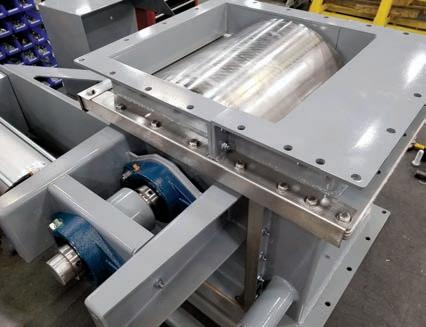
4 minute read
Vortex Global makes conveying cement aglide
Vortex Global makes conveying cement a glide
To make handling dry cement easier, Vortex Global has designed a new air-gravity conveyor system.
HANDLING CEMENT IS A
notoriously difficult process, as it tends to clump together into a solid mass. This can create plugs that block processes and are hard to move.
Vortex Global, a manufacturer of loading spouts, slide gates and other equipment for the dry bulk solids sector, listened to its customers in the cement industry. They wanted a better way to convey the material that was simple, gentle and easy to maintain.
The solution Vortex Global developed was the Aero-Slide.
The Aero-Slide is an air-gravity conveyor, which consists of a rectangular chamber separated by an air-permeable, porous media. The media is placed along a horizontal plane to separate two chambers within the conveyor.
An upper chamber handles the material being conveyed while the lower chamber handles the compressed air. A positive fan or blower injects low pressure, dry air into the lower chamber, which then permeates upward through the porous media. When the air is counterbalanced by gravity, the material flows downstream in a fluidised/aerated form, across a surface similar to an air hockey table.
Laurence Millington, Vortex Global’s managing director, said this method makes cement easier to move.
“Compressed air is relatively inexpensive as a commodity, and the system – once it has been switched on – contains everything within. No dust can escape,” he said.
“It’s a very simple system. There are minimal moving parts and the only wear that occurs is on the bottom mesh. It’s been designed for longevity and to be maintenance friendly.
“Our ethos for manufacturing is to create products that are well designed, made from high quality materials and are engineered to remove issues for our customers.”
Gravity does helps move the material, with most Aero-Slides installed at around six to eight degrees downward to be effective.
Air-gravity conveyors are used to handle a variety of dry, light-weight, easily fluidised powders, such as activated carbon, alumina, bentonite, calcium carbonate, cement, clays, detergent powders, or talc. A general rule of thumb is that the particle size is normally smaller than 50 mesh.
When designing an air-gravity conveyor system, the types of metering gates that control the flow of material are a key consideration. Typically, material is introduced from a bin or silo by opening a slide gate at the bottom of the vessel. The fine material is then aerated and flows into the conveyor.
Vortex Global has also developed the Aero-Drum valve, specifically for use with the Aero-Slide conveyors. The valve can be operated through electric, manual, or pneumatic actuators and does not use the traditional ‘v-notch’. Instead, the drum opening is a parabolic curve that is symmetrical from either side, allowing the drum to be positioned in a full-open or full-closed position.
The internal drum seal is made of needled polyester, increasing rigidity and offering high abrasion resistance. To make maintenance easier, the valve contains a split inlet flange that can be removed independently from the valve body.
One of Vortex’s customers was concerned that a simple, vertically mounted air slide gate would not be able to completely seal material and thus create a cross-contamination issue.
The Vortex drum valve was chosen to act as a flow control and a shut valve for the application, which has worked well for the customer’s application.
Millington said the company is always looking for new opportunities and products to solve its customers’ problems.
“We have a designated team of engineers that are looking at different things we can design to improve our offering,” he said.
“If we can provide better gate valves, loading spouts and conveyors, we can build a system that will offer better results.”
The Aero-Drum valve is designed specifically for use with the Aero-Slide conveyors. The Aero-Slide is an air-gravity conveyor, which consists of a rectangular chamber separated by an air-permeable, porous media.
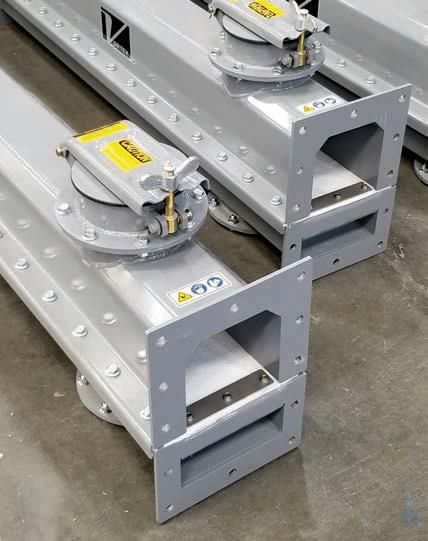
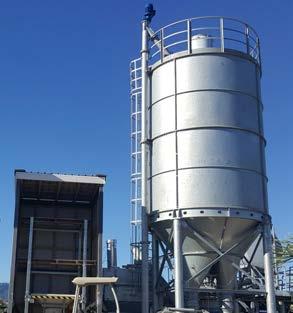
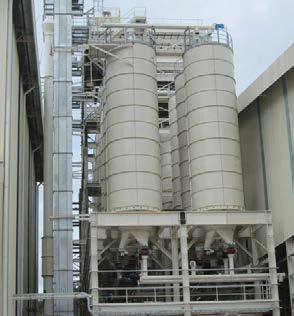
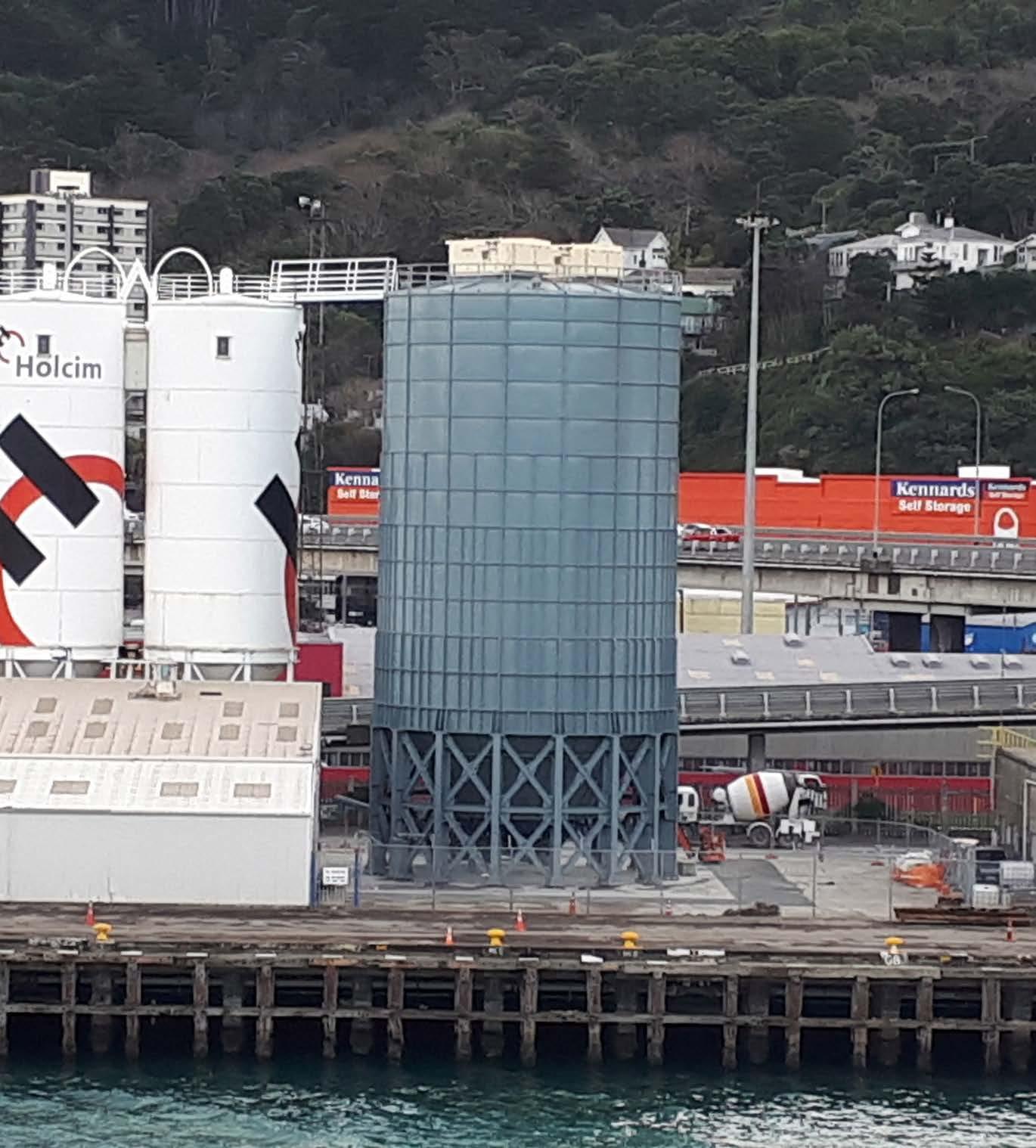
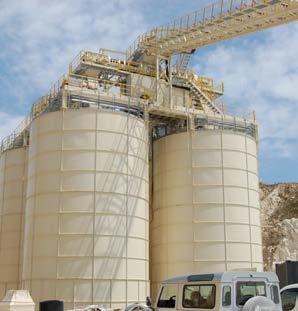
WORLD LEADERS IN MODULAR BULK STORAGE SILOS
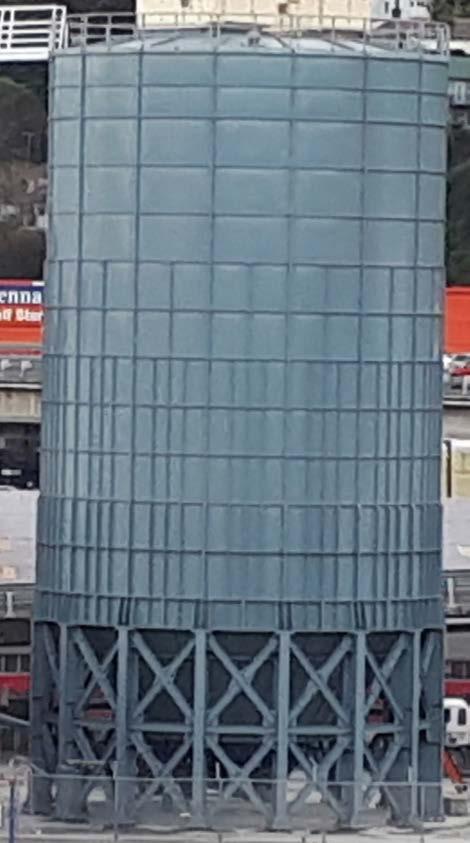
Silos and Conveyors Systems Limited are proud to represent Scutti for past 22 years, the world leading suppliers of modular dry bulk storage silos & material handling equipment. We can service any project across multiple industries within Oceania, Asia and the Pacific.
Specialising in the design and supply of modular bulk dry storage silos and material handling equipment for any project, no matter how big. We have 30 years of experience suppling equipment, project management and design expertise to projects all across Oceania, South East Asia and the Pacific. Our silos vary from 10 cubic metres all the way to 3500 cubic metres in capacity, and the applications can be applied to various industries and supply chains. With multiple happy clients across the South Pacific, it would be our privilege to work with you and your bulk storage handling needs.