
39 minute read
Shaking things up
from ABHR OCT 2020
by Prime Group
When silos, hoppers and bins stop flowing, productivity drops along with it. Using a hammer to break up bridging may seem like a good short-term solution, but it comes with significant safety risks. Oli Vibrators however, offer an alternative fix.
A TELL-TALE SIGN THAT SOMETHING
isn’t right with a processes’ flow are hammer marks and chipped paint on a silo, bin or hopper.
Poor flow can be caused by a number of reasons, whether it is moisture ingress into the product or silo design leading to ratholing and bridging. Whatever the case may be, the flow-on effects can bring significant productivity penalties and safety hazards.
Sean Brewer, Sales Executive at Oli Vibrators, says it can be common for companies to attempt to manually restart the flow.
“Occupational health and safety hazards abound when doing this. Not only is it bad for your bones to be swinging around a large hammer constantly, but it’s also not good for your hearing, we aim to preserve the structure and person.” he says.
“On top of this, a lot of hoppers are elevated, with only small ladders leading up to them. That means you’ll have someone in a precarious position, high above the ground, swinging heavy objects. It’s a recipe for disaster.”
Dents in expensive equipment can further aggravate bad flow, as the engineered metal is bent and warped out of shape through sustained abuse.
It’s also a poor use of labour resources. Not only are employees wasting energy and time on heavy manual labour, but customers and transport workers will be waiting for the load to finish – adding to costs incurred.
Industries involved in bulk solids handling also tend to be ones that can’t afford to have their supply chains held up – concrete needs to be laid and food needs to be distributed.
Part of Brewer’s job is visiting sites that are struggling with flow issues in their vessels and finding a long term, effective solution.
“It starts with a phone call,” he says.
“We head out onto site and find out what would help improve productivity at the site in the best way possible.”
“We service pretty much any industry you can think of – our products can be found in industrial estates, farms and factories all around the country.”
Oli Vibrators specialise in industrial vibration technology, providing highquality, European-built industrial vibrators, electric vibrators, frequency converters and aerators. The company has operated in Australia for more than two decades and has built up expertise in providing the right tools for the job.
Specialists will find the right vibrator or aerator for a site, using the supplied dimensions and weights involved. Oli’s experts will collaborate with the site’s staff to find the most effective and economical product from their extensive range each to correct and maximise flow.
Brewer says the company is proficient in the knowledge of its products and how to properly apply them.
“Our staff have worked with silos and
The company stocks industrial vibrators, electric vibrators, frequency converters and aerators.
materials handling for years and we have enough case studies under our belt where we can use previous experiences to find new solutions,” he says.
Oli Vibrators’ competitive advantage, according to Brewer, is the high-quality materials and precision engineering that goes into making each of the vibrators. The company is based in Italy and imports its products from overseas where they must meet rigorous Australian and International quality assurance standards.
With agents in every state of Australia and across New Zealand, the company has managed to continue operating throughout the COVID-19 restrictions with minimal disruption. Its mission statement, ‘when you need it, where you need it’ has helped form its strategy to keep all 20 of its global trading subsidiaries well-stocked. In addition, the company’s manufacturing plants in Italy and Europe have managed to continue production without needing to pause, further bolstering the supply chain.
Using hammers to manually restart flow can lead to dents and damage.
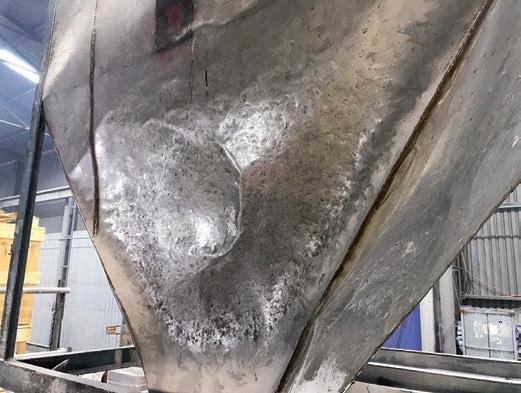
Brewer says the local branch prides itself on its stock holding, which helps set it apart from other international brands.
“A lot of our customers use imported equipment, and one of the main bugbears they have is shipping delays if something does go wrong,” he says.
“They may need to wait for a shipping container to be sent over or pay expensive fees for air freight to ensure they can continue operating. At Oli, if we need to supply a replacement, there’s a very high chance we will already have a backup on hand.”
As a result of Oli’s high standards for quality, its products often last for more than a decade. Each component is tested at the company’s manufacturing plant before it goes to the customers to ensure every installation is as reliable as possible.
Going forward, the company aims to
World Leaders in Bulk Materials Handling with over 40 years of experience in Research and Consulting
We are experienced and offer assistance in everything that is BULK SOLIDS, including:
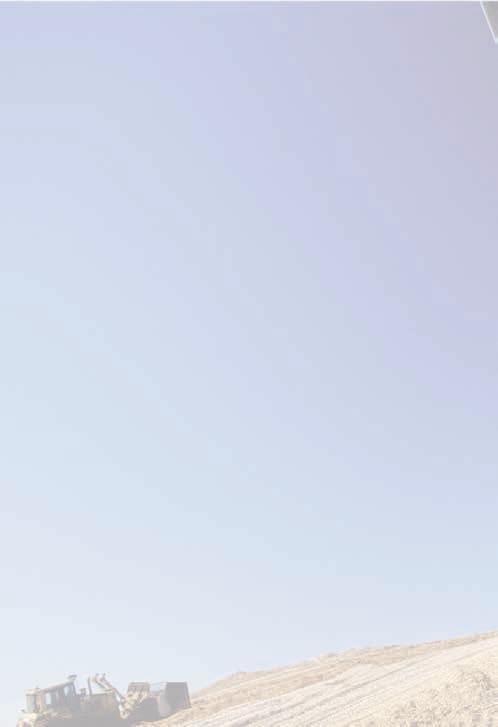
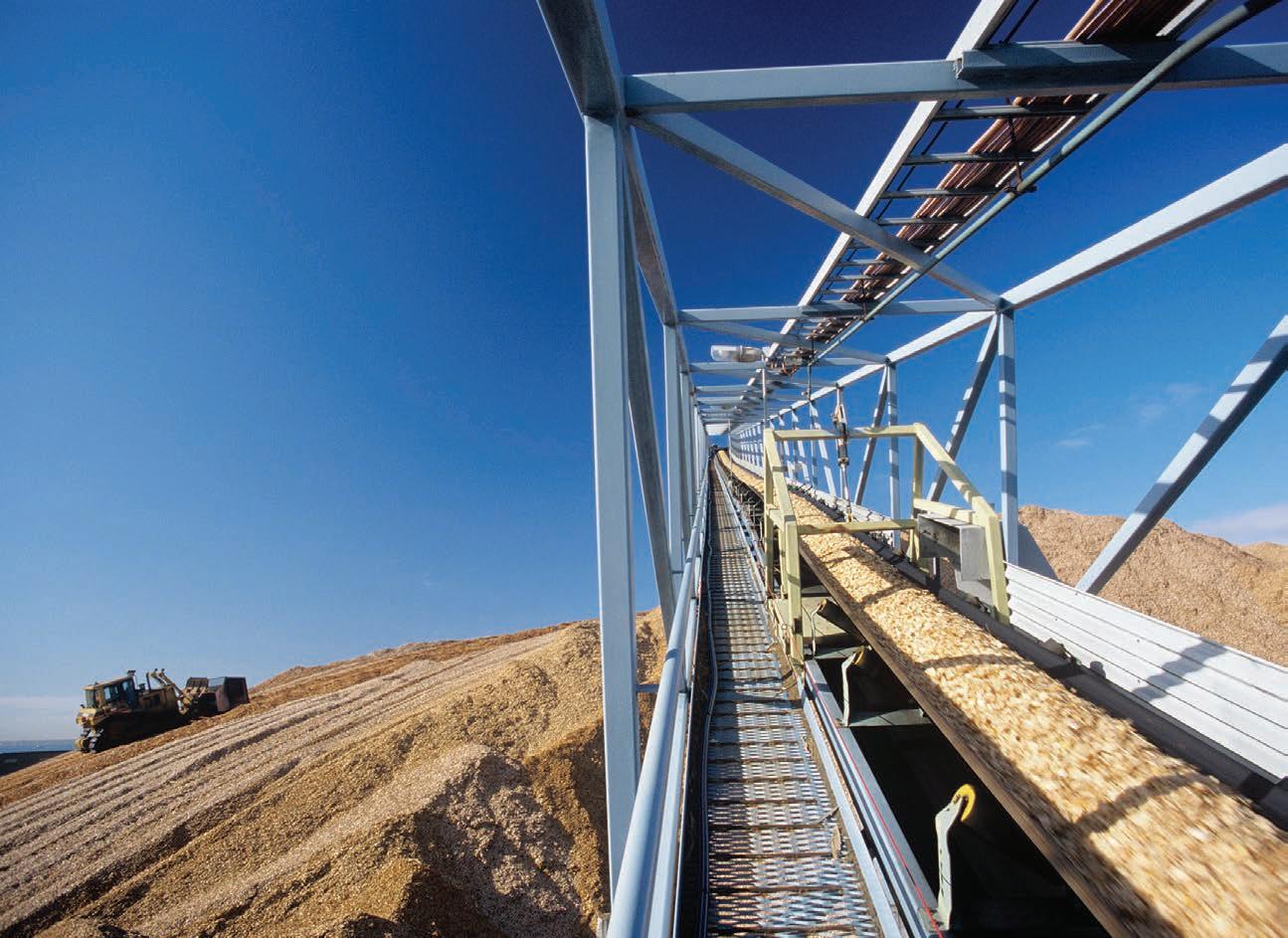
• Testing of Bulk Materials and
Bulk Materials Handling Equipment • Consulting Services for Storage, Flow and Handling • Conceptual Design of storage and
Handling Systems
Online Short Courses 2020
21-23 September – Transfer Chute Design 9-13 November – Storage, Feeding, Transfer & Belt Conveying

For more information, visit www.bulksolids.com.au or call +61 2 4033 9055
Chipped paint on a hopper can be a sign a site could benefit from a flow aid.
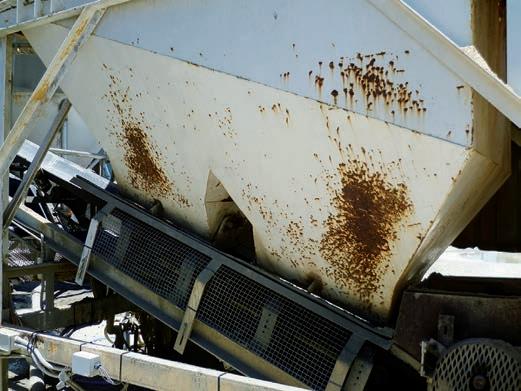
continue offering its services throughout the COVID-19 pandemic and has adopted a number of digital solutions to remain safe while providing its services.
“During these unprecedented times, and being a supplier to the essential manufacturers, producers and supply chain, Oli has remained open and will remain open,” Brewer says. “We’ve stocked up heavily and are ready to supply our products throughout the country.”
talk
STEVE DAVIS In his regular BULKtalk column, Steve Davis considers the basics of bulk handling that sites often struggle with. Steve has worked in bulk handling for 30 years, for both resource companies and professional engineering firms, in Australia, South Africa, the Middle East and Canada. His experience encompasses such commodities as iron ore, coal, potash, phosphates, petcoke, sulphur, sands and grain.
The evolution of guarding
Conveyor guard standards have evolved over time to reflect higher safety expectations. Steve Davis, Senior Bulk Handling Expert at Advisian, explains how the technology has developed and what is available now.
MY FIRST UP CLOSE INVOLVEMENT WITH
machines that could cause injury was as a machine hand at a small fabrication shop in the UK. We had every kind of pre- computer numerical control metal fabrication machine in use, and not too much thought in guarding.
I managed to survive with only a few cuts and scrapes and an allergy to cutting fluid and some regard for my own safety. Everyone else in the shop had lost at least one finger. Many had scars and disfiguration from various entanglements. These were almost badges of honour.
After graduating, I moved into an automated fabrication facility, initially using cam timers, and then early cassette-controlled programmable logic controllers (PLC). We even had a robot. Guarding was taken seriously here, and automated systems were fully enclosed with Castell interlocks to prevent any possible contact. We soon learned that the tape in a cassette stretches and confuses the PLC with consequential random machine operation. Guards were designed to surround the total locus of movement, so it would be
ESS modular guard system.
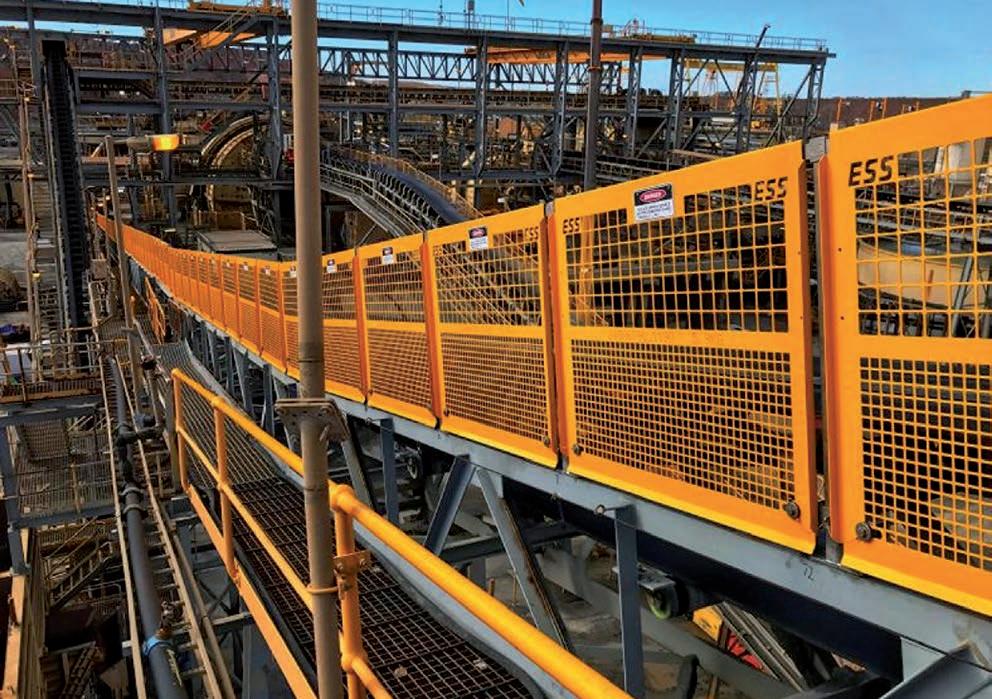
virtually impossible to get hurt. Small machines and easily managed.
In South Africa where I started my materials handling career as a maintenance engineer at a gold mine, guards were random steel and mesh barriers and a total contrast to previous experience.
Safety was an arbitrary concept and guards were poorly conceived with little thought. Many were heavy, difficult to remove, even more difficult to replace, fragile and rusty. In reality these were only a small part of a non-existent mine safety culture.
Over the years and movement into the design field, I saw guards and health, safety and environmental standards gradually improve, but not much further than identifying the region that needed guards on a design arrangement drawing for the fabricator to develop.
The outcome was predictable, random attempts to provide guards that were easy to fabricate and install and did not consider operation and maintenance. The gaps between, under and over would not come close to current Australian Standards. There was never any pushback from end users and only a vague safety culture. A recent visit to an older plant in South Africa was a stark reminder of some of the issues.
On to Australia, a few years after AS1755 was first published, and set a good standard for guarding for the first time. Sadly, it was still common to identify the areas requiring guarding on the drawings, but now the note would say “Guards to AS1755”. The assumption being that the fabricator would know what this meant, have read the Standard, and diligently applied it.
Over the last 20 years, I have seen
DIACON Australia HDPE modular guard systems.
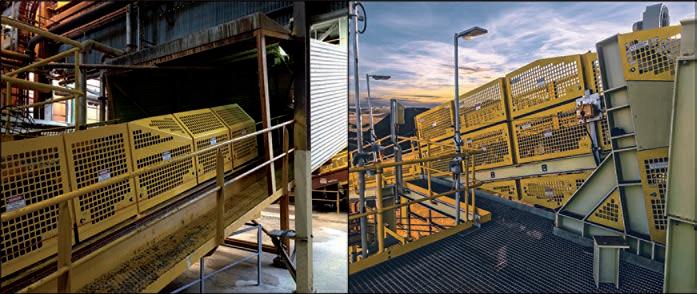
many well-meaning failures in providing guards that meet the standard. Being yellow, looking like guards and in the way of contact does not mean that they comply. I am intrigued by the lack of pushback by end users when the safety focus today is a primary concern. We are improving but not always as good as we should be.
AS1755 has improved and now is part of the AS4024 series. These are good standards, but the end results do not just happen because of a note on a drawing. Compliant guards must be designed to meet the key reasons of limiting access to moving parts, nip points and so on, and gaps and limitations are clearly defined. Guards must also resist the loads defined in the Standard.
What is not defined in the Standard are the other aspects that should be considered in design. Guards are an impediment to operation and maintenance, and many often need to be maintained frequently themselves. Guards are often an ergonomic nightmare for removal and replacement, as this aspect has not been considered in design. Guards should be designed to be easily removed and replaced using the obligatory tool, should be lightweight, should be corrosion resistant, should consider where they will be stored when removed and meet all the safety aspects. Guards that are fastened with more than two tool removable fixings are too complex.
Fortunately, the supplier industry in Australia and other countries observed the shortfall in guard performance in recent years, and we now are able to choose from well thought out, and well-defined guard systems. These guard systems comply with gap and distance, strength and are operation and maintenance friendly.
I favour Australian sourced and supported products for Australian use. ESS have an excellent modular guard system in steel or aluminium and supply other conveyor safety accessories.
There are two suppliers of modular guard systems that have taken practicality to new levels. Both DIACON Australia and DYNA Engineering supply excellent conveyor guard systems that are specifically designed for Australian conditions and to the Australian Standard.
Both guard systems use HDPE as the main guard component, and both are fully modular custom fit for application. Expected life is more than 15 years and the self-coloured guards are fully recyclable at end of life. Key issues are: • Guards are made to measure for every installation • Significantly lighter weight than steel, most are easy single operator lifts, weight is permanently marked
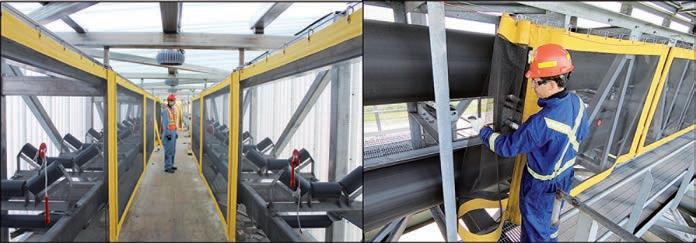
DYNA Engineering HDPE modular guard systems.
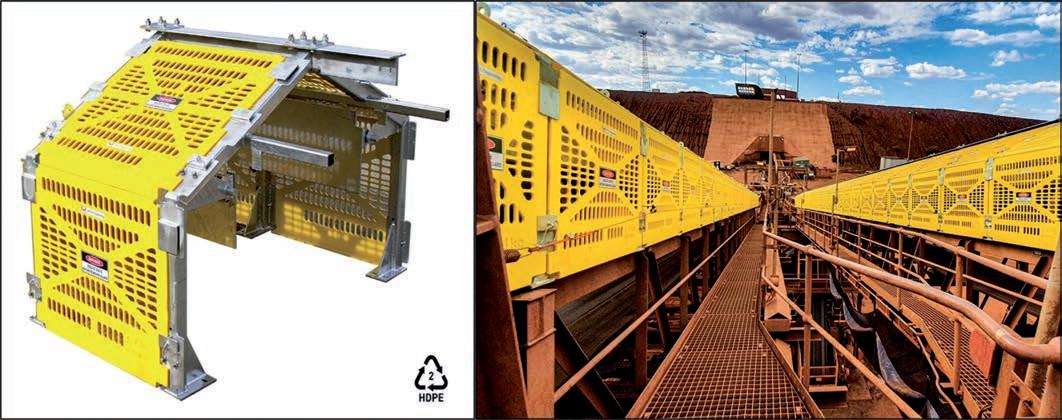
• Simple, consistent fixing methods that facilitate removal and reinstallation • No corrosion, no sharp edges, no mesh to snag • Shape is retained, so no force fits back into place • 100 per cent Australian made
There are many differences between the two systems, but both have considered the operation and maintenance aspects in detail. In my view both systems also look great when installed and should stay this way for many years.
Another guard system that has impressed me is from a Canadian company, soon to establish in Australia. Enduride supply a curtain guard system
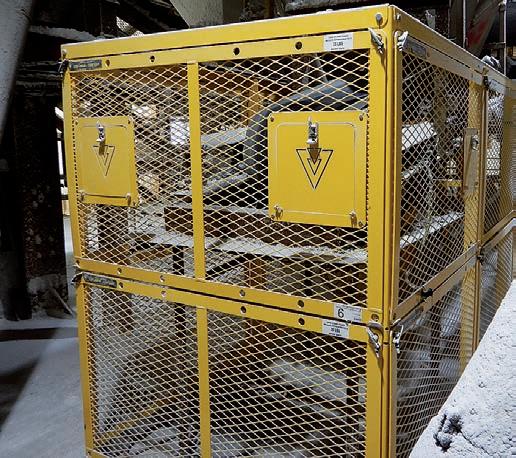
Belt conveyor guarding modular system. The system is novel in that the curtains are suspended between upper and lower steel cables and have a latch system that, when released with an Allen key, allows the curtains to slide back to provide access. Quick access, no lifting, storage in situ and easy reinstallation. Corrosion-resistant materials and they offer a completely different solution to safety.
which has application in confined spaces, and wider application elsewhere. The system complies with North American and European Standards and has been tested to meet Australian Standards.
The system is novel in that the curtains are suspended between upper and lower steel cables and have a latch system that, when released with an Allen key, allows the curtains to slide back to provide access. Quick access, no lifting, storage in situ and easy reinstallation. Corrosion-resistant materials and they offer a completely different solution to safety. There are two suppliers in the USA and one in Canada that provide well thought out modular systems for conveyor guards and for many guard and other safety accessories, being Martin Engineering, Asgco and Belt Conveyor Guarding. The systems favour metal guard systems with flat panels and modular supports. These systems are specifically suited to North American Regulations but are functionally able to meet Australian needs.
While we are discussing guards, we should not forget those other tricky components such as chute doors, guards for belt cleaner, drive components, idlers and the like, all of which are available from specialist suppliers, including those already mentioned and from others such as BendTech in Australia.
There really is no excuse for having noncompliant conveyor guarding on new installations, with several excellent choices, and I doubt there is any difference in cost over “traditional” methods. For older installations direct fit made to measure guard systems are readily available. I am certain there are similar suppliers that I am not yet aware of.
Excellent guarding makes a safer environment. Lightweight low maintenance easy to remove guards reduce hazards, reduce maintenance time, and save operating cost.
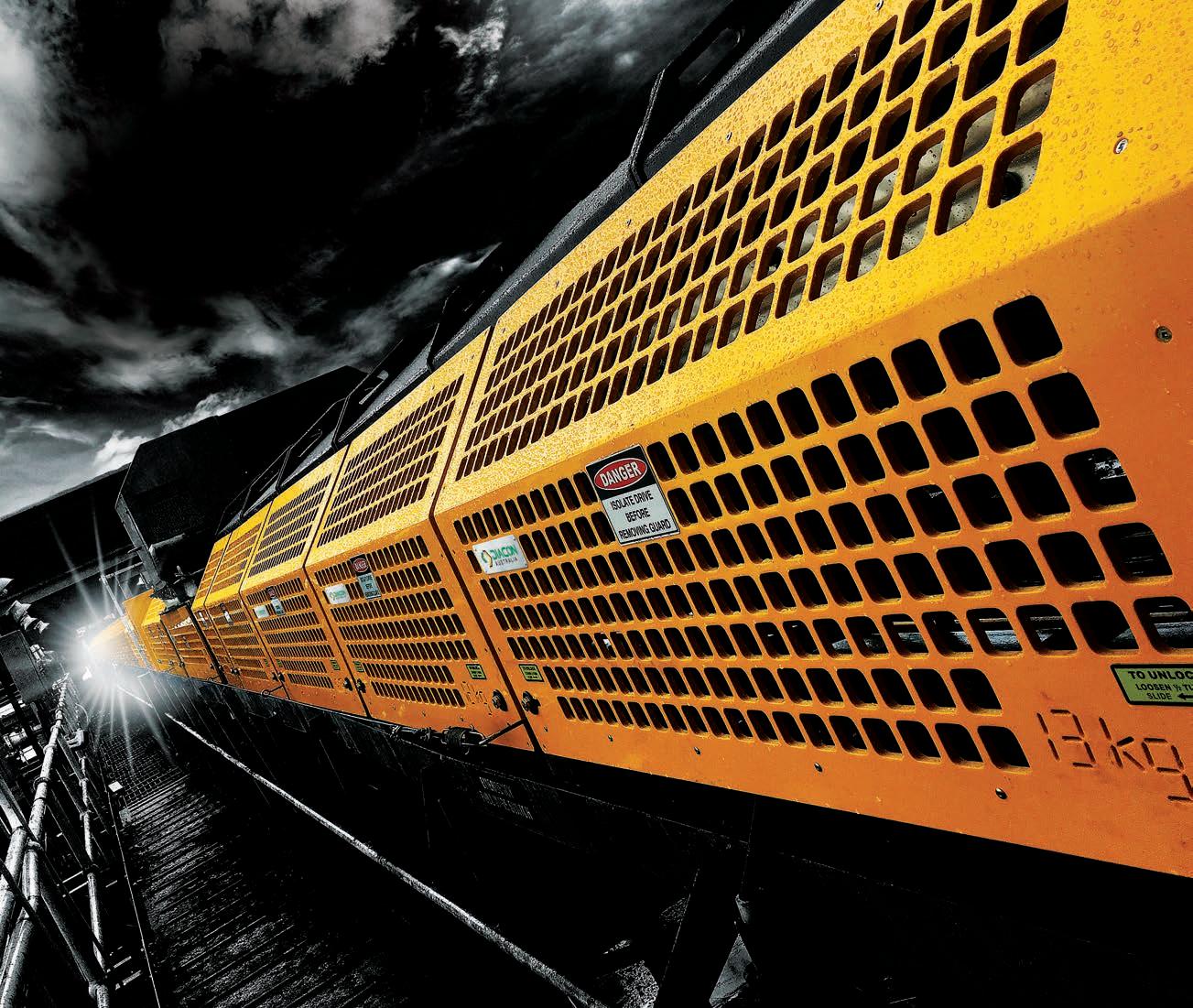
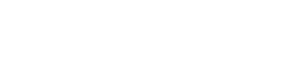
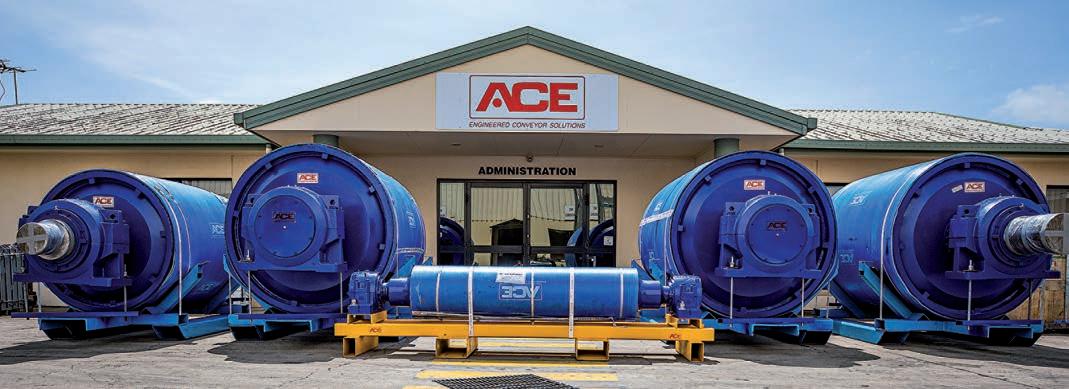
The company’s ACE team in Mackay has expanded significantly over the past seven years.
Fenner Dunlop wins head to tail overland conveyor contract
Fenner Dunlop ACE has been contracted to deliver an overland conveyor system for Anglo American’s Aquila project. ABHR speaks to Brendon Harms, Regional Manager of ACE Queensland to find out more.
THE BOWEN BASIN COALFIELDS
is home to one of the largest coal reserves in Australia, producing almost 100 per cent of Queensland’s coking coal and 60 per cent of its thermal coal.
The region is home to dozens of coal projects, including Anglo American’s Aquila – an underground hard coking coal mine near Middlemount.
As part of this project, Anglo American selected Fenner Dunlop ACE to design, supply and install the ACV002 Overland Conveyor. The conveyor measures 2.6-kilometres long and includes four drives, a transformer, loop take-up, elevated gantry sections, overland structure and belting. Included within the scope of works are the
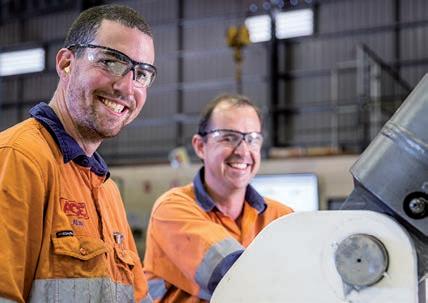
Alan Esau (workshop manager) and Dean Bazley (senior projects coordinator) mechanical and electrical installation, belt installation and commissioning.
Brendon Harms, Regional Manager of Australian Conveyor Engineering (ACE) Queensland, says the conveyor is a key piece of infrastructure for the mine, as it will be the sole source of product transportation from the underground works to the stockpile.
“Fenner Dunlop ACE will be responsible for the complete install and commissioning of the overland conveyor, providing even further responsibility and ownership for the project,” he says.
“We’re very excited to be working on this project, as we believe we have created a culture of delivering on our promises. Completing the design, supply and installation give us a great opportunity to ensure effective conveyor operation for our client.”
The overland conveyor will run from the underground to the surface and then move up to the stockpile. Often, the product will be put onto a stockpile outside the mine, but because the project will make use of an existing stockpile and wash plant, the conveyor will help connect the infrastructure together.
Included within the design are a number of custom components, such as a horizontal curve in the conveyor and an elevated stacker to load onto the stockpile.
Fenner Dunlop ACE will provide support from the beginning of the design phase to commissioning and throughout operation. Harms says this is part of the company’s head to tail approach which can significantly simplify communications and increases the accountability of a project.
“Accountability is a key part of Fenner Dunlop ACE,” he says. “We take pride in building something right the first time, every time.”
“If something does go wrong, it means that there are no arguments between multiple suppliers, we simply provide the most effective support possible to solve any problems as early as possible.”
Ongoing maintenance will be offered by teams in Mackay and Emerald, providing belt works and servicing over the life of the project. The company’s ACE team in Mackay has expanded significantly over the past seven years to ensure it can handle large projects such as this.
The Overland Conveyor project is expected to be commissioned in the second half of 2021.
Nelson Silos
Suppliers to Australian Industry Nationwide
If you need a better way to store dry bulk solids, Nelson can deliver it. Nelson are totally committed to innovative design and product development, and are now engineering silos with a proven 4-leg base design mounted on load cells. This unique Nelson design development ensures accurate weight measurement. For grain, legumes and plastic granules, Nelson 4-leg design silos are available in pre-painted steel. For flour, sugar, PVC and industrial powder, Nelson are building fully welded stainless steel silos, also with the proven 4-leg design, mounted on load cells.
With the Nelson CAD programme, we have the capacity to develop a cost-effective design package to meet the needs of the industry. We then engineer your order in our own complex - with a fixed price that will save you up to 50% of the cost of on-site construction.
And Nelson can deliver, install and commission purpose-built silos, with an absolute minimum lead time.
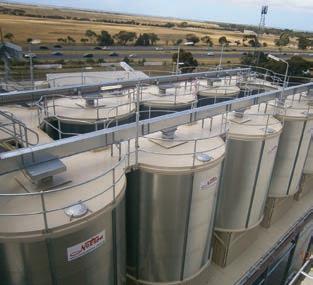
For all your bulk storage problems, please call Nelson Silos, Rochester Victoria Toll Free on: 1800 801 966
Head Office T: 03 5484 1577 F: 03 5484 1593
New South Wales Email T: 02 6862 3688
info@nelsonsilos.com.au
Website www.nelsonsilos.com.au
We have technical consultants based in Melbourne, Sydney, Brisbane and Auckland (NZ)
Australia’s largest manufacturer of transportable silos.
Vortex Global’s support to help weather the storm
Installation and maintenance support are core to how Vortex Global does business. Adam Schrage, Vortex Global’s Engineering manager for Loading Solutions, explains how it will continue offering these services throughout COVID-19.
THERE IS A CERTAIN NUMBER OF
unforeseeable factors involved in any project that involves installing new equipment, whether it is an upgrade to an existing system or a brand-new facility.
Transportation of equipment could lead to potential damage before a component reaches the site, human error could see it installed suboptimally or incorrectly, or so-called black swan events – the unknown unknowns –
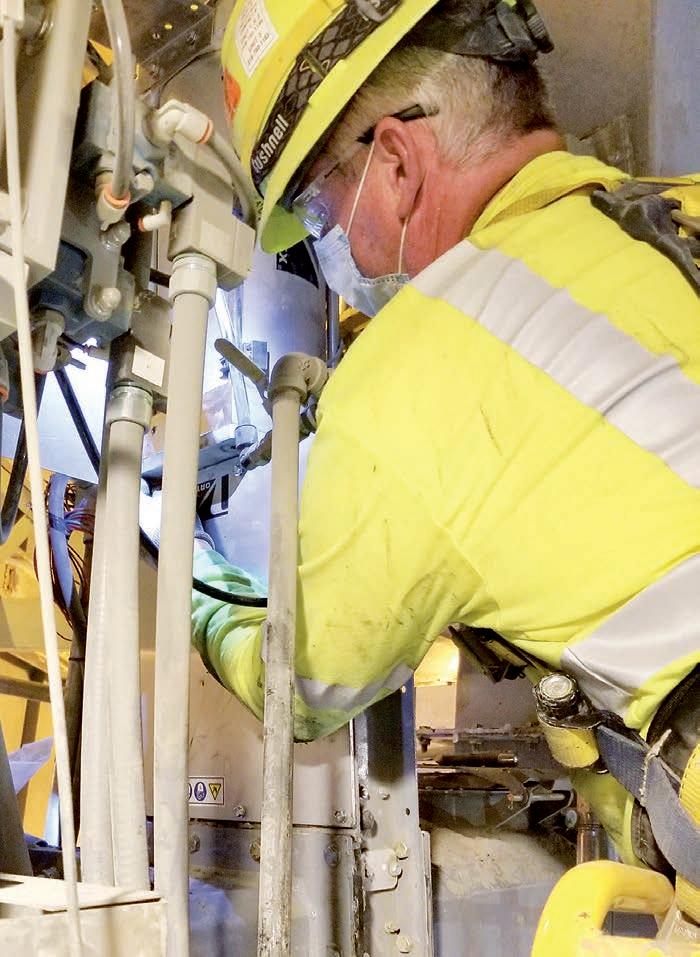
Vortex engineers are often on site during installation. could potentially see a project stall.
Often, delays are not acceptable as sites work to meet specific production deadlines. On larger plants in particular, a small delay can stall a multi-milliondollar operation.
Adam Schrage, Engineering Manager of Loading Solutions for Vortex Global, says this is why the company invests heavily in aftersales support.
“A lot of the time, depending on the project’s size, we will offer to send out one of our people to be on site during startup for a nominal fee,” he says.
“This means that if something goes wrong, we will be able to quickly identify the issue and fix it there and then. Any issues can be identified more quickly at startup than if a site visit is scheduled later on.”
One example of this process was when a new cylinder installed in an air line had some debris in it, which stopped it from opening and closing properly. Vortex engineers were quick on hand, equipped with a number of spare parts, to troubleshoot the wiring and find where the issue had occurred and fixed it immediately.
According to Schrage, this not only helps Vortex’s customers start production on time, it protects Vortex’s reputation as a provider of high-quality loading solution equipment.
Vortex Global is a manufacturer and supplier of bulk solids handling equipment. It focuses on equipment that improve solids process efficiency, ensure dust-free environments, and establish long-term reliability. This includes products such as slide gates, diverter valves, shut off and control valves, and loading solutions for ports, silos, stockpiles and more. Most Vortex products also come with a one-year
warranty period.
Based in Kansas in the United States, Vortex Global has sales representatives and offices around the world, including the Brolton Group in Australia. Schrage says that these representatives, in conjunction with Vortex’s own sales and engineering teams, allow the company to provide the best service possible as fast as possible.
“Our representatives are our eyes and ears to find out what needs to be done and how it can be fixed. They obtain the pictures and data as our first line of communication into the plant,” he says.
“If at all possible, we try to eliminate the need for service trips to help save our customers as much time and money as possible. For example, we will look at the cost of replacement parts compared to the cost of a potential overseas trip. If it makes more economic sense and is easier for the customer, we can simply send an entire replacement product instead of just the components.”
COVID-19 and the associated lockdowns and travel restrictions have affected how the company provides support for its customers. It’s much more difficult, if not impossible, for field service employees to get onto a site to help fix issues.
In response, the company has embraced remote maintenance services, using a combination of digital technology such as Zoom, Facetime and GoToMeetings, with traditional phone calls and emails to determine the root cause of a problem both visually and audibly.
“We encourage our customers to send us videos or photos of their equipment if it’s not working to their expectations. We provide step by step instructions for our customers’ maintenance teams, guiding them through how to best solve any problems should they arise,” Schrage says.
“Supporting our equipment and customers is vital for us as a business, as it helps us grow. We will be continuing to offer support to all of our customers, no matter where they are located, to ensure they get the best results.” Vortex Global’s sales engineers have more than 150 years of combined experiencing dry bulk solids. Over the past 39 years, the company has handled a number of dry bulk materials, including: • activated • copper carbon • crushed glass • aggregate • fertiliser • alumina • flour • animal feed • hot adhesive • barley pellets • bark • iron oxide • bauxite • lead • beans • milk powder • bicarbonated • nuts soda • oats • blasting • phosphate media • resin • boric acid • sugar • cake mix • vitamins • calcium • wheat • carbon • yeast • cement • zinc • coffee beans
RopeCon ® – Efficient Solutions for Bulk Material Handling
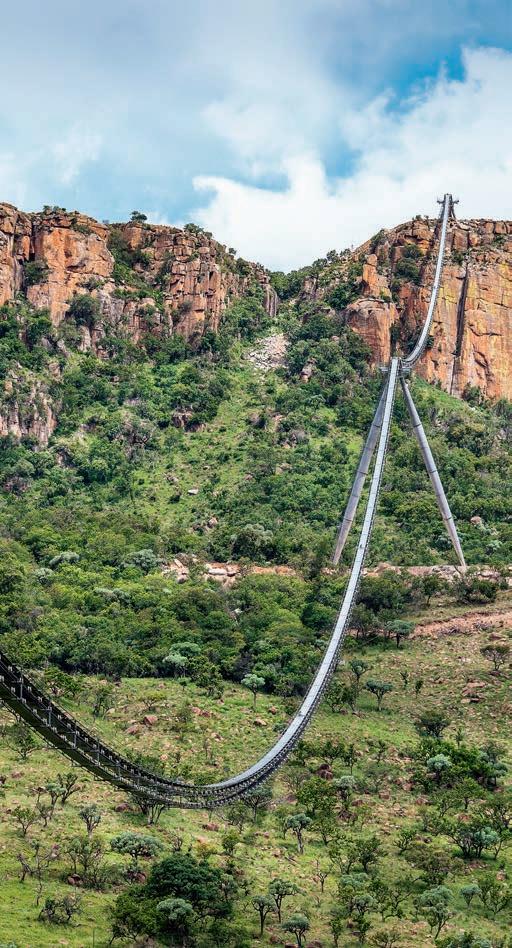
Wherever bulk material needs to go – across impassable terrain, rivers, highways and buildings – RopeCon ® delivers without a hitch!
Long distances, capacities of up to 25,000 tonnes/hour, minimal environmental footprint, quiet operation plus low operating and maintenance costs: These are the features that convinced leading mining businesses.
doppelmayr-mts.com
TS Global mergers grow product development
Australian conveyor accessory manufacturer TS Global has undergone significant expansions over the past 12 to 18 months. The company’s General Manager, Graham Holford, details how it has grown and plans for the future.
IN 2018, CONVEYOR ACCESSORY
manufacturer TS Global acquired APM Engineering.
APM Engineering is a manufacturer of custom polyurethane products that focuses on supplying its clients with customised solutions, which aligns well TS Global’s business model. In addition, APM’s manufacturing facility at Tomago delivers increased capacity to undertake the manufacture of TS Global components, making this a perfect fit for TS Global.
Graham Holford, General Manager at TS Global, says the companies have now been fully integrated into single trading entity increasing manufacturing volume and product range.
“This increase will provide our clients with an improved purchasing experience and more responsive service,” he says.
As APM was the distributor of RKM rollers in NSW, this acquisition also allowed TS Global to take on a larger responsibility with the RKM product and is now the original equipment manufacturer’s representative on the East Coast of Australia.
RKM has a reputation as a quality designer and manufacturer of conveyor
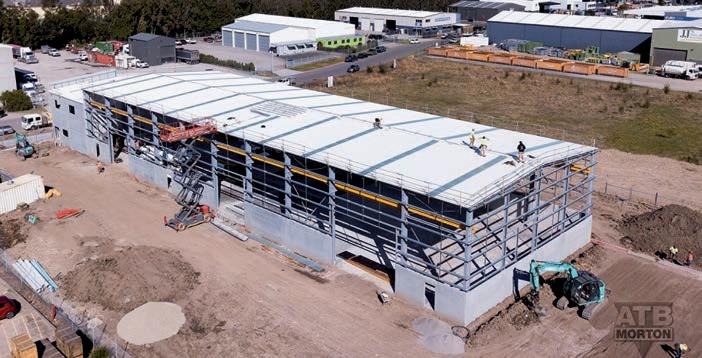
idlers and mine infrastructure. This The developments include new partnership also gives TS Global access technology which will provide real time to RKM’s advanced testing laboratory, data to service personnel and greatly in-house custom design calculation reduce risk associated with clamping or programs and third-party independent raising a belt for repairs. The technology testing for ongoing research and has now been registered globally and is development. The addition of RKM into patent pending. the TS Global business allows them TS Global is also taking this to provide the market with a more comprehensive product range. opportunity to expand and invest into conveyor pulley manufacture and pulley ProLink CMS: Systematic Condition Monitoring
In other developments, in September lifting equipment. TS Global has been 2019, TS Global was appointed as the manufacturing and maintaining pulleys Versatile, modular, and easy to interlink exclusive stockist and distributor for Tru for the last five years, however, the Trac Belt Trackers. output during this time was specialised. It
“The partnership is based on a shared focused on providing quick turnarounds desire to add value to our client’s sites in breakdowns and shutdowns, where The ProLink multi-channel condition monitoring system monitors the condition of machines and and offer expertise to ensure products the pulleys needed to be manufactured or equipment by means of vibration measurement. It is optimally suited to machine monitoring in com are installed correctly and operate to repaired in under two weeks. plex systems such as those found in the paper and cement industries. Thanks to separate sensors, maximum efficiency,” Holford says. “We’re spreading out wider to provide the ProLink condition monitoring system is ideal for use in harsh environmental conditions.
In addition to the RKM and Tru full design, manufacture and service Trac products, TS Global have been heavily involved in the development capabilities at scale,” Holford says. Looking ahead, TS Global is Product advantages of new conveyor accessories to assist investing in equipment to scale up its maintenance providers. • manufacturing process, including a new Simple initial operation thanks to the automatic monitoring
“After our bid for a Federal facility in Tomago, NSW. The facility is configuration for standard units such as motors, fans, Government innovation grant was the company’s new central headquarters and pumps accepted, we partnered with the • for the business, located next to the Configuration, trend displays, and initial analyses take place University of Newcastle to develop a existing TS Global workshop and directly on the device using the integrated web server and a new range of belt clamps and belt lifting warehouse. The new building is close to standard web browser devices,” he says. • major transport corridors and will provide A great variety of options for integration into the customer’s around 50 per cent more floorspace. infrastructure using digital interfaces (e.g. OPC/UA) and a Holford says the expansion aims to modular field bus module; this allows the highest possible level improve efficiencies, cutting down travel of transparency by providing all measured information about the times between TS Global’s sites and machines’ condition, e.g. for the customer’s own plant visualiza creates a business hub. “We were very tion, maintenance planning system, and quality assurance grateful to have found such a convenient and suitable site to allow us to come Potential applications and fields of operation together as a business,” he says. “Our • • new headquarters will help us continue to grow and develop in order to service our clients in the best possible way.” Paper industry Metal production and processing • The company plans to launch some Cement industry of their new products at the opening TS Global’s new building is close to major transport corridors and will provide ceremony of its new facility later around 50 per cent more floorspace. this year.
ProLink Multi-Channel Condition Monitoring System
The ProLink multi-channel condition monitoring system monitors the condition of machines and equipment by means of vibration measurement. It is optimally suited to machine monitoring in complex systems such as those found in the paper and cement industries. Thanks to separate sensors, the ProLink condition monitoring system is ideal for use in harsh environmental conditions.
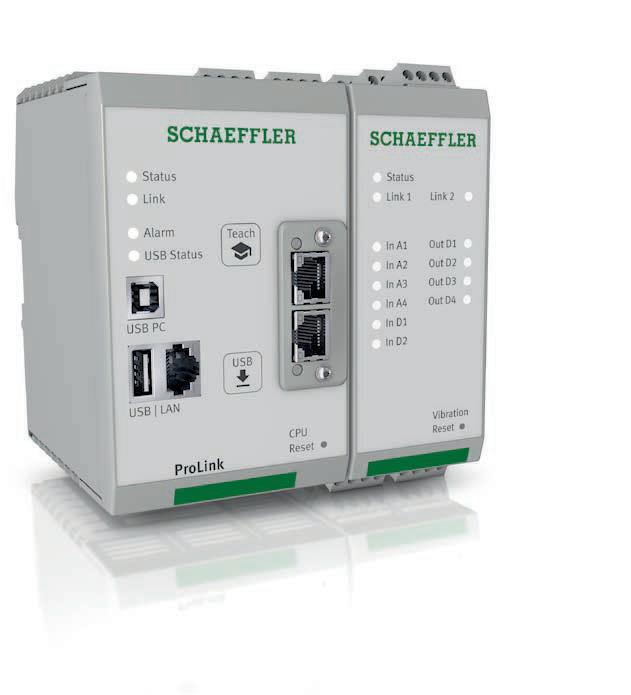
ProLink CMS: Systematic Condition Monitoring Advantages of the ProLink condition monitoring system • Templates for monitoring rolling bearings, motors, gearboxes, fans, and pumps that make further configuration easier; information about the machine geometry (such as the installed bearing type or the number of fan blades) is all that is required The ProLink multi-channel condition monitoring system monitors the condition of machines and • The learning mode allows individual adjustments to alarm thresholds in order to optimize monitoring equipment by means of vibration measurement. It is optimally suited to machine monitoring in com• Customers can optionally use the ConditionAnalyzer via the integrated cloud interface plex systems such as those found in the paper and cement industries. Thanks to separate sensors, • Added Value Through Digitalization and Digital Services the ProLink condition monitoring system is ideal for use in harsh environmental conditions. • Enhance availability and increase productivity
Paper industry
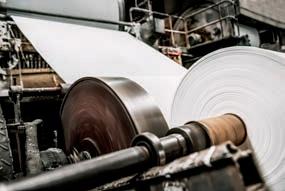
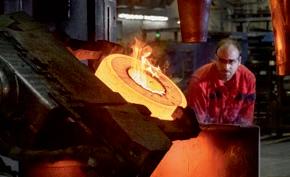
Metal production and processing Schaeffler offers a standardized hardware and software infrastructure – from components equipped with sensors through to digital services. One component is the ProLink condition monitoring system. This offers the perfect setup in combination with the ConditionAnalyzer – the automatic vibration diagnosis system.
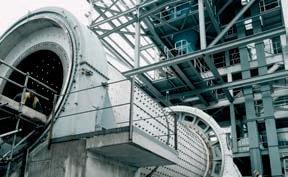
Schaeffler Technologies AG & Co. KG
Georg-Schäfer-Straße 30 97421 Schweinfurt www.schaeffler.de industrial-services@schaeffler.com
Every care has been taken to ensure the accuracy of the information in this publication. However, no liability can be assumed for any errors or omissions. We reserve the right to make technical changes. © Schaeffler Technologies AG & Co. KG Issued: 2020, July This publication or parts thereof may not be reproduced without our permission.
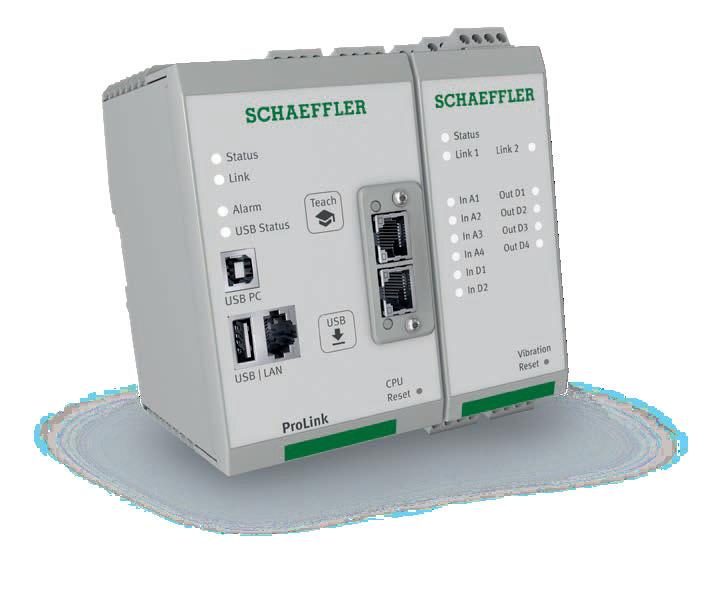
Schaeffler Australia Pty Ltd Suite 3, 13B Narabang Way Belrose NSW 2085 (02) 8977 1010 www.schaeffler.com.au sales.au@schaeffler.com
No stopping Altra Motion
ABHR speaks to Rex Sinclair, National Sales Manager for Altra Motion Australia, about the service division team maintaining Altra products across the country.
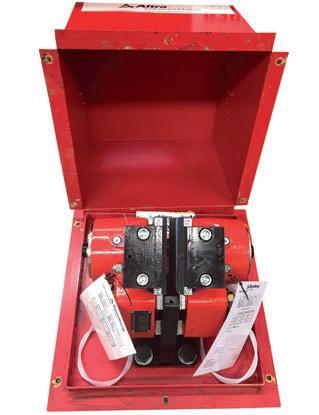
ALTRA MOTION AUSTRALIA,
the local subsidiary of global company Altra Industrial Motion, has been active in the bulk handling space for more than 85 years. It specialises in mechanical, hydraulic, electromechanical, and pneumatic power transmission and motion control components and systems.
Altra Motion Australia’s service division offers on-site and workshop
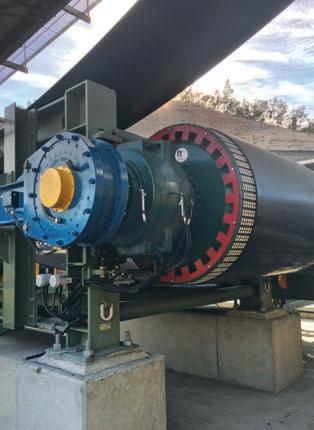
The company offers on-site and workshop capabilities across Australia.
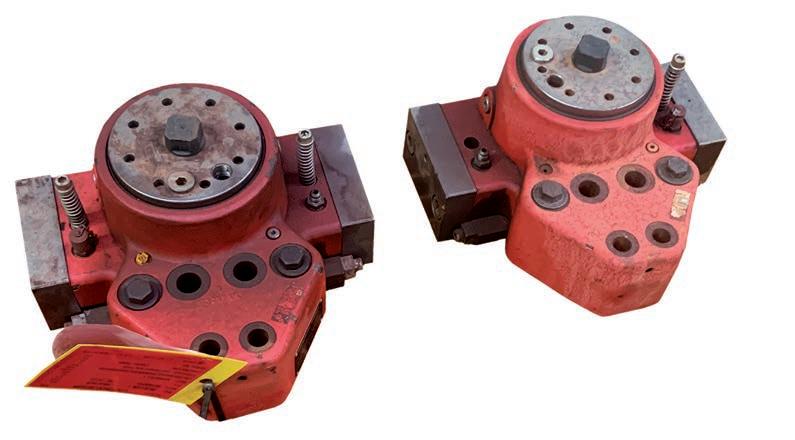
capabilities across Australia and the Oceanic region.
“Our service division maintains the products in the field that we sell,” Rex Sinclair, Altra Motion Australia’s National Sales Manager says.
“We specialise in the installation, commissioning, regular servicing, site audits, troubleshooting, and overhauling for Australia’s bulk handling industry.”
Sinclair says Altra doesn’t only sell products, it supports them from the cradle to the grave by offering regular maintenance through its service division.
“When we sell a product, we will support it for its whole life. Our customers want to know that when they buy a product, they’ll be able to depend on us,” he says.
“This leads to greater uptime, as our staff assists during scheduled shutdown periods. Keeping everything in working order avoids potential unwanted delays and downtime.”
“Our service team is factorytrained, which means we send them to various factories over the globe to see the manufacturing process in person.
Altra Motion Australia’s service division can overhaul Altra products to as new condition.
They are trained in both technical and practical programs by qualified professionals.”
In Australia, the service division works closely with various bulk handling customers to overhaul Altra products within various applications to as new condition, using original equipment manufacturer parts and offering a factory warranty on completion.
Sinclair says Altra are already recognising the benefits of having a service division through recognition from key mining customers, thanking the staff for making their lives easier.
An excellent example of Altra’s capabilities is servicing Svendborg brakes regularly on critical pieces of customer equipment to increase uptime.
COVID-19 hasn’t stopped the service team from going out to different sites, though staff has changed how they operate to ensure they align with each site’s specific safety requirements.
The company is experiencing significant growth as more of its products are used. Altra Motion Australia is building up its service division on the east coast for Australia, putting on more technicians to assist customers.
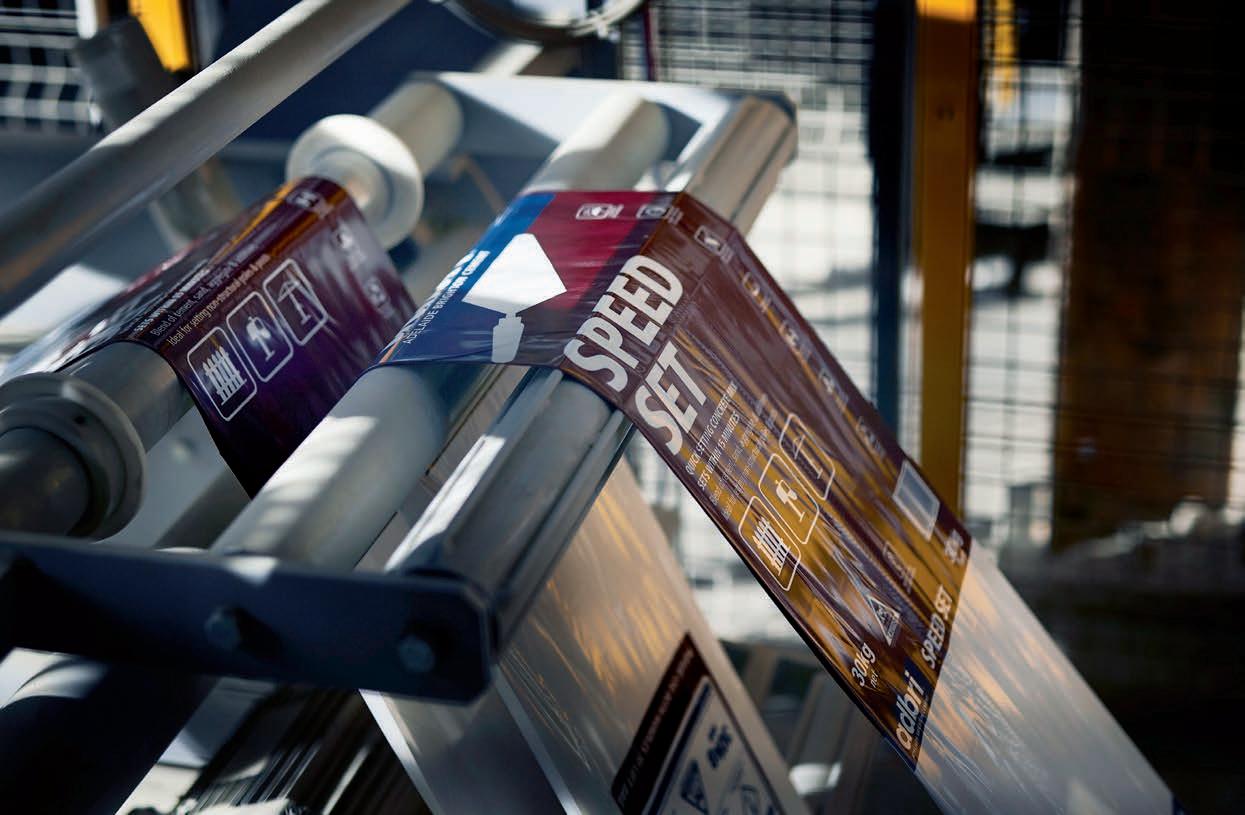
The packaging line is fully automated, improving safety and efficiency.
Concetti keeps upgrade on track through lockdown
Halfway through a major plant upgrade at Adelaide Brighton Cement (an Adbri Ltd company), Australia’s borders shut down most international travel. Tara Gracie, National Packaged Products, tells ABHR how the company kept on track.
LIKE MANY CEMENT PRODUCERS,
Adelaide Brighton Cement used valve paper bags for its preblended dry mix products. One of the issues with this type of material is that it could potentially allow water into the bag, which needs to remain dry.
The paper material also needed to be kept away from sharp objects like nails in pallets or forklift blades, which could tear and begin spilling the product.
Tara Gracie, National Packaged Products Manager at Adbri, says the company decided to introduce a new type of packaging into its product range to solve these issues, provide many added benefits to both retailers and end users and gain a competitive advantage in the market.
“Overseas and more recently in Australia, there has been a market trend for dry mix products in form filled and sealed bags, to take advantage of the benefits plastic polyethylene (PE) packaging provides” she says.
“We previously saw success and wide market uptake in Western Australia, when Adbri company, Cockburn Cement introduced the innovative packaging in 2015. Both retailers and end users have since recognised the advantages of the rain proof packaging as it provides flexible storage options, less product wastage, longer shelf life and reduced dust.”
“Stores that once might have been limited to indoor storage space can now keep the rainproof drymix products outside, which can greatly benefit their product range throughout the store. End users can also experience cost savings by less product wastage due to moisture ingress”.
In order to begin using the new packing material, Adbri needed to
To further support Australian customers, Concetti has also launched a partnership with Victorian-based company Automaint Solutions. Automaint has almost 50 years of experience in automation and technical assistance of highly mechanised systems. The companies work together to provide remote assistance managed directly by specialised Concetti technicians in Italy, and field interventions within a few hours, by Automaint engineers.
upgrade its bagging system. The company purchased two Concetti Continua Form, Fill and Seal turnkey packaging lines, each with an integrated net weighing scale and screw feeding system.
Adbri had worked with Concetti previously and was familiar with the performance and after sales support available to them. During the tender process, Concetti demonstrated a good understanding of what the company required from its new equipment. In particular, Adbri was looking to automate the machine as much as possible to remove human intervention and improve safety.
The previous plant required a significant amount of interaction with the equipment such as manually positioning valve bags, for filling onto the manual bagging machine. The process was labour intensive and meant workers were frequently close to moving parts. The Concetti packaging lines are fully automated – the mixture recipe and process parameters are set, and material is automatically fed into the machine, where it is packed and placed onto a pallet for storage and transport.
The integrated weighing system is significantly more accurate, which helps avoid overpacking and reduces product wastage.
The packing system has been configured such that it connects back securely to Concetti’s headquarters in
Italy, which Gracie says has been critical for the commissioning process during COVID-19.
The global pandemic hit just as Adbri’s old packaging line had been removed, the new installation just completed and commissioning about to commence.
“To meet market demand, we needed to continue on with the commissioning, but Concetti weren’t able to send their specialists due to locked down borders,” Gracie says.
“Instead, the company worked with us jointly through a video surveillance system. They could see what was happening and how it was performing and could tweak the system remotely if we were having issues.”
Concetti’s turnkey approach to the installation greatly simplified communications across the globe. The equipment testing in the Concetti factory is second to none with the entire line assembled and repeatedly tested with products, bags and pallets. This helps with the re-assembly on site and subsequent commissioning, made achievable with clear communication and video resources over WhatsApp.
Embracing digital communications meant the business could resume production within a tight deadline, even with the additional challenges presented by COVID-19.
Gracie says she couldn’t imagine what the process would have looked like if multiple suppliers had been involved.
“Concetti’s time-efficient assembly allowed us to build the packaging line on site much faster than if we had to wait to receive a lot of parts and information from multiple sources,” she says.
“Both teams deserve huge credit for their continued dedication to the project to complete commissioning.”
Material is automatically fed into the machine, where it is packed and placed onto a pallet for storage and transport.
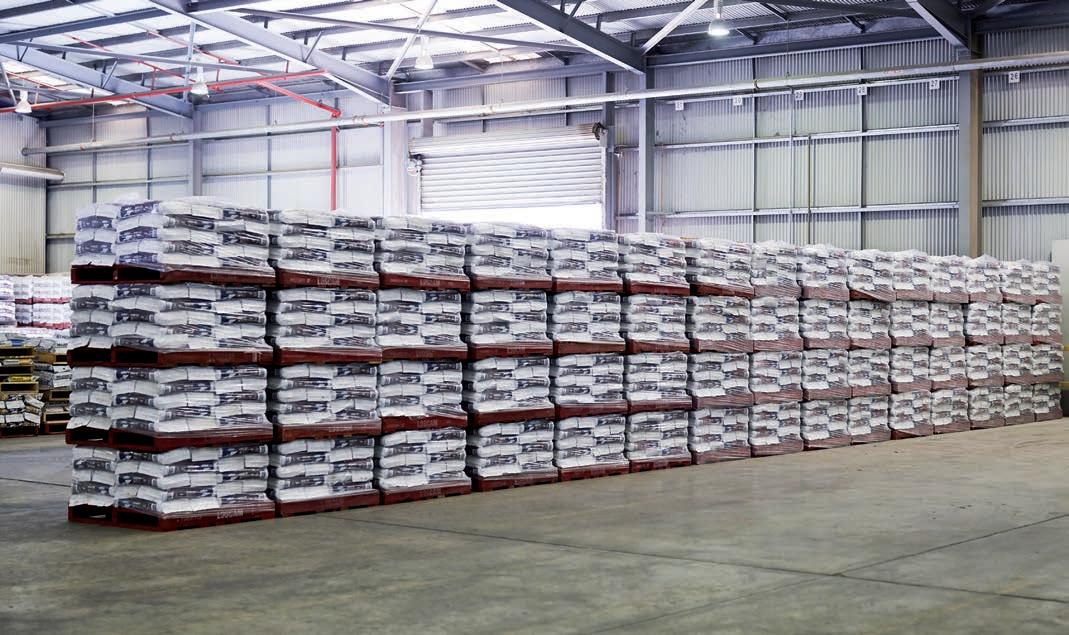
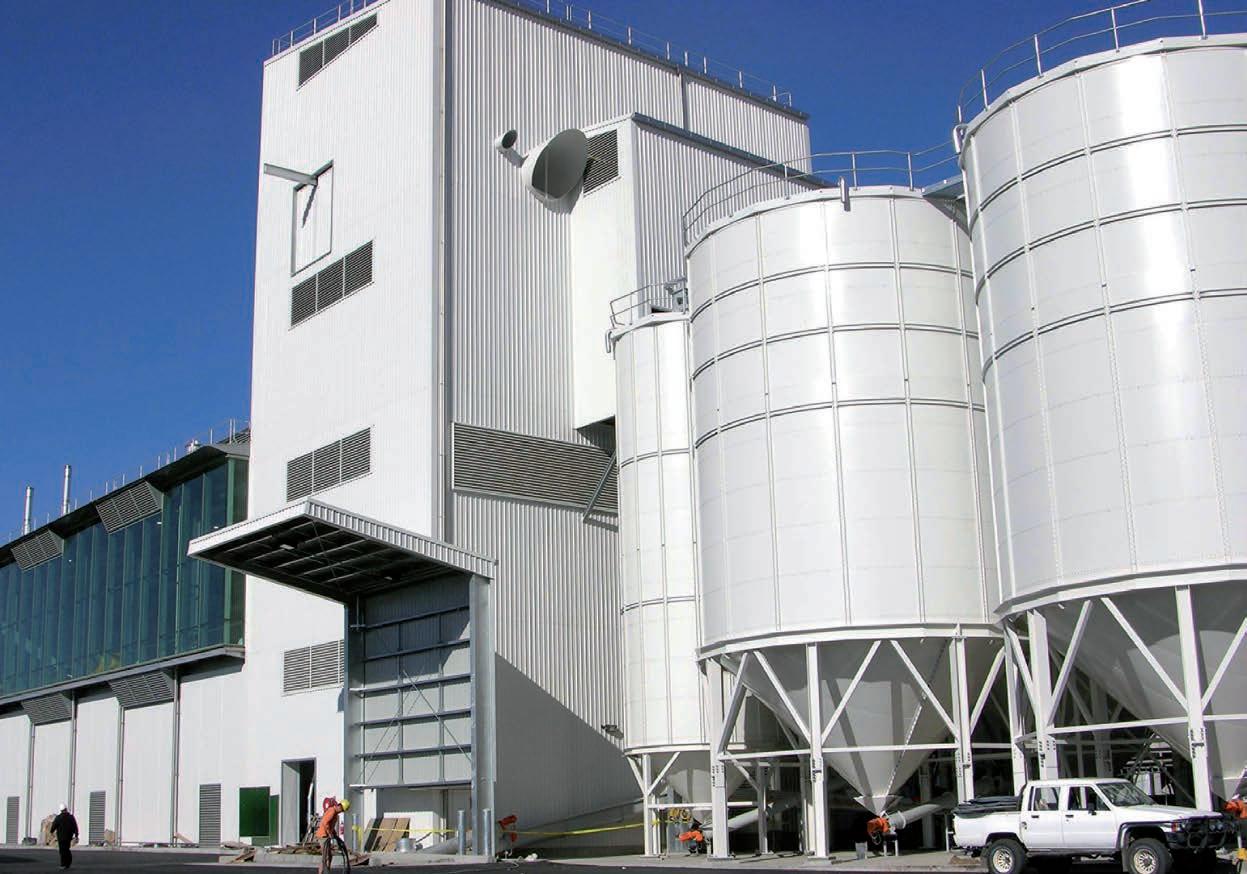
Each project Nelson Silos undertakes takes into account the different site conditions.
Evolution of a silo manufacturer
Nelson Silos has undergone a number of gradual changes to adapt to emerging market needs and provide reliable, custom products.
ERIC NELSON, DIRECTOR OF SILO
manufacturer Nelson Silos, says to build a product that is fit for purpose, it must be built to the customers’ needs from the ground up, not just adapted from existing stock.
“We start with an indicative proposal and basic drawing of what might be required and then send it through to [the customer]. After this, we will often visit the site to determine what kind of design and equipment is required,” he says.
“We use consulting engineers that have a broad knowledge of all the different industries and the various techniques and designs for silos to safely store and unload the material from the silos.”
Different conditions at sites are to be expected, and each project takes this into account. For example, the installation of a silo in a built-up urban area may require the installation team to work in a more compact area. A site’s soil test may indicate the foundations can be built with piling or may need a floating foundation over a deep concrete slab.
Infrastructure at a site is also something that must be taken into account. At industrial facilities, there is often established infrastructure that must be straddled or incorporated.
The material itself also plays a major role in the design of the silos. Nelson says the company has extensive experience in handling notoriously difficult to store materials, such as mill runs – a waste product from the flour milling process.
“Mill run bridges and seals up right across the diameter of the vessel,” he says. “To solve that, we used a combination of vibrating cones and compressed air. This design is also popular in the tea industry to create blends.”
“Many of these solutions can be found in other industries, meaning our designers can look to what has worked elsewhere to find a solution to almost any problem.”
Materials can also present safety risks for storage, particularly if a silo will be used to products like flour or ammonium nitrate. In these situations, Nelson Silos ensures the proper vents, sacrificial plates and spark-proof materials are used.
Following the design of a silo, the engineers work in conjunction with the manufacturing team at one of the company’s three production facilities. For larger silos, they are built in sections
Nelson Silos began in 1962 to help distribute one of the first transportable grain silos.
to minimise on site erection, reducing installation cost where possible.
Nelson says transport plays a large part in the business, with a number of people working full time delivering silos around Australia.
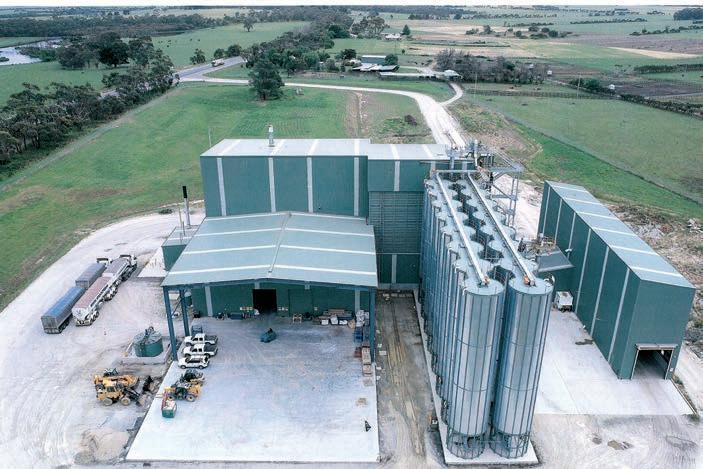
“We’ve delivered silos to Darwin, Port Headland and Kalgoorlie ourselves,” he says. “We don’t use contractors because it gives us more control over the customer experience. Our delivery team can also do the installation side
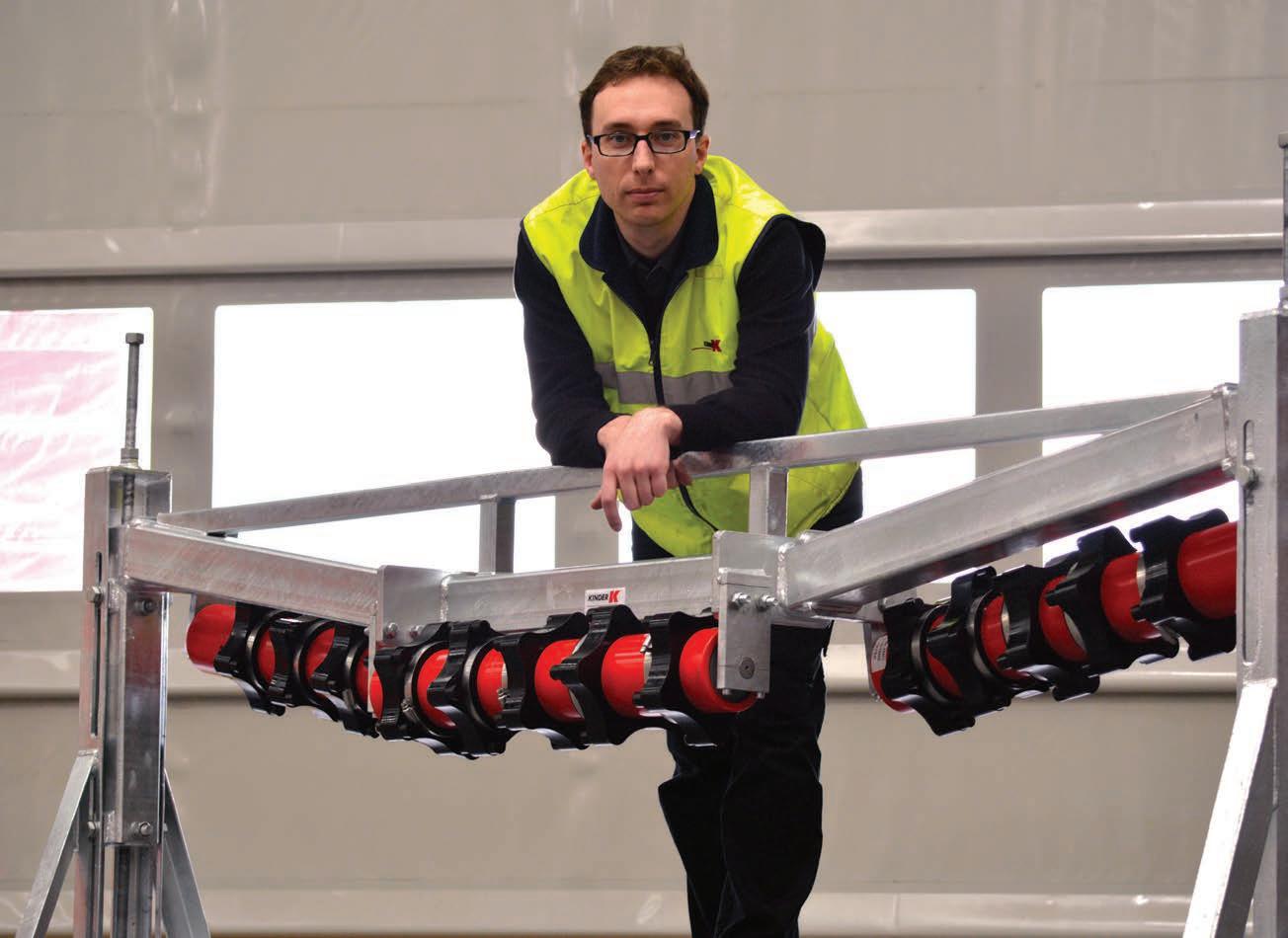
of things, with staff in the pilot cars for heavy transport vehicles able to get out and build them.”
Nelson Silos began in 1962, founded by Lindsay Nelson to distribute one of his inventions, one of the first transportable grain silos. The product proved so popular that Nelson was gradually forced to develop a multi-million-dollar engineering company to keep up with the demand.
The company has evolved significantly to provide a full range of silos capable of storing anything from grain, to plastics or chemicals for the mining industry. And while COVID-19 has limited the amount of site visits, the company has adapted by offering its services via Zoom meetings.
“Technology has also become a vital part of the monitoring and manufacturing side of things,” Nelson says.
“Our equipment is now PLC controlled and laser cut to provide the precise, reliable equipment we need.”
Resin compounder prevents blowouts with pneumatic deflection elbows
Without proper engineering, abrasive materials can cause havoc in pneumatic conveying systems. HammerTek has engineered a solution to this problem that reduces labour, downtime and material degradation.
Rhe Tech installed 140 90º deflection Smart Elbows, preventing blowouts and pellet degradation.
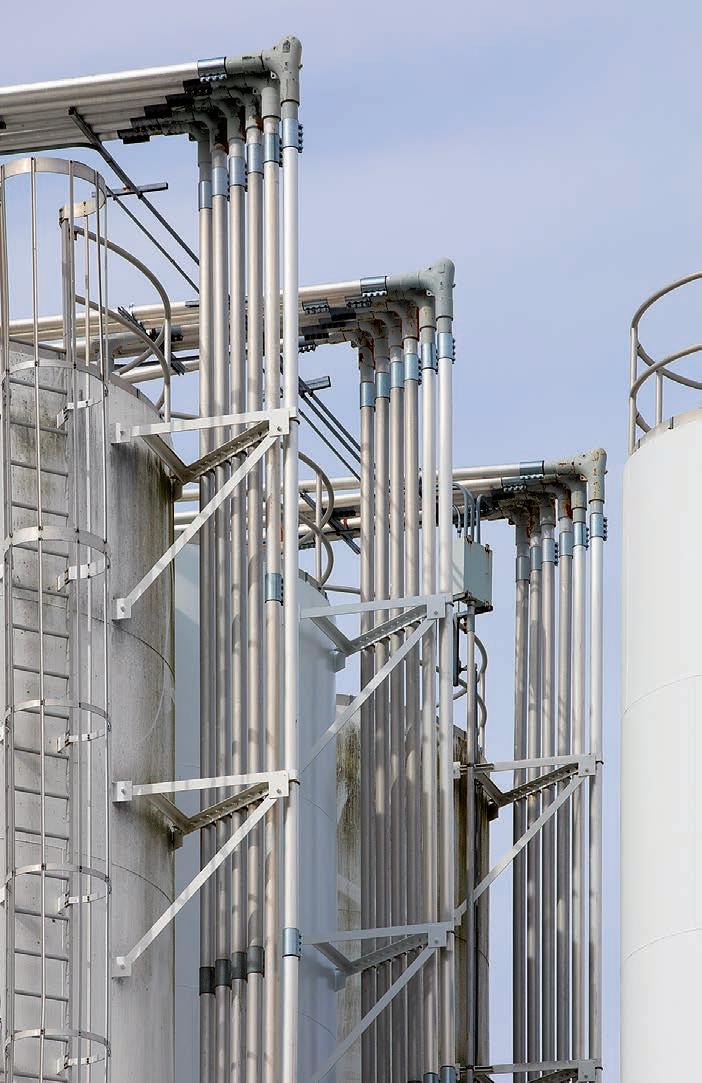
MOVING GLASS-FIBRE-REINFORCED
resin pellets through dilute-phase pneumatic conveying lines can be a challenging process. Plant engineers must not only design conveying systems that minimise pellet damage, which affects product quality, but also reduce damage to the lines themselves from the reinforced polymer.
Assuring line integrity is especially critical at bends, where material impacts elbow walls when changing direction, often causing blowouts and related downtime.
RheTech Inc., a supplier of proprietary thermoplastic polyolefin alloys and compounds, has found a way to pre-empt such damage.
The company’s production facilities at Whitmore Lake and Fowlerville in Michigan, United States, run 24 hours per day, five days a week. Its pneumatic lines, which transport pellets from extruders to storage silos to trucks, were previously blowing out conventional stainless-steel long-sweep elbows at a rate of once a month per elbow.
Steve Mosher, Maintenance Manager at the RheTech Whitmore Lake plant, says polypropylene pellets with glass reinforcement impacted sweep elbows at high speed. They wore through elbow walls as if they were sand blasted. The impact also created dust and frictional heat that caused pellets to melt as they skidded along hot elbow walls, forming streamers.
It took one hour to replace each elbow, at a cost of $169 to $212 per elbow, and $39 per hour for labour – plus interruption of production, Mosher adds.
To address these issues, RheTech began specifying 90º deflection elbows,
which prevent the pellets from impacting the elbow wall. It has since installed 140 of them at both plants, preventing blowouts and associated costs of parts, labour, downtime and pellet degradation.
Manufactured by HammerTek, the Smart Elbow design features a spherical vortex chamber protruding from the elbow. When material transitions into the elbow, part of the flow is automatically diverted into the vortex chamber, where it forms a loosely packed mass that rotates slowly in the direction of flow, gently deflecting incoming pellets around the bend.
The phenomenon prevents abrasion, degradation, frictional heat and streamers, while causing pellets to exit evenly across the elbow outflow in a laminar state, maintaining the dilutephase distribution of particles required to maximise conveying efficiency.
RheTech installed around 100 deflection elbows on 11-centimetre diameter pneumatic lines from the
Rhe Tech has only replaced six elbows since installing the original 140 units years ago.
extruders to 70 silos and truck stations at the Whitmore Lake plant. It also installed 40 elbows on 13-centimetre diameter lines running to 30 silos and truck stations in Fowlerville.
“We’ve replaced only six elbows since installing the original units years ago,” Mosher says. “We are more likely to
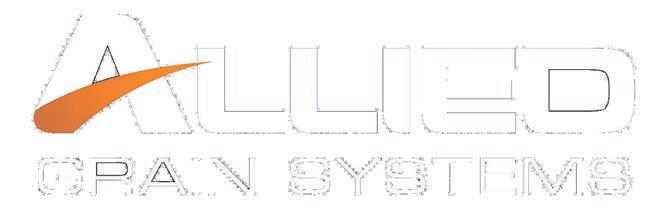
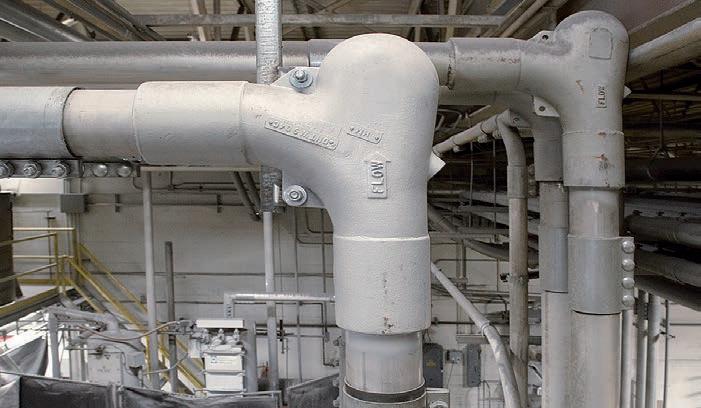
replace the straight sections of pneumatic lines than we are the HammerTek elbows. Blowouts and replacements haven’t been an issue for years.”
He adds that the elbows, along with adjustments to flow, pressure, and heat throughout the conveying system, have also eliminated streamers.
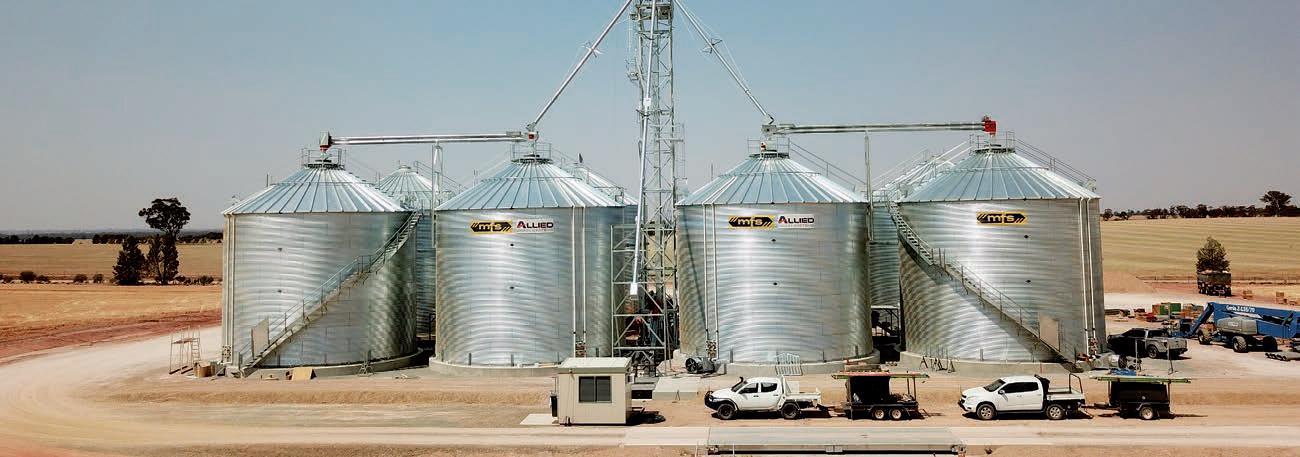