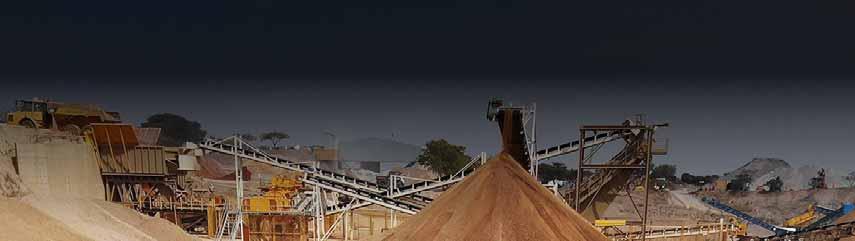

Pilot Crushtec’s Stage-V powered TwisterTrac p48
HEAD OFFICE
EDITOR: Guy Woodford
ASSISTANT EDITOR: Liam McLoughlin
CONTRIBUTING
EDITORS: Munesu Shoko, V.l. Srinivasan, Shem Oirere, Partha Basistha, Eugene Gerden, Shadrack Kavilu
EQUIPMENT EDITOR: Mike Woof
DESIGNERS: Simon Ward, Andy Taylder
PRODUCTION MANAGER: Nick Bond
OFFICE MANAGER: Kelly Thompson
INTERNET, IT & DATA SERVICES DIRECTOR: James Howard
DATA & MARKETING MANAGER: Alan Cansick
WEB MANAGER: Sarah Biswell
SOCIAL MEDIA MANAGER: Tatyana Mechkarova
MANAGING DIRECTOR: Andrew Barriball
PUBLISHER: Geoff Hadwick
CHAIRMAN: Roger Adshead
ADDRESS
Route One Publishing Ltd,
Second Floor, West Hill House, West Hill, Dartford, Kent, DA1 2EU, UK TEL: +44 (0) 1322 612055 FAX: +44 (0) 1322 788063
EMAIL: [initialsurname]@ropl.com (gwoodford@ropl.com)
ADVERTISEMENT SALES
SALES DIRECTOR:
Philip Woodgate TEL: +44 (0) 1322 612067
EMAIL: pwoodgate@ropl.com
Dan Emmerson TEL: +44 (0) 1322 612068
EMAIL: demmerson@ropl.com
Graeme McQueen TEL: +44 (0) 1322 612069
EMAIL: gmcqueen@ropl.com
SUBSCRIPTION / READER ENQUIRY SERVICE
Aggregates Business is available on subscription at the rate of: £85 / US$145 / €111 per annum. Single copies £20 / US$35 / €26 Email subs@ropl.com for further details. Subscription records are maintained at Route One Publishing Ltd.
SUBSCRIPTION / READER ENQUIRIES TO: Data, Route One Publishing Ltd, Waterbridge Court, 50 Spital Street, Dartford, Kent DA1 2DT, UK
TEL: +44 (0) 1322 612061 FAX: +44 (0) 1322 788063
EMAIL: data@ropl.com
No part of this publication may be reproduced in any form whatsoever without the express written permission of the publisher. Contributors are encouraged to express their personal and professional opinions in this publication, and accordingly views expressed herein are not necessarily the views of Route One Publishing Ltd. From time to time statements and claims are made by the manufacturers and their representatives in respect of their products and services. Whilst reasonable steps are taken to check their accuracy at the time of going to press, the publisher cannot be held liable for their validity and accuracy.
PUBLISHED BY © Route One Publishing Ltd 2024
AGGREGATES BUSINESS USPS: is published six times a year. Airfreight and mailing in the USA by agent named World Container Inc, 150-15, 183rd Street, Jamaica, NY 11413, USA.
PERIODICALS POSTAGE PAID AT BROOKLYN, NY 11256
US POSTMASTER: Send address changes to Aggregates Business, World Container Inc, 150-15, 183rd Street, Jamaica, NY 11413, USA.
Air Business Ltd is acting as our mailing agent
PRINT: ISSN 2051-5766
ONLINE: ISSN 2057-3405
PRINTED BY: Warners (Midlands) PLC
stablished in 1934 as only the second cement manufacturer in South Africa, AfriSam has built an impressive 90-year legacy of quality and expertise that ranks among the world’s best.
According to Richard Tomes, AfriSam’s sales and marketing executive, this success is driven as much by the company’s technical performance and service as by remaining relevant and true to its communities. In a fascinating thoughtleadership piece given to ABI, Tomes highlights the leading role taken by AfriSam in driving product quality alongside rising sustainability concerns to reduce carbon emissions. At the same time, the company plays a broader role in strengthening livelihoods and cohesion in the economies and communities in which it operates.
AfriSam’s 90 years began as Anglovaal Portland Cement Company, diversifying early into readymix concrete and aggregate production as Anglo Alpha. Its more recent history saw the business acquired by the global leader in cement, Holcim, before returning to local ownership. Tomes points to the world-class skills and infrastructure within the business, an example of which was its Ulco cement factory being ranked as the third-best performer in the Holcim group during its time in that stable.
“To reach 90 years old in a sector like construction demands a constant commitment to being ahead of the game and delivering leading-edge solutions at the highest level,” says Tomes. This allowed AfriSam to play a central role over the years in iconic structures from Johannesburg’s 50-storey Carlton Centre in the 1970s to the Gautrain in the lead-up to the 2010 Soccer World Cup.
Today, the company is among the most trusted names in South Africa’s readymix industry, having retained and enhanced its institutional skills in concrete technology. This has been vital for the beleaguered local construction sector, where the right-sizing of
most large contractors has left them with fewer in-house resources.
“Our many years in business have taught us more about our broader responsibility, and we are also proud to play an active role as responsible corporate citizens,” explains Tomes. “This ranges from our leading efforts in making cement production more sustainable, to supporting initiatives that build communities and promote social cohesion.”
AfriSam says it was the first cement manufacturer to launch a ‘green’ cement by scientifically adding cementitious extenders to reduce the content of energy-intensive clinker while not compromising quality or performance. Through its continuous investment in research and development, it has taken South Africa to the forefront of cement technology related to using ground granulated blast furnace slag (GGBFS) and pulverised fly ash as extenders.
Returning to AfriSam’s positive local economic impact over the decades, Tomes stresses the key role played by its cement, concrete and aggregate experts in building the country’s infrastructure to its current levels.
“Irrespective of economic cycles and other disruptions, we consider it essential to maintain and sharpen our expertise and industrial capacity in service of Africa’s development,” he says. “Even if economies stagnate for long periods, they can recover if there is a core of critical skills to build the necessary infrastructure.”
In this way, he says, AfriSam creates opportunities for communities to build livelihoods, especially in an environment where housing shortages are common. Alongside its cutting-edge technology, for instance, is its quality Starmix readymix solution—a costeffective product for residential builders that can be ordered in small quantities.
“We recognise the value of sport in improving lives and attitudes, so over the years, we have partnered with teams from Orlando Pirates [football] to the Springboks,” says Tomes. “Youth entrepreneurship is another important focus for us to inspire and empower future generations.” GW
“LSC Infratech is continuing its multi-site, new technology-led, business-upgrade programme with its Haldwani crushing facility in North India, the latest site to benefit” p11
Further cementing a legacy
Pan-United eyes growth after leadership shake-up; Kleemann impresses in Istanbul Financial Centre (IFC); Amsons moves to acquire Bamburi Cement
All the key events in the quarrying & aggregates world
Metso lays out path to an exciting crushing & screening future
CRUSHING & SCREENING – 2
Astec and SBM Mineral Processing lit up Hillhead with their focus on product innovation and global sales growth 30 LOADING
OEMs have been unveiling their next-gen machines with an eye-catching number of electric wheeled loader and excavator models
New Volvo CE rigid dump trucks & a major new West African partner for Rokbak 36 CONVEYORS, STACKERS & STOCKPILERS
New models and a big focus on sustainability are enriching the quarrying conveyors market 40 SCREENING BUCKETS & ATTACHMENTS
Maximising screening bucket efficiency leads to high-quality aggregates at a reduced cost per tonne
Powering into new export markets
42 DEWATERING
46 ASPHALT PLANTS
V-powered TwisterTrac widens export markets for Pilot Crushtec
Why electric dewatering pumps are becoming an increasingly attractive option to aggregates site operators
A new green-hydrogen-burner generation system from Benninghoven is making asphalt production even more sustainable
Stage V-powered TwisterTrac creates new export markets for Pilot Crushtec
50 TROMMELS
The new EDGE 10-metre trommel is claimed to do the
08 MARKET REPORT
Growing emphasis on premium crushing and screening plants and wider technology-led quarry operations enhance Indian aggregates-production efficiency
16 INSTACRETE
A Kenyan concrete & mortar revolution
24 INTERVIEW
11 QUARRY PROFILE
LSC Infratech investment galvanises Haldwani site
Brian James on why new developments are putting recycled aggregates use in jeopardy
Singapore-listed concrete innovation leader Pan-United Corporation (Pan-United) has appointed May Ng as the executive chair of the company’s board and Ken Loh as CEO.
Ng and Loh, who have been instrumental in Pan-United’s growth, will relinquish their positions as CEO and COO of Pan-United, respectively, and assume their new appointments immediately. This continuity in leadership ensures a stable transition and a clear path for Pan-United’s future growth.
Chan Wan Hong has joined the Pan-United board as an independent director, bringing over 25 years of legal expertise. Concurrently, Fong Yue Kwong has been redesignated from independent director to lead independent director. Both positions are also immediately effective.
Ng succeeds Tay Siew
Choon, who retired as a director of Pan-United under Regulations 89 and 90 of the company’s constitution at the annual general meeting held in April 2024. The board of directors thanked and recorded their deepest gratitude and appreciation to Tay for his invaluable contributions to Pan-United during his nearly 20-year tenure as a director, four years of which he served as chairman.
Ng has been CEO of Pan-United since March 2011 and has led Pan-United’s transformation into a global leader in low-carbon concrete technologies. She said: “We are very pleased to announce Ken’s appointment as CEO. Ken has been instrumental in our transformation from a brick-and-mortar concrete company to a global leader in low-carbon concrete technologies. We have worked very closely over the years,
and I look forward to continue working with him to innovate and decarbonise our world with concrete to ensure a safer world for future generations.” Loh first joined Pan-United as general manager in 1999, with the mandate to spearhead the growth of Pan-United’s then-new ready-mix concrete business. Under his steady and strong leadership, Pan-United has become Singapore’s largest concrete producer, with an established regional presence in Malaysia and Vietnam. Loh said: “I would like to thank May for her trust and the Board of Pan-United for their confidence and support. I aim to build a strong future for Pan-United, guided by our vision to become a technology company in the concrete and logistics space and to fulfil our mission to be the global leader in low-carbon concrete technologies.”
Kleemann’s MOBIREX MR 130i EVO2 mobile impact crusher and MOBISCREEN MSS 802i EVO mobile scalping screen are producing material for concrete production and road substructures in Istanbul Financial Centre (IFC).
The Kleemann plant duo will operate in IFC in Ümraniye district, on the Asian side of the Turkish megacity, for around one-and-a-half years. It will process approximately a million tons of excavated material on a building site. In the middle of a dense development, flexibility is required at this location, both in view of the special surroundings and the material. The excavated material is processed directly on-site with the two Kleemann plants, and some of it is combined with other materials. Depending on the weather, the 0-500/600 mm feed material is at times wet and muddy, at other times dusty and dry. The
solution for these changing conditions: In wet weather, the MOBIREX MR 130i EVO2 impact crusher is preceded by the MOBISCREEN MSS 802i EVO scalping screen. It loosens the sludgy material, screens it coarsely and prepares it for feeding to the impact crusher. The first step is not required in dry conditions. The excavated material can then be transferred directly to the impact crusher.
“It has been shown that this combination produces excellent results,” says Feyzullah Kahraman, managing director of the building company Safir Proje, which operates the building site. “We produce grain sizes of 0/30 and 0/60 and, depending on the final product, can achieve an hourly output of 200 to 300 tons with a consumption of 24 litres,” explains the business operator. The quality of the final product also meets the requirements for the cubic material very well.
The fact that only one machine needs to be refuelled in dry conditions when the impact crusher is running without prescreening is very cost-effective. This lowers the operating costs and the scalping screen can then be used for other tasks on the building site. With its proportionally controlled running gear, the MSS 802i EVO
can be moved quickly with short set-up times.
Thanks to the intuitive SPECTIVE operating concept, the new Kleemann impact crusher is said to be quick and easy for employees to familiarise themselves with. The favourable ergonomics and easy access to all relevant parts for service and maintenance make the work more efficient.
Tanzania’s manufacturing and energy company Amsons Group has issued a bid to acquire a 100% stake in Kenya’s Bamburi Cement valued at US$180mn (Sh23.2) billion.
The acquisition will make the transaction one of the largest investment deals within the East Africa region, highlighting the group’s intent to invest in one of Kenya’s major blue-chip companies listed on the Nairobi Securities Exchange (NSE).
Amsons Group, through its Kenyan subsidiary and investment vehicle, Amsons Industries (K) Ltd, has issued a notice of intention to launch a public take-over offer that will involve acquiring up to 100% of the shares in Bamburi for Sh65 per share.
According to the Tanzanian firm, this acquisition aims to bolster Amsons’ presence in the East African cement sector and represents a significant step in regional economic development and market integration.
“We have great plans to deepen our investment in Kenya
and Bamburi,” said Amsons Group managing director Edha Nahdi. The cash offer by Amsons Group represents a premium above the Bamburi Cement share price as of the closing of trade at the NSE on 9 July 2024.
The group’s acquisitions come barely a few months after it acquired the Mbeya Cement facility in Tanzania, which was purchased from Holcim. Recently, Bamburi Cement has sold off its stake in several regional cement
companies. Early this year, the company completed the sale of its 70% stake in its Ugandan subsidiary, Hima Cement, for an estimated $84mn (Ksh12 bn).
Holcim’s regional head of Asia, Middle East & Africa, Martin Kriegner, expressed confidence in Amsons Group as a strategic partner capable of developing Bamburi Cement’s business in the long term.
“This agreement to sell our stake in Bamburi Cement advances Holcim’s strategy of extending our leadership in our core markets as the global leader in innovative and sustainable building solutions.
“With Amsons Group, we are pleased to have found a strategic and trusted partner best positioned to develop Bamburi Cement PLC’s business in the long term,” said Kriegner. Amsons Group’s intention to acquire Bamburi Cement is part of its broader market expansion plan. Further investments in Kenya are anticipated in the coming months.
BKT is making a major move towards greater sustainability by adopting greener principles. The Indian off-highway tyre manufacturing giant has joined the Global Platform for Sustainable Natural Rubber (GPSNR). According to BKT, this will help promote long-term sustainable practices, culminating in environmentally conscious production in line with the principles defined by GPSNR.
Natural rubber production offers environmental and social opportunities for improvement. Expanding rubber plantations will likely influence tropical forests, but sustainable practices can help protect biodiversity and reduce greenhouse gas emissions. Similarly, ensuring dignified working conditions and respecting workers’ rights on rubber plantations can help promote an ethical and sustainable industry.
To address these challenges and promote sustainable solutions, the Global Platform for Sustainable Natural Rubber brings together natural rubber producers, traders, tyre manufacturers, non-governmental organisations, academic institutions and other industry partners.
Through its membership of GPSNR, BKT is strengthening its commitment to aligning the natural rubber supply chain with the organisation’s guidelines. As a member of GPSNR, the company has access to a platform that aims to standardise manufacturers’ sustainability reporting and digital platforms for compliance with the requirements of the European Deforestation Regulation (EUDR), which will come into effect in December 2024.
“The principles on which GPSNR bases its roots align with our ESG policy. This path will allow us to develop and align our digital tracking initiative
for the sustainable sourcing of natural rubber in accordance with internationally accepted principles. At the same time, the GPSNR membership allows us to sustain and expand our sustainability initiatives to accelerate structural and quality changes in our natural rubber supply chain over the next five years,” said Rajiv Poddar, joint managing director of BKT.
To support its mission, BKT is cooperating closely with several Indian government agencies, including the Rubber Board and Automotive Tyre Manufacturers Association of India, and with some of the world’s leading players in the natural rubber industry.
“Being a member of GPSNR also means that we have direct contact with suppliers of premium natural rubber across the world, which is crucial for a company like ours that has always focused on high-quality standards,” added Poddar.
India is witnessing an emerging trend towards using alternative materials to curtail the use of virgin aggregates. However, quarry owners and cement plants remain critical of largescale adaptation of mineral extraction, loading, and hauling solutions powered by battery and electric sources. Partha Pratim Basistha reports
To encourage sustainability in India's infrastructure construction, the country’s government advocates the greater use of waste and recycled materials. It is working on newer guidelines in close consultation with industries providing secondary building materials, production technology, and linked services.
Speaking at a recent summit of the Indian Construction Equipment Manufacturers Association (ICEMA),
attended by Aggregates Business International, Nitin Gadkari, Minister of Road Transport & Highways, Government of India, said: “We aim to extract value from everything, including waste heat, scrap, demolition materials and slag. This intends to curb the consumption of virgin aggregate materials in India and lower the costs of road infrastructure construction. Every usable byproduct is repurposed.
Steel slag is a versatile material with numerous applications such as road construction, artificial reef, harbour
development, wastewater treatment (as it can remove mercury), and carbon dioxide capture. Steel slag can also act as a soil modifier in agriculture, a project our ministry is actively working on.”
India's Central Road Research Institute (CRRI) has recently developed national guidelines for the ‘Utilisation and Processing of Steel Slag as Processed Steel Slag Aggregates for Road Construction’. The guidelines, penned by CRRI, provide a comprehensive framework for the effective and safe use of different
types of steel slag in various types of road construction works. They include a detailed framework for properly handling and storing steel slag to prevent environmental contamination.
V. K. Saraswat, a member (Science) of India's NITI (National Institution for Transforming India) Aayog, said: “The adoption of the national guidelines for construction and maintenance of road networks using steel slag is expected to bring benefits like cost saving, reduced environmental impact, and improved road performance.”
Prof. Manoranjan Parida, director of the CSIR’s CRRI (The Council of Scientific and Industrial Research’s Central Road Research Institute) and Satish Pandey, principal scientist and inventor of steel slag road technology, noted: "Steel slag aggregates are used for bituminous roads and cement concrete roads, providing durable and optimised options for road construction. They are an excellent substitute for natural aggregates, a scarce resource."
India is the second-largest steel producer in the world. Steel slag is one of the major solid wastes the steel industry generates, with around 19 million tonnes produced annually in India from various integrated steel plants. This quantity is expected to reach 60 million tonnes by the end of 2030. The disposal of steel slag is a significant concern for steel industries as it is considered waste material and is largely disposed of as a landfill or piled up inside steel plants.
Over many years, the extraction of natural aggregates has significantly impacted India's natural habitat. In states like Jharkhand, the hilly terrains and natural features are
adversely affected, impacting ecology, groundwater availability, and other resources.
Based on minimising the use of virgin aggregates, CSIR-CRRI conducted a significant research project funded by the Ministry of Steel and major Indian steel industry players including AM/NS, JSW Steel, Tata Steel, and Rashtriya Ispat Nigam Limited. “With this support, we have successfully demonstrated the usage of steel slag in road construction in different parts of the country, from Surat in Gujarat, Western India, to Arunachal Pradesh in North Eastern India, and in Dolvi, Maharashtra, Western India.
“India’s first steel slag road was built at Hazira Surat by AM/NS India and CSIRCRRI in April 2022 using 100,000 tonnes of processed EAF steel slag aggregates developed at AM/NS India Hazira plant,” said Parida. The Hazira Surat sustainable road project received national and international recognition.
V R Sharma, vice chairman of JSP Group Advisory Services, said that his company uses steel slag for various projects like road construction, foundations, boundary walls, etc. This has reduced its stone aggregate requirement by 44% to 45%. The company also offers aggregates free of cost to promote its wide application in construction projects.
While steel slag offers the potential for usage, there are prevailing issues. There are higher transport costs associated with the transport of steel slag from the production source to the users in India. This poses a significant challenge, potentially increasing the overall cost of steel slag aggregates and making them less competitive for road builders.
Interestingly, with the thrust by the Indian government towards the usage of waste and residual materials, companies are finding it as a potential business opportunity. Manish Bhartia, CEO of CDE Asia, said: "Producing washed sand from rock-crushing plants has been our expertise. We have expanded our capabilities. This is based on the growing opportunities in India to process overburden materials. This is because, given the abundant supply of overburdened materials, the Indian government is considering monetising them. CFlo now offers solutions for producing sand from construction and demolition waste, as well as from overburden materials collected during the preparation of open-cast coal mines at a 1:7
ratio. Additionally, CFlo provides plants for manufacturing M-Sand (manufactured sand) from various other mining waste, and our advanced solutions can even process sea sand to produce M-Sand."
CFlo has recently implemented and commissioned projects featuring its latest Turbo Dual Washing Technology in Central India, specifically for processing overburden materials for Northern Coal Fields, a subsidiary of Coal India. The company has also conducted a similar pilot project for other Coal India subsidiaries.
There is a growing trend towards using recycled materials in road construction and concrete. The Indian government regularly floats tenders for processing previously discarded overburden materials. CDE sees this as a significant business opportunity for coal mining companies to produce IS: 383 BIS specification sand from their overburden stockpiles using specialised solutions.
"To further support the quarry and road building industries, we are strengthening our efforts with our patented Combo washing technology and other specialised solutions. We are collaborating with crushing plant owners to identify new applications that maximise plant usage and profitability," explained Bhartia.
He added: "What sets the Combo technology apart is its ability to simultaneously produce washed sand and washed aggregates. It can support crushing and screening plants up to 500 TPH. Combo Mega, our latest launch, can wash 200-350 tonnes per hour of sand and aggregate in a single chassis, a first in the industry.”
Gujarat, Western India-based Neptune, a manufacturer of bricks, concrete, and paver block machinery, is also quite optimistic about increasing opportunities to monetise waste materials.
Company director Soham Panchal said: "So far, we have been manufacturing plants to process fly ash and other materials. These have been for independent pavers, blocks, and brick producers. There is now emerging demand, interestingly, from quarry owners having their crushing and screening units. There are requirements for block-making machines as high as 50,000 blocks per day. The quarry demand is likely to become firmer as owners look towards higher profitability."
There is growing interest in monetising alternate materials with newer technologies by substituting the use of virgin aggregates.
However, the adaptation of electric and battery-operated extraction, haulage, and loading solutions has been somewhat tardy.
India's Road Transport and Highways Ministry has been insisting construction and mining equipment manufacturers come with electric and battery-operated solutions. Based on this insistence, companies have launched a fair number of products recently. However, quarry owners and cement producers have reservations about adapting the solutions.
T.V. Srinivas, general manager of the Heavy Equipments Machinery Division of Shree Cement, said: "We have found safety risks associated with using electric tracked excavators linked with cable wire for transmitting the power. There is a high possibility of the power cables getting entangled during frequent movement of the excavators. Given the nature of operations in our limestone mines, we must continuously shift the excavators in the limestone mine benches across varied distances. This is to segregate the materials and load them in the rigid dump trucks (RDT). Besides, there are restrictions on the power cable length, which will deter the electric excavators' long march.
"Further, given the large scale of operations, diesel-powered wheeled loaders at our mines are deployed to work for long eight-hour shifts. Based on the tasks the
loaders have to perform, it will be prohibitive to take the battery-powered loaders to the charging stations covering long distances.”
Srinivas continued: "We also have reservations about the charging efficiency of the battery-powered wheeled loaders. Diesel engine wheeled loaders of five-tonne capacity deliver high torque and loading forces. This makes them suitable for digging out clinker and limestone from the heaps, hauling and loading them into the RDTs at very fast cycles and even large quantities of fly ash from the pit. If the electric wheeled loaders are broken down, they will have to be towed to the workshops for examination. This will disrupt the cycle of operations.”
Srinivas said that manufacturers of electric wheeled loaders are trying to justify the equipment's low operating cost on [saved diesel fuel] litres per tonne. “This is because the machines do not consume any oil. It will be more pertinent to prove the machines' performance on an operating cost per tonne basis."
Ram Kripal Singh Construction, a major subcontractor for Coal India for movement of coal overburden materials and owner of more than 400 RDTs covering brands like Volvo, Scania, Bharat Benz, and Ashok Leyland, is also guarded on the usage of electric RDTs.
A spokesperson said: “Given the intense scale of operations at Coal India's subsidiaries like Northern Coal Fields and Eastern Coal Fields, we have to strictly deliver the guaranteed throughput for transporting the overburden materials from the deep mines covering steep gradients to the surfaces and long distances at very fast cycle times. This requires the RDTs to be highly available and reliable. Any batterypowered RDTs engaged in overburden material transport cannot frequently be taken to the charging stations."
Rasbehari Singh, owner of Mirzapur Crushers based in Mirzapur in Uttar Pradesh state, North India, said: "The initial procurements costs of the battery wheeled loaders are very high. This contrasts the diesel-operated loaders, which can work at longer stretches with high productivity levels. We find this economically unconvincing, given the pressure on margins of aggregates business in India due to very high competition. This is especially true when you are operating in quarry clusters. There are higher unit electricity costs in our area as well. Full seven-hour charging will make these machines too costly to operate.”
Upendra Singh, the owner of Pranjal Stone Crushers in the Mirzapur quarry crushing cluster, and H. Rama Gowda, owner of Gowda Stone Crushers in Bangalore, in the South Indian state of Karnataka, echo Mirzapur Crushers’ concerns over the use of battery-electric powered wheeled loaders.
V. Vivekanand, managing director of Caterpillar India, said: “Since the purchase cost of the [battery-electric wheeled loader] equipment is higher, it will take time for their adoption in India unless the highly intelligent Indian customers are fully convinced about the utility of the machines. They have to be well oriented to the applications and working economics."
Not all are sceptical about the benefits of deploying electric wheeled loaders in Indian quarries. Modern Stone Crushers based in Uttrakhand, North India, uses a new LiuGong 856HE lithium battery-powered wheeled loader in its work. "The machine has negligible engine maintenance and less downtime. With lower maintenance costs, the payback period will be less than five years. This is likely to discount the high initial costs of the equipment,” said the company’s owner, Pramod Aggarwal. AB
LSC Infratech is continuing its multi-site, new technology-led, business-upgrade programme with its Haldwani crushing facility in North India, the latest site to benefit. As well as driving down mineral-product production costs, the investment has boosted LSC Haldwani’s sustainability credentials. Partha Pratim Basistha reports
LSC Infratech is a major Indian aggregates company known for its higher plant-optimisation levels. Its latest capital investment is galvanising mineral extraction, processing, loading, hauling, and conveying at its renowned Haldwani plant in Uttarakhand, the company’s oldest facility opened in 1991. The latest capital expenditure at LSC Haldwani includes a significant investment in a number of LiuGong electric wheeled loaders and excavators.
Spread across 60 acres in the picturesque Himalayas, the LSC Haldwani plant produces nearly 5,500 tonnes of crushed aggregates daily and manufactured sand. It is one of seven LSC plants in Uttarakhand. The six others are Gobra, Tehsil Bajpur, Ajitpur, Kishanpur, Gangapur and Sitarganj. Together,
the plants produce around 25,000 tonnes of crushed aggregates per day.
According to Saurabh Agarwal, director of LSC Infratech, demand for crushed aggregates has been firm. He expects it to remain steady from new road projects across North India.
“Aggregates demand is also led by the expansion of railway infrastructure, with the laying of new tracks and the doubling and tripling of existing tracks, all requiring ballast. There is also new demand for housing projects in the Lucknow, Bareilly and Moradabad regions. To cater for the rising demand, we are going in for phased expansion to raise the aggregate throughput of the LSC Haldwani facility to 8,000 tonnes per day by April 2025. This will add another 150 tonnes per hour of crushing and screening capability, ramping up the crushing capacity of the plant to 500 tonnes per hour.
This is while ensuring safe operations of the plant to the fullest levels and curtailing operations costs in the highly competitive Indian aggregates business.”
Agarwal continues: “ For the new plant, we will go for a jaw similar to Titan, while the QM 250 cone crushers will be from Coimbatore, South India-based Propel Industries. We have gone in for customised engineering of the concave and mantle of the cone crushers with increased thickness. This characterises the better levels of metallurgy from Propel. These changes will increase the productivity and life of the plant while lowering maintenance costs.”
Crushed aggregates and sand are often taken from LSC’s Haldwani facility by North India-based road and other infrastructure contractors working in Uttarakhand, Uttar Pradesh, India’s capital state of Delhi, and
its National Capital Region, comprising the bordering states of Haryana and Uttar Pradesh. Railway ballast is transported by wagons and rakes.
LSC’s Haldwani fixed plant has a jaw crusher, primary and secondary cone crushers, and a three-deck screen. The jaw crusher is a Titan Diamond 3628, while the TC-1000 cone crushers are from Terex India, made at the Hosur facility near Bangalore, South India. The plant produces aggregates sized 5-8 mm, 8-17mm, 14-22mm, 35-42mm, 42-65mm, and 65-90mm.
Agarwal notes that the work being done to optimise the upgraded LSC Haldwani plant has been done using existing raw-material stock. “There are restrictions on the quantity of river bed boulder materials (RBM) that can be extracted for crushing by the Indian Institute of Soil & Water Conservation UK. The volumes of RBM to be extracted are also decided by the state government following surveys of the rivers. Besides, the number of daily single-shift truck movements bringing RBM to the plant is strictly restricted to 1,200.
“Uttarakhand’s rivers are the natural source of raw materials for LSC’s plants in the state, and many other small and medium Uttarakhand crushing plant owners. They are also the source of direct and indirect employment and business for almost three thousand tipper truck owners transporting the (RBM) to the plants daily for six months. The RBM for LSC’s Haldwani plant is sourced from River Gaula. The other Uttarakhand rivers supplying LSC’s other plants in the state are Dabka, Nandhaur and Kosi.”
Agarwal states that LSC Haldwani also benefits from the crushing plants and conveyor circuits that are now completely covered. “By covering the entire plants, we have been able to arrest the spread of heavy dust from the crushed and moved boulders. This has ensured the health, safety, and productivity of our workers.
“To increase plant productivity with more end product, we have extended the lengths of the conveyors. This has allowed us to bring large numbers of multi-axle tip trailers or conventional trailer trucks with higher payloads for loading the crushed aggregates. This supplements the Indian standard wooden-bodied trucks and the rigid dump trucks (RDTs). With the larger deployment of trailer trucks, site management has become easier for us.”
Agarwal says LSC Haldwani has done internal research to minimise the cost of running the conveyors. Transmission losses have been cut by installing a bevel helical gearbox from Bonfiglioli, where motors are coupled directly to the gearboxes, resulting in negligible transmission losses.
He continued: “LSC has also introduced to Haldwani 10 Bharat Stage VI, 8x4 Ashok Leyland rigid dump trucks. Their engines are highly fuel efficient and have lower operating costs. The new rigid dump trucks transport crushed aggregates to the stockyard. Under our expansion plan, LSC will acquire a further five of these trucks.”
Working towards sustainable operations and reducing plant-operations costs, LSC has deployed one new two-tonne LiuGong 820 TE electric wheeled loader. The 820 TE comes with an LFP battery with a storage capacity of 70.5kWh, operating up to seven hours on a full charge. The 820 TE has a 1.2m² bucket and a peak power of 50kw. It features a LiuGong transmission with a countershaft power shift and a 19km/hr maximum travel speed. The loader has an air-conditioned cabin and LiuGong’s I-Link telematics. It is offered with a quick-release coupler, gripper, and forks as optional.
LSC has also deployed a bigger batteryoperated 856HE MAX wheeled loader. The 5.8-tonne payload capacity machine is powered by a lithium iron phosphate battery. The model has a 350kWh-rated storage capacity and a 3.5m³ standard bucket. This bigger loader is being engaged to load the crushed aggregates on the tipper trucks and arrange the crushed materials in the LSC Haldwani plant stockyard.
Another recent LSC Haldwani facility purchase is a LiuGong 922FE, 22-tonne electric excavator with 1.0m³ HD/1.25m³
general-purpose bucket for the infrastructure and quarry sectors. LSC uses the 922FE to work in the stockpiles, arrange the processed aggregates stocks, and do the heaping job. It is also extensively used for loading manufactured sand into rigid dump trucks.
The 922FE’s electric system features an IPMSM motor delivering up to 140kW,
powered by an AC 380V working input voltage. Power is supplied to the excavator through a cable attached to a rotating pulley mounted on a temporary lattice tower. The cable draws power from the local grid, with LiuGong supplying the equipment set.
LSC has also mounted an electric cable pulley onto the body of one of its Ashok
Leyland RDTs. This allows the RDT to move alongside the excavator across the LSC Haldwani quarry site, undertaking various jobs.
As part of its Haldwani site expansion, LSC will soon purchase five additional electric excavators and three wheeled loaders from Liugong India. LSC says the decision to purchase further LiuGong machines was made due to LiuGong India’s “proactive product support”.
LSC Haldwani has an impressive reputation for sustainable practices, which include high levels of water conservation. For this, the site has recently received an award from the Government of India. LSC says its CDE C-Series, 75-tonnes-per-hour sand-washing plant, has been key to its water-conservation capability. “We have been given a complete solution by recycling 90-95% of the water used in our sandwashing operation. This truly addresses the concern of depleting natural resources such as sand and water,” stresses Agarwal.
Along with introducing newer technologies and advanced operating processes, LSC is working on new equipment-maintenance processes at its Haldwani operation. LSC has installed ERP-monitoring software for optimum plant and machinery operation, fleet management, and preventive maintenance.
For higher equipment availability, Sushil Chauhan, LSC Haldwani’s head of plant operations, says the site has an elaborate checklist of the components to be repaired.
They are repaired or replaced during daily, weekly and annual maintenance at four integrated workshops for each plant, all featuring inspection bays and engineoverhaul facilities.
Agarwal concludes: “Since materialhandling equipment at all our plants operates 300 days a year, between 12 to 15 hours a day, equipment reliability, lower maintenance and optimum performance, supported by appropriate product support, is vital for LSC.
“Getting timely product support for plant operators like us, who handle large quantities of material, is crucial. We prefer working with manufacturers with established manufacturing, marketing, sales and support networks in India. However, we do in-house maintenance and services to reduce dependence on OEMs [original equipment manufacturers]. Besides, we prefer to replace the defective components rather than repairs.” AB
The Kenyan concrete and mortar industry has traditionally been dominated by big players focusing on wet concrete mix and mortar for contractors involved in large infrastructure projects. This trend has ignored the many small-to-medium construction projects that require smaller concrete quantities, thus creating a notable concrete and mortar supply gap. A new start-up company is filling that gap with its innovative dry concrete mix and mortar solutions. Shadrack Kavilu reports
Instacrete Kenya (Instacrete) is an ambitious start-up that recently became the first company in Kenya to enter the dry concrete mix and mortar market.
The company’s dry concrete and mortar technology solution involves pre-mixing aggregate, cement, sand and ballast in a controlled environment and delivering the resulting product to Kenyan construction sites as dry mixtures.
The innovation, the first of its kind in the East African region, is increasingly gaining momentum in Kenya as developers seek cost-effective and time-saving construction solutions.
Instacrete management says its dry concrete mix and mortar products eliminate the need for large, cumbersome concretemixing trucks and reduce logistical challenges, especially in areas that are not accessible by big trucks.
Kennedy Zackary, Instacrete’s production manager, says dry concrete, also known as dry mix concrete or dry batch concrete, requires only the addition of water for activation. Unlike traditional concrete,
delivered in a wet form, dry concrete is typically mixed in a controlled environment and stored in a semi-dry state until needed.
“The end users only need to add water at the construction site,” says Zachary, adding that concrete mixed at Instacrete’s production plant guarantees quality control via precise measurement of the individual ingredients, ensuring consistent mix ratios and even batch strength and durability.
Zackary says sand is the most important element in Instacrete’s innovative product mix. Most of the sand used in Kenya’s construction industry has impurities from the harvesting sites. Such impurities may include clays, organic matter, and silt, among others. When used in this state, the constructed structure may experience stripping, mold formation, and a loss of binding capability. These effects can be seen on walls where there is moisture exposure with stripped tiles, discolouration and, ultimately, loss of structural soundness.
“We process sand to ensure 99.99% purity and remove all clays, silts and organic matter. Nobody is doing this in the country
at this time. The result is clean, pure sand that ensures the structure under construction is sound, with no damage to paint or loss of tiles. We also remove dust and other impurities from the aggregates received from the crushers. So we provide very high-quality material,” Zackary tells ABI
“We have two products currently in the market and two more in the pipeline. The products in the market are Instacrete Mortar Mix, a blend of cement and sand, and Instacrete Concrete Mix, a blend of cement, sand, and ballast,” explains Zackary.
In Kenya and most emerging economies in sub-Saharan Africa, the use of dry concrete mix and mortar is widely gaining traction given that the use of traditional wet concrete and manual mixing of stockpiled aggregate materials lead to material losses, wastage, poor quality control and poor estimations of quantity resulting in unnecessary labour overheads.
Zackary says one of the key trends in the dry concrete market is the growing adoption of ready-mix dry concrete, eliminating the need for on-site mixing.
“This saves time and labour, ensures consistent quality, and reduces wastage.”
Industry experts believe that, based on application, the plaster segment is projected to dominate the dry mix mortar market. Plaster is used widely in construction projects due to its ability to set very quickly when added to water compared to other substitute products.
In the region, dry concrete mix and mortar uptake are increasing at unprecedented levels, largely driven by ambitious government infrastructure projects, urbanisation trends and rising demand for housing and commercial spaces.
The increasing preference for ready-mix dry concrete in large construction projects, such as infrastructure development and residential buildings, also drives market growth.
According to research by leading market research firm Stellar Market Research, the dry mix mortar market in the Middle East and Africa was valued at US$6.51 billion in 2023.
“The total revenue is expected to grow at 3.6% through 2024 to 2030, reaching nearly $8.34 billion by 2030,” says the research firm in its report titled Middle East and Africa Dry Mix Industry Analysis 2024-2030
The market is projected to be driven by the increase in construction activities in the commercial and industrial construction sectors in constituent countries. In Africa, the report highlights Tanzania, Nigeria, South Africa, Guinea, Egypt, and Algeria as countries with the highest project values that are expected to drive the growth of the dry mix mortar market.
The International Monetary Fund (IMF), in its Regional Economic Outlook report for sub-Saharan Africa, says economic growth accelerated from 2.9% in 2018 to 3.5% in 2019 and 3.6% in 2020. This growth trend has been followed and is expected to continue in all countries in sub-Saharan Africa.
According to projections, industry players are optimistic that the dry concrete market will witness significant growth in the coming years, driven by its cost, time, and convenience advantages. The market is also likely to benefit from the growing popularity of ready-mix dry concrete and the development of specialised dry concrete mixes for various applications.
Though dry concrete and mortar use is growing rapidly, industry players are not ruling out the use of wet concrete mix and mortar as each has its own advantages.
“Wet mixing has its niche, and we are not in the market to compete with this type of consumption. However, there is a market where the wet ready mix cannot serve. For those very large and medium size projects, a wet mix is ideal. If a project needs to pour at least ten cubic metres or 23 tonnes of concrete in a very short time, a wet ready
mix would be the most appropriate and certainly most cost-effective. However, there are limitations in accessibility, location, and speed of placing as well as the quantities,” says Boniface Njoroge, Instacrete’s director and CEO.
Njoroge adds that although his firm targets all kinds of concrete users, the optimal benefits of his products are gained by retail consumers, especially for those mid-level to small projects that fail to be executed due to exorbitant overheads, which defeats the purpose of such projects.
“We are still penetrating the market as dry mix concrete products are new concepts which need to be explained clearly and easily for people in the African markets to understand. For projects such as the concreting floor of a parent’s house in the village, building a home at a very friendly pace, fencing, repair works, remodelling,
retrofitting, landscaping, plastering, tile laying where concrete and other cement products are needed but in small quantities over some time ( one day and above), the ready dry mix is not only most appropriate, but it is also most effective in terms of convenience, quality assurance, wastage control, project management, and cost-effectiveness,” explains Njoroge.
Although dry concrete mix has certain advantages, Njoroge says it cannot replace wet concrete mix.
“One is not a replacement for the other. Each one has its advantages and its unique application. You cannot use one in place of the other. For example, it would be insensible to bring wet mix trucks to do small repair work or to install fence posts. It would not be very cost-effective to use bagged concrete to pour a large amount of concrete in a very short time. So, the two have their own uses and are not mutually interchangeable,” said Njoroge.
Instacrete’s production manager says that although the firm started production and distribution recently, the customer feedback is very positive.
“Customers are very positive about the products. Those who have used the materials generally appreciate the convenience, cost savings, and ease of construction,” says Zackary.
However, like any start-up trading in novel ideas, Instacrete is also experiencing a fair share of market challenges. The production manager says most of the challenges the firm faces in the market are related to the novelty of the products.
“As a new concept, construction workers are not familiar with how the products are used. There is a misconception that using these products requires specialised skills. The truth is that they don’t need special skills to use. In fact, anybody can use the products and don’t need any special skills.”
The firm’s operations are currently focused on Kenya. However, Njoroge says there is a
blue ocean of prospects for the firm in the regional market.
“This type of technology is not available anywhere else in Africa. As markets open and allow, we hope to eventually spread to other needy regions within the continent,” says Njoroge.
Njoroge says the firm’s innovation was inspired by a project he was involved in as a student at the university.
During the project, he discovered there were struggles to get concrete in small
quantities to accomplish small day-to-day construction work.
“After college, we started looking at ways to mix and bag small quantities, where the user would just need to add water without having to go through the process of procuring different components, transporting, and mixing at the site,” he says, adding that this experiment simplified the consumption of concrete as a retail product and made it convenient, quality-assured, and costeffective. AB
Metso is growing fast. A big recent announcement on the Finnish quarrying, mining and recycling equipment manufacturer's future Finnish machine production and R&D plans coincided with the unveiling of the first two products from Metso's new Lokotrack EC Series range. Guy Woodford travelled to Tampere to get the inside track.
Metso is investing €150 million in a modern technology centre in Tampere, Finland. The major Finnish quarrying and mining plant manufacturer will gradually move its operations in Hatanpää, Tampere, to a new Lokomotion technology centre built in Tampere’s Lahdesjärvi district.
In the future, at the new Lahdesjärvi facility, Metso will design, test, and manufacture technologies, equipment, and components for the production of aggregates and sand. Acquired by Metso in 2021, the Lokomotion Technology Centre site covers 23 hectares. It will host over 900 Metso employees. The initial total building area of the centre is about 66,000m², of which the first phase will be about 34,000m². The investment in the first phase is about €150 million, spread over three years. Construction started in July 2024 and will include assembly and testing facilities for manufacturing mobile crushers and storage facilities for components and materials used in aggregate equipment. Investment in 2024 is estimated at around €30 million. Production of the track-mounted crushing plants, Lokotracks,
is scheduled to start in Lahdesjärvi during the third quarter of 2027.
According to the plan, the crusher factory, research centre, maintenance workshop, and office facilities will move from Hatanpää to Lahdesjärvi later. The new technology centre is expected to be fully completed by the mid-2030s.
The Lokomotion project aims to develop and build a new modern technology centre for sustainable manufacturing operations. The centre will provide an environment and facilities to meet the most demanding sustainability and environmental objectives. The project has applied for BREEAM certification with a "very good" rating. The City of Tampere has also defined a green factor in the land-use plan for the area, which will guide the design and implementation of the project in terms of climate resilience and nature-based solutions.
Metso's current site, Lokomo, focused on the aggregates business, is located in Hatanpää,
Tampere, and it has had industrial activities for more than 100 years. Metso owns approximately 17 hectares of land and buildings in Lokomo. The company intends to move all Metso's Lokomo activities in a phased approach to the new technology centre in Lahdesjärvi, and then to close down and leave the Hatanpää site and buildings.
"Tampere is a very important location for Metso, and with our long presence in Lokomo, we are also an important part of the city's industrial history. We are very pleased to be able to implement the Lokomotion project, which is a significant project for Metso and will allow us to continue our operations in the area in a new state-of-the-art technology centre and production facility. The project involves a number of partners and will have a significant employment impact in the area," says Markku Simula, president of Metso's Aggregates business area.
The aggregates produced by Metso's equipment are used, for example, in constructing roads, railway tracks, and other infrastructure, for building foundations, and as a raw material for concrete. The equipment can also crush construction waste to be recycled and produce
industrial sand to replace natural sand for concrete production.
Simula gave Nordic and international trade media an overview of the Lokomotion Technology Centre during a special Metso dieselelectric Lokotrack EC Series range launch event in Tampere from 14 to 16 May 2024.
The new EC range's first two products, which were unveiled at the event, are the Lokotrack LT400J, a 68-tonne mobile jaw crusher that primarily crushes hard rock and recycled aggregates, and the Lokotrack LT350C, a 50-tonne mobile cone crusher for secondary and tertiary crushing.
The trade media heard that Metso posted sales of €5.4 billion in 2023, with the company investing €73 million last year in research and development. Renaud Lapointe, senior vice president of Metso Products Business Line, highlighted recent sustainable technology developments from Metso during the trade media press conference. These include the Nordberg HP350e Series cone crusher, the NW8HRC—the first portable HRC 8 crusher for manufactured sand, and the Remote IC Lokotrack process control app.
Speaking to Aggregates Business after the press conference about how Metso sees the current and medium-term global quarrying machinery market, Simula said: “If you look ahead over the next few months, uncertainty is likely to continue. Inflation will be slightly lower, but interest rates will likely remain high. Everyone has a lot of inventory across our industry, whether in manufacturers' or distributors’ backyards. The rental machine business is busy but is not converting [to increased rental orders]. Part of that is down to market uncertainty and is linked to high interest rates. From our perspective, the worst time is behind us. However, we are not back to normal or a busy time.
“If I take a three-years-or-more perspective, I think uncertainty will reduce, and inflation will not likely be as big an issue. Interest rates will also be a bit lower. What will be important is that inventory from everyone’s backyards is back to normal levels. It will take a year or two before
that happens. When all these factors are in place, I think there will be healthy unit demand in many places.”
Simula is buoyed by the likely positive impact of long-term megatrends on the global quarrying equipment market. “Urbanisation, electrification, and sustainability are favourable to us. The ways that people are fighting global warming are favourable to us.”
In March this year, Aggregates Business reported that Metso's 2023 annual report had revealed a big rise in Planet Positive-linked sales. The Finnish quarrying and mining equipment major's Planet Positive-related sales were worth €1.447 billion in 2023, up from €1.225 billion in 2022. Metso's Planet Positive initiative helps customers cut their CO2 emissions and achieve their other sustainability priorities, such as reducing pollution.
The Planet Positive portfolio already includes more than 100 Metso products, and the company aims to have a Planet Positive product for every part of a customer's value chain. To achieve this, all Metso's R&D projects must have sustainability benefits, with a target of 80% of R&D spending on Planet Positive product and service offering development by 2030.
Simula stresses that some of Metso’s new crushing and screening plant solutions are wellsuited for recycling applications. “They are ideal for recycling concrete to recover good quality stones and sand that can easily be reused. There is also an even bigger potential long-term gain from recycling cement. Revitalising it for reuse would be hugely significant environmentally. There are 700kg of CO2 emissions for just one tonne of cement. I did some rough calculations on this, and if you can recycle the cement with one of our plants, the carbon credits you receive would pay back the investment in the plant in just a couple of years.”
Simula said the Metso Lokotrack EC Series range launch event had highlighted another key industry trend. “I’ve been having many
conversations with customers, and many say that [machine operation] data is increasingly important to them. How we can create useful data for them that they can utilise will be increasingly important.
“One corporate customer told me that when their company had a big CO2 reduction target, they found that by looking at their [machine operation] data, they could make their production 20% more efficient, which delivered practically the same in terms of CO2 reduction. Automation, digital tools, and data will give us benefits we don’t realise today.” AB
strategic partnership with Martin’s sales and service teams ensures the most cost-effective and productive solutions to your specific bulk material handling issues. Our certified, factory-trained specialists provide the industry’s best inspection, installation and maintenance services. Their knowledge and capabilities are guaranteed to improve the cleanliness, safety and function of your entire belt conveying system. This factory-direct expertise delivers the confidence you need to focus on your operation’s bottom line.
The 40th-anniversary edition of the Hillhead quarrying, construction and recycling show at Tarmac’s Hillhead Quarry near Buxton, Derbyshire, England, included cutting-edge aggregates-processing solutions from two leading manufacturers. Guy Woodford reports
Attendees at Hillhead 2024 (25-27 June) enjoyed the live demonstrations of Astec’s FT4250 HSI (horizontal shaft impactor), a popular US market crusher, and GT205 screener. Large numbers also took in the manufacturer’s impressive show stand, where the Americanheadquartered off-highway industry major also showcased an extensive product range from its Rock to Road solutions portfolio.
Astec expanded into Northern Ireland in 2014 after acquiring Omagh, County Tyronebased Telestack, a major global bulk materials handling solution manufacturer. Last year, Astec finished the US$6.5 million 44,000ft² expansion of its Doogary facility bringing the site to 100,000ft². This extension takes Astec’s total investment since its acquisition of Telestack to more than $10 million. The US giant employs more than 230 people in Northern Ireland.
More than half of the global market supply for mobile crushing and screening equipment originates in Northern Ireland. Astec’s greater manufacturing presence will enable it to grow its international market business and better serve its customers and partners.
During Hillhead 2024, Aggregates Business spoke to Damian Power, Astec Europe managing director, and Michael Norris, Astec Group president, Materials Solutions.
“All the machines you see here at Hillhead were manufactured in Omagh,” explains Power. “The GT205 is our new 20” x 5” triple-deck rinsing screen. It’s the first designed and fully tracked mobile plant out of Omagh. We also
think there will be a pretty good international market demand for the FT4250 HSI.”
“We have a stronger focus on Europe, and Damian was recently appointed our European managing director,” says Norris. “The machines we are designing and building in Omagh are specifically for the international market.”
Telestack was at Hillhead 2024, exhibiting its highly mobile and versatile TSR 40 radial telescopic stacker.
Asked about Astec- and Telestackbranded machine production volumes at the Omagh facility, Power replied: “The industry accelerated out of COVID but has cooled off a little. We are in a multi-election year across the world. We expect that the current [market] slowdown is temporary. We have invested
in Omagh to grow the business out of there significantly over the next three to five years.”
“We want to increase production out of Omagh seven to ten-fold,” added Norris.
Has Astec found it hard to recruit engineers, welders, and other skilled workers to work at its Omagh facility due to the number of competitor OEMs [original equipment manufacturers] with a strong presence in Northern Ireland?
“We have an employee-focused culture, and recruiting has not been difficult. We are on a growth trajectory, and people can see that.”
“We are a unique proposition to employees in that we are high growth with a strong record in the [global] aggregates industry, in crushing and screening specifically,” says Power. “We are not just some start-up. We have substance behind us.”
“We are an over 100-year-old company when it comes to crushing and screening. We have that expertise,” emphasised Norris.
Among other Astec machines exhibited at Hillhead 2024 were the 3,000 tonnes per hour HF24 hopper feeder and the versatile, custombuilt 220 tonnes per hour Kolberg 9225S sand plant. “Part of our offer out of Omagh is going to be our washing product line,” said Power. “Astec has been in washing for many years, and there has been good collaboration between the US and Omagh teams to pretty quickly bring the new [Kolberg 9225S] sand plant to the market. There’s a real opportunity to internationlise much of our washing product range, tweaking the design of some of the washing modules to best suit European customers that tend to work in a tighter footprint than in the US.”
“Over the last couple of years, we’ve been delivering our strategic business plan focused on our employees and working culture and ensuring we are taking care of our customers and getting their feedback about our new products,” explained Norris. “The innovation side and coming up with new products is the DNA of our company.”
Power said Astec was also reviewing how its existing European dealer network fitted into its international growth plans.
SBM Mineral Processing (SBM) also had a strong presence at Hillhead 2024. The Austrian aggregates-processing specialist focused on the benefits of fully hybrid processing. The spotlight was on the REMAX 600 tracked heavy-duty impact crusher, celebrating its official UK market launch.
"Despite the currently rather subdued mood in the UK market, which was probably also reflected in the strongly fluctuating visitor numbers during the show’s three days, we are satisfied with the overall result," says Helmut Haider, sales director processing at SBM. "In addition to international visitors, particularly from Scandinavia and occasionally from the Far East, we were able to welcome interested experts from all over the UK, from all target sectors and decision-making levels – including construction and recycling companies, project and quarry managers, as well as chief buyers from large building materials groups. This is a clear endorsement of our significantly increased market presence."
In addition to existing partners Banner Equipment (Midlands, North/West England)
and Orba Group (Greater London/South East England), SBM also signed a long-term agreement at the show with new dealer Fitzgerald Plant (Wales/South West England) to provide sales and service throughout England and Wales.
"The Scotland and Ireland markets are managed centrally from Austria, but we intend to establish a direct foothold in those countries soon. Talks with suitable partners are nearing completion," said Haider.
Diesel-electric and hybrid drives for mobile processing plants were dominant themes at Hillhead 2024. "For us, of course, this was something of a home game, as we have been offering this technology for more than 40 years,” said Haider. “Today, we focus exclusively on highly efficient, environmentally friendly and mature hybrid solutions in all machine classes across all systems.”
Haider continued: "UK operators of mobile crushing plants in the quarrying and recycling sectors still rely predominantly on jaw crushers, often with downstream screening equipment. On the stand, we presented our 'all-rounder', the JAWMAX 450, which, with a weight of around 40 tonnes and a maximum throughput of 450 tonnes per hour, is aimed at precisely this wide range of applications."
Haider said that SBM had received great praise for the user-friendliness of the CRUSH CONTROL system on its machines.
Furthermore, SBM’s REMAX impact crushers also attracted great interest at Hillhead, particularly the REMAX 600 on the SBM stand and the REMAX 450 with a single-deck secondary screen in the live demonstration zone. The latter nearly 53-tonne machine processed 1,500 tonnes of limestone from 0/800 to Type 1 0/40 in up to five short demos per day, achieving a maximum of 300 tonnes
per hour with an average consumption of just under 25 litres per hour. "Our REMAX models are particularly popular with UK contract crushers and stationary operators. They combine class-leading crusher sizes, welldimensioned primary and secondary screens, optimised transport dimensions, and low operating costs. Our dealers also confirm this," said Haider.
SBM’s REMAX 600 impact crusher has a maximum output of 600 tonnes per hour and can produce up to five end products in a single pass. "Of course, you don't sell a machine like this at a trade show - but we were actually surprised by the number and specific nature of the enquiries and expect the 600 to establish itself quickly in the UK market," said Haider.
There was also great interest at Hillhead 2024 in SBM’s ‘autonomous crusher’ being developed in partnership with experts from the University of Leoben, and based on the REMAX 600:
"We are well on schedule and currently optimising the AI-supported, real-time detection and classification of feed material and crushed products as the basis for the fully automated crushing process. This process is continuously validated via a global data exchange with our central competence centre and automatically adjusted if necessary," explained Haider. “The technology is expected to be ready for market launch and use in other crusher classes as early as 2026. Thousands of stored rock and process data will make it easier to plan mobile operations, while extensive self-monitoring, including wear detection, will ensure plant availability. This technology is expected to set new standards in environmental efficiency thanks to the autonomous control concept that is consistently focused on quality and performance parameters.” AB
Brian James is a high-profile figure in the European aggregates sector, having formerly held senior roles at both Aggregates Europe - UEPG and the UK MPA covering the recycling of construction and demolition waste and other secondary sources. He now speaks as an independent voice in support of recycled aggregates and the circular economy. He tells Liam McLoughlin that a number of recent trends and regulatory developments in Europe and the UK could threaten the ability to use recycled aggregates.
If you want to discuss the ongoing potential for the use of recycled aggregates in construction, then Brian James is the man at the forefront of figures in the European aggregates sector to speak with.
A chartered civil engineer and longstanding member of the UK Institution of Civil Engineers, James worked until recently as special advisor at the UK Mineral Products Association and was also chair of the recycling task force at European aggregates association AE - UEPG.
The European Union has set out a goal for 70% of construction and demolition (C&D) waste to be recycled, and although it is considering increasing this percentage, no formal change has been proposed.
James says that such high targets for recycling of C&D waste, and indeed the ongoing use of recycled aggregates in construction projects across Europe, could be in jeopardy due to a number of recent moves by governments and agencies in the region.
Prominent among these is initial guidance on the use of recycled aggregates brought in by the Republic of Ireland’s Environmental Protection Agency (EPA) in October 2023. The EPA’s guidance – National End-of-Waste Decision EoW-N001/2023 – is available at: https://www.epa.ie/ publications/licensing--permitting/ waste/Final-Decision---National-End-ofWaste-Criteria-N001-2023.pdf
It covers aggregates that are recycled from C&D waste, including soil and stone, concrete, bricks and ceramics. It is designed to establish criteria determining when recycled aggregates resulting from a recovery operation ceases to be waste.
James says: “The guidance is so heavily restrictive that it as good as dammit killed any hope of developing the country’s recycling industry.
“To put it in perspective in Ireland at the moment, if you had a load of concrete that
went out and was not used and sent back to the depot, allowed to go hard, you cannot break it up and use it as general aggregate. The new regulations only allow very limited use, for example to an area 100m by 100m, such as for a car park sub-base, but that’s itit’s not allowed in structural concrete or any other usage.
“Consequently, you are now getting piles of materials building up around Ireland, mainly in quarries I would imagine. So, with this very heavy legislation and an abundance of hard rock, the companies won’t invest in it.”
James says there is a stark contrast between what the Irish guidance is leading to and what the European Commission wants to achieve in pushing up the level of recycling as part of the drive for the circular economy.
He adds that the Irish move on aggregates recycling could have a wider impact on subsequent developments in the EU and the UK: “They produce documents, and those can subsequently be picked up by other member states. This happens all the time, and although the UK is outside the EU the influence is still there. At present this problem is particular to Ireland and that the AE - UEPG will help try and resolve, but it’s a tough one.”
Another recently identified trend in Europe is the cross-border trade of construction
and demolition waste, with the biggest market thought to be from Germany to the Netherlands due to the latter’s lack of quarries.
“There are moves at the AE - UEPG to instigate an economic study to find out where these cross-border movements are going,” says James. He adds that the cross-border trade development will impact the EU Waste Framework Directive that controls all the regulatory practices around movements of C&D waste.
The practice also raises questions about the increased carbon footprint of C&D waste, which is often recycled at inner city sites with no long-distance transporting of material. With cross-border movements, longer distances are involved at a time when the industry is supposed to be moving to net-zero targets. James was a delegate at the recent Aggregates Europe – UEPG Recycling Task Force meeting in Zurich and says that a recommendation for an initial study of the issue was made.
Another important recent development impacting aggregates recycling is the proposal by the European Union’s chemicals agency, ECHA, to change the status of recycled aggregates which is currently classified as an article, to that of substance (which is classified as being of very high
concern). The change would be made under the EU REACH regulations which covers risks to human health and the environment from chemicals.
“This would mean that recycled aggregates would have a lot more hoops to jump through before they can be approved for use,” says James. “This would be a backwards step because recycled aggregates have always been classified as an article, and it would mean it is put on the same level as some sort of hazardous material, until you can prove otherwise. If that got off the ground the whole recycled industry is in jeopardy.”
The proposal was due to be decided on at a meeting of the ECHA steering group in May this year. AE - UEPG has already responded on behalf of the European industry with further representation in hand.
A further development, this time in the UK, affecting recycled aggregates is the potential introduction of mandatory digital tracking of all waste products including construction and demolition. The UK government released a discussion paper on this in 2023 with the potential for enactment in April 2025.
“At this stage it is UK-only, but if it expanded to be pan-European this would tie-up with the cross-border aggregates trade issue,” says James.
“It’s currently a comprehensive 30-page document, which unfortunately, tends to get put on the shelf and forgotten. I’ve made the suggestion to the EDA that there needs to be a two- or four-page key messages paper that you can back up with the full reference document.”
Commenting on the importance of the EDA guidance document, he continues: “It sets out the process of pre-demo assessment so that hazardous stuff is identified, the various valuable waste/recycle streams recovered (eg. metals/cables etc) before the structure comes down. Hence for aggregates we generally get a cleaner, safer raw material to work with.”
In 2008, the European Commission’s Waste Framework Directive set a target of having 70% of construction & demolition waste in the EU being recycled by 2020. However, the EC found in 2018 that, with the exception of a few EU countries, only about 50% of C&D waste was currently being recycled.
understand that this [the EU economic report] has now been withdrawn.”
James says that there is a failure among authorities to talk to the aggregates industry to fi nd out what it can actually do, and consequently the wrong messages get out.
“One of the serious problems you face with all of this is that the ideas get kicked off in one area and they spread around and they suddenly become the norm – whereas the people in the industry who have to actually make this work have never had a hand in how that decision is made.
“From my time working at the AE - UEPG, you were always trying to play catch-up. We didn’t know what the EU regulators were thinking until they published a draft or a consultation, and then you were trying to argue against it/for reality. You will find a politician will jump on, for example the report that was demanding 60% recycling, and it could be this false golden panacea that undermines any new quarries being given permission.”
Commenting on these simultaneous developments – the restrictive aggregates recycling guidance in Ireland, the potential reclassifying of recycled aggregates as hazardous material by the EU’s ECHA, the cross-border trade in C&D waste in Europe, and the UK mandatory digital waste-tracking proposal – James states: “You can see there are a whole host of potential issues facing aggregates recycling in Europe.”
On a more positive note for the recycling sector, James says he has been involved for several years in working with the European Demolition Association (EDA) to develop the initial demolition protocol. The European Commission is now in the early stages of upgrading the protocol in conjunction with the EDA. “This is just another example of the valuable work done by industry trade bodies,” James adds.
The EDA is also compiling a comprehensive guidance document on the use of recycled materials which is close to publication. “The document is from the demolition perspective, so aggregates are only a part of that. Again AE - UEPG is supporting the EDA.
In terms of whether governments and regulators are realistic about targets for the use of recycled materials, he responds: “The answer is no. Across the whole of Europe there are countries like the UK, Belgium, Netherlands, and one or two others, that are hitting around 25-30% levels of recycled aggregates, while there are others where it’s less than 1%.”
As an example of what he believes is typical of the misguided thinking, James highlights a recent EU economic report which suggested that there should be 60% recycled aggregate in all concrete applications.
“We don’t have enough material to meet 10% let alone 60%, it’s just physically not possible,” he adds. “There are people within research groups advising ministers, and all they are doing is jumping on the sustainability bandwagon and have no understanding as to what the industry can actually do. Following representation, I
The MPA has stated that there is a need for more industry data on recycled aggregates to be made available through official government sources, particularly given the challenges ahead around circularity, sustainability and for all sectors to meet the Net Zero target by 2050.
The MPA’s own data is collected mainly from the sources that the association can follow up on, predominantly its membership, and the UK government does not collate any figures about recycled aggregates, either on usage or planning.
The landscape is similar throughout Europe with realistic data being difficult
to obtain, and figures are mostly provided through the efforts of the trade associations across the region.
The UK is among the European leaders in the use of recycled primary and secondary aggregates, alongside countries such as the Netherlands and Belgium. Primary aggregates include quarried crushed rock and both land-won and marine-dredged sand and gravel, while secondary encompass recycled construction, demolition and excavation wastes (CDEW) or are derived from other industrial, production or extractive processes.
Belgium had the highest percentage share of recycled and secondary materials in total aggregates sales at around 29% in 2021, according to estimates by the MPA and AE - UEPG, with the Netherlands in third position at just over 25%, behind Great Britain. “Unfortunately, there are too many Member States that need to embrace the use of recycled aggregates,” James says.
The amount of recycled aggregates in Great Britain has averaged around 28% of total aggregates produced in recent years. The rate increased to just over 30% in 2022, according to the latest MPA estimates. In 2022 total recycled and secondary sources of aggregates accounted for an estimated 74 million tonnes of total aggregates supply in Great Britain. The MPA estimates that some 191.1 million tonnes of primary aggregates (quarried crushed rock and both quarried and marine-dredged sand and gravel) were produced in the UK in 2022.
Is there much scope to increase the recycling rates in the EU and UK further? “You get fluctuations around that core 28 to 29%, but my personal view is that it’s as good as it’s going to get,” says James.
He says that the availability of materials such as fly ash, for example, for recycling is reducing. “As we get away from fossil fuel power generation, you are losing fly ash because you are not producing any. There are areas where they are digging up old fly ash tips to reprocess it, so it’s a diminishing resource.”
In 2016 fly ash accounted for 1.1 million tonnes of the total 7.8 million of secondary aggregates that were produced in the UK. The MPA figures for 2021 shows UK fly ash production of 388,000 tonnes.
China clay waste is another major secondary aggregate in the UK, with 1.6 million tonnes of China and ball clay waste produced in 2021, according to MPA estimates.
The UK supply of China clay is predominantly in Cornwall in the south west of England. Moving this has previously been limited by the difficulties of transporting it to the rest of the country, but the situation has improved. The supplies from Cornwall are shipped to ports in the south-east of England including Dover, Shoreham and Tilbury. Dover now has an aggregates terminal which recently came on stream.
In terms of the general sources of construction and demolition waste, James says that this is totally dependent on demolition, and its fluctuations are linked to the growth levels of the economy. Demand
for aggregates (primary, secondary and recycled) fell in the UK during 2023 because of a fall in demand from the construction sector. The MPA reported in February 2024 there was a 5% decrease in total aggregates sales volumes in 2023. The association says that new construction projects in the pipeline are stalling due to cost pressures, planning challenges and a poor economic and investment backdrop.
“If you’re not building anything you are not, generally speaking, demolishing anything, and that will fluctuate in its own right,” says James.
“If you are trying to make a building more sustainable, and make it more re-useable, then that first line of demolition has been lost instantly. You can see the pattern – if you push it in one direction you lose something in the other, which is nothing new.”
He says, for example, that the HS2 highspeed rail project has recently accounted for most of the available recycled material in the central area of the UK for use in building haul roads and other temporary works, etc. for the scheme, but this was a short-term trend and was not going into the full-blown construction market as part of permanent works. “However, it will reappear at the end of the construction period!” he adds.
James says that in his opinion, the biggest barrier to the use of recycled aggregates is education and acceptance. “You have a culture where people want the best. In terms of health and safety if you use anything other than the best you are perhaps [seen as] undermining the responsibility of your approach.
“There is always a tendency for engineers and architects to use the best product and material every time. But in truth you have got one set of technical and environmental standards, and if your material complies with those technical standards then it is fit for purpose.”
He says that it can be difficult to convince consulting engineers that a recycled product is going to do the job as well as a primary one.
“You get consultants in certain architectural practices who take these things on board and they want to use it as a part of their credentials,” he states. “But generally, you have to get that education and acceptance across that recycled material is an equal product, and that comes from people like us talking about it, making them understand that we are meeting the same technical and environmental standards all the time.”
James says that the leadership on this issue needs to come from government bodies, who are the biggest purchasers of aggregates materials.
He adds that he is not a fan of specifying a set recycled percentage within any contract because that distorts the situation, but says that to have recycled material as a fully accepted alternative source of supply would be useful.
The use of defined amounts of recycled aggregates was reportedly specified in contracts for the London 2012 Olympic
Village. “With contracts being frequently prepared on a ‘cut and paste’ basis, then you quite often find that these clauses crop up in other places where you’ve then got to look and see is it appropriate or not,” James says.
He adds that, from what he has gathered anecdotally, the recycled targets in the London Olympics contracts were not met because the quantity of recycled material was simply not available. “It’s that realism of what can be done that is the missing link. There has been a lot of activity in the concrete field for substitution, and in theory you can make concrete in the laboratory out of virtually anything. It’s how it all gets put together, is it going to work in practice and can you deliver it at an economic price?”
He adds that there are additional problems in concrete supply with many concrete plants being in tight urban locations because that is where the concrete is used. “There just isn’t the storage facility for yet another supply [of recycled material for use in concrete] for different jobs,” says James. “In addition to these practical issues there is the thorny old problem of water-to-cement ratio and those sorts of arguments. You have to balance what is possible and what is not.
“There are some concrete companies that trade on the term that it is ‘eco mix’. There is research that has shown you can go to around 15% of the coarse aggregate being recycled material and it doesn’t make a vast amount of difference in terms of strength. But you’ve got to have that material available,
and it’s got to be of a consistent quality because the whole thing with concrete is that it has got to be consistent and then you know what you’re dealing with.”
Recycled use cases
In terms of the respective use of recycled and secondary aggregates in specific applications, he says: “To look at high-strength concrete as an example, you want to make sure that your aggregates are consistently of the quality required. With recycled material, because your sources are variable, the material is variable.”
He adds that there are plenty of natural aggregates where they are limited to strength of concrete. Oolitic limestone in the UK is a prime example because that is normally limited to a lower strength concrete. “Whereas if you have higher-spec limestones and granites then you can push the strengths right up to the ultimate levels. It’s a very simple approach – use it for what it’s sensible to use it for and don’t over-specify,” James adds.
Regarding the use of secondary aggregates, he says there is a major opportunity to use a secondary aggregate when doing a mass concrete pour for a big foundation where the actual strength requirement is nowhere near as critical as when doing, for example, a slender column. “These are the sorts of areas where education is important for acceptance into the right places to use these materials.”
He adds that the majority of recycled aggregates goes into highway construction simply because it’s a great way of using the material efficiently and is an area where it does the job well.
James says most construction companies are realistic about what they can and can’t do with recycled aggregates in terms of their overall supply chain. “If your local ready-mix supplier for a project is not in a position to supply material with a recycled element it doesn’t even come into consideration. Look at your supply chain because they are buying materials in. For example, doing drainage on a motorway where there are slip drains with aggregate on the top. If that is viable the specification allows you to use a secondary material. But is it available locally, is it in supply, can you get it there?”
He says contractors are there to make money and are looking for the most efficient and cost-effective supply materials. “It’s got to
be consistent. It’s no good having an order for umpteen hundreds of thousands of tonnes of material if it’s not going to be delivered on time because a day lost on your contract is going to cost you millions.”
Looking back on his career, Brian James says: “In a sense I’ve had two careers – one in construction and one at the MPA, the trade body for the materials supply-side. I spent the first half of my career using the materials, and the second half supporting and promoting the supply of it.”
In terms of achievements in his initial career of construction, he says that one of the most notable projects early in his professional life came when he was involved in tunnelling and was responsible for the biggest pipe jack that had been laid in the UK at the time. “It was technically a fairly difficult job through the Blackheath beds of sedimentary deposits in south-east London...... like digging through
Source: ONS, BGS, MPA calculations
marbles!” Other significant projects have included major highways, bridges and tidal/sea defence works.
In his activities outside the UK, he is particularly proud of his work in the mid-1980s on the construction of the King Fahd Causeway, a 25km series of bridges and causeways between Saudi Arabia and Bahrain, on which he was the construction manager responsible for joining the two Gulf states together. “That was one of the biggest projects in the world at the time and I worked on it for about a year, linking all the roads and bridges that linked up to Bahrain. Their version of Spaghetti Junction if you like.”
Outside of his professional life his interests have centred around sport. He previously played junior club-level rugby and squash, and now owns a yacht which he sails on the east coast near Ipswich.
Brian James can be contacted at: brian.james26@outlook.com AB
Source: UEPG, MPA calculations
CE
Major OEMs have announced new electric machines that are suitable for loading in quarrying applications. Liam McLoughlin reports.
Volvo CE and LiuGong are both introducing new wheeled loader and excavator models that can be used by quarry operators.
At June’s Volvo Days 2024 event in Eskilstuna, Swedish-based quarrying and construction equipment manufacturer Volvo CE said it is launching a modernised range of excavators, equipped with advanced technology for outstanding performance. It is also extending its wide range of electric machines, including its first electric wheeled excavator, displayed alongside its broadest range of charging solutions yet.
On top of a modernisation of its conventional offerings, Volvo CE says it is again delivering on its pledge to lead the industry transition towards fossil-fuelfree construction with several electric introductions in the mid-size segment.
Alongside already-launched electric solutions such as the 23-ton EC230 Electric excavator and cable-connected EW240 Electric MH, the company presented an array of new battery-electric equipment. These include the EWR150 Electric, the first of Volvo’s electric wheeled excavators, and the L90 Electric and L120 Electric wheeled loaders, scheduled for stepwise introductions from late 2024 in limited volumes across selected markets.
They are supported by its broadest range of charging solutions yet with the
launch of the PU40 mobile power unit, for compact equipment, available across select markets and an addition to the already available PU500 mobile power unit. As part of its efforts in securing a reliable electric ecosystem, Volvo CE is also introducing the new My Equipment digital app to help customers manage the charging process more efficiently.
The PU40 power unit is one of a variety of flexible charging solutions. Carl Slotte, Volvo CE head of sales region Europe, said: “Volvo Days demonstrates how far we have come on our electromobility journey, from our first commercial launch in 2019 through to the broad line-up of electric machines and charging solutions we present today, amplified by our range of smart digital tools. The steps we are taking into the electrification of medium- and heavysegment machines paves the way for more customers to decarbonise their operations and seize new business opportunities as societies worldwide transition to a low-carbon future.”
Elodie Guyot, head of electromobility sales for region Europe at Volvo CE, said: “Our commitment to building a better world relies on us driving sustainable change across different equipment types and size classes. We already have dependable electric solutions out in the field across our compact portfolio and a growing part of our mid-size
range. We are excited to continue delivering on this commitment now with three mediumsized zero-emission innovations, across new lines and sizes, all of which benefit from our industry-leading, high-performing electric technology.”
The first electric wheeled loader in its class, the 15-ton Volvo CE L90 Electric is a multi-role solution suitable for a wide range of jobs. These include industrialmaterial handling, forestry, agriculture and landscaping, quarries and mining and waste and recycling.
Like the L120 Electric, it not only has dedicated electric motors for propulsion and hydraulics, enabling full available power to both systems, but enjoys a faster response and shorter cycle times than conventional models.
The L90 Electric will last for approximately 4-5 hours of operation across most medium-duty applications and a full working day in lighter applications. Also similar to its larger brother, the electric-drive motor on the L90 Electric recuperates energy by acting as a generator when decelerating, ensuring a longer run-time and brake life.
It can charge 0-100% in about 70 minutes using a 150kW DC fast charger or PU500 mobile power unit, while its AC on-board cable can power up in 6-7 hours for overnight charging.
The L90 Electric will be available to select markets in Europe in 2025.
Volvo Days is the first major showcase since the company announced the Eskilstuna site as its new corporate headquarters in August last year.
Melker Jernberg, head of Volvo CE, commented: “In this time of rapid change, the global community needs the construction industry to step up and meet societal challenges with safer, smarter and more sustainable solutions. That is why we at Volvo CE are taking a leading role in driving this transformation, investing and partnering across the entire value chain to push boundaries in the right direction. At Volvo Days, we display our most ambitious response yet to those challenges, working together with customers to move our industry forward.”
One of the most significant changes in this year’s Volvo Days was a shift away from silo-ed products and services towards total solutions – tailored to customer needs, no matter where they are on their decarbonisation journey, so that they can take on new challenges and opportunities with the support they need.
In line with Volvo CE’s multi-pronged technology approach to meet varied customer needs, the company has also unveiled a new generation of innovative excavators, the Volvo EC500, EC400 and EC230. The range, which also includes the EC210 and ECR145, has been equipped with intelligent technology in a new electrohydraulic system and improved human machine interface (HMI), and designed for increased fuel efficiency, productivity, safety, and total cost of ownership.
Just like other conventional Volvo CE machines, the new additions to the portfolio can be powered by renewable HVO100 (hydrogenated vegetable oil), which significantly reduces carbon emissions compared to traditional diesel.
Joakim Arndorw, Volvo CE head of sales region international, said: “These new ranges, alongside our electric solutions, prove that Volvo CE is well-equipped
to respond to the different needs of our customers in both regulated and less regulated markets, leveraging our strength to implement meaningful innovation across all our offerings as we move closer towards our ambition for net-zero greenhouse gas emissions by 2040.”
The newest models have been revamped to be more spacious and ergonomic than ever before as part of an ambitious design concept to help customers achieve outstanding results. Volvo CE says the new range – thanks in large part to a new operator environment with improved human machine interface (HMI) – has been built to robustly respond to the challenges of today and tomorrow.
First to be introduced in Europe and Turkey are the newest EC500, EC400 and EC230 crawler excavators – all of which benefit from the same range of technologically advanced features and were unveiled at Volvo Days 2024.
A stylish new operator environment provides even more space and comfort, with a cool box to store items and USB and Bluetooth connections to charge
mobile phones, play music and aid on-site communication. Furthermore, thanks to an improved HMI, a keyless engine start and an always-on camera, a productive working day can be carried out with ease and safety.
China-based LiuGong says it is changing the game in the UK with a range of fourthgeneration battery-electric-vehicle (BEV) machines developed alongside European customers. The ‘green team’ includes electric wheeled loaders, mining trucks and electric excavators, all underlining the company's leading role in BEV technology.
The line-up is headed by the new 856HE European edition electric wheeled loader. Packed with a 423kWh battery pack, the tough machine can work 10-12-hour shifts on a single charge. Powered by two independent motors, one for the driving transmission and one for the hydraulic loader arms and auxiliarys, the 856HE is described as an immensely powerful machine offering full drive traction from as little as 2km/h.
The machine has proven itself in the field. Early production units, tested with customers, have exceeded 15,000 operating hours yet still have more than 88% stateof-health in their batteries. LiuGong says this fact alone proves that its machines are capable of delivering the total life endurance capability demanded by genuinely tough working conditions.
Next is the new 870HE electric wheeled loader. Powered by the same 423kWh battery as LiuGong's popular 856E but with increased power and load-carrying capacity, this machine typically comes with a 4.7m3 bucket and slots into the 250-3050hp segment. Targeted at heavy applications such as quarrying and aggregates, this powerhouse has already received phenomenal interest in Europe from aggregates businesses and key account customers.
The new 820TE electric wheeled loader is LiuGong's first compact wheeled loader product. The machine has a large spacious cabin, is capable of 40kph travel speeds and is powered by a 70kWh battery. The 820TE delivers 5-6 hours of tough work between charges and can recharge within 60 minutes. At a maximum height of 2.5m and available
with a 4th-line auxiliary spool, this machine is excellent for agricultural and industrial applications.
The new 922FE medium-class electric excavator is powered by a 423kWh battery. This excavator can work a full 8-10-hour shift and is a high-performance machine with a motor delivering 165kWh of power, around 45kWh higher than a typical diesel model.
Also taking the field is the new 9027FE electric excavator. This compact model takes LiuGong's popular short tail swing 9027F and changes the power pack to a 20kWh LFP battery pack. The smallest of LiuGong's new machines was on show at June’s Hillhead 2024 quarrying and construction exhibition in Derbyshire, UK. It enables 3-4 hours of constant work and a rapid charging time of 90 minutes when using a fast charger.
LiuGong says that it has long been at the forefront of China's revolution in BEV research and development, driving design and innovation to create even greater sustainability and customer value.
LiuGong’s strategic aim is to be a top 10 construction-equipment brand in Europe by 2027 and No. 1 in BEV product innovation and sales. Its ambitious plans will see it launch more than 40 BEV models by 2027, including new electric excavators, wheeled loaders, motor graders, dumpers and access equipment.
Back in 2014 LiuGong's designers and engineers were adapting standard diesel machines to carry battery packs and electric drivelines. Now, LiuGong is launching its fourth-generation machines, designed around the total needs of the operator and supported by the European R&D centre,
working closely with customers to fine-tune for the UK market.
Global sales of BEVs have already topped 3,500+ units, and LiuGong has achieved more than one million operating hours for BEV machines. The company says its 856HE electric loader has played a key part in this success. With more than 2,000 machines currently working in the field, LiuGong says the 856HE is easily the most popular loader in China, the world's biggest market for BEVs.
LiuGong's latest BEV machines are based on proven technology and extensive field trials with European customers deeply involved in the development process. With their distinctive green livery, these machines have been designed to deliver for the owner, the operator and the environment.
Harry Mellor, LiuGong European product director, said: "We have proved and are continuing to prove our capability in BEV technology. Our new 4th-generation wheeled loaders clearly show that we have the knowledge and credibility in BEVs that customers want and respect. This knowledge has not been acquired overnight but is the result of tough work in the field."
Develon, formerly known as Doosan Construction Equipment, demonstrated a number of its loading machines at Hillhead 2024.
The static display on Develon‘s stand featured the DX530LC-7 53-tonne crawler excavator and the DL420-7 wheeled loader. In the demonstration area, further products for the quarry face showing their paces included the DX420LC-7 43.5-tonne crawler excavator and the DL550-7 wheeled loader.
Among new products being shown for the first time at Hillhead on the Develon stand
was the DX235LCR-7 24.3 tonne crawler excavator.
The DX420LC-7 and DX530LC-7 are part of the range of large crawler excavators from Develon that also includes the DX800LC-7 80-tonne and DX1000LC-7 100-tonne machines. Overall, all the models in the DX-7 range of crawler and wheeled excavators from 14- to 100-tonne combine enhanced comfort with the latest features to boost fuel efficiency, uptime and return on investment, with a focus on increased power, robustness and agility.
The DL420-7 and DL550-7 are two of the four biggest standard models in the DL-7 range of wheeled loaders from Develon, that also includes the DL480-7 and DL580-7 models. With redesigned buckets offering up to 7% more capacity, these DL-7 wheeled loaders provide easier and faster loading with maximum bucket capacities from 4.5 to 6.4 m3. Altogether, the eleven DL-7 wheeled loaders in the Develon range with bucket capacities starting at 2.0 m3 provide increased productivity for a very wide range of material-handling applications.
HD Hyundai Construction Equipment introduced two heavy crawler excavator models and its largest wheeled loader at the Hillhead 2024 quarry exhibition.
The company has announced its largest Stage V crawler excavators, with the arrival of the 80-tonne HX800A L and the 100-tonne HX1000A L. These heavy-duty machines have been designed to operate in mines and quarries, as well as in bulk earthmoving for construction and infrastructure project applications. They deliver maximum productivity with reduced total cost of ownership (TCO).
Both excavators are powered by Perkins diesel engines, delivering class-leading power and economy. The HX800A L uses the six-cylinder Perkins 2506J, providing 400kW (539hp) at 1,800rpm and 2,468Nm of torque at 1,400rpm. The larger HX1000A L is powered by the Perkins 2806J, offering 460kW (629hp) at 2,000rpm and 2,952Nm at 1,300rpm.
“These heavyweight excavators will build on HD Hyundai’s presence at the heavier end of the market across Europe, providing a highly productive digging and loading solution for mines, quarries, bulk earthmoving contractors and heavy civil engineering sites,” said product manager Gert Peeters.
The HL985A loader builds on the success of smaller A-Series machines, adopting the same robust, durable design, with proven driveline components and an exceptional operating environment. The machine is powered by the latest Cummins X12 diesel engine.
Product manager Stefan Schwill, comments: “Suitable for a wide range of tasks, in quarrying, recycling and rehandling applications, the HL985A offers more power for less fuel used, delivering a total-cost-of-ownership benefit for customers.” AB
A major quarrying and mining hauler manufacturer has extended its rigid dump truck range, while another big sector name has signed a key distribution deal in West Africa. Guy Woodford reports
Following the success of the R100 hauler, Volvo Construction Equipment’s (Volvo CE) launch of the 55-tonne payload R60 and 65-tonne R70 rigid haulers broaden quarrying and light mining customers’ hauling options.
Like its bigger 95-tonne brother, the R100, the R60 and R70 are designed to help drive down the total cost of ownership and introduce the latest comfort and safety features.
While the R60 has a body volume of 36.04m³, the R70 offers 42.4m³. They may be smaller in size, but fans of the flagship R100 will see many of the same features and benefits of the latest E-generation in the new machines.
Launching these new units gives quarry and light mining customers greater production options – not just with these three rigid haulers but also Volvo CE’s articulated hauler range. (The R60 rigid has the same 55-tonne payload as the company’s A60H articulated hauler).
The choice between a rigid hauler and an articulated hauler in quarrying and mining
sites depends on various factors, including the specific needs and conditions of the operation. While rigid haulers thrive on sites with wide, firm, well-maintained haul roads, where they can travel fast (up to 61km/h) over long distances, articulated haulers’ trump card is on uneven, narrow, slippery and steep haul roads, where the haul cycle is shorter. Introducing the R60 and R70 allows Volvo to tailor hauling solutions to suit the particular site dynamics. Volvo Site Simulation service can help meet production targets, reduce CO2 emissions and boost profitability by recommending the optimal site set-up/machine fleet.
The new machines are being made at Volvo CE’s Motherwell plant in Scotland, a site that for nearly 75 years has been the global heart of rigid hauler development. Its haulers are famed for their high productivity, low maintenance requirements and long service life, and the R60 and R70 are no exception to that rule. With a low centre of gravity, balanced weight, and tough-yetflexible chassis, these machines embody the robustness, performance, and reliability that deliver low operation costs.
Maximising tonnes of material moved per hour is said to be a core tenet of the design of the R60 and R70. The new machines feature
a V-shaped haul body that is designed to deliver maximum load retention while at the same time minimal material carry-back postdumping. The dumping process itself is also speedy, thanks to a fast-tip system. Providing real-time insights on payload, the optional onboard weighing system helps operators apply the industry standard 10/10/20 payload policy – where the machine can take 10% overload for 10% of the time but should not exceed 20%.
Regarding grip, the high-drive axle multiplication ensures maximum traction. At the same time, the already efficient hightorque engine is further supported in cutting fuel consumption by the automatic adaptive gear selection offered by Volvo Dynamic Shift Control. The engine also has a selectable Eco mode that defaults to the most efficient gear, while the auto engine idle shutdown reduces engine wear – and both of these boost fuel efficiency.
As with the R100, the R60 and R70 are said to be a haven for operator comfort and safety. Starting with safety, the cab is fully ROPS/ FOPS certified, and access is gained from both sides via anti-slip steps. When moving, the haulers feature gear-dependent speed control and a selectable brake or transmission retarder. The gearbox also has overspeed protection and a neutral coast inhibitor for downhill operations. There is fail-safe braking
and a secondary steering system to keep the machine on the right track. Visibility is among the most important elements of safety, and the operators of the R60 and R70 have perfect vision – a result of the large windscreen and low-raked dashboard, further supported by the left-positioned operator station (that aids safe passing) and 360-degree Volvo Smart View option.
Volvo CE says that one of the strengths of the R60 and R70 is their ease of maintenance. Helping to keep repair costs and downtime down, the units have long 500-hour service intervals, ground-level tagout, and easyto-reach service points. Common-sized bearings keep parts stockholding simple and cost-effective. Technology also plays a part in onboard service diagnostics, while the CareTrack telematics system looks on from afar. These help to rapidly identify potential faults and maximise uptime.
The capacity of the R60 and R70 are well matched with the loading abilities of Volvo CE’s EC950F crawler excavator, and the L350H wheeled loader. Introducing the R60 and R70 usefully increases Volvo CE’s portfolio for the quarrying and mining segment.
Rokbak, a Scottish articulated hauler manufacturer and member of the Volvo Group, has partnered with Heavy Machinery Dealership (HMD), a premier provider of construction, mining and quarrying equipment in West Africa.
Established in 2003, HMD has built a strong reputation as a specialised distributor of premium heavy machinery and parts and is dedicated to contributing
to Africa's infrastructure development. As an experienced local partner, HMD will help bring Rokbak ADTs to an extensive customer base in Nigeria, Ghana, Senegal, Benin, Guinea and Cote d'Ivoire. HMD is said to assist the growth and success of its customers through reliable, tried and trusted equipment, together with strong spare parts availability and aftersales support.
"Rokbak has an excellent reputation, and our customers know and trust the Volvo brand," says HMD CEO Mathew Khouri. "Rokbak haulers will complement our product portfolio well, offering the thriving mining, quarrying and construction industries in West Africa a reliable and efficient ADT. With Rokbak, we will deliver high-quality trucks alongside our exceptional service and support."
Africa's construction market is estimated to be worth US$58.42 billion (bn) and is expected to reach $74.81bn by 2029. In particular, West Africa's construction industry is experiencing substantial growth, driven by urbanisation, infrastructure development and mining activities. Nigeria and Ghana are the biggest mining markets in the region, with the global push for green energy solutions, meaning reserves of critical minerals such as lithium, manganese, and nickel are in high demand. The Nigerian mining sector alone is estimated to boast 44 different types
of commercially viable minerals worth an estimated $700bn.
The demand for reliable, high-performance machinery is at an all-time high. Rokbak offers two hauler models. The RA40 is the largest with a gross power of 331kW, a maximum torque of 2,225 Nm and a 38-tonne payload. It is a popular choice for major infrastructure and mining projects, with its effective powerto-weight ratio enabling the fast movement of heavy materials. Like the RA40, the 28-tonne RA30, with a gross power of 276 kW and a maximum torque of 1880Nm, benefits from a transmission retardation system, a fully adaptable drivetrain and easy maintenance to suit a variety of different job sites.
"Our partnership with Rokbak represents a significant advancement for our customers in West Africa and continues our vision to become the leading supplier of heavy machinery in Africa through customising solutions to customers' needs," says Khouri. "Rokbak's robust and reliable haulers are perfect for the region's requirements. We look forward to working closely with Rokbak to enhance the capabilities of our customers and contribute to the development of the local infrastructure and important applications in the region."
Rokbak's articulated haulers are renowned for their durability, efficiency, and ease of use, making them ideal for the region's challenging terrain and demanding projects. HMD's local expertise and infrastructure will provide essential support and training, ensuring optimal use of Rokbak equipment.
"We are delighted to partner with HMD in West Africa," says Rokbak’s managing director Paul Douglas. "HMD's reputation for excellence and customer satisfaction aligns perfectly with Rokbak and the Volvo Group's values. This partnership is a testament to our commitment in expanding our global reach and supporting customers in even more territories in the construction, quarrying and mining industries.
"Our high-quality haulers, combined with HMD's vast experience and local expertise, will deliver exceptional value to our customers." AB
No matter how challenging your needs, BKT is with you offering a wide range of OTR tyres specifically designed for the toughest operating conditions: from mining to construction sites. Sturdy and resistant, reliable and safe, able to combine comfort and high performance.
BKT is with you, even when work gets tough.
For
europe@bkt-tires.com
A first-of-its-kind radial telescopic conveyor is set to attract great interest from quarry operators' attention globally. Guy Woodford went for a close-up look.
At this year’s recent edition of Hillhead, the international quarrying, construction and recycling equipment show, Telestack showcased its new quarrying-suited TSR 40, the industry’s first roll-on-roll-off (RORO) radial telescopic conveyor.
Road transport is a common problem with standard radial telescopic conveyors, especially in areas with restricted road access aligned with permit stipulations and special load regulations. This is a major issue with radial telescopic units because these are typically transported in euro-liners or containers and then built up on-site with cranes and/or tools. It generates extra costs in labour, vulcanising, and the extra set-up time required. The new TSR 40 eliminates this transport problem because it can be transported like any normal RORO-tracked mobile unit. The unit can be transported at a width of 3m x height of 3.5m x length of 23.2m, making it easy to transport within many road networks, especially in, for example, areas of Europe with more restrictions.
Another standout feature of this unit is its ability to be driven electrically, differentiating it from standard diesel hydraulic systems. The TSR 40 is an ‘all-electric’ driven unit with an integrated diesel electric generator built into the
chassis to power all unit functions, including tracking and conveyor-drive operation. This feature also allows the operator to plug in their own 3 x phase electric power on-site, lowering fuel consumption and reducing their overall carbon footprint.
“The TSR 40 is a very versatile unit. It can track itself up, down, and off a low loader and is
ideal for working on difficult-to-get-to sites that require bigger throughput rates. It is a very good rental unit for a dealer, and its on-board power generator makes it a good option for customers with no power available on-site,” Alan Gilmore, Telestack’s regional sales manager, tells Aggregates Business at Hillhead 2024, staged 24-27 June at Tarmac’s Hillhead Quarry near Buxton, Derbyshire, England.
He continues: “We are pushing the TSR 40 in Europe and have already sold two units, one to a customer in Sweden and the other to a Netherlands-based customer. We think it will be a big seller in Germany and Scandinavia, as they are bigger mobile (radial telescopic conveyor) markets. Our dealer in Norway, Fredheim Maskin, is a big driver of all-electric drive solutions.”
The TSR 40 utilises its radial, telescopic, and luffing features to allow the operator full control and flexibility when stockpiling a range of materials. Gilmore notes that the up to 800 tonnes/hour unit has an integrated PLC (programmable logical controller) stockpiling system that eliminates material segregation, degradation, contamination, and compaction— all key to maintaining the quality of your material during the stacking process.
The TSR 40 has a large stockpile capacity,
The TSR 40 is ideal for automated stockpiling and perfect for use after secondary crushers, screeners, and fixed conveyors.
RORO Mobility - Transport the TSR 40 as easily as any Roll-On Roll-Off tracked mobile unit. No need for onsite cranage or vulcanizing!
Enhanced Product Quality - Increase stockpile capacity by up to 30% compared to conventional fixed-length conveyors. The integrated PLC system maintains material quality by preventing segregation, degradation, contamination, and compaction during stacking.
Eco-Friendly Design - The all-electric TSR 40 features a built-in diesel electric generator to power all operations, including tracking and conveyor drives. Utilise on-site 3-phase electric power to reduce fuel consumption and improve your carbon footprint.
which, claims Telestack, allows up to +30% larger stockpile capacity than conventional fixed-length conveyor systems with increased site mobility.
A lattice-frame design allows the TSR 40 to automatically stockpile from secondary crushers, screeners and fixed conveyors while stockpiling materials such as aggregates, sand, and gravel. The proven lattice-frame structure also ensures maximum strength with reduced overall mass and an impressive radial potential of up to 270˚for maximum stockpiling capacities.
Telestack says introducing the first RORO mobile radial telescopic conveyor to the market highlights how the Astec-owned company is ahead of the curve and constantly assesses market demands. The Omagh, Northern Ireland-headquartered firm has a full range of radial telescopic conveyors up to 58m long and with a maximum throughput of 3,500 tonnes/ hour.
“We will continue to innovate, and the TSR 40 is another model in our arsenal,” says Gilmore, adding, “We have a larger range of radial telescopic conveyors than any other industry manufacturer. We are also all about customisation. We will meet any specific requirements a customer has for a project.”
Smiley Monroe unveiled its new look brand identity and an exciting new product prototype at this year’s Hillhead show.
The Northern Ireland-headquartered conveyor belt manufacturer selected Hillhead as the local industry gathering to bring its refreshed brand identity to life, signifying Smiley Monroe’s evolution into a global business on a mission to revolutionise belt conveying.
The geometric brandmark with its origins in the hexagon is a nod to the Giant’s Causeway and Smiley Monroe’s Northern Irish heritage (and the company’s description as the ‘Giants of Belting’) , while the shape, like the company, is on an upward and outward trajectory.
Smiley Monroe says its ‘Giant Leap’ group sustainability strategy is key to achieving its ambitious growth plans and 2030 goals, aligned to seven of the UN Sustainable Development Goals (SDGs). Smiley Monroe’s UK operations are zero waste to landfill and have been powered by 100% renewable electricity since 2019, reducing their absolute Scope 1 and 2 Greenhouse gas (GHG) emissions by 52% by 2023.
The Smiley team reports that the prototype 'Go Lite' belt was well received at Hillhead. With a 40% reduction in belt weight and matched, or superior, performance compared to existing
thicker, heavier alternatives, ‘Go Lite’ also comes with a significantly lower carbon footprint - good news for design engineers tasked with minimising more than just machine weight.
With expressions of interest welcomed at Hillhead, Smiley Monroe is now working closely with customers to field-test the ‘Go Lite’ belts, which they hope will support the positive in-house lab test results.
Martin Engineering has unveiled its next generation of secondary conveyor-belt cleaners engineered to reduce dusty carryback and lower maintenance time. Designed to withstand the stress of heavier loads carried on wider, thicker belts at higher speeds, the Martin SQC2S Orion secondary cleaner (Orion) features individually cushioned tungsten carbide blade cartridges for effective cleaning without risk to the belt or splices. A two-tiered tensioning system means minimal adjustments and monitoring throughout the blade's life.
The heavy-duty blades are mounted on a slide-in/slide-out assembly for faster and safer one-worker external servicing. The result is improved belt cleaning with less dust and maintenance for greater workplace safety at a lower cost of operation.
“We field-tested the Orion over several months with competitor designs in punishing mining environments and found that the new design significantly outperformed the competition,” said Dave Mueller, conveyor products manager for Martin Engineering.
“At the end of the testing period, customer participants started replacing all their heavyduty secondary cleaners with the Orion. We
now view this design as the future of our secondary cleaner line moving forward.”
Secondary cleaners play an essential role in the belt-cleaning process by significantly reducing the volume of dust and fines dropped
as carryback on the belt return. Primary cleaners release most of the abrasive material on the belt after discharge. Located below the head pully just behind the primary, secondary cleaners scrape off the fines and dust that hide in cracks and divots in the belt. Carryback is attributed to many environmental and operational issues,
such as air quality violations, fouling of rolling components and machinery, and increased labour for clean-up and maintenance.
The Martin SQC2S Orion secondary cleaner is appropriate for all bulk-handling material applications. The unit comprises six-inch (152.5mm) blades mounted on a square steel tube assembly. It is not designed for reversing belts but is suitable for 18 – 96 inches. (4572438.5mm) belt widths, belt speeds up to 1200fpm (6 MPs), and temperatures up to 250ºF (121ºC).
“What sets this unit apart from others on the market is the innovative, dual-tensioning system with independent heavy-duty tungsten blades which are game-changing design features,” Mueller explained. “The first tensioning level is supplied to the entire assembly using the heavy-duty SQC2S Tensioner, which applies light upward torque evenly across the belt profile for less friction and no wear on splices.”
The second level of tensioning is on the individual blade assembly. Each Orion blade assembly is attached to a steel square tube assembly secured by a mounting plate. The square tube houses a rubber tensioner with a torsion arm bolted to each side. A specialised tungsten blade is attached to the arm. The system is mounted at a 90-degree angle and then tensioned so each blade is vertical and perpendicular to the belt. As the belt runs, each blade assembly adjusts independently to precisely match its profile, permitting it to compensate for camber, flaws/blemishes, and stubborn material stuck to the belt’s face. To accommodate belt cupping and other uneven surfaces, the blade assemblies can be individually adjusted to match the belt profile.
The blades are designed for heavyduty abrasive applications in dry and wet environments. Tested on hard rock and slurry belts, the Orion blades offered superior cleaning results with a longer equipment life. This is due to the rugged tungsten carbide core surrounded by mild steel. Blades are also available in stainless steel for specific corrosive materials.
The blade design features a deflector shield made from polypropene or rugged nylon for high-temperature applications. Mounted directly to the blade in an outward scoop
design, the shield ushers loosened material away from the mainframe and toward the discharge chute. This mitigates build-up on the assembly, extending the blade’s effectiveness and reducing the amount of maintenance.
Safety and ease of maintenance are key features and a core priority for all Martin Engineering designs. The slide-in/slide-out design allows a single worker to perform maintenance with easy access outside the conveyor structure, eliminating the need to crawl underneath or awkwardly reach inside. This greatly improves workplace safety and reduces the time and labour required for maintenance, significantly lowering the cost of operation.
“Every bulk-handling operation is unique and requires versatile and adaptable equipment, and I think we’ve achieved that with the Orion,” said Mueller. “Martin Engineering products are developed to improve efficiency and safety without compromising belt health. This design gives customers more options and superior results, regardless of the material or the process.”
McCloskey International, whose wideranging off-highway equipment portfolio includes feeder, tracked and wheeled stackers, has appointed Jane Halfpenny as sales director – EMEA & Southeast Asia. Halfpenny is responsible for sales activities in Europe, the Middle East, and Africa, as well as countries in the Southeast Asia region.
She joins McCloskey International with over 10 years of experience in the global heavyconstruction-equipment sector. Throughout her career, she has held roles in sales, distribution, and marketing on the OEM side for companies such as Hyundai Infracore and CNH Industrial, as well as in commercial vehicle and financial services.
Halfpenny will lead McCloskey International's regional sales teams, sales development, and dealer growth.
“I’m keen to speak to prospective dealers interested in serving markets where we seek to develop our distribution,” says Halfpenny, who will be based in the UK.
RotaLube, a leader in conveyor- lubrication technology, has launched the RotaLube ECO Lubrication Kit. This innovative solution brings
the precision of RotaLube’s patented sprocketshaped applicator to a handheld, user-friendly format, offering significant cost and operational efficiency benefits for a wide range of industries.
David Chippendale, director of RotaLube and an experienced conveyor engineer, developed the original sprocket-shaped applicator to address the prevalent issue of inefficient lubrication in conveyor systems. Ineffective chain lubrication leads to costly production downtimes, excessive wear, unnecessary oil consumption, and product damage due to oil contamination. By applying lubricant indiscriminately and inefficiently, traditional lubrication methods often miss the crucial pins and bushes where friction and wear occur.
Chippendale's solution was to design an applicator that ensures lubricant is applied precisely where needed. Initially part of an automated lubrication system, this applicator proved highly successful across various industries. Recognising the need for an alternative solution, RotaLube has now adapted this technology with a handheld spray can.
“The automated RotaLube system, while effective, isn't suitable for all customers due to space constraints, low-lubrication-frequency needs, or budget limitations,” Chippendale explains. “Our goal was to make precise lubrication accessible to a broader spectrum of customers.”
The new RotaLube ECO Lubrication Kit includes everything needed for targeted lubrication using a handheld spray can. The kit includes a RotaLube applicator, mounting bracket, flexible tube, aerosol-can adapter, connectors, and a restrictor to control lubricant release. It works with appropriate lubricant, but RotaLube recommends its biodegradable chain lubricant for optimal performance.
“The ECO in the name highlights both the economic and ecological benefits of the kit,” Chippendale said. “It's a cost-effective alternative to automated systems and supports environmental care by reducing oil consumption and spillages. The flexible tube design also promotes safe and efficient maintenance by enabling technicians to apply lubricant from a distance without removing safety guards.” AB
MB Crusher says the use of suitable screening buckets can enable stockpiles to be moved quickly and cheaply, improving the efficiency of quarries
Casting off old practices can be a brave move in the use of crushing and screening buckets, and doing it by enhancing your machines with suitable equipment adds efficiency, speed and profitability. Liam McLoughlin reports.
Aggregates are the most used material in construction, being the basis for the construction of roads and infrastructure and constituting a fundamental element for asphalt pavements and concrete. This is why any company that relies on aggregates can drastically reduce costs and complete projects on time with the appropriate screening buckets, according to MB Crusher.
The Italy-based crushing and screening bucket manufacturer says that demand for aggregates continues to grow with urbanisation and infrastructure development, leading to the difficulty of supply and high production costs becoming increasingly evident.
It has set out the ways in which the equipment it produces is key to obtaining highquality aggregates at a reduced cost per tonne.
Once accumulated, the overburdened materials resulting from the preparation of a quarry often occupy large areas, which could limit the operation of the quarry. Moving these huge stockpiles means moving – at very high costs – thousands of cubic metres of material.
MB Crusher says that some materials producers have found a solution, installing an MB-S23 screening bucket with a 10cm x 10cm grid basket on the Hitachi Zaxis 460 LCH excavator already working in the quarry. In doing so, the customer obtained two types of material: one with dimensions greater than 10cm, retained in the basket, which was directly loaded on the dumper and transported to the crushing plant to continue the
processing process. While the material with dimensions less than 10cm, is used for filling and making embankments, thus avoiding additional costs for its disposal.
“From an expensive process, therefore, to an activity that has also increased profit margins: now the customer not only saves on the costs of getting rid of the overburden, but also has inert material for his plant and can even resell the excess,” the company states.
MB Crusher adds that even the off-cuts in the aggregates-production process can find a new use, with producers sometimes not realising that they are sitting on waste that can be turned into profit.
“We are talking about extraction and production waste, which is stockpiles to take up space, unused . Instead, it can be transformed into quality material, ready to be reused or resold with the MB Crusher bucket,” it says. “To sum it up, nothing is thrown away: by giving value to the stockpile already available, costs are therefore reduced. As did a company in southern Italy, which had a big problem with the waste of stone material, which continuously required significant transport, disposal and treatment costs. So, they decided to "change course" and by installing a crusher bucket on his 9 tons JCB 4CX backhoe he crushed the waste, producing
sellable inert material for the installation of substrates.”
Raw materials used in construction are not infinite, and for this reason, MB Crusher says that using ‘secondary aggregates’ – such as the rubble derived from the demolition and redevelopment of old buildings – is a good habit that leads to rewards. These materials used to be considered waste and would have incurred expensive landfill fees. They are now processed so that they can be reused. By taking full advantage of the heavy machines already present on site, it is easier done.
“As during the demolition of an old grain deposit, where the steel present inside the reinforced concrete was recovered and resold, while the overburden material was reused as a road substrate,” says MB Crusher. “How? With a BF90.3 crusher bucket installed on the excavator that was already in place.”
MB Crusher says it units are designed for versatile use in recycling plants, quarries, landfills and directly on construction sites and are a solution for the independent production of aggregates.
Italian screening buckets manufacturer Simex has expanded its family of VSE screening buckets for excavators.
Simex says that finding an effective way to separate and screen materials directly on-site is vital for cost and time-saving-conscious construction and earthmoving fleet operators. Available in eight models for excavators from 1.2 to 50 tonnes, Simex VSE screening buckets are specifically designed for separating different-sized materials directly on-site. The VSE product range features the rapid adjustment of output size via an instant control in the cabin. This exclusive patent allows the shafts to be instantly distanced and closed, with a maximum travel of 40mm.
Simex’s FIT screening-tool technology, another standout feature of VSE screening buckets, remains popular with customers three years after its introduction. The low-maintenance system allows for the easy interchange of every single disc or blade without unstrapping shafts. The Italian company says this means 75% less maintenance costs than the previous system. Multiple configurations are possible, depending on the materials to be screened. Simex offers users four different set-ups, but many others are possible thanks to the 100% interchangeable screening elements.
In backfilling operations of pipelines, especially in the oil and gas industry, the instant, adjustable output size leads to numerous benefits in terms of saving time and money. Simex’s patent allows various output sizes of the screened materials to be obtained rapidly, both for bedding and for the subsequent backfilling of the excavation. With Simex VSE there is no downtime due to technical interventions for the spacing operations of the shafts, as happens in traditional screening systems.
The operator instantly closes the shafts, loads the bucket and screens a small-grainsize material (0-15 mm) for bedding, avoiding damage to the pipes from rubble and stones.
With the same control in the cab, the operator instantly opens the shafts obtaining a medium-grain-size material (15-55 mm) to backfill the excavation. Oversize material will be deployed.
Given the growing demand for specific screening buckets for the sector, Simex is launching a new large model, for heavy excavators, called VSE 50, in order to guarantee maximum performance in covering underground pipes, with the correct output size. With its SAE bucket capacity of three cubic metres, the VSE 50 is designed for 35-50 tonnes excavators and will be the biggest screening bucket of the range.
Simex concludes that its VSE screening buckets aim to sustainably recover and reclaim soil and aggregates resulting from demolition, helping deliver a circular economy.
Building on decades of field experience with its CW coupler platform, Caterpillar has announced three new Hydraulic Connecting CW (HCCW) coupler models in the Africa, Middle East, Europe and Turkey regions. Connecting seamlessly to the machine’s hydraulics, HCCW quick couplers are designed to allow operators to switch between hydraulic attachments with full functionality in seconds from the safety of the cab.
Compatible with any Cat hydraulic attachment, quick changes with the HCCW give the operator the ability to use the right attachment for the job, increasing overall productivity and tool utilization. Fast attachment swap-outs with the hydraulicconnecting interface can help save time over static couplers or pin-on attachments. The field-proven CW coupler platform is built to
status to the operator. Complying with the European EN474 standard, multiple electronic and mechanical measures help to secure the attachment, even in the event of pressure loss. Visual and audible confirmations inside the cab inform the operator of successful attachment connection.
The new design features enhanced hydraulic flow to reduce hydraulic restriction, minimizing heat build-up and reducing the amount of engine power required for operation. Machined and sized for highflow performance, the couplings ensure hydromechanical attachments operate to full capability with limited back pressure. Their reliable hydraulic-fluid connections help to prevent spills when changing the attachment, while the quick-disconnect design helps improve the lifespan and facilitates servicing ease.
Customers with existing Cat excavator fleets using CW hinges do not need to retrofit their machines to use the new HCCW quick couplers. Fabricated tools, such as buckets, can seamlessly switch between existing CW and new HCCW couplers. New Hydraulic Coupling (HC) brackets allow the use of existing hydromechanical tools like shears, hammers and grapples with the HCCW.
Internally routed hoses in the coupler and bracket protect against damage and reduce overall hose and repair costs. They leverage the trusted quick-coupler platform with the addition of proven, durable and high-performing male and female quick disconnects located in the coupler and the attachment bracket. The cover lid and sealing provide added protection for couplings and prevent hydraulic-system contamination. AB
A major global manufacturer makes a cogent case for electrifying quarry dewatering. Meanwhile, new dewatering products and installations and a new strategic partnership create a lively global market. Guy Woodford reports
Niccolo Tivelli, product application manager - surface pumps at Atlas Copco Power and Flow, and Bart Duijvelaar, product marketing manager - submersible pumps at Atlas Copco Power and Flow, have told Aggregates Business how electrifying the dewatering process in quarries is a leap towards efficiency.
“In quarry operations, dewatering – the process of removing unwanted water from the job site – is indispensable to ensuring the efficiency of critical quarry and mining operations. Traditionally, this process has often been carried out using diesel pumps. However, this essential process is undergoing a significant transformation toward electrification. This shift promises enhanced operational efficiency and aligns with the global push toward a more responsible industrial practice. This article explains the fundamental steps to electrify the dewatering process in quarries.
“The first step towards electrification is thoroughly evaluating your current dewatering process. This involves understanding the volume of water to be managed, the layout of the quarry, and the existing dewatering infrastructure. It's also crucial to consider the availability of electrical
power sources nearby or the feasibility of integrating renewable energy sources as part of the electrification process. Lithiumion batteries and photovoltaic panels have become solid complements to the onsite power grid, sometimes becoming a reliable alternative in remote locations.”
Tivelli and Duijvelaar say these technological innovations foster the evolution of rugged and reliable mobile energy-storage systems (ESS), giving quarrying operators greater flexibility and increased operational efficiency by optimising energy generation, distribution and consumption.
“Once you understand your needs, the next step is to explore the available electrified dewatering solutions. Electric submersible pumps are among the most reliable choices for quarry dewatering, known for their efficiency and ease of installation. Atlas Copco’s WEDA electric submersible pumps deliver best-in-class performance over a longer lifetime than comparable pumps. The WEDA pumps feature innovative elements, including a high performance-to-weight ratio, hardened high-chrome impellers, and stateof-the-art Wear Deflector Technology. This unique technology is designed to minimise wear, ensuring durability for a longer working life than other alternatives in the
market. The pump range has been designed with the latest 3D modelling techniques to deliver high efficiency and reduce unplanned downtime in demanding working environments such as quarries.
“Electric self-priming dewatering pumps offer practical solutions for specific dewatering requirements, providing end-users with a wide array of solutions to match application requirements. For example, Atlas Copco’s E-Pump range comprises an innovative portfolio of electric self-priming dewatering pumps featuring canopy and open-set configuration models. These digitally connected surface units offer an exciting alternative to diesel-powered dewatering pumps, with lower local emissions and a reduced total cost of ownership. Developed to provide high performance, reliability, and ease of use, these electric self-priming pumps are plug-and-pump solutions, making them quick to install.”
Tivelli and Duijvelaar explain that transitioning to an electrified dewatering system requires an upfront investment. However, they stress that the long-term benefits often outweigh the initial costs. “Conducting a cost-benefit analysis can help quantify these advantages, considering factors such as reduced fuel consumption,
lower maintenance costs, and potential tax incentives for adopting new technologies. Additionally, the positive environmental impact and the enhancement of a company's sustainability profile can lead to improved stakeholder relations and potentially open new business opportunities.
“Implementing an electrified dewatering system involves careful planning and execution. It's essential to work with experienced suppliers and installers who can guide the transition and ensure that the new system is correctly integrated into your operations. Therefore, partnering with a manufacturer that provides expert consultation can help assess a quarry's specific needs and design a tailored dewatering solution that maximises efficiency and meets sustainability goals, considering the site's unique characteristics.
“Equally important is investing in training for the team, ensuring that they are equipped with the knowledge and skills to operate and maintain the new system effectively. Relying on a manufacturer that offers comprehensive training and ongoing support is highly recommended. This includes operational training, maintenance best practices, and troubleshooting, ensuring that the quarry can leverage the full potential of the electrified dewatering process.”
Once the electrified dewatering system is operational, Tivelli and Duijvelaar emphasise that continuous monitoring is essential to ensure optimal performance and predict service and maintenance actions. “Data analytics tools can be invaluable, enabling the tracking of efficiency, early identification of potential issues, and informed decisionmaking to optimise the process further.
Leveraging Atlas Copco’s connectivity tools can aid in continuously monitoring and optimising the dewatering process. This data-driven approach allows for informed decision-making, ensuring your operations remain efficient.
“Electrifying your quarry dewatering process is not just a step towards modernisation; it's a commitment to responsible operational excellence. By
embracing electrified solutions, quarries can significantly reduce their environmental impact, enhance efficiency, and position themselves as leaders in the responsible extraction of natural resources. The journey towards electrification requires careful planning, investment, and adaptation, but the environmental and economic rewards make it a compelling choice for the future of quarry operations.”
One of the contractors' largest challenges when pumping slurry water is finding the right equipment to efficiently and seamlessly complete the job. Pumping from pits containing sand, grits, or debris requires heavy-duty equipment designed to handle abrasive materials and work continuously without failure. Tsurumi Pump says its Agitator pumps are the answer.
Agitator pumps use an agitator propeller with the same shaft as the pump's impeller. While the two spin in the same direction, the agitator blades are in the opposite orientation
to those of the impeller. The agitator provides a propelling force to stir up solids near the floor while the impeller pumps the now-suspended solids along with the fluid. They keep the mud circulating to prevent solids from settling while allowing pumping to continue without obstructions.
“The use of agitators in coal mines and quarries is well known, but not everyone is aware that they can be used for any liquid containing solids that need to be pumped,” explains Kevin Boicken, Southeast US sales manager at Tsurumi Pump. “We recently installed an agitator with solids suspended in the pumped water at a construction site. A standard dewatering pump could become suffocated by sucking the solids to the small hole screen, preventing the liquid from being pumped.”
Boicken emphasises that not all agitators deliver the same results. They must be made of strong, durable materials as they consistently handle rough, abrasive particles. Tsurumi’s line of agitator pumps is manufactured with wear-resistant components such as high-chrome impellers and hard cast-iron volutes, which ensures higher durability and efficiency. To pump owners, this means minimum equipment downtime, longer lifecycles and lower total cost of ownership (TCO).
“Over the last 60 years, Tsurumi has built a reputation in North America and other parts of the world as a provider of high-quality pumps in applications that require robust equipment, especially in mining activities. And that’s mostly because of the materials they are made of,” Boicken says. “When customers install our agitator pumps, we often hear that our pumps are heavier and feel much sturdier than competitor brands that use aluminium. While this material is much lighter, the pumps don’t last as long.”
Tsurumi’s agitator pumps include three features that make them even more reliable: potted cable, oil lifter, and thermal protection.
The potted cable is an extra layer of cable protection. In case of accidental nicking of the exterior cable, moisture will not wick through the cable or reach the motor. As a result, contractors don’t need to rush to replace the cable. The additional cord protection prevents moisture infiltration and, ultimately, motor failure.
The pump’s oil lifter allows for a longer mechanical seal life. The shaft rotates, and the oil lifter spins and flings oil throughout the seal chamber. This provides lubrication and cooling of the seal faces down to a third of the normal oil level without additional power or external equipment.
Finally, the built-in thermal protection component prevents motor failure due to overloading and accidental run dry.
“These special features reaffirm that our pumps are extremely reliable, which can be the difference in finishing the job on time while minimising additional costs that could emerge from equipment failure,” Boicken concludes.
Tsurumi offers several agitator pump models to meet specific application demands. Considered one of the largest in the Agitator series, the GPNs feature side discharge up to eight inches and three-phase, four-pole motors of up to 50HP for lower impeller tip speed that prolongs their life. The GSDs, often found at construction sites and mines, are equally popular. With discharge sizes up to 10 inches, they provide high performance.
Finnish company Dynaset, a major manufacturer of hydraulic generators, power
washers, and compressors, is well-positioned for a big future. The family-owned and run firm’s wide product portfolio includes HPW dust-suppression solutions and HSP hydraulic submersible (dewatering) pumps for customers working in industries including quarrying.
During a May 2024 visit by Aggregates Business to Dynaset’s HQ just outside Tampere, the company was in the final stage of significantly expanding its on-site production capabilities. Jyri Hartikainen, Dynaset’s marketing manager, explains that the enhanced production site will make manufacturing more efficient while supporting the company’s growth strategy. Currently a €28.6 million annual turnover business, Hartikainen says Dynaset has 186 dealers globally selling its products to quarrying, mining, construction, demolition, recycling and other industry customers in over 80 countries.
rocks and other solid substances. This is done by a bevel-edged intake plate and a special fan blade that can even cut roots.
As well as being compact, versatile, easy to move, light in weight, high in efficiency, and very safe to use, Hartikainen says the “reliability” of the HSP range, and, indeed, all Dynaset’s other products, is the company’s key USP (unique selling proposition).
“What insulates us from market disruption is that we serve customers working in many different industries,” stresses Hartikainen. “Europe is our main market, and it's been quite good this year. The United States offers huge potential for us. We have hired two new salespeople to develop our market in the States.”
Dynaset has a four-strong line-up of powerful HSP hydraulic submersible pumps. Depending on the model, they produce 900 litres/minute up to 8,500 litres/minute of water flow. The HSP range’s compact size and durable design enable the submersible
Dynaset’s HRVB Hydraulic Recycling Vacuum Bucket was awarded a gold medal in the Earthworks, Demolition & Transport category at the prestigious Intermat Innovation Awards 2024. Company CEO Anni Karppinen and R&D director Pasi Yli-Kätkä proudly received the prize during a special awards night at the big Parisbased off-highway equipment and linked technology exhibition (24-27 April 2024). The HRVB Hydraulic Recycling Vacuum Bucket combines the movability of a traditional excavator bucket with a powerful vacuum cleaner and an air blower.
“It is a great achievement for a truly market-disruptive product and great to gain such international visibility for it,” says Hartikainen.
The Multiflo EC multi-float pontoon system (Multiflo EC) exhibited by Weir Minerals Europe at Hillhead 2024 near Buxton, England (25-27 June) is a versatile, galvanised steel frame designed for easy shipping while offering superior stability and carrying capacity.
The galvanised steel frame supports various Weir Minerals dewatering pump types, including vertical, submersible, and horizontal pumps. Multiflo EC safety features include a one-way gate, handrails, and a life buoy.
Simon Jones, Weir Minerals Europe’s pumps product manager, tells Aggregates Business that the system design also allows pumps to undergo normal servicing and maintenance without needing to be removed from the pontoon or taken shoreside. “We’ve got an Accumin greasing solution that automatically grease-purges the ends of the [pump] bearings and keeps dirt and water out, prolonging their life. This is an example of how we lower the total cost of ownership,” he emphasises.
The Multiflo EC comes in four-, six-, eight-, or 10-foam-filled UV-resistant polyethylene float versions, providing optimum buoyancy. They are rotomolded to ensure seamless construction with ribbed reinforcing for superior durability. The foam filling prevents instability and maintains buoyancy in the event of external damage.
The Multiflo EC is also designed to support optional extras such as lights and walkways upon request.
Atlantic Pumps, a UK-based pump solutions provider and manufacturer, has entered a strategic partnership with Kronoa Engineered Solutions, a renowned manufacturer based in Barcelona, Spain.
This collaboration aims to improve the quality of progressive cavity pumps and grinders available to various sectors, including quarries, biogas, water and recycling.
Through the Toro brand, Atlantic Pumps will now offer an extended range of progressive cavity pumps powered by Kronoa to meet its customers' diverse needs.
Atlantic Pumps’ international heritage and in-house team of experts will advise you on your business's pumping needs and requirements, providing timely, responsive solutions, strong customer service, operational efficiency, and valued engineering techniques.
With over 25 years of experience, Kronoa has developed a high-quality range of progressive cavity pumps for maintenancefree operation, solving the problems
encountered in various installations. Manufactured entirely in the European Union, Kronoa’s products are recognised for their exceptional mechanical robustness, high reliability and minimal maintenance costs. These progressive cavity pumps are designed to exceed industry standards and offer superior performance and durability, making them an ideal choice for demanding applications.
This strategic alliance leverages Atlantic Pumps' and Kronoa's strengths by combining Atlantic Pumps’ extensive market presence and expertise with Kronoa’s innovative engineering and manufacturing capabilities. Together, they are setting new standards in the pump industry and providing customers with advanced, reliable, cost-effective products that improve operational efficiency and sustainability. AB
Maturing technologies such as green hydrogen and waste heat recovery systems are helping to make asphalt-plant production even more sustainable. Liam McLoughlin reports.
Wirtgen-owned Benninghoven has launched what it says is the world’s first burner that can be operated only using 100% green hydrogen. The asphalt-mixing plant manufacturer says the first customer has now been able to produce several thousand tonnes of asphalt with virtually no emissions.
On the way towards making future road construction more sustainable, Benninghoven says the biggest lever here is asphalt production. Low-temperature asphalt, recycling rates of up to 100% reclaimed asphalt, and now hydrogen as the most environmentally friendly energy source are sustainable, future-proof, and cost-effective solutions that offer significant reductions in emissions.
A thermal process is required for the production of asphalt. In this process, industrial burners heat and dewater the starting material – aggregates and/or reclaimed asphalt – before it is mixed with bitumen. To make this process as efficient as possible, Benninghoven has developed a new generation of burners that includes the control and drying system alongside the burner itself. With this system, up to four separate burners can be operated at the same time. This flexible approach to usage increases the cost-effectiveness of the overall facility, as its owner can always use the best-available energy sources.
The hydrogen burner from Benninghoven is supplied with an intelligent control system that ensures the carefully coordinated hardware
and software solution can maximize process efficiency during asphalt production. This includes control of the feed systems, including the pressure-control section, drying section with burner, and burner control. Switching between fuels or combinations of multiple fuels is done on the fly, meaning that no shutdown or downtime is required and with only minimal temperature fluctuations in the process. Emissions – especially the nitrogen oxides (NOx) produced when using hydrogen as a fuel – are kept very low.
Alongside the climate-friendly, flexible use of a choice of fuels, the power draw has also been reduced by 20% while keeping the feedcapacity constant. Heat-transfer efficiency has been significantly improved by maximizing the use of the burner space, and providing a burner control and geometry that ensures optimum flame production for each fuel.
Another significant benefit for plant operators is the 5dB reduction in noise emissions.
Green hydrogen is currently the most sustainable fuel available: it produces no greenhouse gases and is suitable for the heating process thanks to its high-energy density. In many cases facility operators, wanting to start using hydrogen as a fuel, experience difficulties due to current limitations in infrastructure. When facing this challenge, they can count on support from asphalt-mixing plant specialist Benninghoven and its network.
The burner technologies from Benninghoven can be used to equip both new
facilities and existing asphalt-mixing plants, while Retrofit solutions can also be deployed in plants from other manufacturers. This gives every plant operator the chance to upgrade to the latest technologies at any time – an important aspect for ensuring economic, sustainable asphalt production and long-term plant operations.
UK-based Aggregate Industries says it is continuing to lead the way in sustainability by implementing waste heat recovery systems at three of its UK asphalt plants. The installation commences Aggregate Industries’ goal of ten implementations by the end of 2024, saving a total estimated 1,000 tonnes CO2 per year.
Based on a thorough feasibility study of the recovery technology, conducted by Aggregate Industries and working in collaboration with Invertech Solutions – a maintenance contractor specialising in energy efficiency – the construction and building giant says it is committed to realising the significant reduction in carbon emissions that can be achieved using these systems.
Currently implemented at the three active asphalt plants in Liverpool, Astley and Darwen, the process focuses on harnessing waste heat from the asphalt-manufacturing process to preheat air entering the dryer.
It involves: capturing waste heat; extracting thermal energy from the exhaust gases at the optimal locations; pre-heating process - using captured thermal energy to preheat clean incoming air; and supplying the dryer - directing the preheated air into the dryer to raise the thermal efficiency of the process.
Rory Fulwell, decarbonisation engineer at Aggregate Industries, comments: “By capturing and utilising otherwise wasted heat from the dryer exhaust, we can raise the thermal efficiency of the process and reduce fuel consumption and thus carbon emissions.”
Already, the active sites have demonstrated promising results, with a 12-15% improvement in fuel consumption when compared to the previous year, with improvements expected to stabilise between 6-10% over the course of the year.
Featuring an air-heat exchanger, the heatrecovery system has a semi-self-cleaning design to allow dust and debris to fall free of the exchanger, easy access for maintenance and cleaning, and minimal resistance to flow. Additionally, it includes an intake fan sized to match the blower fan on the burner, steel ducting and a heat-exchanger bypass valve.
Fulwell adds: “By recovering waste heat from the exhaust using a specially designed heat-exchanger system, we are enhancing the efficiency of the rotary dryer, which in most cases consumes up to 15 million kilowatthours annually. The new system aims to achieve a 10% reduction in fuel consumption, translating to significant carbon savings.”
Lintec & Linnhoff is continuing its global expansion with the sale of its first Lintec asphalt-mixing plant in Australia. The Lintec CDP5001M continuous asphalt-mixing plant
has already completed its first project and has moved on to its next task, fully utilising the benefits of the built-in chassis facilitating fast remobilisation.
Acquired by KEE Surfacing, the Lintec CDP5001M was immediately sent to support upgrade work at CBH Group’s Latham grainreceival site in Western Australia. Alongside pavement and earthworks construction, KEE Surfacing’s main task involved the conversion of a temporary gravel bulkhead into a permanent 52,400 tonne asphalt open bulkhead. Boosting storage by almost 10,000 tonnes, the Lintec CDP5001M has helped reduce the distance farmers need to travel to deliver their harvest.
After finishing the job for CBH Group, the mobile plant was then driven 80km northwest to supply hot-mix asphalt for similar work at the CBH Morawa grain-receival site. With two new open bulkheads, this increases total storage capacity by 78,350 tonnes.
“These are just the first of what we expect will be many successful regional projects across Western Australia for our Lintec CDP5001M, thanks to its compact design and easy mobilisation from one site to another,” says Anthony Serpo, production manager, KEE Surfacing.
Lintec & Linnhoff has also signed an exclusive distributor agreement for the Kingdom of Saudi Arabia with construction and industrial equipment dealer Middle East Development Co. (MEDCO) at Big 5 Construct Saudi 2024.
This announcement comes just a few weeks after Lintec & Linnhoff announced a distributor agreement with Tutt Bryant in Australia.
The MEDCO distributor agreement will cover the full range of Lintec & Linnhoff’s asphalt-mixing and concrete-batching plants, including but not limited to the Lintec CSD containerised asphalt-mixing plant and Lintec UCP Ultra concrete-batching plants.
MEDCO was founded in 1967 and is a 100% Saudi Arabian-owned business.
A significant part of Saudi Arabia’s infrastructure has been built with the quality brands that are represented by MEDCO, and many airports, highways, and buildings have benefitted from the premium and high-quality products supplied and supported by MEDCO.
Grupo Constructor Pirámide (GCP), a Mexican company with more than 50 years of experience in the construction sector, has acquired an Ammann ABP 280 Universal Asphalt-Mixing Plant. The plant is unique in Latin America because of its ability to process large quantities of reclaimed asphalt pavement (RAP) with the help of its RAH60 dryer. The objective was clear: to technologically transform the asphalt-mixing production process.
“We are convinced that we are taking the right path to modernise and transform the production of asphalt mix through innovation,” said Mario Serrano García, chairman of the board of directors of GCP. “We want the public and private sectors to promote and use sustainable asphalt mixes that are produced with new processes and technology that seek harmony with the environment and the urban surroundings.”
The shredder, an Ammann RSS 120-M, optimises the reuse of the material.
“It reduces waste and ensures the quality and characteristics of the material,” said Ricardo Galvis, regional manager at Ammann. “This is combined with the acquisition of a very modern and complete laboratory that is capable of carrying out all the necessary tests to guarantee the quality of their product.”
The UK-based Asphalt Industry Alliance (AIA) has appointed a new chair. David Giles, UK director at Continental Bitumen, part of the Colas group of companies, has taken over from Rick Green, who is retiring after seven years in the position and following a 40-year career.
The AIA is a partnership between the Mineral Products Association and Eurobitume and was established in 2000 to increase awareness of the asphalt industry and its activities, as well as the uses and benefits of asphalt. A key part of its activity is the Annual Local Authority Road Maintenance (ALARM) survey, which helps to raise awareness of local road maintenance and funding issues in England and Wales.
Giles has extensive experience in the bitumen sector, previously with Shell for over 36 years and as UK general manager of Eurobitume between 2018 and 2021, when he played an active role in the AIA. AB
Pilot Crushtec International (Pilot Crushtec) is introducing its new-generation TwisterTrac mobile vertical shaft impact (VSI) crusher powered by a Stage V diesel engine. The move to a motor that complies with EU Stage V regulations unlocks new export prospects in highly regulated markets such as Europe and North America.
Designed and manufactured in South Africa, the TwisterTrac VS350E VSI has gained popularity over the years in export destinations such as Australia and New Zealand. To provide context, Pilot Crushtec has sold more than 50 units since 2013, with almost 90% of these deployed into export markets.
To further grow its export sales, the company has become one of the first South African original equipment manufacturers to build a Stage V enginepowered machine. Previously driven by a Tier 3 Volvo TAD1651GE engine, the new TwisterTrac VS350E VSI now comes with a Stage V Volvo TAD1382GE motor, allowing Pilot Crushtec to offer the legendary tracked VSI in emissions-regulated markets, in particular Europe and North America, as mentioned above.
“The Stage V project has been in the pipeline for a while as part of our export focus. Our machine development strategy has always placed greater emphasis on
offering exportable products and this move allows us to unlock new markets and grow our export sales. We are excited by the prospects of growth in emission-controlled markets such as Europe and North America. In addition, this project speaks to customers in some of our traditional markets such as Australia, where there is a strong focus on adopting high emissions standards,” explains Sandro Scherf, CEO of Pilot Crushtec.
Jorge Abelho, Pilot Crushtec’s technical support director, says the company opted for the 13-litre TAD1382GE from Volvo
because it is a powerful, reliable and economical motor built on the dependable in-line six design. The engine incorporates a suite of advanced technologies that work together to reduce emissions and deliver significant improvements in power density, performance and operating efficiency.
Designed for easy, fast and economical installation, the engine’s high-tech injection and charging system with low internal losses contributes to excellent combustion and low fuel consumption.
“Volvo has been our preferred engine partner for a while, largely because of
the efficiency of their engine technology. In addition, we find them easy to deal with in terms of information sharing and guidance on the technology. To provide context, we had a technical representative from Volvo at our Jet Park workshop for a week-long factory testing before deploying the machine for field testing in a tough crushing application with great success,” says Abelho.
In addition to the transition to new engine technology, Pilot Crushtec took the opportunity to redesign some areas of the machine. For example, says Abelho, the machine now comes with an integrated cooling pack and the whole power pack base has become much smaller.
“We have also re-arranged some of the key components to make the cabling and piping shorter and simpler. For instance, we have moved the operator panel from the left-hand side to the right-hand side of the machine. This reduces the number of cables required on the machine by bringing panels closer together. We have also made the operator panel easier to use,” explains Abelho.
In addition, the size of the hydraulic tank has been reduced and the tank has been moved closer to the pumps. These refinements were informed by knowledge and feedback gained over the last ten years of operating the TwisterTrac VS350E in the field.
Scherf is confident that the latest developments will further entrench the TwisterTrac VS350E’s dominance in the global marketplace. Designed for tertiary and quaternary crushing applications, the TwisterTrac VS350E is renowned for its versatility, reliability and efficiency. A fully mobile track-mounted VSI crusher, the machine can be easily moved between or within a site. Its compact design and robust construction make it suitable for various applications, including road construction, quarrying, mining and recycling.
“One of the standout features which has made this machine popular is the unique
crushing concept. This uses rock-on-rock crushing principles, making it the perfect choice for producing cubical material for road and concrete aggregates. Another big advantage, which we believe will make it popular in new export markets, is that it is a diesel-electric machine, which results in
increased operational efficiency while at the same time reducing carbon emissions,” concludes Scherf. AB
A newly-launched electric trommel is suitable for diverse screening needs, while the versatility of a 37-tonne trommel is proving a major success in improving a company’s sustainable recycling operations. Liam McLoughlin reports.
Terex Recycling Systems has introduced the TTS-620SE Static Electric Trommel Screen which is designed to offer operators unparalleled versatility in applications, production rates and effortless serviceability. It is specifically designed for screening gravel, construction and demolition waste, compost/organics, biomass and soil.
The TTS-620SE Static Trommel features an electric head driven feed conveyor to prevent the slippage associated with a tail-drive configuration whilst under load. This ensures a consistent material feed onto the screening drum, enhancing screening efficiency and throughput. Terex says this enables heightened operational efficiency, improved screening quality, and reduced maintenance needs. The controlled material feed minimises wear and tear, extending equipment lifespan, while the user-friendly design adds operator convenience. With increased versatility and optimised performance, the TTS-620SE Electric Trommel is intended as a reliable solution for diverse screening needs. Supplied with a free-standing control panel, the intuitive user interface allows for easy set-up and running. Simple controls allow for quick adjustments to the feeder and drum speeds to tailor the trommel screen to suit your application.
Terex Recycling Systems comments: “Due to ever-changing market conditions and demands of the modern trommel the machine will be available as a standalone unit or it can be incorporated into an existing plant or part
of a new recycling plant. This will allow for easy customisation and adaptation to different applications and environments.”
UK-based waste-management business SED Services has invested in an EDGE TRM831 trommel. SED Services, founded in 2005 and located in the North West of England, has grown to become one of the leading companies in the waste-processing sector.
SED offers waste producers cost-effective and environmentally friendly recycling solutions for non-hazardous wastes and helping to reduce greenhouse gas emissions. Earlier this year it expanded its operations with the acquisition of a state-of-the-art 110-hectare composting site at Kirkby, bringing to four the number of sites it now operates in the Merseyside region, the others located in Wigan, Formby and Hightown, employing a total of 180 staff. The site will save some 280,000 tonnes of waste from entering landfill.
To meet demand SED Services invested in what is the largest trommel of its kind, a 37-tonne TRM831 from EDGE Innovate. It is fitted with a tri-axle bogie complete with fifth-wheel hook-up and air brakes. Transportation between sites is exceptionally easy with redeployment taking a matter of minutes thanks to hydraulic folding discharge conveyors and chassis jacklegs.
With extensive stockpiling capabilities thanks to its end-discharge conveyor design,
screening material at 400 metres per hour, the TRM831 design prevents product crosscontamination and reduces the double handling of material. This is complemented by a remoteoperated, 180° radial fines conveyor which has the capacity to stockpile up to 1030m³.
It has been a game-changing investment according to SED Services MD Stuart Baldwin, who says: “The 10 metre EDGE TRM831 does the work of two six-metre trommels. The screening drum is taller and has a bigger screening surface giving us the option to process more tonnage per hour. It is so much more cost-effective; rather than running two trommels, we are now running just the one.”
Its high production rate is maintained thanks to EDGE’s intelligent load-management system which prevents drum overload and ensures that the trommel screen is always operating at optimum performance with minimal supervision. Enhanced trommel screening results are achieved thanks to a variable drum screening angle. Baldwin says he also likes the fact it is mounted on wheels. “A static unit which is usually tailor-made for a customer would invariably be scrapped once it outgrows its use, so the fact this new trommel is on wheels gives us the option to move it from one site to another – and it always has a secondhand value, meaning you have something to trade in if you want to upgrade .”
Powered by a 188hp (140kw) Caterpillar C4.4 Tier 4 Final / STAGE V engine, resulting in extremely low engine and noise emissions, the EDGE TRM831 incorporates a host of other impressive design features such as an eco-power-saving functionality which reduces unnecessary running costs and a user-friendly HMI control panel for the easy adjustment of machine parameters. AB
OCTOBER
2-4: SIM 2024
Dijon, France
Organisers: Exposition SIM https://www.expositionsim.com/ en/index.htm
NOVEMBER
26-29: bauma China 2024
Shanghai, China
Organiser : Messe Munchen
Tel: +86 21 2020 5500 baumachina@mm-sh.com https://bauma-china.com/en/
DECEMBER
11-14 bauma CONEXPO INDIA 2024
New Delhi, India
Organisers: Messe München
Tel: +49 89 949-20255
Email: franziska.dorfmueller@messe-muenchen.de https://bauma.de/en/india/ 2025
JANUARY
21-23 World of Concrete 2025
Las Vegas, NV
Organisers: Informa
Tel: +1 212 951 3525
Email: registration@worldofconcrete.com https://www.worldofconcrete.com/
MARCH
12-13 SaMoTer Paving Show & Congress 2025
Verona, Italy
Organisers: Veronafiere
Tel: +39 045 8298 133
Email: exhibitors@samoter.com https://www.samoter.it/en/paving-show-andcongress-2025
25-27 World of Asphalt 2025
St. Louis, MO
Organisers: NAPA, AEM & NSSGA
Tel: +1 (864) 208 3372
Email: exhibitors@aem.org https://www.worldofasphalt.com/
25-27 Agg1 2025
St. Louis, MO
Organisers: NSSGA
Tel: +1 (800) 867 6060
Email: exhibitors@aem.org https://www.agg1.org/
APRIL
07-13 bauma 2025
Munich, Germany
Organisers: Messe München
Tel: +49 89 949 11348
Email: info@bauma.de https://bauma.de/en/trade-fair/
WARM-MIX ASPHALT WITH AMMANN FOAM TECHNOLOGY
HEATING PROCESS
• Highly efficient heat transfer
• No parasite air
• Optimised regulation burner / drum
BURNER
• Various fuels available
• Ideal combustion process
• Optimised energy consumption
USE OF RAP MATERIAL
• Full range of technical solutions
• Additions of RAP up to 100%
• Industry-leading partner in the use of RAP
BST – BLUE SMOKE TREATMENT
• Captures vapours during loading
• Filters trapped fumes
• Removes oil particles
EMISSIONS
• Lowest VOC (TA-Luft)
• Complete dust suppression
• Odour management solutions
• Noise reduction kits
AVOIDING HEAT LOSS
• High insulation up to 200 mm
• No thermal bridges
• Flaps to close the storage silos
• Reduction of wasted material
AS1 CONTROL SYSTEM
• Wide range of modules for software upgrading
• Expert use of inverter
• New professional and ergonomic user interface
• Energy management of photovoltaic systems
• Automatic burner control ADX