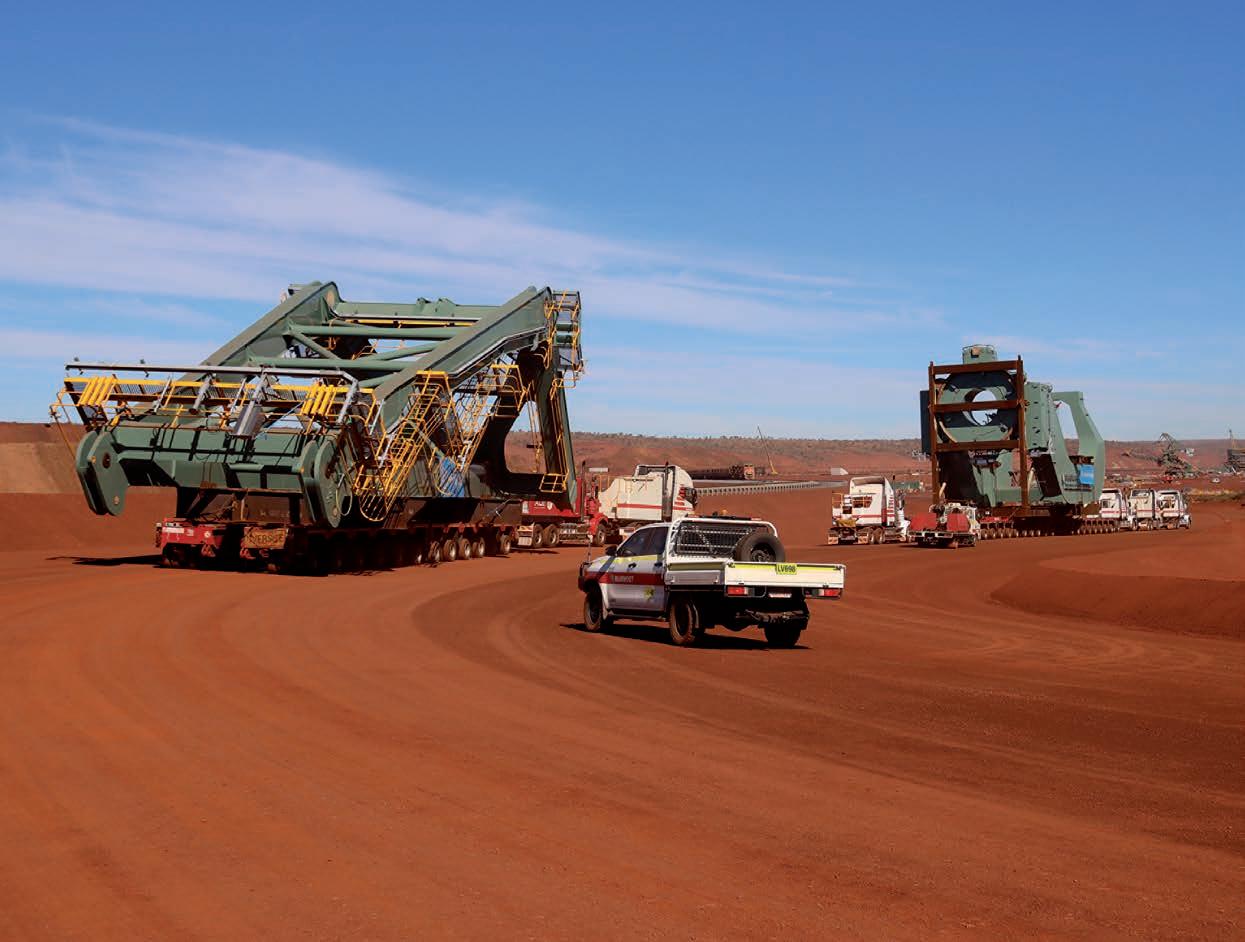
9 minute read
24
from ABHR OCT 2020
by Prime Group
Modularisation was an important consideration in order to design machines of this size.
ABHR speaks to the team at thyssenkrupp Industrial Solutions Australia to learn how the company supplied some of the world’s largest stackers and reclaimers for BHP’s US$3.6 billion South Flank project.
BHP’S SOUTH FLANK PROJECT
is expected to produce 80 million tonnes of iron ore per year, making it one of the largest iron ore operations in the world.
Billions of dollars have been spent on the project, which will involve the construction of a new crushing and screening plant, stockyard and train loading facility, a new mining fleet, substantial mine development and an overland conveyor.
To help deliver this sizable project, BHP engaged thysseknrupp Industrial Solutions Australia to design, construct and commission three new generation stock yard machines, some of the largest rail mounted machines ever built.
Danny George, Project Engineering Manager at thyssenkrupp, said the company had a long history of successfully delivering balanced machines and designing bespoke equipment.
“Our installed base of the highest capacity iron ore machines in the Pilbara gave us the ability to deliver the machines,” George says.
“We have been reclaiming minerals up to a rate of 33,000 cubic metres with our giant bucketwheel excavators working in Germany.”
The scope of supply includes two rail mounted stackers and one bucket wheel reclaimer. Process plants tend to operate on a 24-hour schedule, with all product fed into a stacker via a conveyor belt and stored in a longitudinal stockpile. When trains arrive at the mine facility to transport the commodities to the port, the bucket wheel reclaimer recovers the ore from the stockpile to feed the train.
The two stackers and bucket wheel reclaimer that thyssenkrupp supplied the South Flank project are capable of stacking and reclaiming at a nominal throughput of 20,000 tonnes per hour and can travel along the length of the stockyard, which is approximately 1700 metres long, at a maximum speed of 0.75 metres per second.
Each stacker weighs about 2000 tonnes with the reclaimer weighing in at around 3000 tonnes. The machines can slew and luff, and a combination of three movements allows them to feed and reclaim product into and from all allocated and available space within the stockyard bunds area.
Modularisation was an important consideration in order to design machines of this size. The large physical dimensions needed to fit within strict transport envelopes and weights to maintain optimal logistical expenditure.
Anthony Squire, thyssenkrupp Project Site Manager, says the machine modules were designed to maximise structural, mechanical and piping and electrical and instrumentation preassembly at the Australian Marine Complex.
“Due to the machine module size, careful consideration must be given to the constructability and transportation of modules,” Squire says.
“Transport limitations around the Perth metro area and the subsequent weight and physical dimensional limitations during sea and road transport to the mine site, along with the final erection and module interface
connections were also key factors that needed to be kept in mind.”
Multiple manufacturing facilities were engaged in a collaborative effort to deliver the machines, including Western Australian businesses Civmec, AGC and Doina – creating around 540 local jobs. The facilities were selected based on individual capabilities and transport restrictions to the Australian Marine Complex, where the modules were leadout on vessels for sea transport.
Onsite installation of the modules also brought with it a unique set of challenges to be overcome. Due to the overall size and weight of the modules, very detailed construction methodologies and erection sequences were engineered based on minimising risk.
Stability factors, especially during cyclone season, were important when building the machines. As a result, large fabricated modular support structures were designed and used during the construction phase of the project.
Once the machines are fully erected and balanced, only then could these construction aids be removed. Due to the weight of the modules, these construction aids are specifically designed taking worst case scenarios into account to ensure stability of machines and safety of all personnel on site.
All machines included within the scope of supply were designed with hydraulic drives in lieu of the
thyssenkrupp will supply the required OEM spare parts and provide specialist field service technicians. traditional electro-mechanical drives where possible. Uwe Zulehner – Head of Business Excellence and Sales, says this was done to increase reliability and efficiency of operation.
“In high power demand operating regimes, such as that seen with reclaimer digging, hydraulic systems have proven to offer more efficiency and reliability than conventional electro-mechanical systems,” Zulehner says.
“In addition to the introduction of hydraulic drives, all prime movers on the machine whether electrical or hydraulic are fitted with condition monitoring

Each stacker weighs about 2000 tonnes with the reclaimer weighing in at around 3000 tonnes.
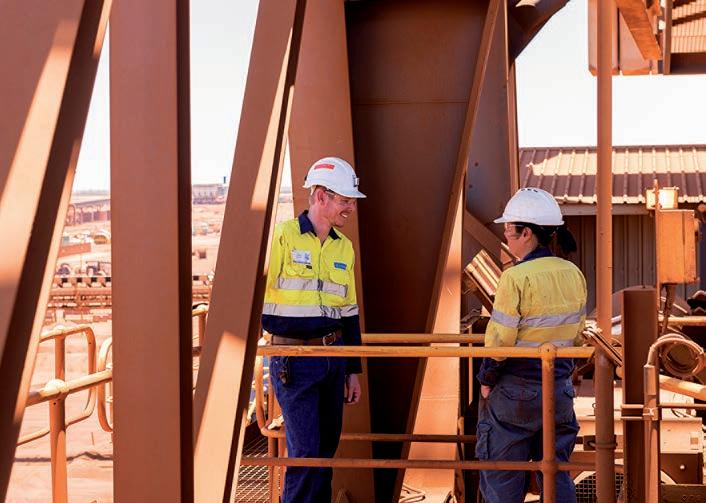
instruments, such as accelerometers, to predict premature failure of equipment.”
A number of safety features were also included in the design, such as an anti-collision system to prevent the machine from colliding with surrounding infrastructure like yard conveyors and stockpiles during operation. Other features include automation systems to prevent the machines from stacking over the yard conveyor and speed control limitations for all machine movements.
As part of the contract, thyssenkrupp will supply the required OEM spare parts and provide specialist field service technicians to work closely with BHP throughout the life of the assets.
Zulehner says the two companies have a longstanding, strong relationship when it comes to maintaining thyssenkrupp branded machines to the best optimal performance and reliability.
“Only thyssenkrupp has the technical experience and expertise to ensure these machines are well maintained and operate at their best to produce the required output for our clients,” he says.
“Further to this we have highly trained technical specialists who will carry out the offsite repairs and refurbishment of critical machine parts and components.
“Going forward, automation and digitalisation will play an important role to underpin our strong position in serving our customers.”
HDPE conveyor guards built for a sunburnt country
Diacon Australia’s HDPE conveyor guards are lightweight, safe and designed for the harsh Australian conditions.
ACCORDING TO THE BUREAU OF
Meteorology, Australia has one of the highest levels of ultraviolet light (UV) exposure in the world.
Just like skin, these harmful rays of light can cause materials to crack and degrade. When plastic materials are used to build safety guarding for conveyor belts, this UV can drastically affect the lifespan of the products.
Brendan Refalo, Managing Director at Diacon Australia, one of the nation’s leading conveyor guarding specialists, says this is why it is critical to use products designed and manufactured in Australia, for Australia.
“Internationally, there are some companies that say their materials will last for 10 years, but these are designed to last in places like Europe, where the UV levels are much lower,” he says.
Diacon guards come with a hook and hang system that makes removing the guards easy and avoids creating tripping hazards.
“Often, when these get put into operation, the Australian sun will quickly degrade them, reducing their lifespan by years.
Diacon Australia is a manufacturer of high-density polyethylene (HDPE) conveyor guards, designed specifically for Australian conditions. The products were the result of two years of research and development in 2010, after the company saw a need for significant improvements in conveyor productivity, machinery guarding, work area demarcation, and fall protection.
At the time, existing steel guards were cumbersome and had a short life due to the amount of corrosion in workplace environments. To limit corrosion, steel guards must be maintained and kept painted, or replaced prematurely which is costly.
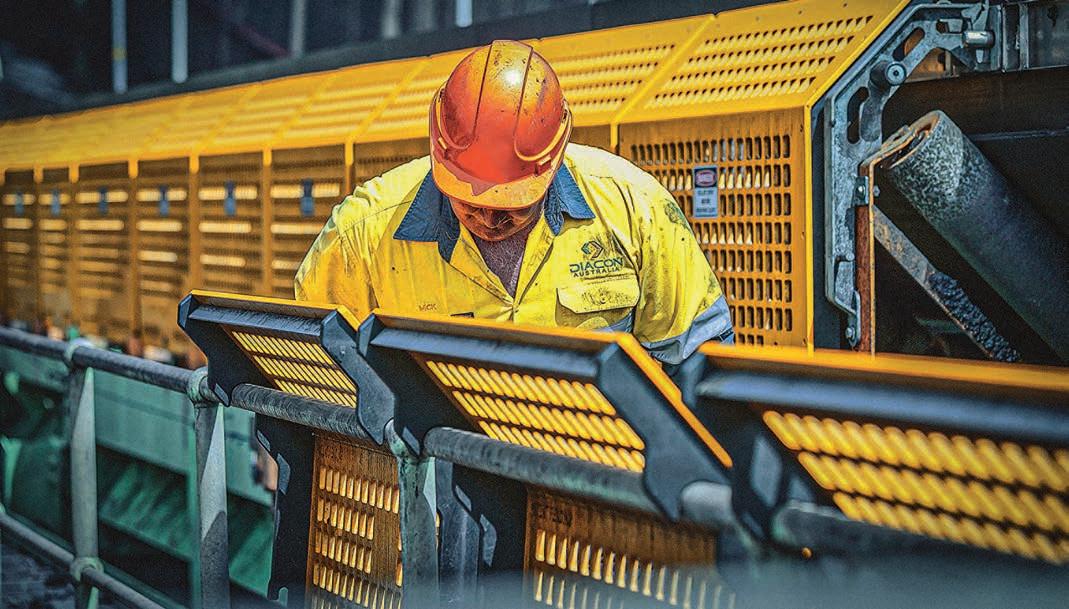
Diacon’s HDPE conveyor guards take advantage of the fact they are made of plastic, meaning they are up to 40 per cent lighter, never have to be painted and can be easily recycled at the end of their useful life. In addition, Diacon guards have UV stabilisers and guarantee a 15- year lifespan in Australian conditions, unlike any other supplier.
Refalo says Diacon was one of the first companies to design and manufacture a plastic conveyor guarding system in Australia, with a high level of user friendliness in mind.
“The system can be removed by loosening two bolts instead of removing and storing fasteners. The bolts are also captive in the guards, so they can’t be dropped or lost, a major benefit when working up high,” he says.
“The hook and hang system
User friendliness is incorporated into the design of the guards.

means it is quick and easy to remove the guards without them becoming a tripping hazard – something particularly important when removing multiple guards.
“Conveyor maintenance can often mean 10 or 12 guards need to be removed, which can be a long process when moving them down to a safe area, or an expensive one if a crane is used. Removing Diacon guards takes mere minutes as they can be stored on the nearby handrail.”
The Diacon system is made up of three components – hungry boards, mounting brackets and guards. Installation only requires three steps: attaching the mounting bracket to the troughing frame, connecting the hungry board to the bracket with the locking wedge, and hanging and locking the safety guard panel to the bracket. During onsite installation no steps require hot work, removing a key potential hazard from the process.
All of Diacon’s guards are specifically engineered to meet the requirements of AS4024.3610-2015 for general conveyors and AS4024.3611-2015 for belt conveyors for bulk materials handling. In particular, the system focuses on the suitability of material for purpose, aperture size considerations relative to reach distance, deflection criteria when the guard is under load, correct signage, and the ability to unlock through the use of a tool.
Refalo says Diacon designs and tests its guarding systems and products rigorously, using best practice manufacturing techniques and software.
“We use laser scanning equipment at a site to measure the conveyor system before designing the guarding on top of a 3D model that includes all of the potential interferences and obstacles,” he says.
“Then we can manufacturer the guards and provide a full installation that meets and exceeds Australian Standards in a full, turnkey package.”
The company continues to grow and plans to move into a new larger factory by the end of the year. The move will provide Diacon Australia with more space to design and test the guards, along with improved production capacities.
MAXXFLOW HTC FLOW MEASUREMENT FOR DRY BULK SOLIDS
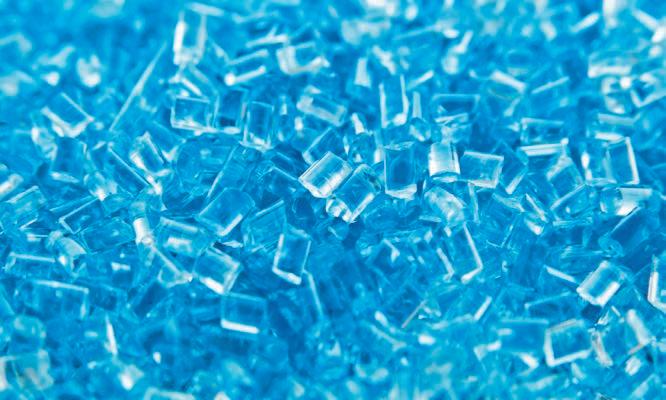

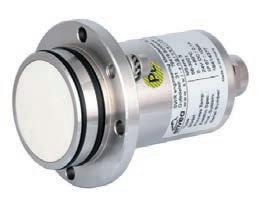
M-SENSE 3 ONLINE MOISTURE & PROCESS TEMPERATURE MEASUREMENT WITH FLOW DETECTION • • Powder Dust NEW • Granules • Bins • Feeders • Conveyers • Mixers
AIRSAFE CONTINUOUS AMBIENT AIR DUST MONITORING
• Powder • Dust • Granules • High Temperature • High Pressure • Non Contact DETECTION OF SILICA DUST
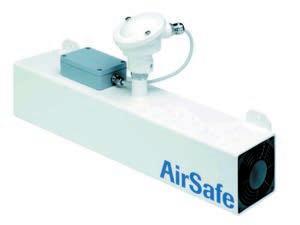