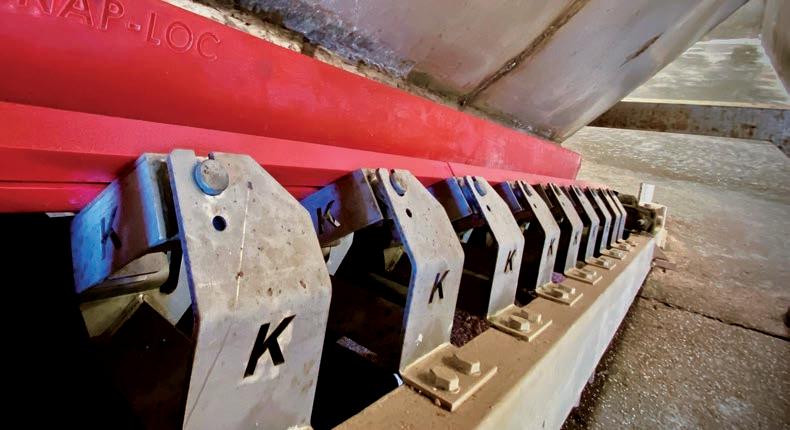
4 minute read
Kinder K-sure creates corrosion-free transfer zone at fertiliser plant
When a Toowoomba-based fertiliser supplier needed help fighting rust and corrosion, it turned to Kinder Australiaforthe answer.
TIM STORER WAS ON THE
way to the airport to head home after meeting with a distributor in south-east Queensland.
But before the Kinder Australia field application specialist could catch his flight, he received a phone call from a local supplier of fertiliser-blended products.
Storer’s role means it’s job to visit bulk material handling sites to qualify and quantify the problems they are facing and to provide solutions. After a quick discussion in the car, he made a U-turn and headed towards the site.
The client’s core business relies on various material blends, such as phosphate and calcium, processed and mixed in the plant’s hopper. The finished fertiliser product is then bagged and sent to nearby shopping retail outlets.
Storer said the moment he walked into the bagging house, the issue was evident.
“Spillage had become a serious problem at the site, to the point where the fugitive material had created a false floor which was a O/S issue. Looking at all the machinery, there were clear signs of significant rust and corrosion,” he said.
“The technology used in the plant was older and couldn’t keep up with the amount throughput required.”
The plant used steel idler frames with soft rubber skirting for its primary line of support within transfer point areas. Site inspections found the highhumidity environment and atmosphere generated within the hopper from blended materials was a key contributor to the rust and corrosion damaging critical plant and equipment.
Corrosive rust present on the idler frames was so severe that the frames were ready to collapse, a situation that could cause production havoc and short-term shutdowns for the operator.
Belt sag between the idlers was also identified as a key area for rectification. The material being loaded was not being adequately supported, which caused
The system after the K-Sure and K-Snap-Loc were installed. skirting to lift away from the belt line.
This caused major spillage and product loss, with up to one tonne of product written off each season, not to mention additional maintenance and clean-up costs to remove spillage.
After a thorough audit, Storer recommended Kinder’s conveyor belt support and skirting solution.
“Because of the nature of the system, they needed to control the load and capacity,” he said. “Due to the corrosive nature of the fertiliser blend, we switched from mild steel to stainless steel, introduced the slider rail and got rid of all of the rollers and moving components.
“The installation of stainless-steel idler frames and brackets ensured rust and corrosion wouldn’t be an issue.
“The K-Sure Belt Support System also made it so the material had nowhere to go, improving the K-SnapLoc skirting system effectiveness.”
The K-Snap-Loc Dust Seal System is made from engineered polyurethane which can withstand high abrasive and high-temperature applications. It has an inherent “memory-set” that is used to apply downward pressure onto the belt’s surface to create a fine tight seal, without the need for manual adjustment.
Storer said fitting the K-Snap-Loc took around five minutes, with no specialised tools required to replace it.
One of the key things that sets it apart from other skirting systems is the way it lays in on the belt, conforming to whatever is sitting underneath it. In tandem with Kinder’s belt support system, the skirt can stay in one position to contain the material and its polyurethane places less stress on the belt than rubber does.
Following the installation, the targeted area of the plant now runs cost-effectively at full capacity, without issue.
Storer said material spillage has dropped from one tonne per season to around one kg, which is likely to be from loading the hopper above.
“I’ve been in contact with the site over the past 12 months to see if they were happy, or if there were any modifications required. They’re happy to report everything is working amazingly well,” he said.
“We followed up with another site visit to make sure everything was working as intended. They have a good understanding for what they need to do, and we offer fully after sales support if they require it.”
Kinder has a full engineering team that works with field application specialists to determine the most effective solutions. The team will work with clients to develop concepts, provide preliminary drawings, and can make adjustments where needed.
The company can manufacture its components locally or overseas, depending on how fast the components are required.
Storer said he plans to do many more day trips to Queensland, Victoria, and the Northern Territory.
“It doesn’t take us long to find the cause of the problems,” he said. “Our field teams are highly experienced and have developed an eye for finding the problem.
“We also work across a wide range of industries. We might be down at a quarry in the morning, at a woodchipper for lunch and visit a fertiliser plant in the afternoon.
“Our team have experience working with plenty of machines and are eager to show how we can help.”
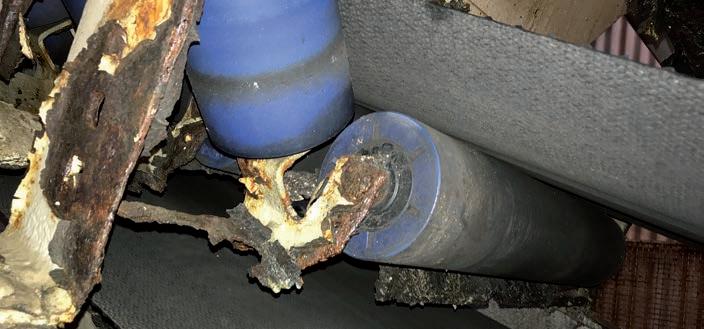
The presence of corrosive rust caused conveyor componentry damage.
Bulk solids storage and handling solutions generated in Australia for Australian Conditions



Walla Walla, NSW Toowoomba, QLD Perth, WA
(02) 6029 4700 (07) 4634 4622 (02) 6029 4700