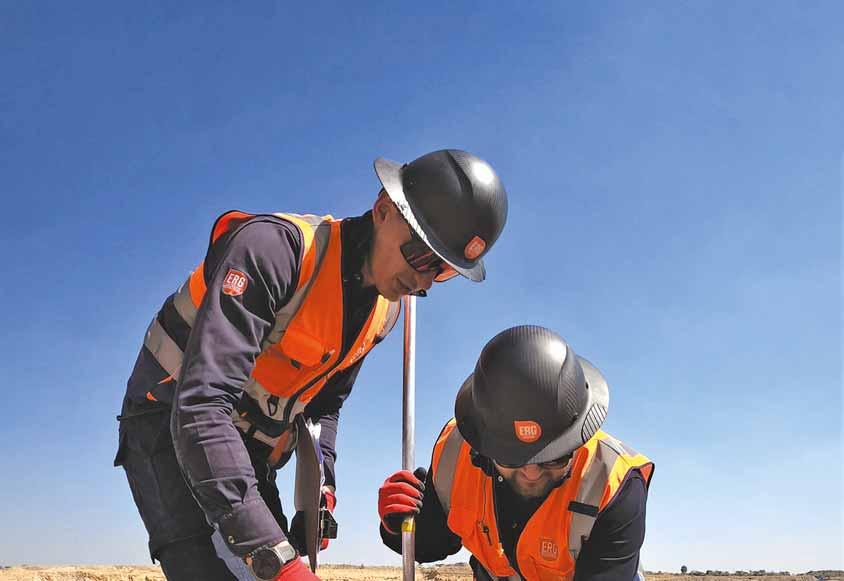



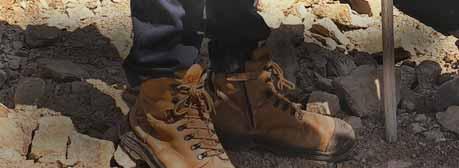
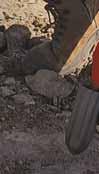
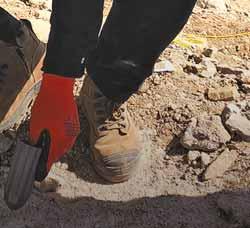



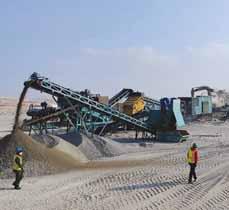
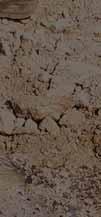




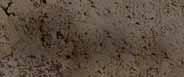
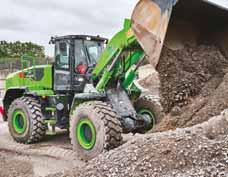

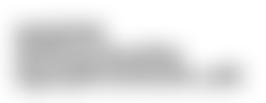

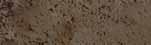
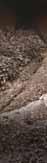
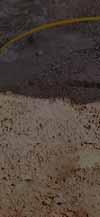
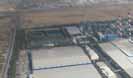
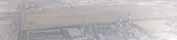

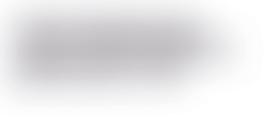


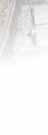

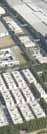

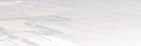

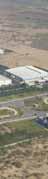



MOBISCREEN MSS 802 EVO
IMPRESSIVE FROM A TO Z. Thanks to its robust design and extensive range of screen linings, the MSS 802 EVO can easily adapt to changing locations and new operating conditions – making it ideal for a wide variety of applications. The coarse screening plant features an intuitive system control that reduces the risk of operating error. And all relevant functions can be operated from a safe distance for increased work safety. The MOBISCREEN MSS 802 EVO –the heavy-duty, versatile solution in natural stone and recycling.
www.wirtgen-group.com/kleemann
05 COMMENT
Middle East eyes on the C&D waste-reuse prize
06 NEWS
Cemex opens C&D waste facility in Israel; Sustainability & early success at new Ammann factory in China; XCMG sees big rise in overseas revenues
50 EVENTS
All the key events in the quarrying & aggregates world Features 28 CRUSHING & SCREENING
New international players target impact in crushing and screening
32 LOADING
A lot of headline-grabbing loading-unit news makes for a vibrant sector of the quarryingequipment machine market
35 HAULING
Driverless hauling passes its exhibition close-up
37
Indeco’s growing attachment to the new marketplace; Epiroc’s a prized Czech mate
41 TYRE TECHNOLOGY
Fresh strategic investment powers BKT’s growth vision
44 WATER RECYCLING, FILTRATION & MANAGEMENT
Showcasing the fully automated soil- and water-treatment plant
48 BLASTING & ALTERNATIVES
Impressive new ways to optimise your quarrying blasts
Eugene Preis (right), with Reinhardt Steyn, operations director of ERG Industrial, working at a customer site
HEAD OFFICE
EDITOR: Guy Woodford
ASSISTANT EDITOR: Liam McLoughlin
CONTRIBUTING
EDITORS: Munesu Shoko, V.l. Srinivasan, Shem Oirere, Partha Basistha, Eugene Gerden, Shadrack Kavilu
EQUIPMENT EDITOR: Mike Woof
DESIGNERS: Simon Ward, Andy Taylder
PRODUCTION MANAGER: Nick Bond
OFFICE MANAGER: Kelly Thompson
INTERNET, IT & DATA SERVICES DIRECTOR: James Howard
WEB MANAGER: Sarah Biswell
SOCIAL MEDIA MANAGER: Tatyana Mechkarova
MANAGING DIRECTOR: Andrew Barriball
PUBLISHER: Geoff Hadwick
CHAIRMAN: Roger Adshead
ADDRESS
Route One Publishing Ltd,
Second Floor, West Hill House, West Hill, Dartford, Kent, DA1 2EU, UK
TEL: +44 (0) 1322 612055 FAX: +44 (0) 1322 788063
EMAIL: [initialsurname]@ropl.com (gwoodford@ropl.com)
ADVERTISEMENT SALES
SALES DIRECTOR:
Philip Woodgate TEL: +44 (0) 1322 612067
EMAIL: pwoodgate@ropl.com
Dan Emmerson TEL: +44 (0) 1322 612068
EMAIL: demmerson@ropl.com
Graeme McQueen TEL: +44 (0) 1322 612069
EMAIL: gmcqueen@ropl.com
SUBSCRIPTION / READER ENQUIRY SERVICE
Aggregates Business is available on subscription at the rate of: £85 / US$145 / €111 per annum. Single copies £20 / US$35 / €26 Email subs@ropl.com for further details. Subscription records are maintained at Route One Publishing Ltd.
SUBSCRIPTION / READER ENQUIRIES TO:
Data, Route One Publishing Ltd, Waterbridge Court, 50 Spital Street, Dartford, Kent DA1 2DT, UK
TEL: +44 (0) 1322 612061 FAX: +44 (0) 1322 788063
EMAIL: data@ropl.com
No part of this publication may be reproduced in any form whatsoever without the express written permission of the publisher. Contributors are encouraged to express their personal and professional opinions in this publication, and accordingly views expressed herein are not necessarily the views of Route One Publishing Ltd. From time to time statements and claims are made by the manufacturers and their representatives in respect of their products and services. Whilst reasonable steps are taken to check their accuracy at the time of going to press, the publisher cannot be held liable for their validity and accuracy.
PUBLISHED BY © Route One Publishing Ltd 2023
AGGREGATES BUSINESS USPS: is published six times a year. Airfreight and mailing in the USA by agent named World Container Inc, 150-15, 183rd Street, Jamaica, NY 11413, USA.
PERIODICALS POSTAGE PAID AT BROOKLYN, NY 11256
US POSTMASTER: Send address changes to Aggregates Business, World Container Inc, 150-15, 183rd Street, Jamaica, NY 11413, USA.
Air Business Ltd is acting as our mailing agent
PRINT: ISSN 2051-5766
ONLINE: ISSN 2057-3405
PRINTED BY: Warners (Midlands) PLC
This magazine was delighted to report earlier this year on how the Middle East has seen a resurgence in postCOVID-19 construction activity, particularly in the Gulf Cooperation Council (GCC) region, partly due to high oil prices. What has until now been less covered by the world’s building-materials-industry trade media has been the fact that due to the region’s high price of premium building materials, the sheer volume of construction activity, and environmental sustainability concerns, Middle East developers are increasingly using recycled aggregates from construction and demolition (C&D) waste.
Countries including Saudi Arabia, the United Arab Emirates, Qatar, Kuwait and Egypt, a country linking northeast Africa with the Middle East, are benefiting from a notable increase in the deployment of C&D waste in new major construction works. Indeed, governments such as the UAE, Saudi Arabia and Qatar have enacted legislation allowing construction firms to use a minimum of 20% to 40% of the recycled aggregates in their infrastructure works, including new commercial and residential builds.
It has been a remarkably quick turnaround in building works’ best practice, given that until the last couple of years, most C&D waste generated by infrastructure building works in the Middle East was dumped in landfills.
In this edition of ABI, contributing editor V L Srinivasan examines the Middle East construction industry’s comprehensive embrace of C&D waste in new building projects.
As Srinivasan notes, not only is the growing availability of recycled aggregates providing much-needed relief for bottom-line-minded project managers, but the greater use of recycled aggregates reduces a project’s carbon emissions and developers’ reliance on imported building materials.
He cites the study, Securing Valuable Resources for a Sustainable Future, by Boston Consulting Group, which states that GCC countries are generating between 105 and 130
million tonnes of waste per annum, primarily from C&D waste, municipal solid waste (MSW), and agricultural waste, with Saudi Arabia and the UAE accounting for around 75% of it. The Boston Consulting Group says GCC countries are trying to build their reuse of C&D waste in building works while trying to overcome the not-insignificant challenges posed by limited C&D and agricultural waste tracking and illegal waste dumping.
Among many senior executives Srinivasan spoke to in compiling his excellent feature was Salman Zafar, an expert in waste management and founder of EcoMENA, a volunteer-driven initiative creating environmental awareness and fostering sustainability worldwide, particularly in the MENA (Middle East - North Africa) region. He made a critical point when highlighting how recycling C&D waste can expand the lifespan of landfills and help reduce the cost associated with maintaining and building new ones.
Zafar said that recycling also helps conserve natural resources and diverts construction waste from landfills, which can generate a substantial volume of harmful odours and gases. This shows how the greater use of C&D waste in new building works can be as much of a public health win as it is for Middle East building materials sustainability and the regional construction sector’s circular economy.
Elsewhere in this issue, another of our contributing editors, Munesu Shoko, sits down with the multi-talented and personable Eugene Preis, co-founder and managing director of South Africa-based mining and blasting company ERG Industrial.
Formed just four years ago, ERG Industrial is a global consumables supplier to the mining, quarrying, civil and construction industries, with a portfolio of products focused on maximising value and return on investment for its customers. Preis explains how he and co-founder and operations director Reinhardt Steyn take a hands-on approach to the business, deploying various high-end technologies during testing and implementation. GW
Cemex has inaugurated its new construction, demolition, and excavation waste-recycling facility in Tel Aviv, Israel. To mark the commencement of operations at the facility, the site was visited by a group of senior representatives from the Cemex EMEA (Europe, Middle East, Africa & Asia) management team.
This site will play an important role in the growth of Cemex’s circularity efforts under the banner of its new Regenera business. It will eventually receive up to 500,000 tonnes of building waste per year. Where appropriate, this material will then be processed and used in recycled building materials.
The main material suppliers for this location are anticipated
to be companies engaged in demolishing existing buildings and companies that transport construction waste. Customers for recycled materials in Israel include concrete companies, flooring contractors and infrastructure companies. The facility
HOFFMANN GREEN SIGNS FIRST SAUDI
Hoffmann Green Cement Technologies (Hoffmann Green) and the Shurfah Group have signed a 22-year exclusive licensing agreement to build several Hoffmann Green production units in Saudi Arabia. The landmark agreement will support the decarbonisation of the construction sector in the country.
The first clinker-free Hoffmann Green cement plant will be built in 2024, and it will be a replica of H2. The engineering and production process will be carried out by IBAU Hamburg, the German general contractor with whom, as a reminder, Hoffmann Green signed an exclusive partnership agreement in June 2022 to support the construction of Hoffmann units worldwide. This and all subsequent vertical units will be built entirely with Hoffmann Green cement.
was acquired earlier this year as part of Cemex’s purchase of a 51% stake in Israel-based SHTANG Recycle.
Sergio Menéndez, president of Cemex EMEA, said: “This new facility in Tel Aviv marks a significant milestone in Cemex’s
commitment to circularity, which is of such importance to our global ambition of reaching net zero by 2050. I thoroughly enjoyed visiting our Israeli operation and opening the plant. I was inspired by the passion of my local colleagues for innovation and collaboration in pursuit of a better future.”
Regenera provides sustainable solutions for three major waste streams: municipal and industrial waste, construction, demolition, and excavation waste (CDEW), and industrial byproducts. Regenera is present in all of Cemex’s regions of operation: Mexico; the US; Europe; the Middle East and Asia; and South-Central America and the Caribbean.
Ammann’s new factory in China is hailed as a major turning point in the company’s growth plans for Asia – and a major win for sustainability in China.
The Zhangjiagang, Jiangsu province-based factory will manufacture asphalt-mixing plants and parts for China and beyond.
“The design of the new (manufacturing) plant adheres to the Swiss concept of environmental respect, i.e., reducing energy consumption, plant emissions, and its impact on the environment,” said Zhang Liguang, general manager of Ammann China.
The factory’s final products – the asphalt plants themselves – will adhere to tight Swiss sustainability standards. That includes Ammann’s global
Green Plant initiative, which promotes sustainable technologies, innovative solutions, and environmentally friendly asphalt-mixing practices.
50,000m², with 5,000m² dedi-
produce 80-100 asphalt-mixing plants annually. Additionally, the factory will produce spare parts
The new Ammann factory’s location in the Yangtze River Delta region will be crucial to
the factory site was chosen to reduce shipping costs, improve travel distances for importing finished plants, quickening delivery times, and increasing access to strategic markets throughout China and the AsiaPacific region.
Ammann entered the Chinese market in 1997. It
opened a Beijing office in 2000.
The growth spurred the development of the Shanghai factory, which began manufacturing asphalt-mixing plants in 2005. It has built 500 plants since opening and will continue to operate.
“The opening of the new factory continues the firm investments made by Ammann in the Chinese market for many years,” said Hans-Christian Schneider, CEO of Ammann Group, in a speech at the factory’s opening ceremony. “I would like to thank all the governmental authorities who have helped us with the new plant project, our partners who have worked so hard together, and the Ammann China team who have worked so hard to make this happen.”
IQ Malaysia has won the Caernarfon Award for the mineral products industry, receiving the accolade for the first time.
Since 1989, the international honour has been presented annually to a member of the UK-headquartered Institute of Quarrying (IQ) anywhere in the world who has made a significant contribution to the advancement of the science and practice of the mineral products sector.
The international presidents of the IQ have revealed the winner and runners-up of the 2023 Caernarfon Award.
The presentation by Zeems Foo Kheng Sin FIQ - Quarrying in the Era of Environmental, Social, and Governance (ESG)impressed the international IQ presidents. Delivered at the IQ Malaysia conference in October 2022, his paper showcased
the Environmental, Safety and Productivity (ESP) Quarrying Best Practices model. It highlighted the positive impact on the environment and co-existence between the local community and quarrying.
Ultimately, the ESP model will likely lead to the rebranding
of the Malaysian Quarry Industry, which aims to transform the traditional ‘quarryman’ from a 3D (Dirty, Dangerous and Difficult) job to highlighting it as a professional career in Malaysia.
Nirmala Devi is the manager of the Institute of Quarrying Malaysia (IQM). He says: “Zeems
was initially nominated due to the quality of his presentation, which gave insight into how local communities perceive quarrying and how the relationship has improved over the years. IQM is beyond proud of Zeems for being recognised as this year’s Caernarfon Award winner, a first in history for an IQM member.”
IQ International presidents’ chair Viv Russell said: “We received an exceptional number of high-level entries to this year’s Caernarfon Award. It is a great reflection on how our international network of IQ organisations continues to deliver high-quality, informative and educational sessions for their members. On behalf of the IQ network, I congratulate our winner, Zeems Foo Kheng Sin, and each of our highly commended runners-up.”
Chinese off-highway machinery major XCMG saw a 33.5% year-onyear increase in overseas sales revenue in the first half of 2023 to 20.9 billion yuan (US$2.85bn). Total sales revenue for the halfyear was worth 51.28bn yuan (US$6.98bn).
Sales of energy products in H1 2023 were worth 5.27bn yuan (US$717.56mn), a 174.9% growth year-on-year. Meanwhile, the market share of XCMG’s major products has increased by 1.93% yearon-year, says the company.
Domestically, XCMG claims it now sells more milling machines and asphalt-mixing stations than its Chinese peers.
XCMG’s first-half-year gross profit margin of 22.86% has increased by 2.44% year-onyear; the net profit margin on sales reached 7%, up 0.19% year-on-year, with the Q2 2023 performance reaching 7.54%, a 1.77% increase year-on-year.
“XCMG has been advancing steadily to achieve a resilient, high-quality development. In the context of a complex and fast-changing market environ-
regions worldwide, providing not only “advanced and endurable” products, but also integrated services and spare parts support.
XCMG’s overseas revenue of US$2.85bn in H1 2023 accounted for 40.75% of total company revenue, an 11.08% increase year-on-year, with multiple regions and products achieving rapid growth.
new ideas, new concepts, and new mechanisms – is pushing forward the intelligent and digital transformation following the five strategies of ‘high-end, intelligent, green, service-oriented, and globalisation,’” said Yang Dongsheng, CEO of XCMG.
XCMG has established a ‘four-in-one’ international development model of product export, overseas factories, cross-border mergers and acquisitions, and globally collaborative R&D. XCMG now exports to more than 190 countries and
Company revenue in West Asia, North Africa, and Central America has risen by over 200%, sales in Europe are up 150%, and around 100% revenue growth was achieved in Central Asia and North America.
XCMG has opened sales companies in Great Britain, Singapore, Saudi Arabia, the United Arab Emirates, and Vietnam, with more production bases, R&D facilities, and spare parts centres under construction and planning.
“XCMG is navigating through the industry cycles with innovation and internationalisation as the core focuses; it’s our goal to build a world-class enterprise with leading advantages in products, scale, services, digital and intelligent technologies to achieve strategic transformation and continuous breakthroughs,” said Yang.
Founded by three partners in July 2019, ERG Industrial has changed the face of blasting, a critical parameter in the quarrying and mining value chain. As with all other successful businesses, the young business was founded on the back of several failed ventures, recalls Eugene Preis, who says that the knowledge acquired through failure facilitated successful entrepreneurial re-emergence for the three ERG partners.
When establishing the business, the three partners – two mining engineers and one civil engineer – were driven by their desire to help mines and quarries optimise their drill and blast practices. Why blasting? “As the very first process in the mining value chain, blasting has a significant bearing on the performance of all other downstream processes,” explains Preis. “By making a small change in outcomes at the beginning of the value chain, operations can see exponential gains downstream.”
From a macro perspective, he adds that if all mines and quarries could improve their blast outcomes by 5%, for instance, there would be an incredible knock-on effect on their bottom line and the industry’s contribution to the global economy. He says this was one of the founding reasons behind ERG Industrial – to help the industry improve its fortunes through blast optimisation.
After identifying drill and blast as their preferred area of the mining value chain, the three partners further narrowed it down to stemming – an important parameter in good blast outcomes. As a result of their market research, they stumbled upon the Varistem stemming plug, designed and manufactured by a United States-based company, MOCAP. Following discussions with the company, ERG Industrial was initially awarded the distribution rights to the Varistem plug for the African territory.
“We identified stemming as a crucial area of focus for our business,” says Preis. “During blasting, stemming plays a key role in confining the explosives and effectively utilising blasting energy. Typically, the loss of explosive energy through stemming ejection reduces the performance of the blast. Therefore, the core principle behind stemming plugs is to improve the effectiveness of stemming material in the blasthole. As a result, this helps better contain the explosives’ energy within the rock mass and yield a more controlled and efficient blast.”
Bringing the Varistem plug to market, however, was not without its challenges. Soon enough, the team realised that there was a generally negative perception towards stemming plugs in Africa. “Initially, 99% of our engagements with potential clients were unsuccessful. We quickly realised that there was a misconception about stemming devices, stemming in general and its value in the blasting process,” he says.
The only way to quell the perception was to prove that the product worked. As a result, ERG Industrial adopted an in-field, test-based
On the back of a massive growth trajectory since its inception some four years ago, ERG Industrial, a young South African company specialising in blast optimisation for quarries and mines, is taking a global view of its business. The expansion drive, confirms MD Eugene Preis, has been set in motion with the recent conclusion of the worldwide distribution rights deal for Varistem stemming plugs and will be further reinforced by establishing a new global headquarters in Ireland. Munesu Shoko reports
approach to its business. “We started doing in-field tests to demonstrate the product’s capabilities and build collateral. The science behind the product made sense, but the tests were meant to prove to the customer what could be achieved in their unique operating environments,” says Preis.
The testing approach soon translated into paid deals as customers saw the product’s value firsthand. The first paying customer was South Africa’s Raumix Aggregates, part of the larger Raubex Group. It started using the Varistem product at its Eastern Capebased Aliwal North Quarry in January 2020. However, soon after that, the COVID-19 pandemic hit, with lockdowns bringing the industry to a standstill in March 2020. As a service provider to the mining industry, which was classified as an ‘essential service’, ERG could continue with its operations during the lockdown.
In fact, the COVID-19 pandemic, says Preis, shaped the ultimate structure of the business – to be as lean as possible. The company generally outsources much of its non-core functions, such as warehousing and logistics, essentially converting what should be operating costs into direct costs.
While the pandemic harmed at a macroeconomic level, with shipping costs going through the roof and lead times doubling, Preis says the period actually ushered in a sustainable growth trajectory for the business. Over the past four years, ERG has averaged a 323% annual growth rate, with a whopping 450% growth projected for the current financial year.
Central to the growth, he says, has been the company’s ability to prove the capabilities of the technology through scientific evidence. “A founding principle of the business was not only to help mines and quarries optimise their blasts but also to quantify and demonstrate the benefits and value created to the customer. During in-field testing, we started using drones and other monitoring technologies to collect data to scientifically show the value created by our Varistem stemming plugs,” explains Preis.
The overarching philosophy of the business is that it only sells where it can demonstrate the value of its product. “We do not have a copy-and-paste approach to our product sales. For every new site, no matter how big or how small, whether it’s a mine or a quarry, we treat each operation as unique. Our process is to first understand the sitespecific challenges and then determine if there is an opportunity to change the blasting recipe by adding the Varistem plugs to the equation,” he adds.
Following its success in Africa, ERG started receiving more enquiries from beyond the continent, which informed the next step of its growth trajectory. Having seen the growing global appetite for the Varistem product, particularly as a result of its aggressive LinkedIn marketing campaign, ERG approached MOCAP for global distribution rights of the Varistem plug, with an official agreement reached in June this year.
“We are now the global distribution rights holder for the Varistem. From a customer perspective, one of the key benefits of this development is that we have standardised the pricing of the plugs globally, barring the shipping costs and duties, which vary from country to country.
“The reason behind that approach is to ensure there is no unscrupulous sales activity, especially in the resale and redistribution game,” he says. “The standardised global price also makes sense for multinationals operating across various mining jurisdictions in the world.”
As with its successful approach in Africa, the initial focus in the global market is not necessarily on immediate sales but on in-field testing to build up collateral.
The challenge, however, is to get stock to different markets for testing, which is why ERG has set its sights on establishing logistical centres in various markets.
The strategy has been set in motion with the establishment of a warehouse in the United States in June this year. The facility will keep inventory for the United States, Canada and South American markets. The same approach has been adopted in the UK, where the first batch of inventory arrived in September this year. The UK facility will cater for England, Scotland, Wales and England.
The same model is in the pipeline for Perth, Western Australia, where ERG is working with a longstanding Varistem supplier in the country.
The next step of the expansion strategy is establishing a headquarters in Ireland, which will take priority in the next six months. The move is a necessary structure aimed at optimising the distribution of products to different markets worldwide.
As part of its UK strategy, the company has partnered with Ground Engineering Applied Research Services (GEARS), which has developed innovative AI-based software for analysing blasts in quarries. GEARS confirms Preis has already conducted several test blasts at quarries in the UK, using its
software to evaluate the impact of Varistem stemming plugs on blast outcomes.
Commenting on the business’s overall success, Preis is impressed by some of the flagship projects the company has executed thus far. A case in point is the blast improvement feat achieved for the manganese and iron ore commodity areas.
“There are two main products in the manganese and iron ore sector – lump and fines,” he explains. “Fines are anything less than 6.3mm, while lump is anything between 6.3mm and 26mm. Whatever the lump market value is at the time, there is an immediate 30-40% discount on the fines, which is why it is important to find a good balance between your lump size and fines.”
He says that manganese and iron ore mines generally work on an 80:20 lumpto-fines ratio. “Based on the work we have done with manganese and iron ore mines over the past few years, we have successfully shifted the lump-to-fines ratio to 85:15. The financial benefit of that shift is incredible. To provide context, on one of the mines, this shift generates an additional ZAR150 million (about £6.5 million) per year for the mining company.”
ERG has also had massive successes in other commodity areas such as diamond, gold, coal and PGMs (platinum group metals). Remarkable projects have also been successfully executed in the quarrying industry, where the focus is largely on improving fragmentation. Good fragmentation, according to Preis, has a positive impact on downstream processes such as load and haul, as well as crushing and screening. It also eliminates the need for costly secondary or mechanical breaking of oversize material.
“Because quarries are also by their nature close to communities and existing infrastructure, they need to find ways to control flyrock and keep their noise and airblast down. Using our Varistem stemming plugs, we have proven on many quarries that we can reduce the likelihood of stemming ejection and flyrock,” concludes Preis. AB
“During in-field testing, we started using drones and other monitoring technologies”
INNOVATION
Page 2: Sustainability and Muscle-Power
PASSION
Page 3: The Ideal Solution for the Quarry
Pages 4–5: Full Power with Electric Drive
NEWS
Pages 6–7 From the Smart Job with Surface Miners
MOBIREX MR 130(i) PRO IMPACT CRUSHER
The MOBIREX MR 130i PRO mobile impact crusher is the latest representative of the PRO line from Kleemann. Thanks -
ronmental standards as a primary and secondary crusher in natural stone and recycling applications.
Wherever high output and outstanding versatility are required, the MR 130i PRO is in its element. With a processing capacity of up to 600 tons of material per hour, it
range. The high output is enabled by the combination of a crusher unit with a-
tric power demands of the impact crush-
E-DRIVE concept. Thanks to an external power supply option, the plant can be operated with zero local emissions. This guarantees a low energy consumption -
ment is considerably reduced by water spraying at relevant points.
gles and a variety of blow bar options with an optionally available 8.4 square meter double-deck post screening unit. This enables the production of two clas-product quality.
The intuitive SPECTIVE operating concept makes the everyday work of its users easier and simultaneously enables high productivity. In addition to a large touchscreen panel and two SPECTIVE wireless remote control units – one for the convenient control of all relevant functions of automatic mode from the excavator –-
work site digitalization of the MOBIREX MR 130i PRO.
LEGAL INFORMATION
THE ROCK
The WIRTGEN GROUP’s Magazine for Materials Processing
Publisher
WIRTGEN GROUP, Branch of John Deere GmbH & Co. KG, Reinhard-Wirtgen-Strasse 2, 53578 Windhagen, Germany
E-mail: magazine@wirtgen-group.com, www.wirtgen-group.com
Mannheim District Court, HRA 704371, VAT ID No.: DE 283 504 884
General Partner
John Deere GmbH, limited liability company based in Luxembourg, Commercial Registry No. R.C.S Luxembourg B 161281
General Managers
Dr. Volker Knickel, Markwart von Pentz, Dr. Thomas Peuntner, Alejandro Sayago
Editorial Team
Wirtgen Group Corporate Communications
Production
muehlhausmoers corporate communications gmbh
The outstanding product quality delivered by the MOBIREX MR 130i PRO is guaranteed by the combination of a robust crushing unit with two impact tog-
red the MOBIREX MR 130i PRO is uaranteed by the combination a roust unit wit h two impact tog -
The MR 130i PRO can be operated with zero local emissions and thus guarantees a low power consumption per ton of
Discover more online
With its double-deck post screening unit, the MR 130i screening and outstanding product quality with just one single plant – without the need for an additional
The new impact crusher has been hard at work – and showing its particular strengths – in a quarry in western Germany since August 2022.
The Kalkwerke Oetelshofen quarry in Wuppertal has been a source for the limestone re-
naces of the iron and steel industry for many years. Since August 2022, quarry operator AMIRO GmbH now relies on a combination plant in which the screening unit is connected directly to the crusher. The perfect solution for this challenge is the new Kleemann MOBIREX MR 130i PRO impact crusher, which is now demonstrating its numerous advantages
screening and outstanding product quality. And all of this with just a single plant and no additional screening system. An
consumption, as only one machine, which is also characterized by low fuel consumption values, needs to be fueled.
At AMIRO GmbH, the long-standing collaboration based on mutual trust played an important role in the decision to invest in the Kleemann plant. In the words of CEO Dirk Frorath, after his visit to the Kleemann factory in Göppingen, where he was able to take a close and critical look at the impact crusher, "The massive running gear with its heavy-duty frame construction, the ladders and platforms for easy access to all components, and the solidly-built double-deck post screening unit all made a per-
concept. The plant operators in the quarry are already familiar with the concept from their work with other MR 130 EVO2 plants. "Time and again we receive very positive feedback from the users," reports Christoph Obalski, sales and marketing specialist at Kleemann, "the plant operators have no problems at all with the system. Once you're familiar with how SPECTIVE works, you can operate all Kleemann crushing plants intuitively.
Emil Steidle GmbH & Co. KG from Sigmaringen is breaking new ground Kleemann.
As a part of its diverse portfolio, Emil Steidle GmbH & Co. KG, founded 200 years ago, has also been extracting and processing quartz sand for over 50 years. After preliminary processing, the company directly markets some of the material produced, for instance for the construction of sports facilities, while the greater
of glass or building materials such as plaster or adhesives. The screening plants.
Eventually, the company decided to invest in a which has now been in operation since March 2023. On the one
hand, it has a very wide, large screening surface that can deliver a very high output. On the other hand, Kleemann provides an option for purely-electric operation of the plant – a future-oriented drive system that works on site without CO2 emissions – which assurance of quality. To guarantee the power supply on site, the company built a transformer station that accompanies the plant, which is moved 2–3 times a year. “All things considered, we regard this as an investment in the future,” says Achim Haßdenteufel, Division Manager at Steidle. “As far as the subject of energy is concerned, we have always been a forward-looking company. In the medium-to-long term view, we intend to generate our electric power with a photovoltaic system here on our systems and self-generated electricity.”
so this must equally apply to the plant. After all, there are many properties, we need to perfectly match the screen medium, screen pitch, the speed, and many other factors," says Michell Blasczyk. Here is where the technically mature and well-thoughtout details of the MSC 702i EVO come into play. Several factors in the collaboration with Kleemann impressed the Swabian com-
pany. "It was simply very professional how the Kleemann team made sure we had the right settings and optimized the screen pitch or the choice of screen media. The delivery was also fast. You can just sense the presence of committed, experienced employees who know exactly what they are doing." explains Achim Haßdenteufel. "The output of the plant is impressive,” adds Walter Kieper, Operations Manager at Steidle, “everything can be operated very conveniently by remote control. Although it was totally new to employees previously used to controlling plants with hydraulic levers, they very soon managed to get to grips with the digital display. It all has a logically structured and intuitive layout." What also impressed was the fact that the John Deere engine and the plant are produced by members of the same company group, which guarantees smooth and seamless collaboration.
ration tool for rapid determination of theurator. It saves time, provides safety and with the lowest possible wear and fuel consumption in the hands of both inexperienced and experienced plant users.
The applications for crushing plants are diverse. The parameters required depend on the feed material and the desired end result, and it takes time and plant operator’s day-to-day work much the SPECTIVE touch display.
For automatic optimization of the crushing process between crushing plants, and to achieve maximum utilization of the plant train, Kleemann plants are simply linked with one another by smart line coupling. There is now a wireless line coupling option as an alternative to safety-relevant cable coupling. Wireless line coupling is easier to handle and considerably reduces the plant operator’s daily workload.
Genuine wear linings from Kleemann extend the service life of
nents. Crushing and screening plants are always subject to high forces and, in many cases, particularly high wear – above all in certain areas, or on components that are in direct physical contact with the material to be processed. This wear results from pressure, impacts and friction.
In Bad Fredeburg, in the Sauerland region of Germany, two Hamm H 25i VC compactors with special crusher drums were used to crush and simultaneously compact slate for the construction of an up to 15-meter-high embankment for a new bypass. The use of the VC compactors enabled the contractor to streamline the construction process, removing the need for a separate stone crusher and eliminating a major part of the material transport required. This speeded up the process and simultaneously reduced the overall costs. "As soon as I saw the rock, I had a feeling that the Hamm compactor would be perfect for crushing this material," said Michael Tillmann, Construction Manager from lead contractor Straßen- und Tiefbau GmbH. The slabby rock in question was Fredeburg slate, also known as schisty graywacke. Originally, the materials was to have been broken up to a maximum particle size of 200 mm at source by several jaw crushers, then loaded onto trucks by excavators and transported to the embankment construction site. Dozers would then have distributed the broken material to allow compactors to compact it layer-by-layer.
A trial soon showed that the Hamm VC compactors delivered the right crushing pattern for this application. Site inspectors
the degree of compaction achieved in the layers making up the embankment. As Michael Tillman explains, "After a few days, it was clear that we were working much faster than when using crushers, mainly because of us working layer-by-layer.” “By decoupling the process steps, we were able to handle around 4,500 cubic meters of material per day. That’s almost twice as
cantly fewer machines were required, the costs for crushing and compaction were able to be reduced by around 50 percent. At the same time, the CO2 the entire construction site.
The Wirtgen Surface Miner 280 SMi is being used for the selective mining of limestone in northern Estonia. The big advantage? The material is broken down to the required size during cutting, so that it can be used directly without the need for additional crushing and screening. Thanks to the Wirtgen Surface Miner’s leveling technology, the oil shale can be cleanly separated from the limestone layers, which ensures that the materials are extracted in exceptionally high quality and purity. In addition to the selective mining of materials, precise leveling also enables optimum regulation of the water balance at the mine. The Surface Miner 280 SMi creates surfaces with
the drainage of water from the working area.
The central-drum concept of the 280 SMi is the ideal solution, deposits. Wear-resistant toolholder systems and picks mean fewer idle times, and the hard-rock cutting drum unit provides maximum durability in hard rock layers. In addition, a variety of automatic functions contribute to operator comfort, reduce the risk of fatigue and assist in the achievement of high productivity. And that in a region that presents the enormous challenges of temperatures reaching into the double digits below zero and around 100 days of snow per year.
KLEEMANN ORIGINAL TRON BLOW BARS
POWERFUL,
parts.wirtgen-group.com
Resilience is a notable characteristic of the UK and Ireland aggregates and quarrying machinery markets, with much of it on show in 2023. Experts tip it to continue next year as new economic and political factors emerge. Guy Woodford reports
The Mineral Products Association (MPA) has published a new regional construction and mineral products market report, giving a detailed assessment of historical, current and future trends across every region of Great Britain.
Primarily prepared to help inform and support the local mineral planning system, the annual report compiles industry data and broader context to paint a clear picture of the main drivers of activity in heavyside construction materials and industrial minerals, an essential tool for producers and planners alike.
The report includes summaries for all regions and devolved administrations in Great Britain, illustrating the recent performance of the construction and mineral products markets, with critical insight into the sectors expected to drive growth in the UK’s around 280 million tonnes a year (Aggregates Europe – UEPG 2021 estimate) mineral product demand over the next five years (2023-27).
While London is often regarded as the key hub of new construction projects and infrastructure, representing 21% of the total value of construction output in 2022, the report highlights that the East of England and the Yorkshire and Humber area are both expected to see the fastest rate of growth (2.2%) over the next five years, led by energyrelated projects.
Data on mineral-product sales volumes is collected through a rigorous survey among MPA producer members, representing most mineral products markets, including 90% of total GB market sales for primary aggregates and asphalt, for example, and 75% for readymixed concrete.
The report reveals that construction demand for mineral products in 2022 recorded a gradual loss in momentum as the year progressed due to a worsening macroeconomic environment and slowing activity in key construction segments.
Tonnages of primary aggregates sales fell by 8.2% annually compared to 2021, asphalt by 6.5%, and ready-mixed concrete by 3.8%.
The East Midlands was the biggest asphalt and crushed rock market in 2022, accounting for 15% and 29% of total sales in Great Britain, respectively. The region also emerged as the most resilient to the downturn last year, recording the smallest falls in demand.
Meanwhile, London was the biggest demand centre for ready-mixed concrete, accounting for 19% of total sales volumes from fixed plants. Demand in London last year remained broadly flat, in contrast to the 5.5% decline recorded at a national level.
Finally, much of the sand and gravel used in Great Britain to manufacture ready-mixed concrete is produced from the West Midlands, the East of England and the South East, accounting for 53% of total sand and gravel sales in 2022.
Luke George, economist at MPA and author of the report, said: “This new report provides a valuable insight into the contrasting dynamics in construction and mineral products markets across the various regional and devolved administrations of Great Britain. We aim to provide a unique, easy-to-use point of reference to support MPA members, planning professionals and other industry experts in their decisionmaking processes. This report cuts through the overwhelming quantity of industry data that’s available and revised almost daily.
“Minerals and the wide range of construction products derived from them are key elements to successfully delivering many of the Government’s ambitious policy objectives, such as on housing and
infrastructure, including achieving the energy transition and delivering Net Zero. The UK economy's success in delivering on these objectives will depend on local mineral planning authorities and mineral producers having robust evidence around future market needs, given delivery is heavily reliant on the availability and supply of essential mineral products.”
Mick Knight, industry manager – Quarry and Aggregates, for Finning UK & Ireland, Caterpillar’s UK and Ireland dealer, says quarry operators, especially larger companies, are increasingly focused on meeting their net-zero emissions goals.
“We can do a lot now to drive best practices and make sites and operators more efficient to reduce fuel use and carbon emissions. For example, using telemetry to connect equipment, operators, and sites has produced significant gains.”
Knight explains that while machine technology is widely used in the aggregates and quarrying sector, there is huge scope to increase the use of telemetry as well as semi-autonomous technology, such as Cat Command, and other features in the use of machines to provide greater productivity, efficiencies and ensure operator safety.
“Better use of telemetry on the machines can significantly improve site productivity and play a pivotal role in ensuring machine performance and health, improving efficiencies. Technology such as VisionLink Productivity provides valuable insights into the performance of the equipment. It can also uncover potential site set-up issues and pinch points. Telemetry can highlight operator performance issues and the correct use of the ease-of-use functions. It can also reduce machine idle time, fuel consumption and exhaust-pipe carbon emissions. The Next Gen technology features built into the latest Cat machines, such as ease-of-use features, are designed to improve operator competency precision and ensure safety is paramount.”
“Our customers are still busy, and demand for machines remains high”
Finning has introduced a dedicated ‘eco-drive’ training programme aimed at operators to hone and develop their skills and make the most of the technology features they offer. In addition, Knight says the company has also introduced an ‘eco-training advanced’ scheme aimed at managers involved in planning operational logistics, focusing on using data insights to pinpoint opportunities for efficiency improvements across sites.
Knight added: “Sustainability continues to drive other operational decisions in the aggregates sector. This is evidenced by the increase in the volume of machine rebuilds that Finning conducts for companies in the sector, including Hanson, Aggregate Industries and Imerys. Rebuilds also offer other significant benefits for aggregate firmsfinancially, with firms typically saving around 55 – 60 per cent when compared with the cost of a new machine.”
Asked about aggregates demand levels in the UK and Ireland, Knight says: “Although official figures show the industry is contracting, our customers are still busy, and demand for machines remains high.
“It’s important for Finning that we provide our customers with a range of options regarding fleet succession planning. We’re seeing a surge in demand for used machines, particularly those well maintained under a Finning service programme. To reassure customers, we can also provide a full machine inspection and service records for used machines.”
Commenting on large UK & Ireland construction projects influencing demand for aggregates, machine purchases, and rental, Knight says: “HS2 is ongoing and continues to drive demand for aggregates and will do so for the foreseeable future. We’re also seeing several significant rail infrastructure projects driving demand – such as the works to upgrade the Lower Thames Crossing and the road improvements on the A428 in Northampton and the A303 and A30 in Southwest England. We’re also involved in several power-generation developments; an accelerated programme of renewable developments is underway, which is also driving demand for aggregates.”
Looking ahead to aggregates and quarrying machine demand over the next 18 months, Knight continues: “The latest MPA market forecast [April 2023] indicated a deterioration in market prospects for mineral products sales in 2023, underpinned by a shallow recession this year, slowing construction activity and heightened delivery risks of the existing project pipeline.
“Sales volumes for primary aggregates and ready-mixed concrete (RMC) are expected to fall at an annual rate of 3% in 2023, with reductions of 4% for asphalt and 8% for mortar. These markets are then expected to resume modest growth from 2024, assuming a rebound in private house building and roads after a short-term blip, two areas particularly exposed to the impact of weakening economic activity and the surge in cost inflation. Meanwhile, throughout this year and next, sales volumes should continue to be supported by infrastructure, driven by major projects including HS2, as well as by work in industrial warehouses and logistics projects.”
Volvo Construction Equipment (Volvo CE) also has a strong presence in the UK quarrying machine market. Speaking to Aggregates Business, Phil Battle, director of strategic accounts at SMT GB, Volvo CE’s UK distributor, emphasised the “remarkably
resilient” nature of the British quarrying and aggregates industry. “It is an industry which is going through a great deal of change to develop and innovate its customer solutions to lower overall greenhouse gases (GHGs) in all its operations. The leading quarrying and aggregates companies are extremely focussed on detailed roadmaps to decarbonise their industries, and SMT is helping to support and advise on this strategy.”
Battle says the present economic climate is challenging for the UK quarrying and aggregates industry, but this is “nothing new” for an industry that has, in the last couple of decades, had to navigate through the impact of the financial crisis in 2008, COVID-19 and latterly the macro-economic fallout from the war in Ukraine, including supply chain issues and high inflation costs. “Looking at the situation today, it is clear that certain sectors such as housebuilding are in a slowdown as a direct impact of higher interest rates set by the Bank of England to combat inflation, which in turn filters down to housebuilding demand in the market due to the higher mortgage rates for lenders. Regarding the quarrying and aggregates companies, this has meant less demand for some of their products, such as asphalt and ready-mix, which are largely dependent on a strong and healthy housebuilding market. However, the latest data suggests that commercial building continues to expand, which may (in the short term) soften the impact of the decline in housebuilding.”
Battle says that despite media attention and some criticism of government spending levels for core infrastructure,
civil engineering projects have remained robust, albeit the pace of growth has slowed recently. “As this sector has remained strong in the first half of 2023, primary quarries with supply chain contracts in place have seen their output remain steady, and as we track machine utilisation across both major projects and downstream primary quarries, we can see that civil engineering projects remain busy, despite delays in infrastructure timescales.”
Does Battle think current demand levels are likely to change in 2024? “Listening to the two main political parties, they are both in agreement that it is paramount that there needs to be significant investment in Great Britain to drive growth and prosperity, including generating good quality and well-paid jobs. The political party that is successful in the general election next year will need to quickly spell out their plan to drive growth and explain where it will make key investments. There needs to be a structured plan for energy, with a mixture of large projects such as Sizewell C and Small Modular Reactors (SMRs), to ensure we have a reliable (secure) energy supply to meet current and future energy demand.
“However, in the short-term, we need to see a commitment to a well-funded transport policy, including backing for Road Investment Strategy (RIS) 2 and 3. This will include important projects such as Lower Thames Crossing (LTC), A303 Stonehenge tunnel and many other significant National Highways schemes aimed to connect Britain. I would also like to see the successful party commit to HS2 in full and a better focus on the overall levelling up agenda. This should include
projects such as the Northern Powerhouse rail link, which will be a key investment into the future economic success of northern England.”
Battle stresses that investment in core British infrastructure needs to be done in a way that will decarbonise construction activities and help to accelerate change towards diesel-free jobsites. “Quarrying and aggregates companies, supported by Volvo CE and SMT, are already working in partnership to lower the impact of CO2 by utilising net-zero construction-equipment machines, supported by solutions. Volvo CE has the largest range of commercially available electric construction equipment products in the market. SMT and Volvo CE are fully committed to introducing a full range of technologies and solutions to help our customers decarbonise, and the pace of this transformation is accelerating. However, SMT is also supporting customers to minimise their CO2 footprint with their existing fleets of diesel internal combustion engine machines, which will continue to operate for many years. It is critical that we work with customers to lower their CO2 impact across the whole lifespan of their machines, which includes how we rebuild and recycle machines at the end of their life.”
Battle explains that the leading quarrying and aggregates companies are looking past some of the short-term economic uncertainties and see the climate-change situation as a far greater threat to their longterm security and, therefore, something that they need to act on today, rather than wait for legislation or for the perfect solution to become available. “The real pioneers are already taking a close look at our solutions and are considering how they might need to
adapt how they have worked in the past to adopt and embrace the future,” he concludes.
Retail sales of UK construction and earthmoving equipment bounced back in June 2023 after falling below yearon-year levels in May, according to the Construction Equipment Association (CEA) and Systematics International’s construction equipment statistics exchange.
Sales in June were more than 8% above those in the same month last year, including very strong sales of mini/midi excavators, the most popular product in the UK. As a result, sales in Q2 ended up at 3% above the second quarter last year.
Sales in H1 2023 reached 19,600 units, 7% ahead of the same period of last year. While the CEA notes that current sentiment in the market is still anticipating a modest downturn in sales in the second half of the year, this will be from 'record' high levels achieved in the year's first half.
Road rollers show the strongest growth at 37% above last year's levels, following very strong sales in June.
The pattern of sales on a regional basis in the UK and Northern Ireland is mixed. This year's strongest sales are still in Scotland and the South East of England, where sales remain around 30% ahead of last year's.
Only three regions are seeing lower growth than last year, consisting of the North West of England (-16%), Northern Ireland (-5%) and London (-4%)
Equipment sales in Ireland are also reported in the statistics exchange. Sales in May and June 2023 were at similar levels to the same months of 2022, and sales in the first half of the year are 3% above last year's, due mainly to a very strong first quarter
GlobalData, a leading global business intelligence consultancy, reports that the Irish construction market size was $26.2 billion in 2022. The same source projects the market to achieve an AAGR (annual average growth rate) of more than 4% during 2024-2027, assuming an improvement in the wider economy, and this will be supported by investment in the transport and electricity sectors. The rise is good news for the country’s building-materials producers, off-highway machine manufacturers, and machine dealers
The leading contractors in the Irish construction market are SISK Group, P.J. Hegarty & Sons UK Ltd, Royal BAM Group NV, John Cradock Ltd, McKeon Group, Quintain Ltd, Stewart Construction, Ronan Group Real Estate, SIAC Construction Ltd, and Wills Bros Ltd. SISK Group led the market in 2022. AB
The Middle East has seen a resurgence in post-COVID-19 construction activity, particularly in the Gulf Cooperation Council (GCC) region, partly due to high oil prices. Given the high price of premium building materials and environmental sustainability concerns, developers have increasingly sought to use more recycled aggregates from construction and demolition (C&D) waste. V L Srinivasan reports
Not long ago, most C&D waste generated by infrastructure building works in the Middle East was dumped in landfills. Not anymore. Across the region, C&D waste is now turned into quality recycled aggregates and used in many major construction projects.
The price of sand, gravel, clinker, cement and other key building materials has soared due to the sheer volume of Middle East construction activity, regional economic expansion and growing urbanisation. As such, the growing availability of recycled aggregates provides much-needed relief for bottom-line-minded project managers. Furthermore, a greater use of recycled aggregates reduces a project’s carbon emissions and developers’ reliance on imported building materials.
Governments such as the UAE, Saudi Arabia and Qatar have enacted legislation allowing construction firms to use a minimum of 20% to 40% of the recycled aggregates in their infrastructure works, including new commercial and residential builds.
According to the study Securing Valuable Resources for a Sustainable Future by Boston Consulting Group, GCC countries are generating between 105 and 130 million tonnes of waste per annum, primarily from C&D waste, municipal solid waste (MSW),
and agricultural waste, with Saudi Arabia and the UAE accounting for around 75% of it. While these estimates are based on official reporting, the study said that GCC countries face additional challenges from limited waste tracking and illegal waste dumping, particularly agricultural waste and C&D waste.
Salman Zafar, an expert in waste management and founder of EcoMENA, a volunteer-driven initiative creating environmental awareness and fostering sustainability worldwide, particularly in the MENA (Middle East - North Africa) region, said that recycling C&D waste can expand the lifespan of landfills and help reduce the cost associated with the maintenance of existing landfills and building new ones.
Zafar said that recycling also helps
conserve natural resources and diverts construction waste from landfills, which can generate a substantial volume of harmful odours and gases.
He continued: “Recycled aggregates are less expensive to produce than virgin materials. Using recycled aggregates in construction projects will decrease the load on existing landfills and help companies
“Recycled aggregates are less expensive to produce than virgin materials. The use of recycled aggregates in construction projects will decrease the load on existing landfills and help companies meet their sustainability targets.”
Salman Zafar, founder of EcoMENA
meet their sustainability targets. By diversion of construction waste from the landfills, companies will also be able to cut down on landfill tax/tipping fee.”
In the UAE, C&D waste constitutes 70% of the total weight of solid waste. Dubai alone produces nearly 5,000 tonnes of C&D waste every day, with Abu Dhabi generating around 7,000 tonnes daily, accounting for 71% of total waste in the Emirate.
The UAE’s Ministry of Climate Change and Environment issued a Ministerial Resolution in 2019 on recycling C&D waste for roads and other similar infrastructure projects. Government and private contracting organisations can use recycled aggregates for 40% of their total building material needs as part of the new resolution, and the decision is implemented by various departments and local civic bodies across the Emirates.
While some developers remain apprehensive that recycled products are inferior to virgin materials, once they confirm the prescribed specifications, they can outperform or remain at least just as good as virgin materials.
The UAE government has even established the Abu Dhabi Waste Management Centre – Tadweer – which not only deals with C&D waste, but also other refuse such as used engine oil, old tyres, and plastic items.
Tadweer has set up two factories established for this purpose. The first is in
Abu Dhabi and managed by This Middle East Services; the second is in Al Ain and managed by Star International Waste Management LLC. These two units together handle 10,000 tonnes per day.
Tadweer also opened Ghayathi Crusher in the Al Dhafra region in 2018 but closed the plant after a year. The unit had a stockpile of 1.6 million tonnes of material ready to be crushed at the time of closure. It was re-opened in 2021 to promote environmental sustainability and develop an integrated waste management system in Abu Dhabi.
The Ghayathi crusher can handle 2,000 tonnes of C&D waste daily and produces high-quality aggregate for the construction of vital infrastructure projects, such as roads, to contribute to the sustainable development of the Al Dhafra region.
Dr Salem Al Kaabi, director general at Tadweer, said that the decision to reopen the unit aligned with its continued efforts to fulfil Abu Dhabi’s vision of diverting 75% of its waste from landfills.
“The crushers run by Tadweer play an important role in achieving this target through recycling huge quantities of C&D waste and turning them into useful materials to use in vital projects in Al Dhafra region and across the country.”
The facility will ensure significant savings for the local economy and articulate Tadweer’s strategy of meeting the demand for recycled aggregates from the Emirate’s crushers, using them in vital projects in collaboration with other government entities and private sector partners.
“All operations at the plant comply with the highest international standards and
“The crushers run by Tadweer play an important role in achieving this target through recycling huge quantities of C&D waste and turning them into useful materials to use in vital projects in Al Dhafra region and across the country.”
practices, and the materials generated by the facility will play a critical role in driving construction and infrastructure development in the region,” added Al Kaabi.
Private sector’s role
The private sector is playing an active role in recycling C&D waste via companies such as Ducon Green, Al Dhafra Recycling
Industries, The Rostamani Group and Dulsco.
Al Dhafra Recycling Industries has supplied 1.2 million tonnes of recycled aggregates to the prestigious $11 billion Etihad Rail project undertaken by the UAE government to link all seven Emirates.
BEEAH Recycling is another UAE-based company that has developed a selfsustaining model for waste management and zero-waste strategies. The company has made great headway towards a zerowaste solution, achieving a more than 76% diversion rate.
Dulsco, a people and environmental company based in Dubai, has signed an agreement with the UAE Ministry of Environment and Climate Change to set up two C&D waste recycling plants in the emirates of Ajman and Um Al Quwain. These facilities recycle the entire C&D waste from the two emirates, converting them into recycled subbase and aggregates for use in construction, replacing up to 40% of the virgin materials.
Climate Change, Sheikh Dr Faleh bin Nasser bin Ahmed Al Thani, said: “My ministry has a fundamental role in the success of sustainable development projects, achieving the country’s goals in preserving the environment, promoting green growth, and limiting the effects of climate change.”
Qatar, which has completed major infrastructure projects including seaports, airports, roads and developing new cities, valued at around $300 billion during the run-up to the 2022 FIFA World Cup, is not far behind compared with other countries in dealing with C&D waste.
An estimated eight million tonnes of C&D waste are generated annually. Qatar’s National Environment and Climate Change Strategy (QNE) has implemented a robust policy framework to safeguard Qatar’s environment for future generations. As part of the policy, the government has set a target of using 35% of recycled aggregates in various construction projects.
Al Thani’s ministry released a book titled Implementation of Recycled Aggregate in Construction in January 2022. “With the vast investment made in infrastructure projects, Qatar has set targets for the efficient use of natural resources, with a recycling target to use 20% of recycled aggregate to replace primary aggregate in government construction projects by 2022,” the ministry said in a statement at the book’s official launch.
The state-owned Qatar Primary Materials Company (QPMC) signed a MoU with Qatar’s Ministry of Municipality and Environment in 2019. It has been treating C&D waste in the Rawdat Rashid landfill and converting it into materials usable in construction projects.
Besides the Rawdat Rashid landfill, QPMC also manages three more sites at Umm Al Zubar, Jary Alsamar and Bu Salba, respectively, which are the recycling sites of Qatar’s Ashgal (Public Works Authority). The combined production of recycled aggregates is 660,000 tonnes per month, according to
the Ministry’s book.
The company is also looking at the possibility of producing washed sand in the facility that will be established for use in infrastructure projects and construction projects (including concrete and asphalt layers) to meet Qatari specifications and standards.
In Saudi Arabia, the Kingdom’s Sovereign Wealth fund – the Public Investment Fund (PIF) - has set up the Saudi Investment Recycling Company (SIRC).
The state-of-the-art facility is the first step toward meeting the national ambition of diverting 60% of C&D waste from landfills by 2035 in line with the Kingdom's effort to accelerate the transition to a circular economy.
The aim is to produce recycled aggregates that can be used for new roads and buildings while at the same time reducing the estimated 20 million tonnes of C&D waste dumped in vacant plots around the city each year. Located in Al Khair, north district of Riyadh, SIRC's new plant treats up to 600 tonnes of C&D waste per hour.
Riyadh region’s Mayor, Prince Faisal bin Abdulaziz bin Ayyaf, assured his administration’s support in the project’s implementation, saying: “The waste recycling facility in Riyadh will offer numerous economic, social, and environmental benefits to society that are above and beyond the direct return on investment.”
Besides SIRC, in 2021, Averda, a global waste management company, opened an integrated and environment-friendly waste management facility for the $20 billion Red Sea Project in Saudi Arabia. Averda said all forms of waste generated by the project were considered in the design of the waste system. Tonnes of rubble, rock and concrete generated by the construction of the foundations, buildings and infrastructure were sorted and treated by special machinery,
“My ministry has a fundamental role in the success of sustainable development projects, achieving the country’s goals in preserving the environment, promoting green growth, and limiting the effects of climate change.”
transforming it into smaller particles. The company said they are then being reused for other purposes, such as aggregate for building roads.
Kuwait
Kuwait has also recognised the environmental and economic benefits of using recycled aggregates. According to a study titled Integrated Solid Waste Management System, 76.2% of Kuwait’s waste can be recycled. By installing seven recycling plants, 90% of Kuwait’s C&D waste and 95% of its waste tyres and organic waste can be recycled. The raw materials produced by the recycling plants could generate revenue of US$137 million per year. The estimated total profit from the system would reach $450 million in 2040, the Kuwaiti study said.
The state-run Public Authority for Industry is planning to build an industrial zone housing companies specialising in waste recycling, including C&D and industrial waste. The zone will cover a two km² area with 215 factories specialising in recycling waste, including tyres, plastics, wood, metals, and construction materials.
Sharifa Al-Shalfan, a member of Kuwait’s Municipal Council, has an answer to minimise the impact of C&D waste. She submitted a proposal to the Municipality nearly ten months ago to dismantle buildings instead of demolishing them.
“Dismantling is a good option to reduce waste by reusing and recycling the parts and pieces of buildings. This should be made mandatory for public buildings and optional
for privately owned structures,” she suggested.
According to Al-Shalfan, the demolition of buildings causes pollution to the environment due to dust resulting from the process, disturbing the owners of neighbouring buildings, and other financial losses from not using the discarded building components.
“Deconstruction contributes to enhancing sustainability by reducing solid construction waste. It leads to promoting the concept of reuse and recycling in the Kuwaiti society, which results in positive effects on the environment and the economy, as well as preserving natural resources,” she added.
Egypt Egypt has undertaken several projects, including constructing a new capital city, the New Administrative Capital. The C&D waste from these projects is estimated to be four million tonnes per year, constituting 60%-70% of the total waste generated in the country. This waste is managed through disposal in landfills, causing huge deposits of C&D waste, thus posing an environmental problem. Currently, there are eight C&D waste management plants in the country, and 31 more are under various stages of construction. AB
Find out more: eu.develon-ce.com
The recent steinexpo quarrying show in Germany threw the spotlight on two brands planning to expand their presence in the international crushing and screening market.
Liam McLoughlin reports
Metso is aiming to further expand the global footprint of the Jonsson mobile crushing and screening brand that it bought in 2018.
Speaking to Aggregates Business at September’s steinexpo quarrying and construction equipment event in Germany, Timo Nakari, VP of the Jonsson business line, said that when Metso acquired the Swedish company its business was centred in the Nordics but Jonsson machines are now available around the world.
The massive 133-tonne Jonsson L120330 mobile crusher was on display at the steinexpo show in Nieder-Ofleiden. The machine can be transported and takes around two hours to set up.
"Most of our customers [for Jonsson machines] will be quarry operators," says Nakari.
All Jonsson machines are electric and Nakari says the L120-330 is unique as it has two crushers - a jaw and a cone - on the same chassis.
The large Jonsson machines include primary crushers ranging from 80 tonnes to 150 tonnes. "We also have five cone models and plenty of screeners," says Nakari.
Around 300 exhibitors and 440 brands were present at steinexpo this year, and for the first time this included Chinese crushing and screening equipment manufacturer
Mesda, which was making its debut at a European show.
Baojian Wang, VP international cooperation of Guangxi Mesda Group, said his aim is to bring the company to international markets, particularly Germany and other European countries.
He added: "Mesda promoted electricpower mobile machines in China from the very beginning. For a decade of growth, the sustainable, and environmentally-friendly power solutions have been a very important value of Mesda, that we would like to offer to the [international] markets."
As part of its expansion plans Mesda appointed Patrick (PJ) O’Donnell to the new position of business development director at the end of 2022.
He will be responsible for development of the global network for Mesda's crushing and screening business, and to establish a sales and service network which is close to Mesda's end customers.
Having worked for a number of global manufacturers O’Donnell has over 20 years of business development and sales experience in the crushing and screening industry.
Metso has extended its manufacturing capacity of mobile track-mounted crushing and screening equipment in the Indian city of Alwar with the opening of new manufacturing facilities. The manufacturer
says the extended facilities will help it capitalise on market opportunities for its quarrying equipment across India, south-east Asia, the Middle East and southern Africa.
Following the extension, the total size of the Alwar factory will be approximately 340,000 square metres, adding 35% more capacity to the factory.
Markku Simula, president of the aggregates business area of Metso, says the Alwar site in the state of Rajasthan has had several extensions since it initially opened in 2008, with the latest being the largest yet, increasing the size of the factory by about one third and making it the company's largest manufacturing facility.
He added that the new extension will focus entirely on producing mobile trackmounted crushing and screening machines from several Metso Group brands. In addition to the mobile Metso Lokotrack equipment, the increased capacity will be used to manufacture mobile McCloskey and Tesab equipment. At the same site, Metso also produces wear parts and pumps for the aggregates and mining industries.
Simula says that India, south-east Asia and the Middle East represent "tremendous growth markets" for Metso.
"If you look at our aggregates business globally, we are extremely strong in North America and Europe," he added. "Where we see the future growth opportunities is the
Powered by
Want to find out more? Scan the code:
You can acquire new and used Zaxis excavators and ZW wheel loaders, with our hassle-free financing packages, supported by BNP PARIBAS Leasing Solutions. Contact your local Hitachi dealer and discover how we can tailor our services to meet your specific requirements.
eastern hemisphere. The countries that are most vibrant right now are India and Saudi Arabia. There is a lot of activity in quarrying in India. The Indian domestic [crushing and screening quarrying equipment] market is very competitive. We are by far the number one international player in India and the second largest overall after one of the domestic players."
Simula says particular opportunities in India come from the Indian government's plans to increase highway construction in the country from 39km per day to 60km per day.
Metso's NW Rapid range of portable wheel-mounted crushing machines, which can be set up very quickly, was developed to meet the needs of the Indian quarrying sector
Simula adds that there are also major opportunities for Metso's business in Saudi Arabia from a number of huge projects such as The Line linear smart city that is under construction in Tabuk Province.
The 170km-long city is part of the Saudi Vision 2030 project to diversify the country away from its current dependence on oil production.
The Alwar factory now employs approximately 1,300 people in total. The official opening of the new facilities took place on September 19, 2023, and Metso says that production ramp-up to reach full capacity will continue until the end of the year.
Currently, 38% of the Alwar plant's output is for the Indian domestic market with 62% being exported to 80 different countries.
The new factory showcases the most modern manufacturing practices, hosting several sustainability-driven functions like automated warehousing, automated assembly lines, modern painting lines and 13,000 solar panels installed to enable the increased energy production. After the extension, solar energy covers 85% of Alwar’s total power generation, which is the maximum permitted as per state government guidelines.
“With the increased manufacturing capacity, Alwar becomes the major Metso site for increased domestic business in India and exports to Metso’s customers globally," Simula says. "Additionally, significant investment has been made in engineering and R&D resources, making it one of our key global engineering hubs."
The expanded engineering centre at Alwar now has around 100 engineers and Simula says it will play an important role in product development for the company.
Kleemann has launched the MOBIREX MR 100(i) NEO/NEOe mobile impact crusher, the first member of the new NEO line.
The Germany-based manufacturer says the machine is efficient, powerful and extremely flexible – and all-electric operation is possible with the NEOe variant.
It adds that the machine's compact dimensions and a low transport weight mean the new MOBIREX MR 100(i) NEO/ NEOe can be used flexibly, quickly and in a very wide variety of applications. Operation in tight spaces on work sites or in frequently changing places of work is easily possible. Operation ranges from different recycling applications, such as the processing of concrete, rubble and asphalt, to the processing of soft to medium-hard natural stone.
The new impact crusher is available with two versions: Depending on the application area, it can be run all-electrically with the drive concept E-DRIVE and thus, locally, free of CO2 emissions [MR 100(i) NEOe]. Alternatively, the machine is available with the tried-and-tested diesel-direct drive D-DRIVE.
Kleemann states: "Very high product quality is expected from an impact crusher, and this is precisely what the MOBIREX MR 100(i) NEO / NEOe delivers. This is guaranteed not only by the powerful crushing unit with its 4-ledged rotor with a large impact range and versatile rotor ledge options, but also by the 4 m2 large, optional, single-deck secondary screening unit. This
makes it possible to produce a classified final grain size. Through the use of an optional wind sifter, the final product quality can be additionally increased."
It adds that, thanks to a SPECTIVE operating unit specially tuned to the functions, operation of the MR 100(i) NEO / NEOe is simple and intuitive. With SPECTIVE CONNECT, operators have all relevant data on speed, consumption values and fill levels at their fingertips on a smartphone or tablet and prepared in a clearly arranged manner. SPECTIVE CONNECT also offers detailed troubleshooting aids to assist with service and maintenance. A unique feature in this machine class is the fully automatic crusher gap adjustment and zero-point determination. Zero-point determination compensates for wear during crusher start and a homogeneous crushing product is retained.
The new MOBIREX MR 100(i) NEO/NEOe machine will be introduced gradually starting in 2024 in Europe and North America.
Terex-owned Simplicity, an established name in the aggregates and mining Industry, has introduced the new MHS620X Modular Screen Plant, a mainstay of screening efficiency in Terex’s modular product offering.
The MHS620X features the new “extra clearance” 6’x20’ ESX Horizontal Screen launched earlier this year at ConExpo providing increased space between the screen decks resulting in easier maintenance access to the media, therefore improving overall maintenance safety. Other key features of the MHS620X include an extra heavy-duty I-beam frame, rigid diagonal truss construction and galvanized steel structure including walkways, stairs, and guard rails. The MHS620X emphasises safety, sustainability, ease of operation, and streamlined setup times.
The complete Simplicity’s modular product line consists of several pre-designed wet and dry screening “plug and play” modules. The variety of bolt-on options are interchangeable and can be fastened on-site using basic hand tools, eliminating any disruptions to ongoing operations. For use in various applications like mining, aggregates, demolition and recycling and industrial minerals applications, this product offering can be incorporated into a compact site or as part of a multi-plant system. AB
Reduce your carbon footprint and fuel consumption by 20% compared to a conventional excavator. With a total hybrid power of 235 kW / 315 HP these 36-tonnes-class hybrid excavators have logged millions of fuel-saving hours for our customers around the world. This 3rd generation Komatsu hybrid and advanced technology in the industry today.
Komatsu has unveiled its all-new digital solutions for quarry and large construction sites.
A major global manufacturer’s new cutting-edge digital solutions for quarry and large construction sites, two exciting next-generation loader series from leading sector players, and eye-catching electric-powered wheeled loading shovels from a top Chinese manufacturer start work at a major UK building-materials supplier’s key London facility. Guy Woodford & Liam McLoughlin report
Komatsu has unveiled its all-new digital solutions for quarry and large construction sites. Using these solutions, customers can further improve jobsite safety and operational efficiency. Whether you want to increase production, identify bottlenecks or quickly collect reliable machine and production data, the Japanese off-highway machinery giant says it has the ideal digital solutions.
Thanks to the one-second logger data Komatsu quarry machines collect, a fully configurable dashboard is offered for Komatsu quarry fleets. Using the factory-fit telematics hardware, data collection is made easy. Figures such as fuel consumption, ton/hr, idling times, error codes and machine health are presented to you when, how and where you want.
Komatsu’s Operator Guidance Monitor (OGM) provides real-time feedback to your operator using an in-cab tablet, which collects data directly from the machine. Applicable for Komatsu's bigger rigid dump trucks, OGM will automatically evaluate major KPIs (key performance indicators), such as payload, cycle times, fuel rate, idling and productivity immediately after each cycle. Operators will get alerts in case of overspeeding, sudden
braking or other areas for attention. Komatsu says you will improve your operators' skills and awareness, and the quarry’s safety and overall cost will also improve. Due to a series of back-office dashboards, quarry management can follow up on production, fuel consumption and machine use.
In the coming months, Komatsu will
Komatsu’s Operator Guidance Monitor (OGM) provides real-time feedback to your operator. Pic: Komatsu
introduce Smart Quarry Site, an all-in-one fleet management system for your quarry. Smart Quarry Site offers a complete package to follow up and control your multi-brand fleet using an in-cab-screen and CAN bus connectivity. Smart Quarry Site offers the flexibility to be used at every company level thanks to a real-time overview of your machines, configurable PDF or CSV reports, API service, and a series of dashboards. Features such as operator IDs, pre-start checks, overspeed alerts and a mesh network between machines will increase the jobsite safety. Komatsu says Smart Quarry Site will help you understand and control every aspect of your quarry exploitation area. Goals such as CO2 reduction, cost control, saving labour hours, controlled machine downtime and increased production and safety are “within reach”, says the manufacturer.
As part of its commitment to net zero, UK-based Aggregate Industries has deployed its first electric-powered loading shovel.
The LiuGong 856HE wheeled loader is now operating at the Aggregate Industries London Concrete plant in Bow, East London. The 856HE is claimed to be the world’s first commercially available battery-electric loader and is the first fully electric wheeled loader that LiuGong has supplied in Europe.
Oliver Keates, European product manager for the LiuGong Machinery wheeled loader range, says that more than 2,000 similar LiuGong electric wheeled loaders have already been deployed in China.
He adds of the 856HE loader: "This machine is suitable for a range of functionalities including quarrying applications, batching plants, recycling of materials and hopper loading."
At Bow, the 856HE loading shovel will be used to load aggregates from the site’s railhead and will also be used on the London Concrete Readymix plant to keep the site tidy and to manage stockpiles.
The 21,000kg vehicle has a 423kwh lithium iron phosphate battery with a fast-charging capability of 1.7 hours. The machine has a 160kw engine and 3.5m3 bucket capacity and can operate for more than 11 hours on full charge. The machine can be charged from 20% to 95% in around 45 minutes using the Kempower-supplied charger at the Bow site. Most importantly, it uses zero fuel, has zero emissions and produces low noise and vibration.
It joins London’s first all-electric readymix concrete mixer truck at Bow, a 26-tonne Renault Trucks E-Tech D Wide deployed earlier this year. Electrification of the fleet and plant is central to Aggregate Industries’ wider approach to reach net zero before 2050. Kirstin McCarthy, Aggregate Industries’ director of sustainability, said: “We are delighted to be working with LiuGong and that we are the first customer in Europe to be deploying this all-electric vehicle.
“We have worked closely with the manufacturers to get the specification and testing right and it is routinely delivering a 10-11 hour shift on full-charge and will be a real asset to our operations.
“Aggregate Industries has a clear direction of travel for how we intend to reach zero emissions before 2050, and as a business that has a lot of vehicles and burns a lot of fuel, electrification of our fleet is a key part of that overall strategy.
“Change begins small and then gathers pace, and we will be rolling out further electric vehicles across the business during the rest of 2023 and 2024 as we move towards low- or zero-carbon fuels or energy sources.”
LiuGong's Keates added: “Working with Aggregate Industries has helped LiuGong to deliver our message of productivity and efficiency with reliability.
“This is a journey that began in 2018 for LiuGong, and we continue to grow and expand our electric fleet of vehicles. More and more companies can now see the benefits these machines bring to businesses. Through LiuGong’s iLink Telematics, companies are seeing real benefits which are helping them achieve the ambitious targets that have been set by the Government.”
A second LiuGong 856 HE is due to be delivered to Aggregate Industries before the end of the year. The first 856 HE currently operating at Bow will then be moved around other Aggregate Industries sites in the UK.
Aggregate Industries launched its Journey to Net Zero Strategy in May this year, outlining how it plans to reach zero emissions before 2050.
Remaining with LiuGong, the manufacturer exhibited its new 52-tonne 952F excavator prototype at the steinexpo quarrying equipment show in Germany.
James Higgs, product specialist at LiuGong Europe, said the machine has
been specifically designed for the European quarrying and demolition sectors.
Two prototypes of the 952F excavator are being tested - one at an aggregates recycling facility in Berlin and the other with a LiuGong customer in the UK.
In addition to Europe, LiuGong says the machine suits North American customers. Powered by a 282Kw Cummins X12 engine, the machine could be on the market as early as Q1 2024.
Volvo Construction Equipment (Volvo CE) L60F, L70F, and L90F wheeled loaders for Middle East and Africa customers are being upgraded to the H-Series generation with Tier 3 engines this year, ensuring customers get the same powerful and reliable operation as before but with several additional benefits. The new models will, says Volvo CE, increase operator comfort, lifting capacity and fuel efficiency while reducing service costs and wear and tear, resulting in a smooth operator experience on almost any job site.
With this series upgrade, the Volvo L60Gz and L90Gz models will be phased out by the end of 2023.
The H-Series wheeled loaders boast a brand-new look and feel and several performance-enhancing upgrades that can be boosted further when paired with a wide range of optional equipment.
Some of the most noticeable improvements are as much to do with the machine itself as they are to do with the experience of operating it.
Those stepping inside the cab are set to enjoy a much more comfortable and productive work environment thanks to new features such as Rimpull Control, which allows operators to adjust the wheeled loaders’ rimpull to match slippery ground conditions, thereby reducing wheel spin and wear and tear, additionally resulting in better fuel efficiency.
The H-Series’ Smart Control also balances the energy flow between the hydraulic and the drivetrain systems, providing the right amount of power for exactly where and when it is needed.
In addition, the upgraded wheeled loaders come with an electrically opened engine
hood, slide-out coolers and quick oil change connectors, providing better access to service points and making maintenance routines simple and hassle-free.
Meanwhile, a new optional lock-up torque converter helps increase productivity and fuel efficiency in load and carry applications while reducing operators' fatigue and increasing site productivity.
Another fuel-saving feature is the Eco pedal. When pressing down on the gas pedal, operators will sense a light pushback, indicating they are at the top limit of the economic working range for the engine rpm. Operators then have a choice to stay in this range – and therefore operate most economically – or push beyond this limit if required.
All these new functions allow operators to work smarter, not harder, all the while ensuring the maximum uptime for site productivity and greater fuel efficiency.
Customers looking for further uptime can choose from Volvo Services, such as On-Board Weighing and Volvo Co-Pilot, which allow the H-Series to perform accurately, productively and safely.
The upgraded wheeled loaders can be fitted exactly to customers’ varying needs thanks to a complete range of options and attachment coverage.
Develon, formerly Doosan Construction Equipment, has completed the launch of the 19-strong latest generation ‘DX-7M’ range of tracked excavators from 2 to 53 tonnes for Tier 2 and Tier 3 markets worldwide. The new excavators are designed for various markets, from construction, rental, recycling, waste processing and utilities to mining and quarrying.
The range models are: the DX27Z-7M and DX35Z-7M 2-3-tonne miniexcavators, DX200A-7M, DX210-7M, DX220LC-7M and DX220AF-7M 20-22tonne crawler excavators, DX225LC-7M and DX225LCA-7M 22-tonne crawler
excavators, DX300LC-7M, DX300LCA-7M, DX360LC-7M and DX360LCA-7M 31-37tonne crawler excavators, DX400LC-7M, DX450LC-7M and DX450LCA-7M 41-45tonne crawler excavators, and the DX490LC-7M, DX490LCA-7M, DX530LC-7M and DX530LCA-7M 49-53-tonne crawler excavators.
From the smallest model in the range, the DX27Z-7M 2.8-tonne mini-excavator, to the largest, the DX530LC(A)-7M excavators, the ‘DX-7M’ models are all said to offer significantly improved performance compared to the previous-generation machines. This is due to many enhancements, including more powerful engines and new higher-flow hydraulic systems.
The DX200A-7M 20-tonne excavator and all the larger excavators from the DX300LC(A)-7M upwards incorporate Develon’s Virtual Bleed Off (VBO) cuttingedge technology. The VBO system utilises an electronic pressure-controlled pump within a closed-centre hydraulic system for claimed productivity increases of up to 17% and claimed fuel-efficiency improvements of up to 32%, depending on the model and the mode selected. The closed-centred main control valve minimises pressure loss, while the electronic pressure-controlled pump manages and optimises engine power more effectively.
Improved feedback to the operator through the joystick results in enhanced machine control and less operator fatigue. The acceleration and deceleration of the excavator workgroup functions are smoother, allowing operators to perform repetitive swinging and digging motions with less jerking movements.
Another feature of most models from 20 tonnes and above that contributes to decreased fuel consumption is the advanced Smart Power Control (SPC) system from Develon. The SPC system controls engine RPM automatically to supply the appropriate
An aerial view of BKT’s Bhuj facility torque, depending on workload and speed, to ensure the best fuel efficiency.
The completely redesigned cabs on the DX-7M excavators provide maximum comfort and total control of all aspects of the equipment. Several ventilation and air conditioning options are offered to meet any additional needs.
Enhanced safety is also ensured by the seat-belt warning alarm system and the AVM (around view monitor) system, designed to prevent accidents caused by blind spots.
Other comfort aspects of the new cabs include a new interior with a dark grey base for a modern look, upgraded heating and ventilation functions for the operator, an eight-inch touchscreen monitor for intuitive operation, a DAB audio (handsfree, Bluetooth), a choice of fabric seat with heating function or leather seat, multipurpose cup holder and storage availability, an ergonomic footrest (reduced ankle fatigue), LED cab lights, and a rear sun visor.
The DX200A-7M and DX220AF-7M models have additional reinforcement for claimed exceptional off-road performance. Every key component meets Develon’s global standards. In the DX200A-7M, the hydraulic components and the engine tank have been strengthened, and the robust frames and structures are designed to stand up to the rigours of tough workplaces. Similarly, the DX220AF-7M is fully armoured from top to bottom to help maximise uptime on all types of extreme terrain, including forestry work.
Another important feature of the newgeneration Develon excavator range is the installation as standard of the latest version 3.0 of the Develon Fleet Management system, which provides a telematics management system by collecting data from sensors on the machines. The DX27Z-7M mini-excavator is now the smallest model in the DEVELON range with the successful Develon Fleet Management system. AB
A close-up look at driverless hauling, a mobile haul-road dust-suppression water truck from the world’s biggest off-highway machine manufacturer, and a top articulated dump truck manufacturer is a big draw at a popular industry exhibition. Guy Woodford reports
US-based technology company xtonomy says it provides the most advanced next-gen autonomous solution for mining and quarrying. In collaboration with Germany’s Bell Equipment distributor, Kiesel, the firm recently illustrated its claim by demonstrating its fully operational autonomous haulage system (AHS) on a Bell B40E articulated dump truck (ADT) at steinexpo 2023, staged in Europe’s largest basalt quarry in Homberg/ Nieder-Ofleiden in the central Germany state of Hesse. Attendees at the five-day event (24-28 August) watched the articulated hauler making driverless cycles around the Quarry Vision area.
After many years of development, xtonomy AHS for trucks is now transitioning to full production. It is designed for smaller truck fleets that the excavator or loader operator may fully operate. Although the autonomous trucks automatically follow the excavator position on the bench and adapt the queuing position, cusp point and loading position automatically, the operator can adapt all points to assist the process further. No additional personnel are required to supervise the fleet, as all underlying processes are fully automated. Robust radar onboard mapping and object detection continuously monitor the environment. At the same time, motion planners freely plan the best routes and dynamically react to
xtonomy’s AHS on a Bell B40E ADT at steinexpo 2023. Pic: xtonomy
changes instead of driving from one fixed point to another on virtual rails. Furthermore, xtonomy AHS handles the interaction of multiple trucks in such unstructured environments. This is only possible, the company says, through autonomy at the highest system levels.
Several safety layers .guarantee dependable operation via radio communications, high-precision GPS, radar and ultra-wideband (UWB) localisation. Manned machines may be integrated into the ecosystem for safe interaction in complex scenarios.
Furthermore, the xtonomy autonomy system does not require uninterrupted coverage of high-bandwidth comms throughout the mine site. This dramatically reduces the system implementation effort.
Properly watered haul roads directly impact fleet cycle times and the ability to meet production targets. As haul-road dust affects safety and productivity at mines and quarries, the water truck is one of the site's most important support equipment. The new Cat 777 (05) Water Solutions Truck provides an integrated solution to help reduce haulroad dust by solving overwatering and underwatering issues.
The new 777 (05) is built on the Cat 777E truck platform, proven at mine, quarry and construction sites globally. An innovative truck that uses less water for controlling haul-road dust, the design integrates the
truck, tank, and water delivery system, connected with technology. Its Cat Water Delivery System (WDS) combines with Cat MineStar Edge connectivity to help operations manage the site more safely and productively with flexible levels of technology to meet site needs.
Boasting a 75,700-litre Cat-branded water tank, the 777 (05) has a spray system, splash guards, fill chute and rock ejectors. It is powered by the 765kW Cat C32B engine that meets China Nonroad Stage III emission standards, equivalent to U.S. EPA Tier 2.
The new water truck’s exclusive Cat WDS features a self-contained hydraulic system that controls spray patterns independent of engine RPM for consistent watering. Based on the truck’s speed, variable water flow automatically starts and stops when the truck slows or comes to a halt, preventing overwatering and subsequent poor traction at road intersections. The pump features soft startups and automatically shuts off when the tank is empty to prevent system damage.
WDS components include a water cannon, oil cooler, variable displacement pump, hydraulic oil tank, electronic control boxes and hydraulic motor/water pump. Covering up to a 24-metre wide road in a single pass, the system sprays at rates reaching 0.8 l/m² at speeds from 4 to 40kph (3 to 25mph). With its maximum 61-metre-spray distance, the truck’s water cannon offers a maximum flow rate reaching 4732l/min.
Factory-installed, ergonomic water controls are integrated into the truck’s design for convenient operation. Its innovative automated water delivery feature enables the operator to focus on driving and site traffic to enhance safety. Complete with auto shut-off to prevent overfilling, the water tank is filled remotely, allowing the operator to remain inside the cab during the cycle to reduce potential operator slips and falls.
Flexible levels of the cloud-based MineStar Edge technology are integrated with the Cat WDS to collect and communicate machine data, allowing site supervisors to monitor the water truck to know where and when it’s spraying water. Asset management options include productivity, water usage, fuel and water tank levels, when and where to apply water, geofencing, asset location, and remote management of water distribution.
Providing tracking capabilities without infrastructure investment, Edge Equipment Tracking delivers basic connectivity without interfering with existing fleet management systems. Helping to achieve a lower total cost of ownership, Equipment Tracking provides insights to help mines better manage their assets. It features service meter readings, fuelling and recording data, location accuracy and replay, time utilisation tracking with downtime and operator tracking, automatic stoppage measurement, and health event recording.
Paired with Equipment Tracking, MineStar Edge Production Recording delivers premium connectivity with an accurate and automated near-real-time measurement solution that reports on every aspect of the watering cycle without requiring operator input. Giving visibility to the entire operation it helps to discover opportunities for improving productivity. This premium package also includes water usage by truck/fill station, volume and rate of water put down over time and area covered, water delivery system setting by location, truck, and conditions, activity breakdown with time and distance –watering, not watering, stopped, etc.
The Cat dealer and parts network fully supports this integrated system with Cat-branded tank options. Covered by the Caterpillar factory standard warranty, the water truck, including the tank and components, is eligible for Cat equipment protection plans (EPP) and customer value agreements (CVAs). Cat dealer installation of the integrated system is available, and retrofit kits for existing Cat 777E truck platforms in the field have planned availability in the future.
Rokbak’s RA40 articulated hauler was showcased at this year’s Maxpo (31 August – 2 September), Finland’s largest exhibition of land construction and environmental maintenance machinery. Visitors got a close-up look at the RA40, courtesy of Kivisampo, Rokbak’s trusted dealer in the Nordic nation.
As a biennial global exhibition, Maxpo presents ‘the biggest and greatest machines’
to almost 10,000 visitors at Hyvinkää Airfield, approximately 40 miles (60km) north of the Finnish capital Helsinki.
Kivisampo has been attending Maxpo for two decades. This is the first time a Rokbak hauler has been exhibited at the event since the rebrand in September 2021. The rebrand followed huge investments and improvements after the Volvo Group’s 2014 acquisition.
“For us, Maxpo is a big deal,” explains Kivisampo sales director Sakari Rantanen.
“It’s the time of the year when the customers come to you instead of the other way around. We’re delighted to present the truck to the masses. Rokbak is still a relatively new brand, but, especially in the Nordic countries, Volvo is a name on everyone’s lips, and the truck’s Scania engine is very well-liked.”
Featuring a 75,700-litre Cat-branded water tank, the Cat 777 (05) has a spray system, splash guards, fill chute and rock ejectors. Pic: Caterpillar
In the first half of 2023, the Nordics accounted for 16% of the European market for ADTs. This is a 52% increase in share compared with 2022. In the Finnish market, the over 35-tonne class is the largest sector.
The RA40 has been on demonstration in Finland and was introduced to the wider market at Maxpo. Arriving in a straightto-the-point sand-coloured palette, the 38-tonne RA40 is a heavy-duty articulated dump truck that makes light work of largescale quarry, mine and construction jobs. Offering reliability and performance, the RA40 delivers cost-effective productivity in the toughest conditions and roughest sites, from quarries and infrastructure developments to commercial construction projects. AB
Italian attachment specialist Indeco is adapting to a changing construction and quarrying industry marketplace with big growth plans for its product range and customer support. Aggregates Business editor Guy Woodford caught up with Michele Vitulano, Indeco’s global sales and marketing manager, at this year’s SaMoTer and co-located Asphaltica exhibition in Verona to get the full picture
Michele Vitulano is his usual quick-witted and colourful self as we sit down to talk during the early stages of the 31st edition of SaMoTer and co-located Asphaltica (3-7 May 2023).
He highlights a growing demand for attachment products compatible with smaller-sized excavators, with the company looking to increase its range in response to this market trend. “We already have breakers from 60 kilograms to 11,000 kilograms, so we are talking about pulverisers, demolition crushers, mulching heads, and grabbers. We are growing these ranges going down and are very close to launching a 150-kilogram grabber. We will also have 900-kilogram and 500-kilogram demolition crusher attachments out very soon.”
Vitulano notes that Indeco benefited from a particularly strong performance in North America in 2022, where the Bari, Puglia-headquartered company enjoyed its best-ever sales year at just under $50mn. Indeco North America is now looking to expand its Milford, Connecticut facility to
meet the strong demand for equipment. The site also manufactures several items, such as mounting brackets for hydraulic hammers and compactor attachments.
“Our Milford premises is huge, and from it, we can deliver 98.5% of requested parts within 24 hours,” emphasises Vitulano.
“We can also deliver spare parts from there to customers in Canada, Mexico, Peru, Colombia and Chile.”
Vitulano says he is also looking for a suitable business to add to Indeco’s portfolio.
“We are looking to add another product to our basket. The choice is always to start the product from zero like we did with our steel shears or buy a company already producing them as we did with our mulching heads. We are watching some European and US companies and have our eye on several possibilities.
“Indeco is financially really strong. That is why we don’t use any bank financing. We reinvest all our profit as we are doing with our new €8 million Bari production plant. It will be used for welding and cutting of what we call silent demolition tools, like pulverisers and steel shears. It will also be used to produce the casings for our hammers. This plant will easily double our production
capacity. We will take on more people and have more robot stations for better efficiency. The space used before in our main premises for metal carpentry will increase our semifinished and spare part inventories. The latter will help our dealers offer even better service to customers. I hope this new plant starts operating in June.”
A global employer with 240 employees worldwide, Vitulano says that in December 2022, Indeco responded to its workers’ concerns over rising energy and other living costs by raising salaries by around 10%. “At the end of the day, a company succeeds through the efforts of its people,” he stresses.
Indeco has made its first sales of breakers in Japan, a significant success given the strength of Japanese hydraulic breaker firms in the home market. Improving construction and mining customer demand in Australia is also good news for the company, which has distribution and service premises in Melbourne and Sydney.
The first manufacturer to launch the smart hammer on the market in 1985, Indeco is among the first to offer a range of hydraulic attachments with 4.0 technology. This is thanks to the new remote-monitoring system Indeconnect, based on the principles of the Internet of Things, to prevent equipment obsolescence and maintain optimum performance over time.
Indeconnect consists of a proprietary device to be mounted on various equipment, provided with 4G technology for wireless interconnection to the network and a cloud-based web platform accessible from mobile (via app) or PC, with which to consult the data transmitted in real time by each installed device: hours of work performed, working position in space, hydraulic oil temperature, ambient temperature, and GPS location.
Returning to Indeco’s trading priorities, Vitulano says: “The challenge over the next year will be to increase our attachment product efficiency even further as construction machines become increasingly electric powered. Our hammers have a fuelsaving system. Our hammers require 18-19% less oil than comparable attachments to do the same work on the same excavator. A gas-powered hammer has an efficiency of 55%; our hammers have an efficiency of between 65 and 70%. If a hammer requires less input energy from the machine carrier, then greater output energy can be generated by the hammer. It lowers the carrier machine’s engine RPM, reducing gas consumption and customer fuel costs.
“An excavator’s fuel cost, right now, is a lot of money. We were doing some calculations at a huge quarry in India that primarily treats construction and demolition waste and turns it into gravel. We reviewed the customer’s 100-tonne excavator and hammer operating and maintenance costs, then looked at the fuel cost and said, ‘My goodness. It is five to six times all the other costs.’ Talking to your customers and learning from your markets is important.”
Commenting further on Indeco’s key sales markets, Vitulano says: “We generate most of our sales in Europe and the US, so we are reinvesting some of our profit into offering even more to customers in those markets. For instance, I remember years ago when we invested significantly in Indeco UK, near Manchester in England. A colleague expressed concern over the investment size, but I said, ‘No, we must invest to employ more people and to have a better workshop and offer a better service.’ It is important for a company to put money back into the markets that have enabled it to grow. We put passion into what we do and love our customers.”
Vitulano comments on Indeco’s trading in China and Southeast Asia: “We sell big steel shears and hydraulic hammers in China. Unlike in China and South Korea, the European community has no agreement with Southeast Asian countries regarding zero [export and import] duties. A hammer going to Indonesia from Europe has 14% more duty to pay than if it was imported from China or South Korea. That means selling our products in Indonesia and other Southeast Asian countries costs much more. We are trying to do business in important markets like that, but it is difficult.” AB
“It is important for a company to put money back into the markets that have enabled it to grow”
Michele Vitulano, Indeco
A surface drilling team in the Czech Republic provides first-class drill and blast services to quarries nationwide after purchasing a new fleet of Epiroc equipment. Guy Woodford reports
Some years ago, the Fospol division of Explosia decided to renew its fleet and has since been continually phasing out its older drill rigs and replacing them with modern equipment. The company currently has six drill rigs, three of which are from Epiroc, including the top-ofthe-range SmartROC D50 MKII. It aims to boost its capacity to five Epiroc rigs by yearend 2023.
These SmartROC T40 MKII rigs are equipped with the Hole Navigation System (HNS) and are expected to be delivered in the second half of 2023. In addition, the whole fleet will be backed up by Epiroc’s ROC Care service and maintenance contract, which includes regular service inspections using Epiroc’s RigScan scanning technology.
Prˇemysl Gromada, head of the FospolExplosia Drilling Group, points out that when the first SmartROC D50 arrived in the Czech Republic, it represented a milestone for Explosia.
“It was a DTH [down the hole] rig unlike any other in the whole country, and it was a great success for our company,” he says. “It felt like a reward for a job well done in terms of the company’s modernisation and investment plan.
"Since then, we have increased our productivity by about thirty per cent, not only due to the modernisation of the fleet but also to the replacement of personnel in drilling positions."
The Epiroc fleet performs well in the hard rock quarries of Litice-Plzenˇ, achieving penetration rates of 0.3-0.5 m/min, as well as in the softer limestone quarries of Velké Hydcice, where the average penetration rate is 1.3 m/min.
With tophammer drilling, the rigs drill 89, 95 and 102 mm diameter holes and 100 and 105 mm diameter holes with DTH drilling. The holes are normally drilled to depths of 15–20m.
Gromada says a hole of 15–29 metres is completed in 30-60 minutes, much to the drillers’ satisfaction.
He continues: “As our previous rigs were about 15 years older than the latest models, our drillers see improvements on almost every level. But they probably most value the automatic processes, such as full drill cycle automation DTH, tophammer rod extraction assistance, remote control and the Hole Navigation System.
“This high level of automation eliminates interventions by the driller and accelerates the whole drilling process.”
The drillers look forward to achieving efficiency gains with features such as one-hole automation and the Hole Navigation System (HNS). However, the company says it is early days, and the full
benefits will not be fully realised until 2024. However, performance monitoring using the Epiroc Certiq system has already proven its worth.
Gromada says: “We have been using Certiq since the autumn of 2021 when we purchased the Epiroc SmartROC T40 and T45 drilling rigs, which was a big change for us. It was a move towards more efficient monitoring of production and simplification of records.
“This gave us a much better overview of inputs and outputs of individual drilling rigs, which made calculations easier for us.”
The same can be said of the My Epiroc application, which Explosia also adopted into its drilling operations in the second half of 2020. This tool, Gromada points out, has been particularly helpful in production
monitoring and planning of regular service activities.
In addition, the company has noted significant improvements in overall fuel consumption. The average consumption of diesel using the previous Epiroc ROC L6 drill rig was approximately 1.9 litres per drill metre.
With its replacement, the Epiroc SmartROC D50 MKII, its 2023 fuel consumption averaged 0.96 litres per drill metre – almost half. Currently, the monthly savings on diesel average about 3,000 litres.
In the past, due to its ageing fleet and lack of repair and maintenance services, Explosia has urgently and regularly had to request assistance from its competitors to complete drilling projects, but not anymore, explains Prˇemysl Gromada.
“The situation has changed significantly over the last three years, and this is the first year that we can offer drilling work to companies in the Czech Republic who unexpectedly get into a situation where they cannot meet deadlines.
“Fortunately, Explosia realised in time that without modernisation and investment, it would not be possible to continue fulfilling our existing or future obligations, let alone be a full-fledged competitor to other companies in the drilling business. The drilling quality is completely different now and much better.”
drill rigs, the drilling team has reduced fuel consumption by 30-50%.
Přemysl Gromada, head of the Explosia Drilling Group. Pic: Epiroc
“The drilling quality is completely different now and much better”
Pr emysl Gromada, Fospol-Explosia Drilling Group
In terms of all its operations, Explosia is a company with a comprehensive sustainability policy. By commissioning the new Epiroc
“Whether it concerns raw materials, energy, production or any other resource, sustainability is important for everyone,” continues Prˇemysl Gromada, who proudly claims a strong personal commitment to environmental protection.
FreeFlow™ is a fully mobile washing solution for aggregate and sand classification with integrated water recycling, ideal to: •access difficult locations •move from one site to another •facilitate planning & authorisation
“Epiroc has helped us by significantly reducing exhaust fumes, primarily as the new rigs have better fuel consumption than the old ones, and lowering emissions further through AdBlue. So, I can see that over the last four years, Explosia has significantly shifted ecology towards conservation and more consideration for nature.” AB ENGINEERED FOR YOU.
Indian off-road tyre giant BKT, Balkrishna Industries, recently invited the world’s trade media to its state-of-the-art site at Bhuj in Gujarat to showcase the group’s exciting plans for the future. These include a doubling of the company’s turnover to US$2bn by 2026 and an increase in annual tyre production to 600,000 tonnes. Guy Woodford reports
Speaking at BKT’s newly acquired 65-acre site, just a short distance from the company’s main site at Bhuj, marketing and communication manager Gabriella Usiello outlined the company’s plan of action.
This will include a second carbon-black production facility dedicated to external sales, a second power plant to supply the significantly enlarged operation and an assembly line making rubber tracks for agricultural machinery.
“We are incredibly proud of this new acquisition and the growth opportunities it offers BKT. We are constantly looking for ways to improve and grow. This additional land is going to be another game-changer for us, giving us more room to expand our production capabilities and take our operation to the next level,” she said, adding: “We are confident that with this new site, we will continue to produce the highest quality products and meet the demands of our customers.”
Usiello’s speech followed an extensive tour for the assembled media of the facility which will employ more than 4,770 workers. The vast site is more like a village, complete with growing onsite accommodation for employees and their families. There are shops, a school, medical services, and sports and other recreational facilities. By the end of next year, 1,240 employee families and 400 single men will be living at BKT Bhuj. Work on the site is expected to be completed in 18 months to two years.
Day two included a press conference at The Trident Hotel in Mumbai focusing on the trip’s theme, Enter the Future. The media party heard from a number of top
BKT executives, including chairman and managing director Arvind Poddar and joint managing director Rajiv Poddar.
“In our future, BKT will double its turnover. In our future, the combination of production, distribution and brand promotion will allow us to achieve new standards,” said Arvind Poddar.
“People have asked me if all this was really necessary … so much in such a short time. The goals we set ourselves when we decided to open the Bhuj site were proportional to the financial solidity of the time but above all to a vision which is as great as it is concrete,” said Rajiv Poddar.
“Growth has always been in step with demand. Global tyre demand is growing, and
we see no signs of it slowing down over the next five years. This demand started to rise during the 2020 pandemic, which today is above pre-Covid levels.
“The journey we started out on at Bhuj in 2012 was never a return journey, but one to prepare ourselves to discover the future.”
BKT’s 25” to 57” off-the-road (OTR) tyre range supplies many industries, including construction, quarrying, mining, industrial, earthmoving, ports and agriculture. The company has more than 10,000 employees and offers a staggering 3,200 products in 160 countries across five continents. With its global headquarters in Mumbai, the company has three subsidiaries: BKT Europe in Seregno, near Milan, Italy – which has a
10% share of the continent’s OTR tyre market; BKT USA in Copley, Ohio; and BKT Tires in Toronto (Canada). There are six production sites in India, one in Bhiwadi, Chopanki, Dombivli and Bhuj, and, since autumn 2021, two in Waluj, a large village located to the west of the city of Aurangabad in the central part of Maharashtra state.
BKT’s consistent investment in digitalisation and automation at its current Bhuj site has increased production speed, volume and final-product quality. The amount of product discarded has been reduced, increasing the sustainability of the manufacturing process and reducing production costs.
Processes are also becoming increasingly reliable, and most importantly for BKT, occupational health and safety risks have been drastically reduced, and worker comfort improved.
The extended facility, including the new fully digitalised carbon-black plant dedicated to external sales and the stateof-the-art rubber-tracks assembly line, will meet significantly increased market demand for these products. It is anticipated that 5% ($100mn) of BKT’s targeted $2bn annual turnover by 2026 will be generated by carbon-black sales with the 198,600 tonnes earmarked for tyre tread production in 2023 predicted to rise to 500,000 tonnes per year by 2026.
Moving the rubber-tracks assembly to a new purpose-built site will free up space to allow BKT to increase its off-the-road tyre output at times of higher customer demand.
Carbon black is produced by a hydrocarbon fuel [gas or oil] reaction to limited combustion air at temperatures of 1320 to 1540°C. The unburned carbon is collected in an extremely fine, fluffy, black particle, 10 to 500 nanometres (nm) in diameter, and this ‘carbon black’ is used to strengthen the tyre rubber compound.
BKT Bhuj’s carbon-black plant began operating in 2017 with 65,000 tonnes of hardgrade carbon black for tyre treads produced in that year. In the following year, production increased to 110,000 tonnes. The production of soft-grade carbon black started in 2018. This is used in the casing compound to improve strength and durability, generating less heat. In 2021, the total production of the two types of carbon black reached 138,000 tonnes per annum, while last year, it rose to 165,600 tonnes. The goal for 2023 is 198,600 tonnes. BKT Bhuj’s research and development centre plans to add a third ‘speciality’ type of carbon black, which has different properties to the carbon black used in rubber compounds. These properties offer high resistance to colouring, a high purity level, a low ash level and a very low level of PAHs. This makes speciality carbon black suitable for specific applications such as paints, plastics and inks.
BKT has also introduced a new approach to carbon-black production, making the whole process more sustainable. For carbonblack transportation, BKT substituted
bulk bag containers with mobile silos. This means that the tyre-production plant receives the carbon plant using mobile silos transported pneumatically to the storage. This will eliminate the need for BKT to use 100,000 bulk bags over the next few years. Furthermore, the whole transport system is designed to reduce energy usage and consumption. Every transfer system is controlled by weight and energy used – with BKT aiming to reduce energy consumption by up to 70%. This will save more than two million kilograms of CO2 emissions annually, comparable to the emissions rate of 5,000 100m² apartments.
At the same time the gas used to manufacture carbon black is now ending up in a co-generation plant able to reuse 75,000m³ of gas per year. This saves 215,000 tonnes of coal per year.
BKT Bhuj’s power plant became operational in 2013, giving the site a reliable and controlled source of electricity. Today, solar panels and the cogeneration plant allow the facility to produce its own energy. Last year, the cogeneration plant was expanded from 20MW to 40MW per year, and work is underway to increase the power generated by self-produced renewable resources.
Water is also at the heart of BKT Bhuj’s power-plant sustainability. Since 2019, a zero-liquid discharge (ZLD) principle has been adopted, meaning no liquid waste is released outside the plant. All water used in the plant is treated, purified and reused. The objective of the ZLD principle is to conserve water resources, reduce the environmental impact of wastewater discharge and improve the plant’s overall efficiency and sustainability.
When the first tyre rolled off the Bhuj production line in 2012 following a $500mn investment, the plant was located across 123 hectares. Before starting the works, the landscape was completely arid with neither water nor electricity. After laying many kilometres of drinking-water pipes and power lines the site grew exponentially: 126
A BKT employee inspecting a giant BKT off-the-road tyre at the company’s state-of-the-art facility in Bhuj, Gujarat
hectares in 2016, 131 in 2019, 137 in 2021, and 258 in 2022. By the end of 2023, it is forecast to reach a total surface area of 323 hectares, of which 283 acres have already been acquired.
More space provides the possibility to install new machines, accommodate more test areas, and increase volumes and all that goes with it. From 92 tonnes of daily production in 2015, BKT Bhuj ended 2022 with its best result ever - 436 tonnes daily. This is timely as BKT’s business has, as Rajiv Poddar noted in the Mumbai press conference, increased by 49% compared to the pre-pandemic period. This remarkable achievement reflects the Indian multinational’s readiness to embrace new opportunities and challenges.
BKT spends 3.5% a year of the company’s turnover on research and development (R&D). Its R&D Centre is said by the company to be the “cradle which allowed the Bhuj site to grow into what it is today”. Established in 2017, this hub develops products and processes to ensure BKT can maintain its leadership in the international off-the-road tyre market. Led by a specialist team of researchers and analysts, it remains one of the world’s most important and up-to-date tyre research centres.
Finding the right solutions requires testing. For this reason, a special test track was inaugurated in the R&D centre’s first year. With six different tracks, this circuit includes tracks for tyre-performance tests in both dry and wet conditions, an asphalt track and a sloping concrete track. Thanks to a wide variety of tests, many important characteristics such as traction, handling, comfort, soil compaction, and much more, can be measured here, thanks to highprecision devices and instruments.
Having seen the vast BKT Bhuj site firsthand and after listening to BKT’s senior management team lay out the company’s hugely ambitious plans for growth, few would bet against such a vision becoming a reality in 2026. AB
the toughest operating conditions: from mining to construction sites.
Sturdy and resistant, reliable and safe, able to combine comfort and high performance.
BKT is with you, even when work gets tough.
Italian companies Tecnoidea and Ma-estro have collaborated on the new W-Portal automated control system for water- and sludge-treatment plants, which enables both increased sustainability and cost savings. Liam McLoughlin reports
Tecnoidea Impianti SRL has developed a new automated production control system for water- and sludge-treatment plants in collaboration with fellow Italian company Ma-estro. The system, which is a Tecnoidea product powered by Ma-estro, is to be called W-Portal – with the W standing for Water. It features a web app and portal where both Tecnoidea and the plant operator can log in to check and extrapolate all the plant data.
“The system enables the complete control of the treatment plant by maximising production efficiency and minimising production costs,” says Marco Doniselli, project engineer at Tecnoidea.
He adds that the two main aims of the automated control system are to enable increased sustainability and cost savings. “These aims are reached by tracing process parameters (energy consumptions, CO emissions, environmental data) and implementing automatic actions,” he says. “For example, based on the quality of the input material you can adjust water fl and therefore save energy.”
The system is designed to enable predictive maintenance and the optimisation of spare parts use with less wastage. It also provides the ability to do scheduled, and therefore less frequent, planned downtimes.
Doniselli says that the soil-washing and water-treatment processes are often regarded as being two different entities which are unrelated and unable to communicate.
“We believe the innovation in our new system is that it treats these two processes
as more of one single 360-degree industrial process,” he adds.
Both companies are bringing specific quarry-industry expertise to their collaboration. Ma-estro has developed an advanced system for tracing, managing and controlling entire plant processes at quarries. It provides its quarry customers with tools for identifying plant inefficiencies. Tecnoidea has strong expertise in enabling water- and sludge-treatment turnkey solutions.
“Together our combined expertise enables water- and sludge-treatment plants to be capable of achieving 100% of their operating performance and optimising production costs,” says Doniselli.
The two companies have previously
prototype of the integrated system has been developed for Beton Lana, a constructionmaterials company in northern Italy. The washing plant handles 220 ton/h input material, with 400 m3/h water and 15 ton/h dry solids to the filter press.
The new automated production control system will be available as an add-on package to new and existing Tecnoidea plants. The system will be able to communicate with the PLC (Programmable Logic Controllers) of the washing plant when this has been designed by Ma-estro.
The system is currently undergoing testing, and the plan is to go live with making it available globally to customers in January 2024 in any location that has an internet connection.
Tecnoidea was founded in 1981 and since then has deployed around 2,000 water- and sludge-treatment plants around the world, with more than 1,000 of these being at quarries. “Quarrying is the most important part of our business,” Doniselli says.
Tecnoidea’s plants are also used beyond the quarrying sector. One of the most eye-catching projects it is involved in is connected to the 2026 Winter Olympics which will be held in Milan and Cortina d'Ampezzo. As part of the construction project for the event, Tecnoidea has provided a soil-washing plant in the Santa Giulia district of Milan. This is improving the poor soil quality in the area by washing a total of 1,000,000-tonnes over the next three years and restoring it into the ground to enable new building to take place. Santa Giulia is the location for a new 16,000-capacity area where the ice hockey tournament will take place. Poor soil quality in the area has previously been a barrier to new buildings being constructed. The washing plant handles 200 ton/h input material, with 600 m3/h water and 40 ton/h dry solids to the filter press.
Europe is the main market for Tecnoidea’s plants - specifically central Europe including Italy, Switzerland, Germany and Austriawith the support of the company’s strategic partner metcam. Swiss-based metcam has played a major role in the deployment of a Tecnoidea mud-slurry treatment plant at the Gloggner company in Perlen, Switzerland. The washing plant (2 lines) handles 20 ton/h drilling mud and 15 ton/h road-sweeping material, with 150 m3/h water (each line) and 10 ton/h dry solids to the filter press (each line). Tecnoidea plants have also been deployed in France, the UK and other countries around the world.
things are always going on at Tecnoidea and we do not stand still. We are always trying to improve our machines and products. An important new feature of 2023 is the new pump-testing facility where the most advanced technologies have been employed to test our ABRA POMPE with the aim of granting the highest performance.
In terms of the company’s future plans and innovations, Doniselli says: “A lot of
“In my three years at the company I have seen its plans getting bigger and
more complex, but to the end customer the products and the PLC architecture seem even simpler.
“In between there is a lot of work around automation. We are trying to introduce automation even into the sub-features of our machines because we don’t want the operators to bother about anything, just to be concentrated on the final aim and let the machine do the rest.” AB
A newly-deployed Terex Washing Systems (TWS) filterpress is improving the quality of water treatment and water recycling at a quarry in North Wales
The Aberdo quarry at Pentre Halkyn is owned by CCP Building Products and produces quality limestone aggregates that supply the markets of North Wales, Cheshire, Lancashire, Liverpool and Manchester.
In late May this year the quarry started operating a Terex WS FP215 filter press, which features 1.5m x 2m filter plates, and an automated control system.
CCP Building Products says the TWS-supplied wash plant doubles the output from its quarry operation, working alongside the quarry’s current crushing process.
The washing plant allows the quarry to produce high-quality premium limestone aggregates in 10mm, 20mm, 40mm and 4/20mm sizes. The wash process also produces a quality manufactured 0/4mm
limestone sand that can be used in concrete production. Much of that material production is currently generated from the years of quarry overburden which had been stockpiled onsite as a ‘waste’ material and which the plant was designed to process.
Terex Washing Systems describes the installation at Aberdo as ‘Feeder to Filter press’ because all the wash-plant machinery and crushing and screening equipment at the site is designed, manufactured and supplied from Terex Washing Systems and its other sister brands. These include a Powerscreen Metrotrack jaw crusher at the front end, a Powerscreen Warrior 2100 scalping screen, a Powerscreen Premiertrack 1150 cone crusher, a TWS AggreSand 206 sand-washing plant, a TWS AggreSand 150 scrubbing plant, a TWS FDU (flocculant dosing unit) 5000,
TWS Rake thickener, buffer tanks and the FP215 Filterpress.
Fergal McPhillips, global business development manager for TWS, says that having all the plant from Terex-owned brands is a major benefit for the operator from a servicing and parts perspective as it is a ‘one-stop shop’.
“There is a lot of interest in this deployment around the filter press itself,” he adds. “Health and safety is very high on the priority list for our filter presses. It has stainless steel sliding isolation doors, and the automated maintenance and control system means it is user-friendly.”
More than 95% of the water in the watertreatment process at the quarry is recycled by the Terex WS system. The filter press and washing plant produce 20-tonnes of dry filter-
cake waste product which is put back into the quarry.
“The filter press is in place to recycle the maximum volume of water, minimise the water usage, and produce a dry filter cake that is easy to transport,” McPhillips says. “The recycled water is fed back into the washing process.”
CCP Building Products says that, from render and floor screeds to concrete materials and paving courses, the washed aggregates that the quarry produces have an array of uses.
“Their versatility, high quality, strength and workability make them ideal for all kinds of projects and uses, including the production of concrete, asphalt, drainage and landscaping projects to name just a few,” it adds.
Washed aggregates undergo a specialised process to remove impurities, such as clay, silt, dust and other unwanted particles, which can have a negative impact on the strength and workability of concrete, one of their key uses. The washing process also eliminates sulphate and chloride to meet the specifications for the British standard of sand used in concrete. By ensuring cleanliness and adhering to quality standards, washed aggregates provide numerous advantages over non-washed.
The firm took over a 50-acre quarry in the Kemerburgaz-Cendere region in 2015 to begin processing crushed sand and aggregates for its own concrete production.
Terex Washing Systems has a history of deploying similar filter presses across Europe and the USA, designed and manufactured at its HQ in Dungannon, Northern Ireland.
Turkish concrete producer Bogˇçziçi Beton has commissioned a new CDE wash plant to increase its output levels.
Established in 1997, Bogˇaziçi Beton has 28 separate concrete batching plants in Turkey pouring six million m3/year. In total, the firm has poured some 35 million m3 of concrete which has been used in major construction projects in Istanbul, including the new central bank, metro construction projects, highways and viaducts and high-rise buildings in the financial district.
The following year, Bogˇazççi Beton increased crushing-plant capacity at its Cendere quarry to 2,000tph, enabling the firm to process up to six million tonnes of crushed material annually.
In Kemerburgaz, where Bogˇçziçi Beton’s site is located, all quarries have natural sandstone which has a major waterabsorption problem in crushed sand.
With approximately 15-17% of 0–63micron content after crushing, Bogˇazççi Beton was producing methylene blue test results above the acceptable limits which resulted in higher production costs due to the need to add additional cement to the concrete mix.
Seeking to address this, Bogˇçziçi Beton engaged with wet-processing experts CDE to design and commission a plant to remove excess fines content in its sand and decrease
water absorption with the aim of achieving a lower methylene blue result in line with industry standards.
The issue central to Bogˇazççi Beton’s high methylene blue values is the integration of bucket wheels in the existing plant, which increase water absorption.
CDE commissioned a 220tph EvoWash 251 to help improve the quality of the product whilst also increasing outputs.
A compact, modular sand-washing system, CDE’s EvoWash screens and separates the smaller sand and gravel fractions through an integrated highfrequency dewatering screen, the hydrocyclone technology provides unrivalled control of silt cut points and eliminates the loss of quality fines.
The feed material is delivered to the plant dry, before being adequately fluidised. From here it is pumped to dual 500mm cyclones via an integrated slurry pump to remove minus 63-micron fines away from the product.
By removing the fines, the product has a maximum of 3% 0–63-micron content which dramatically changes the methylene blue quality measure of the material, aligning it with industry standard.
The EvoWash 251 was seamlessly integrated to efficiently process the fines material. The resulting output contains a
maximum of 2.5%–0–63-micron content, down significantly when compared to the output of the dry crushing process.
Japan-based water-pump manufacturer Tsurumi Pump exhibited a major display of its latest pumps, technologies and services at WEFTEC from October 1–4, at McCormick Place in Chicago.
Tsurumi displayed its newest line of wastewater submersible pumps, the AVANT MY Series, to the public for the first time. These pumps are built to the same standards under the Tsurumi AVANT™ line of explosion-proof, FM-approved submersible pumps. These durable pumps feature multiple impeller options and have an accessible price point.
“The MY Series is more of an on-the-shelf option and is designed for industrial and smaller municipal applications,” said Chris Bristol, municipal product sales manager at Tsurumi. “It’s an economic option for smaller manufacturing and municipal wastewater facilities. Our pumps are known to be very reliable and last for many years, but it’s good to know that on-the-shelf availability means quicker turnaround times for customers.”
Along with the MY Series, Tsurumi is introducing new FM-approved MMR Series submersible mixers, which feature built-in IE3 premium-efficiency motors. Submersible mixers are the most practical and efficient solution for mixing, agitating, homogenizing and equalizing wastewater at treatment facilities. They are used in aerobic as well as anaerobic and anoxic stages of wastewater treatment processes to prevent sedimentation and maintain constant concentration levels in the tanks.
US-based McLanahan has analysed which type of dewatering equipment is best for the management of tailings: a decanter centrifuge, a belt press, or a filter press.
All aggregate and mining operations with a wet-processing plant will produce a waste stream. This waste stream consists of tailings – the process water and fine solids, clay and other deleterious material removed during the washing process. Traditionally, these
tailings are sent to a settling pond or lagoon to separate the solids from the liquid in the waste stream.
However, McLanahan says settling ponds can be time-consuming and expensive to maintain, take up valuable land space and/ or cover up mineable reserves. They are not the best method for tailings management, especially when mechanical dewatering options are available.
It adds that mechanical dewatering equipment improves tailings management by separating the solids from the liquid to produce a solids product that is suitable for mechanical handling.
When it comes to tailings management, the best equipment for one site may be different than the best equipment for another site. Decanter centrifuges, belt presses and filter presses are all suitable choices for pond reduction/elimination, so the best one depends on the tailings management goals of the site.
The main thing to consider is the type of material being dewatered. Decanter centrifuges work best with material that has a larger particle-size distribution and is more easily dewatered. They are also ideal for material with low clay content, and they are less sensitive to changing feeds.
Belt presses can be used to dewater a variety of different slurries in a wide range of applications, but they don’t perform well with varying feed conditions.
Filter presses are ideal for dewatering tailings from mineral and aggregate wash plants, mineral concentrates and most underflow slurries coming from a thickener or clarifier. However, the feed percent of solids and particle-size distribution does have an effect on the overall dewatering efficiency of a filter press.
In terms of operational costs, decanter centrifuges and filter presses are fully automated, whereas belt presses require an operator.
Filter presses do not require the addition of chemicals to aid in dewatering, while belt presses do. Decanter centrifuges may benefit from the use of chemicals, but that depends on the material being dewatered.
In terms of capital cost, belt presses are generally less of an upfront investment when compared with centrifuges and filter presses. Additionally, filter presses require ancillary equipment, such as a surge (or buffer) tank.
Maintenance costs are higher with belt presses because maintenance intervals are more frequent than centrifuges and filter presses. Belt presses require frequent belt washing, and the rollers and bearings are known for requiring frequent replacement, which means more downtime to perform maintenance.
In terms of footprint, belt presses and centrifuges take up less space than filter presses.
McLanahan states: “When determining which solution is right for handling your tailings, make sure you consider the type of material the equipment will be processing as well as the initial investment and long-term operational and maintenance costs.” AB
Developing technologies and software solutions are making quarrying operations leaner and safer, and companies are bringing value-adding services to their digitalised solutions for blasting operations in the sand and gravel sector. Liam McLoughlin reports
EPC-UK successfully launched its subsidiary company EPC Metrics last year, and with it a team of experienced engineering specialists capable of offering technical support and services to improve blasting, site mapping and monitoring within quarrying operations.
Ryan Ward, commercial manager at the UK-based commercial explosives and drilling & blasting services provider, says that the technical and consultancy services provided by EPC Metrics are increasing the quality of data available to make informed decisions within the quarrying industry.
“This enables us to support and improve a cross-section of quarrying disciplines utilising state-of-the-art drone-mapping services to help sand and gravel production become increasingly efficient,” Ward adds. “EPC Metrics’ additional specialisms of noise monitoring, vibration-monitoring equipment provision, hire and calibration, and engineering consultancy can also realise a series of problem-solving solutions related to the sand and gravel field.”
By drone mapping a site and processing gathered data for examination within an interactive software platform, sand and gravel operations can have digitalised access to information detailing their haul-road gradients, bund-height calculations, stockpile surveys, and volumetric analysis, as well as project tracking.
The data can also be used to conduct safety telematics and ensure compliance, study interactive 3D models, utilise distance and height-measurement tools and support quarry development planning.
“There are currently 36 Civil Aviation Authority (CAA) qualified drone pilots within the EPC-Metrics team,” Ryan continues, “with the skills to operate drones nationwide, including a WingtraOne Professional vertical take-off and landing (VTOL) fixed-wing drone from within a modern fleet. The drones are used to safely capture data from any area of a quarry which is then used, in conjunction with photogrammetric techniques, to create highly accurate, fully geo-referenced 3D models, from face profiles to full quarry maps, which can be regularly recreated as a quarry environment changes.
“The technology we’re bringing to the field is also enabling EPC Metrics to perform
fully remote, environmental monitoring on site,” Ward says. “Through our partnerships with leading system manufacturers we can measure noise, vibration, air over-pressure and environmental conditions. As most drilling and blasting operations must adhere to strict, site-specific planning regulations, including noise restrictions, we’re working to make sure that activities, including those relevant to sand and gravel processes, remain compliant. We use, and can hire out, permanent fixed monitoring stations to gather event data and real-time results in the field. These results can then be fed back to an online platform, reviewed and analysed, then easily communicated to relevant parties.”
Using its drone technology, EPC Metrics has supported digitalised quarrying processes at several quarries across the UK, recording and analysing the data gathered, and safely optimising aspects of mineral-extraction
ABOVE: Maptek’s BlastMCF software offers comprehensive blast design and analysis
performance.
By combining advanced photogrammetry techniques and browser-based 3D surveys, EPC Metrics has helped to prioritise the quarries’ operational safety and enhance site efficiencies, development and mineralextraction planning. By improving data accuracy, using highly detailed imagery from a 42-megapixel camera, advanced data analysis from volumetric cut-and-fill measurements has been made possible. This has enabled EPC Metrics to progress its work in safety analytics, face height and distance measuring. Furthermore, as the information can be geo-referenced using GPS, EPC Metrics’ surveying practice has been made more accurate, cost-effective, and reliable.
Automated drill and blast design can significantly improve the efficiency, safety, and cost-effectiveness of quarry operations, according to US-based Maptek, which provides software, hardware and services for the mining and quarrying industries
Maptek BlastMCF is a software solution offering comprehensive blast design and analysis, which can guarantee improved productivity and safety. The company says this is particularly relevant given that engineering-intensive methods are impractical for lean operations.
Safety is a paramount concern in the quarry industry. Automated drill and blast -design tools allow for better control over blast patterns and sequencing, reducing the risk of accidents and hazardous situations for quarry personnel.
With the BlastMCF automation approach, Maptek says operators can easily generate scenarios that help them understand the interrelated factors that influence blast performance.
Quarry operations often need to adhere to environmental regulations and minimise their impact on the surrounding ecosystem. Automated blast-design software can help optimise blast patterns to reduce vibration, dust, and noise, thus aiding compliance with environmental standards.
Efficient blast designs can improve the overall productivity and throughput of a quarry. By automating the design process and optimising blast parameters, quarries can increase production rates and meet market demands more effectively.
They also lead to significant cost savings in terms of reduced drilling, blasting and material-handling expenses. By automating the design process, quarry operators can identify the most cost-effective blasting strategies and minimise resource wastage.
BlastMCF can generate precise and accurate blast designs based on geological data, quarry layout and other critical parameters. This reduces the chances of over-blasting or under-blasting, which are known to lead to wastage of resources and increased operational costs.
Controlling the fragmentation size of the blasted material is crucial for quarry operations. Automated design software can optimise blast patterns to achieve the desired
fragmentation, which in turn improves downstream processing, reduces wear and tear on equipment, and enhances the quality of the final product.
Maptek’s BlastMCF allows for the integration of various data sources such as geospatial data, drilling data and geological models. This integration helps quarry operators make informed decisions and adapt to changing conditions in real time.
A generic algorithm enables faster, easier scenario analysis to objectively validate and verify design concepts quickly. This allows operations to benchmark the critical factors that impact blast performance specific to their site conditions.
A significant advantage of BlastMCF is the automated generation of drill pattern, per -hole charge plan and timing in a single step.
Detailed reporting and analysis capabilities allow quarry managers to track performance, make data-driven decisions, and continuously refine blast designs for ongoing improvements.
Mark Roberts, global product strategy manager at Maptek, says that BlastMCF automated drill and blast-design tools play a crucial role by enhancing safety, precision, cost-effectiveness, and environmental compliance. The combination of online subscription licensing, machine learning and cloud processing can save thousands of dollars per blast, to help quarry operators optimise their blasting operations, resulting in improved overall efficiency and profitability.
Australia-based multinational Orica has released a new integrated digital solution for the quarry market to streamline and optimise blasting operations.
BlastIQ Quarry is a smart solution that harnesses the power of digital technologies to help quarry operators optimise their
drill and blast activities in near real-time. Developed by Orica Digital Solutions, BlastIQ Quarry allows quarry operators to design blasts according to performance objectives and presents drill and blast insights for continuous blast optimisation.
Developed with customer feedback and deep blasting experience in quarry operations, the smart digital blast-optimisation platform provides a single source of truth and delivers instant pre- and post-blast insights. Instead of manually handling paper-based information, operators can now also collate their data digitally and derive insights to inform their drill and blast performance.
Head of blast design and execution for digital solutions at Orica, Cu Luu, details the key benefits of the new blast-control solution, saying: "Overall, BlastIQ Quarry is a powerful and comprehensive solution that can help quarries improve the efficiency of their drill and blast operations, reduce overall cost, ensure data accuracy, drive productivity, and maintain regulatory compliance. Its integrated and connected components provide a complete solution that delivers real results and drives continuous improvement for the industry."
Complementary applications to enable a synergistic workflow include the SHOTPlus blast-design and modelling software; BlastIQ Mobile Lite which places blast designs and hole conditions in the palm of operators’ and engineers’ hands; and BlastIQ Insights which enables the tracking of key performance indicators and comprehensive document storage. These technologies work together to offer customers improved productivity with blast-loading instructions and rules being instantaneously and digitally communicated to field operations to ensure the right explosive product and quantity is used at the right place and initiated at the right time. AB
JANUARY
23-25 World of Concrete
Las Vegas, NV
Organiser : Informa Tel: +1 212 600 3525 registration@worldofconcrete. com
https://www.worldofconcrete. com/en/attendee.html
MARCH
25-27 AGG1
Nashville, Tennessee
Organiser: NSSGA Tel: +1 (800) 867 6060 https://www.agg1.org
APRIL
24-27 INTERMAT Paris 2024
Paris, France
Organiser: Comexposium Email: laura.sanchez@ comexposium.com https://paris-en. intermatconstruction.com/
JUNE
15-17: Hillhead 2024
Hillhead Quarry, Buxton, UK
Organiser: QMJ Tel: +44 (0)115 945 4367 Email: hillhead@qmj.co.uk www.hillhead.com/
OCTOBER
SIM 2024 (dates TBC) Bordeaux, France
Organisers: Exposition SIM https://www.expositionsim.com/ en/index.htm
These dates were correct at the time of going to press, but please note that the COVID-19 pandemic means some events may be rescheduled with little advance notice
INTRODUCING THE REVOLUTIONARY ELECTRIC RANGE:
• eATR Rammer: Unleash the force of compaction, rivaling its petrol counterpart!
• eAPF Vibratory Plate: Power-packed performance, matching the output of traditional petrol machines!
• eARX Light Tandem Roller: Go big and green! Fully electric, 8+ hours of non-stop operation without recharging! Get the job done efficiently and eco-friendly with your electric trio!