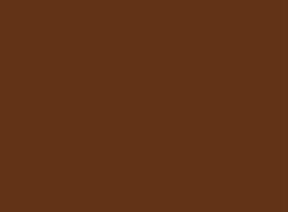
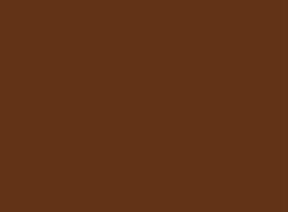
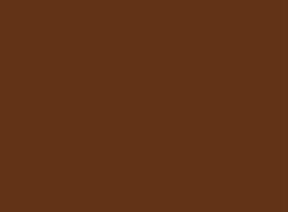

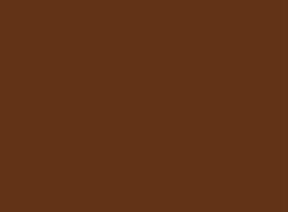
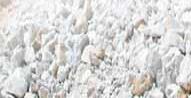

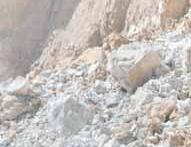
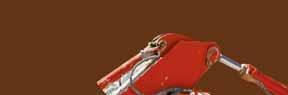
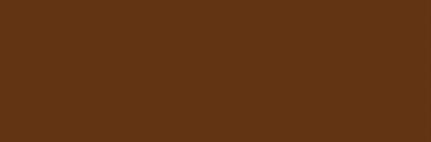
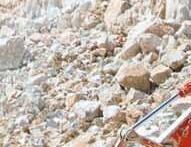
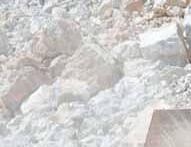
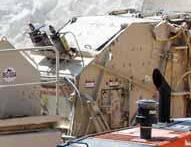




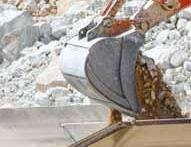
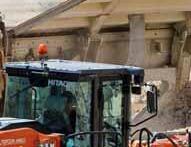
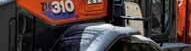

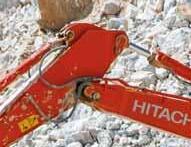
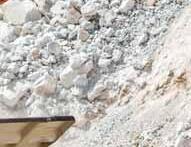
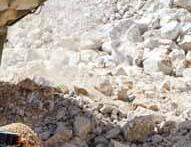
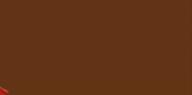

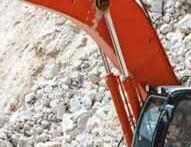
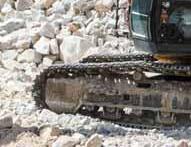


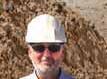
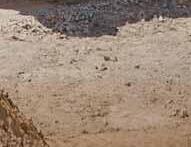

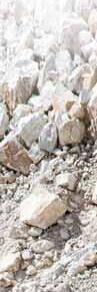
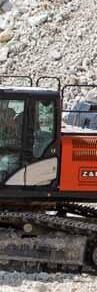
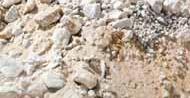
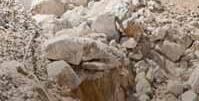

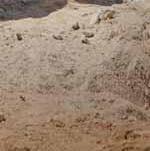
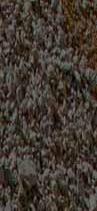

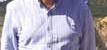

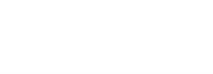
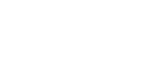
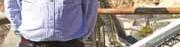







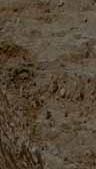
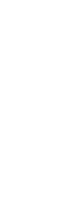

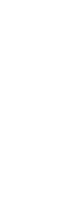





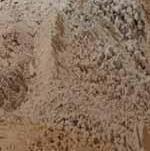




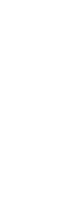




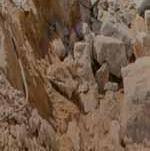
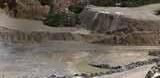




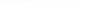

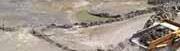




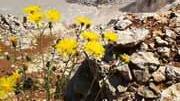


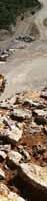
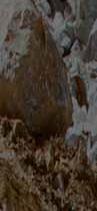

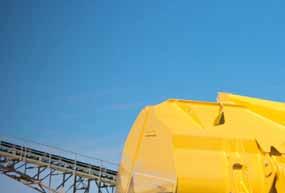
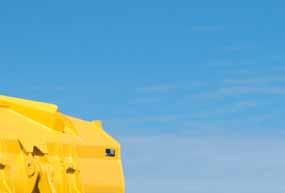

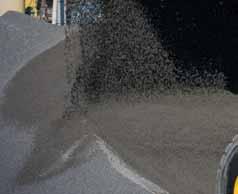
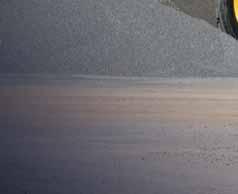
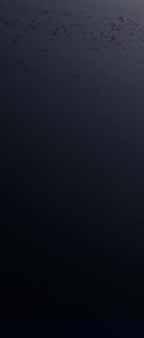

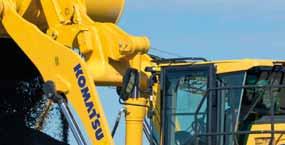

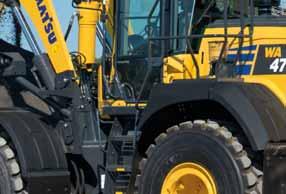
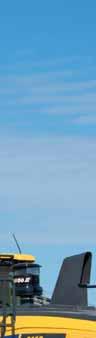

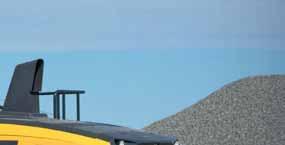




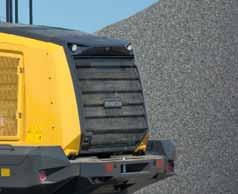
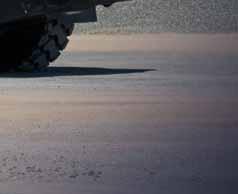


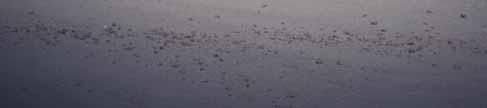
Komatsu WA475-10 – Get ready to rumble!
With the Komatsu Hydraulic Mechanical Transmission (K-HMT) that delivers an outstanding combination of ultra-low fuel consumption and massive productivity increase, the all-new WA475-10 is an industry-leading top performer. A unique, independent control of driveline and work equipment eases operation and shortens cycle times like you never experienced before in a wheel loader.
“Problems in obtaining permissions for quarrying and how to increase the use of recycled material are affecting aggregates supply in Germany.” p15
Brexit, disputes and the aggregates industry
Global OEMs’ new equipment launches and applications
58 EVENTS
All the key events in the quarrying & aggregates world
A major North American screening media producer’s big European market plans; while a top European plant producer is proving a big energy cost saver in Estonia
Quarry wheeled loader and crawler excavator experts at two manufacturers discuss their companys’ new model plans 26 HAULING
A new articulated hauler from a top producer and why Algeria is such a hot hauling market 28
Leading quarry conveyor and associated kit manufacturers are finding their products in big demand globally
The global screening buckets and attachments market is competitive, with innovation and aftermarket support key features of many leading manufacturers’ product
Buyers of environmentally sound off-the-road (OTR) retreads are being given discounts and a certificate attesting to the amount of raw materials they are helping to save
08 INTERVIEW
Iñigo Ajuria, OSF Group owner & general manager, discusses the Spanish group’s sustained success, despite operating in what continues to be a challenging domestic building materials market
15 ForumMIRO REPORT
Difficulties in obtaining permissions for quarrying and how to increase the use of recycled material are affecting German aggregates supply
36 CONEXPO-CON/AGG 2020 PREVIEW
The full lowdown on all the major equipment launches and North American product debuts at the big Las Vegas construction and quarrying machine exhibition
43 CYPRIOT AGGREGATES INDUSTRY
An island rich in aggregates-production history, Aggregates Business takes a firsthand look at the current and likely future health of the Cypriot aggregates industry
47 SaMoTer 2020 PREVIEW
The lowdown on the SaMoTer Innovation Award winners and what will be on show at the exhibition taking place in Verona, Italy, from 21-25 March
52 MARKET REPORT
Increased government spending on new infrastructure is creating welcome new commercial opportunities for Spanish and Portuguese aggregates producers
55 QUARRY PROFILE
A Command Alkon software solution has helped Day Aggregates become an ultraefficient business success story
HEAD OFFICE
EDITOR: Guy Woodford
ASSISTANT EDITOR: Liam McLoughlin
CONTRIBUTING EDITORS: Patrick Smith, Dan Gilkes
EQUIPMENT EDITOR: Mike Woof
DESIGNERS: Simon Ward, Andy Taylder, Stephen Poulton
PRODUCTION MANAGER: Nick Bond
OFFICE MANAGER: Kelly Thompson
CIRCULATION & DATABASE MANAGER: Charmaine Douglas
INTERNET, IT & DATA
SERVICES DIRECTOR: James Howard
WEB ADMINISTRATORS: Sarah Biswell, Tatyana Mechkarova
MANAGING DIRECTOR: Andrew Barriball
PUBLISHER: Geoff Hadwick
CHAIRMAN: Roger Adshead
ADDRESS
Route One Publishing Ltd, Waterbridge Court, 50 Spital Street, Dartford, Kent DA1 2DT, UK
TEL: +44 (0) 1322 612055 FAX: +44 (0) 1322 788063
EMAIL: [initialsurname]@ropl.com (psmith@ropl.com)
ADVERTISEMENT SALES
SALES DIRECTOR:
Philip Woodgate TEL: +44 (0) 1322 612067
EMAIL: pwoodgate@ropl.com
Dan Emmerson TEL: +44 (0) 1322 612068
EMAIL: demmerson@ropl.com
Graeme McQueen TEL: +44 (0) 1322 612069
EMAIL: gmcqueen@ropl.com
SUBSCRIPTION / READER ENQUIRY SERVICE
Aggregates Business International is available on subscription. Email subs@ropl.com for further details. Subscription records are maintained at Route One Publishing Ltd.
SUBSCRIPTION / READER ENQUIRIES TO:
Data, Route One Publishing Ltd, Waterbridge Court, 50 Spital Street, Dartford, Kent DA1 2DT, UK
TEL: +44 (0) 1322 612079 FAX: +44 (0) 1322 788063
EMAIL: data@ropl.com
No part of this publication may be reproduced in any form whatsoever without the express written permission of the publisher. Contributors are encouraged to express their personal and professional opinions in this publication, and accordingly views expressed herein are not necessarily the views of Route One Publishing Ltd. From time to time statements and claims are made by the manufacturers and their representatives in respect of their products and services. Whilst reasonable steps are taken to check their accuracy at the time of going to press, the publisher cannot be held liable for their validity and accuracy.
PUBLISHED BY © Route One Publishing Ltd 2020
AGGREGATES BUSINESS INTERNATIONAL USPS: is published six times a year. Airfreight and mailing in the USA by Agent named Air Business, C/O WorldNet Shipping USA Inc., 156-15 146th Avenue, Jamaica, NY, NY11434.
PERIODICALS POSTAGE PAID AT / US POSTMASTER
ADDRESS CHANGES TO: Aggregates Business Europe, Air Business Ltd, C/O WorldNet Shipping USA Inc., 156-15 146th Avenue, Jamaica, New York, NY11434
PRINT: ISSN 2051-5766
ONLINE: ISSN 2057-3405
PRINTED BY: Warners (Midlands) PLC
Aggregates demand has been low in much of southern Europe over recent years, with highway and residential and commercial infrastructure works shelved or scrapped due to budget crises amid often volatile and deeply divided national political landscapes.
In Spain, while FdA (The Aggregates Federation) figures show estimated aggregates consumption rose to 121 million tonnes in 2018, a 25% rise compared to 97 million tonnes in 2013, it is still just under a quarter of the 486 million tonnes of aggregates produced in the country in 2006.
Meanwhile, UEPG (European Aggregates Association) production estimate figures show that while Croatian aggregates output rose from 13 million in 2012 to 17 million in 2017; and Slovenian aggregates production reached 11 million in 2017 compared to 9 million in 2012, the same source estimates Italian aggregates production at 160 million in 2017 compared to 195 million in 2012; and estimates Portuguese aggregates output down from 43 million in 2012 to 30 million in 2017.
Having personally visited many highly skilled and shrewd aggregates businesses in Italy, Spain, Portugal and other parts of southern Europe in my five-and-a-half years as editor of this magazine, the know-how and capacity is there in these businesses to cater for a significant rise in aggregates demand. But the catalyst for increased demand must come from far more focused and determined political and business leaders committed to finding ways to kick-start national economies.
This edition has a very southern European flavour. Our Market Report feature takes an in-depth look at the Spanish and Portuguese aggregates sector, while we focus on Italy’s quarrying and construction equipment market in our comprehensive preview of the SaMoTeR and co-located Asphaltica 2020 exhibitions taking place in Verona (21-25 March 2020).
The Greek aggregates industry appears to be somewhat bucking the wider southern European trend. According to the UEPG estimated aggregates production data, Greece
produced 43 million tonnes of aggregates in 2017 – a rise of 72% on the 25 million tonnes produced in 2012.
The country also has many mineral product producers keen to embrace production innovation. For example, the May-June 2019 edition of ABE reported on how Iktinos Hellas and its quarries manager, Charalambos Almbanopoulos, are using Maptek’s Vulcan software at the company’s Platanotopos marble quarry in north-eastern Greece for resource and reserve estimation using quality indicators.
Cyprus, whose aggregates output rose 5.5% in 2019 compared to the previous year, is another prime example of a nation with a highly skilled and ambitious aggregates production industry looking to its political leaders to play a leading role in creating the right economic conditions to stimulate building materials demand.
Having visited five of the island’s quarries in early January 2020, I heard how the government’s belated releasing of funding for various large-scale highway, residential and commercial building infrastructure projects, and the encouraging progress being made on the proposed EastMed natural gas pipeline megaproject, were creating new business opportunities for native aggregates producers.
As you’ll read in my special report in this issue on the Cypriot aggregates sector, while matters such as aggregates pricing, perceived excessive bureaucracy, and the need to safeguard Cypriot aggregates provision, preferably, say quarry operators, through extending existing quarry sites, still need to be resolved, the sight of more construction equipment hard at work across Cyprus on new infrastructure projects is a very good start on achieving at least short- to mid-term growth in the nation’s aggregates demand.
Aggregates producers in other parts of southern Europe will be hoping the more positive outlook in Greece and Cyprus is soon mirrored in their own domestic industries. GW gwoodford@ropl.com
Germany’s construction equipment makers are cautiously optimistic about future market demand, according to the results of a VDMA survey of its construction machinery manufacturing members.
The survey notes that Germany’s VDMA members are looking to the future with confidence, despite industry representatives expecting a 3-5% drop in sales in 2020. Once a year, the specialist group meets in January to discuss operational issues
Finnish quarrying plant maker
Metso posted a record financial year in 2019, with company CEO and president Pekka Vauramo describing it as a “historical and transformative” 12 months for the
Metso’s year-on-year sales grew 15%, totalling €3.635 billion.
rm’s operating profit increased to €418 million. Metso reports “healthy” market activity, with orders received also up 5% compared to 2018 to €3.69bn. Further figuresfor Q4 2019 - show Metso sales up 7% to €963mn, with operating profit
“The last year was in many ways historical and transformative for Metso. It also marked a record in nancial performance, as our sales increased in both segments
and our profitability was higher than ever in the company’s history,” said Vauramo. “Other significant accomplishments included the launches of many new products as well as new initiatives in sustainability. What is common to our new products is that they are designed to accommodate our customers’ focus on improving their productivity.”
In 2019, Metso made two major strategic decisions, which Vauramo said were “transformative to both Metso and our industry”. The first was the acquisition of McCloskey, a Canadian supplier of mobile aggregates crushers and screens. After the closing of the acquisition in October, Metso’s offering strengthened in the mobile aggregates equipment market, which
is estimated to see the industry’s fastest-growing demand.
The second and truly transformative step was the decision related to the partial demerger of Metso, after which Metso’s Minerals business will be combined with Outotec to create Metso Outotec, a unique company in the minerals, metals and aggregates industries. At the same time, the valves business will continue as an independent listed company named Neles.
Vauramo continued: “We are confident that, as a result of this transaction, both companies will be well-positioned to grow and create value for our customers and other stakeholders. According to our current estimate, we expect the closing to take place on June 30, 2020.”
and projects for the current year. In economic terms, the industry is still at the record level of 2018, and industry sales in 2019 will match the previous year’s figure. The forecast of growth of 3-5% has not been met, and the cyclical downturn began early with road construction machinery. The decline of -12% in sales and -21% in new orders could not be offset by the slight increase in building construction and earthmoving machinery. Domestic sales for manufacturers at the German production location amounted to €4.3 billion, exceeding all expectations. Exports dropped slightly by 1% to €8 billion. Except for Germany, the trend reversal began towards the middle of the year after bauma 2019. Excluding Turkey and Russia, growth in Europe is at 7%.
A new £3.8 million (€4.51mn) dry discharge system at CEMEX’s Northfleet Wharf in Kent, south-east England, has been officially opened.
The building materials supplier partnered with the Port of London Authority (PLA) on the investment, which will ensure a more sustainable and flexible operation.
Following this investment CEMEX’s marine dredgers, which bring sand and gravel from CEMEX’s licensed offshore locations in the North Sea and the English Channel into Northfleet, will be able to arrive fully laden for the first time. This will increase capacity of the site by approximately 350,000 tonnes per year to between 800,000 and 850,000 tonnes.
This will allow CEMEX to provide more material to its on-site building products plant, reducing the need for aggregates to be transported in from other locations. This offers considerable sustainability benefits, as every dredger load reduces the need for 250 lorries on the region’s busy roads.
Prior to this investment, the wharf at Northfleet was the only wet discharge system remaining in CEMEX’s UK portfolio, and was prone to blockages and limited the products and capacity that could be brought into site. The new dry discharge system will increase the reliability and flexibility of the wharf, reducing the risk of blockages and ensuring ships can bring in exactly the right materials needed.
Laurence Dagley, CEMEX UK Materials South’s managing director, said: “CEMEX’s UK strategy focuses
on London and the other metropolitan markets across the country, as we believe increasing urbanisation will drive greater demand growth in these markets. It is therefore vital that our sites in these areas are developed to ensure they can support this strategy.
“Thanks to the funding from PLA, we have been able to invest our own resources into other assets, such as CEMEX Go Innovation, our state-of-the-art marine dredger which will arrive in the UK later this year.”
Robin Mortimer, PLA chief executive, said: “This investment is central to our long-term Thames Vision work to maximise the use of tidal river between Teddington and the coast, for both freight and passenger transport.”
Ofitas de San Felices Group (OSF Group) is a major family-owned Spanish independent aggregates and ballast products business with a proud history of serving its diverse customer base, including many major government rail and highway project contractors. Guy Woodford spent a day with Iñigo Ajuria, OSF Group’s owner and general manager, to find out more about the key factors behind the company’s sustained success, despite operating in what continues to be a challenging national building materials market
The year 1960 was hugely significant in OSF Group’s history. It was when Iñigo Ajuria’s father, Andoni Ajuria, OSF Group’s then owner and founder, decided to switch from being a predominantly limestone aggregate producer to become mainly a producer of ophite, much harder greenish mottled rocks with ophitic texture such as diabase.
“My father could see that the future was
in hard stone. Everybody else was producing limestone products. There was too much competition,” explains Iñigo.
After opening Ofitas de Santutis quarry in Álava, south of Bilbao in the Basque Country, northern Spain in 1960, Andoni bought the giant Ofitas de San Felices quarry, near Haro in La Rioja in 1973, when the then owner was forced to sell due to bankruptcy. At the time the quarry, which celebrated its centenary in
2019, was the only ophite rock quarry in La Rioja and the neighbouring Basque Country. Five highly productive years of aggregates production at Ofitas de San Felices were painfully interrupted one day by a tragic accident. “In 1978, my father and one of his guys fell into a working crusher hopper. My father survived but his colleague died. I was shocked. I was just a 12-year-old boy at the time,” recalls Iñigo. “I was so glad my father
survived, but it was a very difficult time for him and the business.”
Between the early 1980s and the early 1990s, the Spanish quarrying sector developed massively due to increased aggregates demand brought on by an abundance of civil infrastructure works. In the Basque Country, neighbouring OSF Group’s traditional Haro base, such works were evident in Bilbao and other key regional cities and towns.
In the second half of the 1990s, the high-speed rail line between Barcelona and Madrid was created, generating huge demand for ballast and a great business opportunity for the OSF Group. After securing a lucrative supply contract for the new Barcelona-Madrid rail route, OSF Group made a large investment in upgrading its machine fleets at the company’s two northern Spain quarries. In the late 1990s, the company also invested heavily in new equipment for its 1991-purchased Ofitas de Cerro Sillado quarry in Guadix, Granada, southern Spain. This allowed the firm to cater for high ballast demand from contractors working on the new Málaga-Córdoba high-speed rail link in the south of the country. Along with acquiring new loading and hauling models for its three quarries, OSF Group purchased new crushing and screening plant from premium original equipment manufacturers (OEMs) such as Metso.
“In the period 2000 to 2007, the Spanish economy was booming. We had a greater aggregate consumption than Germany! We were at 500 million tonnes a year. Aggregates, ballast and other building materials were all in huge demand. In 2007, more houses were built in Spain than in Germany and France together. I was OSF Group’s production manager at that time, my elder brother was managing director, and my father was the company president.”
Iñigo’s elder brother left OSF Group in 2006 and not long after Andoni fell ill, handing over the running of his company to his youngest son.
“I have more or less followed my father’s teachings but have taken on board the evolution of quarrying production and the general running of a business,” says Iñigo.
The global financial crisis of 2007-2008 hit hard in Spain, not least in its quarrying sector. As a result, national aggregates demand is now around 105 million tonnes a year –around a fifth of 2007 demand.
“The most important thing following the global financial crisis was the survival of the company. Nobody saw the crisis coming. I’ve always been very loyal. I was loyal to my father and I am loyal to our team. When I took over the company from my father in 2007, the team helped me a great deal. I was also in a dialogue with my father about how we were investing in our quarries. He was completely supportive.”
Iñigo says the full impact of the global financial crisis was felt most severely in northern Spain from 2010 onwards, due to funding having been already committed to longer-term infrastructure projects.
believed to be among the oldest and possibly the largest of its type in Spain, and its wide range of aggregates includes some of the highest quality ballast in the country – which is taken out by train.
Currently the quarry, which employs 30 people, produces some 4,000 tonnes of ophite a day due to current lower demand, although at full capacity the all-Metso plant can produce 8,000 tonnes a day. Around 30% of current daily output is railway ballast; 60% smaller chips and sand and 10% is fines. The site also produces 6,000 tonnes of limestone products each day.
“We changed the position of the crushing plant at San Felices step-by-step from 2008 as the quarry reserve was underneath it. We also wanted a new plant that was bigger and smarter,” explains Iñigo. “The new plant was fully installed by 2011, just as our turnover was falling by 66% due to the impact of the global financial crisis. At that time, we had to lay off half of our workers. We had two working quarries, San Felices and Cerro Sillado in Granada, and decided we must invest money in our plant capabilities
screening more efficient.”
Next to Ofitas de San Felices quarry, Iñigo has a 34-hectare vineyard where he has grown Tempranillo grapes for about ten years, the bulk of which he sells to a winery in Haro. The town itself is noted for its annual wine festival on 29 June which includes a ‘Batalla de Vino’ and youth bullfights.
As reported in Aggregates Business November-December 2019 issues, OSF Group is currently producing out of the 2016-reopened Santutis quarry ballast for the ambitious Basque Y high-speed rail project linking three major Basque Country cities – Vitoria-Gasteiz, Bilbao and Donostia-San Sebastián. Originally due to be completed by 2023 but now behind schedule, the 194km(157km double track and 37km single track) route will transport passengers and cargo, the latter between the ports of Bilbao and Pasaia. Basque Y is set to reduce journey times between Vitoria-Gasteiz, Bilbao and Donostia-San Sebastián to less than one hour, compared to anything between one hour 40 minutes and two-and-a-half hours currently. The new line will also connect the
Basque Country with the rest of Spain.
For Iñigo, the sight of ballast production at Santutis quarry represents a happy ending to a bureaucratic battle lasting 14 years. “I was fighting to get permissions and authorisations to reopen Santutis quarry since 2002. We knew the market would pick up as the Basque Y project was many years in the planning. We simply had to have Santutis up and running. It’s the only quarry that has been opened or reopened in the Basque Country in 20 years.
“We have six million tonnes of reserves at San Felices quarry – that’s 12 years of reserves at current 500,000 tonnes a year production. We have 15 million tonnes of reserves at Santutis quarry.”
Alongside ballast and highway workssuited aggregate products, OSF Group produces concrete, asphalt and a rock product
After long and bitter battles between various political parties vying for power, the Socialist Party (PSOE) leader and now prime minister is pinning his hopes on the fledgling coalition with the radical left Podemos party being even harder to oust than it was to put into power. Undoubtedly, the holding of four general elections in Spain in the last four years has done nothing to improve the country’s fragile economy and encourage business investment.
“There is no political stability in Spain, and investment in civil work is not profitable,” notes Iñigo. “I also foresee another big global recession coming.”
Despite the tough current and future economic outlook, Inigo says OSF Group is in good shape to withstand any new major economic turbulence. “I believe we are ahead of our competitors. The quality of our final product is the best, and the quality of our production plant is also the best on the market. This reduces our cost of production compared to our rivals. We also have huge knowledge of the aggregates business in the regions where we operate, and our reputation both locally and nationally among rail and highway contractors is very strong.
“I have successful quarries in the north and south of Spain. I would also like to
Group reopened Ofitas
ABOVE: Ofitas de San Felices quarry currently produces around 4,000 tonnes of ophite aggregates a day
BELOW: Iñigo Ajuria in front of the all-Metso up-to-8,000-tonnes-per-hour plant at Ofitas de San Felices quarry
establish OSF Group as an aggregates company name in the centre of the country, near Madrid. We are looking to open a quarry like San Felices in that area within the next three years. It’s a very good region for aggregates demand.”
As well as shaping OSF Group’s current trading and working on future company goals, Iñigo still finds time to indulge in his passion for Deportivo Alavés, a Spanish La Liga football team, watching them play in games at their home stadium in VitoriaGasteiz, and in away games in cities and towns all over Spain.
Summarising his approach to work and the demands of running a successful Spanish aggregates products business industry, he says: “I have been working with aggregates since I was a child. I like to have new challenges and I love to overcome them. I am very proud of my team and what OSF Group has achieved.”
AB
MORE POWER, MORE UPTIME, MORE PRODUCTIVITY. ALL WITH LESS COMPLEXITY, LESS WEIGHT AND LESS SERVICING.
THE L9™ PERFORMANCE SERIES ENGINE FROM CUMMINS DELIVERS BENEFITS TO EQUIPMENT MANUFACTURERS AND OPERATORS ALIKE. THE HIGHER POWER OFFERS THE OPPORTUNITY TO INCREASE MACHINE CAPABILITY. ITS SIMPLER, EGR-FREE DESIGN IS EASIER TO INSTALL. FOR THE USER, IT IS MOREPRODUCTIVE, MORERELIABLE ANDMOREEFFICIENT.
TO SEE HOW CUMMINS L9™ SETS THE BAR FOR PERFORMANCE VISITUSAT CONEXPO-CON/AGG 2020, SOUTH HALL 4 – S84407 OR SEE CUMMINS.TECH/CONSTRUCTION.
The EU Green Week is the most prominent annual event in the European environment policy calendar and UEPG (European Aggregates Association) will actively take part in it. This year’s Green Week Conference will take place 2-5 June in Brussels, with partner events taking place throughout Europe 4 May-14 June. The focus, this year, is on the preservation of nature and biodiversity.
Biodiversity conservation can in fact benefit from a more dynamic management. Although aggregates extraction sites, by their very nature, can be natural biodiversity hevens, a Biodiversity Management Plan helps to create new habitats and attract pioneer species. By allowing a temporary activity such as extraction, companies will gradually restore the area and implement plans enabling the development of high biodiversity value.
To instil the European aggregates industry’s contribution to biodiversity and nature conservation objectives, UEPG will host a session in the EU Green Week 2020 conference programme on ‘Biodiversity Management & Temporary Nature in Extractive Industries’, jointly organised with the European Cement
Association and promoting their cooperation with BirdLife Europe.
This session moderated by Luc Bas, director of the European Regional office of IUCN (International Union for Conservation of Nature) , will explore how to bring nature and extractive industry together. It will provide an overview of opportunities arising from innovative approaches developed by the aggregates industry to not only protect but also foster biodiversity before, during and after extraction. Examples will be presented on ways to overcome barriers, benefiting both nature, society and economic development, with smarter implementation of environmental legislation to help reach the targets of the new EU Biodiversity Strategy 2030.
To this end, environmental NGOs (non-governmental organisations), academia, policymakers and industry will discuss in a panel the opportunities and challenges of bridging socio-economic and nature conservation objectives. The aggregates industry, acting as an agent of change for the protection of biodiversity in extraction sites, will seize this opportunity to promote the concept of temporary nature and dynamic
management of biodiversity.
In this framework, UEPG encourages its members across Europe to organise open-door events which will be promoted at European level, offering a chance to demonstrate how extraction sites are indeed a shelter fostering biodiversity. AB
To register your partner event or for more information on events organised during EU Green Week, visit the official website of the EU Green Week 2020:
www.eugreenweek.eu
Since the UK left the EU on 31 January 2020, the enforcement of UK judgments has come back into focus.
For businesses who operate across borders, like many in the aggregates sector do, this is an important issue.
When disputes involve organisations (or individuals) based in different countries, there is often an array of complex issues in various jurisdictions. Add Brexit into the mix, and the picture becomes even more complex.
Cross-border disputes raise a number of issues, including jurisdiction and which countries your claim can be brought in; consideration of which jurisdiction it would be most advantageous to bring your claim in; and finally, enforceability and consideration of whether a judgment will be recognised in another jurisdiction. This article focusses on the latter point of enforceability.
With disputes such as claims for breach of contract often having significant sums at stake, it is important to understand how Brexit could affect enforcement of English judgments abroad.
Pre-Brexit, enforcement of English judgments in the EU wasn’t too much of an issue because the UK is party to international agreements governing cross-border enforcement. However, the UK is party to many of these international agreements by virtue of its membership of the EU, so leaving the EU changes things and brings with it new challenges for enforcing judgments in the EU and beyond. Careful consideration and strategic planning are required whether you have obtained your judgment, are involved in ongoing litigation or are contemplating commencing a claim.
Date of dispute will be crucial
Due to the passing of the Withdrawal Agreement Bill, there will be a transition period until the end of this year. During the transition period, the current legislation applicable to jurisdiction and enforcement of judgments will continue to apply.
If court proceedings are commenced before the end of the transition period, the current rules will apply, and English judgments will be enforceable in EU countries. If court proceedings are commenced after the end of the transition period, the enforceability
Commercial disputes are a fact of life for all businesses, including those in the aggregates sector. From breach of contract claims to disputes about interference with mineral rights, what will Brexit mean for disputes and the enforcement of UK judgments abroad? Catherine Mathews expert in commercial disputes at Stephens Scown LLP, explores the issues.
This will bring welcome certainty for businesses trading outside the UK.
of any judgment will depend on a variety of factors, including the terms of any international agreements that the UK enters into during the transition period.
During the transition period, the UK courts will also continue to recognise and respect “choice of law” clauses in contracts. These clauses are particularly important in contracts where the parties are based in different countries, as they specify the applicable law in the event of a dispute.
In the absence of such a clause, the law applicable to the contract is determined by rules set down in legislation. This legislation will also continue to apply during the transition period, and the government has also indicated that it will be retained in domestic law following Brexit. This will bring welcome certainty for businesses trading outside the UK.
It is essential to plan ahead before you enter into any international contracts, particularly following Brexit. Preventative steps can be taken, for example, by ensuring that any agreements you are entering now are drafted to protect you as robustly as possible and ensuring that they include appropriate “choice of law” and jurisdiction clauses. The importance of well-drafted contracts cannot be overstated. Having contracts professionally drafted will
ensure that crucial terms dealing with the manner and timing of performance of the parties’ obligations under the contract, payment and termination are clear. This will reduce the scope for a dispute to arise in the future.
As well as taking protective measures, if a dispute has regrettably already arisen or you are considering litigation, it is crucial to take expert advice, so you are clear about what options are available to you. In many cases, court proceedings can be avoided by taking advice and communicating with the opposing party at an early stage, as soon as it appears that a dispute may arise. AB
Catherine Mathews is a partner in the dispute resolution team at Stephens Scown. Her key areas of work are commercial litigation and contract disputes. The firm has over 70 years of experience in the mining and minerals sector and its specialist team is recognised by independent legal guides Legal 500 and Chambers.
To contact Catherine please call 01392 210700 or email solicitors@stephensscown.co.uk. For more information visit www.stephens-scown.co.uk
We’ve taken another giant step to be close to our customers, by opening our first manufacturing facility in North America.
With 40 years’ experience under our belts, we’ve now got feet on the ground in Franklin, Kentucky, where we’ll be well placed to help you keep the show on the road, every single day.
Join us at CONEXPO Las Vegas to see how our Zip Clip® replacement conveyor belts are maximising machine uptime around the world and helping to grow the mobile equipment sector’s aftermarket.
Problems in obtaining permissions for quarrying and how to increase the use of recycled material are affecting aggregates supply in Germany. Liam McLoughlin reports
Around 570 participants from aggregates companies, machinery suppliers, government ministries, authorities, NGOs and MEPs gathered at the annual ForumMIRO in Berlin last November to discuss major issues around the supply of domestic mineral raw materials.
The event, hosted by German aggregates industry association MIRO, kicked off with a political discussion that gave attendees the chance to hear from German members of parliament and policymakers on topics, including how to achieve greater use of recycled materials in construction and the importance of the aggregates sector in helping Germany meet its pressing need for more social housing over the next decade.
Problems arising from differences in federal and regional government policies towards the aggregates sector were a major issue. Attendees heard that the ease of gaining permissions for new quarrying and excavating activity varies considerably across Germany, and this is leading to problems in obtaining the raw materials that are much needed for housebuilding in the country.
MIRO’s newly re-elected president Dr Gerd Hagenguth called for more central government involvement in setting out the country’s raw materials strategy. “The government should say ‘we need raw materials’,” he added. “The problem is that the government says one thing and regional authorities say something else. There need to be directives from central government. Germany needs two million in social housing over the next ten years, and therefore we need the raw materials.”
Hagenguth stressed the importance of the minerals industry, and added: “The level of recycling taking place is not enough for the amount of aggregates that are needed in Germany.” He said that new regulations on the re-use of construction waste that are being planned by the Economic Ministry could impact the amount of recycling that takes place. It is proposing to ban the use of construction waste containing dangerous substances such as asbestos. “The Ministry wants to have more recycling, but its rules do not make this possible,” according to Hagenguth. “Sometimes you get the feeling that authorities are against giving permissions.”
Dr Hildegard Wilken, Federal Institute for Geosciences and Natural Resources, said the recycling of raw materials is an important issue in Germany. “But we have enough raw material deposits in Germany [for construction and housebuilding], we just don’t have enough access to it,” said Wilken. “We can employ technical solutions to use lower quality aggregates.”
SPD member of parliament Michael Thews said that recycled aggregates are only used at the moment in road building in Germany, and not in the construction of new buildings. “We need high-quality recycling so this material can be used in modern products for housebuilding,” he said. According to Thews, the period of time it takes to obtain permissions to excavate new sites in Germany has increased from six to 12 years in recent times due to regional authorities being under-staffed and to increasing environmental regulation. He added that the authorities are only just beginning to hire new people.
CDU MP Matthias Heider said that companies should be given incentives for recycling waste.
FDP MP Olaf in der Beek said that there
should be less bureaucracy in the granting of permissions and that the process needs to be accelerated. “No one can explain to me why the process takes so long,” he added.
In der Beek said there needs to be more cooperation between the Economic and Environment ministries over environmental issues. He proposed that the excavation of areas and the repopulation to restore them to nature should be carried out in cycles.
“We are proposing to excavate an area for a certain period of time and then repopulate and restore it for nature,” he added.
Michael Basten, secretary general of the Federal Association of the Building Materials, Rock and Associated Products Industry, called for greater tax incentives for the recycling of materials such as construction waste. He was critical of the proposal for a new tax on building materials such as gravel, which is intended to reduce the use of primary materials and encourage recycling.
“Gravel sells for around €6 per tonne in Germany, so with the proposed new €3 per tonne tax on it there is not much money left,” said Basten. “I don’t think the tax will lead to more recycling and could destroy smaller businesses.”
The cement industry is a major producer of carbon dioxide emissions and has to pay €10 per tonne of CO2 it produces. There are now government plans to extend this tax to other sectors (including gravel/aggregates and construction) for their CO2 emissions. “The government wants to increase the CO2 tax to a maximum of €60 per tonne in future,” said Basten.
Walter Nelles, vice general manager of MIRO presented his report of the association´s work during the delegate assembly. He said that there is a lack of consistency at the European level for
standards of aggregates. “We at MIRO are trying to push for better standards. In addition, MIRO also wants to configure the revision of the EU Waste Directive, so that non-hazardous waste could be re-used for backfilling purposes,” he said. “In terms of PR there is a need for better communications, organising political breakfasts and debates with policymakers.”
Jörg-Andreas Krüger, newly elected president of German wildlife group NABU, told forum delegates that there are a lot of biodiversity partnerships between NABU groups and companies at a regional level, including projects on pollination, bees, bats and owls. “The nature discussion is coming more and more into the public arena in terms of sustainability and resource efficiency, and a lot of changes are coming,” he added. “The door is open for dialogue on this issue and the important thing is to be honest. “In terms of sand and gravel pits, we have to look at both sides of the coin – excavating on the one hand and giving nature back on the other. We need these habitats for wildlife, not only after quarrying has finished, but also during the lifetime of the quarry.”
The German aggregates sector is predicted to continue its current steady growth rate over the coming years. The country is the largest producer in Europe, and currently accounts for around 18% (500 million tonnes) of Europe’s annual aggregates production of 3 billion tonnes, according to MIRO, which adds that annual production in Germany is increasing at 2-3% a year.
In 2016 Germany used a total of 563.7 million tonnes of primary raw materials, according to figures from consulting company SST. The largest category of this was sand and gravel (247 million tonnes),
followed by natural stone (218 million tonnes).
The total amount of secondary raw materials in 2016 was 101.5 million tonnes, of which by far the largest part was RC (recycled) construction materials at 72.2 million tonnes.
Primary aggregates are predicted to total between 592.8 million tonnes to 615 million tonnes in 2020, and between 555.2 to 650.2 million tonnes by 2035. The SST study estimates that secondary aggregates will total 102.3 million tonnes in 2020, and between 87.7 million tonnes to 98.5 million tonnes by 2035.
Currently, more than 90% of the annual mineral building waste incurred in Germany is recycled in an environmentally-friendly way, according to a survey by the German Institute for Economic Research Berlin and consulting company SST. The survey found this means that only a slight increase in the already high recycling/recovery rate of building waste materials would be possible.
German companies are looking into various possibilities of using alternatives to diesel for powering their aggregates, quarrying and mining operations. Mineral processing and mining technology group Schmidt Kranz has assessed the possible use of hydrogen power, and the company’s CEO Mortimer Glinz said: “It’s cheaper with hydrogen than with diesel, so it’s an option for each company to produce its own hydrogen.” He added however, that there is currently no legislation in Germany that allows the use of hydrogen power.
“For customers this [hydrogen] system is positive and it’s now up to the government to bring in regulations so it can be operated,” said Glinz. After around 20 years of talk but little action around the use of hydrogen power the last year has seen more
MIRO president Gerd Hagenguth called for more central government involvement in setting out Germany’s raw materials strategy
practical government and political discussion of the idea, according to Carsten Krause, MD of AREVA H2 Gen, which manufactures machines that produce hydrogen from water and electricity. “Electricity can only run for a short time,” Glinz said. “Hydrogen can save for a long time, so it’s good for mining.”
Gelsenwasser, which produces drinking water by excavating sand from quarries and
Matthias
wants more incentives for companies to recycle
the sea, has built a wind turbine to power this process as the cost of electricity is so expensive. Bernhard Albers, responsible for energy and measurement technology at the company, says that a 100 metre-high turbine (the maximum height for a wind turbine under German law) can produce 750kW of electric energy.
Solar power is also on the radar, and
gravel works operator Ossola has built a solar cell that floats on the sea. Two thirds of the energy that this ‘photovoltaic plant’ produces are used to excavate sand and gravel from the sea, and the remaining third is sold to private electricity utilities. “It’s the first time in Germany that a solar energy plant has been built on the sea,” according to company CEO Armin Ossola. AB
Guy Woodford visited the European headquarters of MAJOR, a leading global manufacturer of high-performance wire screening media, to learn more about the North American firm’s ambitious expansion plans for the key regional market. Meanwhile, a Keestrack plant solution is proving a big energy cost saver for a major Estonian quarrying firm
AHaver & Boecker company, MAJOR’s European operation (MAJOR Europe) is based in Battice, Belgium. The company currently sells its product range directly to customers in Germany, France, Belgium, Switzerland, Austria, Slovenia and Croatia. While working to increase its direct dealership reach in Germany and France, MAJOR is supported by dealer-led sales in the UK, Finland, Sweden, Netherlands, and Turkey.
Manufactured in Canada, Flex-Mat highvibration wire screen media – available in TENSIONED and MODULAR form and in D, S, DD (impact resistance), L (sand screening), and T (fine screening) series variants - is seen by MAJOR as a key product range for European customers.
Flex-Mat TENSIONED allows wires, bonded to lime-green polyurethane strips, to vibrate independently from hook to hook for faster material stratification. The screen media is available in a side-tensioned or end-tensioned configuration.
Flex-Mat MODULAR comprises direct switch-and-replace polyurethane modular panels said to provide substantially more open area than traditional panels, increasing the throughput of spec material.
Unlike imitation self-cleaning screens, MAJOR designs Flex-Mat to fit all decks, from scalping to finishing screening. It features up to a claimed 40% more screen capacity than traditional woven wire and a claimed up to 50% more than traditional polyurethane and rubber panels.
As of late October 2019, over 1,000 FlexMat applications had been carried out on quarrying, mining and construction job sites in Europe since 2015 – 30,000-plus globally.
A further 100-150 plant assessments have also been conducted in Europe over the past four years.
During a visit to MAJOR’s European HQ in autumn 2019, Aggregates Business learnt that plans are in place to begin producing the Flex-Mat product range in Europe within the next two years. MAJOR’s Woven Screen product range for European customers is currently made in Battice.
MAJOR’s original Battice workshop, excluding office space surface, was 1500m². The firm expanded the workshop surface up to 3700m² in 2016 by adding a new 2200m² facility. The company is in the process of extending the automation of its wire weaving machines in North America and Europe.
Globally, around 60% of MAJOR’s customers are in the aggregates sector; with 30% in mining and 10% in the recycling industry.
Speaking to Aggregates Business, Lars Bräunling, MAJOR Europe director of product technology, talked about why MAJOR, a company with a proud 130-year plus history, needed to operate differently in Europe, and not simply mirror its successful North American business set-up.
“We have a homogenous dealer-led approach to market in North America, where you can largely operate in one language and customer product needs are pretty consistent. In Europe, company type and size, produced product standards and how the products are made varies a great deal. Then there are 15-20 countries featuring many different languages that we are targeting sales-wise.”
Matej Grm, MAJOR Europe sales manager, said the diversity of the European
have a particularly strong focus on localised customer service, both in assessing and installing the best product solution and subsequent aftersales support.
“We are in the process of building a ‘tool kit’ to allow our dealers to serve our customers even better,” added Bräunling.
MAJOR’s research and development (R&D) focus is on wire screen media products delivering continuous improvement, better performance, and longer wear life. New products must also be capable of more varied applications.
The R&D focus ties in with MAJOR’s corporate philosophy, which it refers to as ‘the MAJOR way’. It includes the company’s emphasis on advanced technology, screening know-how, and business operation – helping drive materialsproducer profitability.
In November 2019, MAJOR introduced the Flex-Mat Sensor, a valuable and easyto-operate vibration data-measurement tool users can utilise to review results and finetune their screen machine without shutting down equipment. The app-controlled vibration analysis sensor enables readings of screen-box vibrations within seconds and generates a report that can be sent or reviewed.
The operator connects the single sensor to the Flex-Mat Sensor app on their phone before placing the sensor on one corner of
the machine. The user continues to move the sensor to each corner of the machine until finished. Once the measurement process is completed, the information will be delivered to the phone in the time it takes to climb down from the machine. Alternative systems may not provide the data until the following day. Machine information is stored locally for ease of use and viewing in areas with cellular limitations. Once a signal is available, the information uploads to MAJOR’s cloud service where it is viewable from a web browser. Historical equipment performance data is also viewable through the cloud.
of Keestrack’s track-mounted R6e impact crusher and three-deck C6e classifier as part of a comprehensive modernisation of its processing technology is set to save Paekivitoodete Tehas (PT) nearly €100,000 a year in energy-related operating cost at the company’s flagship quarry near Estonia’s capital city, Tallinn.
The impressive saving forecast by PT and Keestrack was made after the R6e and C6e began operating at PT’s Väo Quarry in June 2019. Connected to the grid, the new plant set-up cuts PT’s cost per final product tonne to €0.42, compared to the calculated total of €0.58 per tonne of the same machine duo’s annual diesel-electric powered operation (approx. 600,000 tonnes a year).
The reduction of pollutant emissions on site through all-electric crushing and classifying is also significant, with around 400 tonnes per year of climate-damaging CO2 avoided.
Since the installation of the R6e and C6e, the three-man working teams (excavator-wheeled loader-all-electric plants operator) have also been reaching their daily production target of 3,000 tonnes in one long or two short shifts, bringing further significant savings compared to the previous three-shift pattern, requiring 15 PT personnel.
The modernisation of the PT quarries’ set-up cost just under €1mn, with 35% of funding being provided by the Estonian Environmental Investment Centre (EIC) using EU regional funding. The significance of the project was demonstrated by the presence of numerous high-ranking representatives from politics and business
offering the full flexibility of the dieselelectric hybrid drive.
Since 1959, Paekivitoodete Tehas – ‘Limestone Factory’ in English – has supplied high-quality mineral and aggregates for the Estonian road and construction industry. Since 1989 the former state-owned enterprise has been gradually transformed into a private company and developed into one of Estonia’s leading construction materials suppliers, under the leadership of the long-standing director, today’s chairman of the board and majority shareholder, Vladimir Libman.
Today, up to 20% of the Estonian annual demand for crushed aggregates comes from PT’s Väo and Maardu quarries, with their combined extraction quantity of around 750,000 tonnes of material per year. Together with washed sand and gravel from mining residual masses with high contents of fines or clay and marl impurities and the company’s recycling activities, PT’s total production amounts to around 1.2 million tonnes per year.
On the Baltic coast, high-quality limestone is found close to the surface in 5-6-metre widths. In the past, PT has responded to the rapid growth of aggregates demand with three decentralised stationary processing units (totalling 400 tonnes per hour), whose raw materials, intermediate and end products had to be extensively hauled by rigid trucks. This low efficiency operation became problematic as the mining zone with its dust and noise emissions moved ever closer to the rapidly expanding Tallinn residential district of Lasnamäe, and its 120,000 inhabitants.
relief has been achieved through investment
•Is ideal for production volumes with large proportions of RAP
•Can use discarded consumables such as printer cartridge toner and tyres
•Features warm and cold recycling systems that can be used simultaneously
•Incorporates an integrated parallel drum system, positioned directly above the mixer, to optimise material flow and minimise wear
The Ammann ABP HRT (High Recycling Technology) plant is the industry’s recycling leader. The HRT plant:
of the production processes has focussed especially on the protection of residents and a general reduction of the environmental impact. To replace the existing installations, a mobile processing line for the production directly in the mining zone was favoured for the main Väo quarry site as well as for temporary operations in the smaller Maardu quarry (150,000 tonnes per year), 10kms away.
The entire PT processing modernisation project was supervised by Johann Prüwasser, CEO of Keestrack Engineering, the Austrian design and development branch within the Keestrack Group.
operation in the Väo quarry with all the advantages of our proven track-mounted technology,” he adds.
Two 200-metre cables from the specially installed 400V transformer station on the quarry floor now feed the Keestrack R6e and the downstream C6e classifier, directly connected to the crusher via power supply and communication cable for data exchange between the plant controls.
Powerful electric motors for the crusher drive (250kW) and the pump units of the central plant hydraulics (R6e: 90kW, C6e: 45kW), as well as electric belt drives and ancillary units, enable complete emission-
A combination of Keestrack’s R6e impact crusher and three-deck C6e classifier is set to save Paekivitoodete Tehas (PT) nearly €100,000 a year in energy-related operating cost at the company’s Väo Quarry, near Estonia’s capital city, Tallinn
Belgium, produces around 60,000 tonnes of building material products each year, with just over 50% for export customers in Europe or further afield.
In early 2019, the company identified a lack of consistent quality in every other truckload of variously sized quartz, silica, marble or limestone products processed through its Mogensen SN1544 four-deck sieving machine.
The company turned to screening wire system manufacturer MAJOR Europe, a leading manufacturer of high-performance
of Euroquartz’s other screening machines, for a solution. This led in May 2019 to MAJOR Europe installing its Flex-Mat high-vibrating wire screens on two of the Mogensen SN1544 unit’s four decks.
Eddy Depraetere, Euroquartz’s chief technology officer, said the introduction of Flex-Mat wire screens is expected to reduce the Mogensen SN1544’s production cost by 30%, with the company set to fit Flex-Mat to the machine’s two other screen decks.
When Aggregates Business visited Euroquartz in late October
of material with the Mogensen SN1544 without any problem.
“We are now able to produce a better quality product, while saving a lot of time and money through reduced maintenance. Before, we were losing one to one and a half hours of production time every time we had a problem with material throughput, such as plugging” said Depraetere.
“We initially installed the FlexMat on two decks of the Mogensen unit as we wanted to compare its performance against the screen media that came with the machine.
The successful introduction of Flex-Mat on the Mogensen SN1544 could not have been better timed as demand for Euroquartz’s product range is growing year on year. The company’s six-hectare manufacturing and storage site has been operational for more than 10 years.
“We have a wide client base. Our biggest export market is other European countries, but we also sell our products to customers in South America, China and Thailand. We also sell our sand products to the Saudi Arabians!”
crawler excavator range cabin more spacious. Each cabin also has an eight-inch hi-res display screen and reduced noise and vibrations compared to its predecessors.
The global quarry loading machine market is vibrant with many leading manufacturers due to unveil new models over the next 12-18 months. Guy Woodford spoke to experts at two leading wheeled loader and crawler excavator manufacturers to find out more about their new model plans, along with the key benefits of their current quarry-suited machine line-up
Hitachi Construction Machinery (Europe) NV (HCME) has been talking to Aggregates Business about current excavator and wheeled loader demand among European quarrying and mining customers. The major original equipment manufacturer (OEM) is launching its next-generation Zaxis-7 crawler excavators for the European market in spring 2020, and its upcoming wheeled loader models will be introduced later.
“Our large quarry and mine-suited excavators are very reliable workhorses that are thoroughly tested before coming to market. Customers using our machines recognise all these aspects,” said Wilbert Blom, HCME’s excavator product manager. “When you look at our European market share for excavators, we have close to 20% share for the 50-tonne class and up to 30% for the 85-tonne class. Customers for these models demand uptime and performance. They do not want to lose money on excessive maintenance and other issues. The machines need to deliver.”
Blom said that as HCME large crawler excavators have Hitachi-designed and engineered hydraulic systems, the manufacturer has “total control” of their quality.
He continued: “I think we can grow our market share in around 50-tonne class excavators. The market is flattening a bit. Customers are a bit more hesitant on purchasing new equipment. In the shortterm, this may help with lead times.”
Commenting on what quarrying and mining customers can expect from the next-generation large HCME Zaxis-7 crawler excavators, Blom said: “We’ve been able to make some significant improvements to the hydraulic system. This will deliver significant savings on fuel consumption, which equates to lower TCO [total cost of ownership].
“Since 2018, we’ve also had the ConSite oil sensor in our up-to-85-tonne class ZX890-6 model. It’s an oil sensor in the engine and hydraulic system, monitoring engine and hydraulic oil quality 24/7. What is unique about the oil sensor is that it’s Hitachi patented system. It detects various material contamination and the algorithms behind it measures the quality of the oil before something happens. This might, for example, detect an increase in iron particulates in the engine or hydraulic system oil and stop the main control valve from getting seriously damaged, preventing major maintenance work.”
Blom said that HCME had also listened to customers by making the new Zaxis-7
Focusing on another area of improvement, he said: “In 2018 we started supplying Hitachi-branded buckets for excavators, like we have done for some time with our wheeled loaders. Some of our excavator customers had been flagging up to their Hitachi dealer that their bucket attachments didn’t seem to work well with their machines. After exploring the root causes, we were finding that the installed bucket was too big. Now we can safeguard performance by supplying our own buckets.”
Asked about the potential for electricpowered large crawler excavators for quarrying customers, Blom said: “We already have electric-version machines for mining customers that hook up to the grid. I’ve not seen many requests from quarry customers to connect, say, an 80-tonne machine to the grid. If hydrogen fuel cell systems really become commercially viable for quarry machines, that will be interesting. Maybe some hybrid solutions can be developed which are less sophisticated. I think quarrying and other jobsite machines will become smarter, making more use of sensors to further measure productivity and safeguard their uptime. There will also be far more localised spare parts provision.”
Bill Drougkas, HCME’s wheeled loader product manager, said quarrying and mining customers are focusing on easy wheeled loader bucket filling, resulting in fast cycle times and very low total cost of ownership. “There are several sub parameters connected to this: the wheeled loader must be of high quality, come with low fuel consumption and maintenance cost, while also demonstrating an investment in operator cabin comfort, and an absolute focus on safety. With excavators, the machine is standing safely and operating in one area at a time. But for wheeled loaders, they are constantly travelling around a quarry or mine and there are on- and off-highway trucks coming in and going out of the work site. This means safety is of utmost importance.”
Drougkas said the current ZW-6 wheeled loaders have additional safety features compared to their predecessors. “One of these is for example our remote fleet monitoring system, ConSite, that could indirectly inform the operator that their operational behaviour will not result in a long lifetime for the machine. It’s important to note that doing this does not sacrifice in any way the performance of the wheeled loader. An identified problem might be, for example, an operator constantly pushing the brake pedal. Through our global e-Service platform we can detect operator behaviour that is below the average for Hitachi wheeled loaders globally. We can then pass on advice to the operator on how they can change their behaviour. By doing this, machine lifetime is significantly increased.
“We have also invested a lot of time on how to best position the engine on the frame in order to allow direct visibility to the rear two sides of the counterweight. Of course, operators use their rear-view monitor camera, but they are also always looking around as they drive the wheeled loader.”
The ZW-6 wheeled loader range also has improved traction force, said Drougkas, which has increased the filling capacity of their buckets. “Being Hitachi, we are experts in hydraulics, and can match a higher quality powertrain with high-quality components.
“In recent years Hitachi wheeled loaders have also been well received in quarries and mines due to their proven low fuel consumption. It depends on the customer work site and how they are used, but generally current generation ZW-6 wheeled loaders achieve a 10% reduction in fuel consumption than previous generation machines. Some of this is due to improved axle components and reduced friction meaning lower hydraulic losses therefore reducing fuel used to run. Overall, we have seen that the ZW-6 generation machine is very competitive.”
Drougkas said that HCME was also investing heavily in its aftermarket business. “Our Hitachi-branded buckets allow us to give a total solution to our wheeled loader
customers. There are also many initiatives for our dealers, such as how to promote Hitachi Genuine Parts. We are also providing tools like a ‘preventive maintenance cost planner’. This enables dealers and customers to really prepare servicing and maintenance needs in advance, so that when a technician visits a customer work site, they have the correct replacement parts and will not need to make one or more repeat visits. Doing more preventive maintenance also means that customers will not experience unnecessary downtime and cost due to the need to replace major wheeled loader components.”
Highlighting what quarrying and mining customers will see in the heavier upcoming models of the wheeled loaders range, Drougkas said: “They will take the machine performance and health information available to the operator to the next level. This means using a smart monitor to convey key messages via this monitor about operator behaviour and what is happening to the machine. The messages might say: ‘If you do X, you will reduce fuel consumption by Y and increase the lifetime of your machine by Z. It is moving to a kind of artificial intelligence where it comes from machine to operator communication.”
Drougkas emphasised that the design of the upcoming wheeled loaders range will follow Hitachi’s concept to preserve their strong emphasis on safety. The “highly advanced” joystick control of ZW-6 models will be enhanced further on the nextgeneration machines, he added.
Turning his attention to current European heavier wheeled loader line market demand, Drougkas said: “The demand is still there thanks to the number of major infrastructure projects taking place. We are expecting demand to remain stable in 2020.”
In the November-December issue of Aggregates Business we reported on Hyundai Construction Equipment Europe’s (HCEE) launch of its new HL900 A-series wheeled loader range with three Stage V compliant wheeled loaders: the HL940A, HL955A and
the HL960A.
For this issue, Stefan Schwill – HCEE’s wheeled loader product specialist, spoke to us about forthcoming quarrying-suited HL900-A series models. He also discussed HCEE’s plans to develop its market share for heavier, 20-tonne class plus wheeled loader models.
“We will be launching the 24.2-tonne HL970A with a 4.2m³ bucket and 31-tonne HL980A with 5.6m³ bucket models in the first half of 2020, and the 26.5-tonne HL975A with 4.8m³ bucket and CVT (continuously variable transmission) in the second half of next year,” said Schwill. “We also have the HL965 20-tonne Stage IV engine machine with 3.6m³ bucket, but there is no launch date currently for an A-series Stage V version of that model.”
Like the smaller models in the range, the 20-tonne plus A-series wheeled loaders come with an in-cabin menu allowing for three engine operation modes: Power, Power Smart and Economy, offering full engine power or reduced fuel consumption depending on the application. The new-for-Stage V models Power Smart mode in addition with EGR (exhaust gas recirculation) removal is said by Schwill to result in reduced energy losses and up to 5% fuel savings. In addition, the engine performance is optimised to deliver higher torque at lower rpm. This provides another means for improved fuel efficiency, while optimising engine power and improving engine response time.
Schwill said: “All Hyundai A-series wheeled loaders are equipped as standard with a rear-view camera developed in-house. Hyundai also offers an optional reverse-drive radar system, like a car’s, allowing the operator to quickly and reliably detect obstacles within 10 metres during day or night.”
For increased safety on the job site, Schwill highlights Hyundai’s new AAVM (advanced around view monitoring) fourcamera system which is available as an option with Hyundai Stage V A-series wheeled loaders and crawler excavators.
“The system has around view monitoring [AVM] and intelligent moving object detection [IMOD]. IMOD alerts the operator when a person or potentially dangerous object is moving too close to the machine. There are audio and visual alerts at five
in the jobsite office. The heavier A-series wheeled loaders also come with five-speeds and a lock-up function, offering further assistance with fuel saving.
Schwill continued: “A remote door opener allows you to use a small smart key
from Bosch Rexroth. Our Stage V models will only have Cummins engines, which don’t use EGR and have increased engine combustion efficiency. Having only one engine supplier allows Hyundai to connect it through ECD (engine connected diagnostics)
Liebherr’s next-generation 27-tonne TA 230 articulated dump trucks are now in production
Liebherr has launched the first of a new three-strong, next-generation articulated dump truck series, while Terex Trucks has big plans to increase its presence in Algeria’s strong construction sector. Guy Woodford reports
The first of Liebherr’s keenly awaited next-generation 27-tonne TA 230 articulated dump trucks (ADT) has gone into production. From April 2020, the initial production machines will be delivered to Liebherr rental parks and dealer rental parks in Europe, with wider sales to European customers following on in 2021. In 2021, the TA 230 will also be available from dealer rental parks in North America. The TA 230 will be followed by next-generation Liebherr 36-tonne (TA 240) and 41-tonne (TA 245) ADTs in 2023.
Last autumn, Aggregates Business watched a pre-series, next-generation TA 230 ADT being put through rigorous semi-autonomous testing at Liebherr’s cutting-edge test track and development facility in Kirchdorf an der Iller (Kirchdorf), Germany, during the manufacturer’s 2019 information event for the international construction industry press.
During the well-attended event, Werner Seifried, managing director, Research and Development, Liebherr-Hydraulikbagger, gave a presentation on how Liebherr develops and tests its earthmoving machines, citing as an example the TA 230, TA 240 and TA 245 next-generation ADTs.
During a section on the testing element of Liebherr ADT development, he said: “Articulated dump trucks are frequently used in environments where their task is to transport materials over long distances. These roads, often referred to as haul roads, are usually gravel or dirt tracks with rough services. As the usage duration of these haul roads increases, their condition deteriorates, i.e. the number of potholes and bumps rises while the quality of the road worsens.
These haul roads are now simulated on our [Kirchdorf] rough road track. This way, we can simulate realistic conditions in detail and with high-quality reproducibility in tests.”
After showing a video of four ADTs being subjected to partially autonomous, varied ground-profile testing at the Liebherr Kirchdorf facility, Seifried widened his presentation to include all earthmoving machines.
“Before we dispatch our machine, we firstly conduct an internal test for over 100 hours”
“Despite ideal conditions in our development and test centre here in Kirchdorf, tests under real conditions at our customers’ premises are indispensable. Our field test managers in technical testing have a pool of customers at their disposal who have kindly agreed to test our vehicles in their specific applications. However, before we dispatch our machine, we firstly conduct an internal test for over 100 hours. This needs to be passed successfully without any issues.
“It goes without saying that we attempt to enable the broadest possible range of applications and to find out and learn from the special requirements that many customers have. This way, we can plan for all kinds of unexpected and unanticipated
events that may occur in real-life conditions at the site of use.
“For documentation purposes, the data loggers installed in the vehicles are, of course, assessed on a regular basis. In addition, specialists perform examinations specifically at the defined critical points and check the status of crucial components at fixed intervals. Evaluating these documents is indispensable in order to better understand how components are stressed under specific conditions and how they then behave.
“After all product development milestones have been successfully completed, there are no longer any obstacles to the successful start of series production and a long and successful product life.”
Amid falling revenues from oil and gas exports in Algeria, non-oil sectors such as construction are driving the country’s economy. Algeria sees a robust and stable construction industry as a key component for a successful future – so Terex Trucks sees it as the right time to reinforce its commitment to deliver its robust, straightforward articulated haulers to customers across the country.
As one of Africa’s main oil producers, the Algerian economy is heavily dependent on revenues from oil exports. However, the low oil and gas prices of the last few years have weighted on the country’s economic performance. To reduce its dependence on oil, the Algerian government aims to diversify into non-oil sectors such as construction, to drive private and foreign investments.
This year, the total construction project pipeline in Algeria – as tracked by data provider GlobalData – stands at £109 billion (DZD 16.3 trillion). Due to a focus on residential construction and building affordable houses, GlobalData expects the residential construction market to account for 38.8% of the construction industry’s total value in Algeria in 2023. The development of transport infrastructure is also expected to further drive the construction industry.
The upward trend in investment in infrastructure, residential and energy construction projects in Algeria coupled with the recent investments Terex Trucks has made in its products, people, processes and facilities make it the perfect time for the company to reinforce its commitment to customers in the region – together with Matera, Terex Trucks’ dealer in Algeria. A successful collaboration that spans 15 years,
Terex Trucks and Matera are reaching out to new customers, introducing them to the robust articulated haulers, the TA300 and TA400.
“At Terex Trucks, we are dedicated to building powerful articulated haulers,” said Etienne Lalande, regional sales director at Terex Trucks. “That’s what we are specialised in. Our customers in Algeria know that they can rely on our haulers even in the toughest environment. Our dealer Matera is particularly strong in providing excellent service and support to customers, and together we want to bring our haulers to more customers in the region.”
“With our deep knowledge of Terex Trucks’ machines and our broad network, we maintain great relationships with our customers and stay in touch with them at all times,” said Benoit Strauven, managing
director at the Matermaco Group, Terex Trucks’ dealer in the Benelux region and parent company of Matera. “In a country like Algeria, good geographical knowledge and strong local connections are key. It’s a vast country – the last Terex Trucks hauler we sold was delivered to a place that’s farther away from the Algerian capital than Brussels.”
Algeria’s economy is dominated by public companies which use Terex Trucks’ articulated haulers for construction work, infrastructure developments and earthmoving projects. Customers appreciate the simplicity, quality and reliability of the haulers. Terex Trucks has recently made significant investments to ensure their machines support customers in the toughest applications. Towards the end of 2018, the TA300 was upgraded and it’s now manufactured with the latest EP320
transmission. The updated machine delivers a 5% improvement in fuel efficiency, a 5 km/h increase in speed to 55 km/h, an extended maintenance period and enhanced performance when compared with the previous model. All of this means that customers can be more productive, achieving faster cycle times, lower cost per tonne and reduced carbon emissions.
The TA400 boasts a heaped capacity of 23m³ and is powered by a high-performance, fuel-efficient engine that develops a gross power of 331kW and a maximum torque of 2,255Nm. The planetary gear transmission provides smooth, efficient gear shifting for optimized fuel consumption and reduced cost of operation. Ground-level test points and a fully tilting cab, combined with an electronically raised hood, ensure ease of service and reduced downtime. AB
Two companies in Turkey and East China have both updated their conveyor systems to achieve greater efficiency and ease of maintenance. Liam McLoughlin reports
Turkey’s recent building boom has led to growing demand for cement, and manufacturers in the country are modernising their cement production methods.
One of these is Göltas Cemento, located close to Isparta in western Turkey, approximately 130 kilometres north of Antalya. The company opted for modernising its kiln and increasing the performance. An increase from 250 to 400 tonnes per hour of the conveying-technology capacity was required, for a chain apron conveyor that transports the clinker from the kiln-cooling system to the silo.
To achieve more economical production, Göltas Cemento has been increasingly opting for alternative fuels in recent years, which meant that the content of fines particles also increased continuously. The existing conveyor already transported high quantities of material, and the process had become extremely dirty, with personnel constantly needed to perform cleaning work.
To find an efficient solution Göltas Cement turned to its long-standing partner,
system provider Beumer Group. Germanheadquartered Beumer has supplied two clinker transport systems and four belt bucket elevators over the course of their existing partnership. The project phase began mid-2015 and the contract was awarded in the beginning of 2016, followed by the installation and commissioning in the autumn of that year.
“For a more powerful chain apron conveyor, we would have needed to take down the entire system including the building structures and the concrete tunnel,” said André Tissen, sales manager for customer support at Beumer Group, who was responsible for the project with his team. “This wasn’t necessary when opting for the belt version. It reaches double the conveying speed, so that the Beumer Group engineers could design the system for an increased capacity while keeping the same width. The conveyor bridge and the selfsupporting steel structure, as well as the concrete foundations remained.”
According to Tissen, Göltas Cement was able to considerably reduce costs and put
the system quickly into operation.
“The silo is 50m high. In order to overcome an inclination of 40 degrees, we installed a steel box conveyor,” he said, adding that it releases almost no material to the environment, despite the higher content in fines particles, which is designed to create a cleaner work environment.
Tissen says that apron conveyors are particularly efficient for the transport of clinker. In general, the clinker should cool down to the ambient temperature plus 80°C, but during the process a so-called ‘raw meal flash’ can occur in the shell section of the preheater tower, caused by breaks in the kiln outlet sealing. “It doesn’t happen often, but it does happen. It can’t be completely avoided,” Tissen explained. Within a few seconds, several tonnes of raw meal or clinker run through the cooler. The material cannot cool down and arrives on the conveyor at extremely high temperatures.
“The cement plant operators are still not able to ensure with 100% certainty that the material does not leave the clinker cooler at temperatures of 500 to 800°C,” said Tissen.
He adds that Beumer Group apron conveyors are completely heat-resistant. The specific design of the cells allows safe, low-friction transportation of any hot material. Sealed and overlapping side walls and bottom plates in the cells prevent the clinker from exiting and minimise the escape of dust. Operators get the Beumer apron conveyors SZF and GSZF with cell-width gradations from 500mm to 2,000mm, centre distances of more than 250m and conveying capacities of over 1,300m³ per hour.
LEFT: Track-mounted designs allow components to slide in and out easily for maintenance
Beumer claims that the use of its steel wire belt instead of a chain lowers maintenance costs and extends maintenance intervals. Chains can also break, if preventive maintenance is not performed properly, which will lead to the conveyor collapsing. “The belt with the steel wires only ages and the rubber becomes brittle, but it would never completely break,” said Tissen. Lubrication is also not required for the belt, whereas it is used frequently on a chain, if for no other reason than to reduce noise levels.
Grease and oil are not only a cost factor, but are also detrimental to the environment and the conveyor. The clinker dust gets stuck on it and settles in the chain links, which accelerates the wear and tear. Beumer’s belt apron conveyors are in operation for nearly 150 companies.
In Eastern China a coal plant had belt damage, spillage and dust issues at two conveyor transfer points with outdated equipment in the loading zones. Raw coal ore was loaded onto the 1,000mm-wide belts traveling at 500 fpm (2.56 mps). The first chute had a 5m-high drop chute that loaded into a 12m-long loading/stilling zone. The second chute had a similar drop, discharging into a 26m-long loading/stilling zone.
Suffering from an old design, the belts were supported by impact idlers and a troughed roller system, neither of which was equipped to cope with new production demands. Equipment failures happened regularly, and without proper accessibility for routine maintenance, long periods of downtime were common. Belt sag created gaps between the belt and rollers, causing fugitive dust emissions throughout the facility.
Inadequate impact control led to spillage becoming entrapped between the belt and tail pulley, damaging them both. Excessive downtime, costs for cleanup and equipment replacement seriously impacted profitability. Managers at the coal plant sought a solution that better protected the belt, sealed the chute from dust and spillage, and offered easier inspection and ongoing maintenance.
Technicians from the Chinese division of bulk materials-handling solutions provider Martin Engineering were invited to perform an on-site assessment and suggest an affordable solution.
After offering a detailed proposal, the team installed modern equipment that addressed the issues on both conveyors. The first chute was equipped with a track-mounted impact cradle to improve loading and protect the belt and tail pulley. In addition, slider cradles for smoother centering were installed, along with a full-length apron seal to prevent dust and spillage from escaping. A comparable solution was installed in the longer chute, with added cradle support down the entire length. Both chutes featured non-powered dust-bag systems to collect emissions.
Since installation, Martin Engineering says that spillage around the loading zones is under control and dust emissions have been drastically reduced. Operators report that a considerable drop in equipment failure rates has resulted in a substantial increase in productivity. Contributing to the success was workers’ ability to easily inspect and service components by sliding them out and servicing them outside of the conveyor.
“After more than 75 years of working with bulk handlers all over the world, Martin Engineering has discovered that ‘access’ is a common element for both safety and productivity across all industries,” said Daniel Marshall, product engineer at Martin Engineering. “By adding easy access and monitoring in the design phase, equipment can be better maintained using less labour, leading to reduced downtime. This is reflected in the cost of operation, offering a better overall return on investment.”
Many conveyor transfer points still have an antiquated roller system tasked with
absorbing impact and centering the cargo, according to Marshall. “These components often break and seize, causing friction and a potential fire hazard,” he said. “To replace them, several workers must remove the skirtboard and break the plane of the conveyor to reach across the stringer with heavy tools to assess and repair equipment.”
To reduce maintenance time and labour, improve safety and extend equipment life, operators should consider track-mounted impact cradles and belt support cradles. Located under the skirtboard and mounted with rugged steel assemblies, the cradles feature large impact-absorbing UHMW polymer ‘box bars’ engineered with smooth surfaces that the belt can slide across with little friction or belt wear. These assemblies can be pulled out by a single worker and – working safely from outside the conveyor and using only a single tool – the box bars can be simply removed and flipped in a matter of minutes to double the service life.
Along the cargo path in the settling zone and beyond, retractable idlers support the belt and maintain the trough angle. Exposed to the punishing environment, gritty dust and extreme weather, rollers can seize over time. Often set closely together in the loading zone to avoid belt sag, slideout/slide-in roller frames permit workers to perform idler service outside of the belt plane without the need to raise the belt or remove adjacent idlers.
“Wear parts such as belt cleaner blades need to be monitored, serviced or changed regularly to prevent carryback from causing dust and spillage along the belt path,” Marshall said. “However, blade adjustments and changes can require several hours of downtime.” AB
Inspection doors and track-mounted components facilitate maintenance for extended equipment life
ALLU’s M-Series Transformer screener crusher
Finnish company ALLU has big growth plans aided by the growing popularity among quarrying and other industry customers of the firm’s Transformer screener crusher. By reducing the number of process steps needed, the hydraulic attachment helps achieve maximum efficiency on job sites, across all kinds of applications.
Aggregates Business spoke to Jeroen Hinnen, ALLU sales director, to find out more about the firm’s plans for 2020 and beyond.
Commenting on the current state of the global quarrying attachments market and ALLU’s position within it, Hinnen says: “ALLU can help benefit customers by providing a new, cost-efficient (and improved) way of crushing material by, for example, pre-screening it before it is fed into the crusher. This simple process eliminates fines and therefore will increase throughput and lower wear in the crusher. Customers also benefit from removing big rocks and large particles from harming the conveyer belts with the ALLU Transformers.
“Competition in the quarry market comes mainly from different methods used. ALLU, although present in the quarrying market for many years, is in many ways a rather new name to this market and proving that ALLU reduces Capex [capital expenditure] and maintenance needs to be proven in practice. That said, our Transformers are now working globally in many soft rock quarries and mineral surface mines where the results have been exceptional, as shown by the number of repeat purchases.
“We respect all manufacturers, as we know how hard it is to make the right
product for the right application, but in our ‘attachment’ business, we do not feel that we really have a like-for-like competitor due to the advanced nature of our solutions.”
Hinnen says ALLU works with professional partners all over the world, making it possible for the company to stay close to and provide “true added value” for its customers.
“The range of applications for ALLU is wide to say the least. In cases of selective use of material, the primary optimisation would be separating waste rock before transportation - eliminating wear, need and cost of transportation. With other typical cases, ALLU benefits customers with lowered running and maintenance costs and enhanced material separation which leads to
ALLU sales director Jeroen Hinnen
The global screening buckets and attachments market is competitive, with innovation and aftermarket support key features of many leading manufacturers’ product offer.
improved (customer) business performance. In all of these cases, everything starts from understanding the customer’s process at the site. By finding the bottle necks, we can really add value.”
Focusing on the popularity on ALLU’s M-Series Transformer range with quarry customers, Hinnen says the crusher screener buckets benefit from being a “unique” example in the industry. “The best customer testimonials come from surface mines where hardened, lumped material needs to be returned to a flowing, granular format. In these kinds of applications, the production has reached 600 tonnes per hour and has been a highly cost-efficient solution to the problem for the customer.”
Hinnen says ALLU has enjoyed strong growth in recent years, both in terms of sales volume and geographical footprint. A huge modernisation of processes in the back office has, he notes, also contributed greatly to the manufacturer’s success.
Asked about the success of his first couple of years as ALLU sales director, he replied: “Personally, growing the sales team and people has been the greatest achievement. This business is all about the people and the team serving the customers. When we’re able to grow the people, we’re able to have happy customers.
“For ALLU, growth opportunities exist in numerous areas and applications. Being able to facilitate the growth and support the team to grow strongly further is my main aim.”
Speaking about how his experience and knowledge gained in previous roles have assisted him in his senior executive role at ALLU, Hinnen says: “I guess life is about
lessons learned; some bring great memories, and some provide great food for thought. I do remember many wonderful people who wished to be of support along the way. The international market has its ways and tricks and when you have somebody walking side by side with you, that’s the greatest gift I feel anybody can receive. I’ve been very lucky with those supportive people. Whoever you work for, or whatever you do in life, you must learn. During my time with other companies I learnt many things daily, but the global nature of business, dealing with unique individuals and being exposed to some of the latest thinking, have certainly stood me in good stead.”
Hinnen stresses how ‘Customer First’ is one of the three guiding ways of working with ALLU. “ALLU invented the methodology of the transforming and processing attachment being used today and innovation is in the DNA of the company. There are many projects in the pipeline, and I’m convinced all of them are for the benefit of our customers. We will be introducing some
Commenting on how ALLU’s manufacturing capabilities and footprint have evolved during his time as sales director, and future company plans in this area, Hinnen says: “Strategically ALLU wishes to work together with professional partners in all fields of the business and this applies to manufacturing as well. For ALLU, being a Finnish family company, Finland has a special place in our hearts. Thus, we have strong partners in Finland. However, the business is highly competitive, and ALLU needs to follow the most cost-effective and productive path. We have a duty to our shareholders, stakeholders, employees, partners and customers to run a highly efficient operation.”
The aftermarket side of ALLU’s business is very close to Hinnen’s heart, as he explains: “ALLU Support is one of the major attributes of our business. We have a specialist team in charge of the customer service, which includes training, effective equipment usage, and parts. We ensure our dealers are stocked with the most commonly occurring wear
from the equipment and can advise the customer how to best use their ALLU. If the dealer requires more specialist advice, we possess a global team who literally travel the world visiting customers and dealers. We have found this to be particularly appreciated.
“In 2019, ALLU introduced the ALLU APP, which provides customers and dealers with access to all ALLU information, data and support. Safety and speed of information sharing are very important when it comes to supporting customers. Therefore, the ALLU APP was developed, which we believe was a first in the world in our niche business.”
German aggregates supplier TBS Transportbeton Schüssler (Schüssler) has invested in Hitachi rock buckets to support its quarrying operations in Kerpen-Manheim. The company is also using a fleet of four Hitachi wheeled loaders at its two sites, from which it supplies 600 types of readymixed concrete, sand and grain from several locations across Germany.
Schüssler’s two ZW310-6s and two ZW370-6s have been equipped with Hitachi rock buckets, which are designed for heavyduty work and loading of rocks. They are also said to be optimised for good penetration and breakout performance. On site, the ZW370-6 wheeled loaders are excavating material and transferring it to a conveyor. Around 200m³ of filtered material is loaded onto trucks by each ZW310-6 per eight-hour shift.
Said by the Japanese manufacturer to be exceptionally reliable and durable, Hitachi buckets have been designed to enhance the performance of Hitachi wheeled loaders in a wide range of working conditions. By contributing to maximum productivity and uptime on the job site, they not only help to increase profitability, but also provide peace of mind to companies who want to get the most from their machine.
Schüssler selected the Hitachi buckets based on the advice it received from authorised local dealer Kiesel. “It recommended them based on our requirements, and we trust in their opinion,” said Schüssler’s executive director Jochen Wonka. “We have a very good relationship with Kiesel. They provide an excellent
service, provide us with everything we need, and the Hitachi wheeled loaders have proven to be very reliable.”
Simex CEO Mirco Risi spoke of the continuing success of the Italian manufacturer of hydraulic attachments for earthmoving machines in a festive December 2019 message praising the “efforts and excellent work” of the company’s employees, associates and distribution network.
“2019 is drawing to a close and we look back on a positive year, considering that after years of double-digit growth our numbers stabilised with respect to 2018,” said Risi. “This success is a result of various factors that, depending on market demand, have led our products to be winners.”
Risi said that while strengthening of Simex’s distributor network and the company’s work to support it had a positive impact on the firm’s year end, he was convinced that the result was also thanks to the constant R&D focus on new products to expand the company’s attachments range, or variations on existing products.
He continued: “Another factor I believe very important for maintaining growth is the ability to adapt to the constant variations in the markets and the demands of our customers, who are always in search of attachments that provide a concrete response to their application requirements, but without shortcuts when it comes to reliability, productivity and profitability.
“Towards that goal of delivering a better and faster response to the market and users’ needs, 2019 saw us making an important investment that in early 2020 will materialise in the completion of our new 7,000m² structure containing a large area for loading/ unloading and sorting of materials, a warehouse with high storage capacity, new offices, and, in a second phase, the new painting plant. This new structure meets two needs: first, it will allow us to avoid production slowdowns caused by our suppliers’ longer delivery times, especially regarding hydraulic components; and second, it will lead to faster order fulfilment. Over the last few years we have noticed an overall tendency on the part of users to place orders after having the certainty of the work order, for us which entails accelerated turnaround times. As a result, having more attachments ready for delivery means a concrete support to our customers throughout the world.
“Altogether, 2019 was a positive year that saw us making strides on several fronts to assure our growth and performance on all markets where we are present. On that premise, our success should not be viewed as a point of arrival, but as a step along our path.”
A Simex VSE 20 screening bucket has been recently performing soil screening for green areas as part of a major renovation of a traditionally designed Lombard farmstead in Trivolzio, near Pavia, in south-west Lombardy, northern Italy. Ripristina, a construction and renovation contractor, is turning the farmstead, which also contains a building dating back to the Middle Ages, into a mixeduse residential and commercial complex.
Giacomo Negri, Ripristina’s technical manager, said the VSE 20 took care of all the project’s screening problems. “We were looking for a screening system that would achieve good productivity and allow for a certain amount of mobility. We excluded a mobile screening unit due to space restrictions, but on the suggestion of CGT Edilizia we solved the problem by renting a CAT 313F excavator mounted with a VSE 20 screening bucket. Besides its great productivity, this solution afforded us great mobility on the job site, a critical factor for screening in all the areas designated for green spaces.”
MB Crusher’s MB-S14 screening buckets were used for site preparation works for the five-star waterfront resort in Salwa, Qatar, which opened in 2019.
The MB-S14s were used with Hyundai 220LC crawler excavators during works aimed at reducing environmental impact by using material already available at the site.
This Salwa luxury resort comprises a hotel managed by Hilton Hotels & Resorts, 2800m² of health clubs and spa, several outdoor pools, meeting rooms for events, 13 fine dining restaurants and 90 villas. AB
Bärnreuther+Deuerlein has been using environmentally sound retreads at its seven quarries in Germany
Customers who buy environmentally sound off-the-road (OTR) retreads are being given discounts and a certificate attesting to the amount of raw materials they are helping to save. Liam McLoughlin reports
Bavarian quarry operator
Bärnreuther+Deuerlein has been rewarded and received a certificate attesting to the environmental benefits created by its choice of premium quality OTR retreads.
Until the end of 2019, any end user from the DACH countries (Germany, Austria and Switzerland) purchasing at least four Marangoni OTR retreads from a selection of specific tyre sizes (up to 24.00R35), obtained a discount of up to €90 per tyre. In addition, the eligible customer receives a certificate from the company attesting to the savings in terms of raw materials achieved with their sustainable choice.
The document was delivered to Frank Eichler, purchase - QS - plant manager at Bärnreuther+Deuerlein by Anton Zehner, OTR tyres area manager at Marangoni. It declares that, having opted for the 24.00R35 MDT retread, the company has preserved 550 kg of material per tyre, equivalent to 64% of the original product weight.
Bärnreuther+Deuerlein places careful focus on the environment and has been relying on the retreading of its tyres for many years, thereby helping to save significant amounts of resources in addition to reducing their operational costs.
The enterprise was founded in the 1930s and employs 150 workers. It operates seven quarries in Bavaria, where it produces quality-controlled gravel material for road construction, asphalt pavement, concrete manufacturing, as well as for landscape-design projects.
Bärnreuther+Deuerlein has been working with Marangoni for almost 10 years. At the beginning of the cooperation a delegation visited the Italian plant in Rovereto to observe the retreading production.
Eichler commented on the visit: “During our stay, we also took an in-depth training on the OTR-casing selection that provided us with great best practices for tyre management. ”
In order to make the most out of its tyres, Bärnreuther+Deuerlein ensures that they run out in good conditions with recommendations from Marangoni and on-site regular checks.
The company says it is committed to continuously improving the efficiency of its operation by using tyre-monitoring sensors and raising awareness among its drivers of optimum tyre use, thanks to specific training activities and rewards for the most ‘green’ driving performances.
In addition, Bärnreuther+Deuerlein enforces a tyre policy which always involves the combination of premium new tyres and Marix OTR retreads supplied by Marangoni. The latest 24.00R35 Marix MDT retreads supplied to the Bavaria-based firm were mounted on its Komatsu HD605 rigid dump truck. The MDT pattern is particularly suitable for use on dump trucks operating in heavy-duty applications, such as those at the Bärnreuther+Deuerlein quarries. The tread compound developed by Marangoni for this product is characterised by a very low heat development, which is designed to ensure optimal hourly performance.
Romanian truck retreading company
PneuMaxx, which operates as Bedelco East Europe, produced its 100,000th retread using Marangoni’s RINGTREAD system in October 2019. The event was marked with a commemorative plaque presented by Daniel Brichta, area manager of Marangoni Retreading Systems to Mihai Ionescu, executive director of Bedelco East Europe.
PneuMaxx was founded in 2005 and, since the beginning, has focused on premium quality truck tyre retreading using the RINGTREAD System.
Ionescu commented: “In 2020, we’ll keep focusing on high-quality retreading, since it is an important part of our business.” Bedelco East Europe owns a retreading facility with a capacity of 18,000 retreads per year, reached after the addition of a second TRM autoclave and a shearography machine. The company operates through a network of four sales outlets located in Bucharest, Arad, Constanta and Ploiesti.
At the forthcoming 2020 ConExpo construction show in Las Vegas (March 10-14), Continental is introducing several new and improved tyre products to cover complete solutions for the construction and other on/ off-road industries.
The company will highlight its newest technologies including three new truck tyres, off-road tyres (including a new General Tyre bias line), a large mining tyre, conveyor belting products, industrial fluid hose, air springs, rubber tracks and an interactive truck-cab model demonstrating in-cab technologies as well as other cabin elements and materials.
Bridgestone Specialty Tire Manufacturing (Thailand), a subsidiary of Japanese multinational Bridgestone, has held an opening ceremony for its new factory for radial tyres for construction and mining vehicles in Thailand. The opening ceremony last October was attended by executives as well as members of the Board of Investment for Rayong Province, and representatives from the Japanese Embassy.
Italy-based OTR tyre maker BKT has renewed its agreement as the official and exclusive tyre manufacturer for the Monster Jam truck competition. The partnership, started in 2014, will continue for a further six years.
The renewed agreement with Monster Jam promoter Feld Motor Sports will see BKT as the official tyre manufacturer at the more than 100 Monster Trucks events being staged in the US and around the world this year.
BKT says its event sponsorship has generated a big increase in brand awareness for the company and its tyre products. AB
No matter how challenging your needs, EARTHMAX SR 41 is your best ally when it comes to operations that require extraordinary traction. Thanks to its All Steel radial structure and the special block pattern, EARTHMAX SR 41 provides excellent resistance against punctures and an extended service life. In addition to long working hours without downtime, the tyre ensures extraordinary comfort.
EARTHMAX SR 41 is BKT’s response to withstand the toughest operating conditions in haulage, loading and dozing applications.
europe@bkt-tires.com
Welcome to the Aggregates Business magazine preview of the CONEXPO-CON/AGG 2020 exhibition. Over the next six pages, we will highlight all the key product launches and North American debuts during what promises to be the event’s biggest-ever showcase.
Metso says that its new MX3 boosts crusher productivity and reduces operating costs with a design optimised for mid-sized quarries
Premium aggregatesprocessing plant maker Metso is showcasing its innovative MX3 crusher and a special Lokotrack mobile crushing plant equipped with an MX4 crusher.
Metso’s cutting-edge MX Multi-Action conecrushing technology has been embraced by quarry operators globally, with nearly 100 units sold worldwide.
Metso’s new Lokotrack ST4.10 mobile screen is a high-capacity screening plant for quarrying, which further adds to the Finnish company’s range of hybrid equipment.
A pioneer in collecting and utilising operational data to optimise machine
performance, Metso’s Metso Metrics Services package can manage and monitor a Lokotrack fleet to optimise utilisation, reduce surprises, and keep costs in check. It is backed by Metso’s industry-leading portfolio of parts, including the new Contender Series for thirdparty equipment, upgrades, and worldwide service and partner network.
Metso is also introducing the Nordtrack product family with purpose-designed and field-proven features for general contractors and small- to medium-capacity aggregates producers. The new Nordtrack range includes track-mounted crushers
and screens as well as track-mounted and wheelmounted stacker conveyors for recycling, demolition and small quarries.
Kleemann says that its latest mobile crushing and screening equipment offers versatility for customers.
The latest MOBICAT MC 120 Z PRO jaw crusher and MOBISCREEN MS 952 EVO mobile screening plant are said to offer high-quality output, combined with high throughput for more efficient operations onsite. Highly mobile for units in their capacity classes, the units can be commissioned quickly onsite as well as being folded down for transport again with minimum effort.
A tough, long-lasting truck body designed to suit any hauler is another Metso product introduction.
Lightweight and robust, the design can help to boost payloads and productivity. According to the firm, its innovative Metso Truck Body can allow customers to haul more with fewer truck cycles.
The complete solution is available for all major off-highway truck models used in quarrying and mining operations. www.metso.com
Effective diagnostics allow users to ensure that the units are maintained efficiently, while servicing is said to be easier due to grouped service points and extended intervals. www.kleemann.info
Versatility and ease of transport are claimed for Kleemann’s MOBISCREEN MS 952 EVO mobile screening plant
Sandvik says that its CH840i cone crusher features mechanical upgrades, connectivity, advanced automation and rebuild possibilities.
Advances also include predicting performance, maximising uptime and low cost of operation. The crusher comes with the firm’s sophisticated Automation and Connectivity System (ACS) as standard. This package can continuously monitor and optimise crusher performance and control the complete lubrication system, increasing uptime and reliability.
Connected to My Sandvik, Sandvik 800i crushers allow managers
and operators to make decisions and identify areas for improvement, increasing uptime and availability.
Meanwhile the new SJ circular motion screen range is specially designed for extra heavy-duty, medium- and fine-screening applications. This inclined screen range suits screening after primary and secondary crushing as a splitter screen to divide flows within a plant and for final screening of a finished fraction.
Sandvik’s UJ440i mobile jaw crusher is said to be sophisticated, fuel-efficient and user-friendly. The firm claims that the machine is a high-quality, robust and reliable unit that is well-proven in an array of
Finnish firm ALLU is offering an expanded range of hydraulic attachments, with existing models also benefiting from major improvements.
The versatile units can be used with an array of carriers such as excavators, wheeled loaders and skid steers.
The firm says that its products offer a one-stop-shop for screening, crushing, aerating, mixing and loading operations. It also says that this helps boost profitability as less material goes to landfill, lowering haulage costs and landfill fees. The re-use of material on site also means that there is no need to purchase virgin material due to the recycling of left-over materials.
climactic conditions. New technology means that the UJ440i is automatically monitored by the control system that operates the unit, helping optimise production.
Sandvik claims high performance for its Leopard DI650i downthe-hole (DTH) drill rig.
This machine has been designed for demanding high-capacity production drilling applications in large surface-extraction applications. In addition to a powerful engine and compressor, Leopard DI650i benefits from a new iCAB cabin that offers efficient ergonomics. www.sandvik.com
Simex’s current VSE screening bucket range comprises the VSE 10, VSE 20, VSE 30 and VSE 40 models compatible with 8-45-tonne excavators with load capacities ranging from 0.4m³ to 1.8m³. Independent of model, all the screening buckets feature easy loading, simple use and high productivity. In addition, the exclusive Simex patent is said to allow a rapid size adjustment of the material to be screened in only a few seconds via a control in the operator cab.
Simex says that thanks to its patented system, the Italian manufacturer’s screening buckets are the only ones that enable output size adjustment even when emptying material loaded into the same bucket without long downtimes or complicated mechanical procedures. This is said to ensure optimum productivity and profitability.
The VSE range also offers excellent levels of production due to the rhomboid-shaped elements with disks in varying diameters that make up the shafts. This specific shape of the tools produces an intense whirling of the material to be screened, all to the advantage of hourly productivity. www.simex.it
The company says that its Transformer range now offers improved performance. The DL
thinnest blade model), while the DH 3-17 uses 16/32 TS blades, the DH 4-17 uses 25/50 TS blades
3-20 uses 50mm TS blades. The company says that its innovative TS blade structure is a modern development for the screener/ crusher market. According to ALLU, it offers new levels of efficiency and productivity and will further enable customers to use their Transformer units in more than one way.
Meanwhile the firm says that its Processor is a power mixer attachment that converts an excavator into a versatile tool capable of penetrating and mixing a variety of difficult materials. Powered by the excavator’s hydraulic system, the Processor 300 HD can reach difficult or soft areas to mix materials.
www.allu.net
CDE has added new enhanced features to its Combo all-in-one wet processing & water treatment system
CDE is showcasing its latest Combo all-in-one wet processing & water treatment system.
The patented Combo – said to be world’s first all-in-one wet processing plant – was unveiled at bauma in April 2019. It was the first fully integrated, modular, patented turnkey sand classification and water treatment solution for the production of premium manufactured sands.
The latest model in the Combo range has a number of enhanced features that CDE says have been specifically designed to enable operators in the Americas to capitalise on new opportunities.
Lower power consumption complemented by claimed industry-leading water treatment and management allows customers almost total independence of water supply with up to 90% of process water
Terex FM UltraFines plant is said to guarantee efficient management and recovery of ultrafines material from wastewater streams produced during material washing processes. The ultra-fines recovery unit from Terex Washing Systems can process up to 450m³ per hour of slurry, recovering material as low as 40 microns. This reduces the volume of solids entering storage ponds or water treatment plants.
Bringing together a centrifugal pump, a hydrocyclone cluster and a high-frequency dewatering screen on one chassis, the FM UltraFines also boasts an innovatively designed conical tank and anti-turbulence system, an essential element of ultra-fines recovery.
Part of Terex Washing Systems (TWS), Terex AquaClear Water Management Solutions (Terex AquaClear WMS) offers a full portfolio of water management equipment including clarifying
tanks, flocculent dosing systems and filter presses, creating a onestop solution for washing and water management.
Terex AquaClear WMS is supported by a dedicated technical team consisting of a product manager, engineers
recycled for immediate re-use in the system.
Importantly, the Combo is portable and incorporates all fi essential processes – feeding, sizing, sand washing, stockpiling and complete integrated water management – onto one compact and modular chassis. With a 30% reduced footprint compared to traditional setups it requires less civils expenditure & planning requirements. www.cdeglobal.com
MAJOR is introducing the Flex-Mat Sensor to its range of products for highperformance screening media. This vibration datameasurement tool allows users to review results and fine-tune a screen without shutting down the equipment. The appcontrolled vibration-analysis sensor allows fast readings of screen box vibrations and generates a report that can be sent or reviewed. The design also provides data without the requirement for a plant shutdown for sensor
and applications specialists, together with a new, cutting-edge laboratory specifically designed for material testing and sample pressing. This ensures optimum equipment selection and specification for customers. www.terex.com/washing
the single sensor to the Flex-Mat Sensor app on a smartphone before placing the sensor on one corner of the machine. The user moves the sensor to each corner of the machine and information is then delivered to the phone in seconds. Data is stored locally for and viewing in areas with cellular limitations. Once a signal is available, the information uploads to MAJOR’s cloud service where it is viewable from a web browser. Historical equipment performance data is also viewable through the cloud. The sensor measures g-force, stroke, rpm and orbit, including lateral movement. Producers can use the data to monitor and fine-tune screen box performance as well as make parameter decisions. The data can also give indications of what kind of screen media would best suit the machine. Though the sensor is not meant to serve as a diagnostic tool, the information can point to possible problems.
www.majorflexmat.com
Caterpillar says that its advanced new 325 and 395 excavator models offer increased efficiency. According to the firm, sophisticated engine technology and an advanced control system have been fitted to the new 325 medium excavator.
These features help to reduce fuel consumption by up to 25%, while a precise combination of lower engine speed and large hydraulic pump pressure and flow delivers more work/unit of fuel. Extended maintenance intervals mean that the new 325 offers more productivity while reducing maintenance costs by up to 20%.
The new 395 excavator is built to move material more quickly and efficiently.
With 10% more swing torque and 10% more stick force than the model it replaces, the firm says that operators can achieve faster
cycle times with bigger buckets for greater groundbreaking power and production. Cat PAYLOAD is also offered as standard, allowing operators to validate production at the end of every shift. The machine is said to be twice as durable structurally than previously, allowing a longer service life. In addition, extended service intervals will help to lower maintenance costs by up to 20%.
Caterpillar claims to have improved the performance of its highly successful 725 articulated hauler, providing faster cycle times and better productivity.
New cab features make the machine easier to operate over a full shift and include assisted hoist, automatic retarder control and advanced automatic traction control. www.cat.com
Hitachi Construction Machinery says it has increased tractive effort by more than 30% on its ZW310-6 and ZW370-6 wheeled loaders.
“This technological advance is accomplished by creating more advanced software,” said Mel Wade, Hitachi applications engineer. “The end user will experience the difference when digging, dozing, climbing hills, or other high rimpull-requiring applications.”
In the larger Hitachi ZW370-6 and ZW550-6 loaders, the Traction Control System (TCS) can be operator-activated and deactivated via the display main menu. As these machines are less likely to move from site to site, this is a ‘set and forget’ feature. In the smaller,
compact hydrostatic Hitachi wheeled loaders, the tractive effort is regulated with a TCS switch. TCS is useful for snow applications, as well as muddy environments, because it eliminates unnecessary tyre slippage and increases tyre life.
“It’s an intuitive system that balances hydraulic power consumption with powertrain consumption,” said Wade. This system maximises the use of the available power. The software collects real-time data, such as hydraulic pressure, engine torque, and application demand. TCS determines the appropriate balance to make the wheeled loader as efficient as possible for that situation. www.hitachicm.com
The 90-tonne crawler excavator is equipped with a 603 hp (450kW) Volvo D16 Tier 4 Final engine that delivers high torque at low rpm.
The machine is designed for fast and efficient on-site production. Volvo says that pairing the EC950F with the company’s A60H articulated hauler can enable customers to realise extreme productivity potential. The
EC950F fills the 54-tonne, 33.6 m³ haul truck in just four bucket passes, with an average cycle time of 20-25 seconds.
Volvo’s optimised hydraulics are designed to deliver constant high pressure across each phase of the digging and lifting cycle. The hydraulic system increases pump power for fast and smooth operation, while the electro-
hydraulic system controls on-demand flow and reduces internal losses in the hydraulic circuit. The EC950F also comes with a boom-swing priority valve which adjusts the priority of hydraulic flow between boom-up and swing so that truck-loading cycle times can be set to truck-loading working conditions.
Volvo’s ECO Mode is designed to help the EC950F achieve outstanding fuel efficiency while the integrated work mode allows operators to choose the best work mode for the task at hand: select from I (Idle), F (Fine), G (General) and H (Heavy).
To boost machine versatility, the attachment management system can store settings for up to 20 different attachments, enabling the operator to pre-set hydraulic flow and pressure through the in-cab monitor. Smart features such as the optional Dig Assist – powered by Volvo Co-Pilot – are designed to assist the operator in digging more efficiently. www.volvoce.com
Metso
Töölönlahdenkatu 2
00100 Helsinki Finland
www.metso.com
MARKETS SERVED
Metso is a world-leading industrial company offering equipment and services for the sustainable processing and flow of natural resources in the mining, aggregates, recycling & process industries and serve our customers all over the world.
TARGET CUSTOMERS
We focus on innovation and technology to provide more sustainable solutions, efficiency and productivity to our customers in the quarry, mining, recycling and flow control industries. At the heart of Metso is our drive to make the big difference to our customers.
PRODUCTS AND SERVICES
Our products range from mining, aggregates, and recycling equipment to industrial valves and pumps including services that cover their whole lifecycle.
Dependability matters. Choose the brand known for it.
In the world of construction, dependability matters. At Metso, we’ve turned our 150+ years of crushing and screening experience into solutions that aggregate producers and contractors all over the world depend on to increase production and profitability.
At CONEXPO/CON-AGG 2020, we are proud to present our new compact size Nordtrack™ mobile range for recycling, demolition and small-scale aggregate production.
Experience our latest innovations and special previews:
• Lokotrack® ST4.10™, a new large mobile screen
• Lokotrack® LT4MX™ special edition for ConExpo
• Metso MX3™ cone crusher and crusher automation
• NW™ Rapid portable units for North America
• Metso Metrics Services for remote monitoring and management
• Hammerless attachment system for new generation polyurethane screen panels
• Metso Trellex™ Poly-Cer liners, a unique design with ceramic inserts
• Metso Truck Body, a lightweight haul truck body that lets you haul more with less
• Contender™ Series premium parts designed for non-Metso crushers
Komatsu’s more than 20-machine line-up includes a number of models making their North American market debuts. The Japanese manufacturer says it’s focused on creating connections to empower the success of its global network of distributors and customers in the aggregates, construction and other industries.
Featured new and current machines include the PC238USLC-11, PC210LCi-11, PC290LCi-11, PC360LCi-121, PC490LCi-11 and PC1250-11 crawler excavators; WA320-8, WA480-8 and WA500-8 wheeled loaders; the HM400-5 articulated hauler and HD605-8 rigid hauler; and D51i-24, D61i-24 and D155AX-8 LGP dozers.
Komatsu D51i-24 and D61i-24 dozers are configured with claimed industry-first technology in the form of patent-pending proactive dozing control. It enables operators to use machine control from “grass to grade”. The machine records terrain data as it moves. Using real-time conditions and the recorded terrain data, the system makes calculated decisions about whether to cut and carry material, spread or fill that material, or whether to perform finish grading. www.home.komatsu/en/worldwide
Terex Trucks, the Motherwell, Scotland-headquartered articulated dump truck maker, is showcasing its TA300 and TA400 models.
• Symons™ crusher upgrades
Find out more on www.metso.com/company/ See us at ConExpo-CON/AGG 2020 booth C31531
In North America, the TA300 and TA400 are sold with a threeyear warranty, telematics and planned maintenance included as standard – and there are competitive finance packages available for lease and wholesale. One example of the recent improvements Terex Trucks has made is the product upgrade on the TA300. Since the beginning of last year, the TA300 has been manufactured with a new transmission, leading to improvements in fuel efficiency, performance, productivity and operator comfort, when compared to the previous model working in the same application. The 28-tonne workhorse delivers a 5% improvement in fuel efficiency, a 5km/h increase in speed to 55km/h and an increase in the length of time between oil maintenance intervals from 1,000 to 4,000 hours.
The TA400, the largest articulated hauler on offer from Terex Trucks, has a maximum payload of 38 tonnes and a heaped capacity of 23.3m³. Powered by a high-performance, fuel-efficient engine that develops a gross power of 331kW, the TA400 is designed to meet the demands of the most extreme operations such as quarries, mines and large-scale construction projects. www.terextrucks.com
More info: metso.com/events/2020/conexpoconagg/
Ammann claims that its ACP 300 ContiHRT continuous asphalt plant offers high-quality production. Designed to meet the needs of the North American market, the ContiHRT is capable of producing high-quality mix with more than 60% recycled asphalt (RAP). The new plant features Ammann’s novel recycling technology, already proven worldwide, which maximises RAP utilisation and meets the world’s most stringent emissions guidelines. The gentle pre-heating of the RAP, compared to the application of traditional cold feed to superheated virgin aggregates, prevents thermal stress on the asphalt concrete (AC) content and ensures a highly homogenous final mix. That process also minimises fuel burn and reduces the levels of CO₂ and other pollutants.
The plant incorporates a RAP dryer for the addition of recycled materials and a separate cold recycling feed. The plant is capable of
incorporating shingles, liquid additives, fibre granulate and foam AC. It can access a recycling system for RAP utilisation up to 60%; a separate cold recycling system for 30%; or a combination of the two. The ACP 300 ContiHRT can also produce high amounts of mix without any RAP. Warm mix can be produced with or without RAP. Continuous
production capacity is 300tonnes/hour. The system utilises proven technology and is also said to address the need to reduce emissions. Additional plant innovations include the proprietary as1 Control System. This advanced system provides data that enables high production while optimising the use of fuel and aggregates.
Installation and relocation are said to be quick and uncomplicated. The horizontal design ensures fast and easy assembly and disassembly.
www.ammann.com
With a bucket capacity of 5.4m³, Doosan’s DL580-5 top-of-the-range wheeled loader has a similar look to the next machine down in the range, the DL550-5, while also featuring robust structural components and an advanced sophisticated double circuit axle oil cooler system. This is said to provide an ideal solution for applications such as block lifting and other heavier material-handling needs in industrial, construction, recycling, mining and quarrying applications.
To meet these requirements, the DL5805 has a 36.03-tonne operating weight and higher static tipping loads (straight/full turn 40°) of 29.7 tonnes and 26.2 tonnes, respectively.
The DL580-5 has reinforced Z-bar kinematics for heavier lifting with few moving parts. This design also helps stabilise the loader, enables rapid bucket movements and keeps the bucket at a right-angle position.
The DL580-5 is powered by the Scania DC13 6-cylinder engine producing 283kW
of power at 1800rpm. The Scania DC13 engine provides a generous maximum torque of 1765Nm at 1300rpm and up to a 10% reduction in fuel consumption and excellent response.
Doosan’s new Stage V-compliant DA45 articulated hauler has a 41-tonne payload and is powered by the new Scania Stage V DC13 13-litre diesel engine with an output of 368kW.
While the core of the Scania engine, which has been responsible for its exceptional reliability, has not changed, the main difference in the new engine from its predecessor is the improved after-treatment system.
The new DA45 Stage V machine features a new cab and a semi-levelling front suspension that adjusts itself independently depending on the operating conditions to ensure a comfortable working environment for the operator.
www.doosanequipment.eu
The new Epiroc SmartROC D60 down-thehole (DTH) surface drill rig for quarrying, mining and construction has been updated with Epiroc’s automation-ready platform.
The SmartROC D60 is designed to provide the intelligence and power to efficiently drill high-quality blast holes with accuracy and precision. It has smart features such as automated drilling and rod handling to increase safety, efficiency and consistency for a lower total cost of ownership (TCO).
The automation-ready platform also includes the new Auto Feed Fold feature. With a single action, Auto Feed Fold enables the operator to fold the feed for tramming or position it for drilling. This is also useful when operating one or more drill rigs remotely with the BenchREMOTE option.
Available with a shorter boom specially designed for efficient and demanding quarry work, the D60 can drill holes of 4.6 to 7 inches (116.84mm to 177.8mm) in diameter and to a maximum depth of 182 feet (55.47m).
www.epiroc.com
Cyprus has a rich aggregates production history with its 25 quarries spread across the island known for their high-quality diabase-based, limestone and calcareous limestone mineral products. Guy Woodford recently visited the country to find out more about the current and likely future health of its aggregates sector.
The EastMed pipeline megaproject – a 1,900km undersea pipeline to carry natural gas from the eastern Mediterranean to Europe, potentially cutting dependency on Russia for energy supplies
– will require huge quantities of aggregates, generating highly attractive commercial opportunities for Cyprus’s aggregatesproducing businesses.
The highly ambitious works moved a step closer on 2 January 2020 when Cypriot president Nikos Anastasiades, Greek prime minister Kyriakos Mitsotakis, and Israeli prime minister Benjamin Netanyahu attended
a ceremony in Athens to seal the accord for the project.
The three governments will now put the EastMed pipeline proposal out for financing bids from private investors. Cyprus, Greece and Israel are looking to reach a final investment decision by 2022 and have pencilled in completion of the pipeline by 2025. European governments and Israel agreed last year to proceed with the eye-catching project, which could cost up to €7bn.
Significant progress on the EastMed pipeline plan is being made at a time when Cyprus aggregates production is already rising, with the government having released
long-held funds for various new highways projects and commercial and residential construction works. A variety of rock armour coastal defence projects are also set to be commissioned in the next few years, each requiring high volumes of aggregates.
Cypriot aggregates production in 2019 stood at 8,422,664 tonnes – up just over 5.5% on 7,978,000 tonnes in 2018. However, the 2019 production volume is still only around 60% of peak annual Cypriot aggregates output of 14,174,480 tonnes in 2008. As these figures indicate, Cyprus has not been immune from the impact of the 2007-2008 global financial crisis. As highways and building projects were shelved or abandoned
altogether, annual aggregates production fell significantly, reaching a nadir of 3,941,378 tonnes in 2015.
Cypriot aggregates exports are linked to specific projects, such as Greek railway or Israeli natural gas underwater pipeline works. Around 300,000 tonnes of aggregates went to export customers in 2018, with no exports recorded in 2019.
Based in Pyrga, south-east Cyprus, Skyra Lima, a quarry company owned by the Iacovou Group, a Cypriot construction company giant, produced 1.15 million tonnes of diabase aggregates and sand in 2019 for its large highways and commercial and residential building customer portfolio. This makes it the biggest supplier of diabase aggregates on the island.
In recent years, Skyra Lima has provided aggregates sourced from its 380,000m² quarry for key infrastructure projects including Larnaca’s new airport, the new Limassol-Nicosia highway and a major Limassol traffic-congestion-easing project.
“We have invested €2.5 million in upgrading our crushing plant to a Metso solution, and a further €2 million on our earthmoving machine fleet, with new Caterpillar and Hitachi models,” said Iacovos Stefanou, Skyra Lima’s quarry manager, during ABI’s visit to the company’s production site and office. “We crush our aggregates and wash our sand products
president of UEPG (European Aggregates Association), who are accompanying me on my quarry firm visits, stress that as unoccupied space in Cyprus is at a premium, it is vitally important for the island’s quarries to be good neighbours to nearby villagers and small businesses.
“Protecting the environment is our number one priority. There is a house only 250 metres away from our quarry,” explains Stefanou. “Dust can be a problem during summer production, so we have invested in a state-of-the-art dust suppression system. We also measure noise levels and don’t operate at night-time. We crush and screen Monday to Fridays and carry out plant maintenance on Saturdays.”
Stefanou and Latouros explain how for each tonne of Cypriot aggregate sold - with current prices (depending on aggregate type) ranging from €4 to €9 per tonne - operators of Cyprus’s 25 quarries, plus two gypsum sites, need to pay a 40-cent environmental royalty. This builds into a significant sum over the course of a year, which is used on community improvement projects focused on schools, local galleries, public parks or other facilities.
For example, the 800 residents of Ayios Theodoros, where Stefanou lives and is president of the village council, have seen environmental royalties from neighbouring Latouros Gypsum, Latouros’s gypsum quarry business, fund a new park, a local industrial history museum and an art gallery.
“Protecting the environment is our number one priority. There is a house only 250 metres away from our quarry,”
Iacovos Stefanou
“We are talking about a village receiving as much as €100,000 a year towards community improvement projects. That’s a substantial amount of money,” highlights
Stefanou says that Skyra Lima’s investment in its crushing plant and earthmoving machine fleet leaves it well placed to increase production in order to cater for a forecast further rise in Cypriot aggregates demand.
“Government funds are being released for a new Nicosia ring road, a new parliament building in the city and a new archaeological project based there. There are also many new residential skyscrapers planned in Limassol and Larnaca. We sell our aggregates and sand to customers in a 50-kilometre radius of our quarry – which covers all these works.
“We get a lot of information through Antonis and the UEPG about what’s happening in the wider European aggregates industry. I think there is potential for us to export our aggregates, such as ballast for the Greek railway network. Greece has limestone which isn’t suitable for producing railway ballast. There is also obviously big potential to supply aggregates to cover and protect the underwater pipes on the EastMed pipeline project.”
The nearby Pyrga quarry, operated by Latomio Pyrgon, part of Antonis Latouros’s Latouros Group (LG), produced 360,000 tonnes of diabase rock aggregates of various sizes and sand in 2019, mainly for concrete
plant customers. The quarry was opened in 1986, before Latouros Group bought it off J&P Construction in 2011.
“The Cypriot aggregates market is okay,” says Achilleas Tsiopanis, the quarry’s longstanding manager. “It’s definitely better than 2013-2014. The most aggregates we’ve produced here in any one year was 700,000 tonnes in 2008. The economy is improving so let’s see what happens.”
Turning to Latouros, he smiles and adds: “He’s a very hands-on boss and we have a close working relationship.”
The quarry had subcontracted its loading and hauling work up until the end of 2019 and is currently looking to recruit new operators. “Trying to find young skilled operators is not easy,” admits Latouros.
The site has what Latouros describes as a highly productive and efficient Metso Nordberg crushing plant, installed in 2000, and equally as efficient Telsmith screens. Production efficiency has benefited further from last year’s installation of a new conveyor system from Israeli manufacturer Elkayan Metal Industries. The system has reduced the need for wheeled loader transportation of crushed and screened material to stockpiles, thus reducing fuel cost and production time. Latomio Pyrgon was also due to benefit from the scheduled March 2020 delivery of two new Caterpillar 772G off-highway trucks and a Caterpillar 988K wheeled loader.
The amount of bureaucracy in the Cypriot aggregates industry is, says Latouros, a major issue for producers. “You need all kinds of different permits to operate and they can take a long time to process. We need a one-stop shop relating to a permit that covers everything. Our national aggregates association has had some success in making the town planning permit valid for the life of a quarry’s production, instead of needing to be renewed every five years.
“Cyprus also has government-designated quarry zones. If an existing or proposed new quarry is in a quarry zone, it should be far simpler to get working permits.”
We travel half an hour or so to Hellenic Mining’s quarry in Mistero, a town just south of Cyprus’s capital, Nicosia.
Demetris Vattis is Hellenic Mining’s Mistero area manager. “The Mistero area was the centre of Cyprus’s iron pyrite ore and copper sulphate mining business until the mid-1980s. Now it’s known for its limestone, and we have five limestone quarries, including ours, in a one square kilometre area. In the past we were able to produce one million tonnes of aggregate products a year, now we produce around 100,000 tonnes of aggregates and sand each year.
“The limestone in this area has good properties. It’s not too dense with a 2.2-2.3 SG (specific gravity) ratio and 25-30 LA (Los Angeles) abrasion rating, and its water absorption is relatively high, above 3.5% to 4%. It means you can produce very high-quality sand. A new crushing plant is being installed here which will increase our production capability.”
Vattis notes that since Cyprus joined the European Union in 2004, the country’s aggregates producers have needed to comply with EU standards on limestone density, which needs to be higher than 2.3 SG when supplied in large pieces known as
armourstone, used for marine projects like marina and sea coast defences.
“Armourstone is the most expensive aggregate in Cyprus because of its scarcity. It’s a very important product for all quarries in the Mistero area. Armourstone pieces come in three sizes: 1-3 tonnes, 3-6 tonnes or 6-10 tonnes. Between 2008 and 2010 alone, Hellenic Mining supplied customers with armourstone pieces totaling a combined weight of 120,000 tonnes.
“The quarries of Mistero supplied armourstone for the marina and coast defences in Zygi, a small village between Limassol and Larnaca on the south coast of
Cyprus. Armourstone was also supplied from the Mistero area for the Limassol marina project and will be supplied to the yet-tobe-completed Ayia Napa marina on the south-east coast.”
As well as being able to draw on a further 40 years of limestone reserves, Hellenic Mining’s Mistero quarry also houses a lime kiln, which produces 7,000-10,000 tonnes of hydrated lime each year. Hydrated lime is used to improve the plasticity, cohesiveness and water retention of Portland cement mortars and renders.
While en route to see the next quarry business, located near Limassol, Latouros talks about his part-owned, July 2019-established construction and demolition (C&D) waste recycling business, Recycling Point – Latouros & Xenis Bros, of which LG owns 51%. The company was in the process of installing a C&D recycling plant, from Israeli manufacturer Elkayan Metal Industries, at the time of ABI’s visit. Latouros also discusses the ongoing success of Agrolab RDS Cyprus, a company providing integrated laboratory and consultancy solutions related to geochemistry, environmental issues, food chemistry and microbiology, in which his group owns a 30% stake.
M.S. (Skyra) Vassas’s quarry is Cyprus’s biggest, with a production capacity of 2 million tonnes of diabase aggregates a year.
“The biggest issue for us is price,” says Phidias Savvides, MS (Skyra) Vassas executive director. “Competition is unbelievable in the Limassol area. Nobody really makes any money. We currently produce around 69,000 tonnes a month, mostly for customers in Limassol and Paphos, a city on Cyprus’s south-west coast.
“The pricing issues means we have to look to export more aggregates. We produce ballast and have been exporting it to railway customers in Greece since 1999. Back then demand from those customers was 500,000 tonnes. The customers kept saying they wanted ‘more, more, more’, so I built a bigger factory then Greece went bankrupt. Now Greek ballast demand is half of what it was in 1999, but there is talk of demand rising to 500,000 tonnes a year by the end of 2020. Given that, I’m keeping a close eye on that market.”
Savvides has also exported his aggregates to Lebanon and is interested in new business opportunities in that market. “The political situation there is not easy which makes it harder to do business,” he laments.
“Israel is another interesting market. Over a five-week period in the summer of 2018, we shipped 190,000 tonnes of 40mm-100mm aggregates to an Israeli customer involved in an underwater natural gas pipeline project. It was a very complex and demanding job as each freight ship required 17,000 tonnes to be loaded onto it in just 12 hours. Ships were going and returning in 48 hours, and you needed six to seven excavators and 20 people at Larnaca port, 70 kilometres from here, working 19 hours a day, every day.
“We have proven we can handle this type of contract and we are interested in bidding for an Athens-Crete pipeline project likely to begin this summer. Obviously, we are also monitoring what’s happening with the EastMed pipeline project.”
After our conversation, Savvides takes ABI on a tour of M.S. (Skyra) Vassas’s vast quarry site, which includes a giant €45mn, 1,200 tonnes-an-hour FL Smidthmanufactured aggregates processing plant. The set-up includes a €7mn automation system which allows for total remote production plant control by a single system user. This ensures complete flexibility in how much of the plant is operating at any one time, ensuring optimum production efficiency.
K. Kythreotis Holdings quarry in Parekklisia, a village near Limassol, operates next to two other quarries. This creates similar aggregates-pricing issues to those articulated by Phidias Savvides at M.S. (Skyra) Vassas. All four quarries serve the same market.
“As we are one of three quarries in the same area, we also get some complaints from local villagers about dust and when blasting takes place,” explains mining engineer George Piperides. “We produce around 700,000 tonnes of diabase aggregates a year but have the capacity to handle 1.2 million tonnes annually. “It’s very difficult to justify investing in new equipment given how we have to price to secure business. The Cypriot authorities have also set an even higher durability threshold for diabase aggregates than EU guidelines. This means we will struggle to meet any rising Cypriot aggregates demand.”
The K. Kythreotis Holidings quarry also contains concrete and asphalt plants,
creating a more diversified product offer. “While we have this, the asphalt and concrete supply market is also very competitive in this part of Cyprus,” says Piperides.
The following day, ABI is in the boardroom at Latomia Latouros’s calcareous limestone sand quarry in Dali, LG’s flagship quarry site situated just under 20kms southeast of Nicosia. Less than two kilometres away, Latomia Latouros operates Elmeni (Latomia), another calcareous limestone sand quarry under LG’s group. The Cyprus Aggregates Producers Association board is discussing the health of the Cypriot aggregates industry, echoing many of the views expressed during the previous day’s tour around some of the island’s quarry businesses.
Additionally, the board discusses the situation in Paphos, where the aggregates deposits within the existing footprint of the city district’s three limestone quarries are running out. The operators of the quarries would like to extend their sites to access new mineral reserves, but as their area has been designated an EU Natura 2000 nature protection area, new quarrying licences are not being issued.
“It means that quarries often some distance from Paphos will need to cater for the city’s aggregates demand, which will generate much higher supply costs,” explains Latouros. “We would prefer the government authorities to identify a new quarrying zone in that area.
“Regarding the rest of the island, we would prefer the government authorities to deeply investigate the possibility of expanding the existing quarries, wherever this is possible, in order to secure longterm deposits, rather than continuing as they are to look for a new quarry zone for the Larnaca area. These expansions
together with the creation of buffer zones of between 300 and 500 metres around the existing quarries will give much more long-term deposits. It is also a much more environmentally friendly approach compared to opening a new quarry zone.”
Given the progress on the EastMed pipeline project and the overall increase in Cypriot aggregates demand due to increased government funding on highways and commercial and residential building infrastructure, ‘expansion’ is a good word to describe what appears to be in store for the island’s aggregates sector over the next few years. AB
David Arminas reviews the recent SaMoTer Innovation Award winners and looks at what will be on show at the exhibition in Verona, Italy, from 21-25 March
Environmentally friendly asphalt-mixing plants that minimise dust, noise and odour and maximise the use of RAP will be a highlight at the Ammann booth.
Ammann noise reduction solutions eliminate up to 25dBA, says the company. As well, bitumen fumes are reduced at points along the production process which includes bitumen tanks, skip and load-out levels and the stack. At the lower inexpensive end is the addition of cold RAP into the mixer; RAP and aggregates are dosed separately into the mixer. This process is available on new Ammann plants and as a retrofit on other
manufacturers’ plants. RAP use of 25% to 40% is possible.
The addition of warm RAP via a separate RAH60 parallel dryer in combination with the cold-feed system means 60% use of hot recycled materials is possible.
For recycling rates of 100%, according to the company, warm RAP with a counterflow RAP dryer protects bitumen from damage during the heating process. The RAP is warmed so gently that there is no radiation heat making it a highly efficient system with extremely low emissions. www.ammann.com
The winner in the SaMoTer Innovation Award category for Software Applications was Doosan for its Xitecloud system. It can estimate the volume of material to be moved in relation to specific soil features, for example, rock or earth. Doosan says that Xitecloud provides essential support for operational planning and efficient task management, including machinery fleets and timing.
Products being shown for the first time at SaMoTer include Doosan’s new Stage V-compliant 30- to 40-tonne crawler excavators, such as the DX350-7.
The 36-tonne machine’s Stage V engine exceeds regulations without exhaust gas recirculation (EGR), by boosting the quantity of air available during combustion, increasing the temperature of the process and greatly reducing the particulates produced. This is combined with super-efficient DOC/
Komatsu will be showcasing one of its most successful new wheeled loaders, the WA475-10. The 24-tonne loader features the Komatsu-developed Hydraulic Mechanical Transmission (KHMT) and boasts an EU Stage V engine putting out 217kW of power which makes the machine up to 30% more fuel efficient than its predecessor. An electric tiltable engine hood provides full access to the engine compartment. The bucket capacity is 4.2-4.9m³ and the tipping load is 18.8 tonnes.
A variable speed control adjusts the machine’s top speed to the jobsite’s requirements while the adjustable variable traction control effectively limits wheel-spin in difficult ground conditions. Hydraulic speed can be controlled directly by the accelerator pedal making it easy for the operator to find the right balance between traction and lifting power. The optimised Z-bar linkage system provides much more lift force and a higher tonnes-per-hour production rate. Response time of the hydraulics and the dumping or lifting can be set to specific job sites. www.komatsu.eu
DPF+SCR after-treatment technology to ensure minimal emissions. Maintenance of the diesel particulate filter (DPF) has been greatly reduced, with none required until 8,000 hours of operation.
Complementing these products, Doosan is showing new technologies under the company’s ‘Powered by Innovation’ umbrella, expanding its Smart Solutions portfolio to give visitors a preview of what will be coming in the future, including Concept-X, a new comprehensive control solution to operate equipment without human intervention. Doosan will show new fuel-cell drones for monitoring machine performance on large construction sites as well as in mining and quarrying operations.
The DL420CVT-5 wheeled loader is the rst model in the Doosan wheeled loader range to be equipped with a Continuously Variable Transmission. CVT is composed of a hydraulic motor with a hydraulic pump which provides a smooth and continuous speed variation. A 15% fuel saving can be achieved, according to Doosan. www.doosanequipment.eu
Liebherr’s active rear-personnel detection system
Liebherr walked off with the top prize in the Wheeled Loader/Special Applications category of the SaMoTer Innovation Award for its active personal detection system. Through a system of sensors, it distinguishes between people and objects. A warning appears on the machine display and sounds
acoustic signals if there is danger in the wheeled loader’s rear area. If a person is located in the rear area of the wheeled loader, the system alerts the operator at a greater distance than for stationary objects, such as walls or columns. A more precise warning is given to the operator if there is a risk of personal injury. To boost
Cifa says that it will showcase three of its best sellers – the Carbotech K47H and Steeltech K42L truckmounted pumps as well as the MK28L-5 truck mixer pump.
The K47H, launched in 2018 to celebrate the company’s 90th anniversary, is the longest and lightest pump on the market, according to CIFA. It is within the European legal
sections of the boom. The boom is five sections with an RZ folding geometry and CIFA’s Smartronic electronic management system. This software collects information to manage the vehicle’s functions simply and accurately. It also provides information on the machine status at all times and manages the pumping unit, pressure and speed of the motor autonomously to
safety even further, the company says that by the end of the year, it will add a brake-assistant service to the detection system.
Liebherr also announced that it will have four wheeled loaders on its stand, including the L586 XPower –at 32.6 tonnes the largest in the group. www.liebherr.com
Epiroc will have on display its hydraulic breaker solid body SB 1102, a new model with an operating weight of 1.06 tonnes, which completes the company’s range of medium SB breakers. The solid body design eliminates the weaker parts of traditional hammers – guide elements and tie rods – in favour of greater durability and lower operating costs thanks to a tapered, compact and light design.
The energy-recovery system automatically uses the piston-recoil energy to increase percussion performance and reduce vibration levels. The maintenancefree, high-pressure accumulator, equipped with a patented diaphragm support, delivers constant performance and maximum reliability. The full-guide floating bushing with patented tool-locking system allows quick and easy on-site replacement of the tool.
www.epiroc.com
MB Crusher’s BG90.3 jaw crusher bucket attached to a
represent the Steeltech line – noted for durability – and will be equipped with the HP1608EC closed-circuit pumping unit with 160m³/ hour of production and 80 bar maximum pressure for concrete. Electronic management is via Smartronic GOLD with ASC (advanced stability control).
Cifa’s MK28L-5 truck mixer pump was remodelled last year into a hybrid version – the first in the world, says CIFA. The pumping unit, the PB808, produces up to 80m³/hour and up to 80 bar of pressure to manage both quantitatively demanding castings and to operate with additivated concrete that requires higher than standard pumping pressures. The MK28L-5 will also have large aluminium hose holders on the sides and the concrete shut-off valve on the end hose. It has the LSC (light stability control) management system that controls correct stabilisation of the pump. www.cifa.com
MB Crusher says that it will have more than 20 units at SaMoTer, including seven jaw crusher buckets, four screeners, the newest shaft screeners line, drum cutters and grapples. There will be a range of attachments suitable to plug into excavators, loaders, skids and telehandlers – many being demonstrated in the company’s outside area.
MB Crusher’s screening buckets have a wide cone-shaped sifting surface with the cones made of interchangeable modular panels allowing quick changes. The shaft screeners have interchangeable shaft kits to adapt to the need of each job site. The company’s drum cutters are equipped with power-boost for the rotary cutter to overcome the different hardness of the material. www.mbcrusher.com
Hyundai Construction Equipment Europe scooped the SaMoTer Technical Innovation Award in the Medium Wheeled Loader Category with its new HL960A wheeled loader. The Stage V machine will take centre stage on the Hyundai booth at SaMoTer where, says the company, there will be a strong focus on wheeled loaders, including the new HL940A and the HL955A models.
The A-series machines comply with the European Stage V emission levels, in this case exceeding requirements, according to the company.
The company’s crawler excavator, the new HX300ANL, will also be at SaMoTer; N stands for narrow tracks, specifically for the Italian market.
Cabin space for drivers has increased by 13% and the ECO Gauge gives instant fuel-efficiency feedback. You can also monitor detailed information on average, hourly and daily fuel consumption. The optional Advanced Around View Monitoring (AAVM) system gives a 360° overview of
Hidromek rode the SaMoTer Innovation Award waves with its HMK230NLC hydraulic excavator triumphant in the Hydraulic Excavators for Construction and Special Design categories.
The HMK230NLC is part of Hidromek’s H4 series which stands out for its operating speed because of major improvements to hydraulics. The electronics have an increased capacity to monitor the condition of the machine and how it is using the attachments. H4 cabins offer maximum safety and durability under ROPS & FOPS standards. The red handles and warning labels on the new series of the machines are designed to increase the operator’s safety to the highest level. The overall design allows greater operator vision – nearly eliminating blind spots – and LED headlamps significantly improve night vision.
Along with the award-winning HMK230, HİDROMEK will exhibit other H4 series machines – the HMK 145 LC SR, HMK 310 NLC and HMK 390 NLC crawler excavators.
From Hidromek’s wheeled loader range, the heavy-duty HMK 635 WL will be on display. The product is more environmentally friendly and productive with its Stage V MTU Mercedes engine. The HMK 635 WL shortens the cycle times and provides high load in a short time.
the machine’s immediate working environment. It also includes Intelligent Moving Object Detection (IMOD) technology that senses and warns the operator when people or objects come within 5m of the machine.
Entry to and exit from the HX300ANL’s cab are easier because of the large doors. There is also high-performance air conditioning and the adjustable reclining air suspension seat offers lumbar support.
www.hyundai-ce.com
The 635 WL is frequently used for mining and quarrying operations as well as with batch plant and other industrial applications. www.hidromek.com
Big job or small job, Promove has a complete line-up of highperformance pressurised hydraulic breakers –including the new 600kg XP600 and 200kg XP200. Promove’s XP series has an energy recovery system, anti-blank firing system and a power/frequency automatic regulation system. There is also a “smart valve” to enable a plug-and-play system that allows installation of the breaker without having to adjust any settings on the excavator. This saves significant time and costs – as well as eliminating future problems such as premature breakages due to extra flow. Importantly, this system also allows the breaker to be moved to various machines, making it easier to rent equipment.
www.promovedemolition.com
Looking for efficient dump trucks? Then inspect the DP 705 WD from Italian dump truck manufacturer Perlini, part of the Cangialeoni group. The 705, with a payload of 65 tonnes, now boasts a Scania DC 16385A engine – a four-cycle, watercooled 90° V8 power plant that is EU stage 5-compliant. The electronic management of the engine remains in communication with the parent company which can diagnose issues and organise repairs and vehicle downtime.
Italian buyers can also take advantage of a new tax reduction scheme – thanks to the National Industry 4.0 Plan – for buying more efficient “smart” construction vehicles, such as the 705. Its GPS monitoring system can track kilometres travelled, monitor body positions, hours worked and help reduce fuel consumption even further because it will prevent overloading of the vehicle. www.perlinidumpers.it
Spain’s estimated natural aggregates production remains at around a quarter of the peak of the Spanish construction boom in the years 2000-2007. Pictured is a quarry in Galicia, north-west Spain Picture: FdA
Spanish and Portuguese aggregates producers have had a tough time in recent years due to sluggish national economies suppressing demand for building materials. But with major new infrastructure spending having been approved by both countries’ governments, the future looks somewhat brighter. Guy Woodford reports
Given it’s 505,990km² size and population of more than 46 million, it is surprising that Spanish aggregates demand is not greater.
But analysis of the country’s turbulent modern economic and political history sheds a lot of light as to why estimated natural aggregates consumption stood at 121 million tonnes in 2018. While this represents an increase of 25% on 97 million tonnes in 2013, it is still way down on the 486 million tonnes of aggregates produced in 2006, during the 2000-2007 Spanish construction boom. The figures have been compiled by the FdA (The Aggregates Federation), which represents the interests of Spanish aggregates producing companies, both nationally and internationally.
While the world has had to adjust to a new financial reality following the 2008-2009 global financial crisis, Spain is among countries that have been hit particularly hard. The country is still gripped by a degree of political uncertainty despite the installation on 8 January 2020 of Pedro Sánchez as the leader of modern Spain’s first coalition government. After bitter and protracted stand-offs between various political parties competing for power, the Socialist Party (PSOE) leader and now prime minister is gambling on a coalition with the radical left Podemos party being even harder to oust than it was to put into power.
On a more positive note, aggregates production estimates from the UEPG (European Aggregates Association) show that despite a reduction in the total number of Spanish aggregates-producer companies (1025) as of 2017, compared to 1,140 in 2012, the number of extraction sites has risen from 1,175 to 1,874 over the same five-year period. This indicates encouraging capacity among producers to meet a rise in aggregates demand.
Further encouragement for Spanish aggregates producers can be found in Global Data’s Construction in Spain – Key Trends and Opportunities to 2023 report published in June 2019. The report by the major global business market research consultancy highlights how Spain’s construction industry grew by 7.6% in real terms in 2018, notably up on average annual growth of 3.1% during the preceding four years. Growth during the study’s review period (2014–2018) was said to be driven by positive developments in regional economic conditions and government investment in commercial and industrial infrastructure, as well as recovery in the residential construction sector.
GlobalData states that over its report’s forecast period (2019–2023), the Spanish construction industry’s output will be supported by improvements in consumer and investor confidence. The Spanish government’s efforts to enhance regional connectivity through the development of the
country’s transport infrastructure, coupled with efforts to boost the residential construction market, will support the industry’s growth over the forecast period. An increase in the number of new building permits issued is expected to support new construction activity over the same period. In addition, the government’s aim to expand renewable energy resources is expected to attract investments in energy infrastructure projects, which will in turn fuel growth in the industry.
GlobalData expects the infrastructure construction market to record a forecastperiod compound annual growth rate (CAGR) of 4.29% in nominal terms in 2023, supported by the government’s plans to develop and modernise the country’s transport infrastructure. In 2019, the country will invest €2.3 billion in the construction and maintenance of roads, €829 million in ports and €689 million in airport infrastructure.
Meanwhile, the total construction project pipeline in Spain – as tracked by GlobalData
Source: FdA
and including all megaprojects with a value above US$25 million – stands at €67.7 billion.
The pipeline, which includes all projects from pre-planning to execution, is skewed towards late-stage projects, with 54.8% of the pipeline value being in projects in the pre-execution and execution stages as of June 2019.
During a tour with Metso around aggregates producers in eastern and northern Spain in late summer 2019, Aggregates Business discovered how OSF Group’s 2016-reopened Ofitas de Santutis quarry is supplying ballast for the Basque Y high-speed rail project linking three major Basque Country cities – Vitoria-Gasteiz, Bilbao and DonostiaSan Sebastián. Currently behind its scheduled 2023 completion date, the 194km-route is set to reduce passenger and cargo journey times between the three cities to less than an hour, compared to anything between one hour 40 minutes and two-and-a-half hours currently.
Commenting on the current and likely future health of the Spanish aggregates sector, Angel Luis Garcia, Metso’s Spanish sales manager, said: “Building construction works are taking most of the produced aggregates. Civil works are not in a good shape. Aggregates demand is slowly increasing but too slowly. The reason for this is that in recent years Spain has not had a stable government that is investing in civil works.
“In the last few years a lot of small and poorly performing quarries were closed, and some big companies left their Spanish operations. Now new large and resized medium- and small-sized operators own and run aggregates production companies.
“Generally, aggregates prices have remained higher in the north than in the centre and south of Spain. The environment and health and safety have become priority concerns for Spanish quarry operators.”
Established in 2007, the FdA represents about 700 Spanish aggregates production companies and 1,100 aggregates sites across Spain.Speaking about the contemporary Spanish aggregates industry, César Luaces Frades, FdA director general, said: “Due to the fact that the current aggregates consumption by Spanish inhabitants is less than half of the EU average, the future potential for growth is between +60% to +80%, which would create a reasonable [consumption] situation. However, this will come slowly due to the combination of several factors.
“First of all, the country is still recovering after the [global financial] crisis and national debt is about 100% of GDP. Working within budget constraints, national government policies need to find the right balance between social expenditure and investment in civil works. The maintenance of existing
infrastructure is at risk. Public investment in Spain for civil works is 63% less than the investment average of Germany, the United Kingdom, France and Italy. This situation is not sustainable anymore and some infrastructure plans need to be developed.”
Turning his attention to the range of companies operating within the Spanish aggregates production industry, Luaces Frades continued: “The industry includes a small number of international big players that account for less than 20% of total Spanish aggregates production. Around 35% of medium-sized, family-owned companies account for 60% of production, and a wide range of small micro-enterprises account for around 20% of production.
“Big players and medium-sized, familyowned companies are producing and delivering aggregates in the urban markets, while small micro enterprises are covering low rural areas with low population density.”
Luaces Frades notes that according to a recent study, the average size of Spanish aggregates companies in terms of production by site is 21% below the average of the big four (Germany, France, United Kingdom and Italy). The production by company is also 45% lower than the average in the same big four countries.
“One critical issue for the sustainability of the Spanish aggregates industry is to increase the average size of sites and companies,” said Luaces Frades.
Commenting on whether there are regional differences in Spain regarding the size of aggregates producers and the types of aggregates products made, Luaces Frades said: “In terms of products there are few differences between regions, because of the need to comply with CPR (EU Construction Products Regulation), CE (Conformité Européene) marking and national regulations. Of course, by geological reasons, the number of types of rocks is large (among 30 different types of rocks) and, in some regions, a specific type of rock is more relevant than the other.
“Where sand and gravel pits are the main type of sites, their average size is smaller. This is the case for La Rioja, Castilla and Leon, Aragon and Castilla - La Mancha, where sand and gravel sites predominate, above 70%.”
Luaces Frades explains that the main rocks used in Spain to produce aggregates for construction are limestone (45.6%), sand and gravel (29.1%), granite (6.4%), dolomite (5.2%), silica sand (1.3%), porphyry (1.1%) and ophite (1.1%). These categories of rock represent 89.9% of construction consumption.
For aggregates for other industrial uses, the most commonly used are limestone (65.6%), marl (12.1%), sand and gravel (5.2%), dolomite (3.5%), silica sand (2.9%).
Although Portugal’s annual aggregates demand fell from 43 million in 2012 to 30 million in 2017, according to UEPG production estimates, the country’s approximate 150 aggregates producers have reasons to be optimistic, notably due to the Portuguese government’s commitment to a host of big money infrastructure megaprojects.
GlobalData’s Construction in Portugal –Key Trends and Opportunities to 2023 report published in September 2019 notes that Portugal’s construction industry registered growth of 6.3% and 2.2% in real terms in 2017 and 2018 respectively, following an average annual growth of -3.1% during 2014-2016. The consultancy attributes the growth to an increase in private consumption, rising household real disposable income, declining unemployment and rising wages.
Over the study’s forecast period (20192023), the Portuguese construction industry is expected to be supported by the government’s focus on developing cross-border transport infrastructure to improve the country’s trade activities. GlobalData highlights the Portuguese government plans to build the Southern European Rail Line to connect Évora in Portugal to Elvas, a town bordering Spain. The project is a part of the €2 billion Ferrovia 2020 plan and involves an investment of €509 million by 2022. Of this total, €232 million will be invested by the European Union (EU). GlobalData also states that the Portuguese government’s focus on developing the renewable energy infrastructure and rising number of building construction permits are also expected to drive public and private sector funding towards construction projects.
Last year saw Portuguese government approval for other big infrastructure projects. July 2019 saw the green-lighting of the
expansion of Terminal XXI and construction of the new Vasco de Gama Terminal on the Port of Sines in Setúbal to expand the port’s capacity and address the rising demand for containerised cargo. GlobalData reports that the plan involves an investment of €547 million to expand and renovate the Terminal XXI, while €642 million will be invested in the construction of the Vasco de Gama Terminal.
In January last year, the government approved the 10-year National Investment Program (PNI). As a part of this programme, the government plans to invest €22 billion in transport, energy, environment and irrigation projects by 2030. Of the total, €12.7 billion will be spent on 44 transport projects, €4.9 billion on eight energy projects, €3.6 billion on 18 environment projects and €750 million on irrigation projects.
The total construction project pipeline in Portugal – as tracked by GlobalData and including all megaprojects with a value above US$25 million – stands at €19.3 billion. Just under two thirds (65.9%) of the pipeline value were projects in the pre-planning and planning stages as of September 2019.
Export markets also remain attractive to Spanish and Portuguese aggregates producers. Aggregates Business has visited Solancis, a high-quality stone product maker,
which extracts around 800,000 tonnes a year of limestone blocks across its nine quarries in the picturesque Serra De Aire region of central Portugal. The company’s products are in great demand globally for buildings such as hotels, offices, department stores, sports stadia and residential properties. Around 95% of Solancis’ sales are exports to customers in more than 50 countries. China, the US, France and England are among the company’s biggest export markets.
Back at company headquarters after seeing how a Caterpillar loading and hauling machine fleet had increased production efficiency and lowered operating costs at Solancis’s Salgueira quarry, Samuel Delgado, owner of Solancis, stressed how the firm was well equipped for future success. “I have a very positive outlook,” says Delgado “We are a business with a high specialism that works closely with many top architects, and there is a big world market for our limestone products.”
Given the very welcome increased infrastructure-projects-spending commitment by the Portuguese government, as well as new residential and commercial construction works, domestic aggregates demand is set to rise, with producers able to look a lot closer to home as well as to export customers in order to achieve sustainable sales and revenue growth. AB
The installation of a comprehensive Command Alkon software solution has helped a leading heavy building materials supply firm in south-east England become an ultra-efficient business success story. Guy Woodford reports
The rapid growth of big data has had a huge impact on the heavy building materials sector.
The correct use and analysis of the vast amount of data available to a business has the potential to transform supply chains as we know them, but also, paradoxically, the power to disrupt.
Without the appropriate tools and expertise to manage large volumes of data, companies can become overwhelmed and unable to gain valuable insights, causing issues across the supply chain and wider business functions.
Day Aggregates, a division of Day Group, is a family-owned company that has been in the heavy building materials for over 70 years. Headquartered at a former British Rail goods yard in Brentford, west London, England, the firm handles over
Headquartered at a former British Rail goods yard in Brentford, west London, Day Aggregates handles over five million tonnes of construction material each year
five million tonnes of construction material each year and is one of Britain’s leading bagged aggregates suppliers. The company also provides decorative aggregates for householders, soil for gardeners, postcrete, cold lay asphalt, and other pre-packed items such as these.
Day Aggregates needed guidance for its dispatch operations. The firm had outdated technology that was hugely limited and needed more insight-rich data to help managers make better dispatch decisions.
The company hired a consultant to find a software producer but did not have much luck in finding what they needed.
It’s the instinct of an ambitious business to relentlessly seek answers when they are needed. Occasionally, though, through good fortune, the answer comes straight to it.
At that time, Phil Ramsey, now CEO of Command Alkon, was a sales representative
for Command Data before the company merged with Alkon. He came to Europe on a family trip and, as fate would have it, helped Day Aggregates discover that the COMMANDseries business systems could work best for them.
The COMMANDaggregate feature in COMMANDseries is still used throughout Europe and has had a tremendously positive impact on Day Aggregates’ business processes.
With Command Alkon’s software, Day Aggregates gained visibility at each of their sites and better communication between staff.
“Long-term success has been made possible by Command Alkon. We wouldn’t have been able to build our business up in the way that we have without the useful information that these products deliver,” said Dominic Day, director at Day Aggregates.
Day Aggregates has 18 sites now that operate using COMMANDseries. The company is growing and continues to aspire to aspire to be more effective and productive, and to deliver high-quality materials to its large portfolio of valued customers.
Dominic Day added: “COMMANDaggregate and COMMANDseries have made us more profitable and helped to make more informed decisions. We can work smarter, rather than continuously trying to work harder.”
Construction material to be turned into recycled aggregates and other products arrives at Day Aggregates’ Tolworth site
In the future, Day Aggregates hopes to integrate more Command Alkon software solutions to continue to amplify their operations.
COMMANDseries integrates with other Command Alkon solutions for batching, quality control, in-cab telematics, mobility, enterprise content management, and business intelligence. It allows quarry operators, construction materials supply
Day Aggregates has 20 sites now that operate using COMMANDseries. Pictured is an example of COMMANDseries software’s COMMANDaggregate feature
firms and other businesses to share data across all aspects of their operations to reap efficiencies.
Among the large number of major international and leading small to mediumsized independent building materials supply firms using Command Alkon software packages in their quarries and other production sites, are CEMEX, LafargeHolcim, HeidelbergCement, CRH and Colas. AB
COMMANDseries integrates with other Command Alkon solutions for batching, quality control, in-cab telematics, mobility, enterprise content management, and business intelligence
The Day Group has a strong record of investing in new technology to improve its operational efficiency.
Aggregates Business reported in 2018 on how the group sources large quantities of both primary and recycled aggregates from various quarries across the UK, all of which require bagging before customer deliveries are made. This was posing a logistical problem, as transporting heavy loads of
aggregates over hundreds of miles increases both handling and energy costs. Furthermore, the alternative solution of building on-site factories for the purposes of bagging also required capital expenditure.
Having recognised these challenges, Day Group approached ABB AVP RM Group. The two companies had already worked together on previous projects when Day Group rented RM Group’s mobile packaging plant.
Comprised of a trailer equipped with an IRB 460 ABB robot inside to palletise the bags, the mobile packaging plant provides a versatile, efficient and easily transportable solution for bagging products at source. Impressed with the technology, Day Group immediately ordered its own fleet of nine mobile packaging plant. All have since been successfully deployed around the group’s many quarries.
The advanced technology of an Ammann ABA UniBatch asphalt-mixing plant is helping a Russian company attract customers by minimising the cost of high-quality mix – and reducing hauling distances.
Tiger Mix, based in Vladivostok in south-eastern Russia, has been a concrete producer since 2016. It recently began asphalt production with the purchase of the Ammann ABA UniBatch.
Tiger Mix chose the Ammann plant in part because of its ability to utilise multiple fuel types, enabling the company to take advantage of the lowest-cost options as prices fluctuate. The flexibility ultimately will help Tiger Mix appeal to new customers and retain current ones by minimising mix prices.
Tiger Mix is also benefitting from Ammann’s environmentally friendly systems that lessen noise and dust levels. A green plant such as the ABA UniBatch can be located in residential areas and city centres, thereby reducing the customers’ hauling distances. Shortened routes can lower customer costs significantly in terms of fuel consumption, the number of haul trucks required – and the number of drivers, too.
The plant can also be fitted with components that can employ high levels of recycled asphalt (RAP). Tiger Mix sees a need
for the increased use of RAP in the future, so the company was sure to acquire a plant that could easily add those capabilities.
The Ammann plant began operation in September. It was a quick turnaround from deciding to enter the asphalt market to producing the first batch of mix.
“The idea to expand production and acquire an asphalt-mixing plant first came up less than a year ago,” said Ilya Nemaltsyn, the general director of Tiger Mix. “The construction of the plant was relatively short – about eight months from the moment of the idea to the choice of a supplier and then finally to the commissioning.”
Nemaltsyn confirmed that fuel flexibility was a key factor in the purchasing process. “What’s unique about this plant is that it can operate on three types of fuel: natural gas, oil and diesel,” he said.
Having these options provides more than price protection. Some fuels are better at creating certain types of mixes, he said. “These choices provide flexibility in the production of mixtures and also meet all environmental standards.”
The plant can incorporate varied aggregates and bitumens and meets international quality standards. It produces about 210 tonnes of mix per hour.
“All the innovations that are available are applied in this plant,” said Oleg Avakin, Ammann area manager for the Far East. “All Ammann equipment is distinguished by a high degree of design study, reliability, economy in terms of energy efficiency, and environmental friendliness.”
www.ammann.com
Finnish company Robit has started to deliver first production batches of its Diamond Button series for top hammer bits to selected global key accounts.
The Diamond Button series –which enables percussive hard rock drilling with diamonds – was first announced last October and production started immediately. The first bits being produced are suitable for use in underground mining, open-pit mining and quarrying. Before the October announcement Robit had carried out testing and development on the diamond button bits for several years.
“Mines are pursuing innovative ways to improve safety and productivity and remote control drilling is part of that,” said Jorge Leal, head of offering at Robit.
The first bit sizes are 89mm and 102mm production drill bits. Leal says that other sizes could be produced depending on the specific demand from customers. He adds that the availability is not constrained by bit size, and that Robit is currently testing bits in the field starting from 48mm size.
80m, while with diamond bits over 1,000m has been achieved. During the extensive field-testing the hardest drilling conditions reduced the normal bit life down to 15m. “Even in those conditions the diamond bit lasted 15 times longer,” according to Ojala.
“Moreover, as the diamond buttons practically don’t wear like normal buttons, the drilling speed remains the same throughout the bit’s lifetime,” he added.
“Similarly, the diameter of the borehole does not decrease as the bit ages, resulting in a more consistent and predictable end result in production drilling.
The diamond bits are designed to be suitable for customers whose use cases require longer bit lifetimes. The pilot cases have focused on customers using remote control drilling in top hammer applications, but Robit says there is also customer potential in tunnelling and DTH (down-the-hole) applications, and that development work has started for these use cases.
Robit says the technological answer for customer needs is a highly developed coating of diamond added on the typical tungsten carbide buttons. The Diamond range is designed to drill for a greater period of time and depth without interruption or the need for downtime due to bit change.
Niko Ojala, R&D engineer and materials specialist at Robit, said that when drilling hard Finnish granite it is quite usual to have to change a normal tungsten carbide button bit after
The many-times-longer change interval of the bit saves time and is particularly important for remote-controlled drill rigs in fully automated mining environments where people are not present during the process.”
Robit is planning an official launch of the Diamond Button series family in September this year at MINExpo in Las Vegas. www.robitgroup.com
10-14 CONEXPO-CON/AGG
Las Vegas, NV
Organiser: AEM
Tel: +1 414 274 0644
Email: customerservice@ conexpoconagg.com www.conexpoconagg.com
21-25 SaMoTer
Verona, Italy
Organiser: Veronafiere S.p.A. Tel: +39 045 8298561
Email: customercare@samoter.com http://www.samoter.it/en
23-25 Hillhead
Hillhead Quarry, Buxton, Derbyshire, England
Organiser: The QMJ Group Tel: +44 (0)115 945 4377
Email: Harvey.sugden@qmj.co.uk https://www.hillhead.com/ exhibitors/hillhead-2020#/
JULY
08-11 EIG 2020
Exeter, UK
Organiser: EIG Conferences marcus.dorey@hanson.biz https://www.eigconferences.com/ future-conference 2020
26-29 Steinexpo
Homberg/Nieder-Ofleiden, Germany
Organiser: Geoplan GMPH Tel: +49 7229 606 30 +49 7229 606 30 https://www.steinexpo.eu
SEPTEMBER
16-18 Construction Indonesia Jakarta, Indonesia
Organiser: PT. Pamerindo Indonesia Tel: +49 3999905 0 contact@merebo.com
16-18 Concrete Show
South East Asia Jakarta, Indonesia
Organiser: PT. Pamerindo Indonesia Tel: +49 3999905 0 contact@merebo.com
MEET THE TEAM
Aggregates Business travels the globe attending conferences, events and equipment shows, keeping you informed of the latest offerings. Come and join us for a chat at any of the events below.
MARCH 2020
10-14 CONEXPO-CON/AGG 2020
MARCH 2020 21-25 SaMoTer 2020 Verona, Italy
JUNE 2020
23-25 Hillhead 2020
Hillhead Quarry, Buxton, Derbyshire, England
JULY 2020 08-11 EIG 2020 Exeter, UK
Advertisers in AGGREGATES BUSINESS can now be contacted via their websites - for instant links to all the websites listed below, by category, go to: www.AggBusiness.com
Ammann p21 www.ammann.com
BKT Tires p35 www.bkt-tires.com
Cifa p49 www.cifa.com
CMS p18 www.cmscepcor.com
ConExpo p42 www.conexpoconagg.com
Cummins p11 www.cummins.tech/construction
Hitachi p7 www.hitachicm.eu
Hyundai OBC www.hyundai-ce.eu
Indeco p17 www.indeco.it
Komatsu Europe IFC www.komatsu.eu
MB Crusher p33 www.mbcrusher.com
RM Group p12 www.rubblemaster.com
Sandvik p4 www.rammer.com
Simex p51 www.simex.it
Smiley Monroe p14 www.smileymonroe.com
Terex Washing p31 www.terex.com/washing
Trimble p27 www.trimble.com
Verona Fiere IBC www.veronafiere.it
You are about to enter a new world – one where anything is possible and
Samoter Technical Innovation Award in the
Thinking about adding the HL960A to your team? Go to www.hyundai-ce.eu/en/dealer-locator and contact your dealer for more details.