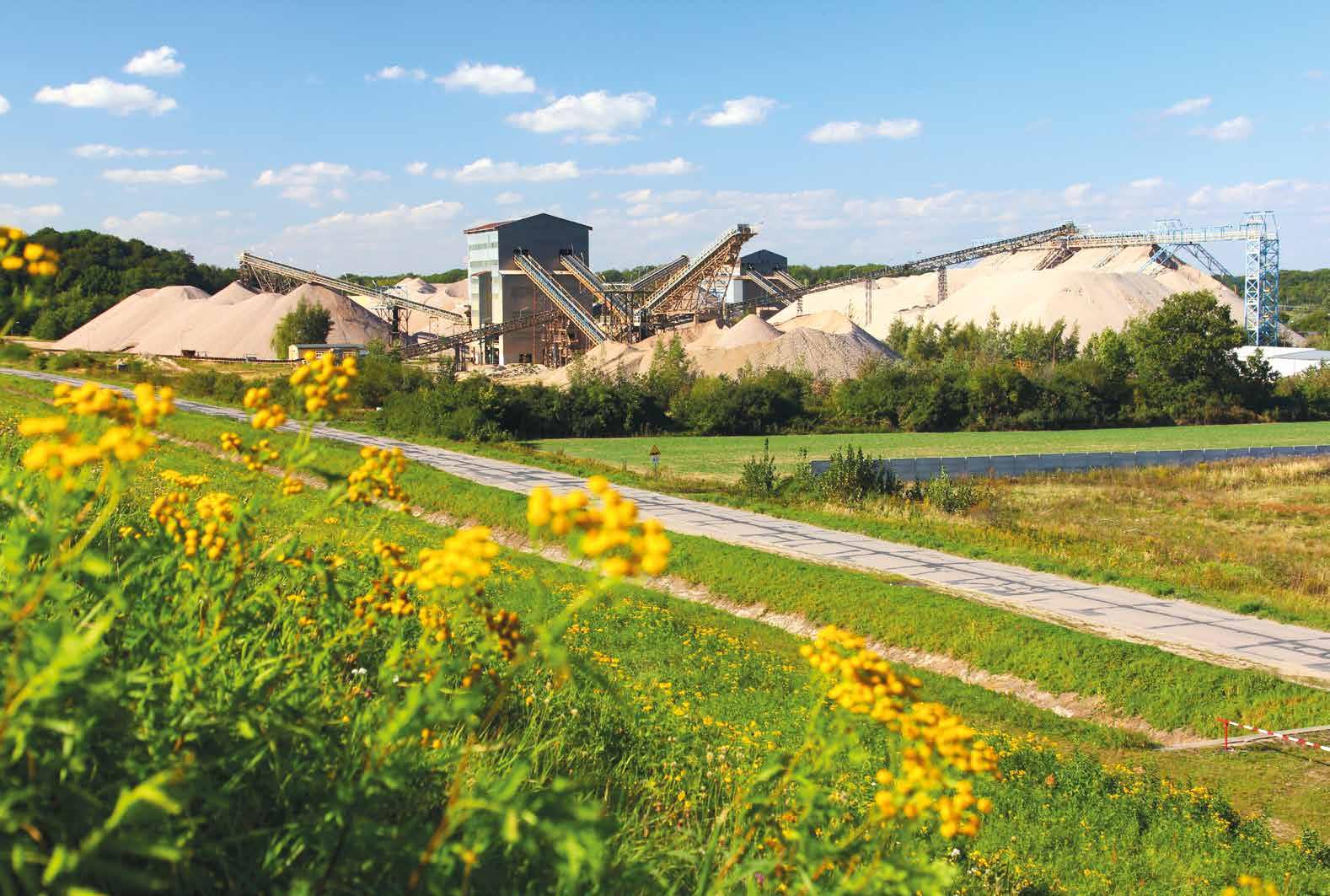
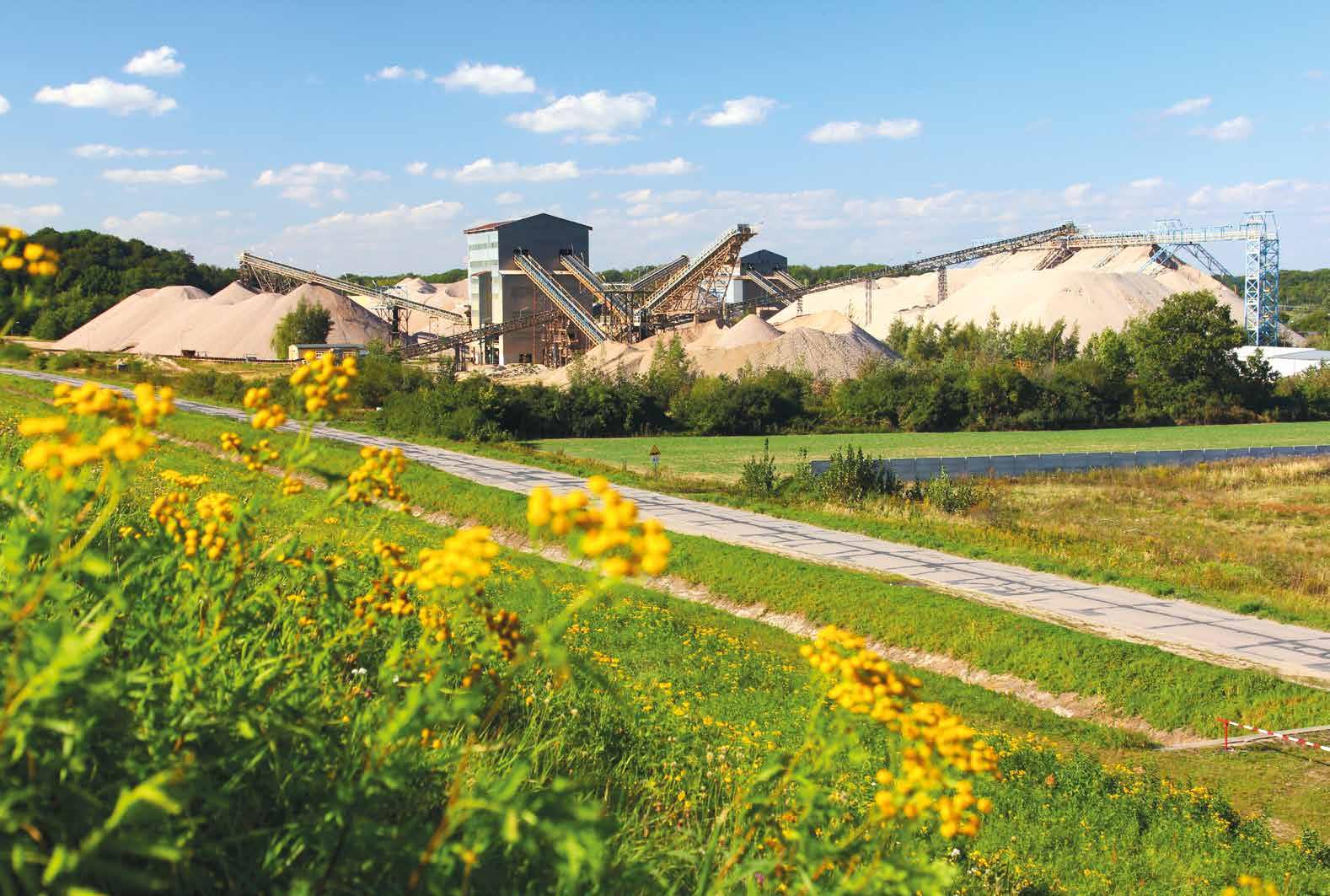
Aggregates ascent
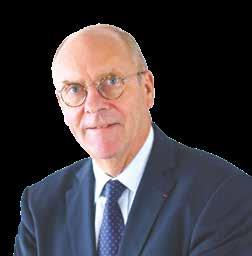
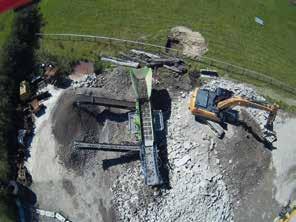
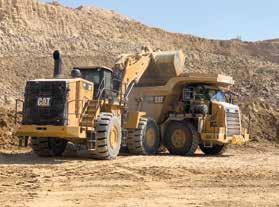


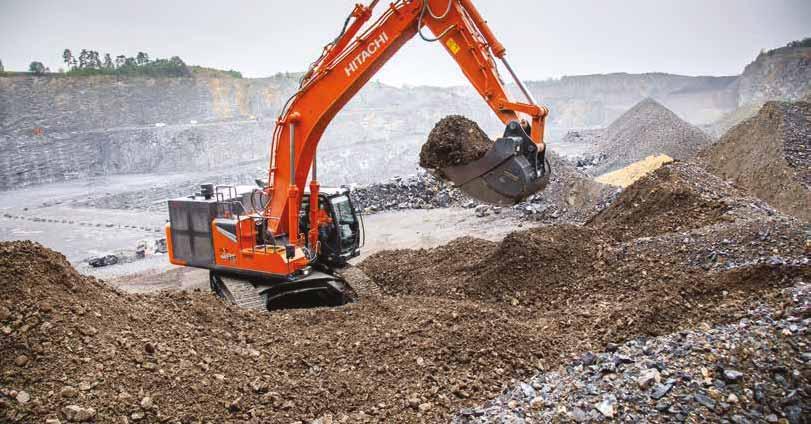
“Job-site
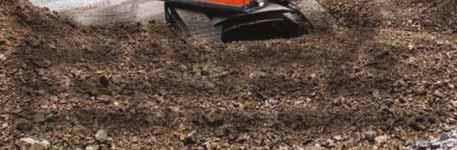
Investing


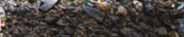
and management solutions is a must in modern quarrying 39 ROTARY CUTTER HEADS
Rotary cutter heads are making an increasingly strong case for their deployment in quarries globally
Hi-tech solutions for optimised drill and blast in quarries and surface mines
Specials
Arnaud
Premium
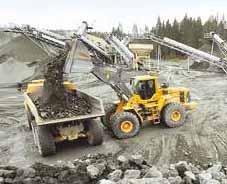

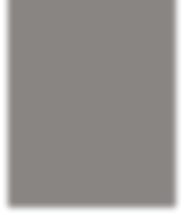

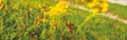



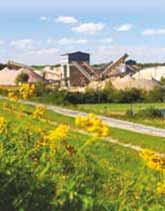




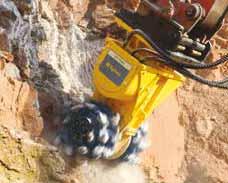

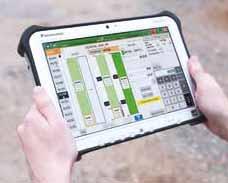

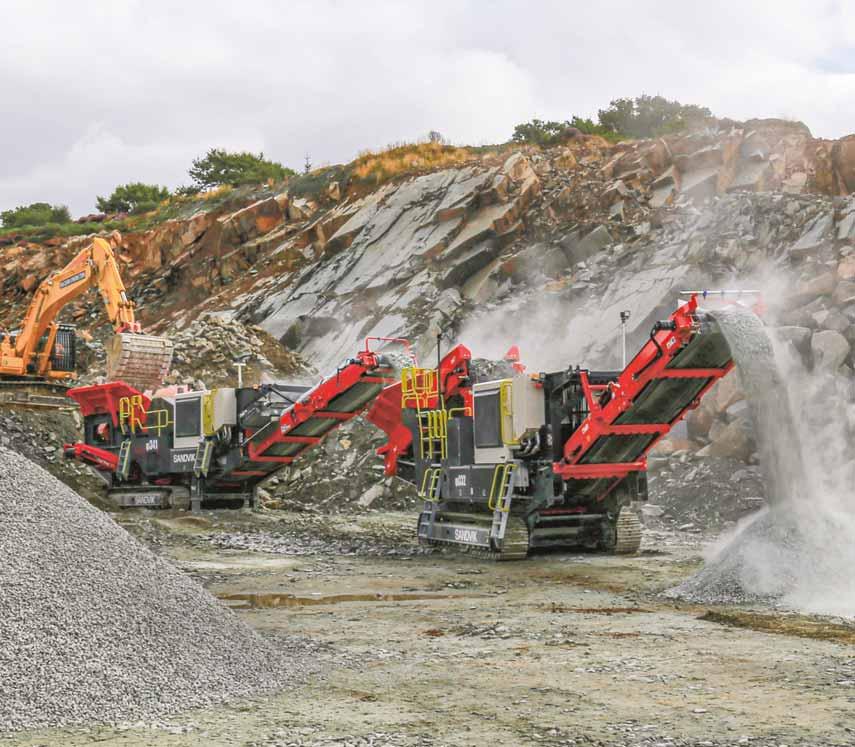
RELIABILITY AND VERSATILITY SECOND TO NONE
of our customer, Macleod Construction Ltd in Scotland. As a longstanding customer of over two decades, Macleod invest in Sandvik mobile crushers and screens due to their reliable Fleet telematics as standard, which gives you access to your equipment data 24/7, enabling you to operate smarter and maximize uptime.
HEAD OFFICE
EDITOR: Guy Woodford
ASSISTANT EDITOR: Liam McLoughlin
CONTRIBUTING EDITORS: Patrick Smith, Dan Gilkes
EQUIPMENT EDITOR: Mike Woof
DESIGNERS: Simon Ward, Andy Taylder, Stephen Poulton
PRODUCTION MANAGER: Nick Bond
OFFICE MANAGER: Kelly Thompson
CIRCULATION & DATABASE MANAGER: Charmaine Douglas
INTERNET, IT & DATA SERVICES DIRECTOR: James Howard
WEB ADMINISTRATORS: Sarah Biswell, Tatyana Mechkarova
MANAGING DIRECTOR: Andrew Barriball
PUBLISHER: Geoff Hadwick
CHAIRMAN: Roger Adshead
ADDRESS
Route One Publishing Ltd, Waterbridge Court, 50 Spital Street, Dartford, Kent DA1 2DT, UK
TEL: +44 (0) 1322 612055 FAX: +44 (0) 1322 788063
EMAIL: [initialsurname]@ropl.com (psmith@ropl.com)
ADVERTISEMENT SALES
SALES DIRECTOR:
Philip Woodgate TEL: +44 (0) 1322 612067
EMAIL: pwoodgate@ropl.com
Dan Emmerson TEL: +44 (0) 1322 612068
EMAIL: demmerson@ropl.com
Graeme McQueen TEL: +44 (0) 1322 612069
EMAIL: gmcqueen@ropl.com
SUBSCRIPTION / READER ENQUIRY SERVICE
Aggregates Business International is available on subscription. Email subs@ropl.com for further details. Subscription records are maintained at Route One Publishing Ltd.
SUBSCRIPTION / READER ENQUIRIES TO:
Data, Route One Publishing Ltd, Waterbridge Court, 50 Spital Street, Dartford, Kent DA1 2DT, UK
TEL: +44 (0) 1322 612079 FAX: +44 (0) 1322 788063
EMAIL: data@ropl.com

No part of this publication may be reproduced in any form whatsoever without the express written permission of the publisher. Contributors are encouraged to express their personal and professional opinions in this publication, and accordingly views expressed herein are not necessarily the views of Route One Publishing Ltd. From time to time statements and claims are made by the manufacturers and their representatives in respect of their products and services. Whilst reasonable steps are taken to check their accuracy at the time of going to press, the publisher cannot be held liable for their validity and accuracy.
PUBLISHED BY © Route One Publishing Ltd 2020
AGGREGATES BUSINESS EUROPE USPS: is published six times a year. Airfreight and mailing in the USA by agent named WN Shipping USA, 156-15, 146th Avenue, 2nd Floor, Jamaica, NY 11434, USA.
PERIODICALS POSTAGE PAID AT BROOKLYN, NY 11256
US POSTMASTER: Send address changes to Aggregates Business Europe, WN Shipping USA, 156-15, 146th Avenue, 2nd Floor, Jamaica, NY 11434, USA
Air Business Ltd is acting as our mailing agent
PRINT: ISSN 2051-5766 ONLINE: ISSN 2057-3405
PRINTED BY: Warners (Midlands) PLC
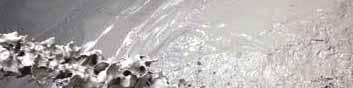
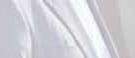

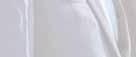
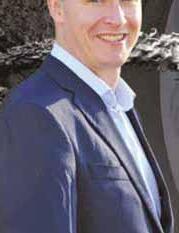

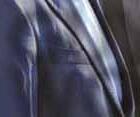
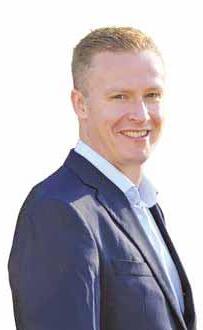
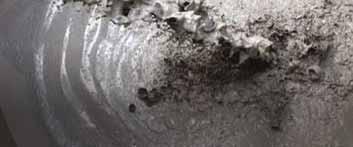
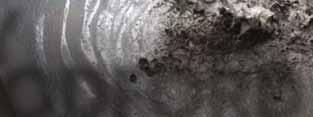

OThe race is on to deliver carbon-neutral concrete by 2050
n 1 September 2020, 40 of the world’s leading cement and concrete companies unveiled a joint industry ‘2050 Climate Ambition’, with an aspiration to deliver carbon-neutral concrete to the world by 2050.
Launched by the London, Englandheadquartered Global Cement and Concrete Association (GCCA) on behalf of its member companies, the ambition statement represents a critical milestone for the industry. It is the first time it has come together globally to state a collective ambition for a carbon-neutral future. The statement identifies four essential levers for achieving carbon-neutral concrete: reducing and eliminating energy-related emissions; reducing process emissions through new technologies and deployment of carbon capture, more efficient use of concrete; reuse and recycling of concrete and buildings; and harnessing concrete’s ability to absorb and store carbon from the atmosphere.
The 2050 Climate Ambition builds on the long-standing climate commitments and sustainability progress of GCCA member companies and affiliate associations across the world, setting out a global vision for the longterm sustainability of concrete. This magazine wholeheartedly agrees with the GCCA when it refers to concrete as a vital building material that has shaped the modern world.
Speaking on 2050 Climate Ambition launch day, Dinah McLeod, GCCA chief executive, said: “As we face the challenges for future generations and begin global economic recovery, concrete will be even more critical to building the sustainable world of tomorrow. That’s why we are making this commitment today so that our crucial industry aligns with global targets, including the Paris Agreement.
“Concrete has a vital role to play in addressing the need for sustainable communities and prosperity. It is a key ingredient of infrastructure, homes, clean water and community resilience as our climate changes. Crucially, it will also help facilitate
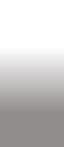
the transition to clean/green energy. We believe this journey will be challenging but are fully committed to working together with our members, partners and stakeholders across the industry and supply chain to achieve this ambition.”
As the GCCA notes, the concrete and cement industry is an essential part of the construction sector – which accounts for 13% of global GDP (gross domestic product) – with a track record of taking climate action. This has included delivering a 19% reduction in CO2 emissions per tonne of cementitious material along with a nine-fold increase in alternative fuel use since 1990.
Albert Manifold, GCCA president and chief executive of CRH, said the 2050 Climate Ambition represents the industry’s commitment to further reducing emissions and ensuring that the “vital product we provide can be delivered on a carbon-neutral basis by 2050”. He added: “There is a significant challenge involved in doing so and achieving alignment across our industry on a sustainable way forward is an important first step. We cannot, however, succeed alone and in launching our ambition statement, we are also highlighting the need for our industry to work collaboratively with other stakeholders in support of our ambition for a more sustainable future.”
GCCA member companies are currently developing a 2050 concrete roadmap which will set out the detailed actions and milestones that the industry will enact to achieve its ambition. It will include working across the built environment value chain to deliver the vision of carbon-neutral concrete in a circular economy, whole-life context. The 2050 concrete roadmap is due to be published in the second half of next year.
Aggregates Business Europe/International will be keeping a close eye on the delivery of the 2050 Climate Ambition in the years to come. We wish all involved with the project great success. GW gwoodford@ropl.com
FRENCH QUARRY LAKE USED AS FLOATING POWER STATION
The Saint-Maurice-LaClouère quarry near Poitiers has become the second-largest floating photovoltaic power station in France.
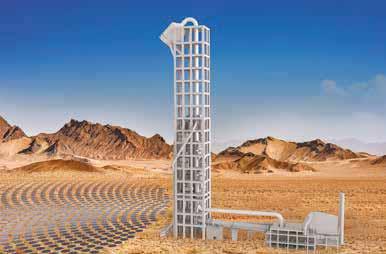
Synhelion’s 250kW solar receiver glows after testing because it reached over 1,500°C
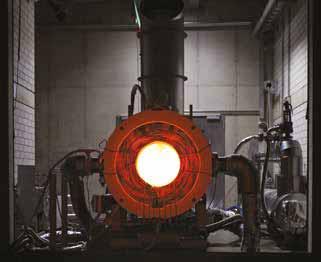
A total of 8,330 floating solar panels have been installed on 4.5 hectares of redeveloped water at the limestone quarry. The power they generate will cover the electricity needs of 2,000 inhabitants.
CEMEX sun-seeking route to decarbonised cement
Global building material giant CEMEX and Synhelion have developed a groundbreaking technology designed to fully decarbonise the cement manufacturing process based on solar energy.
The groundbreaking advancement is an important element of CEMEX’s current Climate Action strategy. Synhelion, based in
emissions, which are then utilised as feedstock for fuel production, enabling cement manufacturing to achieve net-zero level. This is made possible by the unprecedented temperature levels of solar heat provided by Synhelion’s technology and its pioneering process to turn CO2 into synthetic drop-in fuels, such as kerosene, diesel, and gasoline.
expected to be incorporated into an existing CEMEX cement plant by the end of 2022 and gradually extended to a fully solar-driven plant.
The floating power station could be 10% more efficient than a conventional photovoltaic power station because, in hot weather, the water that evaporates cools the solar panels, which improves their production. produces quality limestone used in the preparation of concrete.
The floating photovoltaic power station will be inaugurated and commissioned at the end of September.
This solution is the very first to offer a comprehensive approach to decarbonise the cement industry. Following the research collaboration completed in spring 2020, CEMEX and Synhelion plan to adopt a staged approach towards implementing the technology. A pilot installation is
“Our solar receiver demonstrably provides process heat at unparalleled temperatures beyond 1,500°C, and offers a clean alternative to burning fossil fuels,” said Gianluca Ambrosetti, CEO of Synhelion. “The CO2 emissions from the cement manufacturing mix with the heat transfer fluid for our solar receiver and are integrated into the process. As we are working in a closed-loop system, the CO2 emissions can be easily extracted. We then close the carbon cycle by using CO2 to produce fuels.”
HeidelbergCement supplies material for Germany’s first 3D-printed residential building
Germany’s first 3D-concrete printed residential building.
The high-tech material, ‘i.tech 3D’, was developed by the HeidelbergCement subsidiary Italcementi specifically for 3D printing and is suitable for versatile use with various
The two-storey detached house in Beckum, North Rhine-Westphalia, with around 80m² of living space per floor, consists of three-shelled walls filled with insulating compound. The premiere house was produced by a 3D concrete printer installed on site. The printing results of HeidelbergCement’s material are convincing, and the
for 3D printing is a major challenge. It should be easy
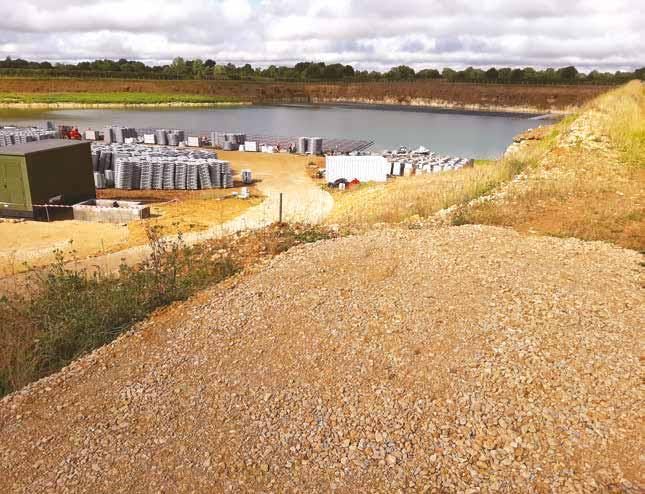
head of the Engineering & Innovation department at HeidelbergCement Germany. “It must also quickly develop sufficient load-bearing capacity so that the lower layers do not give out under the load of the upper layers. At the same time, the bond between the layers must be ensured,” says Scheydt.
The house in Beckum is printed by PERI, one of the leading manufacturers of formwork and scaffolding systems for the construction industry. “The construction of the 3D-printed residential building in Beckum is a milestone for 3D construction printing technology”, says Thomas Imbacher, Innovation & Marketing director at
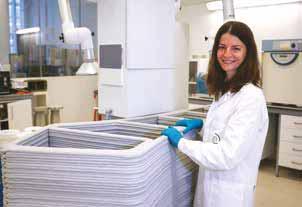
The HeidelbergCement research team is developing material formulations that can be used in various 3D printing techniques
PERI. “We are very confident that construction printing will become increasingly important in certain market segments over the coming years and has considerable potential.”
Engineering company Schießl Gehlen Sodeikat helped secure official approvals for the project. This included the pre-application testing of the project’s 3D concrete printer conducted by staff based at the Technical University of Munich. The 3D concrete printer was developed by COBOD, a Danish manufacturer PERI has held a stake in since 2018.
Pic: GPI HC Group
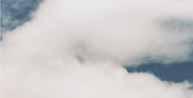
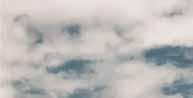

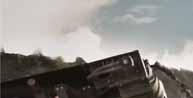
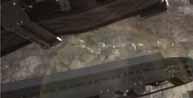

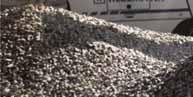

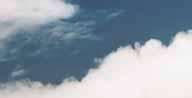
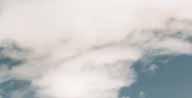
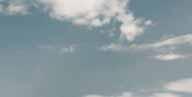
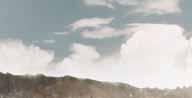
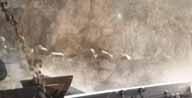
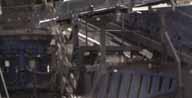
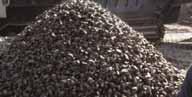
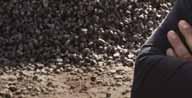

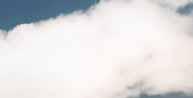
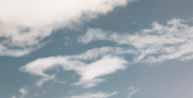

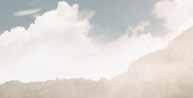
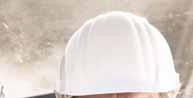
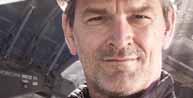


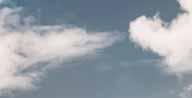
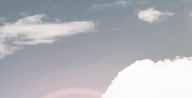
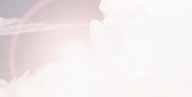
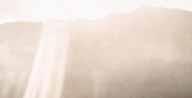

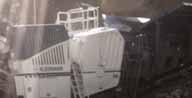
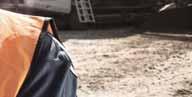


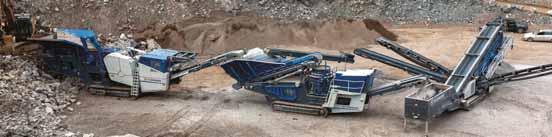
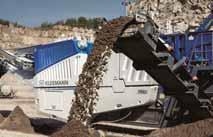
WHEN FLEXIBILITY AND HIGH PERFORMANCE ARE PARAMOUNT. The MOBICAT MC 120 Z PRO mobile jaw crusher and the MOBICONE MCO 11 PRO mobile cone crusher are exactly what you need – perfectly combined with the mobile screening plants from KLEEMANN. Their high production output and low-maintenance operation make them a real alternative to stationary solutions. The PRO-Line from KLEEMANN: Power packs for the quarry.
www.kleemann.info/pro
MCO PRO MC PRO
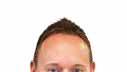
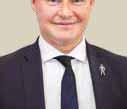
NEW PRESIDENT STARTS AT INSTITUTE OF QUARRYING
Martin Riley, senior vicepresident of Tarmac, has been appointed the 69th president of the Institute of Quarrying (IQ), taking over from the previous incumbent, Phil Redmond.
The new president, like his predecessor an FIQ (Fellow of the Institute of Quarrying), was officially confirmed at the Institute’s AGM, which took place via video conference on 22nd September 2020.
Riley said: “I’ve been involved in the aggregates industry all my working life. I have been a proud member of the Institute of Quarrying for almost four decades. It is a fantastic opportunity to represent IQ at such a critical time for both the industry and our members, as we enter a post-pandemic economy.
“As a proud former industry apprentice, for me, one of the key motivational factors for taking on the role of IQ president is the opportunity to ‘make a real difference’ within the field of education, training and professional development. I hope to use my position to better engage with younger members and attract potential ones by raising awareness about the rewards of working in the quarrying and mineral extractives sector and breaking through the misconceptions that jobs are mainly for men.
“The growth of IQ in the past few years has been impressive and shows how important the industry considers education, training and professional competence. So, it is a huge honour to be the new IQ president, and I am more excited than ever to be playing my part in the Institute’s ongoing development and look forward to championing the needs of the sector at every opportunity.”
Norway government backs Norcem Brevik carbon-capture project
The Norwegian government has formally proposed to the national parliament the launch of the carbon-capture project at HeidelbergCement company
Norcem’s Brevik cement plant.
With 400,000 tonnes of CO2 to be captured annually and transported for permanent storage, HeidelbergCement is planning for Brevik to become the first cement production facility globally to implement an industrial-scale carbon-capture and storage (CCS) project.
The proposition of the Norwegian government is the second last step in the approval process for the project. As the final step, the Norwegian parliament is expected to sign off the project budget later this year.
“We are very pleased with the proposal of the Norwegian government,” said Dr Dominik von Achten, chairman of the managing board of HeidelbergCement.
“This allows us to continue the pioneering work that we started together with our partners in
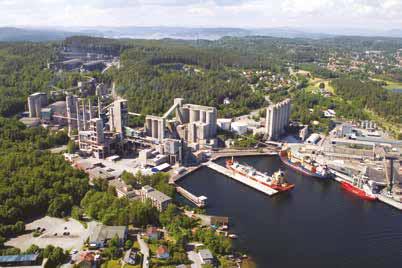
Brevik. The carbon-capture and storage project in Norway is an important cornerstone in our climate strategy. It will enable us to significantly reduce otherwise unavoidable greenhouse gas emissions related to the cement production process.”
Giv Brantenberg, general manager HeidelbergCement Northern Europe and chairman
of the board of Norcem, said: “We have been developing this project since the first desktop studies in 2005 and have interacted well over many years with the Norwegian authorities and our supportive partners. We are proud and honoured that we may soon initiate the building of the world’s first fullscale carbon-capture plant in the cement industry.”
Hanson UK launches new marine aggregate dredger
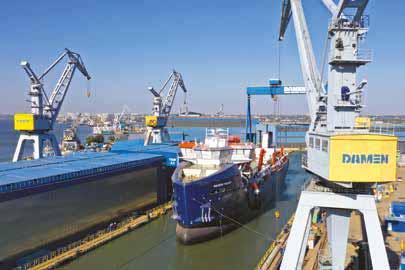
Hanson UK has successfully launched its new marine aggregate dredger (MAD), Hanson Thames. The MAD 3500 model, built by Damen Shipyards Group at its Galati yard in Romania, is capable of extracting marine-dredged aggregates in water up to 55 metres deep and has been designed to ensure safe, comfortable operations – even in
adverse conditions.
The vessel’s innovative design provides increased payload and efficiency, which will allow it to carry up to 7,000 tonnes of marine aggregate per trip, as well as improved fuel consumption and operational and maintenance savings.
It is also equipped with enhanced safety features including an enclosed bow to protect equipment and dredge pipes positioned above the main deck. Hanson Thames will operate in the North Sea and the English Channel.
Hanson CEO Simon Willis said: “The introduction of the new MAD forms part of our strategy to replace our existing ageing dredgers, which supply essential sand and gravel to ready-mixed concrete, concrete block and aggregate bagging plants.
“Coordinated teamwork and Damen’s robust approach to safety have been instrumental in ensuring production continued during the COVID-19 pandemic, so its launch could be completed. The project team have been commendable, and we look forward to working with the group during the next phase.”
Damen will complete further work on Hanson Thames before commissioning, including its dredge equipment and screening installation.
Hanson UK has successfully launched its new marine aggregate dredger (MAD), Hanson Thames
HeidelbergCement’s Norcem Brevik cement plant
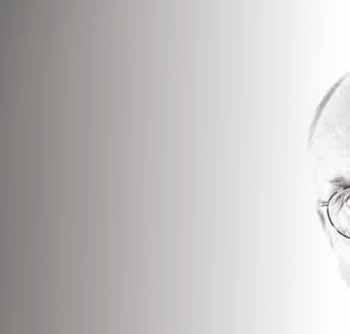

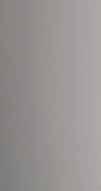
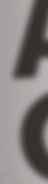
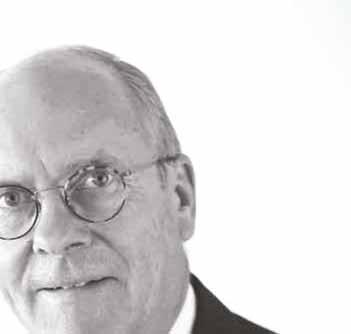

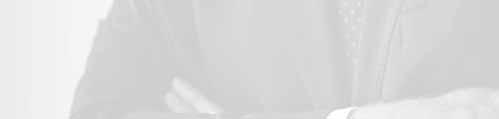
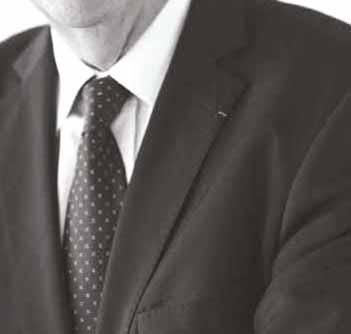

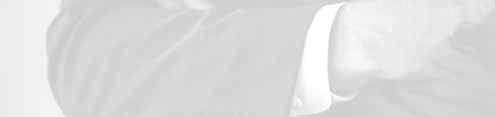

Fighting to secure a rock for all ages
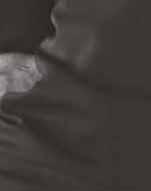

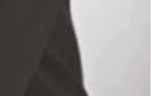
A long-standing and passionate campaigner for mineral-resource sustainability, Arnaud Colson had a highly rewarding career at French building materials giant Lafarge, while holding presidencies and vice-presidencies in a wide range of industry unions and associations. Now running a successful environmental development consultancy, Colson talks to Guy Woodford about his impressive career and the key current and likely future issues within the European and wider-world mineral products industry
After a long and distinguished career in the European building materials sector, Arnaud Colson now runs Paris-based Territoires Consulting
To any large or ambitious small to medium quarry operator looking for advice on more sustainable ways of running their production sites, Arnaud Colson’s CV catches the eye.
After nearly four decades working for Lafarge, the giant French building materials maker, including many years at the forefront of delivering on the company’s sustainability goals, the 67-yearold established ‘Territoires Consulting’ (www.territoires-consulting.com), a Parisbased environmental consultancy helping companies and public and private landowners in their development projects.
Colson left Lafarge in 2017, two years after the firm’s merger with Switzerlandbased Holcim. As a former president of UEPG (European Aggregates Association), an ex-president of UNPG (the Association of French National Aggregates Producers) a former vice-president of UNICEM (the French National Union of Quarrying and Building Materials Industries), and in his long and highly successful career with Lafarge and as chair of the UEPG Environment Committee, Colson has been a prominent champion of the quarrying industry, not just in France but across Europe.
As such, his thoughts on what more still needs to be done in terms of improving mineral-resources sustainability are well worth hearing.
“The European Commission should more pragmatically tackle the issue of mineral resources by deploying and putting in place tools, including directives, regulations and good practices, for equitable access by all countries. We don’t want something like the EU Framework Directive on Water, which, in my view, is very unevenly applied. Improving and achieving consistently high standards of health and safety in building materials production across European countries, including reducing employee exposure to crystalline silica dust, must also be a priority.”
Born in Ksar-es-Souk, a city in east-central Morocco now known as Errachidia, Colson, whose father was a mining engineer, speaks of his alarm at the findings of the United Nations Environment Programme’s (UNEP) 2018 report on sand and sustainability around the world. “The impact of the extraction of the world’s most widely used solid material is increasing as reserves decrease. Some continents such as Asia, South America and Africa exploit these reserves. Europe is, in general, way at the top of CSR (corporate social responsibility) in this area.
“I have seen in Vietnam or Morocco how these sands are squandered. In Morocco, my mother used to walk me on the sandy beaches of Casablanca. Today, this beautiful sand no longer exists. It has been looted and leaves the mother rock bare.
“Let’s not forget that only 50% of the aggregates sold in the world comes from sandpits while the remaining 50% comes from massive rock quarries, extracted by explosives and crushing. It is regrettable that the drafters
of the UNEP report do not mention this nuance.”
Colson welcomes the efforts of GAIN (the Global Aggregates Information Network), created and managed by former UEPG president Jim O’ Brien, to create a worldwide network of aggregates quarries and to produce more statistics and analysis on this issue.
“To save mineral resources, the solution is for engineers and architects to use a combination of building materials and to place great emphasis on construction innovation,” stresses the former Lafarge senior executive.
I ask Colson about his biggest frustrations and obstructions in his work for Lafarge and in his leadership positions at UEPG, UNPG and UNICEM.
“It is to have started a global vision for concrete- and aggregates-sector sustainability, but one that is still to be fully understood by French and EU policymakers. Other building material lobbies such as those around wood are strongly carried by ecological movements because of their obviously apparent link to nature. However, this can create a misunderstanding about concrete, which is a very noble building material that offers great lifetime durability.
“Wood is not recyclable and will inevitably release CO2 into the atmosphere at some point, either by burning or drying. Contrast this with concrete, which is eternally recyclable, and the aggregates that make up its structure are more useful and necessary than ever. The everyday reality is that politicians act under pressure and follow fashion, which is often dictated by ill-informed lobbies. It also shows the importance of better
“I spent 39 years working for what was one of the most beautiful French flagship companies”
communication of how concrete can exist in perfect harmony with people and is a material consistent with approaches to tackling climate change.”
Colson says there is a big difference between the countries operating in Europe when it comes to the pace of adoption of environmentally friendly production methods for building materials. He believes this also has an impact on competition in the international market.
“Marine aggregates production is another good example of an inconsistent European approach,” he continues. “For example, it may take 10 to 20 years to obtain an operating licence in France, but only three to five years in the UK. I would also like to ask why European politicians are slow to recognise the contribution of quarries to biodiversity? The UEPG also fights illegal extractions in some European countries alongside the authorities, which are sometimes deprived by national governments of the means to control the problem.”
A Maritime Spatial Planning Framework Directive, adopted in 2014, gives EU member states sole competence on land-use planning and permitting; so a new framework directive formalising a consistent approach to marine aggregates production licencing applications

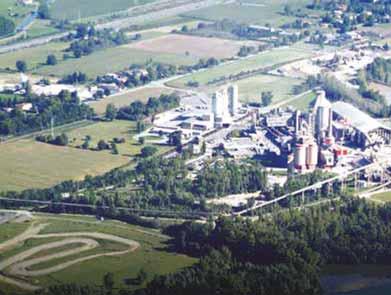
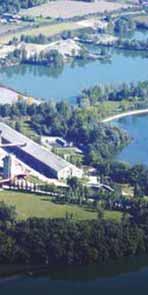
Arnaud Colson’s final role in his 39-year career with Lafarge was as the company’s director of French Public Affairs and Sustainable Development (Aggregates, Cement & Concrete). Pictured is the LafargeHolcim Martres-Tolosane cement plant in south-west France. In recent years, the site has benefitted from a €100mn modernisation project

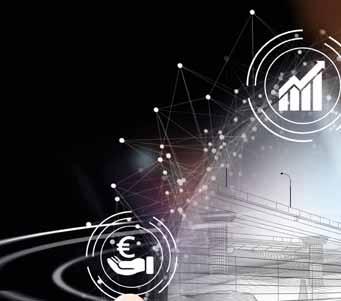

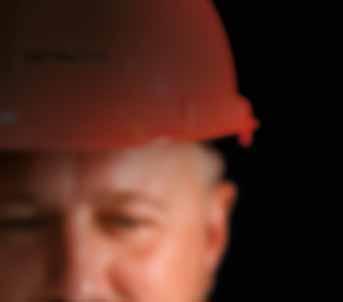
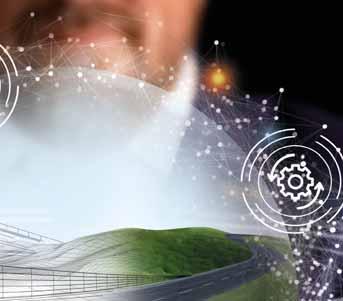

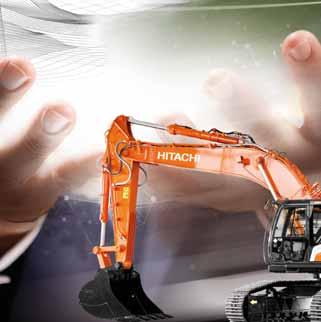


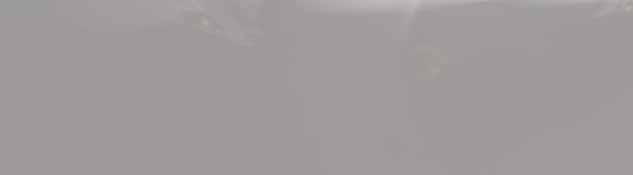
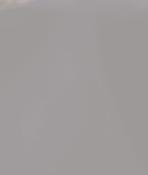
is likely to require a change of EU treaties.
Colson had a near four-decade working life at Lafarge, with his final senior role being the company’s director of French Public Affairs and Sustainable Development (Aggregates, Cement & Concrete).
“I prospered there and was very proud to have been able to participate in the launch of a true approach to sustainable development via the launch of an environmental policy encompassing the company’s 500 establishments (quarries, ports, cement plants, concrete plants) and driven by the dynamism and vision of Bertrand Collomb. Bertrand was, for me, a captain of industry, a strategist and a real team player.
“In my personal opinion, Lafarge merged with, or more accurately, was bought by Holcim because of too much debt and strategic errors. I spent 39 years working for what was one of the most beautiful French flagship companies in the world of heavy industry, but I did not enjoy my latter time before leaving the group. LafargeHolcim is now a new group established by and managed from Switzerland. It is well structured internationally and well managed.”
Returning his attention to how to achieve a more sustainable building materials industry, he says: “It is essential to consider the size of the industry’s carbon footprint. Financial analysts need to regain confidence in the building materials industry and major companies like LafargeHolcim. This requires tangible results on CO2 reductions, the use of alternatives to fossil fuels, and water management. New constructive systems are an opportunity. The consideration and improvement of biodiversity in aggregates extraction sites is a key issue for site staff and the sector in general. It also creates new jobs. A lot has already been done. The UEPG has gathered around 200 good biodiversity practices in aggregates extraction sites on its website, but there is still room for progress. That has not escaped NGOs (non-government
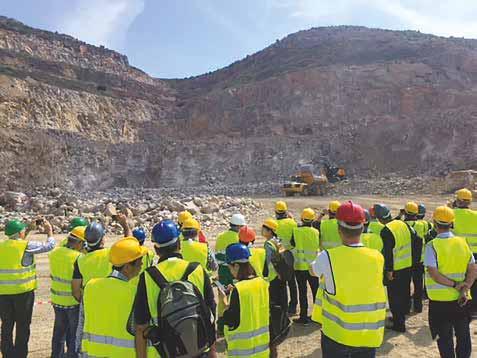
2006 and 2017, and I still expect an ambition to be laid out in this regard by LafargeHolcim. From a European policy perspective, it would be nice to introduce a tax at Europe’s borders to limit the unfair competition of low-cost materials, especially cement. This would certainly be a guarantee of improving the competitiveness of our European businesses. These companies absolutely need to get their profit margins back.”
Colson served as UEPG president from 2012 to 2015 and is a firm believer in the association’s ability to represent the interests of and campaign for the continent’s €15-20bn turnover, 15,000 companies-strong mineral products industry in its dealing with EU policymakers.
“I am still a member of the UEPG board of directors as honorary president. The association does an outstanding job with a small and close-knit team representing 23 member countries.”
The UEPG ‘engine room’ comprises four committees, their task forces and working groups, plus a standalone public relations and communications task force. The four committees are Health and Safety (RCS [respirable crystalline silica] working group); Environment (biodiversity; air quality; marine aggregates; and water management task
The top-level meeting is the delegates assembly held in May or June each year, where all members debate and decide on UEPG activities and strategy.
Colson says: “More than 30 years ago, UEPG invented a sustainable development competition chaired by an independent external jury every three years. The association also organises multiple field trips for members covering various topics. We did not hesitate to intervene on behalf of the various member countries, as I have been able to do in Romania or Poland to promote a virtuous industry, helping to eradicate corruption, truck overload, and compliance with safety rules. What is important in the future is to improve the visibility of UEPG and the recognition of the importance of aggregates for the European construction sector.”
Colson has some thought-provoking and data-supported views on the current state of the COVID-19 pandemic-disrupted European quarry and building materials sector.
“It will undoubtedly emerge better from this delicate period than those of services, aeronautics or automobiles. We need to build. XERFI [a leading French business market research company] estimates that the decline of French GDP is expected to be in the order

A quarry site visit during the UEPG General Assembly in Barcelona, Spain, in 2018
A site visit during the UEPG General Assembly in Helsinki, Finland, in 2014
accommodation and catering are logically the sectors most directly affected by COVID19 closures and administrative restrictions, followed by some trade and household services, such as nursery and school childcare, leisure and cultural activities. On the other hand, real estate leasing activities, the agri-food sector, energy, water and waste management, financial and non-market services are cushioning the economic shock. Other industries and business services are now halfway towards recovery.”
Colson notes that in France this year, it is estimated by market analysts that aggregates sector production will be down around 17%, assuming there is no further lockdown due to a second wave of COVID-19. He says a production increase of “at least 15%” could take place in 2021 but stresses that there are currently no official figures on this.
“Aggregates quarrying activity in Europe is down. The UEPG-estimated percentage difference in full-year 2020 production compared to 2019 shows that the least affected countries are expected to be Norway, with no decline in production; Denmark -2%; Germany -2.5%; and Hungary -3%; The Netherlands -10%; and Belgium -25%. The most affected nations are tipped to be Italy and Spain at -40%; followed by Greece and the United Kingdom at -30%.
“Overall, UEPG estimates there will be a 15.4% decrease in European aggregates production to 2.61 billion tonnes in 2020
compared to 2019. This would be comparable output to 2013. The UEPG estimates that production will rise to 2.71 billion tonnes in 2021, 3.7% up on 2020. In 2021, some countries are expected by UEPG to see a particularly notable recovery, including Spain +25%; France +15%; and Denmark and the Netherlands, rising by 10% and 15% respectively. Overall, however, there is a low degree of optimism about a wider economic recovery in 2021. After the crisis of 2008, there were five years of decline, then six years of recovery.”
Colson believes that for construction and wider industry, the possibility of a production catch-up is limited or delayed by capacity. “To catch up, we would have to produce more building materials, and for several months. This would mean mobilising additional resources, but where would they come from?”
The French-German-led initiative seeking to revive Europe-wide economic activity via a massive €750bn EU economic stimulus fund may, says Colson, be the key to getting out of the current COVID-19-induced economic crisis. Colson believes it could accelerate ecological and digital transitions, increasing the EU’s resilience and economic and industrial sovereignty and giving new impetus to the single market.
Looking further ahead, Colson is optimistic about the long-term future of the European building materials and construction sectors.
“The arrival of the circular economy, along
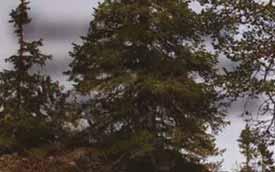




with recycling, and composite materials or even bio-based materials, will profoundly change some areas of construction. However, we will always need natural aggregates, exploited rationally and economically, for civil engineering and construction projects.
“When I left Lafarge three years ago, I immediately set up my Territoires Consulting business. It helps companies and public and private landowners in their development projects. Working in the renewable energy sector, I have also established a partnership with a company that creates and sets up photovoltaic [solar] farms on sites, including quarries. I am very pleased with this innovative approach to renewable energy. It is a natural extension from my career with Lafarge.”
A long-time resident of Paris, when he’s not working Colson, a former student at the city’s Ecole Nationale des Ponts et Chaussées (National School of Bridges & Causeways), enjoys spending time with his wife, four children and four grandchildren. He also finds time for many other interests. “I also enjoy skiing, high mountains, nature and time spent as a reserve officer of the French army and as an auditor at the Institute of Higher National Defence Studies (IHNDS). This allows me to delve deeper into geostrategic issues related to national defence.”
Working to defend a nation as well as a continent’s mineral products industry. Life remains full for Arnaud Colson. AB
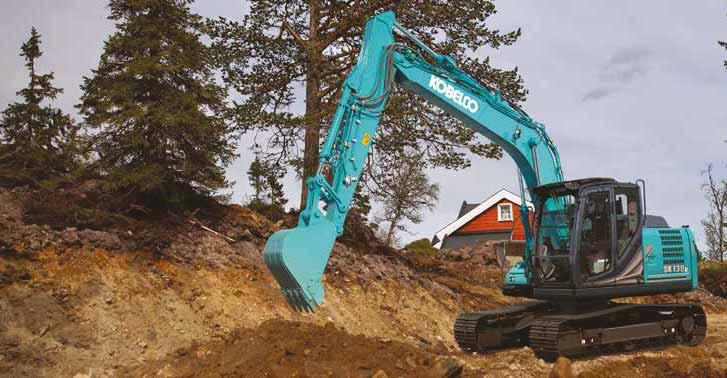
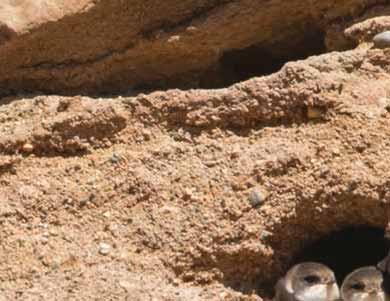



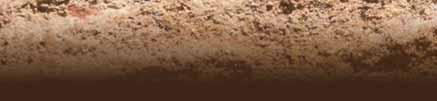
UEPG at a virtual EU Green Week 2020
The COVID-19 crisis has affected the health of people on a global scale, as well as the economy. It has also shown the impact of human activities on the environment and what it can trigger, from the coronavirus pandemic to the reappearance of nature induced by a temporary general lockdown. Climate change, the unprecedented loss of biodiversity, and the spread of pandemics sent a clear message on the need to change and improve our way of life.
The European Commission put on top of its political agenda the adaptation to climate change, reversing biodiversity loss, increasing circularity and digitalisation of the economy. The Covid-19 crisis has increased further the urgency to address our impact on the environment. Therefore, to accelerate the process, European institutions opted for a ‘green recovery’. The European Commission will put the European Green Deal and its new EU Biodiversity Strategy 2030 at the heart of the economic recovery.
The EU Green Deal is a package of measures addressing several policy areas to modernise the European economy, enable a sustainable green transition and to become the first climate-neutral continent by 2050. It is the new growth strategy of the European Union for the coming years. It includes among the proposed measures, a new EU Biodiversity Strategy, considered a central element in the EU recovery plan.
The European Commission will address these issues at its largest
European Environment Conference: the EU Green Week, but this time in the virtual world. The 2020 edition will be taking place from the 20 to 22 of October 2020 on the theme ‘Nature and Diversity’. The conference will focus on how to build a resilient society and a sustainable economy, by reversing biodiversity loss and stimulating a green recovery. Exchanges will examine how to change economic activities, driving biodiversity loss and balancing the implications for the future of the economy and society.

solitary bees among many other species. Biodiversity protection can surely benefit from the dynamic management of extractive sites.
Given the ongoing COVID-19 pandemic and related health policies and travel restrictions, the European Commission will organise the entire EU Green Week event exclusively online, in a new virtual experience. Conference sessions and the exhibition area will be designed for virtual visits, enabling live interactions with speakers and exhibitors, providing the possibility to explore the stands and network with other participants.
UEPG, the European Aggregates Association, will have a virtual stand at the EU Green Week 2020. This will be an opportunity to present the aggregates industry’s contribution to the conservation of nature and demonstrate how it can be part of the solution, as a partner that can extract raw materials and at the same time help to protect and to restore nature. By the very nature of its operations, aggregates extraction sites create new habitats and attract pioneer and rare species, such as the sand martin, eagle owls, lizards, natterjack toads, and
UEPG will display over two hundred good practice examples across Europe, showcasing the compatibility of sustainable aggregates extraction with nature conservation objectives. As one of the few sectors represented among major actors on the EU Biodiversity Policy, the European Aggregates Industry is now widely recognised as a trusted partner for nature conservation by EU institutions and a growing number of NGOs and academic researchers.
These exceptional circumstances make way for new opportunities. The messages of our industry will reach out to a broader and more international audience for the first time through an online and virtual Green Week.
Indeed, not only will it reach out to high-level EU decision-makers but also stakeholders throughout Europe and the whole world, from local authorities to companies, from industry representatives to environmental organisations and citizens. Be part of these exchanges, discover how the aggregates industry can contribute to nature conservation. More information and the registration portal for the EU Green Week 2020 is available on the following link: https:// www.eugreenweek.eu/en. AB
• For more information on UEPG and its activities, please visit: http://www.uepg.eu/
The UEPG is taking part in a virtual EU Green Week 2020. Pictured are sand martins, Europe’s smallest hirundines.
Source: UEPG SDA 2019, Destia, Finland
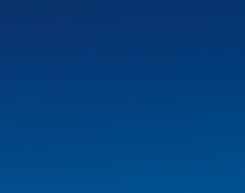
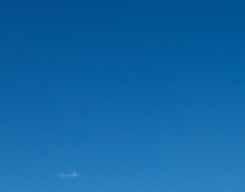
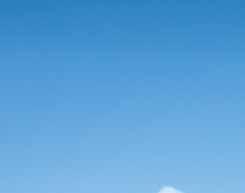
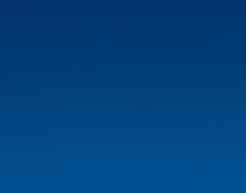
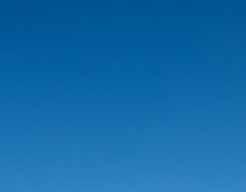
Our expert engineers design customised solutions which transform natural sand & crushed rock reserves into high-value products for an exceptional return on investment. An integrated water management system recycles up to 90% of process water for immediate re-use in the system, significantly reducing footprint & maintenance of settling ponds.
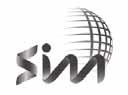
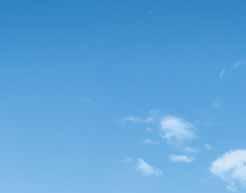

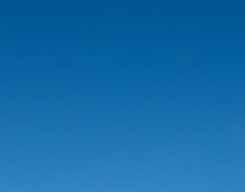
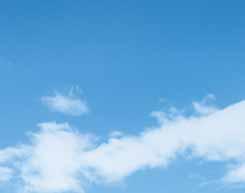

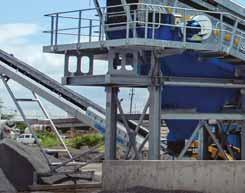
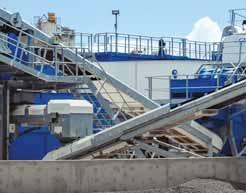
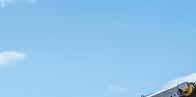
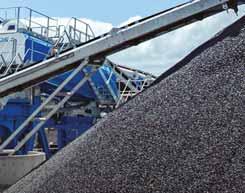




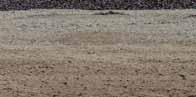
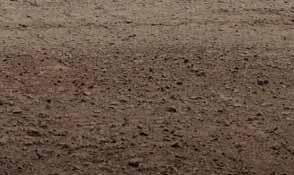


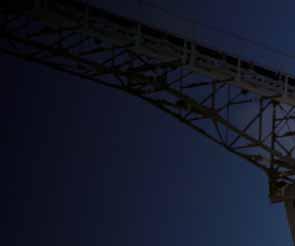
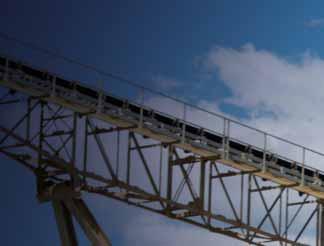
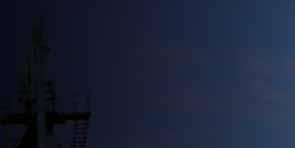
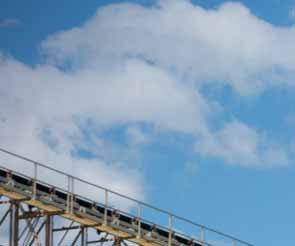
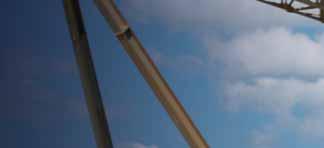
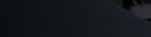
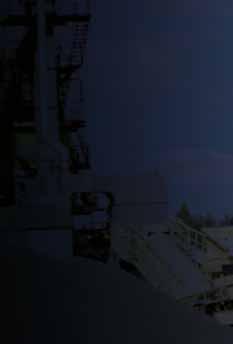



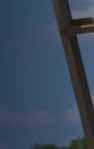

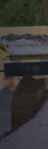
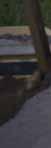
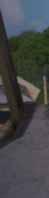
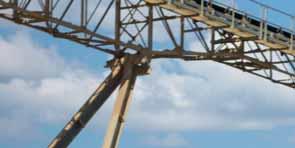
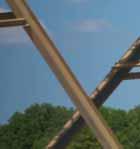
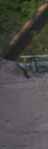

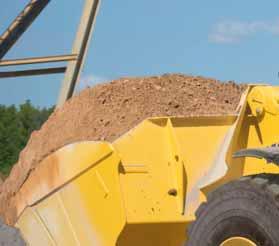
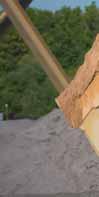
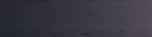

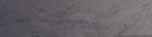

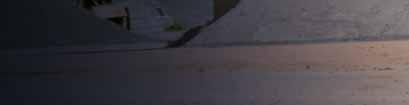
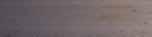
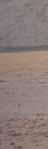
WA475-10 WHEEL LOADER


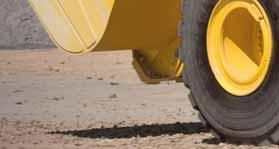
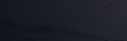
Komatsu WA475-10 – Get ready to rumble!


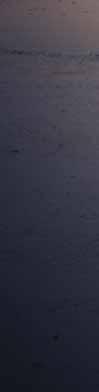


With the Komatsu Hydraulic Mechanical Transmission (K-HMT) that delivers an outstanding combination of ultra-low fuel consumption and massive productivity increase, the all-new WA475-10 is an industry-leading top performer. A unique, independent control of driveline and work equipment eases operation and shortens cycle times like you never experienced before in a wheel loader.
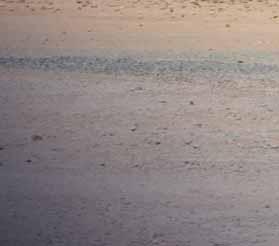
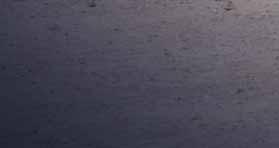
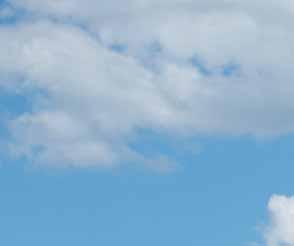
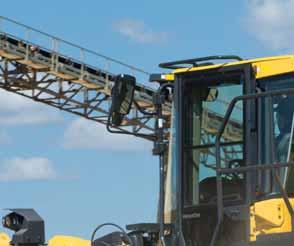



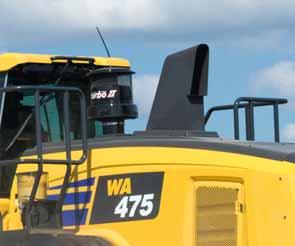
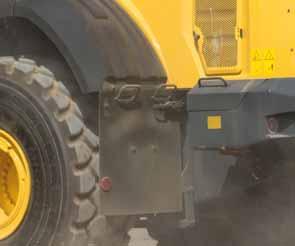
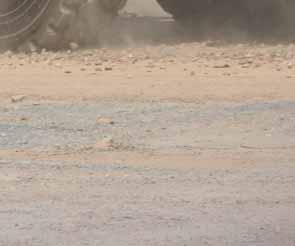
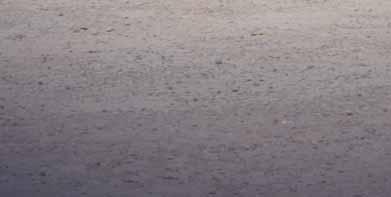
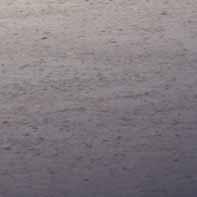
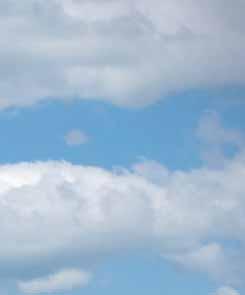
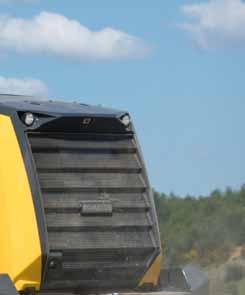
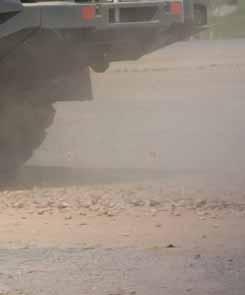
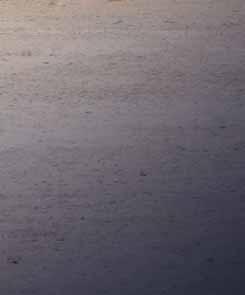

INTELLECTUAL PROPERTY MYTHS DISPELLED
Intellectual property is an asset that adds value to your bottom line and stops others benefitting from your innovation. Specialist intellectual property lawyer Kathryn Heath explains why aggregates businesses should protect their intellectual Property and dispels some common myths about it
Intellectual property (IP) refers to creations of the mind and includes inventions, designs and symbols, names, images, and written materials.
There are various ways to protect your IP, including the use of patents, copyright, trademarks, confidentiality obligations and unregistered and registered design rights. IP is intangible, and perhaps that is why there are many myths and misunderstandings around it. One of the best ways to understand IP is to dispel some of those myths.
I don’t have any IP
Aggregates and mining businesses are likely to have a variety of IP rights. Innovations in this area which are likely to attract IP rights include tools and machinery, sensors, robots, software, and autonomous vehicles. These innovations may be used to carry out assessments, improve productivity, increase yields, and increase safety.
Collaborations and joint ventures are also common in the aggregates sector, with organisations often working together to create intellectual property jointly.
Intellectual property rights will also exist in digital assets such as data analysis software and modelling tools for mine designs, as well as digital mapping technologies.
Written reports with photographs and diagrams and the use of academic research are also impacted by IP rights.
I can’t afford to worry about IP I would argue that you can’t afford not to worry about it. IP is a valuable asset. Protecting it properly will add value to your business and prevent competitors from using it. If you do not adequately protect your IP, it is likely to cost you more in the long run.
I have a domain name – I don’t need to register my trademark
Owning a domain name, or being a wellestablished business in your market place, does not protect your business name or brand. The only way to do that and prevent others from using it is to register your trademark in the territories you operate in.
“You need to look at how to protect your IP in each territory and seek specialist legal advice”

Someone created materials for me; I paid them – I own it
Although copyright occurs automatically, the owner will usually be the person who created the work. This can cause issues, for example, where a contractor (such as a web developer, designer or consultant) completes work on your behalf. It is important to ensure this is assigned to you in a written document.
NDAs are not worth the paper they are written on
Correctly drafted non-disclosure agreements are a useful way to protect your business and can act as a deterrent. NDA’s limitations often arise when they have been poorly drafted. Issues to think about include; who needs to sign the document, what the remedies will be if there is a breach, what territories the agreement needs to be enforceable in, etc.
I do not need to think about IP unless I spot an infringement If you leave it until you spot an infringement, unless you already have the relevant registrations and protections in place, there is often very little you can do about it. Unregistered rights are usually much harder and more expensive to enforce.
I am covered in the UK; therefore, I am covered everywhere else IP rights are territorial in nature, so just because you have a trademark or other right protected in the UK, it does not mean you will be protected overseas. If, like many aggregate
and mining businesses, you work across multiple territories, you need to look at how to protect your IP in each territory and seek specialist legal advice.
My developer is working on an agile basis, so I cannot write a contract Agile is a development methodology which gives increased flexibility for developers and their customers as it enables the parties to continue to define the project as they go. It can be an effective way of working, but the flexibility can cause tension, so having a wellwritten contract is imperative. It is possible to create contracts which will work with an agile methodology, and it is important you put written contracts in place with thirdparty developers to protect your business adequately. AB
CONTACT
Kathryn Heath is a senior associate in the intellectual property and IT team at Stephens Scown LLP. The firm has over 70 years of experience in the mining and minerals sector, and its specialist team is recognised by independent legal guides Legal 500 and Chambers.
To contact Kathryn please call 01872 265100 or email solicitors@stephens-scown.co.uk. For more information visit www.stephens-scown.co.uk
The ‘Le Grand Paris’ project has been a main source of recent demand for France’s aggregates and concrete producers.
Image: @Eurovia/Przemek Kulaga



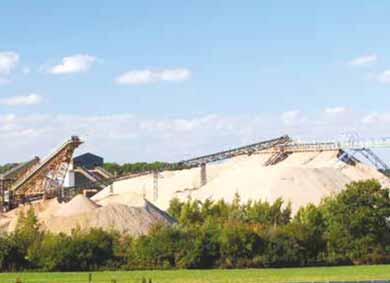
“Grands projets” give cause for optimism in France

The French aggregates and construction materials markets are among the most heavily impacted in Europe from COVID-19, but ongoing major construction projects such as the “Grand Paris” redevelopment scheme and the 2024 Olympics can help maintain materials demand. Liam McLoughlin
The demand for aggregates in France reached 435 million tonnes in 2019, according to data from UNICEM, the national quarry industry and construction materials association. Most of French aggregates production (65%) is used for road construction/maintenance and railways, network and infrastructure, 27% is dedicated to concrete production, and 7% to coated road materials.
UNICEM says it expects overall production to be down between -15% to -20% in 2020, much of this decline stemming from the impacts of the COVID-19 pandemic.
In a statement issued at the end of July UNICEM commented on how aggregates market conditions had unfolded this year: “While the activity indicators for the very beginning of 2020 seemed rather well oriented with a certain strengthening of the production of materials, the arrival of the Coronavirus epidemic on French territory and the start of containment in mid-March put a stop to a large part of economic activities, especially in the construction sector.”
In terms of materials, UNICEM said that activity plunged over the first four months of the year, while in mid-June, even if almost all sites were open, their activity rate still remained at -5% to -10% below their pre-crisis level.
Mathieu Hiblot, secretary general of the National Union of Aggregate Producers (UNPG), says that over the last two years the works related to the massive ‘Le Grand Paris’ urban renovation project in the French capital have had the biggest influence on demand for aggregates and ready-mixed concrete.

“This effect applies both in the Ile de France region, but also in neighbouring regions that supply materials for the construction of stations, roads, housing and business premises etc.” says Hiblot.
Started in 2007 under Nicolas Sarkozy’s presidency, the Grand Paris scheme encompasses large and iconic initiatives such as the Grand Paris Express public transport project, a rethinking of road transport, the creation and strengthening of urban centres, better integration between districts, and preservation of the green belt.
Etienne Lalande, Terex Trucks regional
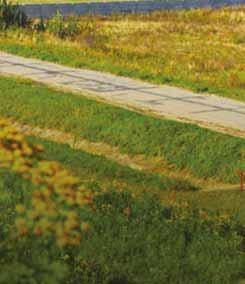
sales director for France, Germany, Central Europe, North Africa and the Middle East says that the Seine-Nord Europe Canal is another important project that is expected to boost the French construction sector and provide business opportunities for original equipment manufacturers (OEMs). The scheme will involve the construction of a 107km inland waterway link extending from France to Belgium, connecting the Seine basin north of Paris to the Rhine basin and the northern European waterway network.
“For the construction [of the Seine-Nord Europe Canal] 55 million m3 of earth will have to be excavated and transported,” Lalande says. “Robust and reliable dump trucks like the [Terex Trucks] TA300 and TA400 are the natural choice for this task.”
Florient Myrope, GCI (global construction & infrastructure) marketing manager at Bergerat Monnoyeur, dealer in France for quarrying equipment manufacturer Caterpillar, says: “The Grand Paris project is moving forward, the 2024 Olympics Games [in Paris] are coming up. There is mid-term
In terms of how the French aggregates sector can recover from the pandemic, Myrope says this will depend on France’s aid plans for the construction and building sectors, but he adds that Caterpillar believes that demand will still be strong in 2020 and
He says that, for the most part, quarries in France did not stop producing during the health crisis, although they were no longer
“Quarries used that time to reorganise
Mathieu Hiblot, secretary general of the National Union of Aggregate Producers (UNPG)
their stocks and take care of the crushing of non-treated demolition materials,” says Myrope. “On the balance sheet, the months of April and May were very weak in terms of generated revenue but made it possible to organise a good recovery in June and July.”
Hiblot says that, although quarries and materials production sites were heavily affected by the drop in activity, they were very quickly reopened, or even still available during the containment period.
“The configuration of the production sites – outside and with few contacts – explains why, at the beginning of May, at the height of the crisis, nearly 88% of the sites were open,” he says, adding that it was chiefly the lack of demand that prevented quarrying activity.
Since the deconfinement period, aggregates production activity has picked up again. Hiblot says that aggregates production was at around 75% of the normal level in May and around 100% or even more in June, according to the latest UNICEM surveys. Moreover, by mid-June, almost all France’s materials production sites were open (98%).
“The COVID-19 pandemic has affected almost all markets and industries and France was no exception, with many activities coming to a standstill,” says Lalande. “However, the population has been returning to work and our dealers are once again busy with their sales activities.”
Of the annual 435 million tonnes of aggregates in 2019, 314 million tonnes were produced in quarries and 121 million tonnes (28%) came from recycling. Recycling in quarries, with materials from demolition, has been growing rapidly for the last five years.
This is a fundamental trend that will continue to grow in the coming years, according to Myrope.
“We can see it all over the country. The large quarries all have their own areas
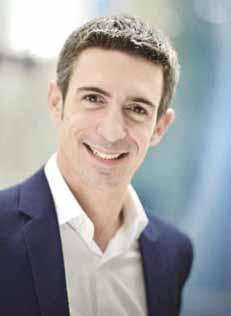
dedicated to this activity, and we know that it is profitable,” he adds. “This trend will be confirmed in 2020, and the customers of quarries are increasingly demanding this share of recycling in their requests.”
Hiblot estimates that the use of recycled aggregates has doubled over the last ten years, which has led to a decrease in aggregates production at French quarries.
Over the last 20-30 years, the average annual production level of aggregates in France has been around 370-380 million tonnes. Since aggregates demand peaked in 2008, French producers are now producing 100 million tonnes a year less. This can be explained by a sharp drop in demand and a significant increase in aggregates recycling, according to Hiblot.
“Today’s production does not cover
the entire demand and requirements for aggregates,” Hiblot says. “Indeed, in addition to the different substances extracted (which varies according to the uses and destinations of the aggregates - concrete, asphalt mixes, ballast, public works uses, etc.), a significant proportion of materials are produced in the circular economy through recycling and recovery.”
In 2018, the demand for aggregates in France was estimated at 445 million tonnes, of which one-third was accounted for by recycled materials.
Major building materials suppliers in the French market expect a heavy ongoing impact on their business from COVID.
In its 2020 half year report, building materials supplier LafargeHolcim said that cement volumes in some major European markets such as France had been particularly impacted by the COVID-19 pandemic with construction activity heavily down compared to less affected territories like Germany, Switzerland and Eastern Europe. The group’s cement volumes in Europe in H2 2020 reached 20.9 million tonnes sold, or a 7.0% decline on a like-for-like basis compared to 2019.
HeidelbergCement became a large player in the French building materials market through its acquisition of Italcementi in the second half of 2016. This deal saw it take ownership of Ciments Calcia (cement production and distribution), Unibéton (ready-mixed concrete), GSM (aggregates production and distribution) and Socli (lime production). HeidelbergCement also owns Tratel, a major transport company of pulverulent/bulk powder products.
In June 2019 HeidelbergCement also finalised the acquisition of 100% shares in the aggregates and ready-mixed concrete activities of Cemex in central France. This deal saw it acquire production sites and distribution facilities for aggregates, including 28 ready-mixed concrete plants and seven aggregates quarries, strengthening the group’s vertically integrated market position in central France.
In its financial report for the first half of 2020 HeidelbergCement said that economies in countries such as France suffered significantly in the first half of 2020 due to the
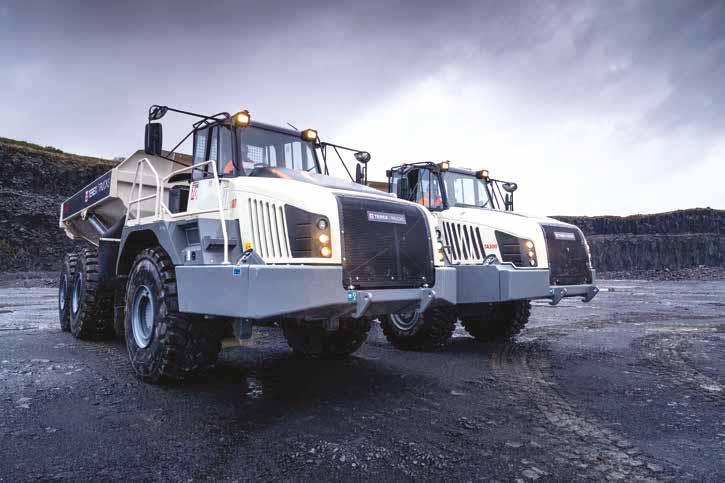
Florient Myrope of Caterpillar dealer Bergerat Monnoyeur
Terex Trucks says its robust vehicles will be suitable for the demands of the Seine-Nord Europe Canal project
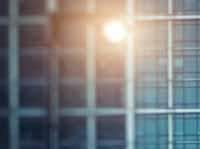
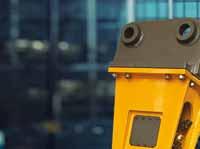
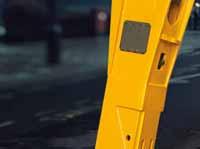
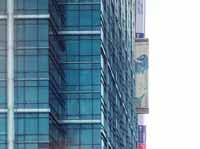
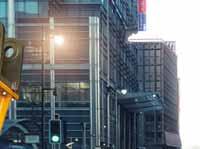
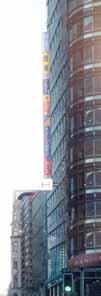

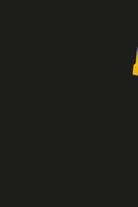

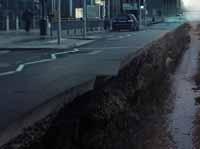


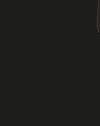
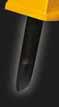
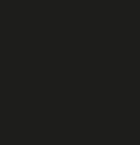


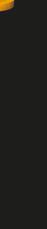

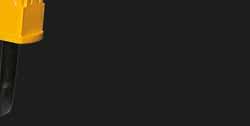
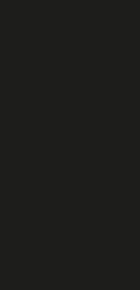


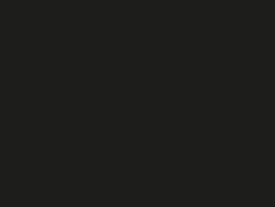
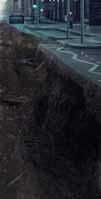
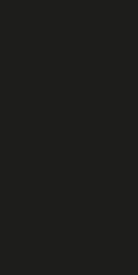

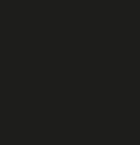


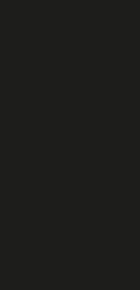
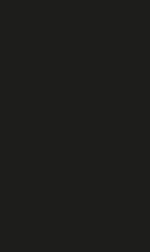
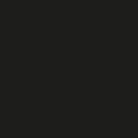
pandemic. For the full year, the European Commission expects a decline in economic output of over 10% in France.
In terms of products that are most in demand from French quarry operators Florient Myrope says rigid trucks are very popular, such as Caterpillar’s range of 770G to 777G (100 tonne) models.
He adds that Caterpillar wheeled loaders are also in demand: “For wheeled loaders working at the quarry loading sites from the 950M to the 980M, and for those working at the quarry face, from the 980M to the 992K. Those models combine maximum driving comfort with minimum fuel consumption for optimum efficiency.
“But it’s not just about the equipment, quarries constantly strive to maximise their productivity, and of course, safety is paramount.”
To meet this requirement and support its customers, he adds that Caterpillar has developed a range of services and connected solutions such as the Cat Driver Safety System (DSS), an in-cab monitoring technology that helps keep operators alert. It also provides proximity awareness systems, and fleet management solutions to increase fleet utilisation, control costs and use capital more efficiently.
France is the second-biggest market for articulated trucks in Europe and an important market for Terex Trucks. “The largest of our two articulated dump trucks, the TA400, is the most popular with customers in the French quarrying industry due to its bigger payload,” says regional sales manager Etienne Lalande.
“Customers are looking for robust haulers with a strong body and low operating cost, as well as quarry tyres and telematics – all of which our trucks can deliver. One of the reasons customers choose our trucks is because they are robust and reliable. At a quarry, continuous production is key – so you need a durable truck that will deliver high uptime.”
Rigid trucks such as the Caterpillar 770G are popular with French quarry operators
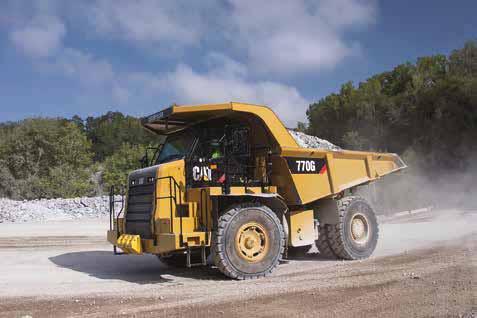
He adds that another important aspect for customers is aftersales service. Terex Trucks is expanding its distribution network in France and currently has four dealers: The Manu Lorraine Group, Framateq Sud-Est, Promatex and Griset Materiel.
“All our dealers have a strong reputation for customer service excellence and a vast amount of experience,” he says. “They sell both the Terex Trucks TA300 and TA400 articulated haulers, as well as stocking parts and components.”
Framateq recently sold one of Terex Trucks’ upgraded TA300s to a company in the south-east of France, which is using the truck at a quarry. Lalande says the hauler delivers a 5% improvement in fuel efficiency, a 5 km/h increase in speed to 55 km/h, an extended 4,000 hours oil change period and enhanced performance.
Founded in 1996, Griset Materiel was relatively recently appointed as a Terex Trucks dealer. It sells, services and repairs construction equipment from two locations in the Rhône-Alpes area.
Looking ahead at potential developments in the quarrying and aggregates sector over the next 18 months, Myrope says: “We notice a trend for tertiary material demand (0-35mm diameter) for surface layer road maintenance and concrete. Less demand for primary and secondary aggregates which sometimes need to be re-crushed in some quarries.”
Mathieu Hiblot of the UNPG says the best-case current scenario is a level of activity close to 10% below normal at the end of 2020. In other words, beyond the technical rebound of the summer, activity would not return to its ‘normal’ level and the year 2020 would end at 15% down for aggregates. Fiscal 2021 would also remain below normal, in part because of the effects of the pandemic.
The construction project pipeline in France provides cause for optimism, having been estimated at a total value of €374.8bn. Under the Housing First plan, the French government is investing €4bn to build 40,000 affordable housing units per year across the country until 2023. AB
National production of quarry and marine aggregates in France (1998-2018)
Source: UNPG
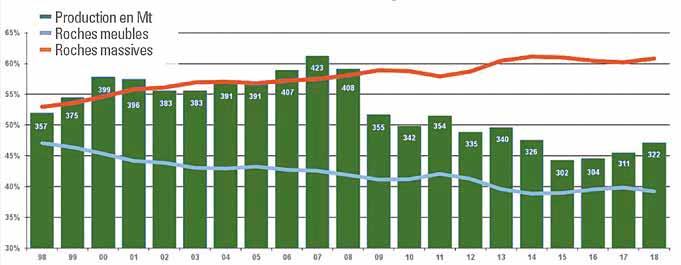
Production (in millions of tonnes)
Loose rocks
Large rocks
Falkland Islands quarry upgrades to meet thriving demand
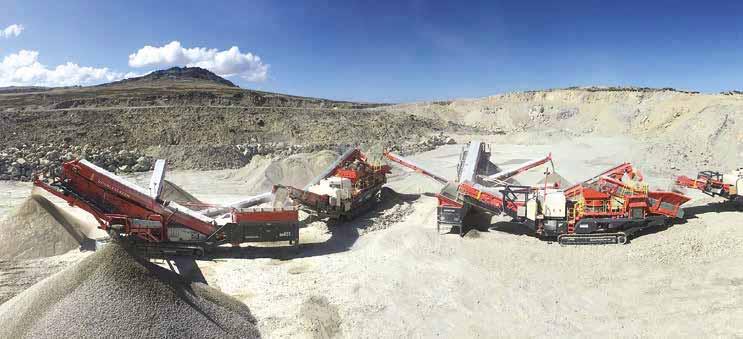
The only operational quarry in the Falkland Islands has invested in new mobile crushing and screening equipment to meet the South Atlantic Ocean archipelago’s increasing demand for aggregates. Liam McLoughlin reports
Pony’s Pass Quarry in the Falkland Islands has invested in three new crushers, an impactor and two triple deck screens. Despite its isolated position on East Falkland, the quarry is a booming site which annually produces 160,000 tonnes of quartzitic sandstone using a state-of-the-art mobile crushing and screening train.
Sandvik Mobiles has advised the quarry on a train of equipment to best complement the uptime required for an operation of this scale. The chosen crushers and screens have been deployed since the start of 2020 and comprise a UJ440i jaw crusher, two UH440i cone crushers, a QI442HS impactor and two QA451 triple deck doublescreens.
Pony’s Pass currently provides perfectly sized aggregates for road construction and infrastructure development projects as well as supplying an on-site asphalt plant. Future developments are likely to see the current 160,000 tonnes annual production increase to over 300,000 tonnes per year.
Due to the isolated geographic position, over 300 miles from the mainland of Latin America, and the extreme weather conditions that are frequent, this meant that the solution chosen had to tackle all potential challenges. As the only Falkland Islands quarry, almost every project on the island requires aggregates from Pony’s Pass, meaning
service and aftermarket support is also a vital component to keep operations running smoothly.
The new equipment has performed with output levels always meeting expectations, according to Pony’s Pass quarry manager Marc Short, who added: “We currently use our mobile crushers to produce three small end materials: these being 10/20mm, 5/10mm and 0/5mm crusher dust. However, we have the ability to produce type 1 (all in
bottom of the quarry) where they are fed with as-blasted material.”
The feed material is crushed quarzitic sandstone, with a maximum feed size of 700mm.
The abrasive nature of the rock and the need for machines that can deliver maximised uptime meant that it was essential for the quarry to have a durable and productive primary jaw crusher before the material is passed through to the secondary
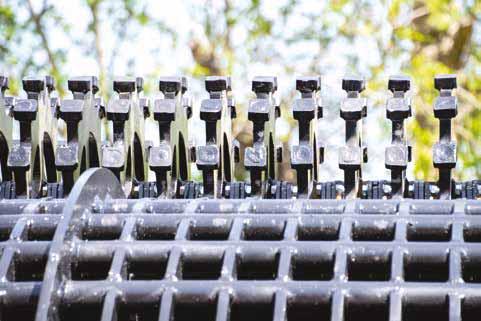
The new crushing and screening train in action at Pony’s Pass, East Falkland
The new trommel drum cleaner from MDS
hydraulically with a choice of jaw plates to suit the needs of the operation. This means that the crusher can work at optimum levels for longer periods, with all impact zones having a rubber lining to reduce wear and noise. In addition, the 62.5 tonne crusher has a 1,200 x 830mm jaw opening enabling it to deal with Pony’s Pass’ 700mm feed. The UJ440i can crush at a throughput of 250mtph.
Following on from the UJ440i jaw crusher, the rock is then fed into the UH440i cone crushers and the doublescreens for precision sizing. Sandvik claims that its QA451 is the world’s first triple deck doublescreen, whilst the 50 tonne UH440i cone crushers are specifically aimed at large-scale aggregates producers’ requirements. The result is the production of fractions the quarry’s customers require.
“0/5mm, 5/10mm and 10/20mm is used for concrete and asphalt production,” said Short. “Type 1, secondary and crusher dust is used for road construction. Some of the larger products are also used to build up sites with fill etc.”
He added that one of the main reasons for choosing Sandvik was the fact that the quarry already has the same type of cone crushers on the site which is beneficial for compatibility.
“We also already use two Sandvik drill rigs on site which adds to this,” said Short. “A lot of research was carried out prior to committing to Sandvik, they proved to be a good return in investment. The procurement of a mobile crushing train was a huge commitment and investment which took a lot of research. In the end, these particular machines best suited our requirements.”
In addition to the above, the highway’s section acquired a QI442HS impactor to provide primary and secondary crushing and screening in one unit. The features include a new rotor position and locking device, innovative hammer-locking wedges for quicker removal and fitting, as well as a new wedge removal tool to provide safer installation and removal. This means that it is also able to deliver a wide range of high reduction ratios, superb product shape and outstanding uptime which are essential to the requirements of the island’s authority.
UK trommel screen and accessories manufacturer MDS says its new drum cleaner
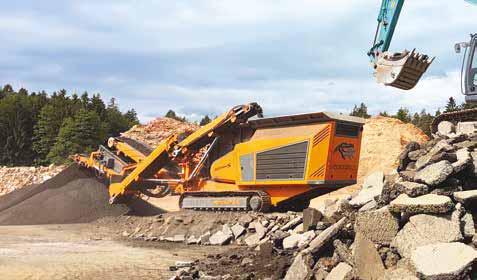
is a “game changer” for the trommel market.
The trommel drum cleaner features a cog wheel-style configuration that meshes with the drum openings and punches out the holes to keep them clean. The cleaner is designed to replace the traditional method of trying to brush trommels clean.
MDS says the drum cleaner is at its happiest when punching out the soils and clays that traditionally blind over scalpers in both quarries and recycling yards.
Luke Jones, quarry manager for Whitelock Developments, near Skipton, North Yorkshire, England, said: “Without the [MDS] drum cleaner we wouldn’t have been able to screen our wet and sticky recycled products. It gives us a competitive advantage in the market when others can’t produce clean aggregate material.”
All the current MDS trommel range can be fitted with the drum cleaner. This includes the tracked range (M412, M413, M515 two or three split, and M518R) and the static range (M615, M620, M720, M820 and M925).
MDS says its business has continued to grow despite the global pandemic, and the company has made a 15,000 square feet extension adjacent to its current factory.
The new unit will provide increased production capability for the existing range in addition to extra capacity for new product introductions such as the M518R and other trommels that are planned for launch in 2021.
ABOVE: Bauhof Deutschlandsberg has deployed a Rockster R1000S impact crusher BELOW: MDS is expanding production capacity for its trommel range
its products has meant the new facility is a necessity to maintain its existing lead times.
Jason Purllant, MDS UK and EU sales manager, commented: “We needed to maintain our target of 6-8 weeks lead time on all products whilst introducing new products into the range.”
MDS CEO Liam Murray added: “We are really excited about the continuing growth of our business globally with new dealers being appointed all around the world.
“We plan to have an open day towards the end of the year to celebrate the opening but also give future and current customers the chance to see first-hand what we do at MDS.”
Austria-based Bauhof Deutschlandsberg is a major player in the country’s provision of high-quality recycled building materials. As part of its recycling activities the company has deployed a Rockster R1000S closed-circuit impact crusher with a screening system & air blower since the beginning of 2020.
In addition to a trommel screen, excavators, loaders and road rollers, Bauhof has also previously used a rented crushing plant which processed around 40,000 tonnes of debris, asphalt and concrete per year.
At the end of 2019, the company decided to replace this rented plant with a new closedcircuit impact crusher R1000S from Rockster.
The company says the crusher has three major assets in terms of guaranteeing high quality of the end-product in one workflow: a screening system for a precisely defined size of end-product; a magnetic separator for removing iron and other metals, and an air blower for separating non-aggregates such as polystyrene, wood, plastic, paper and similar.

“To be honest, we were surprised at how well the Rockster Air Blower works, especially when it comes to recycling debris, it brings a huge increase in efficiency,” says Pistolnig.
Since being deployed in January, the R1000S has already produced 16,000 tonnes of concrete 0/80, 8,000 tonnes of asphalt 0/18, 600 tonnes of wall ballast 0/16 and 500 tonnes of construction debris 0/20.
“We are extremely satisfied with the quality of the end-product,” Pistolnig adds. “The mixture of coarser and fine grain is just right for further use in the concrete mixing plant or on construction sites.” Rockster’s hydrostatic crusher drive is particularly responsible for the sizes of the final product to be precisely adjusted to the desired quality.
Bauhof’s processing capacity is 80,000 tonnes per year - which corresponds to a saved landfill volume of 55,000m³ - and it has a recycling rate of 98%. Its principle expertise
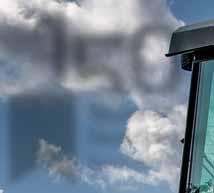
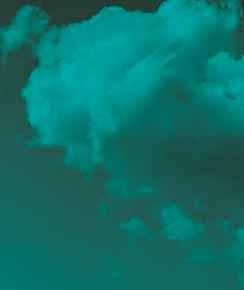
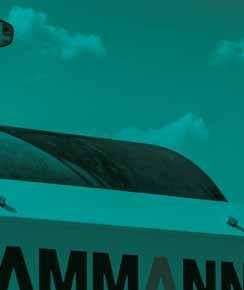
AMMANN ARS SOIL COMPACTORS
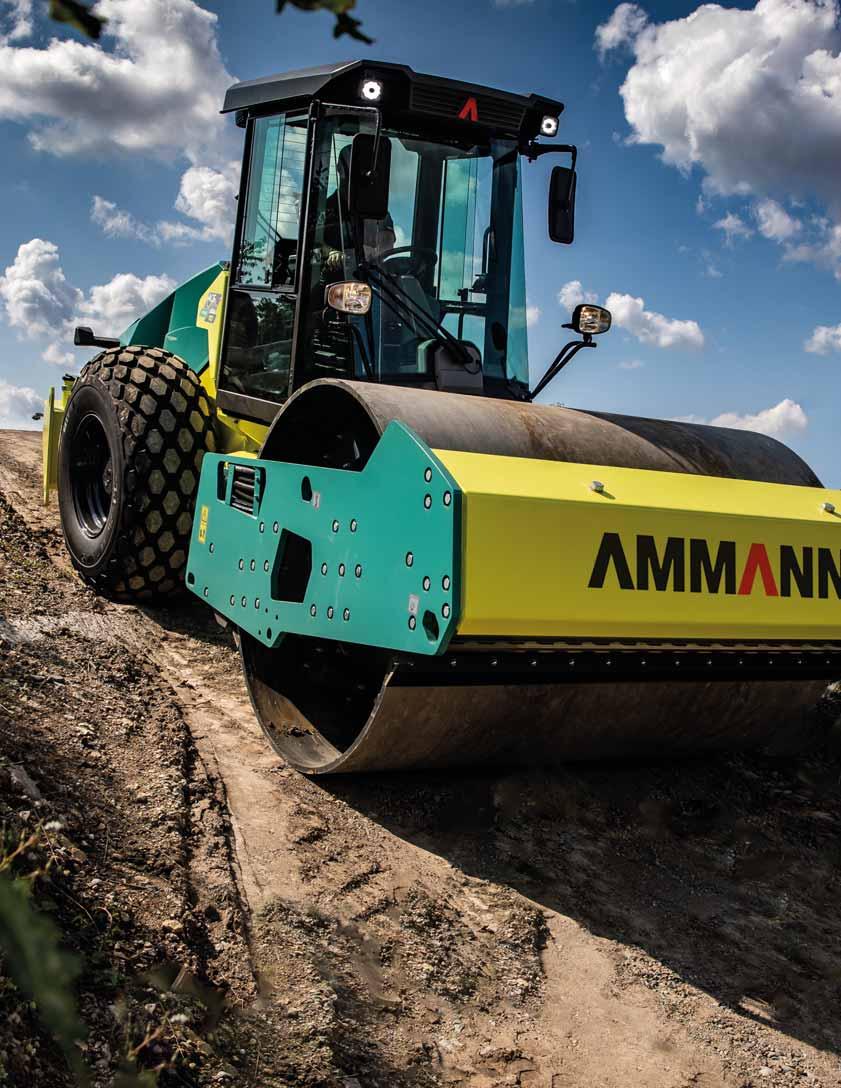
PRODUCTIVE. SUSTAINABLE. COST-EFFECTIVE.
• Multiple vibration frequencies and centrifugal forces enable productivity on a wide range of materials and compaction thicknesses.
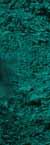

Ammann ARS Soil Compactors utilise advanced technology that meets the latest emissions standards, reduces fuel usage and gives operators valuable data that eliminates unnecessary passes.
That’s just the beginning of the advantages these machines offer.


• The new ECOdrop initiative and new technologies improve efficiency and reduce fuel consumption and the amount of required fluids.
• The compactors are extremely manoeuvrable and stable thanks to the no-rear-axle structure.
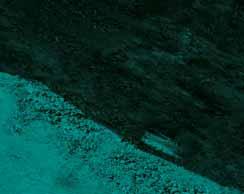
is in building demolition, container services and the recycling of all types of construction debris.
Pistolnig commented: “The management of construction waste is of growing interest for both the construction industry and waste management. Residual building materials that do not end up in a landfill but are returned to the economic cycle as highquality RC [recycled] building materials are an ecological necessity.”
Lars Bräunling, director of product technology at wire screen manufacturer MAJOR, says that self-cleaning screen media offers a number of benefits, including the elimination of pegging and blinding for aggregate and mining operations. However, certain design characteristics, such as limited opening sizes, leave producers with little option on where to employ self-cleaning screen media in their operation. Because of this, self-cleaning screen media is often thought of only as a bottom deck solution.
Bräunling adds that, recognising the opportunity to take the principles of selfcleaning screens a step further, engineers looked for ways to increase durability and provide application-specific customisation for a productivity-boosting solution producers could use on any deck. The result was a new category of screen — high-performance screen media.
In terms of what makes high-performance media different, Bräunling says: “One of the biggest drawbacks of using traditional self-cleaning media on upper decks is that it cannot stand up to the impact and abrasive forces of larger material. High-performance screen media addresses these issues by incorporating enhanced wire and a unique structure to maximize durability and wear life.”
It begins with the wire, according to Bräunling. Wire quality plays an essential role in screen performance, and he says many manufacturers choose their wire based on current market prices, resulting in fluctuating wire quality and inconsistent performance. “Some manufacturers, on the other hand, rely on high-quality wire in their screen media to ensure consistent quality and durability. It offers improved molecular structure over other techniques for optimum tensile strength, hardness and ductility, resulting in the highest quality, longest-lasting wire.”
High-performance screen media’s strategically engineered wires are held together with polyurethane strips, eliminating the need for cross wires with high wear spots. This innovative design maximises open area and extends wear life as much as five times longer than wire alone — even on top decks.
Taking advantage of these design benefits, Bräunling says that producers who employ high-performance screens on the top deck are able to realize the screen media’s payoffs earlier in the screening process, as well.
He adds that stratification is one of the key benefits. “High-performance screen media wires vibrate independently from hook to


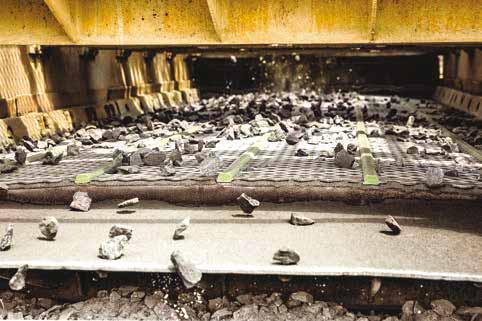
hook under material contact, supplementing vibrations from the screen box with additional frequency to accelerate the stratification process.,” says Bräunling. “This added frequency can be as high as 8,000 to 10,000 cycles per minute — up to 13 times higher than the standard screen box vibration — helping fine material to stratify and pass through the screen faster.”
Optimising stratification at the very start of screening results in faster screening and optimal throughput, according to Bräunling. Greater quantities of fine material pass through the screen media’s open area earlier in the process, which increases the effective capacity of the machine and virtually eliminates carryover. Some aggregate and mining producers have shown as much as a 40% increase in overall production with highperformance screen media.
UK plant hire company P&L Barton - based in Carnforth, Lancashire - has reconfigured its EvoQuip Colt 1000 scalping screen to meet the requirements of the latest project it is involved in. The application has been to produce limestone walling stone for one of its regular clients where space was limited.
P&L Barton set about reconfiguring the Colt 1000 so that both conveyors discharged out the same side into segregated areas, maximising the area available and eliminating double handling.
Richard Barton, plant manager at P&L Barton, commented: “The Colt 1000 is the perfect machine for us due to its flexibility. Being suited to scalping and fine screening and the ability to quickly convert from
3-way to 2-way split and to swap conveyor configurations means it’s suitable for many applications and job sites.”
P&L Barton purchased the Colt 1000 in June 2019 from equipment supplier Blue Central, and since then the machine has been on hire contracts in multiple configurations to suit the required job sites. “We have been able to run the machine in 2-way split on one project then convert it so that mids and fines are discharged on the same side on a really compact site, and in standard set-up on another site,” said Barton. “With the range of media options available I don’t think there is any job she can’t do.”
P&L Barton started out in 1972 when Peter Barton invested in his first digger, a JCB 3C, and set up P Barton Plant Hire. Almost 50 years later the company remains a familyrun business and has evolved and expanded working on a vast array of projects. Its clients include private households and businesses, local councils and large multi-nationals. It provides plant and services on a sub-contract or hire only basis, offering a wide range of services to the quarrying, construction, groundwork, civil engineering, recycling and haulage industries.
The Colt 1000 is able to operate in both heavy-duty scalping and precision-screening applications and is designed to manage the most difficult of materials. Flexibility is enhanced with configurable conveyor options and two-way split conversion. It features an aggressive double deck screen, variable screening angle with numerous screen media options, broad fines conveyor, quick set-up time and tall discharge heights. AB
LEFT: An aerial view of the EvoQuip Colt 1000 scalping screen BELOW: Using high-performance screen media can extend wear life up to five times, according to manufacturer MAJOR
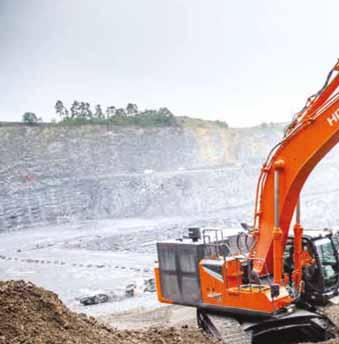
Loads of appeal to quarrying customers

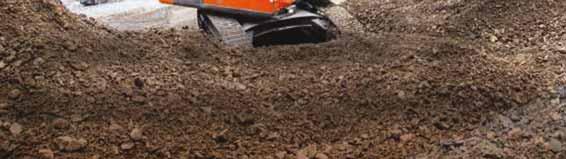
The new Hitachi ZX490CLH-7 crawler excavator is part of the quarrying-suited, next-generation Zaxis-7 range of large excavators
Next-generation, quarrying-suited excavators and high-perfoming wheeled loaders are contributing to an eye-catching global loading machine market. Guy Woodford reports
Hitachi Construction Machinery (Europe) says it is putting owners and operators in complete control with its next generation of Zaxis-7 large excavators. The new ZX490LCH-7, ZX530LCH-7, ZX690LCH-7 and ZX890LCH-7 Stage V-compliant models have an industry-leading cab with firstclass comfort and safety features. Hitachi says their exceptional reliability, efficiency and productivity provide owners with opportunities to increase profits and reduce costs.
An impressive claimed fuel saving of up to 20% in PWR mode (power mode) compared to previous models is said to be achieved by Hitachi’s industry-leading HIOS-V hydraulic system. This also enhances efficiency in the swing, boom lowering and arm bucket rollout. Productivity is further increased by the improved front speed for loading operations, and the increased engine output of the new Zaxis-7 machines contributes to a higher workload.
The fuel efficiency of Zaxis-7 large excavators can also be controlled by using the new ECO gauge, clearly visible on the cab’s multifunctional eight-inch monitor. Besides reducing costs, better fuel economy has a positive impact on environmental performance. The new machines are Stage V-compliant thanks to the combination of the SCR (selective catalytic reduction) system, DOC (diesel oxidation catalyst) and CSF (catalysed soot filter).
A new Hitachi
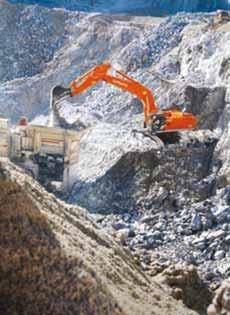
The state-of-the-art, ultra-spacious cab is the perfect working environment. It is said to offer operators ultimate comfort and quality, with reduced noise and vibration levels in the cab, both vital in the quarrying and mining industries.
New features include the synchronised motion of the seat and console – to reduce operator fatigue – and the adjustable console height with three positions to choose from. Easy operation comes from the ergonomic

design of the console and switches, and the hi-res anti-glare screen is also easier to view.
Job-site safety is said by Hitachi to be enhanced by the exceptional view from the Zaxis-7 large excavators. Operators can control their own safety, as well as that of those around them, thanks to the Aerial Angle camera system. It provides a 270° bird’s-eye view, and users can choose from six image options to see the machine’s immediate environment. When working in challenging conditions, new LED work lights and a windscreen wiper with an increased sweeping area further improve visibility.
Tested rigorously at dedicated facilities in Japan, Hitachi Zaxis-7 large machines have been built to last and maximise uptime. New engine parts enhance reliability, oil leakages are less likely, and the durability of the track frame has been improved.
In addition, the undercarriage of the ZX490LCH-7 has robust new components that prevent potential damage. Hitachi says the ZX530LCH-7 has 30% greater traction force than the ZX490LCH-7 and increased steering force – particularly advantageous for manoeuvrability on sites with inclines, such as quarries.
The ZX690LCR-7 and ZX890LCR-7 models are built with reinforced parts that are ideal for the digging and loading of heavy materials. Strengthened to cope with the rigours of mining and quarrying, they provide lower costs over the machine lifetime.
Easy maintenance and cleaning features
ZX890LCH-7 crawler excavator feeding a primary crusher
on all Zaxis-7 large excavators save operators and owners both time and money. The fuel filter is now integrated with the water separator, and the larger radiator improves heat dissipation and is easier to clean.
To enable owners to feel in total control of their fleet and workload, Hitachi’s remotemonitoring systems, Owner’s Site and ConSite, give them access to vital data and tools. Both systems send operational data via GPRS or satellite from the excavator to Global e-Service on a daily basis. ConSite summarises the information in a monthly email, while the ConSite Pocket app shows real-time alerts for any potential issues.
The quality of the engine and hydraulic oil is monitored continuously by a Hitachi innovation. Two sensors detect if the oil quality has deteriorated and data is transmitted to Global e-Service. This novel feature provides customers with peace of mind on the condition of their excavators and reduces maintenance and unscheduled downtime.
“We’re proud to present the latest range of Hitachi large excavators to our European customers,” says Hitachi Construction Machinery (Europe) NV president Makoto Yamazawa.
“Hitachi has continuously improved on previous generation machines to enhance the operator’s experience in the cab, to meet the needs of owners, and to provide support over the life cycle of our machines. By working in partnership with customers, we can help them to create their vision.”
Doosan has launched the new DX800LC-7 Stage V-compliant 80-tonne crawler excavator, the largest excavator model ever manufactured by the company. Coinciding with the launch, Doosan has announced the sale of the first DX800LC-7 in Europe to a customer in Finland.
Driven by the most powerful engine in the 80-tonne class, the DX800LC-7 also has the highest hydraulic flow for this size of machine, providing best-in-class performance, with higher productivity, lower
fuel consumption and smoother controls.
Like all Doosan excavators, much attention has been given to operator comfort and safety. The DX800LC-7 has a new, very spacious operator cab, equipped with ergonomic controls and instrumentation. Special care has been taken to ensure noise is kept to a minimum through enhanced sealing of the engine compartment and extensive use of sound-dampening materials.
All components and assemblies are designed, built and tested to ensure durability. Multi-stage filters and features such as track guards and cylinder guards for the boom and arm, the auto grease system and greased and sealed track links are designed to provide superior reliability and long service life. The DX800LC-7 is easy to maintain, further reducing downtime to a minimum.
The DX800LC-7 excavator is powered by the new stage V version of the well-proven Perkins 2506J diesel engine, providing a high power output of 403 kW (548 HP), more than any other machine in this class. The engine meets Stage V emission regulations by utilising exhaust gas recirculation, selective catalyst reduction, diesel oxidation catalyst
system (D-ECOPOWER+), providing a bestin-class hydraulic flow of 1008 l/min and a high system pressure of 343 bar, together contributing to the best performance in the 80-tonne market.
Doosan’s D-ECOPOWER+ technology utilises an electronic pressure-controlled pump within a closed-centre hydraulic system to optimise productivity and fuel consumption, depending on the mode selected. A closedcentre main control valve minimises pressure loss, while the electric pressure-controlled pump manages and optimises engine power more effectively.
Software is utilised to electronically reproduce the full benefits of an open-centre hydraulic system with very little energy loss. The hydraulic system and engine output are fully optimised and synchronised, further reducing losses within the system.
Improved feedback to the operator through the joystick results in improved machine control and less operator fatigue. The acceleration and deceleration of the excavator workgroup functions are smoother, allowing operators to perform repetitive swinging and digging motions with less jerking movements.
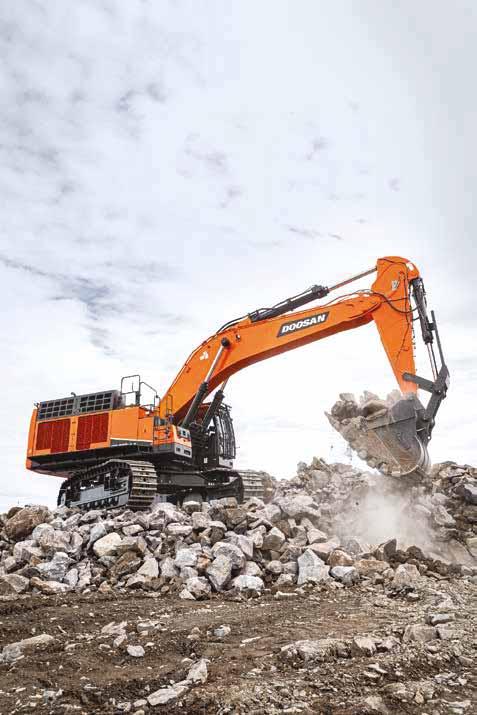
The high output of the engine is combined
The DX800LC-7 is primarily intended to serve customers in mining and quarrying applications, removing overburden and loading large amounts of material into articulated dump trucks or rigid frame trucks. The DX800LC-7 may also be operated on large construction and infrastructure projects, particularly where considerable amounts of material need to be excavated and stockpiled or loaded into trucks to be moved.
Cements and Materials of Mali (CMM), a subsidiary of the Vicat Group, is a specialist in the production and distribution of cement in Mali. To ensure the operation of its up to 800,000 tonnes per year cement plant, the company has substantial human resources, and two Volvo L120Gz wheeled loaders.
Established in 2004 in Bamako, CMM produces high-quality cement at its grinding site in Diago, 35km from Bamako. Today more than 150 people work on site. To ensure the productivity of its activities, the company recently invested in its two Volvo L120Gz wheeled loaders by signing a maintenance contract with the local Volvo dealer, the company SMT.
This acquisition is part of a larger investment project. The purchase of a new crusher in September 2019 required the acquisition of machines responsible for stacking aggregates. Indeed, the loader in place during the construction of the plant was too large and was not as handy as desired. The two Volvo L120Gz wheeled loaders are more versatile and allow faster and easier filling of the crusher. So, these loaders take turns feeding the crusher practically 24 hours a day for better productivity.
One of the decisive points in the purchase by CMM was said to be the speed and efficiency of onsite loader maintenance. Indeed, the role of the loaders is essential to the supply of raw material to the crusher and the continuity of cement production
Doosan has launched the new DX800LC-7 Stage V-compliant 80-tonne crawler excavator

in the factory. Therefore, these cannot be unavailable for too long to carry out routine maintenance.
Didier Kabore, purchasing manager at CMM, said: “The most important point for us was the relationship with the brand, the availability and the speed of maintenance of our machines. SMT was able to meet and exceed our expectations. We now have a technician dedicated to our two Volvo wheeled loaders on our site thanks to our maintenance contract.”
With hot and dry local working conditions, it was crucial to have a loader offering good value for money. Above all, it was necessary to have an after-sales service corresponding to the expectations of the CMM company.
Elhadji Mamadou, director general at SECK, said: “We needed a loader that suited our needs and was of good quality. Several operators take turns in the cabin to supply the crusher. So, we had to invest in a reliable brand with a good offer of maintenance and monitoring.”
After several months of running the two Volvo L120Gz wheeled loaders on the cement plant site, the CMM company is satisfied with its investment, both in the relationship it maintains with SMT and in the after-sales service and the quality of its new loaders.
Turkish construction and quarrying machine manufacturer Hidromek exhibited a wide range of its innovative models at the NordBau 2020 Fair in Neumunster, Germany.
Staged 9-12 September 2020, NordBau Fair is one of Europe’s leading construction and quarrying equipment exhibitions. This year, it opened its doors for the 65th time. Last year, 836 exhibitors from 13 countries participated in the fair, which welcomed 62,600 visitors.
Attending NordBau Fair for the third time, Hidromek displayed some of its new H4 Series hydraulic excavators - including the quarrying-suited HMK 310 LC. Other on-show models will include the HMK 640 WL wheeled loader.
Offering high performance, Hidromek’s new H4 Series excavators stand out with their operating speed. By changing the diameter of hydraulic cylinders, tubes and bars, H4 series units have a higher working speed. Hidromek says the model range’s power boost and their maximum hydraulic system pressure are improved. These improvements are said to have led to produce faster, more productive and more efficient machines. Customerearning potential is more now than ever with H4 Series, says Hidromek, as the units process more material with less fuel.

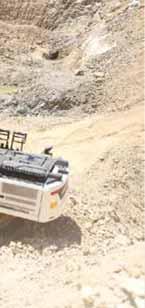
H4 Series excavators have an electronic system that can ascertain the condition of the machine and co-ordinate its integration with other equipment. H4 model cabins are designed and built to offer maximum safety and durability under ROPS & FOPS standards. The red handles and warning labels on the new series excavators are said to be made to increase the operator’s safety.
A popular machine in quarry and mining operations, concrete plants and industrial applications, Hidromek’s HMK 640 WL heavy-duty wheeled loader has a 26.3tonne operating weight and a 4.2m³ bucket capacity. It also features a 239kW Mercedes engine which, along with 1600Nm of torque, offers users high loading capacity at low fuel consumption, as well as short cycle time.
The HMK 640 WL is said to supply high breakout force and excellent control capability. The machine also offers durability and efficiency for many years with its axles and components used explicitly for highdemanding working conditions. With its ergonomic operator cabin with ROPS / FOPS certificates, comfort and increased security are priorities. The HMK 640 WL is also said to offer easy serviceability with its 35° tilting cabin feature. The model has won international design awards such as the Red Dot Best of the Best Award.
Hidromek aims to strengthen its place in the global industry by expanding its dealer network and product range while also increasing production. Combining its 42 years of production experience in the sector with its design and R&D power, Hidromek has more than 45,000 machines operating in more than 100 countries on six continents.
Hidromek has nine dealers in Germany. Through Hidromek West in Spain, Hidromek manages its dealers and sales and after-sales in Europe. Hidromek also performs these activities with Hidromek Rus in Russia, Hidromek Construction Equipment Thailand (HCE) in Thailand and Hidromek Japan in Japan. Hidromek says it attaches great importance to aftersales services; in this sense, it offers spare parts and service to its customers with its authorised dealers in more than 80 countries and more than 100 overseas service points. AB
One of two new Volvo L120Gz wheeled loaders purchased by Cements and Materials of Mali (CMM)
Hidromek’s HMK 310 LC crawler excavator loading a truck in a quarry. The model was among those exhibited by the Turkish manufacturer at NordBau 2020
Hardy hauling
A new Doosan articulated haul truck is proving a reliable workhorse for a Bavarian clay and loam pit operator.
Clay and loam pits are tough workplaces for machines, where the access roads are often poor and can only be travelled by vehicles that have excellent rough terrain capabilities and enormous power. This is especially the case at the clay and loam pit run by Creaton in LangenreichenButtenwiesen in Bavaria, southern Germany.
To overcome these tough conditions and ensure the efficient and safe transport of materials at all times, Creaton relies on articulated dump trucks (ADTs) from Doosan. The latest addition to the Creaton fleet is a new Doosan DA45-7 ADT, powered by the new Scania Stage V DC13 13-litre diesel engine, purchased from Süddeutsche Baumaschinen and its distribution partner, Nestel Baumaschinen.
Although the routes in and out of the Langenreichen-Buttenwiesen clay pit are not too long, at around 500 metres in length, the terrain is extremely challenging, especially in wet conditions. Soft ground and ascents and descents with gradients of up to 25 per cent are all par for the course. One thing above all counts in these conditions, and that is rough terrain capability. And Doosan ADTs, such as the new Doosan DA45-7 model, are said by the manufacturer to offer this like no other machines on the market.
Like all Doosan ADTs, the new DA45-7 features an articulation hinge positioned behind the turning ring to provide equal weight distribution to the front axle even during maximum steer articulation. This, combined with a free-swinging rear tandem bogie, ensures equal distribution of weight to each wheel and guarantees permanent six-wheel contact and drive for equal power distribution and excellent performance particularly on difficult terrains such as soft ground, uneven surfaces, very steep slopes, tight turns or a combination of all of these problematic conditions.
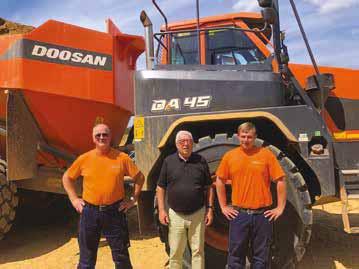
Combined with its high engine power of 368kW, the DA45-7 efficiently manages to transport its 41-tonne payload of material up the steep inclines to the intermediate storage area at the pit, even in wet and extremely slippery conditions.
Quarry manager Roland Kanefzky said: “The DA45-7 has the best off-road capability of all the brands we tested. The previous generation of this model, the DA40-5, has been in service with us for five years and has been very impressive.”
The Creaton quarry’s DA45-7 driver, Christoph Schimpp, added: “Thanks to the high engine power and the eight-speed transmission, the DA45-7 offers great power, even when fully loaded. The new self-
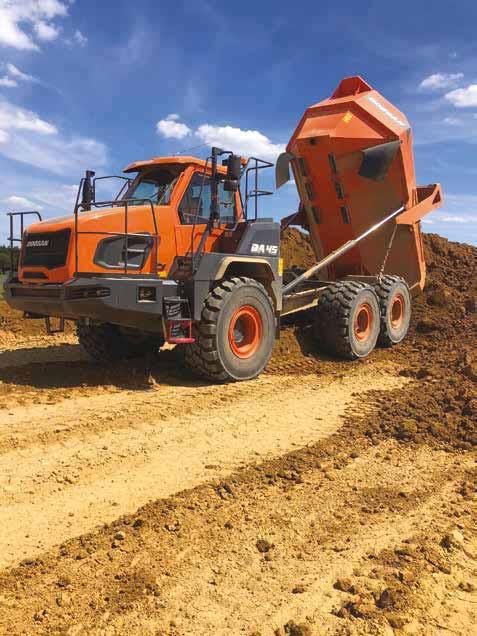
adjusting front axle has also significantly improved driving comfort compared to the DA40-5.”
Creaton has equipped the DA45-7 with some special features for use in clay and loam pits. For example, the wide Michelin 875/65 R29 XADN tyres with their low ground pressure further enhance comfort for the driver in the ADT. The Grammer adjustable, suspended operator seat, an improved layout for the display which is easier to use even for tired eyes and the
clay and loam pit at Creaton, a member of the
have scored lots of points in this area with its exceptionally low downtime. “The ADTs from Doosan have proved to be extremely robust, and if there is an issue, we can always rely on the very fast, good quality service provided by Süddeutsche Bau and Nestel Baumaschinen and on a fast supply of spare parts,” Kanefzky emphasised.
Süddeutsche Baumaschinen, founded in 1991, with its distribution partner, Nestel Baumaschinen, based in Krauchenwies, has been a Doosan dealer since 2002. From its headquarters in Neu-Ulm, the company has around 120 employees and offers its customers a comprehensive range of services for the sale, rental and servicing of construction machinery. Also, there is an engineering shop and services available in the field of processing technology. The company has 12 customer service vehicles at its six branches. AB
TOP: The new Doosan DA45-7 at work at Creaton’s clay and loam pit in Langenreichen-Buttenwiesen, Bavaria ABOVE: From left to right: Roland Kanefzky, Creaton group manager; Hans-Jörg Nestel, Nestel Baumaschinen; and Christoph Schimpp
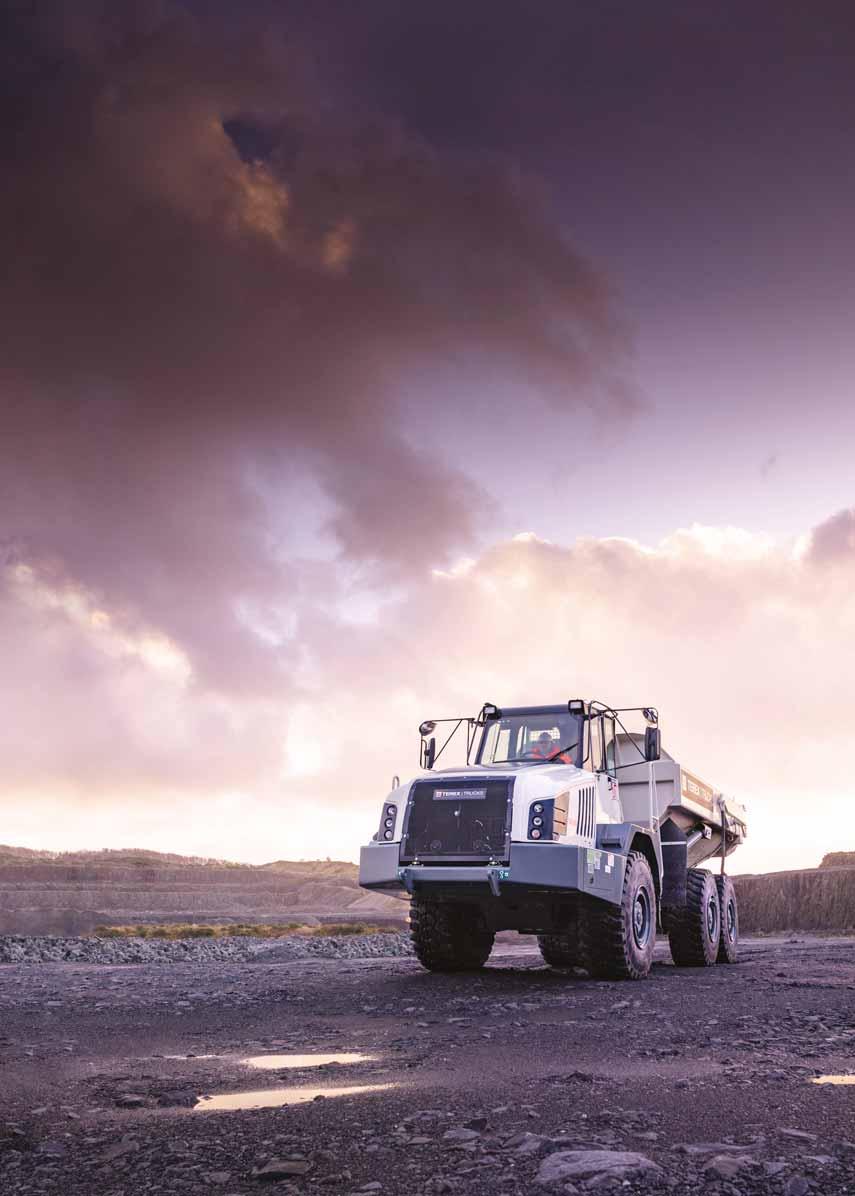
Epiroc’s PowerROC D55 is said to provide both high performance and low total cost of ownership for drilling 90–165 mm holes
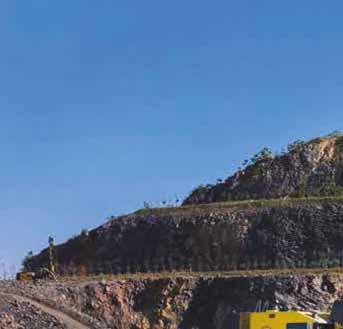
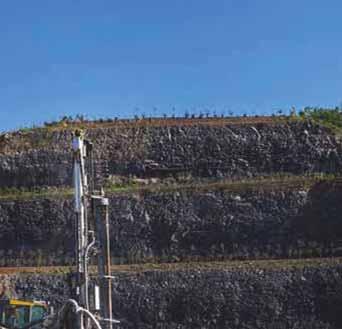
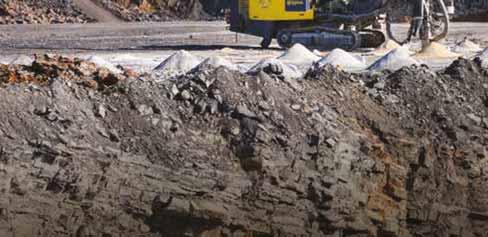
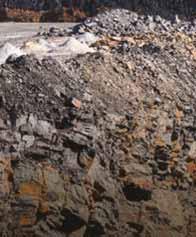
Highly productive drill rigs, top hammers and breakers

Premium drill rigs, top hammers and breakers are proving in demand on quarry and surface mine sites globally, with new supporting products also coming on to the market.
Guy Woodford reports
Epiroc’s PowerROC D55 DTH (downthe-hole) surface drill rig is said to be unlocking the next level of productivity and efficiency at a limestone mine in Nanjing, China.
Following a new standard of green operations in the mining and construction industry in China, many small mine owners and contractors have quickly disappeared from the market along with fleets of outdated equipment. Nanjing Anjite Mining Engineering Co., Ltd. (commonly referred to as Anjite) is a surface drilling contractor established back in 1972 which has steadily expanded its business from Nanjing to other regions of China.
Anjite was awarded the highest qualification for Green Mining and Master Blasting Company in Jiangsu province, successfully cooperating with the public security bureau for ammunition destruction, and it is now a key player in China’s blasting industry.
The Baota Hill Mine site is located northwest of Nanjing city, just 40km away from downtown. Although the limestone mine is situated close to residential areas, no air pollution affects local residents. When entering the worksite, it looks more like a lush garden than a mine, with green trees and plants on both sides of the open-pit ramp. Finished exploitation benches are
located a distance away and are flat and green, which contrasts typical perceptions of open-pit mining or quarrying.
Anjite’s capabilities in mining and handling blasting tasks rely on the use of a drill rig fleet from Epiroc, acquired from 2008 onward. This includes the FlexiROC T35, FlexiROC D50 and PowerROC D45. The limestone quarry has a production capacity of up to 14 million tons per year. The high productivity and good working environment, with minimised dust, has been achieved thanks to the introduction of two PowerROC D55 drill rigs, products that were designed
and manufactured in Nanjing.
The PowerROC D55 units work in favourable conditions at an altitude of 250m in a normal temperature, limestone mine. The drill rigs are said to have demonstrated outstanding performance and reliability with low fuel consumption of 35 litres per hour, as well as an availability of up to 98% per year. Drilling 140mm holes in rock conditions of 60-80MPa, the PowerROC D55 achieves a maximum penetration rate of 40 metres per hour to ensure the high annual productivity. The rigs work on +-20m high benches using a drilling pattern of 4x6m.
An operator changing a filter on a PowerROC D55 DTH surface drill rig at Baota Hill Mine
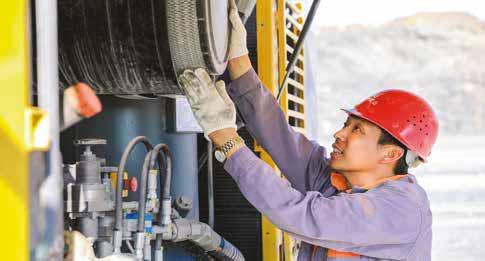
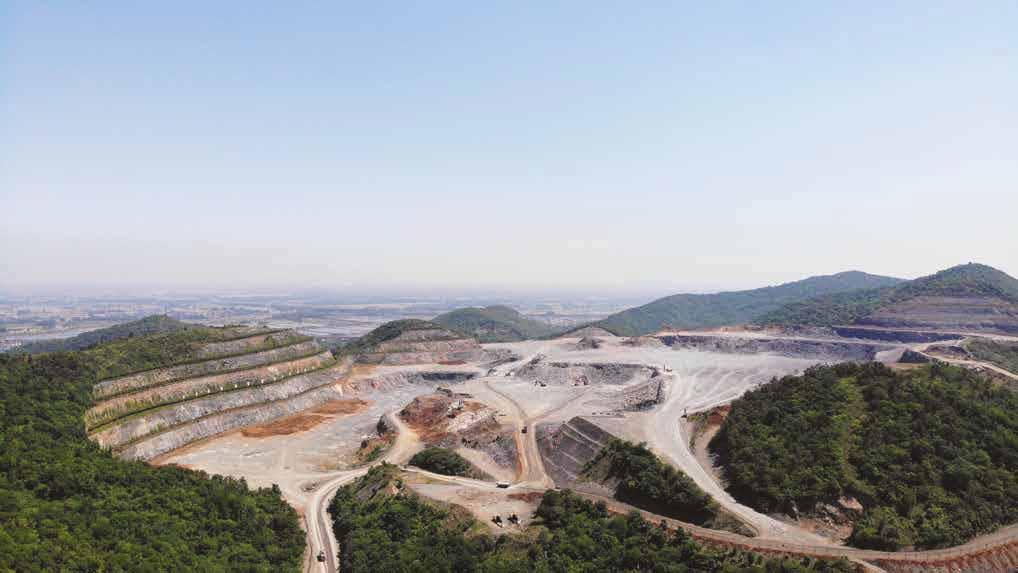
The PowerROC D55, a down-the-hole (DTH) surface drill rig, provides both high performance and low total cost of ownership for drilling 90–165mm holes, as Wei wen Xu, business line manager at Epiroc’s product company in Nanjing, points out. “The straightforward design of PowerROC D55 is easy to operate and maintain which is very appreciated by customers. Other reliable components of proven Epiroc technology enable high availability, ensuring the high productivity that customers need to expand their business. The RHS and the down-thehole drilling method help to drill straight holes with very good quality,” Wei wen Xu adds. This assessment is echoed by Sheng Wang, general manager at Anjite: “We trust the performance of Epiroc-branded machines as Epiroc is a leading company in the mining and construction industry. The strong cooperation between us began with our previous general manager, and we continue to order drill rigs due to their reputation for excellent reliability ever since.”
“Thanks to the dust collection system, Epiroc products have helped us achieve the Green Mine Star and other awards of distinction from the government,” Wang continues. “We are the only company in Jiangsu Province that promotes the electric digital detonator in domestic China, which together with Epiroc equipment has contributed to our Green Mine distinction. We hope the cooperation will continue to advance our goals for sustainable productivity.”
Following the successful deployment, there are now three PowerROC D55 units in
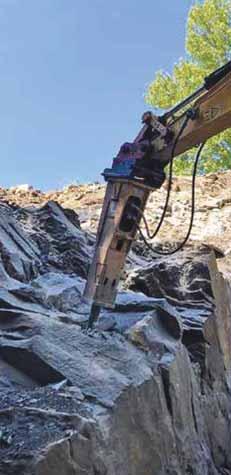
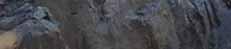
daily operation at Baota Hill Mine. Another hydraulic surface drill rig, the PowerROC D45, is being used to help Anjite complete a national water conservancy project on the Qinhuai river for the state waterways which requires significant capacity and time-sensitivity. “The outstanding availability surprised us as the drill rigs can work 4,800 engine hours per year, with three shifts per day. That is why we call it the workhorse on site,” says Zhoujun Jiang, site equipment chief at Anjite. He continues: “I appreciate the ergonomic design of the cabin with FOPS and ROPS certification, which protects operators from injuries if the equipment rolls over on the bench. The drill rig is easy to operate and maintain due to its straightforward design. And the rigs can work twenty hours per day with regular maintenance twelve times a year.”
Thanks to the partnership and continued use of Epiroc products, Anjite stands ready to expand its footprint across China with cutting-edge productivity and a green mine profile that sets a new benchmark for future operations.
The Lange e.K. quarry and sawmill in Sprockhövel, North Rhine-Westphalia, Germany, features a rather compact Ruhr sandstone, even harder than most granites. The site’s material coupled with a need to boost production levels led Thomas Lange, owner of Lange e.K., to purchase an HP 2500 FS (fuel saving) hydraulic hammer.
“We decided to switch to the HP 2500 FS and mount it on a JCB 220 XLC excavator. Our choice was guided by the fact that the HP 2500 FS was able to increase our production
Baota Hill Mine in Nanjing
An Indeco HP 2500 FS hydraulic hammer is being used at Lange e.K.’s quarry and sawmill in Sprockhövel to help process its tough Ruhr sandstone
by 30%, as it then demonstrated in the quarry.
“It’s already quite clear to us that the promises Indeco Deutschland made to us have been more than fulfilled,” said Lange. He added: “The excellent results we achieved soon convinced us of the Indeco hydraulic hammer’s superior technology.”
“As so many users around the globe have been saying, Indeco breakers have an excellent ratio between energy input and energy output and consequently optimum efficiency,” said a spokesperson for Indeco Deutschland.
All Indeco top hammers are installed with the ABF (anti-blank firing) system, Indeco’s patented technology that considerably improves the performance and durability of the breakers. In addition to a hydraulic system with improved efficiency, the HP series displays the FS (fuel saving) mark, indicating that the top hammer needs less hydraulic power to operate, resulting in a claimed significant reduction in the carrier machine’s rpm and fuel savings of up to 20%.
While delivering consistently excellent performance and maximum productivity, Indeco top hammers are said by the company to require less oil per minute and lower operating pressures than similar size and weight hammers made by other manufacturers.
Sandvik Rock Tools is launching a new product for the brand’s bench drilling top hammer customers. The ‘Guide Adapter’ is said to enable customers to reduce hole deviation in challenging conditions by up to 50%, while also achieving considerable cost savings.
Significant hole deviation of 8% or more can pose problems for many bench drilling companies that operate in challenging ground conditions such as bad and soft rock, as well as deep overburden. This often results in reduced productivity, safety risks and increased tool wear.
“We are very happy to be able to offer the Guide Adapter to customers facing deviation problems in their day-to-day bench drilling operations. The Guide Adapter helps them
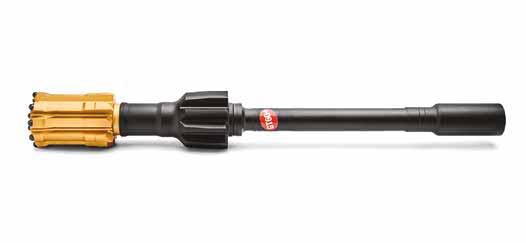
to increase the service life of their drill string and also reduce the number of drilled holes, as well as the amount of blasting needed,” says Fredrik Björk, product manager Top Hammer Surface Tools, Rock Tools Division, Sandvik Mining and Rock Technology.
Sandvik’s new Guide Adapter enables customers to achieve greater productivity, longer tool service life and improved safety. Ultimately, this can also lead to lower total operational costs.
“We have conducted in-depth testing with our customers around the world and the results really do speak for themselves. By using the Sandvik Guide Adapter, our customers achieved a hole deviation between 3% to 5% - a reduction by up to 50% - and also increased the service life of their rock tools by up to 40%. This truly has an effect on both productivity and in turn, profitability”, says Björk.
The Guide Adapter is now available for T51 and GT60 Top Hammer threads in different diameters.
Doosan Infracore Europe has launched the new HB-series hydraulic breaker range for the European market.
The new range of five HB-series breakers provides a novel concept with high performance and a simplified design, specifically optimized and fully certified for Doosan excavators with carrier weights
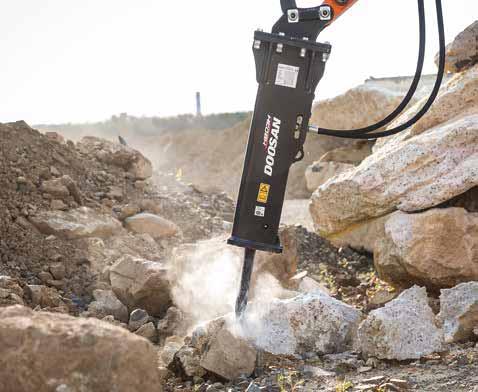
from 1.2 to 15 tonnes. As a result, Doosan HB breakers are said to offer the highest possible productivity, whether the operator is demolishing concrete or breaking rocks.
The high quality of the breakers is backed by a claimed industry-leading two-year warranty and they are available at costeffective prices, providing customer benefits in terms of total cost of ownership. According to Doosan, all these features together are aimed at greatly exceeding customer expectations for hydraulic breakers.
In common with all Doosan machines and attachments, the new Doosan breakers are covered by the outstanding Doosan dealer service network and Doosan product specialists, providing fully comprehensive ‘one-stop service’ support.
The service life of the breakers is extended through the adoption of an advanced heat treatment process and quality proven materials for key components including the cylinder and piston. The energy of the piston stroke is accumulated by charged nitrogen gas and the breakers use an inward valve system with a simple structure and fewer inner parts.
A urethane damper prevents vibration that might damage the carrier and improves operator comfort. The front head supports the breaker and assemblies with bushing, which buffers the shock from the tool. The low noise housing is ideal for working in urban zones, where noise levels must be controlled or where local regulation may require silenced breakers.
The HB-series range offers five hydraulic breaker models - the HB03, HB04, HB06, HB08 and HB15 - for use on Doosan miniexcavators and Doosan crawler and wheeled excavators. Ideally suited for demolition work, the Doosan breaker range is also intended for general construction, rental, quarrying and mining applications.
The range begins with the HB03 breaker, which is suitable for use on the Doosan DX17z 1.7-tonne and DX19 1.9-tonne mini excavators. Next in the range is the HB04 model for the DX27z 2.7-tonne and DX35z 3.5-tonne mini excavators. The third model in the range - the HB06 breaker - is designed for use on the 6-tonne Doosan DX57W-5 wheeled excavator and DX62R-3 and DX63-3 miniexcavators.
The fourth model in the range is the HB08 breaker for use with the Doosan DX85-3 8-tonne mini-excavator. The top-of-the-range HB15 hydraulic breaker is designed for use with the Doosan DX140LC-5, DX140LCR-5 and DX160LC-5 crawler excavators and the Doosan DX140W-5, DX160W-5 and DX165W-5 wheeled excavators.AB
Sandvik Rock Tools says its new Guide Adapter helps customers to increase the service life of their drill string and reduce the number of drilled holes
A Doosan HB03 hydraulic breaker, part of a new five-strong HB series
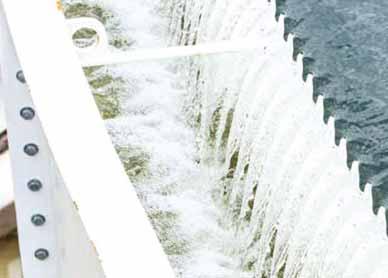
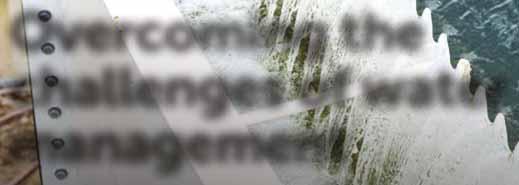
Quarries and materials processors face increasing regulations governing the responsible use and management of water


Overcoming the challenges of water management
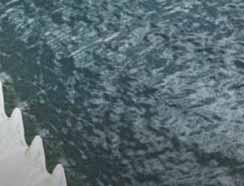
Water recycling makes sense both from an environmental perspective and in terms of meeting increasing legislative requirements. Liam McLoughlin reports
Innovations in the washing sector are supporting quarry operators and materials processors alike to overcome the challenges stemming from water management; cost-based, efficiency, sustainability and regulatory.
Prominent among these is the modular wet processing equipment from CDE. The Northern Ireland-based company says its solutions can contribute to the easing of water scarcity issues arising from the materials processing industry’s consumption of water resources, significantly improving water efficiency, and better wastewater management practices. It adds that developing technological solutions to tackle these mounting challenges is paramount for many materials processors seeking to boost the profitability of their operation by minimising the consumption of costly water resources.
Stefan Hunger, CDE regional manager for Europe & Russia, and Daniel Webber, CDE regional manager for Australasia, report increasing regulations governing the responsible use and management of water in the industry, including those aimed at protecting marine environments and water sources from pollution and over-abstraction.
Hunger says: “It’s important to acknowledge that water is renewable when its usage is regulated and managed responsibly, but it is also a finite resource. Not only does water recycling make sense from a global environmental perspective backed up by increasingly stringent legislative requirements, but it also ticks all the right
boxes in terms of return on investment.”
In Europe, there are approximately 26,000 aggregates sites, nearly 60% of which are involved in materials washing activities.
Webber explains that the Australian mining industry has adapted to more regulations surrounding its water usage than most other industries.
“Each stage of the mining cycle requires permits, including, among other utilities, water permits. The impact of operation is also subject to strenuous environmental assessments to evaluate the management and use of water resources and the processes that will be employed to prevent the contamination of groundwater.”
In terms of sector, agriculture remains the largest user of water in Australia, accounting for almost 70% of total water footprint. Industry, however, including mining and quarrying, is on the rise at a time when water storage levels hit a 10-year low in 2019/20.
Webber continues: “Pressure on Australia’s water resources is mounting on account of population growth. With this comes greater demand within the agricultural and industrial sectors to support such growth and urbanisation. We’re finding mine and quarry operators are in effect competing against the needs of urban populations, farming, and the environment in terms of water demand which is why governments are

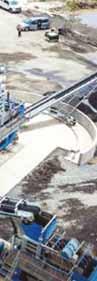
CDE’s AquaCycle water management solution
taking greater action to regulate its use.”
CDE says it is therefore increasingly crucial for materials processors to invest in an effective water management strategy that ensures a steady supply of clean water to their plants through cost-effective means.
While laws governing water vary around the world, it is a resource that is essential to the extractive industries and is therefore increasingly under the water management microscope.
Earlier this year, in the United States, the Environmental Protection Agency (EPA), provided further clarification to its Waters of the United States (WOTUS) rule which aligns with the Clean Water Act.
Darren Eastwood, CDE business development director for North America, explains: “Confusion caused by the 2015 WOTUS rule resulted in many aggregates businesses across North America incurring high costs due to the uncertainty around when federal permits were required. Its reclarification provides a clear regulatory framework to which aggregates producers can align. Its new definition clarifies that pits and water treatment basins are not subject to additional federal regulation.”
Water as a resource delivers economic value to a range of industries. Within the extractive industries, the value of materials significantly increases when washed, but wet processing in mining and quarrying operations is dependent on water availability
and processing plant efficiency.
Hunger comments that customers do want to wash: “But footprint, particularly in urban settings, is prohibitive. This is why CDE has invested significant resources into the design and development of compact and modular equipment that can be commissioned in urban areas while also offering the ability for future migration of the plant to where opportunities lie.”
Webber adds: “More often it’s water availability and access that prevents producers from getting into the washing business in the first place. That, and the uncertainty around typical top-up water requirements which, in the case of CDE water management solutions, are very low. The focus is on recycling and recirculating as much water as possible through the system.”
Bruno Paladino, CDE regional manager for Latin America, says the combination of regulatory and environmental considerations with economic factors presents a significant challenge for operators washing sand and aggregates.
“Water supply is a key determining factor when assessing the viability of a new project or when considering expanding operations at an existing site,” says Paladino. “Insufficient water supply, particularly in arid regions, will drive up operational expenditure costs significantly in an industry where energy prices already represent 20% of these costs due to the investment in water infrastructure

A LONG WAY TOGETHER
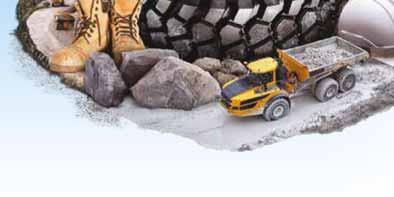
to ensure an adequate supply of clean water is pumped into the plant.”
In the Americas, customers using settling ponds to recycle water often encounter significant operational and logistical challenges.
Eastwood explains: “These require constant maintenance as they accumulate sludge, silt, and other solids that must settle and separate from the water before its removal. Not only do these limit the water storage capacity of the pond, but they incur significant maintenance costs. Further still, the limitations of settling pond systems often result in the loss of valuable fines, one of the key considerations in the design of CDE water management solutions.”
Paladino stresses the importance of safe water management in all regions but highlights the urgent relevance of such practices in Latin America.
“Over the past few years, mines in Latin America are looking for new and sustainable ways to continue their exploration, ways that are less impactful on the environment and surrounding communities. The use of water is a key factor, as is overall footprint and energy usage. CDE’s modular plant design with water recycling system is the perfect fit to help mines meet these new challenges.”
CDE says it consistently invests in research and development to enhance the capabilities of its premier water recycling and management equipment. At the forefront of its
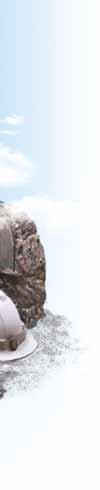
EARTHMAX SR 41
o matter how challenging your needs, EARTHMAX No 41 is your best ally when it comes to operations SR at require extraordinary traction. Thanks to its All th eel radial structure and the special block pattern, St ARTHMAX SR 41 provides excellent resistance EA ainst punctures and an extended service life. In aga dition to long working hours without downtime, add e tyre ensures extraordinary comfort. th ARTHMAX SR 41 is BKT’s response to withstand EA e toughest operating conditions in haulage, th ading and dozing applications. lo
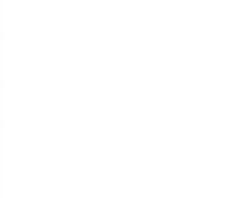
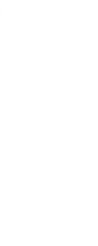
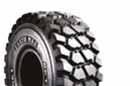
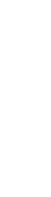
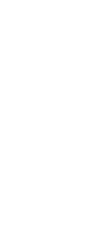
water recycling systems is the AquaCycle, a single, compact unit suited to high and low tonnages across many markets.
AquaCycle is designed to accelerate return on investment by maximising production efficiency, minimising the loss of valuable fines, and reducing water and energy costs.
According to Dennis Zink, global product manager at US-based water management solutions provider McLanahan, filter presses provide the best solution for the issue of settling pond elimination.
He adds that several types of dewatering equipment are available to separate solids and liquid in slurries to reduce or eliminate settling ponds, but one is better for overall tailings and water management.
The aggregate and mineral industries have historically used the simplest and cheapest dewatering technology to manage waste slurry tailings. These old methods include dumping directly into streams, rivers and lakes or using mining surfaces or underground quarries/pits for disposal.
For a number of decades these industries have been pressured to eliminate older ways of waste dumping and look for more efficient waste management technologies.
Initial improvement in tailings management technology involved creating ponds or large impoundment dams to hold the waste slurry for the life of the quarry or mine.
Over the past 10 years or more, pressures to improve tailings management practices have increased further due to a number of factors. Zink states that these include stricter environmental regulations, rising operational costs, higher waste handling costs, increased water conservation requirements, catastrophic impoundment failures, the need for better risk mitigation, and physical space limitations for operational expansion.
Zink adds that leaders in the aggregate and mineral industries have started evaluating and investing in more efficient, cost-effective systems to dewater tailings. The systems include: ultra-fines separation, slurry thickening and slurry dewatering equipment technologies.
The UFR (ultra fines recovery) and thickener equipment technologies separate and concentrate the waste materials, while the dewatering equipment recovers additional water from the waste stream and creates nearly dry solids.
The types of competing dewatering equipment used in the aggregate and mineral industries today include plate filter presses, belt filter presses and centrifuges.
Centrifuge dewatering is a high-speed process that uses the force from the rapid rotation of a cylindrical bowl to separate wastewater solids from liquid.
Zink says: “These dewatering devices work best with material that is more easily dewatered, has a larger particle size distribution and/or a low clay content, though they generally are not going to be as efficient as a filter press since they cannot generate the high-pressure dewatering forces of the latter.”
Centrifuges operate as continuous feed units that remove solids by a scroll conveyor and discharge liquid over the weir. Centrifuge equipment has high up-front investment cost and high operating cost. It is built to tight mechanical design specification to operate efficiently at very high rotational speeds. Operating costs are high due to significant electrical power requirements, expensive replacement parts and the need to use dewatering chemicals.
Belt filter presses are another type of equipment used to remove water from waste slurries to produce a non-liquid material referred to as a “cake”. In a belt filter press, the waste slurry is forced between two tensioned porous belts. As the belts pass over and under rollers of various diameters, the liquid is squeezed out of slurry while the solid cake material is retained between the belts.
There are many designs of belt filtration processes, but all incorporate some basic features: polymer conditioning zone, gravity drainage zones, low-pressure squeezing zone, and high-pressure squeezing zones. Advanced designs provide a large filtration area, additional rollers, and variable belt speeds that can increase cake solids by 5%.
Belt filter presses have low to medium initial capital cost, with a smaller footprint for installation. Operating costs tend to be high due to the need for a full-time operator and the use of chemical dewatering aids. Belt presses have a reputation of requiring frequent belt washing and are very sensitive to process variations.

SOME THINK THAT TRANSPORTING RAW MATERIALS REQUIRES A COMPLEX INFRASTRUCTURE. WE THINK DIFFERENT.
Recessed plate filter presses are used to create a dewatered cake material by separating the liquid and solid materials in waste slurries. These filter presses are among the oldest types of dewatering devices and are commonly used in aggregate and mineral processing waste slurry applications.
The up-front investment for a plate filter press can be high due to the size of the equipment and required support structure.
Depending on the type and amount of material being dewatered, McLanahan’s Zink states that modern filter press equipment can be very big and require a large space for installation and operation.
Plate filter press operating costs are low due to the requirement of only a part-time operator, lower wear parts cost and typically no need for chemical dewatering aids.
Because the slurry material is captured completely between the filter plates, very high dewatering pressures (up to 225 psi or higher) can be applied to the slurry. The high dewatering pressures produce the highest cake solids concentration possible of any mechanical dewatering equipment.
Plate filter presses can also employ a second type of plate called a membrane plate. In this case, the plate has a flexible membrane surface made from polypropylene or other synthetic flexible material such as hard rubber. The membrane can be thermally fused to the concave plate core, or the synthetic membrane’s edge can be embedded into the concave plate core in a small channel machined in the plate surfaces.
The same initial process is used in a membrane plate press, with a high-pressure slurry pump feeding the press to fill and dewater as much slurry as possible.
After the slurry feed pump is stopped and while the filter plates are still clamped together, the membrane surfaces are expanded using compressed air or water. This inflated membrane compresses the cake material, removing additional moisture to the lowest possible levels.
Zink says that no other dewatering process has shown to be more efficient at removing liquid from slurries as the plate filter press. He adds that additional benefits of plate filter presses include: the highest amount of recovered water, driest cakes, lowest operating cost, lower waste handling
Thickeners such as those from McLanahan can enable producers to recover up to 90% of their water for reuse
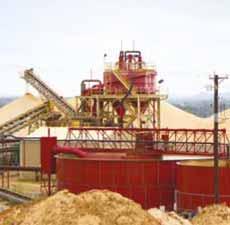
cost, less water hauled, and most stable solid material generated
“Because of these advantages and the high efficiency of the plate filter press, it is the best choice of equipment to eliminate settling ponds,” Zink adds.
Northern Ireland-based Terex Washing Systems (TWS) has a product portfolio that includes Terex AquaClear Water Management Solutions. Barry McMenamin, TWS business line director, highlighted the benefits of the water management solutions, commenting: “A lot of our customers have a need for water management, which is a continually growing sector given the way environmental legislation is evolving in certain regions.”
TWS water management portfolio includes clarifying tanks, flocculent dosing systems, filter presses and all associated equipment to provide a one-stop solution. With installations globally the company says it is leading the way in providing ‘End to End Washing Solutions’ from a single source supplier.
Water management solutions vary in size and complexity, but generally comprise three stages; flocculation, sludge thickening, and de-watering of solids via a filter press.
For stages one and two TWS offers a wide range of AquaClear floc dosing units paired with a choice of deep cone thickener, or low-level rake thickener. The choice of thickener is dependent on the application and the plant layout, according to TWS product manager Mark Follis.
“The deep cone thickeners offer a fantastic simple solution for sludge thickening,” says Follis, “with a small footprint, no moving parts, and the ability to use the natural pressure in the tank to achieve higher sludge concentrations over 50% solids, ideal for discharge directly to a sludge pond.”
For many applications TWS says stage one and two is the complete water management solution, with the AquaClear thickener providing 80% water recovery back to the main washing process, and the thickened sludge only being discharged to settling ponds, thus significantly reducing the area required for ponds or sludge storage.
An example of this was the recent TWS installation at Grahams Concrete in Queensland, Australia, where the DC140 deep cone thickener can be seen working alongside the AggreSand 165.
This natural sand and gravel application operating at 100tph feed rate requires only 30-40m cubed/hr top-up water to keep the system running, while flocculant usage is optimised using the AquaClear DCU (dosing control unit) which continually monitors sludge settlement rates to ensure the correct dose of floc is provided to the plant.
Adding stage three, TWS says that its AquaClear filter press maximises water recovery by creating a completely closedloop system, where sludge is dewatered under high pressure and expelled as solid filter cakes with a dry solids content of up to 85%. AB
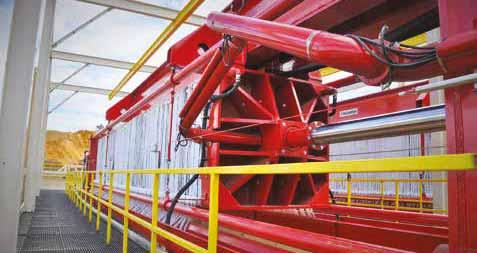

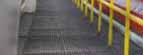



Filter presses are the best way of settling pond elimination, according to McLanahan
The TWS AquaClear filter press
The extremely short cutting units, combined with their sturdy and tough housing, make quick work of removing rock
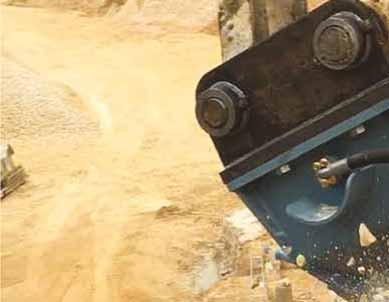
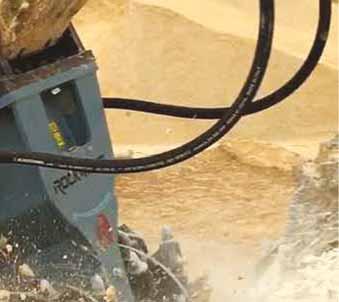

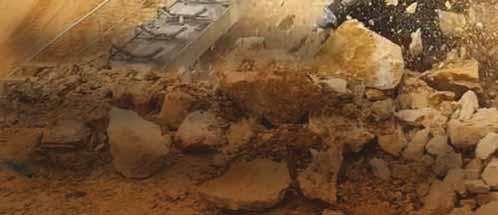
Rotary cutter heads making a real breakthrough
Rotary cutter heads are making an increasingly strong case for their deployment in quarries globally. Roger Murrow reports
Traditionally, drill and blast, breakers and hydraulic hammers have undertaken the heavy work required in quarries and surface mines, providing a tough, productive and efficient solution. Sometimes, however, their use may be precluded due to noise, dust emissions, the location of urban dwellings or a requirement for greater accuracy. In response, many quarries have utilised hydraulic rotary cutting technology. These are commonly referred to as ‘drum cutters’, ‘cutter heads’, ‘rock grinders’ or ‘rock wheels’. These are a flexible, cost-effective and adaptable solution for rock excavation, trenching and mine/quarry wall scaling, being suitable for any application requiring materials to be cut or ground.
A rotary cutter head is a hydraulic attachment on which drums equipped with numerous picks spin around at rapid speed to cut rock, concrete or frozen ground. The picks that perform the cutting job are wearresistant, have exchangeable teeth and are generally designed for efficient operations. They may also be equipped with dustsuppression systems to improve a quarry’s or mine’s environmental credentials, as well as maximising safety (in the US this has helped quarries and aggregates plants deal with the recent silica dust regulations).
The cutting heads have proved to be ideal for rock or concrete wall and surface profiling, trenching, frozen soil excavation, soil mixing, rock excavation in quarries, as well as utility work, demolition, and dredging (most appear able to work in water up to 30m in depth). Manufacturers of the equipment supply the cutters with a large variety of cutting heads for various applications, all being able to deliver precise and accurate work even in difficult conditions.
Due to both build and operating characteristics, cutting heads can be utilised in noise- and vibration- sensitive areas, as a low-vibration profile results in no or little damage to sensitive structures, thus enabling usage without inconveniencing others in the locale. This means that they are now seen as a real alternative to hydraulic breakers by generating higher productivity in quarrying due to their design and being able to provide high levels of performance and precision, especially when working in sensitive environments.
Wide cross-section of manufacturers
There is now a vast array of different cutting heads available on the market from a large cross-section of suppliers. These range from specialists in the design and manufacture of hydraulic cutting heads, whose business
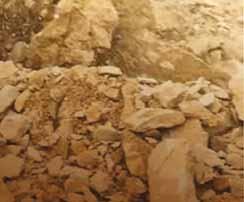
is entirely focused on these solutions, to multinationals with an offering that encompasses whole ranges of equipment for quarrying, mining and construction. One such latter company is Sandvik Mining and Rock Technology, which produces a range of rock cutters with fixed teeth for excavators ranging from 2.5 to 70 tonnes.
Sandvik’s RC series cutters have been designed to cut through hard rock quickly and efficiently, combine high productivity with minimal noise and vibrations, having hydraulic-powered cutting heads that can be mounted on excavators quickly and easily. They all possess efficient, geometricallyoptimised cutting heads that can be used in a number of applications, including production, scaling, tunnel rehabilitation, roadway levelling, trenching and demolition. The models range from the relatively lightweight Sandvik MA520 for lighter carrier vehicles to the heavy-duty MA720. They are designed for quick change coupling between the carrier vehicle and attachment, which makes the cutting heads productive tools for any quarrying, mining or construction application. Thanks to very low maintenance requirements and minimal operating costs, they are also a highly cost-effective solution. Another global behemoth, Epiroc, has also spotted the attributes of the cutter heads, and
in order to provide a full offering acquired German company Erkat whose product line features rigid and wear-resistant gear housings to ensure a smooth cutting action, while providing maximum cutting power to penetrate the rock. The cutters have proved to be particularly adept at removing precise layers of rock or frozen ground and are fitted with a central fixing system enabling the cutter to rotate 360° without having to be disconnected from the excavator. With low vibration and quiet operation, Erkat’s cutters can also work in sensitive areas. The attachments have also been designed to help save on material costs as they don’t need to remove all of the materials, but rather just the damaged or worn surface. In some applications, the spoils from the material being cut by the cutter can be used as backfill or elsewhere on the jobsite.
A company best known for its underground equipment is US-based Antraquip, which manufactures an extensive line of hydraulic rock wheel cutters for a range of applications. Its cutters are suitable for material with uniaxial compressive strength (UCS) ranging from 500 to 25,000 pound-force per square inch (PSI) and come with such features as high torque hydraulic motors, robust, customisable cutting drums with durable spur gears and housing. Drawing on its experience of dealing with various rock types, Antraquip’s offering has been designed to suit different types and locations of rocks, as well as fitting different carrier machines.
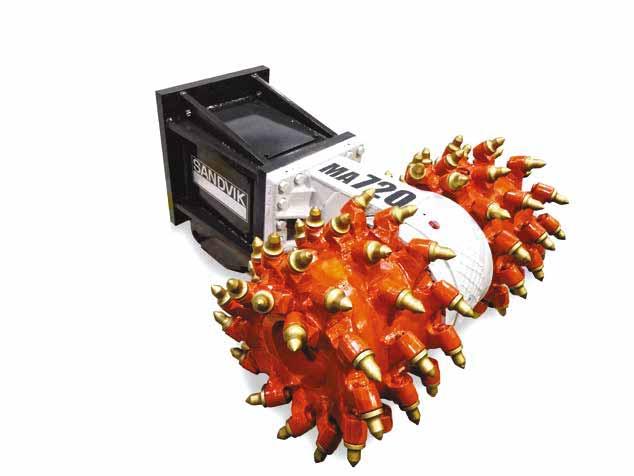
Sandvik’s cutters have been designed to cut through hard rock quickly and efficiently
Applications of Antraquip cutters include an AQ-5 model operating at a limestone quarry in Australia, where the cutter was mounted on a CAT 374 excavator. Here, the rock being cut was a combination of medium-hard shale and hard limestone with compressive strength of up to 180MPa (26,000psi). In Colorado, an AQ-4 was fitted to a PC360 excavator operating in a quarry for production mining and quarry-roadway development work. The limestone production achieved (with average compressive strength of 10,000 psi or 70 MPa) was up to 100 tonnes per hour of net cutting.
Compact but still productive
As well as companies that are specifically associated with mining and large-scale mineral excavation and quarrying, some specialist attachment companies are also producing more compact, but still productive equipment. Two Italian companies, in particular, have drawn on their experience in producing hydraulic excavator and loader attachments. MB Crusher’s cutting heads have been designed to deal with particularly resistant and tough materials, such as fragmented rocks, although they can also deal with softer materials, such as asphalt. They have been designed to perform excavation with extreme precision. Aimed at the more compact sector of the quarrying industry, the cutters are designed to be fitted to three-12-tonne excavators as well as skid steers and backhoe loaders from three-eight
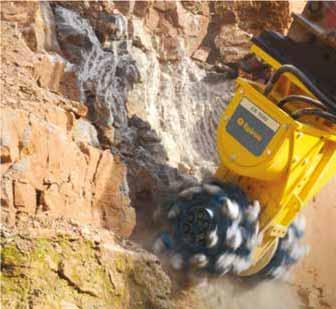
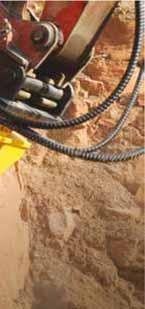
The Erkat attachments have also been designed to help save on material costs as they don’t need to remove all of the materials, but rather just the damaged or worn surface

Drawing on its experience of dealing with various rock types, Antraquip’s offering has been designed to fit various types and locations of rocks
tonnes. Amongst the many features of the cutters are minimal vibration and noise emissions, with a cutter body rotation that enables the operator to rotate the cutter directly from the cab.
Simex’s TF cutter heads have been purpose-developed for trenching, profiling rock and cement walls, tunnelling, quarrying, demolition, dredging, finishing operations and underwater works. They have proved to be particularly effective where conventional excavation systems are too weak, and percussion systems have little effect. Recently, the cutters were used in sedimentary rock quarries in Malta dealing with Calcarenite, which is used both as a construction material and as an aggregate. The rock has a characteristic compressive strength which ranges from approximately 20 MPa to almost 60 MPa according to the zone.
Due to the small size of Malta, many quarries are sited near urban areas or tourist attractions. This often precludes the use of drilling and blast or breakers in quarrying, which has led directly to the use of Simex cutter heads, which are capable of minimising any environmental impact but still produce cut rock to the desired sizes. The cutter head used, a TF2500, has been designed for excavators weighing 40-55t and delivers a torque of 31.7kNm and a cutting force of 83.7kN. It is also fitted with an integrated large displacement hydraulic piston motor that ensures high efficiency and high torque. Thanks to the double bearings supporting each drum on the cutter, the shaft transmits only motion and bears no load.
Kinshofer is another company that has developed its own range of hydraulic cutting attachments, recently re-badged as ‘KDC’. These are driven by high torque motors, feature modular construction and robust spur gearing with a gear reduction to increase cutting force. The attachments are also suited for underwater operation of up to 25m deep, thanks to the heavy-duty sealing system. The optional 360° rotation function allows exact positioning in corners, on quarry walls and other vertical surfaces for more accurate contouring. The optimised arrangement of picks ensures a high loosening performance and low wear. Three drum versions are available including an excavating version for cutting soft to medium-hard rock, a profiling version for shaping and levelling soft to
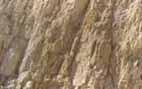
MB Crusher’s cutting heads have been designed to deal with particularly resistant and tough materials, such as fragmented rocks.
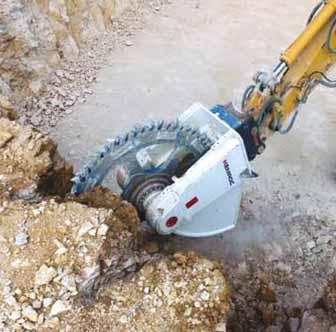
medium-hard rock and a demolition version for cutting medium-hard to hard rocks and concrete.
Specialist manufacturers
As well as those manufacturers who produce wide arrays of associated equipment, or are hydraulic attachment specialists, two companies stand out as specialists in the field of producing hydraulic cutting heads. The design of German company Kemroc’s cutting attachments is based on many years of experience in the industry. It aims to provide maximum cutting performance with minimum wear costs, with a selection of picks and boxes and a pick pattern for enhanced rock cutting.
Kemroc has given particular attention to the design and working of the ‘picks’ on the cutting heads. When working with round picks each tool penetrates into the rock along parallel paths and breaks material out from
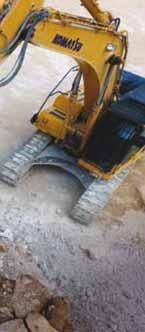
the space between the paths. Therefore, the cutting rate depends to a large degree on the uniaxial compressive strength of the rock being cut. Other significant factors affecting production rates include the hydraulic pressure and flow that the excavator is able to supply to the attachment, as well as the stability and weight of the excavator.
The company’s DMW range has been purpose-designed for cutting hard rock with a uniaxial compressive strength of 120MPa for excavators from 14 to 60 tonnes. It is able to cut down to 1m and comes with a choice of wheels with different tooling configurations and a range of widths up to 400mm being available. The EK range of cutters is designed for use on excavators from two to 50 tonnes, being ideal for cutting stone with a uniaxial compressive strength up to 100MPa. They are efficient, vibration-free attachments for the excavation of deep, narrow trenches delivering an optimal trench profile. They
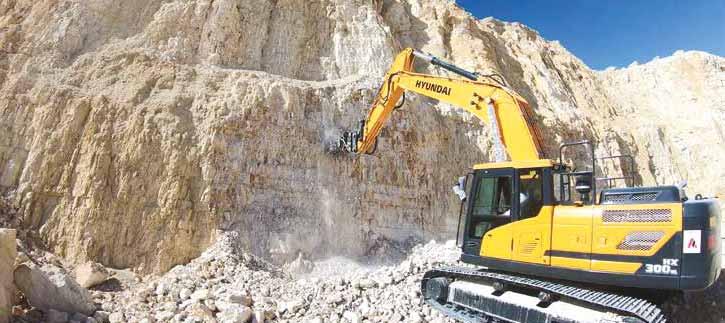
Kemroc DMW cutters are able to cut down to 1m and come with a choice of wheels with different tooling configurations
are also suited to the quarrying of medium to hard minerals with compressive strength from 15 to 60MPa where drill and blast are not possible.
The effectiveness of the EK range is illustrated by the way in which a German company has made radical changes to the extraction and mineral processing methods at one of its gypsum quarries by using an EK 140 mounted on a 45-tonne excavator. The chain cutter replaced a hydraulic breaker as the primary extraction tool which reduced costs at the crushing plant. Changing the extraction method resulted in considerable savings in both plant and labour costs as extracting gypsum using a hydraulic breaker mounted on an excavator was proving to be generally a slow and difficult procedure for both man and machine.
When compared to the breaker, the chain cutter worked with less vibration resulting in lower maintenance requirements for the excavator. Furthermore, when a breaker was used, the material produced lay on the ground in large blocks that had to be further broken down by the breaker before the gypsum could be sent to the processing plant for crushing. Using the chain cutter made the extraction process more efficient by eliminating many of these processes, as the chain cutter enabled the excavator operator to start the production process by placing the chain cutter at the top of the wall of gypsum, then cutting its way down to the bottom. The material produced by the chain cutter also has a much smaller grain size and doesn’t require any extra work before being transported to the processing plant, thereby lowering crushing costs.
Anglo-German partnership
A rare industry development has been the pioneering ‘rock wheel’ cutting attachments, designed by a UK company but now being manufactured and marketed by a German company. Sheffield-based Webster Technologies traces its beginnings to the
early 1960s, designing, manufacturing and distributing mining equipment, being one of the first companies to use hydraulics for cutting. The Webster roadheader quickly became well known in the industry and is still used in quarrying and mining applications today. Building upon its reputation as an industry pioneer, in 2013 Webster Technologies licensed the manufacture, global sales and distribution of its Rockwheel cutter to German company Rokla GmBH. This collaboration has combined creative technical design, quality manufacturing and sales and service focus.
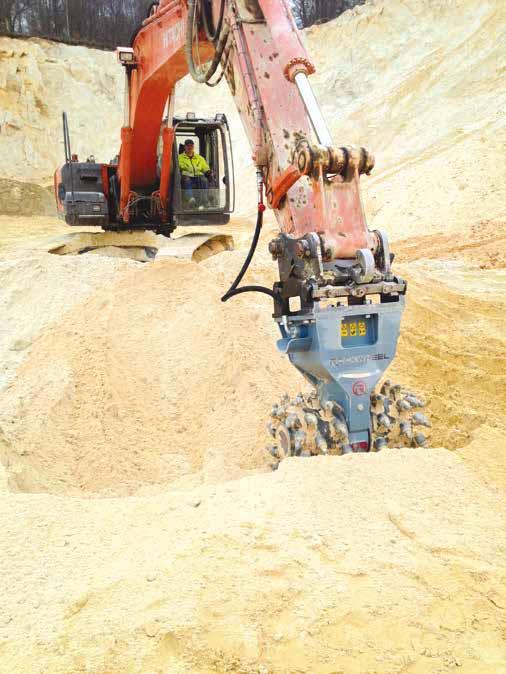
The combined rock wheel cutting technology maximises precision as well as being said to be two to three times faster than the usual speeds achieved with breakers. The extremely short cutting units, combined with their sturdy and tough housing, make quick work of removing rock. Moreover, they leave projections clearly visible and immediately workable, unlike ripper teeth which break up large pieces of rock and make work difficult for excavator operators. When the removed

material is internally processed as aggregate, the Rockwheels kill two birds with one stone, as excavated material will already be one to three cm in size.
Illustrating the benefits of the Rockwheel is a particular Germany quarry which has highly abrasive rock, specifically sand and gravel. For many years scarifiers had been used for quarrying the rock (classed as a seven conglomerate,) resulting in high levels of wear and tear. The extreme impact required also placed a huge stress on the excavator being used. Having only three major components (housing, motor and cutting heads equipped with picks) meant that these difficulties were overcome by the Rockwheel D30 model, supplied with two excavating drums equipped with 60 wearproof special picks for use in highly abrasive sand and gravel conglomerate.
All the Rockwheel cutting units possess solid drive shaft bearings and are designed for long service life. Their sealing system also enables them to operate underwater without the need for any conversion. As a rule, maintenance times are short, as all components can be easily replaced. Furthermore, when compared to the use of a breaker, the cutter produces a smaller, more consistent grain size, resulting in savings in crushing costs and material handling. The German quarry owners have been so impressed with the cutters that they are now using them at their gypsum quarries when drill and blast are not suitable for the extraction of the mineral. AB
The Rockwheel D30 model with the two excavating drums is equipped with 60 wear-proof special picks for use in highly abrasive sand and gravel
BlastLogic is said by Maptek to deliver productivity and efficiency gains beyond the drill and blast space
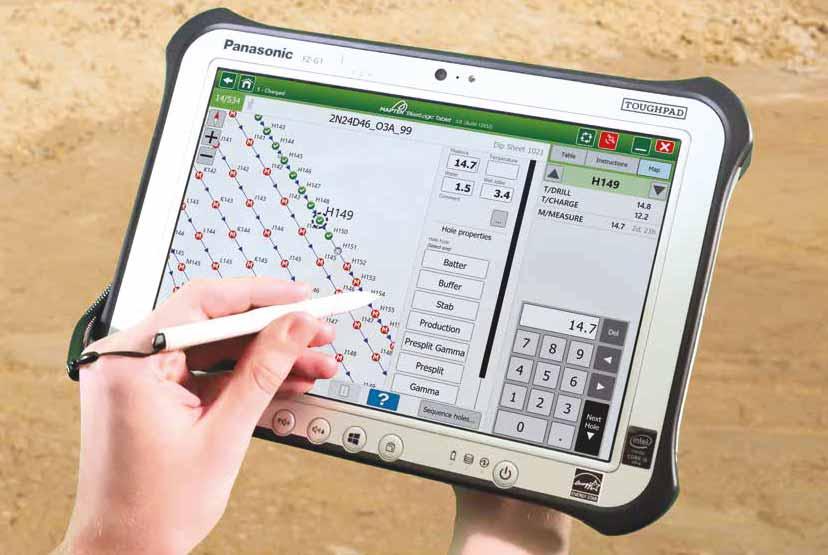

A premium Maptek approach to blast execution & analysis
A long-time leading global name in premium site analysis software for quarrying and mining professionals, Maptek remains on a firm growth path. Guy Woodford conducted a Q&A with Mark Roberts, Maptek group product manager for mine operations, to learn more about the Australian-headquartered company’s work on drill and blast optimisation
How does Maptek see the current global surface mining sector for its product range around blast execution and analysis?
Most surface operations have piecemeal solutions to drill and blast - one system tracking drilling, another blast hole loading, another post-blast analysis, as well as ad hoc attempts to audit and analyse historical information - all in a disparate collection of paper sheets, survey data and file formats.
Measurement While Drilling (MWD) systems are great, electronic firing systems are great, intentions are great, but the information cannot be cross-correlated in a timely way to be of ultimate benefit to the operation.
Maptek BlastLogic is termed a quality management system or a design and reconciliation system, and regardless of those descriptions at the end of the day, the solution provides a unified platform (one-stop-shop) for improving drill and blast.
Customers describe the value delivered through BlastLogic as providing transparency and accountability on their blast designs and how well these are executed. The combination of blast design, integration and reconciliation tools through a paperless system with near-live
synchronisation is how Maptek differentiates its solution from siloed reporting mechanisms.
Reporting tools collect the data during the shift or a production cycle, bring it together and report it. By then, the shift is over, and it’s too late to apply the analysis to make informed decisions mid-shift when it can actually make a difference.
Importantly, BlastLogic delivers productivity and efficiency gains beyond the drill and blast space. Linking the performance of the blast to geology, the production plan and downstream processes add agility to
Mark Roberts, Maptek group product manager for mine operations
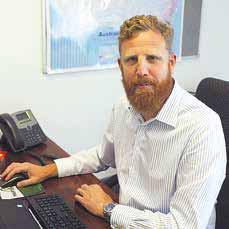
planning and production. For example, integrating dig rates or vibration results means all stakeholders overseeing the safety, production and cost drivers of the mine or quarry can apply information around ‘how well that blast performed’ to the knowledge of the impact on the overall operation.
Correlating all of the blast-related data in one place and getting objective validation and analysis around that data, with results transparent to all teams in surface operations, facilitates greater coordination among functional groups. The learnings gained from analysing that data are fundamental to blast performance.
The founding premise of an all-inone design and reconciliation package is in substantiating how well you are executing your design. Think of it as a way of measuring confidence. If you measure something, you can benchmark it because you now have a baseline that guides the metric for improvement.
Closing the feedback loop between planned outcomes and what actually happened from blast design to reconciliation provides the certainty that businesses look for.
Don’t get me wrong, trial and error still exist. No-one wants to tell their manager or shareholders that they couldn’t show where
improvements were made because they weren’t tracking performance.
Analysis of the blast outcomes over time provides decision guidance on how to improve - either improve blast designs or look to the execution phase to identify where gains can be made.
What impact has COVID-19 had on market demand?
Early on with COVID-19 when customers relocated their staff away from sites or corporate head offices, it became even more important to transition to digital tracking and reconciliation systems. The single source of blast data could easily be available to everyone, regardless of where they worked.
Maptek Account enables web browser access to all Maptek software entitlements, even for customers who may work offline. In this way, blast engineers and field crews can still record, model and analyse their blast data to support the operational production cycle.
Where do you see growth coming from in your product offer to open-pit mining customers?
Tighter integration between drill and blast and other operational processes is a key consideration in the Maptek development strategy. Surface operations need a continuous feedback loop of collecting, validating and reconciling data to better manage their planning and production cycles, and allocate resources efficiently.
Field and management teams at quarries and open-pit mines are supported by the digital data flow to respond appropriately to the need for changes in real time, knowing that their decisions are founded on current information and actual conditions.
The drive for optimisation solutions, by which we mean a balance between value and practicality, is behind an ambitious new Maptek project to automate the currently
When stock levels can be updated dynamically in the field using Maptek’s BlastLogic Tablet, possibly confusing paper-based record-keeping is unnecessary, and manual calculation errors reduced

intensive engineering design process.
We’re using our scalable cloud platform, the Maptek Compute Framework, to build a new blast optimisation tool. BlastMCF applies an evolutionary algorithm to handle multiobjective, many-constraint, population-based modelling. The approach has been proven in our scheduling and domain modelling solutions to generate realistic results faster than with traditional methods.
The outcome is a dramatically improved workflow for blast engineers. Instead of focusing their time coming up with one design (that may prove to be sub-optimal), they will pivot to trading off the multiple designs that are automatically prepared. Typically these are more than 90% ready to be executed, and the chosen design can still be updated manually in BlastLogic if minor tweaks are required.
What success have you had in the marketplace with your latest product solutions centred on blast execution and analysis? Can you give a couple of customer examples?
Specialists tasked with continuous improvement and innovation are typically keen to look at their mining or quarry operation holistically.
Proper explosives handling and tracking is crucial to safety and efficiency, and going digital is key to ensuring operational
compliance. When stock levels can be updated dynamically in the field using the BlastLogic Tablet, potentially confusing paper-based record-keeping is eliminated, and manual calculation errors are minimised to account for all explosives used on a particular blast, or not used and returned to the magazine.
Tablet data is synchronised with the BlastLogic desktop application and central server, and reports can be created and printed for regulatory sign-offs. Live dashboards give a real-time view of inventory and allow flagging and investigation of stock discrepancies.
Digital record-keeping is secure, provides greater clarity and aligns with the industry trend for paperless operations. The BlastLogic digital workflow is helping customers reduce downtime and reap the benefits of a datadriven, decision-making approach.
Is Maptek planning to introduce any new products for surface mining sector customers in the next 12-18 months? If so, when are they likely to be made available? And crucially, how will they add to/differ from what is already on the market?
BlastMCF mentioned above is one of the key areas where automation can deliver benefits to surface operations such as open-pit mines and large quarries.
Maptek will soon introduce the ability to record as-drilled data on our tablet applications. This will benefit many operations that cannot access drill navigation technology on all their drills.
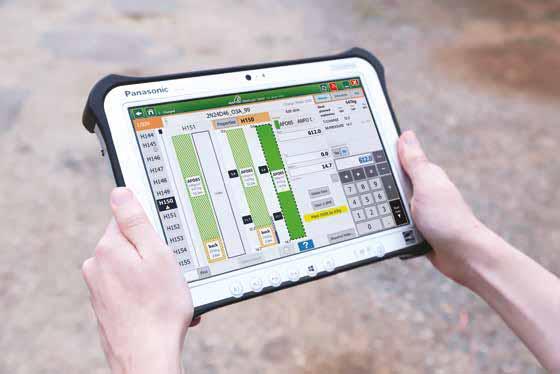
For example, contractor equipment which may not have drill navigation installed, or sensors may not be functioning correctly and awaiting repair. With BlastLogic, drill operators will be able to use the BlastLogic Tablet instead of paper plod sheets. As-drilled data like drill operator name, drill ID, drill time, depth and custom drill properties that are supported in BlastLogic will be recorded, making it immediately available to be consumed in the design-validate-reconcile feedback loop for
The recording of accurate digital data has shown to significantly improve overall performance by enabling this measurement to be used earlier in the drilling and blasting process, so re-drills and backfilling are accurately performed in time for charging. AB
BlastLogic digital explosives management

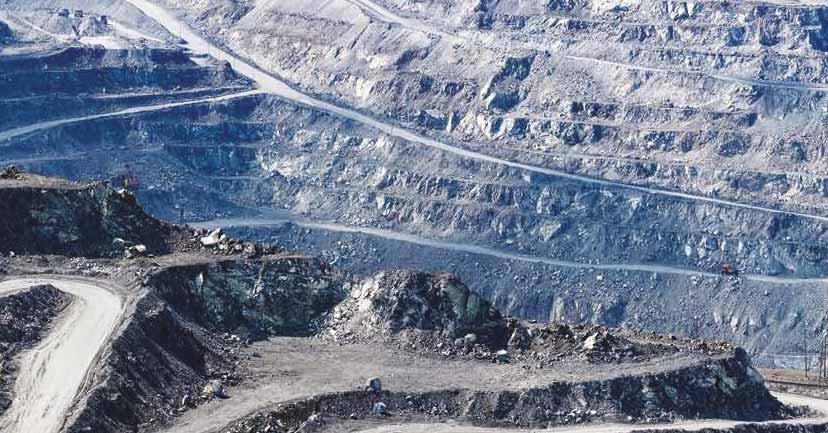
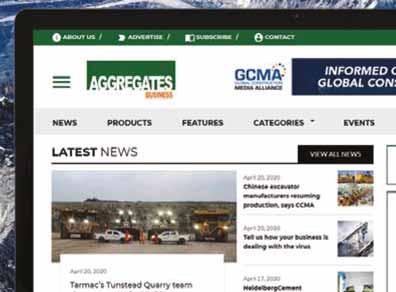

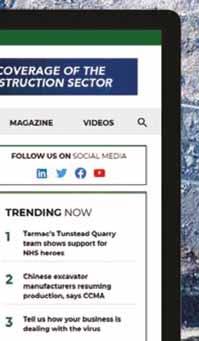
Going wireless in surface mining
Orica has achieved great commercial success with its groundbreaking wireless WebGen solution for the drilling and blasting process in surface and underground mining. Guy Woodford reports
In early 2017, Orica launched WebGen, the world’s first fully wireless initiating system as the critical first stage in fully automating the drill and blast process in surface and underground mining. One of the most exciting blasting technologies to be developed since the introduction of electronic blasting systems in the early 2000s, WebGen has already been fired in over 1,000 blasts in both surface and underground mines around the world.
The system allows for groups of in-hole primes to be wirelessly initiated by a firing command that communicates through hundreds of metres of rock, air, and water. This is said by Orica to eliminate the need for down wires and surface connecting wires, enabling new mining methods and blasting techniques that are safe and reliable. Using low-frequency magnetic signals to communicate with each WebGen primer before a blast, WebGen is also the only commercial explosives product with a safety integrity level (SIL) 3 rating.
WebGen has demonstrated the benefits of its fully wireless blasting technology in many underground mines and has enabled the development of seven innovative mining techniques such as the temporary rib pillar (TRP) method and the sub-level cave (SLC) mining method.
The success of WebGen in underground mining is said by Orica to have led to increased adoption of the technology in surface mining. With its fully wireless capability WebGen presents an opportunity to overcome one of the industry’s most persistent limitations: a physical or wired connection to each primer in a blast.
Wired systems have a large physical presence and are susceptible to damage at every point along the connecting line. The potential for misfires due to downline damage has commonly led to the application of redundant initiation systems and can impede the loading of adjacent blast patterns due to flyrock damage. These contributing factors, says Orica, increase
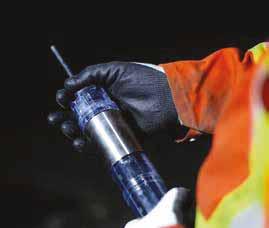
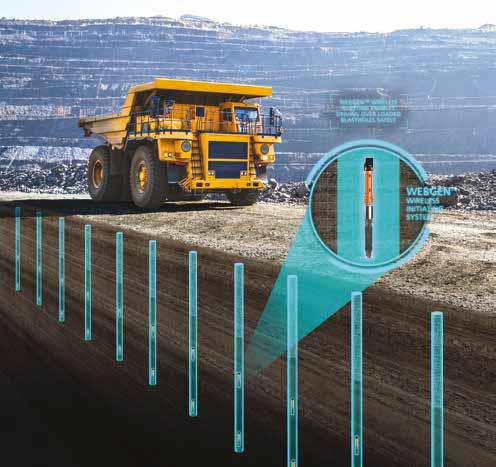
blasting costs, reduce mine efficiency and limit blast productivity. Wired systems also require precautionary measures in priming, loading, stemming and tie-in activities to protect wired connections, adding burden to manpower needs and timing.
Being fully wireless, the application of WebGen in surface mining is said to simplify bench operations with no tie-in process and reduced on-bench resources, inventory, and misfires that occur due to line damage or cut-offs, slumping or operator error. Stemming costs are also reduced, and back-up inventory is eliminated with wireless systems.
Orica says WebGen also improves employee safety in surface mining operations by reducing the time spent on the bench in extreme heat and dusty conditions and by reducing physical movement. This reduction is significant when charging significant blasts or when facing extreme conditions around the world.
The absence of downlines also removes the interaction between heavy vehicles and initiating systems while reducing people’s exposure to on-bench hazards. The tie-in process is eliminated, and spotters are not required to protect downlines, nor are they exposed to the dust and dangers from typical stemming operations.
With increased flexibility in pit planning and blasted inventory, Orica says that mine operations enabled by WebGen can also prime and load larger single blasts as well as eliminate firing window variability. AB
ABOVE: WebGen includes an i-kon III plug-in detonator, a Pentex W booster and a DRX - a digital receiver comprising a multidirectional antenna and a battery, which serves as the in-hole power source
WebGen is said to unlock endless possibilities including safe drive over WebGen loaded blast holes, increasing vertical advance
New Cat models at work: a Cat 988K wheeled loader, Cat 772G rigid hauler and Cat D10T2 crawler dozer helping Latomia Latouros process calcareous limestone
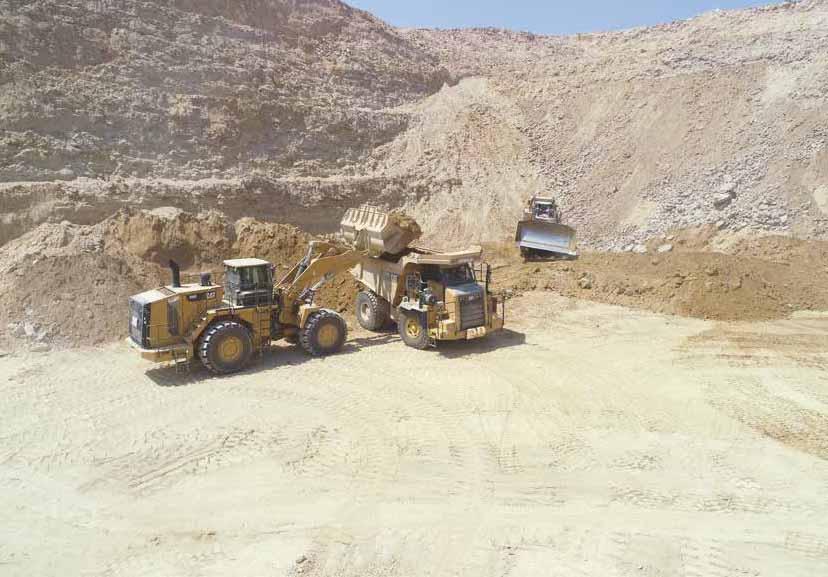

CATERPILLAR CONTINUITY FOR LATOUROS GROUP

A new fleet of premium Cat excavation, loading and hauling machines is helping Cyprus’s biggest quarrying group bounce back rapidly from a COVID-19-induced operational shutdown. Guy Woodford reports
It was no surprise that when Antonis Latouros, head of the Latouros Group, wanted to update the excavation, loading and hauling fleet working across his Cyprus-based group’s four businesses that he opted for Cat models.
“If you cut me, my blood is going to be yellow. I am Caterpillar’s biggest customer in Cyprus,” explains Latouros. “We have used Cat machines for so many years as they are reliable. They have a strong dealer and aftersales presence here, which helps with maintenance and machine uptime, and Cat machines retain a good resale value after you’ve used them for seven to 10 years. This offers better value for money.”
Latouros is also impressed with his new Cat machines’ fuel efficiency and productivity. “Caterpillar has improved the fuel efficiency of its machines a lot, most notably with its new models. We discussed fuel consumption with Caterpillar before purchasing our new Cat 966M XE wheeled loader, and they guaranteed us 50% fuel saving compared to the Cat 966H we had been using.
“We have a subscription to CatConnect and ProductLink and the technology on our Cat machines allows us to produce much more. My team and I are very experienced when it comes to working with Cat machines.
Our chief mechanic, for example, was previously working at the local Cat dealer. Our operators also say how comfortable they are in the cabin during their work.”
Latouros’s highly successful quarrying group consists of Latomia Latouros, which operates Latouros Group’s (LG) flagship calcareous limestone-based sand quarry in Dali, situated just under 20kms south-east of Nicosia. The group also operates another calcareous limestone-based sand quarry, Elmeni (Latomia), less than two kilometres from the Dali site. Latomio Pyrgon produces diabase rock sand/aggregates of various sizes at Pyrga village. Latouros Gypsum is LG’s gypsum quarry business, with its impressive “95% purity” gypsum exported via Larnaca port to customers in countries including Israel and Lebanon. A fourth company, Recycling Point – Latouros & Xenis Bros., is a 2019-established construction and demolition (C&D) waste recycling business, 51% owned by LG.
LG sells around 1.75 million tonnes of sand/aggregates and gypsum products produced each year at the group’s four quarries – generating approximately €15 million in annual sales revenue. The Dali site accounts for around 600,000 tonnes, with a further 400,000 tonnes of sold product originating from Elmeni (Latomia) quarry.
Latomio Pyrgon production accounts for 400,000 tonnes of sales, with Latouros Gypsum’s gypsum quarry output resulting in annual sales of approximately 350,000 tonnes. Combined, LG companies’ 90 million tonnes of deposits ensure the long-term operations of the group for decades to come.
Latouros’s 11 new Cat models were delivered in the spring and summer this year. All are now operating across several LG work sites.
At Latomia Latouros’s Dali quarry, new Cat 988K and 966M XE wheeled loaders, three new Cat 772G rigid dump trucks, and the new Cat D10T2 crawler dozer have impressed. Fitted with a CAT C18 ACERT 403kW Stage V engine, when utilising economy mode the Cat 988K is said to offer up to 15% better fuel efficiency than its predecessor. The model is also said to come with up to 10% lower maintenance cost, thanks to grouped service points making regular maintenance more convenient, and up to 10% more productivity in most truckloading applications when using performance series buckets with increased capacities. In terms of Cat machines, Latomia Latouros also operates another Cat 966M XE, bought new in 2017, which with the new Cat 966M XE is loading the finished products to the customers’ trucks.
At Latomio Pyrgon’s quarry, another new Cat 988K wheeled loader, and two other Cat 772G dump trucks are proving highly efficient and productive in their loading and hauling duties. With a 47.2-tonne payload, Cat 772G trucks come with a 415kW Cat C18 ACERT Stage IV engine and 31.2m³ body capacity. Speed limiting is a new feature for G Series trucks and is offered as an alternative to gear limiting. It offers customers both fuel-saving and component-wear benefits. Speed limiting allows the truck to find the most fuel-efficient gear and engine speed while travelling at a set limit. Speed limiting will also work with Automatic Retarding Control (ARC). Latomio Pyrgon, just like Latomia Latouros, bought in 2017 a new Cat 966M XE for loading the finished products to the customers’ trucks.
A new 87-tonne class Cat 390F hydraulic excavator has replaced a Cat 390D model at Latouros Gypsum’s quarry. The Cat 390F features a Cat C18 ACERT Stage IV engine. It is said to offer up to 5% more productivity as the model’s hydraulic system allows for quicker and more precise material movement. The model’s cab is 3 DB(A) quieter, allowing operators to work in greater comfort due to less interior noise. Bought new in September 2014, the replaced Cat 390D is now working at Latomia Latouros’s Dali site.
Finally, a new Cat MH3024 material handler is busy helping to recycle C&D waste for Recycling Point – Latouros & Xenis Bros. Benefiting from a premium Cat C7.1 Stage IV engine and constant power
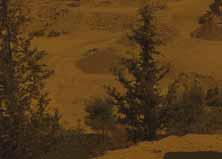
“If you do not have a quality recycling system, it’s virtually impossible to operate in Cyprus due to water scarcity.”
Antonis Latouros, head of the Latouros Group, at Latomia Latouros’s flagship calcareous limestone-based sand quarry in Dali
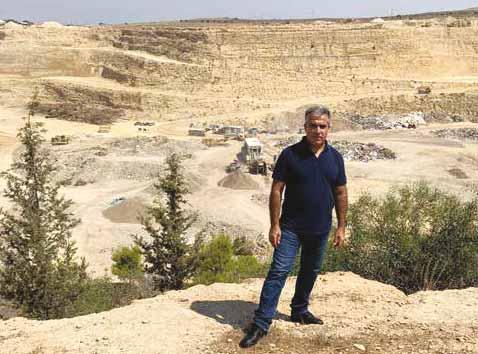
The sand products produced at LG’s calcareous limestone quarries are unique, given how the island was created by, as Latouros puts it, “coming up from below the sea”. As such, Latouros says it is not unusual to find fossils at his group’s calcareous limestone quarry sites.
“We work with natural sea sand. All other quarries in Cyprus produce crushed sand. Our natural sand’s particles are spherical shaped, so it works like a bearing when used in construction applications as part of a concrete mix. This gives better workability and allows you to reduce the water-cement ratio in your concrete. The less water, the higher the concrete strength. It also means you use less cement, reducing your costs.
“We have a very good reputation in Cyprus

As the COVID-19 pandemic reached its height in Europe during the second quarter of this year, a Cypriot government decree shutting down construction sites between 25th March and 4th May led to most quarries, including LG’s four sites, reducing and latterly completely stopping production due to what Latouros describes as “near to zero” sales during that time. “We operated for a couple of weeks in order to increase our stocks of finished products, and then we carried out some maintenance works on our crushing plants and machines,” he explains.
Latouros says that quarrying and construction sectors are now pretty much back up to full operational speed, with demand for building materials remaining strong.

“The coronavirus affected us in the delays
Latomia Latouros’s calcareous limestone quarry in Dali
taking place at the ports around the world. Our new models have come from Caterpillar factories in the USA, Brazil, France, India, and China.”
At Latomia Latouros’s Dali quarry, two parallel plant lines are used to process the initial Cat D102T crawler dozer ripperexcavated calcareous limestone. The new Cat 988K wheeled loader loads the excavated material into the Cat 772G RDTs which haul it to the Telsmith grizzly feeders which feed the excavated and hauled material into 500 tonnes per hour Telsmith 3050 and 2250 jaw crushers. On being crushed by the Telsmith 3050 plant, the material goes through two 7ft x 20ft Telsmith double-deck screeners. The second plant line sees material fed via the grizzly feeder into the Telsmith 2250 jaw crusher and then screened by a 6ft x 20ft and a 6ft x 16ft double-deck Telsmith screeners. Around 90% of the quarry’s final 0-4mm product is passing 2mm.
Any +5mm oversize material remaining after the initial crushing and screening process on the two plant lines is conveyed to two up to 350 tonnes-per-hour capacity Magotteaux MAG’Impact 2400 VSI (vertical shaft impactors, one for each plant) and then looped round via a conveyor to the Telsmith screeners for processing into final grade product. Any undersized material is conveyed to two (for each plant) rod mills, each fitted with an Elkayam hydrocyclone, for washing out/removing the fines and processing into a saleable product.
All the 1,000m³/hour of water used at the two plants for washing the sand is then passed through a water recycling plant manufactured by French company MS, managing to retain 95% of the water used in the site’s production. “We use around 1,000m³ of water per hour in our production. If you do not have a quality recycling system, it’s virtually impossible to operate in Cyprus due to water scarcity. The only water we lose is the humidity in our products and in the filter-pressed cakes. Our recycling system was installed in 2004 and is the only one on the island. In 2013, we won a UEPG (European Aggregates Association) Environmental Best Practice Award for operating it.”
Around 95% of LG’s sand/aggregates products are used in concrete for infrastructure and commercial and residential building projects. The rest is used in plasterbased applications.
Cypriot aggregates production in 2019 stood at 8,422,664 tonnes – a rise of 5.5% on 7,978,000 tonnes in 2018. After a period of COVID-19-induced disruption, Latouros, who is president of the Cyprus Aggregates Producers Association and UEPG’s first vice president, says sand/aggregates product demand is very good again thanks to the start of some major government – and private investment-backed construction works.
Given the return of a promising trading outlook, LG’s significant investment in new Caterpillar machinery is looking like a shrewd and potentially lucrative move.

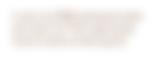

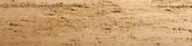

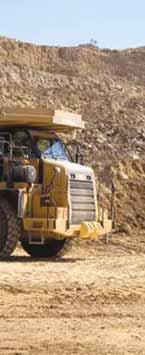
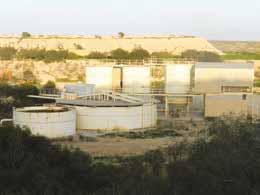
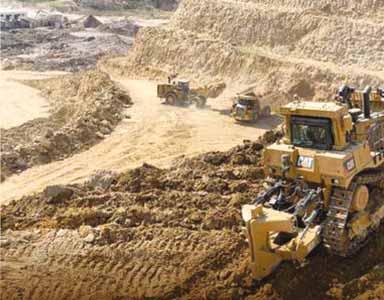
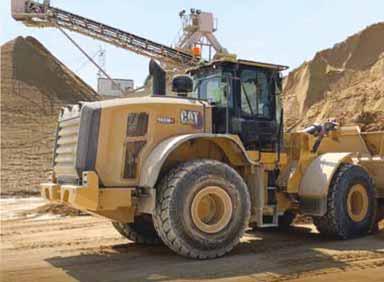
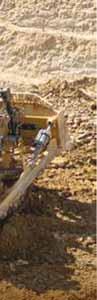
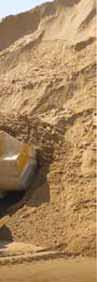
AB
Filter presses at Latomia Latouros’s Dali quarry
Latomia Latouros’s water recycling plant was installed in 2004 and remains the only one in Cyprus
A new Cat D10T2 crawler dozer ripper-excavates calcareous limestone at Latomia Latouros’s Dali quarry
A new Cat 988K wheeled loader and new Cat 772G rigid dump truck at work at Dali quarry
Latomia Latouros’s new Cat 966M XE wheeled loader gathering material
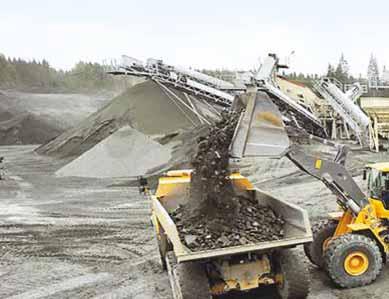

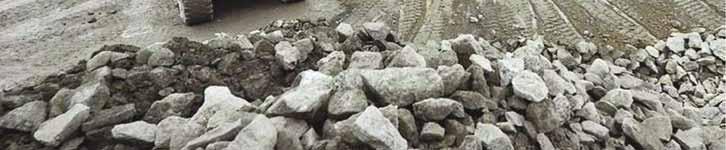
All change in Russia’s aggregates sector
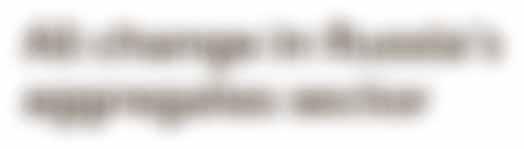
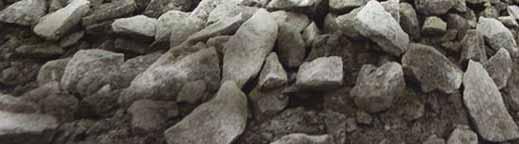
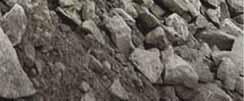
The Russian aggregates market is facing a period of realignment due to the economic impact of the continuing COVID-19 pandemic. Eugene Gerden reports
The coming months are set to see a survival of the fittest when it comes to companies trading in Russia’s huge aggregates sector. The COVID-19 pandemic has hit Russia’s economy hard, with aggregates industry analysts stating that the current national economic stagnation is likely to lead to some smaller local aggregates supply firms going out of business, and larger but no longer profitable companies becoming prime targets for acquisition by ambitious rivals. As such, surviving larger local and regional producers can expect to gain greater market share when the economy picks up and pent-up aggregates demand returns.
A period of sector realignment has already begun with the eye-catching acquisition of the Novosibirsk Quarry Administration, the largest producer and processor of building stone in Russia’s 13,100,000km² Siberia region, by the National Nerudnay Company (NNC), one of Russia’s largest producers of construction materials.
For NNC, south-west Siberia-based Novosibirsk Quarry Administration (NQA) has become the company’s first large-scale
aggregates asset in Siberia. According to analysts, the deal allows NNC to significantly strengthen its position in the massive geographical region, which remains one of the most promising in terms of aggregates consumption in Russia.
While the financial details of the NNC-NQA deal have not been disclosed, Russian aggregates industry analysts estimate it to be worth around RUB 2bn (€22.5mn).
Presently, the NQA remains one of the largest enterprises in the Siberian aggregates sector, with its production focused on the processing of building stone. Its structure is currently comprised of five quarries with different stone types, all of which are located within either the city of Novosibirsk or its surrounding area. Total balance reserves of these sites are estimated at more than 200 million m³.
So far, among the largest customers of NQA in the domestic market have been some major private and state-owned corporations, including RZD, the Russian railway monopoly, as well as some construction companies, most of which are based in Russian Siberia.
In 2019, the company’s output amounted
to 8.6 million tonnes of rubble, while most analysts believe in its potential for a significant increase of these figures in years to come.
One of the largest players in the Russian aggregates market, NNC’s site portfolio consists of 12 plants, located across Russia - from the Krasnodar Territory to Karelia.
In 2018, the company’s revenue stood at RUB 22bn (€247.3mn), and net profit at RUB 2.6bn (€29.22mn). Earlier, some Russian media reported that it is owned by a well-known Russian businessman and developer, Yuri Zhukov. Currently the company holds about 8-9% of the domestic aggregates market. One of its major assets is the Pavlovsk Nerud enterprise, situated on Europe’s largest Shkurlatov granite deposit in the Voronezh region of central Russia.
According to analysts at Finam, one of Russia’s leading finance and construction research and analyst agencies, NQA accounts for about 20% of crushed stone production in the Siberian region and about 3% of the entire Russian market. Its sale to NNC will increase NNC’s share of the Russian aggregates market to 11-12%. Some analysts predict that figure could be even higher (by +3%-5%), although it
Loading and hauling work at a quarry operated by First Nerudnaya Company, Russia’s largest crushed stone producer

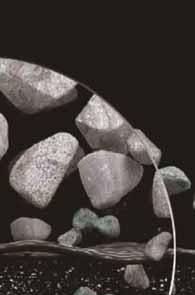
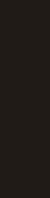

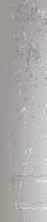
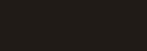
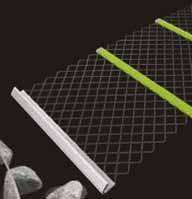


europe@majorflexmat.com

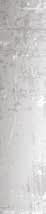

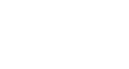
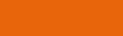
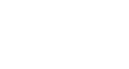

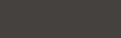




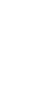



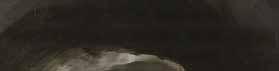
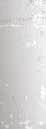






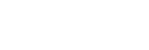














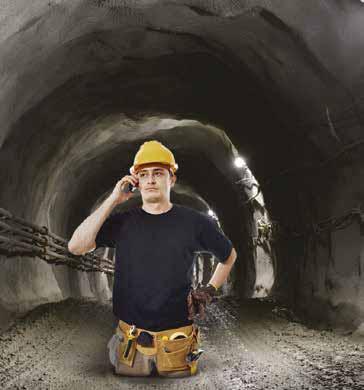

In addition to domestic producers, some global aggregates players are looking to increase their footprint in the Russian market
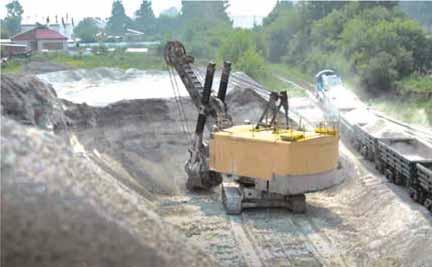
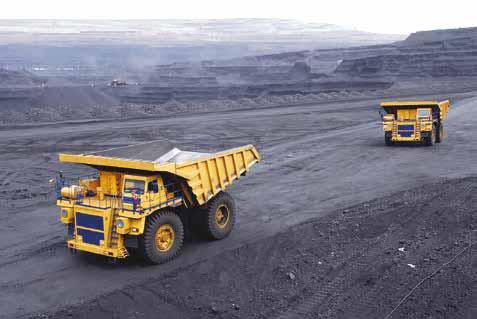
for building materials in the Russian market over the next few years.
Analysts all agree, though, that the NQA acquisition will prove a major long-term growth gain for NNC. A key factor behind that is the improving demand for crushed stone and other construction materials in Russia linked to the resumption of a number of national road infrastructure and housing projects. The majority of these projects involve massive building of residential housing in the country as well as implementation of other major infrastructure projects.
Despite the general economic slowdown in Russia, caused by the pandemic, the volume of crushed stone production in the country this year continues to grow.
In the meantime, NNC is not the only aggregates producer in Russia set to implement an expansion strategy in the next few years. According to some national aggregates market sources, notable growth plans are being considered by several other leading local players, including First Nerudnaya Company (FNC) headquartered in Yekaterinburg, Western Siberia, and Lenstroykomplektatsiya, a St. Petersburg, north-west Russia-based construction materials firm.
RIGHT: Denis Manturov, Russia’s Minister of Industry & Trade and the state official responsible for the development of the national aggregates industry

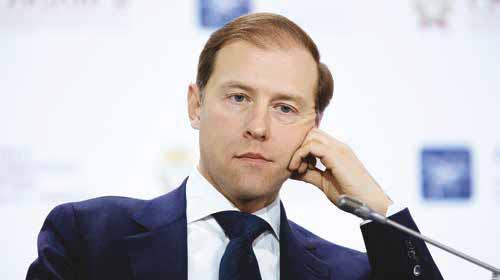
Further expansion ambitions have also been recently announced by some leading producers from Karelia - a republic in northwest Russia, which along with St. Petersburg, currently remains one of the great centres of Russian aggregates production. Last year the volume of aggregates production in the region grew by 3% compared to 2018. Prominent aggregates producers in that part of Russia also include LLC Karelprirodresurs, LLC Prionezh Mining Company, and LLC Lafarge Aggregates and Concrete.
The planned expansions are largely based on the accelerated enlargement of existing production capacities and the opening of new sites.
In addition to domestic producers, some global aggregates players are looking to increase their footprint in the Russian market to optimise their production and increase profitability. One such company is Lafarge, which at the end of last year completed a big management shake-up of Lafarge Aggregates and Concrete, its Russian aggregates subsidiary. According to some analysts, this will enable Lafarge to speed up its growth plans in the country.
Russian analysts also note the recently announced plans of some former Soviet countries to increase their supplies of aggregates to the Russian market.
For example, Turkmenistan hopes to become one of the largest producers and exporters of aggregates in the former Soviet region and Central Asia. To support this ambition, some Turkmen producers are already working on gaining a foothold in the Russian market.
Russian aggregates sector analysts believe an influx of cheap aggregates imports from former Soviet nations may lead to the change of balance in the Russian market and, under certain circumstances, result in a reduction in market share for many local manufacturers. Currently, imports account for only 4% of Russia’s local aggregates market.
Presently, aggregate remains one of the largest segments within the Russian construction materials sector, valued at RUB 211bn (€2.37bn) per year.
The construction season in most regions of Russia starts at the end of March and lasts until October. During this time, the level of utilisation of local producer-sourced aggregates is close to 100%.
Most local producers are still hopeful that demand for their products will completely recover in 2021, which will allow them to significantly increase their output. However, much will depend on the level of Russian government agency support on offer to the domestic construction industry. AB
A Russia Siberia-based quarry under the management of the Novosibirsk Quarry Administration
LEFT: BelAZ rigid haulers are used for transporting crushed stone from the fields of National Nerudnay Company sites
CASE rolls out upgraded telematics platform
CASE Construction Equipment has launched the latest version of its SiteWatch telematics platform.
The upgraded platform features an all-new dashboard, more intuitive navigation and new overview sections which the company says spotlight critical information without requiring the user to search extensively for the data.
The SiteWatch option can be ordered for all CASE equipment and is also available for the aftermarket as a retrofit with a subscription plan of one to five years.
CASE states that SiteWatch complies with the Association of Equipment Management Professionals (AEMP) 2.0 telematics standard, ensuring that the solution is compatible with mixed fleets.
Aggregate Industries launches ProLay asphalt system
Construction and infrastructure company Aggregate Industries has launched the ProLay system offering asphalt solutions tailored to specific applications.
The new system offers datacapture capabilities to drive project cost efficiencies and extend the life of pavements, with up to a 10-year warranty on approved applications.
Aggregate Industries says that, through a consultative approach and early involvement in a project’s design stage, its contracting division is able to carry out site investigations to identify and deliver tailored whole-life solutions via the ProLay system.
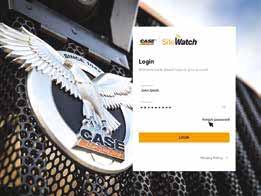
“The new CASE SiteWatch telematics platform presents users with a high level of critical data on a very clear and intuitive dashboard, whether you’re at your desk or on your tablet in the field,” says Marnix Korpershoek, construction equipment digital precision solutions and telematics sales & support manager Europe, CNH Industrial.
The new dashboard features an easy-to-read horizontal menu at the top of the screen above five widgets that focus on core operating information such as an equipment summary, equipment search, fuel level reports and alarm status. A dropdown menu provides main reports and fleet and maintenance overviews. Alerts for geofence, curfew and fault codes are also immediately visible in the dashboard.
CASE says that SiteWatch can help fleets of all sizes work more efficiently in many ways, including simplified fleet management. The operator always knows where each machine is, what its working status is and if maintenance or service is required. www.casece.com
The new service is designed to assist clients in identifying the right first-time pavement design solution, and smart surfacing technology captures the pavement data required to support asset management. The ProLay system comes complete with
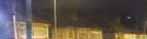
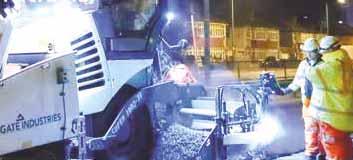
as-built digital data records and an end of warranty report (as applicable).
The ProLay System offers a new range of exclusive products that contain high-grade bitumen, that can be mixed at low temperatures to reduce CO2
The range includes the carbon-efficient ProLay Ultra 942 solution. Aggregate Industries says this is a specially designed asphalt that, in combination with rolling-resistance technology, leads to customer fuel efficiency.
Other versions are: ProLay Curve for high stress applications; ProLay Single, for thick lifts and self-regulating; ProLay Silent, an environmentally friendly ultralow noise solution; ProLay Grip Grip, an alternative to highfriction surfacing and ProLay Light, which contains Lytag - a low-density aggregate with a dense asphalt mix, making it an ultra-lightweight solution that is suitable for applications where weight restrictions apply. www.aggregate.com
Orba Group supplies wash-bear solution in UK & Ireland
Orba Group is the official UK/ Ireland dealer for wash-bear machinery, which is manufactured by Germany-based Moerschen.
The mobile wash-bear system is purpose-developed for the separation of light materials from heavier particles such as building rubble, and London-based Orba Group says it has proved to be an effective solution in quarrying,
Wash-bear can be used in quarrying, recycling, demolition and construction
recycling, demolition and general construction applications.
The wash-bear works according to the floating-sinking principle and is designed to reliably and cleanly separate light materials such as wood, artificial and insulating materials from the minerals.
Orba Group says that all mineral substances can be
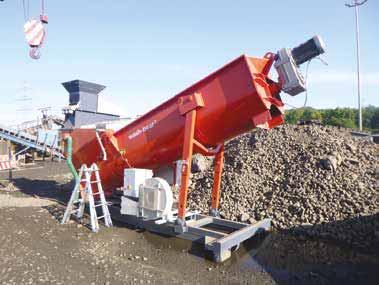
cleaned, but most of all, RCL building materials.
The closed system consumes whatever water adheres to the discharged mineral, meaning that in a 10-hour shift 4-8 m³ is used in practice, whereby the inlet is controlled automatically by floats. Orba Group says this technique avoids the build-up of chemicals in the eluate.
The water used is absorbed into the basic moisture of the RC material. What comes out with regard to the chemical composition, at most, is what was discarded by the rubble in the system. The energy expenditure is at around 8-15kW/h during operation, which is claimed to be significantly lower than an air sieve with a similar performance.
The wash-bear can be integrated into the overall process chain even on narrow construction sites.
www.orbagroupltd.com
The ProLay asphalt system is designed to cut CO2 emissions


Liebherr concrete mixing plant for smaller budgets
Liebherr has launched the new LCM 1.0 concrete mixing plant which is capable of producing up to 60m³ output per hour.
The Switzerland-based equipment manufacturer says it is reacting to market requirements as the demand for smaller, transport-optimised plants for a manageable budget is growing. It adds that concrete production with an in-house mixing plant is becoming more attractive.
In addition to stationary use, pre-assembled subassemblies and steel foundations make the plant suitable for mobile operation, for example on construction sites or leased land.
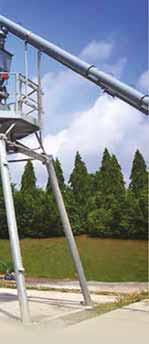
The plant can be operated by an intuitive control system via a laptop. Ascent and platforms are spacious and designed to ensure optimal accessibility, simplifying cleaning and service work. The Liebherr ring-pan mixing system enables an output of up to 60 m³ of fresh concrete, and various aggregate silos with a storage volume of 40 to 100 m³ are available.
The plant can be equipped with up to 3 cement silos (100 tonnes each). Optional equipment can be ordered including moisture measurement, ice scale, cladding and control container. www.liebherr.com
Magna expands Dutch-made range
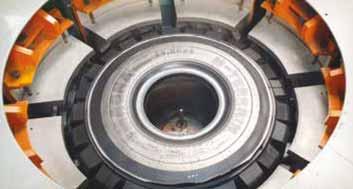
Magna Tyres has started producing its long-standing 29.5R25 M-Terrain E4/L4 tyre at its factory in the Netherlands for the first time.
The E4/L4 tyre is specifically developed for medium and large wheeled loaders and articulated
dump trucks. The M-Terrain tyre pattern is suitable for earthmoving equipment operating on challenging off-road surfaces.
Being manufactured in the Netherlands qualifies the tyre for the EUR.1 certificate, which enables Magna customers in some
All-terrain unit from Portable Vacuum Solutions
UK-based Portable Vacuum Solutions has provided an all-terrain vacuum unit to one of its quarry customers.
The customer in the west of England required a vacuum system that could be used to handle stone dust and spent stone from the conveyors feeding and discharging three large stone crushers at the quarry.
The requirements for the vacuum unit were strict. The site maintenance team needed to be able to use the unit at night, and it needed to be sufficiently powerful to handle dust and stone chippings over a significant distance. It needed to be easily towed into position by tractor and capable of being easily reversed as some locations had access issues.
The solution was provided by a powerful, trailer-mounted vacuum unit that Portable Vacuum Solutions had just taken delivery of from Italy. This 75kw diesel unit featured a 6m³ tipper-based collection tank and ticked the all-important environmental boxes with its filtration system.
The only problem was that this unit had been designed to be towed to site by a truck fitted with a 5th wheel, not a farm-type tractor fitted with conventional towing ball. To solve this issue the trailer’s running gear was re-engineered and the towing method was changed within a 10-day period.
www.portablevacuumsolutions.co.uk
countries to import it at a reduced or nil rate import duty under trade agreements between the EU and beneficiary countries.
This 29.5R25-size tyre has been in production at Magna’s factories outside the Netherlands for many years and the company says this will continue.
Magna says the demand from the market for ‘Made in Holland’ tyres is increasing strongly, in particular the 29.5R25 size. The company now produces three of the M-Terrain series domestically, ranging from 17.5R25 to 29.5R25.
The company comments: “With this latest release of the 29.5R25 E4/L4 tyre we serve to anticipate on current and future needs from our major mining and earthmoving customers.” www.magnatyres.com
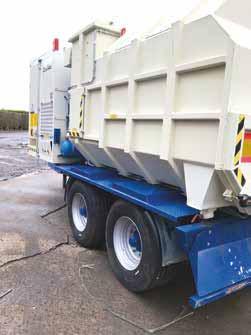
The trailer-mounted tractor vacuum unit
The LCM 1.0 mixing plant is suitable for stationary and mobile operation
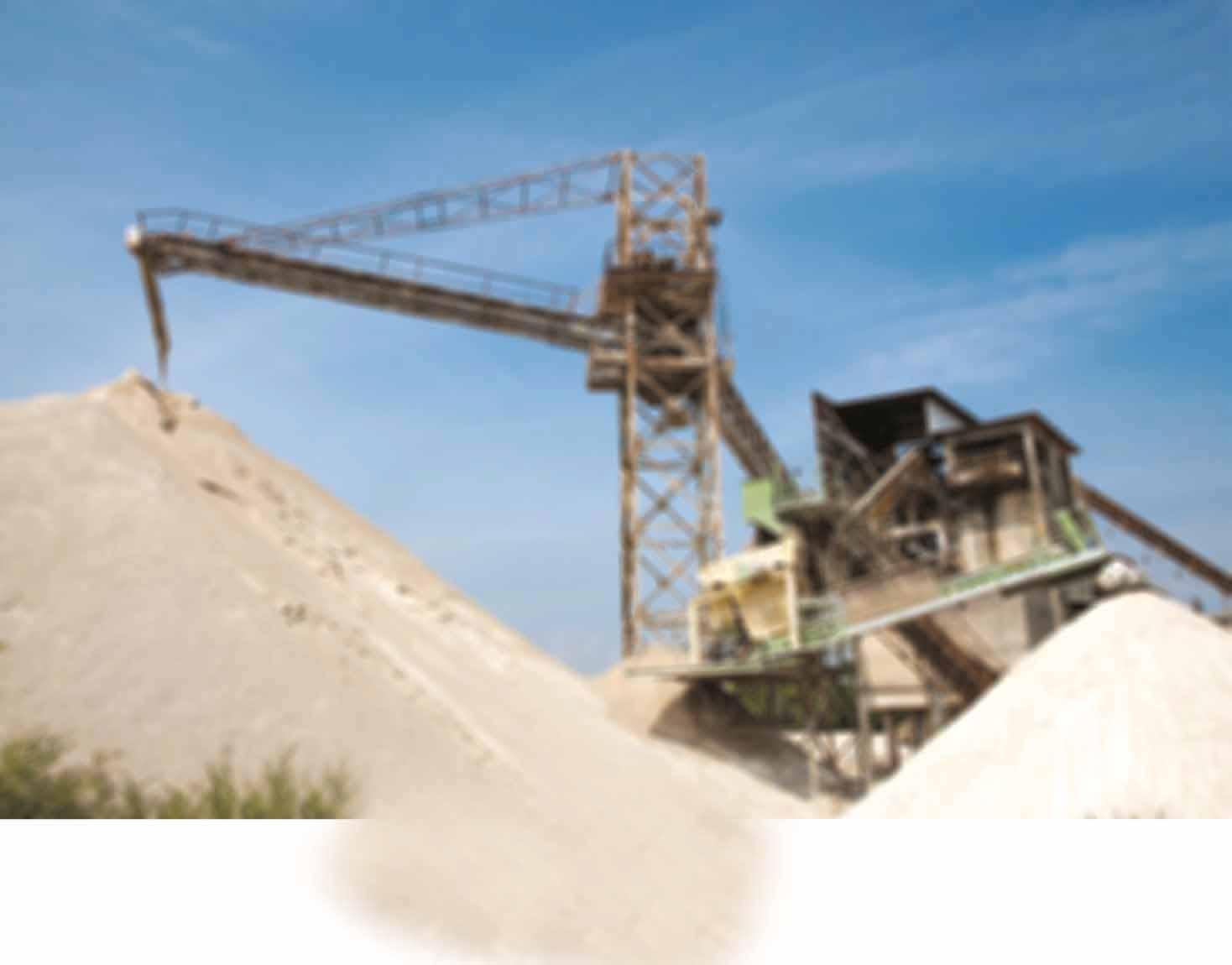


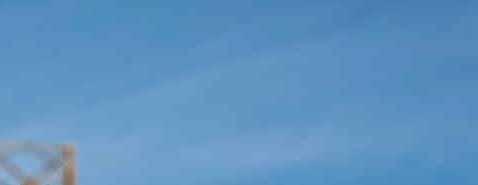
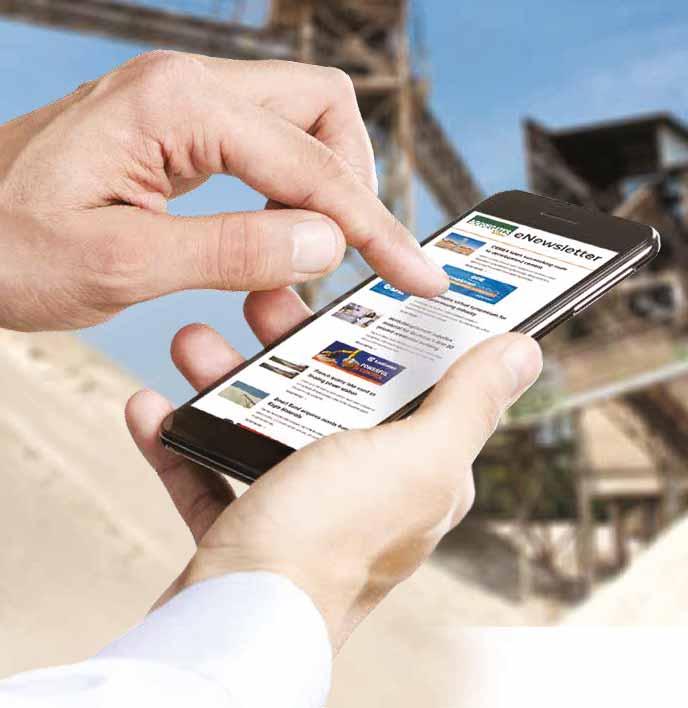




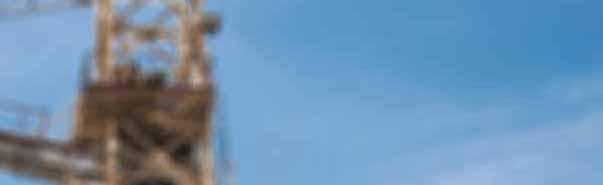
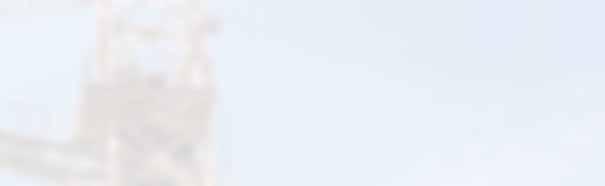

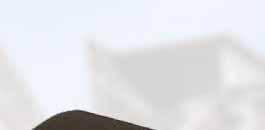

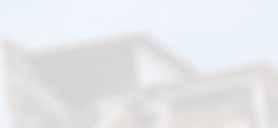
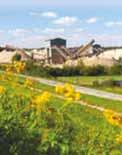

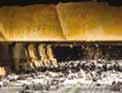

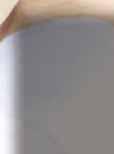
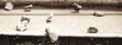



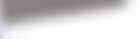
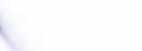

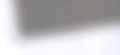


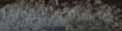
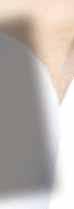

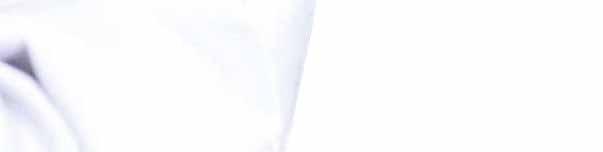

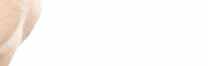
2020
NOVEMBER
24-27 bauma China
Shanghai, China
Organiser: Messe München Tel: +49 89 949-20252 info@bauma-china.com https://www.bauma-china.com
2021
FEBRUARY
23-26 bauma Conexpo India
Gurugram/ New Delhi, India
Organiser: AEM and Messe München Tel: +49 89 949-20251 info@bcindia.com https://www.bcindia.com/en
MARCH
03-07 SaMoTer Verona, Italy
Organiser: Veronafiere S.p.A. Tel: +39 045 8298561 customercare@samoter.com http://www.samoter.it
APRIL
14-17 steinexpo 2021
Homberg/Nieder-Ofleiden, Germany
Organiser: GEOPLAN GMBH
Tel: +49 7229 606 30 info@geoplangmbh.de https://www.steinexpo.eu
19-24 INTERMAT
Paris, France
Organiser: Comexposium laura.sanchez@comexposium.com https://paris-en. intermatconstruction.com
MAY
25-28 bauma CTT Russia Moscow, Russia
Organiser: Messe München Rus Tel: +49 (0)89 949 20251 info@bauma-ctt.ru https://bauma-ctt.ru
JUNE
22-24 Hillhead
Hillhead Quarry, Buxton, Derbyshire, England
Organiser: The QMJ Group Tel: +44 (0)115 945 4377 Email: Harvey.sugden@qmj.co.uk https://www.hillhead.com
JULY
07-10 EIG 2021
Exeter, UK
Organiser: EIG Conferences marcus.dorey@hanson.biz https://www.eigconferences.com/ future-conference-2020
SEPTEMBER
15-18 Construction Indonesia
Jakarta, Indonesia
Organiser: PT. Pamerindo Indonesia Tel: +49 3999905 0 contact@merebo.com https://ci.merebo.com
OCTOBER
13-16 bauma CONEXPO AFRICA
Johannesburg, South Africa
Organiser: AEM and Messe München GmbH Tel: +49 89 949 21480 johannes.manger@messemuenchen.de https://www.bcafrica.com
MEET THE TEAM
Aggregates Business travels the globe attending conferences, events and equipment shows, keeping you informed of the latest offerings. Come and join us for a chat at any of the events below.
JUNE 2021
22-24 Hillhead 2020 Hillhead Quarry, Buxton, Derbyshire, England
JULY 2021
07-10 EIG 2021 Exeter, UK
These dates were correct at the time of going to press, but please note that the COVID-19 pandemic means some events may be rescheduled with little advance notice
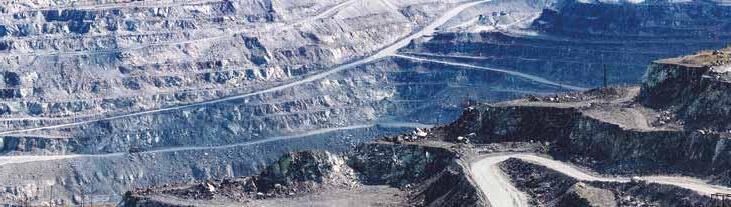







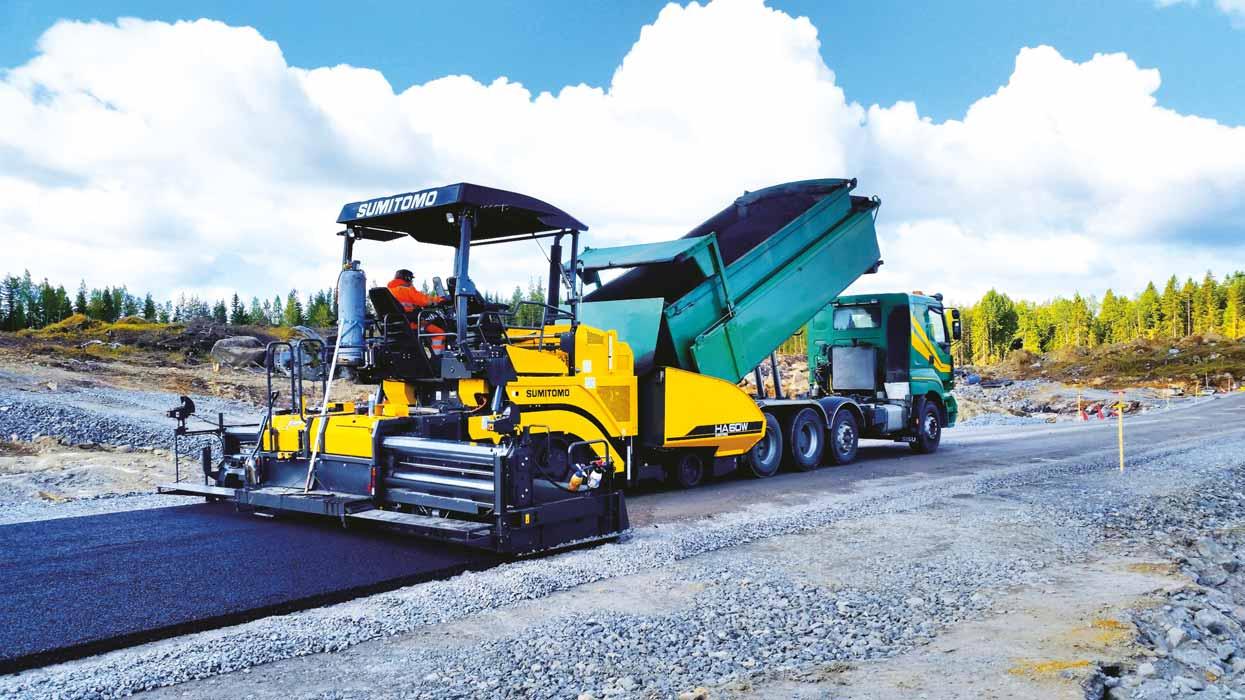
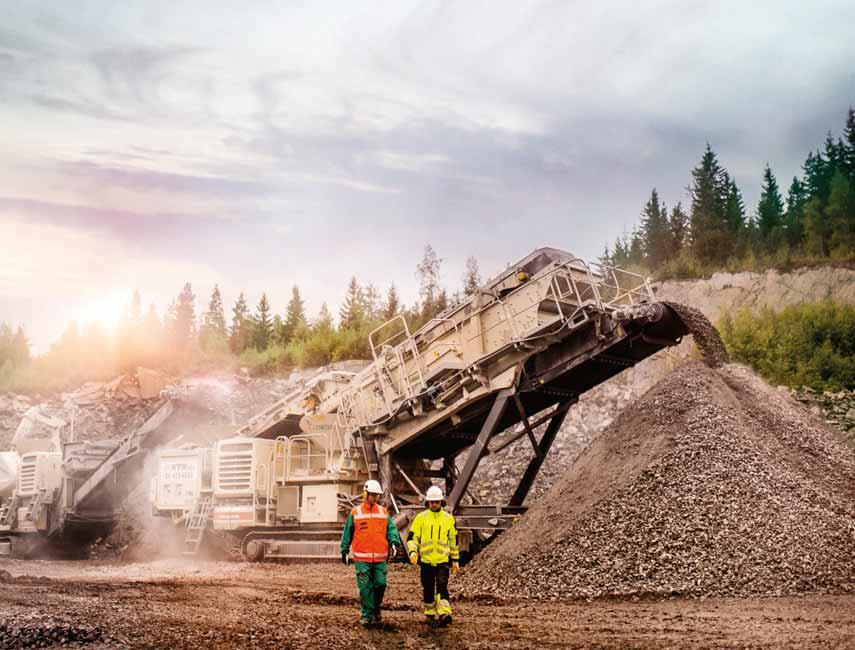
Looking for a long-term partner? Look no further.
Aggregates production is demanding on your crushers and screens. performance is not easy.
Metso Outotec has designed wear and spare parts that are built to last even under heavy duty applications. We have also upped our game with some of the highest crusher parts inventory levels in the business, for parts that are available when you need them most.
With an Equipment Protection Services (EPS) plan, you also gain extended warranties, inspections and remote monitoring with Metso Metrics Services for maximum performance. Today and into the future.
Partner for positive change.
mogroup.com
Visit our webpage