
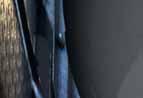
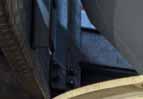
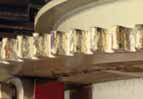

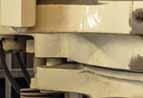
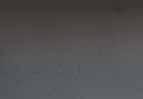
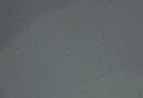
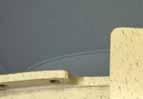
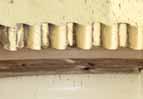
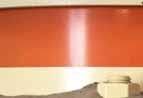
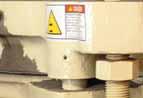
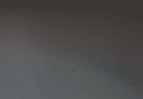
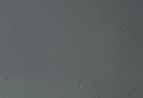
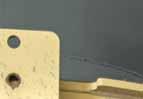
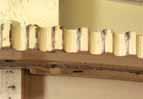
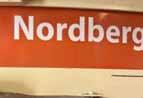
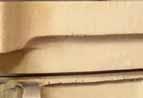

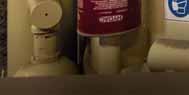
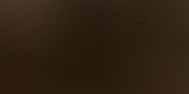
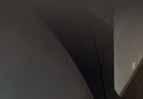
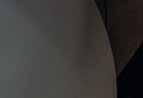

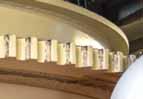
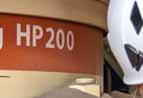
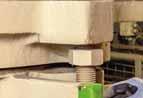



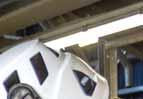
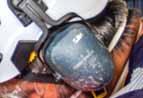
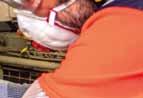

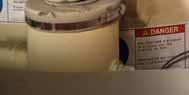
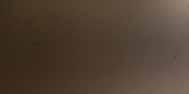
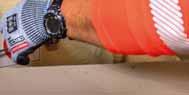

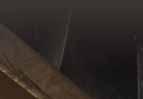
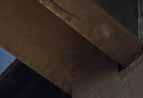
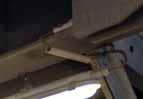
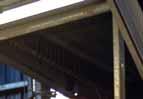
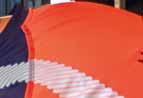
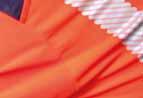
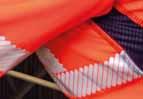
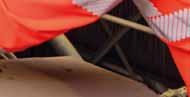


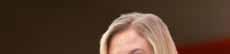
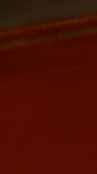


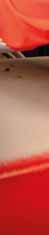
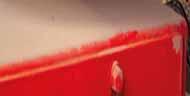


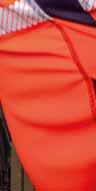
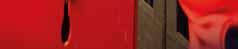

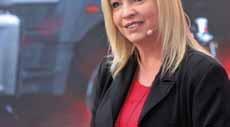
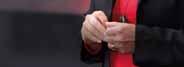

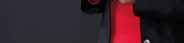
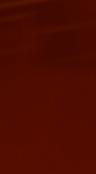




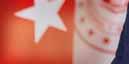
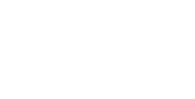




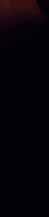
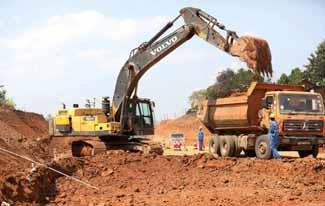
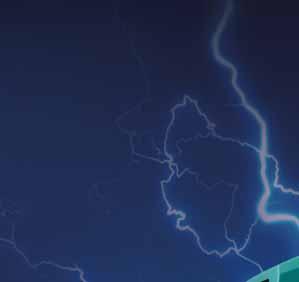
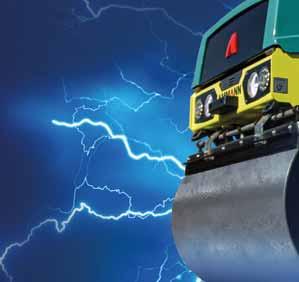
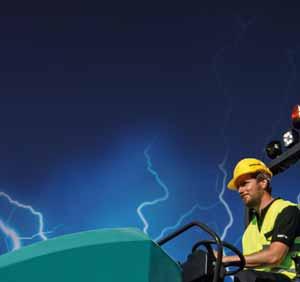

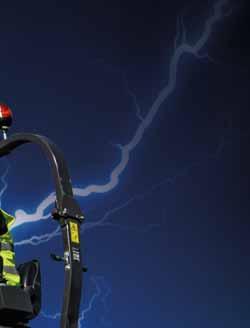
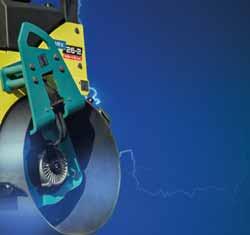
• Fully electric drive and vibration • 1 Shift = 1 charge • Zero-emission
• Ecodrop and Ammann Servicelink • Energy recuperation = extended operation
• Advanced battery pack with long life cycle, high capacity and optimal safety
• 100% Traction control for performance on difficult terrains
HEAD OFFICE
EDITOR: Guy Woodford
ASSISTANT EDITOR: Liam McLoughlin
CONTRIBUTING
EDITORS: Patrick Smith, Dan Gilkes
EQUIPMENT EDITOR: Mike Woof
DESIGNERS: Simon Ward, Andy Taylder
PRODUCTION MANAGER: Nick Bond
OFFICE MANAGER: Kelly Thompson
CIRCULATION & DATABASE MANAGER: Charmaine Douglas
INTERNET, IT & DATA SERVICES DIRECTOR: James Howard
WEB MANAGER: Sarah Biswell
SOCIAL MEDIA MANAGER: Tatyana Mechkarova
MANAGING DIRECTOR: Andrew Barriball
PUBLISHER: Geoff Hadwick
CHAIRMAN: Roger Adshead
ADDRESS
Route One Publishing Ltd, Second Floor, West Hill House, West Hill, Dartford, Kent, DA1 2EU, UK
TEL: +44 (0) 1322 612055
FAX: +44 (0) 1322 788063
EMAIL: [initialsurname]@ropl.com (psmith@ropl.com)
ADVERTISEMENT SALES
SALES DIRECTOR:
Philip Woodgate TEL: +44 (0) 1322 612067
EMAIL: pwoodgate@ropl.com
Dan Emmerson TEL: +44 (0) 1322 612068
EMAIL: demmerson@ropl.com
Graeme McQueen TEL: +44 (0) 1322 612069
EMAIL: gmcqueen@ropl.com
SUBSCRIPTION / READER ENQUIRY SERVICE
Aggregates Business is available on subscription at the rate of: £85 / US$145 / €111 per annum. Single copies £20 / US$35 / €26 Email subs@ropl.com for further details. Subscription records are maintained at Route One Publishing Ltd.
SUBSCRIPTION / READER ENQUIRIES TO:
Data, Route One Publishing Ltd, Waterbridge Court, 50 Spital Street, Dartford, Kent DA1 2DT, UK
TEL: +44 (0) 1322 612061 FAX: +44 (0) 1322 788063
EMAIL: data@ropl.com
No part of this publication may be reproduced in any form whatsoever without the express written permission of the publisher. Contributors are encouraged to express their personal and professional opinions in this publication, and accordingly views expressed herein are not necessarily the views of Route One Publishing Ltd. From time to time statements and claims are made by the manufacturers and their representatives in respect of their products and services. Whilst reasonable steps are taken to check their accuracy at the time of going to press, the publisher cannot be held liable for their validity and accuracy.
PUBLISHED BY © Route One Publishing Ltd 2023
AGGREGATES BUSINESS USPS: is published six times a year. Airfreight and mailing in the USA by agent named World Container Inc, 150-15, 183rd Street, Jamaica, NY 11413, USA.
PERIODICALS POSTAGE PAID AT BROOKLYN, NY 11256
US POSTMASTER: Send address changes to Aggregates Business, World Container Inc, 150-15, 183rd Street, Jamaica, NY 11413, USA. Air Business Ltd is acting as our mailing agent
PRINT: ISSN 2051-5766
ONLINE: ISSN 2057-3405
PRINTED BY: Warners (Midlands) PLC
ub-Saharan Africa is a key regional market for this magazine, so a new report from GlobalData, a major international business market intelligence firm, makes for concerning reading.
The Construction Market Size, Trends and Growth Forecasts by Key Regions and Countries, 2022-2026 report states that construction output in sub-Saharan Africa grew by an estimated 1.7% in 2022, compared to a growth of 3.2% registered in 2021. Although the industry is forecast by the same source to record growth of 3.2% in 2023, significant downside risks persist, most notably the region’s rising debt levels. Any negative impact on the sub-Saharan Africa construction sector would hit demand for aggregates and other building materials such as cement and concrete.
GlobalData’s new report also notes that the sub-Saharan Africa region’s postpandemic economic recovery has been halted since the second half of 2022, with the IMF’s (International Monetary Fund) October 2022 WEO (World Economic Outlook) forecasting GDP growth in the region to remain subdued at 3.7% in 2023 following a deceleration to 3.6% in 2022. Public debt has reached about 60% of GDP, with several countries in the region in debt distress condition or at high risk of debt distress.
Dhananjay Sharma, an analyst at GlobalData, comments: “With the gloomy economic backdrop and additional challenges specific to the construction industry, notably high construction material costs, the region’s industry will remain subdued in the short term. Both public and private sector projects will face hurdles, with the government’s revenue continuing to be directed at efforts to deal with immediate socioeconomic crises. Concurrently, high construction material prices will make projects unviable for the private sector.”
GlobalData highlights that Chinese funding has been a major source of growth for infrastructure projects in the region in the last two decades, helping Africa bridge its $100bn-a-
year infrastructure deficit. However, the post-pandemic Chinese economic slowdown, coupled with the substantial losses on the loans it granted to multiple countries, is resulting in a recalibration of Chinese focus on the Belt and Road Initiative (BRI) and a slowdown in Chinese investment in the region. Alongside this, a tightening monetary policy across developed countries is also affecting the region. At the same time, higher interest rates due to high inflation weigh on both business investments and household consumption.
Sharma concludes: “Over the longer term, growth is expected to pick up from 2024 onwards, with energy and utilities outperforming other sectors. In the short term, growth will be driven by increased activity in oil and gas projects due to continued higher prices, while longer-term investments will be driven by the shift towards green energy and the underlying potential of renewables in the region. Along with energy and utilities, investments in infrastructure and the institutional sector will be driven by the continued realisation of the inadequacies of the current transport and utility systems and education and healthcare facilities.”
This edition of ABI has a strong African theme with V.L. Srinivasan’s in-depth analysis of the Middle East-North Africa aggregates market. Shem Oirere writes about efforts to update East Africa’s stone-, sand- and gravelprocessing-linked explosives and blasting regulations to ensure quality and safety amid booming demand for building materials in the new infrastructure-hungry region. Finally, Munesu Shoko interviews Maretha Gerber, vice president of sales and marketing at Daimler Truck Southern Africa, who is encouraged by the strong demand for construction-type trucks in southern Africa over the past year.
Hopefully, Gerber’s buoyant analysis rather than GlobalData’s more cautious sub-Saharan Africa market commentary bears out in 2023 and beyond. GW
Electric-powered and technology-based loading for today and tomorrow
Productivity and efficiency gains from deploying premium articulated and rigid haulers
A keenly anticipated updated version of a smart technology-based top hammer drill
All the key events in the quarrying & aggregates world
Weighing technology companies are introducing innovative new solutions
08 INTERVIEW
Daimler Truck SA’s Maretha Gerber believes the South African construction industry is on an upward trajectory
12 MARKET REPORT
Construction activity in full swing in the MENA region
The first models of a new fully-electric range of Lokotrack crushers and screeners will go into production later this year at Metso Outotec’s renowned Tampere facility in Finland
Seeking a better-regulated East African construction sector
45 bC INDIA 2023
The 6th edition of bauma Conexpo India attracted 41,108 visitors from 83 countries
Volvo Construction Equipment (Volvo CE) has announced an investment into battery pack production at its excavator plant in Changwon, South Korea, again signalling its ambition to drive industry transformation with sustainable solutions.
With the SEK 80mn (around $7.8mn) investment from Volvo Group, a new production facility and equipment will be built at the Changwon plant in South Korea – which at around 1.1mn m2, is the largest excavator production site in Volvo CE, producing around 55% of its total excavator volumes.
The new facility at the Changwon plant will produce a wide range of common electric storage solutions (battery packs) for Volvo Group and become a core competence centre for electric excavators. This will enable Volvo Group to offer more sustainable solutions to its APAC markets in a more flexible, cost-effective and agile way and include supply chain, manufac-
CEMEX ACHIEVES RECORD SALES OF SUSTAINABLE VERTUA PRODUCTS IN UAE
CEMEX says it is the first company to introduce lower carbon cement & concrete in the United Arab Emirates.
The building materials giant adds that, in line with its climate action strategy, more than 50% of CEMEX UAE concrete mixes are sold as Vertua –Lower Carbon.
This concrete is used in some of the most prominent projects in the country, saving approximately 55 million KG of CO2 so far.
“In 2021, we launched Vertua concrete in UAE as a rollout of the global launch of innovative products that positively contributes to our Climate Action Strategy,” said Rafael Vilallona CEMEX UAE country director.
“Reaching more than 50% replacement of our concrete mixes to be Vertua speaks volumes of UAE awareness and alignment of our strategy with the country’s vision. We aim to reach full adoption of our sustainable products and continue to avail cement & concrete that build a sustainable tomorrow.”
turing and logistics.
Andy Knight, head of operations excavator and managing director of Volvo Group Korea, says: “As the largest plant in Volvo CE and the core site for excavator development and production, Changwon is at the forefront of our shift to a sustainable future.
“This investment is an important milestone in our electrification roadmap and supports our recent investments in production facilities for electric
excavators. Changwon is ideally located close to battery module supply partners and other key suppliers in South Korea to meet the needs of customers in the future. We are also home to a highly skilled and motivated workforce who are fully committed to meeting our future environmental targets.”
The new production facility will be built inside the current component workshop at Changwon – without disruption to the existing operation. Once
complete, the facility will be approximately 2,500m2, including assembly and logistics areas. The building work will begin in April 2023, with battery pack production expected to commence in June 2024.
Coming soon after an announcement to invest in the production of electric wheeled loaders at its plant in Arvika, Sweden, and electric haulers from the company’s production facility in Braås, Sweden, this is another sign that Volvo CE is committed to becoming completely fossil-free by 2040 – in line with the Paris Agreement and as laid out in its Science Based Target goals.
Volvo CE has already successfully introduced compact electric excavators to the global market with the ECR25 Electric, ECR18 Electric, EC18 Electric and the mid-size EC230 electric excavators. With its compact electric wheeled loaders, Volvo CE has one of the largest electric ranges on the market.
in a silo. With a mechanical strength of up to 60 megapascal at 28 days, its strong technical performance makes it suitable for all types of concrete applications in buildings and on roads. H-EVA is notably used by the Bouygues Construction group in the context of 0% clinker clay concrete projects.
Julien Blanchard and David Hoffmann, co-founders of Hoffmann Green Cement Technologies, commented: “Following the granting of a first patent for our H-P2A technology, we are delighted to announce the strengthening of our intellectual property in the Chinese market with the granting of a patent for our clay-based H-EVA cement. This confirms once again our technological lead and the relevance of our low-carbon solutions.”
Keestrack has appointed Song Yik Chong as its new area sales manager for Southeast Asia.
With over 29 years of experience within several multinational construction companies like Ammann, Caterpillar and Wirtgen, Song will bring ‘extra knowledge and professionalism’ to the Belgium-headquartered crushing and screening plant manufacturer’s regional market offer. His main focus will be business management, development,
and sales, including after-sales.
A Malaysian citizen with a permanent residence based in Singapore, Song is looking to establish an extensive dealer network to cover the complete product range of Keestrack in Southeast Asia.
Keestrack CEO Frederik Hoogendoorn says he is very excited Song is joining Keestrack. “Song brings a huge knowledge in road construction which benefits Keestrack to grow
The Indian construction industry is expected to receive a significant boost in 2023, supported by a sharp increase in capital expenditure as part of the financial year (FY) 2023/2024 (April 2023 to March 2024) budget, says GlobalData, a leading data and analytics company.
In its latest budget, Narendra Modi’s government increased its total expenditure by 7.5%, from an estimated expenditure of INR41.9 trillion ($522.2 billion) in FY2022/2023 to INR45 trillion ($561.6 billion) in FY2023/2024. The capital investment outlay for FY2023/2024 is equivalent to 3.3% of the country’s GDP and is nearly three times the outlay made in FY2019/2020.
Pooja Dayanand, an analyst at GlobalData, said: “The sharp increase in capital investment is in line with the government’s focus on boosting economic growth and increasing job creation through investment in infrastructure development. The increase in funding will also be necessary for assisting ministries in implementing projects that have been delayed by constraints such as rising interest rates and construction material prices, and labour shortages.”
The budget is based on seven key priorities, including
inclusive development, reaching the last mile, infrastructure and investment, and green growth.
As part of the latest budget, the government increased its allocation to the state-owned National Highways Authority of India (NHAI) by 14% to INR1.6 trillion ($20.2 billion). It had also announced a record-high capital outlay of INR2.4 trillion ($29.9 billion) for the Ministry of Railways.
Dayanand comments: “The NHAI had been facing constraints in reaching its construction targets and is likely to miss its target for the second time in a row – in FY2022/2023.
The increase in its budget allocation could help the NHAI in meeting its targets in the
upcoming financial year while completing its backlog targets. The significant capital expenditure allocations for highways and railways will also help in improving connectivity, easing traffic congestion, and reducing travel times.” The government also increased its allocation to the PM Awas Yojana (PMAY) by 66% to INR790 billion ($9.9 billion) in FY2023/2024.
Dayanand continues: “The increase in allocation for the PMAY will help in increasing the supply of affordable housing and addressing the issue of housing shortages. However, increasing inflation and rising interest rates are likely to affect housing demand in the short term.”
our markets in existing and new products.”
“I believe I can build on my network and relationships, my long work experience within the construction industry, and my drive to help Keestrack improve its position in the market”, says Song.
As well as Southeast Asia, Song will cover the Papua New Guinea, Taiwan, South Korea, Japan, Hong Kong, and Mongolia markets.
Off-road tyre manufacturer Magna Tyres Group is growing its global footprint with the acquisition of Tirepoint, one of the largest tyre dealers in South Africa. Founded in 2004 and operating in the Gauteng, KZN and Western Cape regions, Tirepoint has established itself as one of the largest tyre dealers and service providers in South Africa. Magna Tyres says that Tirepoint has an exceptionally strong foundation of tyre industryrelated experience and adheres to good business practices created to place the customer first. It adds that, as an independent, multibranded organisation with strong supplier relationships, Tirepoint is positioned to consistently provide exactly what clients need.
Michael de Ruijter, president & CEO of Magna Tyres Group, stated: “With their expertise and excellent longstanding reputation as well as their ability to satisfy customers with tailor-made solutions, Tirepoint is a valuable addition to our global network. It perfectly fits our joint belief of ‘Customer First’ mentality.”
Following years of a protracted downturn, the Southern African construction industry is seemingly bouncing back. If demand for construction-type vehicles is anything to go by, says Maretha Gerber, vice president of sales and marketing at Daimler Truck Southern Africa, the industry is on an upward trajectory. Munesu Shoko reports
The Southern African construction industry has been in dire straits for the past five years, if not longer. However, based on the growth in sales of construction vehicles, the market is seemingly bouncing back. This is the view of Gerber, who has seen an increased demand for constructiontype trucks in the past 12 months in South Africa, and the Southern African region at large.
Construction, says Gerber, has been part of Mercedes-Benz Trucks’ ‘DNA’ for many years, and remains a big focus for the brand. In fact, some 10 years ago, the construction industry constituted 50% of Mercedes-Benz Truck sales in Southern Africa. During those years, the company actually had a stronger focus on its construction range than on longhaul vehicles, with the previous Axor range enjoying a good run in the market.
“While the protracted slump in the construction environment hit us hard in the past few years, we have always believed that the market would rebound at some point,” says Gerber. “We are glad that construction is starting to show signs of recovery, with almost every original equipment manufacturer (OEM) struggling to meet demand.”
Despite a long market slowdown, Daimler Truck Southern Africa has, in recent years, boosted its offering with a range of models and solutions that speak directly to the needs of construction and quarrying customers, further reiterating its commitment to the sector.
The arrival of the Arocs in early 2019 marked a new era in the company’s construction portfolio. Unfortunately, the range arrived at the height of the construction downturn and therefore struggled to gain the traction that the company had envisaged. However, sales of Arocs trucks have been growing by more than 30% year on year, over the past three years.
The complementary FUSO range, which was brought in to meet the growing demand for value offerings in the construction and quarrying space, is also enjoying good sales growth. In the past six months, says Gerber, demand for the 6m³ concrete mixers, in particular, has increased. However, supply chain issues and bodybuilder backlogs remain a challenge for every OEM.
“It is encouraging to see our customers starting to enquire more about the Arocs and the FUSO FJ ranges. The challenge, however, is that when construction and quarrying customers want their trucks, they want them ‘now’, irrespective of the supply chain disruptions. On the one hand, we are trying to manage customer expectations, and on the other, to be proactive. For example, some of the dealers, in collaboration with bodybuilders, are proactively buying their construction trucks and bodying them up, so that when a customer walks in and wants a truck now, they have a standard offering available immediately,” explains Gerber.
One of the new trends in the construction/
Construction
quarrying market, says Gerber, is that end users are now looking beyond the truck –they are looking for efficiency, productivity, bodybuilder friendliness and value for money. When it is procurement time, she adds, they look for products that tick all the boxes for all involved parties in the decision-making process, all the way from the CEO to the operational manager.
The Mercedes-Benz Arocs range for construction is optimised for reliability, robustness and bodybuilder friendliness. The company initially launched two construction models in 2019 – the Arocs 3336K/36 Tipper Chassis and the Arocs 3236B/51 8x4 Mixer Chassis. These were later augmented by a further three models: an 8x4 tipper (the Arocs 4152K/51) and two all-wheel drive off-road vehicles (the Arocs 1836AE/45 and the Arocs 3352AE/48).
Drive programmes are available which have been specifically developed for the vehicles’ varied ranges of applications. For construction vehicles, the “Off-Road Drive” programme is standard. Off-road drive mode offers Standard, Economy, Off-road and Manual driving set-ups. It is optimised for the special requirements of constructionsite traffic and supports economic driving styles just as much as improved handling when pulling away or manoeuvring on building sites or when driving slowly along challenging terrain in quarries.
On gravel roads or off-road, the above-mentioned drive modes offer ideal performance in terms of dynamism when pulling away under high loads, gearshift points and shift dynamics.
The Arocs 3236B/51, an 8x4 concrete mixer with 35-tonne gross vehicle weight (GVW), features a weight-optimised hypoid rear axle, light-weight aluminium fuel tank, disc brakes and aluminium rims to reduce kerb weight and increase payload. This enables the 8x4 mixer chassis to supply 8m³ of ready-mixed concrete on every trip.
The Arocs 3336K/36 is a versatile tipper chassis with a short rear overhang featuring robust planetary axles, a double disc clutch, robust drum brakes, optimised for off-road use and a 16-speed Powershift 3 automated transmission with the “Off-Road Drive” programme as standard.
The application-specific mounting elements provide for a bodybuilder-friendly and fast-mounting process. All mixer chassis are standard with the mixer mounting brackets, and all tipper chassis come standard with the tipper mounting brackets, together with the modular bolted frame and the 50mm chassis hole pattern. With the new-generation Parameterisable Special Module (PSM), the turnaround time at a bodybuilder is significantly reduced.
The Arocs benefit from a number of innovations such as electronic parking
brake, multifunctional steering wheel and keyless start, amongst others. The electronic parking brake activates automatically when switching off the engine, but can also be switched on and off manually, using the lever in the cockpit. The integrated HOLD function activates when the vehicle is at a standstill simply by pressing the brake pedal more firmly, for example, at a red traffic light or on an uphill gradient.
While the Arocs is a top-of-the-range offering for the high-end construction market, the FUSO plays in the value end of the market, speaking directly to the emerging contractor market and small-scale quarries.
In response to the growing demand for 6m³ truck mixers, Daimler Truck Southern Africa introduced the FUSO FJ26-280C HYP
in April 2021. This model is specifically fitted with hypoid rear axles (single reduction axles), contributing extensively to low fuel consumption and reducing the tare weight of the vehicle. This is to ensure that the vehicle can accommodate a 6m³ concrete mixer and still comply with the permissible axle loads.
Traditionally, says Gerber, most construction and quarry truck owners have never taken a total cost of ownership (TCO) approach to their truck purchases. While many still largely consider the capital cost of the product, Gerber says several industry players are starting to develop a much better understanding of TCO, showing interest in not only purchase costs but also in the costs related to keeping the equipment running.
There are several pillars to TCO. For Gerber, it’s all about the reliability and efficiency of the truck, as well as the aftersales care that comes with it. Daimler Trucks Southern Africa makes sure that when a customer walks in, they walk out with a solution that meets their needs, not just a truck. For example, the company offers a service contract as a maintenance option. Together with its dealers, the OEM makes sure that the truck is kept in good condition throughout its lifespan. Customers also have access to the OEM’s in-house finance solution, among other offerings such as driver training.
“For us, it boils down to value for money, efficiency and productivity. It’s also about building a modular solution that meets the customer’s needs. Some customers, for example, might not want a service contract, but finance would be important to them. One doesn’t necessarily have to take the full basket of solutions to put together a TCO solution. We can come up with a solution that speaks directly to the customer and their contracts,” she says.
Looking ahead, Gerber says moving towards cleaner fuels is imperative for the construction/quarrying industry and the automotive industry at large. Going the Euro 5 or Euro 6 route exposes the industry to a wide product range and an array of other operational benefits, such as better fuel efficiency and reduced environmental impact.
“If customers are willing to move to Euro 5 and Euro 6, we are able to bring in a broader product offering because these have become a priority for many of our source plants across the world. I believe that the next four years are going to be interesting for the Southern African market. Neither we nor our customers are waiting for legislation. The industry needs to evolve, and fast,” concludes Gerber. AB
“I believe that the next four years are going to be interesting for the Southern African market. Neither we nor our customers are waiting for legislation. The industry needs to evolve, and fast”
Maretha Gerber, vice president: Sales and Marketing at Daimler Truck Southern Africa
The Middle East and North Africa (MENA) construction sector is on the upswing largely due to the revenue surpluses generated by high prices of fossil fuels derived from the region's oil-producing countries. VL Srinivasan reports
Some suffer, and some gain from rising fossil fuel prices, with the MENA region, firmly residing in the latter camp. Additional funds generated by oil producers across the region due to the sustained fossil fuel price hike are largely being spent on various forms of construction, which, in turn, have pushed up demand for aggregates, such as gravel, concrete, sand, and crushed stones. The GCC (Gulf Cooperation Council) countries have taken the lead in the past year, announcing building projects worth billions of dollars.
MENA’s construction sector growth, particularly in the oil/refinery, petrochemical/industrial, and commercial construction, is fuelled by US$90 to $125 per barrel of crude oil. As of 8 March 2023, the price of Brent crude oil stood at $80 but is expected to rise in the coming months.
More importantly, the huge spending by various governments in the region in executing various infrastructure projects is expected to create thousands of direct and indirect jobs leading to more economic activity throughout the region.
50% or 52% by 2030.”
Even in Egypt, which is recovering from the post-COVID-19 effect, the award of construction projects is set to grow by 18% to $23.5 billion in 2023 from $19.9 billion in 2022. While the building sector walked away with a lion’s share of USD9.7 billion in 2022, it was followed by the industrial USD5 billion and infrastructure USD$2.7 billion sectors, respectively.
Coming to the GCC, two major events – the 2022 FIFA World Cup in Qatar and Expo 2020 in Dubai (the event was deferred by one year due to the COVID19 pandemic) – gave a fillip to the construction activity in the region.
Encouraged by the success of World Expo 2020 in the UAE, Saudi Arabia wants to hold the World Expo in 2030 as the Kingdom has already initiated infrastructure projects worth more than $750bn, including NEOM city, which alone is estimated to cost around $500bn.
For instance, Morocco has approved 26 investment projects under a total budget of $2.8 billion, and these projects will create over 3,735 direct jobs and 23,182 indirect jobs, the country’s investment commission, chaired by Morocco’s Prime Minister Aziz Akhannouch, said on 23 January 2023.
A few days later, Akhannouch told delegates at the annual Davos summit in Switzerland that his country has become a leader in sustainable development and is targeting 50% reliance on renewable energy by 2030, saying: “Renewable energies now account for 38% of our energy mix, and our ambition is to reach
Fitch Solutions, which offers credit risk and strategy decisions with reliable data, has forecast the region's construction industry to exhibit overall real growth of 5.0% y-o-y in 2023, ahead of the global industry's 2.3% y-o-y expansion, as activity in the region continues to benefit from elevated energy prices, impending disinflation in the price of materials and burgeoning project pipelines.
“Countries such as Libya, Egypt, and Iran will see the fastest individual real growth rates among markets in the region in 2023, while Qatar will feature one of the region's slowest growth rates as FIFA World Cup-related construction activity dissipates,” it said.
Fitch Solutions said it would remain bullish on the growth prospects for the MENA as a whole and the GCC countries, as these countries are generally characterised by young populations and robust economic diversification initiatives and will be able to allocate more resources into their respective infrastructure sectors as oil prices rise.
According to the UAE-based BNC Construction Intelligence, there are 24,664 active urban construction projects in the GCC, estimated at USD513.9 billion. The GCC's urban construction sector constitutes 81% of the number of all active projects in the region.
“In dollar terms, urban construction projects account for 32% of the total estimated value of all sectors in the region,” BNC said (see info graph). Active projects include concept, design, tender, under construction and on-hold projects.
Grant Earnshaw, manager for Holcim, MENA Region, said that the region has seen a reasonable recovery in the postCOVID-19 era with governments returning to spending in construction. Infrastructure development remains an area with significant growth potential across the region, given its key role in improving the efficiency of trade flows, living standards and job creation, he said.
“Many economies in the region are hydrocarbon-based, so governments are seeing rising revenues that allow for increased spending through state budgets.
“Renewable energies now account for 38% of our energy mix, and our ambition is to reach 50% or 52% by 2030”
Aziz Akhanouch, Prime Minister, Morocco
We currently see a softening of volumes in the private residential sector, which is largely impacted by inflation,” Earnshaw said.
In its latest report on the MENA construction equipment (CE) marketGrowth, Trends, Covid-19 Impact and Forecasts between 2023-2028, Mordor Intelligence, a global market intelligence and advisory firm, said that various ongoing and future projects, which the local governments have initiated in the region to improve the infrastructure, were creating a demand for construction equipment.
The report said that the CE market in these countries is valued at $4.26 billion and is expected to reach $6.4 billion by 2028, registering a CAGR of 4% over the next five years.
Saudi Arabia represents the secondlargest market for the construction sector in the GCC region after the UAE, which occupies more than 34% of the revenue generated. Saudi Arabia holds a revenue share of 29%, followed by Qatar and Oman with 12% and 10%, respectively. The construction of highrise buildings like the Jeddah Tower in Saudi Arabia is anticipated to increase the demand for construction equipment in Saudi Arabia, the report said.
The COVID-19 pandemic severely affected the construction industry and associated equipment demand due to disruptions in the supply chain, reduced investment in new equipment procurement, the halting and postponement of construction projects, and unstable economic growth in many countries.
“However, since last year, the construction industry across the region has been experiencing significant growth in investment and economic development, witnessing major orders for CE from GCC countries in the region which is likely to drive the market in focus during the forecast period,” the report noted.
In August last year, Doosan Infracore Co., a subsidiary of Hyundai Construction Equipment, won an order to supply 62 units of construction equipment to major
customers in Saudi Arabia and Bahrain, the report said.
One of the major factors driving the growth of the CE market is the growing construction industry, especially in developing countries, owing to numerous growth opportunities in infrastructure, residential, and non-residential sectors.
The rise in the construction of multi-family houses (with the growing trend for nuclear families), and increasing investments in the construction of roads, highways, smart cities, metros, bridges, and expressways are due to the growing population and urbanization.
The growing trend toward automation is expected to drive the growth of the market, the report said.
Each country in the Middle East region has grown in the construction sector in its unique way over the years, adhering to its own pace, norms, and ambitions.
The UAE is responsible for significant projects, owing to the fact that Dubai has more robust development and investment than the rest of the Middle East. High economic growth, a growing elite population, increased foreign investment, and other factors have contributed to this.
In fact, Saudi Arabia, the UAE, Oman, and Egypt are launching several infrastructure projects, including new megacities, railway projects, harbours, airports, housing projects, and so on, all of which are expected to boost construction demand.
“The city's infrastructure development also contributes to the need for construction equipment. The building of major rail networks like Etihad Rail in the UAE is also projected to propel the market for construction equipment in the Emirates,” the Mordor Intelligence report added.
According to Earnshaw, sustainability and efficiency are the two trends marking the construction equipment market in the region. Customers are looking for improved sustainability performance as well as energy efficiency, which can help to lower operations costs, he said.
“Thanks to ECOPlanet, the construction of the Alamein Downtown Towers has saved 2,900 tons of CO2 (compared to reference OPC) for an emissions reduction of 45%, demonstrating that green construction at scale is possible,” Earnshaw said.
With construction activity gaining momentum, the demand for construction equipment has gone up in the last few months. Holcim is involved in major projects across all countries in the region - from the
new Central Bank of Iraq to the Alamein Downtown Towers project in Egypt, he added.
The region’s aggregates market is facing some challenges, such as the scarcity of skilled manpower and the high cost of construction materials. These factors are likely to restrain market growth in certain countries.
There is significant opportunity within the sector. Egypt hopes for more favourable macroeconomic factors in 2023 as material prices are increasing, and imports are becoming more expensive amid currency devaluation, inflation, and supply chain shocks emanating from the Russia-Ukraine war.
Even Kuwait is not immune as its construction sector has been grappling with contractual disagreements, increasing the possibility of a wave of contract terminations, a report by Arabic daily AlRai said.
The report went on to say that some contractors refused to implement contracts that they had signed at the start of 2022 and did not commence the projects due to reasons such as the issuance of licences or considerations related to either party.
“The contractors justified this with compelling reasons related to an unprecedented increase in the prices of construction goods. This led to high inflation rates that have strained the contractors’ ability to continue with the implementation,” AlRai added.
Another major factor that is expected to push up the demand for construction aggregates is the tragedy that struck two Middle East countries - Turkiye and Syria - in the form of a massive earthquake on 6 February 2023.
A fortnight after the disaster, Murat Kurum, Turkey’s Minister for the Environment and Urbanisation, said: “At least 164,000 buildings containing 520,000 apartments have either collapsed or are so damaged that they need to be demolished. Most of the destroyed buildings were built before 1999, and no inspection was carried out in these buildings during the construction stage.”
“Many economies in the region are hydrocarbonbased, so governments are seeing rising revenues that allow for increased spending through state budgets. We currently see a softening of volumes in the private residential sector, which is largely impacted by inflation”
Grant Earnshaw, manager for Holcim, MENA Region
The Turkish government’s initial plan is to build 200,000 apartments and 70,000 village houses at a cost of at least $15bn. The reconstruction of infrastructure projects like buildings and roads and some airports is likely to take at least three to five years.
While Turkey is expected to recover fast from the ill effects of the disaster as it has abundant mines and natural reserves, it will take some time for war-torn Syria as some of the affected areas are still held by antigovernment rebels.
Even 6Wresearch, a global market research and consulting firm, said the Middle East construction aggregates market is projected to grow from 2022 to 2028, mainly due to the increasing demand for infrastructure projects in the region, particularly in Saudi Arabia and the UAE.
The main drivers for the growth of the market are increasing infrastructure development and construction activities in the region, as well as rising demand for construction aggregates from the residential, commercial, and industrial segments.
Additionally, the major regions that are expected to account for most of the market are Saudi Arabia, the UAE, Egypt, and Iran, 6Wresearch said.
These countries are witnessing high growth rates owing to their large population bases and growing economies. Additionally, these countries have embarked on several industrialization projects over the past few years, which have led to an increase in demand for construction aggregates, the report added.
Laura Morgan, Market Intelligence Lead
“At least 164,000 buildings containing 520,000 apartments have either collapsed or are so damaged that they need to be demolished. Most of the destroyed buildings were built before 1999, and no inspection was carried out in these buildings during the construction stage”
MEA, Project & Development Services, at Jones Lang LaSalle (JLL), said that the GCC and wider MENA region have performed well considering periods of economic volatility, based on the Vision Programmes throughout the region with committed efforts to economic diversification. The value of the projects pipeline, correlated with elevated oil prices, all point to a strong construction sector in 2023.
She said that the region, like the rest of the world, has witnessed elevated construction prices attributed to global economic and geopolitical events. Issues relating to the availability of materials or disruptions to the supply chain can impact prices, as seen over the last two years, she explained.
On the possibility of a spurt in demand for
construction aggregates, she said the region always relied on imports from both within the region and outside, and the Arab world is advantageously placed to access construction materials from varying locations but is not immune to rising prices, like the rest of the world.
Generally, MENA is performing well in comparison with other regions, both at a macroeconomic level and a strong construction sector. Including an ambitious pipeline of unawarded contracts, she said.
“This is a force for new construction trends such as modern methods of construction, along with construction technologies and a greater sustainability influence. We are seeing an increasing interest to source materials locally, which in the long run supports a growing manufacturing sector to meet such trends,” Morgan added. AB
“The region always relied on imports from both within the region and outside, and the Arab world is advantageously placed to access construction materials from varying locations but are not immune to rising prices, like the rest of the world”
(Sociéte de Concassage et de Préfabrication de la Réunion) aims to treble its production of alluvial gravel and sand products thanks to its major investment in a new and bespoke Metso Outotec crushing and screening plant for its 2020-established Pierrefonds site in La Réunion, an island and overseas department and region of France in the Indian Ocean. Guy Woodford reports
The tailor-made Metso Outotec plant for SCPR’s Pierrefonds site is comprehensive, along with being highly productive and efficient. It consists of a Nordberg C130 jaw crusher, a PF561 pan feeder, Nordberg GP100S and HP200 cone crushers, a Barmac B7150SE impact crusher, an MB352 Rockbreaker, a CVB 103P inclined screen, ES203 and ES403 horizontal screens, conveyors and auxiliary equipment. The plant configuration can produce up to 376 tonnes of product per hour.
SCPR, a Colas Group company, signed the installation contract with Metso Outotec in December 2019, with engineering beginning in January 2020. Primary foundations were set in April 2020, with secondary and tertiary foundations completed the following month. Mechanical erection began in July 2020, completing in February 2021. Plant commissioning and start-up began in January 2021, with the set-up fully operational since May 2022.
“The site is a completely new one. Before, there were only mango trees on it,” explains Thierry Le Cloître, SCPR’s head of materials services. “Our previous site was around five to six kilometres away. It included a Metso crusher and some Metso screens, but the crusher was over 30 years old. We were keen to invest in a new site. We are extracting the alluvial material for the new site from the same place near a river where we sourced the material for the old site.”
Le Cloître says SCPR’s old materialsprocessing site processed just over 300,000 tonnes of material per year, with the objective for the new state-of-the-art Metso Outotec plant-equipped Pierrefonds site three times that level.
“We don’t have any more capacity at our other processing site in the west of the island, so we are crushing all the additional material for customers in the south [Pierrefonds]. We have a large customer base in La Réunion, including those working in road construction and concrete production and companies and individuals involved in smaller building
projects.
“Our new Metso Outotec plant has two production chains: one for sand and gravel crushing, screening and washing for concrete customers; the other for big rocks over 80mm which are crushed and screened for asphalt plant and other customers.”
With a population of just over 873,000 and covering an area of 2,511km², La Réunion is located around 950km east of the island of Madagascar and 175km southwest of the island of Mauritius. Le Cloître says this makes exporting SCPR’s products too expensive.
Commenting on SCPR’s working relationship with Metso Outotec before closing the deal on the new plant installation, Le Cloître says: “We knew what type of installation we wanted. We have four crushing plants across the island and know exactly what material we have to crush and how to crush it. What we needed to work with Metso Outotec closely on was the exact detail of each production chain that enabled us to match our [treble] production objective and be able to measure exactly what we
produce. We also wanted to be very selective about what we produce, so we produce only what we needed, with no waste.”
Le Cloître says SCPR put the new Metso Outotec site set-up through a rigorous two-week testing period before it went fully operational to check whether the new installation was likely to meet SCPR’s ambitious long-term production target of 900,000 tonnes of material processed a year. “It met our production targets for those two weeks, but it was a very challenging time, as it was during the COVID-19 pandemic.
“We started operating the plant fully last year over one shift of seven hours per day, five days per week. In September 2022, we pushed that up to ten hours per day. In December, we went up again to 14 hours of operation across two seven-hour shifts. We aim to run the plant 21 hours a day over three seven-hour shifts by the end of March or early April 2023. That five-day running
“Automation is the key to managing this plant, to enable the customer to be selective in the product they are producing”
time will take us to 900,000 tonnes a year.
“You expect to need to adjust things when you open a new site and run a new crushing plant of this size, but in less than a month, we had the final product quality we wanted.”
Touching on the servicing and maintenance needs of SCPR’s new Metso Outotec plant, Le Cloître says the skill and experience of the company’s engineering team and its familiarity with Metso Outotec plants and replacement parts mean that production issues that arise can generally be resolved in-house. “Metso Outotec engineers make visits to the island twice a year to see us and other customers to check crushers and other installed plants. They also came in December last year, just two days after we highlighted a particular issue [with the new set-up].”
“We had a lot of discussion with the customer before we settled on the final plant solution,” explains Marc Fourneret, senior project manager for Metso Outotec’s aggregates business area. “The biggest challenge was supplying the right solution that fitted the budget of the customer.”
“Automation is the key to managing this plant, to enable the customer to be selective in the product they are producing,” says Françis Lacôte, process and application expert at Metso Outotec. “If you want to produce more or less of a certain product, you can do that with automation, with all the [Colas] software-generated information coming to a single [customer] point. There is more variation in the material content fed into this plant than was planned.
“The plant we supplied can react quickly to any changes in the feed material,” continues Lacôte. “You get a full overview of the plant, and if you are a specialist, it is really easy to investigate and find any trouble spots.”
Speaking about challenges that arose during the plant installation for SCPR, Fourneret says: “The first challenge was
COVID-19. Just two months after we started the engineering process, we were in the pandemic. After that, there was the challenge of transporting all the required equipment to the island. That took time. Now the plant is running, I think it’s performing even better than what was specified in our contract with the customer.
“We have a very good relationship with SCPR and Colas and have just signed a contract with Colas for another big plant in French Guiana [an overseas department of France on the northeast coast of South America].”
Fourneret and Lacôte were speaking to Aggregates Business in January 2023, with Lacôte highlighting that Metso Outotec engineers were due to visit SCPR’s Pierrefonds site in mid-February. “The company’s production is changing to reflect the changing market. So, we need to adapt [the plant] and ensure even greater flexibility.” AB
Volvo Construction Equipment (Volvo CE) has launched a solution to convert its L120 mid-sized wheeled loaders to electric.
The solution has been developed in conjunction with partner Parker Hannifin and converted by Volvo Group’s own CE Engineering Solutions. The 20-tonne L120H Electric Conversion will be commercially available for selected customers in Europe during 2023.
Volvo CE states: "Using the market -recognised conventional machine as the base, which will still be offered to customers, the electric conversion model will deliver the same performance with the upside of doing so emissionfree."
Major loader manufacturers are launching new electric models and technologies that they say are extending versatility and transforming the industry towards a carbon-free future. Liam McLoughlin reports
of commercialised electric solutions across all segments and applications. This latest collaboration to expand its line of electric wheeled loaders follows Volvo CE’s investment in Dutch manufacturer Limach, announced in June 2023, to broaden the company’s electric excavator portfolio.
The manufacturer says this partnership approach, which allows for speedier implementation to the market, happens in parallel with the company’s continued development of more electric solutions –like the EC230 Electric, a 23-tonne battery -electric excavator, built on Volvo CE’s own technology. It adds both approaches are
needed if the industry as a whole is expected to reach carbon-reduction targets, like Volvo CE has set out in its commitment to achieve net-zero greenhouse gas emissions by 2040 –with significant emission reductions as early as 2030 – as part of the Science Based Targets initiative.
Volvo CE adds that it is working with CE Engineering Solutions and selected electromobility partners to accelerate the availability
Carl Slotte, head of sales region Europe at Volvo CE, comments: “There is no time to wait – we need to deliver solutions that allow our customers to achieve their decarbonisation goals. Change starts here. Our commitment to partnership allows us to take a leading position in transforming our industry, with electric solutions that are built to fulfil market demand and tailored to suit the changing needs of our customers.”
The L120H Electric Conversion will be available this year for selected customers in Europe. Volvo CE says it delivers the same powerful performance as its diesel counterpart, but with zero exhaust emissions
Volvo CE says its new conversion solution for its L120 mid-sized wheeled loaders makes it easy for customers to go electric
and near-silent operation. These benefi combine to offer enhanced comfort for both the operator and those working near the machine.
Powered by 240 kWh batteries, it provides a runtime of approximately five hours in most medium-duty applications. Consistent with Volvo’s existing charging solutions, it is estimated to charge from 0-100% in just 1.5-2 hours.
The L120H Electric Conversion offers the following features as standard: Comfort Drive Control, Load Assist with On-Board Weighing plus radar detection with the new Collision Mitigation System. In addition, the L120H Electric Conversion will be supported by dedicated electromobility applications which allow the operator to check battery and charging status and to preheat the cab.
Volvo CE says that, depending on market demand, it brings the possibility to convert existing customers’ L120H wheeled loaders to electric in the future.
Volvo CE has also announced an investment into battery-pack production at its excavator plant in Changwon, South Korea, again signalling its ambition to drive industry transformation with sustainable solutions.
With the SEK80m (around US$7.8m) investment from Volvo Group, a new production facility and equipment will be built at the Changwon plant in South Korea –which at around 1.1m2 , is the largest excavator production site in V producing around 55% of its total excavator volumes.
The new facility at the Changwon plant will produce a wide range of common electric storage solutions (battery packs) for Volvo Group and become a core competence centre for electric excavators. This will enable Volvo Group to offer more sustainable solutions to its APAC markets in a more flexible, costeffective and agile way and include supply chain, manufacturing and logistics.
Andy Knight, head of operations excavator and managing director of Volvo Group Korea, says: “As the largest plant in Volvo CE and the core site for excavator development and production, Changwon is at the forefront of our shift to a sustainable future.
“This investment is an important milestone in our electrification roadmap and supports our recent investments in production facilities for electric excavators. Changwon is ideally located close to battery module supply partners and other key suppliers in South Korea to meet the needs of customers in the future. We are also home to a highly skilled and motivated workforce who are fully committed to meeting our future environmental targets.”
The new production facility will be built inside the current component workshop at Changwon – without disruption to the existing operation. Once complete, the facility will be approximately 2,500m2 , including assembly and logistics areas. The building work will begin in April 2023, with batterypack production expected to commence in June 2024.
ABOVE: LiuGong's 856H-E MAX wheeled loader on show at CONEXPO/CON-AGG 2023
Coming soon after an announcement to invest in the production of electric wheeled loaders at its plant in Arvika, Sweden, and electric haulers from the company’s production facility in Braås, Sweden, Volvo CE says this is another sign of its commitment to becoming completely fossil-free by 2040 –in line with the Paris Agreement and as laid out in its Science Based Target goals.
Volvo CE has already successfully introduced compact electric excavators to the
global market with the ECR25 Electric, ECR18 Electric, EC18 Electric and the mid-size EC230 electric excavators.
LiuGong North America has sold it first battery-electric vehicle in the United States.
The Chinese manufacturer says the new 21-tonne 856H-E MAX wheeled loader is part of its worldwide range of electric construction vehicles. Powering the machine is a 432kWh large-capacity lithium-ion phosphate battery from renowned battery manufacturer CATL.
alongside Volvo CE’s A25G or A35G ADTs in large earthmoving, roadbuilding, or quarrying applications.
The excavator is fitted with Volvo Smart View with Obstacle Detection, providing a real-time view of the machine’s surroundings. It is a safety system that issues automatic alerts when obstacles are detected.
Operator comfort has been a priority during design and the EC500 features a new and improved operator interface and cabin design.
“The 12.1" ergonomic touchscreen is said to provide easy, intuitive operation, reducing confusion and work interruptions versus the multitude of separate sub-systems that are all too common today”
The 856H-E MAX is capable of 10 hours of working time for light applications and eight hours for heavy applications. It also features an Intelligent Battery Management System that can be fast charged in 90 minutes.
"The industry is talking about battery -electric vehicles at a greater volume than in years past," said Andrew Ryan, president of LiuGong North America.
"LiuGong is the world's largest manufacturer of wheeled loaders, so it makes sense for our company to lead the industry in the adoption and application of battery technology."
The 856H-E MAX has already proven its reliability in the field, with more than 2,000 electric wheeled loaders operating in the world's toughest conditions as of October 2022, and exponential growth is expected. Its reliability is reinforced by the IP67-rated wiring harness and waterproof integrated battery package. All of that is backed by a standard five-year or 10,000-hour battery, motor, and controller warranty.
LiuGong says the 856H-E MAX thrives in work sites where traditional combustion engines aren't allowed or fixed-site operations where investments in charging
infrastructure make sense.
In addition to making work easier, the wheeled loader's new electric technologies are also environmentally conscious while offering a competitive cost of ownership. The 856H-E MAX consumes zero fuel, produces zero emissions, and significantly lowers noise and vibration levels.
The 856H-E MAX features intelligent controls and a human-centric design for a claimed superior operator experience. This includes load-sensing hydraulics, an EAT700 transmission with an electro-proportional valve for fast, smooth shifting, and independent control of the dual-motor drive for maximum hydraulic lift.
The LiuGong Intelligent Auto Digging System automatically cycles repetitive digging to reduce operator fatigue. Its electric control box also improves transmission efficiency compared to conventional machines.
In the non-electric, heavy-excavator sector Volvo CE says that its powerful new EC500 model has been designed to deliver high-performance outputs as well as superior levels of safety in use.
Replacing the EC480E, this new 50-tonne class excavator is well-suited to working
Stephen Roy, president of Volvo CE North America, said that the pre-production model on show at CONEXPO-CON/AGG 2023 “gives an insight into the future, with enhanced safety, operability and productivity.”
The next-generation excavator is set up to access a range of machine options to help operators complete tasks faster, more easily and more safely. It will also boost performance and productivity levels.
Manufactured at Volvo CE’s crawler excavator plant in Changwon, Korea, production of the EC500 will commence at the end of 2023 and the machine will be available in selected markets such as North America, Europe and Korea.
Komatsu Europe has unveiled the Komatsu SubMonitor system for wheeled loaders.
Focusing on simplified operation by merging many features into one device, the SubMonitor creates a new touchscreen interface for the operator to interact with the machine's assist systems, which include an Extended Load-Pilot, a new rear-view Supervision system with a high-definition camera and rear-radar obstacle detection, and an all-new, performance-boosting Efficiency Trainer module.
"The 12.1" ergonomic touchscreen is said to provide easy, intuitive operation, reducing confusion and work interruptions versus the multitude of separate sub-systems that are all too common today. The Komatsu SubMonitor is the base for a new era of machine features that deliver unrivalled control, comfort, and safety.
The Komatsu Load-Pilot as a weighing system has been updated in terms of
functionality and controllability. Accurate and fast weighing results with the improved auto-weighing function, material definition at will and productivity and efficiency display for different materials enable smooth operation. Since all important elements are displayed on the monitor, the adjustment can be easily made on the screen with just a few clicks, without diving into the machine menu. The tidy arrangement of all functions is selfexplanatory.
The SubMonitor is available as a fitting option for Komatsu's WA380-WA500-8 wheeled loaders.
Northern Irish waste firm Skipway Waste
purchase of two brand-new A-series wheeled loaders.
Belfast-based Skipway briefed its trusted dealer, Northern Lift Trucks, to source machines that would be durable, with a focus on good fuel economy and operator comfort. The machine that stood out as perfect for the job was the HL960A – and Skipway ordered two of them.
Matthew Heatrick, systems manager of Skipway, commented: “We’ve only ever used Hyundais here at Skipway – mostly 770 models over the years - so we knew that we liked and trusted the brand, and wanted to stick with them for our next
using half the diesel of the previous ones which obviously makes a huge difference to our finances.”
The two machines have been earmarked and specified for different uses – one of the HL960As will be based at a materials -recovery site in Belfast and used for the heavy-duty tasks of stockpiling waste and loading rubble and timber. This machine has been fitted with longer arms and supplied with different bucket attachments to ensure the HL960A can tackle any load, terrain and material in its path.
The second HL960A will be used for waste transportation at a second Skipway site in Newtownards, where flexible and robust machines are key to running an efficient
As producers of quality aggregates, Longwater Gravel has invested in an expanding fleet of Hitachi construction equipment to work across its three quarries at Coxford Abbey, Horstead and Wymondham in Norfolk. Celebrating its platinum anniversary in 2022 and ongoing partnership with Hitachi Construction Machinery (UK), the Costesseybased company has purchased the first two ZW310-7 medium wheeled loaders in the UK for the Coxford Abbey site near Fakenham.
The impressive new machines have been added to Longwater Gravel’s expanding line-up of Hitachi wheeled loaders: two ZW310-6s, a ZW220-5 and a ZW220-6 at Coxford Abbey; a ZW310-6 and a ZW220-6 at Wymondham; two ZW220-6s at Horstead; and two ZW180s servicing the stockyard at its Costessey headquarters.
In addition, the company has a ZX210LC-6 medium excavator working as the main production machine at each of the quarries.
As an example, the two ZW310-7s and ZX210LC-6 at Coxford Abbey help to achieve an annual production of 120,000 tonnes of sand and shingle, type 1 sub-base, natural shingle, and recycled, decorative and specialist aggregates. Once excavated and loaded on to an articulated dump truck, the raw materials are hauled to the production
One of the wheeled loaders feeds them into the hopper and on to a dry screening process. This separates the large (25mm and bigger) from the fine materials, with the former being crushed and the latter being moved along to a washing barrel, which separates the sand and cleans the stone.
The stone then emerges from a wet screen into the bays for 10 and 20mm gravel, as well as coarse and soft sand. The water from the process is recycled into a lagoon, with the silt being periodically removed by an excavator. The new Hitachi wheeled loaders are also used for loading trucks, material handling and creating stockpiles.
Simon Smith, Longwater Gravel’s operations director, says: “Our Hitachi fleet has been reliable over the past eight years. The machines work well and there’s minimal downtime. In addition, the all-important support we receive from HCMUK is
Major manufacturers of haulers say they are seeing great commercial potential for their products in regional markets, particularly in the United States, and also in Australia, South America and the UK. Liam McLoughlin reports
Rokbak says its RA30 and RA40 articulated dump trucks (ADTs) are proving a very big hit in the US market.
“Rokbak is seeing huge demand for its RA30 and RA40 articulated haulers in the US,” says Robert Franklin, Rokbak’s director of sales – Americas. “The US is leading articulated hauler demand globally with huge infrastructure spend. There is a lot of construction activity at the moment around house and road building, so we are keen to meet with customers and discuss how the RA30 and RA40 can help with these projects.”
The 28.9-tonne maximum payload RA30’s new transmission and high-performance 276kW engine improves fuel efficiency, operator comfort and, with 1880Nm maximum torque, delivers power when operators need it. The new transmission retardation system is combined with exhaust brakes and fully enclosed oil-cooled multidisc brakes to cut operating costs and increase safety and stability. The RA30’s drivetrain is also said to be perfectly balanced to provide excellent performance and productivity in all hauling conditions.
Ground-level test points, a fully tilting cab
and an electronically raised hood make the RA30’s servicing quick and easy – maximising uptime. Furthermore, Rokbak’s bespoke Haul Track system gives RA30 hauler operators more visibility and control of their machines, with live data viewable on desktop computers or mobile devices. This allows companies to protect their investment even when not on-site.
The 38-tonne maximum payload, 331kW high-performance-engine-equipped RA40 is a heavy-duty articulated hauler said to make light work of large-scale quarry, mine, and construction jobs, offering high capacity and claimed high performance in the toughest conditions.
The RA40 benefits from the same transmission retardation system, fully adaptable drivetrain, easy maintenance, and Haul Track system as its smaller RA30 sibling. The RA40’s planetary gear transmission is said to deliver smooth, efficient gear shifting, cutting fuel costs and increasing operator comfort – even under the most challenging conditions.
With sustainability in mind, the Rokbak event booth materials are all recycled or reusable. Two 40ft customised shipping containers, adorned in the recognisable
Rokbak aesthetic, will be used for meeting rooms and product information displays. Following the event, these will be shipped back to Motherwell, Scotland, for reuse at future events.
Global ADT specialist Bell Equipment says that, four years after commencing extensive testing, its autonomous technology is now at the adoption stage with more customers in the United Kingdom, South America, and Australia set to introduce autonomous Bell ADTs on their worksites during 2023.
“We’re extremely excited to have reached the adoption stage,” says Bell Equipment product manager Brad Castle. “Right now, we are working closely with one of our UK customers. They are a leading mobile plant supplier and earthmoving contractor that has a large existing fleet of Bell ADTs and is looking to initially install an autonomous system onto two B30Es for a quarry application. Initially, they will be introducing autonomous ADTs on two of its sites as part of a continuous drive to improve safety.
“At the same time, we have a mining customer in Australia who will be introducing five autonomous Bell ADTs later in the year. Both these customers have chosen xtonomy as their preferred guidance system.”
Castle says that providing autonomousready machines will be a part of Bell’s core business in the future, but in terms of sensing and guidance systems the company has decided that it makes more sense to partner with market leaders and innovators, as it does with drivetrain, hydraulics, and electronics technologies in Bell trucks.
“Bell currently has two approved service providers, xtonomy based in Europe and Pronto AI in the United States, both of which can work with Bell customers from anywhere in the world,” he adds.
Volvo Construction Equipment (Volvo CE) has released a new aftermarket option update – Downhill Speed Control – for the Volvo A60H articulated hauler.
The Downhill Speed Control update will further enhance the A60H’s already leading class comfort and control – helping to increase safety and efficiency on site by allowing operators to maintain their control and speed. The update is available as an aftermarket retrofit kit for all the A60H machines in the aftermarket, with new machines having the feature as from the factory.
Italy-based Perlini has introduced the new “little one” in its hauling range, the 26.5-tonne DP265WD.
Downhill Speed Control works by helping the operator to maintain a constant speed downhill and is easily adjusted by either the brake, retarder or accelerator pedal. The function is controlled by the new combined engine brake or Downhill Speed Control switch. It is activated by pressing the lower part of the switch, indicated by the symbol and the speed is set to the current machine speed when releasing the accelerator, brake or retarder pedal. A conversion kit is required to make the functionality available on older machines.
As well as providing enhanced safety, comfort and productivity in all conditions, it also benefits customers by reducing brakedisc wear, as well as activating the best combination of Volvo Engine Brake and service brakes. The feature is also already
Perlini says the new dump truck has been developed by combining the company’s decades-long tradition in mining haulers with the latest technologies, such as new control electronics, modern GPS monitoring and electronic weighing systems to produce a versatile, economical and reliable vehicle.
The manufacturer states: “With ‘small’ dimensions, the new Perlini DP265 is the ideal vehicle for quarries and public works, the width of less than 3m also allows road transport without the need of special transit permissions or escorts.”
It adds that the vehicle is equipped with the usual Perlini features, including the brake/retarder system with oil-bath brakes, oil-pneumatic suspension, and typical Perlini stability and comfort. It is also equipped with a Stage V Scania DC09 engine and an Allison 4430ORS transmission with updated
After 50 years of production, the Elnesvågen plant outside Molde in Norway, where the Doosan range of articulated dump trucks (ADTs) is produced, is celebrating the completion of the 10,000th machine to be built at the plant. According to plant manager Jan Roger Lindset, the Doosan ADT with production number 851951 will be delivered to Rental Group in Norway.
Production began at the plant in 1972 when the business was called Glamox. Since then, the brand has had several names, such as Moxy, Moxy Industrial, Brown Engineering, Moxy Trucks, and Moxy Engineering. In 2008, the name changed to Doosan when the South Korean manufacturer bought the factory and the product. In 2021, Hyundai Heavy Industries bought the Doosan construction equipment range, including the ADT line, and the name of the business was changed to Hyundai Doosan Infracore (HDI).
There are currently 150 employees at the Elnesvågen plant. With both Doosan and Hyundai ADTs now being produced at the factory, the workforce is expected to expand to meet an expected 40% growth in production. The Doosan ADT range comprises two 6x6 models - the DA30-7 and DA45-7 Stage V-compliant machines - the DA30-7 has a payload of 28 tonnes, while that of the DA45-7 is 41 tonnes. The range was extended at bauma 2022 Munich with the launch of a new 4x4 version of the DA45-7 ADT, intended to compete with rigid dump trucks (RDTs) in the 40-tonne class.
Doosan Infracore is replacing the Doosan brand on its construction equipment and introducing its new brand named Develon which is now in a transition period.
“When coming up with a new name, we had many ideas that could represent our brand’s direction and value,” says Hyundai Doosan Infracore CEO Youngcheul Cho. “That is why we came up with the combination of the two words ‘Develop’ and ‘Onwards’. We believe these words show the brand's purpose to advance the development of our world with new products and solutions.” AB
An updated version of a premium tophammer surface drill rig offers much for sustainability and productivity-minded quarrying customers, while a major Italian breaker company is making big strides in the US. Guy Woodford and Mike Woof reports
Epiroc is launching an updated version of its SmartROC T45 tophammer surface drill rig, further reducing emissions and boosting productivity while providing valuable data through smart technology and enhanced automation.
The updated model, optimal for quarrying and construction, includes several new features and options and will be available to order for all markets from May 2023.
The SmartROC T45 is designed for fuel efficiency and productivity. The larger capacity and performance of the rig allow for maximised production, and fuel costs are dramatically reduced by only using the energy needed for the work at hand. Furthermore, Epiroc's Smart technology provides valuable data to help manage and optimise workflow - the SmartROC T45 includes digital features which help to ensure that drilling always goes as planned.
The control system of the SmartROC T45 is based on a proven, intelligent design which presents information to the operator via an easy-to-use touchscreen interface. Enhanced automation helps achieve new levels of output, as a SmartROC does more of the work itself and reduces the demands placed on the operator.
"Efficiency is at the heart of the SmartROC T45," says Ulf Gyllander, Global Product Manager at Epiroc. "More uptime means more drilling, and using less fuel equals further cost savings. The productivity comes not only from state-of-the-art equipment but also from the ergonomic design choices and the Smart technology that assist the operator every step of the way."
"The intuitive SmartROC T45 is designed to dramatically reduce the risk of manual errors and human mistakes," continues Gyllander. "The operator enjoys assisted troubleshooting from the large touchscreen display, with monitored cables, sensors and modules. The FOPS- and ROPS-approved cabin offers excellent visibility and reliable LED lights with an option for an expanded lighting kit on both sides and support for two cameras. As a result, the risk of manual errors is reduced, and downtime is kept to a minimum."
The SmartROC T45 will be available to order for all markets from May 2023. Italian attachment specialist Indeco benefitted from a particularly strong performance in North America in 2022. Michele Vitulano, global sales and marketing manager for Indeco, commented: “The US is doing very well. We are very happy with the American market, and 2022 has been the best year ever for us in America, mostly on the smaller models.”
The productivity is further enhanced with the intelligent drill rig architecture on Epiroc's standardised platform and clever Smart options and features such as Hole Navigation System (HNS), Measure While Drilling (MWD) and ROC Manager. The result is excellence through precise drilling and consistent operation, improving blasting results.
Productivity is boosted thanks to precise drilling and consistency in operations, which delivers improved blast results and further cost-savings throughout operation.
Epiroc SmartROC rigs offer the lowest fuel consumption in the market, and the SmartROC T45 is the most energy-efficient rig in its class, thanks to the smart Rig Control System (RCS). This system constantly monitors compressor load and engine RPM to ensure no fuel is wasted and that environmental impact is kept to a minimum.
Manual control by the operator can optimise energy consumption, and the hydraulic system is optimised to deliver just the amount of oil needed. These features help reduce the environmental footprint and improve the operator's work environment. Epiroc uses quality components and parts commonality thanks to a standardised platform.
BELOW: Epiroc’s updated SmartROC T45 tophammer surface drill rig will be available soon RIGHT: An Indeco HP1800 breaker in action
The firm is now looking to expand its facility in the US to meet the strong demand for equipment. The site is also used to manufacture a number of items, such as mounting brackets for hydraulic hammers and hydraulic compactor attachments.
In addition, Vitulano said he is looking for a suitable business to add to Indeco’s portfolio. “We are scouting for an acquisition, a small company with a good product but that’s maybe been undercapitalised.”
With the firm having had great success in the compact breaker market in the US, Indeco is also looking to widen its product offering for more compact demolition tools, such as cutters for use on mini excavators. Vitulano said that he believes this offers considerable business potential for the future.
On another note, Vitulano said that Indeco is now achieving its first sales of breakers in Japan, a significant success given the strength of Japanese hydraulic breaker firms in the home market. However, he said that entering the South Korean market with the Italian breakers has proven considerably more challenging.
actuation, Ciccolella does not believe there will be any quick advances with these systems for units such as breakers any time
All excavator operators, contractors and OEMs who control their fleet via the Vemcon CoPilot platform now have access to operating modes for Lekatech's electric tools via an integrated app.
Vemcon CoPilot allows excavator operators to work faster, safer and more precisely by enabling them to control their mining and construction attachment via just one display. The platform's newly integrated Lekatech app allows operators to combine different frequency and energy settings for their Lekatech electric hammer attachment. At the same time, excavator operators can monitor their electric hammer attachmentgenerated data at a glance. As well as operating hour readings, the app displays various electric hammer safety functions and warnings.
Looking ahead in terms of technology, Vitulano commented that Indeco is monitoring the development of electric construction machines very closely. “We should think to the future when machines go electric,” he said.
However, with regard to the electric actuation of units such as breakers, there are
major technical challenges to be overcome, according to Indeco’s chief engineer, Alessandro Ciccolella. He said: “There is no loss in power as electric machines are very efficient.” But he questioned the ability of electric actuation systems to cope with the massive mechanical shock loads transmitted in units such as breakers. While the firm has been carrying out research into electric
Vemcon founder and CEO Jan Rotard: "Our CoPilot system sends all data to the respective fleet management system used by the contractor when required. In doing so, all components can be individually combined with each other by the user at any time and expanded almost indefinitely."
Founded in 2018 in Kausala, Finland, Lekatech aims to revolutionise hammer and other attachment technology through its direct electric drive products. AB
Weighing technology companies are introducing innovative new solutions that enable direct control of load volumes and tyre pressures, digital weighing data acquisition, and avoidance of engine idling. Liam McLoughlin reports
On-board weighing technology company Outset has launched a T1 Bluetooth transmission module, designed to allow direct and constant control of a vehicle’s load volumes and tyre conditions. The system works via an Android App for smartphone or tablet.
Outset, based in Vicenza in the north of Italy, says the module is suitable for use in articulated lorries, wheeled loaders, excavators, and aggregates dumper trucks.
All weighing and TPMS (tyre pressure monitoring system) data can be transmitted via a serial line to the on-board computer or directly in-cloud on external devices, helping users maintain the control and management of productivity, in addition to the safety of their vehicle fleet.
The data can be transmitted via GPS, SIM card or Wi-Fi to the cloud platform, with printed reports to ensure the continuous updating and management of the loading process and tyre monitoring activity.
Luca Toneatti, export area executive at Outset, says the company has more than twenty years' experience in on-board weighing. It supplies TPMS devices for commercial vehicles, earthmoving machines, mining, and logistic vehicles.
Outset technology is designed to provide precise and efficient weighing while loading, in addition to continuous monitoring of tyre pressure and temperature.
Toneatti says that Outset makes constant, significant investments in R&D to improve its products and develop new, innovative instruments that incorporate the best new technology. The company also works hard,
he says, to maintain its reputation for developing user-friendly tech.
The company has an extensive network of authorised sales partners around the world, and plans to expand its network further in the coming years.
Outset provides a range of technologically advanced devices compliant with Industry 4.0 directives, and it works closely with operators to optimise loads. The company’s systems ensure that payloads stay within legal limits and that vehicles do not get overloaded.
In separate news, Outset says it has changed its legal form and become a “Benefit Company.” Outset says this move, made on 30 December 2021, formally recognises how it has established a raft of social responsibility and ethical policy commitments in recent years, all of which are now an integral part of the company's DNA.
“As a B Corp we operate responsibly, following sustainable and transparent criteria, which are rewriting the way of doing business globally,” says Toneatti.
A Benefit Company is one that integrates into its corporate purpose, in addition to profit objectives, the aim of having a positive impact on society and the biosphere, says Outset.
"First of all, we thought about the people who work with us, their well-being and happiness, the enhancement of their talents and the creation of new jobs," Toneatti adds.
"We aim to create a healthy and meritocratic environment where people are happy in the company and put passion into what they do."
The new hydraulic WK60 excavator scale from mobile weighing systems provider Pfreundt impresses with digital weighing data acquisition, precise measurement results and intuitive operation.
The WK60 excavator scale enables material weighing directly in the work process and thus fast and accurate loading of transport vehicles. Equipped with four pressure and four inclination sensors, the robust mobile weighing system reliably delivers precise measurement results even on uneven terrain. Digital management, analysis and further processing of the recorded weighing data is also easily possible through a connection to the Pfreundt web portal.
The weighing electronics are available in the three different versions, WK60-XS, WK60-S and WK60, and can be flexibly adapted to individual customer requirements and operating procedures thanks to the different functional scope of these versions. The hydraulic excavator scale can also be retrofitted at any time into excavators with
mono booms of all manufacturer types.
By recording the weighing data directly during the work process, the hydraulic Pfreundt excavator scale enables fast and accurate loading of transport equipment. This accelerates logistical processes and optimally utilizes production capacities.
Due to the optimal loading of means of transport in compliance with the permissible total weight, overloading is avoided. Penalties as well as repair and maintenance costs due to overloading are saved.
The hydraulic excavator scale ensures transparency in the material flow. By analysing and evaluating the recorded data via the Pfreundt web portal, internal material movements can be traced. This helps to optimise the operating processes, e.g., the avoidance of idling - energy is saved, costs are reduced.
Pfreundt says the hydraulic WK60 excavator scale provides a number of benefits including: dynamic weighing in the working process for fast and accurate loading; precise weighing results even under extreme conditions; fast availability of weighing data even with a high number of short loading cycles; maximum freedom of movement of the machine is fully maintained; easy and intuitive operation of WK60 weighing
electronics through 7-inch touch display; extensive and customisable master and weighing data management; and installation or retrofitting possible in excavators with mono booms from a wide range of manufacturers.
Tamtron Group says it is continuing to invest in growth and has entered into an agreement to acquire the entire share capital of fellow Finnish weighing technology company Lahti Precision.
“The acquisition will enable Tamtron to provide its customers an even wider global range of weighing and dispensing technologies, advanced SaaS solutions and lifecycle services to ensure customer success,” comments Tamtron Group MD Mikko Keskinen on the background of the arrangement.
“Lahti Precision’s System sales solutions form a new business sector and foundation to the Tamtron group which will help us serve an even wider international clientele.
“It is fantastic to be able to collaborate with the professionals of Lahti Precision and collaborate in the development of the most advanced solutions in the industry. Both companies have a strong culture of continuous development and therefore we will be a good match. Tamtron is in a phase of strong growth and the acquisition represents an important step in achieving our strategic objectives.
“I welcome the 94 experts of Lahti Precision Oy, the current and future customers, partners and stakeholders to build mutual success.”
Lahti Precision has more than a hundred years of weighing industry expertise, specialising in the development of industrial competitiveness. Its head office is in Lahti. The products and services of Lahti Precision cover industrial weighing solutions (e.g., truck scales, big bag stations, conveyor belt scales, dispensing systems, lifecycle services and calibrations) and mScales, a SaaS-based material-flow management system. During 2022, the company’s turnover reached €17m and EBITDA (earnings before interest, taxes, depreciation and amortisation) totalled €1.8m. The company employs 94 experts. The customer base consists of leading industrial, recycling, mining and logistics companies, including manufacturers of battery materials used in electric vehicles.
“Together with Tamtron, Lahti Precision will create a strong actor on the Finnish and Nordic markets,” says Juho Koskinen, managing director of Lahti Precision. “A comprehensive portfolio of weighing systems, a Nordics-wide after-sales service network and the combination of two market-leading SaaS-based material-flow management systems will provide significant benefits to customers now and going forward. Lahti as a location will be a major centre of expertise in the heavy weighing sector of Tamtron Group. We are also confident that our international success will develop further with the addition of Tamtron’s foreign subsidiaries and partners into our distribution channel.” AB
MDS, an Irish manufacturer of heavy-duty and recycling mobile and static trommels, apron feeders and conveyor systems, is well placed for growth after a major investment by parent company Terex in its manufacturing capabilities and product development Guy Woodford reports
Conor Hegarty, MDS's general manager and business line director, tells Aggregates Business that the Co. Monaghan-based fi has exceeded its trading expectations following its summer 2021 acquisition by Terex.
He explains that MDS, whose product range includes its flagship M515 mobile heavy-duty track trommel, has a healthy plant order book, with works to signifi expand the company’s current 34,000ft² manufacturing facility set to begin later this year.
Hegarty says that MDS is also benefi from being able to utilise Terex’s Materials Processing (Terex MP) business division’s extensive global dealer network to grow its potential sales market, offering quarry and other industry customers of Terex MP’s Powerscreen, Finlay and other branded crushers and screeners a premium heavy-
duty trommel add-on option for their tougher rock and recycling applications.
“We have exceeded our post-acquisition sales and production expectations by 20%. We have done a lot of improvements at our factory site, replacing a lot of old equipment and investing in a new paint shop facility,” says Hegarty. “We’ve also added new dealers in the UK, Ireland, Denmark and other parts of Europe. We took our time in adding them as we had orders we needed to satisfy with our existing dealers.”
“We have exceeded our post-acquisition sales and production expectations by 20%”
Hegarty says that MDS’s manufacturing site expansion includes a new plant assembly hall, with a planning application made to relevant local authorities to build on land adjacent to the current factory. “We expect to break ground by quarter three [2023] and the extended facility to be operational by the start of next year. It will give us an additional 22,000ft² of manufacturing capacity.”
MDS currently offers four mobile and three stationary products. While operating in what he describes as a niche sector of the screening market, Hegarty believes the heavy-duty mobile and stationary trommels market offers promising growth potential. “We are seeing more and more enquiries about our static trommels, our initial product offering before we expanded into mobile machines. All our recent focus has been on our mobile units, but we plan to relaunch our static range this year as we get more manufacturing capacity.”
MDS’s M515 trommel was proudly showcased during the company’s debut appearance at CONEXPO-CON/AGG in Las Vegas, USA (14-18 March). Ideal for creating rock riprap and recovering rocks mixed with clay and other sticky materials, the updated M515 has been redesigned to include new features that improve transport, access, and stockpile heights.
The plant’s 'swing out' engine and cabinet access platform features allow
“Our main markets are North America, the UK, Europe, and Australia – with North America supplying the bulk of customers”
for easier plant maintenance. The M515’s extended fines and mid-product conveyors increase stockpile heights. Additionally, Hegarty notes that the location of the engine has been changed to the side of the unit, enabling customers to fit the unit on smaller bed trailers in North America, lowering customer transport costs.
“Our main markets are North America, the UK, Europe, and Australia – with North America supplying the bulk of customers. Their focus has historically been on the M515, our biggest-selling model. However, we are seeing an uptick in North American interest in some of our smaller models. In Europe, the preference has been for our smaller trommel models. I think that’s because Europe typically has customers involved in more recycling rather than [rock] riprap applications.”
Focusing on how MDS has built up the aftermarket side of its business, Hegarty, a former international sales director of Terex MP’s environmental business, Terex Ecotec, says: “We have invested heavily in it, building it up from what was a very basic offering. We have been able to tap into Terex MP’s after-sales departments and utilise existing dealer help desks, the online warranty portal and the Dungannon-based [replacement] global parts hub. It’s been a seamless transition to move our after-sales function into a much bigger Terex MP aftermarkets team.”
Asked what heavy-duty and recycling trommel customers can expect to see next, plant-wise, from MDS, Hegarty says: “The revamped M515, with lots of new features, was launched at CONEXPO. We also had a recent plant forum in Chicago with our North American dealers to hear directly from them what their customers were saying about what they’d like to see. Off the back of that, we have a clear roadmap of what we’d like to develop. We will be launching a new M518R in the fourth quarter of this year. That was a product MDS had introduced previously, but we have effectively gone back to the drawing board and redesigned the machine with a lot of improvements.”
Hegarty stresses that the M518R’s redesign ensures easy transportability, power unit maintenance access, and increased stockpile height advantages. AB
No matter how challenging your needs, EARTHMAX SR 41 is your best ally when it comes to operations that require extraordinary traction. Thanks to its All Steel radial structure and the special block pattern, EARTHMAX SR 41 provides excellent resistance against punctures and an extended service life. In addition to long working hours without downtime, the tyre ensures extraordinary comfort.
EARTHMAX SR 41 is BKT’s response to withstand the toughest operating conditions in haulage, loading and dozing applications.
Metso Outotec’s new Nordberg HP200e cone crusher
Major global market crushing and screening plant manufacturers were out in great numbers at the recent CONEXPO/CON-AGG 2023 exhibition in Las Vegas, USA, to highlight new solutions and comment on evolving market trends. Guy Woodford reports
Being able to showcase their new and latest products to more than 139,000 attendees at CONEXPO/ CON-AGG from 14-18 March was a great business opportunity for the world’s biggest crushing and screening plant names – and they certainly made the most of it.
Some global and many North American product launches lit up the Las Vegas Convention Center, while expert market analysis by senior top manufacturer executives added much to the five-day showpiece event for the construction, mining, quarrying, and recycling industries.
Metso Outotec unveiled its new Nordberg HP200e (HP200e) cone crusher for the global aggregates market. The plant has been designed to offer customers better performance and improved uptime levels in a more sustainable way, says the manufacturer. These changes have been enabled by
kinematics and new chamber designs.
The model’s new liners are fitted in the crushers without backing material, making maintenance breaks shorter and the liner replacement faster, safer and less hazardous for the environment.
”The evolution of Metso Outotec’s cone crusher technology brings multiple benefits and presents a true evolution for aggregates producers in terms of performance, uptime, serviceability and application coverage,” says Ilkka Somero, product manager, Nordberg HP Cone Crushers in Metso Outotec.
“The concrete benefits include enhanced performance, 10% more head motion, 20% more kW power, 20% more force, new and more efficient chambers, an anti-spin brake for higher uptime, serviceability improvements … and a feed cone lifting tool.
“Environmentally, the new HP200e crushers are also a more friendly solution, as they do not require backing material. We
are truly happy to be able to offer this latest evolution of our leading crusher technology to our customers,” he said.
Metso Outotec is also offering strong aftermarket support and parts availability for the HP200e crushers. The majority of spare parts in the current HP200 and the new HP200e are common, which will enable continued global spare part support for new units.
The Finnish crushing and screening plant giant has also established a start-up inventory for HP200e-specific parts in Europe and North America. Furthermore, a full scope of HP200e crushing chambers will be available in main stocking locations for the launch markets.
Metso Outotec also provides a head & bowl upgrade kit for the existing HP200 cone crushers, allowing the installation of no-backing chambers and for customers to enjoy the same health, safety and environmental benefits as with the new HP200e model.
Three other HPe cone crushers – the HP350e, HP450e, and HP600e – will be introduced over the next two years.
Terex’s sustained strategic investments in product electrification and other parts of its business have left the off-highway equipment giant in a strong position to grow and capitalise on major market trends, such as the growing importance of digitalised production to customer operations.
“Electrification started three years ago, but it’s picking up steam everywhere. Around 60% of our Terex Materials Processing business’s products are offered in some form of hybrid or electric form,” said John Garrison, Terex CEO and president. “That train is leaving the station, and it is accelerating as we go forward.
“The whole world is digitising, and we are not immune to that. We have to figure out how we utilise digitalisation to be successful.”
The Terex Materials Processing (Terex MP) business division of Terex includes, among other brands, Powerscreen, Finlay, EvoQuip, Terex Materials Processing Systems (Terex MPS), Terex Washing Systems (TWS), Ecotec, and MDS.
Garrison continued: “We are trying to grow as a company and improve our customer’s product lifetime experience. I am delighted with the great work that our MP business segment has done in expanding the addressable markets and expanding into new spaces with new products and distribution channels.”
Among many recently introduced Terex MP brand products are Powerscreen’s Gladiator MT1150SR wheeled crushing and screening plant and Titan 2300 screener, Finlay’s C-1550+ tracked cone crusher, Terex Washing Systems’ FM Pentium washing solution, EvoQuip’s Cobra 230R impact crusher, and Terex MPS’s Cedarapids CRC1350S portable cone crusher and Simplicity ESX620 'Extra Clearance' horizontal screen.
Kieran Hegarty, Terex MP president, said Terex MP sees itself as a diversified and
specialised manufacturer for customers in industries including, among others, construction, quarrying and environmental management.
“In the last three years, we have continued to evolve and grow. For example, in March 2021, we bought a factory in China with a view to manufacturing crushing, screening and environmental equipment, primarily for the Chinese market. That’s been a really good long-term investment in a very large market.”
McCloskey International believes widening its electric-powered plant range will help the company build on its very strong trading start to 2023, after celebrating record sales revenues and product deliveries in 2022.
Acquired by Metso Outotec in 2019, McCloskey International is part of a group of construction, quarrying, construction and demolition (C&D) and wider recycling industry-suited plant brands that includes McCloskey Environmental, Lippmann, MWS Equipment, and Tesab.
“Last year was a really busy year for us, and a record-breaking year, both for McCloskey International and the wider group [of brands], and we are growing again this year,” says Toni Laaksonen, senior vice president of McCloskey International.
“The acquisition of Tesab last year helped grow our revenues. It was a very big thing for us. We have also expanded organically, recruiting more dealers. For example, in Africa, we have grown our dealer networks significantly.
“We have also seen good dealer growth in North America, helping us secure new business.”
Laaksonen says that customers globally are looking for more and more sustainable products, including more electric-powered equipment: “There are certain markets that are very demanding on the electric plant side, such as the European market. We are also seeing this trend in certain American states.
We are also electrifying our heavy-duty jaw crushers, including the J6. Our screeners are already available as dual-power plants.
“We are also looking to grow our business organically through further acquisitions.”
Among McCloskey International’s new machines are the ultra-efficient S190 dualpower portable vibratory screener, and the ST100TVR stacker, the latter said to reach new heights in sustainability, efficiency and fuel savings with its dual-power option and lift-axle option, allowing it to switch from track mode to radial mode in seconds.
SBM Mineral Processing (SBM) is delighted
and end products. In real time, those values reach centralised digital labs at SBM, where they are further analysed. Necessary adjustments are then made on the ‘digital twin’ of the working machine and re-transmitted directly to the REMAX 600 in the field.
Known as ‘Crusher 4.0’ and developed together with the University of Leoben, the REMAX 600 was presented at the bauma Munich exhibition in October 2022. Largescale field tests of a REMAX 600 are currently being carried out at an Austrian quarry partner.
“We have made three REMAX 600 plants so far. The first has already done 1500 hours of testing with an Austrian quarry customer. All has been good so far on testing,” said Erwin Schneller, SBM managing director.
“The first sold machine will be delivered to a customer this year, with the others being delivered by mid-next-year.”
Another big machine for SBM is the JAWMAX 400 jaw crusher, said to feature one of the most advanced diesel-electric drive concepts on the market. A combination of fuel-efficient onboard diesel and a performance-tuned generator powers the plant’s materials processing.
SBM’s mobile plant range comprises 12 track-mounted JAWMAX jaw crushers and REMAX impact crushers, capable of 250 –800tph production. The plant range shares the same innovative drive concept, with fewer hydraulics ensuring less risk of failure, lower maintenance and parts inventory costs, and thus higher availability, says SBM. Overall savings from running the plants can, says the OEM, be 40% to 75%.
SBM sees the US as a major growth market. Schneller said very good discussions are taking place with a number of potential dealer partners in different parts of America. “I think there is the potential for us to sell 50 machines a year in the US,” he added. AB
A lively global mineral washing plant market is good news for customers and a range of premium solution manufacturers. Guy Woodford reports
When a Swiss customer needed an end-to-end excavation wash recycling system for its DORO site in DIttingen, a municipality in the district of Laufen in the canton of Basel-Landschaft, Terex Washing Systems and its dealer, Avesco, answered the call.
With thousands of tonnes of construction and demolition (C&D) and excavation waste being stockpiled each year, a system that can recycle this waste into a saleable product has environmental as well as financial benefits to aggregates producers. It is exactly the solution Albin Borer AG, a Swiss Group in construction, infrastructure and material treatment, had been seeking when they began to investigate a way to recycle the waste they were sending to landfill.
Terex Washing Systems (Terex WS) was tasked with finding a solution to this problem for this customer, which resulted in the design, manufacture and installation of a complete end-to-end excavation wash recycling system. Everything from the feeder
Albin Borer AG's plant solution combines material feeding, rinsing, crushing, aggregate scrubbing & sizing and sand production
to the filterpress was included in the resulting installation, which manages to achieve throughputs of 250 tonnes per hour (tph) of C&D and excavation waste, producing nine saleable products. The close working relationship between Albin Borer AG, Avesco and Terex WS, along with a high level of aftersales support, has led to this bespoke project being commissioned successfully.
Albin Borer AG is an independent, family-owned company, that has been in business since 1932. It is a strong, futureoriented business that provides high-quality products for infrastructure and roads, concentrating its strengths on a wide range of construction industry services. From its locations in Erschwil, Laufen, Bolligen and Basel, the company operates in the cantons of Solothurn, Aargau, Bern, Jura and Basel. Many family members are still very active in the company and are part of the innovative advancements it has made over decades.
Albin Borer AG wanted to start processing its own waste material that was accumulating from infrastructure work that
was happening in the region. Ultimately, the business wanted to generate a saleable product and open up a new revenue stream.
A major part of the overall Terex WS plant design was based on high capacity on a small footprint, due to site space restrictions. In addition, there was not a lot of water available on the site, coupled with environmental legislation around water use, which demanded additional design expertise from Terex WS for the final solution. The state-of-the-art Terex WS washing solution, which ensures that 95% of the water is recycled and reused within the wash plant, was achieved by the innovation team of applications and engineers at Terex WS in partnership with Avesco. The resulting full ‘feeder to filterpress’ solution also incorporates crushing capability from fellow Terex Materials Processing brand Terex Mineral Processing Systems (Terex MPS), as well as Terex WS’s AquaClear full water treatment solution. AquaClear features a Terex-designed and -manufactured filterpress with the capability of processing 250tph of feed material, and the ability to process 25 tonnes of sludge/final waste per hour.
Terex WS and Avesco continue to provide 24/7 aftercare support to Albin Borer AG as and when it may be required.
feed material from the loading shovel and removes oversized stones (larger than 150mm) from the material, which is achieved by the 150mm gaps in the finger bars installed. These oversized stones are stockpiled for later use. Medium-sized stones 150/80mm are sent via a side chute into a feed hopper, feeding the Terex MPS HSI 3434 horizontal shaft impactor. Since occasional pieces of metal were present within the feed material, an over-band magnet has been installed after each of the feed hoppers.
Out of the Terex MPS HSI impact crusher, the crushed stones are either passed to a dedicated stockpile, a dry 0-40mm stockpile, or onto the main conveyor sending the raw material to the washing plant.
After oversized stone and any metals are removed from the feed material, it makes its way up the main conveyor and enters
into a Terex 20 x 6 (6m x 1.80m) three-deck rinsing screen. This 20 x 6 ‘pre-screen’ Rinser gives the material an initial wash before the various fractions are split with different apertures on the screen mats. The sand (0-4mm) and water from the rinsing screen pass to the ‘Prewash’ tank. The Terex WS Pre Wash has novel design features which allow the operator to process difficult or dirty material and ensures the production of sand products that conform to strict specifications.
The four 4-80mm aggregrate fractions pass into the new Terex-patented HydroScrub logwasher.
This HydroScrub is a unique design logwasher for aggregates scrubbing, patented by Terex, which allows operators to hydraulically adjust the hull angle from 9°
to 16°, depending on the raw material to be treated. This gives the operator the ability to process a wider range of feed materials and is ideally suited for recycling applications. If the raw material is containing a lot of light-density contaminants like wood, roots, plastics etc, the angle is set up high, and floating elements are easily removed. Likewise, if the raw material is containing more clay conglomerates, then the angle is set low, which results in better stone-onstone scrubbing giving better throughputs and a cleaner aggregates product and eliminating the need for secondary scrubbing on high clay bound or dirty material.
The post-screen of the HydroScrub classifies the material into two different sizes - 4-40mm and 40-80mm. The 40 -80mm can
be sent back to the crusher, or it can be sent to the dry classifying screen. The 4-40mm is also conveyed to the set of dry screens.
The water that has washed the aggregates up until this point in the process, along with the sand, is collected in the Terex WS PreWash tank. This unique solution is receiving all of the process water from the upstream process, with the sand, extra fines, clay, contaminants, and light-density particles.
The Terex WS PreWash tank allows the ability to produce sand products to the required specification from materials with high silt content. It is a must for recycling applications and plant operators. The principle of it is to pump less volume out than is entering the tank. It is designed to ‘overflow’ gently, separating out extra fines and the light density contaminants, keeping only the sand 0-4mm. This is then sent by a centrifugal pump to the sand-washing Hydrocyclones module.
The Terex WS FM200 Sand Plant is part of the wider solution, and it is fitted with separators, high-performance cyclones, which are also specially designed for recycling applications. The use of separators means the plant can handle the variability of material that is often the case with construction, demolition and excavation material and results in a reduction in losses of valuable sand product, and the production of an in-specification material.
The FM200 also features a double-wash process. The Terex WS double-wash process ensures maximum recovery of sand through the removal of silt, slimes and clays below 63μm. The sand slurry (0-4mm and water) is pumped to the primary separator for an initial wash. The underflow discharges onto the dewatering screen, where it receives a further rinse. Any fine sand which passes through the screen is collected in the sump and pumped to the secondary separator for a final wash. It was necessary to double wash the material at the Albin Borer AG site due to the high percentage passing 63-micron in
After this double-wash process, the two specification grades of sand are dewatered onto the high-frequency dewatering screen, which reduces residual water content in the final product to 10-15%. The water from both separators containing the minus 63-micron material is collected in a ground sump and pumped into the thickener tank—where the water-management process begins.
The wastewater is pumped into a low-level thickener with flocculent added, from the central control room housing unit. Within the low-level thickener, the waste particles of silt (minus 63-micron) and clay combine with the co-polymer, or flocculent, to create a larger, heavier particle that sinks towards the base of the cone. The flocculent dramatically speeds this process up and allows the clean water to pass over the top weir of the thickener into a collection tank, where it is recycled back into the wash plant.
The sludge that has been collected at the bottom of the deep cone thickener is pumped
is transferred into a filterpress. The filterpress on this Albin Borer site is the Terex WS 165 plate press, with a plate size of 2m x 2m. The function of the press is to recover the last remaining water within the thickened sludge.
The filterpress has a working pressure of 16 bar (232psi). Each plate is covered in a nylon filter cloth, which, when filled with sludge under pressure, forces the remaining water to be removed from the sludge. This water is then recycled back into the wash plant to be used for washing aggregates and sand once again.
After the water has been removed from the sludge, bomb doors below the filterpress open, and the hydraulic ram begins to decompress. The slurry cakes are then rapidly discharged into the bay below the filterpress. Particularly sticky cakes are removed with a pneumatic plate shaker that ensures all the plates are ready for the next cycle. The cakes below can then be re-used for several applications, such as lining for ponds.
Albin Borer AG opted for an automatic cloth-wash system on their filterpress so that the lifespan of the filter cloths could be extended while optimum performance is ensured. This system cleans each cloth individually using a high-pressure water jet.
Johnston Patterson, product & applications manager at Terex WS, explained: “This wate-management system recycles 95% of the water used for this application. Albin Borer AG only needs a small tank of water to top up the system every so often. This has a hugely positive impact on the environment and has financial benefits.”
The result for Albin Borer is the sustainable production of usable and saleable sand and aggregates product from C&D and excavation waste. This also has the environmental benefit of being diverted from landfill. Additionally, the water-management products recycle the dirty water from the process and return clean water back to the process again for use.
Patterson added: “The customer is very pleased to have a solution in place to recycle their C&D and excavation waste. The working relationship between Terex Washing Systems, Avesco and Albin Borer AG has played a huge part in achieving a high level of performance for this plant.”
CDE is primed for growth in North America as the region’s customers increasingly look to turn dirt into dollars.
With 30 years of experience providing optimised, proven solutions to customers worldwide, Cookstown, Northern Irelandheadquartered CDE’s technologies have successfully diverted more than 100 million tonnes of CD&E waste from landfills, while turning construction, demolition and excavation (CD&E) materials into highspecification outputs.
The company’s AggMax scrubbing and attrition system, its Counter Flow Classification Unit (CFCU) for density separation and the EvoWash sand classification and dewatering system are among its proven plant solutions.
“We all understand that the depletion of natural aggregates is happening at a rate that is pretty scary. CDE has proven solutions that will slow that consumption of materials,” said Darren Eastwood, business development director at CDE, during CDE’s CONEXPO/ CON-AGG 2023 press conference.
“We’ve been proving our solutions for the past 20 years, and in the last number of years, have brought them to the US and Canadian market. The recycling of inert and contaminated construction, demolition and excavation wastes can make a big difference to the construction industry across those countries, easing the pressure on landfills. It also eases the pressure on the trucking industry, which is often having to shift materials over long distances into cities. Most importantly, it eases the pressure on existing quarries and the valuable precious material that they have. We can also keep required material as close to the demand centre as possible.”
Eastwood said CDE’s two latest US customer recycling plants have gone live in California and Pennsylvania. The California plant is the first CDE sale in the Golden State. It will treat and process a variety of construction and demolition wastes. “This will make a big difference to the circular economy there. It will produce dependable recycled products for surrounding cities while doing away with the need for excessive long-distance trucked-materials supply. It will also have a big impact in lowering the cost per tonne of production and in the gas trucks need to use.
“The Pennsylvania facility is a stone’s throw from a city centre. It will be producing
C33 [product] and a range of aggregates.”
At CONEXPO/CON-AGG 2023, CDE also unveiled its new P2-168 Infinity screen. With a processing capacity of up to 700 tons per hour, it's the largest model in CDE's range and has been designed specifically for the US market.
Matec Industries (Matec) will be opening a new factory in June to produce its massive Twin Freccia Rossa, the world’s biggest filter press.
The new factory is in Mulazzo, in the Italian region of Massa-Carrara, North Tuscany. It will be the sole production facility for the 50-metre-long, 600 tonnes per hour Twin Freccia Rossa.
The filter press is designed to combine the efficiency of two machines into a single product, offering faster sludge feeding and cake-discharge time.
Speaking at CONEXPO/CON-AGG 2023, Matec marketing manager Tatiana Bini said the company is taking on 60-70 new employees to work at the new factory in its offices and workshop.
"We are opening the new factory as we have had a lot of new orders and need to increase production," she added.
Italy-based Matec will now have three manufacturing bases. In addition to the new factory, Matec recently acquired the Alfa Pompe factory in Verona and has a manufacturing facility for small and medium machines at its headquarters in the town of Massa which is also in the Massa-Carrara province.
The Twin Freccia Rossa was first unveiled at the bauma trade show in Munich, Germany, in October 2022.
MWS Equipment, one of five McCloskey International business group brands under parent company Metso Outotec, is incorporating Metso Outotec pumps and cyclones into its machines - an industryfirst pairing within the sand and aggregates processing industry that will bring new levels of efficiency to MWS Equipment’s product range. On display at the recent CONEXPO/ CON-AGG 2023 exhibition in Las Vegas (14-18 March) were the MR200E Pump and the 650 Cyclone.
“A key focus is to expand the business’s [market] coverage, with more distributors coming from North America, Europe, and Asia-Pacific,” said Niko Lamminmäki, director of MWS Equipment and McCloskey Environmental. “We are also using different sales channels. In India and Norway, for example, we are using Metso Outotec direct sales teams, who have a strong foothold in those countries. We also manufacture our washing equipment in India [at the Metso Outotec facility in Alwar, Rajasthan].” AB
The first models of a new fully-electric range of Lokotrack crushers and screeners will go into production later this year at Metso Outotec’s renowned Tampere facility in Finland. Guy Woodford visited the famous site to get the lowdown on the keenly awaited new plant range and other latest big product development news. He also gained a fascinating insight into what makes Tampere a spiritual home for the successful quarrying, mining, construction, and recycling plant manufacturer
The results of a €20mn primarily Tampere facility-based investment in research and development (R&D), Metso Outotec’s new fully-electric crushers and screeners for aggregates and recycling customers are set to become highly soughtafter solutions among premium plant customers upon their release, with the first models in the range set to come onto the market later this year.
Speaking during Aggregates Business’s visit to Metso Outotec Tampere in November 2022, Jarmo Vuorenpää highlights how the all-new, fully-electric Lokotrack EC range machines are based on Metso Outotec’s new electric platform and can be run from an integrated genset or external grid to lower operational cost.
Vuorenpää, director of the new Lokotrack offering, says the new machines are reliable plants that are easy to use, maintain and
combine, and represent scalable solutions that are easily adaptable for different capacities and applications.
Lokotrack crushers and screeners were first launched onto the global market in 1985, but Vuorenpää stresses that the new fully-electric model range has been a case of “starting from scratch”.
“It has been our biggest-ever product range-based [Aggregates division] investment,” he emphasises. “We have been building our electric platform since 2020. It allows us to have scalable solutions for different capacities and applications. I don’t think anyone else in our industry is doing it this way.
“There are two main reasons for our approach. The first is the short-to-mediumterm advantage of having a plant range with fewer parts and harmonised design. Our partners, distributors, and customers will get the same building blocks for each machine. The other advantage is that our modular
electric platform will allow us to react much quicker when hydrogen fuel cells and other power technology options become available. We will be able to accommodate them far more easily.
“As well as extensive testing by Finnish customers of the first new Lokotrack plants, we are doing parallel technology testing. The latter testing is not related to the first few new Lokotrack launches but is preparing us for the future.”
“The new range has improved automation and connectivity among its new features. Our performance and plant-servicing baseline is pretty high, and we believe we can lift it still further,” adds Kimmo Vesamäki, vice president of technology and aggregates site manager at Tampere.
The new Lokotrack range will be fully compatible with the Metso Outotec Metrics (Metrics) online digital monitoring and data analysis solution. As well as increasing plant uptime by optimising maintenance
scheduling and EPS (equipment protection services) inspections, Metrics enables users to carry out remote and self-service troubleshooting, and, in partnership with their dealer distributors and Metso Outotec, to measure, analyse and improve plant capacity and performance and achieve productivity (KPIs). MO Metrics also delivers big sustainability gains to customers globally via higher efficiency, production, yield, and plant utilisation while ensuring less idling, energy, wear, and waste. This, along with electric-power usage, dramatically lowers operators’ CO2 per tonne.
“We are trying to have all our equipment connected to Metrics on leaving the factory. There are a lot of people in our business who say, ‘I think so,’ when it comes to aspects of their plant’s operation, but we want to definitely know and have information that can improve things. Metrics supplies this and is its basic philosophy,” explains Pekka Itävuo, Metso Outotec digital development manager. “We have three types of Metrics users: the sales, distributors and customers, who have slightly different needs, and we need to be aware of this in supporting them.”
Tuomas Martinkallio, Metso Outotec vice president of digital services, says the evolution of Metrics will eventually see it extended, with the help of AI (artificial intelligence), to give the user more live, automated, actionable data analytics across multiple Metso Outotec crushers and screeners on a single job site.
The manufacturing of crushers at the 117-hectare Metso Outotec Tampere site started more than 100 years ago, in 1921. The very first four Blake No.2 model crushers were delivered to the Finnish Roads and Waterways Administration in 1921, and they were the first machines suitable for producing aggregates needed in road building.
By 1949, these initial machine ranges had gained considerable success, and a new jaw crusher that operated with a single
toggle plate was launched. Research and development around rock crushing continued, and in 1976 the new C Series jaw crusher was launched.
The current Metso Outotec business was still part of Rauma-Repola in the 1980s, and the Tampere factory – then called Lokomo – became the world’s largest crusher manufacturer in 1989. This milestone was made possible after the acquisition of Ateliers Bergeaud’s operations in France, followed by Nordberg’s US functions a year later. As a result of this expansion, the manufacturing of crushers doubled in Tampere. Even though the company had already manufactured the Blake model, a predecessor of a mobile crusher in the 1920s, the launch of the iconic mobile crushing and screening plant Lokotrack in 1985 has turned out to be a true success story.
Metso Outotec’s Tampere facility has produced thousands of crushers. The company hosts a 2008-established crushing test laboratory in Tampere, where customers’ rock samples are analysed, and then the best possible combination of machines to meet the customer requirements can be recommended. Ville Viberg, the Tampere facility engineering and testing manager, tells Aggregates Business how he needs a minimum of 5kg of customer site material to carry out standard or advanced tests, with around 300 tests a year carried out onsite. There is an average fiveday turnaround in site material being received to the customer getting a detailed laboratory test report.
“For standard tests, we check the customer
material’s solid density, crushability, and abrasiveness. The latter gives an indication of a crusher’s wear parts,” highlights Viberg. “ In our advanced tests, we put the material through our lab jaw crusher, which is a smaller version of a Metso Outotec jaw crusher, with sensors measuring the crushing force, capacity, and power draw during operation. We can assess the product curve and how it compares to other tested products, detect problems with the final product shape and may recommend an alternative crusher for this type of material.”
Assisting Viberg in his work is Bruno, Metso Outotec’s intuitive software program for simulating the aggregates production process. First launched in 1996 and developed over time, Bruno covers all Metso Outotec feeders, crushers and screens. The user enters basic feed material and machinery data into the process, and the software predicts how the process will perform. The user can then determine the optimal process for each specific need.
As well as being responsible for assembling the new fully-electric and current Lokotrack plant ranges, Metso Outotec’s 900-plusemployee Tampere site remains the home of C Series jaw crusher and GP series cone crusher manufacturing. C Series plants are used in the primary crushing of excavated rock and ore. GP Series units are used in secondary, tertiary and fine crushing to manufacture rail ballast, cement and asphalt grades, and manufactured sand.
On our tour of the Lokotrack assembly lines led by manufacturing manager Annukka Tyynelä, Aggregates Business learnt how 60
The
years ago, in 1921
people are involved in the assembly of the 60-tonne-plus plants. Assembly is carried out on stationary workstations, with workers working a single 7- or 8-4pm shift, Monday to Friday. Lokotrack models assembled comprise the LT1110, LT220D, LT330D, LT120(E), LT130E, LT300HP, and LT300HPS. The lead time for these larger Lokotrack plants as of November 2022 was “weeks”.
Meanwhile, around 100 people are tasked with assembling the below-60-tonneclass Lokotrack plants. Most assembly line personnel work one of two shifts, with those working longer day shifts over a two-week period offered the Friday or evening shift off in the third week. The motor-line assembly employees work a single shift. Lokotrack
models assembled on this line are the LT96(S), LT106(S), LT116(S), LT1213(S), LT200HP, LT200HPS, LT200HPX, LT220GP, and LT7150. It takes around seven-to-eight days to assemble each below-60-tonne-class machine, with the lead time as of November 2022 as little as just one week.
There are 1300 to 1900 pieces on each Lokotrack, with bigger plants tested in a dedicated outside area within the Tampere facility. Each Lokotrack plant has a 2,000-hour/12-month warranty.
Metso Outotec Tampere’s solar-panelbased power plant has 777 panels on the rooftop of the Lokotrack assembly hall. The electricity production is 180MWh/ year, covering 10% of Lokotrack hall energy consumption. This year there is another solar-power plant being built on the rooftop of the main office building producing 103MWh/year and covering 25% of the office building’s energy consumption.
The Tampere facility is a ‘Tampere climate partner’: among Tampere regional businesses working with local authorities to deliver a greener environment for local communities.
A ‘Less Final Painting’ project means that new paint for the Tampere manufactured and assembled plants dries faster and at room temperature, making the painting more energy efficient. There is LED lighting in assembly halls, with lights and heating only on in the assembly areas where people are working. Diesel forklifts have been replaced by electric forklifts.
The Tampere site’s strong green credentials provide a fitting link back to the imminent launch of the first models in Metso Outotec’s new fully-electric Lokotrack range. “Why this focus on electrification? Sustainability is, of course, a key focus of many of our customers,” says Kimmo Vesamäki. “Customers already benefit from existing Lokotracks’ lower dust and noise generation, and this will continue with the new electric range. In certain countries, you need to use electric-powered plants to get certain contracts. Electric-powered plants are also important from a lower operational cost perspective. We see great industry opportunities for the new electric Lokotrack range.” AB
East Africa’s construction industry has been on a growth path in the last few years, triggering an increase in demand for construction materials, especially stone, sand and gravel and a review of industry regulations to ensure quality and safety. Shem Oirere reports
East Africa’s construction sector has been a longstanding success story. A report titled Opportunities in East Africa’s Construction Industries by Frost & Sullivan, a leading growth strategy consulting and research firm, projected the value of the region’s construction industry to expand by US$3bn between 2016 and 2021, driven largely by government initiatives, especially in Kenya, Uganda, Tanzania and Ethiopia.
The rapid growth did not stop in 2021. Ongoing huge demand for construction stone, sand and gravel is also great for the East African quarrying industry, as is the demand for production equipment and industrial explosives linked to mineral products processing.
With infrastructure projects, valued at an estimated US$61bn according to Deloitte Africa’s 2021 edition of the Africa Construction Trends report, the East Africa region, comprising countries such as Burundi, Comoros, Djibouti, Eritrea, Ethiopia, Kenya, Rwanda, Seychelles, Somalia, Tanzania and Uganda, is a key consumer of quarry products generated from rocks that are broken loose using industrial explosives.
A few major construction aggregateconsuming projects have recently been completed in the region, such as the US$9.8bn Kenya-Uganda-Rwanda-South Sudan rail project and the US$5bn Lamu project in Kenya.
But despite the increasing number of construction projects and corresponding changes in how they are researched, designed, and implemented, including deployment of information technology, little has been done in East Africa to amend regulations on the manufacture, transport, storage and use of construction raw materials, especially industrial explosives.
Some of the key projects in East Africa expected to boost consumption of construction aggregates include the US$10bn Bagamoyo mega port, the US$ 7.6 billion Tanzania-Rwanda-Burundi railway, the US$7.5bn Dar es Salaam-Mwanza standard-gauge railway, the US$3.6bn Stiegler’s Gorge/Rufiji hydropower project, the US$1.7bn Karuma hydropower plant, and the US$1.3bn Bugesera International Airport among others.
Quarry markets such as those in Kenya, Uganda, Rwanda and Tanzania, despite reporting huge strides in their economic and social developments, are still relying on old explosives regulations that are not in tandem with current construction industry trends in the region.
In Uganda, for example, the country’s Law Reform Commission says the landlocked country of 45 million people with a GDP of about
US$40.53bn, has experienced phenomenal economic and social growth changes, yet “there has been no major reform of the law (explosives Act) to respond to these changes.”
“The different amendments that have taken place have been piecemeal and minor, targeting specific provisions,” the Commission says in a report.
The Commission has been involved in the review of Uganda’s Explosives Act, Cap. 298, which deals with the manufacture, storage, sale, transportation, importation, exportation, and use of explosives in the country.
“The review was intended to update and modernise the Act particularly to ensure a balanced approach in managing the sifting of explosives, managing security risks while minimising the impact on business and supporting innovation and competitiveness,” the Commission said.
At the end of the review, the Commission submitted to Uganda’s Attorney General the report and draft bill for fine-tuning and subsequent submission to the national parliament for approval.
A road construction site in Uganda where a new regulatory regime on industrial explosives for quarries is expected soon. Pic: Uganda National Roads Authority (UNRA)
But by the end of 2021, Uganda’s Ministry of Internal
Affairs indicated the government was determined to “fast track the review of the Explosives Act”.
A review of Uganda’s Explosives Act is critical due to the country’s expanding mining and quarrying business.
For example, mining and quarrying registered a 15.8% growth in 2010/2011, according to the Commission. The sector has maintained a positive growth trajectory ever since, with the executive director of the Uganda Bureau of Statistics, Chris Mukiza, saying growth hit 17.1% in 2019/2020 before registering a decelerated growth of 14.5% in 2020/2021.
In spite of the mining and quarrying business’ positive performance over the years, the sector has become a point of reference on how not to do quarry business in Uganda.
structured development of quarries, particularly on a large scale or in a location that would necessitate an environmental impact assessment (EIA), can create detrimental impacts such as noise, vibration, dust, variation in the amount and quality of water, the lowering of the water table, and affect natural and cultural heritage, the landscape, traffic and waste materials.
The Commission’s report points out that quarry operations, although not specific to Uganda, “present social and health issues such as compensation and resettlement of persons and protection measures for workers.”
The Law Review Commission cites the example of Mukono district in Uganda, where local communities “have complained over damage to houses and crops resulting from quarry operations, others reported health concerns. Currently, there is no specific legislation regulating quarry operations or business.”
The situation leaves the quarry sector to self-regulate through the Uganda Quarry
Operators Association. At least 100 registered entities are engaged in the country’s stone quarrying business.
Although there is no report available on these companies’ compliance levels with existing industry regulations, the government of Uganda has provided various requirements to govern quarries’ operations, including the deployment of industrial explosives.
For example, the process of deploying explosives in Uganda’s quarries starts with the identification of a rock deposit of commercial quality and sufficient quantity suitable for the Ugandan construction market, according to Uganda Artisanal And Small-Scale Mining & Quarrying (UGASM-Q).
The prospective aggregate producer would then proceed to acquire from an individual or community the rock deposit “by negotiating a fair market value”.
Ideally, a formal transfer of ownership of the rock deposit is done, and a certificate of title is processed. This process is followed up by conducting an EIA of the proposed stone quarrying business on the surrounding area and communities in conjunction with a government official, according to UGASM-Q.
Once Uganda’s National Environment Management Authority (NEMA), a semiautonomous institution established in May 1995, approves the EIA and the applicant has paid the requisite fees, “the authority will issue an environmental permit detailing the scope of the quarrying operations and urging the holder to religiously abide by the terms and conditions contained therein.”
But the final greenlight for a prospective quarry owner to start blasting the rocks with explosives will be given by the General Security Officer at the Ministry of Internal affairs, “who will, in turn, visit the site with his committee on a fact-finding mission to establish the suitability of the location for conducting blasting operations.”
Once all approvals have been received, the new quarry operator enlists the services
of an explosives expert to assess the number of explosives required to conduct a blast at the site.
“All explosives used in commercial quarrying are interned at a military facility in Iganga in Eastern Uganda, where an agent of the company that is a paid-up member of the stone quarry association presents the proof of payment and a release order of the said materials, which are then released into the custody of Uganda Police personnel to escort to the blast site,” the current Explosives Act says in part.
Back at the blast site, it is required that the district security authorities are notified of the intended blast and the blast radius secured and evacuated before the blast can be conducted.
Once the blast is done, the blasted material forms the raw material that is fed into the stone-crushing machines to produce the machine-crushed aggregate in three or four principal sizes, according to the Uganda Law Review Commission report.
But because of the lack of any legal framework to govern the outlined practices in the mining and quarrying business, the industry “is vulnerable to unfair practices and abuse without any recourse to clear legal remedies.”
“In view of cross-cutting issues raised by quarry operations and the complaints that have been raised by the local population, it is important that regulations are put in place to regulate quarry operations and activities,” the Commission adds.
The Commission proposes a review of the current industrial explosives regulations with emphasis on environmental and health issues as well as those affecting the local population, such as pollution, and damage to property and crops.
Although nearly all entities involved in quarry operations in Uganda use explosives, “there is no specific legislation governing the
quarry business or operations in Uganda.”
The Explosives Act only makes provisions, restricting the use of blasting materials that are commonly used in quarry operations. “This has created a gap in regulation and left persons in the quarry business to selfregulation.”
Under the current Explosives Act, explosives have been categorised as either authorised or unauthorised.
The authorised explosives include ammunition of various kinds (cartridges), detonators, fireworks of various kinds, fuse igniters or tshisa sticks, gelatinous explosives, gunpowder, nitro-cotton, non-gelatinous explosives, percussion caps, safety fuse and sporting powder.
Furthermore, the Act says imported explosives that have already been approved for use in Great Britain, are deemed as having
been authorised in Uganda.
In Rwanda, the country’s Mines, Petroleum and Gas Board (RMB) put in place requirements to streamline the use of explosives in mines and quarries.
In 2021 the RMB published reviewed requirements for the issuance of a recommendation letter for granting authorisation to import, manufacture, transport, trade-in, and use dynamites in mining, quarry operations and other associated services.
“It has been observed that the demand
trend of use of explosives is increasing,” said Francis Gatare, RMB’s chief executive officer.
“So, it is imperative that the processes that govern their administration are also reviewed and improved accordingly,” he said at the time.
For quarry operators, the reviewed regulations have listed several documents required for the approval of the importation of explosives for quarry activities.
Although the RMB has outlined specific requirements for the importation, usage, storing, trading, and manufacturing of explosives for storage and use under the reviewed regulations, all applicants for approval to acquire and use explosives must have a local registration certificate, provide a detailed description of the type of explosive to be used and also proof of expertise in handling explosives.
Rwanda’s mining and quarrying sector has been on a growth path in the recent past, with the National Institute of Statistics saying the sector’s performance increased by an all-time high of 34.5% in the month of June 2020.
Overall, the Institute says mining and quarrying in the first half of 2022 grew by 12.1%, “mainly supported by increasing mineral prices on international markets.”
Elsewhere in Kenya, the quarry sector remains largely unstructured, hence making the implementation of any regulations, such as the use of explosives in blasting rocks, difficult to monitor.
Kenya has an Explosives Act in place to govern the manufacture of explosives,
storage, licensing of dealers, importation, exportation and use, as well as transport of the products and powers of licenced explosive inspectors, but the sector is largely unstructured.
A September 2020 report by Kenya’s Auditor General, Nancy Gathungu, says Kenya’s quarrying activities are largely uncontrolled and causing a “significant impact on the environment”.
“Blasting of rocks with explosives in order to extract materials for processing gives rise to noise and air pollution, damage biodiversity and habitat destruction,” she said in a report tabled in the Kenyan parliament.
Gathungu says there are huge gaps in Kenya’s legislation on the quarry business that has left the quarrying activities in the country unstructured.
For example, construction minerals such as stones, gravel and sand are not listed in the First Schedule of the Mineral Act 2016, hence making regulating the products difficult.
“Both the department of mining and NEMA (National Environmental Management Authority) do not have a well-defined structure with regard to the management of quarrying activities,” observed Gathungu.
“This may have attributed to haphazard and unsafe quarry operations since it is difficult to ensure compliance and enforcement of licence conditions,” she said. The licence condition includes compliance with the country’s Explosives Act.
In fact, Kenya’s key oversight agencies “have different roles and responsibilities with
regard to the quarrying sector management with the agencies generally operating independently without synergy.”
A survey by officials from the Auditor General’s office found “not all quarries in Kenya have obtained EIA licences due to low awareness of licensing, insufficient monitoring and evaluation, weak enforcement by NEMA, land ownership problems and the unregulated artisanal quarrying.”
Lack of EIA licences has resulted in the “proliferation of illegal quarries that pose danger to both human and animal lives, biodiversity loss, land degradation as well as the issuance of EIA licences to applicants who have not met all required conditions for a given (quarry) project.”
Kenya’s mining and quarrying industry has been growing in the last few years, with the Kenya National Bureau of Statistics indicating the value of the sector’s output increased by 5% in 2018/2019 year from KES 69bn (US$545mn) to KES 73bn (US$577mn).
A similar growth trend was recorded in 2019/2020 when the value of the sector’s total output increased by 6.8% from KES 73bn (US$577mn) to KES 78bn (US$ 617mn).
As an indication of the likely trend for the mining and quarry sector in East Africa, Uganda has recently proposed to the East Africa Legislative Assembly (EALA) member countries increased cooperation among the East Africa Community (EAC) to ensure proper and beneficial exploitation and use of the proceeds from the extraction of natural resources that exist within regions such as mining, quarrying, oil, and gas extraction and dredging industries.
This proposal is likely to trigger debate and possible agreement among the East African countries on harmonising their respective regulatory frameworks on quarrying, including the management of, and trade in, associated quarry-blasting chemicals. AB
The 6th edition of bauma Conexpo India (bC India) at the India Expo Centre in Greater Noida/ Delhi NCR (National Capital Region) attracted 41,108 visitors from 83 countries. As well as higher levels of business confidence shown by exhibitors, the event was characterised by a large-scale showcase of electric and diesel-electric hybrid solutions. Partha Pratim Basistha reports
India’s Union Minister for Road Transport & Highways, Nitin Gadkari, set the tone early at bC India 2023 (31st January – 3 February), when saying: “Electric, hybrid and bio fuel-compatible machinery holds the sizeable potential to reduce fossil fuel dependence by the Indian construction industry along with improving productivity and cost efficiency.”
Volvo Construction Equipment (Volvo CE) had on show its new EC 55 electric compact excavator, which will be on the market in early 2024. The company also displayed its EC 200D crawler excavator with a quick coupler, along with an HB 22 breaker.
Dimitrov Krishnan, MD, Volvo CE India, said: “The EC 55 electric compact excavator is a revolutionary product. This assures at least a 50% reduction in energy costs and over 30% savings in maintenance expenses. It opens up new opportunities for businesses to operate profitably in noise-sensitive areas, low-carbon zones and indoors.”
SDLG India exhibited its electric L956HEV wheeled loader. The machine comes with advanced shock-absorption technology, prolonging the life of lithium-ion batteries in the harshest applications.
SDLG's L956HEV electric wheeled loader was a popular show atrraction
SDLG India also displayed its E6135Fi hydraulic excavator and L933H wheeled loader. Surat Mehta, head of SDLG Business in India, said, “E6135i, a 13-ton excavator, is designed and built for heavy applications. It features a powerful four-cylinder DDE engine coupled with energy-saving, load-sensing
hydraulic system delivering best-in-class performance. A genuinely versatile and stable machine, it is suited for a variety of urban and rural work applications. Our L933H wheeled loader is a feature-packed machine, widely preferred at construction sites and aggregates plants and for bulk material-handling operations like RMC plants. It is powered by an advanced CEV-IV engine and a fully hydraulic load-sensing steering system offering remarkable levels of flexibility and ease of operation. The engine is fitted with a diagnostic interface which, along with the state-of-the-art instrument panel, ensures
smart checks and controls every stage of operations.”
LiuGong India exhibited its new batterypowered 5.8-ton 856H-E MAX wheeled loader.
Nischal Mehrotra, vice president (sales & marketing), LiuGong India, said: “The new loader delivers all the benefits of electric power and zero emissions, without sacrificing performance. The 856H-E MAX features lithium-ion battery technology and offers equal or greater performance than their diesel-powered equivalents. The battery systems deliver high energy density and long service life and do not require routine maintenance. The wheeled loader provides about eight hours of continuous runtime and requires just 70 minutes for a full charge.”
Mehrotra continued: “With zero emissions, the machine supports environmentally sensitive worksites and allows users to operate in areas where diesel exhaust is restricted. The wheeled loader’s electric power system contributes to an exceptional operator experience with drastically reduced noise and vibration, which both operators and job site bystanders will appreciate.”
Komatsu India showed its HB365LC-1 hybrid excavator. The subsidiary of the Japanese off-highway equipment giant said the machine is 20% more energy-efficient than its predecessor, helping to reduce carbon emissions. Komatsu India also displayed its PC 300 LC-8 hydraulic excavator fitted with a parallel cabin and orange peel grapple for scrap handling. “The demand for the product is expected to grow in India with the new automobile scrapping policy,” a subsidiary spokesperson told Aggregates Business International
Other Komatsu India products on display included the PC 210-10MO Super Long front, hydraulic excavator and the new PC 500LC10R hydraulic excavator developed for the mid-mining segment.
Tata Hitachi displayed its new five-ton indigenous wheeled loader, the ZW225, Shinrai PRO backhoe loader and new hydraulic EX 200 Infra hydraulic excavator, among other excavator models. Also on
display were the KDC 45 drum cutter, the Miller quick coupler, the Sandvik rock breaker BR 2577i, block-handling buckets, and the NX30 next-generation mini excavator with ConSite and Insite telematics solutions.
BKT launched its Earthmax Crusher Haul and Earthmax SR 34 off-the-road (OTR) tyres. The Earthmax Crusher Haul is designed for quarry and haulage applications. “The all-radial steel tyre comes with a block-type tread pattern that provides higher levels of traction. The special compound ensures cut, chip and wear resistance, guaranteeing durability and mileage. Designed for rigid dump trucks working in industrial and construction segments, the Earthmax Crusher Haul suits longer haul with heavier loads.” said Rajiv Poddar, BKT’s joint managing director.
Designed for wide-bodied mining trucks, the new Earthmax SR 34 is ideal for applications in heavy-duty conditions. According to Poddar: “The non-directional block tread design pattern provides advanced levels of traction and stability on any type of terrain. The strong all-steel casing features high resistance to snags and punctures.”
Sany Bharat displayed its new SY60C-
10, fully upgraded, new-generation, six-ton compact excavator. The machine is equipped with a fuel-efficient engine for maximum output. It also features keyless engine ignition, a touch display screen and a wide cabin. Sany also showcased its new SPARC series excavator with improved fuel efficiency and operator comfort. Deepak Garg, managing director of Sany Bharat & South Asia, said: “ Our new product range showcases our manufacturing capabilities and technological expertise. This will translate into enhanced productivity and profitability for our customers.”
In a bid to strengthen its presence in the construction and mining sectors, Daimler India Commercial Vehicles (DICV) exhibited its BharatBenz 3532 CM tipper truck, 2832 CM mining tipper truck and 5232 tip trailer. Rajaram K-Vice, Bharat Benz president of sales, marketing and customer service, said: “The new model range comes with a more powerful 320hp BSVI diesel powertrain providing high wheel-end torque to negotiate high-gradient mining roads. The trucks come with industry-leading body capacities, benefitting customers in the mining sector.”
The company also displayed its 48-ton RDT and 28-ton ready-mix concrete transit mixer with engine-driven power take-off solutions. Indian Crushing and screening equipment conglomerate Hailstone Innovations displayed its wheel-mounted 200 tph, four-stage crushing solution in a grizzlyjaw-cone-screen configuration. Equipped with Hailstone’s JC100 jaw crusher and HF220 cone crusher, the plant is suitable for crushing hard rock types such as granite and basalt.
Hailstone Innovations’ ‘Smart Impact’ series models include the vertical shaft impactor VSI EP7X187. The wheel-mounted
plant is also suitable for crushing hard rock types such as granite and basalt. The company also showcased its 650tph HTS 1860 4D four-deck tracked screen with a 6000x1800mm deck size.
JK Tyre launched three OTR tyres: the 26.5-25 Loader Champ 28PR E4/L4 TL, the 23X8.50-12 Jet Trax Ultima 6PR TL, and the 5.7-12 Jet Trax Super II 4PR TL. Anuj Kathuria, president of JK Tyre (India), said: “JK Tyre is at the helm of introducing several cutting-edge products. Our strong position in the OTR segment resonates with our commitment to innovation and making products that maximise performance and durability, even on the most challenging terrains. Our three new tyres in this category will be breakthrough products and will further strengthen our position in the OTR segment.”
Srinivasu Allaphan, JK Tyre director of sales & marketing, added: “The tyres are manufactured with a new age silicabased tread compound that provides better resistance to wear and tear. The tyres also feature a robust wide wall and rim guard design which provides additional resistance to external damage and greater protection against damages in the side wall and rim flange area. The specially designed stepped lugs provide excellent self-cleaning advantages.”
Schwing Stetter India exhibited a range of new products designed to cater to new application areas, including challenging conditions. V.G. Sakthikumar, the company’s managing director, said: “Our new products are based on our understanding of the pain points of customers. Based on the same, we have designed solutions that enable higher productivity deliverance. For instance, we have come up with a completely new self-loading concrete mixer that has an air-conditioned cabin, better visibility, and railing and hand bars for ease of climbing, besides a brand-new variant of our trailermounted concrete boom pump. We have made a product that goes beyond processing concrete to make a plug-and-play modular machine that will reduce temperatures.
“With large numbers of irrigation projects in the pipeline in India, we have come up with a robust yet lightweight canal paving machine. It has undergone rigorous field tests, and customers have given positive feedback as regards its performance.”
Schwing Stetter has, for the first time in India, come out with a conveyor for river dam construction. The product has been made following the acquisition of US-based company Loopbelt. “We have taken the technology from the company to make the product in India. This conveyor can be used to move concrete that is difficult to pump, and also to move sand and aggregates. This is a foldable machine, and being locally made, it comes at a significant lower cost,” said Sakthikumar.
Schwing Stetter also exhibited its 21-ton 215XCMG excavator beside its 25-ton excavators, 60-ton truck cranes, 100-ton
crawler cranes, piling rigs, motor graders, smaller mini excavators, and aerial work platforms. “With the addition of a new dry mortar plant, the company has established its brand as a complete solution provider for mortaring and concreting,” added Sakthikumar.
He continued: “Our strategy is to migrate beyond concreting. We have attained a 6% [Indian] market share in excavators in the third year of our operations, despite the presence of more established players. We have a sizeable market share in self-loading concrete mixers by producing 100 units per month. We are now coming up with a 38-ton excavator. We are also doing well in cranes and piling rigs.”
Having launched itself into the Indian market in 2012, MB Crusher used bC India 2023 as a platform from which to announce its long-term investment plans in the country.
Piero Guizzetti, the Italian manufacturer’s CEO, said: “India was always amongst our important markets, and we have now drawn up long-term investment plans for the country.
“With our bucket crushing and screening attachments, fixed with any class and model of backhoe loaders, contractors can earn high profits by doing in-situ crushing. We are placing ourselves as the most reliable primary crushing solution provider.”
MB Crusher offers a wide range of solutions for every material crushing and screening need. The firm offers screening buckets both for excavators and backhoes with its MB-S attachments line.
Guizzetti added: “We have positioned the screening bucket as an attachment for many applications, such as road construction, quarrying and mining, C&D waste, and piping. This attachment is provided with a mesh that can be changed as per the requirement. The machine is low and quick maintenance that can be carried out at the job site, and can work underwater in riverbed applications for washing residual materials.”
suitable for internal roads, onsite mixes and mountainous terrain for road contractors constructing rural roads, culverts, etc.”
MB Crusher offers crushing attachments for backhoe loaders, wheeled loaders, and skid steer loaders under its MB-L bucket crusher series. For excavators, the company is offering eight models under its BF mobile jaw crusher line of attachments which are suitable for all seven 100-ton class excavators. “Our attachments are fully compatible for working in any hydraulic driven machine with the given hydraulic oil flow,” added Guizzetti.
Armix India displayed its self-loading, concrete mobile transit mixers, planetary mixers, block-making machines and hydraulic wet press machines designed to deliver higher quality and productivity with a lower operational cost.
Manoj Kumar, managing director of Armix Construction Machinery, said: “Our two- and four-cubic-metre self-loading transit mixers are made as per Italian design standards and manufactured at our Bangalore facility. Their compact footprint enables efficient working on shorter radii, making them highly
He added: “The user-friendly product comes with an advanced spiral drum design for complete discharge of concrete, and without leaving any residual materials. Faster discharge of the concrete is through special design and powerful motors and other accessories related to it. The advanced design of the drum and the positioning of the axles are very important and guided by certain design parameters to provide the required stability to the machine.”
The Armix planetary mixers are based on a German and Italian concept design applicable for ready-mix concrete, precast, blocks, bricks and paver production as well as pipe and allied products. Specially designed motors and gearboxes from international brands ensure the homogenous concrete necessary for each application. The proven liner plates help prolong wear parts longevity, while simultaneously reducing maintenance needs and customer costs. The provision to reverse the liner plates and multiple door and moisture probe options are a very novel feature in this segment.
Kumar continued: “One of the key competitive features of our mixer (not provided by any other manufacturer) is the provision for sampling while the machine
is working. There is also a unique water spraying arrangement through a spiral system instead of the small holes which normally used. Armix makes planetary mixers between 375, 500, 750, 1500 and higher capacities up to 3,000 litres. These mixers are being exported to global markets on a regular basis.” Gujarat, western India-based crushing and screening components manufacturer Electromagnetic Industries serves the requirements of major crushing OEMs including Sandvik and Metso Outotec. The company is bullish about its 2023 business prospects due to large-scale quarrying activities supplying contractors involved in India’s increased road infrastructure works.
Electromagnetic Industries’ product line includes vibratory screens, circular vibratory screens, vibratory conveyors, vibrating grizzly feeders, and vibratory motors.
Speaking at bC India 2023, R.B. Patel, Electromagnetic Industries’ managing director, said: “While we are stepping up our production at our existing Por facility and also at the new facility, we are undertaking higher levels of value-added product customisation. This is through improved design, based on the specifications of the clients, improved quality of raw materials and superior levels of fabrication. This is essential to reduce the wear and tear of the materials while ensuring higher levels of performance.” AB
The Lintec CSM4000HRC containerised asphalt batch plant, operated by Lu An Highway Industry in China, has mixed more than two million tonnes of hot mix asphalt with a high percentage of reclaimed asphalt pavement (RAP).
After reaching this milestone, it has now finished supporting construction of the S244 regional expressway and other rehabilitation projects in China’s Anhui province.
The installation process began in February 2016 on a site in Lu’An city. The plant began
operations the following June, providing hot mix asphalt for the 23.04km Huoqiu Garden to Xuji interchange section of the S244. The plant produced approximately 150,000tonnes for the 03 section of the highway, after which the project was completed in 2022.
Having concluded work on the expressway, the equipment has since been used to carry out asphalt pavement repair and maintenance projects on other expressways in Anhui province.
To date, total production for the plant has now passed the
2-million-tonne mark. Thanks to the HRC component in the CSM4000HRC asphalt plant, 40% of the hot mix asphalt was from RAP, making it a more environment-friendly choice.
The Lintec CSM4000 asphalt mixing plant with a 320-tph capacity paired with the HRC hot recycling system yielded efficient integration of RAP with exceptional productivity. The HRC attachment is able to be retrofitted into any Lintec asphalt plant for the processing of milling waste or material excavated from road pavement recycling. This
will then result in a significant contribution to the conservation of natural resources while massively reducing the transport and production costs of bitumen and aggregates.
“Over the years, the superb output and quality of our Lintec CSM4000 has been greatly supported by the hot recycling system. It has given us huge cost savings while ensuring mix quality remains at the highest level – all while being extremely simple to operate,” said a spokesperson from Lu An Highway Industry. https://lintec-linnhoff.com/
Conveyor belt cleaning accessories provider Martin Engineering has introduced a direct retrofit replacement for the Richwood 1C & 1C-ITC cleaners, designed to provide superior construction at a lower cost.
The company says it is providing operators who use the 1C & 1C-ITC cleaners with a better performing product that lasts two times longer than the original. Engineered to fit existing assemblies and tensioners, operators will experience a seamless transition , with a money back guarantee. Along with highquality construction to improve performance and extend the equipment life, the replacement cleaners lower the cost of operation.
“Some operators prefer a flat-tip blade and pressure tensioner configuration of the Richwood,” said Dave Mueller, conveyor products manager at Martin Engineering. “To accommodate this preference, we designed a replacement blade system that fits existing assemblies but lives up to Martin Engineering’s quality specifications. Since we formulate high-quality materials for all of our blades in-house, we adapted those materials for this blade construction. This approach improved the overall quality of the replacement blade and lowered the cost of construction, benefits that
are passed on to the customer.”
The flat-topped rectangular primary cleaner blade has painted steel side plates and end castings. Mounted beneath the head pulley, the pressure tensioner holds the blade firmly. This positioning offers the proper resistance to put pressure on the belt for clearing adhered material from the surface while reacting to fluctuations in the belt and gliding smoothly over splices. When the top side of the cleaner is worn unevenly or displays a degradation in performance, the blade can be flipped to extend its equipment life.
Primary blades are available in lengths of 24 inches (610 mm) to 72 inches (1829 mm) to accommodate most standard belt widths found in underground and above-ground bulkhandling applications. With nine dimension options to choose from, blades fit the needs of most standard conveyors.
The secondary blade is positioned behind the primary cleaner to clear adhered dust and fines that may have been missed. Constructed of a metal-tipped blade with painted steel side
plates and end castings, it glides smoothly with vertical variations in the belt. The downward weight of the belt and the upward action of the tensioner provides enough pressure to clean any leftover carryback.
Martin Engineering adds that “Richwood” is a registered trademark of Richwood Industries, Inc., Huntington, WV. Martin Engineering is not affiliated with or authorised by Richwood Industries.
https://www.martin-eng.com/
Command Alkon launches mobile app for accurate materials tracking Software and solutions provider Command Alkon is introducing a “Customer Portal” mobile application that is designed to provide visibility in the construction materials delivery cycle. Command Alkon says Customer Portal allows materials buyers to streamline their operations. The new package delivers instant, reliable data sharing and will help materials buyers create, manage, and track orders 24 hours a day.
The new app is fully integrated with the company’s COMMANDbatch, TrackIt, and Command Alkon Dispatch systems, which are called COMMANDseries, Integra, and Dispatch. The manufacturer says that the new app can also integrate with other third-party systems through open APIs.
“If materials are late, it creates a ripple effect that affects every single jobsite activity and significantly adds to project costs; the value of Customer Portal is that it answers the question ‘where’s my truck?’” said Ranjeev Teelock, chief product officer at Command Alkon.
“Ticket data shared through Customer Portal informs buyers of when the driver picks up the materials and the exact quantities that are on the way to the job. Sharing order information with customers gives them the insight that they need to improve planning and utilisation and can dramatically cut down on unnecessary phone calls – by as much as 30%.” Sharing truck locations and ETAs provides visibility from dispatch to delivery and gives customers confidence and trust in knowing where orders are and when they will arrive, says Command Alkon.
“Field personnel can monitor inbound movement of supplies so that they don’t stack up at the gate and instead can flow easily in and out of the jobsite,” said Deepa Vangimalla, senior product owner at Command Alkon. https://commandalkon.com/
Keestrack is launching a new B7H heavy-duty hydraulic jaw crusher, specially designed for the US market and the toughest of rock conditions in quarrying and mining applications.
The 70-tonne B7H hydraulic jaw crusher has a 30-tonne jaw and is adapted from Keestrack’s existing B7 electric jaw crusher which was launched in 2018. It has a vibrating feeder with 2-step grizzly of 2,200mm x 1,080mm (LxW) and a bottom deck in wire mesh of 1,450mm x 870mm (LxW) to optimise crushing results and to reduce wear.
The feed size of the material is up to 700mm, the feed opening is 1,200mm x 830mm and the outlet adjustment CSS is min.-max. 75mm–250mm.
The jaw crusher is equipped with the patented NSS, non-stop system, which protects the crusher from uncrushable feed and resets the CSS auto-
matic during operations.
Keestrack sales director Frederik Hoogendoorn says the mobile crushing and screening equipment company is a pioneer in electric quarrying and mining machinery, having launched its first electric machine in 2006.
He adds that 90% of Keestrack machines are available in three versions: hydraulic, electric, and zero-emissions plug-in.
“A focus on sustainability is at the core of our company as this is the origin of our business,” Hoogendoorn said.
“Producing and recycling valuable raw materials is what mobile crushing and screening is all about, and our efforts are definitely having a positive impact on the ecological footprint.”
https://keestrack.com
Kleemann says its feed control CFS (continuous feed system) optimises the crushing process of the Kleemann plant automatically so that material is always conveyed with maximum efficiency through the machines.
At the same time, the manufacturer says the filling level of the plant’s crushing chamber is monitored. If the filling level reaches a height that can be defined in advance, the material feed of the machine is adjusted accordingly.
For automatic optimisation of the crushing process between crushing plants and to achieve maximum utilisation of the plant train, Kleemann plants are simply linked with one another via intelligent line coupling. The safety coupling has now been extended by a wireless version. Wireless line coupling is easier to handle and makes the typical workday of the operator easier.
CFS forms the perfect basis for the intelligent line coupling of an interlinked plant train: The optionally available probes at the crusher discharge conveyor and/or fine grain conveyor of the upstream machine monitor the previously defined filling level of the respective upstream machine. When the desired filling level is reached, the production output of the upstream machine is reduced temporarily. This prevents overloads, reduces the wear on
the plants and results in higher availability and output.
In an emergency, it is sufficient to press any emergency stop on the plant train – and all machines stop. This is guaranteed by the safety coupling of the plants, which now not only has a connection via cables but has also been extended by coupling technology via a radio system. https://www.wirtgengroup.com/en-gb/company/ kleemann/
MAY
02-04: UK Construction Week
London
ExCeL, London
Organiser: Media 10 Ltd
Tel: +44 (0) 20 3225 5200 https://www.ukconstructionweek. com/
03-07: SaMoTer 2023
Verona, Italy
Organiser: Veronafiere S.p.A. Tel: +39 045 8298561
Email: customercare@samoter.com www.samoter.it/en
JUNE
06-08: APEX 2023
Maastricht MECC, The Netherlands
Organiser: Industrial Promotions
International Tel : +44 (0) 7821 655 244
Email: max.hollick@khl.com https://apexshow.com/
13-15: Plantworx 2023
Peterborough, UK
Organiser: CEA
Tel: +44 (0) 208 253 4517 https://plantworx.co.uk
AUGUST
23-26: steinexpo 2023
Homberg/Nieder-Ofleiden, Germany
Organiser: Geoplan GMBH
Tel: +49 7229 606 30
Email: info@geoplangmbh.de https://www.steinexpo.eu/
20-23: BICES 2023
Beijing, China
Organiser: AEM
Tel: +86 (10) 67870972
Email: bob.ban@e-bices.org http://www.e-bices.org/engdefault. aspx
OCTOBER
04-06 SIM 2023
Bordeaux, France
Organisers: Exosition SIM https://www.expositionsim.com/ en/index.htm
24-27 INTERMAT Paris 2024 Paris, France
Organiser: Comexposium
Email: laura.sanchez@ comexposium.com https://paris-en. intermatconstruction.com/
25-27 Hillhead 2024 Hillhead Quarry Buxton UK Organiser: QMJ +44 (0) 115 945 4367
Email: hillhead@qmj.co.uk www.hillhead.com/
These dates were correct at the time of going to press, but please note that the COVID-19 pandemic means some events may be rescheduled with little advance notice
Ammann IFC www.ammann.com
BKT p30 www.bkt-tires.com
Indeco p25 www.indeco.it
Outset p26 www.outset.it
Terex Washing Systems p11 www.terexwashing.com Wirtgen OBC www.kleemann.info
MOBIREX MR 130 PRO
PERFORMANCE, PRECISION AND SUSTAINABILITY. The MOBIREX MR 130 PRO mobile impact crusher excels with outstanding performance in a diverse range of applications. With its double-deck post screening unit, the plant ensures top product quality with up to two graded end-products, while achieving impressive throughput rates of up to 600 t/h in natural stone and recycling. The all-electric E-DRIVE is not only efficient, it can also be operated with zero local emissions. Operation is intuitive thanks to SPECTIVE components. The MOBIREX MR 130 PRO – the sustainable powerhouse.
www.kleemann.info