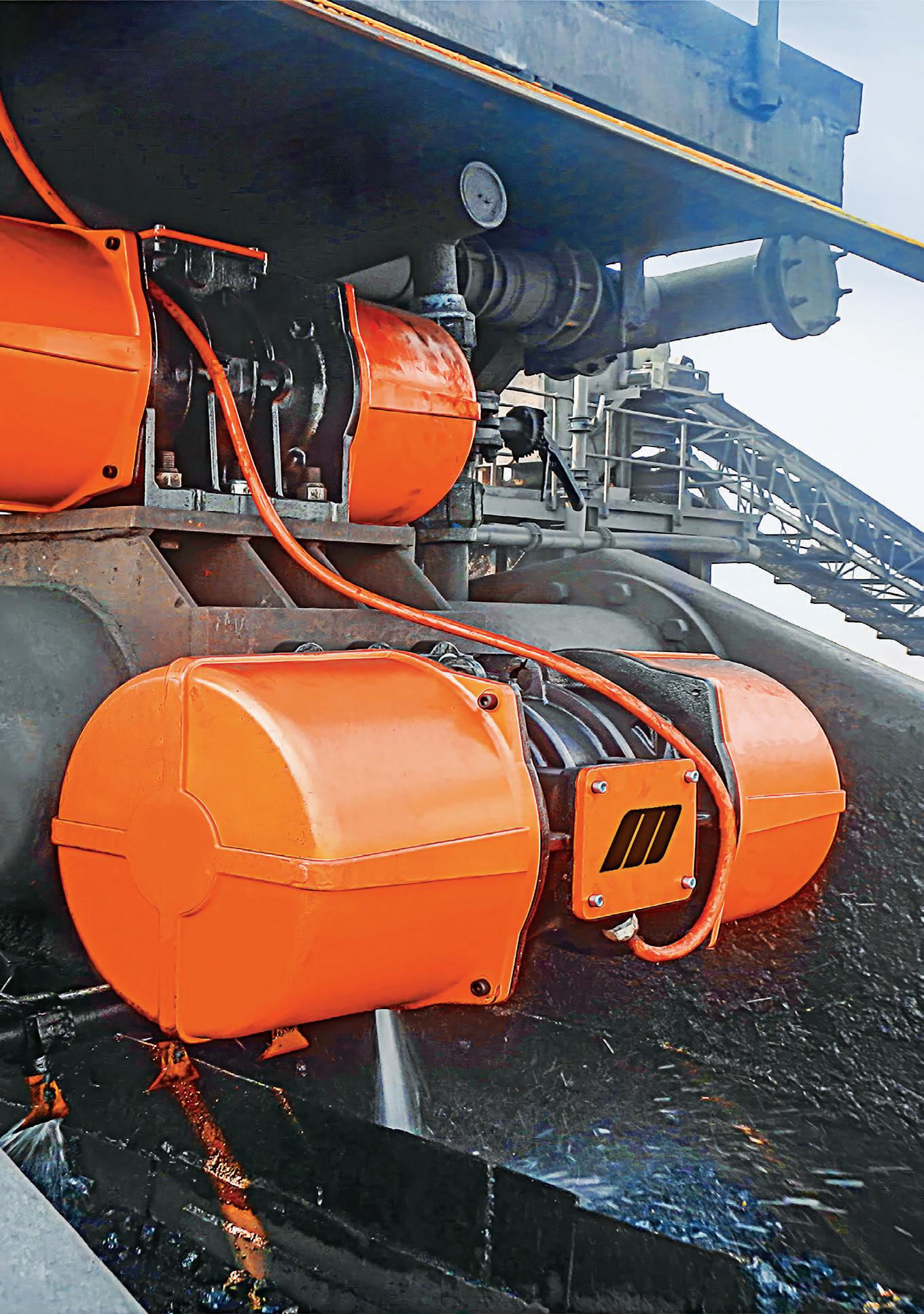
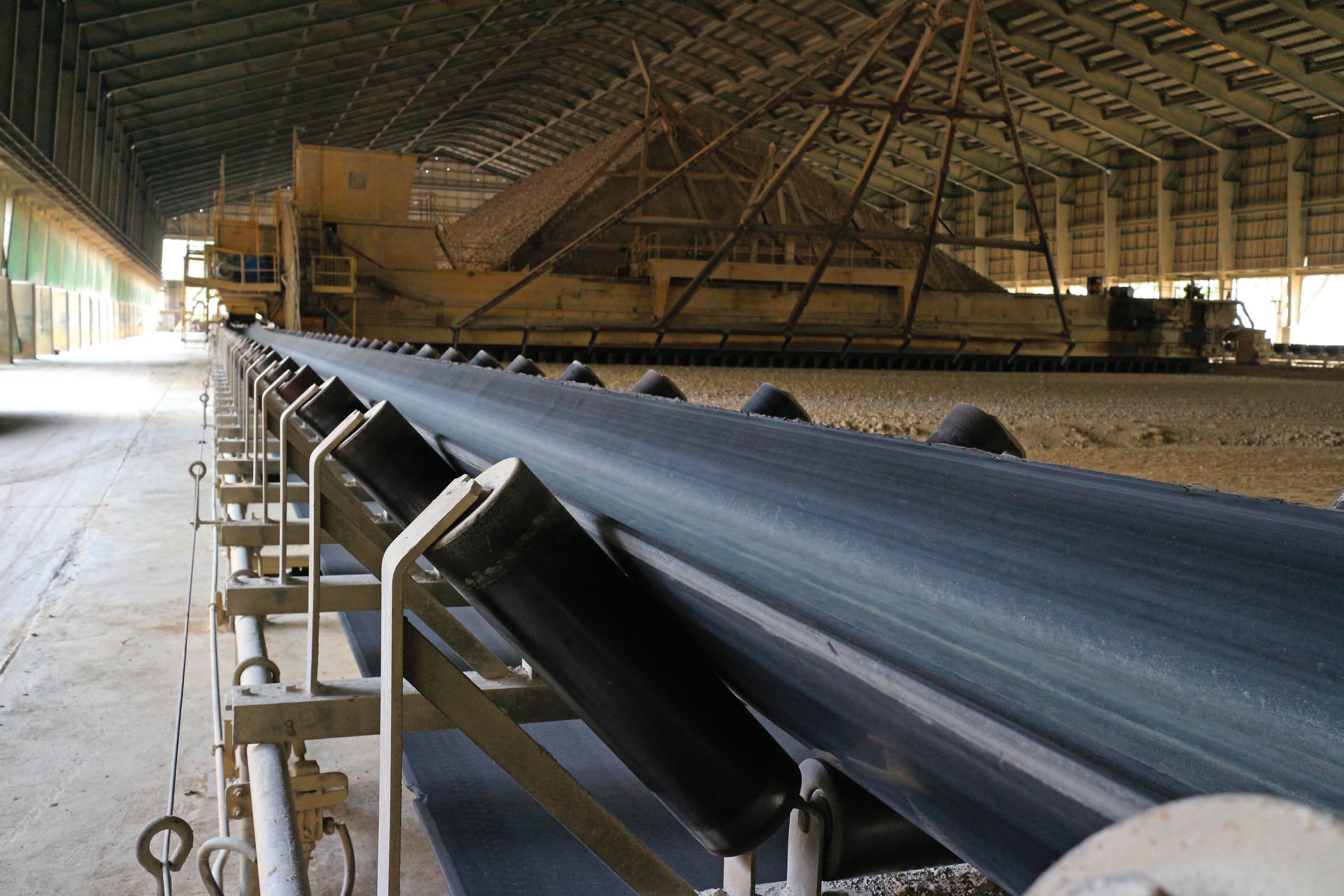
VORTEX DESIGN PHILOSOPHIES:
Vortex believes in offering only value-added products that are designed for purpose, rather than producing off-the-shelf, commodity components. With an in-house team of application engineers, Vortex designs for the most demanding applications.
Vortex closely studies the characteristics of thousands of dry bulk materials and how they interact with various materials of construction. We assess the wear potential for each client’s process and make application-specific modifications to ensure reliability, durability and longevity.
Our priority is to keep you up and running – because in your world, there is no time for downtime. Vortex components are engineered with in-line service features that accelerate the system maintenance process, saving your team time and money.
Vortex approaches wear parts with simple, durable design. Doing so means maintenance procedures are also kept simple while the need to perform maintenance is infrequent. This leads to a reduction in spare part inventories and a reduction in costs.
End users are often attracted to equipment on the fallacy of low price, ignoring the cost-benefits of reliability and longevity. Vortex believes in designing products that will out-perform and outlast market alternatives – so that end users realize the full value of their investment.
Facilities have an ethical obligation to protect against the hazards of manufacturing. Vortex closely studies trends in air quality, environmental dust emissions, workplace safety and evolving regulations. Our components are designed with these concerns in mind.
48
Published by:
379 Docklands Drive
Docklands VIC 3008
T: 03 9690 8766
www.primecreativemedia.com.au
COO
Christine Clancy
E: christine.clancy@primecreative.com.au
Editor William Arnott
E: william.arnott@primecreative.com.au
Assistant Editor: Adam Daunt
E: adam.daunt@primecreative.com.au
Business Development Manager
Rob O’Bryan
E: rob.obryan@primecreative.com.au
Client Success Manager
Janine Clements
E: janine.clements@primecreative.com.au
Head of Design
Blake Storey
Design
Laura Drinkwater
Subscriptions
T: 03 9690 8766
E: subscriptions@primecreative.com.au
www.bulkhandlingreview.com
The Publisher reserves the right to alter or omit any article or advertisement submitted and requires indemnity from the advertisers and contributors against damages or liabilities that may arise from material published.
© Copyright – No part of this publication may be reproduced, stored in a retrieval system or transmitted in any means electronic, mechanical, photocopying, recording or otherwise without the permission of the publisher.
And just like that, we’re more than halfway through the decade already. Welcome to 2025, a lot has changed, but even more has stayed the same.
It’s pretty safe to say the 2020s will be remembered through the lens of COVID-19. The pandemic caused levels of global disruption that had not been seen for decades, changing how people lived their lives.
It also led to a massive shift in how people work. While thousands of people moved to work from home, roads still needed to be built, food still needed to be made, and ore still needed to be mined.
Bulk handling was a core part of many critical industries, moving the raw materials needed to keep society functioning while everyone else was cooped up inside.
Lockdowns also highlighted some of the long-term challenges that have plagued the bulk handling sector for years.
In particular, it became very apparent that labour was in short supply, especially in niche sectors that require high levels of expertise.
The ageing industry has also highlighted how important it is to support the next generation of engineers.
Engineers Australia CEO Romilly Madew said the organisation’s analysis of engineering in Australia revealed a deepening skills crisis.
“As the world continues to embrace technology and systems, becoming more sophisticated and interdependent, our economy and society are more reliant than ever on the engineering profession. This report reveals a growing gulf, with Australia sliding towards a ‘new norm’ of an economy hampered by an engineering skills shortage,” she said.
“The implications range from delays to nation-building projects, stifled productivity, and low growth; failing to reach our net-zero goals and missing out on the next wave of wealth creation in ecotechnology and innovation.”
The future of Australian bulk handling depends on collaboration between governments, industry, the education sector and professional associations to overcome the challenges facing the sector.
Arnott Editor
INTRODUCING AN EASY WAY TO PROTECT YOUR WORKERS AS WELL AS PROTECT YOUR INVESTMENT INTO YOUR EQUIPMENT.
THE CONVEYOR SAFETY SYSTEM™ IS AN EASY, COST EFFICIENT WAY TO GET PEACE OF MIND AND PROTECTION FOR CONVEYOR EQUIPMENT. BY BUNDLING OUR MODEL RS MODEL TA BELT ALIGNMENT SWITCH, MODEL DB DAMAGED BELT DETECTOR WE HAVE YOUR WORKERS AND EQUIPMENT COVERED. COUPLE THAT WITH ADDING ONE OF OUR MOTION SWITCHES (MAG-NEAT-O™ OR MODEL CMS), YOU CAN FEEL CONFIDENT KNOWING THAT YOUR SYSTEM AND WORKERS ARE PROTECTED FOR A FRACTION OF THE COST OF DOWNTIME, REPAIRS AND REPLACEMENT EQUIPMENT.
event in July 2024, the Papua New Guinea Industrial and Mining Resources Exhibition and Conference (PNG Expo) is set to return in 2025. The event will be held at the Stanley Hotel in Port Moresby from 2–3 July, and off ers attendees plenty of networking opportunities, including a gala dinner and welcome drinks.
Prime Creative Media marketing manager of mining events Rebecca Todesco said the team looks forward to welcoming even more exhibitors and attendees to the 2025 event and networking opportunities.
“Creating bespoke networking opportunities for our sponsors is a benefit
of the event being located in at a highquality hotel in PNG,” she said.
TriCab, a premium supplier of high-performance flexible cable and accessories and a silver sponsor of the 2024 event, has renewed its sponsorship for 2025.
TriCab Queensland state manager Shane Plumridge said the company is keen to showcase its commitment to supporting and growing the blooming PNG sector.
“At TriCab we pride ourselves on supplying premium, high-performance flexible cable and accessories that reflect our values of innovation and quality,” Plumridge said. “Providing engineered cable solutions, which save our customers time and cost, is where we make our difference. At TriCab, we listen and respond to a range of customer needs, remaining innovative in our operations to ensure we can meet demands of all markets, existing and emerging.”
Plumridge said the company was proud to be a silver sponsor at the 2024 expo, being able to showcase its products
and people to the interested attendees.
“The ability to see people from the local area in the one place all with the same values, who were looking for new and innovative products and services, was a tribute to the organisers,” Plumridge said.
“It gave TriCab the ability to expose our vision of demonstrating our capabilities in the growing demand for the mining market in PNG.”
Plumridge is encouraging all stakeholders involved in the mining and industrial support channel to attend the 2025 event.
“The organisers have created a concentrated group of suppliers in a safe and easy-going atmosphere, where the cream of the mining supply chain providers are showcasing innovative products,” he said.
“Events like the PNG Expo are vital in bringing like-minded consumers and suppliers together in the one space where it is mutually beneficial to all parties, in a relaxed and safe environment.”
AUSTRALIAN MINISTER FOR infrastructure, transport, regional development and local government, Catherine King, formally opened TasRail’s federally funded $82 million Shiploader Project at an offi cial event at the Port of Burnie.
Tasmanian premier, Jeremy Rockliff, Labor senator for Tasmania, Anne Urquhart, mayor of Burnie, Teeny Brumby, as well as key customers, stakeholders and contractors attended the event.
TasRail CEO, Steven Dietrich, said the official opening was a result of a shared objective between all levels of
government – federal, state and local.
“We are immensely grateful for all the support that this project has, and continues to receive,” Dietrich said.
“The new shiploader will provide certainty to TasRail’s existing customers and help attract investment into new mining projects in the state.
“Importantly, our shiploader was built by Tasmanians for Tasmanians. At the peak of constructions, the project employed an estimated 140 people across a range of businesses across the state.”
TasRail’s Shiploader directly loads a range of bulk commodities and is connected to the rail and road
network via TasRail’s Bulk Minerals Export Facility.
In the last financial year, TasRail shiploaded 575,047 thousand tonnes of minerals for export.
• Providing complete packages to receive, store, and feed bulk materials with precision and reliability
• Offering site audits, troubleshooting, and refurbishment or upgrade options
Accurately feeding troublesome materials like beta-spodumene into a mixer at a precise mass feed rate requires a reliable Loss-In-Weight
With years of expertise in designing large screw feeders, we recently delivered a custom solution for an expanding WA lithium mine.
• Abrasion-resistant materials to ensure durability and mass flow
• A vented filling screw to manage displaced air efficiently
• Emergency discharge outlet for easy removal of off-spec material
Looking for a feeder system tailored to your challenging applications? Contact us today to discuss your project.
• accurate control of poor flowing materials
mass flow rates from 20kg/hr to 120 TPH
automated construction and demolition waste plant is dramatically improving waste recovery rates in the Brisbane metropolitan area.
The hybrid plant, which integrates both wet and dry processes, helps capture high-value construction materials that would have otherwise gone to landfi ll. Washing specialists CDE designed and engineered a wet
processing solution that integrates with the Turmec-supplied dry processing system.
The interconnected system can accept a wide range of highly variable waste streams, including
commercial skip and bin waste, C&D waste, hydro excavation waste, concrete, and excavated fi lls.
Linked by a network of conveyors, waste materials transition between the wet and dry systems without manual input. First, feed material is processed via Turmec’s dry mixed recyclables plant to separate fi nes and removes contaminants before passing through CDE’s wet processing plant to produce a range of washed and graded recycled sand and aggregate products.
CDE Australasia general manager Daniel Webber said it’s the fi rst time two systems of this kind have been brought together in this way, under one roof.
“This really is uncharted territory,” Webber said.
“It’s living proof that wet and dry waste recycling can coincide, and it highlights the power of collaboration because the results are undeniable.”
The facility has a maximum
processing capacity of 475 tonnes of C&D waste per hour – equivalent to 1.5 million tonnes per year.
Rino Recycling general manager Daniel Blaser expects it to reach full capacity in the next 12 to 18 months.
“We’re currently operating at around 50% of our total capacity, but this is steadily increasing to the point we anticipate reaching full capacity by the end of 2025,” Blaser said.
“A major component of the work we’re doing is about educating the industry about the potential of recycled construction materials. We’re making a very strong case in favour of recycled sand and aggregate.
“More and more are adapting and as that increases so too will our capacity to meet that growing demand. We see a greener, cleaner future just over the horizon and are steadfast in our commitment to see it realised.”
C&D waste accounts for 38 per cent of all waste generated in Australia and in the year 202021 the sector produced 29 million tonnes of waste, according to fi gures from the Department of Climate Change, Energy, the Environment and Water.
Webber said the location of the plant is also supporting the construction industry.
“Historically in this region trucks had to travel considerably long distances to access resource recovery facilities,” Webber said.
“It essentially made waste recycling a cost-prohibitive exercise. This solution and its proximity to Brisbane’s central business district – the beating heart of many major infrastructure projects – will help reduce the sector’s carbon footprint by tackling the waste burden, repurposing materials, and limiting the need to extract new raw materials.”
Corporation has completed the Narrabri to Turrawan Line Upgrade just in time for what’s anticipated to be one of the largest grain harvests for farmers in north-west New South Wales.
Fully funded by a $44.7 million investment from the Albanese Government, the rail upgrade between the Hunter Valley and Narrabri North significantly improves freight efficiency and connectivity in the region.
It also aligns seamlessly with the future interface of the Inland Rail at Narrabri North, positioning the region as a key hub for freight movement across NSW and beyond.
“The Albanese Government is proud to have fully funded this critical upgrade, which will be an important link between Northern NSW, Inland
Rail and the port of Newcastle,” Infrastructure, Transport, Regional Development and Local Government Minister Catherine King said. .
“These improvements not only strengthen the rail network but also boost economic growth by facilitating the transport of grain and other freight.
“This means more grain and goods can be transported in a single trip, providing smoother connection and reducing transportation costs.”
The upgrade supports heavier train loads, allowing each train to carry more freight – up to 25 tonnes per axle, increasing the total weight bearing load for each train while enabling trains to travel at up to 80 kilometres per hour.
The 35-kilometre project involved
the replacement of outdated steel and timber sleepers with heavy-duty concrete sleepers, upgrading existing rail and associated civil works.
“The completion of the Narrabri to Turrawan Line Upgrade is a significant boost for the NSW northwest communities and the broader economy,” Australian Rail Track Corporation CEO and managing director Wayne Johnson, said.
“This improves efficiency of logistics for agricultural producers and freight movers, helping them and the communities where they operate to be more sustainable.
“We extend our gratitude to all stakeholders involved in this project, including our customers and the Australian Government, for their collaboration and support in delivering this essential upgrade.”
AUSTRALIAN ENGINEERS HAVE found a way to make stronger, crackresistant concrete with carpet fi bres.
Lead researcher Chamila Gunasekara from RMIT University said the team had developed a technique using waste carpet fibres to reduce early-age shrinkage cracking in concrete by up to 30 per cent, while also improving the concrete’s durability.
Published in the Construction and Building Materials journal, the team has shown that waste carpet material can be used to improve concrete.
“Cracking in early-age concrete slabs is a long-standing challenge in construction projects that can cause premature corrosion, not only making a building look bad but also risking its structural integrity and safety,” Gunasekara said.
“Scrap carpet fibres can be used to increase concrete’s strength by 40 per cent in tension and prevent early cracking, by reducing shrinkage substantially.”
Laboratory concrete samples have been created using the various textile materials and shown to meet Australian Standards for engineering performance and environmental requirements.
Gunasekara said the disposal of
carpets and other textiles including discarded fabrics poses an enormous environmental challenge.
“Australia is the second largest consumer of textiles per person in the world, after the US. The average Australian purchases 27kg of new clothing and textiles every year, and discards 23kg into landfill,” he said.
“Burning carpet waste releases various toxic gases, creating environmental concerns.”
Shadi Houshyar, a textile and material scientist at RMIT, said firefighting clothes waste also posed a challenge, as the same qualities that made these materials ideal for firefighting also made them difficult to recycle.
THE PORT OF NARUNGGA HAS BEEN built near the existing Wallaroo port and will off er an important boost to South Australia’s agricultural export options and employment across the Yorke Peninsula region.
Wallaroo Harbor has been divided
into two sections – the Flinders Portsoperated Wallaroo Harbor and the new T-Ports-operated Narungga Harbor – to ensure safe and efficient operations.
“We are extremely proud be part of an Australian first, which celebrates and honours the enduring cultural connection
DHHI’s local After Sales team supports your operation and equipment throughout its entire lifecycle, providing reliable and cost effective solutions every step of the
GRAINCORP’S SITES IN NORTHERN
NSW are on track for their second-best season on record with Coonamble, the largest in its network, having already surpassed the 400,000-tonne mark this season.
What’s more, Coonamble’s harvest began with a historic milestone when trucks rolled through the gates 20 days earlier than ever before.
According to area manager Tom Koerstz, the site’s success is a testament to the dedication and adaptability of the site team.
“We faced some delays while waiting on extra equipment, like mobile stackers, but our team adapted quickly and efficiently,” Koerstz said.
“Once the additional equipment and people arrived, we brought turnaround times back to standard and kept operations running smoothly.
“Overall throughput has been impressive, with peak days exceeding 23,500 tonnes across wheat, barley and canola combined.”
This unprecedented early start saw tonnes of grain pile onto the bunkers at pace – and to manage the surge, the team had to adapt swiftly, reallocating people
and equipment from other sites to meet growers’ needs.
In response to increased canola deliveries, the team shifted a stacker from wheat to canola, significantly boosting site efficiency.
This adjustment led to a recordbreaking performance: for seven consecutive days, the team received over 4,500 tonnes of canola, setting a new daily record for canola receivals by 2,000 tonnes.
The Coonamble team comprises a mix of seasoned locals and new
THE CSIRO HAS NETTED SOLAR venture record seed funding to accelerate clean energy transition with FPR Energy, a new venture cofounded by CSIRO, RFC Ambrian and Concentrated Solar Thermal (CST).
This venture aims to help reduce industrial emissions in heavy industries, such as minerals refining, steel, cement and chemical production.
FPR Energy has secured $15 million in seed funding to commercialise next-generation solar thermal
technology that will help reduce industrial emissions, which account for 20 per cent of Australia’s annual carbon footprint.
The company was launched on Tuesday November 26 in collaboration with global advisory and funds management firm RFC Ambrian and utilities leader Osaka Gas, raising the largest seed funding for a CSIRO cofounded venture to date.
CSIRO energy technologies research director Dr Daniel Roberts
recruits brought in to manage the bumper harvest.
The harvest has also highlighted the exceptional quality of grains and oilseeds being delivered across the region. With nearby Gulargambone and Gilgandra sites receiving their fair share of this whopping crop, this harvest will be one for the books.
Gilgandra and Coonamble sites have benefited from GrainCorp’s recent investments, with an extra 500,000-plus tonnes of storage built across the region in recent years.
said FPR Energy is a major step in meeting the growing demand for renewable solutions in hard-toabate heavy industries.
“FPR Energy is building on years of solar thermal research, demonstrating CSIRO’s commitment to supporting emissions reduction using impactfocussed science and technology,” Roberts said.
“Diversifying the way we harness Australia’s abundant solar resources will help develop a low-carbon economy
and support economic growth and job creation in the Hunter region.
“Helping heavy industries to transition to cleaner energy sources is essential to reaching Australia’s netzero emission targets.”
FPR Energy aims to cut emissions in heavy industries such as minerals refining, steel, cement and chemical production using CSIRO’s particlebased Concentrated Solar Thermal (CST) technology, capable of producing temperatures up to 1200 degrees Celsius – an industry first.
The technology uses abundant and low-cost ceramic particles to store sunlight as heat, enabling long-duration energy storage to support industrial processes, green fuel production and reliable, dispatchable power.
FPR Energy plans to develop a 50-megawatt thermal demonstration plant, with up to 16 hours of integrated thermal energy storage. The plant aims to prove the commercial viability of FPR Energy’s CST technology at a utility scale.
Our Analytical Stockpile Assessment (ASA) solutions offer unparalleled accuracy in evaluating your stockpiles, providing you with critical data on volume, tonnage, and composition. Whether you are optimising resource consumption, improving financial reporting, or ensuring compliance with stringent regulations, our advanced technologies and proven methodologies empower you to make informed decisions with confidence. Our tailored services are designed to meet your unique business needs, supporting your operational and financial targets efficiently.
With a global network of experts and a reputation for confidentiality and quality, Intertek Caleb Brett is the partner of choice across diverse industries. Trust us to deliver precise, reliable, and actionable insights that drive your strategic planning and financial success.
TO LEARN MORE, SCAN THE CODE!
PORTS’ PORT OF Bunbury received its fi rst shipment of sugar in two decades with more than 7000 tonnes of sugar unloaded from Sugar Australia’s MV Pioneer.
The MV Pioneer is the world’s only specialised food grade bulk refined sugar vessel.
Southern Ports chief executive officer Keith Wilks said the business continues to diversify its trade across its ports, welcoming Sugar Australia as its newest customer.
“Sugar Australia’s decision to service its WA-based customers through our Port of Bunbury is testament to the capability of our ports, our teams, and our ability to manage the bespoke requirements that come with managing diverse trade,” Wilks said.
“These capabilities coupled with berths that back onto substantial laydown area means the Port of Bunbury is often the port of choice for incoming trade that requires temporary storage before it heads to Perth, Collie or elsewhere in our state’s south.”
Sugar Australia is Australia’s largest sugar refiner and supplies crystal sugars
and liquid sugar to industrial food and beverage customers, as well as consumer crystal sugar, treacle and golden syrup under its retail brand CSR.
The Queensland-grown sugar was processed at Sugar Australia’s Racecourse Refinery in Mackay before being transported around the country to Bunbury.
“Sugar Australia has a long, storied history working with an important section of the nation’s agriculture sector, so it’s pleasing to welcome them as a new customer,” Wilks said.
Previously the MV Pioneer has predominantly travelled between Mackay and Sydney prior to Sugar Australia investing in supply chain capability enhancements this year.
Sugar Australia chief operating officer Paul Gregory said improved onboard bulk filling equipment enabled the company to expand MV Pioneer’s service to valued WA customers.
“The Port of Bunbury was selected for its location, flexibility and capacity to support the unloading of a highvolume cargo vessel, with a capacity of over 20,000 tonnes,” Gregory said.
“Sustainability is a priority for Sugar Australia, so the Port of Bunbury’s commitment to ethical and responsible environmental practices was integral to our burgeoning partnership.
“Sugar Australia is excited about its new partnership with Southern Ports and appreciates the support and flexibility the team have demonstrated for this year’s first voyage.”
The MV Pioneer is scheduled to make multiple trips between Mackay and the Port of Bunbury during 2025.
Sugar adds to the more than 16 commodities traded through Southern Ports’ three ports.
ONE OF AUSTRALIA’S BIGGEST fertiliser suppliers has begun work on a $70 million fertiliser distribution centre (DC) in Western Australia, after a fi re destroyed the company’s existing bulk fertiliser site in February.
Since the fire, the Fremantle Ports Authority has supported Nutrien Ag Solutions to continue operating at the
Kwinana Bulk Jetty precinct to meet the needs of its customers.
“My government is committed to locking in quality local jobs and a strong economy for the long term, and is working to futureproof Perth’s major industrial precinct with $20 million to expand capacity at the Kwinana Bulk Jetty precinct and other investments,” WA Premier Roger Cook said.
The new, larger DC – to be located just two kilometres from the previous facility at the Kwinana Bulk Jetty precinct – will increase the company’s bulk granular fertiliser storage capacity by 20 per cent, to 130,000 tonnes.
Combined with a new, streamlined distribution process, the centre will ensure WA’s world-leading farmers have guaranteed access to
fertilisers when they need them.
The single biggest on-farm investment, fertilisers are supplied by Nutrien Ag Solutions to grain, pasture and horticulture operators.
“This new facility increases Nutrien Ag Solutions capacity, securing supply so that farmers can access fertiliser at the right time to optimise yields. WA’s
agricultural sector is integral to our state’s economy and a key industry in the Cook Labor government’s plan to diversify WA,” Jackie Jarvis, agriculture and food minister, said.
“I welcome this significant investment by Nutrien Ag Solutions that will support our farmers to remain internationally competitive,
drive economic growth and create local jobs.”
Bolstering the jetty is key to transforming the surrounding precinct into a Global Advanced Industries Hub, which will create long-term local jobs and diversify the state’s economy.
Nutrien Ag Solutions’ new facility is expected to be operational in 2026.
Martin Engineering president emeritus R. Todd Swinderman o ers field-tested advice and methods for handling dust that have delivered results for bulk handlers around the world.
AROUND THE WORLD, LEGISLATION is changing on dust emissions. Often, these rule changes cause a ripple effect internationally and serve as a template for similar policies worldwide.
On August 1, 2024, the US Mining Safety and Health Administration’s (MSHA) final rules on dust emissions came into effect. MSHA measures the dust personal exposure level (PEL) in a time weighted average (TWA) by a personal dust monitor carried by trained workers throughout their eighthour shift. The volume is measured in micrograms (μg) in cubic meters (m3).
The final rule establishes a new PEL of 50 μg/m3 for a full-shift exposure, calculated as an eight-hour TWA, and an action level of 25 μg/m3.
These standards also apply to miners diagnosed with or showing early signs of pneumoconiosis (black lung).
The MSHA mandates operators seek to install or repair equipment that offer engineering controls which control or eliminate sources of dust. This is supplemented with administrative
controls. Temporary personal protective equipment is also required for exposures above the PEL but is not considered a long-term solution.
Martin engineers have dedicated years to reducing conveyor-borne dust by designing accessories and engineered solutions that improve workplace safety and production efficiency.
Conveyor belt dust is largely generated at the loading and discharge zones. Passive dust reduction means no machinery or electricity such as air cleaners, pumps or HAVC are needed.
Passive dust reduction strategies include:
• Fully enclosed transfers – Completely enclosing the loading, stilling and settling zones contain the dust. Items like dust curtains and dust bags control airflow and capture dust.
• Shorter or sloped loading – Transfer chutes that minimise the impact of cargo on the belt reduce the amount
of turbulence and volume of dust within the loading zone.
• Belt training – Belt training when entering and leaving the loading zone ensures centred belt loading and minimises material shifting. It also controls belt drift for less spillage and dust along the run.
• Preventing belt sag between idlers – The belt can dip slightly between idlers, creating gaps that release dust and fines. Using an impact cradle with shock-absorbent polyurethane bars reduces strain on the belt and creates an even belt plane. Cradles can extend along the entire length of the stilling zone.
Many sources suggest belt speeds of 2m/s or less for reducing dust generation. However, with lower belt speeds, the belt width must increase to convey the same tons-per-hour creating a capital cost vs operating cost dilemma. The Conveyor Equipment Manufacturers Association (CEMA)
Classification and Definitions of Bulk Materials (ANSI/CEMA 550-2003) lists miscellaneous properties of materials that benefit from lower belt speeds:
• B-1 Aeration-Fluidity
• B-6 Degradable-Size Breakdown
• B-8 Dusty
• B-20 Very Light and Fluffy
Idler spacing and belt tension
Managing belt tension so the sag between idlers is minimised reduces the number of escape points for fugitive spillage and dust from material trampling and splash. Splash is material spread after impact on the belt during loading. Material trampling is the particle-to-particle movement created by the change in the bulk material profile as it goes over the idlers. The higher the belt tension, the lower the trampling loss.
Similar to turbulent air caused by impact, at a critical speed, bulk material moving over idlers loses contact with the belt at the idler and is launched into the air, falling back onto the belt at a slightly lower speed and releasing dust. Keeping the belt sag to one per cent between idlers is a frequent specification.
Idler spacing is critical to controlling belt sag. To reduce gaps where spillage and emissions can escape and retain an even belt profile
in the loading zone, idlers should be placed as closely together as possible. Outside of the loading zone, CEMA has some recommendations based on volume and belt width.
The amount of dust that can become airborne is directly proportional to the volume and speed of the airflow through the transfer point. If the openings in the chute work are restricted to the practical minimum, the inward airflow is restricted. A useful dust control strategy is to capture the material shortly after discharge and keep the stream coalesced as tightly as possible to reduce induced air. Extend enclosures apply dual skirting to seal the enclosure and use dust curtains to control airflow
and allow dust to settle back into the material stream.
Conveyor transfer points have a history of being drafted rather than designed. Design tools and material flow modelling software helps reduce dust emissions in the transfer point design phase.
How the conveyor is operated and maintained also has a significant effect on dust generation and release. In initial conveyor system designs, emphasis is commonly placed on maximising production. But experts recommend operators engage in feasibility studies on how the conveyor systems create and emit dust with the goal of improving air quality and workplace safety while still increasing operational efficiency.
Asia-Pacific’s International Mining Exhibition is relocating to Adelaide in 2025 following Prime Creative Media acquiring the event in May 2024.
by the South Australian government and influential mining stakeholders, Asia-Pacific’s International Mining Exhibition (AIMEX) – Australia’s longest-running mining event – will relocate to Adelaide in 2025.
This new partnership marks a pivotal moment for the industry, with AIMEX committing to a decade-long stay in South Australia’s capital.
The decision underscores Adelaide’s emerging role as Asia-Pacific’s fastest-growing centre for modern and sustainable mining.
Prime Creative Media (PCM), which acquired AIMEX in May 2024, will host the exhibition at the Adelaide Showgrounds every two years.
This move not only strengthens AIMEX’s standing as a key industry
event, but also reflects South Australia’s leadership in forward-looking mining practices, which increasingly focus on decarbonisation and sustainable mineral extraction.
“We knew we needed to do something big to attract key players in the industry. When the mining industry asked us to come to Adelaide, we thought this change of location was the best way to serve this important sector,” PCM general manager of events Siobhan Rocks said.
The choice of Adelaide for AIMEX’s new home is a response to shifting trends within the mining sector. As mining in New South Wales adapts to evolving demands, South Australia has emerged as a progressive leader, with a clear vision for the future of responsible mining.
The state’s focus is less on traditional fossil fuels like coal and more on critical minerals, such as copper, which are essential for the global transition to greener technologies.
Additionally, South Australia’s robust efforts in renewable energy and hydrogen projects align with this transformation, making it a natural choice to showcase innovative mining and energy solutions.
“With our natural advantages and ingenuity, South Australia has the potential to lead the world in decarbonisation of critical minerals, including green steel and copper,” South Australian premier Peter Malinauskas said.
“We have a compelling story to tell, and AIMEX being hosted in Adelaide
for the next decade provides a strong platform to do just that.”
“AIMEX is a significant win for Adelaide, one which will generate more than $250 million for the State economy over the next 10 years,” Business Events Adelaide chief executive officer Damien Kitto said.
The influx of national and international mining professionals and suppliers will enhance Adelaide’s status as a thriving hub for
innovation in sustainable mining.
For South Australia, hosting AIMEX goes beyond economics. It’s about positioning the state as a top-tier jurisdiction for the critical minerals required in the global energy transition.
The exhibition will spotlight South Australia’s leadership in areas like green steel production and hydrogen energy, showcasing a region at the forefront of responsible and innovative mining practices.
One of the most anticipated additions to AIMEX will be a dedicated energy focus, highlighting South Australia’s impressive renewable energy projects and expertise.
The pavilion will feature key local and international companies, including major players like Santos, which are leading the charge in green energy solutions.
“There’s no denying that there’s a link between the mining industry and renewable energy. South Australia is a world leader in renewables and the global transformation economy, and we’re proud to partner with the state to showcase the world-class change the resources sector is driving,”
John Murphy, CEO of Prime Creative Media, said.
A specialised Energy Stage will provide a platform for discussions about South Australia’s progress in hydrogen and other renewable technologies, as well as the future of critical minerals.
This new focus aligns with South Australia’s commitment to
decarbonisation. The state’s existing projects in hydrogen and renewable energy networks have already set a strong foundation, and AIMEX’s presence will only amplify its leadership in these areas.
“This is a critical time for the industry. South Australia is emerging as a frontrunner in responsible mining and production of the minerals, metals, and fuels of the future. It aligns with our purpose to deliver a forwardfocused mining event for the next generation of Australian mining,” Murphy said.
While AIMEX has a long history of championing the latest trends and technologies in mining, the 2025 event in Adelaide will introduce several new elements designed to reflect South Australia’s leadership in critical minerals and sustainable development.
One of these innovations is a Research Pavilion, which will bring together leading universities and research institutions to share groundbreaking work that pushes the industry forward.
A main conference stage, curated in collaboration with the South Australian government, will feature prominent speakers from across Australia, facilitating critical discussions on the future of mining.
The event is set to draw thousands of attendees, from local mining leaders to international delegates, reinforcing South Australia’s growing reputation as a powerhouse of sustainable mining.
ESS considers the factors that lead to material build-up and reduced flow when designing air cannons.
a signifi cant challenge to plant effi ciency by decreasing live capacity and obstructing material fl ow through bulk storage containers.
This issue can lead to several knockon consequences, including material shortages, disruptions in product
flow, and altered impact zones, which may cause wear in unexpected areas. Such wear can result in misalignment, leading to spillage and damage to conveyor belts. Addressing material build-up is essential for maintaining optimal plant performance and reducing operational costs.
ESS air cannons offer a solution to these problems. ESS air cannons are high-pressure vessels that blast air at high-velocity speeds, dislodging buildup and allowing sites to maximise storage capacity.
Tom Stahura, accounts development manager for Western Australia and
overseas projects, said the company has more than 45 years of experience delivering air cannons.
“Our extensive application experience makes our Air Cannons stand out,” he told ABHR
Stahura knows just how valuable and versatile ESS Engineering’s flow-aids can be in the bulk material handling industry. ESS air cannons have been used in numerous applications. They can quickly solve bulk flow problems in silos, hoppers, chutes and storage piles and are often used where vibration is not practical or other methods are too expensive.
“I think wherever bulk materials are being handled, there is a need for a flow-aid to help them with their product,” Stahura said. “I’ve had clients use air cannons on everything from cereal manufacturing and grain storage to bricks, cement works, and heavy-duty bulk handling of iron ore and coal.”
Safety is ESS’s top concern, as dealing with compressed air is hazardous. The
company designed air cannon systems to store air in 40L, 70L, 150L or 250L receivers. The cannons are designed to fill with air just before they are fired, which minimises the time the air cannon is charged and reduces risk. Air escapes directly through valves into a discharge pipe to affect the area of influence during the dispersal.
Stahura said the 150L air cannons are also cast vessels, which effectively has an infinite life in terms of pressure cycles. “Because the air cannon is cast, there are no welded areas prone to fatigue over time,” Stahura said.
“When combined with a remotecontrol system that allows you to fill the cannon just before you discharge it, it lowers the hazard class significantly as the cannon is not sitting around filled with pressurised air at all times which is typical of other air cannons in the market.”
ESS valves feature a single moving part with no metal-on-metal contact,
Book a free on-site review and analysis of your current pallet wrapping performance
NZ 0800 55 77 33
AU 1800 318 019
hello@aurora-process.com
eliminating fatigue-prone components to extend their lifespan.
ESS can help customers optimise air blasting outcomes through certain design features, such as tailored pipe designs or a chute mounting arrangement that will maximise the efficacy of a blast through proper design and firing sequence.
Stahura said ESS’s high-quality air cannons and commitment to providing end-to-end service, from design and manufacturing to installation and ongoing maintenance and service, keep customers returning, which has allowed the company to grow globally.
“Air cannons are cheap insurance. If you don’t have product moving through your plant, you’ve got nothing,” he said.
“Currently, we have projects in Africa, the Philippines, and more.
“Our customers love them. In fact, when our clients move overseas to international projects, they will often contact us to help them solve material handling problems at their site.”
Our breakthrough new range of pallet wrappers deliver real cost reduction per pallet and an extra level of performance.
Intelligent technology to get the best load containment whilst reducing your wrap usage.
Unusually shaped loads, unstable or light loads, sharp edges, and loads in cold or hygiene zones – we’ve got it covered.
Full range of performance wrap and pallet consumables - specified by process technicians not stationary suppliers.
Fully installed and serviced.
Ask us about paper wrapping options too.
With a continuing focus on critical minerals, Bulk Handling Technologies has designed and manufactured a Loss-InWeight Feed System to control the mass feed rate of beta-spodumene at an expanding lithium mine in WA.
system designed and supplied by Bulk Handling Technologies to receive, store, and feed beta-spodumene into the process, it was important that this very fi ne, abrasive, and hot bulk material could be accurately fed into a mixer at a measured mass feed rate.
Due to beta-spodumene’s unique handling characteristics and the range of feed rates required, a ‘loss-in-weight’ system was deemed to be the most reliable option.
Loss-In-Weight (LIW) Feeders operate by constantly weighing the stored product in a small hopper and, using an integral controller, they measure the loss in weight over time as the product is discharged into the process. The rate of loss in weight determines the mass feed rate, and by continually adjusting the speed
of the feeder (in this case, a screw feeder), the system will automatically maintain the target set point in tonnes per hour despite variations in product bulk density.
Bulk Handling Technologies
engineering manager Paul Ingleson said beta-spodumene can be a difficult bulk material to handle.
“Not only are we dealing with a hot product in this case, but beta-spodumene is well known for being extremely abrasive and for compacting and bridging in silos and hoppers,” he said.
For this reason, the LIW Feeder hopper has been carefully designed based on material property testing results to achieve mass flow.
“The steep and rounded shape of the hopper reflects the
poor flow characteristics of betaspodumene,” Ingleson said.
“This hopper design will prevent hang-up and rat-holing and, when combined with a correctly designed feeder, will ensure uniform draw-down and ‘first-in, first-out’ performance.”
Another important consideration for any LIW Feeder is how it is filled. As the hopper discharges the product over time, the hopper will eventually need to be re-filled. The typical rule of thumb is that the LIW Feeder should measure the weight loss in ‘gravimetric’ mode 90 per cent of the time and then switch to ‘volumetric’ mode for 10 per cent to allow for a fast refill of the hopper.
“In this case, the same design principles were applied to the larger filling screw feeder and the main product storage bin to ensure reliable filling of the LIW Feeder hopper,” Ingleson said.
“The filling screw is much larger as it must deliver the product at a rate of more than ten times the LIW Feeder discharge rate, but it must start and stop the flow reliably when required.”
Leveraging many years of experience in large screw feeder design, the engineers at Bulk Handling Technologies designed a custom feeder with abrasion-resistant materials, which would also ensure mass flow from the main bin.
The filling screw incorporates a vent line above the outlet, which allows displaced air from the LIW Feeder hopper to escape through a filter bag during filling, and also an emergency discharge outlet below the main storage bin to allow any product out of specification to be removed from the system.
Ready and available Established in 2012 and offering extensive materials handling
OPTIMISE YOUR ENTIRE PACKING
Get your free PROCHECK Guide LINE WITH THE HAVER & BOECKER PROCHECK LIFECYCLE APPROACH FOR PACKING PLANTS
equipment and systems, Bulk Handling Technologies specialises in customised and innovative solutions. With its custom bin and hopper design experience and extensive range of bulk materials handling feeding, conveying, and weighing solutions,
Bulk Handling Technologies can offer complete packages to receive, store, and feed any bulk material reliably and accurately. The company can also assist with site audits and troubleshooting and, where practical, provide refurbishment and upgrade options.
DHHI’s “new way of working” has seen it succeed in 2024. ABHR speaks to the company’s sales manager to find out how.
reclaimers, and shiploaders requires specialised skills and capabilities. These massive machines form a critical path for the supply chain of millions of tonnes of bulk commodities both exported and imported by major mining Companies across Australia.
High capital investment, complex engineering standards and high availability/reliability demands are just a few of the reasons mining companies are looking to DHHI to as their complete lifecycle solution for balanced machines services.
DHHI sales manager Will Haua told ABHR that the balanced machines supplier landscape has undergone significant changes over the last
years. The complex and often variable engineering processes under fixed price engineering procurement construction (EPC) style contract arrangements and challenging Australian construction industry environments combined with lead times up to three years resulted in the leading suppliers walking away from the industry.
However, this departure of original equipment manufacturers presented DHHI with an opportunity to establish itself as Australia’s leading balanced machine supplier.
“We had a very successful year in 2024, from a business and a personnel growth perspective,”Haua said.
“No other company has successfully designed, supplied, and constructed as many balanced machines as DHHI
over the last years to the Australian market and all in compliance to the latest Australian Standards and strict client specifications.”
“Furthermore, earlier this year we were able to secure a significant project at one of the Pilbara’s major export terminals including what will be one of the most impressive delivery concepts ever seen in the balanced machine industry, watch this space.”
To keep up with a rapidly changing industry landscape, DHHI has put in place several strategies to ensure its longevity in the market.
One of the key strategies has been the growth of its project execution office in Osborne Park, Perth, which has undergone significant expansion. The company has recruited leading
balanced machine engineers, project execution, and aftermarket personnel to ensure it can lead projects across all disciplines directly from Australia for the whole lifecycle of the machine.
Haua said a common misconception is how much of the company’s machinery is made up of Australianbased content.
“Due to the large amount outsourcing required for mechanical and electrical components onboard our machines, as well as support from local subcontractors with specialised labour such as engineering and site construction, the majority of our content is Australian-based,” he said.
“Growing our presence and service capabilities across regional mining hubs will form a key strategy in ensuring we meet our local content and community engagement objectives moving forward.”
“The DHHI management team, including myself, are well experienced in the balanced machines industry. These experiences inherently come with lessons learned and thankfully DHHI have approached the growth strategy of the Australian business with an open mind and flexibility to structure our organisation in a way which avoids making the same mistakes.”
DHHI values its company culture, seeing it as key to long-term success and growth. It aims to break old industry habits and create a team workplace of respect, inclusivity, and flexibility that empowers its employees to innovate on complex projects and provide better results for clients.
Company culture is also a key driver in the business relationships with its customers. DHHI prefers a streamlined management structure and open access to single points of contact with the authority to quickly resolve issues during the project.
Major mining companies are also recognising the importance of creating more sustainable project execution and complete lifecycle service business models for the balanced machines business.
These machines are required to move high tonnages of bulk materials and are designed to very detailed client specifications.
The resulting high capital expenditure and long lead times has historically meant the industry had a cyclical nature, resulting in few opportunities each year to secure orders, which in turn cause cash flow constraints and make it difficult to retain key resources from moving project to project
Haua said DHHI’s strategy is to form long term partnerships, which includes complete aftermarket lifecycle support services.
“Almost every client we deal with has established relationships with Australian suppliers and service providers particularly those with established networks for ongoing technical support, maintenance and spares strategies,” he said.
“These are the type of companies DHHI looking to partner with.”
In 2024, DHHI focused heavily on building up its Australian aftermarket capabilities. This has allowed the
company to react to local needs quicker, while still benefitting from an immense manufacturing capability and engineering expertise offshore.
Moving forward, the company is committed to growing its Australian presence to provide clients the complete lifecycle service opportunities, particularly across the Pilbara region.
Haua said standardisation of structural and mechanical components, as well electrical systems, will form a critical part of DHHI’s design processes moving forward.
“Standardisation will help to derisk our projects by providing more predictability in design processes, project schedule and pricing,” he said.
“DHHI would like to make it known to the market that we as are also looking form long term partnership agreements with key equipment suppliers and subcontractors who share the same vision and benefits of standardisation.”
DHHI has five large manufacturing and research facilities across the province
of Dalian, China totalling more than 2.5 million square meters of real estate, including direct access to multiple deep water port loading facilities.
Its manufacturing capabilities range from bulk handling machines, conveyor systems, port machines, metallurgical and power generation equipment, logistics centres, heat treatment, advanced machining computer numerical control workshops, foundries, spare parts workshops as well as our own electrical manufacturing and control equipment plant.
“To put into the scale of our combined workshop capacities, in 2024 DHHI set the target to manufacture 642,000t of steel for our entire product range,” Haua said.
A new event for the municipal works, commercial and civil construction industries. Melbourne,
Converge is Australia’s premier event for Sub-Contractors, Project Engineers, Council Fleet Managers, and Large-Scale Construction Contractors across the municipal works, civil construction and Through a mixture of live demonstrations, equipment showcases, and conference spaces, Converge will bring industry experts together to share knowledge and deliver solutions for building and
LEARN MORE infrastructure space. maintaining Australia’s future.
Intertek’s stockpile analysis methods are helping bulk handling businesses save potentially millions of dollars.
IN
handling, understanding the value of assets is critical. Whether it’s acquiring a new company, selling assets, transporting bulk materials or trialling a new product, the ability to accurately assess the value of a stockpile is key to success.
Dry stockpiles, however, can be difficult to accurately assess. Current methods rely on volumes and average bulk densities to determine tonnage, resulting in inaccurate results. As companies frequently require independent or third-party assessments to confirm the value and quantity on-hand at any one time the accurate assessment of the tonnage of material on hand is of critical importance
That’s where Intertek comes in. The company uses science-based, analytical methodologies to accurately measure stockpile tonnage and value.
Nicholas Davies, commercial director of Intertek’s analytical stockpile assessments (ASA), told ABHR about the company’s patented process.
“Determining the in-situ bulk density of the product is an important part of the tonnage calculation. When measuring bulk density, we consider a range of variable factors such as compaction, height and depth, storage environment and conditional factors including humidity,” he said.
“It means we can measure the total tonnage of material on the ground for when it is not feasible to weigh or cutout the material.
“The method essentially breaks the stockpile into layers. Each layer is then analysed for individual density – because as you get lower the density increases under gravity and our method accounts for the compression of the stockpile under its own weight.”
It began offering this service in the Australian coal industry for thermal power stations. Initially, customers needed to ascertain the tonnages of their stockpiles. One of the company’s scientists in its Sydney lab developed and patented the ASA’s method, where it is now used across the bulk handling industry.
Intertek provides this service for high value commodities, such as mineral concentrates, cement products, mineral sands, sugar, wheat, and more. The ASA method can be used for stockpiles housed in sheds, on outside stockpile pads, and product housed in silos and domes.
The company provides accurate tonnage assessment of dry bulk particulate stockpiles, with up to 1.8 per cent accuracy. This often results in significant financial gains for customers, often adding up to millions of dollars.
Davies said the feedback from clients has been excellent.
“We had one client who was initially quite sceptical,” he said. “After we went through the process with them, it enabled them to sign off on their financial reconciliation with their auditors and establish their business in Australia.
“They could accurately understand what they had available and use the scientific method to showcase this to the regulators.”
As part of the process, Intertek will tailor its approach to meet the client’s operational and financial requirements. It also has an international network of experts and access to some of the latest technological developments.
Davies said that since it was introduced, Intertek’s method has been improved by unmanned aerial vehicle 3D LIDAR technology.
“We’ve brought in this technology to get more accurate assessments,” he said. “We’re looking to go down the automation route eventually.”
“We’re very much at the start of the growing process. The method has been around for several years, but no we’ve brought on more team members.
“In 2025, we plan on talking to more customers and help improve our processes even further.”
Container Rotation Systems talks to ABHR about its range of customised solutions for handling dry bulk goods.
Container Rotation Systems (CRS), has made a name for itself with an innovative container-emptying system that tackles the challenge of effi ciently unloading bulk cargo.
This solution, already gaining traction on a global scale, is employed across various industries for handling a wide range of materials – from alumina to coal.
CRS has developed a diverse range of customised solutions, including its rotatable containers, which integrate with the Rotainer range. These systems are designed for the optimal unloading of dry bulk goods such as coal, zinc, copper, mineral sands, aluminium, iron ore, sugar and grains.
A recent highlight for CRS occurred in mid-September, when the company’s engineering team oversaw the assembly of its latest innovation in Thailand – the MH4240, a 40-foot container rotator.
This unit was crafted at CRS’s manufacturing facility in Sydney and showcases 15 years of expertise in container rotation technology. Assembly on-site was quick, taking less than a day to complete.
The MH4240 is a modular, singlebeam container rotator designed to manage large quantities of low-cost bulk goods from land-based stockpiles to ship.
It reflects CRS’s ongoing commitment to advancing technology in containerised bulk handling. With its single-beam design, it offers an efficient and robust solution for shipto-shore operations.
One of the features of this installation is the second-generation
electrics, developed specifically for CRS’s 360° multidirectional drive system.
This innovation enables a swift 40 seconds for complete 360 degree rotation, making it ideal for industries requiring rapid unloading of large volumes of lightweight materials, such as biomass, woodchips, and waste.
The MH4240 is engineered to deliver exceptional performance, boasting unmatched speed and precision.
Adding to its appeal, the MH4240 is a pioneering addition to the containerised bulk handling market. It’s designed to fit a Sany ship-toshore (STS) crane and can be powered by either electric or diesel engines, making it a versatile option for both reachstackers and STS cranes.
The recent installation of the
Rotainer Eurospec MH4240-360 marks a milestone for CRS. The commissioning of the unit, completed on the second day, demonstrated the efficiency and adaptability of this container-handling technology.
CRS’s MH4240, with its patentpending innovations, further solidifies the company’s status as a leader in transforming container-handling solutions worldwide.
The images captured during the installation and commissioning process highlight the sleek, effective design of the unit.
This latest addition to CRS’s Rotainer portfolio not only turns heads, but also redefines the standards for efficiency and performance in container handling.
Kilic Engineering general manager Craig Dennis discusses how the company is addressing labour shortages across the agricultural sector.
population has grown increasingly urban – it’s a process that has been underway for more than a century.
According to the Australian Bureau of Statistics, the urban population increased from 58 per cent in 1911 to 90 per cent in 2021. In addition, cities like Melbourne and Sydney tend to attract more young people – with the median age almost five years younger in capital cities than the rest of Australia.
This creates challenges for vital regional industries like agriculture. As more young people leave, it’s harder to find labour during one of the most important times of the year – the harvest.
Kilic Engineering general manager Craig Dennis told ABHR that every year, customers tell them about how much harder it is to find operators for the harvest.
“In the agricultural industry, there’s seasonality – the number of full-time jobs is stable, but there’s a peak demand for workers during the harvest,” he said.
“Businesses need to put time and money into training their workforce
who stick around for three to four months. Maybe they come back next year, or maybe they disappear by the next harvest.”
“One of the other major challenges is keeping up with technological advancement. As farms embrace new technology, it means crops are coming off faster and faster. This increased rate of product means sites need to unload faster to keep up, compounding workforce issues even more.”
To help its customers handle the increased demand and labour issues, the South Australian business has changed how it delivers its material handling systems to sites.
Historically, Kilic Engineering would spend two full days unloading the machine and undergoing a handover process.
This process has evolved, allowing its team to unload the machine in one day, spending the second day on training customers on how the equipment works, to give them a better understanding of the equipment and how to make the most of it.
This process has become even more important for the agricultural industry, as there are fewer permanent staff located at a site.
Kilic Engineering also provides long-term support, helping customers move machines between sites if needed, in addition to maintenance and spare parts service.
Dennis said the company even has refurbishment and upgrade services, for when clients have a leaner harvest.
“If you have our bunker stacker equipment, we can review what needs to be upgraded, comparing it to the features that are available on our current designs,” he said.
“This comes with the mechanical, electrical, and hydraulic changes necessary.”
Dennis said that passing on Kilic Engineering’s operational expertise is vital.
“Not only are we providing training, but we are also changing our technology. We’re looking at automation to make our machines easier to use, and so that operators have more time to focus on other things at the site,” he said.
“That means less people are required to keep Kilic equipment working at optimum levels. It means that sites aren’t hurt if there isn’t enough staff, and it also reduces the burden of hiring and training.”
“We have a goal to eventually become fully automatic, though that’s an ambitious goal and in the future.”
Kilic Engineering maintains a technology plan, which was outlined several years ago. Initially, it involved relatively straightforward additions, such as inclinometers to inform operators about
the boom or a grain valve indicator to better understand the level of flow.
In 2024, the company began testing an automated flow control system, which will begin rolling out across certain machines this year. Dennis said this new system means the valve automatically regulates the product on the conveyor, eliminating the need for manual input.
“It helps customers keep up with the flow of product, putting the optimal amount onto the stacker belt,” he said.
“It eliminates underfilling, which wastes capacity, and also means the belt is not overloaded, which can cause a machine to stop. It gives customers confidence they’re getting the most out of our equipment.”
Additionally, the company has been working hard on new products. It’s flagship product, the SuperRoo is a 750tph stacker that has undergone significant development.
Last year Kilic Engineering began incorporating an auger as part of the
bunker stacker machinery instead of an underbelly conveyor for certain clients.
Now, the company has its set its sights on creating an even bigger SuperRoo, with a design capacity of 1000tph.
Named the SuperRoo 4000, the increased capacity is expected to help customers keep up with the increasing flow of grain from farmers.
“We’ve changed the belts from PVC to a cleated rubber belt, and have increased belt width from 660mm to 900mm,” Dennis said.
“The entire boom structure and base of the conveyor have been re-engineered to take the additional load.
“For us, it’s an iterative step. There’s already been a fair bit of interest in it from our customers.”
A SuperRoo 4000 is currently under construction and will be delivered to a customer’s site upon completion where it will be tested. Following these tests, Kilic Engineering intends to invite other
customers to get up close and see the machine in action.
The machines have been designed to meet Australian Standards for guarding and operational safety.
The company is also looking to export its bunker equipment into the United States, with several demonstrations planned overseas.
Dennis said the company is well positioned to continue helping Australian agriculture deal with the challenges it faces.
“Recently, Australia has seen good harvests, though our customers will continue to see increased competition globally, as markets go through periods of stability and instability,” he said.
“There is also the challenge of getting consistent utilisation of sites, and the realities of the Australian climate.
“We’re busy developing the tools needed to address these problems, and are excited to see what 2025 brings.”
For 40 years Kinder Australia has been a leading independent supplier of engineered products that enhance the performance and efficiency of conveyor systems.
Our extensive range of products, including dust mitigation systems, are engineered to meet your conveyor’s needs.
Our engineers are innovation experts who can design bespoke solutions that increase efficiency and reduce downtime.
We specialise in:
› Belt Support
› Conveyor Skirting
› Belt Cleaning
› Conveyor Hardware
› Safety and Environmental
› Flow and Anti-Wear
› Process Equipment
Book a FREE conveyor inspection today. Kinder’s Field Application experts can pinpoint problem areas, recommend tailored solutions, and help improve efficiency.
NORD Australia director Max Jarmatz speaks with ABHR to learn more about the gearboxes that are powering one of Europe’s longest overland conveyors.
THE BUCIM COPPER MINE IS ONE OF the only operating copper mines in North Macedonia.
Ore was discovered pre-World War II, with active exploration beginning in 1979. Soon, the site featured an open pit copper and gold mine, along with a floatation mill.
Here, 4.5 million tonnes of highly sought after ore is processed annually.
Within the Bucim project is the Borov Dol mine, which aims to extend the life of Bucim’s operations to at least 2030.
As part of this project, a 6.3km overland conveyor belt was constructed to connect the historic production site with the new mine.
At the beating heart of this conveyor are three NORD Drivesystems 400kW industrial gearboxes.
NORD Australia director Max Jarmatz told ABHR that the company’s equipment plays a critical role in ensuring the proper output torque is delivered to power long overland conveyor belts.
“Without robust, efficient gearboxes, conveyor systems risk unplanned downtime, increased costs, and decreased productivity,” he said.
“Motors typically produce lower torque with higher speeds determined by the electric grid’s frequency. Frequency inverters can modify motor speed, or larger motors can generate more torque.
“However, the most economical method uses a lever effect in gearboxes, which reduces speed mechanically while increasing torque. We’ve perfected this over nearly 60 years with solutions provided to over 100 industries.”
With production facilities in 36 countries, NORD has been assembling its high-quality drive solutions in Australia since 2008.
NORD’s gear units are manufactured with the UNICASE design, developed in-house in the 1980s to endure harsh industrial conditions. The UNICASE housing, machined from a single piece, integrates all transmission elements
and heavy-duty bearings. This design is a hallmark of NORD’s MAXXDRIVE industrial gear units, which offer high output torques from 15,000 to 282,000 Newton metres, with power inputs between 1.5 and 2000 kilowatts.
The MAXXDRIVE range is specifically engineered for heavyduty applications like conveyor belt drives, making it ideal for industries requiring high input powers across wide-speed ranges.
Because the Borov Dol mine is located in a complex ecosystem, with the conveyor crossing a major road, making sure the equipment is reliable was vital.
Fast-moving conveyors generate significant thermal energy, leading to thermal losses. To mitigate this, NORD developed the highly efficient MAXXDRIVE XT industrial gear unit equipped with fins that radiate more heat and reduce the risk of thermal overload. Additionally, the XT design requires a lower oil level. This allows conveyors to operate faster and handle
higher loads without overheating or requiring external cooling systems.
Jarmatz said quality aftersales support is vital when it comes to major projects like Borov Dol.
“For critical projects, we engage local service providers with the necessary personnel and tools close to our customer, while NORD provides expertise, drawings, and spare parts,” he said.
NORD can also equip gearboxes with pre-installed sensors for integration into SCADA systems, enabling predictive maintenance through monitoring of vibration, temperature, and other critical parameters.
The MAXXDRIVE gear units are available as helical or bevel gear units, with various output shaft and flange options for optimal application connections. With additional options for harsh environments, MAXXDRIVE units – in particular – are designed to withstand fluctuating ambient conditions. TACONITE seals, heavyduty bearings and NSD5 paint specs guarantee a long service life.
Over the past decade, NORD has developed three new motor generations driven by European government standards. NORD IE3 motors are up to 94 per cent efficient. NORD’s gearboxes utilise highly efficient bevel and inline gears, achieving 96 per cent efficiency per stage, minimising thermal losses, and reducing a mine’s carbon footprint.
“Our gearboxes often come as part of a base frame arrangement with a
motor and additional components like couplings, brakes, or IoT sensors,” Jarmatz said.
“Each NORD industrial gearbox project is like a mini engineering project, as we strive to meet all customer specifications and requirements.”
In recent years, NORD has expanded its customer base in traditional mining sectors such as iron ore and copper while also delivering innovative solutions for the rapidly growing lithium ore market.
To further support Australian industries, NORD operates a gearbox assembly facility in Melbourne, Victoria, and offers an Australia-wide service partner network for repairs, spare parts, and after-sales support.
“We take pride in supplying highly efficient gearboxes to the lithium industry, fuelling the demand for electric vehicles worldwide. This collaboration is a perfect match, combining German engineering with Australian entrepreneurship,” Jarmatz said.
A new list has revealed the key critical minerals for the UK to highlight their importance to the region’s economy.
THE UK CRITICAL MINERALS
Intelligence Centre (CMIC) has revealed its latest list of critical minerals to help support future policy around the UK economy.
The latest assessment was commissioned by the Department for Business and Trade (DBT) as part of CMIC’s programme for 2024. CMIC is led by the British Geological Society (BGS)
and released a criticality assessment in 2021, but the 2024 one was larger in scale.
“This assessment confirms that the growing diversification of the UK economy — alongside the expanding reliance on global trade — brings an increasing vulnerability in terms of disruption to the supply of critical minerals,” said Dr Gavin Mudd,
director of the Critical Minerals Intelligence Centre.
“There are similarities to other criticality assessment lists across the world, but the demands and challenges facing the UK economy are dynamic, and we need to match the demand for minerals with sustainable and reliable supply.
“In particular, as the UK continues its efforts in decarbonisation of its economy, we are seeing significant shifts in numerous minerals as coal-fired power has now been closed and new technologies are being used. This brings both benefits and risks to the UK.”
The new assessment is expected to have some influence on policy in the years to come. Sarah Jones, who is responsible for the industry portfolio in the UK, welcomed the findings.
“[It] which shows a sustainable supply of critical minerals will be more vital than ever,” she said.
“That’s why next year we’ll launch a new Critical Minerals Strategy to help secure our supply chains for the
long term and drive forward the green industries of the future.”
In 2021, the assessment looked at 26 candidate materials, with 18 listed as critical, compared to 34 minerals out of 82 candidate materials this year. Compared to the 2021 assessment, 17 of the 18 critical materials have remained on the 2024 assessment, with only palladium dropping out.
The assessment used data from various sources and also considered diplomatic efforts to secure trade relationships for the material, investment in exploration, mining and processing and the pursuit of alternative materials.
CMIC’s criticality assessment lists the ten most critical materials out of the 34: Niobium, Cobalt, Rare earth elements, Germanium, Magnesium, Phosphorus, Ruthenium, Tungsten, Gallium and Rhodium.
Other materials within the criticality threshold include lithium, platinum, tin, nickel and iron. Others, including silica industrial sand, kaolin clay and copper, have been listed under the criticality threshold. Nickel, iron, germanium, aluminium and chromium are notable additions to the 2024 list after not featuring in 2021.
Being listed as a critical mineral, as opposed to essential or important, is designed to highlight the risk of supply disruption for the materials, which could create a headache for the UK economy. For example, if the next criticality assessment were shorter than the 2024 iteration, it would highlight that the UK has mediated several concerns around the supply risk for some critical minerals.
According to the report, the UK relies on international supply for most of the 82 materials assessed, with 49 of those provided primarily through importing. These materials are used in many of the emerging technologies of the future. Cobalt plays a key role in the manufacturing process for rechargeable batteries, which are used in hybrid and electric vehicles. Germanium is used to create optical fibres, infrared optics and solid-state electronics.
Others, including tungsten and niobium, are used to create tools and
equipment. Due to its properties, tungsten is used in cutting tools for drill bits, defence equipment, and superalloys. Niobium is also used to create superalloys, which produce high-strength steel used in vehicle body manufacturing.
Certain materials, namely lithium, are expected to be subject to significant growth in global demand. Recent data, including the criticality survey, expect the mineral to increase more than tenfold by 2050
In his discussion of the findings from the 2024 assessment, Mudd believed the non-inclusion of copper in the list would be the “focus of much attention”.
“In similar lists focused on economies across the EU, Japan, India, China, Canada and now the USA, copper is identified as critical. Under the methodology within our report, the material did not meet the necessary threshold, as with Australia’s latest assessment,” he said.
“Based on the scientific data used in our report, copper is not critical.
Through available data, projections of refined copper production can be judged likely to meet copper demand for the relevant policies and announced pledges scenarios.
“This assessment recognises that concerns around the capacity to increase global copper mine supply may lead to an increased global supply risk and, in turn, result in copper becoming critical in the future. When the data shows this point is reached, such assessments will reflect it.”
Mudd said he hoped the release of the new criticality assessment would help support policymaking in the future.
“This assessment is intended to stimulate discussion and allow us as a country to continue to plan effectively for the future of our economy and its place within an increasingly sophisticated and interconnected global supply chain,” he said.
“That discussion should be vigorous and impassioned; disagreement is an inevitable outcome. I look forward to taking part in such conversations.”
While much of the focus in heavy industries is on decarbonising equipment, site facilities could be the next key area in the pursuit of net zero.
of the game for many bulk handling operations within Australia.
That is best exemplified in Australia’s heavy industries, which are some of the country’s largest bulk materials sectors, as businesses pursue their netzero targets.
In mining and quarrying, much focus has been given to how machinery can be transitioned to electric drives or alternative fuels. This peaked last year when Fortescue signed an equipment partnership agreement with Liebherr to develop zero-emission technology and solutions.
According to Fortescue, the deal, worth US$2.8 billion, could create one of the “world’s largest zero-emission mining fleets” as part of its transition from conventional fossil fuels.
Liebherr will supply 475 new machines, while Fortescue’s technology arm, Fortescue Zero, will provide a zero-emission battery power system for the battery-electric trucks and PR 776, Liebherr’s flagship dozer.
The agreement is Liebherr’s biggest deal in its 75-year history and
Fortescue’s largest single contract. In another way, it highlights companies’ urgency to decarbonise their operations as their net-zero deadlines approach as 2030 draws near.
“‘This is an important next step in our 2030 Real Zero target – to eliminate emissions from our Australian iron ore operations by the end of the decade,” Andrew Forrest, founder of Fortescue said.
“We invite all companies in the mining, heavy industry and haulage sectors to join us. The solutions are there, and the missing ingredient is leadership.”
As companies pursue their net-zero ambitions, many may wonder what other avenues can be explored to reduce carbon emissions. An example of the next frontier for emissions reduction lies in Berrima.
Once a major town, Berrima is now a historic village that sits between Sydney and the Australian capital of Canberra.
For those in Australia’s heavy industries and construction sector in New South Wales, the Berrima Cement Works, owned and operated by Boral,
is a recognisable name. According to the Australian construction materials producer, Berrima supplies up to 40 per cent of the cement in NSW and the Australian Capital Territory.
The long-standing facility was opened in 1929 after two years of construction and helped create New Berrima in 1928 for the cement workers to live in. It currently employs 115 people in operational and administrative roles and contributes to a further 350 roles across integrated sites in the Southern Highlands. This, along with its indirect contribution to other jobs and industries, makes it one of the largest employers in the local government area of Wingecarribee.
Despite its almost 100-year history, one of its most significant chapters occurred when Boral unveiled a series of upgrades at Berrima Cement Works at the end of 2024.
The upgrades were supported by funding from the Federal and the NSW governments.
Federal Minister for Energy and Climate Change Chris Bowen attended the ceremony of the upgraded site alongside Boral chief executive officer Vik Bansal before the pair engaged in a site tour to showcase the size and scope of the cement facility.
Bansal, who has led Boral since 2022, said the company is earnestly taking its responsibilities under the Safeguard Mechanism and its net-zero target.
“We all understand that though cement is vital to construction and building our nation, it is carbon intensive. Boral takes its responsibility to decarbonise our operations and comply with the Safeguard Mechanism obligations seriously,” he said.
The cornerstone of the upgrades is a chlorine bypass facility, which will the build-up of chlorides and other alternative fuel by-products during production.
According to Boral, this facility will enable to site to increase its alternative fuel usage to around 60 per cent over the next three years and transition from fossil fuels, which will help reduce carbon emissions.
The company has estimated this will reduce the emissions by 150,000 tonnes per year.
“The chlorine bypass facility reaffirms this commitment and moves our vital cement manufacturing infrastructure and Southern Highlands operations into a new era - one with less impact on the planet,” Bansal said.
“I think we’re a fan of the safeguard mechanism, I think it is needed in this country, in my opinion. What it also does is provide certainty of policy. With certainty of policy, I think companies like Boral can’t invest in the future.
“Ultimately, I believe companies can do carbon reduction if there is certainty of policy; when you have uncertainty, that is where the issues are. This is a
great example of a good policy and a good funding policy and business getting on and investing.”
While the transition of equipment has been a significant focus for many within the sector, the facilities themselves will undergo a level of transformation to support these net-zero ambitions.
In his press conference at the unveiling, Bowen pointed to Cement Australia’s facility at Railton in Tasmania as another example of how cement industry companies are changing their sites to support decarbonisation.
Bowen said he believed the upgraded facility would provide a bright future for Boral and the wider region.
“Cement is very important to our industrial future. It’s very important to our transformation. There’s more cement in a wind farm than there is steel and I want to see that cement being Australian made. And here at Berrima they’ve been making cement for 100 years almost,” he said.
“And this investment means that they can continue to make cement and they can be showing their consumers, their investors, their insurers, their staff that they have a serious plan – Boral has a serious plan to reduce emissions and that’s what the market will increasingly demand. So, that makes this facility secure into the future.
“This is about working together, business and industry. Our safeguard reforms were designed and have sent a clear signal to industry about expectations for carbon abatement and provided a secure, certain, sensible policy environment so that companies like Boral can make investments like this.
“So, I very much welcome this investment. I congratulate Vik [Bansal, CEO] and the Boral team for this investment. It’s a good day which will see emissions come down and in due course, jobs come up because this facility will be viable for the next hundred years as well.”
Both belt and product are carried on a cushion of air
MONEY SAVING FEATURES:
• Low power consumption • Reliability • Low wear and tear • Low maintenance • High capacity • Light weight belt • Steep angles of inclination • High belt speeds • Dust tight • True belt tracking • Complete settling of materials on belt • Simple conversion from open to closed conveyor
Strain gauging is an indispensable part of the engineering toolbox. Matt Rudas from Aspec Engineering covers the principles, applications and significance of strain gauging in engineering practice.
of machines is based on strength of material calculations, where the quantity of interest is typically stress. Determination of structural stresses requires knowledge of the loads to which the structure is subjected, and this information is not always readily available. One practical method for the determination of stresses is based on the relationship between material stress and the accompanying deformation, called “strain.”
Strain gauges function because the electrical resistance of metal changes proportionally to the amount of deformation that is caused in it by an external force.
Strain gauges consist of a thin metal grid that is etched onto an electrical insulator backing. The strain gauge is bonded to a structure and deforms at the same rate as the structure surface. The measured resistance change in the strain gauge can be used to calculate the surface strain of the structure.
The resistance change that a strain gauge undergoes during deformation is very small. In order to accurately measure it, an electrical circuit called a Wheatstone bridge converts the small resistance change into a voltage change which can more easily be measured. Strain gauge amplifiers can be set up for various Wheatstone bridge configurations, depending on the strain gauge arrangement and temperature compensating requirements for the structure.
Strain gauges are almost always installed onto the surface of structures, and it is typically necessary to measure three strain directions at a single point to completely define the strain field. Measuring strains in three directions is done by installing a stacked strain gauge rosette. There do however exist situations where fewer gauges are required:
• Components with uniaxial, isotropic, and pure torsional stress states require a single strain gauge.
• Components with biaxial stress states only require two strain gauges, however they need to be aligned with the principal stress directions.
Strain gauges can also be installed and wired to either amplify or cancel out particular strain components.
A screenhouse tripper had experienced premature failure of wheel and cam follower bearings due to higher-
than-expected long travel skewing loads. ASPEC installed strain gauges to measure the lateral loads during tripper movements. A wireless telemetry strain gauging system was installed with a 5G network connection that allowed remote and live viewing, processing, and collection of strain data. The system had been calibrated prior to being put into service using a rotable spare bogie set and hydraulic jack for application of the calibration load.
A strain gauging system was installed onto the long travel arrangement of a bucket wheel reclaimer. There was concern that misalignment of the long travel rails was inducing high lateral loads in the equalisers, causing cracking of bogie pillow blocks. The aim of the strain gauging was to determine whether there was a correlation between measured strains and the position of the reclaimer along the rail length, to use the correlation to identify areas where the rails required improved alignment and to generate estimates of the lateral and skewing loads on the equalisers.
Strain gauging is a measurement technique that gives deep insights into structural behaviour. Understanding this behaviour allows engineers to detect weaknesses and address vulnerabilities before they escalate into costly failures and extended downtime.
ABHR finds out what major solution Kinder has for reducing dust exposure on bulk handling worksites.
belt operations presents risks to human health and the environment. Crystalline silica dust, a common byproduct in these operations, has been linked to severe health conditions such as silicosis, chronic obstructive pulmonary disease, and even lung cancer.
The effective containment of dust emissions around high impact load zones and poorly designed conveyor transfer points is of paramount importance to today’s environmentally conscious material handling operators.
For 40 years, Kinder has helped operators across diverse industries address their toughest dust and spillage challenges. It has also designed and built several solutions to reduce dust exposure and this includes a unified system made up of three solutions.
While gas masks are mandatory on sites, some workers outright refuse to work due to the fear of exposure to hazardous dust, including crystalline silica.
“The dust contains crystalline silica, which has a massive impact on causing silicosis. It gets into the lungs, causing irritation and damage to lung tissue, which then leads to permanent scarring
conditions like pulmonary fibrosis. Kinder sees it as its responsibility to prioritise mitigation,” Josh Kay, fields application engineer at Kinder, said.
The risks extend beyond respiratory issues. Workers are exposed to high concentrations of airborne dust that can accumulate in the body over time, exacerbating long-term health problems.
“If we can mitigate it early, we protect not just the workforce, but also the surrounding environment for the long term,” Kay said.
Kinder has developed a specific solution to tackle dust exposure, made up of several products working in tandem. At the centre of this system is DustScrape, which uses a filter box to trap dust while allowing clean air to circulate.
“The DustScrape box contains cloth-like filter material that captures dust particles while ensuring proper airflow,” Kay said.
The system protects workers and enhanced operational efficiency by suppressing dust where it forms. However, to further reduce emissions the company combines it with AirScrape, a unique skirting system.
“The AirScrape sits off the belt and creates a Venturi effect, sucking air into the impact zone and keeping dust contained,” Kay said.
The contact-free system acts as a side seal, suspended over the conveyor belt. With its unique diagonal arrangement of hardened lamellae, air is led from the outside into the middle of the belt, creating powerful air suction.
The material movement together with the moving belt support increases the suction effect enabling fine dust particles to remain in the conveyor section.
“The AirScrape is maintenance-free and doesn’t touch the conveyor belt, meaning there’s no wear and tear on the belt itself. Companies save money on reduced maintenance and longer belt life,” Kay said.
Kinder also provides TailScrape, which fully integrates with AirScrape to deliver outstanding sealing at the rear area, resulting in dust and material spillage reductions, and significant cost savings and resources.
TailScrape proprietary blade structure on the underside ensures a
negative pressure environment within the conveying area. This prevents dust and other material spillage from escaping through the millimetrethick gap.
While Kinder’s solutions can be used independently, the greatest benefit comes from using them together.
“The perfect solution for dust mitigation involves using the AirScrape, TailScrape, and DustScrape in tandem. This combination ensures that dust is handled within the impact zone and doesn’t escape into the environment,” Kay said.
Such systems also contribute to environmental sustainability, as they minimise dust release and protect nearby ecosystems.
“By containing dust effectively, we ensure worker safety, environmental health, and even cost savings for companies,” Kay said.
“Kinder’s products are designed to be maintenance-free and extend the life of conveyor belts. Over five years, the initial investment pays for itself through reduced maintenance costs and fewer belt replacements.
“If businesses don’t address dust issues, they risk litigation and harm to their reputation. Implementing solutions like ours is not just about compliance – it’s about doing the right thing for workers and the environment.”
“We don’t just offer products; we offer solutions. Kinder’s systems ensure dust is controlled effectively, benefiting everyone – from workers to wildlife. It’s an investment in a safer, healthier future.”
By adopting Kinder’s dust control technologies, industries can protect their workers, preserve the environment, and ensure long-term operational success.
drive systems for maximum productivity and reliability
Robust with UNICASE housing
Ready-to-install system solution from a single source
Reliable due to great production depth with high quality standard
Vortex Global has expanded its worldwide operations with recent partnerships and acquisitions.
handling solutions provider, aims to provide innovation, effi ciency, and tailored customer service. To deliver this, the company has entered into new partnerships and acquisitions.
ABHR analyses the latest business moves the manufacturer has made to grow across the world, and what it might mean for the future.
Vortex Global is strengthening its presence in Africa by appointing GNV Enterprise as its official representative for the continent.
This partnership is vital in Vortex’s mission to deliver dry bulk handling solutions tailored to meet the needs of African industries.
“During our initial discussions with GNV, it became evident that their extensive knowledge of industries across Africa would be an invaluable asset to Vortex Global. GNV’s deep insights into various African industries highlight their potential to greatly benefit Vortex Global,” Laurence Millington, managing director of Vortex International, said.
Founded in 2019, GNV Enterprise has pioneered and provided reliable, effective, and cost-efficient solutions. The company serves diverse sectors, including aluminium, mining, pulp and paper, and agriculture. By leveraging strategic partnerships with global technology leaders, GNV ensures seamless integration of advanced solutions into existing operations.
This partnership promises to combine Vortex’s material handling technologies
with GNV’s understanding of African markets, addressing the region’s diverse challenges with precision.
As part of its realignment in the United States, Vortex Global has announced that Adams Brothers Inc. (ABI) will take over representation for the Virginia territory starting January 1, 2025. This transition marks the conclusion of a fruitful 18year partnership with Pace Company, which has been a cornerstone of Vortex’s operations in the region.
Pace Company’s Doris Harkness, alongside her son Nik, have been instrumental in Vortex’s success, bringing unparalleled expertise and dedication since 2006.
“I have had the pleasure of working with Doris and Nik the past four years
and have seen firsthand the drive and knowledge they have to be a top Manufacturers Representative in our industry,” Vortex regional sales manager Matt Fry said.
Pace Company will now focus on air filtration, continuing its legacy of representing top manufacturers in keeping Virginia’s air clean. Meanwhile, ABI, a partner of Vortex for more than 17 years, will take up the mantle. Led by Daniel Smith from its Virginia Beach office, ABI’s seasoned team will ensure a seamless transition and maintain the high standards set by its predecessors.
In a move to enhance its capabilities in the dry bulk material handling industry, Vortex Global has acquired SolidEx, a premier integrator of railcar loading solutions based in Louisiana, US.
This acquisition brings SolidEx’s innovative spin loader technology under the Vortex umbrella, promising to
revolutionise railcar loading efficiency.
SolidEx’s spin loader, developed by founder Tom DePierri, addresses traditional challenges by increasing railcar fill rates from 80–85 per cent to an impressive 99 per cent.
This advancement not only generates cost savings but provides an environmentally friendly alternative, aligning with the operation clean sweep initiative to prevent plastic pellets, flakes, and powders from entering the environment.
Vortex has collaborated with SolidEx for more than a decade, manufacturing components such as positioners and loading spouts to complement the spin loader. By integrating SolidEx into its operations, Vortex aims to offer a suite of solutions for customers seeking cleaner, more efficient loading systems.
Driving innovation across borders
From enhancing its presence in Africa to realigning its representation in Virginia
and acquiring technology through SolidEx, Vortex is focused on growth and customer satisfaction.
By partnering with companies like GNV Enterprise and ABI, and incorporating SolidEx’s technologies, Vortex is making waves in the dry bulk material handling industry.
Not only is it focusing on these developments, but it’s also dedicating itself to creating value for its customers via its innovative and collaborative efforts.
Kotzur understands that one size does not fit all when it comes to silo design.
SILOS HAVE A VERY IMPORTANT, yet simple job in a bulk solids handling operation – store material for later use.
If a silo isn’t fit for that purpose, it can cause all kinds of operational issues.
For example, if a silo is not designed with the material’s bulk density in mind, it can lead to structural issues. This can lead to disaster, causing the structural supports to fail, or the bottom of the silo could tear away and fall out.
Ben Kotzur, chief technical officer at Kotzur, said friction also plays a key role.
“The critical difference between bulk solids silos and bulk liquid tanks, is that solids can carry a shear load. The material sits against the walls of the silo and puts a vertical load into the wall,” he said.
“Also, if the internal friction parameters aren’t understood correctly, it can lead to anything from ratholing to mechanical arching. The material just doesn’t flow, and the silo becomes inoperable.”
Moisture also plays an important role in silo design. If a product goes in moist and dries out or vice versa, the material parameters can change drastically to the point where it will no longer flow.
Corrosion can also take its toll on silos, eating through the structure and weakening it.
“A silo is not a simple structure –it’s a sophisticated piece of equipment that needs to fit the client’s needs,” Kotzur said.
“When we design our silos, there are two main factors – the product being stored and the operational requirements. If you take fertiliser, for example, it needs to be maintained very dry and will cake when too much moisture gets into the product, so the aim is to protect against moisture.
“For mode of use, we look at how quickly the silo needs to be emptied. Does the process require metering? What is the desired flow rate and accuracy? What are the wind and seismic loading requirements? Is the silo subject to a corrosive
environment? These affect both the silo and the systems that sit around it.”
Kotzur has a 70-year history of designing, engineering, manufacturing and delivering industrial equipment in Australia.
The family-owned company, founded in Walla Walla, NSW, has expanded significantly, with facilities in Toowoomba and Perth.
Kotzur said the team believes that every bulk material and engineering challenge can be resolved – it’s just about finding the right solution.
“Our range of custom silos highlights this. It’s not a one-sizefits-all situation – we ensure the glove fits the hand.”
One of the common custom silos that Kotzur manufactures are designed for pellet storage.
Maintaining the quality of the product is one of the highest priorities, which means keeping the material cool and dry, which also controls the risk of self-combustion for some pellet types.
Tempering silos are used to help increase the moisture content of grains, meaning there is a mixture of grain and free water.
Kotzur said that an important part of the process is accounting for swelling loads during the tempering process, which needs to be done during the design phase.
“Not only that, but the mixture of grain and water promotes microbial activity, which in turn creates a corrosive environment,” he said.
Powders can be tricky to handle, which makes understanding the material properties even more important. One example of this is the compressibility of the powder – how the material can increase in density under its own weight. In large silos, these compressive loads can increase the overall density of the material quite significantly.
“We don’t tend to say no to projects. If you’ve got a challenging product, it’s in our nature to think about how we can find a solution.”
In addition, some powders need to be kept dry to ensure they will reliably flow. They also may need to use a screw feeder and appropriately designed hopper arrangement.
To ensure its silos are fit for purpose, Kotzur spends a significant amount of effort at the start of the process to learn about the material being stored.
The engineering team will work with the sales team and the client to create a preliminary design of the silo, allowing the client to provide feedback.
By the time the company is ready with the price and delivery time estimates, its team has a strong understanding about what is required, and what will be included.
Often this process includes analysing sample of material, site visits, and learning more about the physical makeup of the product.
Bevan Austin, Kotzur Bulk Solids national sales manager, said it helps prevent any surprises, and allows the company to discover any issues with the design as early as possible. We always endeavour to have the correct solution or design at the front end to ensure we are offering the best possible solution for the client.
“We also have Kotzur Maintenance Services if a client has any maintenance issues. Our record keeping is very thorough as well –even if a one-off client calls us for help with a 10-year-old silo, we can track down and provide them information easily,” he said.
“Everything is designed in-house – we don’t rely on a third party for design and engineering.
“We don’t tend to say no to projects. If you’ve got a challenging product, it’s in our nature to think about how we can find a solution.”
Engineering and critical equipment supply for the world’s only large-volume, drive-through dome silo in Australia.
is 42 metres high with a capacity to store up to 52,000 tonnes of cement is the dominating landmark of Hallett Group’s Port Adelaide green cement distribution hub.
The almost 20-storey tall structure is one of the first dome silos for Australia’s cement industry and thought to be one of the world’s first large-volume, drive-through dome silo facility. To turn this conceptual design of the dome silo into reality,
Hallett Group awarded IBAU Hamburg the task of designing and supplying the required equipment for the dome silo’s aeration and material recovery system, along with the material handling, transfer and blending processes within the dome silo and the truck-loading and external material transfer from the dome silo.
Hallett Group is a 100 per cent South Australian-owned business and one of the largest integrated construction and building material
suppliers to the South Australian construction industry. Manufacturing locally at its plant in Port Augusta with existing South Australian material reserves, Hallett plans to provide the market with at least 30 million tonnes of new locally sourced supplementary cementitious material (SCM) over the next 20 years.
The new SCMs add new sources for local supply and allow Hallett Group to reduce the carbon content of blended cement as opposed to
traditional clinker-based cement. This gives Hallet Group the capability to supply some of the lowest carbon concrete compared to anywhere in the world from South Australia.
The Port Augusta plant will draw on millions of tonnes of fly ash left behind by Port Augusta’s demolished coal-fired power station and use fume slag waste materials from Nyrstar’s Port Pirie smelter. The Fly ash and slag products will be milled, processed and blended at Port Augusta before being transported to the Port Adelaide distribution hub and the dome silo for final processing and distribution of the green cement, both to domestic and overseas customers.
With Flinders Port Holdings, Hallett Group upgraded the wharf
at Berth 25 at Port Adelaide’s Inner Harbour to serve as its green cement distribution hub. The upgraded wharf will be a common-user berth, increasing import and export capacity, and will be able to service vessels up to an overall length of 185 metres. Besides the 52,000-tonne cement storage dome to minimise dust and other emissions, Hallett Group’s hub will have a 15,000-tonne flexible SCM storage shed and stateof-the-art on-demand green cement blending and distribution ability. The on-demand cement blending facility will accelerate cuts in embodied carbon in concrete. (Concrete is the highest volume construction material used globally.)
IBAU Hamburg, a Haver & Boecker company, is well known for its advanced silo technology and economic silo systems, silo conversions, terminals, carriers, ship unloaders, all relevant components, spare parts and services. Included in its portfolio of offerings is plant design with complete engineering and EPC contracting, supply and erection, technical supervision of civil works, steel structure and electrical and mechanical works.
The company has one principle: to always find appropriate, high-quality, innovative, customer-oriented solutions, making it well-positioned to partner with Hallett Group on the dome silo project.
A unique and innovative feature of the dome silo facility is the inclusion of a self-contained batchtype mixing plant within the dome silo. This involves the integration of several smaller storage silos and state-of-the-art, on-demand green cement blending and distribution function complete with truck loading within the dome silo structure.
The unique drive-thru, truckloading aspect of the dome silo effectively splits the dome silo in two. To provide the required 300 tonnes per hour discharge capacity, the resultant 42-metre diameter base of the dome silo required highly
efficient and effective aeration of the massive floor space. Each half houses approximately 900 square metres of aeration pads, an IBAU cut-off gate, an IBAU lump-crusher, an IBAU flowcontrol gate, blowers complete with 45 kW motors and silencer hoods for silo bottom aeration.
To prevent the buildup of cement upon the internal structure that encompasses the additional storage silos, blending and drivethrough/ truck loading facility, the 1000-square-metre roof space required a comprehensive array of additional air pads and a dedicated air supply for effective aeration.
The respective batch-type mixing plant and truck loading facility contained within the dome silo comprises two small day silos for dosing cement as required, three additional small raw material/ ingredient silos, discharge and dosing equipment from silos to a mixing station involving two weighing bins feeding into a batchtype mixer installed underneath with a capacity of up to 150 cubic metres an hour.
The facility also contains a pneumatic screw pump to transfer blended product to provisional storage silo’s external to the dome silo, fluidslides to truck loading, a high-pressure fan and IBAU loading chutes with capacities of 420 cubic metres per hour.
The scale and depth of these features position the dome silo as a true feat of modern engineering and a shining example of IBAU Hamburg’s capabilities.
TUNRA Bulk Solids engineer Ben McPherson and engineering manager Dr David Bradney discuss the challenges surrounding gravity-reclaim stockpiles and the risk of stockpile dozer engulfment.
GRAVITY RECLAIMING IS A WIDELY used method in bulk material handling systems, particularly in industries dealing with coal, ores, and similar granular materials. The process involves a series of ground-
level hoppers buried beneath a stockpile of material. These hoppers remain closed while the stockpile is being built. Once the hoppers are opened, the material begins to flow down through the base of the
stockpile, feeding onto a conveyor or cart system below. This method leverages the natural flow properties of bulk materials, providing an efficient means of reclaiming large volumes of material.
However, the operation is not without challenges. The flow within the stockpile is often uneven, with distinct zones of movement and stagnation. The flowing regions form around the hoppers, while large portions of the stockpile remain static, creating risks of instability.
• Arching occurs when a stable obstruction occurs across a hopper outlet, effectively blocking material flow. Arching may result from the mechanical interlocking of larger particles or cohesive bonds forming between material fines. Mechanical intervention is often required to break arched obstructions.
• Ratholing is often exhibited by materials with a high proportion of fines or high cohesive strength and involves the flow of material through narrow vertical paths above the hoppers, leading to stagnant areas surrounding the hoppers. When flow problems like ratholing
occur, heavy machinery, such as dozers, are often deployed to dislodge stagnant material. While effective, this practice carries significant safety risks. The use of dozers in areas prone to collapse, such as unexposed ratholes, has led to numerous incidents of equipment engulfment and operator injury. This underscores the importance of establishing and maintaining safety radii for stockpile dozer operations.
The flow properties of bulk materials are fundamental to understanding how they behave during handling and storage. These properties are influenced by factors such as particle size and shape, moisture content, bulk density, consolidation pressure, and internal friction. These properties govern the material’s ability to flow, form arches, or resist movement, making them critical for the design and operation of stockpiles, hoppers, and
conveyors. The flow characteristics can vary significantly depending on environmental conditions, such as humidity or compaction, further complicating handling processes.
The design of gravity reclaim stockpile storage facilities requires knowledge and precise quantification of the flow properties of particular materials under a range of operating conditions, including varying consolidation pressures, storage times and moisture contents. The comprehensive laboratory facilities at TUNRA Bulk Solids permits the characterisation of bulk material properties using well-established test procedures. Flow properties testing is typically conducted to identify the “worst-case” scenario for material handling. This is often associated with the material exhibiting its highest strength and cohesion. Under these conditions, the material is more prone to forming arches or cohesive
blockages, resulting in issues such as hang-ups in chutes, buildup in hoppers, and poor flow through reclaim systems.
In contrast to the aforementioned “worst-case” scenario for bulk material properties, safety concerns for stockpile dozers arise when they operate in proximity to areas of low bulk material strength in a stockpile. These areas of low bulk material strength are much more likely to collapse and fail around any unexposed ratholes that may have formed, leading to increased
probability of equipment engulfment accidents (as seen in Figure 1).
TUNRA Bulk Solids have been engaged on several occasion to use flow properties testing to determine the minimum dozer safety radii. Using supplied material samples, the TUNRA Bulk Solids laboratories can conducted flow properties testing to determine the moisture state in which the coal samples exhibited the maximum and minimum bulk material strength. The bulk material sample can then be tested in its weakest moisture state to determine
key aspects of its behaviour via, direct shear testing, angle of repose (AoR), and drawdown testing.
The flow properties results obtained by the TUNRA Bulk Solids laboratory can then be used to determine the critical rathole geometry for a stockpile at the weakest-state moisture content. The predicted rathole shape and geometry are subject to variability depending on the applied theory, as certain approaches are known to predict varying degrees of conservativeness of the estimates.
TUNRA Bulk Solids use two main theories to determine the minimum safety radii of the dozer. One theory stems from the measured AoR of the bulk material, and the other is based on the materials measured internal strength. The final rathole safety radius is chosen to represent key aspects from the main predictive theories, acting as a middle ground in terms of conservativeness.
It should be noted that the safety radii represent the outer bounds of the estimated rathole, and so a stockpile dozer safety zone exceeding this is advised.
Overall, gravity reclaiming is a widely used method for handling bulk materials in high-throughput applications, but it comes with inherent challenges, such as ratholing and arching, particularly when material flow properties are not fully understood. These challenges pose significant safety risks, especially for stockpile dozer operations. To address this, TUNRA Bulk Solids uses flow properties of the stockpile material to identify critical conditions that contribute to stockpile instability. Through laboratory testing, including the angle of repose, drawdown angle, and flow property assessments, TUNRA can determine the weakest moisture state of the material and use predictive theories to calculate minimum safety radii for dozers, allowing clients to establish safer operating zones, minimising risks associated with unexposed ratholes, and ensure enhanced safety for their stockpile management practices.
Industries that incorporate bunkers, silos, chutes, transfer points or hoppers into a system encounter bulk material blockages, reducing productivity and, in some cases, bringing operations to a halt.
The ESS Air Cannons are pneumatic bulk material flow aid systems that utilise the release of a volume of compressed air.
This sudden release of energy is directed through a transition pipe into compacted material in a bin, silo or stockpile to dislodge that material, restore flow and regain storage capacity.
BENEFITS OF ESS AIR CANNONS:
• Enhanced Material Flow - Effectively clears blockages and prevents build-up.
• Increased Equipment Lifespan - Eliminates components prone to wear, like springs.
• Improved Safety - Reduces hazards with on-demand filling and remote activation.
• Remote Activation - Controlled via a Sequence Controller for precise timing & coordination of multiple air cannons.
• Customisable Solution - Wide range of configurations and tank sizes to meet specific requirements.
Daniel Ausling and Steve Ash of BG&E Resources explain how a novel innovation involving 200 tonnes of Australian-made steel solved crusher vibration at Rio Tinto’s Hope Downs 4 Site.
operations are often faced with oversized material impacting the primary sizer or ‘balling’ of rock within the primary sizer, causing severe vibration.
Balling is the bouncing of large boulders in between the sizer heads and against the walls - it leads to high impact-related damage, fatigue, and maintenance issues.
This was certainly the case at Rio Tinto’s Marandoo Hope Downs
4 (HD4) primary crushing facilities, where excessive levels of vibration were identified at the facility over an extended time. Structural fatigue/failure, equipment failure, building components rattling loose, and risk to personnel safety were all witnessed as a result.
BG&E Resources (BGER) and Engineering Dynamics Consultants (EDC) were engaged by Rio Tinto to deliver an innovative design solution to solve the excessive vibrations. By leveraging proven technologies from other industries,
BGER and EDC delivered a fit-for purpose solution in what is believed to be a world-first application without any unknown risks for the asset owner.
Understanding the problem
Rio Tinto identified the primary crusher building as a significant health and safety risk to workers due to guarding, handrailing, grid mesh clips and stairs coming loose due to the excessive vibration. Under further investigation, it was discovered that the severity of the
crusher vibrations was so extreme that the reliability and structural integrity of the entire facility was compromised, presenting an unacceptable risk level to personnel and operations.
Unravelling the challenges
Rio Tinto required a solution that not only kept the original level of functionality but would ideally increase functionality and throughput to new levels. It was concerned with the possibility of significant lost production and the requirement to re-train site personnel on the use of new, or substantially different, equipment.
Strengthening the existing structure to reduce the vibration to acceptable limits would have proven almost impossible to achieve within reasonable cost. This is due to the level of vibration experienced and the complexity of the system, coupled with the inability to effectively position additional structural supports. Fundamentally, a complex
problem lay ahead, and a different structural form was required.
Delivering a novel solution
BGERs multidisciplinary structural, mechanical and electrical engineering capabilities, combined with EDC’s
expertise in detailed dynamics modelling and on-site dynamic testing, resulted in the creation of a world-first application.
Proven technologies from high-rise earthquake isolation, haul trucks and rail chassis were borrowed and combined to minimise the risk of design uncertainty
TUNRA Bulk Solids develops custom solutions to suit the individual needs of our clients.
Flow Properties and Materials Testing
Dust (environmental) Testing
Wear Testing (Impact, Abrasion and Erosion)
Conveyor Belt, Idler Roll and Pulley Testing
Discrete Element Method (DEM) Modelling
DEM Calibration Testing
Materials Handling Consultancy and Contracted Research Bin and Stockpile Design
Pneumatic and Hydraulic Conveying
Computational and Scale Modelling
Site Visits
Professional Development Courses
VORTEX DESIGN PHILOSOPHIES:
Vortex believes in offering only value-added products that are designed for purpose, rather than producing off-the-shelf, commodity components. With an in-house team of application engineers, Vortex designs for the most demanding applications.
Vortex closely studies the characteristics of thousands of dry bulk materials and how they interact with various materials of construction. We assess the wear potential for each client’s process and make application-specific modifications to ensure reliability, durability and longevity.
the construction contractor utilised the VR environment to prepare for timesensitive shutdown work with in-depth inspections into the model. This helped to identify and plan mitigation strategies of potential on-site complications.
Providing stakeholders with the opportunity to understand the design and witness verification of the physical system’s performance under test conditions during the factory acceptance testing phase was a key to success. This reduced the time taken to assemble steelwork on-site by allowing a firstpass assembly, proof of concept and spot-checking of any fabrication/ assembly errors.
All too often, standardised designs or methodologies are used at the expense of providing an optimal solution.
The project team takes on a bespoke methodology of ‘complex to simple’ –where we take a complex problem, reduce
Our priority is to keep you up and running – because in your world, there is no time for downtime. Vortex components are engineered with in-line service features that accelerate the system maintenance process, saving your team time and money.
Vortex approaches wear parts with simple, durable design. Doing so means maintenance procedures are also kept simple while the need to perform maintenance is infrequent. This leads to a reduction in spare part inventories and a reduction in costs.
End users are often attracted to equipment on the fallacy of low price, ignoring the cost-benefits of reliability and longevity. Vortex believes in designing products that will out-perform and outlast market alternatives – so that end users realize the full value of their investment.
Facilities have an ethical obligation to protect against the hazards of manufacturing. Vortex closely studies trends in air quality, environmental dust emissions, workplace safety and evolving regulations. Our components are designed with these concerns in mind.