
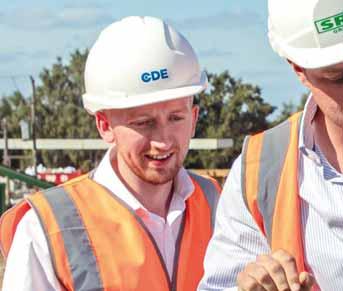
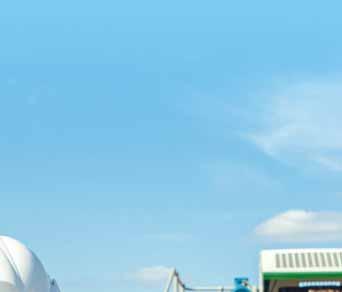
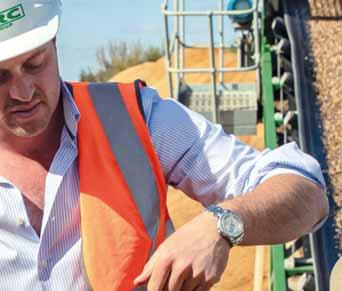
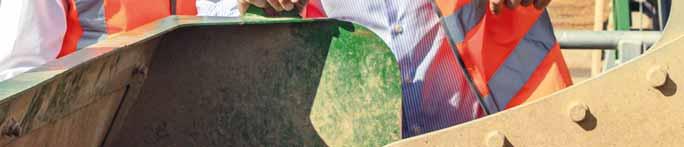

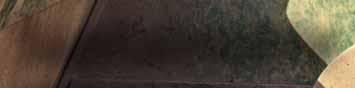


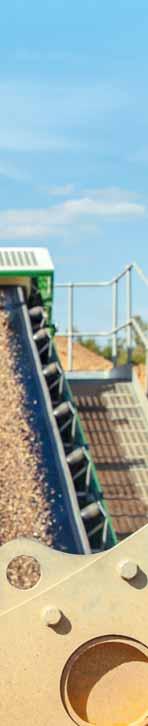








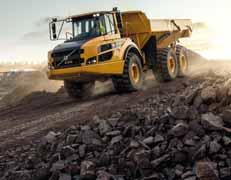
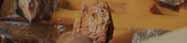


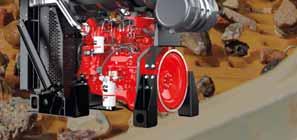
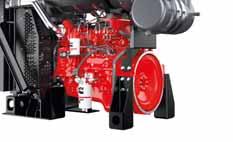


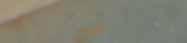

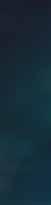
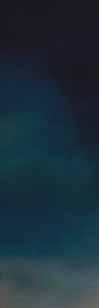

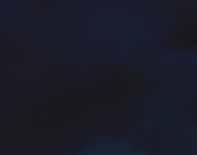
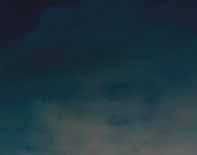


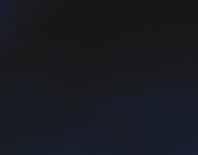
All the features. All the choices. All the production and performance. Get everything you love about the M Series plus much more. Starting with the 980, 980 XE, 982 and 982 XE, each new Cat® medium wheel loader delivers fully loaded trucks at a lower cost per ton — redefining your bottom line.
“Off-highway engine makers are revved up for
05 COMMENT
Welcome, renewed focus on gamechanging cement & concrete innovation
06 NEWS
HeidelbergCement to build the world’s first carbon-neutral cement plant; Oxbotica-TRL UK quarry autonomous-vehicle pilot
42 ASSOCIATION NEWS
UEPG stresses aggregates producers’ importance to EU Industrial Strategy 2.0
43 LEGAL UPDATE
The road to net zero: adapt and thrive
50 EQUIPMENT UPDATE
Global OEMs’ new equipment launches & applications
51 EVENTS
All the key events in the quarrying & aggregates world
19 CRUSHING & SCREENING
Four leading manufacturers whose new models are looking to help customers meet their sustainability goals
22 LOADING
A top OEM’s large crawler excavator is making a big impact in one southern European nation’s quarrying sector, while new zero-emission loading models are also making headlines
26 HAULING
Connected machines are helping quarry operators monitor hauling payloads in real time and helping to control their cost per tonne
29 RECYCLING – PART 1
Recycled and secondary aggregates demand is strong and growing in the UK and other parts of Europe and the wider world
32 WEAR PARTS
by
09 INTERVIEW
Aurélie Delannoy, MPA director of Economic Affairs & UEPG Economic Committee chair, discusses the current health of and big issues within the UK and wider European mineral products industry
44 MARKET REPORT
The UK and Ireland’s aggregates outlook is positive, but caution is advised
47 QUARRY PROFILE
Easy access to high-quality replacement machine parts is a must for any savvy quarrying operation
35 ENGINES – PART 1
Demand for quality off-highway equipment engines is likely to rise as the world emerges from severe COVID-19 pandemic-induced disruption
40 PORTABLE POWER
Proven and reliable portable power solutions for aggregates production
How a state-of-the-art CDE plant is boosting SRC Group sustainability
HEAD OFFICE
EDITOR: Guy Woodford
ASSISTANT EDITOR: Liam McLoughlin
CONTRIBUTING
EDITORS: Patrick Smith, Dan Gilkes
EQUIPMENT EDITOR: Mike Woof
DESIGNERS: Simon Ward, Andy Taylder
PRODUCTION MANAGER: Nick Bond
OFFICE MANAGER: Kelly Thompson
CIRCULATION & DATABASE MANAGER: Charmaine Douglas
INTERNET, IT & DATA
SERVICES DIRECTOR: James Howard
WEB ADMINISTRATORS: Sarah Biswell, Tatyana Mechkarova
MANAGING DIRECTOR: Andrew Barriball
PUBLISHER: Geoff Hadwick
CHAIRMAN: Roger Adshead
ADDRESS
Route One Publishing Ltd, Waterbridge Court, 50 Spital Street, Dartford, Kent DA1 2DT, UK
TEL: +44 (0) 1322 612055
FAX: +44 (0) 1322 788063
EMAIL: [initialsurname]@ropl.com (psmith@ropl.com)
ADVERTISEMENT SALES
SALES DIRECTOR:
Philip Woodgate TEL: +44 (0) 1322 612067
EMAIL: pwoodgate@ropl.com
Dan Emmerson TEL: +44 (0) 1322 612068
EMAIL: demmerson@ropl.com
Graeme McQueen TEL: +44 (0) 1322 612069
EMAIL: gmcqueen@ropl.com
SUBSCRIPTION / READER ENQUIRY SERVICE
Aggregates Business is available on subscription at the rate of: £85 / US$145 / €111 per annum. Single copies £20 / US$35 / €26 Email subs@ropl.com for further details. Subscription records are maintained at Route One Publishing Ltd.
SUBSCRIPTION / READER ENQUIRIES TO:
Data, Route One Publishing Ltd, Waterbridge Court, 50 Spital Street, Dartford, Kent DA1 2DT, UK
TEL: +44 (0) 1322 612061
FAX: +44 (0) 1322 788063
EMAIL: data@ropl.com
No part of this publication may be reproduced in any form whatsoever without the express written permission of the publisher. Contributors are encouraged to express their personal and professional opinions in this publication, and accordingly views expressed herein are not necessarily the views of Route One Publishing Ltd. From time to time statements and claims are made by the manufacturers and their representatives in respect of their products and services. Whilst reasonable steps are taken to check their accuracy at the time of going to press, the publisher cannot be held liable for their validity and accuracy.
PUBLISHED BY © Route One Publishing Ltd 2021
AGGREGATES BUSINESS USPS: is published six times a year. Airfreight and mailing in the USA by agent named World Container Inc, 150-15, 183rd Street, Jamaica, NY 11413, USA.
PERIODICALS POSTAGE PAID AT BROOKLYN, NY 11256
US POSTMASTER: Send address changes to Aggregates Business, World Container Inc, 150-15, 183rd Street, Jamaica, NY 11413, USA. Air Business Ltd is acting as our mailing agent
PRINT: ISSN 2051-5766
ONLINE: ISSN 2057-3405
PRINTED BY: Warners (Midlands) PLC
To mark World Creativity and Innovation Day on Wednesday 21st April 2021, the GCCA (Global Cement & Concrete Association) announced the expansion of its innovation programme, ‘Innovandi’, to encompass a new Open Challenge innovation accelerator programme. The Open Challenge programme brings together start-ups and leading cement and concrete producers to create innovations needed to reduce their carbon emissions and solve the climate emergency.
I’m in strong agreement with the GCCA when it says that innovation is vital for the cement and concrete industry as it aims to provide society with carbon-neutral concrete by 2050. As the GCCA notes, this goal is ambitious – requiring huge changes across the value chain in how we manufacture, use and recycle concrete. As the GCCA also highlights, innovation will be crucial at every stage, from new cement and concrete chemistries to kiln technologies, clinker production, fuel switch and carbon capture to ensure lower emissions in line with the global climate ambition.
In 2019, the GCCA launched the Innovandi Global Cement and Concrete Research Network to bring scientific institutions and industry leaders together to collaborate on innovation to aid the sectors’ goal of reducing carbon emissions. The network, which has 40 leading scientific and academic institutions and 30 industry partners, focuses on scientific research and has made initial progress with the agreement of projects across several areas.
GCCA and GCCA-member commitment to cement and concrete industry sustainability came over loud and clear last year when I interviewed the Association’s then-new chief executive, Dinah McLeod, for Aggregates Business Europe
A vitally important part of the GCCA’s sustainability plan is getting big industry buy-in, and the Association’s member companies make up 40% of global cement production. Having secured the big industry players, including LafargeHolcim, CEMEX, HeidelbergCement, CRH, Buzzi UNICEM, Dalmia Cement, Titan Cement, Vicat and
Votorantim, the GCCA is now looking to recruit more small and medium-sized ambitious sector companies.
As the GCCA states, the cement and concrete industry is already transforming, driven in part by a range of emerging technologies that will play a key role in its sustainability mission. These innovations include CCUS (Carbon Capture & Usage) pilots working in varied global locations. Within the built environment, innovative uses of concrete include 3D-printed and self-healing concrete, porous concrete that allows water to flow through it to eliminate flooding and prevent damage to communities and ecosystems, and concrete roads that will enable electric cars to recharge.
Membership of the Innovandi Research Network is open to cement and concrete producers and admixture companies. For more information about how you could support this vitally important and now expanded industry project, visit https://gccassociation.org/ innovandi/
Speaking of eye-catching new projects, how about creating printed Lego-style bricks from waste construction materials?
Engineers behind the three-year DigiMat project at Brunel University London hope to develop and demonstrate an eco-friendly cement mix created from building waste, easily printable into new, tight interlocking blocks for use in new buildings.
The university’s EU Commission-funded research team says its objective is to decrease the CO2 footprint of printed products compared with that of traditional virgin concrete and cementitious mortars by developing printable mixtures that will use up to 100% recycled aggregates. The team ultimately plans to demonstrate its technology by printing out a series of 50cm x 50cm recycled bricks slotted together to form an interlocked wall, similar to one built from Lego.
With the term ‘Build back better’ being very much in vogue among governments announcing their COVID-19 pandemic recovery plans, ‘Lego’ bricks could be in great demand. GW
HeidelbergCement is upgrading its plant on the Swedish island of Gotland to become the world’s first carbon-neutral cement plant.
The German building materials giant will scale the installation at the Slite plant of its subsidiary Cementa to capture up to 1.8 million tonnes of CO2 annually, corresponding to the plant’s total emissions.
Additionally, using biobased fuels in the cement production at Slite will increase in line with the group’s commitment to significantly raise the share of biomass in the fuel mix. The full-scale capturing of the plant’s CO2 emissions is targeted for 2030.
“HeidelbergCement will be the leader in the global cement industry on its transformation path towards climate neutrality,” said Dr Dominik von Achten, chairman of the managing board of HeidelbergCement. “Key for decarbonising our industry is to find, apply and scale technical solutions for carbon capture
and utilisation or storage. After gaining valuable experience with CCU/S technologies in Norway and other countries, we are excited to take the next step with a completely carbonneutral cement plant in Sweden. This will be a game-changer for our industry.”
The breakthrough project supports Sweden’s ambitious carbon-emission reduction goals. The carbon-capture facility will be built next to the existing plant in Slite, where three-quarters of the cement used for concrete production in Sweden is currently produced. The authorisation processes and the construction period are estimated to take just under ten years.
several kilometres down in bedrock.
A feasibility study, which has already been launched, will address critical issues related to technology selection, environmental impact, legal issues, financing, logistics, and energy supply. The captured CO2 will be safely transported to a permanent storage site offshore,
HeidelbergCement is currently building the world’s first full-scale installation for carbon capture at the Brevik cement plant in Norway, capturing 400,000 tonnes annually or 50% of the plant’s emissions from 2024 onwards. “Based on the positive collaboration with the Norwegian government
and other partners at our site in Brevik, we have now chosen to significantly ramp up our ambitions for a carbon-capture installation in Sweden that is four times larger,” said Giv Brantenberg, general manager of HeidelbergCement Northern Europe. The planning for the plant in Slite will benefit significantly from experience gained at Brevik.
Oxbotica and TRL have piloted the use of the first code of practice for the safe and cost-effective deployment of autonomous vehicles in unstructured off-highway environments, with a live trial conducted in a UK quarry using several off-road vehicles.
The Innovate UK-funded consortium has developed and demonstrated capabilities to adapt and retrofit autonomy to any vehicle, using robust, low-cost sensors and has drafted a code of practice that identifies the key elements for safe and efficient deployment of autonomous vehicles in offroad industries.
To demonstrate the code of practice and highlight its potential to work across various vehicles and industries, Oxbotica and TRL deployed a Ford Ranger and Range Rover Evoque, retrofitted with Oxbotica’s world-leading autonomy-software platform, in an unnamed British quarry in April 2021. The vehicles were fitted with a full suite of sensors, including LiDAR, RADAR, and stereo cameras. Oxbotica’s world-leading
technology has already operated in various environments without road markings across Europe, Asia and America. Its pioneering software seamlessly transitions between sensors to work across multiple domains and environments. The software can use sensors independently or fused in any combination, meaning vehicles can drive with or without maps, depending on what is available at any
Ben Upcroft, VP of Technology at Oxbotica, said: “Our autonomy-software platform is capable of being integrated with any vehicle, in any environment. To harness the true power of this technology, operational regulations need to be developed in unison to ensure safe and efficient deployment. Consortiums such as this are a key stepping stone in ensuring the safe operation of autonomous vehicles in complex scenarios, and enabling the scale-up to full commercial deployment in industry settings.”
Dr Ianto Guy, project lead at TRL, said: “This code of practice seeks to provide highlevel guidance to organisations, in all sectors of the off-highway industry, on the ways in which working practices should be adapted to ensure that the adoption of autonomy is as smooth and safe as possible. It is hoped that off-highway industries will use this code of practice as a starting point for discussion and build on the recommendations made here to develop comprehensive best-practice guidelines.”
The HD605-8 integrates the latest Komatsu engine technology, for increased power and reduced fuel consumption. Productivity is maximized and costs are reduced. The hydraulically-controlled wet multipledisc brakes and retarder give the operator great controllability, and a new spacious and ergonomic
As independent, family owned Longcliffe Quarries fast approaches its milestone centenary celebrations, the company, founded in 1927, recently partnered with wet processing equipment manufacturer CDE to help realise its ambitious environmental objectives by unlocking value from its discarded quarry byproduct, a significant waste stream at its Brassington Moor Quarry.
The Derbyshire-based business produces over one million tonnes of high-quality calcium carbonate powders and granules every year. Quarried from pure limestone deposits, its calcium carbonate products are vital components in animal feeds and pet foods. Its powders and granules are also supplied into the glass, plastics, and pharmaceutical industries and many more.
“We are quite a wasteful industry,” remarked Longcliffe Quarries Managing Director Viv Russell, adding that the company generates “about 300,000 tonnes of waste per year.”
The materials processor, in an effort to strengthen its commitment to sustainability in the UK’s quarrying sector, sought to address the issue by investing in a state-of-the-art turnkey CDE wet processing solution.
Previously discarded clay-bound material is now being processed through the wet processing plant at a rate of 220 tonnes per hour recovering up to six different products from heavily contaminated material and creating new, high-value revenue streams for Longcliffe Quarries.
High-quality single-sized aggregates and sand grades are among the key products being recovered which is maximising available reserves and supporting Longcliffe Quarries to realise its environmental targets by upgrading its low-grade quarry by-product into saleable resources which can be returned to the local construction market.
Longcliffe Quarries is committed to a sustainable future and its CDE solution is supporting the company to achieve zero-carbon quarrying operations by 2027. Already, 98% of its energy is generated by renewable sources.
Its CDE wet processing solution, the single largest investment made by Longcliffe Quarries, has led to a significant 12% reduction in the quarry’s load and haul fuel usage by efficiently processing its clay-bound material. The company’s recent achievements in further enhancing its environmental footprint follows an almost 70% reduction in net emissions recorded at Brassington Moor Quarry since 2014/15.
“We’re recovering up to six new products from heavily contaminated material.”
Viv Russell
CDE operates a unique co-design approach which involved working closely with Longcliffe Quarries to design a customised wet processing solution tailored to meet its specified commercial and environmental objectives as well as integrating seamlessly with the existing equipment already on site.
Engineered to maximise product yield from heavy clay-bound feedstock, the resulting plant features an R4500 primary scalping screen; CDE’s signature AggMaxTM modular logwasher setup for scrubbing and sizing; CDE’s patented EvoWashTM classification and dewatering system; and an AquaCycleTM thickener for industry-leading water management.
Oversize product is fed into the R4500, the highpower conditioning system created to handle the most difficult and heavily contaminated material. This prescreening method removes the +90mm oversized material and classifies it for further processing. The AggMaxTM combines feeding, scrubbing, screening and sizing on one chassis. Suitable for a variety of material streams and across various industries, it maximises product yield from feed material producing a wide range of sand and aggregate products. CDE’s EvoWashTM fines material classification systems recovers and dewaters fines producing consistent graded sand products ready for market straight from the belts.
Central to the system and to addressing the availability of clean water at Brassington Moor Quarry is CDE’s AquaCycle thickener. It is supporting Longcliffe Quarries to maintain its environmental commitments by allowing for up to 90% of the process water to be recycled and recirculated back into the system.
Offering near-total independence from fresh water supplies, the CDE wash plant requires only a small top-up water supply resulting in a highly efficient system extending significant operational savings to Longcliffe Quarries.
In addition, the plant also features CDE CORE, a suite of smart technology tools that offers plant operators greater control over their plant and access to real-time data on how their
plant is operating to maximise plant uptime and throughput.
The total solution delivered by CDE has exceeded expectations and is supporting Longcliffe Quarries to both maximise new commercial opportunities with its recovered sand and aggregate products and achieve its longer-term sustainability aims.
The materials processor is now processing high volumes of low-grade feed responsibly and efficiently, turning heavy clay-bound material into saleable products for the ready-mix and decorative markets.
Talk to CDE today about your processing needscdeglobal.com
Aurélie Delannoy is the director of Economic Affairs at the MPA (Mineral Products Association) and the Economic Committee chair at UEPG (European Aggregates Association). She spoke to Guy Woodford about the current health of the UK and wider European mineral products industry and highlights the big industry issues her vital work is helping to address
Whether you need crushers, screens, feeders, washers, conveyors, air separators, or all of the above, the Trio ® range has you covered. We’re not here to sell you one piece of the puzzle, our highly skilled team of Weir Minerals engineers look at your entire operation and decide how the Trio ® range can help. It’s everything you need to run a Construction Aggregates plant, all in one place. Visit www.theanswer.weir to learn how the Trio® range helped CNC Crushers.
Last year’s UEPG-estimated and COVID-19 pandemic-influenced reduction of just 5% on 2019’s 4.2 billion tonnes aggregates output of the EU27, UK, EFTA (European Free Trade Association - Iceland, Liechtenstein, Norway and Switzerland), plus Ukraine, Belarus, Moldova, Turkey, Israel and the Balkans, tells you all you need to know about the sector’s resilience, says Aurélie Delannoy.
Unsurprisingly, the MPA’s director of Economic Affairs and UEPG Economic Committee chair has other figures close to hand that illustrate the aggregates and wider mineral products industry’s ability to adapt and continue to operate in extreme conditions.
“The UEPG collates production data from 42 European countries, and what we saw is that some countries were hit quite hard – such as Spain, France, Germany, and the UK. But there were also some countries, like Poland and Norway, that posted growth rates in 2020 compared to 2019. I think this is partly based on how COVID-19 lockdowns were approached, along with some countries being better equipped to operate in extreme circumstances. However, out of 42 countries – 10 saw growth, and 16 showed a less than feared production decline. We are waiting to confirm data on the other countries.”
Delannoy says efficient administering of the €750 billion EU [COVID-19] Recovery Fund in the 2021-2023 period will be crucial to sustaining growth in European mineral products demand.
“The caveat to all big political spending commitment announcements is the time lag from when the announcement is made to seeing the difference on the ground. While the Fund is linked to COVID-19 recovery, it will also assist in the transition of countries to lower carbon economies and in their digital transformation. From an economic perspective, a lot will also depend on the recovery of the tourism industry, particularly those of southern European countries.”
Delannoy says the UK market last year was very much a tale of two halves. “The first half of the year saw COVID-19 and the first lockdown cause major disruption to both construction activity and the supply chain. There were mass closures of housebuilding and commercial construction sites, and construction output collapsed, especially in April, before starting to pick up a bit in May. Looking at Q2 2020 mineral product demand, aggregate, asphalt, concrete, and mortar sales were all down 35-65% below where they were at the end of 2019. It was an unprecedented decline.
“Unexpectedly, though, there was a very rapid market recovery that came in the
second half of 2020. This propped up mineral product demand and was driven by house landscaping and home improvement works, along with infrastructure works, notably HS2, which is gaining momentum. Last year was still down mineral product sales-wise compared to 2019 as you can’t write off three months and hope to make it up in a short space of time. But the market decline was far less than we originally feared.”
Turning her attention to the first four months of 2021, Delannoy says that the UK construction industry and mineral products demand has shown resilience in the face of a “number of headwinds”. “There has been a further lockdown and associated restrictions, Brexit, and a quite wet winter with heavy rainfall, particularly in the east of England. All these factors impact construction activity and mineral products demand.
“MPA members have told us that March was a lot better than January, but if you look at Q1 data overall, the recovery continued. Construction output is now only 4-5% below where it was before the pandemic. Looking forward, the likes of the CPA (Construction Products Association) and Experian are forecasting double-digit growth in construction output this year and a further 5-7% growth in 2022. The drivers behind this will be housing and infrastructure, as well as repair and maintenance work.”
“Further recovery in mineral product sales during the rest of this year into 2022 is predicated on the infrastructure project pipeline that the government has put in place”
Delannoy says UK mineral products sales have also seen encouraging growth in the first few months of 2021. “They are recovering from last year’s low base. Asphalt sales are particularly noteworthy, linked to a rise in road construction. In fact, on a quarterly basis, asphalt sales have actually exceeded pre-pandemic levels, although annual totals are still down.
“Further recovery in mineral product sales during the rest of this year into 2022 is predicated on the infrastructure project pipeline that the government has put in place. There is quite a lot of concern about demand outside of that, especially in commercial construction.
“Back in 2019, UK commercial construction, including retail and offices, was the second-largest category of new building work after housebuilding. However, before the pandemic, it was already being affected by Brexit-related uncertainties, which reduced investment. The shift to online retail has become more acute during the pandemic, impacting on business confidence. The pandemic has also brought the future of homeworking and office construction to the fore. Given these factors, we don’t expect this part of the construction industry to recover fast. This hits demand for ready-mixed concrete, which is used in a big chunk of commercial construction works.”
Delannoy notes that UK and wider
European market forecasting is made harder by the fact that although the COVID19 vaccination programme in the UK is encouraging, more needs to be done in other countries.
Having worked at the London-based MPA for more than seven years, Delannoy, who hails from Lille, northern France, last year also took on the role as chair of the UEPG’s Economic Committee.
Speaking of her 2021 priorities across the two roles, she says: “The most immediate priority for the MPA and UEPG is to ensure that mineral extraction is considered part of the solution in the context of the post-pandemic recovery and Europe’s long-term growth plan, while, at the same time, meeting and adapting to the challenge of climate change.
“The consensus internationally is that the recovery should include large-scale investment in new large infrastructure based around low carbon and environmental protection. A range of mineral product materials is critical to delivering this, and we want governments to understand that the supply of these materials should not just be assumed; they need to be properly planned, monitored and managed.
“At the MPA, one of the tools we have to inform this debate is long-term mineral products demand and supply scenarios covering the next 15 years. The first document based on these was published in 2016. I hope
“The consensus internationally is that the recovery should include large-scale investment in new large infrastructure based around low carbon and environmental protection”
to fully update this document, taking into account the unprecedented situation we find ourselves in, including the unprecedented policy response by governments. Crucially, none of what governments want to do infrastructure-wise is possible without our industry.”
Delannoy says three big areas are currently dominating MPA members’ discussions with her and Association colleagues. “In the short to medium term, they are looking at the foundations of the pandemic recovery, the implications of Brexit, particularly around trade between mainland Britain and Northern Ireland, and how they can meet the UK Government’s net-zero carbon emissions by 2050 target.”
The importance of the UK mineral products industry is captured in MPA-collated data. The industry directly contributed to the UK economy by generating over £5.8 billion in gross value added in 2018 and a turnover of £16 billion. It also enabled a further £597 billion turnover in industries downstream in the supply chain. The industry employs 81,000 people directly at over 2,000 active sites and plants and supports an additional 3.5 million jobs throughout the supply chain.
“Our industry is critical to delivering both the UK and EU Government’s infrastructure strategies, decarbonisation and the UK Government’s ten-point plan for a green industrial revolution,” explains Delannoy. “Our job at the MPA and UEPG is that policymakers are aware of the impressive contribution the mineral products industry makes, not only in terms of economic activity but in terms of biodiversity and site restoration recovery. A lot of work is also going on in the concrete industry, for example, in going beyond the net-zero carbon emission target.”
Delannoy says the COVID-19 pandemic has placed even more attention on UK and wider European mineral products production site health and safety. “It has enabled the industry to prove its great work in this area and to adapt to extreme working conditions.”
The wide variance in the size of national mineral products markets is an important factor, says Delannoy, when assessing country and regional operating differences within the European mineral products industry.
“There are some very big national producers, like Russia, which produces over 700 million tonnes of aggregates a year. Following that, you have Germany producing almost 600 million tonnes per year, France producing over 400 tonnes, and Poland and the UK, which each produced 272 million tonnes in 2019.
“Another interesting area is per capita annual consumption. In Norway, it’s 23 tonnes per capita. That’s a lot when you consider the UK, for example, is four tonnes per capita. In Ukraine and Moldova, you get down to two tonnes per capita. The variances can be due to the state of the economy, building preferences, and climate.” According to the latest UEPG figures, Europe’s average aggregates consumption is six tonnes per capita.
Delannoy also notes a big difference in recycled aggregates production rates. “In France, Netherlands and Germany, recycled aggregates make up 20-30% of overall aggregates production. The UK has had a 28-29% recycled aggregates rate within overall aggregates production in recent years. That’s twice the rate in the mid-1990s and represents a significant contribution to total aggregates supply.
“In terms of growing recycling rates across Europe, their availability depends on a local and suitable supply of demolition waste, but at the same time, there is more emphasis on a longer lifespan for building products and avoiding waste.
“This means more renovation of buildings and infrastructure, and adapting to climate change and extreme weather conditions, in line with the EU Green Deal.”
I am curious to know whether Delannoy
recovery and what type of policy drivers are put in place.
“If you compare the current crisis to where we were in the 2008-2012 period after the 2008 global financial crisis, they are two different crises. The 2008 crisis was essentially a financial crisis led by the housing sector, which negatively impacted the construction industry. The current COVID-19 pandemic is a health crisis with governments internationally placing construction, via infrastructure investment, at the heart of recovery plans.
“This has created an opportunity to create a new normal: better buildings, improved infrastructure, and a better response to climate change, including more biodiversity.
The MPA has for a long time called for greater clarity in the UK mineral planning system, the absence of which, the Association says, threatens future supplies for construction.
“An area to watch is the Government changes to the national planning regime aiming to make the English planning process faster, simpler and more predictable. However, it is focused on housebuilding and does not consider the more holistic picture, including mineral planning needs.
“From a wider European perspective, a lot of attention is being paid to the EU’s sustainable finance initiatives trying to encourage private financing of projects that improve biodiversity and helps the transition
“Nobody wants a quarry in their back garden, yet everyone wants more housing, better transport and other infrastructure”
“There is also the EU Biodiversity Strategy for 2030, which aims to have strict protection on 10% of European territory, and there is a potential risk for our industry in not being able to access sites within that area. There is a need for policymakers to recognise the work our industry is doing in terms of wildlife habitat creation and biodiversity.”
Focusing on the impact of Brexit, the UK’s withdrawal from the EU and the European Atomic Energy Community on 31 January 2020, Delannoy says: “In mainland Europe, there is very little impact on the aggregates market as materials have very short ranges of transportation. It is more of an issue for the UK market. It exports marine aggregates –mainly to Belgium and the Netherlands, but also to France. There are also exports of mineral products like clays, lime, and dimension stone. On the import front, the UK imports cement and machinery parts, most of which comes and goes from the EU27.
“Since the start of this year, MPA members have been reporting a rather challenging trading environment in terms of non-tariff barriers, more paperwork, and lengthy customs procedures, and added logistic and storage costs. The UK and EU governments can do better on making things more straightforward. Currently, the MPA and MPA Northern Ireland are trying to push governments on both sides to inject a little bit of pragmatism and willingness to improve on this situation as, ultimately, everyone would benefit from that.”
Asked how she sees the aggregates and wider mineral products industry in Europe in a decade’s time, Delannoy says: “I think visually the infrastructure of the industry will look pretty much the same because the fixed plant is bought for the long term. Functionally, the transition to net-zero operating will
have become more apparent. There will have been a change in the energy used to power plants and machinery on-site and vehicles transporting it to customers. Mineral extraction sites will also be more linked to renewable energy production. There are already examples of companies doing this.”
Delannoy believes the European mineral products industry’s work to restore former production sites to nature will be more recognised by government policymakers in 10 years. “The UK mineral products industry, for example, has already created around 80km² of priority wildlife habitat through site restoration, and a further 110km² are set to be created. That’s equivalent to half the size of the Isle of Wight! It shows that our industry is walking the walk when it comes to site restoration and biodiversity.
“I have to admit to being very puzzled at the lack of awareness of what the mineral products industry is and does to help the UK economy and our way of life. Nobody wants a quarry in their back garden, yet everyone wants more housing, better transport and other infrastructure. The reality is not hitting home of what we need to meet this demand, and that’s especially true of Government policymakers.”
Improving the UK and wider European mineral products industry’s diversity is another key issue for Delannoy. “We need to bring more women and ethnic minority workers into the industry and younger people. We can only get stronger by doing this.”
Before joining the MPA’s executive team, Delannoy spent three years as a research officer at the NIESR (The National Institute of Economic & Social Research), Britain’s longest established independent economic research institute.
Her impressive academic background
includes postgraduate research in Petroleum Economics at the University of Lille; a two-year Masters degree in European Economics (first year at Vilnius University in Lithuania, and the second at the University of Kiel in Germany); and a BSc degree in Economic Analysis & Management Studies from the University of Lille.
“I’ve lived, studied and worked in four European countries and travelled across the continent. I was once a cleaner, a call centre operator, and I have been a secondary school and university teaching assistant. I have also been an academic, and now I am a business economist. I think my journey shows that I am really an economist at heart. I am also a mum now to a two-year-old, which has its own challenges.
“I think my life and career to date have given me a certain level of personal resilience. It has also exposed me to people from different backgrounds who have their way of doing things. This is quite important in helping me do my work with the UEPG, in particular. It is not just about different cultures; it is different mindsets. I am used to that and enjoy this side of my work.
“My approach to work and life is to never stop learning. The day you stop learning is the day you stop moving forward. Communication and listening skills are also so important. You need to present concepts and ideas clearly. In my line of work, you also need to be able to handle scrutiny. I also love being so in touch with the mineral products industry, being a practical economist and getting my hands dirty!”
It will be very much to the UK and wider European mineral products industry’s great benefit if Aurélie Delannoy continues to crunch numbers at the quarry data face for many years to come. AB
THE NEW MOBICONE MCO 90 EVO2 WITH SPECTIVE CONNECT
EFFICIENT, INTELLIGENT AND TOUGH. SPECTIVE CONNECT gives you access to all important information on your smartphone – for more efficient operation. Intelligent overload systems ensure stable processes even under challenging conditions. The cone crusher combines high performance with best product quality and stands out with exemplary team capability: In combination with the MOBICAT MC 110 EVO2 jaw crusher, it ensures optimum throughput. Your team player in hard rock: the MOBICONE MCO 90 EVO2.
www.wirtgen-group.com/mco-90-evo2-kleemann
How best to improve crushing and screening plant sustainability is a hot topic in the global quarrying world. Guy Woodford reports on four leading manufacturers whose new models are looking to help customers meet their sustainability goals
Metso Outotec’s new Lokotrack e-Power range brings the diesel-electric Lokotrack mobile crushing and screening units into one distinctive offering. The range includes 15 crushers and six screens, making it the market’s broadest portfolio of hybrid mobile crushing and screening equipment.
“We introduced the first Lokotrack E-models already 35 years ago, so we are one of the pioneers in this field,” says Kimmo Anttila, vice president, Lokotrack solutions at Metso Outotec. “During the past couple of years, the demand for hybrid solutions has really taken off as environmental regulations have become increasingly stringent in more countries. In fact, sales of the Lokotrack E-models have doubled in five years, and we expect the trend to accelerate.”
The Lokotrack e-Power range is an important factor in realising the goals of Metso Outotec’s Planet Positive initiative. With Planet Positive, Metso Outotec is committed to limiting global warming to 1.5°C. Aggregate crushing is very energyintensive; thanks to the development actions to lower fuel consumption, the annual CO2 emissions of the Lokotrack equipment are 20,000 tonnes lower today compared to the situation before 2010.
“Lokotrack design principles are simple: optimise the operating costs, capacity, and end-product quality of the customer application. We give consideration to the total fuel consumption, including the engine and driveline technologies, but also to other
factors, such as the unit transportation weight and the engine stand-by function,” Anttila explains.
“Additionally, we have reduced the hydraulic oil and lubricant volumes by more than half to further ease the environmental burden. Based on our data, a Lokotrack unit uses as much as 80% fewer oils compared to our previous models and compared to many other brands on the market. Naturally, the hybrid driveline reduces the need for oils and lubricants even further.”
He concludes: “A diesel and hybrid offering complete each other; in remote locations where the power grid is not available, a diesel driveline is still the only viable solution. We are investing heavily in the development of sustainable technologies. Lokotrack is robust, energy-efficient, and highly mobile – and it meets the versatile needs of customers today and tomorrow.”
Powerscreen’s electrification strategy now includes an exciting new concept for the future of crushing and screening—the Eco-Warrior battery-powered screener.
Neil Robinson, Powerscreen product and applications manager, said: “Some may view this topic as a recent trend, but for Powerscreen, decarbonisation is multifaceted and has always been at our core. The Powerscreen mobile concept has always contributed towards decreasing the carbon footprint per tonne of material produced. This is done by reducing unnecessary material handling of hauling and loading material to static plants in aggregate production or in the ability to recycle and reuse material at point
of use, for example, in roadbuilding projects where sub-base material is produced in situ. Using stockpiling conveyors as part of a track mobile set-up is another perfect example of how to cut out unnecessary double handling, reducing fuel consumption and therefore carbon production.”
Powerscreen has evolved its product range to reduce environmental impact by making its crushing and screening equipment as fuel-efficient as possible, using direct drive systems for its crushing range and improving engine capabilities and driveline design for its screening range.
Robinson explained: “Direct drive systems are proven to be 13-18% more fuel-efficient when compared with hydrostatic, resulting in significantly less carbon emissions, while improvements to our screening range have reduced engine speeds from 2,200rpm to 1,800rpm, which not only means cleaner engines with less emissions but also reduced fuel usage and therefore carbon produced. For example, a typical mid-size screener running at 1,000 hours per year has a fuel usage reduction of approximately 450 litres, which equates to 1.2 tonnes less of carbon produced annually.”
Another important tool for fuel efficiency is Powerscreen Pulse, in-depth machine telematics that help customers see how and where their machines are being operated, understand fuel consumption and carry out fault-finding activities to ensure optimised performance.
“Powerscreen was the first mobile crushing and screening manufacturer to offer in-depth
machine telematics with the launch of Powerscreen Pulse in 2013,” continued Robinson. “In the early days, it generated a large volume of data, but now our system has been refined to deliver actionable information with customised reports and suggested actions for more fuel-efficient operation.”
Electrification is currently a key focus of the Powerscreen decarbonisation strategy. The Powerscreen Hybrid range, designed to give customers alternative energy options to operate their range of crushing, screening and conveying equipment, has been dramatically enhanced to include more fully electric crushers and screeners and models powered by innovative combinations of diesel and electricity. These options enable customers to choose which fuel to use, depending on cost, location and availability, and are of particular benefit to customers who operate in an area where electricity is more cost effective than diesel fuel, where diesel engine noise is unwanted or on sites where electricity is the preferred energy source.
Robinson added: “Customers using Powerscreen Hybrid units powered off the grid have been able to reduce on-site carbon emissions by 57% per tonne of material produced. While our hybrid customers have traditionally been in environmentally conscious countries and states, where legislation or financial incentives are more focused on green energy, we are witnessing a significant uptake in non-traditional locations, as customers prepare to comply with increased government drives for carbon neutrality.”
engine size has been cut in half compared with the diesel-hydraulic unit, and the battery pack can mean emission-free running or give a power boost.
Working closely with automotive technology and using top-of-the-range, hyper-efficient drives and intelligent control systems, Powerscreen’s Eco-Warrior batterypowered screener has been designed to deliver on the powerful screening action that the Terex brand’s machines are famous for while being a self-charging or plug-in model that features a simple, quiet engine with no after-treatment requirements. The required
Robinson said: “To the best of our knowledge, this is the first battery-powered screener in the world and has been clocking up testing hours since it was built in 2019. It still delivers on the powerful screening action that Powerscreen machines are famous for, and we are now exploring taking it from concept to mainstream.”
Concluding, he added: “This isn’t a publicity stunt; the drive for decarbonisation is real, with the UK and other governments ruling that carbon emissions have to be reduced by 80% by 2050. It’s critical that we dramatically reduce our carbon footprint, and Powerscreen has many solutions available today in support of this. However, we’re not stopping there—we’re taking it to the
The Lokotrack e-Power range is an important factor in realising the goals of Metso Outotec’s Planet Positive initiative
next level, continuing to be the pioneers in adopting technology that supports the industry in meeting the requirements of government decarbonisation laws—this is the future.”
Sandvik jaw crushers are now delivered to quarrying, mining and construction sector customers with everything for plug-and-play installation.
“We deliver our jaw crushers with everything a customer needs for plug-andplay primary crushing operations,” says Mats Dahlberg, vice president lifecycle service, stationary crushing and screening. “It’s just to choose what extra components they require. There’s also a wide range of jaw plates that can be mixed and reversed to ensure optimal, versatile crushing.”
Sandvik says safety and sustainability are the global off-highway equipment giant’s priorities. A company spokesperson said: “We use the highest quality materials and parts in our equipment, while including lifting tools, guarding retraction and a modular maintenance platform for safe operation and maintenance. All Sandvik jaw crushers are built for the circular economy, meaning the complete machine – all the metal and rubber seals can be recycled.”
available with the Sandvik Reliability and Protection package, said to always keep customers in control of costs and efficiency.
“To continue as a leading global supplier, we now include everything our customers need for a fast start-up and reliable operations. Together with easy and safe maintenance, our jaw crushers increase productivity, offer true reliability and excellent availability,” says Martin Johansson, product manager, Sandvik jaw crushers.
Sandvik jaw crushers can be delivered with complete infrastructure including feed hopper, feed hopper interface, drive and subframe with v-belt guard and motor bracket, an innovative guarding retraction arrangement and toggle plate stop.
With the launch of the new MOBICAT MC 110(i) EVO2, Kleemann presents a mobile jaw crushing plant of the new generation. The further development of the tried-andtested predecessor plant is said to offer users groundbreaking technologies for optimising all areas of a typical workday.
In designing the new jaw crusher, Kleemann says it concentrated on the requirements of demolition and building
operators. With an hourly output of up to 400 tonnes per hour, the new mobile jaw crusher meets the requirements in the medium output range. It delivers an impressive performance in a wide variety of quarry and recycling applications, emphasising effective coarse crushing.
The development engineers at Kleemann’s main Göppingen, Germany factory wanted the MOBICAT MC 110 (i) EVO2 to give customers optimum transportability and a fast start-up. The model’s transport height was reduced by 20cm compared to its predecessor to 3.40m. Relocation is now possible with simplified transport utilising semi low-loaders. The start-up procedure itself takes only around 10 minutes and includes set-up times for flaps, belts and feed hopper.
A special highlight of the MOBICAT MC 110(i) EVO2 is a new effective two-stage overload system. It effectively prevents blockages and material bridging that can lead to unwanted downtimes. If uncrushable material enters the crushing process, the CSS (closed side setting) opens two times faster than with the predecessor plant or, as an option, even up to 40 times faster.
This increases the availability and thus the overall output.
With the further development of SPECTIVE, Kleemann says it has set standards for user interfaces in the sector even higher. This digital operating concept has an intuitive structure and revolutionises plant operation with its extensive features. The 12-inch touch panel offers optimised user guidance and visualisation. Furthermore, new components such as a radio remote control and a small radio remote control have been integrated into the SPECTIVE world. The new digital solution SPECTIVE CONNECT sends all-important plant data to the smartphone.
In the new MOBICAT MC 110(i) EVO2, Kleemann has integrated a series of new technologies and improvements. The CFS (continuous feed system) guarantees continued crusher utilisation for daily outputs up to 10% higher. The independent double-deck prescreen effectively separates fines before they reach the crushing process. This increases the total plant throughput and is gentle, for example, on downstream cone crushers in the second crushing stage. Improved feed behaviour is guaranteed on the one hand by the extra-long articulated crusher jaw, whereas a flattened transition to the crushing chamber makes an optimum material flow possible. The accessibility for fast, safe and convenient maintenance has also been optimised.
With its innovative technical solutions, Kleemann concentrates on energy efficiency in all its new and further developments. The company’s improved diesel-direct drive concept can be seen in the MOBICAT MC 110(i) EVO2’s economical use of fuel, minimising operating costs. The plant’s output-dependent fan guarantees an increased cooling capacity, works when required and reduces fuel consumption. With its forward-looking, innovative technologies, Kleemann says it prioritises sustainability and lower customer operating costs. AB
A large crawler excavator from a major global manufacturer is making a big impact in one southern European nation’s quarrying sector, while new zero-emission excavators and wheeled loaders are also making headlines. Guy Woodford reports
Hitachi’s new ZX490LCH-7 large crawler excavator is proving popular among Portuguese quarrying companies, demonstrating a positive impact on productivity and a claimed new comfort level for operators.
The new model – launched in September 2020 as part of Hitachi’s range of Zaxis-7 large excavators – has already been supplied to four quarries by Hitachi’s authorised local dealer in Portugal, Moviter.
Owned by the IGE Group, Windpark purchased a new ZX490LCH-7 to work at its quarry in the Penela region. Its decision to invest was based on its relationship with Moviter and the reputation of the Hitachi brand. “We recognise the high quality of Hitachi products,” says Nelson Simões, CEO of the IGE Group.
of the operations, loading the dump trucks with raw material. It is also being used to load a crusher and trucks with product at the end of the process.
“We wanted an excavator to work long hours without stopping,” explains Abel Torres, Socitop’s CEO. “We needed a reliable machine with a high level of versatility because we will use it on different job sites and applications, such as earthmoving after this contract. The ZX490LCH-7 represents Hitachi quality and excellent value.”
“We considered the total cost of ownership, compared to other machines, and the Hitachi excavator got the best numbers. That fact, together with the relationship we have with Moviter, and the quality of the after-sales service, made it an easy decision. The operators also love the machine, and that is important for us.”
Another ZX490LCH-7 is working at a quarry owned by Agrepor in Canas de Senhorim as part of a contract won by Socitop. The excavator is at the forefront
In Porto de Mós, Leiria, family-run business Garcogel has four quarries and specialises in the extraction of marble and limestone blocks. It is led by founder and CEO Garcia Anastácio and his sons, Paulo and Emanuel, and has recently added a ZX490LCH-7 to its fleet.
“In our region, there are several Hitachi ZX490 excavators,” says Garcia. “Our friends said it is a good machine, mentioning the excellent fuel consumption and overall productivity. It is also fast, extremely precise and easy to work with, and we have found that the hydraulics are spectacular.”
are delighted – the visibility, controls and feeling inside the cab are excellent. The power and speed also live up to the Hitachi name.
“In addition, I am also optimistic about the new digital solutions [provided by Hitachi]. The information can be useful for increasing productivity and reducing downtime and costs. Getting the most out of new technologies will also improve the performance of our overall operation. We can plan the daily work and production cycles of the site, in short and medium terms, to increase profits.
“All things considered, the ZX490LCH-7 is a very important asset to our company. Together, with the support of Moviter, we believe we chose the best solution in the market.”
Adelino Ferreira, CEO of Brivel, believes the new ZX490LCH-7 is an important asset to his company, which specialises in the production of aggregates and ready-mixed concrete. “Our operators
“At Moviter, we’re extremely proud to have supplied the latest Hitachi Zaxis-7 large excavators to four companies operating in the quarrying sector, just within the first month of this year,” says Rui Faustino, Moviter’s commercial manager. “Hitachi has continuously improved on previous generation machines to enhance the operator’s experience in the cab, meet the needs of owners, and provide support over the entire life cycle. By working in partnership with our valued customers, we can help them to create their vision.”
The use of reclaimed asphalt, or RAP, is an absolute necessity today. At Ammann, we offer you custom-made recycling solutions – including high RAP utilisation. At the forefront of these efforts is the Ammann ABP HRT Asphalt-Mixing Plant.
This plant is all about recycling. In fact, HRT stands for High Recycling Technology. The plant incorporates a high degree of technology and innovation, in particular the countercurrent drying process of the RAH100 recycling drum.
Low emissions
• Indirect heating
• Homogenous heat distribution
• Recycling rates of up to 100 %
• Recipe flexibility as there is no need to overheat the minerals
High efficiency
• Low exhaust temperature
• Optimal RAP temperature
Reduced bitumen damage
• No radiation heat
• Gentle heating of RAP
German off-highway equipment giant Liebherr has introduced a pair of new local zero-emission excavators for quarrying and mining extraction customers.
The R 976-E electric crawler excavator and the R 980 SME-E replace the ER 974 B machine. The latest electric excavators to be developed and produced by Liebherr-France SAS in Colmar are not just converted diesel machines; the models and their electric power system were designed and produced entirely by Liebherr.
Robustly designed and capable of withstanding extreme conditions, the R 976-E and R 980 SME-E weigh 90 and 100 tonnes, respectively, and are available in backhoe and shovel versions. They are said to stand out for their low noise level, optimum versatility and zero CO2/greenhouse gas emissions during operation.
In recent decades, Liebherr has demonstrated the quality and reliability of its electric technology with the success of its dedicated product ranges for mining, dredging and materials handling applications.
The electric system in the new Liebherr R 976-E 400kW crawler excavator is supplied with 6000V power via a cable connection, with the cable inlet in the centre of the undercarriage or on the sides if requested. A motor cable drum is also available as an option—a high-voltage 6000V current collector powers the machine. A switch cabinet transformer (high voltage/low
24V networks are located on the upper carriage.
The technology used in the R 976-E and R 980 SME-E is said to offer a host of advantages. Thanks to its constant speed, an excavator with an electric engine has a longer service life, whatever the load. Also, the high availability of transient power for complex machine movements enables very high productivity. The R 976-E’s low-voltage electric squirrel-cage engine drives the hydraulic system. The engine features heat shielding on bearings and motor windings. Integrated into a frame with a reinforced flange, it enables safe, soft starting.
Reduced maintenance and lower operating costs make an electric excavator more cost-effective than a diesel-engine machine, says Liebherr. For greater comfort, the R 976-E and R 980 SME-E are extremely quiet. The robustness, reliability, and costeffectiveness of the R 976-E and R 980 SME-E units make them products of choice
for environmentally friendly extraction applications.
The new Cat 992 wheeled loader for mining and quarrying customers is said to set a new standard by offering up to 32% greater productivity than its predecessor. This new large loader reduces maintenance costs by as much as 10% and offers up to 48% greater payload-per-fuel efficiency than the earlier model, the 992K.
Powered by the new Cat C32B engine with U.S. EPA Tier 4 Final/EU Stage V- and Tier 2-equivalent emission engine options, the new 992 meets the global industry’s demand for high-production equipment with greater payloads. Powertrain design enhancements to the transmission, axles and final drive, along with the new engine, deliver a 20% longer interval for planned component replacement.
Offering both standard- and high-lift configurations, the 992 delivers the lowest cost-per-ton when paired with fleets of Cat 775, 777 and 785 trucks. Standard-lift payload capacities reach 23.1 tonnes for quarry face applications and 27.2 tonnes for loose material handling, while high-lift capacities reach 20.4 tonnes and 24.5 tonnes in respective applications.
A new Z-bar linkage optimised for performance, and improvements to rimpull and breakout force, deliver greater machine capacity and efficiency. The new 992 has demonstrated in field testing up to 48% greater payload-per-fuel efficiency in applications where a four-pass match to 90.7 tonne trucks was achieved, versus five passes with the 992K. The powerful and efficient 992 provides up to 9.5% more rimpull during digging and up to 20% more breakout force, increasing productivity.
The new Cat 992 wheeled loader features an on-demand throttle mode to optimise payload-per-fuel efficiency without slowing production. New standard automatic
retarding controls disable the impeller clutch, enable the lockup clutch, and use the implement and fan pumps retarding to slow the machine on grade. The available advanced automatic retarding controls with engine brake feature offer full control of the loader’s speed on grade to maintain a desired hold speed.
Automating critical digging cycle elements, optional New Autodig Components further improve productivity and efficiency while reducing tyre wear. To stop slippage before it happens, a tyre slip prevention feature reduces rimpull before the tyres are set and increases rimpull when downward force is applied to the tyre. The tyre set function detects pile contact and automatically lifts against the pile to set the tyres and increase available traction. The lift stall prevention feature automatically manages rimpull in-dig to prevent hydraulic stall while lifting through the face, so the 992 spends less time in the pile.
Optional new Payload Overload Prevention allows for productivity and efficiency improvements by providing a large enough bucket to be used to achieve target pass-match across a range of material densities without the risk of overload. With the overload value fully adjustable based on the target payload, this feature can be configured to automatically stop or slow the lift function when the overload value is exceeded.
Improvements to the setback and strike plane angles, a longer bucket floor, and a stronger and larger bottom section increase the bucket fill factor by 10%. The taller side plate with level top surface helps to improve visibility beyond the bucket edge to the material pile.
Available Operator Coaching empowers operators to exceed productivity targets by measuring and providing feedback to teach proper operating techniques. Among other
operating techniques, this feature shows how to properly shorten travel, avoid unracking in-dig, enter the pile with a level bucket, reduce the dump height, and use the kickout.
CASE Construction Equipment has staged the European launch of its new G-Series Evolution wheeled loader range. Complete with comprehensive enhancements across its entire line, the new G-Series Evolution wheeled loaders, upgrading the 2017-launched G-Series models, are said to improve performance and productivity by increasing uptime. They also empower operators with greater control and understanding of the machine and its capabilities, resulting in increased profitably.
Designed to be reliable and save time, the G-Series’ all-new payload system is integrated directly into the wheeled loader’s primary display. It provides bucket-weight, pass counts, accumulated/running weight, job-tracking data and more, for high-volume loading and production environments.
CASE SiteConnect and SiteWatch also come as standard for three years on each CASE G-Series Evolution Wheeled Loader.
CASE SiteWatch telematics is a solution designed to gather critical information about the machine’s performance and location and make that data quickly available. Featuring a new dashboard, SiteWatch is designed for intuitive navigation that identifies issues without requiring operators and fleet managers to be physically present.
This new European product features an
all-new touchscreen display that provides tablet-like performance for accessing all critical machine settings and operational data, allowing operators to anticipate and react more quickly to real-time changes in conditions.
CASE has simplified the previous engine power management operating mode offering with two new ones: Smart and Max. Max mode is ideal when the operator wants to work with maximum engine performance in tough conditions. In contrast, the new Smart Mode delivers high performance and an enhanced operating experience through improved communication between the engine and transmission on less challenging job sites.
Operators can take advantage of the new parallel lift functionality across all boom configurations that assists in material retention and smooth loading by automatically maintaining the angle and position of the bucket or forks.
Thanks to extended service intervals from 500 to 1000+ hours, the total cost of CASE G-Series Evolution Wheeled Loader maintenance has been reduced by up to 20% when compared to the current range.
In addition, CASE has developed CASE Care, a standard, planned maintenance programme with genuine parts and lubricants available in Germany and the UK, with Europe-wide availability planned. The programme is underpinned by the support, logistics and technical expertise of the widereaching CASE dealer network. AB
Quarry operators are increasingly seeking connected machines that let them monitor hauling payloads in real time and help control their cost per tonne. Liam McLoughlin reports
Hauling vehicle operators at quarries are putting the emphasis on high productivity and fuel efficiency in what they seek from their machines, and are also increasingly asking manufacturers for greater connectivity.
That is the view of Trozell Per, product manager for Volvo CE, who adds that the total cost of ownership (TCO) is also key for quarry customers. “They like to keep control of the cost per tonne,” he adds.
Per says connected machines are attractive to hauling operators as they are able to monitor the payload in real time, for example by using Volvo CE’s LoadAssist system.
LoadAssist works in combination with the Maps app, a traffic management system which enables operators to connect all the machines in a large quarry to check on the exact current location of loaders and excavators. “You can also see where you go to dump a load and with that you can keep track of where you have dumped the different materials by type,” says Per.
He adds that the company is continually working on hauling innovations. From June this year tyrepressure monitoring, which is already available on Volvo CE wheeled loaders, has now been extended to its rigid dump trucks (RDTs) and articulated dump trucks (ADTs).
The manufacturer is further developing its Automatic Traction Control (ATC) system with a function called Terrain
Memory. This learns the quarry locations such as gradients where wheel slips have previously taken place and engages the ATC to get better traction and prevent this happening.
Volvo CE also constantly updates its Site Simulation tool, which inputs the data about a quarry to give operators recommendations on the best fleet configuration and site set-up to reduce cost per tonne and maximise profitability. The tool can perform mixed fleet comparisons, and consider factors including machine size, quantity, fleet configuration and the optimal size of attachments such as buckets.
“The emissions and carbon footprint issue is becoming more and more important,” says Per. “The customers of quarry operators are demanding that they show the carbon footprint of crushed material, for example. They come to us as the OEM and ask us for the carbon footprint produced by our products. That is a big focus for us now.”
Per says that safety is another issue that has a high priority for hauling customers. Volvo CE has linked with Hexagon on the latter’s proximity detection system (PDS) that can be installed on haulers in quarrying and mining applications to detect if there is anyone nearby. This is available as an option on haulers made by Volvo CE, which supplies the interface for the Hexagon system.
Europe and the US are the two largest markets for Volvo CE’s haulers, but Per
says that China is growing. He adds that the company has seen no major impact on its hauling business from the COVID-19 pandemic.
“We came from a strong position [pre-COVID] where the factories were running at full capacity,” he says. “Demand for rigid dump trucks and articulated dump trucks is still very high.”
Per adds that the major stimulus packages being made for infrastructure in the US, China and EU in the wake of the pandemic are offering more opportunities for sales of hauling and other quarrying and construction equipment. “They are investing in infrastructure to try and avoid going into recession and that’s positive for us,” he adds.
Volvo CE is also focusing on the development of electric autonomous quarrying solutions, having tested the concept in a 2018 trial at the Vikan Kross quarry near Gothenburg with its customer Skanska.
Following this trial, it has now developed the TARA autonomous transport solution featuring the TA15 electric autonomous hauler – which has a 15-tonne hauling capacity – as a critical part of the offering. The TARA system is currently being trialled with an unnamed customer in Sweden.
“We are working on the industrialisation of the TARA/TA15 system,” says Per. “We plan to make it commercially available with the first customer implementation in Europe by the end of 2021. That is the target but it will be on a small scale.”
He adds that it is difficult to predict the potential for autonomous hauling solutions in the quarrying market, but says: “We will see an increase in these systems once we have proved that they are cost-efficient, environmentally-friendly and that they work.
“We have had interest in the system across Europe including from Switzerland and Germany. The initial set-up costs are a bit higher, but once everything is set up it’s really cost-efficient to move material with this system.”
Per says that an increasing number of customers are now asking when they can expect to see electrified haulers. “Quarrying equipment including crushers and conveyors is increasingly electrified and operators expect us to do the same thing with haulers.”
Other recent innovations on Volvo CE haulers include downhill speed control, and the OptiShift feature which lets operators move from forward to reverse without touching any pedals.
Doosan Construction Equipment has launched the new DA30 and DA45 ADTs for markets in the Middle East and Africa (MEA). The DA30 has a payload of 28 tonnes, while the DA45 can carry 41 tonnes.
The previous version of the DA30 ADT was upgraded in 2018 with a range of features including a new cab, a new selflevelling front suspension and a new tandem bogie system, and these are all incorporated in the new DA30 model. A similar process has been applied in the new DA45, with a new cab and a semi-levelling front suspension that adjusts itself independently depending on the operating conditions to ensure a comfortable working environment for the operator. The cabs on the ADTs have new comfortable hand grips and foot rests and an improved layout for the display which is designed to be easier to use even for older eyes.
The new models offer a number of other features including a new design for the front frame and bonnet components on the trucks, which Doosan says has been created by its design team in accordance with the latest market trends. It adds that the new dynamic look given to the ADTs reflects the high performance, power and robustness of the Doosan hauling range.
new DA30 hauler has a payload of 28 tonnes
A number of functional changes on the new ADTs are designed to improve safety, comfort and serviceability. These include a new positioning of the diesel and tank. The latter is now much lower than before, allowing the operator to fill the tank whilst standing next to the machine (‘ground level filling’).
The new haulers are equipped as standard with a real-time payload measuring system with a light indication for excavator operators, which will help them to place optimal loads in the ADTs to ensure excellent productivity and low fuel consumption.
The greasing system has also been relocated to make it easily accessible from ground level. Space has been provided above the automatic lubrication system (which is standard) for additional grease cartridges and a filling pump.
In addition, the transmission filters have been installed close to the greasing system, where they are also very easy to access. All of these systems are protected to ensure that any excess drops of oil/grease are collected
and can be removed during service and maintenance. New improved maintenance access will also help operators to perform daily checks faster and more safely.
Both of the new machines are equipped with additional external round hand rails to prevent accidents and hazardous situations. Inside the cab, there is a new additional grip on the right-hand side for increased safety for the operator. The electronic and hydraulic systems in the new trucks have also been upgraded to offer improved performance with extended functionality and new technology.
Doosan says the developments in the new DA30 and DA45 ADTs have resulted from intensive market analysis, customer visits, interviews with operators and additional feedback gathered by the Doosan ADT product and R&D teams at the company’s ADT plant in Elnesvågen, near Molde in Norway.
“With all of these advanced features incorporated, the new Doosan ADTs establish a unique benchmark in load-carrying performance, fuel efficiency, enhanced controllability and high operator comfort, together with improved reliability, durability and reduced maintenance and servicing costs,” the manufacturer says.
German OEM Liebherr’s new TA 230 Litronic articulated dump truck has won the Red Dot Award: Product Design 2021. The judges of the international design awards praised the aesthetics and functionality of the Liebherr machine and the other winning
The TA 230 Litronic ADT is configured for maximum payload in continuous operation, including in difficult terrain.
The machine has a new lighting concept that features LED headlights to enable improved visibility and safety, both for the machine operator and those around the hauler. LED dipped-beam headlamps with integrated high beam illuminate the road and the extra powerful, optional LED headlights on the front of the cab illuminate the entire working area. The L-shaped multifunction light with animated light functions is a homage to the Liebherr brand name. AB
Demand for recycled and secondary aggregates is strong and growing in the UK and other parts of Europe and the wider world. Guy Woodford & Liam McLoughlin report
According to the latest Mineral Products Association (MPA) figures, 28% of the 250.9mn tonnes of aggregates supplied to customers in the UK in 2018 was recycled and secondary (R&S) aggregates. Within that impressive figure, 25% was recycled and 3% secondary aggregates (china & ball clay waste, colliery spoil, fly, furnace and incinerator bottom ash, iron & steel slag, slate waste, clay & shale, chalk). That UK R&S percentage of overall annual aggregates supply was the highest in Europe in 2018, with France a close second on 27% and Netherlands third on 24%.
The rise of the European and wider world recycled aggregates market complements the sustainability agenda of some of the world’s biggest building product makers. The likes of CEMEX, LafargeHolcim, HeidelbergCement and CRH have all committed to ambitious carbon emission reduction targets across their global operations.
The above quartet and other significant cement producers contribute to the Global Cement & Concrete Association (GCCA)coordinated Innovandi Global Cement and Concrete Research Network. Innovandi has brought together 40 top scientific and academic institutions and 30 industry partners to develop new ways to aid the sectors’ lower carbon emissions goal.
The Sheehan Group, a leading British construction materials and plant hire company, has called on the UK construction
industry to increase its use of recycled products following the news of another national materials shortage.
The UK Construction Leadership Council confirmed in April 2021 that cement, aggregates and plastic products had been added to the growing list of essential items in short supply, which already includes tiles, bricks, timber and steel.
The Builders Merchants Federation and Construction Products Association warned high demand for construction products combined with supply issues mean challenges will worsen in the short term. A shortage of raw materials was cited as part of the problem.
Following these warnings, the Oxfordbased Sheehan Group is encouraging contractors to source local recycled products and supplies to reduce the UK’s overreliance on global supply chains, improve the environment and support local jobs.
Tara Sheehan, finance director at the Sheehan Group, said: “This is the latest challenge the UK construction industry has been hit with due to an over-reliance on the global supply chain. It is leading to contractors struggling to obtain materials and hampering our economy at a time when the country needs to bounce back.”
She added that the Circular Driven Economy is key to long-term sustainability for the construction industry and the environment. Sheehan said that if more construction companies embraced its core
principle of keeping resources in use for as long as possible, it would help make the UK market more self-sufficient, protect the environment and jobs.
“The UK is over-reliant on raw materials and imported products,” she said. “But we can take greater control by using recycled materials. We produce recycled aggregate, sand, concrete, and blocks used in construction projects and have seen the benefits first-hand.”
The Sheehan Group has a water treatment facility used to wash construction and demolition waste destined for landfill, turning it into reusable aggregate and other products. Half of the recycled material is used in its construction projects, and the rest is sold to contractors.
Quarrying equipment manufacturers see increased business from customers looking for recycling application-suited crushing, screening, and washing plants, complemented by highly productive and ultra-efficient loading and hauling machines.
A new Hyundai HL960A wheeled loader is said to be proving its worth handling a wide range of recycled aggregates at G Webb Haulage’s Little Paxton quarry site in Cambridgeshire, England.
The loader is helping meet increasing demand from developers for recycled aggregates, which can meet a specification at a fraction of the cost of virgin material.
While offering a range of recycled aggregates from Little Paxton, G Webb
Haulage also operates a virgin stone quarry and a second recycled aggregates facility nearby.
The new Hyundai HL960A wheeled loader is already a firm favourite of the longstanding operator and Little Paxton site foreman Nigel Missen.
To handle the large amounts of incoming and outgoing materials, the company relies on a single, frontline wheeled loader. “We have had a number of machines over the years but have recently settled with Hyundai,” Missen explains.
Replacing an 18-month-old HL960, the new HL960A, supplied by local Hyundai dealer Willowbrook Plant, is kept extremely busy five and a half days a week.
The huge Little Paxton quarry contains a massive variety of recycled aggregates and soils ready for dispatch. Incoming aggregates are also catered for with a small processing area occupied by another Hyundai - an HX140 feeding a Sandvik crusher and McCloskey tracked three-way screener.
The arrival of the new loading shovel has seen the older HL960 machine retire to a slightly more sedentary life within G Webb Haulage’s fleet. The company runs a fleet of over 50 wheeled and articulated tippers and a small fleet of earthmoving equipment for both the quarrying activities and outside earthmoving projects the company picks up to service its local operations.
The large Little Paxton site and the variety of materials processed requires the HL960A wheeled loader to be flexible and agile. “With the amount of material we dispatch on a daily basis, having dedicated bays for each material wouldn’t be possible as we stock hundreds if not thousands of tonnes of the most popular products,” says Missen. “This means we need to be travelling from one end of the site to the other, sometimes after each truck. The Hyundai HL960A is ideal for this; it’s the right size for the site to give us the perfect combination of manoeuvrability and performance.”
feels the general-purpose unit fits their needs exactly.
The HL960A is powered by a new Stage V emission-compliant Cummins B6.7 diesel engine, delivering 168kW. The Cummins engine delivers slightly more power and has increased its torque output by 15% over the outgoing HL960 model. Meeting the Stage V regulations involves the loader using Cummins’ Single Module after-treatment system that incorporates a DPF (diesel particulate filter), SCR (selective catalytic reduction) and Urea dosing in a single unit, taking up 50% less space than the previous system. The large bonnet covering the machine’s vital components is electrically opened and gives ample room around the engine and a cooling pack for service access.
The HL960A rides on a pair of heavy-duty axles offering a ground clearance of over 400mm and, due to the short wheelbase, boasts a relatively tight 7.75m turning circle. Wide and well-spaced non-slip steps provide access to the large cab.
a bank of switches to the operator’s righthand side behind the main joystick. Joystick steering can be specified as an option, but Webb did not take this. “I like the steering wheel; it’s responsive and light to use,” says Missen. “I have been very impressed by the noise or lack of it in the cab.”
Willowbrook carries out servicing with remote monitoring of the machine undertaken through Hyundai’s Hi-MATE telematics system. The A model has Engine Connected Diagnostics (ECD), which reports any engine failures immediately to both the Hi-MATE system and the engine manufacturer themselves.
“The fuel consumption is good as is its AdBlue intake,” adds Missen. “If it stays as reliable as my old machine, I’ll be a very happy man.”
With an operating weight of 19.2 tonnes, the HL960A carries a straight-edge bucket with a capacity of 3.3m³. Many heavyduty and light material buckets are available for other applications, but G Webb Haulage
The Hyundai cab features large areas of glass to provide all-around visibility, in addition to
Rubble Master’s RM 120X mobile impact crusher, a hybrid model that can be both diesel-electric and purely electric-powered, has been in series production since autumn 2020. It is the Austrian manufacturer’s first NEXT philosophy crusher, combining enhanced safety, maximum efficiency and maximum performance.
In September 2020, due to increased orders, Taha Zahir, based in Kafr Qasim, a hilltop city near Tel Aviv in Israel, decided to expand its fleet with its second RM crusher, choosing the new RM 120X. Like Taha Zahir’s early-2018-purchased
RM 120GO!, the RM120X is processing construction and demolition (C&D) waste in an enclosed hall. The aggregate produced is then used as road substructure. Given that Taha Zahir’s processing takes place inside a building, the lowest possible dust and noise emissions were key concerns for the company when deciding on its new crusher.
Feed material with an edge length of up to 800mm is now processed fully electrically by the RM 120X to produce cuboid final aggregate (0-32 mm). In order to keep dust levels during the crushing process as low as possible, Taha Zahir also ordered a dust suppression system that minimises dust formation using water mist generated by a water pump and spray bar.
Every day, approximately 1,000 tonnes of C&D waste mixed with plastic, wood, and textiles are delivered to Taha Zahir. To ensure clean, high-quality final aggregate, the firm decided to install a wind sifter on both its RM impact crushers. The C&D waste is now free of unwanted light materials, leaving it able to produce a high-quality final aggregate.
The new RM120X is said to be very user-friendly, both during operation and maintenance. Rubble Master’s proven RM
machine operation and more accessible machine components - has been further developed for the new NEXT machines. With the innovative machine communication lights, the customer can now easily see the system’s current status. If the machine displays the green light, then everything is working perfectly. If the yellow light is on, the operator knows that a service is needed, and the red light indicates a warning.
about the new crusher’s safety features. As the first crusher in the NEXT series, the RM 120X keeps the operator well outside the danger zone during the crushing process. The radio remote control with display, RM GO! SMART (optional) as well as the machine communication lighting considerably increase the safety of the machine operator. All information relating to the crushing process is displayed in the RM GO! SMART App on a mobile device, smartphone or tablet. AB
Aggrecycle has invested more than £100,000 in new vehicles and branding as it relaunches from its urban quarry in the heart of Leicester, central England.
The recycling firm has developed a new offering for small local operators to provide the full range of recycled, decorative, and quarried aggregates for Leicester and the wider Leicestershire county and East Midlands region building trade.
Based at its urban recycling quarry in Syston St East, the company recycled more than 150,000 tonnes of material in 2020, as AR Aggregates.
Almost half of the relaunch funding has been spent on a tipper lorry for small deliveries up to four tonnes—the rest spent on branding activity, including a new livery for Aggrecycle’s large lorries.
The latest investment comes on the back of a £900,000 investment in state-of-the-art German crushing and screening machinery in late 2019.
Andrew Thompson, Aggrecycle’s managing director, who runs the business with his brother, Darren, the company’s operations director, says there is a growing market for clean, quality
recycled materials in the building trade.
“We know from our experience in construction and demolition that 99.9 per cent of spoil arising from these projects can be recycled. It’s part of our job to make that happen.
minimising landfill and keeping the supply of aggregates local to Leicestershire.
“Technology and equipment are so good now that the products we provide are indistinguishable from freshly quarried materials, so it makes sense to use them wherever possible.”
Andrew says Aggrecycle is keen to help reduce the carbon footprint of the regional construction industry by
“If we can do that, by careful pre-planning and maximising the segregation of materials arising during construction processes, then there’s no reason not to either recycle every possible element or arrange for it to happen.
“People talk about the circular economy – we’re putting it into action. We’re keen to work locally if possible and help see our materials, most of which come from local projects, re-used as the basis for new construction projects.”
In the continuing uncertain post-COVID conditions, some quarry equipment distributors are going against conventional thinking and stocking a larger range of wear parts. The increased number of parts might have to be kept in stock for a longer period, but it can avoid expensive air freight charges and lengthy waits for delivery. Liam McLoughlin reports
The current environment of uncertainty worldwide is impacting operations globally, one way or another - including supply chains, equipment manufacturers, distributors and quarry owners. Some producers have delayed their equipment investment decisions because of this uncertainty. Maintaining, or upgrading, their current equipment allows the luxury of time but, as the average age of the fleet starts to increase, parts and service take on a new importance.
Crushing and screening plant manufacturer McCloskey says that the timely and reliable provision of parts, and a proactive approach to maintenance, become the cornerstone of productivity and, ultimately, profitability. It adds that, for distributors, this represents a call to action and offers an opportunity to focus on customer support and service. In addition to price and parts availability, having a knowledgeable staff that knows its customers is key to keeping customers coming back.
Dealers for Metso Outotec-owned McCloskey have commented on how they
are working with customers in the current environment and how their business is adapting to the new environment.
Among them is Mark Senyard, national support and marketing manager for Kemach Equipment in South Africa, who says: “It’s not only about selling a new machine. The hard work starts after that, ensuring that the customer’s aftermarket needs are known and delivered upon.
“It is critical to understand what the customers’ expectations are and how best to support them.”
Tim Watson, marketing manager for McCloskey Equipment in the UK, says that ensuring machines are serviced and/or the correct maintenance items are used is not new or isolated to the aggregates business.
“Machines are used in so many different applications that it is impossible to see every eventuality,” Watson adds. “To assist with reducing any distance between our experts and operators, we are investing and deploying the latest technology to increase remote visibility and make communication easier, regardless of distance or location.”
In addition to price and parts availability, having a knowledgeable staff that knows its customers is key to keeping customers coming back
Philip Barr, CEO at MSC Group of Companies in Australia, has tackled the parts challenge head on by stocking a large range of parts. This might go against a lot of companies’ thinking but “if you don’t have the parts, you’re going to either need really expensive air freight to get them, or have to wait six or eight weeks, which doesn’t work when your customer could have two, three or four machines down. We can have some parts in stock for two, three or four years but it’s worth it in the long run.”
Readily available wear parts are a key component in the ongoing, and uninterrupted, process of crushing stone. Factors impacting a crusher can range from environmental factors, like moisture or temperature, to the material being fed into it, to the most basic of all - age of the equipment. In the current situation driven by the desire to extend the life of currently owned equipment, ongoing maintenance of the protective liners is a relatively straightforward means to achieve longevity.
The focus has turned to proper preventative maintenance conducted both by the end user and the equipment provider. This requirement further increases the need for services, particularly for operations that find they are short of resources at their site.
According to Shane Fleming, managing partner for Rock & Recycling Equipment in the US, “a lot of customers are having trouble finding skilled mechanics. It’s gone from a lot of people working on their own equipment to them needing good, dependable support. What I’ve seen is a shift with more and more people wanting a servicing option, that’s where I see things going.”
The general expectation is that demand will continue to grow as postpandemic stimulus spending is launched by governments to restore balance, and that after-sales support will continue to grow in lockstep.
Barr sums up one of the keystones of a successful after-sales relationship - keeping in touch. “Do what you say you’re going to do and ring people back straightaway. I think that’s really important these days. People want to be talking to someone when they ring you. They don’t want to be stuck on the phone getting passed around. Having one good contact they can talk to is important, a person with a good base understanding of the machines.”
Berco, a manufacturer and supplier of undercarriages and components to the
“We can have some parts in stock for two, three or four years but it’s worth it in the long run”
Philip Barr CEO, MSC Group
world’s main heavy-machinery OEMs, is strengthening its aftermarket business.
With over 100 years of experience and expertise in the industry, the Italian company is extending its high-quality product lines to give customers even better access to replacement components. The extended range will, says Berco, offer a very competitive TCO (total cost of ownership).
In its aftermarket offer, Berco supplies
track chains and shoes, idlers, sprockets, track and carrier rollers. A leader in the mining segment, the new strategic development will see the company boost its aftermarket presence in the highly competitive construction industry.
Through a strong collaboration with company dealers, a service presence will be established in strategically important locations. This will allow customers access to the right product, at the right time, in the right place.
To implement this new strategy, Berco has established a new team composed of dedicated experts who possess the experience and mindset to be successful in the aftermarket. The team will fully avail Berco’s comprehensive original equipment (OE) knowledge and pedigree while expanding its aftermarket construction offer.
Diego Buffoni, Berco’s head of aftermarket, said: “The introduction of a focused aftermarket strategy, a clear structure and an increased product portfolio are already creating many growth opportunities and revenue streams for the company. Our goal will be to provide every customer in our various industrial fields with a one-stop-shop offer for all their heavy-duty aftermarket needs.”
Berco’s aftermarket offer includes three different product lines: Original, Platinum and the most recent, Service. The Original Line provides customers with identical
components to OE parts in terms of design and production process. The Platinum Line goes one step further, surpassing OE in quality, durability and performance. This line offers tailored solutions to large machines that must operate in extreme climatic and soil conditions. With increased reliability and lifespan, the Platinum Line is designed to provide cost savings in the long term by allowing machines to operate for significantly longer periods without interruption.
The Service Line was created to supply machines in the construction industry. The inaugural line, which is aimed at excavators with capacities of 13, 20 and 30 tonnes, is now being made available to customers. This line comes with a very high warranty (2,000 hours under normal running conditions) and better resistance to abrasion, impact and humidity.
As a next step, the Service Line for dozers – chains, rollers and sprockets for the D4, D5 and D6 classes – will be completed during the second half of the year.
Following the launch of Sandvik Optitooth jaw plates, Sandvik Mobile Crushers and Screens has now created a number of complementary ready-to-order maintenance kits which include Optitooth jaw plates and its new Optitooth side plates for the Sandvik QJ241, QJ341 & QJ341+ jaw crushers.
The Swedish manufacturer says that benefits for its crushing and screening customers include longer wear life and convenience. With all parts in one kit, they simplify service, increase maintenance efficiency and consequently increase uptime.
The tailor-made Optitooth kits are designed around the natural usage of the wear parts in the crusher, and offer all components an operator needs with just one part number.
Sandvik says key customer benefits include increased performance – Optitooth Jaw plates are matched with the new Optitooth side plates which are designed to greatly increase the efficiency and extend the wear life of the crushing chamber.
It adds that the maintenance kits also improve profitability by increasing maintenance efficiency and productivity. They also enable equipment operators to replace their wear parts in just one service interval following wear patterns.
Sandvik says the kits also provide greater availability by avoiding delays or parts shortages with delivery of all components in one shipment.
It has created kits in three different offerings for convenience. Firstly, the Optitooth Fixed Kit 1 with an Optitooth jaw plate and new lower side plates.
The Optitooth Swing Kit 2 comes with a Swing Optitooth jaw plate and new lower side plates. Finally Optitooth Kit 3 features
one fixed and one swing Optitooth jaw plate, and new upper and lower side plates.
All the necessary components are supplied with the kit to keep the crushing chamber operating at optimal performance.
Sandvik says the new enhanced side plates introduced with its Optitooth Kits have proven to last up to three times longer in trials.
“This improvement in wear life matches perfectly with our Optitooth jaw plates, making them the ideal combination for superior performance,” it adds.
Volvo Construction Equipment (CE) says that steel hardness is of major importance for the service life of wear parts such as its excavator buckets.
The manufacturer states that the quality and hardness of the steel used in the wear parts can affect how quickly the bucket’s cutting edge wears down.
Volvo CE only uses 500 Brinell steel in its bucket edges, bolt-on edges and segments, which it says delivers superior service life compared to many cheaper offers. The company says that genuine Volvo CE parts are made of steel with consistent properties, with the same hardness throughout and not just a hard surface and a soft centre which can be the situation for other offers.
“By upgrading from 400 to 500 Brinell, the service life can increase by 70%,” the company adds. AB
CAs the global quarrying and construction world pursues growth after a long period of COVID-19 pandemic-induced disruption, demand for quality off equipment engines is likely to rise.
Guy Woodford reports
ummins could see an eight to 12% increase across its off-highway machine engine business in 2021 as the market recovers more rapidly than expected from the COVID-19 pandemic.
That is the view of Eric Neal, executive director of the U.S-headquartered on-highway and off-highway engine maker’s off-highway business, who adds the proviso that the upbeat forecast is valid “as long as we can get the material to build engines. We’ve got a lot of demand right now that can certainly support that growth, and maybe more actually.”
In a COVID-19-hit 2020 of general market contraction, China and, to a lesser extent, India were the countries providing the biggest boost to Cummins’ revenues, both for on-highway and off-highway engines.
Cummins’ full-year 2020 results, published in February, showed that revenues totalled US$19.8bn, 16% down on 2019. Sales in North America declined 21%, and international revenues declined 7%. Sales were down over the year in all major regions except China, where demand for trucks and construction equipment reached record levels.
Speaking to Aggregates Business about Cummins’ 2021 trading outlook, Steve Nendick, the company’s Global Off-Highway marketing communications director, said: “Our recently released Q1 2021 results painted a positive picture of the industry, with strong demand for our products across all global markets. Although this rising demand is encouraging, the rapid pace of recovery has undoubtedly placed a strain on global supply chains, leading to increased challenges. The shortage of key components and bottlenecks in global logistics have been the primary issues we have had to contend with.
“Unsurprisingly, the ability to maintain supply to our customers is our key focus, and we’re doing everything we can to mitigate any impacts of the pandemic. We’re also
“The investment will enable us to continue developing and integrating advanced diesel power for on- and off-road use, as well as alternative powers solutions including hybrid, electric, hydrogen and natural gas”
Steve Nendick, Cummins
ensuring that this is done while keeping our employees and stakeholders safe, taking necessary precautions at our facilities to protect against COVID-19. We remain cautiously optimistic about the global vaccine rollout, and we look forward to opening up our offices for people to return when it is safe to do so.”
Nendick said that since Cummins launched its Stage V Performance Series engine range in 2018, the business continued developing products that add value to customers, particularly for quarry and construction markets.
“This is typified by our recently launched Stop-Start capable B6.7 Performance Series engine, which gives operators the opportunity to eliminate unnecessary engine idling whilst still maintaining performance and reliability, leading to reduced overall running costs, noise and emissions.
“This extension of the Stage V Performance Series range follows on from the introduction of power units, ranging from 75-503kW, which make the integration process into applications such as crushers much simpler, thereby reducing the leadtime and cost for OEMs [original equipment manufacturers]. Similarly, we followed this up by adding dual rear-engine power takeoffs – REPTO, for short - to our B6.7 and L9 power units, increasing the capability of the engine to power more features on the equipment.”
With no further emissions reduction legislation for off-highway machines expected until 2030 at the earliest, Nendick says Cummins’ engineers are continuing to tailor engines for customer installations
to drive efficiency and reliability. “Our work doesn’t stop, and we will bring further developments to the market in the coming years.”
Nendick emphasised the importance of Cummins’ Darlington Technical Centre in North-East England. “It develops engines to meet the latest on-road and off-road emissions regulations for Europe and other regions where the company operates. The team works with the relevant authorities to ensure these products meet the required specifications throughout their useful lives. This includes an in-service monitoring programme for Stage V diesel engines, developing a system to measure real-world emissions in the tough working conditions of construction and quarrying machinery.
“We have plans to develop the centre further and increase its capability over the next few years. The investment will enable us to continue developing and integrating advanced diesel power for on- and off-road use, as well as alternative powers solutions including hybrid, electric, hydrogen and natural gas.”
Nendick said Cummins expects diesel to remain the “go-to power solution” for many quarrying and plant machines for the foreseeable future. “Additional capabilities will help Cummins develop ultra-clean and ultra-efficient diesel engines for the expected Stage VI regulations when they come, as well as Euro VII for on-road vehicles. Work is underway - so watch this space for further news of its progress.”
Volvo Penta is another major supplier of engines to global quarrying and mining plant customers. Andreas Nyman, the manufacturer’s manager of Field Test & Data Management, offers insight into the Swedish company’s approach to designing its quarrying and mining machine engines.
“Stone crushers face tougher working conditions than most construction machines. Moreover, their owners and operators need to count on them performing with power and durability at all times,” says Nyman. “An engine failure in a mine or quarry will not only disrupt production but also potentially
“Your work is much too valuable for you to waste time and resources on engines that cannot do the job”
Andreas Nyman, Volvo Penta
put operators at risk. So, how can engines be optimised to ensure stone crusher performance and uptime in demanding applications?
“Stone crushers need engines with a correctly specified torque curve and an ability to handle both heavy and light loads effortlessly. The engine needs to run at a high capacity and do so steadily without losing speed when handling heavy stones and rocks or high volumes of sand or gravel.
Additionally, Nyman says mining and quarrying customer plant engines should have long service intervals. “Two-hundredand-fifty-hour service intervals are relatively common, but that essentially means that those maintenance breaks that disrupt your uptime are relatively common too. This is partly why Volvo Penta’s engines come with 1,000-hour service intervals. Long service intervals allow you to focus on your operations, without frequent interruptions.”
Engine manufacturers and OEMs should ideally work in close cooperation, says Nyman. He stresses that doing so will foster solutions that are even better at serving the varying needs of their customers. “By getting a better understanding of a particular application or work environment, factors like engine performance, engine maintenance, and fuel consumption can be improved further.”
Nyman says attentiveness and innovation is a key combination when it comes to engine optimisation and development. “All of our Volvo Penta engines can run on HVO 100, for example. This is a much-appreciated feature, not least among customers who want to phase out fossil fuels from their production. There is also a growing interest in diesel-electric solutions for stone crushers. It is a very interesting concept and could be a step towards an increased electromobility portfolio.”
Nyman says Volvo Penta works with its customers out in the field (including down in the mines and quarries) to ensure that its engines always perform as they should, whatever the application.
“Some operators are used to engines failing and may even expect having to restart them from time to time. This practice should be a thing of the past. Your work is much too valuable for you to waste time and resources on engines that cannot do the job.”
A good example of this involved a quarrying project north of Stockholm, Sweden. “One of their stone crushers was overpowered for its workload and application. As a result, we decided to shift from the D8 engine to a D5 engine. We also changed the hydraulic pumps and reduced the rpm by half. This did not in any way affect the stone crusher’s performance or uptime negatively. Instead, we managed to cut fuel consumption by more than a third. Not only is that highly beneficial in terms
of the significantly reduced total cost of ownership, but it is also certainly better for the environment too. Lowered costs, without any compromise in terms of productivity or quality, in other words.”
To verify an engine’s durability, reliability and performance, Nynas says you have to “test it and test it and then test it some more”. He adds: “As for our Volvo Penta engines, they undergo in-house testing in test cells, as well as field tests. In these field tests, we install the engines in customers’ machines and test them in actual operations. This way, we can see how the engines work in – and respond to – certain applications, climates and environments.
“This rigorous testing process makes it easier to adjust and fine-tune the engines and make sure they come with the right torque response, power, emission requirements, etcetera. Our ambition is to test our engines in as many applications as we can, to make them the best and most well-adapted engines possible.”
Nyman highlights how advanced analytics can be used to study individual engines and components, as well as stone crushers and other machines in their entirety. This enables Volvo Penta and its customers to get an even better, deeper understanding of how they work. And, occasionally, why something may not perform quite as intended.
“Through advanced analytics, more specifically machine learning, you can create a virtual machine that receives and processes data from a physical engine, or a stone crusher, for example. The virtual machine learns from this data, gaining insights that would be difficult to get otherwise. This information is highly valuable in terms of product development. Positive features can be improved, and flaws can be detected, fixed and prevented.
“Data analytics is already a key part of our engine development projects. The next step is to use more advanced analytics on our data. That is now used as a proof of concept but will be the next key part of product and solution development. For example, we have used advanced analytics on data from our customers’ production engines; for predictive
maintenance and to learn more and further improve our engines.”
Nyman says Volvo Penta is currently working with OEMs to create state-of-theart energy propulsion systems. “However, it is our belief and experience that we should collaborate even more closely. Doing so allows us to better support OEMs in quality and maintenance and to continue to meet customers’ requirements as these emerge and develop over time. Moreover, it will put us on a common path towards better sustainability solutions for stone crushers and screeners.”
Speaking during a recent JCB virtual press conference event, Tim Burnhope, JCB’s chief innovation and growth officer, stressed how the event-unveiled machines all benefited greatly from the company’s new Stage V-compliant engines.
“The common thread today is Stage V engine technology. We’ve stated previously our clear belief that internal combustion engines will play a leading role in powering construction equipment for the foreseeable future. But the foreseeable future is not forever, particularly when it comes to fossil fuels. We will certainly need alternatives to fossil fuels sooner rather than later. Until then, engines will need to have close-to-zero impact on air quality and offer a route to zero greenhouse gas emissions. Stage V has been an important step on this road to zero.
“As a manufacturer of diesel engines, we have set out to ensure that diesel can be part of the environmental solution, not part of the problem. At Stage V our engines certainly deliver. The three-litre JCB 430 DieselMax engine delivers up to 7% improvement in fuel consumption, a corresponding reduction in CO2 emissions, and a 10% increase in torque to 440Nm for improved response and drivability. It also offers lower noise, virtually zero particulate emissions, and lower running and service costs.
“The higher power 4.8-litre JCB 448 DieselMax engine at Stage V delivers a fuel consumption reduction of over 5%, together with a corresponding reduction in CO2, All our Stage V engines produce virtually zero particulates and NOx [nitrogen oxide]. Our
journey towards zero emissions over recent years has been remarkable. We are very proud of what we’ve achieved at Stage V. Our engines lead the way on innovation. This is JCB’s clean diesel technology. It is here now. It delivers on Stage V, future-proofs the JCB range, and sets a new standard for the industry.”
The JCB press conference included the Stage V-compliant versions of the manufacturer’s popular 140X, 150X and 220X crawler excavators – all of which use the JCB DieselMax 448 engine.
Speaking after the event, a JCB spokesperson said: “They [DieselMax 430 and 448] are well suited to quarrying applications due to their robust fuel and induction air filtration systems. Their power density and delivery also suits quarry machines well either within JCB machinery or for loose engine supply into other quarrying and aggregate production machinery.”
Large engines are well suited for quarrying applications because they provide the power density needed to manage heavy, hard materials. John Deere Power Systems (JDPS) has expanded its engine line-up to accommodate high-intensity, highhorsepower jobs, such as heavy-digging material handling in the mining and quarry industry.
The John Deere PowerTech 13.6L diesel engine provides OEMs with more power per litre than previous 13.5L configurations. John Deere designed this engine specifically to meet customer needs of increased power and torque. With outputs up to 510kW, it has 14% higher power, and 11% increased peak torque, making it a reliable and durable power solution. The John Deere 13.6L engines have been working more than 47,000 hours at high load in various applications. Many operational challenges were even more
extreme than typically confronted in the field; repeating high to low loads to confirm thermal durability, block loading to show strength, and ultralow idling to demonstrate oil pressure capabilities.
Continuing with an analysisled process first used with the 13.6L engine, John Deere Power Systems announced its new 18.0L engine at CONEXPO in 2020. The 18.0L is the largest engine in John Deere’s line-up, offering rated power up to 676kW.
This engine is the second in a new era of products for John Deere that are engineered specifically to address customer and market needs. The 18.0L engine was designed for extreme durability and is ideal for heavy-duty applications around the world.
Since the 18.0L engine builds on the advancements made during the 13.6L engine development, there are multiple technological and design similarities. These include John Deere model-based controls, a rear gear train and streamlined service and repair capabilities.
The John Deere model-based controls offer advanced prognostics capabilities and reduce the overall number of sensors needed, which improves transient response. Switching the location of the gear train from the front to the rear of the engine reduces noise and torsional vibration. In addition, its streamlined design factored in the top 20 service and repair jobs normally completed on an engine as part of the development process, resulting in reduced repair time.
Both engines also feature a three-piece integrated harness with a protective channel — further improving overall reliability.
To meet customer needs for fewer and shorter planned maintenance intervals, John Deere utilised hydraulic lash adjusters (HLAs) in the 18.0L engine design. The HLAs are hydraulically operated and self-adjusting, eliminating the need to manually reset the valve lash — a lengthy service process. This was a key-value point for John Deere customers and internal partners.
The 18.0L also features a three-piece integrated harness with a protective channel, further improving overall reliability.
In addition, locating the gear
train in the rear of the engine improves durability while enhancing operational flexibility, as it enables more gear-drive auxiliary power take-off capabilities.
There is an immediate benefit to implementing a fully electric solution for underground mining: it eliminates all diesel exhaust. Because the application needs are so specific, mining OEMs can pioneer fully electric off-highway solutions even as battery technology develops.
Electrification helps companies obtain the permits needed to start new mines since it allows them to have a neutral environmental footprint. And while electrification also helps with permitting new mines, it also enables companies to drill deeper into existing mines and expand existing mining shafts. Since they’re using electric vehicles, they don’t need to create extra ventilation as they go deeper underground. Even in mining applications where it doesn’t make sense to run a completely electric system, hybrid solutions offer increased benefits. In the on-highway market, it’s been established that electrification improves fuel economy. This benefit still applies to other applications, reducing overall fuel costs.
Because the John Deere solution includes power-generation and traction-drive components designed to work together, JDPS can work with a vehicle system integrator to provide a solution that generates the right amount of energy for the tractive power. OEMs benefit from the knowledge and extensive experience John Deere has developed in designing efficient, reliable drivetrain systems. John Deere can provide OEM customers with integrated electricdrive generation, traction drive and power electronic components to interface effectively with their unique machine and designed for their specific application. AB
Resilient product. Global support. Engines that have the power to do more for you.
The Cummins B6.7 Performance Series engine is proven in a wide range of industrial applications. Power increases to 326 hp / 243 kW enabling replacement of engines with higher displacement with no impact on productivity. cummins.tech/aggbusiness-june21
Battery energy storage solutions like Atlas Copco’s ZenergiZe can store energy from renewable sources, such as solar panels, for use when grid power is unavailable
Liam McLoughlin reports
The aggregates industry is at a turning point when it comes to embracing sustainability. According to research website Our World in Data, 10.6% of energy-related greenhouse gas emissions originate from manufacturing in industries including quarrying and mining, construction, textiles, wood products, and transport equipment.
Bárbara Gregorio, product marketing manager – innovative energies & digital solutions at Atlas Copco’s Power and Flow Division, says that both quarrying and construction operators have to balance the increasing pressure to take steps to address the issue with the need to optimise effi and remain competitive.
“For a long time, the very nature of quarry sites, which are often off-grid and sometimes remote, has meant that they have had to rely exclusively on generators to power and start vital equipment,” says Gregorio. “The European Stage V emissions standards have already set tighter emission restrictions on diesel engines in non-road mobile machinery to improve air quality. Now, li-ion battery energy storage solutions provide new, greener ways to complement the generator’s power.”
She adds that high-density lithium-ion batteries, such as those used in Atlas Copco’s ZenergiZe lithium-ion energy storage units, are lighter and much more compact than traditional alternatives, yet able to provide over 12 hours of power with a single charge. They are not designed to replace a generator as their primary function is different: a battery stores energy while an engine generates it. However, they are ideal for making the use of generators more flexible and energy effi
Gregorio says that one of the greatest benefits of battery energy storage solutions is their capability to store energy from renewable sources, such as solar panels, for use when grid power is unavailable, or the use of a generator is unsuitable.
“This opens up several new applications on-site, from being the sole source of power for low-load equipment, such as telecoms antennas, to working together with a generator to enable electric vehicle (EV) and electric tool charging stations,” she says.
“In the ideal case, the batteries can serve as the standalone power solution when combined with a renewable source. The ZenergiZe unit, for example, can enable a 100 percent reduction in CO2 emissions compared to a generator when used as a standalone power solution in the island mode.”
Li-ion battery storage solutions offer operators several simple ways to make the use of generators more efficient, practical, and environmentally friendly. Gregorio says
Quarry operators can leverage lithium-ion battery energy storage solutions (ESS) to address sustainability challenges and work towards greener and more efficient operations.
that benefits are also felt outside the quarry site, as any steps taken to reduce noise and minimize CO2 emissions can help ensure a good relationship with the surrounding community and protect the brand image.
“That is why forward-thinking constructors are already taking steps to make ESS part of their site’s power network to manage peak power requirements and work towards achieving three zero operation, with zero emissions, zero noise, and zero maintenance,” Gregorio adds.
Atlas Copco has now introduced ZBC, the
to create microgrids. The new ZenergiZe is designed as an ideal solution for demanding applications that require a constant and significant flow of electrical energy.
The ZenergiZe ZBC range offers rated power from 100kVA to 1000kVA and an energy storage capacity of 250kWh and 2000kWh depending on the model, to deliver high power with long autonomy.
Atlas Copco has officially announced Power Technique as the new name of its Construction Technique business area. The company says Power Technique has been chosen as the name because power is recognised by customers as the integral characteristic of the core product categories in the portfolio – air, power (including light) and flow. The business area will serve multiple customer segments including construction, industrial, drilling, oil and gas and petrochemicals. The change is effective immediately.
Moving forward, the manufacturer says the Power Technique business area will offer a core portfolio of products including portable compressors, generators, light towers and pumps along with dedicated construction products including handheld pneumatic, electric and hydraulic tools and compaction and concrete products. In addition, it will continue to provide products and customised solutions for drilling, oil and gas and geothermal exploration applications, among many others.
UK-based JCB has introduced its first Rental Series (RS) generator set with EU Stage V power, which the UK manufacturer says offers customers increased prime output with reduced emissions. The G40RS V replaces the Stage IIIA G36RS model, delivering 40kVA at 50Hz frequency.
The G40RS V rental generator set is a transportable power-generation system that has been designed to work in the harshest rental environments. Built on an over-gauge base frame, with a 2mm thick Galvtec steel canopy, the G40RS V has a 40mm fixed single lift point, four base-frame lifting points and integrated fork pockets, for rapid deployment to site. The integrated fully-bunded fuel tank is compliant with the European ADR standards for safe road transport, and the canopy has vertical hot air discharge vents, to
reduce noise and prevent dust swirl around the set on-site.
The generator is powered by a JCB by Kohler KDI 2504 TCR four-cylinder turbocharged engine, developing 42.4kW (57hp). This uses a single-can diesel oxidation catalyst (DOC) and diesel particulate filter (DPF), that is mounted in front of the radiator to retain slim canopy dimensions. The DOC is maintenance-free and the DPF is regularly cleaned using regeneration. The regeneration strategy has been designed to maintain optimal machine operation, even at low loads and temperatures, maximising uptime for the customer.
Large, lockable doors enable easy access to all service points and routine service intervals are set at 500 hours. All replaceable filters are located on the cold side of the engine, while a lift-off panel provides access to the cooling pack, load bank elements and the DOC/DPF canister. JCB says there is no requirement for selective catalytic reduction (SCR) or diesel exhaust fluid (AdBlue).
The G40RS V can be supplied with DSE7310 or DSE8610 (synch) controllers to provide an industry-familiar control environment. A four-pole Schneider circuit breaker is standard and there is an emergency stop button mounted on the canopy, adjacent to the control section. All controls are located behind a lockable door with viewing window and are shielded from the engine compartment.
The optional DSE8610 synch controller is designed to allow the G40RS V to be easily connected to other machines, to deliver flexible, adaptable power as required. JCB LiveLink telematics provide standard remote monitoring, in effect placing a virtual engineer with every RS generator set on-site. The ADR-compliant fuel tank provides a minimum of 24-hours operating autonomy and the lifting points have been designed to allow fully-fuelled delivery.
JCB comments on the new RS generator set: “With clean Stage V power, common DSE control systems and premium MeccAlte alternators, in a proven robust yet compact package, the G40RS V leads the way for Stage V adoption in the JCB Power Products Rental Series generator line-up.”
Power-systems supplier Kohler has launched its M139 generator canopy. The company says it offers high levels of anticorrosion performance, making it suitable for use in harsh outdoor environments in markets such as Africa and the Middle East.
The M139 integrates powers from 165 kVA to 250 kVA. It completes the redesign of canopies for Kohler’s industrial range, with the previously released M137 and M138 covering 22 to 130 kVA.
The canopy is made from aluminiumzinc coated steel, which is designed to provide superior protection against corrosion compared with standard galvanised steel. Tests at the French Corrosion Institute near Kohler’s headquarters in Brest, northwest France, showed that the M139 continued to provide resistance up to 1,500 hours in a climatic chamber under salt-spray conditions.
The company says the design of the M139 has also resulted in the removal of certain welds, eliminating water traps that can accelerate the spread of rust.
“The M139 canopy integrates generators for prime and back-up electricity production in global markets, and it will find application in a broad range of small industry and retail settings,” said Kevin Bougault, product manager for the small diesel range at Kohler.
Other design advantages include grooved sheets to provide additional structural solidity of the canopy, therefore reducing vibration.
The M139 also comes with a chamfered roof and plastic finishing on the corners, providing additional protection.
“Durability was a crucial factor from the outset,” said Bougault. “Our designers and engineers worked closely with first-class suppliers to ensure the production of a canopy that is built to last.”
Kohler states that day-to-day practicality was also an important consideration. The M139 features a door at the front and a double-sized panel on the side for ease of access for maintenance teams. An oculus on the door provides clear visibility of the generator control panel, and the M139 also features a lifting eye as standard so that it can be easily hoisted from the top.
The M139 will be offered to global markets through an extended distribution network, providing delivery within two weeks. AB
The day after the European Commission published the EU Industrial Strategy in 2020, the World Health Organisation (WHO) declared COVID-19 a pandemic during which “the resilience, ingenuity and adaptability of EU industry” were witnessed, but, equally, “new vulnerabilities and older dependencies” were apparent.
Lessons learned from the pandemic
As requested by the European Commission, UEPG, the European Aggregates Association, reported weekly from March-June 2020 on the impacts COVID-19 has had on European aggregates producers, their challenges, and how companies learned to rapidly adapt if conditions allowed.
During the pandemic, many UEPG members have observed that the continued supply of construction raw materials was not only possible – with companies adapting to COVID-19-related health measures – but also essential to allow construction sites to remain open and operative.
The need to ensure well-functioning construction value chains, identified as one of the 14 industrial ecosystems, is a lesson learned from the pandemic. The updated EU Industrial Strategy now recognises raw materials as one of the six strategic areas and where “industrial alliances are identified as the best tool to accelerate activities that would not develop otherwise”.
Post-pandemic, smart and green recovery under the EU Green Deal, the renovation wave, the circular economy, the Climate Change Mitigation and Adaptation Strategy and the new European Bauhaus will depend on the secured cross-border supply of all kinds of primary and secondary raw materials for construction.
Therefore, UEPG has gathered broader support among the Construction 2050 Alliance partners to give the whole range of primary and secondary construction raw materials more visibility and importance within the Alliance’s Work Programme.
As industrial alliances are playing a vital role in the updated Industrial Strategy, UEPG will strongly contribute as a partner of the European Raw Materials Alliance (ERMA) and as an aligned member of the Non-Energy Extractive Industry Panel (NEEIP) to call political attention not only to critical raw materials but to all raw materials urgently needed for the implementation of EU policies and initiatives.
To address an increased public awareness, acceptance and trust, the European Commission will launch in summer 2021 a ‘Roundtable on Environmentally and Socially Sustainable Raw Materials Mining’, uniting the Commission, public authorities, industry, NGOs, and other social partners. UEPG would like to join this roundtable to provide input about improving access to primary and secondary aggregates.
The UEPG is highlighting the importance of the aggregates sector to E.U Industrial Strategy 2.0 Pic: Fediex - Emmanuel Crooÿ
As UEPG launches its survey on renewable production and the use of renewable energy, the Commission has announced its intention in the EU Industrial Strategy to work with member states to extend their ambitions on renewable energies and the streamlining of permit procedures. The Energy and Industry Geography Lab, a tool under development by the Commission’s Joint Research Centre (JRC) in collaboration with industrial stakeholders, will provide geospatial information for companies and energy-infrastructure planners. The Commission will consider measures to support the uptake of corporate renewable Power Purchase Agreements and remove any unjustifiable barriers.
EU and national policymakers have begun to acknowledge that the supply of domestic raw materials is a strategic area for the economic recovery of Europe. A growing number of stakeholders from the construction industry support UEPG’s call to address the sustainable supply of primary and secondary raw materials. With all the good case studies on biodiversity and environmental management, responsible aggregates production should be seen as compatible with the environment, essential and strategic. AB
With climate change now very much on the global agenda, Natalie Dyson, a solicitor in the Energy team at Stephens Scown and an advocate for sustainability, shares some top tips for businesses wishing to reduce their carbon footprint
With average global temperatures soaring to unprecedented levels, extreme weather events and natural disasters on the rise, the world will soon face food/water insecurity and environmental degradation on a potentially irreversible scale. Climate change is no longer someone else’s problem. Tackling climate change was part of the agenda at the UK-hosted B7 Business Summit on 10 -12 May and the G7 Summit taking place on 11-13 June. In November 2021, Glasgow is hosting the muchawaited UN Climate Summit – COP26 with the “Together for our Planet” campaign aiming to increase awareness of the climate emergency. Businesses are being urged to join the UN’s Race to Zero Campaign – the world’s largest alliance of businesses, cities, regions, leading universities, and investors who have pledged to eliminate their net-carbon emissions by 2050. One third of the UK’s FTSE 100 companies have recently signed up. Apple and Microsoft have announced plans for carbon neutrality by 2030, whilst a recent survey of 502 UK businesses found half of them have the same aim.
Urgent Climate Action Needed Now
While we hear world leaders committing to limit global warming to 1.5°C by the middle of the century, we all need to act now to achieve this. This is not a problem for future generations to solve – immediate, unprecedented, and sustained reductions in carbon emissions are needed now.
Here are eight ways in which your business can “go green” and avoid falling behind the net-zero curve:
#1 – In order to devise an achievable and effective carbon-reduction strategy, businesses must first understand how much carbon they currently emit. There is a wealth of free online calculators to help measure your current carbon emissions, enabling you to implement a targeted, achievable strategy to reduce them. For example, DEFRA (Department for Environment, Food & Rural Affairs) has some excellent guidance and emissions fact sheets and the Carbon Trust has a useful calculator and carbon-footprint guide.
#2 – You should review your entire supply chain, considering everything from your energy supplier, accountant, IT supplies,
“Don’t forget to consider your plastic and paper footprints as well as your carbon footprint”
food suppliers to cleaning company. Where possible, buy only from carbon-neutral suppliers.
#3 – Look at ways to improve your efficiency. Switch to green-energy tariffs and reduce your energy consumption by not heating premises at the same time as cooling them. Consider generating your own solar power and selling any surplus back to the grid. Insulate existing premises or relocate to buildings with strong EPC ratings. Use electric heating and induction cookers instead of gas. Check the energy rating of your appliances. Install low-energy LED lighting and temperature controls. Switch off electrical items and lights when they are not in use.
#4 – Don’t forget to consider your plastic and paper footprints as well as your carbon footprint. And remember that every single purchasing decision should be accompanied by the question “Do we really need this”? Eliminate single-use plastic. Go paperless. Reduce what you use. Repurpose and recycle everything you can. Join local Freecycle sites to give your unwanted items a new lease of life.
#5 – Comprehensively review your policies and make green thinking part of your culture. Huge carbon reductions can be gained by implementing hot-desking and flexible working practices, negating the need for large, energy-hungry office blocks. Encourage greener travel such as walking or cycling to work, car-sharing schemes and home working. Install EV-charging points. Invite ideas from employees and share successes!
#6 – Ideally, you should be aiming to consume less and travel less, but certain travel is unavoidable. Aim to offset the carbon emissions of such unavoidable travel and shipping through carbon credits and carbon-
offsetting schemes (for example, deforestation or renewable energy projects). While treeplanting schemes do help, existing forests contain centuries’ worth of carbon. It is far better to fell fewer trees, so that the carbon already stored is not released.
#7 – Adopt a green cause as your official business charity. You might consider climateneutral certification and/or signing up for the Race to Zero initiative. Genuine green values do attract customers.
#8 – Finally, consider employing external help from specialist net-zero carbon professionals. Find out what green-business grants may be available to assist you. Organisations such as the CBI, GOV.UK, local chambers of commerce and the UK Business Climate Hub have a wealth of useful information.
The UN recently declared that “the climate emergency is a race we are losing, but it is a race we can win”. It is estimated that only 0.5% of annual revenue is needed to offset your entire carbon footprint. Enough people making just small changes can make a huge difference for our planet. The question is not can we afford to become net zero, but can we afford not to?
Stephens Scown have specialist net-zero lawyers who can advise you on all aspects of decarbonised energy. Sonya Bedford MBE, head of our Energy team presented recently at the Zero-Carbon Britain live online event on 21 May 2021. AB
Natalie Dyson – a solicitor in the Energy team at Stephens Scown LLP – can be contacted on 01392 210700 or email solicitors@stephens-scown.co.uk For more information, visit www.stephens-scown.co.uk
Terex Trucks says UK infrastructure projects such as HS2 provide good opportunities for sales of articulated haulers including its TA300
CRecovery in the UK and Irish aggregates sectors has begun following the pandemic and the outlook is broadly positive, but there remains a lot of industry caution stemming from uncertainties around the implementation of major infrastructure projects and renewed COVID-19 outbreaks. Liam McLoughlin reports
onstruction industry demand for big-volume mineral products like aggregates and concrete showed resilience in the first quarter of 2021, despite renewed COVID19 lockdown restrictions, Brexit and particularly wet winter weather hampering activity.
The latest survey from the UK Mineral Products Association (MPA) warns that an encouraging start to the year should not distract from real challenges that lie ahead.
The MPA says the recovery in construction must not be taken for granted because so much depends on the government’s policy stimuli in housing and its delivery of the UK’s planned infrastructure programme. ONS data shows that construction output has flatlined since September, whilst new contract awards have been weak for most of the past year.
Whilst broadly positive, sales volumes for essential mineral products show mixed results for heavy-side building materials such as aggregates, ready-mixed concrete, asphalt and mortar. These core products are mostly used in the early stages of construction — for example, foundations and structures — so their sales provide a unique barometer for the start of new projects rather than the completion of finished ones.
In the latest MPA survey, building materials manufacturers who supply around one million tonnes of mineral products every day reported a slow but
steady start to the year, with construction demand in March much stronger than in January. Sales volumes for primary aggregates and ready-mixed concrete increased by 3.4% and 1.6%, respectively, in the first quarter of 2021 compared to the last quarter of 2020. Still, both asphalt and mortar sales volumes declined over the quarter, down 4.9% and 7.4%, respectively. Robust housing activity, particularly in landscaping and home improvement, and an acceleration in infrastructure work driven by Highway England’s roads programme and the HS2 rail project, were tempered by a combination of factors, including supplychain disruptions, rising COVID-19
infections and a particularly wet winter affecting work on site.
Longer-term recovery for asphalt is supported by renewed momentum in roads construction and maintenance, and market demand has rapidly recovered to pre-pandemic levels. At the start of the year, total sales volumes for asphalt were significantly higher than their previous five-year average (2014-19). Likewise, sales volumes for crushed rock aggregate have also been recovering well, boosted by roadworks and HS2, driving demand for asphalt and bulk-fill materials.
Aurelie Delannoy, director of economic affairs at the MPA, said that a balanced perspective is required: “Mineral products
GB aggregates and building materials sales volumes, 2018-2021: change on the previous period (seasonally adjusted)
* Note: Ready-mixed concrete includes sales from both fixed and site (mobile) plant. Source: MPA, ONS
manufacturers are busy supplying postlockdown, pent-up demand, particularly for domestic activity such as landscaping, repair and maintenance, and home improvements, as well as infrastructure projects already in the pipeline, including momentum building on HS2.
“The outlook for this year and next is also positive, but the stakes are high. Any optimism assumes activity is not disrupted by renewed outbreaks of COVID-19, and most importantly, relies on the government delivering on its planned infrastructure commitments.”
The MPA says the weak recovery path for ready-mixed concrete is a concern, and is likely to be held back by a combination of sluggish new housing activity and a lack of new projects in commercial construction. Over 60% of ready-mixed concrete is used either in new housing or other non-infrastructure projects, mostly in commercial buildings, with London and the South East representing a third of all sales. The total sales volume of ready-mixed concrete at the start of the year remained more than 9% below the previous five-year average, despite three consecutive quarters of growth since last year’s initial lockdown.
In May, aggregates and building materials supplier Hanson informed customers that it would be reducing allocations of bagged cement due to the UK’s current cement shortage.The company said the main factors causing the shortage have been a huge increase in demand across the UK cement market, cement plant shutdowns during the COVID-19 pandemic, and shortages in the availability of both haulage and packaging/ pallets.
Packed products director Andrew Simpson said that Hanson is looking to increase capacity by importing cement, although this is difficult as the increase in demand is global and there is reduced availability of shipping.
Hanson says that the cement market has seen an increase of around 30% across all sectors since mid-2020, and that this is unprecedented as the market normally fluctuates with high levels of activity in one
sector being counterbalanced by lower levels in others.
The bulk cement market consumes roughly 80% of total cement production and Hanson Cement has an even split between bulk and packed cement. The main sectors for cement usage are ready-mixed concrete, concrete-product manufacture, construction site activity and builders’ merchants.
Also part of the fallout from COVID-19 was the postponement of Hillhead, the UK’s biggest quarrying, construction and recycling equipment event. Originally scheduled for 22–24 June this year, the event is now slated for 21-23 June 2022 at its usual site in a former Tarmac quarry near Buxton in Derbyshire. As part of the ‘new normal’ following the pandemic, event organiser
The QMJ Group, for the first time, staged the exclusively online Hillhead Digital event, which attracted 4,988 attendees over two live days from March 30-31.
Adam Benn, director, capital sales, North EMEA, Russia & CIS and Southern Africa at Metso Outotec, says that quarrying and aggregates markets in both the UK and Ireland were impacted heavily in the early days of COVID lockdown in Q2 2020, with many operations having to close temporarily.
“Once the initial challenges were understood and new COVID protocols introduced, the ‘rebound’ was, on the whole, a positive one with the majority of the aggregate producers reporting surprisingly solid production figures, all things considered, but generally down about 10% year-on-year,” Benn says.
He adds that the busy end to 2020 has continued into 2021 with a very positive sentiment in terms of business levels, and in fact shortages of cement and some bulk aggregates in certain regions.
“The current demand is expected to continue in the short to medium term albeit with cautious optimism especially with regards to longer term outlook,” Benn says.
He adds that, in general, the demand for aggregates as a result of road and infrastructure activity is positive, although dependant on rate of spend over the next
few years and the potential reduction in investment/government budget as a result of the impact of COVID.
“Building products in particular have enjoyed a busy period and are facing longer than normal lead times in some areas due to strong house-building activity and in particular the increase in home-improvement projects during the various COVID lockdown periods,” says Benn.
The UK’s HS2 rail project should significantly increase the demand for quarrying and aggregates machinery over the next few years, according to Kenny Price, regional sales manager for EMEA at Terex Trucks.
He says this should provide good business opportunities for his company: “In the first stages of the project, articulated haulers such as our TA300 and TA400 could be used for preparatory tasks and transporting materials before the main construction work can begin. This includes jobs like vegetation clearance and earthwork for tunnel portals and compound facilities.”
He added that, with rail projects always requiring the use of track ballast, the demand for a range of aggregate materials will increase as well.
“A project of this size is a boost for everyone involved in the supply of equipment, materials, as well as services and allows those companies to plan with a more sure-footed outlook,” Price says.
Manufacturers of hauling trucks for quarries felt the impact of the pandemic, especially in the first half of 2020 when global
pandemic-stricken 2020, sales decreased by almost 50%. Around the end of March 2020, in line with its parent company the Volvo Group, Terex Trucks temporarily suspended production at its facility in Motherwell, Scotland, to ensure the health, safety and wellbeing of employees.
Price says that demand returned in the second half of 2020 and the recovery feels like it is well underway.
“Our order book is strong and we’re currently recruiting new team members to match the increase in production, so I’m expecting a good year,” he adds. “In Q1 2021, we’ve already seen very encouraging signs in the articulated hauler market in the UK and Ireland. Machine sales are on an upward trend after a challenging 2020, and the outlook for the rest of the year and into 2022 is positive. We’ve also had a really good order take-up for our new Stage V machines.”
In terms of future aggregates-industry prospects, an interesting area is the UK government’s proposed overhaul of the UK planning system, announced in the 2020 White Paper ‘Planning for the Future’. The proposals were set out in the Queen’s Speech in March 2021 and could lead to a sharp rise in building material demand through the construction of more high-quality sustainable homes due to a streamlined and speeded-up planning process.
UK retail sales of construction and earthmoving equipment in March 2021 were close to double the levels seen in the same month last year when the impact of the coronavirus was felt for the first time.
As a result, sales in the first quarter were 30% above 2020 levels and reached over 8,000 units, according to data published in April by the construction equipment statistics exchange run by Systematics International in partnership with the Construction Equipment Association (CEA).
Sales in the first quarter of the year were expected to show a big increase on last year due to the pandemic, so it is interesting to compare sales with Q1 2019 to put the strength of the recovery into context. This shows that sales this year were 2.9% above 2019 levels and suggest significant
“We’re currently recruiting new team members to match the increase in production, so I’m expecting a good year”
Kenny Price, Terex Trucks
momentum in the market in the early months of the year.
Sales in Ireland are also recorded in the construction equipment statistics exchange and saw a more modest increase in March than in the UK. This resulted in Q1 sales this year ending up at 12% above Q1 2020 levels.
According to the latest figures from industry association Irish Concrete, the country’s 500-plus active quarries produced 38 million tonnes of aggregates in 2019, while national production of ready-mixed concrete totalled 5 million m3. Two million tonnes of bituminous road-surfacing materials were produced, 0.75 million tonnes of agricultural lime, and 2 million m2 of paving products.
The Irish Concrete Federation (ICF) and the national Health and Safety Authority (HSA) jointly supported the “Vehicle and Pedestrian Safety in Quarries” Spring Quarry Safety Campaign that took place in Ireland from 1-12 March this year.
The campaign replaced the previous “Quarry Safety Week” that was typically held in the autumn of the year.
Dr Sharon McGuinness, chief executive officer of the HSA, urged employers to lead the way in delivering safer workplaces, saying: “Since 2011, four people have lost their lives in quarries and many more have suffered serious, debilitating injury which is why Quarry Safety Week is so important –we need people to return home safely from work.”
As part of the campaign, the HSA carried out safety inspections at ICF member quarries, and ICF and HSA are presenting online briefings for quarry management, supervisors and safety officers on topical issues related to vehicle and pedestrian safety.
Irish equipment distributor McHale Plant Sales has called for the country to consider new tax relief on investments in plant and machinery, similar to those recently introduced by UK Chancellor of the Exchequer, Rishi Sunak. The appeal was made in a letter from the company to Finance Minister Pascal Donoghue. McHale, based in Birdhill and Rathcoole, represents quarrying and construction equipment manufacturers Komatsu, Metso Outotec, Terex Ecotec and Merlo in Ireland.
The new UK regulations, operative from April, include a provision that companies investing in qualifying new plant and machinery assets can benefit from a new temporary tax arrangement that delivers a 130% first-year capital allowance. McHale says this is greater in many cases than the purchase price of the machinery itself.
Designed to stimulate business investment, the measure increases the incentive to invest in plant and machinery by offering higher rates of relief than were previously available.
UK HM Revenue & Customs says the measure is expected to bring economic benefits. In explanatory information accompanying its introduction, it states that the new arrangement “will have a positive impact on business investment...by reducing the tax-adjusted cost of capital for millions of companies, large and small, investing in qualifying plant and machinery assets”.
In the letter to Minister Donoghue, McHale Plant Sales finance director Liam Foley expressed his company’s support for the measure, and encouraged the Irish government to introduce a similar provision “in its next Budget or at such earlier opportunity as may present”.
“In circumstances whereby COVID-19 has brought about a halt to major infrastructural development and a virtual closure of the house-building and construction sectors –with all of the consequential losses this has brought to companies operating in the plant and machinery business - the introduction here of an equally attractive provision would be one that would bring great benefit and stimulate employment in the sector,” Foley said.
“Moreover, it would level the playing field between here and Northern Ireland and remove any cross-border sales and marketing imbalances that might arise and could impact negatively on locally-based distributors.”
Over the past decade, independent, family-owned business SRC Group (SRC) has grown to become one of the UK’s leading aggregates suppliers. With demand for its quality aggregate products increasing rapidly and underscoring its commitment to strengthening the circular economy, the company has invested in a new CDE construction and demolition (C&D) waste recycling plant. Guy Woodford reports
Headquartered in Essex, southeast England, SRC provides a diverse range of materials and services for construction, building, and large-scale civil projects throughout the UK.
Originally dedicated to building agricultural reservoirs, the business as it is known today was established in 2009 when planning permission was granted for the development of the company’s first quarry site, Crown Quarry, in Ardleigh, near Colchester.
Two years later, SRC further expanded its operations when planning permission was granted for the development of Highwood Quarry, in Great Dunmow, now the site of its company headquarters.
Today, SRC operates from seven different sites, including four quarries and three recycling depots.
Powering its rapid growth over the past decade is a trusted partnership with CDE, a leading global industry manufacturer of wet
processing technologies, whose engineered solutions have helped SRC to maximise profitability by producing higher quality washed and graded sand and aggregate products and maximising throughput and yield.
SRC’s latest 135 tonnes per hour (tph) C&D waste recycling plant at Martell’s Quarry, just outside Colchester, is the eighth project CDE has delivered for the Essex-based materials processor.
It will enable SRC to process incoming inert and non-hazardous material from its various business activities to maximise the recovery of quality recycled sand and aggregates which can be returned to the local construction industry as a cost-effective and sustainable alternative to virgin quarried materials.
Oliver Rees, SRC Group managing director, says recycling is a very important part of the business and will help it to achieve a more profitable and sustainable future.
“In the past 10 years, SRC Group as you see it today has grown from five employees
and one quarry to operating four quarries, three recycling sites and employing over 250 people. We’re on a high and fast growth trajectory and still see opportunity for future growth. We see recycling having a very important role to play in the future of our business.”
As demand for SRC’s product range continues to rise, a sustainable alternative product that meets the specific requirements of its customers in the local construction industry is required.
“Every six months we’re recording significant increases in the volumes of material we’re moving. We anticipate that upward trend to continue. As we grow it’s just not sustainable – both for us as a business and for the environment – to maintain the same levels of quarried sand and aggregate products.”
Among the contracting services offered by SRC are demolition, earthworks, and site clearance for a huge range of large-scale civil projects, all of which provide a steady flow of incoming inert waste for the business.
“A lot of our material is coming in from Greater London and throughout East Anglia where void and landfill space is limited, so a restorative and circular approach is essential to fulfil the demand of the local construction industry.
“There is need for locally-sourced, quality sand and aggregate products, and there is also a significant waste stream that can be better utilised to respond to that need. We needed a solution that would recover materials from the waste coming in from our other business activities to the highest possible quality standards so that they could be returned to the market for use in new construction and infrastructure.”
Wet processing experts CDE and SRC have a partnership spanning more than a decade. In 2010, SRC purchased its first CDE solution comprising an AggMax, EvoWash and AquaCycle set-up commissioned at Elmstead Quarry, Colchester.
Since then, the two companies have worked together closely on the delivery of eight projects across SRC’s site network.
David Kinloch, CDE’s director of Business Development, UK & Ireland, says collaboration is the key to the longstanding relationship.
to ensure the efficient delivery of difficult material to the wet processing plant and to maintain optimum utilisation of the processing equipment.
“SRC is one of our largest customers in the UK market. We’ve been working together for a long time and over those years both businesses have grown together and developed. It’s CDE’s approach to co-creation in conjunction with our customers that is the bedrock of our relationship and successful partnership with SRC.
“By working in partnership, we understand a customer’s requirements from the outset and co-create a tailored solution that directly responds to their commercial and environmental aims and objectives. Once a project has been delivered and commissioned on site, we then continue that relationship through our unrivalled aftercare support.”
Rees says: “We’ve invested in CDE and likewise CDE has invested in us. When we began to formalise plans for the future of Martell’s Quarry there was no question that we wanted CDE to be part of that journey. CDE plant has been an essential component in our success to date and will continue to play an important role in our future.”
Underpinned by CDE’s co-creation approach and taking into consideration SRC’s site requirements, its commercial and environmental aims and objectives, and the varied nature of incoming feed material, a tailored wet processing solution was developed to recover saleable sand and aggregate products that would otherwise have been destined for landfill.
CDE proposed a solution comprising its R4500 primary scalping screen, AggMax modular logwasher, EvoWash, AquaCycle, and FilterPress.
CDE’s R-series primary scalping screens are designed to maximise product yield from feed material by scalping off oversized material at the beginning of the process
This material is then transferred to the AggMax modular scrubbing and classification system. The industry-standard log washer, CDE’s market-leading AggMax technology is engineered to operate in the toughest of conditions to maximise product yield from the most abrasive of feedstocks. Its versatile design incorporates five processes on a single and compact portable chassis, including pre-screening, scrubbing/attrition, sizing, contaminants removal and stockpiling.
The heavy-duty AggMax can process challenging construction, demolition and excavation waste material containing large quantities of organic and other inert physical contaminants into high-value materials suitable for a variety of applications in the construction industry.
Fine material is processed by CDE’s signature EvoWash technology. A compact, modular sand washing system, the EvoWash
screens and separates the smaller sand and gravel fractions through an integrated high-frequency dewatering screen, sump and hydrocyclones which provide unrivalled control of silt cut points and eliminate the loss of quality fines with significant commercial value.
Incorporating CDE’s patented Infinity Screen technology, the EvoWash offers optimal dewatering results which enable materials processors to produce a range of high-quality sands that are market-ready straight from the belt.
As well as supporting SRC to extend the life of its quarry reserves through the recovery of high-value recycled sand and aggregates derived from inert waste, the CDE solution commissioned at Martell’s Quarry also incorporates market-leading water management to minimise SRC’s environmental footprint.
CDE’s AquaCycle is a single, compact and user-friendly unit that can be applied to high and low tonnages across many markets. It helps to accelerate return on investment by maximising production efficiency, minimising the loss of valuable fines, and reducing water and energy costs. An alternative to water extraction and the costly process of pumping water to the plant, the AquaCycle
is a highly efficient water management solution that significantly reduces costly water consumption by ensuring up to 90% of process water is recycled for immediate recirculation.
This water management system uses a flocculant to separate clean water from the solid particles, which form a sludge which is dried further in the FilterPress, recovering more water for recirculation and creating a dry filter cake which can be used for pipe bedding and landfill capping.
John Hilton, SRC Group operations manager, says consistency of material is one of the biggest challenges.
“The material coming in is never the same, so it’s about identifying material and understanding how it’s going to behave as it goes through the process. Our latest CDE wet processing plant at Martell’s Quarry is mindful of these challenges and offers us the flexibility to adjust the specification of the plant to suit our incoming feed material.”
Incoming inert waste is received from a variety of SRC’s business activities and projects, including demolition and earthworks, and can vary on an almost daily basis. CDE technology accepts a wide variety of feed material and offers the flexibility to adjust the specification of the plant set-up, including, for example, the variable silt cut points of the EvoWash, to maximise material recovery and ensure the plant is running at optimum utilisation to maintain consistent throughput and output.
With the support of CDE wet processing technology, SRC is now extracting valuable sand and aggregate resources with substantial commercial value from incoming inert waste streams, generating additional revenue for the business and diverting significant tonnage from landfill.
More than 80% of all incoming waste can now be processed, recovered, and returned
to market as recycled sand and aggregate products.
Facilitated by CDE technology, SRC, across its three recycling depots, is now diverting up to 800,000 tonnes per year from landfill.
The engineered-to-order wet processing system is supporting SRC to transform 135tph of raw feed into six new products.
As well as supplying its recycled sand and aggregates directly to the local construction market, SRC is also utilising recovered materials in the production of prefabricated concrete blocks for retaining structures, compacted concrete for paving, and more.
“SRC has firmly committed to a sustainable future and we at CDE are very pleased to play our role in helping the business to achieve that vision,” says Kinloch.
“Growth and sustainability need not be mutually exclusive and Oliver and the team at SRC have shown the high returns that can be achieved with a circular economy approach. Our latest commission is helping the business to reduce the burden and reliance on primary sand and aggregate resources, supplementing those with sustainable alternatives, and ensuring SRC has the processing capacity to continue to meet future demand.”
Commenting on the relationship between the two companies, Rees says investment in CDE technology is an investment for life.
“It’s not like purchasing a crusher or acquiring a new screen. To get the best from your plant it needs to be running efficiently and continuously with minimal downtime. The project doesn’t just end once the plant is operational. It requires maintenance, parts. That’s why we’ve stuck with CDE over the past ten years. We’ve a great rapport with the parts department and CustomCare team and are reassured by their consistent and proactive support which keeps us operational across all of our sites.”
Every CDE project benefits from its customer-for-life model, which ensures transparent and effective communication from the beginning of the project until commissioning and unrivalled aftersales support. Kinloch says it’s CDE’s CustomCare team that sets it apart from the competition.
“We don’t stop when the plant has been commissioned. From there our CustomCare team pick up and continue to work in partnership with the customer through the life of the plant.”
CDE’s CustomCare team offers 24/7 technical advice, preventative maintenance checks, responsive on-the-ground support, guaranteed supply of spare parts, and assists with making adjustments to the plant in line with changing requirements and feed material.
Rees concludes: “We learn more with every project and that knowledge informs how we develop as a business. Our latest investment at Martell’s Quarry is ten years of practice and innovation wrapped into a single plant and it, too, will play an important role in the future of the company.” AB
Rapid concrete plants help build Finnish wind farms
Finnish ready-mixed concrete producer Kymppibetoni has deployed two mobile concrete batching plants from Northern Ireland-based Rapid International for the production of wind farm foundations.
The Rapidbatch 120’s compact modular design is designed to be easily transportable and can be fully erected in one working day, reducing downtime. Installation can be carried out via a single crane lift and no foundations, and it features plugand-play electrics.
The integral Rapid twin shaft mixer offers reduced wear with extra thick chill cast tiles and paddles and an aerofoil arm design.
The plant’s integral 3m³ Rapid twin shaft mixer batches up to 120m³ per hour of high-quality homogenous concrete. The mixer’s arm design allows fitment at either 60°/90° and creates an area of high turbulence designed to ensure a homogeneous mix, in a reduced timeframe.
The Rapidbatch plants can deal with the often harsh weather conditions on Finnish wind farm sites
Komatsu has rolled out the PC360LCi-11 and PC360NLCi-11 with iMC (intelligent machine control) 2.0 excavators for the European market.
The excavators are designed to offer high productivity earthmoving and precision grading in one package and incorporate several new iMC features. The new Komatsu Auto Tilt Control for tilting buckets makes operations on slopes and ditch work easier, automatically limits underdigging and increases bucket fill. The bucket automatically tilts to the design surface with no need for the operator to manually intervene.
The new Bucket Angle Hold means the operator no longer needs to use the lever to maintain the bucket angle through grading pass. Once the desired angle is selected, this feature automatically maintains it as the arm moves in. A new iMC 2.0 monitor provides intuitive smartphone-like screen navigation features. Komatsu says it is slimmer, lighter and more compact, with increased memory capacity and fast processing speed.
Kymppibetoni required a mobile batching solution capable of withstanding the often harsh weather conditions faced on wind farm construction sites in Finland.
To ensure maximum output of concrete in adverse weather, the Rapidbatch 120 was fully winterised to include insulated composite cladding, lined doors and a heating system for aggregates, water and the integral Rapid twin shaft concrete mixer. Leevi Grönlund – process designer at Kymppibetoni Grönlund, commented that as a result of these measures: “The Rapidbatch has proven its applicability in our projects.”
Jarlath Gilmore, sales & marketing director at Rapid International, said the company has supplied a number of Rapidbatch plants for wind farm foundation projects around the world. www.kymppibetoni.fi
The iMC system lets operators use excavators for machine grading as well as truck loading
“On the previous model we had examples of customers using iMC to replace standard excavators,” says Rob Macintyre, product manager at Komatsu Europe. “They immediately benefitted from using their machine for grading as well as for truck loading, allowing them to redeploy other equipment and to really optimise their fleet on the jobsite.”
He adds that the new iMC 2.0 versions should give operators more opportunities to do this. Operating weights of the PC360LCi/NLCi11 range from 35,770kg to 36,850kg, and it has a maximum recommended bucket capacity of 2.66m³. The EU Stage V Komatsu engine has a power output of 202kW @ 1950rpm. www.komatsu.eu
Caterpillar says its new D7 bulldozer offers high drive undercarriage design, in addition to increased performance and a broad choice of technology features for customers to get the most from the machine.
The dozer features a fully automatic four-speed transmission that offers optimal fuel and dozing efficiency. At 197kW (265hp) and an operating weight of 29,776kg (65,644lbs), the new D7 dozer replaces the D7E model.
The D7 is claimed to move up to 8% more material per hour than the D7E, with about 6% more weight and 12% more horsepower. Blade capacity is increased by 10%, and the elevated sprocket undercarriage delivers better ride and balance, as well as increased penetration force.
Other features of the D7 include Slope Indicate, which is standard with the premium display package, and shows machine main fall and cross-slope for easy
reference. ARO with Assist is a grade-ready option bundled with basic blade control and a new set of assist features that work in the background to help operators get more done in less time.
The AutoCarry feature automates blade lift to help maintain consistent blade load and help reduce track slip.
Like the D6 and D8T, the new D7 is driven by a fully automatic
four-speed transmission, which continuously adjusts for maximum efficiency and power to the ground without added operator input. Cat says the cab has been completely redesigned and offers operators more space, multiple seat and control adjustments for optimal comfort and an easy-touse 254mm (10”) touchscreen operator interface.
www.cat.com/en
SEPTEMBER
08-12: MATEXPO 2021
Kortrijk, Belgium
Organiser: The Fair Experts
Tel: +32 56 98 07 60
Email: info@matexpo.com www.matexpo.com
15-18: Construction Indonesia
Jakarta, Indonesia
Organiser: PT. Pamerindo Indonesia
Tel: +49 3999905 0
Email: contact@merebo.com www.ci.merebo.com
15-18: Geofluid 2021 Piacenza, Italy
Organiser: Piacenza Expo
Tel: +39 (0) 523 602711
Email: alessandra.bottani@ piacenzaexpo.it www.geofluid.it
OCTOBER
20-22 SIM 2021
Lille, France
Tel: +33 (0) 1 53 10 14 70
Email: contact@lasim.org www.expositionsim.com
21-23: IFAT Eurasia 2021 Istanbul, Turkey
Organiser: Messe Munchen
Tel: +90 212 241 81 71
Email: genc@mmi-eurasia.com www.ifat-eurasia.com/en/
NOVEMBER
03-04: 4th Construction Equipment Forum Berlin 2021 Estrel Convention Center, Berlin Organiser: IPM AG Tel: +49 511 473 147 90 www.constructionforum.eu
DECEMBER
07-11: EXCON 2021 Bengaluru, India
Organiser: CII Tel: +91 44 42444564
Email: excon@cii.in www.excon.in
29-31: World of Asphalt 2022 Nashville, Tennessee
Organisers: NAPA, AEM & NSSGA Tel: +1 (414) 274 0644 www.worldofasphalt.com
Advertisers in AGGREGATES BUSINESS can now be contacted via their websites - for instant links to all the websites listed below, by category, go to: www.AggBusiness.com
Ammann p23 www.ammann.com
BKT p33 www.bkt-tires.com
CAT IFC www.cat.com
CDE Global p8 www.cdeglobal.com
Cummins p39 http://cummins.tech /aggbusiness-june21
Hitachi p4 www.hitachicm.eu
Komatsu p7 www.komatsu.eu
MB Crusher p34 www.mbcrusher.com
McLanahan p15 www.mclanahan.com
Metso OBC www.mogroup.com
Rapid International p18 www.rapidinternational.com
Rubble Master p18 www.rubblemaster.com
Smiley Monroe p13 www.smileymonroe.com
Terex Trucks p27 www.molsongroup.co.uk
Tsurumi IBC www.tsurumi.eu
Weir p10 www.global.weir
Wirtgen p17 www.wirtgen-group.com /mco-90-evo2-kleemann
05-07: RecyclingAKTIV & TiefbauLIVE
Karlsruhe Trade Fair Centre, Germany
Organiser: Messe Karlsruhe
Tel: +49 (0) 721 3720 2300
Email: verena.schneider@messekarlsruhe.de www.recycling-aktiv.com
21-23: Hillhead
Hillhead Quarry, Buxton, Derbyshire, England
Organiser: The QMJ Group Tel: +44 (0) 115 945 4377
Email: Harvey.sugden@qmj.co.uk www.hillhead.com
24-30: bauma Munich, Germany
Organiser: Messe München Tel: +49 89 949 11348
Email: info@bauma.de www.bauma.de/en/
MEET THE TEAM
Aggregates Business travels the globe attending conferences, events and equipment shows, keeping you informed of the latest offerings. Come and join us for a chat at any of the events below.
JUNE 2022
21-23: Hillhead 2020
Hillhead Quarry, Buxton, Derbyshire, England
OCTOBER 2022
24-30: bauma Munich, Germany
These dates were correct at the time of going to press, but please note that the COVID-19 pandemic means some events may be rescheduled with little advance notice