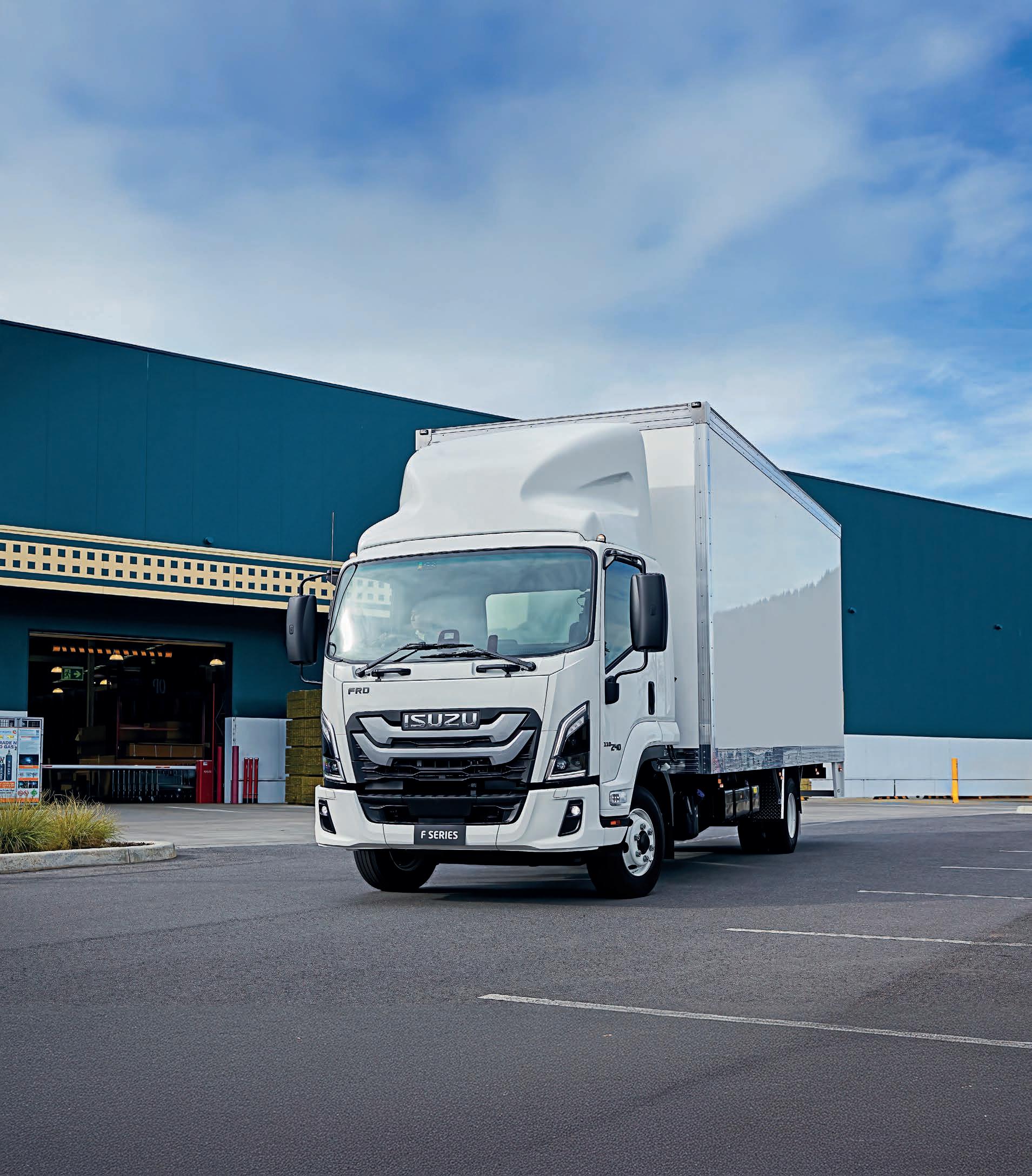

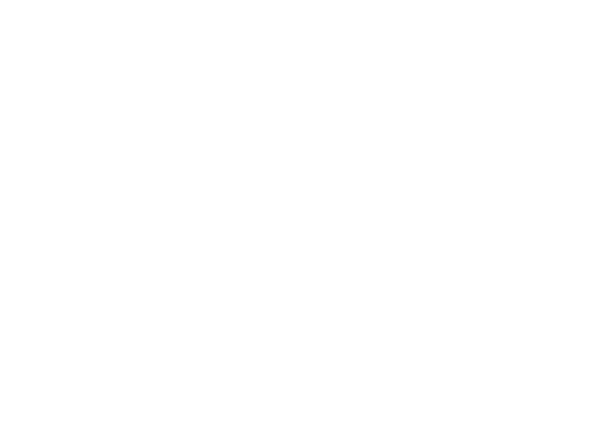



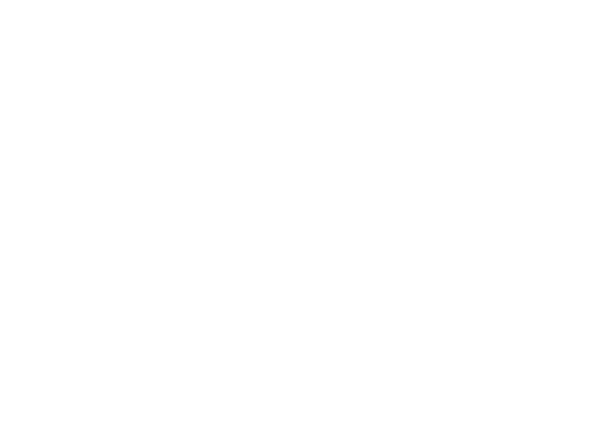


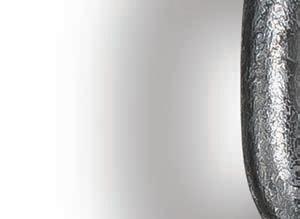
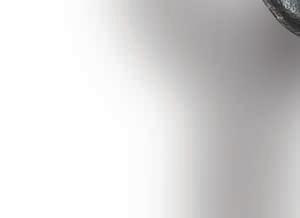
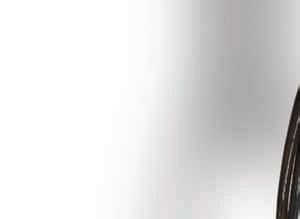


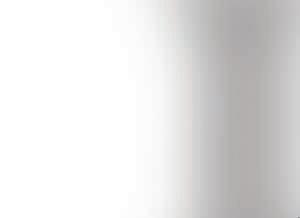
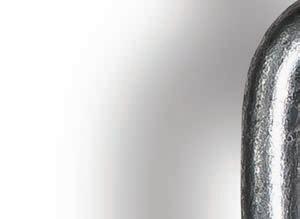
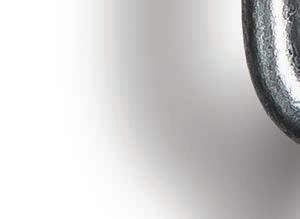
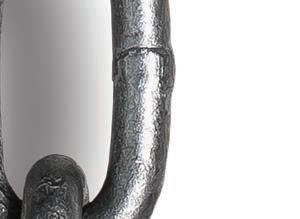
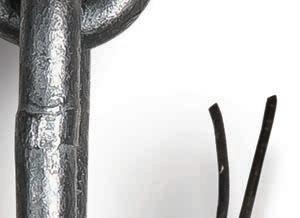
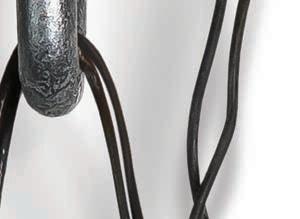


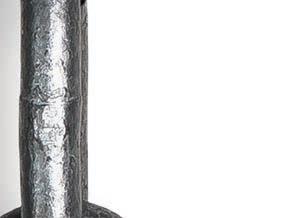
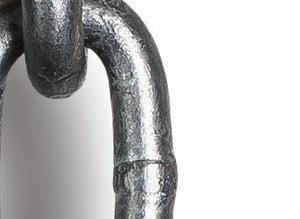
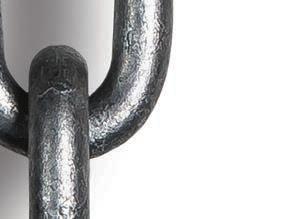

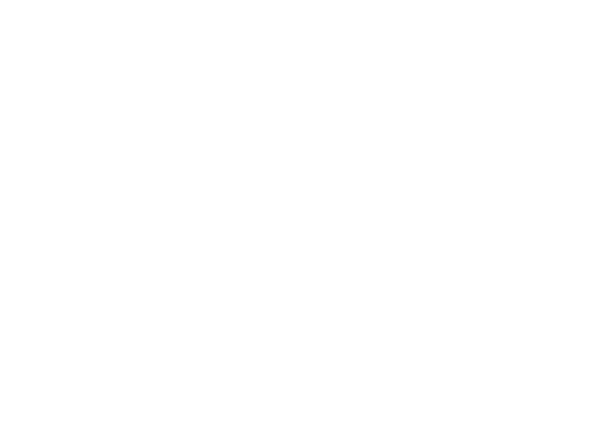

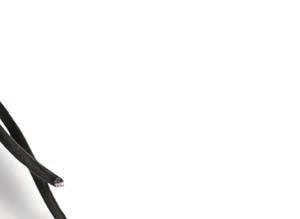
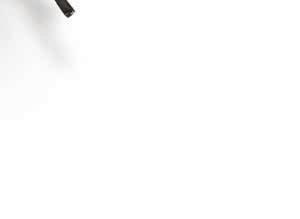
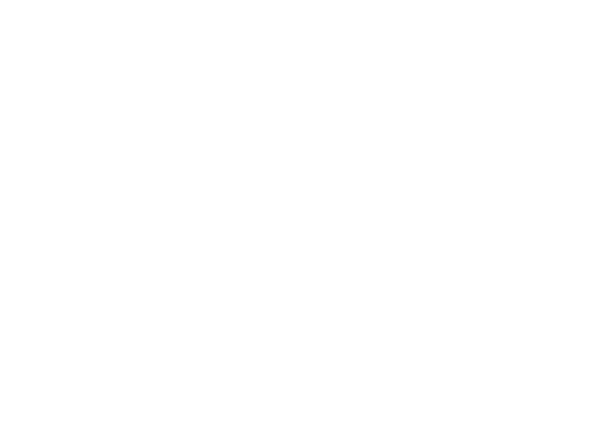



To keep your truck performing at its best, only trust Isuzu-backed parts, which include Isuzu Genuine Parts, Isuzu Best Value Parts & Isuzu Approved Parts. To find out more, see your nearest Isuzu Truck Dealer or visit parts.isuzu.com.au






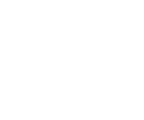














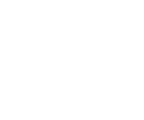







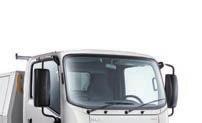











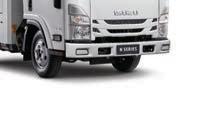
To keep your truck performing at its best, only trust Isuzu-backed parts, which include Isuzu Genuine Parts, Isuzu Best Value Parts & Isuzu Approved Parts. To find out more, see your nearest Isuzu Truck Dealer or visit parts.isuzu.com.au
Hello. I guess that’s as good a way as any to start an introduction and kick off my first column in the Editor’s seat of PowerTorque magazine.
Fitting too that as I sat down to tap the keys, I had an email from our former editor Tim Giles seeking his deadlines for the year ahead and wishing myself and Alex luck with the production side of magazine creation that is no longer a part of his semiretired life.
The good news for PowerTorque readers is we’ll still have Tim out there in the trucking world trialling trucks, following leads, sending us suggestions and bringing us stories for each edition.
When it comes to crafting the mix of articles in the magazine, collating stories, copy tasting, working with clients, working with our designers, reading proofs and liaising with printers and distributors, that’s where I come in.
Reading Tim’s last column for inspiration I feel compelled to acknowledge up front that I do not have a three decades’ long history in transport and have never driven a truck for a living.
My journey to this seat has been working as a journalist and Editor across a wide array of newspapers and magazines for more than 27 years – with transport stories and issues a key part of life for a good part of that.
I’m privileged to have a job that has allowed me to read thousands of stories a year on trucks, buses and cars, and to interview and meet many people from within the transport industry to share their
stories and grow my own knowledge base.
I’ve learnt something new about this industry almost every day I’ve had it as my focus and it’s my hope that as Editor of PowerTorque I will be able to continue on that journey by sharing the latest news, reviews, insights and opinions from our writers and contributors both in print and online.
The first step on that journey is to be found in this edition where Tim Giles takes a look at Isuzu’s big plans for 2025.
Tim was writing about trucks when Isuzu announced their last complete model overhaul, some 17 years ago, and has plenty of information to share about the positive steps into the future represented by the company’s expansive plans for its MY25 model range.
PUBLISHED BY
Prime Creative Media Pty Ltd
ABN 51 127 239 212
379 Docklands Drive, Docklands VIC 3008 Australia
Telephone: 03 9690 8766
Email: enquiries@primecreative.com.au
Chief Operating Officer: Christine Clancy
Editor: Geoff Crockett: 0421 299 963 geoff.crockett@primecreative.com.au
Assistant Editor: Alex Catalano
Technical Editor: Tim Giles
Contributor: Bob Woodward
Correspondent: Will Shiers (UK)
Advertising Manager: Peter Hockings: 0410 334 371 peter.hockings@primecreative com.au
Client Success Manager: Salma Kennedy, salma.kennedy@primecreative.com.au
Circulation & Subscriptions Manager: Frank Rapone
Head of Design: Blake Storey
Designers: Danielle Harris, Jacqueline Buckmaster
On the review front, Tim jumped back in the saddle to test a Scania P500 and experience the 500 hp offering firsthand around the streets of Melbourne. His report is well worth a read.
Alex caught up with the winners of a scholarship program organised by Cummins to find out about their journey into the world of trucks and he has all the news from the recent Technical Maintenance Conference in Melbourne and Australian Road Transport Suppliers Association Institute event in November too.
As we head into a new year, I hope this edition offers you some insight into what’s to come in the world of transport.
I’d also like to extend an invitation to readers to get in touch and let me know about the stories you’d love to see in your PowerTorque magazine.
Official Media Partners: REGISTERED BY Australia Post - ISSN 1445-1158
SUBSCRIPTION
03 9690 8766
subscriptions@primecreative.com.au PowerTorque Magazine is available by subscription from the publisher. The right of refusal is reserved by the publisher.
Annual rates: AUS $60.00 (inc GST). For overseas subscriptions, airmail postage should be added to the subscription rate.
PowerTorque Magazine is owned and published by Prime Creative Media.
All material in PowerTorque Magazine is copyright and no part may be reproduced or copied in any form or by any means (graphic, electronic or mechanical including information and retrieval systems) without written permission of the publisher.
The Editor welcomes contributions but reserves the right to accept or reject any material.
While every effort has been made to ensure the accuracy of information, Prime Creative Media will not accept responsibility for errors or omissions or for any consequences arising from reliance on information published.
The opinions expressed in PowerTorque Magazine are not necessarily the opinions of, or endorsed by the publisher unless otherwise stated.
The Purtill family have built
empire in the New South Wales border town of Deniliquin, and continuing to grow their fuel haulage business has helped it thrive.
20 ISUZU’S GREAT LEAP FORWARD
It has been 17 years since there was a genuine model change, but 2025 will see a new, from the ground up, Isuzu range coming to the Australian truck market.
32 INNOVATION IN ALL AREAS
The ARTSA Institute’s ‘Road Transport – embracing change and innovation’ conference took a lens to how all areas of the industry are tackling the future of transport.
46 NEW YEAR, NEW APPROACH
Three months on from announcing a change of name from MaxiTRANS to Freighter Group, the trailer specialist is stepping into 2025 with big plans.
48 LEARNING ON THE JOB
Hume Transport’s Nellie White is aiming to further advance her career in transport through the help of a new scholarship.
50 CHARGING TOWARDS AN ELECTRIC FUTURE
Electrification specialist Zenobē is looking to off-site charging to solve a key issue in electric vehicle infrastructure.
60 ENTER THE ELECTRIC OPTION
The new Volvo FM Low Entry may have a face only a mother could love, but as Will Shiers discovers, it’s purpose-built for a specific job, which it does remarkably well.
54 TIME FOR REAL HVNL CHANGE
You would think that after six long years of reviewing the Heavy Vehicle National Law, the situation would have been resolved by now, writes NatRoad CEO Warren Clark.
55 PLANNING FOR THE ROAD AHEAD
Routine servicing and parts replacement is common sense for any heavy vehicle operator, including small business Cube Removals.
SCANIA, SMALLER PACKAGE
With the introduction of a 500hp engine in a small P Series truck, Scania have come up with the same thing in a smaller package.
56 FACING THE BIG ISSUES
The next 12 months beckon with many all-too-familiar issues within the transport industry, which the ATA are prioritising.
70 A CLOSER LOOK AT SAFETY SYSTEMS
Knorr-Bremse offered the chance to get a closer look at just how its suite of safety systems works recently at its first Drive Days event since 2019.
74 FASTENERS – OVER TORQUE OR NEVER TORQUE
Fasteners can undergo severe conditions and need to be treated with care to ensure they don’t get damaged.
78 CULTURE, CARE AND CUMMINS
Pride in everything is everything at Scholz Bulk Haulage, a family business based in Wodonga, NSW, which celebrated its 25th anniversary in 2024.
After recently releasing its new range in Europe, Volvo Trucks will be introducing the FH Aero to Australian shores this year.
Volvo says the FH Aero range has been impressing the industry with its on-road refinement and energy efficiency, with European testing showing it has efficiency improvements of up to five per cent.
The FH Aero will be available in Australia with a choice of 13-litre and 17-litre Euro 6 ICE powerplants as
well as Volvo’s heavy duty electric driveline.
ICE powered FH Aero variants will be built at Volvo Group Australia’s Wacol manufacturing facility from mid-2025.
“We’re super excited to be launching the Aero range here in Australia,” Volvo Trucks Australia Vice President Tom Chapman says.
“This truck represents a critical step along the path to sustainable transport as well as lowering running costs for operators along the way.”
Iveco is releasing a new model of its Daily range, recently unveiling the 4×4 line-up in Australia.
It includes a number of upgrades that were in the latest 4×2 range, including enhanced emission performance to meet Euro 6 standards ahead of the incoming mandate.
The latest model retains the Daily’s 3.0L engine with variable geometry turbine – output remains at 180hp (132kW) @ 3,500rpm and 430Nm of
control for the range comes courtesy of EGR and SCR systems.
The engine can be matched to either a 6-speed manual transmission, or the optional 8-speed H-Matic fully automatic.
The new Daily 4×4 is available exclusively with a light truck licensed 7,000kg GVM and 10,500kg GCM rating, with a choice of three wheelbases options – 3,480mm, 3,780mm and 4,175mm – in either
NHVR CEO Sal Petroccitto has announced his resignation, set to leave the organisation on January 24, 2025 after more than a decade.
NHVR chair Duncan Gay paid tribute to the outgoing CEO after he informed the board in October last year.
“On behalf of the NHVR Board, staff and the road transport industry, I want to share my sincere thanks to Sal for his outstanding dedication and passion in championing better outcomes for the safety and livelihood of the heavy vehicle industry and all road users,” he said.
“Sal has worked tirelessly to build industry trust and respect to ensure the modern regulatory approach being implemented by the NHVR will achieve genuine and tangible national safety and productivity reform.
“His no nonsense and practical approach in ‘saying it as it is’ was embraced by industry and a critical part of the partnership and trust he built.”
The Mercedes-Benz eActros 600, which was awarded the International Truck of the Year 2025, is officially in production.
Daimler Truck’s plants in Gaggenau and Kassel, Germany, began installing key components in the vehicles at the end of November, with the first of the new line of vehicles already manufactured and registered by the end of 2024.
The plant in Gaggenau has been the site of the construction of the Mercedes-Benz ‘e-axles’ for the eActros 300/400 models, and will now do the same for the 600. The four-speed axle drive contains a total of around
30 different components, including shafts, gears, synchroniser parts and housing parts.
Gaggenau then supplies these components to Kassel, where the complete assembly of the axle and transmission components takes place.
“At the Mercedes-Benz plant in Gaggenau, tradition and transformation go hand in hand,” says Gaggenau Plant Manager Thomas Twork.
“We are proud to apply our decades of experience in the manufacture of high-precision transmission components to the new electric powertrain.”
Kevin Smith took over as the new General Manager of Penske ANZ’s New Zealand arm on November 15.
Smith replaced previous General Manager Brian Wilson in the role and is charged with overseeing all branch operations across a variety of industries including commercial vehicles, rail, mining, defence, marine, energy solutions and more.
Kevin said the investment Penske is making into its New Zealand operations made it an exciting time to join the company.
“Penske has invested heavily in New Zealand in recent years, opening a brand-new facility in Christchurch and Tauranga to complement the existing Auckland branch,” he said.
“Along with a stable of innovative and well-proven products and brands, the team at Penske is highly experienced and engaged.
“It’s exciting to join an organisation that is so passionate about its customers and services.
“These are all vital ingredients for continuing to build a successful business that delivers outstanding customer outcomes.”
The Australian Renewable Energy Agency (ARENA) has committed $100 million more to heavy vehicle electrification with new funding under the Driving the Nation program. It says it will be targeting three focus areas to support the electric transition.
ARENA is providing $28.6 million in funding to two projects with $19.6 million committed to Linfox and $9 million to Toll – unlocking more than $124 million in investment into freight decarbonisation.
ARENA CEO Darren Miller says the heavy transport sector is a key area that Australia should be focusing on to meet
the country’s wider zero emissions goals.
“The heavy vehicle market has matured significantly over the past year in relation to battery electric vehicles, particularly vehicle availability and infrastructure,” he says.
“However, there are still significant hurdles including upfront costs for operators, challenges with charging technology and infrastructure, as well as the lack of real-world data.
“Transport accounts for about onefifth of Australia’s CO2 emissions, with heavy vehicles a significant share of the transport emissions pool.”
NatRoad has made its submission to the NHVR’s Productivity Plan 20242029, calling for the regulator and the transport industry to do away with road access permits across Australia by 2028.
The recommendation to slash 90 per cent of access permits would boost productivity, reduce cost of living pressures, improve safety and lower emissions according to
NatRoad CEO Warren Clark, who says the bold move would provide much-needed cost-of-living relief for the industry.
“Reforming heavy vehicle access would provide much-needed relief in today’s cost-of-living-crisis,” he
Australia’s economy and supply chains.
“By improving access for heavy vehicles, we can move more freight in fewer individual vehicle trips meaning lower cost, improved safety and reduced emissions.”
The Victorian Transport Association has launched its Greenstar Transition Pathway Program as a part of its recent Alternative Fuel Summit.
The program is designed to support the transport industry in its vital decarbonisation journey by offering education, resources and tailored transition frameworks to help fleet operators adopt low and zero-emission technologies.
VTA CEO Peter Anderson highlighted the importance of Greenstar, emphasising its potential to drive substantial change in environmental sustainability within the transport sector.
“Greenstar is a game-changer
for heavy vehicle operators. By equipping fleets with the tools, training and technologies they need to decarbonise, we can significantly reduce carbon footprints while improving operational efficiencies,” he says.
provides a clear pathway for operators to embrace alternative fuels and innovative technologies, ensuring they are ready to meet government emissions targets and contribute to a greener future.”
PACCAR has officially unveiled the newest iteration of the DAF XG model.
The new DAF XG and XG+ come equipped with the powerful 15-litre PACCAR PX-15 engine, delivering 660hp.
Created through an Australianled project that also involved global PACCAR engineering teams and industry-leading supplier partners, the new models boast superior safety, luxury and aerodynamics to deliver the power and torque that Australian applications demand.
“Throughout the development of the XG, we were eager to extend the capability of this truck to suit the high productivity applications that make Australian transport so unique,” DAF Director of Product Planning Ross Cureton says.
“Through PACCAR’s global powertrain partnerships, we identified the perfect combination to deliver a step forward in performance, fuel economy and durability, while preserving the outstanding comfort, safety and refinement of this next generation DAF.”
The two models are available to order now, with production happening at Kenworth DAF’s Bayswater plant from January 2025 onwards.
English company Zero Petroleum is making moves in the renewable energy space in Australia, building a commercial-scale synthetic fuel production plant in Whyalla, SA.
Plant Zero.SA will be located in South Australia’s Upper Spencer Gulf, and the feasibility study will officially be supported by the state government and run in collaboration with a consortium headed by Adelaide Airport and Qantas.
Whyalla is a key location in the state government’s State Prosperity Project.
A six-month feasibility study will evaluate the technical, economic
and environmental viability of a facility capable of producing up to 10 million litres of synthetic aviation fuel, gasoline and diesel annually.
Synthetic fuels, otherwise known as e-fuels, are created by combining renewable hydrogen with carbon dioxide to produce a low carbon fuel compatible with existing aircraft, road vehicles and maritime applications.
This means that although the study is being supported by players in Australia’s aviation industry, it could have roll-on effects to the nation’s road transport sector should plans for the facility progress.
The winner of the Craig Roseneder Award was announced in October at the Australian Trucking Association’s Technology and Maintenance Conference.
John Jenkin of Tatiara Truck & Trailers was named as this year’s recipient of the Craig Roseneder Award and as part of the recognition he will receive a fully-paid trip to attend the 2025 US Technology and Maintenance Council Annual Meeting and Transportation
Technology Exhibition in Nashville, Tennessee.
Jenkin started the Tatiara Truck & Trailer business with his partner four decades ago in South Australia’s Bordertown and has since grown the workshop into a reputable organisation with 60 employees.
The business has attracted major dealers like Cat, Cummins, Detroit, Perkins, Volvo and Scania, and they serve as a Kenworth sub-dealer.
Achim Puchert has been appointed as the new CEO of Mercedes-Benz Trucks, taking over from Karin Rådström after her appointment as CEO of Daimler Truck.
Puchert also joined the Board of Management as of December 1, 2024.
He was previously CEO of Mercedes-Benz Trucks do Brasil and Latin America and will now be responsible for the regions of Europe and Latin America in his board position.
Puchert started his career in the former Daimler Group in 2002 and was appointed to his current role in 2022.
He has worked for Daimler AG in numerous capacities all over the world, including postings in Brazil and Latin America, Russia, Germany and Asia.
He held the role of Senior Vice President International Sales, Marketing and Customer Service for Daimler Truck Asia for almost three years prior to his appointment with Mercedes-Benz in Brazil.
Coles has welcomed its first ever electric prime mover, taking delivery of a new Volvo FH in partnership with Linfox to add to its delivery fleet.
The truck is already being put to work, helping to deliver groceries to hundreds of stores across Victoria.
Coles and Volvo say the prime mover will save more than 65 tonnes of CO2 emissions per year compared to a regular diesel-powered prime mover, which is the equivalent of
removing 15 cars from the road.
It is expected to make 25 trips per week from Coles’ Victorian Distribution Centre to stores across every state.
“We’re excited to welcome our first EV prime mover to our network which is currently doing about 25 deliveries from our Distribution Centre in Victoria each week to hundreds of stores across the state,” says Coles Chief Operations and Sustainability Officer Matt Swindells.
The Victorian government and City of Greater Shepparton are committing a combined $100,000 towards a study analysing freight and industry trends in rural transport in the Shepparton region.
Titled the ‘Greater Shepparton Integrated Transport and Land Use study’, it will examine how changing land-use patterns should inform decision making for the future transport needs of Shepparton and surrounding communities.
The City of Greater Shepparton will contribute $30,000 to the project, while the state government will invest $70,000 to the project.
The study will help guide planning for economic development in the region, particularly surrounding the continued growth of the transport logistics, manufacturing, agriculture and tourism industries to inform better service planning decisions at the local level.
Isuzu Australia is looking to a partnership with TAFE SA to get more young mechanics in workshops amidst the continuing industry shortage.
As a part of this agreement, TAFE SA recently acquired six IPS 4LE1N industrial power units from their local supplier Engine Pump and Power in Adelaide for students to tinker with, strip-down and repair as part of their learning program.
“We just purchased six Isuzu engines for the workshop, which is what we were after for teaching
those fundamentals,” says automotive technician David Askew.
“They’re simple, mechanical engines, without too much electrical or fuss which is just perfect for us.”
The training provided in these courses prepares a student to tackle a wide range of issues from engine diagnosis through to life skills that are applicable almost anywhere.
This is done through practical and hands on experience, letting students get familiar and comfortable with heavy vehicle components in the classroom.
The ARTSA Institute’s partnership with the ATA, TIC and HVIA has resulted in the release of a report on roadtrain coupling forces and the effect of dynamic loads on coupling.
The final report was released in November at the ARTSA-I Conference in Port Melbourne.
Funded by the NHVR’s Heavy Vehicle Safety Initiative and supported by the federal government, the project made a number of key findings.
“The project, led by ARTSA-I, involved measurement of the coupling forces on quad-trailer 160 tonne road trains during routine daily journeys of hundreds of kilometres in
the Northern Territory,” says Martin Toomey, ARTSA-I Executive member and Chair of the project working group.
“An instrumented dolly was used in different positions on the Direct Haul bulk fuel road train so forces at different locations could be measured.”
Results of the study included:
• The forces experienced by the couplings were similar whether the dolly was underneath the second, third or fourth trailers. This
well predicted using the existing formulae in the Australian Standards.
• There was no evidence of a maximum force plateau that could be expected as road trains get longer. Instead, the peak forces appear to increase in proportion to the overall mass.
• By far the most common occurrence of very high forces was when a vehicle was at very slow speeds or coming to a stop – when braking, shunting, or manoeuvring
The Purtill family have built an empire in the New South Wales border town of Deniliquin, and continuing to grow their fuel haulage business has helped it to thrive
Neville Purtill has lived his whole life surrounded by transport, thanks to the ambitions of his family.
The story started when father Keith moved to Deniliquin in the early 1950s, meeting his soon-to-be-wife Pat and setting about building their family.
While Keith began work as a mechanic following World War II, his dream had been to buy a truck to work as a driver carting stock. This instead resulting in buying a bus, to work transporting children in the region to and from school.
It may not have been his ideal ride, but this was where the foundations of the Purtill Group began. In 2021, it celebrated 70 years in operation, and in 2024 it marked 50 years in the fuel haulage business.
But back to Neville – his earliest memories involved spending time in and around the trucks and buses. Today, as Purtill Group’s Managing Director, a role he took on after his father’s passing in 1988, he says there was nowhere else he ever thought about working.
backyard, so they became our cubby houses!
“Fifty years of the fuel haulage operation is a particularly special milestone for me personally since it’s been around for most of my lifetime, given Dad started the business originally with the buses before I was born,” Neville tells PowerTorque
“I grew up in the bus industry. The buses were always in our
“I was 13 in 1974 when dad started in the fuel jobs, just a kid starting high school. I would spend the weekends and school holidays with the drivers. I got a fair understanding of what it was all about. It had an allure to it.
“I started working after school in Year 12, manning the depot when the staff would go out to drive the buses. I’d man the phones, fill drums and paint them. Probably drive trucks illegally back then too!
“In 1978 I was working part time
finished my HSC I just stayed there and kept doing it. It’s always been the family business. I could have gone to university but the idea of driving a truck around was more exciting.
“As soon as I turned 18 I got my licence and started driving the tankers from then on. I did that for about six years full time, then there was a necessity for me to get back in the office.
“The business was growing, so I was needed more on the management side than out driving trucks.”
So just how did it go from one man driving a bus around to the multibusiness empire that is the Purtill Group?
Nowadays, it consists of Purtill Petroleum, which encompasses the fuel haulage and distribution operations, The Depot, a historic vehicle and memorabilia collection, a restaurant called Cruizin* Diner and the Wired Entertainment store.
“Some of the story of how we’ve grown has become urban myth!” Neville laughs.
“Dad had outgrown our backyard with the buses, so he was looking for a commercial site for them. He found a location that was an ex-Golden Fleece depot. He negotiated to buy it and next thing you know they approached him about restarting the agency again.
“At that stage there were two bus
operators in the area, so he carted half the district’s kids to school and knew all the farmers already. He had drivers that were idle between 9-3, and thought trucking could be a good fit.
“At the 11th hour the Caltex depot was also becoming available. It was already an existing operation with its own depot. He ended up negotiating to take that over instead of negotiating to start from scratch with Golden Fleece.”
Developing the working relationship with Caltex and Golden Fleece, Purtill Petroleum would continue to expand, taking over several fuel depots across the years.
The first was based in Deniliquin, at the corner of Wood and Hardinge Streets. Next was Jerilderie, just a short drive north-east, in 1985. This was followed by an Ampol fuel depot in Hay two years later, and the Finley NSW fuel depot in the early ‘90s.
But with the advent of bigger, more productive semi tankers by the early 2000s, these depots slowly became less necessary as they were able to run the truck further out than ever before.
In the first year of operation, eldest son Norm was able to deliver 1 million litres of fuel within a 60km radius of Deniliquin. Now, a single truck can deliver 86,000 litres in one trip – nearly a 10th of that first yearly total.
The very first truck Keith owned for fuel haulage, an S-Model Bedford, held just 8,000 litres total across four bulk delivery tanks. This would slowly
continue to be upgraded over time, as the fleet and capability of the trucks in it grew.
“Just prior to me starting in the business, Dad had bought an International Acco 1830A, 1976 model with an aluminium barrel on it,” Neville explains.
“Prior to that it was Bedfords with cross tanks on them. When that came along, we were only carting 8,000 litres at a time.
“When I was driving, we evolved into having the first semi-tanker in the mid 80s. We put pumping gear on it and started delivering straight to farms. It all grew from there.
“When we first started, we could only do a radius of 60km from Deniliquin. It was all rural based. In
the ‘80s we branched into retail fuel and service stations. We’ve now got a radius of about 300km.
“The majority of our work is in Southern NSW. We do some in Victoria, we cart our fuel out of there now.
“Back in the early days our fuel only came by rail.
“That was also one of my jobs after school, to unload rail cars.
“The equipment has gotten significantly better, more efficient, safer and bigger. I was running out in a truck that could only carry 16,000 litres and now we’re carting 80,000. There’s a lot more regulations and responsibility that comes with that.”
While they’ve purchased plenty of trucks throughout the years, the fleet
They currently make use of four Volvo FH16 700hp models, which Neville says they chose and continue to buy for the safety offerings they provide.
“We’re running five tanker sets at the moment. There’s four A doubles and a 19 metre tanker,” he says.
“We chose the Volvo models mainly for safety and reliability. In the bus industry we use predominantly European vehicles, so we already have the understanding of that product. They get a very good run.
“We’ve got buses that have done two million kilometres on contract
work. We were happy to embrace the European trucks.
“There’s six permanent drivers and a few part-timers, and managers that will jump into a truck if they need to.”
Neville believes that the Purtill Group has been able to continue growing by always looking ahead at the next innovation – how they can separate themselves from what everyone else is doing.
From Keith’s early days, this was always the priority. They were the only business in the area delivering fuel direct to farms via semi-tanker, offering locals a service they had never had before.
This expanded into pushing where they could for developments in road access and the Performance Based Standards scheme, both of which they would take advantage of.
They would continue to deliver fuel direct to farm into the 2000s, now using B-double tankers with special access permits for local roads.
Neville says that he would often look to other parts of the transport industry for inspiration, and to see how he could go back and apply it to fuel haulage.
“We pride ourselves on innovation, maybe to our detriment sometimes,” he says.
“We took a look at what was happening in the industry. I tend to watch and admire what they do in milk cartage. They always seem to do things first when it comes to tankers.
“I was starting to see these
A-doubles running around northern Victoria and into Southern NSW. At the same time, Victoria was starting to investigate high productivity vehicles and opening freight routes.
“We started to investigate what that meant for us and how we could get better productivity.”
One of the ways they did this was from an observation made at Newport Terminal, watching 30-metre-long container trucks transporting their goods around the Melbourne facility. This sparked a plan to figure out a way to do this with fuel tankers.
Technologically, this proved to be a challenge. Weight was a major factor to consider, with just a single pump and lead system being installed on a new trailer and barrel design to draw from
both the front and back trailer at once.
This both maximised payload and fit with the ADR and PBS at the time. This then also had to be approved through multiple parties including the NHVR to gain road access from Purtill Group’s furthest NSW site all the way into Melbourne.
“We worked with a manufacturer and went through all the approvals for bridges and those sorts of things,” Neville explains.
“Originally when we started, our main route to Melbourne is via Echuca. It was the original old bridge, and we couldn’t take the weight over it. We had to take the trucks via Tocumwal, which adds an extra half an hour on the route.
“As soon as they opened the Echuca Bridge, it made a huge difference to our efficiency.
“All our A-doubles are run under PBS. It’s made a huge difference to what we do and how we operate.
“When we send the 19-metre on a job now we can’t fit everything on because we’re so used to loading up the A-double.”
Like every other operator, Purtills has continually been chasing improvements and advancements like these to make business run more efficiently.
Just getting bigger and better trucks on the road hasn’t been the only challenge though, with plenty to consider behind the scenes too.
“Safety and licensing have been challenges, but a lot of it has resulted in positive stuff,” Neville explains.
“The challenge is in recruiting, training and retaining staff, particularly drivers.
“In my time it’s become an aging workforce. The human resource side of it affects everyone at the moment.
“We’re lucky that we’ve got a great team and we’ve recruited well over the time. They’re very loyal.
“Whilst it’s a challenge for the industry, we’re happy with where we are as a local operator. Drivers like to work for a family company from our experience.”
With the growing need to look at alternative fuel sources across the industry, fuel haulage may be one area of transport that looks very different by 2050.
If electric, hydrogen or other renewable fuels are adopted en masse, operators like Purtills could have their business environment suddenly change.
“We’re watching on the zero emissions front,” Neville says.
“Our belief is that regional Australia is still going to be reliant on petroleum products. Our future is reasonably secure. We’re looking at areas and opportunities.
“When we’re looking at
redeveloping a service station for instance, we’re looking at how we can include EV charging.
“There will be changes in the fuel space over time. Maybe not this year, but over the next five to 10 years.”
And while they are looking at the future, the 50 year milestone of the fuel haulage business is all about celebrating the past of the business, and acknowledging all of the hard work that has gone into, and continues to go into it.
While his brothers have departed the family business, Neville continues to work on seeing it into the future alongside his wife Debbie and his children Matthew and Jenna.
There is now a third generation of Purtills involved within the business, which Neville says brings great joy to he and his wife.
“My son is involved in the retail side of Purtill Group. There is the next generation coming through and showing interest in the transport side.
we do it. I was given an opportunity by my father, and we can hopefully give that opportunity to the next generation.”
To celebrate the 50th anniversary of the fuel haulage business, and more than 70 years for the Purtill Group, they released their own magazines (which you can find on the Purtill Group website), detailing the history of their great family company.
While the magazine acts as a method of preserving history, Neville says it is also an acknowledgement of all the people that helped along the way to keep the Purtill Group as strong as it is in 2025 and beyond.
“We wanted to celebrate and thank those that have been part of the journey, and acknowledge them,” he says.
“We’ve had a lot of good people and good customers over that time. It’s an achievement that we get to celebrate.”
It has been 17 years since there was a genuine model change, but as Tim Giles reports, 2025 will see a new, built from the ground up, Isuzu range coming to the Australian truck market as the long time market leader catches up with the latest technology
is introducing a completely redesigned range of trucks in 2025.
It has to be admitted that 17 years is a long time between drinks, but during that period Isuzu has not only led the Australian truck market every year, but has further entrenched its number one position. It has gained even more market share in the light and medium truck sectors and retained its position in the heavy duty market despite having no viable heavy duty prime mover in play for a lot of that period.
Plenty of new technology has come along in the intervening years, and much of that technology has found its way into the Isuzu range in some form. However, the trucks going on sale in 2025 include all of the new technology as an integral part of the initial design. The engines are also designed and built to comply with the latest exhaust gas emissions regulations.
This launch is not about the path to zero carbon for the brand. These are the pragmatic trucks which the trucking industry will still be dependent on for well over a decade, and which will handle the transport task until the next generation of zero carbon trucks fully emerge in each market sector.
According to Isuzu, the launch of its 2025 models will be the biggest model change the brand has ever been through. The step up to Euro 6 is a significant one for the engine makers, but seeing as this is the fourth exhaust emission regulations change in the last 20 years, the truck manufacturers have
fine tuned their emission reduction technologies to the point where they are effective and familiar.
At the same time, it has been 17 years since a proper model change for the brand. It’s a good time to actually start again from the ground up, and look at every single aspect of the chassis, driveline, cabin and electronic architecture.
The Australian truck market will see a complete change in the look and feel of the N Series, F Series, FX and FY truck models. For now, the same can’t be said for the heaviest model, replacing the Giga, which was phased
out several years ago. This new set of models is already well embedded in the Japanese market, but of course, the versions which will be arriving on our shores for the launch of these models in 2025 have been configured for the Australian market.
This has been one of the strengths of the Isuzu brand, and one of the reasons it has maintained its number one status for well over 30 years. It is the ability to take what is being made in Japan and rethink it, using the existing componentry available, and developing something Australiaspecific where it is needed, to bring something to market which suits the Australian trucking industry in a more precise way than product which would have been directly imported from a overseas truck market.
On this occasion, there have to be new engines, because the move to Euro 6 does mean the inclusion of more technologies.
However, at this point Isuzu is not stressing details about their engine technology and the power and torque outputs, or transmission options, but is instead concentrating on other aspects of this design. One big talking point is the new cabins, which are to be fitted out with all of the latest safety gear.
Up until now Isuzu has been bringing in a mix and match of different safety system technologies
from different suppliers and using them to meet the requirements of the truck buying market. This time around, this is a more integrated system coming out of the Isuzu stable, which encompasses all of the safety systems required now, with room for development into other areas of safety and higher levels of technology into the future.
The results which have come from the purchase by Isuzu of the UD Trucks brand from Volvo are still unclear.
It has been several years since the takeover was announced, but very little information has emerged about the implications of any technology sharing between the Swedish truck maker and Isuzu.
One feature has emerged: the new Isuzu Giga replacement in some markets is basically a UD Quon rebadged with some modifications and sold as an Isuzu. How that will play out in the Australian market is still unclear.
“It’s really interesting in terms of
how long these things take to play out,” said Andrew Harbison, Isuzu Director and Chief Operating Officer. “It really took two or three years before we
F Series that will be here in Australia next year. That’s taken five, six years for that to feed into the offering.”
Things like the new mobility
product portfolio moving forward.
Andrew was willing to say that the replacement for the Isuzu Giga in the Australian truck market will have an Isuzu badge on it, but was unwilling to elaborate further.
The Volvo Alliance, when it was announced, was not spoken of as a short term plan. It was talked about as being a 20-year alliance.
“We will ensure that the product we have here in Australia with an Isuzu badge on it will be in the same vein as all of our other product, that it will be done in such a way that it will be absolutely 100 per cent for the Australian market,” said Andrew.
On the question of whether other Volvo owned technology, outside of the specific UD technology in the Quon, will also be introduced elsewhere in the Isuzu range, Andrew said: “Initially, probably not from a from a hard componentry point of view. Twenty years ago, a truck was nearly
all metal and not much else, whereas now it operates in a very complex environment with a lot of systems and processes. That’s where we’ll see a lot more of the Volvo involvement across the range in years to come.”
The design process for the new 2025 Isuzu range began over six years ago and the designers decided to work from a blank piece of paper and develop the design from the ground up. One big project was deciding how to integrate the fast changing technology, especially around safety systems.
“The biggest challenge for us was, to move from complexity to flexibility and introduce a new platform, a new architecture and a new philosophy of the core dynamics,” Isuzu Chief of Product Matt Sakhaie said.
“Customer preference, that’s the major drive behind these changes.
“What we found through the Isuzu ‘Future of Trucking’ report (FoT) is that the customer is demanding more advanced technology.
“They’re expecting more intelligent vehicles to help them to be more effective and efficient to solve their transportation problems.”
There is a need to add some items to the safety suite in 2025 as three new ADRs come into effect next year.
ADR 35/07 mandates electronic stability control (ESC), ADR 97/00 brings in advanced emergency braking (AEB). Then, later in the year new emissions rules in ADR 80/04 come into effect, mandating lower nitrogen oxide and particulate matter limits in exhaust gases, bringing Australia down to Euro 6 or its equivalent.
On the N Series models, the safety suite includes all of the safety systems carried over from the previous model, plus, a number of new ones fitted as
control (F-ACC), as Isuzu calls it, uses the front facing camera and radar to maintain an adjustable safe distance behind a vehicle in front to the truck. This is available on all models using the auto transmission.
There is also miss acceleration mitigation (MAM), a system popular in Japan, which uses sensors on the truck to detect whether the driver has accidentally pressed the accelerator instead of the brake in a dangerous situation. When it comes to the F Series models there is an auto lighting system (ALS) alongside the F-ACC also seen in the N Series. The heavier FX and FY models will include all of the above, plus ESC and lane keep assist (LKA).
The latest FoT report includes truck buyer’s preferences around safety technology, in a period where the number of safety technologies available to the the truck maker is increasing at a rapid rate. The amount of data flowing through a modern truck’s CANbus coming from smart cameras and myriad sensors, has seen the proliferation of acronyms in a truck’s specification, both as standard or optional.
Because it is a standalone truck maker and not part of a larger automotive global conglomerate, Isuzu in recent years has been lagging behind its main competitors. Isuzu needed a complete renewal of its platform to be able to offer the kind of
the launch of the 2025 models, the range is brought back up to date and able to compete on a toe-to-toe basis with its main competitors.
The FoT report was the tool used by the truck maker to develop the latest models, with customer preferences front of mind.
customers were keen to adopt forward facing cameras which recorded events, like dash cams,” said Simon Humphries, Isuzu Senior Product Manager, Commercial Vehicles and Chief Engineer.
“These are normally an aftermarket fitment, but some vehicles have got
them fitted as standard. The last survey also gave adaptive cruise control a lot higher preference than you might expect from its lack of regulation.
adaptive cruise control in just about every model in the 2025 range.
standard on just about every truck we sell from next year.
“AEB and ESC are up there in the top five in the survey, and they are subject to a new regulation and are, of course, included in the new models.”
Blind spot monitoring and driver monitoring systems also ranked highly in the survey and the technology for them is built into next year’s models.
However, Isuzu is not making them standard from the outset, preferring to do more testing in Australia when the product is on the ground here as the new functions are tailored to our market and our systems.
“We know that all these features, or certainly most of them, are very common in passenger cars and blind spot monitoring was a clear number one in the FoT survey,” said Simon.
“That’s quite interesting, because it’s quite uncommon to find those even on the European sourced trucks at the moment, but it will become a regulation. It’s one of those that’s
a change pops up, adopting one of the European regulations to make DMS standard and mandatory. We’ll be ready for it, of course.
“Stability Control will be pretty much standard on every truck sold from next year, with very few exceptions, plus AEB and then Lane Keep Assist. LKA rated very highly with our survey respondents, and the awareness rate was quite high, because it’s become quite common.”
Another new feature to be introduced will be adaptive driving beam, something that’s appeared on luxury cars now and will trickle down into smaller ones. It will be on most of the new Isuzu trucks next year.
The Isuzu strategy, at this point, is to talk about the safety systems now and go into details about engine and transmission specifications later. One of the buzz words used by Isuzu at this launch was ‘modularity’, suggesting common componentry across the
a fuel cell without having to completely
All of this technology will be on display at the 2025 Brisbane Truck Show, planned to be the official public launch of the 2025 range and the first public showcase on the entire range.
“The way we are doing this new model roll-out this year is very different to the way we have done it previously,” said Andrew.
“The reality is, the world is such a small place, and when a truck gets launched in Japan, all of a sudden it’s all over the internet. So our customers here in Australia are across it and we can’t control the messaging.
“At this point we are choosing to just focus on fundamentals, which is our safety suite.
“This is such a leap forward, not just for Isuzu, but for the trucking industry, it’s a story that deserves focus in and of itself. Please don’t underestimate the differential between what is being mandated and what is available in our safety suite.”
Two young diesel mechanics have had the opportunity to broaden their horizons within the transport industry thanks to a scholarship initiative
Truck driving is not the only job within the transport industry that is experiencing a worker shortage – this also extends to the workshop.
Businesses are continually on the hunt for new mechanics entering the industry to keep their trucks on the road, but this has proved to be a
challenge for many. Initiatives like the Cummins Scholarship program are just one way this is being confronted.
Four apprentices were awarded scholarships this year, getting the opportunity to further their knowledge within the industry.
This was done through a visit to Cummins’ plant in Victoria, as well
as getting the chance to experience the Australian Trucking Association’s Technology and Maintenance Conference in Melbourne in October.
For Josh Troeth of Tatiara Truck & Trailers in Bordertown, South Australia and Zethaniah Copland of McColls Transport, South Geelong, the program was unlike anything they had
done within the industry before.
Josh has just entered the fourth year of his apprenticeship as a diesel mechanic for Tatiara, servicing trucks that come through the workshop on their journeys from Melbourne to Adelaide, as well as performing outcalls for breakdowns and other jobs on the road.
He also works on the local fleets, predominantly servicing Kenworths and DAFs, with the occasional Volvo and Scania coming through.
As prospective recipients had to be nominated by someone within their workplace, you could only guess that the scholarship came as a massive surprise.
“I didn’t know I had been nominated for a long time,” Josh explains.
“One of my coworkers organised it all and my boss got it running. I got a phone call while I was on a job, and I thought it was a scam call. I called them back and found out I’d won!”
Getting out to the Cummins plant was the first part of the package included in the scholarship, before attending the conference.
Josh says that the tour helped him to appreciate other parts of the industry that he hasn’t had much to do with yet.
“I’ve been to the Kenworth factory before, so I’ve seen the motors fitted out and ready to be put into the trucks, but it was pretty cool to see them where they start,” he says.
“We got to speak to the service staff who are on technician support 24/7 and get to put faces to names.”
Zethaniah, or Zeth, echoes the benefits of gaining a wider perspective on what happens beyond the workshop in the greater industry.
He had thought for sure that winning the scholarship was an elaborate prank: “yeah, very funny,” was the initial reaction to the voice over the phone.
But it certainly felt much more real once the recipients arrived at the plant.
“During the walkthrough we got to watch the techs put wiring harnesses on the motors,” Zeth says.
“It was good to see the other side of the industry. I don’t get exposed to that all too much.”
Zeth began his mechanical journey in 2019, when he first started at McColl’s. He’s been there ever since, despite describing his journey there as “falling into place”.
“I’ve always been a work with my hands sort of guy,” he says.
“I’ve always been interested in cars, bikes, boats, jet skis, trucks; anything that’s got a motor in it I’ve always been fascinated by. I never liked the idea of paying someone else to work on it for me.
“I haven’t looked back since I started to work at McColl’s. I love working with my hands and at the end of the day being able to go home and knowing that I’ve worked hard for my money.”
The TMC gave the scholarship recipients the chance to get a look at parts of the industry that they don’t usually see, with technicians, operators, drivers and other interested parties flocking to the Kangan Institute.
“It was good to see the other side of the industry. I don’t get exposed to that all too much,” Zeth says.
“I got to hear different perspectives from an array of different workshops. To hear about truck and dogs, because I mostly work with tankers, I got more learnings about other set ups.
“There’s more to the industry than just what I’m seeing. It makes me feel like I’m a very small fish in a very big pond.”
“Speaking to the different people at the TMC was my highlight of the whole experience,” Josh adds.
“THE REASON I DO THE JOB IS THAT I LIKE SOLVING PROBLEMS”
“Lining up for lunch, I was speaking to one of the drivers of the new DAF XG with the Euro 6 Cummins engine in it. We ended up speaking for the next 45 minutes. That was really interesting to have his insight on what he experienced driving it.
“There was a lot of people that don’t work on the floor there, I thought there’d be more service technicians.
“One of the sessions that I took a whole bunch of notes on was the new after-treatment for the Cummins’ engines session. It was good to know what’s going on and being discussed in the industry.”
Josh had a particularly unique experience at the conference, travelling with Tatiara Truck & Trailers co-founder John Jenkin.
They took the chance to visit clients while they were in Melbourne, and it give Josh new perspective on where a long career in transport can lead.
“John won the Craig Roseneder Award at the TMC, and the amount of people that knew and had respect for him was pretty extraordinary to see,” he says.
“I met so many amazing people that have done so much in the industry and in their careers just from
talking to John and talking to them.
“It’s definitely opened my eyes to how big you can grow your career and business.”
As a fourth-year apprentice, Josh has steadily been taking on more responsibility in the workshop as he learns more on the floor.
Unlike many people who work under and inside trucks, he didn’t get into the industry with any background in transport, or even plans to work in it. He had originally intended to study media at university, before realising after finishing high school that the uni lifestyle wasn’t for him.
“Working as a diesel mechanic was never even something I considered until I finished school,” Josh explains.
“There was a guy I played footy with in my hometown, he was a mobile mechanic. I worked with him for a couple of days to try things out, and I liked how he operated and the work he did. He pointed me down to the Tatiara workshop and that’s how it happened.
“Now, I’m going into my fourth year
as of the end of January. The three years have already flown by.”
A lot of his work is done on local fleets and owners in the Bordertown area, but there are bigger fleets that Tatiara services too.
Josh will perform axle replacements, engine rebuilds and welding work, as well as take on warranty jobs.
He says that the day-to-day challenges keep the work fresh and exciting.
“The reason I do the job is that I like solving problems,” Josh says.
“I knew absolutely nothing about it, I didn’t even know the spanner sizes. The further I get into the job, the harder the problems are getting, which I like.
“I love working with my hands. Nearly every day it’s something different. It’s where I like to be.”
For nearly two years now he’s also been going out on the road, doing call outs to breakdowns and any other issues that arise with trucks on the road.
Josh says this has been one of the greatest things for his career as a mechanic yet.
“My biggest hurdle was communication. I was 19 when I started my apprenticeship, and I’d only ever had farm jobs. That was one of the biggest learning curves for me.
“Fatigue management was new, and it all hit me like a truck when I first started.
“Having to do all the work yourself and figure it out, it’s all been the best thing. It forced me to become a better mechanic. I love doing it, and that’s why I do it.”
Zeth is focused on the McColl’s fleet itself, doing preventative maintenance works and servicing breakdowns.
He has the unique opportunity to work across McColl’s different locations, which he says has inspired him to pursue a different side of his mechanical career.
“I’ve worked around Tongala and Echuca, and Altona too,” he says.
“I’ve worked on an array of different tankers from farm pick-up to dangerous goods tankers.
“We cart latex out of Geelong as well as milk, cream and oil. It’s not one type of carting, so it’s good to get posted around and see different sides of things.
“You’ll do a two or three-week stint at the other workshops. They’re usually pretty flat out, so we try to give them a chop out when we can as we’re a little bit slower in Geelong.
“I’m working towards heading to the army. I think that’s a great pathway especially for younger guys. You can get posted anywhere, and you get to travel around Australia.
“Then on your time off you can do bits and pieces with transport companies that you never would otherwise. You can do part-time work there and get to know them.”
It’s the same trusty workhorse, but not as you know it. Pairing a fresh new design with the features that have made it Australia’s hardest-working light-duty truck. The new look Fuso Canter is now bringing even more to the job site – including brighter LED headlights, a sleek new exterior, and enhanced 8” multimedia touch screen with wireless mobile connectivity. Plus, class-leading payload across most models, active safety systems*, and impressive 30,000km service intervals to take your business further.
The ATA’s Technology and Maintenance Conference was the scene of an important discussion on the future of zero emissions
October saw the return of one of the most highly anticipated events on the trucking calendar – the Australian Trucking Association’s Technology and Maintenance Conference.
The conference was focused on the more technical side of the transport world, with talks about new technology, zero emissions, and the nitty gritty of looking after the parts and technology inside trucks.
There were also a number of live demonstrations, showing off new facets of engines from Cummins, brake testing from Knorr Bremse, and a lesson on how to manage electronic braking and safety systems.
At the forefront of these opportunities was the theme of innovation and how to stay on top of the new and emerging technologies across the industry.
The move to alternative fuels and the rush towards decarbonisation is top of the agenda for the industry’s leading associations, and the topic was tackled at the TMC with a panel comprised of ATA CEO Mat Munro, NatRoad Head of Policy Samuel Marks, ALRTA Executive Director Rachel Smith and zero emissions expert from bp Chris Leat.
With deadlines fast approaching for emission reduction targets, these four industry leaders had plenty to say.
The ATA’s Mat Munro says his organisation has been undertaking significant consultation with the federal government, including multiple meetings across 2024.
“In 2022 the federal government legislated emission reduction targets of 43 per cent and net zero by 2050, with
reference to 2005’s emissions figures,” Mat says.
“Recognising that transport is the third biggest emitter, and without further action may be the biggest by 2030, earlier this year the government engaged in two further consultation processes. The time for developing clear industry positions on these matters is right now.
“In responding to the government, the ATA consulted our members, the HVIA, and many key supply chain partners. In a broad sense, we concluded that the government should focus on the productivity of current fleets.”
Creating and getting high productivity vehicles on the road is one of the ways that the industry has identified of working towards decarbonisation without imposing major costs on Australian businesses.
The equation is simple – less trucks on the road, taking less trips, means
less emissions being created. But this isn’t necessarily possible for everyone.
Any time you look at making a switch to alternative fuels, there is inevitably a cost involved and the panel argued the government has focused too much on only funding moves to electric, and ignored other types of alternative fuels.
With his focus on policy at NatRoad, Sam Marks has seen firsthand how this has affected both the government and industry’s approach to alternative power.
“Decarbonisation is complex for government and for businesses,” he says. “There’s no point in having a plan that only takes a couple of viewpoints into account. The lack of a plan to date has resulted in uncertainty.
“At NatRoad, we’ve had a focus into policy research. We’ve also focused on collaboration. Because this transition is so broad in its impact, it’s important to have those connections.”
Sam believes that more funding needs to be put towards developing incentives for businesses to look at hydrogen or bio-diesel as well as electric.
“It’s important to recognise that the government needs to spend some money. We can’t have emissions reduction on the timescale the government accepts without accelerating the adoption.
“Businesses and industry need financial assistance to get there. Our industry white paper set out key areas of focus. There are also strategies and policies that government and industry will need to work through.
“Regardless of what government may or may not do, there are things you can do today to better position your business for emissions reductions for future expectations from government and customers.
“We’re offering a framework through a five-phase plan to help businesses start thinking about decarbonisation. It’s important to work out what you’re trying to achieve and managing and measuring your emissions. Figure out what options apply for you.”
When looking at the rural transport industry, electric almost appears as a non-option with the current power and infrastructure available.
Even the highest-rated, top of the line, prime movers are barely managing to hit 600km of range at a full charge. When travelling across regional Queensland or Western Australia this massively limits the
nowhere to charge them.
“We face some unique challenges that aren’t present in the USA or Europe, and we’re even more urbanised than China with a smaller population,” ALRTA Executive Director Rachel Smith says.
“The distance that we travel is huge, and we carry much higher masses. Governments haven’t been technology agnostic; they’re very much committed to an electrification journey, so there hasn’t been much investment outside of battery electric vehicles. The next challenge is then grid capacity.
“We’ve got targets and commitments on electrification, but in heavy vehicles, in a rural setting, we need a range of 1,200km or more. We’re just not getting that at the moment. What works for inner city last mile delivery won’t work in the bush. We need investment in renewable diesel, where the engine won’t know the difference.
“We’ve seen a lack of funding in
which make up 77 per cent of our network by a deficit of 1 billion year on year. That comes with increased maintenance costs and loss of efficiency. We also need access for the most efficient routes, and higher productivity vehicles.”
Top fuel providers like bp are also looking at how they can provide the industry with the infrastructure and supply required to get a significant fleet of alternatively fuelled vehicles on the road.
As an expert in zero emissions technology at bp Chris Leat echoes the sentiment of NatRoad, saying more government incentives will be required to come close to meeting decarbonisation goals.
“What seems unfathomable today, might be achievable when supported by government incentives, policy and market demand,” Chris says.
“We know that the energy transition will follow an unpredictable path, and we know that it will be a patchwork of solutions that will get us to net zero.
“We can take an annual outlook at the types of fuels that will dominate the heavy transport sector.
“All of our projections are highly dependent on government incentives to help drive demand and adoption across the industry.
“The EU government have announced that 14 per cent of all transport fuels will come from renewable sources by 2030. As a result they have incentives to drive demand in the market. A lot of big industrials must decarbonise now.
“Bp is looking to trial activities overseas and bring that knowledge to Australia.”
The ARTSA Institute’s ‘Road Transport – embracing change and innovation’ conference took a lens to how all areas of the industry are tackling the future of transport.
The ARTSA Institute’s yearly conference offers a different perspective to many other similar events across the trucking world.
Each year, it focuses on a specific theme related to what is currently at the forefront of the industry, including the PBS scheme, truck safety, data insights and more in the past.
This year, the theme was ‘change and innovation’. Held at Surf Life Saving Victoria in Port Melbourne, attendees got the chance to hear from experts from key industry bodies
and truck manufacturers on the steps they are taking in the coming years in response to industry changes.
Reform and regulation were also key topics of discussions, with speakers from the National Transport Commission and National Heavy Vehicle Regulator presenting on the latest developments in their respective areas.
One of the final presentations for the day, also one of the most substantial sessions, came from Aaron de Rozario, the Executive Leader of Regulatory Reform at the NTC.
The commission recently penned a document explaining proposed changes to the Heavy Vehicle National Law, a number of which were endorsed by Australia’s transport ministers in September 2024.
While some changes have been seen as controversial, including increases in fines for a number of penalties, Aaron and the NTC believe that many will be beneficial to the industry overall.
“This was a review that started early, but it feels like it has going for 10 years,” he says.
“We are at a stage now where we have sat down for consultation on an amendment bill on regulations. What the NTC has been doing in the past few years has been working on behalf of the ministers to update the HVNL.
“Four key consultations and decisions have been made leading to our recommendations. The ministers endorsed 14 recommendations that the NTC made. We went out very specifically in August 2023 to look at some options targeting fatigue management, access and enhanced operator assurance.
“They then decided which of those options would be going forward. All of those things have been baked into the draft legislation.”
A new safety assurance system, which works to address the needs of operators more specifically, is one of the recommendations the NTC says should be introduced.
“We are going to have a tiered safety assurance system. The standard set of rules may not work well for operators, but they can work with the regulator to find alternate ways to reach their obligations. That really takes place in the fatigue space.
“For operators that get accredited, they’ll need to have a safety management system approved by the regulator. We’re trying to uplift that focus on safety. It will also expand driver duty to not drive unfit for any reason, not just fatigue.”
Mass limits will be boosted under the new HVNL amendments, being increased to match the current concessional mass limits. The NTC is also looking to increase the general access mass limit from 4.3m to 4.6m.
from the NHVR for advice on rollover prevention.
“This means that any truck that is able to be operating at 4.6m will be able to do so,” Aaron says.
whatever the new NHVR requirements are will also be able to operate at this height.”
General access length will also be increasing from 19m to 20m under the
SINGLE QUICK COUPLING MOTOR CAN BE USED WITH MULTIPLE QUICK COUPLING PUMPTUBES
NTC’s recommendations.
“This is subject to the NHVR determining the most appropriate controls to mitigate damage to road infrastructure.”
Written work diaries will be simplified, removing some mandatory requirements to make them optional instead. Drivers will no longer have to total up their rest hours.
Warnings will also be issued from now on from the NHVR for fatigue related offences. There will also be formal education introduced for infringements on work diary offences, as opposed to fines every time.
A new National Audit Standard will be developed by the NHVR and approved by ministers.
“If the audit regime for NHVAS has the appropriate robustness, then customers will be able to recognise their particular audit for transport activities that the operator is doing,” Aaron says.
Codes of practices will also be developed and approved by the NHVR, as well as changes coming to ministerial powers.
Gavin Hill from Transport Certification Australia hosted a session which allowed the biggest truck manufacturers to present their plans for the transition to zero emissions.
Representatives from Volvo, PACCAR and Daimler took a look ahead at their manufacturing future, and their unique paths to decarbonisation.
First was Aaron Lewis, Product Manager of Volvo Trucks.
The European brand is looking at a number of possible applications and paths they are weighing up when it comes to the transition.
“Our long-term vision is to become fossil-free,” Aaron says.
“We want to be more productive, but we have to do it within the confines in front of us. The most meaningful effort we can deliver in the transition is to help drive the decarbonisation of the transport industry.
“We’re aiming for 100 per cent CO2 reduction by 2040. This is our timeline that we’re working towards.”
Volvo is looking down three pathways when it comes to the production of alternatively powered vehicles – battery electric, fuel cell electric and combustion engines.
It has already recently introduced the new FH model to Australia, which is available as an electric model, as well as biodiesel options becoming available in Europe.
This is a part of its ‘product pathway’, which will help Volvo to reach its carbon emissions goals.
“Fuel cell electric is the new one we’re working on, which won’t be available until the end of the decade,” Aaron says.
“Australia is unique in its challenges, its environment. We have high temperature, high average speeds. This all makes a difference to how we build our trucks.
“To build development, sustainable solutions is what we start with and work
on. Fuel cell electric is still out a couple of years, but combustion engines are here to stay with biofuels.”
One common thread between the three OEMs was that they have all identified that different types of sustainable fuels will be applicable to different areas of the freight task.
Battery electric is typically suited to smaller travel distances, like last mile delivery and inner city driving. Hydrogen, fuel cell and combustion will then be more suitable for prime movers, and trucks that don’t have to stop and refuel, or charge, as often.
Jonathan Crellin, Product Program Manager at PACCAR Australia explained that these options are all being considered for the future of their truck production.
“We are technology agnostic. Through our Kenworth and DAF brands, we are developing battery electric solutions, hydrogen fuel cell trucks, hydrogen combustion through Cummins and DAF,” he says.
“But how do we focus on the Australian context, build zero emissions trucks that suit our customers going forward? The zero emissions solutions you need for your business will focus on what exactly you’re doing.
“However, we don’t think diesel is going anywhere, whether that is fossil fuel diesel or a HVO biodiesel fuel.”
Jonathan says that PACCAR is focusing on the payload impact that fuel cells and batteries will have on trucks.
While mass increases are being pursued, there is always going to be the fact that these alternatively fuelled trucks will be carrying more weight by design.
He says that impact can’t be ignored by manufacturers.
“Without any axle mass concessions, that weight is coming off your payload, and your payload is money,” Jonathan says.
“Hydrogen comes with heavy fuel tanks. While hydrogen and diesel are similar, electric wins out. The challenge lies in charging time for batteries.
“The big killer will then be the cost of the prime mover. The early adopters are going to have a big cost, and that might be where ARENA funding is required to get alternative fuel trucks in the early stages.
“We need hydrogen hubs to come further before you can confidently run hydrogen-fuelled vehicles in road transport. Unless you can get government financial support, the cost of freight in this country is going to get significantly higher.”
PACCAR, in its development of trucks for Australia, is still primarily focused on heavy duty trucks and prime movers.
Electric may not prove as a viable path forward for this sector of the industry, with long haul and interstate travel the primary focus.
“At least 80 per cent of road transport is done by heavy articulated vehicles, and that’s only increasing,” Jonathan says.
“How are we going to keep building trucks that can suit the transport task in Australia? On average, a Kenworth K220 does 570km a day.
“Trying to convert those to an alternative fuel solution will be a very big challenge into the 2030s and 2040s.
“Using bigger combinations is one way our operators are trying to reduce their CO2 emissions.”
Head of Vehicle Homologation at Daimler Truck Australia Pacific Romesh Rodrigo says the manufacturer is focusing first and foremost on electric development.
He says they’re facing a ‘zero emission vehicle energy quandary’, with the current lack of infrastructure limiting how both OEMs and businesses can approach beginning their moves towards alternative power.
“Electric trucks are great in concept, until you need a charger,” Romesh says.
“Battery electric is what we have here now. The key thing that we want to hone in on is that our future is based on electric power.
“We’re going into a scenario where the energy form is up in the air. What we are looking at here is the power source we need to fuel trucks, whether that’s battery electric, hydrogen fuel cell or hydrogen combustion, we need electric power. Everything is aligning to single power source.
“The engagement level we have at the moment is with the Department of Transport. I want to present the argument that we need to be engaging with the Department of Climate Change
and Energy. We have to start looking at how do we address our challenges.
“This isn’t limited to axle loads, but we’re talking about payloads with zero emissions. We need to look at how we support these vehicles with infrastructure.”
While it was the host of the conference, the ARTSA Institute itself had its own major presentation to give, based on the findings of a study into dynamic loads on trailer couplings.
Conducted in association with the ATA, TIC and HVIA, it came about almost from necessity. Funding through the NHVR’s Heavy Vehicle Safety Initiative allowed ARTSA-I to conduct their first study in the area in 37 years.
As those who work with trailers would know, combinations have changed greatly since the late 80s, a time when B-doubles were a new venture.
ARTSA-I executive member and Chair of the working project group Martin Toomey released the findings ahead of the conference, with a number of key discoveries made.
The project involved the measurement of the coupling forces on quad-trailer 160 tonne road trains in situations that would mimic their daily routine over hundreds of kilometres in the NT.
An instrumented dolly was then used through different positions and combinations on the road train so the research team could measure the forces at different locations.
“Australia has always been a global leader in high productivity road freight,” Martin says.
“There was a lot of uncertainty about the engineering calculations needed to manage the forces of those extra combination vehicles.
“The previous study has never been revisited. We’ve now got vehicles operating in Australia that are much heavier. We put stress sensors on it and we could see what was happening under those new extreme forces.
“We could then validate those findings and come up with conclusions and calculations.”
Well-respected engineer Robert Smedley, the Managing Director of Smedley’s Engineers, was one of the
leads on the project, responsible for one of the research streams.
They tested combinations including AB triple and AAB triple, and used the dolly to test the forces of the exact same load across different combinations. Most of the travel was done between Darwin and Katherine.
“We had a lot of different roads with lots of different surfaces and crossings to give some extreme test outcomes,” Robert says.
“In order to measure the forces accurately, we created arrays of load cells. Each one is calibrated, we designed them ourselves and road tested them. When you combine them in an array, you can get a load force path which operates in all six axles.
“You can get a very good picture of the force and the direction of it.”
With the movement of the dollies across the combination, the research team could get a strong idea of how force affects every trailer coupling along the truck.
They found that the forces throughout the coupling were similar no matter whether the dolly was underneath the second, third or fourth trailers. This was contrary to the conventional understanding that had been developed previously in current Australian Standards.
However, the peak forces that were experienced across the combination were in line with what was expected from the formulas provided in the Australian Standards.
One of the more interesting results from the experiment was that there was no evidence that maximum force would plateau as combinations got longer, with more trailers. Peak forces were proportional to the overall mass of the combination, meaning that it is dependent on weight, and not the amount of trailers.
Extremely high forces would most commonly occur when the vehicle was at very slow speed or coming to a stop. This included situations where the vehicle was braking, shunting or being manoeuvred.
The highest overall forces were measured while underway at low speed over floodways, which would be particularly relevant to rural operators.
With the introduction of a 500hp engine in a small P Series truck, Scania has come up with the same thing in a smaller package for those looking for useful power in an urban prime mover capable of hauling a fully loaded B-double as Tim Giles found out
There’s a wide range of niches and subsets in the trucking industry which suit a particular kind of truck and it’s the job of the truck manufacturers to make sure they offer a wide enough variety of models to be able to fit into as many of their customers’ pigeon holes as possible.
Scania has three cab sizes, the R, G and P. The R Series is designed for the heaviest loads on the longest runs, G Series fitting into the intrastate and tipper markets and the P Series ideal around the city, in crowded environments where the ground level visibility of the lower smaller cab is key to a safe journey.
Up until now the P Series has been denied the higher horsepower end of the Scania 13 litre engine’s rating. The cooling package capable of handling the heat output from a top power 13 would not fit under the low cab engine tunnel.
However, with the advent of the Super engines from Scania in the past couple of years, it was found that the more fuel-efficient engine didn’t produce the same level of heat rejection as its predecessors and the cooling package under the P cab could handle the job. Hence the Scania P 500,
which was tested on the roads in and around Melbourne on a grey day with the rain slowly clearing.
On the test, we managed to get some time in both B-double and single trailer combinations on the sorts of roads these trucks would be expected to handle on a daily basis.
Anyone who has driven a large B-double or even a heavy semi-trailer in tight situations in this environment will tell you that sitting with the cabin lower to the ground and better allround visibility at that lower level is always going to be the safer option. Heading into a crowded yard in a tall highway prime mover can quite often be quite problematic in tight situations.
Walking up to the truck and climbing two small steps up into the cabin, it is clear this is an easy truck to get in and out of — useful on a series of urban runs.
Sitting in the driver’s seat and looking around it is also clear the visibility is good enough for the driver to be able to see any people walking around close to the truck and any objects which may get in the way during tight manoeuvring.
Out on the highway, trying to get a B-double fully loaded to over 50 tons up to highway speed is relatively
simple. The 500 hp kicks in and will satisfactorily get the whole rig up to cruising speed.
If you climbed four steps up into a roomy cabin and pulled out onto the highway, you would expect to get the kind of acceleration you need to get going, but it comes as a bit of a surprise when pulling the B-double up a slope out of a facility to find out you can do it with the 500 P.
There’s enough power under the hood to get the job done, with 500 hp available at 1800 rpm and a decent 2650Nm of torque (1955 ft lb) available all the way from 900 rpm to 1320 rpm. This is the kind of performance which would surprise a driver used to horsepower ratings in the low 400s and having to work hard to manoeuvre a B-double with containers in a tight container yard.
It is also surprising that sitting on a driver’s seat which is set just over 300mm lower than in the higher cabs, that visibility at ground level is so much improved. If there is any disadvantage, then one of them would be that out on the highway on a rainy day, the clearer visibility in the higher cab would come in handy, where the driver is above the spray coming up from vehicles around the truck.
The utility of a truck designed like this, within a fleet which includes a variety of prime movers handling different tasks, is that even if the truck is normally handling relatively small loads over short distances for most of its working life, it would be capable of being able to pick up a loaded B-double set and run it to a changeover in Tarcutta, or something similar, without any major problems.
This smaller cabin still has a reasonably sized bunk which would
be adequate for drivers to get a decent rest when required, but if the driver had to live in something like this for a week, they would certainly prefer the larger G or R Series cabin.
This truck comes with a standard set of safety systems, including electronic stability control, traction control, lane departure warning and blind spot monitoring. The blind spot monitor’s side-mounted radar units are fitted
into a neat package as part of the mudguards for the front wheels and effectively monitor both sides of the truck as vehicles or other objects or pedestrians come into that space. On each A pillar there is a small orange light which illuminates if there is something to be concerned about in within the range of that side’s detection system.
There is also a radar in the front bumper, used in association with the forward-looking camera mounted in the windscreen to enable the function of both the adaptive cruise control and the automatic emergency braking. When driving, the relatively subtle orange warnings lights on the two A pillars are effective and will grab the driver’s attention when they are looking to turn or manoeuvre in a tight delivery situation or in busy city traffic.
There have been plenty of buttons on the Scania steering wheel for quite some time, to go along with the recordbreaking number of buttons on top of the door, where not only the windows and mirrors are controlled, but also the vehicle’s lights.
Those steering wheel controls give the driver easy access to normal cruise control functions and the adaptive cruise control, all of which can be seen, when activated, directly in front of the driver.
We will see the current analog display in front of the driver being replaced with a new screen in the next year or so, but the dashboard will look pretty much exactly the same as the current analogue set-up, only on a digital screen. The new digital set up arrives at that point, as it also complies with the new cyber security regulations which come into force next year in Europe.
This new model from Scania is aimed at what is already a very crowded marketplace. Virtually all of the truck manufacturers in Australia have a product which will compete in the small urban prime mover sector with power ratings varying from the mid 400s up into the low 500s.
Over the years, for Scania, the R Series models have dominated the sales figures the Swedish brand has
extending its reach and joining the other European brands in trying to ensure that it has a truck portfolio which includes vehicles specifically targeted into new sectors, previously dominated by lower specced vehicles.
The advent of higher demands both from truck buyers but also their customers for a higher level of safety systems on board in the truck,
is already in place for trucks working on major infrastructure products both in Melbourne and Sydney, means that operators are looking towards brands like Scania and the other Europeans in order to meet their requirements.
The introduction of models like the 500 P and the development of the Scania brand over the last 10 years or so has enabled Scania to move from
supplier running at about four per cent of the heavy duty truck market, to the position where it is now, regularly, surpassing eight per cent of the heavy duty segment in Australia.
This engine specification is available across the P Series models from a 4x2, 6x4 or 8x4 prime mover to 6x2, 8x4 or 8x2 rigid, if required. In fact, for Scania, the Australian truck
market becomes a more level playing field when it comes to twin steer. Euro 6 doesn’t come without penalties, and one of those is added mass from the new emission systems and a lot of this sits over the steer axle.
Although, in magazines like PowerTorque, we often talk about a truck and highlight the horsepower rating of the engine, it is actually the torque rating which gives us that feeling of being able to get the vehicle to behave as it should and respond appropriately to the right foot of the driver. This kind of really useful torque is what this particular engine does deliver with full torque available all the way from 900rpm through to 1320rpm. This type of performance provides the vehicle with flexibility to make it a more useful tool. In fact, it was a Scania executive in
the UK who once had one of his major national corporate clients ask him if the trucks could be delivered, not with the horsepower rating on the door, but with the torque rating. The logic of this was that it was the torque available to the driver which was the attractive aspect of a truck’s performance and would keep the fleet’s drivers happy.
On the 500 P, this higher torque rating, combined with the fact that this is the Scania Super engine, means that the operator is getting much improved performance but is unlikely to be spending much more at the fuel bowser than they would be with the lower horsepower prime movers.
The other factor which makes this vehicle extremely easy to drive is the fact that, with the flat top torque curve, the AMT has plenty of flexibility to make changes in the transmission which will help fuel consumption without any compromise in the way that the power and torque are reaching the drive wheels.
This kind of drivability, combined with fuel efficiency and the smooth
transmission changes which are possible, makes for a very pleasant driving experience and leaves the driver confident that in any situation the automatic systems will be in the right gear at the right time with the right amount of power, or torque, to do the job required.
When it comes to the latest safety systems, which are now becoming mandated, and will be appearing on all of the trucks this magazine will be reviewing in the future, it will be possible to start differentiating between them, finding out exactly where the sweet spots are for each variant being used in real conditions.
At the moment, as the new technology arrives in every truck coming to market, we will start to see the difference between not only the basic technology being put in place, but also the interface which the truck manufacturers develop to make it easier, or sometimes harder, to use effectively as a safety system.
It may be the case that, as the systems become more and more
common and are found throughout the truck fleet, we will see different preferences appear for operators as they get used to all of these new systems.
As these changes come through, the way that the European truck manufacturers are able to integrate all of these systems within the basic infrastructure of the truck may well be an advantage for them
On the other side of the coin, the fact that there is European truck manufacturer involvement in trucks coming out of North America and Japan means that a global technology will become common throughout most of the trucks coming into our market here in Australia. This is where the interface with the driver may become the differentiating factor.
For now, we are seeing a 500 hp engine in a small heavy duty prime mover, which seems to be quite a useful addition to the Scania range. It will enable the Swedish truck maker to fill a few gaps in the market in where it has not been a player in the past
While Hino is facing production challenges over the coming years, it is taking the opportunity to take a shift in its market approach
Like all truck OEMs, Hino has a firm eye on what the future of trucking in Australia is going to look like, and how they are going to respond to it.
While their next steps are built on the requirements of the market, including Euro 6 compliance, they are also taking on the effect of internal challenges until the end of 2026.
The next two years beckon with a focus on the sales of two model ranges – the 700 Series, and the Hybrid Electric.
Due to an issue with Euro 6 emissions compliance in 2022 in Japan, a flow-on effect has meant that Hino hasn’t been able to begin Euro 6 production for vehicles coming to Australia as quickly as anticipated.
While current orders of the 500 Series will be delivered to Australian customers over 2025, it will be essentially ‘sold out’, and not taking new orders until as far away as late 2026.
This will see Hino focus on their current Euro 6 offerings, as Hino
Australia President and CEO Richard Emery explained at a media briefing in October.
“We have two products that are already Euro 6 compliant, so we will have a big focus on these two products over the next two years because they are ongoing,” he says.
“We’ve got an order bank on the 500 Series that we will be able to supply. We will then see a gap in supply of 10-plus months before we restock with Euro 6 product in late 2026.
“While it isn’t ideal, we’ve managed to balance this approach in our conversations with dealers and customers. The 300 Series will also have a gap in availability. We’ll sustain deliveries until the first half of early 2026 before it will also see a gap in production.
“It’s not a secret in 2022 we had to deal with an emission and certification matter. It was not just Australian product, but it also impacted the domestic market in Japan.
“Through that, we were able to review and revise existing product
lines. In doing so, we stopped all production on Euro 6. Though it’s frustrating for us, our executive team and dealers support this. We’ve taken our network through this.
“Although they’re disappointed and frustrated, they’re staying committed to our joint business through 2026. They support our plan until we get into a normal trade environment in 2027. It’s too early to flag what that will mean for our volume in 2026.”
Not having a full product line available for at least 10 months is going to prove a challenge, Richard admits.
However, it offers the chance to grow sales and market share of Hino models that haven’t been a massive focus in the past.
Hino expanded its Hybrid Electric range in 2023, and while part of this new approach is to consolidate the available models, the OEM is aiming for significant growth in sales across both it and the 700 Series.
The 700 Series meanwhile was last updated in 2021, as Hino’s modern heavy-duty range.
“We still think there is a significant growth opportunity for the Hybrid Electric,” Richard says.
“Our ability to free up the supply line for the 700 Series has been a challenge over the past few years. We believe both of those products can get to 1000 units a year over the next few years. In this window, there’s no reason why they can’t reach that goal.”
As a part of the briefing, Hino presented some of the figures surrounding their sales across 2024, looking back on how the market has developed over the past four years since the advent of the pandemic.
Looking at figures from October 2024, Hino had sold 4,193 trucks in Australia in the year to date, which was tracking extremely similarly to the 2023 figures.
While there was a boom in sales immediately following the pandemic, this is now starting to level out.
“We’ve certainly seen some softening of the market in the past six months after being on a strong run,” Richard says.
“That’s manifesting itself in the light segment, and at the discretionary level. Tradies, retail, mum and dad businesses that may have a ute and a handful of trucks.
“At the corporate level, they’re still
consistent and robust. The market’s been running pretty strong postCOVID. It’s getting potentially back to a ‘normal’ level of units sold.
“There was an acceleration in 201718, settled back down in COVID, but then past 2020 there was a bit of catchup on the latent demand.”
Richard believes that many truck OEMs have almost hit a limit on how quickly they can get trucks out to customers with the supply challenges that the pandemic provided.
This is especially in consideration with the change in what Hino can now produce with Euro 6 emissions in mind. There’s an expectation for a drop off for sales from late 2025 until production on the 500 Series can continue.
“Most of us found it hard to keep up from a supply perspective,” Richard says.
“The industry has held the number back across 2022-23 because of those supply issues. Some of it is structural issues, some is supply, and some is the market cutting back a little bit.
“We think the market is banging up against a glass ceiling due a number of things including lack of supply, getting bodies built, shipping out of Japan and other markets as well. We are bullish about the market out to 2030.
“We believe OEMs are working to control and increase capacity to finish products, and that will break through that ceiling. We’re basing our supply on getting a truck out in 90 days, but
that’s blown down to 120 days. Some customers are waiting for bodies to be built for six to nine months.”
Richard sees an advantage for Hino in its parts and distribution centre.
When they aren’t able to produce as many new trucks for customers across 2025 and 2026, this will continue to offer a servicing option for customers with older fleets.
“Although we’ve talked about our investment in our parts and distribution centre in numerous occasions, we can’t stress how much it has impacted our businesses,” Richard says.
“It has doubled our capacity for our parts business. When supply of new vehicles was under pressure, clients were keeping their old trucks longer. We did see a surge in maintenance across COVID.”
One of the challenges that Hino has faced in recent years which has drawn out production times is delays in the supply of bodies.
While some are built out of Hino’s home country of Japan in factories with full production lines, much of the Australian body building industry is kept relatively local and small-scale.
Like many other OEMs, Hino is beholden to the capacity these body builders are able to supply.
“Our body building industry in Australia is majority mum and dad businesses,” Richard says.
“We build our tippers out of Kyoto in
Japan. It is a production line. We don’t have that scale here. When we spoke to our bodybuilders, they said they didn’t want to commit to a bigger shed and they didn’t have staff.
“30 per cent of our supply line in Australia is already over an 120 day wait. It is certainly a structural issue that we have to work on. It’s in our interest, our dealer’s interest and our customer’s interest to get right.”
What is then done locally comes with significant logistical challenges.
“We have a heap of distribution challenges,” Hino Australia Manager of Product Strategy Daniel Petrovski says.
“We do plenty of alloy trays, but they’re all coming out of Sydney. We can’t do a deal with three different bodybuilders in three different states.
“There’s a balance of 120 days vs 60 days, what’s the cost against the freight task and the quality and warranty? Standard warranty has gone from three to five years, and we have the body included.”
With the greater production of the
Hybrid Electric, Hino is also eyeing off the challenges that brings in the workshop.
Like other areas of the industry, workshop mechanics, and specifically those with expertise in working on
Three months on from announcing a change of name from MaxiTRANS to Freighter Group the trailer specialist is stepping into 2025 with big plans
Tto stand out on truck trailers all across Australia, reflecting the company’s on-going evolution and strengthened connection with its customers.
The Ballarat-based trailer manufacturer recently invested heavily in its state-of-the-art factory and invited customers, suppliers and media along to witness its progress at a grand re-launch event in October last year.
Speaking to PowerTorque in the lead up to Christmas, Freighter Group
says the new name had been well received by the market and the focus going into 2025 was all about meeting and exceeding customer expectations.
He said the Freighter brand had been part of the transport world in Australia since 1946, when the first trailers carrying the name were released to the industry and the new name helped to tie the business back to its heritage.
Greg was upfront about the challenges the company had faced
COVID, when it came to being able to deliver its quality trailers in a timely fashion.
“We recognised where our shortcomings were. The investment into our manufacturing is just one part of our broader plan to address those so we can continue to improve and be more responsive with changing market demands,” Greg says.
“And that’s our goal, whether it’s response time, lead time, delivery and accuracy.
“We want to be the best possible company we can be that can respond to customer needs.”
The $50 million advanced manufacturing facility upgrade at Ballarat is the biggest step forward in the business since MaxiTRANS was bought by a group of local private investors in September 2021.
Greg says the management team is determined to create a new era for the future of the company and the trailer manufacturing industry in Australia.
“This investment has seen the introduction of state-of-the-art equipment and an expansion of the overall footprint of the facility, transforming it into a modern manufacturing environment,” he says.
“The completion of the upgrade puts the business in a position to be able to continue to evolve with the changing needs of our customers long into the future.”
For customers, there are significant upsides to the change.
Freighter Group will now supply spare parts directly to customers through its national Dealer network, a change from the previous agreement, now expired, where parts came from MaxiPARTS.
The group has also launched its own Hitcher Parts range to support its own products and, eventually, aftermarket needs as well.
As another way of assisting customers to get moving quickly, Freighter Group will offer a Ready Range of trailers that are designed to fast-track the time from order to delivery.
“With almost 80 years of experience designing and manufacturing trailers for the Australian market, we have developed a Ready Range solution across our expansive product offering that consists of specifications suited for a wide array of applications,” Greg says.
“This allows our product to be more competitively priced, further streamline the ordering process and deliver shorter manufacturing lead times.”
For those working in the refrigerated transport space a collaboration between Freighter Group and Schmitz Cargobull has created the Freez-R
drivers and fleet operators real time information on driver routes, internal temperature monitoring, tyre pressures, fuel levels and all EBS data, as well as controlling the fridge plant to name just a few, which assists in boosting the efficiency of the operation.
Summing up the changes Greg says it is all about being ready to support the market: “All these announcements lead into our message that Freighter
Freighter Group also manufactures and distributes nationally a range of other market leading brands to the Australian market, including MaxiCUBE, Lusty EMS, Hamelex White, Trout River and AZMEB.
Across all of its brands, Freighter Group provides equipment for the general freight, temperature-controlled freight and bulk transport market sectors. To find out more, go online at www.freighter.com.au.
Hume Transport’s Nellie White is aiming to further advance her career in transport through the help of her new scholarship
It’s no secret that the transport industry is still a heavily maledominated sector. Organisations like Transport Women Australia Limited, led by Chair Jacquelene Brotherton, are helping to promote the importance of diversity in the workplace.
One of the ways that they are doing this is through the ‘Driving the Difference’ scholarship. 2024 was the sixth year the initiative has been run, giving the winners the chance to pursue advancements in their career. There were five recipients of the
latest round of scholarships, including Nellie White of Hume Transport. Based in Albury-Wodonga, Nellie works in transport operations across areas including fleet compliance and fleet allocation.
She is partially responsible for a
start, but after becoming familiar with how a transport operator goes about its business, the opportunity to get more involved in the operations side arose.
Along with her desire to tackle new challenges, it was a natural progression.
“I quickly grew out of accounts and thankfully my boss recognised I could be doing more,” Nellie says.
“He put me through compliance and operations a bit. Six months into my employment we had some stuff shuffle around, so I was offered a few roles. I could stay in accounts, go to
“I WOULD ENCOURAGE MORE WOMEN TO GET INVOLVED”
compliance, or operations, or go to Queensland.
“I knew I wanted to stay because I fell in love with it so quickly. The operations job scared me the most, so that was the one that I took.
“The boys said they wanted me in the ops room. They were really supportive and backed me in to do well there.”
A part of applying for the Driving the Difference scholarship was nominating a course or something similar to undertake to advance your career in transport.
Nellie chose a course at Wodonga TAFE to start the process of getting her licence, starting at HR with the aim of eventually working her way up to bigger rigs.
She sees it as a way to give her the flexibility to jump behind the wheel if needed, whether that be moving trucks around the yard or wherever else they may need to go.
“I see it as a handy thing to have,” Nellie says.
“When I moved into operations the boys were really keen for me to get my licence. I really wanted to get out there and see what it was like for the drivers, see it from their perspective.
“The boys suggested I get my licence, but I was terrified of that! They pushed me and I’m glad they did. I’ve always loved being out on the road.
“I’m not looking at driving as my main job but it will be a good thing to have.
“I just want to start at HR. My boss is pretty keen for me to go all the way, but it’s a discussion to have! Now when I start the course I’ve just got to get a bit of practice in and go for it.”
Hume also regularly brings their fleet to truck shows, and Nellie says she’ll be able to help get the trucks down to those.
“I just got a truck named after me, and I thought it would be cool to be
able to drive that truck to shows.
“I want to get a bit more out there with Hume and build our brand that way. There’s a whole culture in transport, and if you’re not out there on social media you can be invisible in this industry.”
Organisations like Transport Women Australia are continuing to offer opportunities to not just women, but anyone who wants to get involved with or further their career within transport.
Nellie says they have had a massive impact on her, and would advise anyone interested to look at what they can offer.
“I would encourage more women to get involved,” she says.
“Transport Women Australia have been great. It’s not just about women, it’s about everyone. We’re all in this together. That’s where they come from, and I love that attitude.
“I would encourage anyone to join the transport industry, it’s fantastic. It’s definitely a lifestyle, but you’ll fall in love with it so quickly. I never thought I’d be where I am right now, but I love it.”
Electrification specialist Zenobē is looking to off-site charging to solve a key issue in electric vehicle infrastructure
Electric infrastructure in Australia still has a long way to go – it’s one of the major factors, alongside cost and range anxiety, holding more businesses back from fully committing to making the switch.
Add this on top of our freight task being largely reliant on long haul trucking, an area which isn’t yet suited to electric vehicles, and the uptake is maybe not as significant as policymakers would have been anticipating when setting future decarbonisation goals in 2030 and beyond.
But despite this, there are still corners of the industry looking at how they can make the adoption of electric trucking viable for Australian businesses.
Global fleet electrification specialist Zenobē has looked to off-site charging as one solution for electric fleets that lack the infrastructure needed to operate efficiently.
It recently received a grant from federal government organisation the Australian Renewable Energy Agency (ARENA) to the tune of $8.5 million. This is being put towards establishing
an ‘electric charging hub’ in Mascot, Sydney to be initially used by Woolworths to charge its electric vehicles.
It will contain 22 dual-port DC fast chargers all equipped with smart charging software to optimise energy use while also using stationary battery storage made from repurposed batteries from old electric vehicles.
The ARENA funded project will also support a fleet of 60 electric trucks leased to Woolworths and the site has been built with additional capacity for other users, creating a multi-user charging facility.
Zenobē is an expert in the battery business, being the largest owner and operator of battery storage in the United Kingdom and supporting over 2,000 battery electric vehicles globally.
But right now in Australia and New Zealand, they’re working to upgrade and create new electric infrastructure for heavy commercial vehicles, having already completed five electric bus depots in the region since 2020.
PowerTorque spoke to Zenobē’s Australia/New Zealand Director
Gareth Ridge about the charging hub project and how it reflects on the changing landscape of electric infrastructure in the country.
“We had been speaking to a number of players in the market, truck fleet operators, fleet owners, and we also had very good dialog with ARENA thanks to the Leichhardt Next Generation bus depot project,” he explains.
“We know that trucking is prime for electrification, so we were trying to look at what some of the barriers are that we think we can solve through our financing and our ‘as a service’ business model.
“It’s very hard for the market to break that down on its own without some sort of funding support. We selected Woolworths because they were quite a motivated customer to work with.
“The industry identified to us that across a lot of industrial sites, they have space but not enough for all their commercial vehicles to be electrified. The other problem we saw in the sector is that most sites are short on grid capacity
“Even big companies like Woolworths may not have long-term
leases in place, making it difficult to upgrade the grid connection to house the infrastructure. That’s what we saw as the challenges to try and overcome.”
The charging hub is currently under development approval process with the City of Sydney, with the preliminary works and designs already completed.
Across January and February Zenobē will break ground on the install works, with the aim to have the site live and operational by June 2025.
Working on projects like the Ventura bus depot in Victoria and others across the previous few years has given Zenobē the knowledge and practical experience to take forward into the Mascot charging hub.
While truck and bus infrastructure has different requirements to be as efficient as possible, there are factors which can be applied to both.
“I think our experience in bus depot electrification gave us a strong knowledge of the charger types needed,” Gareth says.
“Off-site charging needs fast charging. The other lesson is building on what we already know. We’re understanding more about the site movements, we get a little bit wiser about what works and what doesn’t.
“We can also leverage things like our charging plans. Our internal data analytics team runs all the peak power modelling, and it’s all the same models whether that be for truck or bus as we can load in all the route data we require. Woolworths has a fairly good idea of the number of kilometres required per day, and we can load that into our model with all the different parameters and scenarios and sensitivities to see the outputs required.
“From that we can design what charging infrastructure is required.”
This particular hub is servicing trucks that are doing local deliveries – all on the smaller end of the scale at predominantly 4.5 tonnes.
While they won’t travel far from
South Sydney, they still require a full day’s worth of charge to operate their routes.
“The batteries will be fully utilised across a whole day’s run,” Gareth says.
“Mascot is an area which has a lot of commercial customers as well, so the payloads can be a bit heavier. For this we designed the depot in two ways, to make sure it meets the need for Woolworths but also futureproofed for any new customers or future needs down the track.
“The hub is currently oversized, but it’s done knowing that vehicles and batteries will get bigger, and we’ll be able to service them in the future and not be constrained by the charger capacity.
“Woolworths is the current anchor tenant, but they’re only taking up a portion of the site. We’re in discussions with a couple of other major logistics operators to use the other half of the site.”
One of the predicaments of electrifying trucking fleets is the need for space to either install chargers, or the need to find somewhere to charge your trucks off-site.
Both come with their issues – until electric charging locations become as common as petrol stations, operators looking to go battery electric will have to find an answer for one way or the other.
Off-site charging hubs are one model to solve this, giving trucking businesses easy access to a location without having to invest in the infrastructure themselves. For smaller businesses in particular, this cost can end up being a bridge too far.
Gareth believes that it could be one option for electric fleets in the future, but not the only one.
“Charging hubs will become a key part of the mix, but it won’t be the only form of electrification option,” he says.
“I think on site electrification for large customers who own their sites will be one part, because it’s always
easier to charge vehicles up when they’re back at base, if there’s space that is.
“But there is a large segment, that will need an off-site charging area, like those in last mile delivery. I do think organisations will start to design sites with chargers already built into them.”
While electric infrastructure is still in its early days, funding from ARENA is offering a significant incentive for not only transport businesses, but all sorts of organisations to think about whether electric is the right move for them to tackle their emissions goals.
For Zenobē, these funding programmes validate the need for electrification projects and the services it offers to electrify heavy vehicles in Australian fleets, driving forward the transition to zero emissions.
From their perspective, Gareth says electrification is still extremely early-on in the process Australiawide, but this is evidence that steps are being taken not just by them, but the trucking sector in general.
“I do see an inflection starting to occur in the last mile space and in the prime mover side of the middle mile,” he says.
“The industry is still in the trialing, testing and getting comfortable withit phase, which I understand. I think that’s what’s expected.
“I think we’ll see hundreds of trucks being electrified in the next few years because the economics are starting to stack up. There’s a lot of new truck OEMs coming to the market and the price is becoming more viable.
“On the prime mover and larger vehicle side, vehicle supply or options are still very limited. They’re coming but they’re just not there and they still cost so much more than a diesel engine.
“Compared to the bus side, there’s very little government funding to help. If it’s moving, it’s because it commercially makes sense, not because there’s someone telling them to do so.”
You would think that after six long years of reviewing the HVNL, the situation would be resolved, writes NatRoad CEO Warren Clark
It’s time to face the hard truth: the proposed HVNL reforms are underwhelming. The government’s latest draft amendments to the HVNL are incremental at best.
The reality is that if federal, state, and territory transport ministers continue to fail to act decisively, we risk missing an opportunity to deliver meaningful change for the road transport industry.
While there are some positive steps forward, the proposed reforms do little to address the real issues our drivers face daily. After so many years of discussion and consultation, it’s deeply frustrating to see a missed opportunity to overhaul a system that has not kept pace with the demands of modern road transport.
One of the most pressing concerns is the increase in penalties for offences. The draft reforms suggest a reduction in 21 penalties, but they also propose increasing 50 others.
In some cases, fines could jump by as much as 100 per cent, with maximum penalties nearing $30,000. This is a misguided approach that does nothing to improve road safety.
Instead, it will only exacerbate the growing truck driver shortage, which already stands at over 26,000 positions. How can we expect to attract and retain drivers when they are constantly being penalised for minor infringements, with little to no evidence that these fines improve safety outcomes?
We need to change the conversation around penalties. It’s time to cut the excessive fines that punish drivers for small mistakes. These penalties are not contributing to safer roads, and they’re not helping to solve the problems facing our industry.
The focus should be on fairness, not on imposing higher fines for the sake of political point-scoring. We have recommended more significant cuts to minor penalties and, importantly, the rejection of any new increases to penalties that do not deliver tangible safety improvements.
Another issue that must be addressed is fatigue management. While the draft amendments retain some flexibility, there are disturbing signs the government may be considering rolling back some of the progress made in this area.
Some operators who are currently on Advanced Fatigue Management (AFM) programs may find themselves with fewer options, and this could have a negative impact on safety. Fatigue management flexibility is essential for our industry, allowing operators to manage driver hours in a way that maximises both safety and efficiency. Taking that flexibility away would be a step backwards.
Lastly, there is a critical issue that has yet to receive the attention it deserves: heavy vehicle access.
NatRoad’s position is very clear: governments must eliminate at least 90 per cent of access permits by 2028.
The administrative burden of access permits is one of the most frustrating and inefficient parts of the current system, and it creates delays and disruptions that affect the entire supply chain.
In fact, if nothing changes by 2028, it will be said that the HVNL has been on a decade long road to nowhere. This issue is too important to shove into the too hard basket. It’s not too hard. It’s just a challenge, and our industry never backs away from a challenge.
Quite simply, we have a clear goal:
to see more streamlined access and a faster, more automated system for managing heavy vehicle routes. If we fail to act on this, we will be stuck with a system that continues to hold back the industry for another decade.
The proposed reforms to deliver automated access need more resourcing and a clear commitment to delivery.
Governments must show leadership and adopt a clear vision for the future of road transport—one that is fair, practical, and focused on real outcomes.
That means reducing unnecessary penalties, protecting and enhancing flexibility that allows us to manage fatigue, and tackling access reform with urgency. If these changes are not made, the last six years of review will have been nothing more than a missed opportunity to improve Australia’s road transport system.
For the sake of safety, fairness, and the future of our industry, we need bold, decisive action now.
Routine servicing and parts replacement is common sense for any heavy vehicle operator
For Cube Removals and ownerdriver Clinton Simpson, whose trustworthy 2014 Isuzu FRR 600 has clocked up almost 1.4 million kilometres as of this year, routine servicing is a necessity.
Spending an average of 127,000 kilometres on the road each year, Clinton has been behind the wheel of this particular workhorse for seven of its 10 years in operation.
He took ownership of Cube Removals in 2022, dedicating the specialist interstate removalist service to on-time delivery and the highest standards of freight protection, all while travelling huge distances across Australia.
A massive footprint across the country means Clinton can travel from the Victorian Coast to Far North Queensland and everywhere in between.
“The places I visit sound like the old ‘I’ve Been Everywhere’ song by Geoff Mack—freeways to goat tracks are what this truck travels regularly,” says Clinton.
“Blazing hot summers and flooding rains really do a lot of damage to outback roads, so that causes more wear and tear on the vehicle.
“I know too many operators who think they can push their vehicles and end up broken down in the middle of nowhere, or there are those who don’t use quality parts and either get stuck short term or do long-term damage— sometimes to very expensive trucks.”
Pre-planning the truck’s maintenance and using only Isuzu genuine and approved parts ensures it will perform reliably for Clinton’s clients.
“I am not mechanically minded, but I understand what is important to keep the truck on the road —and that is regular servicing from the team at Wagga Motors and using genuine Isuzu parts,” says Clinton.
“I know that the parts that have
been used in the truck are the same, if not better, than when it was built.”
The last scheduled service included replacing a range of hoses and fittings due to “the Australian environment’s effect on the rubber,” according to John Beattie, Isuzu Brand Manager at Wagga Motors, who takes a dedicated interest in Clinton’s classic Isuzu FRR.
“We scheduled this at a previous service so that we could have everything ready this time around,” says John.
“Because of where the truck travels, we go over the diagnostics and take it all into account when we’re planning for parts replacement on Clinton’s truck.
“Despite it having some 23,000-plus engine hours, we have never had to open the motor for anything other than valve adjustments.
“While the truck has put in a remarkable workload, it is hats off to Clinton for not overstretching the vehicle’s capabilities and supporting it with the best parts for its maintenance and our highly qualified Isuzu-trained technicians.”
The long wheelbase FRR 600 (now Isuzu’s FRR 110-260) is rated to an 11,000 kg GVM and 16,000 kg GCM. When fully loaded with furniture and other household items, this leaves enough capacity to tow a loaded threetonne trailer.
The FRR’s durable truck body has side and rear entry doors for easy cargo access. The truck and trailer floors have been fitted with carpet, ensuring that cargo is protected and less likely to shift around.
A scale model of this thoroughly road-tested and smartly outfitted Isuzu FRR sits proudly on the counter at Wagga Motors.
After almost a decade of calling in at the dealership, John says Clinton remains one of their most loyal and popular customers.
“I have to say Clinton is not simply a customer; he’s part of the Wagga Motors family,” John remarks of the long working relationship.
“He doesn’t simply drop the truck off; he speaks with the technicians and deeply appreciates the work our team does.”
The next 12 months beckon with many all-too-familiar issues within the transport industry, which the ATA are prioritising
2025 will be the first full year with Australian Trucking Association Chair Mark Parry in the head position. He was elected to the role in May last year after previous Chair David Smith announced he would step down at the end of his term.
Mark joined the ATA following more than a decade immersed in the transport industry, most prominently as Managing Director of Ron Finemore
Transport and Deputy Chair of Healthy Heads in Trucks and Sheds, after making the switch from the mining sector.
It has been a dive right into the deep end, in what has been a big year for the progression of reform and regulation within the trucking sector.
“If you take any role, my view is you’ve got to learn the organisation and people first,” Mark tells PowerTorque.
“Between May and now, I’ve really been looking to get to know those people. My role is to ensure the effective functioning of the board and the various councils within the ATA.
“Because the ATA has such an external focus on behalf of the industry, then there’s the various arms of politics that you’ve got to meet and deal with.
“In my previous roles I was certainly aware of the NHVR and similar
organisations and dealing with a lot of people, but now I’m coming in with a different role and mindset.
“You have to look at how you support the board, and in particular making sure that CEO Mat Munro and his team have got the resources that they need to deliver on behalf of our members.”
Mark says that he and the ATA have four main areas that will be of vital importance over the next 12 months – driver licencing and Heavy Vehicle National Law changes being top of the pile.
It proposed a split to the MC driver class in order to reflect the extra skills required to drive bigger combinations including triple road trains, quads and quins, which was presented to Parliament in 2024.
This comes in tandem with Austroads’ proposed changes to the truck driver licensing system, doing away with time-based systems and focusing more on training and assessment requirements.
While this will then come with further regulatory changes and the need to develop a greater training system, Mark says that this will be one of the ways that transport can attract new people to the industry.
“I do think that the federal government, opposition and various states are listening to this,” he says.
“I see a very clear connect between training, licensing and safety outcomes helping to attract people to the industry. Given some of the current training and licensing, we risk having drivers that don’t have enough experience or knowledge getting on the road being potentially unsafe.
“That can also lead to turnover, where people get a licence, start work and go ‘you know what? This isn’t for me’. What we’re advocating is that licensing should have much more skillbased training to ensure that people have capability and competence that is assessed under a known and specific set of criteria.”
bring to the industry. The National Transport Commission proposed several changes to penalties for offences under the HVNL, with many fines increasing.
As proposed changes to the Heavy Vehicle National Law continue to progress, the ATA must be prepared to respond to the impact that they will
The ATA had previously argued for fines related to fatigue and recordkeeping be reduced, aiming for an education over punishment model for truck drivers and operators.
Ministers had a meeting in September 2024 where they endorsed
12 changes to the HVNL, covering areas including unfit driving, mass and length increases, simplifying work diaries and a National Audit Standard.
The ATA will be continuing to hear from industry and discussing the proposed changes with lawmakers.
“I think all these things are a step in the right direction,” Mark says.
“When you’ve got any significant change that’s reliant on each state agreeing, it’s always going to be difficult.
“I’m a great believer in continuous improvement, and I think the regulatory framework, particularly associated with fines, still needs more work. We have to realise that we have to do it in a constructive way that provides evidence for people on why we should make the change.”
He believes that minor breaches such as missing filling out the date in a logbook shouldn’t be punished as harshly as it currently is.
“That to me is an area where you can’t say it’s deliberate. There’s no breach that’s impacted that person’s ability to drive safely, yet the extent of the fine doesn’t equal the misdemeanour.”
The proposed and endorsed changes to truck mass and length are necessary with an eye to the future, Mark believes.
As more alternatively powered trucks come into the picture, Australia’s heavy vehicle law is going to have to continue to change to reflect what needs to be on the road.
It will be necessary to help get the most productive and safe vehicles in our industry.
“When we look at a cleaner energy future, there’s going to be a space in transport for electric, a space for fuel cells,” Mark says.
“If you talk to any of the major European manufacturers, they talk to a timeframe about 15-20 years away for internal combustion technology. Changes to dimensions are important as they can enhance productivity.
“To improve fuel efficiency or reduce emissions, they’re going to require mass and dimensional limits that allow Australian industry to bring in equipment from overseas. We don’t have an industry here building those prime movers or the scale to do that.
“We also know the freight task is going to increase. We know that retaining and recruiting drivers is going to be an issue. The more productive you can make the equipment, the lower the emissions per ton, per pallet or per unit of items moved per kilometre.”
With the move to these new vehicles however comes greater costs, which Mark and the association
“WE WANT TO ENSURE THAT THE INDUSTRY KNOWS WHERE TO GO WHEN THEY HAVE A MENTAL HEALTH PROBLEM”
are conscious of in terms of the effects it can have on the operation of trucking businesses.
“If we are producing hydrogen, we need charge. If we’re producing renewable diesel, we need electricity. People ultimately need cost effective power.
“This will determine whether future technologies, which help decarbonise the industry, are cost effective. If they’re not, that price ultimately has to be passed onto the consumer.
“I’m not anti-renewables, but I do believe that to assist the industry and the consumer have a cleaner energy future, we need reliable power with a sustainable base load at a sustainable price.”
Safety within the industry, both physical and mental, is another big area that Mark and the ATA are continuing to focus on across 2025.
As new safety features are mandated, and the need to become Euro 6 compliant fast approaches, Australia’s aging fleets will need to be refreshed and updated.
While newly produced trucks include all the most updated safety features, many fleets are still falling behind in this area.
“The industry needs to continue to look at ways to ensure that people can invest in the safest, most modern, fuel efficient and emission efficient vehicles,” Mark says.
“The newer and more up to date the fleet is, the more safety features are there. It not only helps protect the driver, but it also helps protect other road users.
“You have most of these systems sitting in most modern European prime movers today. Increasingly
we’ll see more supplementary technology, like fatigue monitoring devices, driver facing cameras and cameras around trailers.”
Fatigue in particular is something that Mark believes the industry can manage better, with current regulation and the use of logbooks.
“I don’t think logbooks manage or control fatigue, only work and rest time,” he says.
“As technology evolves, as companies have the ability to monitor driver hours in real time through EWDs and fatigue management technology, we should be working at driver risk rules that can allow drivers to drive when they’re rested and rest when they’re tired.”
As the Deputy Chair of Healthy Heads in Trucks and Sheds, Mark also places significant value in the importance of mental health in the transport workforce.
Since its launch in 2020, the organisation has worked to provide the transport and logistics industries with resources and programs to understand mental health struggles, and provide safe and healthy working environments.
“We want to ensure that the industry knows where to go when they have a mental health problem,” Mark says.
“We believe we can do more in terms of free training, more road show vehicles to help drivers on the road, and help people deal with their mental health challenges.
“Before I joined I would hear that two or three people in every five have mental health challenges. I would think that’s impossible, but now I look at it differently.
“When you’re a driver in a truck and it can be impacting your mental alertness, on the road by yourself, these things can magnify on you.
”So I think the more support we can get out for people, the more knowledge, the more connections, and the more people in the industry who are trained to help have a conversation, then the better the industry will be.
“And ultimately, I think that will improve safety.”
As we enter the New Year, it’s timely to reflect on the progress we’ve made together and our ongoing goals for the heavy vehicle sector, writes outgoing NHVR CEO Sal Petroccitto
In 2024, we celebrated 10 years since the National Heavy Vehicle Regulator (NHVR) commenced our journey to become Australia’s national regulator. Through collaboration and a commitment to safety, we reached many significant milestones, and while it would be impossible to touch on them all, I’d like to mention some that will have a lasting impact on our customers.
In April, we completed our National Services Transition program by assuming responsibility for heavy vehicle regulatory services in Queensland. As the final participating jurisdiction to transition, this was a huge achievement and a step forward for industry, who now have a single reference for consistent application of the Heavy Vehicle National Law (HVNL).
The NHVR also welcomed many new Safety and Compliance Officers (SCOs) to our Operations team, who work roadside and at vehicle inspection sites. The transition has allowed us to accelerate regulatory compliance harmonisation across state borders and drive a safer freight network.
Improving safety on Australia’s roads remains a priority and last year we conducted 67 safety operations across our participating jurisdictions to help drivers understand their HVNL obligations. For example, in December the NHVR partnered with police as part of Operation Omega. This collaborative effort saw increased patrols on national, key freight routes and highrisk areas to target driver fatigue ahead of Christmas.
In July we launched the National Roadworthiness Survey (NRS) to
improve the mechanical condition of Australia’s heavy vehicle fleet. Our SCOs, police and other authorised officers conducted more than 9,000 visual and mechanical inspections to identify existing and emerging risk trends. The results of the NRS will be compared to previous surveys to determine where we are making improvements in vehicle safety, and where we can focus more attention.
The NHVR continued to improve our data and technology offerings in 2024, with a focus on enhancing the NHVR Portal. The Portal is the NHVR’s digital platform, transforming how we deliver our services to industry. We’re committed to providing all regulatory services through the Portal, and it’s constantly evolving to deliver a more seamless experience for customers. Throughout 2024, the National Network Map continued to evolve with refined data and features, creating a single authoritative location for industry to plan journeys across state and territory borders for their entire fleet.
promote safety, to apply.
Since our inception, the NHVR’s focus has always been on ensuring industry, and all road users, remain safe. Despite the challenges of a fast-growing and evolving freight task, our commitment to an inform, educate and enforce approach continues to improve safety, efficiency and productivity for all.
We were pleased to continue working with safety-focused industry groups through our Heavy Vehicle Safety Initiative (HVSI). With the support of the federal government, we invested $3.9 million in 16 safety projects through Round 9 of the program. The new initiatives will provide tangible improvements for the transport and logistics sector; supporting productivity and making roads safer.
In November, we opened submissions for Round 10 and I’d encourage any group or individual involved in Australia’s heavy vehicle industry or the wider supply chain, that has a project or campaign that will increase compliance and
As I announced last year, January marks my final month with the NHVR. After nearly 11 years in this fantastic organisation, I’m so proud of everything we’ve achieved together. I look forward to seeing the NHVR continue making an impact into the future and ensure safer heavy vehicle movements across Australia.
I wish you all a Merry Christmas and a Happy New Year.
Stay safe.
The new Volvo FM Low Entry may have a face only a mother could love, but as Will Shiers discovers, it’s purpose-built for a specific job, which it does remarkably well
Next Halloween, I’m planning to borrow an FM Low Entry for the night and park it on my drive. That should scare the trick-or-treaters! Maybe that’s a slight exaggeration, but you have to admit Volvo’s new low-entry truck is a bit… aesthetically challenged.
The truck’s unusual cab design is a direct result of the legislation it’s built to comply with. Truck designs are always shaped by regulations — whether in cab dimensions, vehicle length, axle weights, or other requirements — but perhaps none more so than the battery-powered FM Low Entry. This model was created to meet strict demands for enhanced direct visibility and zero tailpipe emissions. True to its name, it features a low-entry cab and is available exclusively as an electric vehicle.
While many of us struggle to see the benefits of electric trucks for long-haul applications, for urban operations in
city centres — where diesel engines are increasingly unwelcome — it makes far more sense.
The FM Low Entry comes with dual electric motors, matched to a 12-speed I-Shift transmission and powered by four 90kWh batteries, delivering a total power output equivalent to 440hp. This configuration gives it a practical range of approximately 200km, aligning well with typical urban and regional tasks.
For those opting for longer wheelbase models, there’s the option to add two more batteries — bringing the total to six and extending the range even further.
The example seen here is an 8x4 Tridem, equipped with a Thompsons Loadmaster tipper body and a Palfinger M125 crane. While I’m unsure of Volvo Trucks Australia’s plans, in the UK it is available in numerous other axle configurations, including 4x2, 6x2, 6x4, and 8x2, with gross vehicle weights ranging from 19 to 32 tonnes
and wheelbase options spanning from 3,900mm to 6,000mm. This adaptability positions the truck as a versatile option for a variety of applications, from parcel and food delivery to kerbside waste collection. At the time of writing, Volvo had already received around 10 orders in the UK across these sectors.
As the name suggests, the FM Low Entry uses a modified FM cab that’s been lowered and shifted forward. This is easier to achieve with an electric truck than with a diesel model, as Volvo’s machine-under-cab (MUC) system can be reconfigured into an ‘S’ shape — a flexibility combustion engines obviously lack.
The FM Low Entry has its own unique, and distinctive, front-end styling. This particular model is painted in a striking Fire Engine Yellow, which is undoubtably the truck’s boldest feature, ensuring
it won’t quietly sneak up on any unsuspecting pedestrians, or pigeons!
Note that it still carries the original FM badge just below the windscreen. I’ve heard rumours that somewhere in Sweden there’s a skip full of “FML” badges, initially meant for the cab’s exterior — until someone remembered that millennials have given that acronym an entirely different spin!
The FM Low Entry’s cab is designed for easy access, featuring a single, wide step. Like all of Volvo’s electric trucks, this model rides on air suspension, allowing it to lower for smooth entry and then rise when needed for uneven terrain — though its substantial front overhang obviously has limitations for off-road applications. Volvo has also introduced a new
option: a bus-style door on the passenger side, so drivers can step out onto the pavement without swinging a door into pedestrian traffic. This particular model has a standard passenger door, but with a low-set glass panel that gives it a top fivestar rating in London’s Direct Vision Standard safety scheme.
Complementing this is Volvo’s Camera Monitoring System (CMS), which replaces traditional mirrors with cameras and interior screens, making it ideal for navigating crowded city streets without the risk of a side mirror accidentally striking a pedestrian or cyclist.
This configuration is a short crew cab with three passenger seats, borrowed from a Volvo coach. These seats are positioned slightly back and higher than the driver’s seat, offering passengers an unimpeded view through the front windshield, rather than the ceiling, as in some competitor models with more intrusive cab
layouts. The FM Low Entry can also be ordered without a passenger seat — an option parcel delivery services might appreciate — or with a conventional single passenger seat.
For the driver, the cab is practically identical to that of a standard FM, with a familiar layout and controls. The primary change is a power gauge in place of a fuel gauge, echoing the FM Electric design. There’s also a slight reduction in lower dashboard storage space, an adjustment made to accommodate the cab’s lower mounting position.
You start the electric motor with a conventional key, rather than a stopstart button, which feels a bit oldfashioned for a truck like this. A soft hum fills the cabin as the dashboard lights up, and I’m off toward central London — exactly the kind of urban setting this vehicle is designed for.
One of the standout features is of course visibility. The low-entry cab places you at eye level with cyclists and pedestrians, making it ideal for navigating busy city streets. The rear-
SPECS:
Model: Volvo FM Low Entry
Cab: Globetrotter short crew cab
Configuration: 8x4 Tridem
Wheelbase: 3,900mm
Engine: twin electric motors
Transmission: 12-speed I-Shift
Batteries: 4 x 90kWh
Performance: 330kWh (440hp)
Range: 200km
it takes a while to adjust to the front overhang. The drive feels akin to that of a luxury coach, but even quieter. The braking system includes three modes for managing energy use and control: “A” (automatic) works with cruise control, “O” allows coasting for downhill sections, and “1” enables regenerative braking for energy recovery. Striking the right balance between coasting and regenerative braking helps optimise efficiency, especially in stop-start traffic.
Acceleration is steady rather than
Similar to old models, yet different.
the journey’s end, I hardly noticed the CMS — it’s that seamlessly integrated.
A speed detection system reads speed limit signs and sounds an alert if you exceed them, though I do encounter a few alerts in error.
All in all, the FM Low Entry proves to be more than just a product of regulatory requirements. It’s smooth, agile, and provides a highly enjoyable driving experience, combining safety with exceptional comfort. Best of all?
From the driver’s seat, the “unique” exterior design is out of sight!
Upgrade your braking system with our retrofit solutions
Unlock peak performance of your trucks & trailers with Knorr-Bremse‘s advanced retrofit solutions, designed to enhance safety and performance.
Our retrofit solutions, including the Trailer Electronic Braking System (TEBS) and Trailer Roadtrain Module (TRM), enable electronic braking, ensuring your vehicles meet modern standards with precise braking control and improved efficiency.
Visit our website or contact your local Knorr-Bremse representative, a member of our Expert Network, or your local parts distributor for more information.
| truck.knorr-bremse.com/en/au/ |
Managing and integrating your telematics solutions, in conjunction with advancements like AI, could be the key to taking the next step with your safety solutions
Telematics, like many other areas in the transport and logistics industry, is grappling with the emergence of AI and how it can best utilise it.
It is a segment that stands to benefit highly from its implementation, dealing primarily with data and the insights it can draw from those figures. AI can help to package that data uniformly and deliver it in an easy-to-understand way for transport operators and fleet managers, saving time and valuable resources on what can otherwise be a tedious part of the job.
How that AI is used alongside more specific solutions like video telematics is something which is still being explored and developed by experts in the area.
AVP of Heavy Transport for Geotab ANZ Andrew Hintz oversees the telematics solution provider’s operations within the heavy transport sector, and has seen first-hand how these issues have arisen.
He arrives at Geotab from a background in the oil and gas industry, spending nearly six years in the UAE before returning to Australia at Teletrac
Navman in his previous role.
Comparing where the transport sector is currently in regards to safety using technology, Andrew says that other industries which employ telematics are more advanced.
“I’ve seen that from a telematics aspect in the oil and gas sector, it’s leading from a safety aspect,” he explains.
“When I say leading, that’s sometimes up to five to six years ahead of other sectors, especially mining. Then typically there’s a flow on down to things like a transport sector and
other areas lagging behind.
“They’re well advanced in using technology to help them and their business. Getting that data off the vehicles, understanding what that means, how they’ve been driven and ultimately taking that data and using it to help coach their drivers.
“There’s data showing at risk behaviours and so forth.”
As the technology continues to advance, customers continue to expect more from what they can do with their telematics.
Video telematics have gone beyond simple solutions like dash cams or rear facing cameras – we are now seeing the technology used for monitoring fatigue, drivers and keeping records of on road incidents when they happen.
This can be vital for fleet operators to not only track their drivers, but also how they drive under various conditions in order to improve their operations and efficiency.
Andrew says he has noticed these trends in video technology to help align with truck safety systems over the past six months.
“If you think of video telematics type of technology, we’re seeing customers now which are hungry for better information,” he says.
“They’re looking, for the next year, at video imagery to back data points which have a lot more meaning when you can see what triggered it by requesting imagery.
“You can get a full view of what’s going on onboard the vehicle through real time video capture, which certainly adds more value. It can help to respond to incidents faster and coach drivers better.
“They can help operators to achieve efficiencies within their fleet using technology that can provide safer following distances behind other vehicles.
“That flows through to a smoother operation of the vehicle which then flows onto to visible fuel savings.
“From customer sessions, we hear things like ‘I’m a transport operator and I want only forward facing camera imagery’. Using AI technology through systems like ADAS you’re looking at warnings if pedestrian walk out in front of you, following distances, lane
departures, things like that.
“Not everyone has drivers who are comfortable with a driver facing camera.”
Some driver facing cameras can now use AI to detect fatigue or distraction by monitoring driver’s eyes and head movements to judge if they focused on the road, and warn them if they aren’t.
Others can see if the driver is properly wearing their seatbelt. All these things can then be converted into data and alerted to transport operators to review their driver performance.
“Some organisations are seeing significant push back in those areas,” Andrew says.
“Other operators want camera systems that are four channel systems, it has to be forward facing, driver facing and I need side load facing or a camera mounted off each mirror facing down the side of the load on the side of the truck. Trailers then become a problem there too.
“There’s also a big question around using imagery to help solve incidents right to the point of insurance claims.”
The other important side of advancing telematics on the video side is through how you can integrate it with the other areas of your transport safety operations.
For Geotab, this is done through its MyGeotab platform, which can link to the telematics within the vehicle to give the clearest picture of all of the data available in one place.
“Integration is probably the keyword there,” Andrew says.
“Something which we’ve heard again and again when you combine that video imagery with the traditional telematics events in the MyGeotab platform, it gives that richer data set which can help to both improve the driver safety and ultimately offer a better customer experience.
“What we hear again and again is we want to work in one software platform and we want a single pane of glass view.
“If you can give us the telemetry data and if you can give us the video imagery, that’s going to help us better manage our fleet and make those informed decisions.”
As a progressive and innovative Australian owned company, Alemlube understands how important it is for workshops to save time, keep things organised and provide employees and visitors with a safe work environment with the aid of the right retractable hose system.
With this point front of mind, Alemlube has teamed up with a longstanding partner to design and bring to market a functional, aesthetically pleasing, new solution and is excited to now present the Rewinda Series of
hose, cable and barrier reels.
With proprietary mouldings and tooling, and a 10-year warranty on materials and workmanship supporting the products, you can confidently install and use Rewinda Series Reels in your workshop or manufacturing facility.
Let’s make your workspace work better for you and your team.
Retractable hose reels have become a must-have in today’s workshops and production facilities, and the new Rewinda range is here to make your life easier. The versatile lineup has
something for nearly every application featuring 20m compressed air reels, 15m hot wash reels, 15m high-pressure water reels, four different welding reels and 15m chemical, herbicide and pesticide reels plus two 30m barrier reels and two handy cable reels—all part of the same family of products.
Whether you’re working in a car dealership, a construction equipment yard, a plant hire facility or a mine site workshop, the Rewinda range of hose, cable and barrier reels are designed and engineered to meet and exceed your needs and expectations. They’re
also perfect for use in quarries, food and beverage facilities and recycling plants. With the Rewinda range, you’ll have the right reel for the job, making your work smoother, more efficient and safer.
In bustling workshops where space can often be at a premium, the Rewinda range is here to help. With a clever variety of mounting systems, you can easily fix the reels to walls or ceilings, freeing up valuable floor space. Keeping your workshop clean and uncluttered allows you to move around safely avoiding trip hazards and obstacles. Plus, if you are on the go and mobile, Rewinda reels can be vehicle mounted. With sturdy locking pins, you can be sure that the reel stays securely in place, making it perfect for all your mobile applications.
Using Rewinda reels is a breeze, thanks to their clever design. The heavy-duty steel swivel allows you to turn the reel up to 180 degrees, giving you great flexibility in how you work. Plus, with the new and innovative stop-at-any-point latching mechanism, you can easily secure the hose at exactly the right length every time. Improvements to the main spring return have been made so you can count on safe operation year on year, with critical spring assembly component at the centre of the reel.
The new speed rewind control system, as available on all models of the hose and cable reels, ensures that they retract smoothly and steadily, keeping everything safe, manageable and WH&S compliant. With these ergonomic design features, using the reels is quick and easy; it helps you maintain safe work best practices and boosts your workshop efficiency.
Enjoy a more streamlined workshop with Rewinda.
In the mix, Rewinda hose reels are equipped with Gen3 polymer hose assemblies that deliver ultimate flexibility while staying completely kink-free under pressure. This feature provides consistent compressed air flow and pressure without obstructions and with no interference to your optimal performance. By keeping hoses free of kinks, you will reduce downtime and minimise the need for repairs and replacements.
Hose longevity is further enhanced through proper hose storage.
Another key feature is Rewinda’s sliding guide system that ensures that the hose returns evenly on to the barrel assembly, eliminating the chance of hose bunching on one side of the reel and thereafter not being able to retract back on to the barrel assembly.
In the same family of reels are two danger and caution barrier reels, both storing and retrieving 30 metres of barrier creation fabric cloth.
The demarcation between your workshop zones is easily managed with Alemlube’s Rewinda Barrier reels. Temporary barriers identify dangerous areas to restrict access or limit foot traffic. These highly visible guides are essential in managing your workplace and employee safety.
At 30m in length, the Rewinda barrier reels are the optimum choice for large freight company receiving and despatch docks, mine and quarry sites, workshops, building sites and even residential apartments that require safety barriers over larger areas. The reels are fitted with a hook so the system can be coupled to your existing fit out or use the durable eyelets to securely fasten the reel to masonry or wood.
Third and finally, cable reels complement the Rewinda range.
Retracting smoothly, these reels prevent tangling or damage to your electrical cables and minimise the trip hazards associated with loose cabling in a workshop or manufacturing facility.
There are 15amp 240V and 10amp 240V cable reels available, with both capable of storing and retrieving 20 metres of cable.
Keep your workshop and fabrication facilities organised, and most importantly safe, for you and your employees.
With longevity in mind, Alemlube designed and engineered the Rewinda Series of hose, barrier and cable reels in a modular design to make servicing and maintenance of the reels a simple and straight forward proposition. Making maintenance a breeze, the reels can be easily inspected for quick upkeep, ensuring your workshop operates effectively and safely, thereby minimising downtime and maximising productivity.
As a focus on sustainability increases, Rewinda leads the way with eco-friendly reel covers made from recyclable polypropylene materials. By using a retractable hose system designed to minimise wear and tear, organisations can significantly cut down on unnecessary waste and the need for frequent replacements. With an unwavering commitment to quality, each Rewinda component is built for a long service life as confirmed by Alemlube’s 10-year warranty on materials and workmanship.
When quality, performance and durability are priorities, Alemlube’s Rewinda Series of hose, barrier and cable reels are the perfect choice for your hose and cable storage and retrieval needs.
Knorr-Bremse offered the chance to get a closer look at just how its suite of safety systems works recently at its first Drive Days event since 2019
How fast do you need to be travelling to cause a truck rollover when taking a turn just a little too tightly? 90km/h? 80?
As we found out, a rollover can occur at as low as 50km/h. That is almost fast enough to cause a rollover incident – at least it would, without modern rollover prevention technology and safety systems.
Electronic Stability Programs (ESP) became compulsory for many heavy vehicles from January 2022, and from February 2025 will be expanded to also cover goods vehicles above 3.5 tonnes (ADR 35/07). This is in addition
to Advanced Emergency Braking Systems (AEBS), which will also be mandatory in new heavy goods vehicles over 3.5 tonnes Gross Vehicle Mass (GVM) as of February 1, 2025 (ADR 97/00).
Companies like Knorr-Bremse have been anticipating this, giving trucking operators and industry professionals the chance to experience their safety technologies at their recent Drive Days event in Shepparton.
We had the chance to jump inside the trucks on display, most predominantly a Kenworth T410 towing a trailer with an outrigger setup to feel just how much these electronic systems
do to keep your wheels – all of them –on the road.
Knorr-Bremse engineer Desmond Chin took us through the whole demonstration, with four different steps to show off just how the systems, both on the truck and trailer, work automatically to prevent a rollover incident.
The tests were split up into four different scenarios, allowing the passenger to observe how the systems work both individually and together.
On the first ride around the track, all systems were completely turned off –we were at the mercy of the truck and the road itself.
Desmond accelerated to just over 50km/h, and started a turn which most certainly felt sharper than it actually no doubt was in reality. Even barely going faster than what you would down a suburban street, the outrigger wheels hit the ground, meaning that without those, the truck would have rolled over.
After this heart-pumping exercise, things were a little bit easier on the anxious passenger. The stability system was turned back on for the truck, but the trailer was left inactive in terms of ESP.
In the second test, going at the same speed but with the ESP switched on, the truck would automatically slow down to a safe speed when going through the turn –this is how the Knorr-Bremse system prevents the truck from rolling.
In the third test, the goal was to aim for as fast a speed as possible around a circle marked on the skidpad, with ESP still active. The maximum that the truck would reach was 38km/h, with ESP taking away engine torque to keep the combination at a safe speed, preventing a rollover.
If you think it looks scary, imagine being inside it!
Technical Sales and Business Development
Roll Stability Program (RSP) is also available on the trailer – that is where TEBS, or Trailer Electronic Braking System, comes in.
Both the truck and the trailer used in the demonstration house KnorrBremse safety systems, and even with just the TEBS active, the rollover prevention braking is incredibly smooth and almost unnoticeable from
We got a closer look at the TEBS system both at the Drive Day, from Technical Sales and Business Development Manager Darren Hillson, as well as from Desmond, Aftersales Manager Rachel Michaud, Technical Services Manager QLD/NSW Ewen Campbell and Lead Applications Engineer Alex Biviano at the Australian
Maintenance Conference.
One of the demonstrations showed the powerful benefits of electronic braking in reducing heavy vehicle stopping distance. This was done by showcasing the difference in brake timing between an electronically vs. pneumatically braked heavy vehicle road-train on custom made electronic timing boards. Leveraging electronic braking via Trailer Roadtrain Modules (TRMs) and TEBS, a 0.6 second advantage in brake timing compared to pneumatic braking could be observed. When travelling at 100km/s per hour, this is 16.8 metres difference before the last trailer in the combination is braking – more than half the length of your average B-double.
influence from crack pressures in pneumatic valves.
“The Trailer Roadtrain Module has the main job of splitting and reassigning addresses to go between the local TEBS and the rear coupling that connects to the trailer. It’s essential in a TEBS trailer that’s going to tow another trailer.
“It’s been tested and effective for up to seven trailers in combination, including dollies.”
North American trucks can also be fitted with the TRM, to communicate electronically with the TEBS.
the advanced emergency braking will activate before any sort of collision incident could happen. This system will also brake the trailer in these scenarios, increasing the effectiveness and stability of the system.
The driver demonstrated how the vehicle would act on a rapid approach, slowing down quickly after the speed of the car in front dropped.
“It means each trailer gets the same signal at the same time,” Alex says.
The systems have already advanced significantly from when the first electronic trailer braking systems were introduced to the industry.
“In 2019, Roll Stability Control was mandated on trailers, essentially mandating TEBS,” Alex explains.
“Not only does it give you Roll Stability Program (RSP), but it also gives you several auxiliary functions that are complicated to realise without it.”
These functions include steer axle lock, auxiliary power outputs, lift axle control and electronic suspension control.
“The biggest benefit relevant to the Australian market is the electronic brake signal” Alex says.
“You get significantly faster brake timing, both on the apply and release of the brake pedal, and the signal to each trailer is the same without any
In addition to the ESP and TEBS safety systems, the Drive Day also offered the chance for us to look at the Bendix Fusion.
The Fusion handles Advanced Emergency Braking, or AEB, through various methods. This was shown off on a Kenworth K220, which was taken around the track following a car out in front.
Included in this system is Adaptive Cruise Control, which is adaptive to the various scenarios that the truck was put through when tracking the car.
The first and most obvious part of this is the view on the dash, which displays the speed and distance of the vehicle in front. This tells the driver that the system has detected a vehicle, and gives the driver some extra information to help judge a safe gap.
If the driver doesn’t react on time,
It doesn’t just activate if the vehicle in front is stopped – the ACC will maintain speed for a safe distance if you hand the acceleration over to the system. With its camera technology, it will track vehicles it is following over hills and corners, not just directly in front.
The activation of the advanced emergency braking was incredibly smooth, even when quickly dropping from as fast as 60km/h to a stop.
Cameras and radar systems are continuing to play an increasingly larger part in truck and trailer safety. Another radar system showcased at the event was Knorr-Bremse’s iReverse which is a radar mounted to the back of a trailer.
Business Development Manager OE Trailer Chris Dudfield demonstrated how the system is able to recognise obstructions behind the trailer while reversing and how the system will apply the brakes before a possible collision.
Companies like Knorr-Bremse are offering the chance to get a look at and understand these kinds of safety technologies as new ADR mandates continue to roll out, with more coming across 2025.
Fasteners can undergo severe conditions and need to be treated with care to ensure they don’t get damaged
When servicing trucks and trailers it is becoming increasingly evident that fasteners are often subjected to two extremeseither over-torqued or not torqued at all. Either of these situations will result in the same outcome: fasteners not doing what they are designed to do. So, why does this happen, and how can it be addressed?
Some suspension fasteners that need be checked regularly are in awkward positions, making them difficult for technicians to access. Added to this is the high torque that many of these fasteners require. The process of looking up the correct torque specification, setting the torque wrench, crawling underneath the truck or trailer, and then reefing on the torque wrench to get a series of fasteners up to specification can be quite a task. Taking the option of leaving it alone if it looks tight can seem to be an appealing option. Especially so if the technician doesn’t see any immediate benefit for this extra effort.
On the other hand, using a rattle gun to check torque is very convenient but inherently flawed. There is no way of telling if the fasteners have been overtightened. Some technicians have been known to run a torque wrench over the bolts after using a rattle gun, to check if they are tight enough. Unfortunately, unless the bolts move when using the torque wrench, there is no way of knowing how much torque has been applied and they may have been tightened past the bolt’s yield point. Unfortunately, neither of these two options provide any assurance that the fasteners will still be in place by the next service inspection. Components like axle U-bolts, pivot bolts and shock bolts will give a little over time because they are exposed to regular shock stresses. Not checking
these components for correct torque at regular intervals will result in components working their way loose. It will simply be a matter of time before this becomes evident and causes damage, such as elongated suspension hanger pivot holes or broken shock bolts.
Either case will result in failure and consequent damage to related components. Depending on which part fails, it could also result in a truck or trailer being out of service and off the road until repairs are carried out. Hendrickson and most other suspension manufacturers provide a schedule outlining which fasteners should be checked for proper tension and how frequently this should be done. While checking the torque of these critical fasteners takes time and effort, it ultimately saves on vehicle downtime and costly repairs by preventing fastener failures down the line.
There are still sweeping changes needed to make day-to-day life in the transport industry safer and better for drivers, writes Bob Woodward
Red tape is certainly not reducing, and based on recent dealings with State and Federal departments I would suggest that it is fast getting worse.
I clearly recall sitting in a Vehicle Standards meeting where a response to a question on amendment delays, it was stated, “it is policy”. On request a copy of the policy was never provided. Policy is often a rhetoric for too hard, or not interested, not doing that and a few other options for procrastination. Process before progress!
In many aspects of road transport process seems to dominate progress; the can-do approach has been lost.
I recall questioning a mechanic as to what torque he applied when checking to the suspension ‘U-bolts’ of a semi-trailer. He quoted a figure and I queried him, ‘so how did you do that?’ – with the workshop torque wrench! Very interesting, that trailer doesn’t have any ‘U-bolts’, the axles and trailing arms are integrated but paper won’t refuse ink!
The science behind designs and developing bolted connections is complex. In the trucking world bolt
torque for specific components is well known. Engine, transmission and differential re-manufacturers are generally religious in using the specified bolt torque on re-assembly, but why doesn’t this same discipline apply to couplings, wheel nuts etc.?
In 2008 the ATA Industry Technical Council released the first edition of the ‘Wheel end security - wheel to hub’ Technical Advisory Procedure (TAP). Whilst this TAP and subsequent editions is somewhat generalised, in summary it seems that there are fewer wheel-offs today than in the period prior to the development of the TAP.
There has recently been some chat regarding mounting bolts on coupling and other critical components coming loose and/or failing. At installation it is paramount that the manufacturers specifications are followed.
Typical bolt torque tolerance on critical connectors may be as much as +/- 10 per cent but it may also be as little as +/- four per cent. Preparations are critical - a lightly oiled thread will provide a substantially different outcome to a dry thread.
If in doubt, ask - determine the
manufacturer/supplier specifications. Follow the engineering process for a safety outcome. Manufacturers of tow eyes provide tolerances for in-service wear, but some also provide tolerances for in-service deformation (bending).
If it’s within the manufacturer’s tolerance and there is no evidence of cracks it is okay. If in doubt – replace. Whilst on the subject of couplings and tow eyes, industry experienced a phase of defects and failures of drawbars particularly on dog trailers.
Just like tyres and other components, drawbars are maintenance items and wear and mishaps needs to be addressed. In early 2021 the ATA Industry Technical Council released the first edition of the Drawbar Trailers TAP. This provides guidelines coupling selection and installation, inspection and maintenance specifics, including recommendations on drawbar deformation.
Failure in engineering applications is often the result of fatigue and the sharing of such information provides opportunities for design revisions. Detailed post failure analysis provides
the key causal factors and by learning from this history hopefully the same mistake/s are not repeated.
Driver fatigue is more complex. There is considerable reference to road fatalities, and the disproportionate number of fatal accidents in regional areas as compared to urban areas. In accident analysis there seems to be an unending appetite for the big three (fatigue, drugs/alcohol, speed).
Drugs and/or alcohol and speed are choices, be it a poor choice. There is much reference to fatigue and the promoted remedy for fatigue being rest/sleep, no arguments here. But specifically in the driving environment, what conditions cause fatigue?
There seems to be little acknowledgement as to the influence of the actual road surface as a contributory factor to driver fatigue. In discussing the impact of road surface condition with many professional drivers, a common agreement is that rough undulating road conditions are more demanding of the driver than the typical smooth freeway pavements.
I agree with the professional driver’s philosophy. It’s definitely less demanding to be motoring on good smooth pavement than narrow single lane rough roads with broken shoulders. In determining the cause of accidents, how many investigations explore the conditions of the pavement in the 200-500 metres prior to the
won’t like this because it puts the responsibility on those who are always ready to blame another party.
I don’t know the number of committees that have looked into rest areas in the past 40 years, but the count is at least four in the past 20 years. Process and process but no progress! Then there is access, not only to the road network but to rest facilities. I recently spoke with a driver, a long-term associate, regarding rest areas and facilities.
“We just need well located rest areas, away from the immediate passing traffic with good clean facilities, clean running fresh water
designed dunnies of varying designs in different colours at the many needed locations.”
If its kept simple, there should be more that can be done with the limited dollars.
Whilst on rest areas — who is responsible for emptying the garbage bins located at a rest area? And what’s the legal difference between stopping bays and rest area parking bays?
What’s needed? Well located rest areas, with practical and clean facilities. Let’s address driver fatigue. The cause is known, so address it by reducing the committee process, and progress with the building of the
Pride in everything is everything at Scholz Bulk Haulage, a family business based in Wodonga, NSW, which is celebrating its 25th anniversary in 2024
SBH was established by brothers Wayne and Craig Scholz at Pleasant Hills, a small town in the Riverina district of NSW, in 1999. They actually purchased their first truck several years earlier, a 1979 Kenworth K125 and a 1984 McGrath flat-top trailer to cart hay. An Alcan tipper was also bought to haul lime, gypsum and grain to Melbourne.
Today, the company is owned and managed by Craig and wife Sharee and has since relocated to a base in Wodonga which is now home to 23 Kenworths and 52 trailers.
SBH specialises in bulk commodity work with A-double, B-double and truck-and-dog combinations hauling the likes of fertiliser, potatoes, grains for stock feed companies, and canola and monola seeds.
A 5000-tonne capacity bulk grain storage shed is located on the Scholz family farm at Pleasant Hills, allowing quick and efficient turnaround for farmers in the region. This grain is then sold to direct buyers in the Melbourne and Gippsland regions.
Craig and Sharee’s passion for trucking is obvious in the premium equipment they operate – variants of the Kenworth-Cummins recipe – and the exceptional condition of their fleet.
A T908 adorned with distinctive graphics looks in showroom condition despite the fact it is 15 years old with more than three million kilometres on the clock.
The new flagship in the fleet is a Legend SAR, equipped – like all recently purchased SBH Kenworths are – with Icepak sleeper cab air conditioning, fridge, microwave oven, diesel heater and TV.
“We’re passionate about what we do here,” says Craig.
“Culture is a big thing in our business. Everyone on our team is valued not only for what they do but for who they are.
“As the saying goes, we treat people the way we want to be treated.
“The boys look after the gear really well,” he adds with a definite tone of pride.
“We’ll park a truck until we get the right driver and we do everything in our power to minimise risk.”
While the subject of decarbonisation is lined with questions, Craig says he is looking to the future positively as Cummins makes clear its plans for further advancements in internal combustion technology to meet increasingly stringent emissions standards.
The next-gen 15-litre Cummins, the X15D, also has Craig’s attention with its projected peak outputs of 660 hp and 2360 lb ft.
“Our standard X15 rating is 600 hp and 2050 lb ft torque but we’d like more horsepower in some of our applications,” he says.
Cummins’ support is a key reason for the rock-solid relationship between the two companies.
“We bought our first Cummins, an N14-400, in the early 2000s to repower
our 1979 Kenworth,” Craig recalls. “We decided to stick with Cummins because we thought the company would be around for a long time which looks certain to be the case.
“We’re also close to the Cummins branch in Wodonga and the service they provide is unmatched. Kaine Norman and his crew in the workshop do an incredible job.”
With the SBH business continuing to expand, Craig and Sharee thought it would be worthwhile to get a business coach involved to ensure their strategic planning is on the right pathway.
“As we are picking up more work with corporate clients, we want to make sure we are delivering the highest levels of certainty and satisfaction,” says Craig.
“We’ve built our business on communicating with our customers honestly and providing good old fashion quality service and loyalty.”
There’s obviously a lot of pride in what has been achieved at SBH, a business built on sensible goals and driven by a team of loyal employees who are acknowledged as being the key to success of this quietly achieving company.
UP TO 20% * IN FUEL AND EMISSIONS REDUCTIONS WITH AUSTRALIA’S ONLY SELF-CHARGING HYBRID ELECTRIC TRUCK.
The Hino 300 Series Hybrid Electric utilises an electric motor and a diesel engine working in parallel, intelligently switching between the two or a combination of both - to boost efficiency. Maximum torque generated at very low rpm minimises fuel use resulting in a reduction in carbon emissions. And as the Toyota Group hydride nickel battery automatically recharges whilst on road during operations, there are no recharging requirements. That’s the power of change, that’s the Hino Hybrid Electric. Visit hino.com.au