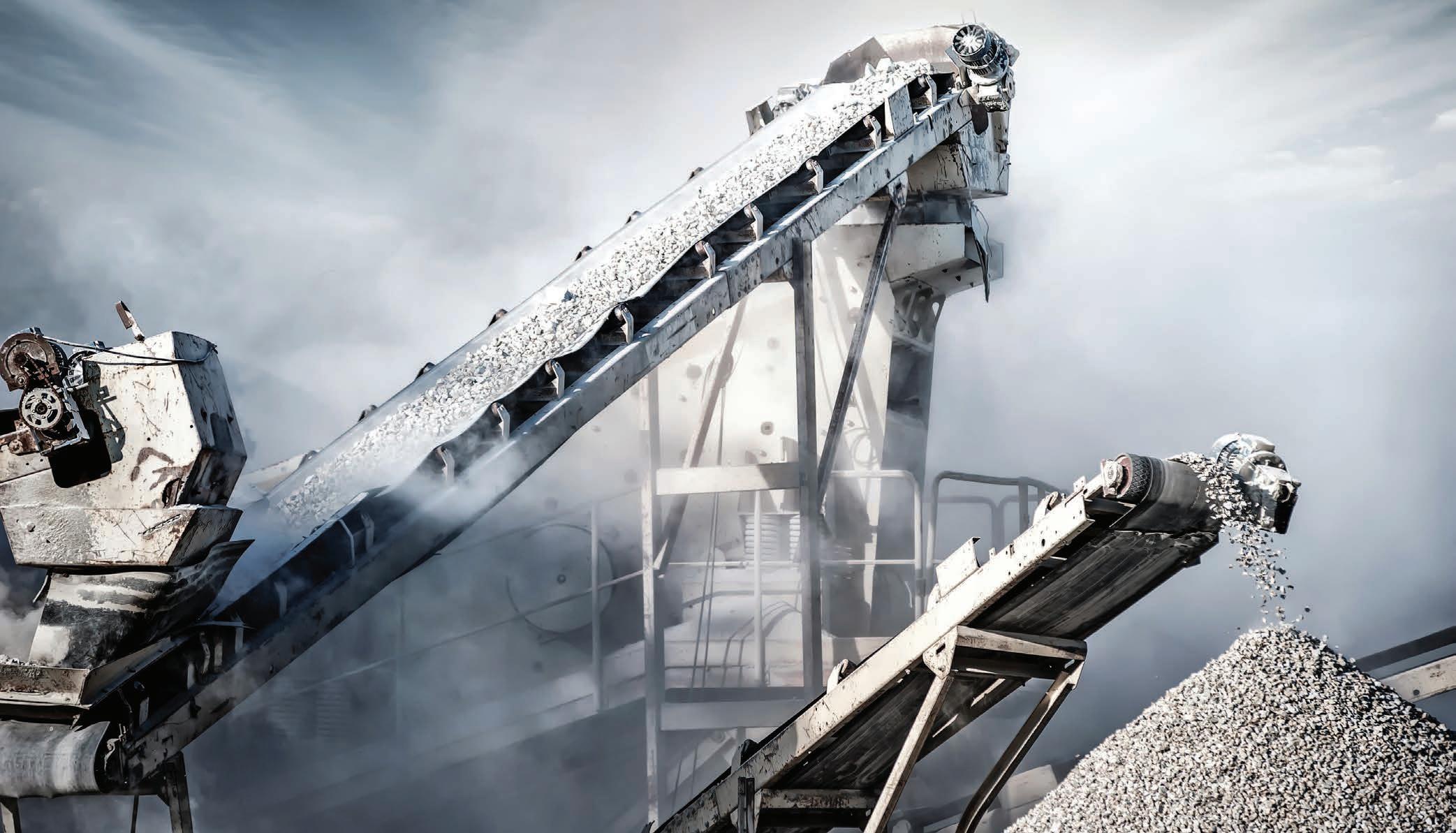
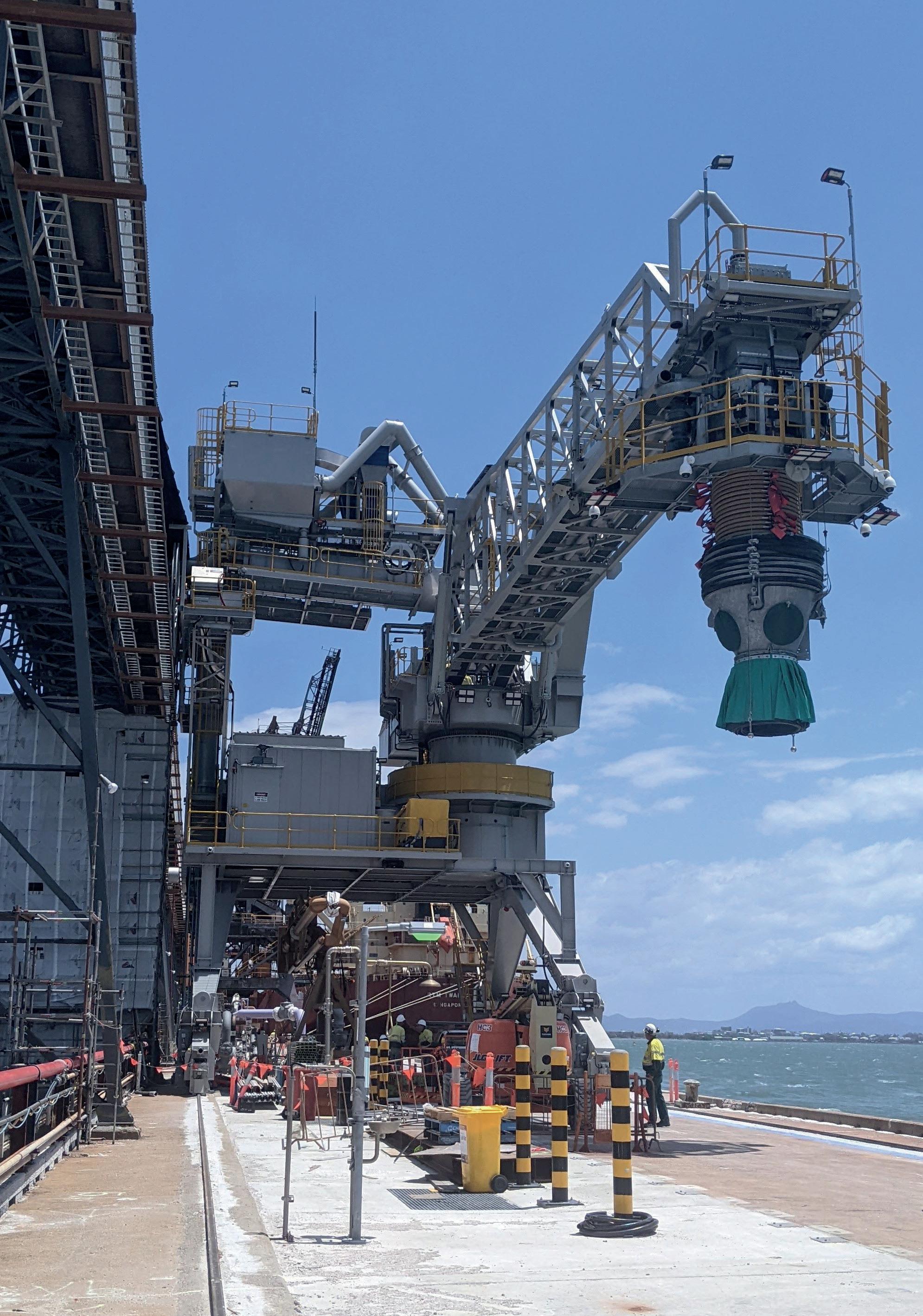
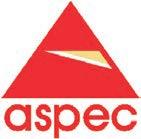
When it comes to optimising powertrain performance, Regal Rexnord provides the bulk handling industry with end-to-end engineered solutions and market leading service and renewal support. So contact us today and discover how we provide complete and fully integrated outcomes that enhance efficiency and reliability.
Published by:
379 Docklands Drive
Docklands VIC 3008
T: 03 9690 8766
www.primecreativemedia.com.au
COO
Christine Clancy
E: christine.clancy@primecreative.com.au
Editor William Arnott
E: william.arnott@primecreative.com.au
Journalist
Adam Daunt
E: adam.daunt@primecreative.com.au
Business Development Manager
Rob O’Bryan
E: rob.obryan@primecreative.com.au
Client Success Manager
Janine Clements
E: janine.clements@primecreative.com.au
Design Production Manager
Michelle Weston
E: michelle.weston@primecreative.com.au
Art Director
Blake Storey
Design
Michelle Weston
Subscriptions
T: 03 9690 8766
E: subscriptions@primecreative.com.au
www.bulkhandlingreview.com
The Publisher reserves the right to alter or omit any article or advertisement submitted and requires indemnity from the advertisers and contributors against damages or liabilities that may arise from material published.
© Copyright – No part of this publication may be reproduced, stored in a retrieval system or transmitted in any means electronic, mechanical, photocopying, recording or otherwise without the permission of the publisher.
When gold was first struck in Victoria in the 1850s, the state underwent a rapid transformation.
People flocked from all around the world, quadrupling Melbourne’s population from 77,000 to 540,000 in just ten years.
When gold overtook wool as the state’s primary export, profits were channelled into public projects. Building supplies, in particular lumber and bricks, began booming as well, along with the food industry to keep up with the expanding city.
Public buildings were rebuilt to signify the city’s grand transformation. Many of them, including Parliament House, the Public Library, Melbourne University and the Treasury building stand tall today.
Streets were paved, infrastructure was built, and the economy flourished. It was a period of incredible growth, and as the saying goes “during a gold rush, sell shovels.”
In this edition of Australian Bulk Handling Review, we shine the spotlight on local manufacturers that have continued supporting the industry through times of boom and bust, providing the vital equipment that industries like mining need to succeed.
Australian manufacturers often play a vital role in regional and rural communities. Factories keep people employed, supporting the community’s economy and cohesion.
They also have the home ground advantage when working with Australian customers, bypassing frustrating language, time zone, and paperwork barriers. Additionally, local manufacturers understand the harsh Australian climate and can build their equipment to last.
Many of these manufacturers will be attending the 2024 Australian Bulk Handling Expo (BULK2024). The event, which will take place at the Melbourne Convention and Exhibition Centre from 18–19 September, will host the latest technology and innovations.
Attendees and exhibitors will come together to connect, network and share knowledge. Key decision-makers from a broad range of industries will have the opportunity to get an close-up look at the latest in technology and innovation, whether they specialise in agricultural silos, shiploaders, or mining conveyors
Additionally, the event will host the Australian Bulk Handling Awards, the only awards program that highlights the quiet achievers of the Australian economy.
ABHR will be providing coverage of the event, and invites you to attend.
ONE SUPPLIER FOR THE LIFE OF YOUR CONVEYOR
Conveyor Belt
Conveyor Components
Conveyor Engineering & Design
Conveyor Systems
Conveyor Technology
Conveyor Services
Phone 1800 Fenner (336 637)
Find out who won what at the recent Women in Industry Awards.
Business Development Success of the Year 2024
Sandra Robinson - United Rentals
Sandra Robinson held the role of BDM for Kennards Major Projects Division for just under a year before she was promoted into the position within less than a year.
Steph Gee - CM & SM Gee Electrical
A fully licensed electrician and business owner, Steph Gee has a knack for making the complex seem simple and leads by example, actively promoting gender equality and empowerment on the jobsite while holding influential positions on national industry boards and Government training and apprenticeship committees.
Kirstin Reblin - Opal
Kirstin Reblin embodied the essence of Mentor of the Year through selfdriven initiatives and unwavering advocacy for women at Opal. She has tirelessly fostered female talent at Opal across all functional areas, hierarchy levels, and sites, ensuring inclusivity and empowerment at every turn.
Safety Advocacy Award 2024
Kathleen Kelly - McConnell Dowell
With a background spanning construction, operations, human resources, OH&S, training, WorkCover claims, and injury management, Kathleen Kelly is deeply passionate about crafting and implementing health, safety, and wellbeing programs.
Kate Leone - UGL - M6 Stage 1 Project
Kate Leone is a versatile, multidisciplinary problem-solver, passionate about engineering for change and being at the forefront of technical innovation. She is an advocate for increasing global access to technology and diversity in STEM and has bold ambitions to lead her own projects with a complete gender balance.
Anne Modderno – Swietelsky
Anne Modderno, the first female managing director of any Swietelsky international subsidiary, has led significant progress since her appointment in May 2023. She spearheaded the development of the company’s Sustainability Strategy.
Allyson Woodford - APA Group
Allyson Woodford is a visible and experienced engineering leader leading more than 355 people to support APA’s $22bn worth of critical energy infrastructure across Australia.
Derelle Mitchell - Health
Focus Manufacturing
Managing director Derelle Mitchell founded Health Focus Manufacturers (HFM) after purchasing the assets of a cosmetic manufacturing company. Starting with just three staff, a basic commercial property and a small office space converted into a lab, Mitchell has built HFM into a $10M business.
Sinead Redmond – GeelongPort
Sinead Redmond has extensive experience in project delivery across various areas and is an influential leader who works within business development, directing large teams and managing stakeholder expectations.
Sinead Booth – Fortescue
Sinead Booth, a leader and trailblazer in the mining industry, epitomises excellence and innovation as the head of decarbonisation delivery at Fortescue.
Vesna Olles - BOC Limited
Vesna Olles is director for Clean Energy and Strategy at BOC South Pacific, and a key member of BOC’s executive leadership team. She has been in this leadership position since October 2019, driving the company’s strategic direction in clean energy.
Derelle Mitchell - HFM
artin manufactures a broad variety of screen vibrators — electric, hydraulic and pneumatic — designed to efficiently sort bulk material by size. Our electric vibrators are the industry’s go-to direct replacement for Derrick® shaker screen motors. And all our vibrators come with an unsurpassed 3-Year Warranty.
Around the world, Martin Engineering delivers the cleanest, safest, most productive solutions to bulk material handling issues — now, for more than 80 years. Get shakin’ with Martin.
Aspec Engineering specialises in addressing complex materials handling challenges. ABHR learns how the company recently helped find the right dust control solution for a critical alumina shiploading project.
Queensland Alumina Limited (QAL) has been one of the world’s leaders in alumina production.
The producer was looking to improve its operations, specifically when it came to dust control. Alumina dust is made up of very fine particles that are easily caught by the wind.
Adam Mayers, principal mechanical engineer at Aspec Engineering, said the site was looking for ways to improve upon its infrastructure, which is why QAL contracted ASPEC to find technologies that could help reduce dust emissions.
“They contacted us to help come up with a concept that would eliminate dust during ship loading, without increasing loading on the existing wharf,” he told ABHR.
“Our first step was to try and identify the root causes. The existing shiploader used air slide conveyors on a boom that ‘luffed’ from horizontal to near vertical. When this happened – usually during a vessel hatch change – it compromised the conveyor seal, allowing alumina to escape and resulting in dust emissions.
“If a ship had five hatches that needed to be visited three times each, you could be looking at up to 15 potential events.
“The conveyors and transfer chutes were also prone to entraining excess air, which when combined with the belt cleaners, allowed alumina product to bypass containment measures and be released as dust.
“Inconsistent feed control to the shiploader from upstream storage sheds exacerbated the dust generation by overwhelming existing materials handling and dust collection systems.”
Aspec Engineering began exploring the market, looking for technologies that could handle the task. One of the first steps in its process was challenging the assumptions and criteria involved.
The engineering team soon found that a luffing motion wasn’t needed to load the vessels. Instead, the new infrastructure would use a ‘slewing’ method. This eliminated the need to lift the boom to the same extent for the hatch change and meant that the conveyor seal and the landward end of the boom could be maintained continuously, keeping the material contained.
In addition, several advanced dust control features were included in the new infrastructure, including enhanced ‘airslide’ or ‘air-gravity’ conveyors that utilise low-pressure air to fluidise alumina. This facilitates sealed downhill flow with no moving parts.
A Cleveland Cascade loading chute was also incorporated to maintain consistent slow flow speed through a sequence of inclined cones within a dust containment shroud, preventing air entrainment and dust generation.
Belt cleaning processes, including primary, secondary, and ‘air knife’ cleaners, were improved at the tripper
discharge point onto the shiploader. Selfcleaning dust collectors also generate negative pressure within the system to prevent dust from escaping.
Mayers said one of the main goals of the project was to ensure the upgrade could be completed without affecting production or requiring major wharf upgrades.
“One of the big challenges was the age of the wharf,” he said. “New machinery tends to be heavier due to modern design standards, but the wharf couldn’t accommodate heavier wheel loads without major changes.”
“Changing the design to a slewing shiploader meant we didn’t need a large tower to facilitate the luffing range, which reduced a lot of weight. It was also not as tall, which was important for keeping the wind loads down through a lower profile.”
“We also helped come up with an innovative risk-based approach to prioritise repairs to the wharf. This helped solve any interface issues and meant the wharf was ready to receive the Shiploader when needed.”
The detailed design and supply of the shiploader and upstream dust control upgrades was awarded
to Reel Alesa, a specialist Alumina materials handling supplier.
Following design, fabrication, off-site erection and pre-commissioning, the machine was transported to the QAL site via heavy lift vessel and delivered, fully assembled, in November 2023 for tie in works and commissioning.
The offshore fabrication and full assembly of the shiploader helped to minimise disruptions to berth operations. Stringent third-party quality inspections were essential to rectify defects identified prior to delivery to the site.
“During the inspection, we identified issues with the quality of the fabrication and painting, so we brought in welding and paint experts to find solutions before the shiploader arrived on site,” Mayers said.
In December 2023, the machine commenced full operations with negligible dust emissions.
Mayers said the project was a significant success.
“Throughout the design process, there was a lot of focus on simplification, to ensure the machine was easy to operate and maintain,” he said.
“QAL appreciated our support. We were with them throughout the entire process, offering our technical expertise. We even went to the United Arab Emirates at short notice to inspect the machine and address any issues before it was delivered to site.”
These kinds of projects are an everyday occurrence for Aspec Engineering. The company has spent the past 20 years offering its engineering support to vital bulk-handling infrastructure. It has also been involved with the design and supply of shiploaders across Australia, supporting the major mining companies.
Over the decades, Aspec Engineering has developed a core team of experts with a deep knowledge of the industry.
Mayers said this depth of knowledge allows Aspec Engineering to react quickly and draw upon a vast network to solve client needs quickly and efficiently.
“Aspec Engineering has a low turnover of staff – the people in the company have been with us for years and understand the specific issues that can arise on bulk handling projects,” he said.
“Speed is really important in the industry, as avoiding downtime is ultra critical, particularly in tight shutdown situations. We often find out about a problem in the morning and can have a solution by the afternoon. Part of this comes from our close relationship we have with our clients – we know
their assets and we have the tools and knowledge needed to get started quickly.
“Aspec Engineering specialises in solving problems that are difficult and unique. We have a lean team that focuses on interesting value-adding ideas and hope to continue to do this work for another 20 years.”
ABHR looks at how automation has transformed weighbridge use to increase process e iciencies, and how METTLER TOLEDO’s innovations are at the forefront of this evolution.
handling, speed, accuracy, and reliability are three fundamental principles businesses rely upon.
The weighbridge, often referred to as the ‘cash register’ of the bulk handling business, is a prime contributor to the importance of efficient material handling. It is the first and/or last point where goods are weighed, and transactions are recorded, making it a critical control point.
Consider current weighbridge transaction scenarios where drivers are exposed to unsafe and inefficient practices. The drivers are required to get out of the truck in a very busy site, go to the weighbridge office, and wait for the paperwork before returning to the truck and heading off.
It is a tediously slow process with the possibility of human error, which, during peak times like grain harvest, sees businesses hampered by these inefficiencies. These factors, alongside technological developments of METTLER TOLEDO, have seen a rise in automation at the weighbridge.
“It is about speed, accuracy and reliability. Weighbridge automation has been widely adopted and integrated into bulk-handling companies’ processes.
As speed reduces transaction time, this means the user experience is so much better,” said METTLER TOLEDO business area manager John Beard.
“The second reason for automation is accuracy as this limits the potential of human error.”
Human errors include incorrect registration plates being recorded, inaccurate weights being documented and wrong selection of products and shipping to address.
There can be concerns when such automation is introduced, including the possibility that solutions will become fragile and unreliable. This is no longer the case and METTLER TOLEDO’s hardware and software components are now proven in several industry segments, many of them in remote locations in Australia.
Across Australia, many companies have upgraded from their traditional weighbridge office to an automated solution. This advancement is seen in new weighbridge installations and upgrades of existing weighbridges. Such upgrades have only been made possible due to the strong return on investment of such automation.
The system can be used and tailor suited in various ways to track
a seamless data transfer. METTLER TOLEDO has a local team of experts that can develop, design and support the weighbridge driver control station (DCS), to collect all required information through various data input capabilities, such as a user-friendly touchscreen, RFID, QR code, and Number Plate Recognition. Depending on the customer’s application needs, these can be easily integrated with the customer’s existing software and IT infrastructure.
Some of METTLER TOLEDO’s recent automated weighbridges have resulted in the company not needing to install an expensive second weighbridge. The reduced time of transaction meant one weighbridge is adequate for peak traffic flow by adding driver control stations.
Many of METTLER TOLEDO’s customers have seen a strong return on investment on their first installation and so, quickly engaged METTLER TOLEDO to roll out the unmanned driver control stations across its other sites.
“This movement towards automation was a game-changer when it started, but it is probably not a game-changer anymore; it has become more of a musthave,” Beard said.
“METTLER TOLEDO started seriously pursuing weighbridge automation about
20 years ago. It used to account for a fraction of our business, now we see significantly more new installations and upgrades, including such automation.”
“The requirements of the industries have changed significantly; they want to get their product weighed, correctly recorded and safely delivered to site as quickly as possible. Many are using these unmanned weighbridges 24 hours a day without incident,” he said.
This is vital for many METTLER TOLEDO customers who are now having issues finding good and reliable labour. Trained replacements are proving hard to find as the older workers retire. Automation can help fill the gap, especially in remote areas where there isn’t quick access to seasonal labour.
One solution does not fit all “We’ve got a range of automation solutions depending on our customers’ budget and the level of complexity that they require,” Beard said. As with most METTLER TOLEDO products, the
manufacturer offers a tiered range of solutions for its weighbridges.
This includes customising a weighbridge automation solution with several value-added accessories, which help to provide excellent efficiencies. These range from driver control stations (DCS), automatic number plate recognition (ANPR), traffic lights, anti-theft devices, and a point-of-sale software solution.
The ANPR and anti-theft devices have recently proven to be a popular choice with customers, as business owners defend against theft and inaccurate number plate recording. It reduces a lot of errors such as wrong invoicing, crediting confusion and improves drivers’ onsite experience.
These automated weighbridges and all the extra measures can help ensure compliance with the chain of responsibility (CoR). The introduction of CoR has meant accountability and transparency is of the utmost importance.
The legislation states, “The Chain of Responsibility (CoR) is the part of the Heavy Vehicle National Law (HVNL) that makes parties other than drivers responsible for the safety of heavy vehicles on the road.”
“There is increasingly significant high pressure on operators to ensure trucks are legally loaded before they leave the site,” Beard said.
“Now we can automatically check gross weights, axle weights and instantly notify the driver if they’re overloaded. Some users already have all the hardware they need, a small software upgrade is sometimes all that is required to gain complete CoR compliance.
“It takes the headache away, helping businesses operate more efficiently, improve accuracy, traceability and compliance with a peace of mind.”
METTLER TOLEDO has the proven technology and expertise to bring new and existing weighbridges into the 21st century.
R. Todd Swinderman, president emeritus at Martin Engineering, covers some of the common approaches bulk handlers use to mitigate dust and spillage.
BELT CONVEYORS WITHOUT an enclosure at the transfer point loading zone may still exist in some operations but are becoming a thing of the past due to dust violations and excessive spillage.
Whether the transfer chute is a dead drop, rock box design, or sloped design, dust and spillage from dry bulk material will still exist and must be controlled. Spillage can limit access to a system for maintenance, foul rolling components, add to labour costs for cleanup, and reduce workplace safety.
A skirtboard on either side of the conveyor belt that is sealed with a cover certainly helps but operators have found that the air turbulence from loading still causes fugitive dust to escape if a wear liner and skirting is not applied. Moreover, there are nuanced details conveyor engineers should consider when designing a conveyor transfer point.
While controlling belt wear and the release of fugitive materials, all components of a skirtboard system must work together to contain the load as it forms a stable profile in the center of the belt. Several skirtboard system design approaches can be used based on industry historical practice and the application.
By far the most common configuration is the vertical skirtboard. It is the easiest to fabricate and is a common detail for most engineering design firms. The height of the skirtboard is based on the sealing system components and is commonly at least 300mm high. The
double wall skirtboard is sometimes used with dust extraction for very fine free flowing materials.
The perpendicular and angled configurations are used in some industries. Angled skirtboards are designed to allow the load to center. Perpendicular skirtboards relieve side pressure on the skirtboard seal. In theory, the perpendicular arrangement should allow for light seal contact but in reality, the angle of attack of the seal is not nearly as important as having a running flat belt surface for the seal and liner system to function best.
Vertical seal with a rubber or elastomeric material is the most common sealing system. The seal is held in place with a series of clamps which can be loosened to adjust the seal against the belt. The main drawback to the vertical seal is that an undulating or vibrating belt can break the sealing contact unless
the belt is supported. The lay-in and lay-out seals are self-adjusting depending on the elastic nature of the sealing material. The double skirting configuration is the most effective in retaining a belt seal. Even if the belt profile fluctuates, the secondary seal rides softly on the belt, retaining the seal. Any material that gets in between the double seal strips is non-abrasive, being carried by the belt, and rolls back to the center once the skirtboard ends.
It is a common belief that the seal material must be softer than the belt, but the real property of concern is the abrasion resistance of the seal should be less than the belt top cover. The seal should be considered sacrificial and designed for easy adjustment and replacement without the need for excessive sealing pressure. Over adjustment can cause excessive friction heat of the seal leading to heat damage on the blet, as well as premature wear of skirting. In extreme cases, the heat
generated can cause the seal to stick to the belt during shut down, which can prevent startup.
The sealing pressure should be light with the skirtboard or the liners designed to reduce pressure on the seal. There isn’t much published on seal pressure values. For the self-adjusting seals, use 15 kPa contact pressure. CEMA proposes added belt tension of about 4 kN/m per side without considering the seal thickness.
The wearliner has two functions. First is to be a sacrificial wear material protecting the skirtboard wall. The second is to reduce the side pressure on the sealing system. Not all systems require a liner. The most common liner is the internal liner made of abrasion resistant material such as AR plate or ceramic blocks. The liner is often attached with bolts through the skirtboard with some ability to adjust the space between the bottom and the belt for initial installation and to adjust for wear.
The deflector liner is a variation of the internal liner that is used to center the load and reduce side pressure on the seal. The canoe liner performs a similar centering effect with a substantial volume of wear material and is often used in heavy duty applications like hard rock mining. Canoe liners can be made from elastomeric materials or very hard cast metals. The most important details for a liner are proper
installation and ease of replacement. The external liner was developed to address these two issues.
With the external liner the skirtboard is raised above the expected depth of material rubbing against it and the liner is attached to the outer surface of the skirtboard. If there is concern over wear caused by full contact with the skirtboards, such as from constant overloading and plugging the exposed upper portion of the skirtboard can be covered in wear resistant material. The external design eliminates the gap between the liner and the seal, created by the skirtboard wall thickness, that can trap materials and damage the belt.
Covers protect the cargo from weather but are used primarily for dust control. Covers enclose the loading zone and contain splashing material caused by significant drop distances from one belt to the other or process equipment such as rotary crushers. The most common
Aurora now supplies the industryleading Robopac fully automatic and semi-automatic vertical and horizontal pallet wrapping machines
• Intelligent technology to get the best load containment whilst reducing your wrap usage.
• Unusually shaped loads, unstable/light loads, sharp edges, and loads that need custom wrap programs – we’ve got it covered.
• Units for low or infrequent use through to 24/7 fully integrated high-speed applications.
• Stainless steel options for hygiene zones.
• Low temp options for freezer zones.
• Corrosion resistant options
• Intelligent, easy to use, highly reliable.
• Specified by process technicians not stationary suppliers.
• Fully installed and serviced.
cover is the rigid flat cover made from steel. When rain protection or buildup of fugitive materials is a concern, angled or semi-circular covers are often used. Plastic covers are sometimes used to reduce weight. Regardless of the cover design, the most critical design feature is ease of access. When there is a lot of positive pressure in the enclosure, sealing the covers becomes an issue.
Porous covers are sometimes used to reduce positive pressure, but the most common membrane applications are rubberized fabric with continuous grip edges that can connect between vibrating equipment such as screens and the skirtboard enclosure.
Unfortunately, in the rush to get back into production, covers are removed during cleaning or maintenance and often not replaced in those areas that require frequent access. Maintaining the integrity of the covers is critical to the control of fugitive material. If it is possible that covers will be walked upon, load bearing work platforms should be incorporated into the design.
Skirtboards are most often installed vertically and parallel to the centerline of the belt. Misalignment of the skirt board system will contribute to pushing the belt to one side and can cause mistracking. Skirtboards for multiple load points, when it is not desirable to have continuous skirting, are often staggered widths with inlet deflectors to consolidate the material at the edges. For continuously skirted loading with multiple loading points, the feeds can be managed to gradually increase until the full cross-sectional area is utilised. Reversing belts must use skirtboards parallel to the belt.
In some cases, such as flat belt feeders, it is desirable to create a relief of the skirtboards in the direction of travel to help more uniformly feed the material from a bin. The notch opening wider in the direction of belt travel can be designed using mass flow techniques. Absent the notch (or “V” design) the material will tend to feed only from the rear and can result in segregation or bin plugging. Using this technique on troughed belts adds to the fabrication complexity so there is often a transition section from the bin to the skirtboards that accomplishes the same end result but simplifies the design and installation of the skirtboards.
The distance the bottom edge of the skirtboard or wearliner from the belt surface often varies by industry. Some designers keep the skirtboard high off
the belt to facilitate idler changes but a better solution is to use retractable idlers. Installing the liner parallel to the belt is required for reversing belts. The primary issue is the flatness of the belt in the loading area. To achieve a good seal without damaging the belt’s surface, the belt must be supported.
Industries that use winged tail pulleys, load on the transition from flat to fully troughed or use widely spaced idlers in the load zone will have a difficult time sealing the belt and preventing grooves made under the seal. If the transition is incorrectly designed the belt can lift off the idler when unloaded requiring the liner to be too far above the belt resulting in spillage and/or trapped material. Winged pulleys should be of the spiral design or wrapped to reduce dust pumping vibration. Common practice is to place the wearliner bottom edge parallel, but close to the belt, with approximately 25 mm of clearance for the skirtboard upright from the belt. The liner is then adjusted to be closer to the belt in the range of 10 to 20 mm and self-relieving in the direction of travel.
Adjustment of the liner so there is a smooth surface presented to the belt without steps or gaps between liner sections is a must to prevent particles from being trapped and abrading the belt.
Each approach is unique to the application and the bulk handling environment, but preventing dust and spillage make the cost of the modifications easy to justify over the long run. Consider installing an enclosed modular loading chute with an external wear liner and double skirting. Make sure that the skirtboard and cover are long enough that turbulent air can slow and dust can settle back into the cargo stream. The modular design makes the chute able to be easily adjusted to changes in production, belt speed, or material and the seal and wear liner are adaptable to those changes. This lowers the cost of future modifications and improves the overall safety the transfer point through the life of the conveyor.
IntroducIng the AlImAk SILO LIFT
The introduction of the Alimak Silo Lift industrial elevator marks a significant advancement in vertical innovative elevator sets new benchmarks for safety, efficiency, and durability. The cost-efficient model effectively streamlines operations by eliminating the necessity for a dedicated machine
Engineered with a focus on reliability, durability, and robustness, the Alimak Silo Lift ensures a
The mining industry has always considered conveyor systems as a high-risk area, which is why Dyna Engineering has an experienced conveyor audit team.
A CONVEYOR AUDIT IS A
professional examination of a facility’s conveyor belt system. It shows opportunities for improvement, decreases total cost of ownership, and identifi es the most pressing issues aff ecting the conveyor system’s performance.
They are extremely important to maintain conveyors consistently and effectively to minimise any potential risk to the health and safety of personnel and improve operational reliability.
DYNA Engineering (DE) has a team who conduct conveyor audits and inspections on any size and complexity of system. As an experienced conveyor specialist with more than 30 years of experience, DE conducts audits under Australian Standards, AS1755 – 2000 Conveyor Safety.
Through a collaborative approach, DE’s team works closely with customers to develop a comprehensive understanding of their needs, allowing for a customised solution which enhances operational efficiency and minimises downtime. Site inspections and data are collected, and a comprehensive report is produced. The report highlights the areas for immediate attention and other areas which need to be addressed.
Sharpening the focus on consistent improvement
Understanding that no two facilities are alike, DE tailors its conveyor audits to meet the unique challenges and requirements of each customer. They are designed to provide specific, actionable insights that are in harmony with the customer’s operational goals. As part of a continuous improvement strategy, regular assessments can ensure conveyor systems are always operating at peak efficiency, not only helping
prevent unexpected breakdowns but also contributing to an overall employee culture of avoiding costly repairs, shutdowns and injuries.
“There have been quite a few occasions over the years where we have saved our customers hundreds of thousands of dollars in maintenance and repair costs through early detection of impending breakdowns due to wearing out or damaged conveyor componentry” said DE’s general manager, Thomas Greaves.
“We provide comprehensive reports on specific components as well as complete conveyor systems to highlight any problem areas in advance. These reports are accurate, fully detailed and up to date and include documenting Standard Operational Procedures for the inspection and maintenance of the conveyor system for both operators and maintenance personnel. The reports identify critical issues and help the customer minimise time spent on
shutdowns and breakdowns. Common areas of attention include:
• belt thickness
• belt tracking
• general access to equipment for maintenance
• idler frame alignments
• impact zone
• pulley alignment
• safety guards to AS1755
The company also produces life cycle and preventative maintenance plans. These assists customers in keeping equipment operating at high efficiency levels.
“Knowing the likely life left before replacement will be required on major conveying componentry means maintenance supervisors can plan fewer shutdowns for optimum efficiency and avoid expensive, unplanned stoppages which could be absolutely disastrous in some instances. It’s like being able to see around corners,” Greaves said.
ABHR learns how Screenmasters Australia forged key partnerships to support the bulk handling sector.
as the bulk handling sector. The industry encompass everything from quarrying to mining, agricultural, chemical production, steel production and more.
To meet the needs of such a diverse sector, equipment distributors need to stock a wide range of adaptable technologies that can work across multiple industries.
Screenmasters Australia is a wellestablished distributor in the industry, proudly celebrating its 30th year in operation. Its hard work and efforts have paid dividends and have earned it a reputation as a reliable, trusted and solid partner for companies involved in all aspects of bulk materials handling.
Screenmasters Australia stands out with its extensive range of equipment from first-rate original equipment manufacturers (OEMs), such as Convir and H-Sensortechnik, offering both standard and bespoke solutions to the bulk handling sector.
ABHR looks at Screenmasters Australia’s offerings from these established international manufacturers and the benefits they offer operators and facilities.
Convir designs cost-effective and highly reliable fixed and mobile conveying solutions for the bulk handling sector for capacities ranging from 100 to 3,000 mT/hr.
Based in the heart of Europe’s manufacturing zone and with almost 20 years of industry experience, Convir has designed, engineered, manufactured and delivered its conveying solutions into ports and terminals, quarries, recycling,
agriculture, mining, food and many other sectors.
Through its valued partnership with Screenmasters Australia, Convir is offering its full range of conveying technologies, including the proven TBC range of Telescopic Conveyors, to the Australian market.
According to Convir, the TBC Conveyors reduce material degradation, particle size separation and fines compaction.
The Telescopic function of the conveyor allows for a far greater stockpile capacity when compared to a standard conveyor of the same footprint. The trapezoidal shape increased stockpile capacity, formed by the TBC, significantly reducing the need for multiple handling by loaders, dumpers and dozers.
The standard TBC range of conveyors has a capacity of up to 1,500t mT/ph and is available in standard widths ranging from 650mm to 1200mm. Drive and power options are available depending on the specific customer requirements, and Convir can offer bespoke solutions where the client’s application is non-standard.
The TBC units are user—and servicefriendly for operators, and the Convir ASP (Automatic Stockpiling Program) is pre-installed on all standard machines.
Customers can opt for remote control access, belt covers, heavyduty tracks, hydraulic drives, Hardox or polyurethane linings to suit different applications, various discharge chutes and galvanised structures.
Depending on power system requirements, they can also add a diesel generator or hybrid system.
The ‘ultimate’ optical belt weigher Sensortechnik has designed and delivered, to the bulk handling sector, what it defines as “the ultimate management tool”.
The Sensortechnik Optical Belt Scanner (OBS) has proven to be one of the leading options for accurately, precisely, and consistently measuring a vast range of bulk materials on a conveyor, fixed or mobile.
Since entering the market, the OBS has revolutionised the way bulk material is monitored and measured.
With a proven global installed base far exceeding 10,000 units in more than 50 countries, it is clear OBS is one of the top performers when it comes to monitoring your production. As the old saying goes, “You can’t manage what you can’t measure”.
The OBS product was specifically designed to ensure that bulk handling companies achieved a new level of “realtime” accuracy, precision and efficiency coupled with GPS reporting innovation. The vast improvement in real time accurate material measurement ensures OBS users, operators and managers alike, can get the best efficient production out of their equipment which ultimately leads to improved results.
The OBS is a contact-free volumetric belt scanner suited for a range of industries from aggregates to waste and recycling, coal or food. It performs equally well on both Stationary and Mobile equipment, such as the Keestrack R6h Impactor.
The OBS units boast a volumetric measurement accuracy of 99.8 percent, far exceeding traditional mechanical belt weighers.
They are mounted onto the conveyor’s head drum, accurately scanning the conveyed material as it discharges the belt.
The OBS is not affected by weather, vibration, dust, or water and is highly compatible with both fixed and folding conveyors.
The OBS utilises the latest laser technology which enables the optical sensors to function without contacting the conveyor belt.
This ensures limited downtime, no wear and tear, minimal maintenance costs and uninterrupted material flow along the conveyor.
Users, operators and managers can view material flow in real-time via GPS.
This instant feedback enables for timely adjustments and optimisation built into the optical belt scanner to ensure seamless functionality in conjunction with existing automation and control systems. In addition to the highly accurate performance
data gathered by the OBS, the unit increases the operator’s ability to identify upstream material production performance, ensuring the minimum downtime and associated wasted operational costs.
By utilising these metrics, businesses can create leaner, more responsive, and more productive bulk handling operations that are vastly improved
compared to those using traditional mechanical weighing methods.
Screenmasters are exclusive Australian Distributors of Convir and Sensortechnick OBS Weighing Scales. With more than 30 years of Australian industry experience, the company is equipped to provide extensive support and services with staff and offices located nationwide.
Flow Properties and Materials Testing
Dust (environmental) Testing
Wear Testing (Impact, Abrasion and Erosion)
Conveyor Belt, Idler Roll and Pulley Testing
Discrete Element Method (DEM) Modelling
DEM Calibration Testing
Materials Handling Consultancy and Contracted Research
Bin and Stockpile Design
Pneumatic and Hydraulic Conveying
Computational and Scale Modelling
Site Visits
Professional Development Courses
Short Course: Storage, Feeding, Transfer and Belt Conveying 13-15 August (Newcastle) 19-21 November (Perth)
There’s a lot that goes into installing the right industrial vibrator, but John Isherwood believes the outcome is well worth it.
JOHN ISHERWOOD, MANAGING director of NetterVibration
Australia, has more than 35 years of local experience working with industrial vibrators.
During his time in the industry, he’s seen the negatives that can come with the process of installing them.
“You can compromise the bin wall by drilling holes, need to get in the bin, require a confined space permit, and may even need to stop the process, depending on the safety policy,” he said.
“It can also lead to air being introduced to the product, sudden noise, and complicated pipework all over the place.
“However, when properly sized and installed, vibrators are all positive in promoting material flow.”
NetterVibration Australia has more than 3000 models in electric, hydraulic, and pneumatic drives. Many are held in stock in Australia, with frequent deliveries from the factory, depending upon demand. It can provide electric, pneumatic, and hydraulic vibrators,
with force outputs from 14N to in excess of 170,000N.
Isherwood said the company supplies its vibrators around the world and has developed a strong reputation internationally.
“NetterVibration has been manufacturing vibrators for almost 70 years, and you can rely on the European standards of quality,” he said.
“Over that time, the business has only focused on vibration and improving its products. It’s developed specialist expertise and understands what works and what doesn’t.
“It’s a global company, with seven branches and about 40 agents located around the world that share knowledge and support.”
The company manufactures its equipment to an extremely high quality in Europe, with ATEX rating as standard on most electric models, and rating 1 and 2 available to order on all models. Stainless steel versions are available for food industries and for aggressive atmospheres.
Page Macrae Engineering reflects on its first full year as a full-time presence in Australia and how it established a solid foundation of support and innovation.
equipment supplier Page Macrae Engineering (PME) is no stranger to Australia. The company has been supporting ports and stevedores in the country for more than a decade.
However, PME wanted to offer more. The company decided it would expand across the Tasman and began building a local operation.
Since then, a dedicated spares storage facility now operational in Melbourne, ensuring critical parts for the company’s diverse product range are readily available within Australia.
Peter Swan, PME’s general manager of sales and marketing told ABHR that the move was vital to supporting local clients.
“This dramatically reduces lead times, minimising downtime and maximising productivity for our port partners,” he said.
“While we’ve made great strides, our commitment to expanding our range of services and tailoring solutions to each client’s unique needs is unwavering.”
The port and stevedoring industry is a demanding one, where equipment is pushed to the limit almost every day. With these conditions, challenges are inevitable.
PME’s Melbourne-based business development manager, Charles Hennessy, backed by the experience of the Page Macrae team in New Zealand, has been instrumental in providing on-the-ground support to navigate these challenges.
“With the combined expertise of PME’s comprehensive design, fabrication, and engineering teams in New Zealand, as well as a network of New Zealand and Australian suppliers and contractors, Charles ensures our clients receive the support they need to maintain business continuity,” Swan said.
Building on the success of BULK 2022, the team at PME is excited to showcase its
latest bulk material handling solutions at BULK 2024 in Melbourne this September.
The company invites industry professionals to visit them at Stand N28 and explore the following the latest technological developments on display.
“Come and see the latest in high efficiency port hoppers, featuring integrated weighing, low power and cost dust collection, delivered in containers or fully assembled. Dust collection and weighing delivered at a cost and capacities to meet our customers budgets and opportunities,” Swan said.
Visitors can also learn about PME’s range of bulk grabs with environmental bucket sealing, dust covers and interchangeable buckets to optimise crane capacities.
The company has a range of log handling grapples and basket loading grapples for high efficiency vessel loading and unloading.
“We also invite visitors to engage in discussions around our cutting-edge electric vehicle (EV) product concepts designed to address the evolving needs of the industry’s infrastructure and
sustainability goals. See preliminary designs and share your feedback to help shape the future of EV technology in bulk handling,” Swan said.
“Witness firsthand how our advanced telematics systems provide real-time data and insights to optimise grab performance, monitor equipment health and enhance overall operational efficiency. This equipment can now be specified for all of our equipment on show.”
“As we look towards the future, PME Australia remains committed to continuous improvement, innovation, and delivering solutions that meet the evolving needs of our clients,” Swan said
“We are confident that our collaborative approach, combined with our expanding local presence, will continue to strengthen our partnerships and contribute to a more efficient and sustainable bulk handling industry in Australia.
“We look forward to seeing you at BULK2024.”
When a belt rips, the costs can quickly escalate. To solve this issue, Flexco has designed a steel cord belt fastening system that gets systems up and running faster.
materials, such as metals or aggregate, sites often trust in the strength and reliability of steel cord conveyor belts.
But in all operations, especially overland conveyor belt systems, damage to the conveyor belt can strike when the operator least expects it.
It’s the conundrum many bulk handling companies have faced, and few have managed to solve. Until Flexco spent years of research and development to create the ideal solution.
Flexco’s FXC steel cord belt fastening system is designed to be installed in hours, ensuring bulk handling companies can get their systems running again.
The wait for a vulcanised splice, especially on an overland conveyor belt system, could be days. In an industry where time is money, many operations are being severely impacted by this downtime.
Mining operations from around the world visited the US-based equipment
manufacturer, wondering how they could decrease the downtime on conveyor belt repairs.
“All over the world, when a belt gets damaged, it needs to be respliced immediately before the product can even be run off the belt,” Flexco principal research and development engineer Brett DeVries told ABHR
“No one controls where the belt breaks … so getting a vulcanising crew out to a remote area could take a week. But this is a steel cord belt, it is a critical belt.
“The FXC steel cord belt fastening system is there for an emergency because when it happens, people need it desperately.”
The FXC steel cord fastener enables operators to quickly install a temporary splice measure, which allows them to run the belt until a vulcanised join can be scheduled.
This reduces the stress, costs, and labour associated with planning and
scheduling a vulcanised splice in a remote area.
Flexco exceeded the original request to design a splice merely to reach the splicing station.
“Our testing showed the FXC can typically run several weeks at full tonnage without risk of failure,” DeVries said.
The company’s testing also showed that the four workers were able to splice a 1800mm wide steel cord belt in four to six hours.
The FXC Steel Cord has also yielded promising results as a tool to help operators string a conveyor in a timely manner and in highly abrasive applications.
Flexco’s testing showed that the FXC steel cord could be used for quick and efficient belt pulling. The company’s data shows a 1800mm wide belt that can be pulled onto a conveyor in three hours.
“There weren’t a lot of products out there to help mines perform a belt pull safely. Things like dummy splice take up cord and time to set it up. There is also some guesswork in the strength of a dummy splice if it is done hastily,” DeVries said.
“We also found steel cord belts were being put in applications where the belt just doesn’t last that long. If you’re running underneath a feeder where the top cover runs out in a year or two, (they) don’t need a vulcanised join; the vulcanised join is way overdesigned for that particular belt.
“By the time you’ve set up scaffolding, it might take you a week to go from taking off the old belt to having the new belt ready to run because of all the safety steps you need to go through for setting and removing the vulcanising press.
“So that was the other opportunity … those belts that are only lasting a year or two and have a low number of cycles and revolutions of the belt around the structure.”
Flexco will work with companies to determine the best fastening solution for their applications. Using the information provided by the companies, Flexco can create a customised FXC fastener kit for belts of all shapes, sizes, and applications.
Flexco has manufactured the FXC fastening system using high-quality products to ensure its durability in harsh conditions, including Australia’s Pilbara region.
The product was subjected to rigorous internal and independent testing. This has led to several companies experiencing positive outcomes with the FXC steel cord around the world.
DeVries told ABHR about an Australian iron ore mine in the Pilbara that installed the FXC on one of its 2400 mm-wide feeder belts,
significantly reducing downtime in its vulcanisation process.
“With this particular feeder, the site must disassemble a portion of the chute and several other bulky components to provide access for the vulcaniser. Taking this into account, the site typically requires 7-8 days to remove these components and reassemble them once the vulcanisation process is complete,”.
“The FXC had this belt back up and running within two days,” DeVries said.
“It was a great test of our installation process in Australian harshest bulk handling conditions.”
Flexco has been a trusted partner of many bulk-handling companies for years. The company has 115 years of experience in mechanical fasteners which have been used worldwide.
Flexco Australia serves the entire Australasian region, from Australia to Papua New Guinea and the Pacific Islands. It has a manufacturing facility in Sydney and offices in Perth and Newcastle, which ensures its Australasian
customers receive full support and servicing, even in remote areas.
DeVries said the FXC steel cord gave companies control over downtime.
“There are places where the vulcanised splice has been the only option for joining a steel cord belt,” DeVries said.
“In places where a vulcanised splice isn’t an optimal solution, we can step in and help.”
Ag Growth International is supplying Australian agriculture with high-quality, long-lasting, and a ordable infrastructure.
P&J HARRIS AND SONS IS A family-owned and operated agricultural enterprise that provides sustainable beef, grain, lamb and wool.
To increase the company’s overall capacity and expand operations within its feedlot, it began work on establishing a brand-new site.
Troy Shields, operations manager at Allied Grain Systems, said P&J Harris and Sons approached the company.
“They asked us if we had the capabilities to provide a storage system and feedlot for the new site,” he told ABHR. “We have previously built silos for them in Northern New South Wales and knew what would work.”
Allied Grain Systems relied on equipment manufactured by agricultural company Ag Growth International (AGI) to supply this project.
“AGI is one of the world leaders when it comes to agricultural equipment,” Shields said. “They have some of the best products out there, they’re state of the art, robust and well built.”
Allied Grain Systems have designed the feedlot with four 48-14 sealed AGI silos capable of storing around 7000 tonnes of materials, along with sweeps, a bucket elevator, a double run grain pump, and a reclaim transfer conveyor.
The site is designed to feature a driveover hopper that has the capacity to load 250tph. The site has an outloading capacity of 25tph through the rolling mill.
Shields said Allied Grain Systems’ engineering department worked closely with AGI to determine the specifications of the equipment.
“We worked very closely with AGI and can order specific equipment, designed for each job,” he said.
“AGI’s manufacturing system and engineering expertise make their silo offering competitive in the Australian market.”
Rustom Mistry, senior vice president – Asia Pacific at AGI said the company’s competitive edge is its global operations and local expertise, meaning it can deliver world-class solutions, custom designed for local conditions.
“Our engineering expertise coupled with our manufacturing excellence, ensure that AGI’s solutions are reliable and durable,” Mistry said.
AGI’s products have been available for more than 40 years in Australia, providing a complete range of farm and commercial solutions. AGI’s offerings include storage, handling and processing solutions for grain, fertiliser, seed, feed and food industries.
Shields said AGI’s wide variety of equipment and brands makes it a onestop shop for jobs like the P&J Harris and Sons project.
“AGI’s global manufacturing infrastructure can custom design and produce high-quality components, which is important for the Australian market. We have a harsh, hot environment, so silos and grain handling equipment need to be well constructed to handle everyday use,” he said.
“Their manufacturing and engineering (capabilities) allow their silos to be competitively priced for the Australian bulk handling industry.”
Allied Grain Systems ensures that all AGI’s products are ready to use in the Australian market, using local gearboxes and electrical components. Its team knows what works well in the local region, which means it will pick the right equipment for the job from AGI’s global catalogue.
Shields said the feedback for the AGI equipment has been glowing.
“AGI is a reputable organisation that can offer an extensive range of large storage and handling solutions,” he said.
“This provides Allied Grain Systems with an edge on engineering design capacities along with leading edge technology.”
Aurora Process Solutions has the technology that could help Australian bulk manufacturers up their productivity and reliability.
PRODUCTIVITY, PUT SIMPLY, IS getting more out of less. And when it comes to Australia’s economy, it is sorely needed.
Alex Robson, deputy chair of the Australian Productivity Commission, wrote in a media release that to increase our living standards in a durable way, we need sustainable, long-term wage growth that can only come through increased productivity.
“But another important driver of our productivity slump last year was that employers didn’t invest quickly enough in the equipment, tools and resources (or ‘capital’) that were needed to make the most of workers’ skills and talents,” he said in a media release.
“As a rule, if workers have access to more capital, each hour worked produces more. We can express that in terms of the ‘capital-labour ratio’. A higher capital-labour ratio is typically associated with higher productivity.”
According to Robson, labour productivity saw one of the sharpest falls in 2022-23. In short, Australians need to be working smarter, not harder,
One way to improve productivity is through automation. Many tasks in the bulk handling industry are ill-suited for people to perform. Stacking boxes, filling packages, and shifting heavy loads can be dull, dirty, and, worst of all, dangerous.
Braden Goddin, marketing and sales manager at Aurora Process Solutions, told ABHR that automation can free up staff performing manual labour, allowing them to focus on jobs that add value to the business.
“We often work with small and medium enterprises, and a lot of the time, ownership are on the floor helping with manual labour during busy periods,” he said.
“That’s not an effective use of manual labour units. There are so many more important things they could be doing to grow the business. Worse, it can create a lull in business during busy times, creating a cyclical pattern which can create cash flow issues.
“Automation makes running your business more accessible and versatile, removing variability.”
Aurora specialises in providing automated and semi-automated bagfilling, closing, conveying, palletising, and wrapping/hooding equipment for the grain, sand, fertiliser, and cement industries.
Aurora often works with businesses new to automation. This means they work with the customer to demystify their concerns and educate them on the benefits of automation.
Automated technology is continuing to become more sophisticated.
floor, it can help allay concerns. We do this through augmented reality, case studies and site visits, letting them speak with other clients that have had great success with the technology.”
Aurora also pays attention to the latest technologies developing around the world to ensure its equipment remains on the cutting edge.
Earlier this year, the company entered an agreement with Italian packaging technology specialist Robopac.
Robopac’s headquarters, in the heart of Italy’s packaging valley, manufactures advanced automated systems to be used in bulk packaging operations globally.
Goddin said one particular technology that stood out to Aurora was Robopac’s line of stretch wrappers.
“There are a lot of stretch wrappers out there, but we decided to partner with Robopac for their advanced technology.”
Goddin said that uncertainty is one of the biggest barriers that stops businesses from incorporating automation.
“If you’re not working with robots on a daily basis, it can be daunting. That’s why we give customers a large degree of time and work with them to show them the benefits,” he said.
“When they can visualise what the automation looks like on their factory
“Because so many manufacturers use stretch wrapping technology, from food, to pharmaceuticals, to trampolines, we saw it as an opportunity. Getting it right can make quite the difference, especially in high volume applications that are producing several pallets an hour.”
One of these advanced technologies is a pre-stretch mechanism for pallet wrapping machines. The mechanism
allows users to get up to 400 per cent more yield out of a roll of wrapping without sacrificing integrity, reducing the amount of plastic used in the process.
It also manufactures options for wrapping pallets for specialised requirements, including in belowfreezing temperatures, hygienic environments, and when dealing with corrosive materials.
Goddin said Robopac’s experience working with a range of industries and countries allows it to spot global trends.
“In Australia, the industry typically uses turntable wrappers. Other countries use ring wrappers, or rotary arm wrappers. That’s something we want to introduce to the local market,” he said.
“It allows a client to wrap a pallet without rotating it, meaning it’s safer for unstable loads as there’s no centrifugal force causing it to shift. It also means you can wrap a pallet a lot faster.”
Automated technology is continuing to become more sophisticated. Aurora’s team saw this in action at trade shows around the world.
Goddin said automation is moving forward in leaps and bounds, with vision technology rapidly increasing what can be automated.
The company plans to attend the upcoming 2024 Australian Bulk Handling Expo (BULK2024) in Melbourne. The show, which will take place from September 18 to 19, will highlight advancements in automation and the Internet of Things.
Goddin said BULK2024 will give Aurora an opportunity to see the emerging technologies and how they are being applied to specific markets.
“We meet with clients face to face on a regular basis, but the show offers us an opportunity to network and see the latest developments in the industry,” he said.
“There’s a lot of clever people and a lot of clever companies out there, and attending the show is a great way to save on a heck of a lot of googling and zooming.”
industries.
Increased production demands have resulted in faster, wider, more heavily loaded conveyor belts and increased carry-back.
Carry-back leads to excessive wear on conveyor components, buildup on return idlers, misalignment of the belt, adverse effects on the conveyor operation and plant efficiency, and increased OH&S risks.
The ESS IPS Cleaners deliver superior belt cleaning performance and unparalleled serviceability for a variety of applications.
The IPS is an upgraded version of the ESS InLine 20-Ten Premium Cleaner & the original ESS InLine cleaner, which set the standard for cleaning performance, safety, and ease of service.
Design features of the new IPS Secondary Cleaner include;
• Improved encapsulated slide design – reduces jamming for easier service
• Stainless steel manufacture – to resist product wear and suitable for corrosive environments
• New tensioning bracket design – increases the cleaners sensitivity to belt movement to maintain optimal cleaning pressure and angle
• New Air and Spring Tensioner design – interchangeable to offer flexibility as the requirements of the client evolves
• Same footprint as the 20Ten Premium InLine cleaner - once an existing 20Ten InLine Premium cleaner comes to the end of its service life, a new IPS Cleaner can be retrofitted.
Satake Australia has recently opened its roller refurbishment facility – ABHR finds out why.
AS PART OF THE CRUSHING AND size reduction process, fl our producers use roller mills to grind grain into a powder.
It’s not uncommon for a flour mill to have up to 20 of these machines, each with different types of rollers inside. Each machine performs a different role in the process of turning wheat into flour.
As with most equipment, these rollers will eventually wear out— often at different rates depending on the application. Satake Australia’s recent expansion has helped address this industry issue. The company has invested in the latest technologies to help its customers refurbish their roller mills.
Roger Cook, senior project and sales manager at Satake Australia, told ABHR the company has invested in a new roller refurbishment facility in Penrith, New South Wales.
“It’s a service we had previously offered the industry,” he said. “We’ve since purchased new computercontrolled machines that provide higher speed and accuracy in the refurbishment process.”
“Satake as a worldwide group was reinvigorated in the flour machinery
a few years ago, and with that comes new machines, new sensors, and new process technologies.
“As part of our offering in the Australian and New Zealand markets, we wanted to back up not only the supply of these new modern roller mill machines, but also provide the best after sales support.”
There are two main styles of roll used in mill applications – rolls that are fluted machined into them, and smooth rolls. Previously, to manually regroove a roll would have required the cogs and gears to be manually changed out, which was a slow process.
Smooth rolls are also normally shotblasted, which traditionally requires using a shotblasting gun and firing it at the roll to achieve an even finish.
Satake’s new technology is preprogrammed with the end specifications in mind.
This enables the machinery to automatically determine the most effective way of achieving the correct finish.
Cook said it’s not just the refurbishment equipment that has undergone an upgrade.
“We’ve also invested in our quality control process to allow us to accurately measure the parameters of our client’s rolls and advise them about which stage the rollers are in their lifespan,” he said.
“This is important, as flour mills need to balance the costs of downtime related to refurbishment, while ensuring they don’t leave it too late, as that could affect the performance of the machinery.”
Satake’s support teams have access to a specialised inspection machine that has a small optical flute testing function. This camera-based sensor technology can zoom in on the flutes and measure how much has been worn. This information can inform clients when they should undergo the refurbishment process and is much more accurate than using the naked eye.
The company acquired the advanced refurbishment machinery in 2023 and spent the better part of that year ensuring its staff were well-trained with the new technology. Several of its Australian factory workers were sent to Europe to be trained at the manufacturer’s facility and to get an indepth understanding of how they work.
The refurbishment service has been operating since the beginning of the year, and clients have provided positive feedback on it.
“Generally, the machines used in Australia for this kind of work were manual,” Cook said. “This investment into cutting-edge technology has been positively received by the industry.”
“The typical time it takes for us to refurbish a roll with the new machines is two weeks, though if clients require the rollers more urgently, we can certainly do that. Most flour mills have several pairs of rollers for each part of the process, but sometimes things happen, and people can get caught out, which is why we offer a 72-hour emergency turnaround.”
While flour mills are the major industry using the technology, the company can refurbish rollers for any industry that uses them, including the feed milling, food, and chemical industries.
Over the past few years, Satake has grown its silo and storage side of the
business. However, Cook said that going forward, the company plans to expand its offering of turnkey services when it comes to project engineering.
“We’re quite a diverse company,” he said.
“We manufacture machines in Australia and all around the world and have a lot of capability for the design and installation process.”
“Customers are looking for a complete service, which is why we have invested in our roller refurbishment facility. It further strengthens our offering and allows us to manage the lifecycle of equipment after delivery.
“The industry is already benefiting from our high level of service, and we plan to continue making our customers’ lives as easy as possible.”
• Output potential of up to 750tph - depending on material type and crusher settings
• Terex Jaques JW55 HD jaw chamber with hydraulic CSS adjustment
• Direct drive chamber via Transfluid KPTO21
• 10m3 hopper capacity with pan feeder and pre-screen (additional capacity available with the optional side extensions)
• An optional bypass conveyor is available, or material can run under the jaw to the product conveyor
Mineral Processing Solutions and Telestack partnered with an Australian mining operation to meet its production goals.
WHEN AN AUSTRALIAN MINING operation approached Mineral Processing Solutions about its plans to bolster its production on-site, they had a clear goal in mind.
The client was looking to achieve a 1000tph feed rate on its site, boosting the project’s efficiency.
Mineral Processing Solutions began collaborating closely with Telestack, discussing potential options to deliver the required production rate.
The two businesses not only met the customer’s desired goal, but they exceeded it significantly with a feed rate of 1600tph. According to those involved, the new feed rate shaved 50 minutes off the loading time per cycle, drastically increasing the project’s efficiency.
Mineral Processing Solutions area manager Adam Dever told ABHR the project was a significant milestone.
“It’s the proudest moment of my professional career. I’ve been in mining for a long time, but the achievements of this project are a career highlight,” he said.
“This collaboration has resulted in substantial cost savings for the customer and minimal downtime for their plant, thanks to the high-quality structure, motors, and gearboxes that Telestack provides.”
The project required an innovative solution for material feeding and
stacking, as the coal was destined for markets in Asia. The product was processed on-site before being transported via truck to the train loadout facility, where it would reach the Port of Brisbane and then go to the Asian markets.
To meet the customer’s desired goals, Mineral Processing Solutions and Telestack designed an innovative system comprising several components.
The system featured a Telestack HF 24T Hopper Feeder, an HF 10T Tracked Hopper Feeder, two TC 424X Tracked Stockpiling Conveyors and three TC 624R Tracked Radial Stockpiling Conveyors.
“We seamlessly integrated our equipment with existing on-site infrastructure to enhance automation and user-friendliness. The equipment has various applications within the Australian mining operation,” Telestack international sales manager Philip Waddell said.
“The ability to integrate the equipment into both mobile and static applications and to supply the equipment quickly with Mineral Processing Solutions stock in the country was also a factor in winning this project.”
The Telestack equipment has improved the Australian mining operation’s project from the initial stacking stage to the final loadout. In the initial stage, where the
coal is stacked directly from the impact crusher, a TC 424X Tracked Stockpiling Conveyor and Telestack Tracked Radial Stacker TC 624R help stack the material.
The TC 424X takes the bypass material (50mm-plus) before it enters the impactor and creates a conical stockpile. This creates a greater stockpile capacity compared to using just the capacity created by the bypass discharge conveyor. The TC 624R stacks the coal from the crusher’s product belt, able to stack up to 10,000m3 of material without moving.
When the coal progresses on-site, it is fed through the HF 10T Tracked Utility Hopper Feeder, which regulates the material flow. The HF 10T Hopper Feeder works with a TC 424X to feed the correct material into the Coal Handling Preparation Plant (CHPP) intake at a height of eight metres.
Once the finished material is processed through the CHPP, two TC 624R radial stackers stockpile the product to be ready for train loadout (TLO).
During the train load-out process, where the coal is brought to the stockyard via truck, the HF 24T Hopper Feeder feeds the TLO system. The high-capacity system can handle up to 1600tph at 35 hertz, with further capacity to run at 55 hertz if required. Its 70-degree tapered hopper, which uses a heavy-duty apron belt feeder, regulates the feed to the TLO.
“Our engineering capability, marked by a dedication to precision and quality, played a pivotal role in this project,” Waddell said.
“At Telestack, we believe that the key to success lies in the fusion of state-of-the-art technology and an unwavering commitment to delivering exceptional results.
“This project exemplifies our ability to create innovative solutions that not only meet but exceed our client’s needs, a testament to our
engineering capabilities and dedication to pushing the boundaries of material handling excellence.”
Since the Telestack system became operational, the customer estimates it has saved millions in engineering and construction costs.
The customer said Telestack exceeded their project expectations, while Mineral Processing Solutions had become their benchmark for aftersales service.
The new system has seen the customer improve operational flexibility
while maintaining high throughput rates and lower operational costs.
Mineral Processing Solutions has locations across Australia to support customers with aftersales service. The company maintains a head office in Perth and facilities in Adelaide, Darwin, Newcastle, Goodna and Melbourne
It is another example of how Mineral Processing Solutions has come to specialise in plants with up to 3000 tonnes per hour throughput rates. The company offers process engineering, equipment selection
profiling, individual component supply, complete process turnkey equipment solutions, and monitoring and efficiency consulting.
“We are thrilled to offer our topnotch after-sales service and readily available spare parts to ensure the customer receives the utmost attention and maximises uptime and efficiency,” Dever said.
“It’s a testament to the power of partnership and quality solutions coming together for outstanding results.”
Sandvik has been working hard behind the scenes to bring its new o ering and capabilities to market following its acquisition of the Schenck Process mining-related business.
IN OCTOBER 2023, ENGINEERING group Sandvik changed the names of the legal entities that came with the Schenck Process (SP) acquisition.
The move was a major milestone in the integration of Schenck Process Mining into Sandvik’s Rock Processing Solutions Business area.
The newly acquired entities provide Sandvik Rock Processing with a much
better global reach, particularly in geographies where it previously had little presence.
This is especially true in Australia, where Sandvik Rock Processing only had a small team, while SP Mining had most of its engineering and R&D teams as well as production and service facilities in Australia.
Schenck Process Australia, which employed over 400 people became Sandvik Rock Processing Australia, and is now a major hub for Sandvik’s global Screening Solutions Division.
Since the renaming of the legal entities, the integration of the SP Mining business around the world has been a key focus area for the company. Part of this work includes the rebranding of all aspects of the business. In parallel the SP Mining and Kwatani equipment offerings have been united under the Sandvik brand.
The company said the result is an unparalleled range of vibrating screens, feeders, screening media and train loaders.
In early May the company achieved another key integration milestone, shipping out the first Sandvik branded SP Mining screen from its Jandakot production facility in Western Australia. Pleased with the result, Sandvik’s global head of marketing – screening solutions, Peter Newfield, previously head of marketing APAC for SP Mining, said,
“Apart from the change to the look, branding and Sandvik nomenclature, nothing else has changed. Our legendary reliability, technology and aftermarket support remains as our customers have come to expect.”
We are now better equipped than ever to help our customers to optimise their comminution and material handling operations for maximum performance, safety, and efficiency,” he said.
Newfield said that combining the industry leading screening, feeding, and loading expertise of Schenck Process Mining and Kwatani with Sandvik’s mastery of crushing and wear protection allows the company to bring an unrivalled equipment line-up to market.
“This unique offering is underpinned by the expert process knowledge of our teams, a full range of digital tools, high quality OEM spare parts, consumables, and life-cycle services.”
But the integration wasn’t just limited to the equipment. Newfield said it has been a major project that involved every part of the business. In essence, the acquired Schenck Process entities had to become Sandvik Rock Processing entities and so SP Mining staff had to embrace the Sandvik culture and learn the company’s systems, and ways of working.
“Of course, a big part of the integration was making sure that our key stakeholders understood the benefits of us becoming a fully integrated part of Sandvik. It takes time for people to adjust to change, and they need to know what is happening throughout
the process. We have worked hard to communicate the changes to all our key stakeholders including our customers and employees,” he said.
The company has changed the branding of all its Australian facilities, motor vehicles, and the work clothes that its people wear on the job every day. The Sandvik Rock Processing Solutions website and other marketing collateral have also changed to showcase its new product offerings and brand. According to Newfield these were the final steps in the integration process.
“Our new offering along with the advances that our combined R&D teams are making, allow us to partner with our customers to address our industry’s biggest challenge - making mineral processing more eco-efficient,” he said.
Rulmeca has a proud history in bulk handling. ABHR learns about the company’s o erings in Australia.
operation in Bergamo’s local mining industry has become an international operation serving some of the world’s biggest bulk-handling companies.
Rulmeca has maintained its proud history as a leading manufacturer of conveyor components for all applications, with a particular focus on bulk materials handling.
The company’s extensive range of conveyor components, rollers, idlers, structures, pulleys, and motorised pulleys have been utilised worldwide.
ABHR sat down with Rulmeca executive vice president and managing director Carsten Spanggaard and Rulmeca Melco Australia’s general manager James Nicholson to chart the family owned company’s journey from a mainly Italian and European based business to a worldwide operation with global manufacturing and clients in 85 countries.
Rulmeca has a strong presence in many global sectors, including mining, aggregates, import and export terminals, and unique markets like sugar and salt.
The company, founded 62 years ago, has experienced significant growth, especially in the past two decades.
Rulmeca has manufacturing facilities in the United States, Canada, Europe, China, South Africa and Thailand, providing comprehensive support for its conveyor components worldwide.
“We do (research and development), design, manufacturing, sales and service 100 per cent ourselves,” Spanggard said.
“If you manufacture with (multiple) global locations, it is easy to work with the same companies across borders, which I think has been a big part of our successes.
“The fact that we’ve also built-up sales and service companies like in Australia to be able to give local service from an engineering and a product specification point of view is one of the reasons (as well).”
Rulmeca has been in Australia since 2011 and recently relocated its headquarters to Perth. This relocation allows the company to provide localised service to key players in the WA mining sector and throughout the country.
“We went there predominantly because we are a supplier to most of the leading mining companies globally, and most of them are also in the Australian market,” Spanggaard said.
While the company offers a wide range of products for Australia’s bulk materials handling sector, its roller range has been particularly successful.
Rulmeca’s range of steel, composite, and HDPE rollers have been used in some of the country’s most significant mining operations. Rulmeca’s products have also impressed customers in highcorrosion applications.
“Australia is a little bit different in the way they are utilising much more composite and HDPE roller technology compared to the rest of the world due to the weight of the product,” he said.
“We have expanded our manufacturing capability and (research and development) of that product line to take into the Australian market.”
Nicholson leads the Rulmeca’s Australian operation. In the past decade, it has developed a strong reputation for delivering on project work, including engineering, procurement, and construction contracts (EPC).
Rulmeca Australia has successfully delivered conveyor idlers, industrial pulleys, conveyor covers, belt cleaners and motorised pulleys to bulk handling companies and project contractors across Australia and New Zealand.
Rulmeca’s Perth headquarters is set up to support clients, with further service offered through its distributor networks. The combined expertise ensures customers receive customised advice.
“Because of our global manufacturing, we can tailor the offering to the EPC depending on the specification and operational conditions and we can select different manufacturers based on what’s required,” Nicholson said.
“We’re focused on manufacturing high-quality rollers to a very select standard. We’ve got the full range for their component requirements. If you need rollers and components, it is all but guaranteed we’ll have the rollers and components you’ll need.”
Rulmeca also offers a digital tool designed to assist Australian customers, the RCS calculator. This calculator helps clients identify the optimal solution for their specific applications by analysing factors such as weight, speed, and other parameters.
Through the online portal and Rulmeca’s extensive digital catalog, Australian customers can easily access and utilise Rulmeca’s products.
“Customers can either do that themselves or have us do it with the information they provide. (It enables the process) to be as autonomous as you like,” Nicholson said.
Spanggaard said the company looked forward to engaging with more Australian customers to design the ideal solution for their conveyor requirements.
“We have the products, and we have the expertise and the calculation program to select the right product for their application. It is not just a roller or
an idler; it is (a solution) specifically for their application,” he said.
“It will give them the lowest total cost of ownership, which is really what we base our business on. We spend a bit more time with the customer in the beginning to ensure they get the best product.
“You mix that with the fact that we’re able to cover a large part of the product range which the customer requires.
“The deeper we can get involved in the customer’s application, the better service we can provide them.”
Rulmeca makes a wide range of conveyor components.
*T&C’s Apply.
ABHR looks at the reasons key bulk handling sectors are turning towards elevators to handle their requirements for working from heights.
FALLS FROM ANY HEIGHT can sound innocous but a worksite fall can quickly move from an accident to a fatality.
Earlier this year, workplaces across Victoria were left shaken after six recorded falls left workers either injured or, tragically, in one case, deceased in March.
“It might be easy to think that a tragic incident will never happen on your site, but if safety is not the top priority every day, then the chances are high that it will,” WorkSafe Executive Director Health and Safety Narelle Beer said.
Working at height is one of the largest threats to worker safety on any worksite. From 2015 to 2019, Safe Work Australia’s research indicated that falls from a height accounted for 13 per cent of worker fatalities.
Increasingly, more bulk materials
companies are investing in vertical access solutions, like the ones provided by Alimak, to support worker safety and address common worker issues, including fatigue, medical emergencies, shutdown, and injury risk.
After all, office workers are not expected to climb stairs with their laptops and keep cups, so why should bulk materials workers, in harsher environments, be expected to juggle tools while climbing stairs?
“In a medical emergency when every second counts, getting a patient to the ground or enabling emergency services to get to a patient in a timely manner could mean the difference between life and death,” Alimak sales manager Andrew Mercieca said.
“A site with a stretcher-capable elevator can save lives. If an employer is ever asked, ‘Have you made your
workplace as safe as possible in the event of an emergency?’ then providing an elevator is a big tick in that box.”
Alimak’s rack and pinion elevators, seen everywhere from ports to iron ore plant systems, help alleviate these concerns.
Rio Tinto engaged Alimak’s services to improve vertical access to its iron ore operation at Cape Lambert in Western Australia. Alimak designed, manufactured and installed Alimak SE 1200kg industrial elevators for the mine’s processing facility.
It marked a significant milestone for the company as they were the first permanent Alimak elevators installed on Rio Tinto’s iron ore screenhouse in Australia. However, they were also crucial to Rio Tinto’s expansion program, which the company undertook to increase the site’s production capacity. The industrial elevators helped ensure materials, equipment and personnel were transported efficiently and safely within the plant. According to Alimak, this resulted in decreased production downtime and enhanced safety.
Across the country, Alimak was engaged to design, manufacture, and install a custom elevator solution for the Williamstown Shipyard at Nelson Pier, Victoria. The solution had to comply with specific requirements for maritime operations and be able to integrate into the shipyard’s infrastructure, which was undergoing a multi-milliondollar upgrade.
The company installed an Alimak SE rack and pinion industrial elevator to serve as the primary access point for the hulls of docked ships. This upgrade marked a vast improvement in safety compared to the previous setup. The industrial elevator provided emergency stretcher access, which suited the safety protocols of the maritime operation and suited for emergencies, including
evacuations and responses.
“Shipyards and ports around the globe use Alimak elevators on ship unloaders to ferry crane operators to the driver’s cabin, often over 30m in the air, cutting fatigue, potential stress injuries from climbing stairs and improving overall efficiency from having a wellrested workforce,” Mercieca said.
Alimak has been designing, manufacturing and advising on elevator solutions across various industries since it was established more than 70 years ago. The company has installed more than 23,000 vertical access solutions globally, some of which are still operational after 25 years.
Mercieca said safety was one of the main reasons these organisations chose Alimak’s solutions.
“Workers are often climbing stairs with tools and parts and it can be hard to maintain the three points of contact while doing this,” he said.
“With Alimak’s elevators, maintaining the three points of contact is no longer an
issue for workers or management, which promotes a safer workplace.
“It can also help aid efficiency, reducing worker fatigue, during working situations like shutdowns and when moving parts and equipment. An elevator also assists older, more experienced workers, who may be susceptible to chronic knee and hip injuries, to keep working in their role.”
As a manufacturer and designer of elevators, Alimak has evolved its designs to be at the forefront of the sector. Over time, Alimak has adjusted and added the latest technology and innovations to its range to ensure they suit many industrial environments, which are often in harsh conditions. The elevators feature three independent braking systems, electrically and mechanically interlocked carriages, and landing doors. The rack-and-pinion drive system has no wire ropes, requiring only one single trailing cable.
The gravity descent feature ensures
the elevator can be safely lowered in case of a power failure. The elevator can be lowered at controlled speed to lower levels without activating the emergency brake, which has its own pinion separate from the drive system.
“With the ability to manually lower the elevator should there be a fault such as loss of power, the Alimak rack and pinion elevator offers many advantages over a wire rope elevator,” Mercieca said.
Due to its streamlined design, Alimak has designed its solutions to work in a relatively small footprint. There is no need for a supporting elevator shaft as the elevator travels through penetrations in the floor, access shafts, or outside of the structure.
Businesses are also not required to maintain a separate air-conditioned machine room.
Alimak designs all elevator machinery and electrical equipment to be located on the carriage’s roof. These safety features are ideal for companies in the bulk materials sector.
TheWeighPoint™Series7200integratorisdesignedforusewithThayerScale’sversatilerangeofRFbelt scalesforoptimalweighingaccuracyandperformance.TheWeighPoint™integratorreceivessignals thataretransmittedfromthebeltscalespeedsensorandweighingsubsystem.Theintegratormeasures beltloading,materialflowrate,andoverallweightfromthesignalstooptimizeplantmanagement, blendingoperationsandinventorycontrol.TheWeighPointisadual-processor,touchscreen-enabled solutiondesignedforcontinuousoperationinharshenvironments.
ABHR finds out how packing operations are benefiting from intelligent system networking.
of bulk products are realising the benefi ts of networking their packing machines with intelligent monitoring and analytics platforms to reduce unplanned downtime, increase production and improve safety, among other factors.
Haver & Boecker, a leading developer and manufacturer of packing technology for bulk, powdery products in the cement, chemical, building materials and food industries, is at the forefront of this aspect of Industry 4.0.
Haver & Boecker sales engineer Alexandre Santi told ABHR networked machines are less prone to stoppages and are quick to signal potential maintenance issues, which minimises waste and resource use.
“By utilising digitisation for process monitoring, control, analysis and optimisation, you can ensure your plant runs at full effi ciency and with optimised processes that minimise consumptions and disruptions,” he said.
Haver & Boecker’s QUAT2RO system provides users with an intuitive networking, monitoring and analytics solution with a variety of features that can be customised to the customer’s requirements.
The system can integrate a monitoring platform for real-time data and has an analytics tool to help diagnose problems.
It can make long-term interpretations of system data in a way that optimises service calls and repairs for maximum efficiency.
“These technologies automatically, effortlessly and securely provide live data that can signal potential maintenance issues while enabling deep new insights into machine productivity, scrap rates and more,” Santi said.
Available data and insights include the ability to monitor the production performance of machines in real-time, recognise signs of wear at an early stage, increase efficiency by comparing different machine data, proactively plan maintenance intervals based on machine data, check the effect of machine settings and optimise resource planning.
“A key offering of QUAT2RO is the direct live connection you get to one of our OEM service experts. With the use of cameras and smart glasses, they can diagnose issues and provide solutions remotely,” Santi said.
Available data and insights include the ability to monitor the production performance of machines in real-time, recognise signs of wear at an early stage, increase efficiency by comparing different machine data, proactively plan
maintenance intervals based on the machine data, check the effect of machine settings and optimise resource planning.
“A key offering of QUAT2RO is the direct live connection you get to one of our OEM service experts. With the use of cameras and smart glasses, they can diagnose issues and provide solutions remotely,” Santi said.
Chemical and building materials
manufacturer KLB Kötztal GmbH is known for its high standards of quality and service. This has been achieved through its innovative concepts, extensive expertise, and efficient production.
When the company wanted to modernise its manufacturing facility to an industry 4.0 standard, it needed a
technology partner that would ensure it upheld this reputation.
After engaging Haver & Boecker to engineer and supply the new mixing plant, comprising mixers, silos, tanks, and containers, along with numerous scales, conveyor screws, pumps, pipelines, and various other components, it was time to ensure KLB had complete visibility and control over the new facility’s operation and performance.
By implementing QUAT2RO, the entire packing chain was networked and made visible on a user-friendly dashboard. Operators could now monitor the plant in real time from anywhere, anytime. They had access to deep analytics to facilitate ongoing optimisation and the option for remote diagnostics by a Haver technician if required.
With QUAT2RO, KLB is now delivering consistent product quality. All product components are precisely weighed and transported to the mixer in the correct
amount and order, and optimal mixing duration and speed are achieved.
The company can trace all processes and raw materials without any gaps. It is capable of managing an unlimited number of recipes and can configure control recipes individually. It also seamlessly handles the creation and scheduling of orders, the generation of batch logs, reports, and statistics, as well as the automated management and documentation of production data, material consumption, inventory, and finished products.
The results are both tangible and measurable: machines and systems are more efficiently utilised, resources such as raw materials, energy, and time are saved, and errors are minimised.
KLB’s new mixing plant has achieved two essential requirements: the precise and reproducible mixing process management and the central monitoring and easy operation of all connected plant components.
Santi said Australian operations can also benefit from QUAT2RO.
“We work closely with our customers to analyse the requirements of their existing packing operation to configure a customised solution that’s right for them,” he said.
“We then plan the installation and training of employees and remain available to assist with the system when needed. Having the kind of data available that QUAT2RO opens up enormous opportunities for reducing costs and improving profits.”
Exploring how ESS Engineering takes a detail-oriented approach when designing its conveyor solutions.
CONVEYOR BELTS PLAY A CRUCIAL role in bulk material handling industries, ensuring the smooth transportation of materials to meet production and shipping deadlines. However, maintenance problems often plague these systems, leading to inefficiencies, safety hazards, and increased costs. Unscheduled belt repairs or replacements can sometimes last days, causing significant and expensive delays in the mine’s operations.
Sites utilise a range of conveyor belt accessories to increase the site’s safety, productivity, and effi ciency. These accessories include belt cleaning systems, support systems, belt alignment equipment, sealing systems, dust control systems, impact beds, idler frames, tracking systems, and guarding equipment.
When a customer approaches ESS Engineering for a solution, Tom Stahura, accounts development manager for Western Australia, emphasises the importance of a comprehensive understanding of the problem through application data sheets, client collaboration and site visits.
Diff erent maintenance needs call for diff erent solutions. A system requiring nightly maintenance needs a vastly diff erent solution than one needing maintenance every 18 weeks.
“We collaborate with the client to get the win-win scenario,” Stahura said.
Stahura always recommends a site visit from trained ESS personnel to “see the plant in operation because we can learn a lot more about what’s going on.”
Each plant has unique systems, practices and material properties which factor into an application.
Stahura emphasised the importance of collaborating with the entire team, not just the person in charge.
“We’ll talk to the service guys and operators and get some history, solutions that they’ve tried, what worked and what didn’t. These guys are there every day, and they’re dealing with it. We get all the data and parameters about the plant, how it performs, and what kind of downtime it has, but a lot of it is about what you are experiencing, and I drill down into that.”
He said that understanding a system’s speed, material, moisture content, loading process, discharge parameters, maintenance schedule, and the tonnes per hour rate, along with worker feedback, are key to forming the best conveyor solution.
“From there, we can look at the confi gurations to put the hardware into place. It’s important because you don’t design for your best days; you design for your worst days.”
When it comes to conveyor accessories and components, ESS Engineering makes the ones that matter.
ESS is committed to providing end-to-end service, from problem identifi cation, solution design, and manufacturing to installation and ongoing maintenance and service,
to ensure the client sees long-term benefi ts for their plant effi ciency.
Often, belt accessories can become system solutions to maximise their eff ectiveness.
For instance, at a head chute that experiences large amounts of spillage, impact cradles stabilise the belt, allowing wear liners and skirting to be closer to the belt for a better seal. High-quality skirting protects the system from dust and fugitive material.
Stahura emphasised the critical nature of conveyors.
“The conveyor is essential. If the material isn’t going from point A to point B along that line, no one makes any money because nothing is going out the door.”
The company’s experienced service technicians install, monitor, and maintain conveyor accessories. ESS also collaborates with the site to inspect the conveyor structure, conveyor accessories, and belt condition to produce a condition report and maintenance plans.
With manufacturing and service facilities around Australia, ESS gives its expansive client base confi dence that whatever solution they require can be made a reality.
“We want to work hand-in-hand with the client; we want to give them value for money, and we want to give them a solution that solves the issue and provides value,” Stahura said. “We want the win-win scenario.”
We are now better equipped than ever to help you to optimise your comminution and material handling operations for maximum performance, safety and efficiency.
Combining the industry leading screening, feeding and loading expertise of Schenck Process Mining with our mastery of crushing and wear protection, allows us to bring you an unrivalled equipment line-up. We underpin this unique offering with our expert process knowledge, full range of digital tools, high quality OEM spare parts, consumables and life-cycle services.
Scan the QR code to discover why we are the industry’s partner in eco-efficient mineral processing.
Sustainable operations and minimising waste are of critical importance to mining companies. ABHR looks at how Fenner Conveyors is designing its products to meet this need.
MINING OPERATIONS IN underground long-wall mining are increasingly considering how to enhance the sustainability of their projects. Key advancements in equipment, including conveyor belting, have helped.
Often, in underground coal mining, operators move the long wall around to diff erent sections of coal. During service, the belt can convey coal and rocks. When cutting through faults, the rock creates high impact, cutting and gouging the belt’s surface. As a result, old sections of conveyor belt are removed and new sections are installed, which leaves the mine with the issue of waste.
The ability to refurbish the belt and reuse it on the same or another system is referred to as recoverability. A cheaper conveyor belt often sees its recoverability drop dramatically, reducing its likelihood of being suitable for reuse on the same or another system.
Fenner Conveyors’ high-quality belts are built to withstand the abuse of underground coal mining for longer durations. The company combines its premium rubber cover compounds, like FireBoss S, with unique weaves for the conveyor belt fabric carcass, to enhance the likelihood of recoverability.
Sales and branch support manager, Craig Larkin, said this brings several benefi ts, including reduced waste and capital costs.
“It tends to vary mine to mine, in terms of how much rock is mixed in with the coal and how much damage is done,” he told ABHR
“Typically, our FireBoss S belt gets 85 to 90 per cent back in the fi rst year, and typically, it’ll go to 80 per cent in the next year. With the less expensive belting, it’ll be 80 per cent
in the fi rst year, 60 per cent in the second year and they’ll be lucky to get 40 per cent in the third year because it’s deteriorating so poorly.”
“We produce multiple levels of quality too. We have a FireBoss PVC, which is used with solid woven belting and is designed for belts in shorter change-out cycles, while the premium FireBoss S product, which is a fabric ply combined with neoprene compound, will typically go on to give fi ve to eight years.”
Fenner Conveyors has been developing the FireBoss product for over 30 years. Through decades of innovation, the FireBoss S belt has proven to withstand the harsh conditions of the Australian mining sector and provide value for money.
The FireBoss S conveyor belt cover compound is designed and manufactured in Australia for underground mining. Fenner Conveyors has constructed the compound with specifi c safety features to withstand the challenges of underground mining operations, including resistance to static and fi re hazards.
According to both internal and external testing, the FireBoss S compound is at the forefront of the market in terms of abrasion resistance, adhesions, tear resistance, and reduced aging. In real-world applications like the Queensland mining sector, some mines have found that they can reuse 8.5-9km of every 10km of belt used in longwall mining for the next mining block.
This higher recoverability rate can lead to a lower cost of ownership for mining operations.
“There’s a lot of moving parts with underground mining, but typically, you get what you pay for, which is what I’ve seen personally and what customers tell me,” Larkin said.
“Above all, you want the longest life out of your belt; you want to avoid the unpredictable time and costs to complete repair works to splices and belt.
“The quality of FireBoss makes it much easier to run, track, and steer, and I often hear that. Customers notice when they install our belt, they don’t have the same downtime attributable to inferior conveyor belt.”
By using FireBoss, mining operations can also improve their sustainability, through increased usage. More than ever, mining operations are thinking about their environmental impact and moving away from unsustainable practices.
So are manufacturers like Fenner Conveyors, which is dedicated to achieving its ambitious sustainability commitments. With a higher recoverability rate, proven by testing and real-world applications, FireBoss can help customers reduce environmental impacts of mining operations.
Support down under
As an Australian-based manufacturer, Fenner Conveyors provides a high level of service to its customers across the country. As part of the investment with Fenner Conveyors, customers will receive complete support across the product’s lifecycle.
Fenner Conveyors employs an expert team of conveyor specialists to provide
innovative and reliable solutions in all material handling situations, including emergencies and site shutdowns. The company performs belt refurbishments, site inspections and maintains a conveyor monitoring database to ensure customer systems are operating at an optimal level.
“It makes sense from our point of view that if we can help customers operate their conveyor systems at their most efficient levels, then they’re going to get value for it,” said Larkin.
“We are here for the long haul. That is the one thing I feel quite proud about working for Fenner Conveyors: if we have a problem, we fix it. If someone has an issue, we respond.
“As a local manufacturer, lead times are reduced; we can produce belting at three locations across the country, have it dispatched and at your door for when you need it. We supply the belt, we install the belt, and we maintain it.
“Because we have been specialising in this for the last 80 years in Australia, we’re able to ensure a consistent level
Helping pack coffee pods to compacting concrete walls for dams.
of quality every time, and customers know they’re going to get the same (quality) time after time.”
Over 3000 models in hydraulic, electric and pneumatic drives
• Filling / emptying truck and hoppers
• Levelling filled containers
• Feeding product to processes
• Settling chocolate in moulds
• Conveying raw materials without belts
• Helping flow from hoppers
• Cleaning silos
• Screening fine material
Kinder Australia’s pulley products help protect conveyor belts and improve productivity.
PULLEYS ARE THE driving force for conveyor belts, but if they are chosen haphazardly, could cause chaos.
Bradley Owen, engineering manager at Kinder Australia, said its risky to take a one-size-fits-all approach, as there is an increased chance of unscheduled downtime, or worse, a dangerous failure.
“Kinder uses classical stress calculations via our own proprietary software to determine the stresses, deflections, factors and formulae for pulley design,” he said.
“Minimising stresses at critical locations around the pulley, such as the welded shell-end disc connection, is important to prevent fatigue cracking.
“Each pulley undergoes dynamic balancing, with the welds fully stressrelieved and crack- tested with magnetic particle inspection and ultrasonic testing to ensure they will stand up to the pressures of their environments.”
Kinder’s K-Conveyor Pulley shafts are a highly specialised solution that are engineered to improve a site’s productivity.
The company’s primary goal with the design is to ensure the shaft has an infinite fatigue life under the expected
operating loads, achieved by utilising Australian design standard AS1403.
The pulleys are manufactured for maximum service life and fit for purpose application, undergoing ultrasonic testing after machining where required to ensure quality and strength. They can be built to meet customer specifications using the latest software and comply with AS1403.
Conveyor lagging provides a protective layer that shields the pulley from wear and tear caused by the belt and materials it carries. Lagging also improves traction between the pulley and belt, preventing slippage and ensuring efficient operation.
Owen said Kinder provides a range of different lagging materials, each suited for specific environments and purposes.
“These include rubber lagging, polyurethane lagging, ceramic lagging, slide lagging, and more – all very durable and high quality,” he said.
For difficult applications where buildup occurs on the pulley face, Kinder can provide several specialised pulleys. These eject fugitive material to either side of the pulley via a centre tapered cone.
K-Conveyor Spiral Pulleys are designed to be used for dry and freeflowing materials. The rotation of the pulley engages the self-cleaning action releasing foreign material through and on to the inner tapered cone which then ejects material outside the conveyor.
K-Conveyor Wing Pulleys can be used for large lump, sharp or sticky materials and are designed to be used in adverse, very abrasive and dirty applications, especially where there is material buildup on a solid conveyor pulley shell.
K-Conveyor HD Wing Pulleys are designed for applications where the standard wing design maybe inadequate for the duty.
“The success of your conveyor system hinges on the informed selection of the right pulley, not a cookie-cutter approach,” Owen said.
“For almost 40 years, Kinder have been leaders in the bulk material handing industry. With teams of Field Application Engineers and Specialists, as well as a dedicated Engineering Department.
“Kinder’s expert team brings their knowledge and a wealth of precision tools to the table, ensuring you get the correct pulley for your exact application.”
CST weighing equipment is popular in mines across the country. ABHR speaks to the company’s Western Australian service manager to find out why.
AUSTRALIAN MINES ARE MASSIVE undertakings, moving monumental amounts of material every minute. If a weighing system is off by a mere one or two per cent, it can lead to megatonnes of lost production potential and money.
This is why Control Systems Technology (CST) has a laser focus on delivering some of the most accurate weighing systems and service practices available on the Australian market.
Andrew Paterson, service manager for CST (WA), told ABHR an inaccurate belt weigher can be disastrous for mines.
“It can lead to underutilisation of a conveyor, blocked chutes, slower ship loading, inventory write-offs, over or underloading of ships, production downtime and lost production capacity,” he said.
“Weighing systems are our core product, supporting processes like stockpiling, primary crushing, train loading, and reclaiming.
“The more accurate they are, the more efficiently a mine or port can run these operations, and the more utilisation they can get out of the fixed plant infrastructure.”
Each mine site and material are different, and even small factors can potentially cause inaccuracies. This is why CST’s design philosophy is to work closely with mines to build a measuring system based on their unique requirements.
CST’s engineers will run a series of calculations to determine what equipment is needed for the application and then design the weigher needed for the specific location and accuracy requirement. This helps guarantee the system will provide the accuracy readings required.
Paterson said offering application and location engineered solutions rather than ‘off the shelf’ weighing systems means major
mining companies can trust in the equipment as installed.
“This is why CST are preferred suppliers to most of the worlds major mining companies, and also why we are able to guarantee accuracy,” he said.
“We have 3000 installations of our weighing systems around the world, and many are trade-certified units where accuracy has been proven through live load testing” he said.
“We have a reputation for having the most accurate systems available in the industry. That’s in part thanks to some of our approach and understanding of the problems of in-motion weighing.
“CST works closely with major mining companies. In this industry, all
it takes is one mistake, and that trust can be broken, which is why we have worked hard to develop the best design and service practices in the industry.”
The company’s research and development department works closely with process engineers, metallurgists and mine electrical departments to find ways to improve its products.
One way CST is helping mines learn more about their process is by using its Mass and Volume Information System. The system integrates a volumetric scanner on CST’s retractable scanner mounting frame, with CST’s industry leading belt weigher system via their MaVIS-ICS-ARM integrator software. The result is a system that not only
accurately measures tonnage and volume, but can also measure product quality via KG/M3 data as a cumulative figure, instantaneous figure, or averaged batch figures.
It also accurately measures how close material is to the edge of the conveyor belt for safety checks allowing sites to ease back on feeds on conveyors spilling rocks or other materials.
Material-to-belt-edge measurement is also used in the control logic to allow sites to optimise the material loading to ensure maximum safe throughput for the conveyor system.
This means that more production is possible from a conveyor that has this system fitted and the conveyor can operate more efficiently and with higher standards of safety.
It can also be used as a dual verification tool between the weightometer and the scanner as a sanity check and to provide potential for dual redundancy.
“This system is a game changer for bulk handling as it changes a belt weigher from something that usually provides only flow rate and cumulative tonnes to something that also provides cross section (m2), instant density (kg/m3), average density, batch density, materialto-belt-edge measurements, surcharge angle, belt edge position for belt tracking monitoring, belt width monitoring, material height monitoring, as well as the usual tonnes per hour, cumulative tonnes, alarms and belt speed,” Paterson said.
“This is a full suite of conveyor belt loading data, allowing all sorts of clever load optimisation algorithms to be implemented into processing control systems.”
On the service side, CST has worked very hard to have the best service practices in the industry.
CST has spare parts available in major hubs in the Pilbara, Queensland and New South Wales. If the team is required on-site, they can quickly get the
parts to the mines to prevent production down time.
CST technicians undergo rigorous training to ensure they know the equipment, like the back of their hands. This training helps minimise delays and cuts down on downtime.
Paterson said a lot of work goes into managing shutdowns and maintenance to keep downtime to a minimum and ensure best quality assurance practices.
“We’ve developed a system that ensures we are providing the best possible outcomes, and allows data to be verified in situ against theoretical data, historical trends and other empirical data,” he said.
“In addition, we have found innovative ways to help minimise downtime for calibrations. Historically, to calibrate a conveyor, you would need to run the belt empty for several hours to complete a calibration. This would potentially delay production.”
“We’ve recognised that this was causing delays and went about developing practices that allow us to calibrate the belt quickly and easily but without compromising accuracy, we now have a system where we can hand back conveyors into production in a fraction of the time but while maintaining the highest standards in accuracy. ”
CST’s research and development (R&D) team have also been hard at work finding new ways to adapt to the evolving needs of modern mines through products like the IntelliRoll.
The IntelliRoll is a low-cost, lowmaintenance wireless, autonomous, self-generating belt weigher in a single roller. It can enable sites to gather data from difficult, hard-to-reach or faraway places and gather useful data between feed points where larger weighers can’t be assembled.
It can connect to an existing PLC via a Wi-Fi network or directly to a smart device using Bluetooth or Wi-Fi. It can also store data on board, which can then be logged later. Multiple IntelliRolls can be linked together to increase the overall accuracy of the weigh data.
With the introduction of the IntelliRoll, CST can bring its weighing capability to whole new markets in agriculture, waste management, quarrying, and smaller mining operations. It can also gather data at a new level for process control in large ore processing plants.
“We plan to continue investing in innovations like the IntelliRoll to make sure CST provides the best weighing systems possible,” Paterson said.
ABHR learns how a local manufacturing presence has helped HE Silos Forbes reach its 55th anniversary.
FAMILY HAS BEEN THE cornerstone of HE Silos Forbes since it fi rst began in 1969.
The multi-generation company, which started out as a general engineering company in regional New South Wales, has grown into a major supplier of silos across the country. In 2006, the company took on an ambitious goal. The team decided it would work towards building a world where nobody went hungry.
Stevie-Leigh Morrison, the company’s executive director, said it’s a challenging problem to tackle, but an important thing to strive for.
“Our focus had always been on storing the nation’s grain, and that every grain counts,” she told ABHR “To reach that goal, we need to build the best silos possible – but also to help our customers weather droughts and floods, the ups and downs.”
As the company grew from small business to a major manufacturer, the company has had to evolve. HE Silos Forbes has two manufacturing sites in the NSW town of Forbes – one which focuses on bulk silos and the other on transportable silos.
Across these factories, around 40 workers ensure that everything is fabricated, formed and tested to meet the company’s strict internal minimums.
Every silo built at the company’s factories are tested regularly to ensure they meet and exceed Australian Standards.
Each product also undergoes finite element analysis to verify the structural integrity of the silo.
Larry Storm, the company’s general manager, said a lot of time and energy goes into ensuring silos comply to the relevant certifications.
“There’s been a strong pull towards food security and best storage practices on farm, which is our biggest driver,” he said.
“To ensure the safety of the food supply chain, grain needs to be stored properly in high quality silos. If we can maintain grain quality, that gives our customers a better product which is more likely to achieve a premium when it goes to market.”
“As the business gets bigger, we have needed to change our systems. We have incorporated things like enterprise
resource planning systems to help us track and monitor our manufacturing processes. All of our costing systems are computer-based, using data to keep costs low without compromising on quality.”
This quality is the cornerstone of the company’s brand. HE Silos Forbes prides itself on the relationships it has cultivated throughout the industry, working closely with farmers to solve their grain storage problems.
One of the most common things Storm hears from repeat customers is the value for money they get from the silos. Many of these customers bought silos 20, 30, or even 40 years prior.
“Word of mouth is everything in this industry,” Storm said. “The relationships we form are worth everything. If you build a connection with a customer, they’re more likely to recommend you to their neighbours and friends.”
“Even the seemingly small things can be really important, which is why if any of our customers need to get in contact with us, they can just give us a call. If needed, we’ll jump into the car and drive to their site.”
Australia is a large country, and silo customers are often located in regional, remote areas. Distance doesn’t daunt the HE Silos Forbes team, who can take advantage of being local to visit customers in person.
The family business isn’t planning on slowing its growth any time soon and has its sights on bringing its innovations to the global stage. The company’s Thermal Insect Control System (TICS) – a thermal syphon used to activate and distribute phosphine gas, operated at ground level – is being showcased at the 12th Conference on Controlled Atmospheres and Fumigation in Stored Products in Winnipeg, Canada.
The system eliminates the need to climb onto a silo to fumigate it, significantly reducing the risk of falls.
“We are now providing the TICS on most of our silos, with the farmers adding the system as part of their order, knowing and understanding the
TICS solves a safety issue and provides a simple, fast, effective and consistent way to fumigate their silos, helping to manage and maintain their grain quality without insect damage, which increases their return on investment,” Storm said.
A scientist from Charles Sturt University, who has been testing and validating the system for over three years will demonstrate the system at the Canadian event and showcase the safety benefits.
HE Silos Forbes staff are also planning to support an agricultural mission in India, focusing on grain storage protection. The company will support trade ministers and governments about improving food and grain storage, from coffee beans to rice.
The company has also recently celebrated its 55th anniversary.
“We have a very busy year ahead of us,” Storm said. “We’re going to more
than 15 trade shows over the next 15 months and have several innovations in development.”
“We plan to keep finding new ways to improve grain storage and keep putting our customers first.”
Dr Daniel Grasser and Dr David Bradney, from TUNRA Bulk Solids, provide an overview of the latest numerical simulation tools to solve bulk material handling problems and to optimise designs.
includes transportation and processing of raw materials. Discrete Element Method (DEM) modelling is a numerical simulation tool used to simulate the bulk particle flow. Each particle is modelled as a discrete element and the interactions of millions of particles represent the bulk particle flow occurring in a mining application. Once calibrated, DEM is a predictive tool and provides valuable insights into optimisation potential, which would not be achievable without numerical methods. However, to use DEM as a predictive tool to assess the particle flow, calibration and a good understanding of this simulation tool are essential.
TUNRA Bulk Solids has decades of experience in applying and calibrating DEM models. These models can be applied to predict the bulk particle flow of cohesionless (dry) and cohesive (wet, fines) materials. The particle
flow behaviour such as the motion of the bulk particle flow including the particle velocity, for example inside a transfer chute, can be predicted and measured. Resulting from this, important conclusions such as design recommendations for chutes and bins, risk of blockage, recommendation on dust mitigation and strategies for increasing the particle throughput can be drawn. Moreover, options to reduce wear (qualitatively and quantitatively) can also be outlined.
From this, the service life can be prolonged and unscheduled maintenance prevented; hence, the efficiency of the bulk materials handling operations can be increased. Importantly, applying a calibrated DEM model can be significantly cheaper and faster than experimental trials, and reduces the risks commonly associated with field tests.
Appropriate calibration of the Discrete Element Method (DEM) model is essential. In addition to qualitative site observations, a validation based on quantifiable measurements is crucial. Examples of calibration tests used at TUNRA Bulk Solids include the angle of repose, dynamic angle of repose, dynamic adhesion drop test, shear box and inclining wall friction test.
These tests are used as calibration and validation and represent different modes of particle flow. For example, the results of the shear box test are determined by the particle-to-particle interactions, where the results of the inclining wall friction test are mainly governed by the particle-to-surface interactions, where steeper shear angles are caused by cohesive materials and steeper wall angles by higher friction parameters.
The frictional parameters are physical parameters, while the shape and size of the particles are often simplified
and upscaled due to computational restraints. For example, the fines fraction is often simplified by larger spherical particles and modelled in combination with a cohesive model. For larger rock particles, a good implementation of the shape (non-spherical) is important and cohesion models are not applied. Careful application of cohesion models and other models such as the rolling resistance (RR) model are important for a good calibration. This allows achieving meaningful results based on validated models in reasonable computational times.
Additionally, DEM can be coupled with smoothed particle hydrodynamics (SPH) in case the bulk flow behaviour of viscous and thixotropic materials needs to be predicted.
Smoothed particle hydrodynamics
SPH has found a wider application in the bulk materials handling sector in the last few years. The SPH method is a Lagrangian mesh-free approach that can be coupled with DEM modelling. This is especially useful when the bulk flow behaviour of two-phase materials, for example viscous slurries such as a mixture of water and particle fines, are modelled. The SPH-DEM coupling is a two-way approach coupling the momentum transfer between the fluid and particles. In detail, each SPH element has a mass, momentum, and a resulting energy, interacting with other elements. Therefore, it is important that the SPH elements (representing the liquid phase fraction) are at least three-times smaller than the DEM particles (representing the coarse fraction with discrete particles). In addition to the calibration techniques mentioned in the DEM section, additional calibration experiments need to be conducted for SPH-DEM. For example, quantifying the thixotropic behaviour of a cohesive slurry during mixing, under different pressures and under vibrations.
Once calibrated, the SPH-DEM model can be used as a predictive tool to forecast the bulk flow behaviour of cohesive twophase materials. This gives additional confidence when designing and reviewing transportation on conveyor belts, chutes and storage bins used to handle viscous two-phase slurries often possessing a complex flow behaviour.
Additionally, the SPH-DEM coupling can be applied to model the abrasion of
slurries (for example, water mixed with sand). Wear rates can be scaled based on experimental investigations and hence SPH-DEM can be applied as a predictive tool for service life estimations. However, it is important to highlight that currently SPH-DEM models require relatively high computational efforts, when compared to DEM models.
semi-solids (slurries) into fluid-governed interactions, other computational tools exist to provide further insight into design problems. Computational Fluid Dynamics (CFD) is used to simulate and analyse the behaviour of fluids (liquids and gases) and their interactions with solid surfaces. In the area of bulk materials handling, CFD is invaluable for modelling and predicting the behaviour of airflows and fluids within equipment such as pneumatic conveying systems and loading/discharge areas around transfer points.
This simulation capability is particularly useful for understanding and optimising dust considerations when handling drier materials and may be used in the assessment of ventilation systems, or in fundamental design to optimise plant geometry to passively reduce dust generation.
CFD allows designers to model airflow patterns within various equipment. By
engineers can identify the most effective designs to ensure proper airflow and gain insight into the dispersion of dust particles, enabling the design of more effective dust control and extraction systems. By understanding how dust behaves in different scenarios, engineers can implement measures to minimise dust spread and improve air quality within facilities.
The design of transfer points is critical for ensuring the efficient flow of materials. This is particularly relevant for transfer chutes, where abrupt changes in the trajectory of the material stream and large free-fall areas can result in significant air entrainment and dust generation. Advancements in computational resources and the integration of CFD with other simulation methodologies, such as DEM, have enhanced the ability to analyse complex bulk material flows. When combined with CFD, this integrated approach can simulate:
• Air entrainment from falling material streams: The interaction between air and falling materials can significantly affect flow patterns and efficiency. Coupled CFD-DEM simulations can model this interaction, providing insights into how air entrainment impacts the overall flow.
• Flow dispersion and collision: Understanding how particles disperse in a flowing system can have a significant impact on the
amount of dust generated within a system. Areas of steep impact with large impact angles generally result in the largest release of dust. With CFD-DEM analysis, it is possible to better quantify the effects of different designs to minimise dust. By leveraging CFD and CFD-DEM simulations, engineers can optimise bulk material handling systems, ensuring efficient operation, minimising dust generation, and improving safety and environmental conditions within facilities.
The accuracy of CFD predictions heavily depends on the quality of the input data, including fluid properties, boundary conditions, geometry discretisation, and material characteristics. Errors or approximations in these inputs can lead to inaccurate results, impacting the reliability of the conclusions drawn from the simulations. Therefore, validation with on-site behaviour and/ or experimental data is typically required and recommended for complex problems to ensure the accuracy of the models. When considering coupled DEM-CFD problems, the following additional considerations are also important: for the scale of most industry-based problems, at present the smallest DEM particle sizes may be in the order of 10 – 20 mm to permit DEM simulations to effectively solve. In contrast, dust particles may be well under 1 mm in size, ranging down to µm in size. It is therefore important to consider the effect of this potential mismatch of scale on the interaction between the air and particles. For problems with larger materials sizes, the influence of the particles on the air becomes more closely aligned to reality, whereas, for fine dust particles, this difference becomes more significant, and may indicate that coupled models are less appropriate or may require more traditional multiphase-focused CFD techniques.
Up to this point, the discussed analysis techniques have primarily focused on understanding the flow and movement of bulk materials. However, the effect that bulk materials have on the structures they interact with is also of high importance
to the safe and efficient design of bulk material handling and storage systems.
Finite Element Analysis (FEA) is a computational technique used to simulate and analyse the stresses and deformations that result from loads applied to structures. Complex physical systems are analysed by dividing these structures into smaller, simpler parts called elements. This method enables detailed analysis of how different loads, including material loads, affect structures.
In the field of bulk material handling, FEA addresses a wide array of problems, including evaluating the structural capacity under bulk material-induced loads on structures like the walls of hoppers, bins, or silos. It can also be used to assess more complex dynamic phenomena, such as quaking in soils or train load-out bins. The tools available within FEA also allow for the analysis of effects such as vibration, dynamic movement, and thermal considerations. This enables an in-depth understanding of the impact that bulk materials can have on the structures they interact with.
The bulk material loads applied in an FEA model can originate from various sources, including hand calculations based on relevant standards and coupling with other numerical techniques like CFD, SPH, or DEM. Coupling techniques such as DEM with FEA allows for the development of complex load cases. However, it is important to note that the accuracy of FEA predictions heavily depends on the quality of the input data, including accurate material properties and boundary conditions. For techniques such as DEM, assumptions around particle stiffness can significantly affect the magnitude of boundary force predictions. Misestimations of the output from one simulation technique can lead to incorrect predictions, affecting reliability of results.
To address these challenges, it is recommended to use alternative methods such as fundamental approaches or on-site measurements to calibrate and validate the load inputs used in an FEA model. This helps to quantify potential modelling unknowns and ensure more reliable and accurate predictions. Integrating FEA with other analysis techniques provides a powerful toolset for understanding and optimising the interaction between bulk materials and the structures they affect, leading to safer and more efficient bulk material handling systems.
Overview of simulation tools
Bulk materials handling problems encompass a wide array of problem types and material conditions, and it is therefore important to select the most suitable simulation method to efficiently and effectively understand each problem. Fortunately, tools now exist to simulate bulk material through the full array of problem types; from dry, dusty material
DEM
SPH-DEM
CFD
FEA
Bulk particle flow (dry and cohesive particles)
Bulk particle flow (viscous two-phase slurries)
Flows (liquids and gases)
Deformation (stresses on solid volumes
through to granular or cohesive flows, and even very wet slurry applications, and their effect can be assessed both in terms of material-material interaction as well as their impact on the structure and equipment they interact with.
Table 1 provides a summary of these considerations.
Ultimately, the most appropriate choice of simulation tool depends on the type of bulk material to be analysed, the particle size of the material being simulated, and the state in which the material is being handled, and the desired level of understanding of the problem. TUNRA Bulk Solids has decades of experience
in both physical lab-based materials testing, and advanced simulation techniques, and can help navigate the challenges of selecting the most appropriate method for each unique bulk materials handling problem.
TUNRA Bulk Solids is a consultancy covering the entire spectrum of bulk materials handling and storage applications. TUNRA was established 1975 and is operating out of the Newcastle Institute for Energy and Resources at The University of Newcastle, Australia.
DAVIS
Steve Davis discusses Australia’s bulk handling sector, highlighting the advancements the industry has made and the organisations that are providing local innovations and expertise. Steve has worked in bulk handling for 30 years, for both resource companies and professional engineering firms, in Australia, South Africa, the Middle East and Canada. His experience encompasses such commodities as iron ore, coal, potash, phosphates, petcoke, sulphur, sands and grain.
Conveyor belt fires are reported regularly in various forums from around the world. Steve Davis explores how Australian bulk handling sites can avoid them.
CONVEYOR BELT FIRES CAN result in injuries and cause signifi cant damage and loss of production. Absence of fi res on your site to date is no guarantee for the future unless good preventive measures are taken on a continuous basis.
Conveyor belt fire causes are well understood and are therefore the result of a lack of the systems and practices required to prevent them.
Fire prevention has three components: design, which should mitigate potential causes of fire; operation and maintenance, which should manage ongoing fire risks; and housekeeping, which should mange external fire risks. Design of the conveyor system should include analysis of perceived risks, including the risk of fire. Potential fire risks should be identified, and mitigation strategies included in the design. The design intent of fire mitigation must be clearly identified to personnel involved in the day-to-day operation and maintenance of the system, and personnel must implement and maintain strategies and equipment. Regular visual inspection of the conveyor system for issues known to cause fires and other problems reduces risks. Housekeeping, including clean-up of material and other spillages, correct storage of all equipment after use and general evaluation of territory reduces risk of fires and improves likelihood of safe egress.
As with any fire, three components are necessary for a fire to occur. Conveyors generally
inhalation.
operate in an atmosphere containing oxygen, the first component necessary to sustain a fire. The conveyor itself provides the second component, the fuel for a fire. Conveyor belts are manufactured from natural, or more likely a synthetic rubber, fabric carcasses, and rubber noodles for steel cord. Most components of a conveyor belt are flammable, although the extent of flammability varies significantly. Some of the conveyor components, such as skirts and cleaners, idler rolls and pulley lagging might be rubber or polyurethane, each with different degrees of flammability. The ignition temperature for rubber is quoted between 300 and 400 degrees Centigrade. Typical mineral oil lubricants in bearings and gearboxes have a flash point as low as 160 degrees Centigrade. Some bulk materials are flammable.
The third component necessary for a fire is an ignition or heat source. Given that fuel and oxygen are always present for conveyors, we must look to potential ignition
sources as the methodology to prevent fires. Except for any deliberate setting of a fire, it should be possible to remove or replace all types of ignition source. In addition, we have several methods available to detect the potential of a fire before it occurs. If we look at the belt conveyor as a machine, the typical ignition sources for a belt fire are friction and mechanical failures. Friction arises whenever the belt rubs against something fixed, or that should be rotating but has stopped. Is the most likely fire the result of a seized rubber lagged pulley or idler, where the belt rubs against fixed rubber and ignites the pulley? If your conveyor has lightweight idlers, is the idler material flammable from rubbing friction? Polymer idlers appear to wear away before this could happen. Could fire be caused by rubber or metal skirting or a wear liner that has been dislodged and become jammed against the pulley or the belt or both? Constant motion from the belt against any non-moving item can create a local fire.
Could fire be caused by a belt rubbing against steel structure, a chute or other component and heating the metal? A short cycle belt could potentially get hot enough to burn from this, however longer cycle belts typically cut through steel structure, or the steel destroys the edge or cover of the belt. Neither of these are good for the conveyor and should be rectified as soon as possible. It is possible that continuous belt rubbing against steel will heat the steel until it is hot enough to ignite the belt cover. We have all seen idlers and pulleys which, when seized, are worn through until there is a knife edge. This could become a friction ignition source, and often cause serious damage to the belt covers.
Most conveyors have an electric motor and gearbox, and all pulleys are mounted on grease lubricated rotating bearings. A fire engineer thought motors the most likely ignition source for a conveyor fire, followed by grease in pulley bearings if the bearing starts to seize and overheats. Brakes are a potential ignition source and reach high temperatures for a short period. Dragging brakes will remain hot during operation.
Considering external ignition sources, we look first for storage and spillage of flammable materials near the conveyor such as oil or grease. These should be removed as they are easy to ignite and then transfer fire to the belt. Pipelines carrying flammable liquids near conveyors could leak and create a fire risk, especially if separation is small such as using the conveyor gallery as a pipe rack. Electrical faults are common fire starters, and we commonly use conveyors as cable racks.
Several bulk commodities are flammable, such as coal, sulphur, and biomass. These may add fuel to a conveyor fire, or if burning prior to conveying may be the ignition source for a fire. Sulphur, coal, and other dusty materials that are susceptible to ignition from static and other sparks maybe easily ignited on or near a conveyor. Conversely, if a conveyor does burn, it is likely to ignite any spillage from flammable bulk materials.
Conveyors that discharge these materials into a bin need special attention as the bin contents can ignite or explode from static and blow back to the conveyor. Other potential ignition sources include mobile hydraulic equipment, hot work maintenance on nearby equipment. Hot work near isolated conveyors has been known to start a fire chain, for example hot work set fire to a rubber lined screen underpan which then ignited the feed conveyor belt. We have prohibited smoking on most sites, but could vapes initiate a fire?
The number of fires we see indicates that we are not perfect in removing ignition sources, so we should now look at reducing the consequences. Consequences of a conveyor fire include potential injuries, smoke, and chemical inhalation from burning rubber and other chemicals. Fires can burn hot enough to destroy all electrical, mechanical, and structural components of a conveyor and may spread rapidly if the conveyor is not stopped at the earliest opportunity. Conveyor
• Increase profits – with clean and weight-accurate processing and perfect presentation
• Maximise benefits – with improved product protection
• Reduce costs – with a cleaner packing environment and less waste
fires are most destructive when the conveyor continues to move, and the fire spreads the full length of both carry and return sides.
Most conveying systems are single stream with no redundancy, and as such there is likely to be substantial downtime for inspections, assessment, demolition, and rebuilding. Alternate methods of material transport may be required at high cost.
Safety in design must consider safe egress from all locations in the conveyor system, with a strategy of dual redundant pathways.
Longer conveyor galleries often cannot comply with regulatory expectations regarding maximum distance to exit point, and this must be considered with application for exceptions if required. Egress may need to consider provision for stretchers. In the event of a fire, emergency services may require specific access to the site and the structures, plus access to a defined water supply. Water supply to elevated gantries may require additional tanks and pumps to meet emergency services’ needs.
Mitigation strategies include choice of belt cover material. Fire Resistant Anti-Static (FRAS) belt is available at a premium over conventional belt. This belt is formulated to ground static charges and to resist fire. The cover will still burn but should self-extinguish if there is no external flame. Use of this belt should be discussed with suppliers, as there are several grades available. I have seen several installations where FRAS rubber belt has been changed out for “standard” rubber to save money. Static earthing is improved by using earthing whiskers onto the belt covers.
Selection of components will impact risk. Cheap idlers with poor sealing arrangements may reduce cost, however in a wet and / or dusty environment bearing failure will be higher leading to more seized rolls. Pulley bearings should be fitted with excellent seals and correct relubrication addressed. Select the correct belt for the duty. Australia has some of the best products and guidance on conveyor component selection and has developed a wide range of monitoring devices for preventing fires.
There are a wide variety of sensors available that can detect temperature, heat, flame, smoke, vibrations, and
chemical emissions. Heat sensing wires can be run down both sides of a conveyor to pick up any change in temperature that could indicate a hot bearing or the start of a fire. Temperature sensors are used to detect temperature trends in bearings, motors, and gearboxes. Vibration detectors can be mounted directly to bearing housings. We have systems that trend the condition of idlers along a conveyor and identify failure.
The key with all monitoring is to understand what the outcome means and how the system should react. Most of this can be managed by the automated control system, however operators should understand what is occurring especially if there are manual inputs required. Monitoring provides a condition trend from a baseline. The trend for conveyor components will typically vary with ambient conditions, load cycles and deterioration. We want to keep the system running but must stop the system when there is a risk of injury and damage. This means we can accept and monitor a gradual trend change, either cyclic or continuous deterioration to a planned maintenance point.
When there is a rapid change in the trend, such as with any indication of a fire, we need to plan the action in advance. An immediate stop for a conveyor, including up and downstream feeds, and initiation of fire mitigation processes seems the most likely course.
After identifying a fire, personnel must evacuate, so an alarm system and exit strategy was included in the design risk outcomes and fire management plan. The design will also incorporate methodology to restrict and extinguish a fire as quickly as possible.
A call to the local fire brigade is necessary. Fire control systems can make this call automatically.
Immediate solutions to fires include: no provisions except those required by the local fire brigade, i.e. let the fire burn as all personnel have been evacuated or, provide localised permanently connected fire systems for fire management. It is common practice to install a dedicated fire water system with fire hose reels and hydrants. Unless site personnel have been trained in using these hoses and have suitable PPE to protect against heat and fumes, this should be left to the professionals.
For some conveyors, where there is a need to provide a safe exit, where the bulk material is flammable, or where there is a desire to protect equipment, we install deluge systems. These either form an extension of the fire water system or can be independent. Foam deluge is an option to water. Deluges are designed to exclude oxygen and cool the fire. Where the conveyor carries flammable bulk, the deluge can wash burning bulk from the conveyor and spread a fire further. Design and installation of deluge systems should be more than just conveniently located piping with available spray nozzles.
Finally, fire management protocols and systems must be always available and require testing and maintenance. Adaptation is necessary if maintenance of the conveyor or the fire system changes the protocols in place, for example, if the water supply must be isolated or an egress walkway blocked, change in use, etc. Australian conveyors may be older than 50 years in their original design, with multiple alterations and upgrades. Is the fire management system still suitable?
ROBUST ✓ LIGHTWEIGHT ✓ ECONOMICAL ✓
DYNA Engineering has developed a “chamfered mesh pattern”, designed to reduce washdown splash back and increase visibility through the guard panels.
This design feature is a major “point of difference” compared to standard HDPE mesh and will improve inspection and cleaning operations.
Washdown Mesh
• Up to 50% additional spray-through for washdown.
Increased Visibility
• Up to 25% additional viewing angle and see-through visability.
Enes Kaya explores the origins, principles, e ectiveness, and limitations of physical scale modelling in chute design, comparing it to other techniques such as continuum mechanics and discrete element method modelling.
THE DESIGN AND OPTIMISATION
of transfer chutes is a critical aspect of the materials handling industry. Properly designed transfer chutes ensure that the desired material throughput rates are achieved, that the material stream is controlled and that dusting, and wear are minimised. Typically, the design of transfer
chutes leverages multiple approaches including empirical methods, including simulation and physical scale modelling.
Jenike & Johanson is excited to combine these techniques to further the science of bulk material flow with the recent acquisition of Bulk Solids Modelling (BSM). This will enhance the company’s capability to solve the
toughest bulk solids handling challenges for clients globally.
Physical scale modelling has its roots in civil and hydraulic engineering, where scale models of dams, spillways, and other structures were used to study fluid flow and structural integrity.
During the 1990s this technique was adapted by BSM for use in materials handling to evaluate chute designs. Engineers were able to observe and test material flow, chute angles, and wear points before full-scale implementation.
The principles behind physical scale modelling are the application of similarity laws ensuring that the model built accurately represents the real system but in a scaled-down form. The two types of similarity considered are:
1. Geometric similarity: Ensuring all dimensions of the model are proportionally reduced by a consistent scaling factor. For example, a 1:10 scale model would have all linear dimensions reduced by a factor of 10.
2. Dynamic similarity: Ensuring that the ratio between the major forces in the system remains constant as the scale of the system changes. These ratios are expressed as dimensionless terms such as the Froude Number.
In physical scale modelling, a scaleddown version of the transfer chute system is constructed, typically using acrylic to allow observation of material flow. The process involves several steps.
1. Construction: Building the model to the appropriate scale, ensuring all geometric proportions are maintained.
2. Material selection: A proprietary blend of surrogate material is used to emulate the behaviour of that in the actual system.
3. Flow simulation: Introducing the scaled material into the model under conditions that replicate the fullscale application.
Testing involves observing material flow, identifying potential issues such as buildup or excessive wear, flow of material onto the receiving belt, and making iterative adjustments to the design. Through repeated testing and modifications, the design is then optimised for full-scale implementation.
Physical scale modelling has proven eff ective for several reasons:
• Visualisation: It provides a tangible, visual representation of material flow, facilitating the identification and correction of design flaws.
• Empirical validation: There is an extensive history of success using dynamic scale modelling techniques. Many chutes that have been designed and validated using scale modelling are used in mining operations globally, demonstrating its reliability.
• Cost savings: Early identification of design issues prevents costly changes during full-scale construction and operation.
All modelling methods have both strengths and weaknesses.
1. Continuum mechanics: This approach uses mathematical models to describe material flow as a continuous medium. It excels in fluid dynamics applications but may oversimplify the behaviour of granular materials common in transfer chutes. Continuum mechanics offers detailed stressstrain analysis but can struggle with particle flow behaviour.
2. Discrete element method (DEM): DEM simulates material flows by calculating the interactions of a discrete set of model particles to represent the real material using Newtons’ laws of motion and particle contact models. It has the advantages that it can be conducted in the virtual space prior to fabrication or modification. DEM output provides critical information about the flow of material such as surface forces and velocities. DEM typically requires significant computational resources. DEM simulations must incorporate valid calibration of the material, correct contact model selection, and input parameters.
3. Scale modelling: A physical scale model is an analogue system which uses a much larger number of particles than a DEM simulation. Once a model is constructed, simulations can be conducted very rapidly. Newtons’ laws are automatically obeyed in this system and particle interactions are set by the selection of the test material. Scale modelling provides an alternative method of validation that is independent of a DEM simulation. Disadvantages of the methodology are that there may be a significant lead time involved in constructing and fabrication the scaled model and that it requires a dedicated space to run the modelling program.
Physical scale modelling remains a valuable tool in the design of transfer chutes, providing unique benefits in visualisation and empirical validation of the designs. Its historical success and practical insights make it a reliable tool for transfer chute design evaluation. Combining physical modelling with continuum mechanics and advanced computational techniques such as DEM can lead to more robust and efficient evaluation of designs. By leveraging the strengths of both traditional and modern methods, engineers at Jenike & Johanson can achieve the most accurate, cost-effective, and efficient solutions for material handling challenges.
When it comes to optimising powertrain performance, Regal Rexnord provides the bulk handling industry with end-to-end engineered solutions and market leading service and renewal support. So contact us today and discover how we provide complete and fully integrated outcomes that enhance efficiency and reliability.
and maintenance. One then led to another, and I’ve now been working in the field for over 20 years.
I am currently researching... solutions to reduce the greenhouse gas emissions intensity in the mining and minerals
Stieber RDBK
mentors over my career who supported my professional growth, allowing me to take stretch roles whilst providing a safety net if I needed it.
The most valuable lesson I have learned is... engineering is a team
The Society also aims to encourage research and development, technology transfer and training. It holds national and international conferences at regular intervals.