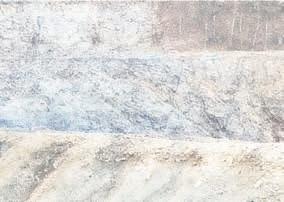
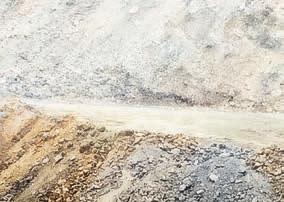


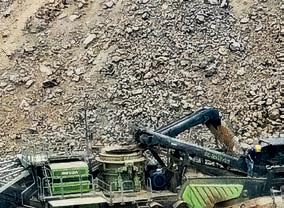
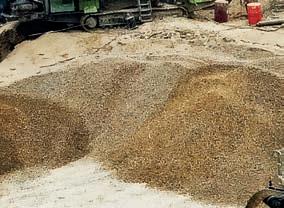
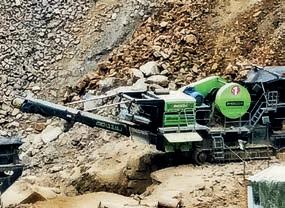
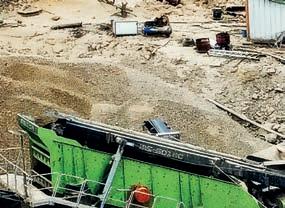
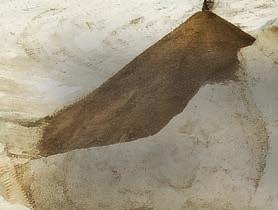
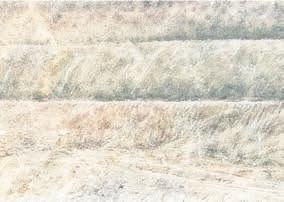
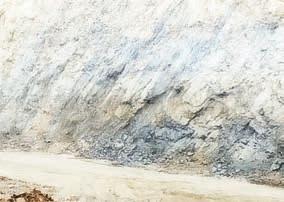
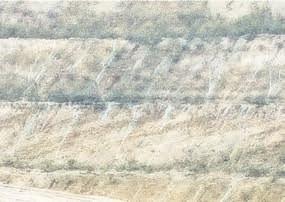
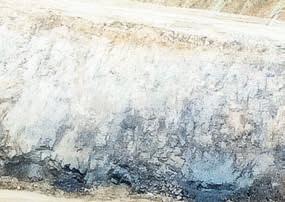
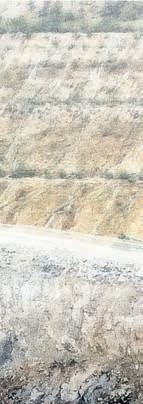

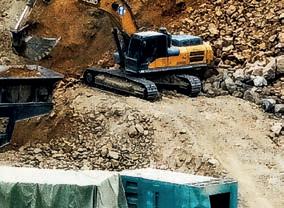
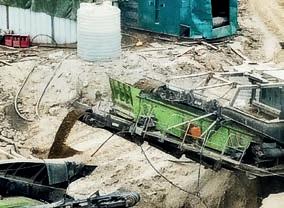


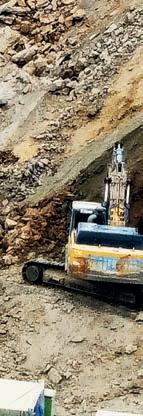
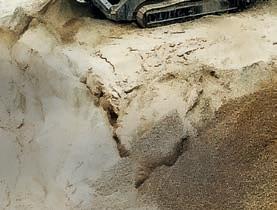
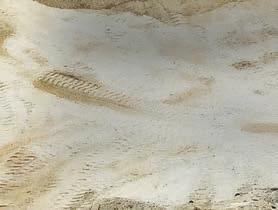

Mesda outlines ambitious plans for the European market
“Already
05 COMMENT
All eyes are on bauma CONEXPO India and the country’s buoyant infrastructure construction sector.
06 NEWS
22 LOADING
Record quarterly profitability for Holcim; AfriSam & Cashbuild form landmark partnership; China aids Volvo CE resilience.
50 EVENTS
All of the key events in the quarrying and aggregates world.
08 INTERVIEW
Antonis Antoniou Latouros: Relentlessly pursuing a long-term aggregate victory.
Liebherr, Volvo CE and Hitachi are among the original equipment manufacturers seeing their latest machinery tested out on job sites.
26 DRONES/STOCKPILE ANALYSIS
How a leading stockpile analysis technology supplier is delivering for a US quarrying customer.
28 ASTEC & TELESTACK
US quarrying and road construction giant Astec and dry bulk material handling solution specialist Telestack are poised to prosper from renewed customer demand buoyancy.
32 CRUSHING & SCREENING
Anaconda with added market bite; Coming to a European quarry near you.
38 SUSTAINABILITY
COVER STORY:
A busy quarry site equipped with a wide range of Mesda crushers and screeners.
36 CRUSHING & SCREENING
China’s biggest crushing and screening brand is keen to make its mark in Europe.
Companies and associations across the aggregate sector are taking action to boost sustainability via new research, initiatives and operational changes.
42 ENGINES – 2
An empowering Cummins response to a testing market.
46 WASHING -2
Premium washing plants scrubbing up well in Sweden and Switzerland, while a leading sector name looks to build on its healthy market share.
14 QUARRY PROFILE
Located on the doorstep of one of South Africa’s largest road infrastructure projects, KwaZulu-Natal-based AfriSam Coedmore is enjoying the best of quarrying times.
18 MARKET REPORT
Chinese aggregates production down amid big sustainability focus.
The only derived fuel from renewable sources (E-Fuel)
No odorous emissions
No CO2 emissions
Promoted by Governments
Same performance as the gas burner
Easier to get “White Certificates”
Cleaner process compared to other fuels
FOR
HEAD OFFICE
Prime Global Publishing Capitol Square 4–6 Church Street Epsom, KT 17 4NR
EDITOR
Guy Woodford +44 (0) 7879 408 069 guy.woodford@primeglobalpublishing.com
ASSISTANT EDITOR
Adam Daunt adam.daunt@primeglobalpublishing.com
SALES DIRECTOR
Philip Woodgate +44 (0) 7795 951 373 philip.woodgate@primeglobalpublishing.com
CHIEF EXECUTIVE OFFICER
John Murphy
CHIEF OPERATING OFFICER
Christine Clancy
GROUP MANAGING EDITOR
Paul Hayes
CLIENT SUCCESS MANAGER
Janine Clements +61 432 574 669 janine.clements@primeglobalpublishing.com
ART DIRECTOR
Michelle Weston
COVER IMAGE CREDITS Mesda Kleemann Aggregates Europe – UEPG AfriSam Coedmore
SUBSCRIPTIONS subscriptions@primeglobalpublishing.com
No part of this publication may be reproduced in any form whatsoever without the express written permission of the publisher. Contributors are encouraged to express their personal and professional opinions in this publication, and accordingly views expressed herein are not necessarily the views of Prime Global Publishing. From time to time statements and claims are made by the manufacturers and their representatives in respect of their products and services. Whilst reasonable steps are taken to check their accuracy at the time of going to press, the publisher cannot be held liable for their validity and accuracy.
PUBLISHED BY
Prime Global Publishing
AGGREGATES BUSINESS USPS: is published six times a yea.
PRINT: ISSN 2051-5766
ONLINE: ISSN 2057-3405
PRINTED BY: Warners (Midlands) PLC
his issue went to press just before the start of bauma CONEXPO INDIA, the 7th international trade fair for construction machinery, building material machines, mining machines and construction vehicles, taking place at the India Expo Centre in Greater Noida, near Delhi, 7–11 December 2024.The last staging of the event, in January 2023, attracted over 600 exhibitors from 26 countries and more than 41,000 participants from 83 countries. Similar numbers were expected at this year’s off-highway machinery showpiece, which covers an impressive 135,000m² of exhibition space.
Global off-highway equipment machinery big hitters showcasing their new and latest products for Indian customers were set to include Caterpillar, JCB, Volvo Construction Equipment, Sandvik, Ammann, Terex, and LiuGong. They were to be joined by Indian manufacturing majors such as Tata Hitachi, HG Infra, and Dinesh Chandra R. Agrawal Infracon.
The buoyancy of India’s infrastructure construction sector is no short-term phenomenon. An eye-catching 21% rise in sales (to 83,912 units) in 2023, reported by leading business market intelligence consultancy Off-Highway Research, took demand to 4% above the previous record sales in 2018. Many industry insiders report continued market vibrancy in 2024, with 2025 set to be another strong year, fuelling demand for equipment.
The Indian construction equipment market is forecast to be worth $7.3 billion in 2024 and $10.9 billion by 2029, growing at a compound annual growth rate of 8.3% in the forecast period (2024–29), according to Mordor Intelligence, another market intelligence company.
“Improvement in road construction infrastructure, increasing urbanisation rate, and higher investment to boost infrastructure activities serve as the major determinants for the growth of construction equipment in India,” Mordor Intelligence stated in its latest India market report. “With better road transportation infrastructure and a rise in urban population, there exists a greater demand for convenience
in personal mobility, healthcare, sanitation, and water supply, among others, which in turn contributes to the boosting demand for construction equipment, attributed to the growth in the construction sector across India.”
Given close ties between construction and quarrying, Mordor’s perspective will hearten quarry machinery manufacturers and customers. Further encouragement is offered in GlobalData’s latest Indian construction market report, published in September 2024, which highlights major infrastructure projects green-lighted this year. They include Indian multinational conglomerate Adani Group’s March 2024 announcement that it plans to develop multiple projects in Madhya Pradesh, including the construction of the Mahan Energen Plant and the Mahakaal Expressway by 2030.
GlobalData notes that in early July 2024, the Indian government also approved the construction of a four-lane road from Silchar to Umiam via East Jaintia Hills district to improve road connectivity between Assam, Meghalaya, Mizoram and Tripura.
India’s aggregate production suffered a decline in 2020 during the COVID-19 pandemic; however, it bounced back with an estimated 6.6 billion tonnes produced in 2023, according to an estimate by the Global Aggregates Information Network (GAIN) based on member data.
Quoting GAIN data is a tting segue into highlighting this issue’s big industry executive interview. Aggregates Europe – UEPG president Antonis Latouros was in Córdoba, Argentina, in October for GAIN’s 7th Annual Conference. He was appointed its vice president, having made history in June this year when he became the rst Aggregates Europe – UEPG president to be elected for a second three-year term.
Latouros spoke to Aggregates Business about his second-term agenda. Given his now global platform and Europe’s often leading role in conveying aggregate industry best practice, Latouros’ candid and thought-provoking commentary should greatly interest this publication’s knowledgeable readership. GW guy.woodford@primeglobalpublishing.com
The records continue for Holcim, with a new profitability high in Q3 2024.
The world’s biggest building materials group posted record recurring EBIT (earnings before interest and taxes) of CHF1647 million (€1760m) in the third quarter, with a margin of 23.5% (+170 bps). Q3 2024 net sales stood at CHF7120m (€7609m), up 0.5% in local currency.
The company’s nine-month net sales of CHF19,933m (€21,303m) were up +1.2% in local currency. The recurring EBIT for the period was CHF3884m (€4151m), up 11.1% in local currency.
The quarter also saw the accelerated expansion of ECOCycle, with a 23% increase in recycled construction demolition materials sales.
“Across all our markets, our teams advanced our sustainable building solutions from ECOPact and ECOPlanet to Elevate, meeting our customers’ most ambitious needs,” Holcim CEO Miljan Gutovic said. “Our Q3 results confirm Holcim’s strong earnings profile, with broad-based growth drivers delivering record recurring EBIT and a record margin. Our disciplined M&A execution has continued with six value-accretive acquisitions to expand Solutions and Products, strengthen our footprint in Europe and grow in attractive Latin American markets.
“With our track record of creating superior value across all market conditions and economic cycles, our resilient business model positions us to deliver another year of record results, executing on our strategic priorities.”
After completing the full acquisition of US-based ASI Mining earlier this year, Epiroc announced that it would no longer market its surface autonomous business under the ASI Mining name but solely under the Epiroc brand.
A major manufacturer of drill rigs and hydraulic breakers for the global quarrying, mining and construction industries, Epiroc said the transition underscores its commitment to delivering advanced surface automation solutions, focusing on accelerating integration and advancing functionality development.
As part of this rebranding, the ASI Mining autonomous mining solution, Mobius, has been renamed LinkOA. LinkOA (open autonomy) is an advanced integration platform revolutionising mining operations by offering claimed unmatched exibility, scalability and safety.
As an OEM-agnostic solution, LinkOA empowers mining operations to integrate eets
of various makes and models seamlessly, ensuring interoperability across all mining systems.
Under Epiroc’s leadership, LinkOA will now be expanded to support a broader range of surface mining applications. Its agship products include the Autonomous Haulage System (LinkOA for Haulage) and autonomous drills (LinkOA for Drills).
LinkOA for Drills improves decision-making and operational safety by integrating drills into a eet-wide autonomy ecosystem,
allowing for real-time data sharing and optimised performance.
LinkOA for Haulage coordinates and controls mixed eets of autonomous haul trucks, increasing safety, reducing downtime, and improving productivity through scalable automation.
LinkOA for Blasting enhances safety and ef ciency with teleoperated, semiautonomous and fully autonomous blast operations, reducing personnel exposure in hazardous environments.
price enquiry (at cashbuild.co.za/ shop). Once the enquiry is received, customers will promptly receive a quote tailored to their speci c application and site location. Finally, customers can securely make their payment online and enjoy the convenience of hassle-free delivery to their construction site.
AfriSam has collaborated with Cashbuild, one of South Africa's largest building material retailers, to offer Cashbuild customers online ordering of AfriSam Readymix concrete.
This is a rst in South Africa and the wider African continent. It aims to provide Cashbuild customers in Gauteng and selected parts of
Mpumalanga with a seamless and ef cient online experience in procuring high-quality concrete for their construction projects.
With this new digital offering, an end consumer can conveniently order AfriSam Readymix concrete online through a simple threestep process. First, customers are encouraged to submit their Readymix
This online offering comes at a time when the construction industry is increasingly embracing digital solutions to enhance ef ciency and productivity. By offering online ordering of AfriSam Readymix concrete, Cashbuild and AfriSam are meeting the evolving needs of their customers and ensuring that they have access to the highest quality construction materials.
Cashbuild customers in Gauteng and selected parts of Mpumalanga can now take advantage of this new online ordering service to streamline their construction projects and ensure timely delivery of high-quality AfriSam Readymix concrete.
Despite a sales drop globally, growth in Volvo Construction Equipment’s (Volvo CE) China market business, fuelled by government policies to stimulate the real estate market, and in South America enabled the construction and quarrying equipment major to showcase its resilience in Q3.
Despite lower volumes in Europe and North America for Q3 compared to the very high levels of last year, Volvo CE said its positive China and South America trading and maintenance of good margins allowed the company to continue what its head Melker Jernberg described as its “steadfast commitment to the industry transformation”.
In Q3 2024, Volvo CE net sales decreased by 23% to SEK18.809
billion (€1.647b), compared to the high earnings of SEK24.296b (€2.127b) for the same quarter last year. When adjusted for currency movements, net sales decreased by 20%, of which net sales of machines fell by 24%. Service sales increased by 2%, reflecting the market’s growing interest in digital solutions.
More positively, Volvo CE's net order intake rose slightly, largely due to a 59% increase in South
America and a 44% increase in Europe, strengthened by a more modest rise in all other regions, except North America. Global deliveries were down from last year due to continued lower market demand and reduced inventories at the dealerships in Europe and North America, partly o set by increased deliveries for the SDLG brand in China.
“We live in turbulent times and, like other companies, are feeling the e ects of a market slowdown,” Jernberg said.
“But we maintain our leading position with a strong portfolio, the continued rollout of new products and services and our steadfast commitment to the industry transformation.
“The ambitions we have set out towards building the world we want to live in remain unchanged, and we take pride in working together to balance today's priorities with our confident vision for tomorrow.”
AMetso LT300HP mobile cone crusher, owned and operated by Danoher Group, a leading mining contractor in southern Africa, has clocked more than 30,000 hours, with more to come.
Acquired in 2012, the Metso LT300HP mobile cone crusher is currently deployed at a job in Mbombela, Mpumalanga, where Danoher Group is contracted to produce 350,000 tonnes of road stone for the rehabilitation and upkeep of the N4 Toll Concession.
The machine was previously deployed on some agship projects in South Africa and Botswana. In the past 12 years, it has been in Botswana
on four occasions, where it executed some major projects at agship mines such as Debswana’s Orapa Diamond Mine and Khoemacau, a long-life copper-silver mine located in the Kalahari Copper Belt. In addition, it has been deployed at Danoher’s own Kgale Quarry in Gaborone.
With just over 30,000 hours on the clock, the machine is one of the several Pilot Crushtec-supplied Metso units in Danoher’s crushing and screening eet with a long lifespan. CEO Scott Danoher said the company has neither retired nor scrapped a single unit in the past 15 years, shining the spotlight on its drive to achieve extended operational
CRH has confirmed its appointment of an interim chief financial o cer who will take over from Jim Mintern in 2025.
Alan Connolly has been appointed as the interim chief financial o cer from January 1 2025. Connolly will take over from Jim Mintern, who will step up as the chief executive o cer of CRH from 2025.
Connolly’s appointment comes as CRH continues its process to find a permanent successor to Mintern in the key position. The company confirmed it had engaged an independent recruitment consultant and is considering internal and external candidates for the role.
“Alan brings extensive and relevant expertise to the interim chief financial o cer role and is deeply familiar with CRH’s business and financials,” Mintern said.
lifecycles out of its capital assets and a testament to the quality of the Metso products.
Danoher Group values several factors when investing in capital equipment, such as standardisation and relationships with suppliers. However, equipment longevity is one of the principal factors that informs the company’s buying decisions. While various elements in uence longevity, Danoher stressed that the fundamental ‘raw material’ is the design of the machine, which is why the company trusts Metso for its comminution equipment needs.
“We do not necessarily buy a crusher or a screen, for example, for whatever amount; we buy the number of hours that the machine gives us,” Danoher said. “For us, it is also not about the price tag but more about the cost per tonne or hour – ‘cradle to grave’, which is a totally different approach. We are prepared to pay a premium upfront in exchange for, say, 30,000 trouble-free hours out of our crushing equipment.”
“As our director of strategic finance, Alan and I have worked closely together on key finance initiatives, and I look forward to continuing to partner with him to execute on our strategy and drive value for our shareholders.
“We are grateful that he is stepping into this interim role while we conduct a search to identify a permanent chief financial o cer.”
Connolly is a chartered accountant with more than three decades of experience. He has held several senior finance roles across the CRH’s European and Americas businesses.
During his time with the company, Connolly served as director of strategic finance, finance and performance director of Europe materials, chief financial o cer of global building products, and director of group finance.
Antonis Antoniou Latouros made history in June 2024 when he became the first Aggregates Europe – UEPG president to be elected for a second three-year term.
Antonis Latouros is used to getting results. A highly successful Cypriot aggregates and waste recycling sector entrepreneur, he is keen to achieve as much as possible after his groundbreaking re-election as Aggregates Europe – UEPG president.
Latouros sat down with Aggregates Business to discuss his rst term at the in uential Brussels-based aggregates industry association, as well as his ambitious second-term agenda
In the immediate term, he urgently wants to see an amendment to the Critical Raw Materials Act or a new Essential Raw Materials Act that prioritises approving new quarry licences and extending existing licences to enable quarrying rms to access more of their mineral reserves.
“The issue of insuf cient new quarry approvals and the challenges in extending existing quarry permits is a pressing concern for the aggregates industry in Europe,” he said. “We are actively addressing this through our collaboration with academic institutions, notably the comprehensive study we’ve commissioned at the University of Leoben in Austria.
“This study aims to identify gaps and problems in the permitting processes across various EU member states and proposes actionable solutions.
“One key nding emphasises the need for streamlined permitting procedures. We’ve recognised that lengthy and complex approval processes hinder the ability to meet the growing demand for aggregates, especially in light of increasing infrastructure needs tied to the Green Deal and other initiatives.
“Establishing a ‘one-stop shop’ for permitting can signi cantly reduce the time and complexity of securing approvals. Some countries have already implemented such systems, reducing permitting times and enhancing ef ciency.”
If these issues remain unaddressed, Latouros said, it could result in a scenario where the supply of aggregates cannot keep pace with demand, leading to potential shortages and increased prices.
“In the medium-to-long term, this could sti e economic growth and hinder the progress of essential infrastructure projects across Europe,” he said.
“Therefore, it is crucial that we advocate for legislative reforms through an amended Critical Raw Materials Act or new Essential Raw Materials Act and improved collaboration among regulatory authorities to ensure that our industry can sustainably meet future demands.”
Aggregates Europe – UEPG has represented the European aggregates industry in Brussels since 1987, with members in 25 countries. It is by far the largest non-energy extractive industry, covering a demand of three billion tonnes of aggregates per year. It is produced on 26,000 sites by 15,000 companies, mostly small and medium
enterprises (SMEs), and employs 187,000 people across Europe.
The Aggregates Europe – UEPG general secretariat conducts public affairs activities. It promotes the interests of its members at national and European levels in economic, technical, health and safety and environmental policies.
The association coordinates the EU network and proactively identi es EU initiatives and policies likely to impact European aggregates producers, keeping members updated on relevant policy developments and ensuring EU decisionmakers consider Aggregates Europe – UEPG positions. The organisation currently has 16 associations as full members, four associate association members, two associate company members, and four af liated members.
“One of the biggest challenges we faced during my rst term was expanding our membership,” Latouros said. “When I was elected in June 2021, I committed to visiting all our current members and reaching out to countries not yet part of our association. Over the past three years, these visits revealed various issues that prevented some countries from becoming full members or even joining.
“To address this challenge, we developed a new membership scheme, which was approved during our last Delegates Assembly. This scheme is designed to be more inclusive and adaptable, allowing us to better
1. Antonis Latouros speaking at Aggregates Europe –UEPG’s Late Summer Reception 2024 event in Brussels.
2. Regular visits to Aggregates Europe – UEPG member quarry sites are a key part of Antonis Latouros’ work as the association’s president.
accommodate the unique circumstances of potential member countries.
“With this new approach, I am optimistic that we will successfully enlarge our membership base in my second term.”
Because of his success in visiting all members and potential new members throughout Europe, Latouros said his Aggregates Europe –UEPG colleagues call him “the travelling president”.
“I have managed to do this because my family, especially my wife Eleni, understands and supports me; otherwise, it wouldn’t be possible,” he said. “In the meantime, this personal touch is very helpful in fostering stronger collaboration among our member associations.”
How does Latouros feel about being named Aggregates Europe – UEPG’s rst two-term president?
“It’s a tremendous honour. This opportunity allows me to build upon the momentum and achievements of our rst term, driving forward our mission to promote sustainable practices, innovation and advocacy within the aggregates industry across Europe,” he said. “I am deeply committed to advancing our industry’s interests, collaborating closely with our members and stakeholders to navigate challenges and seize opportunities for growth and sustainability.”
Latouros, who has served as president of the Cyprus Aggregates Producers Association since 2013, brings a wealth of industry experience to the Aggregates Europe – UEPG presidency. His MSC Latouros Investments group comprises three aggregates quarries (Latomia Latouros, Latomio Pyrgon, and Elmeni Latomia) and one gypsum quarry (Latouros Gypsum). Additionally, the group operates a construction and demolition waste recycling plant and a comprehensive chemical laboratory (Veltia Cyprus). The group’s annual turnover is around €30 million.
Given Latouros’s Aggregates Europe –UEPG commitments and with succession planning in mind, the group is governed by an executive committee whose members are Latouros’s daughters Maria, an Oregon State University industrial engineering graduate with a Master’s in management, and Konstantina, an economist and King’s College, London, alumni; his son-in-law Kyriakos Konstantinou, a Liverpool John Moores University civil engineering graduate with a Master’s in project management; and Christos Zapitis, an Imperial College London mathematics alumni and chartered accountant with vast experience in business development and nancials.
When asked what he sees as the association’s biggest achievements during his rst Aggregates Europe – UEPG presidential term, Latouros is quick to point out that it’s been a team effort in many respects.
“First of all, I want to emphasise that none of the achievements would be possible without the unwavering support of my colleagues on the board, and of the chairs, vice chairs and secretaries of our committees,
task forces, and working groups,” he said. “Their dedication and tireless efforts have driven our achievements, and I am immensely grateful for their collaboration and partnership.
“I also want to express my heartfelt appreciation to the secretariat for their hard work and dedication. Their behind-the-scenes efforts often go unnoticed, but they are essential to the success of our association. A special note of appreciation goes, of course, to our secretary general Dirk Fincke. His leadership and vision have signi cantly shaped our path as an association.
“Regarding our achievements, the most signi cant ones include fostering stronger collaboration among our member associations, getting even closer and having even stronger collaboration with the big international NGOs [non-governmental organisations], enhancing our advocacy efforts at the EU level, and promoting sustainable practices within the aggregates industry.
“We successfully launched initiatives to increase the recycling of construction and demolition waste, strengthened our focus on sustainability through various projects and partnerships, and improved our communication strategies, which helped raise awareness of the importance of aggregates in construction and infrastructure development.
“These efforts have laid a solid foundation for our continued progress, and I’m excited to build on them in my second term.”
So what are the association’s key areas of focus during his second term as president?
“Our priorities will align closely with our newly established Business Plan for 2024–2027, titled ‘Sustainable Foundations: Building Europe’s Future through an Essential and Sustainable Aggregates Industry’,” Latouros said.
“First and foremost, we aim to enhance our role as a global leader in sustainable
aggregate production by promoting innovation, environmental stewardship, and social responsibility. Key initiatives include increasing our public relations and communication efforts to highlight the aggregates industry’s essential contributions to economic growth and daily life.
“We will also focus on enhancing membership value and collaboration, aiming to expand our membership base through a new and invigorated membership policy that comprehensively represents all of Europe.
“Another priority is strengthening stakeholder engagement and public perception through comprehensive programs that bring together NGOs, community leaders and policymakers to discuss industry challenges and opportunities.
“Lastly, we will emphasise our commitment to sustainability by promoting climate resilience, biodiversity and resource ef ciency initiatives, which align with our goals for a circular economy and digital transformation.
“By focusing on these areas, we can effectively address our industry’s challenges and ensure a sustainable future for the aggregates sector in Europe.”
How does Latouros, who was also appointed vice president of the Global Aggregates Information Network (GAIN) during its 7th Annual Conference in Córdoba, Argentina (20–23 October), see the current health of the European aggregates industry? What are its biggest challenges, and from where will growth come?
“The European aggregates industry is relatively stable, although it varies across different countries – some are experiencing downturns, others an upturn, while many remain stable,” he said.
“As I said, the biggest challenges we face throughout Europe primarily involve permitting procedures, which can be slow and cumbersome. There is a pressing need
for fast-tracked and streamlined processes to support timely project delivery.
“Additionally, accessing local resources has become increasingly dif cult, posing another industry challenge.
“While our carbon footprint is relatively low, we are committed to achieving carbon neutrality and have developed a comprehensive roadmap.
“Despite these challenges, growth in the aggregates sector is expected to remain strong. The ongoing need for infrastructure development and construction, particularly concerning the European Green Deal, will drive demand for our products. Moreover, we are seeing signi cant growth opportunities in recycling, which aligns with our sustainability goals and the circular economy.”
Latouros stressed that sustainability is at the core of his work as Aggregates Europe – UEPG president and integral to the association’s mission.
“We recognise that our industry is vital in promoting environmental stewardship, resource ef ciency and social responsibility,” he said. “During my rst presidential term, we initiated several projects that underscore our commitment to sustainability. For example, we launched a comprehensive roadmap to achieve carbon neutrality, outlining speci c targets and actions to reduce our carbon footprint. This roadmap serves as a guide for our members to adopt more sustainable practices in their operations.
“Additionally, we focused on enhancing recycling initiatives, working collaboratively with stakeholders to promote using recycled aggregates. This contributes to resource ef ciency and supports the circular economy by minimising waste and reducing the demand for virgin materials.
“But I want to emphasise that, even though recycling can reduce the need for virgin materials, lower environmental impacts and contribute to a circular economy, it will never be enough.
“We build much more than what we demolish. Even if we use the most modern techniques, it will never be possible to regain 100% of the aggregates used to build a certain building. Today, we demolish buildings that were built 50 to 60 years ago, but what we build today is more durable and will last more than 100 years. Therefore, the available C&D [construction and demolition] waste rate will decrease.
“Our statistics show Europe’s average substitution rate of recycled aggregates is currently 10%. A few countries manage it better, substituting 20 to 25% of their aggregate needs with recycled aggregates while declaring that they recycle all their C&D waste. This indicates that the ceiling for substituting aggregate needs with recycled aggregates is 20 to 25%. Even if we achieve these percentages across Europe, we will always need virgin materials for the remaining 75 to 80% of our aggregate needs.
“Additionally, factors that need to be considered with recycled aggregates are quality, availability and logistics.
“We also emphasised the importance of biodiversity and environmental protection in our extraction processes, advocating for best practices in restoration and sustainable resource management. Through these efforts, we aim to elevate the aggregates industry’s role as a leader in sustainability and demonstrate our commitment to building a more sustainable future for Europe.”
With production process digitalisation and arti cial intelligence (AI) increasingly prominent in the modern European aggregates sector, what effect does Latouros see them having in the long term?
“Digitalisation and AI are poised to signi cantly transform the European aggregates industry, offering numerous opportunities for increased ef ciency, safety and sustainability,” he said.
“In the short term, we are already seeing the adoption of digital tools for operational management, which help streamline
processes, reduce costs and enhance productivity. Technologies such as predictive maintenance and automated monitoring systems can improve equipment reliability and minimise downtime, resulting in more ef cient operations.
“Digitalisation and AI will have a profound impact in the long term. We anticipate these technologies will enable us to implement advanced resource management techniques, optimise production processes and enhance decision-making through data analytics.
AI can facilitate better environmental monitoring, helping us track our progress toward sustainability goals more effectively.
“As we move forward, embracing digitalisation and AI will be critical in fostering innovation and ensuring that the aggregates industry remains competitive in a rapidly evolving market. By leveraging these technologies, we can improve our operational resilience, reduce our environmental
footprint and ultimately contribute to a more sustainable and ef cient industry.”
Given many aggregate professionals across Europe are retiring or nearing retirement age, does Latouros think enough is being done to attract the next generation of industry talent? How is the association supporting efforts in this area of the business?
“Attracting the next generation of talent in the aggregates industry is a critical focus for Aggregates Europe – UEPG,” he said. “Our business plan for 2024–2027 outlines several initiatives aimed at promoting workforce development and inclusion.
“We are implementing industry-wide skillenhancement programs focusing on essential areas such as digital literacy, environmental management and sustainable leadership. These initiatives will help equip young professionals with the necessary skills to thrive in our evolving industry.
“Additionally, we are committed to enhancing diversity and inclusion within the aggregates sector. We aim to create more opportunities for underrepresented groups, particularly women, by promoting inclusive policies, mentorship programs and networking events. Partnering with educational institutions is also a key strategy, as we seek to introduce students to the aggregates industry through internships, scholarships and workshops.”
Latouros stressed that by fostering a culture of equality and actively engaging with educational institutions, Aggregates Europe – UEPG can help attract and develop the next generation of talent needed to drive the industry into the future.
“This comprehensive approach will not only help address the impending skills gap but ensure the aggregates industry continues to thrive competitively and sustainably,” he said.
When re ecting on how he sees the European aggregates industry a decade from now, Latouros envisions it as “a more sustainable, technologically advanced and socially responsible sector”.
“The ongoing focus on environmental stewardship and carbon neutrality will signi cantly change our operations,” he said.
“Average quarry work sites will likely be equipped with advanced technologies such as AI and automation to optimise processes, enhance safety, and reduce environmental impact. We can expect to see the widespread use of digital tools for monitoring and managing resources, which will improve ef ciency and reduce waste.
“Sustainability will be at the forefront, with quarries implementing more rigorous environmental practices. This includes adopting renewable energy sources, enhanced biodiversity initiatives, and strongly emphasising land rehabilitation and restoration practices.
“Moreover, the workforce will be more diverse and skilled, with ongoing training and development programs ensuring employees can handle new technologies and practices. Integrating social responsibility into our operations will be paramount, with quarries engaging more with local communities and stakeholders.”
Latouros said the aggregates industry will be pivotal in supporting Europe’s infrastructure needs while demonstrating a commitment to sustainability and innovation. He believes this evolution will enhance the “industry’s reputation and ensure our longterm viability in an ever-changing landscape”.
“Firstly, the successful expansion of our membership base will be a crucial indicator,” he said.
“By implementing our new membership scheme and fostering stronger collaborations, I aim to ensure we comprehensively represent the aggregates industry across Europe.
“Secondly, I will consider our advocacy efforts to be successful if we have effectively in uenced EU policies and regulations to create a more favourable environment for the aggregates sector.
“This includes streamlining permitting procedures and promoting sustainability initiatives aligning with our carbon neutrality roadmap.
“Furthermore, enhancing the public perception of our industry will be vital.
“We will have made signi cant strides if we can effectively communicate aggregates’ essential contributions to society and infrastructure and demonstrate our commitment to sustainability.
“Lastly, cultivating a skilled, diverse workforce prepared for future challenges will be essential. It will mark a signi cant achievement if we can attract and retain new talent, ensuring that our industry is equipped to adapt and thrive.
“In summary, success will be measured by our ability to grow our membership, in uence policies, enhance our industry’s reputation and develop a capable workforce ready to meet the future demands of the aggregates sector."
When considering how he will measure his two terms as Aggregates Europe – UEPG president, Latouros believes achieving several key objectives will make it a success.
Given his relentless drive and focus, few would be likely to bet against Latouros and the talented and diligent Aggregates Europe – UEPG General Secretariat achieving those goals. AB
Having commenced operations in 1927,
quarries
Several upgrades at AfriSam Coedmore, located at the doorstep of one of the largest road infrastructure projects in South Africa, have put the quarry in good stead to meet local demand for aggregates.
Having commenced operations back in 1927, AfriSam Coedmore is one of the oldest quarries in South Africa. And with an annual production capacity in excess of one million tonnes, it is one of the largest quarries not only within the AfriSam portfolio, but in South Africa at large.
AfriSam Coedmore mines competent quartzite rock, with some dolerite and tillite intrusions.
The dolerite intrusions are generally used to make sub-base materials such as G5, while the other two competent rocks are central to the manufacture of highly sought-after concrete aggregates and roadstone.
Located to the south of Durban in the KwaZulu-Natal province, AfriSam Coedmore has enjoyed high aggregate demand in the past few years, especially given its close proximity to the ongoing agship N2/N3 road upgrades implemented by the South African National Roads Authority Limited (SANRAL). The upgrades, which form part of the national government’s Strategic Integrated Projects (SIP2): Durban-Free State-Gauteng Logistics and Industrial Corridor, are expected to take eight to 10 years to complete.
The upgrade of the N2 focuses on a 55km stretch from Illovu River on the south coast to Umdloti on the north coast, while the N3 project focuses on an 80km section from Durban to Pietermaritzburg. The upgrades entail widening the N2 and N3 carriageways, with four or ve lanes in each direction, as well as recon guring most major interchanges.
One of the major legs of the project to which the quarry supplies materials is the upgrade of the EB Cloete Interchange on the N2. Located within a 10km distance of AfriSam Coedmore, the EB Cloete Interchange is said to currently be the single largest road infrastructure project in South Africa. With a project value of ZAR5 billion (about £220 million), SANRAL said it is the biggest single project value undertaken by the roads authority to date.
“We are fortunate to be situated right at the doorstep of the many faces of the N2/N3
road upgrades,” AfriSam Coedmore works manager Lloyd Maringa said.
“In the past few years we have enjoyed high aggregate demand, initially supplying mostly base and sub-base materials during the early days of the projects. With the upgrades now moving onto surfacing, we are starting to move more high-value products such as roadstone and concrete aggregates.”
Despite a huge spike in demand, AfriSam Coedmore did not necessarily need to invest in more capacity. The existing capacity – a million tonnes per year – put the operation in good stead to meet the rising demand.
“To provide context, we run one of the biggest primary crushers in the South African quarrying sector – a 700-tonnesper-hour [tph] Allis Chalmers 3655 superior gyratory crusher. To meet rising demand, we simply increase the number of shifts when necessary,” Maringa said.
The production process starts in the pit, with at least a single blast per month. Blasts – outsourced to well-known contractor Brauteseth Blasting – are kept reasonably large at an average of 60,000t of material on the ground per blast, according to AfriSam Coedmore maintenance superintendent Dustin Naidoo.
The load and haul function is outsourced and the contractor deploys a 50t excavator, which loads 35t articulated dump trucks (ADTs). The ADTs haul material from the face to the primary section of the plant, tipping directly into the in-pit Allis Chalmers 3655
gyratory crusher. The primary plant then feeds a 280m conveyor belt running from the primary section to the intermediate stockpile (ISP).
“Installing the primary plant in the pit has ensured reduced haul distances, thus cutting down on diesel costs,” Naidoo said.
“This is particularly bene cial, especially given the deep nature of the pit. The depth of the quarry pit is now 140m and is 54m below sea level.
“As part of our ef ciency drive to reduce our cost per tonne of operation, we also found it cost-effective to run an electric conveyor instead of hauling material using diesel-powered trucks.”
From the ISP, the material is fed into a tunnel with two conveyor belts moving material to the secondary crusher, a Symons 5.5-foot cone crusher, running at an average 35mm closed side setting (CSS). AfriSam Coedmore is one of the few quarries in South Africa still running this old-generation cone crusher, which typi es longevity and durability. From here, the material moves to the tertiary crusher, a new-generation Metso HP400 cone crusher running at an average 18mm CSS. The material goes to a series of vibrating screens and is screened into various product sizes, from 50mm down to a -7.1mm sand.
“In recent years, the plant has bene tted from major upgrades, which put us in good stead to meet the current high aggregate demand in our area,” Naidoo said. “One of the most recent upgrades was the installation of the new Metso HP400 tertiary crusher
in 2019, replacing the older Nordberg 1352 omnicone crusher.
“The HP is an industry standard in aggregate production. It features a unique combination of crusher speed, throw, crushing forces and cavity design, providing higher capacity and superior end-product quality in secondary, tertiary and even quaternary applications.”
AfriSam Coedmore also recently replaced its old Nordberg 1144 omnicone crusher with a new-generation Telsmith SBS-38 cone crusher supplied by Astec Industries. One of the key features of this crusher is the large feed opening, which yields high performance.
Quarry operations cannot afford to ignore the bene ts of using the latest technologies to drive ef ciencies. The increased economic and operational pressures, Maringa said, demand that today’s quarries stay ahead to remain competitive.
One area where this is particularly crucial is in blasting – a critical function that signi cantly in uences operational ef ciency, costs and the success of all the other downstream processes, such as load and haul, and crushing and screening.
With the use of electronic blasting systems, it is now possible for AfriSam Coedmore to not only meet higher safety levels and environmental impact control but also to gain more blast control and improve fragmentation, thus delivering more downstream value to the whole operation.
“AfriSam uses the latest technology when executing our blasts. This enables us to operate in harmony with the communities surrounding our operations,’’ Maringa said.
To preserve uptime in loading operations, AfriSam Coedmore quarry is taking advantage of the bene ts of modern Loadrite on-board weighing systems from Loadtech. The company’s three Volvo wheeled loaders, deployed to load customer trucks, are tted with the Loadrite L3180 SmartScale, which uses weighing intelligence and solid-state sensors for more accurate, precise and faster loading.
“Loading is a key function of our operations. Traditionally, we relied on weighbridges alone, which are known to be prone to product errors and weight challenges,” Naidoo said.
“With the Loadrite system, we are able to eliminate guesswork in our loadout processes, which means customer trucks are loaded correctly the rst time.”
In addition, the quarry has recently invested in a Tru-Trac belt scale. The AfriSam Coedmore team had struggled with monitoring production output and inventory, with the margin of errors with the previous belt scale dramatically affecting operations.
“The Tru-Trac belt scale facilitates weighing the real mass of the material from the ISP to the secondary crusher,” Naidoo said. “We have found it to be a simple and extremely accurate system
Coedmore recently invested in a Tru-Trac belt scale, which facilitates weighing of real mass of the material from the ISP to the secondary
engineered to provide precise data. In fact, we were impressed by the static calibration accuracy error levels as low as 0.06%, which is outstanding. Our accuracy error margins were as high as 15% with the previous belt scale.”
Maringa called this type of technology “the lifeblood of our operations”.
“We will therefore continuously investigate new technologies in the market to ensure ef ciency and productivity of the highest orders,” he said. AB
While Chinese aggregate production has reduced in recent years, the world’s biggest producer continues embracing the sustainability agenda.
China’s aggregate production stood at 16.8 billion tonnes in 2023.
That is according to gures quoted by China Aggregates Association’s (CAA) international department director Xu Beibei on RocksTalk, the podcast of Aggregates Europe – UEPG, during an interview at the 7th Global Aggregates Information Network (GAIN) Conference in Cordoba, Argentina, in October.
While that gure of 16.8 billion tonnes is signi cantly down from the nearly 20 billion tonnes produced in 2020, RocksTalk stressed that China remains by far the world’s largest aggregate producer (India is second, producing a GAIN-estimated 5.6 billion tonnes in 2023).
China has around 13,000 extraction sites, a huge reduction from more than 56,000 a decade ago. The nation produces over ve times the tonnage in Europe annually on half the number of sites (Europe has around 26,000 extraction sites). China’s largest quarry sites produce around 100 million tonnes of aggregates annually.
Shortly after the latest issue of Aggregates Business was due to go to press, the global aggregates industry was descending on China for major dual conferences.
More than 1000 senior quarrying sector professionals will share their experience, good practice and vision for
the aggregates industry’s future during the 9th China International Aggregates Conference and the 7th China International Conference on Comprehensive Utilisation of Construction and Demolition Waste, Tailings and Waste Rock.
The CAA was hosting the dual conferences in Chongqing from 16–18 December 2024.
Speaking to Aggregates Business ahead of the big events, CAA president Hu Youyi said the continued decline in Chinese real estate investment and the slowdown in infrastructure spending were major factors in the country’s declining aggregates production volumes and product prices.
“The industry is going to face big challenges for a long time. However, the challenges also provide valuable opportunities for the industry’s transformation and upgrading,” Hu said.
“With the adjustment and transformation of the Chinese macro-economy, the aggregates industry, as the cornerstone of the construction industry, is inevitably impacted.
“According to the ‘China Aggregates Industry Operation Report’, released by the China Aggregates Association, from 1 January to 31 October 2024, China’s national aggregates production was 12.5 billion tonnes, a [year-on-year] decrease of 10.6%. Behind this gure is the grim reality and heavy pressure the industry faces.”
On the supply side, Hu said, the shadow of gradually expanding overcapacity looms over the entire Chinese aggregates industry. Although China’s existing aggregate production lines can meet the current market demand, the continuous addition of new production lines has further exacerbated the risk of overcapacity.
“This phenomenon not only re ects the industry’s blind expansion in the past few years but also exposes the problem of enterprises’ lack of foresight and exibility in the face of market changes,” Hu said.
“Real estate and construction investment have declined on the demand side. Although infrastructure investment has maintained growth, the growth rate has slowed signi cantly, making it dif cult to effectively ll the gap in the real estate market, resulting in insuf cient effective demand for sand and gravel.
“Regarding price, statistics from CAA show that in October this year the average comprehensive price of aggregates in China was CNY94 (US$12.91) per tonne, a year-onyear decrease of 9.6%.”
Looking at the next few years, Hu believes China’s aggregates industry will experience a process of de-capacity and enter a new round of adjustment, deep adjustment and high-quality development. In this round of adjustment, some enterprises with overcapacity, backward technology, high
costs and no comprehensive advantages will be eliminated until the supply-and-demand relationship reaches a basic balance.
“Faced with such a predicament, the aggregates industry started to have profound re ection and self-examination,” Hu said. “How to survive adversity, nd opportunities in challenges, and reshape the industrial ecology under the new situation have become issues that every sand and gravel company must face and think about.”
Faced with a complex industry environment, Chinese aggregates-producing companies have begun to explore the path of transformation and upgrading.
“The aggregates and equipment industry is a eld full of in nite possibilities. A small technological improvement, concept innovation or model change may bring huge bene ts,” said Hu.
The CAA president outlined the key dif culties faced by China’s aggregate enterprises.
For the built quarry, there is still pro t to obtain if the design and equipment selection is reasonable, but as the price of sand and gravel continues to fall, the pro t margin will become smaller and smaller; for enterprises with the cement, aggregate and concrete industry chain, there is still room for price reduction; and for newly-built quarries, the cost of investment in resource fees and construction is large, and it isn’t easy to recover the cost when the price of sand and gravel products is reduced and the company’s funds are tight.
For quarries with unreasonable design and equipment selection, the operating expenses are high and the room for price reduction is limited. Technical improvement is required to reduce costs but requires a large amount of capital investment.
Hu believes innovation is the key to breaking the deadlock, with aggregatesproducing companies’ focus needing to be “actively exploring new market areas and growth points”. He said green building and ecological conservation concepts have become more popular in China, and the
“With the adjustment and transformation of the Chinese macro-economy, the aggregates industry, as the cornerstone of the construction industry, is inevitably impacted.”
Hu Youyi
government’s support for new energy and materials has continued to increase. Hu believes the national aggregates industry can take this opportunity to develop in the direction of high-end, re ned and green products and improve the core competitiveness and market share of enterprises by developing high-quality aggregates products and expanding new application areas and market channels.
“Although the current aggregates industry faces many challenges and dif culties, we should remain optimistic,” Hu said. “Although market demand has declined, the total volume is still huge and a certain intensity of
A Powerscreen Premiertrak 400X jaw crusher being showcased at a Powerscreen open day in Zhejiang province.
construction is maintained. The renovation of old urban communities and constructing small and medium-sized rural infrastructure are also key support projects.
“Accelerating the ‘three major projects’ – construction of affordable housing, the renovation of urban villages and public infrastructure for both normal and emergency use – are major strategic deployments made by the CPC [Communist Party of China] Central Committee and will remain an important task at present and in the future.”
According to Off-Highway Research (OHR), the Chinese off-highway machinery market collapsed in 2022 with a 39% decline to 237,317 units after two years of “abnormally high” sales in 2020 (412,595 units) and 2021 (389,312 units). OHR noted that this was partly due to government stimulus money being spent. The same source adds that the steep fall in demand was also compounded by shocks in the Chinese real estate sector, coupled with dif culties in tackling the COVID-19 pandemic.
A further 38% drop in construction equipment sales in 2023, to 146,981 units, was, OHR said, partly attributable to falling prices and mounting bad debts in the retail estate sector.
OHR forecasts a further 4% fall in sales in 2024 to 140,710 units, which it believes is the market “bottoming out” and “arguably the best-case scenario for the country.” However, further bad news and property developer insolvencies could further depress the equipment market.
OHR also reported that wide-bodied trucks (WBTs) have emerged as by far the most popular type of off-road hauler in the Chinese mining, quarrying and construction sectors, with sales reaching almost 18,000 units in 2023, compared to 260 traditional rigid dump trucks and just three articulated haulers.
Produced exclusively in China by local original equipment manufacturers (OEMs),
WBTs are said by OHR to be manufactured primarily with locally available diesel engines or batteries, transmissions and axles. They feature a large hopper on a relatively low chassis, and have a much lower purchase price than traditional off-road dump trucks and better rough terrain capabilities than standard on-road trucks.
The increased width of the vehicle body has signi cantly improved its load capacity. However, the prominent feature of the ‘wide body’ exceeds the national standard limit of 2.5 metres, OHR said in a November news release. As a result, WBTs are not allowed to travel on the highway but are limited to use in open-cast mines or on private land.
The payload capacity of WBTs usually ranges from 20–130 tonnes. Demand for smaller models with payloads under 60 tonnes was evident around 20 years ago, OHR further noted, while the most popular models in their rst decade of use had a gross weight of 70 tonnes.
MarketsandMarkets supports OHR’s analysis that the Chinese construction equipment market is mainly supported by stimulus spending provided by the government in 2020, which resulted in “tremendous growth” in the next two years.
After weaker demand in 2022 and 2023, akin to pre-2020 sales levels, the leading US-based business markets consultancy predicts a recovery in 2024, mainly due to growing demand for compact equipment and the gradual increase in residential housing projects.
The size of China’s construction market was US$4.7 trillion in 2023, according to GlobalData. The market is projected to attain an average annual growth rate (AAGR) of over 3% from 2025 to 2028. Investment in energy and infrastructure projects will support the sector’s growth.
The Chinese government plans to invest CNY92.4 trillion (US$13.7 trillion) by 2060 for green power transformation. As part of the programme, the government plans to attain net-zero emissions of greenhouse gases by 2060. China plans to source 33% of power from renewable sources by 2025.
At the start of 2023, China’s Ministry of Industry and Information Technology (MIIT) unveiled 15 measures to stabilise growth further and adjust the structure of small and medium enterprises (SMEs). This includes nancing support for highquality SMEs.
GlobalData stated that China plans to increase the number of SMEs involved in manufacturing to 150,000 and ‘little giant’ enterprises to 10,000 by the end of 2024. In September 2023, the Chinese government revealed plans to add 2500km of high-speed railway lines and expand its total rail network by 50,000km by 2025.
Reportlinker, an AI-driven market intelligence platform, agrees with GlobalData’s take that the Chinese construction market will grow over the next three years. The same source said the market’s prospects will be boosted by continuing urbanisation, which leads to a rising demand for sustainable building practices and construction materials like concrete, cement, steel, bricks, sand and gravel.
Meanwhile, the World Cement Association’s chief executive of cer (CEO) Ian Riley has welcomed China’s recent expansion of its national carbon trading market to include the cement industry, among other hard-to-abate sectors, by the end of this year.
The move announced by China Minister of Ecology and Environment Huang Runqiu in June 2024 marks a signi cant step in China’s environmental plans.
L–R: Terex MP president Kieran Hegarty; Terex Materials Processing aggregates business vice president Pat Brian; Terex group engineering director David Trimble.
“The inclusion of cement in the Chinese ETS [emissions trading scheme] is a critical and long-awaited step,” Riley said. “As we have seen in Europe, a well-implemented carbon ETS can be bene cial by not only curbing emissions but also catalysing industry restructuring that favours the most ef cient and lowest-emitting producers.
“This move signals China’s intent to prioritise sustainability in high-emission sectors, a move welcomed by the World Cement Association.
“In addition to the ETS, China has also successfully used energy ef ciency standards to encourage widespread adoption of the latest low-energy technology. This approach is essential for meaningful climate action.”
China is by far the world’s biggest national producer and user of cement, producing 2.1 billion tonnes a year, half the global total. India is a very distant second, producing around 410 million tonnes annually. In January 2024, the China Cement Association (CCA) and the Global Cement and Concrete Association (GCCA) signed a memorandum of understanding (MoU) to help accelerate the sector’s decarbonisation worldwide.
“We are delighted with this MoU and will work with the CCA to deliver a China cement industry roadmap similar to that used in India and the rest of the world to achieve decarbonisation. This means that the roadmaps are consistent and comprehensive across geographies,” GCCA director of concrete and sustainable construction Dr Andrew Minson said during an interview with Aggregates Business earlier in 2024.
“Getting China on board is also signi cant in a wider context, as the country is a signi cant manufacturer of cement and concrete machinery and plants and a big contributor to the industry sustainability research agenda. China is also a major player in developing and commercialising carbon capture solutions.”
The Wirtgen Group showcased new products and technologies for the Chinese and wider Asia market at bauma China 2024 in November. As part of Wirtgen extensive display, its Kleemann brand highlighted how its premium crushing plants can be operated easily and ef ciently with the SPECTIVE operating concept.
Since 2004, the Wirtgen Group has been manufacturing products that ful l German quality standards at its ultra-modern factory in Langfang, a city in China’s Hebei province. Tailored to the speci c needs of the local market, the models manufactured here offer long life, cost ef ciency, ease of use, and low operating and maintenance costs.
Delegates at the China Aggregates Associationhosted 2023 China International Aggregates Conference in Shanghai.
With seven locations, two service centres and an extensive dealer network, Wirtgen China operates an ef cient sales and service network that serves almost all 22 Chinese provinces. The Wirtgen Group subsidiary in China is always close to its customers and can offer solutions from a single source.
During another key industry exhibition, Hillhead 2024 in Buxton, England, in June, Terex Materials Processing (Terex MP) vice president of aggregates business Pat Brian highlighted the notable increase in the production of Powerscreen and Finlaybranded crushers and screeners at Terex MP’s 18,000m² site in Shanghai’s Jiading district.
“We acquired the facility just as the coronavirus pandemic hit. The team there has done a remarkable job,” he said. “This year, we will pretty much double production from last year. We use that facility to supply the local Chinese market and support our business in Southeast Asia and Australia.
“Due to the domestic economy, the China market has been quite dif cult; however, we are seeing a few signs of improvement. To our bene t, some other international [crushing and screening] brands have now exited that market. From our [China] factory, we can, in time, leverage many of our brands and products.” AB
No matter how challenging your needs, BKT is with you offering a wide range of OTR tyres specifically designed for the toughest operating conditions: from mining to construction sites. Sturdy and resistant, reliable and safe, able to combine comfort and high performance.
BKT is with you, even when work gets tough.
OEMs are delivering flagship wheeled loaders to new markets worldwide, and Liebherr, Volvo CE and Hitachi are among the latest to put their machinery to the test.
Afather-and-son team producing some of the nest architectural stone in the world relies on Liebherr equipment for extraction and processing duties.
Gwrhyd Specialist Stone is found high in the Swansea Valley overlooking the Black Mountains of Wales, and it’s here that Michael Walton and son Charles have spent the last decade assembling a eet of specialist equipment to help develop the site to its full potential.
Together, they are responsible for the day-to-day running of a quarry employing 22 people to produce just 5000 tonnes a year; quarries of similar size could output up to 500,000 tonnes a year, but the volume at Gwrhyd is small dues to the specialist nature of its stone.
Liebherr has been an important supplier of equipment since the beginning of Gwrhyd Specialist Stone. The operation still uses its original L 510 Stereo wheeled loader and, over the years, it was joined by an L 509 Tele wheeled loader and an R 926 G8 excavator, the latter having since been replaced by a slightly larger R 930 G8.
“The R 926 did exactly what we wanted it to do and served us well over the past few years,” Charles said.
Working alongside another manufacturer’s used 14t excavator, used for loading the site’s two-deck screen, the new R 930 has been a hit with regular operator Jamie Evans, who came off the 45-tonner initially used at the site.
“It was an ideal machine at the top of the quarry, but as space got a little tighter it proved to be too big,” Evans said.
“The R 926 was also great and a massive step up in comfort over the older model and it’s now the same for the R 930. It’s a really comfortable machine, still has bags of power but hardly uses fuel.
“We don’t do a great deal of ne work here – we’re usually at-out moving the stone – but we’re still averaging just over 16 litres per hour.”
Boom and stick options for the R 930 G8 model include a standard mono boom, a straight demolition boom and a variable arm version, with Gwrhyd specifying the standard con guration, which combines a 6.2m boom and 3.2m stick, topped off with a Miller
Groundbreaking coupler for fast changes between buckets and a breaker.
Regular use of the breaker means the excavator has a dedicated drain line back to the hydraulic oil tank to ensure the oil is returned to lower its temperature as quickly as possible.
The R 930 G8 tips the scales at just under 31 tonnes in its LC undercarriage version and has a Liebherr seven-litre, D 934 engine developing 245hp at 1800rpm. The engine is designed to deliver peak torque at low engine rpm, the R 930 achieving 1255Nm at just 1350rpm. That lowers internal and external noise levels and signi cantly reduces fuel consumption.
The excavator is used for a variety of duties, from frontline extraction to a current major programme of site development. Any spare time is spent moving a large pile of material left over from the previous owner’s operations. That material gets taken to the screener and a portion is then cut into smaller blocks to increase the percentage of usable material being quarried.
“We are hoping to gain planning permission in the future to process the remaining waste material into a variety of crushed and screened aggregates to further increase the percentage of materials we are able to win from the site,” Charles said.
With more than 100 years of reserves, Gwrhyd is set to continue producing its distinctive stone for the building projects of the future – and to provide work for future generations of Liebherr equipment.
The Italian job
Hitachi has also been busy with its customers across Europe, where the company’s ZX530LCH-7 has been put to the test in the north-east of Italy.
Vaccari Antonio Giulio SpA’s basalt quarry in San Pietro Mussolino produces essential materials for railway and road construction projects. With a 15-year licence to continue its operations, the quarry dedicates 60 per cent of its output to railway projects and 40 per cent to road sites, such as the aggregates for the asphalt and required drainage.
Following its positive experience with Hitachi construction machinery, Vaccari recently added the Stage-V-compliant ZX530LCH-7 to its eet, including two other Hitachi large excavators: a ZX470 and ZX490.
The large Zaxis-7 excavator was purchased from local authorised dealer Comac.
1:
2: Hitachi ZX530LCH-7 excavator at Vaccari Antonio Giulio SpA’s basalt quarry in north-east Italy.
3: Vaccari’s experience with Hitachi Zaxis excavators influencedthe decision to purchase the ZX530LCH-7.
“I have been working with Vaccari for four years, and like all our customers they recognise Hitachi as the benchmark for reliability in the market,” Comac Padova branch manager and Veneto regional sales manager Mario Rebella said.
“In addition, the customer signed a maintenance contract of up to 10,000 hours to bene t from our rapid response times.
“This, alongside Vaccari’s previous positive experience with Zaxis excavators, certainly in uenced their decision to purchase the ZX530LCH-7.”
Volvo Construction Equipment (Volvo CE) has taken the step of testing its latest machinery in the considerably warmer climates of the United Arab Emirates (UAE), ultimately launching the L120 Electric wheeled loader in the Middle East.
The L120 Electric is engineered to deliver the same powerful performance as its diesel counterpart and has already undergone rigorous testing in the extreme heat of the UAE, passing all operational and durability benchmarks with ying colours.
The launch of the Volvo L120 Electric wheeled loader in the UAE and Turkey helps to showcase Volvo CE’s commitment to the electric machinery space. A forward-thinking approach to equipment electri cation helps to show the company’s ability to deliver a viable alternative to diesel-powered machines without sacri cing power, reliability or performance.
Before making the L120 Electric available in these key markets, Volvo CE tested the machine thoroughly in collaboration with trusted Volvo CE made the decision to test its equipment in the hotter climates of the United Arab Emirates.
A new Australian event for the municipal works, commercial and civil construction industries.
Melbourne, Australia September 2025
Converge is Australia’s premier event for Sub-Contractors, Project Engineers, Council Fleet Managers, and Large-Scale Construction Contractors across the municipal works, civil construction and infrastructure space.
Through a mixture of live demonstrations, equipment showcases, and conference spaces, Converge will bring industry experts together to share knowledge and deliver solutions for building and maintaining Australia’s future.
How does fast and accurate stockpile inventory positively impact aggregate producers’ bottom lines?
In the fast-paced aggregates world, accurate and timely stockpile inventory is crucial for operational ef ciency and nancial reporting. Yet the traditional methods of measuring bulk materials like rock, dirt and mulch often deplete internal resources and lead to delays, disputes and inconsistencies.
Enter Stockpile Reports, a computer vision software company revolutionising how companies track and manage their bulk material assets.
Stockpile Reports enabled one large global, vertically integrated bulk materials producer to verify more than 10 million tonnes of inventory across 87 sites in less than 24 hours, setting a new industry standard. The sites in question are situated across ve US states.
The challenge of stockpile inventory management
Managing stockpile inventory in the aggregates industry is no small feat.
Companies often grapple with resource intensiveness, as traditional measurement methods require signi cant manpower and time. Then there can be inconsistencies and errors, as manual measurements are prone to human error and internal biases. Delayed reporting prolongs measurement processes and can delay nancial reporting and decision-making. Finally, there are audit risks, with inaccurate inventories potentially causing nancial discrepancies and audit challenges.
These were the challenges faced by Stockpile Reports’ major bulk materials producer customer. With operations spanning multiple locations, the customer needed an accurate, scalable and ef cient solution.
Stockpile Reports offers an enterprise SaaS (software as a service) platform that automates the measurement of bulk materials using advanced photogrammetry and computer vision technology. By leveraging imagery from drones, planes and even smartphones, the company provides precise and reliable measurements without the traditional hassles.
Stockpile Reports’ success with the customer resulted from a meticulously
planned and executed work ow. Site parameters were set up as a one-time task to streamline future measurements, and a coordinated plan was established to capture inventory across all sites simultaneously.
High-resolution aerial imagery was collected without ground control points thanks to ight-to- ight image registration, with the imagery data uploaded to Stockpile Reports’ cloud-based intelligent image processing service on the same day and stored securely.
Managing stockpile inventory in the aggregates industry can be challenging.
Advanced algorithms automatically identi ed individual stockpiles, while automated processes calculated volumes using precise measurements of toes and base planes. Any reports agged for potential issues underwent a quality review. Automated reports were generated and posted on a secure portal.
Interactive site images were provided for product identi cation and veri cation by the customer. The system identi ed risks such as combined piles, obstructions or environmental factors affecting accuracy. Only measurements that met stringent accuracy criteria were nalised and comprehensive PDFs were generated for audit transparency.
A controlled process was also in place to manage any discrepancies or disputes.
Stockpile Reports believes several key attributes set its offer apart from traditional methods and other technological solutions.
The automated system helps to eliminate internal biases and errors by removing the need for manual clicking or point selection. Algorithms are able to handle heavy lifting traditionally performed manually, from pile identi cation to volume calculations.
Company policies for density factors and product speci cations are tightly controlled, which means modi cations to these subjective assumptions are restricted, ensuring consistency and reliability. Each measurement is independently evaluated for over a dozen common problems that can corrupt accuracy. The system provides con dence scores and does not publish unreliable reports, mitigating nancial statement risks. The detailed reports and transparent processes meet the scrutiny of major audit rms, classifying Stockpile Reports as a third-party veri cation service.
EveryPoint in precision measurement Stockpile Reports’ image processing is powered by EveryPoint, an intelligent software service that continuously replicates real-world assets.
This technology ensures that imagery from various sources, such as drones, planes or smartphones, is integrated and cohesively processed.
Obstructions are auto-corrected, with the system identifying and adjusting for equipment, vegetation, or other obstructions. The objective surface scoring provides an unbiased assessment of the stockpile surfaces.
Compared to GIS tools and drone GIS solutions
While geographic information system (GIS) tools play a vital role in mapping for mine planning and inspections, they often fall short of ef cient stockpile measurement, according to Stockpile Reports.
Drone GIS solutions require substantial manual work for measurements and data processing. Stockpile Reports cites studies indicating these solutions can take up to 20 times more internal manpower than its own. The absence of automated pile identi cation and volume calculation is said by Stockpile Reports to lead to inconsistencies and errors.
“Using a traditional GIS tool, the customer likely would have incurred more than 1600 hours of eldwork managing ground control and measurement calculations and reviewing estimates,” Stockpile Reports said.
“This would have required more than 60 FTEs [full-time employees] to achieve in the same timeframe.
“The cost of monthly inventory veri cation using traditional methods is exponentially more expensive than digitisation.”
Stockpile Reports’ automated system helps to eliminate internal biases and errors.
Setting a new industry standard
Stockpile Reports’ collaboration with the customer exempli es how technology can transform traditional industries. By achieving an enterprise-wide inventory across 87 sites in less than a day, the company demonstrated that accuracy, ef ciency and scalability are not mutually exclusive.
This represents a signi cant advancement in operational ef ciency for the industry, Stockpile Reports said. Rapid measurements free up resources for other tasks, reliable data supports nancial reporting and reduces audit risks, and timely and precise inventory data informs better business decisions. AB
The cost of monthly inventory verification using traditional methods is more expensive than digitisation
US quarrying and road construction giant Astec and its dry bulk material handling solution specialist Telestack are among the OEMs whose future-proofing endeavours leave them poised to prosper from renewed buoyancy in customer demand.
It is a very rainy day in late September and Aggregates Business is facing Damian Power, Astec’s managing director for Europe, and Malachy Gribben, Telestack’s commercial director, across the meeting room table at Telestack HQ in Omagh, County Tyrone, Northern Ireland.
Their stark assessment of the state of the present off-highway equipment market mirrors the early-autumn weather.
“I think the equipment market is 15% down year-on-year,” Power said. “On the Telestack side, we’ve not had big dealer inventories, as they would never carry big [mobile dry bulk material handling] rental eets. We’ve been fairly judicious in managing that side of our SIOP [sales inventory and operational planning] process.”
Astec expanded into Northern Ireland in 2014 after acquiring Telestack. The company nished the US$6.5 million 44,000ft² expansion of its Telestack-site-neighbouring Astec Doogary facility in 2023, bringing the Astec Omagh footprint to 100,000ft². The extension took Astec’s total investment since the Telestack acquisition to more than US$10 million, with an employee base of over 230 people in Northern Ireland.
More than half of the global market supply for mobile crushing and screening equipment originates in Northern Ireland. As such, Astec’s enlarged manufacturing presence in Omagh will enable it to grow its international market business and better serve its customers and partners.
“We’ve only been getting out of the blocks in terms of building up our production capability at Doogary, so while we have had the same [market] problem as others, it has not felt as big for us [Astec Europe]. We weren’t running the same [machine] build rates as some other manufacturers,” Power said.
While Gribben described the situation as tough, he pointed to the fact the company started planning for a market slowdown 20 months ago.
“With longer lead time items postpandemic, it has taken our supply chain team time to adjust to our reduction in machine builds,” he said. “We have a strong enough pipeline of work to think that the project side of our business will hold up next year. We appear to be in a better position than many of our peers.
“Astec’s tracked crushing and screening business will be bigger next year than this year, as we’re coming from a very low base.
“Let’s assume the global tracked crushing and screening market is not getting any smaller. The light switch will ick on again in our industry, probably in the second quarter of next year. Astec is already a proven supplier, so can we get our fair share of the market?
“Astec has not just started designing crushing chambers; we pioneered much of the technology that helped introduce chambers to the industry.”
Attendees at this year’s Hillhead exhibition (25–27 June) saw live demonstrations of Astec’s FT4250 HSI
(horizontal shaft impactor), a popular US market crusher, and GT205 screener. Many exhibition goers also visited the manufacturer’s large show stand, where Astec showcased an extensive product range from its Rock to Road solutions portfolio.
Telestack was also on hand at Hillhead 2024 with its highly mobile and versatile TSR 40 radial telescopic stacker. The only ‘Roll On – Roll Off’ (Ro-Ro) radial telescopic unit on the market, the TSR 40 utilises its radial, telescopic and luf ng features to allow the operator full control and exibility when stockpiling a range of materials.
The addition of an integrated PLC stockpiling system eliminates segregation, degradation, contamination and compaction of material, which is critical for maintaining the quality of material during the stacking process. Telestack said the TSR40 offers up to 30% larger stockpile capacity than conventional xed-length conveyor systems, with greater site mobility.
During the key quarrying equipment industry showcase, Aggregates Business spoke to Power and Astec Materials Solutions division president Michael Norris.
“All the machines you see here at Hillhead were manufactured in Omagh,” Power said. “The SF20 is our new 20” x 5” triple-deck screen, and the one we have here at Hillhead is tted as a rinser. The SF20 can be quickly converted from a dry screening to a rinsing con guration. It’s the rst tracked mobile plant fully designed and built by our Omagh-based team.
“We also think there will be a good international market demand for the FT4250 tracked impactor given its success in North America today.”
“We have a stronger focus on Europe, and Damian was recently appointed our European managing director,” Norris said. “The machines we are designing and building in Omagh are speci cally for the international market.”
When asked about Astec and Telestackbranded machine production volumes at the Omagh facility, Power said he expects it to ultimately grow.
“We expect that the current [market] slowdown is temporary,” he said. “We have invested in Omagh to grow manufacturing volumes there signi cantly over the next three to ve years.”
Norris said Astec wants to increase production out of Omagh “seven-to-ten-fold”.
Has Astec found it hard to recruit engineers, welders and other skilled workers to work at its Omagh facility due to the number of competitor original equipment manufacturers (OEMs) with a strong presence in Northern Ireland?
“We have an employee-focused culture, and whilst recruitment is challenging for the industry, we are on a growth trajectory and people can see that,” Norris said. “We are an over-100-year-old company when it comes to crushing and screening. We have that expertise.”
Power agreed that Astec holds a strong position in the market and across the broader industry
“We are a unique proposition to employees in that we are high growth with a strong record in the [global] aggregates industry, in crushing and screening speci cally,” he said. “We are not just some start-up. We have substance behind us.”
Among other Astec machines exhibited at Hillhead 2024 were the 3000-tonnes-perhour HF24 hopper feeder and the versatile, custom-built 220-tonnes-per-hour Kolberg 9225S sand plant.
“Part of our offer out of Omagh is going to be our washing product line,” Power said. “Astec has been in washing for many years, and there has been good collaboration between the US and Omagh teams to quickly bring the new [Kolberg 9225S] sand plant to the market.
“There’s a real opportunity to internationalise much of our washing product range, tweaking the proven designs of some of the washing modules to best suit European and international customers that tend to work in a tighter footprint than in the US.”
“Over the last couple of years, we’ve been delivering our strategic business plan focused on our employees and working culture and ensuring we are taking care of our customers and getting their feedback about our new products,” Norris said. “The innovation side and coming up with new products is the DNA of our company.”
Power told Aggregates Business that Astec is also reviewing how its existing European dealer network ts into its international growth plans.
Back at the meeting room table at Telestack in late September, Power gave more details about how Astec and Telestack have adapted their global growth strategy to meet prolonged market challenges.
“Eighteen months ago, we’d have said we need ‘X’ amount of people on the [Astec Doogary] shop oor, but they’ve not been required, so we’ve not added employees,” he said.
“On the Telestack side, we’ve let natural attrition do its thing. However, we are still hiring the right people and in the past six months we have recruited industry-leading and proven leaders from the industry.”
Gribben said Hillhead was “a real eye-opener for our potential recruits”.
“From the shop oor worker to management roles and all in between; attendees from local industry suppliers who
may not have been as familiar with Astec saw us and recognised the opportunity to partner with us,” he said. “It’s not because we had a lot of equipment there; it’s the good story we have behind it.
“They saw our latest crushers and know we’ve been in that game for 120 years, and we’ve been in washing since 1965.”
Gribben also discussed Astec’s approach to developing its European dealer network.
“The channel network is always a uid process,” he said. “You need to supply it with a product range. That doesn’t get built in a day.
“We’ll have fewer traditional routes to market in the rst couple of years until we build up the range. We’ll have a combination of dealer-led and direct sales and support. It will depend on the national market.”
Power believes Astec currently has areas of strength in Europe, such as in the asphalt solutions and road-building space with Roadtec’s Shuttlebuggy.
“I was recently with a Roadtec European distributor and a signi cant customer who both loved the Shuttlebuggy solution,” he said. “There is some work to do with other products against some major competitors.
“I sense there is a hankering for a proven alternative or something new that our road technology or crushing and screening range could cater for. There could be quick wins with our modular machines and around parts and service.”
Gribben emphasised how a small number of producers dominate European aggregate production.
“We think we can position ourselves so that if we’re sitting in a board room with
Telestack’s TC 420X track-mounted mobile stockpiling conveyor.
one of them and talking to them about the solutions we offer, including bulk material handling, asphalt, concrete, crushing and screening, and washing solutions, they’d be thinking, ‘Well, so-and-so can’t do this or that’,” he said.
“With the right support, we can give them everything they need now that Astec is expanding further within Europe.”
Looking at Astec’s well-publicised growth aspirations, most of it is outside of the US.
“The company’s asphalt business market share in North America is plus-60%. It’s more about protecting and sustaining it,” Gribben said. “For the concrete plant business, it’s a plus-30% market share.
“On the other hand, Astec has a small portion of the asphalt and concrete market share globally, so those businesses must look internationally. You can’t only do that by building equipment in North America and shipping machines worldwide. You often need a production and after-market support presence in Europe and other big regional markets.”
Power believes Astec now has an even greater mindset.
“Jaco van der Merwe [CEO] and Ben Snyman [group president – Infrastructure] have South African roots. Both have highly successful backgrounds in the global mining equipment and linked technology industry,” he said. “Working in this part of the world [Northern Ireland], you can’t just have a domestic focus. If you don’t export, you don’t sell anything. It’s export or die.”
Power and Gribben stressed that the dif cult off-highway equipment trading
environment has not affected Astec and Telestack’s ambitious research and development (R&D) programme.
“We’re committed to accelerating it,” Gribben said. “On the Telestack project business, 50 to 60% of it is based on our product innovation.”
“We have a couple of PhD researchers based here in Europe that work within the Astec Digital Group,” Power said.
“They are developing ideas around crushing chambers and material ows that our engineers and R&D teams are now looking at.
“I’ve got a regular touch point with them and was amazed at what they were doing. They are talking at some very high-level industry conferences. It doesn’t translate into today’s machines, but it’s shaping what we can do in the future.”
Power said Astec’s machine presence at bauma Munich 2025 (7–13 April), the world’s biggest construction, quarrying, mining and recycling equipment exhibition, will be “limited” as the company focuses on building
Inside the busy Astec Doogary facility.
Astec finished the 44,000ft² expansion of its Astec Doogary facility last year.
its Omagh-based operation. Telestack will be represented by its German dealers, C. Christophel and Kölsch Baumaschinen.
After a lively and insightful hour with Gribben and Power, Aggregates Business walked over the road to the Astec Doogary site with Astec senior customer acquisition manager and Mairead McCrory. Telestack operations director Elaine Mallaghan provided a factory tour.
“We have our standard product production areas and NPI [new product introduction] teams with dedicated engineering and supply chain specialists. We also have manufacturing engineers dedicated to fabrication sourcing, working out what we make and buy,” Mallaghan said.
Looking over the factory oor, Mallaghan pointed out production and training rooms.
“We have 50 production staff here working on product assembly,” she said. “Then there’s the of ce staff, stores and materials people.”
Mallaghan also highlighted various working areas.
“That’s our tracked conveyor line, and next to it is sub-assembly,” she said. “Then we have a packing area at the bottom, handling containerisation. It’s mainly for Telestack products.
“The next production line is for crushers. Five different footprints are working at a time. Then we have the screeners and scalpers production line, with a sub-assembly and a testing area. We have our new stores area on the far side of the factory.
“We use Caterpillar engines in the crushers and screeners and some Deutz engines on the tracked conveyors. We have good relationships with both those suppliers.”
The Astec Doogary production team works Monday to Friday on shifts of either 7.00am to 4.00pm or 8.00am to 5.00pm. Mallaghan said Friday afternoons and Saturdays can offer overtime work depending on product shipping demand.
A look at a Telestack LF 523 tracked conveyor being assembled was followed by some crushing jaws and chambers that arrived from the Astec plant in South Africa, where they are manufactured.
“That chamber there is for a [GT] 440 [HSI – horizontal shaft impactor],” Mallaghan said, pointing at the chamber in question. “That other one there is for a [FT] 4250 [Fast Trax impact crusher.].”
In the outside machine-testing area (where the rain was still pouring down) sat another Astec FT4250 HSI – the rst Omaghbuilt units were demonstrated at Hillhead 2024 – waiting to be put through its paces.
“We do a full day’s pre-delivery inspection [PDI] testing on every machine by our quality team. We look at functional running, production speeds and performance,” Mallaghan said.
“The machine then returns to production if snags need to be smoothed out. New test units undergo wet testing on-site [before being prepared for customer dispatch].”
Before ending the tour, Mallaghan highlighted the importance of Astec’s ongoing investments in the future.
“The nal parts of our recent investment have just been completed with an expansion of our entrance and completion of the surfacing of our external areas,” she said.
“After our 2023 and 2024 investments, we now have a large production footprint with signi cant capacity to increase our machine build run rates for multiple products in the future.”
Five years after being acquired by US quarrying and mining equipment giant McLanahan, Anaconda Equipment is going from strength to strength.
Martin Quinn’s passion for Anaconda Equipment (Anaconda) is evident as he talks about how McLanahan’s signi cant investment in the company he co-founded with Alistair Forsyth in 2008 is paying rich dividends.
“It enabled us to get into the crushing plant game, which we’d wanted to do for some time,” he said. “McLanahan gave us access to quality branded crushing chambers that have been on the Western market for over a century.
“We have also given them a lot of new things around our manufacturing processes. We are paperless, working with iPads, 3D models and advanced software.”
Anaconda design engineer manager Jonathan Scott is alongside Quinn on a tour of the company’s manufacturing headquarters in Ardboe, County Tyrone, Northern Ireland.
“One of our manufacturing processes that McLanahan was interested in was our welders’ use of [digital] tablets,” Scott said.
Quinn said Anaconda has come a long way since its rst paint shop, “which was like a chicken coup”.
“We have a whole new factory now,” he said. “The paint shop runs with a full dry-ondry powder-coating system. We were also the rst manufacturer in the industry to use waterbased paint with zero [carbon] emissions. It’s good to be greener in how we do things.
“We also bene t from the extra factory space and more production capacity McLanhan’s investment has given us.”
McLanahan, a six-generation family business, began its partnership with Anaconda in 2017 to distribute and sell the latter’s line of mobile track equipment. As the relationship between the two companies progressed, it became clear that their values and business styles were closely
aligned, leading to McLanahan’s successful acquisition in 2019.
Anaconda has spent the last 16 years developing its extensive mobile-tracked equipment. McLanahan’s durable and ef cient crushing, scalping, screening, recycling and conveying equipment is sold through a global dealer network. In those 16 years, Anaconda has sold over 1500 units in more than 50 countries across six continents. The business has also expanded operations to sell and distribute parts and equipment from the US.
Quinn was excited when discussing how much Anaconda production has increased since the major investment in the new Ardboe factory.
“We have gone from two to four complete machines a week, so that’s double,” he said. “We have added the jaw and impact crushers – the J12 and I12. We’ve also developed a cone crusher, the C12.
“We launched it at this year’s Hillhead [quarrying, construction and recycling exhibition]. We have got one out being tested now.”
Quinn also pointed to a recently completed C12 plant in the factory’s yard.
“We recently sold two of them, one to our Australian dealer and another to a US customer,” he said. “We test all C12s for 500 hours, so we know they’re good to go when they leave here.”
The direct-drive-technology-inclusive C12 scores highly on accessibility and serviceability. It has ground access, quick set-up times, and timed pre-heat as standard.
“We are also developing a larger J14 jaw crusher and a bigger I14 impact crusher, with a full recirculation option. These will be aimed at mining customers,” Quinn said.
“There’s also a new heavy-duty scalper in development. A lot of new stuff. We’ve also brought in a new engineer to focus on dualpower machines.
“We use various engines in our plants – Caterpillar, Cummins, Deutz and JCB. We nd that different customers prefer certain engines, which we can accommodate.
“We use Smiley Monroe belting for all our mobile conveyors. They are good people and a great company to work with.”
Scott believes Anaconda’s ambitious plant research and development (R&D) programme bene ts from McLanahan’s ongoing investment in the Northern Irish manufacturer.
“When there’s a downturn in the market, you tend to R&D yourself out of it,” he said. “This will enable us to hit the ground running when the market returns.
“We’ve got a lot of experienced engineering talent – around 100 to 110 years of experience between us.”
McLanahan’s acquisition of Leicestershire, England-based CMB International (CMB) in 2022 added CMB’s RubbleCrusher brand to its stable. Its compact crushers can be mounted on wheels, tracks or skids and pulled behind a truck.
Founded to support the ‘zero waste’ approach to the construction and demolition recycling industry, RubbleCrusher equipment is ideal for small- and medium-sized crushing and recycling projects that help contribute to a circular economy.
Anaconda is manufacturing RubbleCrusher units in Ardboe.
“They are getting tight on production space, so we’re building around 12 here for delivery to UK customers before Christmas,” Quinn said. “Because of our facility and capacity, we can take a set of [RubbleCrusher] drawings and build a machine in two weeks.
“It’s very signi cant to be helping RubbleCrusher at present in terms of retaining jobs here. The mobile crushing and screening market is very slow just now. Wars, interest rates and national elections don’t help.
“I think the rst quarter of next year will see demand start to return. The washing plant business is a lot busier. I know McLanahan is very busy on that side of its business.”
Cultivating strong partnerships with exclusive dealers throughout the US has been instrumental in placing nearly 1000 Anaconda units in America over the past decade. Quinn said some of the manufacturer’s US dealers have already seen a market resurgence.
“We have signed a new dealer in Texas whose rst customer order was for eight machines – a cone, a jaw, an impactor, four conveyors and an FTR [feeder] conveyor,” he said.
Along with its production capability, another major advantage Anaconda has in seeking to quickly leverage of any uptick in the global crushing and screening
market is the wide plant size range it can now offer customers.
“Our screeners and scalpers range from 4.5 to 40 tonnes, and our crushers from 6.5 to 70 tonnes,” Scott said, adding that the mobile crushing and screening business is increasingly based on recycled aggregates and other sustainability considerations.
When discussing whether McLanahan plans to produce Anaconda machines in the US to reduce lead times for American customers, he said the company nds the cost of manufacturing locally to be “pretty competitive”.
“We can also maintain quality control by keeping things local,” he said.
Quinn, who didn’t take his GCSEs to take up his rst industry job at Dungannon-based Powerscreen in the 1980s, said Anaconda’s close links to local County Tyrone schools and colleges enable the company to identify and recruit apprentice engineering talent.
“We do a Dragons’ Den event with a local primary school. It may spark something career-wise a few years later,” he said. “Young people are very computer-orientated, but a skilled welder can earn quite a lot of money in this industry.
“With all the health and safety we need to consider now, working in a factory like this is a clean job.”
Quinn himself has a long and varied career history with Powerscreen.
“I worked on the shop oor for a year, and then I was put in the drawing of ce for
eight months. I hated it there and told them that, so I was sent to do plant servicing out of Warrington in Cheshire,” he said.
“I covered the whole of England from there for seven or eight months. I then returned to Northern Ireland before being sent to Greece and Turkey for a while. I then ew out to Denver, Colorado, for two years doing plant installation and maintenance. I covered all of the western side of the US, from Alaska right down to Arizona and across to Kansas, Missouri.”
Following his time in the US, Quinn returned to Northern Ireland to drive lorries for another couple of years before returning to Powerscreen.
“My uncle worked for them and urged me to rejoin the company. That was around 1995,” he said. “He got me to work as a factory foreman for two or three years, and
then I worked as a sub-contractor. There was nothing I didn’t build in that period. I was then made a manager at Powerscreen but didn’t enjoy that, so I left and started Anaconda [with Alistair Forsyth].”
McLanahan – Europe’s marketing and communications strategy lead Stuart McCrum is a recent addition to the Anaconda and McLanahan – Europe team.
“Stuart will be producing a series of ‘how to’ videos: How to start a machine, x certain things, and do various servicing and maintenance tasks,” Quinn said.
“These will be very useful for some of our dealers and customers.”
McCrum expanded on his role.
“From a digital perspective, the Anaconda website will be updated, including its dealer network section,” he said. “We want people to go onto the website and see a global map of where our dealers are and click through to them.
“There will be a renewed focus on the company’s social media and marketing as a whole.”
Anaconda also uses Epicor, an enterprise resource planning system (ERPS) that helps businesses plan production and manage inventory.
“We’ve been using it for over a year and are starting to see its bene ts in just-in-time production,” Quinn said. “Epicor is a good planning aid that tells us what stock to carry. We don’t have any more parts shortages. It’s been a game-changer.”
Are smart glasses, eye or headworn wearable computers, or any other advanced technologies used in Anaconda’s Ardboe operation?
“The software we are using can be used like that. I’ve had a demo, and smart glasses will have a place in this industry,” Quinn said.
“Our software creates a 3D representation of each plant model to help our shop oor team build it by illustrating what part goes where. We also have a health and safety app that the team can ll in [to highlight incidents or concerns].
“The experience of our people means that if they see something isn’t being done right during production, they will call it out there and then. The shop oor team also does ‘Tool Box Talks’ at the start of the shift where [manufacturing and assembly] issues are discussed.”
Anaconda Ardboe factory workers work from 8.00am to 5.00pm Monday to Thursday, and 8.00am to 2.00pm on Fridays.
“Welders can get a bit of overtime, but otherwise we have a single-shift, Monday-toFriday work pattern,” Quinn said.
“Everybody pushes hard and tries to do their best. There’s no such thing as, ‘No, I can’t do it’ or ‘That’s not my job’.”
When a RubbleCrusher screen is being welded, everything a welder needs for each machine they’re working on is in a kit placed in a storage bin.
“They don’t need to go looking for anything,” Quinn said.
“Each welder has two iPads: one with a 3D image of the machine they’re working on, with each section of the machine you touch giving you the part number; the other iPad has machine drawings, a parts list and a kit checklist.”
After highlighting the factory’s steelcutting and sheet-metal-folding machines, followed by the shot blasting area and paint shop, Quinn compared the ultra-modern site he works in today with Anaconda’s early production years.
“We did everything in this shed here,” he said, pointing at an old nearby structure. “That produced two machines a week, with the paint shop – which I called the chicken coup – just behind it.
“Now the factory is future-proofed. We have so much space, we could install a second paint shop if needed.
“We have bene ted from McLanahan’s experience as a much older company. They see things further down the road than I can. They have been very good at letting us run this factory how we want. And in meetings with them, they always ask, ‘Do you want anything?’ or ‘Do you need anything?’. That is very reassuring.”
When stepping into the Anaconda factory yard, Quinn points to a number of machines that have already been sold, bound for places like Australia, Slovenia and the US.
“They are going to our dealers who sell them to quarries, mines and one-man-band operations,” he said. “Each machine you see here has been tested for ve hours to ensure no leaks or other issues before being dispatched to customers.
“I just saw on LinkedIn that a dealer had sold a DF410 scalping screen to a customer wanting it to process rubbish in a recycling yard. They had put the plant in as a demo, and the customer liked it and bought it.” AB
China’s biggest crushing and screening brand is keen to make its mark in Europe.
Mesda, China’s largest manufacturer of crushers and screeners, has begun European plant deliveries.
During a recent trip to Northern Ireland, Aggregates Business met three members of the company’s senior management team – managing director and vice president of international cooperation Bao Jian Wang; business development director Patrick O’Donnell; and president of technology development Xiaoju Song – to learn about Mesda’s exciting growth plans.
“In recent years, we have developed our international business after becoming the strongest brand in China, enjoying a high market share,” Bao said. “We concentrated rst on markets closest to China: Southeast Asia, the Middle East and East Asia.
“Right after the COVID-19 pandemic, we evaluated Mesda’s international strategy. We wanted to enter the European market, which requires a commitment to high quality, standards and advanced technology.”
Bao said Mesda’s longstanding focus on quality and signi cant ongoing investment in
research and development (5–6% of annual turnover) have made it the rst Chinese crusher and screener manufacturer whose machines comply with European off-highway equipment industry standards.
“We believe the products available to European customers will be competitive,” he said.
With its advanced manufacturing capabilities, Mesda, founded by Peter Huang, chairman of the company’s board and largest shareholder, can produce up to 2000 equipment units annually.
The company’s extensive range of fully electric, diesel–electric hybrid, and diesel–hydraulic-powered mobile jaw, cone and impact crushers, horizontal and inclined screeners, and scalpers includes the S5D two-deck diesel-powered scalper.
During the Aggregates Business visit, one of these machines was awaiting dispatch to a European customer from a Northern Irelandbased business partner’s site.
“Everyone is thinking about how to take care of the environment with lower engine emissions, which are very important
for heavy machinery,” Bao said. “Mesda machines for European customers are all Stage-V-emissions-compliant. We offer fully electric and diesel–electric plants and are working on a rechargeable battery solution.
“We want to solve customers’ problems with a more competitive offer and environmentally friendly solutions.”
Bao stressed the fuel cost savings from operating hybrid diesel–electric and fully electric-powered crushers and screeners. He also noted that some European countries’ environmental policies and regulations insist on using electric-powered off-highway equipment for civil infrastructure works, urban aggregate processing, and construction and demolition (C&D) waste recycling.
“We are coming to Europe with two main strategic considerations: to deliver machines and services through a distributors’ channel and to establish manufacturing cooperation with potential partners,” O’Donnell said.
O’Donnell said Mesda, which already has customers in more than 40 countries around the world, will use dealer-distributors in Europe.
“This model is already advanced in certain countries, and we will appoint more dealers in the coming months and years,” he said. “Some long-established dealers are interested in our machines and want to discuss taking them on. They like the dual-power options that we offer with every one of our models.”
O’Donnell and Bao both emphasised that the company can provide custom solutions and that listening to customers and quickly reacting to a changing market are “key values within Mesda”.
“Mesda has been working for years on bespoke machines for speci c customer projects and applications,” O’Donnell said.
Mesda is also establishing plant servicing and replacement parts hubs in Europe.
“They will be a key element in supporting our European dealer network. We are looking at here [Northern Ireland] and Germany for those,” O’Donnell said.
Speaking of Germany, will Mesda be on hand when bauma Munich, the world’s biggest construction, quarrying, mining and recycling machinery exhibition, is being staged again from 7–13 April next year?
“We will be there with some new products,” O’Donnell said.
“This will be the third time Mesda has participated at bauma,” Bao said. “We are looking to recruit more high-level industry professionals as well as broaden our work with partners.”
A Kleemann plant train comprising a mobile jaw crusher and a scalper is processing material to rehabilitate the infrastructure at an Indonesian lignite mine.
The particular challenges in extracting the material are its scattered locations on the mining site and the frequent need for blasting. Given these issues, the ability to easily and exibly relocate the machines was said to be a very important criterion for the mine operator.
The MOBICAT MC 120 PRO is used as a primary crusher, while the downstream MOBISCREEN MSS 802 EVO mobile scalper screens the crushed material.
The rst results show that the mobile plants from Kleemann enable trouble-free processing of the andesite rock. It was also clearly demonstrated that the machines had no problems with the special demands of processing this volcanic rock.
Both machines feature technology
L–R: Mesda managing director and vice president of international cooperation Bao Jian Wang, Mesda business development director Patrick O'Donnell, and Mesda vice president of technology development Song Xiaoju.
that allows operation from an external electric power supply – a future-proof and sustainable option. The infrastructure for this will be realised soon, but until then the operator bene ts from the low fuel consumption of the two machines.
“The option for electrically operating the machines takes a big step toward achieving our sustainability goals. Nevertheless, the fuel consumption is very low when we run the machines on diesel,” mine operator PT Bukit Asam Tbk sales engineer Aditya Maulana Bainal said.
Many of the jaw crusher’s features positively contribute to an ef cient work ow. The hopper extension, for example, makes it possible to take on larger quantities of material and increases the hopper capacity from 10 to 13 cubic metres. The hopper walls can also be folded out by remote control from the ground.
The feed material is screened effectively by the independently vibrating double-deck prescreen, which removes nes via the side discharge conveyor before they reach the crushing chamber. The conveyor unit is also hydraulically foldable and can remain on the machine during transportation.
The rock chisel, a further equipment option for the jaw crusher, can break up larger boulders in the feed material at the machine before it is passed to the crusher. This allows easy removal of blockages caused by material bridging during the passage of material from the prescreen to the crusher. The fact the rock chisel can remain on the machine during transportation is an additional advantage.
Another decisive factor alongside the performance and equipment options that ensure an ef cient and effective production process is the outstanding on-site service.
A Kleemann service technician spent two weeks at the site setting up the machines and instructing the local personnel in their use in readiness for the start of production. This involved a series of theoretical training sessions, practical application training and trial runs. AB
Cemex Egypt has inaugurated its cuttingedge decarbonisation equipment at its Assiut cement plant.
Sustainability is one of the aggregate world’s primary concerns, and organisations across the sector are taking action through new research, initiatives and changes to support this goal.
Anew industry white paper has highlighted electri cation and carbon capture, utilisation and storage (CCUS) as the two keys to achieving greater sustainability in the aggregates industry.
The white paper from ABB details challenges the global cement industry must tackle to decarbonise operations in line with global emission-reduction targets, as well as the vital role technology will play in the success of this endeavour.
This new publication explores cement’s sustainable future by combining insights from a range of key industry players, including customers, technology partners, industry media and associations, with ABB’s domain expertise. It includes discussions around how sustainable cement could be de ned and
practical advice on what steps producers can take now in their decarbonisation journey.
Electri cation is a major component in decarbonising the cement industry. In particular, the ability to replace fossil fuel burners with electri ed or zerocarbon solutions is predicted to help signi cantly reduce emissions in line with industry ambitions.
With more than half of the cement industry’s carbon emissions generated during the calcination process, which requires chemical reaction and large amounts of energy to reach an intense heat, current short-term solutions will not be enough to solve the problem. ABB’s white paper delivers insights on electri cation pathways designed to transform the process used to heat materials to these high temperatures.
“No single player in the value chain has all the answers to cement production decarbonisation, which is why sharing crossindustry insight, like that included in this latest white paper, is so critical to achieving a sustainable future,” ABB Process Industries global cement business unit manager Bodil Recke said.
“We have worked closely with a wide range of industry partners to showcase solutions on maximising sustainability, performance and energy cost savings through a cycle of monitoring, forecasting and optimising energy consumption and supply.
“We are excited to bring this to the market and demonstrate that cement’s carbon-free future is possible.”
The research comes as more companies invest in new equipment to help aid their targets for decarbonising operations.
Cemex Egypt recently inaugurated its decarbonisation equipment at its Assiut cement plant, which was designed and built by local engineering teams. The new equipment can transform residues
into energy by using energy from the current process, combined with a highef ciency separator and modi cations in the calciner process.
This advanced system and operational modi cations achieve approximately 32kg of CO2 reduction per tonne, equivalent to 290,000 tonnes of CO2 annually. According to Cemex, this reduction is comparable to removing 69,000 gasoline-powered passenger vehicles every year.
Additionally, Cemex turns 500,000 tonnes of municipal waste into energy to operate the Assiut plant every year, which is equivalent to the total waste generated yearly in a city with 1.3 million inhabitants.
“The inauguration of the decarbonisation equipment at the Assiut plant is a testament to our ongoing efforts to create a more sustainable future for our communities and the planet,” Cemex Egypt and UAE president Yago Castro said.
“We are committed to leading climate action in the industry, using the highest alternative fuels substitution rate in the cement industry in Egypt.”
The transition towards greener building materials is not one without some
Advanced
systems
business incentive, according to new research by Arizton, a major business market intelligence consultancy.
The world’s green building materials market was valued at US$310.25 billion in 2023 and is expected to reach
US$618.89 billion by 2029, according to the new research. Arizton estimated the 2023–29 period will see the green building materials market grow at a compound annual growth rate (CAGR) of 12.2%. The Assiut cement plant said the
Sharing cross-industry insights is key to decarbonisation in cement production, according to ABB.
market is undergoing signi cant growth, fuelled by various factors including consumers and businesses prioritising environmental sustainability, which is driving demand for buildings with a reduced environmental footprint.
In response, governments all around the globe are enacting stricter regulations and policies to promote energy ef ciency and sustainable construction practices. Such factors create a substantial market for green building materials that adhere to these new standards.
Arizton has found North America leads the global green building materials market, due to its established building codes and certi cations like leadership in energy and environmental design (LEED), increasing consumer demand for sustainability, and stringent energy ef ciency regulations. This market emphasises high-performance insulation, energy-ef cient windows, and building products low in volatile organic compounds (VOC).
Furthermore, the Asia–Paci c region is projected to witness the fastest growth
in the global green building materials market during the forecast period due to rapid urbanisation, a surge in construction activities, government initiatives promoting green construction, and rising environmental awareness in several countries.
Europe’s green building materials industry is bolstered by strict environmental regulations and ambitious sustainability goals, making it a major player in the development and use of bio-based materials such as wood and cellulose insulation.
While the Middle East and Africa and Latin America are in the early stages of green building materials market development, growth is anticipated due to increase government support for sustainable construction, heightened climate change concerns, and the rising demand for energyef cient buildings.
It should be noted, however, that certain green building materials may be limited in some countries, and high initial costs and limited awareness of those materials present challenges.
The research from Arizton highlighted the fact companies are improving cost ef ciency to make green building materials more accessible. Many international players are expected to expand worldwide during the forecast period, especially in the fast-developing in Asia-Paci c and Latin America regions.
These factors are all driving companies to invest in more technologies and products
to support the expanding demand for greener materials.
Heidelberg Materials is continuing to develop circular technologies through its investment in EnviCore, an innovative clean-tech start-up based in Canada that is developing low-carbon solutions.
EnviCore has developed advanced proprietary technology for reprocessing construction and demolition waste into supplementary cementitious materials (SCMs) involving a dry thermochemical process. SCMs are naturally occurring and industrial by-product materials that can be used to replace part of the energy-intensive clinker in cement or concrete, resulting in up to 25% replacement of ordinary Portland cement in concrete mixes.
Based on the results of an upcoming feasibility study, the companies will decide on deploying a pilot SCM production facility close a Heidelberg Materials recycling hub. The facility would validate EnviCore’s technology under industrial conditions and optimise SCM production at scale. Heidelberg Materials also acquired a minority stake in EnviCore as part of this collaboration.
But it is not just policies and new products that organisations are using to shape their sustainability objectives. Many, like the UK Construction Plant-hire Association (CPA), have invested in specialised positions to lead their initiatives and policies in decarbonisation and sustainability.
The CPA recently appointed Luis Bassett
“Decarbonisation is a huge challenge for the sector, a tricky terrain to navigate, and will require support and understanding from those who set environmental policies and targets”
as its decarbonisation and sustainability manager. Bassett, who joined the CPA from the London Borough of Merton, has extensive experience in low-emission solutions for the construction plant sector.
Bassett’s main role at London Borough of Merton was in the cleaner machinery team, which implemented the London NRMM Low Emission Zone on behalf of 32 local authorities.
Bassett became the team’s technical lead on compliance queries, guidance documentation, training materials and emissions calculations. He represented eet and site operators, taking the lead on supplier engagement, most recently specialising in low-emission solutions to site power, including Stage V generators, battery
solutions and ybrid technology.
“I am really excited to join the CPA,” Bassett said.
“Decarbonisation is a huge challenge for the sector, a tricky terrain to navigate, and will require support and understanding from those who set environmental policies and targets.
“I am looking forward to getting to know CPA members and supporting them throughout this journey.” AB
V.E.R.A is a central and eye-catching feature of Cummins’ new 738m² powertrain test facility in Darlington.
Cummins o cially opened its new, fuel-agnostic powertrain test facility in northeast England in July 2024.
It was a great pleasure to meet V.E.R.A. After all, it’s not every day you get the chance to get up close to a virtual engineer robotic assistant, but that is exactly what happened when Aggregates Business was recently introduced to V.E.R.A.
V.E.R.A is a central – and very eye-catching – feature of Cummins’ new 738m² powertrain test facility at its 1800-plus employee state-of-the-art Darlington campus in north-east England.
An expansion of its European Technical Operations (ETO) function, the new facility puts the US on- and off-highway power solutions giant at the forefront of ultra-low and zero-emissions power technologies at a time when the industry is focusing on reducing greenhouse gas contributions and improving air quality.
More than £13 million (US$16.65m) has been invested in the two-storey site that will signi cantly increase Cummins’ testing capacity, focusing on a wider range of vehicles and machinery powered by hydrogen, renewable natural gas, advanced diesel, or battery-electric. It is also the latest standout element of Cummins’ ‘Destination Zero’ strategy, supporting the company’s and its customers’ energy transition goals.
During a presentation before the powertrain test facility tour, Cummins director of laboratory operations within ETO, Tom Partridge, explained that Cummins
engineers are expanding their capabilities using highly advanced dynamometers to test chassis-installed powertrains.
Previously focused predominantly on engine testing, they can now develop full drivelines for on-road use, from compact SUV (sport utility vehicle) size to 44-tonne trucks and double-decker buses, plus off-road use in construction and agricultural machines. These can be two- or four-wheel drive.
The new powertrain test facility and wider engineering focus also support compliance with regulatory standards, including those linked to CO2 heavy-duty vehicle emissions and the upcoming Euro 7, which lays down emission limits for road vehicles and battery durability. Indeed, Partridge noted that 80–90% of powertrain test facility work in its rst two years will involve on-highway trucks due to the need for them to meet Euro 7 rules, which come into force on 1 July 2025. A second powertrain testing chamber within the facility will be used as on- and off-highway customer demand increases in the coming years.
“This is the only facility of its kind that Cummins has globally. We expect to pull in work from all over the world,” Partridge said. “For example, I expect we’ll have 15 to 25 on-highway trucks in a year, each being here for an average of two to three weeks.
“I think it’s also the only facility of its type in Europe, and OEMs [original equipment manufacturers] will likely come and use it
for some of their internal powertrain testing, including some testing of non-Cummins powertrains. In those instances, we have set up the facility so any data relating to those tests will travel via a secure network only the customer can access.”
Partridge also discussed the rationale behind the new Darlington powertrain test facility.
“In 2018, I was asked to look at what it would take to get us where we needed to be beyond Euro 6 [on-highway engine emission regulations] to meet Euro 7, and then assess what was coming at us. Were our existing [Darlington] facilities good enough, or did we need to do something different?” he said
“I spent a lot of time researching this and what became clear was the need to move to vehicle-level rather than just engine-level understanding and development.
“A big part of Euro 7 concerns vehiclelevel CO2 emissions and VECTOs [vehicle energy consumption calculation tools]. When you look at what Cummins can do, we can do engines, transmissions and axles. We are not yet doing tyres, and we are not doing aero [dynamics]. Those two parts are down to [vehicle] OEMs.
“My research and others supporting me found that we needed vehicle-level fuel consumption [testing capability] to have high con dence in our actions. We also needed fuel-agnostic [engine testing capability], an understanding of a much
wider range of duty cycles and, with Euro 7, a deep understanding of how to analyse a lot lower pollutants.
“A whole part of my team is now dedicated to MUAs [measurement uncertainty analysis] to see how accurate we are in measuring low [pollutant] values, be it fuel economy or emissions. It’s a massive part of what we didn’t have to do before.”
Partridge stressed that the new Darlington powertrain test facility had undergone a full computational uid dynamics (CFD) assessment. CFD uses computers to predict liquid and gas ows based on the governing equations of conservation of mass, momentum and energy.
“One of the most important things in making a fuel-agnostic powertrain test facility is the need to be safe in hydrogen mode,” he said. “Over 20 computers took ve to six weeks to do the full CFD. It included analysing what would happen if we had a credible hydrogen leak on a vehicle and an ignition source.
“The CFD told us we needed to protect the people in the control room and our assets at the back of the facility. As a result, the facility’s concrete walls have the highest level of blast protection, including tethered blastrelief panels.
“In the worst-case hydrogen-leak scenario, the walls would move but not crack and carry on supporting everything. This was a big part of the blood, sweat and tears
Emma [Laidler, Cummins ETO powertrain operations manager] as project leader and I experienced during the build. It drove up costs, as did the COVID-19 pandemic, which increased the cost of building materials and made concrete harder to source.
“To get the facility built in two years is pretty good given its size and complexity.”
Partridge highlighted that besides supporting the development of cleaner power solutions, the Darlington powertrain test facility also provides local environmental bene ts as part of its daily operation.
The advanced dynamometers feature energy recovery systems to generate £10,000 worth of free electricity a month that can be used across the Cummins site and reduce the impact on the local grid. Additionally, water consumption is reduced by harvesting rainwater, using a similar system already in place in the engine plant.
Cummins’ Darlington campus also has a pilot centre for customer equipment repower.
In 2023, 72,325 engines were assembled and shipped from Cummins’ Darlington engine plant.
The pilot centre and powertrain test facility operate as the company’s ETO division.
The Darlington engine plant assembles Cummins’ 3.8–9-litre diesel and natural gas-powered engines, 72,325 of which were assembled and shipped in 2023 alone. For context, Cummins’ global off-highway business sold 200,000 engines last year. The specialist marine (engine) up- t centre is another notable feature of the plant.
Darlington is also home to Cummins’ Emissions Solutions division, where automotive and industrial after-treatment production, development and testing occur. A total of 41,785 after-treatment solutions were shipped from the site last year. Furthermore, the Darlington campus houses Cummins Business Services, which includes shared services for HR, nance, IT and other resources.
Partridge highlighted that further earmarked investment in the Darlington site includes a new $30 million Long Block (engine assembly) line, upgrades to the Short Block (engine assembly) line, and the transfer of the company’s Euro 6 Module line to Darlington.
In an earlier presentation, Cummins head of global off-highway business Marina Savelli outlined the company’s global footprint. Cummins, whose product portfolio includes 2–15-litre on- and off-highway diesel or
alternative power engines, has 75,000 employees and trades in 190 countries and territories. The 105-year-old business has 19,000 certi ed dealer locations, with its off-highway OEM customers including Komatsu, Hyundai, LiuGong, Hitachi Construction Machinery, Volvo, Liebherr and Doosan.
Cummins’ 2023 revenue stood at US$34.1 billion (£26.6b) – with 80% relating to on-highway and 20% to off-highway business. Its EBITDA (earnings before interest, taxes, depreciation, and amortisation) in 2023 was 15.4%, and last year saw US$1.4 billion (£1.09b) invested in research and development.
The company also launched Accelera by Cummins, a signi cant step forward in its efforts to achieve its ‘Destination Zero’ strategy. It focuses on evolving Cummins technologies to reach zero emissions across its product portfolio. The Accelera by Cummins launch followed the previous year’s acquisition of Meritor, a major global supplier of drivetrain, mobility, braking, after-market and electric powertrain solutions for commercial and industrial vehicle markets.
Under its ‘Planet 2050’ environmental sustainability strategy, Cummins aims to reduce Scope 3 absolute lifetime greenhouse gas (GHG) emissions from its newly sold products by 25%. It is also targeting a 55-million-tonne cut in Scope 3 GHG emissions from its products in the eld, a 50% reduction in absolute GHG emissions from Cummins’ facilities and operations, and a 50% drop in volatile organic compound emissions from plant and coating operations. Cummins is devising a circular lifecycle plan for every (engine) part to ‘use less, use better and use again’.
The company wants to generate 25% less waste in facilities and operations as a percentage of revenue. It intends to reuse or responsibly recycle 100% of packaging plastics while eliminating singleuse plastics in dining facilities, employee amenities and events. Cummins aims to cut absolute water consumption in its facilities and operations by 30%.
Darlington engine plant operations manager Patrick McGonigal told Aggregates Business that, in 2023, 72,325 engines were assembled at the plant and shipped – with a daily target of 280 fully assembled units (including testing). Equipped with the latest robotic and other technology to assist employees, the engine plant runs three shifts Monday to Friday: 6.00am to 2.00pm, 2.00pm to 10.00pm and 10.00pm to 6.00am. Plant maintenance shifts are often also available as overtime on Saturdays.
McGonigal stressed Cummins’ emphasis on plant employee health, safety and welfare.
Popular company-organised social events involving plant employees and their families are held several times a year. At a day-to-day level, large whiteboards are prominently placed around the plant to encourage employee feedback, including suggestions to improve each stage of the engine assembly process.
Among several large and colourful company message boards near the entrance to the plant is one detailing ten elements of ‘Operational excellence’:
• Put the customer rst and provide real value
• Synchronise ows (material, physical and information)
• Design quality in every step of the process
• Involve people and promote teamwork
• Ensure equipment and tools are available and capable
•Create functional excellence
•Establish the right environment
•Treat preferred suppliers as partners
•Follow common problem-solving techniques
•Use Six Sigma as the primary improvement method
Another standout feature of the facility is its dedicated training and education area, where younger employees can hone the skills required for engine assembly under the guidance of experienced plant technicians.
Speaking in a Q&A before the tour of the Darlington engine plant, Cummins director of off-highway sales Ali Baynes outlined that 80% of the company’s off-highway sales are related to construction customers, 10% to agriculture, and 10% to defence and underground mining.
“The construction market is experiencing quite a decline in Europe, by 20% or more. Although we predicted that to some extent, it’s quite a challenge for us,” she said.
“In other parts of the world, though, we are seeing market stability or some levels of growth. China is holding up quite well and North America is slightly more progressive than expected in that region.
“Overall, the global market is attish. There are a lot of changes in [national] governments this year. We are keeping a close eye on major infrastructure projects kick-starting again.
“When you consider the longer term and at what point the construction [machine] market starts to transition away from diesel, we have a pretty good idea that that is a long time away. In the meantime, Cummins is investing signi cantly, initially in on-highway platforms. This allows us to see how this investment impacts at scale and how these platforms can be adjusted and adapted for construction and other off-highway markets.”
Baynes said Cummins has also brought forward some of its product development, including the Intermat 2024 Paris launch of its Next Gen X15 Performance Series. The platform offers 10% better fuel economy than
its predecessor, improved GHG ef ciency, and longer service intervals.
Cummins’ construction business is also being more targeted in its approach to growing market share.
“In the construction [machine] market, we have traditionally seen growth solely linked to changes in engine emissions regulations,” Baynes said. “We are now focused on understanding where we will take market share from our competitors over the next four years. We have a good story about our investment and some of our other capabilities. I think we can help a lot of large and critically important off-highway OEMs be successful more quickly.
“We also see a lot of interest from off-highway machine customers in what we’re doing on hydrogen internal combustion engines [for on-highway truck customers]. A lot want to just test out the technology, even if it’s still up to 10 years from coming onto the [off-highway machine] market.” AB
The global aggregates industry’s demand for wet processing technology is buoyant, as many leading players continue implementing their ambitious growth plans.
McLanahan executive vice president of sales and business development Cory Jenson was very upbeat when he spoke to Aggregates Business in late November after returning from a visit to Diefenbach’s production facility in Italy.
Acquired by McLanahan last year, Diefenbach is among the industry leaders in liquid–solid separation, specialising in lter presses and thickeners for customers worldwide. As part of its ongoing investment in the brand, McLanahan is looking at an additional site to increase Diefenbach’s production footprint.
Another key Diefenbach development is a new lter press plate cloth change-out solution that Jenson said will reduce plate
cloth replacement from 10–15 minutes to just two.
In addition to signi cant time-saving bene ts and increased uptime, lter press operators do not need to use heavy lifting equipment and climb on top of the machine to reach down to the lter press plates to make plate cloth change-outs. All plate cloth change-outs can be done standing on a side-on lter press platform.
This patent-pending feature will be available on all McLanahan and Diefenbach Overhead Beam lter presses.
“We hope to have something on this on display at bauma 2025 in Munich [7–13 April],” Jenson said. “It solves a big tailings problem for many companies across the aggregate, sand and mining industries. It
should also signi cantly help with gold and mineral concentrate lters.
“Around bauma, people should be able to order Diefenbach or McLanahan lter presses with this solution. While lter presses that include the rapid [plate cloth] changeout solution will cost a little bit more, the customer will gain signi cant time savings and health and safety bene ts.”
Depending on the type of material, Jenson explained that the typical 220-plate lter press requires roughly 4.5– 5 plate cloth change-outs a week, averaged over 2000 hours.
“When you consider that these machines are working 48 to 50 weeks a year, that’s a lot of saved time,” he said. “You can quickly pull the cloth off and inspect the plate at eye level in a couple of minutes. We think it’s going to be a very popular option.”
McLanahan acquired the Leicestershire, England-based CMB International (CMB) in 2022. Along with its very popular RubbleCrusher-branded compact crushers
that can be mounted on wheels, tracks or a skid and pulled behind a truck, CMB is renowned for its wide range of screening products, including inclined, horizontal, dewatering, coal, asphalt, four-bearing and grizzly screens.
Now rebranded as McLanahan products, Jenson said the heavy-duty screens are big sellers as part of a McLanahan wash plant and crushing set-ups or as individual screener solutions.
“We can make a screen to t any customer site footprint,” Jenson said. “Some of our competitors won’t make a customsized screen.
“The way we’ve developed our screens since acquiring CMB means we can easily adjust their size. We have some screen options without any bearings that you must lubricate daily.
“One major UK company wants this as standard on all our screens installed in its asphalt plants. This means they don’t have to go up and down the hot asphalt towers daily to lubricate screens. If they need to change out the [screen] vibratory mechanism, they don’t have to repack bearings on the screen up in the tower. They can unbolt components and put on new ones, and we can work on repacking bearings in a clean workshop environment.
“This is important from the maintenance perspective, as well as the often lack of skilled labour availability.”
Jenson commented on the wider McLanahan group’s current trading health.
“We’re extremely busy. Next year, with our order backlog, it will be even busier than this year,” he said. “We’ve hired many people and are looking to hire many more in 2025.
“Some of our biggest growth is in the washing space, and the UK and mainland Europe are key developing markets for us. We have our Northern Ireland-based production facilities for McLanahan on the washing plant side and Anaconda’s for crushing and screening plants.
“We also produce some Eagle Iron Works’ washing equipment in Northern Ireland. We have some Eagle Iron Works’ washing equipment, including very nice sand classifying tanks, at a big new tunnel project connecting Italy and other parts of Europe.
“The sand classifying tanks are helping to produce very high-spec products. We already sell many of our sand classifying tanks in North America. They use sophisticated programmes to blend sand from highly variable feeds to produce spec products.
“We think the sand classifying tanks can do well in Europe, as we don’t have any competitors making them.”
Jenson said McLanahan is keen to hold further customer open days in the UK and mainland Europe after the success of an October 2024 event at customer Goonvean Aggregates’ Melbur Quarry in St Austell, Cornwall, south-west England.
McLanahan held short education sessions to provide more than 60 attendees with key learning opportunities around construction and demolition (C&D), recycling and tailings, and water management.
Goonvean Aggregates partnered with McLanahan to design a wash plant with water recycling capabilities that could integrate with its existing crushing plant or be fed independently. McLanahan supplied an UltraWASH Modular Wash Plant,
of sales and business development Cory Jenson; McLanahan business line director David Hunter.
UltraSAND Plant, and 10m EcoCycle HighRate Thickener.
“The feedback from the Goonvean Aggregates open day has been phenomenal. Attendees climbed all over the wash plant and said how robust it was and that they could see the difference in quality,” Jenson said. “It’s been installed for a couple of years, and a guy at the open day told me that he’d been running wash plants for 30 years and had never seen a wash plant in such a good state after that amount of production time. He was very impressed.”
McLanahan will make further strategic acquisitions in Europe in the next couple of years, following successful moves for Anaconda, Diefenbach and CMB.
“We have other deals in active discussion. There will be news next year, possibly before or at bauma 2025,”Jenson said.
CDE, a major wet processing plant manufacturer, has supplied a 250-tonneper-hour set-up for the Swedish rm
CDE and Swerock have enjoyed a very successful business relationship since 2005.
Swerock. The solution is recovering sand and aggregates from quarry overburden for Swerock’s concrete business.
Part of the Peab group, Swerock is one of Sweden’s largest suppliers of materials and services to the construction industry. The company provides services across the Nordic region, including supplying concrete, gravel and rock materials, transport and construction machinery, and environmental services such as recycling, soil remediation and water treatment.
CDE and Swerock have a long-standing relationship, with CDE installing Swerock’s rst project at its Blentarp site in 2005.
“Having worked with CDE for many years, we knew they could deliver a plant to meet our speci c requirements,” Swerock operations manager Christian Lindgren said.
“As this plant represents a signi cant investment, and as one of the rst to supply this type of material for concrete production in Sweden, we wanted to make sure it is capable of meeting our needs.
“With our historical relationship, we have a lot of con dence in CDE’s process and technology and we’ve been glad to partner with the team again.”
One of the greatest concerns Swerock wished to address was the amount of quarry waste the rm was producing.
Quarry waste can be a challenge for operators across Scandinavia and wider Europe, potentially leading to surplus stockpiles that can block access to reserves, take up valuable space, and be costly to store or dump.
Swerock sought to overcome this challenge by consulting wet processing experts CDE to design and install a plant that could process large amounts of overburden, also known as moraine, a by-product of quarry operations. This would reduce costs, stockpile storage, and produce material that could be repurposed into the industry to help reduce waste and maximise resources.
Given Sweden’s material shortage, the ability to recycle is particularly important, so the new investment contributes to Swerock’s sustainability and self-reliance goals.
Investing in technology to respond to this speci c problem solidi es Swerock’s commitment to producing in-spec concrete in-house in its concrete division. It also allows the rm to better adapt production to customers’ needs.
This new pioneering plant at Swerock’s site in Blentarp processes feed material at a rate of 250 tonnes per hour to reduce the organics’ content in the output.
It comprises CDE’s R4500 primary feeding and scalping screening system, the M4500 modular wash plant to pre-screen the material with two integrated counter ow classi cation units (CFCU) density and sizing classi cation systems, the AggMax scrubbing and classi cation system, the EvoWash sand wash system, AquaCycle thickener, and the organics static screen.
Swerock requires a very speci c sand output, 0–2mm, with tight speci cations, which leaves little room for error. This is an important component in concrete production and replaces natural gravel. The feed material’s variable particle size distribution (PSD) was a major challenge in ensuring an in-spec 0–2mm fraction output.
This solution has two CFCU density and sizing classi cation systems to increase the separation surface area and increase organics removal. All of the ne sand removed in the CFCUs is captured and dewatered as a ne sand product through the additional EvoWash and stockpiled.
To provide the best opportunity to achieve the required gradation, the CFCUs are used directly after the cyclones. The cyclones perform the primary removal of the -63μm, with the over ow from the cyclone going to the AquaCycle. The cyclone under ow passes directly into the CFCUs, where a variable rising current of water and a uidised sand bed impact the amount of ne sand removed, generally up to 0.25mm.
CDE introduced the ability to remove some 0.25mm material after the CFCU, which can either be discharged away from the 0–2mm washed sand or proportionally reintroduced to it to nurture the 0–2mm grading according to the requirement.
The CFCU will continue to smooth out the variability of the incoming material to ensure much more consistent output sand while removing the lightweight organic material.
The use of a unique corrective solution eliminated any concerns around removing too much sand at the bottom end of the sand curve. This gave more control over the gradation of the nal sand product and allowed for adjustment to ensure the required speci cation was met while providing exibility to produce other speci cations if desired.
CDE incorporated an AggMax to address the concerns about lignite and organics throughout the feed material. The AggMax has an integrated trash screen that effectively removes organics and other lightweight contaminants, ensuring production of the highest-quality nal aggregates.
The static screen on the recycled water circuit also suits the overburden feed material because it catches many of the lightweight, oatable materials that the cyclones carry to the AquaCycle. These materials can saturate and become suspended in the water, leading to blocked spray nozzles, but the static screen reduces the potential for this situation.
The plant allows Swerock to produce seven products: the 0–2mm used in concrete production; two additional sand fractions in 0–0.25mm and 2–4mm; and four aggregate fractions in 4–16mm, 16–32mm, 32–100mm and +100mm used for a variety of construction and infrastructure projects.
Lindgren said the new plant is allowing Swerock to produce a highly speci c, quality sand contributing to self-suf ciency.
“We are really focused on becoming more sustainable and reducing our carbon footprint, and it’s technology like this that is driving us towards our goals,” he said.
“This plant is allowing us to enhance other business divisions internally, so we can focus on our commitment to become more sustainable and offer more durable products of consistent quality to our customers whilst also allowing us to reduce the amount of quarry waste that we’re stockpiling and re ne products from surplus material.
“This is an exciting part of our journey, and we look forward to our continued partnership with CDE.”
CDE head of business development for Europe Eunan Kelly said these plants are the future.
In collaboration with Avesco, Terex Washing Systems is providing Ghelma with a solution that turns previously waste material into high-value products.
“It’s been a pleasure to work once again with Swerock. Over the years, we’ve nurtured and developed a fruitful relationship and we’re delighted that they chose to partner with us on this pioneering project,” he said.
“The remit was a challenging one that both Swerock and CDE worked long and hard on together. It is always satisfying to see the sand fall off the end of the belt on complex projects like this one.
“Through our long-standing relationship with Swerock, we have continued to act upon the learnings and feedback from previous projects to ensure we were always one step closer to the perfect solution.
“The longitude and evolution of our work with Swerock is a real-life embodiment of our ethos of putting our customers rst. We’re committed to creating a sustainable future for all, and designing and installing a plant like this cements our dedication to building our best world, a tonne at a time.”
Ghelma, a leading Swiss construction company, needed a solution to process excavation material, sand and gravel, much of which was previously considered waste.
To address this challenge, Terex Washing Systems, in close partnership with Avesco, delivered a bespoke washing solution tailored to Ghelma’s needs.
Avesco is the of cial distributor for Terex in the Swiss market. The family business, which has been around for more than 150 years, focuses on supplying capital construction equipment to customers in Switzerland, the Baltic States (Estonia, Latvia, Lithuania), Finland, Austria and Slovenia.
The companies have collaborated on various tailored solutions for customers, including for Albin Borer, a Swiss company focused on construction, infrastructure and material treatment. Their collaboration saw them design and commission an end-toend excavation wash recycling system, which helped turn Albin Borer’s waste into a saleable product.
The Terex and Avesco partnership has helped deliver Ghelma a modern system
designed to maximise the recovery of highvalue materials and integrate state-of-the-art washing and recycling technology.
The design included an H9 Feeder, PS60 Logwasher, FM60C two-grade double wash sand plant, 12x5 two-deck pre-screen, 6x2 trash screen, and 8x4 three-deck full rinser post-screen. Also included were an FM60C two-grade double-wash sand plant, a dewatering system, TC4026 stockpile conveyors, a freshwater pump and a settling pond.
The PS60 Logwasher enables robust scrubbing and removal of tough clays and contaminants suited to Ghelma’s natural sand application. It was key to scrubbing the heavily contaminated material, ensuring a clean material output.
The 12x5 two-deck pre-screen ef ciently pre-screens material to remove undersized material and improve yield. The 6x2 trash screen helps separate unwanted material, including organics and debris, further enhancing material quality. The 8x4 threedeck full rinser post-screen can be used to rinse and classify materials into nal products for the Ghelma operation.
The FM60C two-grade double-wash sand plant is capable of precise sand classi cation and washing, which helps Ghelma produce a range of high-quality sand materials. The freshwater pump helps ensure water circulation while processing occurs, while the settling pond enhances the site’s water treatment and recycling, supporting its water management.
In collaboration with Avesco, Terex Washing Systems is providing a solution that turns what was previously waste material into high-value products. By processing excavation material and natural sand and gravel, the plant produces a range of materials for the construction material market.
Ghelma produces various products, including +32mm oversize, 16–32mm aggregate, 8–16mm aggregate, 4–8mm aggregate, 1–4mm sand, 0–1mm ne sand, and trash, mainly organics.
The collaboration throughout the project ensured that Ghelma could maximise
material recovery while reducing operational costs associated with waste disposal. The plant’s ability to process and re ne what were previously considered unusable materials into high-quality products is cost-effective and supports Ghelma’s commitment to sustainability and the circular economy.
Terex Washing Systems worked closely with Ghelma and Avesco throughout the project, maintaining strong communication and collaboration at every stage. From the initial consultation to the plant’s installation and commissioning, Terex Washing Systems’ teams ensured the solution was customised to t Ghelma’s exact needs, providing ongoing support to ensure the plant’s performance exceeded expectations.
The advanced washing solution delivers high-quality materials and promotes a circular economy by recovering and recycling resources. Ghelma can convert waste into valuable construction materials, minimising the need for virgin resources.
The project has delivered Ghelma multiple bene ts, including waste reduction, resource ef ciency, water conservation, cost savings and sustainable growth.
The new system can help Ghelma divert materials from land lls and repurpose them for construction while maximising the use of all materials processed at the site. The system enables ef cient water management and conservation through on-site water recycling through the integrated water treatment system.
These factors have led to increased cost savings, mainly through reduced disposal costs and the ability to generate revenue from recycled products. Sustainable growth also has a wider impact, reinforcing Ghelma’s commitment to sustainability and the circular economy.
“This advanced washing plant enhances Ghelma’s operational ef ciency and supports its sustainability goals by promoting the circular economy and conserving resources,” Terex Washing Systems said.
“This project is a testament to the bene ts of working closely with customers and distributors to achieve long-term success.”
11–14
bauma CONEXPO INDIA 2024
New Delhi, India
Organiser: Messe München Tel: +49 89 949-20255
Email: franziska.dorfmueller@ messe-muenchen.de
Web: bauma.de/en/india
21–23
World of Concrete 2025 Las Vegas, NV
Organiser: Informa Tel: +1 212 951 3525
Email: registration@ worldofconcrete.com Web: worldofconcrete.com
12–13
SaMoTer Paving Show and Congress 2025 Verona, Italy
Organiser: Veronafiere Tel: +39 045 8298 133
Email: exhibitors@samoter.com
Web: samoter.it/en/paving-showand-congress-2025
25–27
World of Asphalt 2025
St. Louis, MO
Organisers: NAPA, AEM & NSSGA
Tel: +1 (864) 208 3372
Email: exhibitors@aem.org
Web: worldofasphalt.com
25–27
Agg1 2025
St. Louis, MO
Organiser: NSSGA
Tel: +1 (800) 867 6060
Email: exhibitors@aem.org Web: www.agg1.org
APRIL
07–13
bauma 2025 Munich, Germany
Organiser: Messe München
Tel: +49 89 949 11348
Email: info@bauma.de
Web: bauma.de/en/trade-fair
As Australia’s longest running mining show, Asia-Pacific’s International Mining Exhibition (AIMEX) has a long, established history of showcasing and supporting the latest trends and developments in the industry.
AIMEX is relocating and will call South Australia home for the next 10 years, following market feedback and strong support from the local government and key mining players.
The move marks an exciting new chapter for the event and the region’s resource sector, with the state leading the way in future-focused mining.
AIMEX offers unparalleled opportunities to connect with Australia’s largest community of mining suppliers and professionals in an environment that stimulates innovation and collaboration.
MOBIREX MR 130 PRO
Performance, precision and sustainability. The MOBIREX MR 130 PRO mobile impact crusher excels with outstanding performance in a diverse range of applications. With its double-deck post screening unit, the plant ensures top product quality with up to two graded end-products, while achieving impressive throughput rates of up to 600 t/h in natural stone and recycling. The all-electric E-DRIVE is not only efficient, it can also be operated with zero local emissions. Operation is intuitive thanks to SPECTIVE components. The MOBIREX MR 130 PRO –the sustainable powerhouse.
www.wirtgen-group.com/mr-130i-pro-kleemann