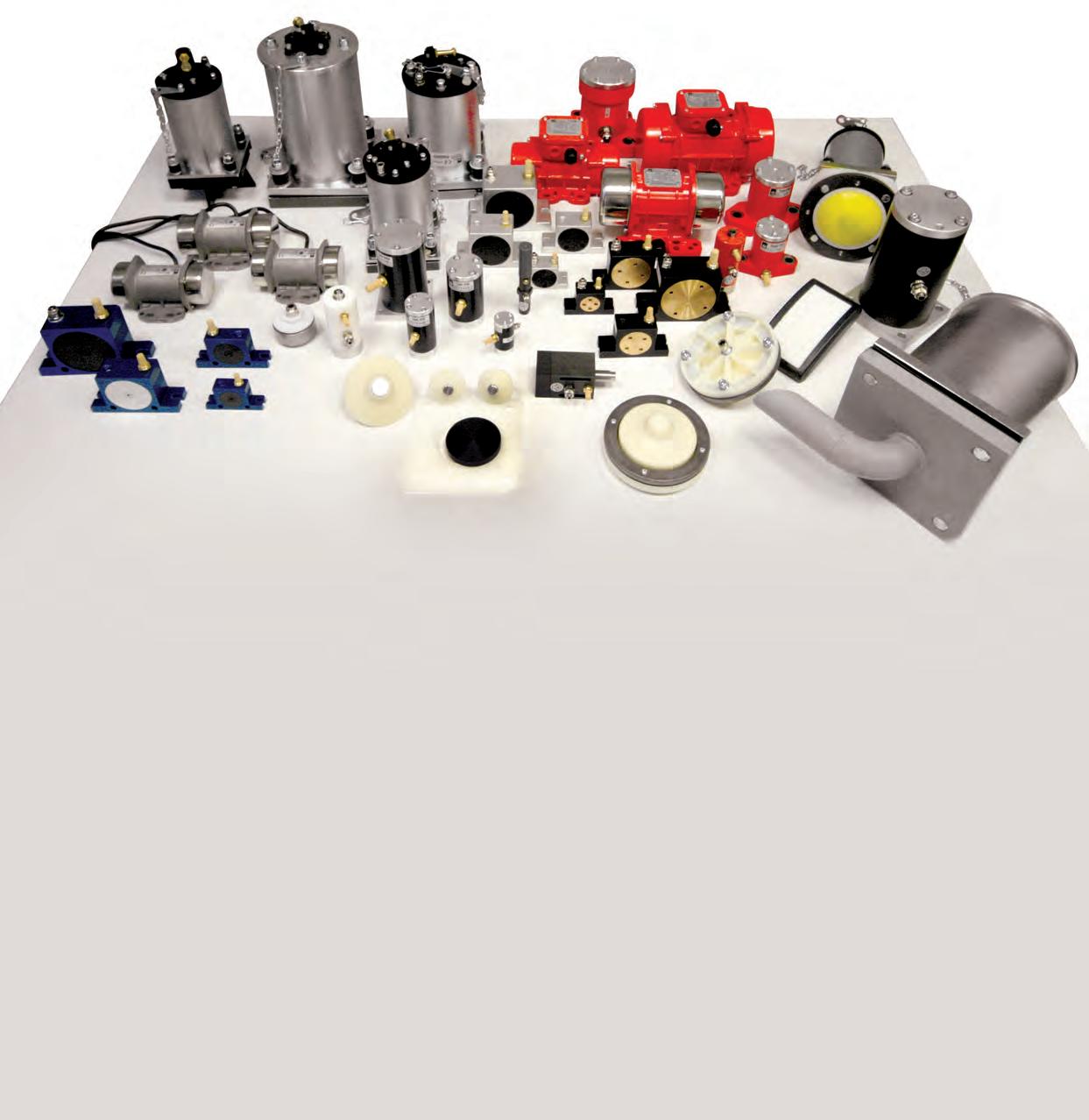
4 minute read
Bulk packaging sorted with Oli Vibrators
Mark Thompson, Director at Oli Vibrators, explains how industrial vibrators can help reduce waste andimprove consistency on packaging lines.
Oli’s product range is rated at a T4 Temperature Rating and are IECEx and IP66 rated.
AN AUSTRALIAN BISCUIT
company faced a dilemma. It was producing an enormous amount of waste due to product degradation during the packaging process.
As the biscuits were straightened to line up in the package, many would break. To solve the problem, the company reached out to vibration specialists, Oli Vibrators.
Mark Thompson, Director at Oli Vibrators, says after installing Oli’s vibrators, the company was able to save almost 98 per cent of what used to become waste.
“When it comes to packaging, customers are looking for two main things: reasonably high, reliable speeds and accuracy,” he says.
“Our vibrators can be used to help straighten products before they go into a bag or box, or to consolidate light and fluffy products such as flour before they are packed into a bag.”
Because packaging is a broad industry, Oli Vibrators are used across many industries. Thompson says the vibrators have been used to line up metal tops for cans, help thread prawns onto skewers, and help pack icing sugar.
With so many different products and industry, the company works closely with its customers to learn as much as they can about the process. Often the customer will provide a checklist of important information along with some technical drawings to get started.
Knowing he characteristics of the material is also vital for success, as different bulk densities, weights, stickiness, and temperature can change the parameters of what is needed.
With that information, the company’s engineers will usually find a solution that will work for the customer within 24 to 48 hours.
Thompson says it’s important to install the right tool for the application, as not all vibrators will do the job a customer wants.
“We once had a customer who wanted the biggest vibrator we had. We told them that they could get what they were looking for out of a smaller vibrator that was half the size. Using the larger vibrator could have done damage to the machine – bigger
isn’t always better,” he says.
“Knowing what the process is also keeps maintenance to a minimum. If a vibrator is being used move 800 kilograms of materials instead of the 600 kilograms it was designed for, it won’t be as effective.”
One specific task that vibrators can assist with is microbatching. This is where gentle vibrations are used to ensure the screws on a screw conveyor are full, to prevent bridging. This helps to keep the feed rate reliable and effective.
Oli Vibrators ensures its own equipment can be relied on with rigorous testing at the company’s global manufacturing facilities. Oli Vibrators’ parent company, Oli SpA, recently opened its new headquarters in Medolla, Italy, which will be used to coordinate the firm’s international branches.
The new facility features advanced manufacturing equipment and uses high quality materials to provide assurances of reliability to its customers. Its product range is rated at a T4 Temperature Rating and are IECEx and IP66 rated. In addition, all its equipment has a two-year warranty, which includes full replacement or repair.
Thompson says the manufacturing process for the vibrators uses state-ofthe-art technology and testing.
“We claim to have a price to performance ratio that is second to none,” he says. “It’s part of our goal to

The company supplies vibrators that offer three kilograms of force up to 26,000 kilograms.
Vibrators have been used to compact icing sugar into bags.
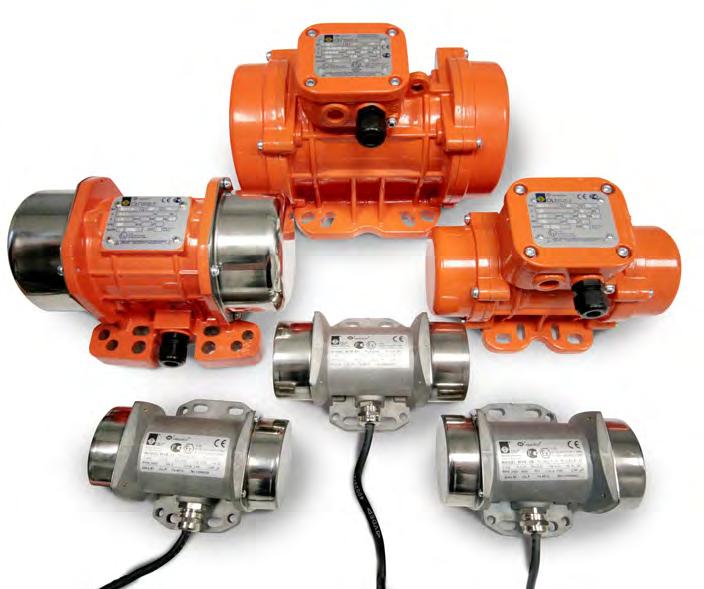
remain affordable and available.”
The company works closely with the bulk handling industry to supply vibrators that offer three kilograms of force, up to 26,000 kilograms. Its equipment is used on hoppers, bins, feeders, chutes and conveyors for several reasons.
The company has operated in Australia for more than two decades and has built up expertise in providing the right tools for the job. Thompson says Oli Vibrators’ staff are knowledgeable about its products and know how to apply them to all kinds of situations.
“They’re also virtually maintenance free and easily replaced. Once fitted, they go about their business based on the operation. They can be programmed to work in conjunction with the process and are energy efficient.”
Oli Vibrator’s mission statement is ‘when you need it, where you need it’. To deliver on that, the Australian business keeps plenty of spares on hand if required and can call upon the global company’s trading subsidiaries.
Thompson says the Australian branch has stocked up significantly for the new year and have several new products they are working on for its electric and pneumatic range.
“Oli Australia is here to help with any vibration problems and have a good team of engineers ready to assist,” he says.
“We’ve made sure to increase our local stock holding to ensure we have adequate supplies.”