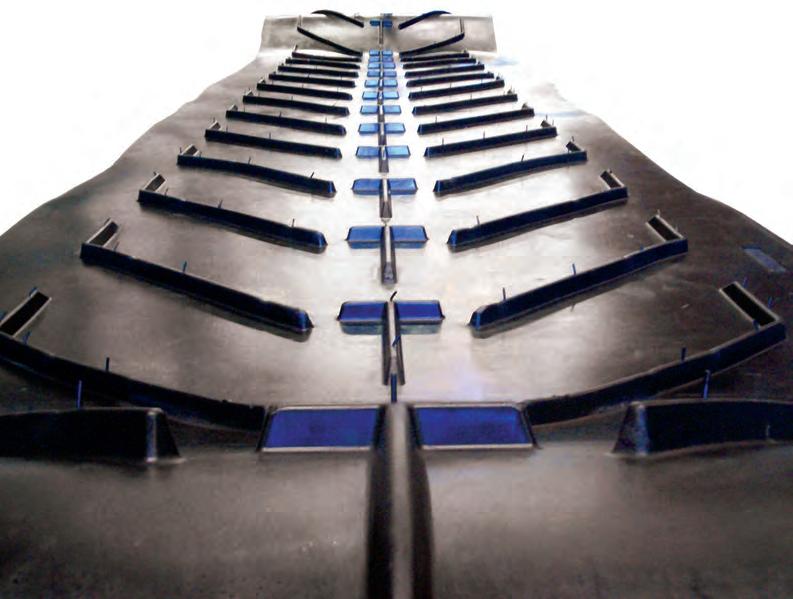
3 minute read
Brushing up on belt cleaners
Thomas Greaves, Managing Director of DYNA Engineering on the benefits of brush cleaners for conveyor systems.
A Chevron rubber conveyor belt.
CONVEYOR BELT CLEANING
cleaning equipment today is a diversified range of specialised types of cleaning devices. Each has been designed to be effective for the material being conveyed. This ensures it will deliver the best result in removing carryback and fugitive material from the belt before it causes excessive wear or damage to the conveying system.
Brush cleaners
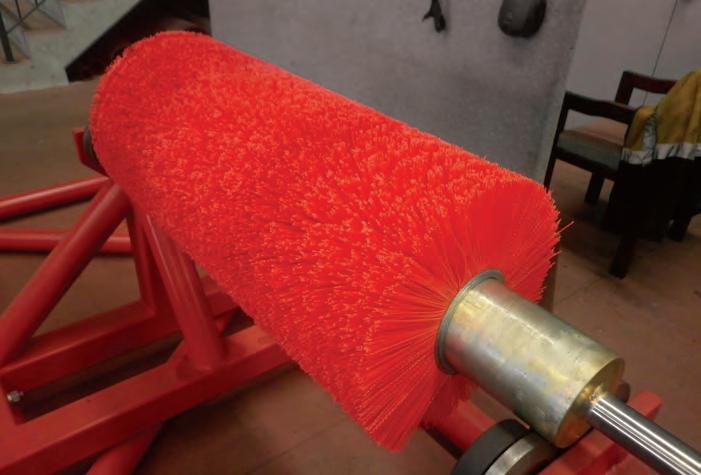
As the name suggests, a brush cleaner is a conveyor cleaning product designed to clean conveyor belts with a sizeable brush. It is usually connected to a gear box and motor which causes it to consistently rotate. It can be driven in either direction to provide the best clean possible with its large bristles which sweep the surface of the belt to remove excess material.
Although brush cleaners can be used on all conveying applications, they are most effective when the material being conveyed is dry and granular, or where the material may be sticking to the belt surface by way of static charge or by some adhesive properties of the material. They are particularly suited to conveyors transporting fine particle materials such as mineral sands, cement, salt, sugar, fertiliser, dust, wood chips and other fine powders.
Brush cleaners are ideal for belts which do not have flat surfaces. They are also suitable for reversing belts. Normal scraper cleaners are not effective in both these cases.
Some examples of non-flat conveyorbelts are:
• Grooved rubber belt • Cleated rubber belt • Mechanically joined conveyor belt (the metal clips can get caught in conventional scraper cleaning products) • Chevron rubber belt
The bristles on a brush cleaner are able to weave in and out of troughs and up and down raised sections of non-flat belts without increasing the wear or reducing the service life. The bristles are supple and able to clean without becoming caught on anything and potentially damaging the conveyor belt.
They can be used in conjunction
DYNA Engineering brush cleaners are spiral bound, providing superior cleaning efficiency compared to other types of brushes.
Brush cleaners can be rotated in either direction, depending on the best cleaning action.
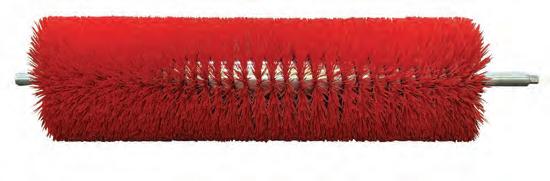
with a primary scraper when the initial material may be too high for the brush cleaner alone.
Unlike conventional belt scrapers, brush cleaners can handle metal-clipped belts, as well as worn or repaired belts, without suffering loss of brush life. This results in lower maintenance costs and shorter planned shutdown times.
Another situation which brush cleaners are suited to is in confined space applications. When space is limited and conventional cleaning products such as scrapers and spray bars are difficult to install and maintain, brush cleaners can be a simpler and less expensive solution. They are easy to install and can be designed to fit in just about any space.
Locally made
DYNA Engineering’s brush cleaners are designed and fabricated at the company’s workshops in Bayswater, Western Australia, so long and costly shipping times and unexpected delivery delays, as can be encountered with imported ones, are never a problem. Quality is also guaranteed as all the steelworks in DE brush cleaners are fabricated “in-house” and the brush/bristles componentry is closely checked for consistence in maintaining or exceeding Australian standards. This doesn’t always occur with imported units.
Additional features
DYNA’s Brush cleaners can be fitted with many types of bristles for a large range of applications. This includes hard, soft, short, long, anti-static, natural fibre and even wire. Match these with different directions and speeds, and the variants are endless.
Another feature is that brush wear can be adjusted by the built-in adjuster mechanism.
DYNA Engineering has been specializing in the design and manufacture of quality conveyor components since 1986. The company’s key business focus now is on innovations for bulk material companies to be able to operate their conveyor systems while improving the environmental impact of their operations.