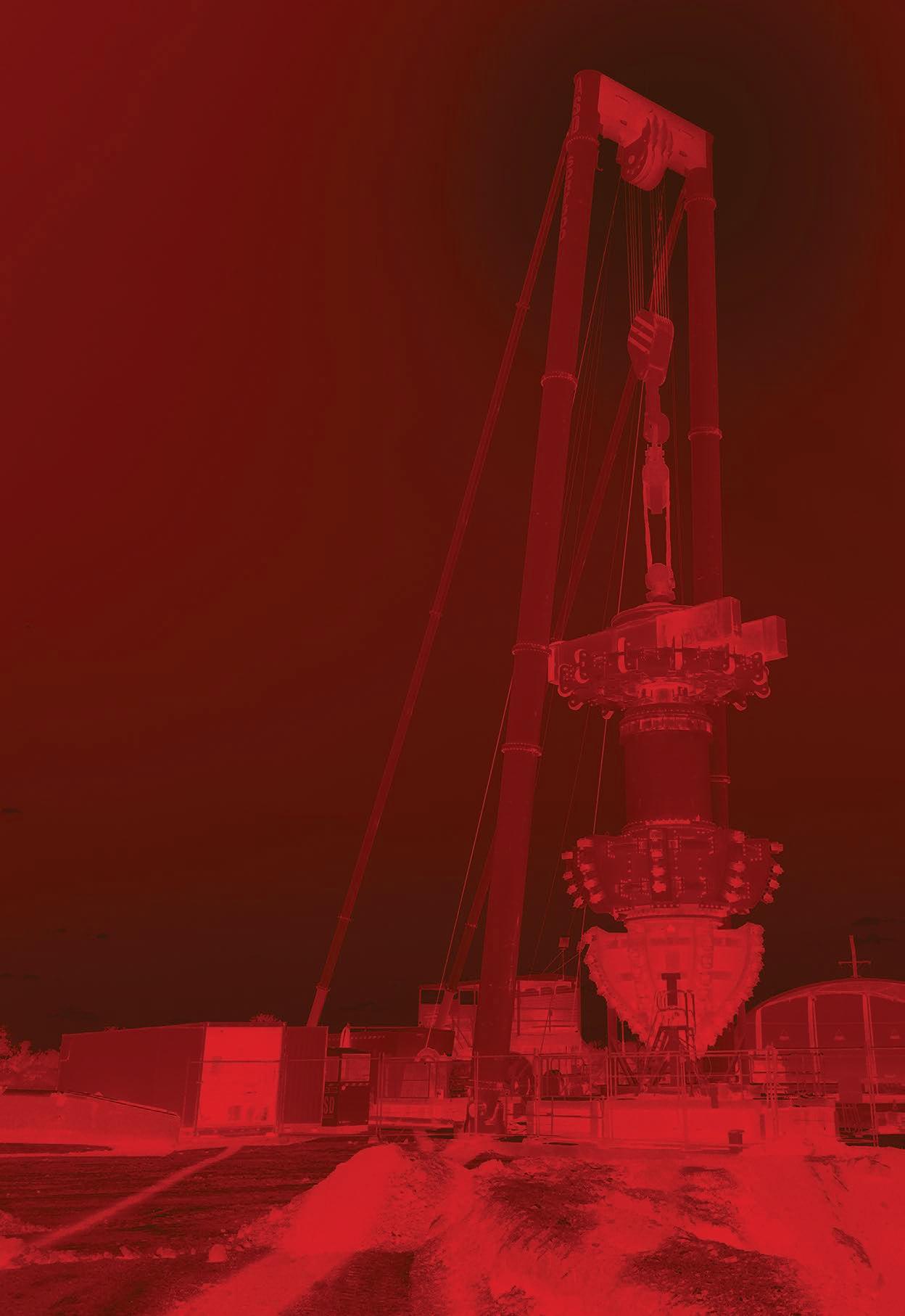
AT THE HEART OF AIMEX
MAGNETITE MINES MANAGING DIRECTOR TIM DOBSON DISCUSSES WHAT THE COMPANY WILL BE SHOWCASING AT ASIA-PACIFIC’S INTERNATIONAL MINING EXHIBITION IN 2025.
Asia-Pacific’s International Mining Exhibition (AIMEX) is set to return in 2025, highlighting the latest trends and developments by bringing local and international mining suppliers and industry professionals under one roof at the Adelaide Showground.
Making its debut this year is AIMEX’s Mining Pavilion, which is designed to act as an epicentre for industry innovation on the exhibition floor.
unparalleled exposure to thousands of mining delegates from Australia and around the world,” Prime Creative Media marketing manager –mining events Rebecca Todesco told Australian Mining.
This year’s Mining Pavilion has an impressive line-up of producers and contractors set to showcase their initiatives.
One such participant will be
connections between the industry’s key players and organisations, providing
“We’ll have an increasing presence in the state, employing South Australians for many decades to come,” Dobson told Australian Mining
“The amount of equipment and people we’re going to need to build and run this operation will be quite significant, so interfacing with the mining services industry will be essential for the success of the project.”
During Razorback’s construction
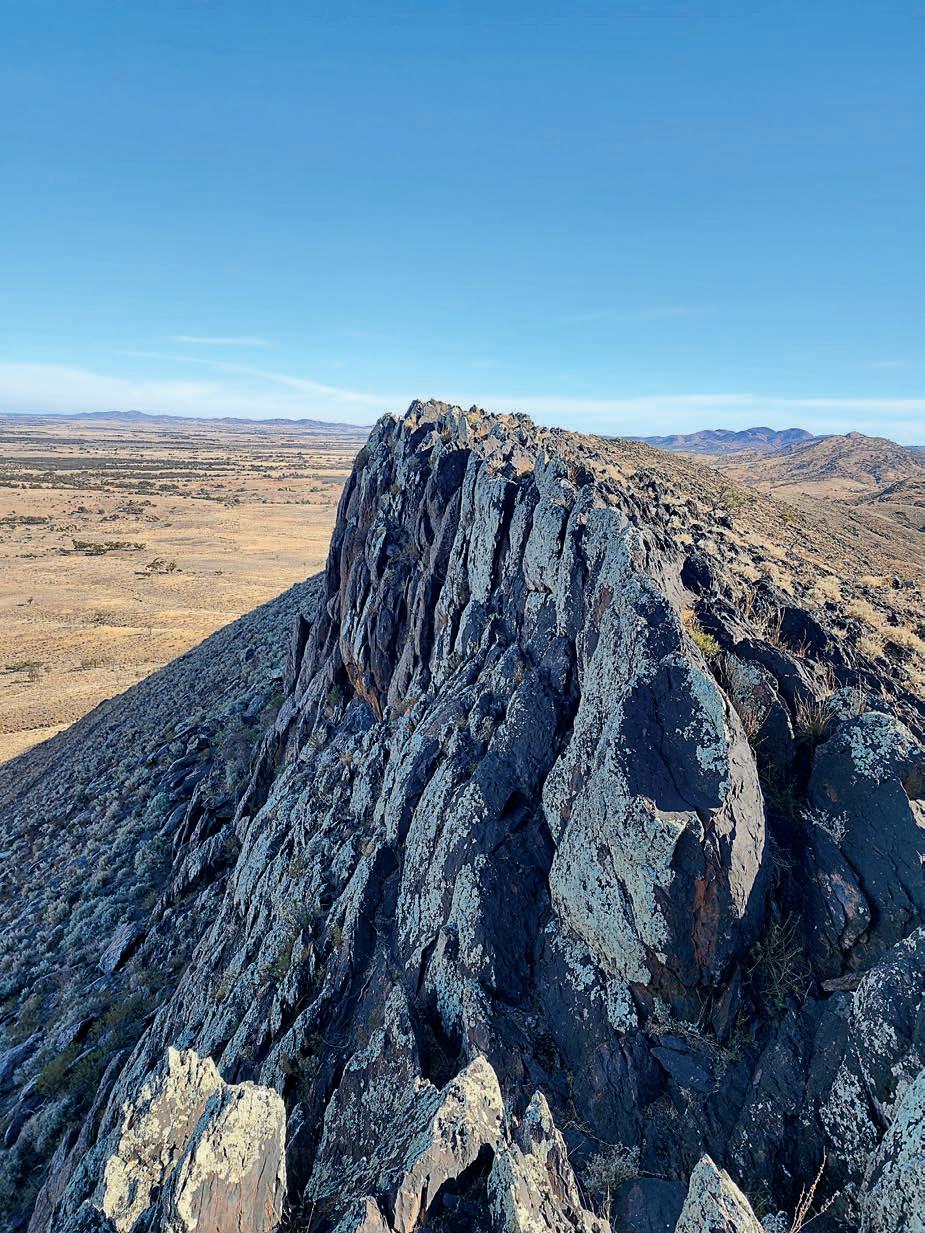
how the local community can participate in Razorback’s growth.
“We see South Australia’s stature as a mining state growing, and by having AIMEX there, our presence at the Mining Pavilion will be timely,” Dobson said.
Dobson will participate in the AIMEX conference program, shedding light on Razorback’s role in decarbonising the steelmaking process through green metals such as magnetite.
“South Australia’s magnetite production potential is significant,” Dobson said.
“We’ve been studying, interfacing and collaborating with industry partners on the steel industry’s transition to green steel. Green iron will be produced without using fossil fuels and sought after by our major trading partners.
“At AIMEX, we’ll help educate and provide information about this massive opportunity for the state in both economic growth and future prosperity.”
Magnetite Mines is part of Green Iron SA, a consortium designed to accelerate South Australia’s green iron industry. Other members include construction and engineering company GHD, freight rail transport company Aurizon, and Flinders Port, which operates seven ports across the state.
“We’ll be able to showcase what the Green Iron SA consortium brings to the table,” Dobson said.
“We made a submission to the South Australian Government last year, which outlined how a green iron industry could be brought to life through Razorback and how Port Pirie can be evolved into a new green iron production hub. That’s another element we’ll be showcasing at AIMEX.”
The Federal Government’s recently announced $1 billion Green Iron Fund to support the evolution of this new industry will also be at the forefront of discussions at AIMEX.
“Events like AIMEX bring together a community of like-minded people to effectively exchange and share ideas,” Dobson said.
“We’ve got several messages to communicate, and being able to do that face-to-face with people at the Mining Pavilion provides a great opportunity to inform the industry and hopefully build new relationships.” AM
AIMEX 2025 will be held at Adelaide Showground from September 23–25. To take part in the event, visit aimex.com. au/getinvolved


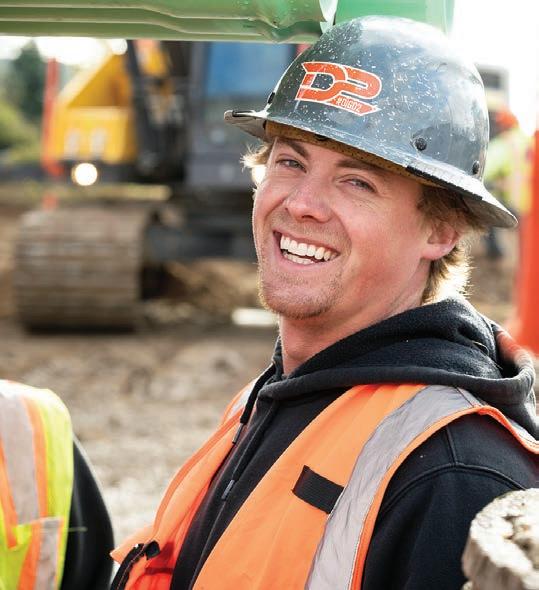
ASIA-PACIFIC’S
MINING EXHIBITION IS MOVING!
As Australia’s longest running mining show, Asia-Pacific’s International Mining Exhibition (AIMEX) has a long, established history of showcasing and supporting the latest trends and developments in the industry.
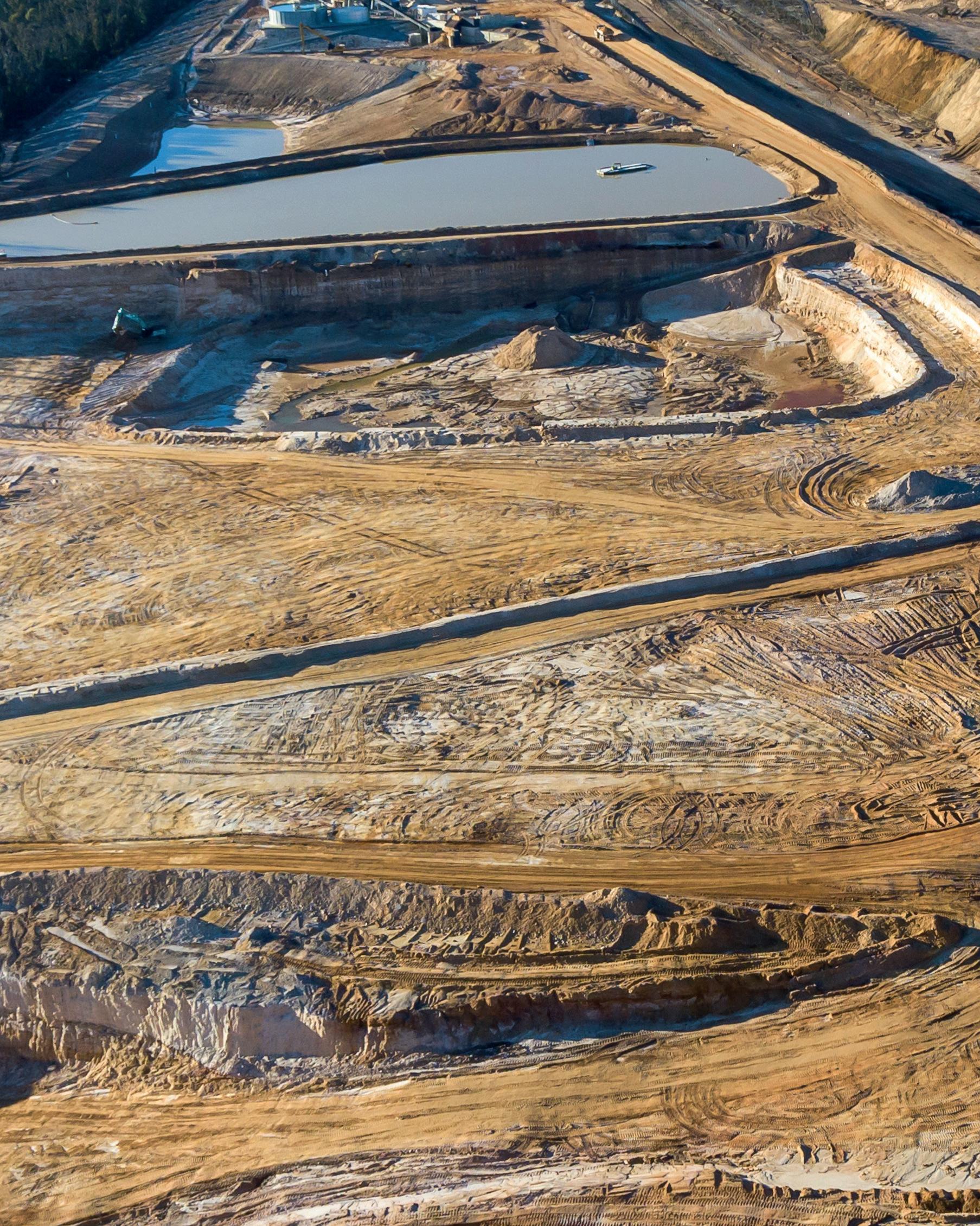
SEPTEMBER 2025 23-25
AIMEX is relocating and will call South Australia home for the next 10 years, following market feedback and strong support from the local government and key mining players.
The move marks an exciting new chapter for the event and the region’s resource sector, with the state leading the way in future-focused mining.
AIMEX offers unparalleled opportunities to connect with Australia’s largest community of mining suppliers and professionals in an environment that stimulates innovation and collaboration.
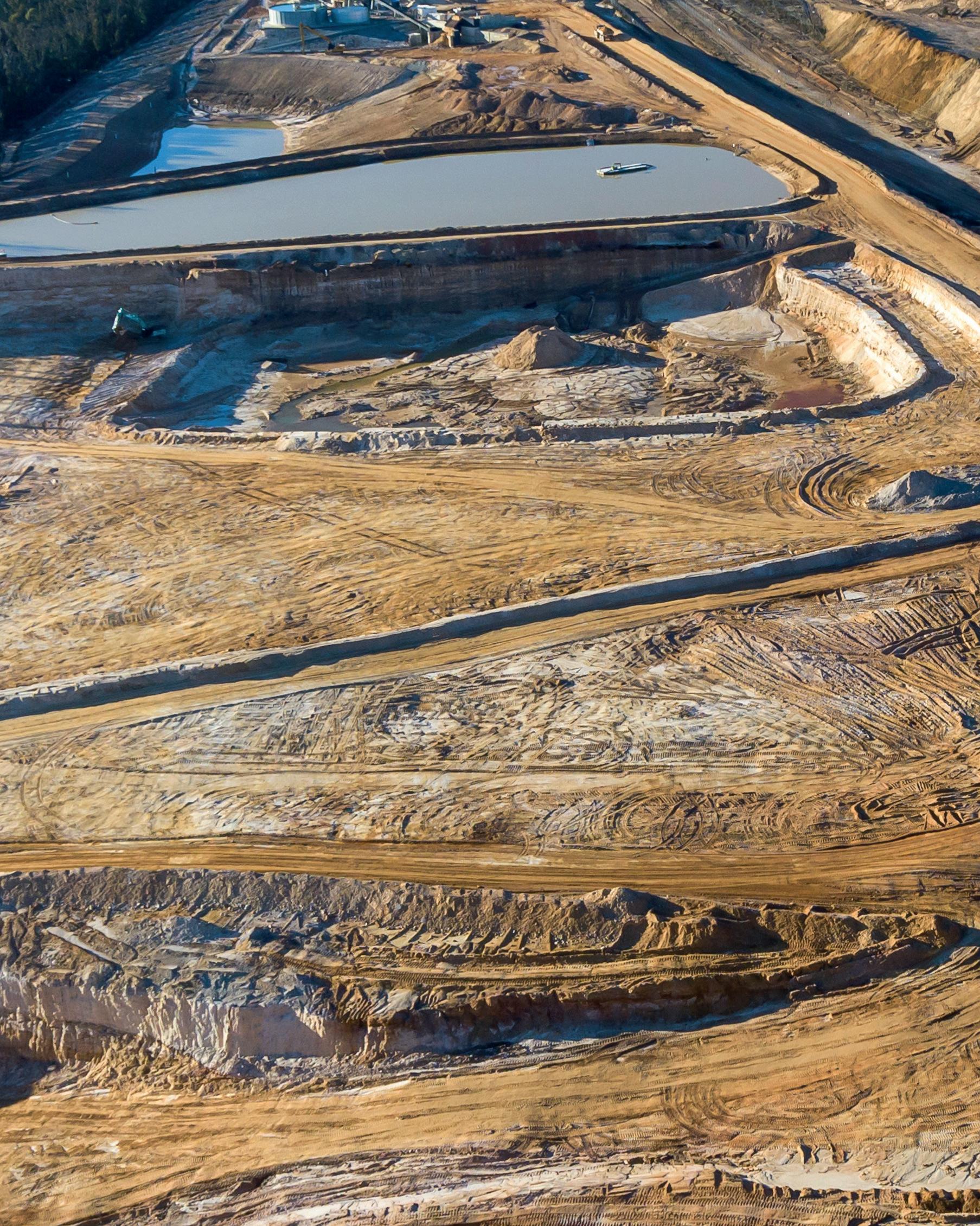
STRENGTHENING PARTNERSHIPS AT WA MINING 2025
DENVER TECHNOLOGY SEES THE WA MINING CONFERENCE AND EXHIBITION AS THE PERFECT OPPORTUNITY TO BUILD CLIENT RELATIONSHIPS AND SHOWCASE ITS PIT-TO-PORT SOLUTIONS.
Denver Technology is returning as a sponsor of the WA Mining Conference & Exhibition (WA Mining) in 2025, leveraging its deep expertise in asset-intensive industries to engage with new and existing industry players.
Denver Technology general manager – business development and customer success, Matthew Clayton, recently discussed the company’s involvement and goals for the event.
“We’ve been around since 1989, but much of our growth has been through word of mouth,” Clayton told Australian Mining. “Sponsoring the WA Mining Conference has helped us boost our branding and market awareness.”
Denver Technology hopes to boost its visibility in mining and oil and gas – its two core sectors – through the event, while also strengthening industry connections.
The sponsorship plays a key role in Denver Technology’s broader strategic goals. The company, which specialises in technology consulting, provides solutions from pit to port, supporting feasibility studies, operations, care and maintenance, and decommissioning.
“We provide services across every stage of a mine’s life cycle, understanding the challenges at each point and adding value where needed,” Clayton said.
Clayton said conferences such as WA Mining provide the perfect platform for Denver Technology to build client relationships and explain their products in detail.
“Having a stand allows us to connect with people we may not typically have direct access to – both potential clients and industry peers,” he said.
“It helps foster partnerships we may not have previously considered and allows us to gain insight into industry challenges.”
Denver Technology’s client base is extensive, covering key mining regions such as Western Australia and Queensland.
In addition to its local presence, the company has extended its reach into North America, Europe, and Africa, developing partnerships with global organisations.
The WA Mining Conference offers Denver Technology a platform to further
build on these collaborations while exploring new opportunities.
“The conference allows us to engage with industry professionals on different levels,” Clayton said. “It’s not just about meeting prospective clients – it’s about having conversations with peers that can lead to mutually beneficial partnerships.”
When WA Mining Conference & Exhibition returns to Perth in October, the event will leverage its strategic location to bring together key players from across the WA and broader Australian mining industries.
The event’s collaborative environment creates opportunities to explore trends, share knowledge, and stay ahead of technological advancements.
A highlight of Denver Technology’s booth this year will be its pit-to-port life-cycle diagram, which proved to be a popular visual aid at last year’s event.
“It’s a great way to illustrate how we support different mine life stages,” Clayton said. “The diagram details Denver Technology’s role at each stage
highlighting the company’s ability to provide targeted solutions throughout the entire life cycle.
“It’s important for us to show clients that we understand their challenges and can offer relevant solutions no matter where they are in the mining process,” Clayton said.
As Denver Technology evolves, the company is eager to further expand awareness of its services, particularly in Western Australia’s resourcerich landscape.
“Western Australia is central to our operations,” Clayton said. “The WA
navigate complex challenges make it a valuable partner for mining companies looking to optimise their operations.
“We’re not just here for the event –we’re here to foster lasting relationships that add value to the industry,” Clayton said. “That’s what we’re all about.”
With WA Mining 2025 just around the corner, Denver Technology is set to make a significant impact with its tailored solutions, deep industry knowledge and collaborative approach.
Visitors to the booth can expect valuable insights into Denver Technology’s innovative solutions
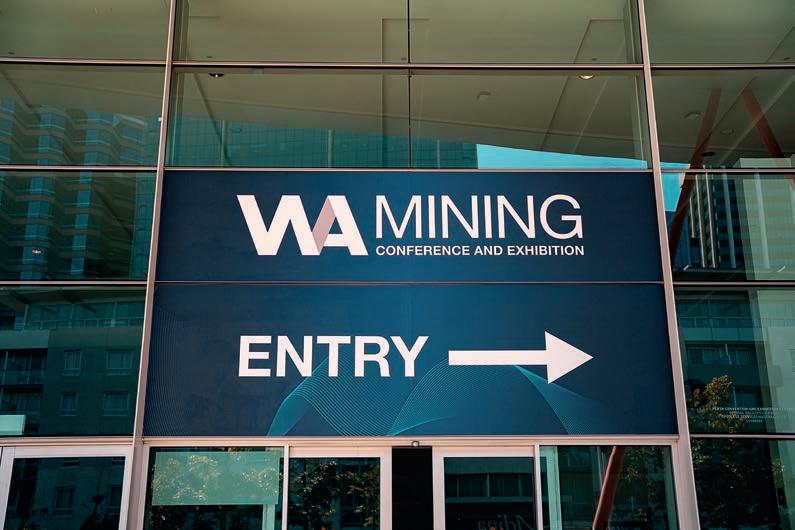
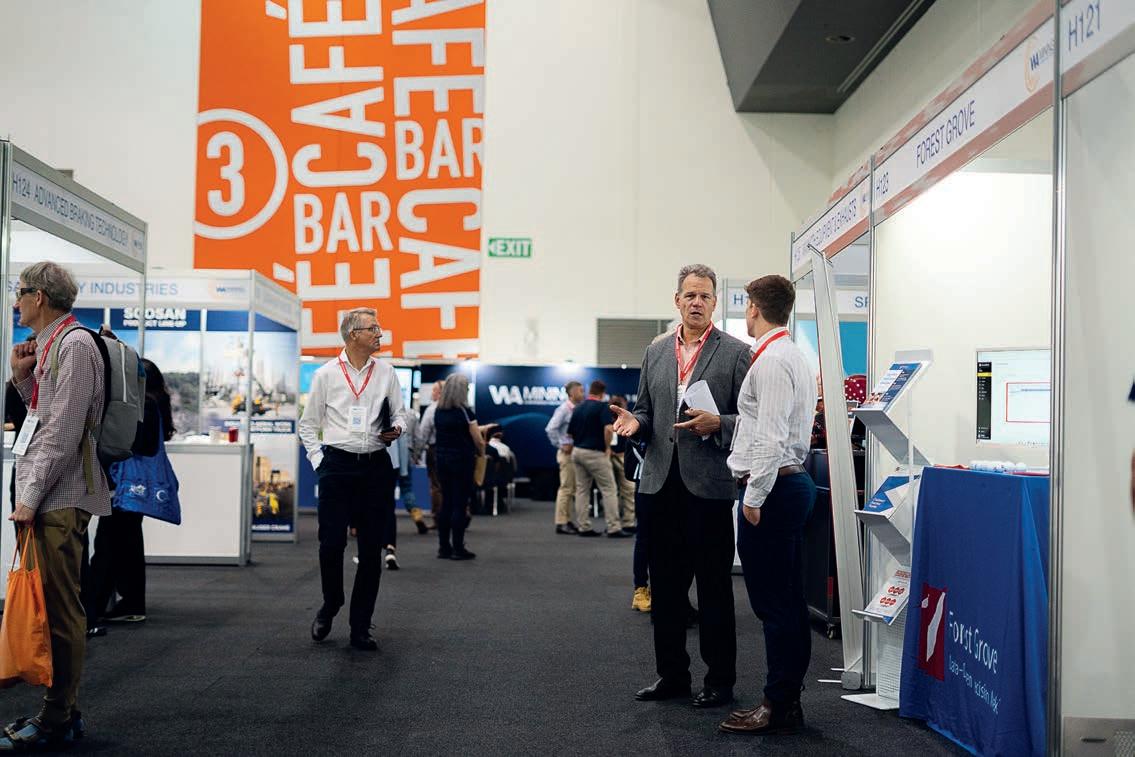
AN EVENT LIKE NO OTHER
THE 2025 PNG EXPO IS FAST APPROACHING, AND AUSTMINE IS ENCOURAGING METS COMPANIES TO GET INVOLVED.
The 2025 PNG Industrial and Mining Resources Exhibition and Conference (PNG Expo) is right on our doorstep, and the entire mining industry is buzzing with excitement.
With industry trailblazers like Metso, Blackwoods, Sandvik, Draeger, Lincom, the Mineral Resources Authority and Putzmeister already locking in their involvement, this is an event the sector cannot afford to miss.
Key industry association for the Australian mining equipment, technology and services (METS) sector, Austmine, has thrown its support behind the PNG Expo once again, with manager – international projects Sheldon Varcoe saying that anyone involved in the PNG mining value chain would gain value from attending the event.
“There are substantial opportunities to deepen collaboration across the Australian and PNG mining ecosystems to support safe, sustainable and productive operations, and the PNG Expo showcases the latest solutions that will usher in this change,” Varcoe said in a statement.
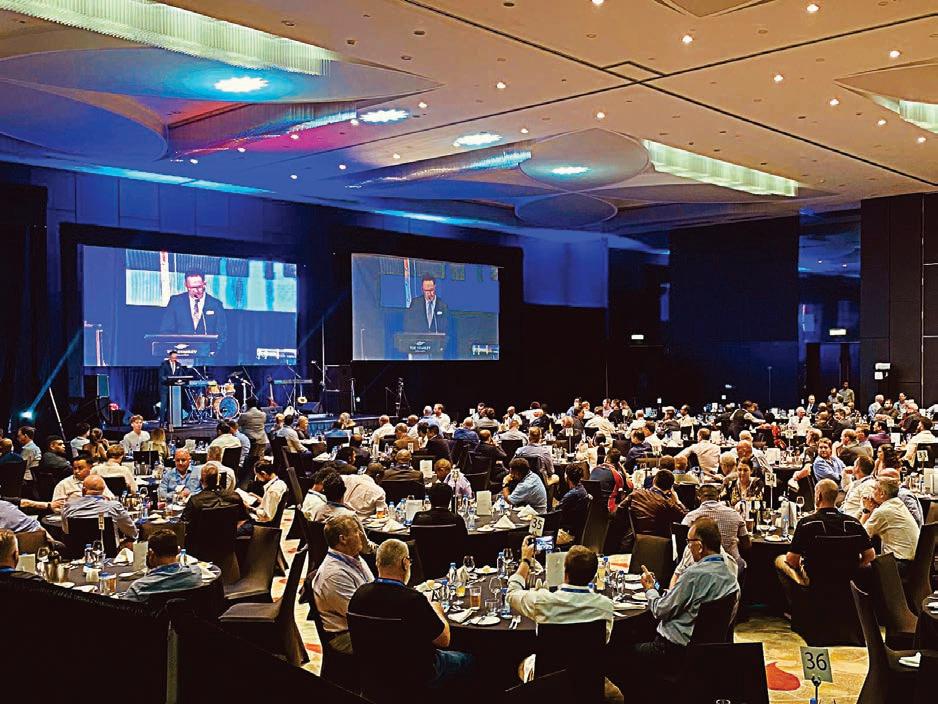
products and services being utilised in PNG, as well as the chance to develop new partnerships with potential distributors and representatives working in-market.
“These events provide an opportunity to highlight the latest trends and technological advancements in the PNG mining industry,” he said. “PNG Expo allows key stakeholders to come together
resources sector and its communities.”
The 2025 PNG Expo builds off the successful event from 2024.
On top of a curated exhibition floor and an informative speaker program, the PNG Expo offers a suite of networking opportunities to help delegates get the most out of their time in Port Moresby and maximise their exhibition experience.
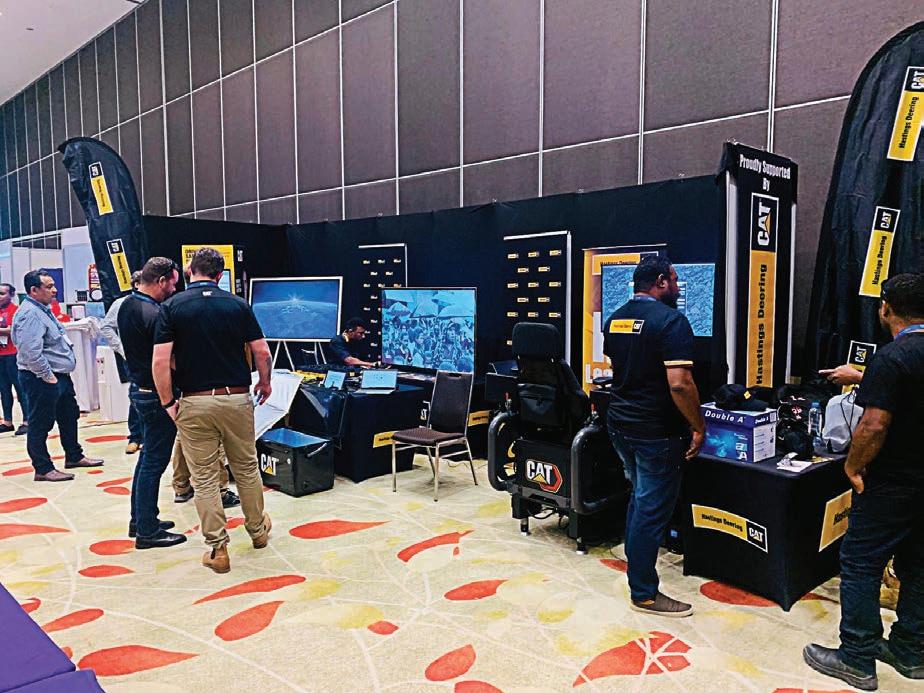
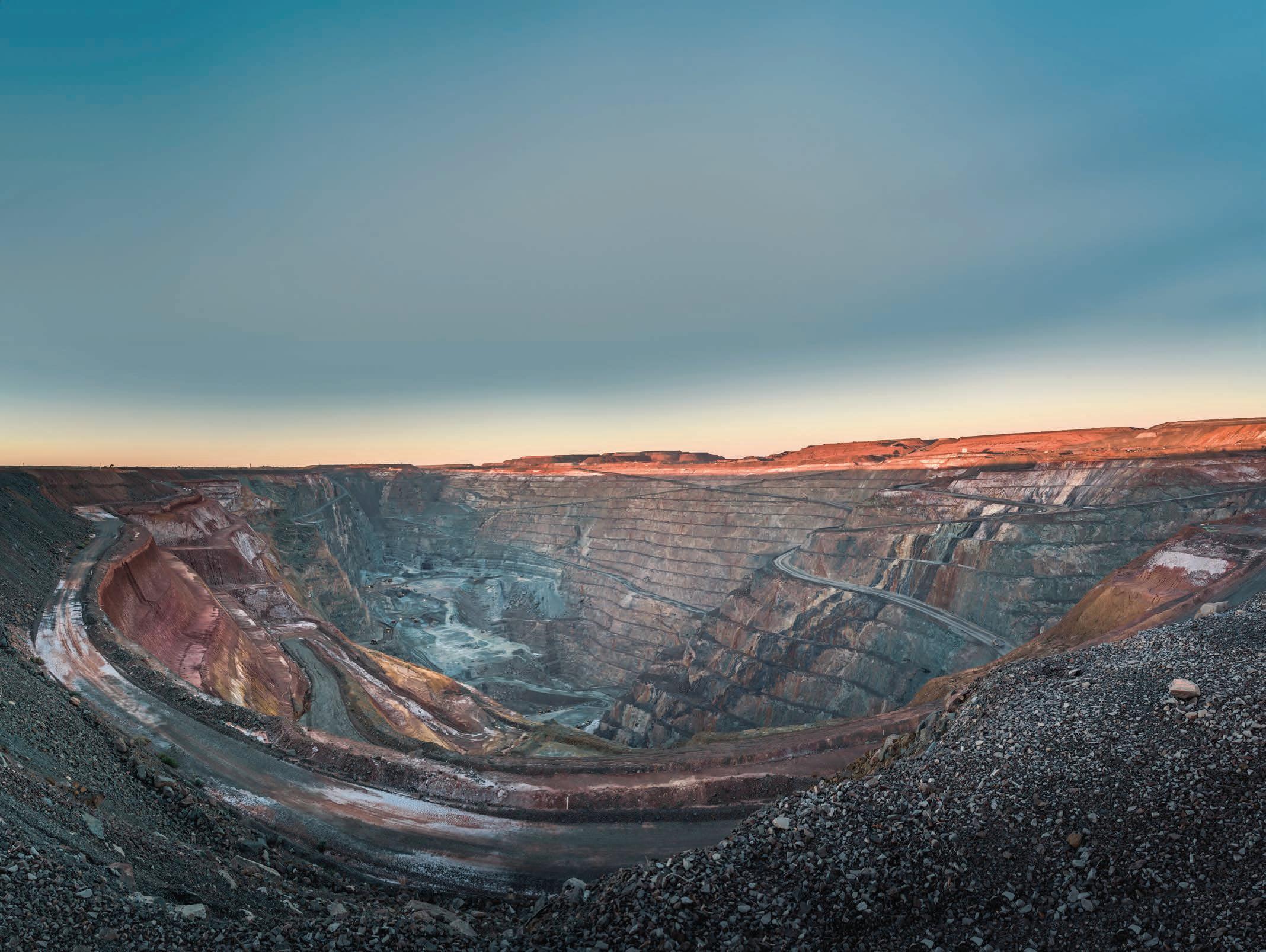
“It offers a platform for businesses to gain insights into market trends, understand industry needs, and explore innovative solutions. It is an opportunity to share expertise, demonstrate high-quality solutions, and support other businesses in achieving their goals.”
The PNG Expo will be held in Port Moresby from July 2–3. To take part in the event, visit pngexpo.com/get-involved


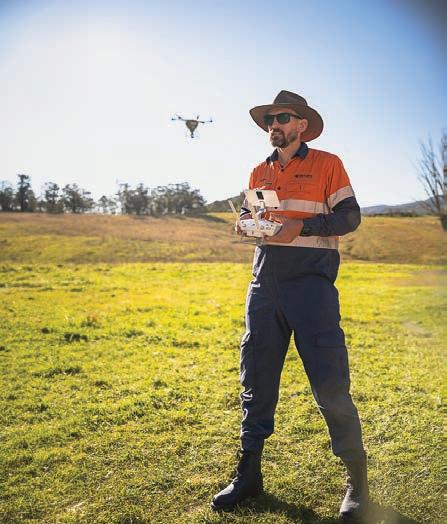
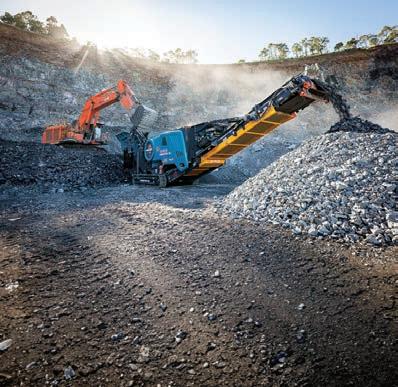
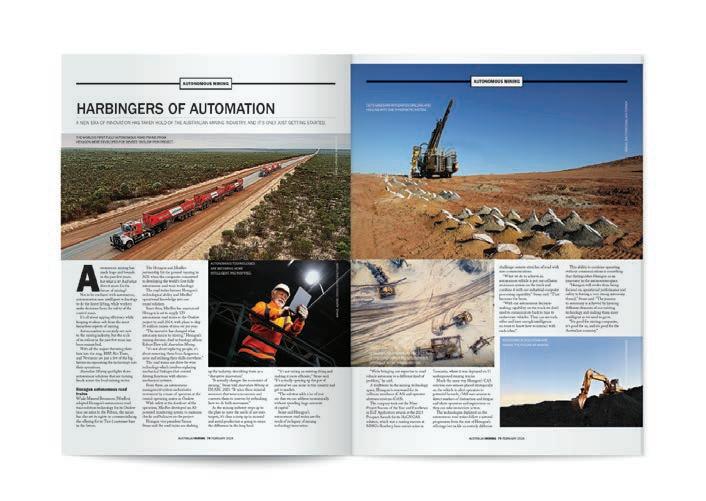
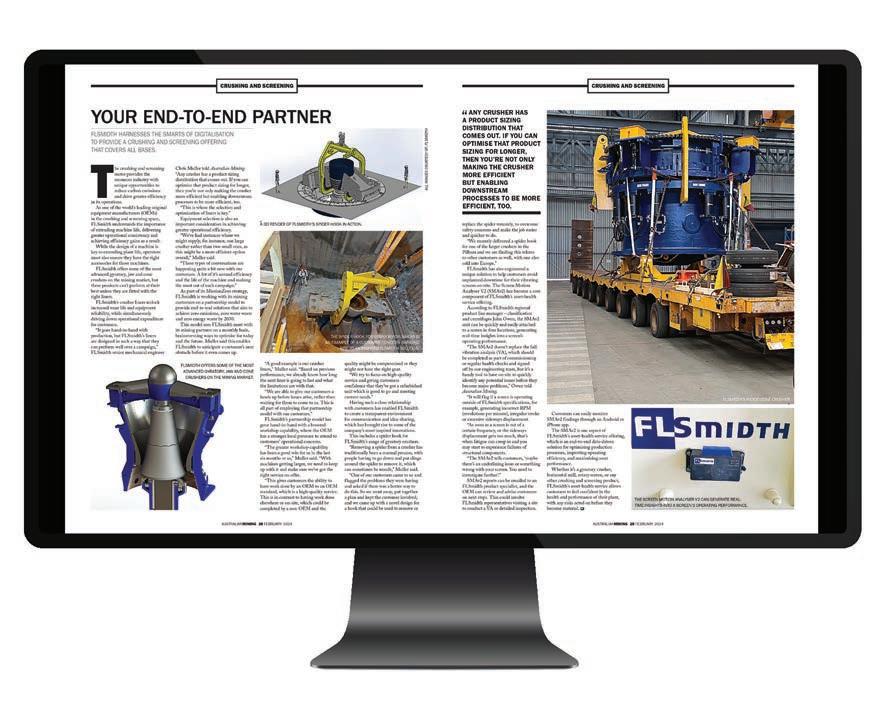
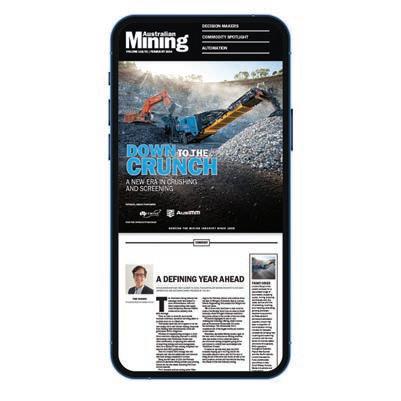
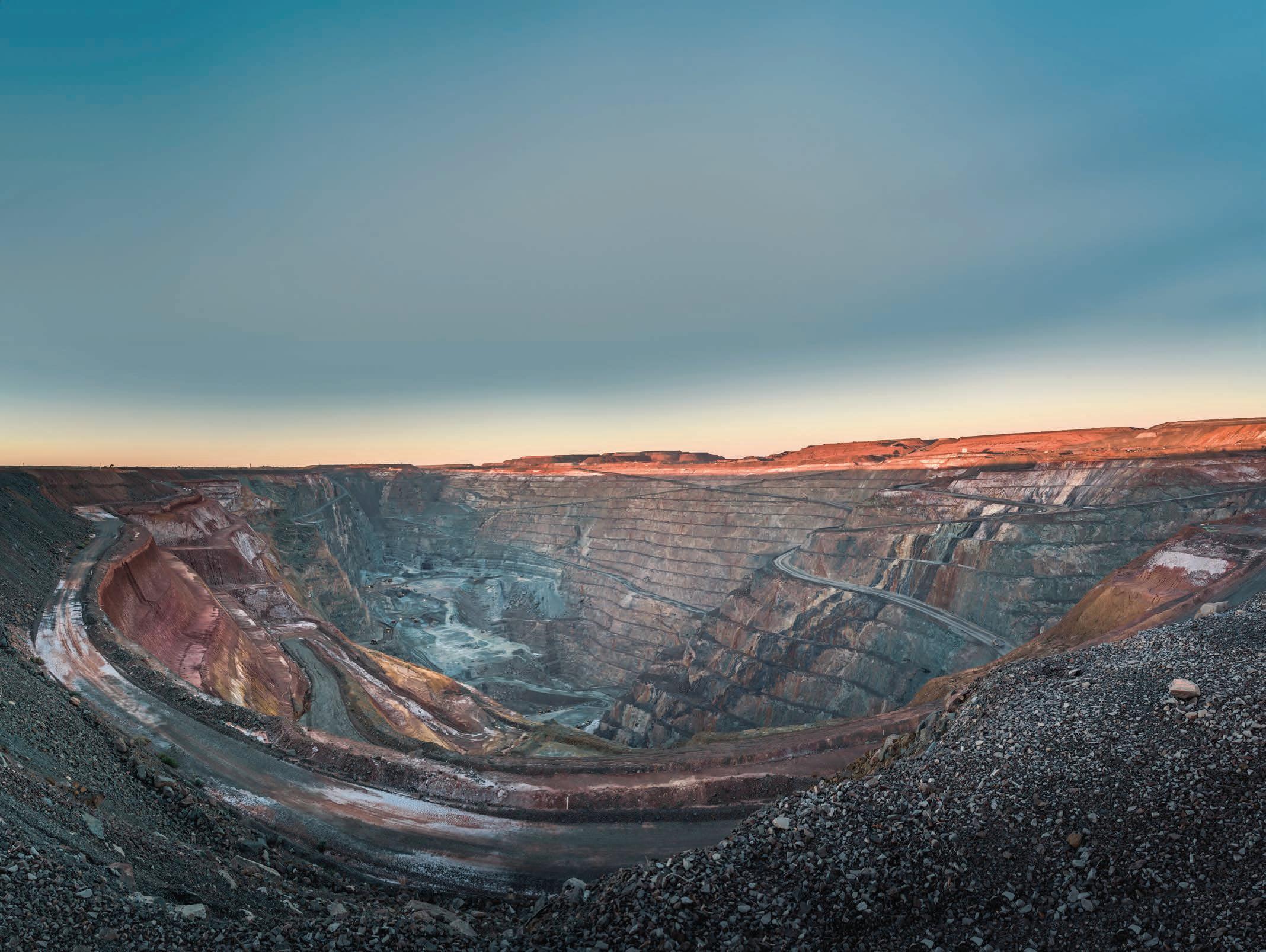
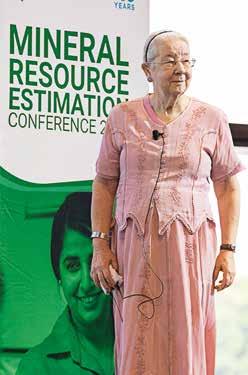
Dr Isobel Clark is a mining industry pioneer.
“I finished my degrees at the end of the 1960s, and in those days women could not be engineers,”
Clark told Australian Mining.
“Even though I went to an engineering university, I thought I was going to be a scientist.
MASTER OF THE CRAFT
THE GLOBAL MINING INDUSTRY IS SET TO CONVERGE IN PERTH FOR AUSIMM’S MINERAL RESOURCE ESTIMATION CONFERENCE IN MAY.
“However, I ended up working for the civil service.”
During her tenure with the civil service, Clark saw an advertisement to teach statistics and computational methods at the Royal School of Mines at Imperial College, London. The rest, as they say, is history.
“My supervisor got a call from a mine in Cornwall asking someone to come and help them match their production with their predictions,” Clark said. “I was about six months into the role. I spent three weeks at the Cornwall mine and that was it; I was hooked.”
Clark’s numerous roles in the global mining industry took off from there. She has worked across most of the mining value chain but now sees her role as an interpreter, connecting the ideas of geologists and their deposit characterisations with her other mining colleagues.
With AusIMM’s Mineral Resource Estimation Conference (MREC) just around the corner, Clark will be a valuable part of delivering the conference program as a committee member.
MREC 2025 is expected to bring over 500 mining professionals to Perth
from May 6–7, showcasing leading best practice, case studies and research on mineral resource estimation.
“The whole structure of MREC 2025 is so different from anything I’m used to, and I do four to five global conference a year,” Clark said.
“The concept of having a conference dedicated to mineral resourcing is incredibly exciting, and it’s not just an academic conference. There’s a practical aspect to the event as well to explore new mineral resourcing methods.”
An original idea coming out of MREC 2025 is the Parker Challenge. Sponsored by Barrick Gold, the Parker Challenge gives mineral resource estimators the opportunity to create a classified model from the same base dataset.
The 2025 Parker Challenge will focus on orientation and getting the directions of continuity right, emphasising critical thinking and selectivity.
Add to that the lively panel discussions, interesting keynote speakers and informative abstracts and papers and you have a recipe for a great conference.
“The panel discussions are always a highlight, especially if there’s lots of audience participation,” Clark said.
“MREC 2023 had a lot of audience participation, so I’ll be looking forward to seeing the same this year.
“There’s also some really exciting papers that I’m keen to learn more about, some of them with titles I don’t even understand. I always used to say to my graduate students that if I understand what you’re doing then it’s not a PhD.”
While MREC 2025 will take place in Perth, the conference is a truly international one, with most keynote speakers coming from overseas.
Clark believes the international nature of the event is what makes it a standout conference.
“Australia has an incredibly wide mining industry but it needs to work with the international sector to move forward,” she said.
“The mineral resource estimation sector is multi-disciplinary and MREC 2025 has room for everyone, so we’re encouraging everyone to attend to help the industry move forward into the next 50 years and beyond.” AM
AusIMM’s Mineral Resource Estimation Conference will be held in Perth from May 6–7.
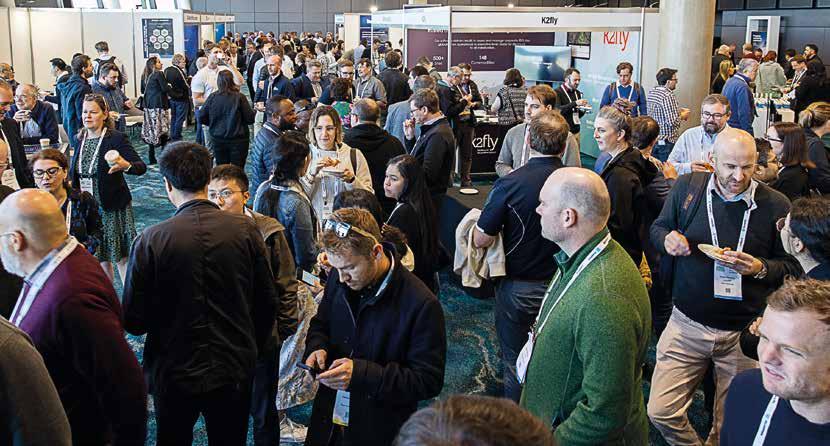
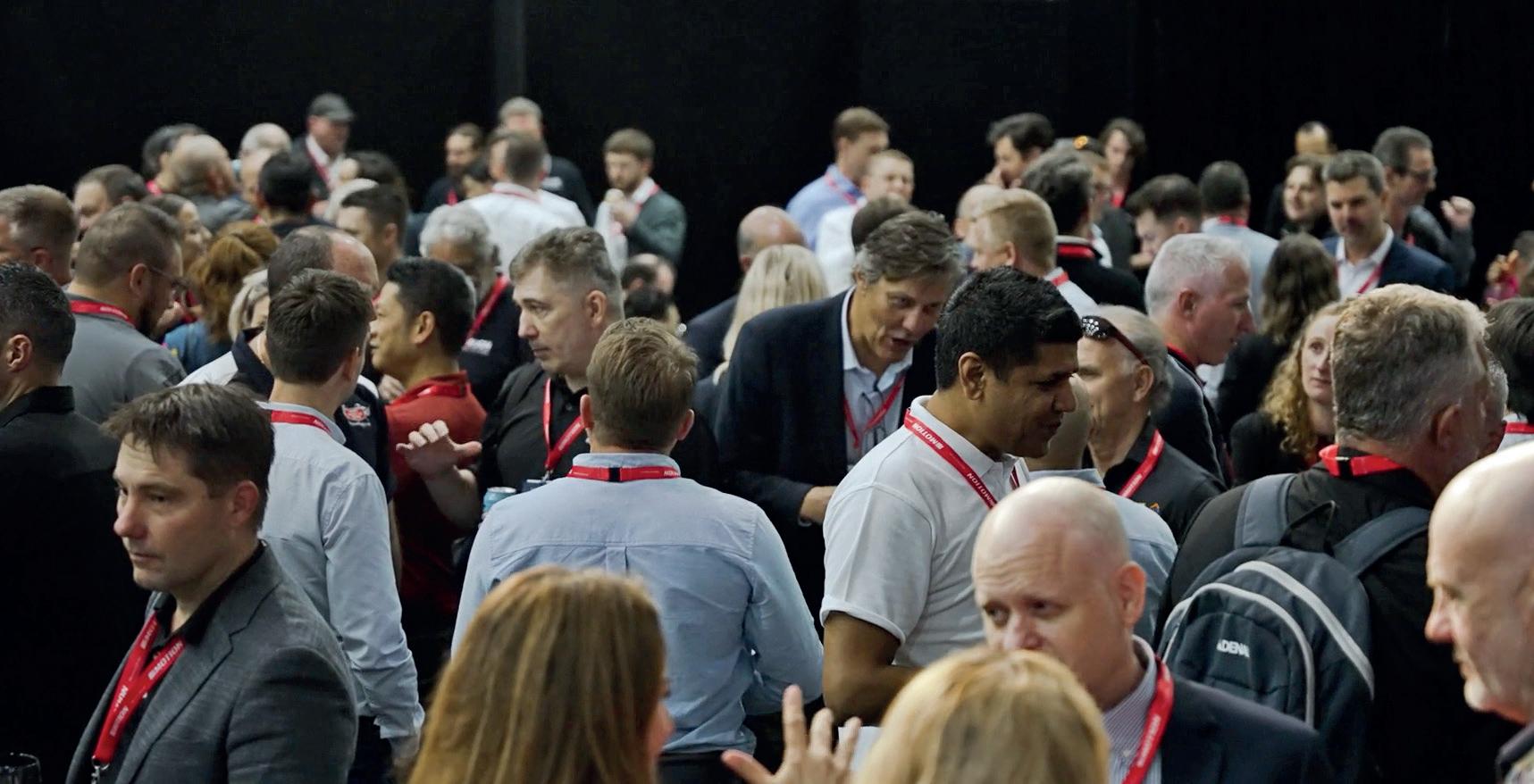
8-9
waminingexpo.com.au
THE NEXT LEVEL OF CONSTRUCTION INNOVATION
AUSTRALIAN MINING PROFILES CONEXPO-CON/AGG, WHICH TAKES PLACE AT THE LAS VEGAS CONVENTION CENTER IN MARCH 2026.
Held every three years, CONEXPO-CON/ AGG has become a must-attend event for construction industry professionals.
The show features the latest equipment, products, services and technologies for the construction industry, as well as industryleading education.
Following the resounding success of the 2023 event, CONEXPOCON/AGG returns to the Las Vegas Convention Center from March 3–7, 2026, with exciting new features and innovations.
“The continued growth and success
a new benchmark for the industry,” CONEXPO-CON/AGG show director Dana Wuesthoff said.
“Building on this momentum, we will deliver an even more impactful event in 2026, continuing to provide unparalleled opportunities for networking, education, and highlighting the latest innovations in the construction industry.
“We are especially excited to create new experiences and features for both attendees and exhibitors, making the 2026 event our most dynamic and engaging yet.”
Groundbreakers stage
The “groundbreakers” keynote stage
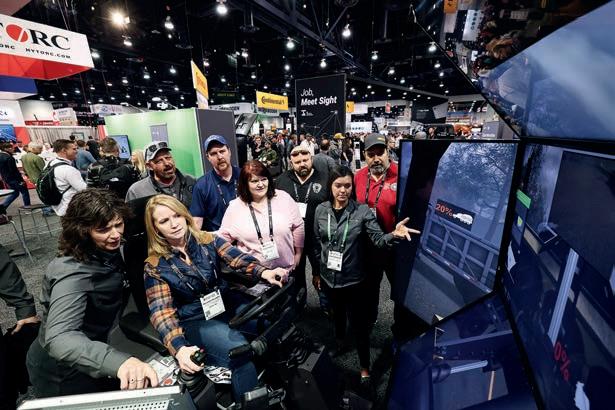
CONEXPO-CON/AGG FEATURES THE
an opportunity to raise awareness of the construction industry’s global contributions.
Key topics include innovation in construction technology and practices, public policy impacting the industry, workforce development and addressing labor challenges, sustainability and environmental responsibility, and mental health and wellbeing in the construction sector.
Women in construction
Join CONEXPO-CON/AGG for the EmpowerHER workshop, a special event dedicated to addressing the unique challenges and opportunities women face in the construction industry.
This program includes networking events fostering connections and community among women in the construction industry, peer-led panel discussions and keynote presentations featuring industry leaders and experts, and sponsorship opportunities to support and promote women-focused initiatives.
Small business workshop
Recognising the vital role of small businesses in the construction sector, the small business workshop addresses the unique challenges faced by small business owners. The workshop will provide networking events to build valuable connections for small business owners, best practices and practical tools owners can bring home to immediately
create pathways for success, and sponsorship opportunities to support small businesses.
Shop talks and walks workshop
The shop talks and walks workshop is a maintenance-focused program designed to provide attendees with practical solutions for everyday challenges.
This program features special events focused on preventive maintenance, equipment efficiency, and increasing uptime, and educational opportunities focused on providing attendees with the tools to solve realworld challenges.
CONEXPO-CON/AGG boasts 260,000 square metres of today’s best equipment and experts, with attendees able to meet manufacturers who build, demonstrate and answer questions, compare tools from all the equipment brands in your industry in the one place, and build relationships with contractors and construction leaders.
The event hosts more than 150 education sessions, with a program including speakers from the biggest names in business, working pros who get their hands dirty, and panel sessions involving unscripted discussions exploring the most pertinent topics to the construction industry. AM
CONEXPO-CON/AGG will be held in Las Vegas from March 3–7, 2026. Registrations open in August.
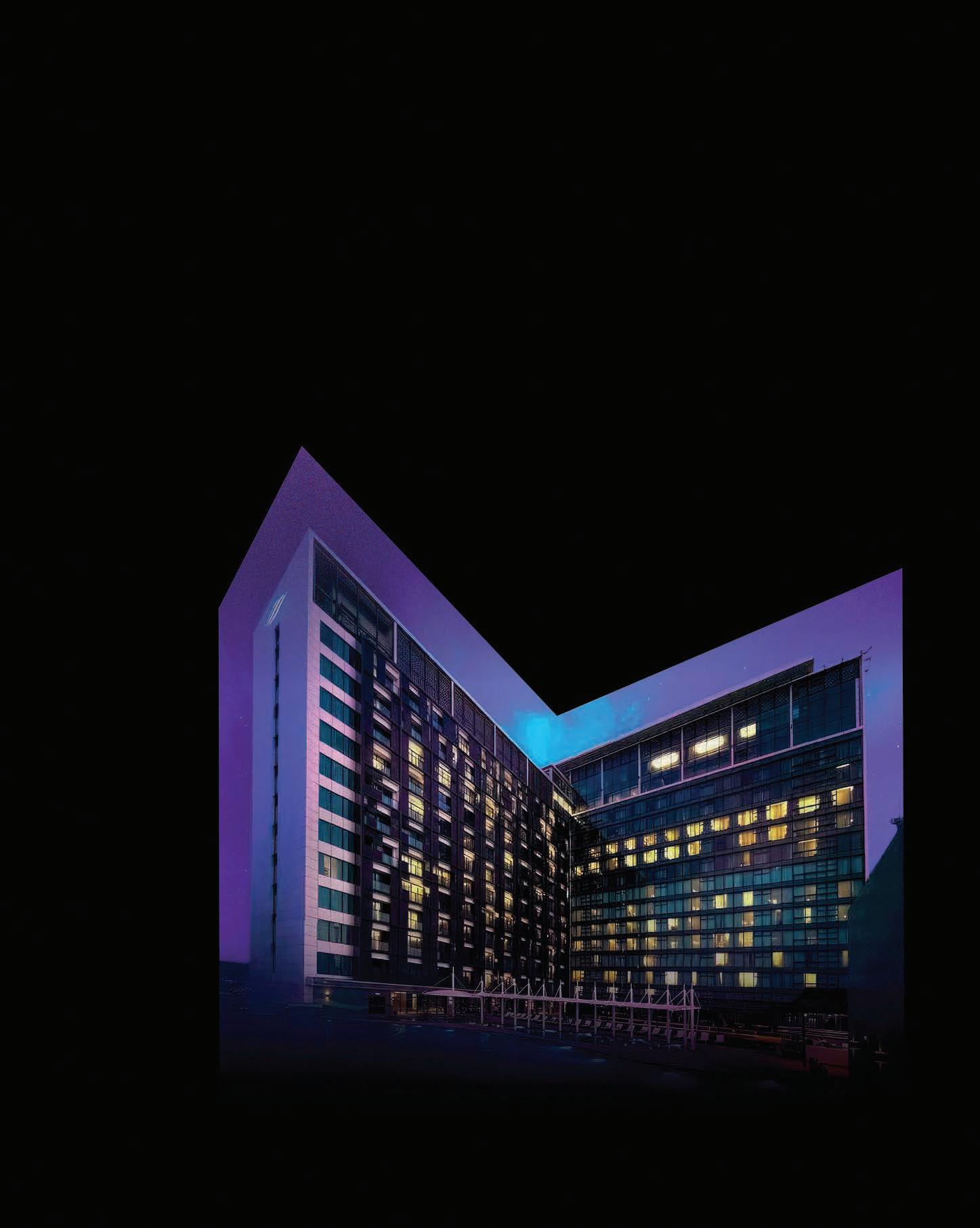
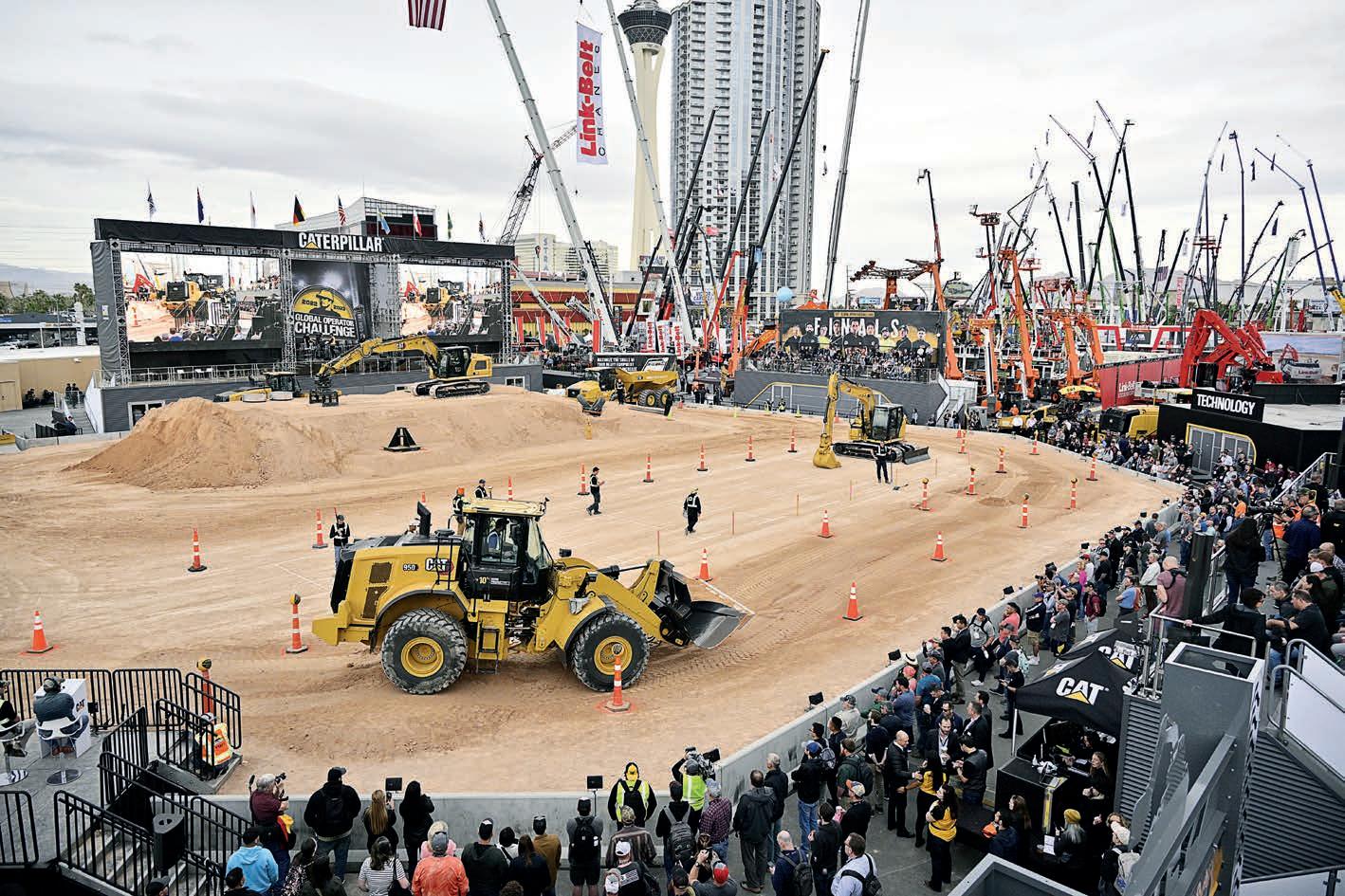
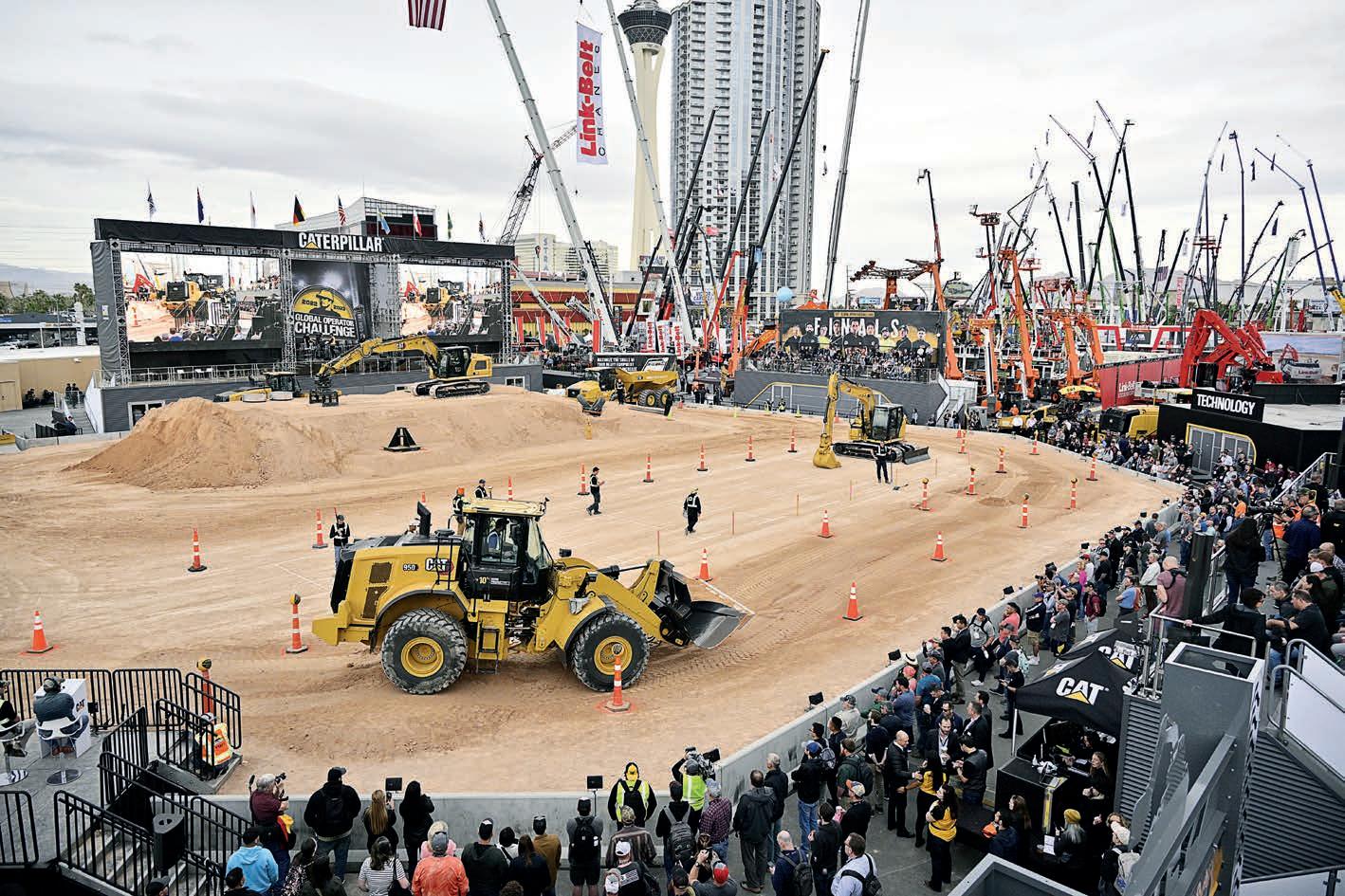
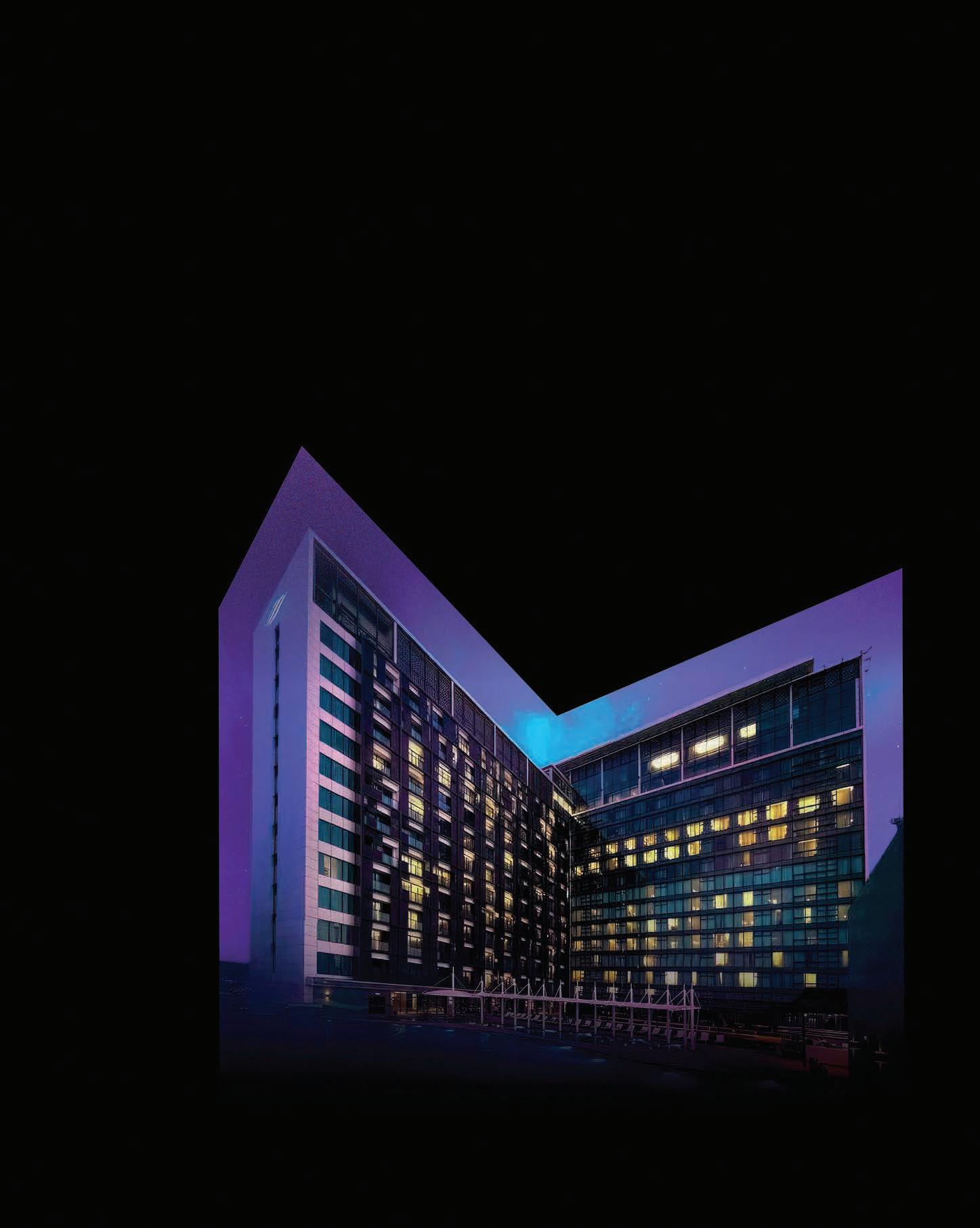
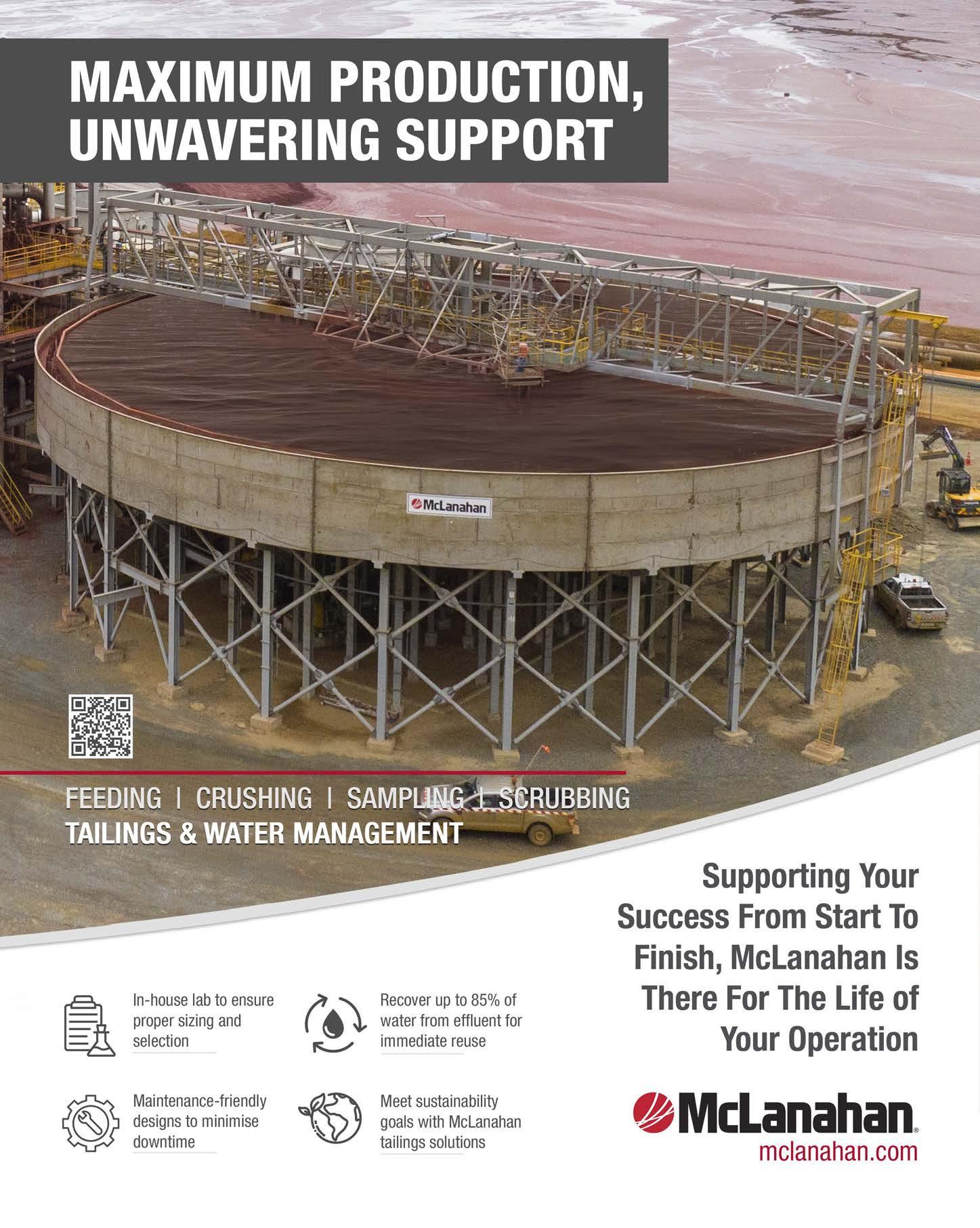