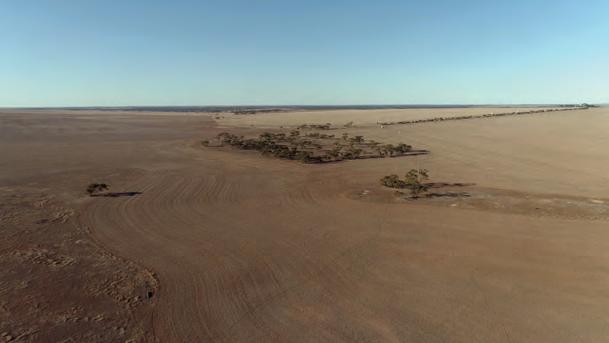
13 minute read
COMMODITY SPOTLIGHT
THE ALLURE OF HALLOYSITE-KAOLIN
OFT-MISUNDERSTOOD, HALLOYSITE-KAOLIN HAS THE POTENTIAL TO BE A LUCRATIVE COMMODITY IF A COMPANY FINDS THE RIGHT BALANCE AND UNDERSTANDS THE COMPLEXITY OF ITS MARKETPLACE.
Halloysite-kaolin is an intriguing commodity. Considered the most researched clay mineral in the world, its potential is largely untapped in Australia.
However, there are a handful of emerging Australian companies staking their claim as future producers of the versatile industrial product.
Andromeda Metals is the most advanced of those, a company racing towards establishing its Great White kaolin joint venture project on the Eyre Peninsula in South Australia.
Working alongside Minotaur Exploration, Andromeda has overcome a number of obstacles to be where it is today and still has objectives to tick off before it can become a producer, however the early signs all point in the right direction.
Much of that can be put down to the expertise of Andromeda general manager James Marsh, whose family has been keenly involved in kaolin over the years.
After working in Cornwall, United Kingdom, where kaolin was first mined in the 1700s, Marsh moved Down Under in 2002 and steadily began lifting the profile of halloysitekaolin, a high-value derivative of kaolin which had seldom been explored in Australia up until that point.
This led him to join Andromeda in 2018, which has grown from a $3-4 million company when he started, to one with a market capitalisation of more than $400 million.
While kaolin has long been used in the filling and coating of paper, its quality for this purpose is lessened when it’s discovered alongside the presence of halloysite.
Halloysite disrupts kaolin’s paper aspirations and can be difficult to identify due to its miniscule size.
However, it’s considered a profitable resource when used in other applications.
Andromeda sees a potential to commercialise halloysite in industries such as construction, agriculture, healthcare, cosmetics and nanotechnology.
The company’s offtake partnerships indicate Andromeda has also proven halloysite’s capability in ceramics.
Andromeda has executed an agreement with Japanese porcelain manufacturer Plantan Yamada for its Great White CRM product, which will see the company purchase 5000 tonnes per annum of halloysite-kaolin at $700 per tonne.
Marsh says his relationships in the field gave Andromeda an advantage in inking this deal.
“We chose ceramics first because we knew it had the halloysite which is where it’s highly valued and luckily with my background – I’ve been selling this stuff for 30-odd years – I’ve got a mass list of customers that I’ve been involved with over the years,” he says.
“So that gave us a huge head start, plus I knew exactly why these buyers would value it and how much it was worth for them because they would never tell you that themselves.”
Marsh says much of halloysitekaolin’s complexity comes down to selling the product. It’s a bit of a catch-22 – the commodity’s many unique uses and applications render it an intricate product to market.
“It’s a very hard material to market because there’s no index pricing for this stuff. In China alone, there’s over 10,000 users of this material and they’ve all got their own different formulations, their own processes, their own people who work different ways,” Marsh says.
“You also don’t talk to the buyers, you talk to the technical people and say, ‘here’s our product, this is its chemistry, this is its particle size, this is how it’s going to perform, this is how to use it in your application’ and convince them how they can use it.”
Andromeda has also established an offtake partnership with Jiangsu Mineral Sources International Trading Co for its Great White PRM product.
This will see the Chinese commodity trading house purchase 70,000 tonnes per annum of Andromeda’s kaolin product for more than $700 per tonne to be used in the coatings and polymers market. This is distinct from the halloysite-kaolin product to be sold to Plantan Yamada.
With Great White’s potential,
HALLOYSITE-KAOLIN IS A DIFFICULT PRODUCT TO COMMERCIALISE.
HALLOYSITE-KAOLIN IS A HIGHVALUE DERIVATIVE OF KAOLIN.
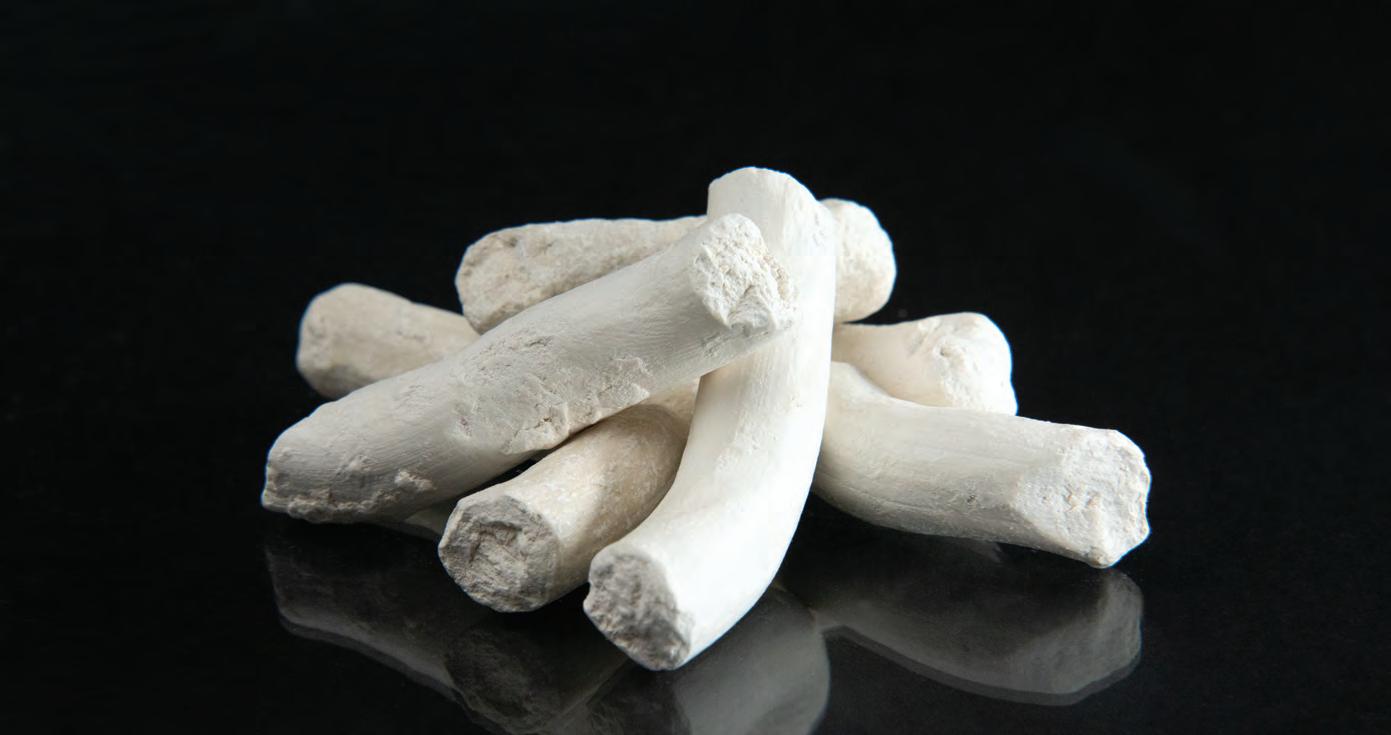
which Andromeda says is at 40 per cent halloysite purity and growing, the recent approval of the project’s mining lease, the established offtake partnerships and other commercial ventures in the works, Andromeda is well placed to elevate Great White into production.
Andromeda aims to break ground at Great White in 2022 after it has its Program for Environment Protection and Rehabilitation (PEPR) approved.
The total life of mine from the known resource is expected to be 26 years with a production rate of 500,000 tonnes per annum of raw material.
Other explorers in the Australian halloysite-kaolin space include Latin Resources, Oar Resources and Suvo Strategic Minerals, all in lesseradvanced phases of development than Andromeda.
There’s also iTech Minerals, a company focussed on developing battery and critical minerals such as graphite and rare earths. iTech has its Franklyn and Eyre Peninsula halloysite-kaolin projects in South Australia, the former of which is more developed given the company inherited exploration assets from Archer Materials in 2021.
“Both of them (Franklyn and Eyre Peninsula) are relatively early stage. We do have a head start at the Franklyn project … in that we’ve inherited about 10 years of historical exploration from Archer,” iTech managing director Michael Schwarz says.
Archer defined an exploration target of between 45 and 91 million tonnes of halloysite-kaolin at Franklyn prior to iTech taking over and Schwarz says the predecessor found some of its Franklyn drill holes to be particularly halloysite-rich.
After iTech completes preliminary testing to identify further halloysitekaolin prospects at Franklyn, the company will look to resume drilling at the project in 2022. iTech then plans to move its drill rig over to the Eyre Peninsula project where it has various exploration priorities including its Ethiopia prospect. Schwarz says the Eyre Peninsula project is well placed due to its location.
“(The Eyre Peninsula project) is probably only about 50 kilometres away from a port at Lucky Bay and 70 kilometres away from Whyalla,” he says.
“That’s important because these are industrial bulk commodities in the first instance before you do any value add, so transport to port is one of the big factors you have to consider.”
Port access is just one of the many variables influencing the capability of a halloysite-kaolin project.
First and foremost, understanding the market and establishing the quality of the product is critical in making a run at this intricate commodity.
Once a company has certified that, it has every chance of capitalising on the expansive buyer base halloysitekaolin can offer. AM
ANDROMEDA EXPECTS TO COMMENCE OPERATIONS AT GREAT WHITE IN 2022.
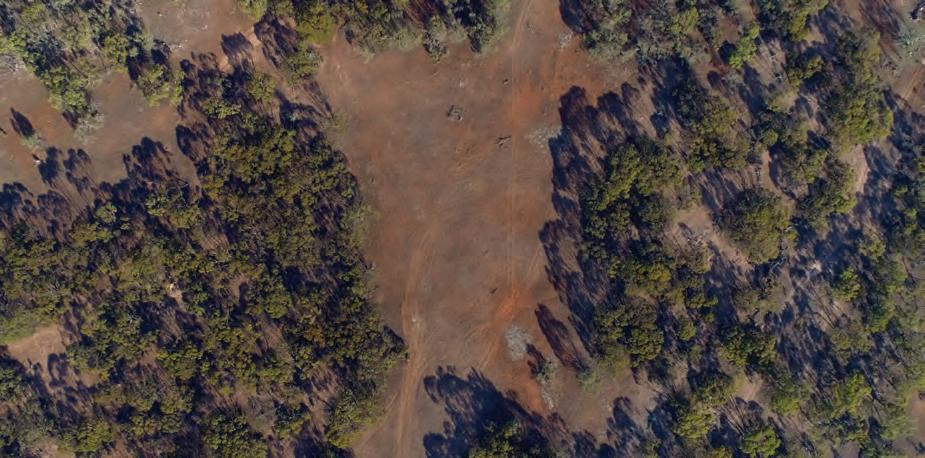
TRUSTED RELIABILITY. CONTINUED SUPPORT.
We bring the world’s best material handling equipment to you.
1800 182 888 | www.lincom.com.au | sales@lincom.com.au |
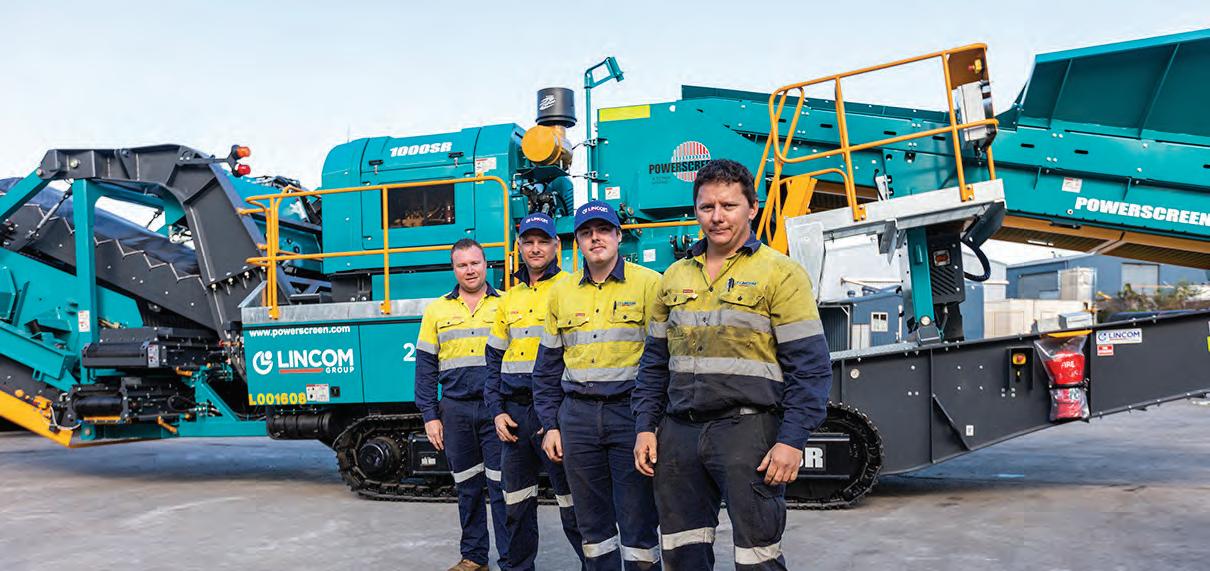
POWERSCREEN WARRIOR 2400
• Heavy duty, apron or incline belt feeder with hydraulic folding hopper sides • Jack up screen facility to aid mesh changes • Hydraulic folding conveyors with excellent stockpiling capacity • Hydraulic load sensing on under screen conveyor circuit and fines circuit • Heavy duty triple shaft screenbox with adjustable frequency, timing, and amplitude
SALES | HIRE | SERVICE | PARTS
AUSTRALIA’S IRON ORE MINERS HAVE AN OPPORTUNITY TO EMBRACE GREEN STEEL.
IRON ORE’S UNCOMFORTABLE TRUTH
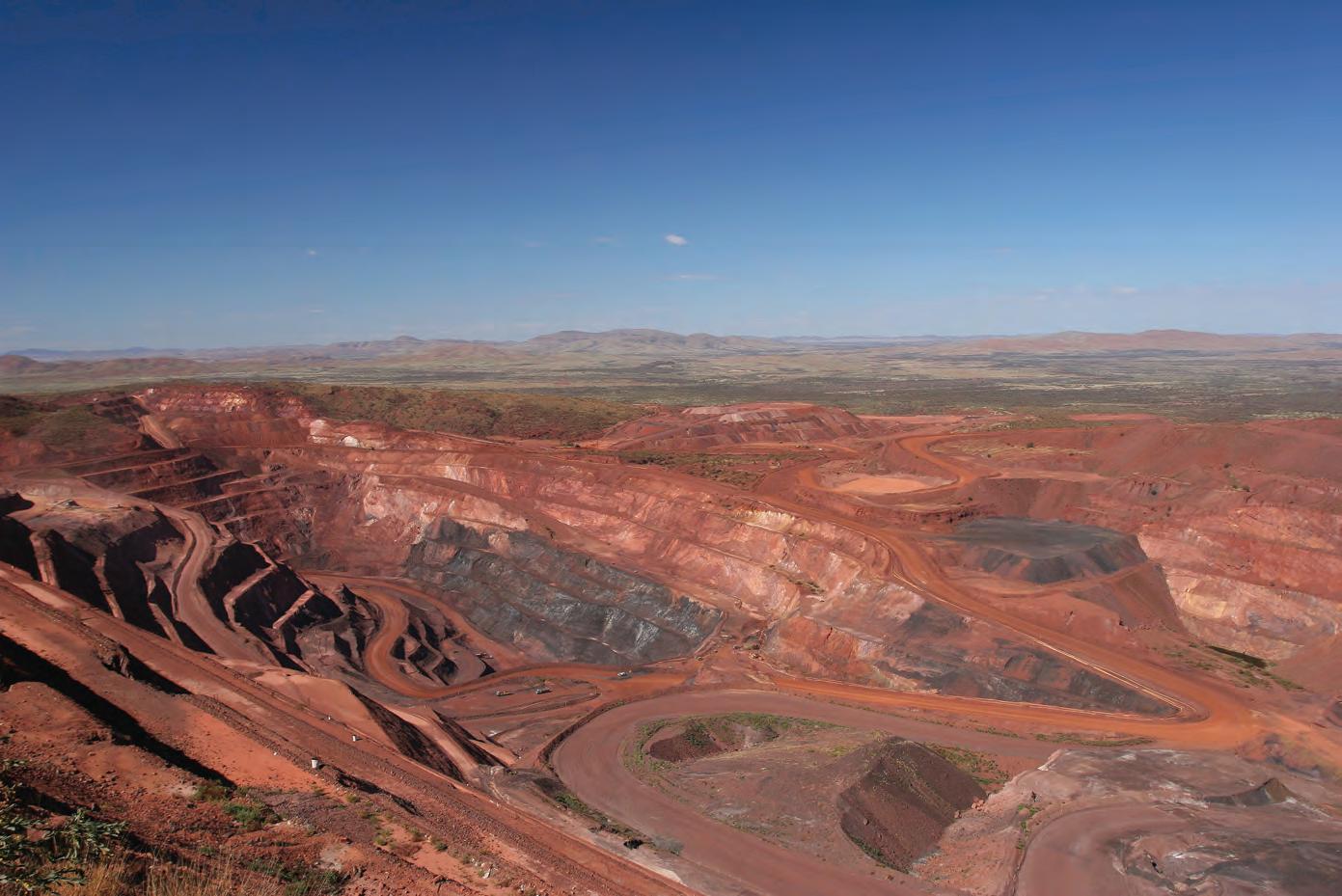
AUSTRALIA’S CARBON-INTENSIVE IRON ORE INDUSTRY WILL FACE AWKWARD QUESTIONS AS THE WORLD’S NET-ZERO PURSUIT STRENGTHENS, AND THE NEED TO EVOLVE HAS NEVER BEEN MORE PERTINENT.
Hampered by decreased prices and inconsistent demand, Australia’s iron ore industry has experienced a difficult end to 2021.
Numerous iron ore mining companies were forced to halt operations as a result of the crunch, including Venture Minerals’ Riley mine in Tasmania, Mount Gibson Iron’s Shine project in Western Australia (WA), while Indus Mining had to put its WA Ridges project into care and maintenance.
This came as China, Australia’s biggest iron ore customer, began reaching its steelmaking thresholds earlier than expected, while its growth-minded economy slowed in the wake of a boom early in 2021.
The environment had a big part to play as well, with the need to reduce air pollution a priority ahead of the Winter Olympics in February.
Despite the momentary drop in demand, given iron ore’s role in the world’s industrial movement, there’s going to be a continued need for this resource. According to Fitch Solutions, worldwide iron ore mine output is set to average 2.4 per cent growth from 2021 to 2025, with Australia’s iron ore production set to increase at an annual average of 1.7 per cent over the same timeframe.
Production may increase, but steelmakers will become more discerning as net-zero targets loom large, and low-grade or less sustainable iron ore producers risk being left out in the cold if they don’t make alterations.
This is where the concept of ‘green steel’ comes into the picture: a phenomenon that replaces fossil fuels with renewable energy in the steelmaking supply chain.
The green steel process also necessitates the use of high-grade iron ore, something which miners can achieve through practices such as beneficiation.
Global mining technology developer Metso Outotec is playing, and will continue to play, a critical role in the green steel movement.
The company’s involvement in sustainable steelmaking dates back to the 1980s when its predecessor Lurgi Metallurgie developed the Circored process.
Circored uses hydrogen instead of fossil fuels in the reduction of iron ore fines to make direct-reduced iron (DRI) or hot briquetted iron (HBI). This can then be used as feed material in electric arc furnaces for carbon-free steelmaking.
Circored had only been semicommercialised to this point, but Metso Outotec launched the next generation of the Circored process in December.
Metso Outotec Asia Pacific president Stuart Sneyd believes this method has an important role to play moving forward.
“Circored is already ready and configured for hydrogen reduction, whether it be grey, blue or green hydrogen – it’s ready to go in that sense,” Sneyd, speaking at the 2021 AusIMM Iron Ore Conference, says.
“It can produce a zero-carbon product in the end and we argue that the technical feasibility (of Circored) is proven at an industrial-scale (through a demo plant in Trinidad).”
The pilot plant commenced operations in 1999 and produced more than 300,000 tonnes of highquality HBI across several months.
Circored is the only 100 per cent hydrogen-based iron ore reduction process capable at such a scale and Metso Outotec aims to announce further additions to its capabilities during the first quarter of 2022.
The company is also at the forefront of sustainable pelletising.
Proven at producing high-quality pellets at low costs, Metso Outotec’s pellet plants are in use at iron ore operations across the world.
According to Sneyd, pellet plants will be an important fixture in an advancing green-steel world and Metso Outotec continues to explore opportunities in this regard.
“Pellet plants are likely to play a prominent role in the future and what can be done to support a carbonneutral future as far as this particular technology is concerned?” Sneyd says.
“Things that we consider are alternative burner fuels such as biofuel and hydrogen in pellet plant
powering, process modifications for energy efficiency and new hoods for electrification – all of these things are under development are being considered.”
Metso Outotec has added a digital solution to its iron ore pelletising process with the aim to improve production capacity and quality, while reducing energy and costs.
The company has iron ore pellet plants in Brazil, China and Africa but not Australia, according to public contracts.
Hydrogen is a hot topic in the mining industry as the green push strengthens, yet there are still unanswered questions that encircle the resource.
At this point in time, hydrogen is expensive to produce, difficult to transport and store, and highly flammable and dangerous.
Deeming the obstacles as opportunities not impossibilities, there are already initiatives in play which are aiming to further unlock the resource.
In November, the Western Australian Government awarded a contract to GHD Group to investigate the role the state’s iron ore can play in the global green steel movement, unpacking hydrogen capabilities as part of that.
In partnership with ACIL Allen, GHD Group will initially identify opportunities and current barriers for WA to support this revolution.
The next step will be to examine infrastructure needs, market dynamics and policies to solidify the state’s understanding of the green steel value chain.
Minerals Research Institute of Western Australia (MRIWA) chief executive officer Nicole Roocke says the state’s examinations would be centred around its Pilbara and Mid West regions.
“(By analysing future market dynamics) we’ll be looking at what the demand for low-grade and high- grade ores are going to be into the future, and look at the jurisdictional and mineral endowment differences,” Roocke, speaking at the AusIMM conference, explains.
“Also, to understand that if hydrogen is to be part of the solution, where does it have a role to play and what do production costs need to be to be able to make it economic.”
Roocke says the examinations will establish the clarity Western Australia needs to explore a green steel opportunity intelligently and efficiently.
“The whole intention of doing this work is to be able to ensure that both from a Western Australian Government and industry perspective, we have an understanding of what the opportunity is, and we have a better understanding of what the risk is to the state,” she says.
Having brushed off the toils of 2021’s closing months, Australia’s iron ore industry can expect more trying enquiries from sustainably-minded steelmakers in 2022.
Nevertheless, with the green steel movement in play, iron ore has the opportunity to evolve and prove the viability of a new direction – one that seems to be inevitable in a lowemissions future. AM
PELLETISING IS IMPORTANT TO THE GREEN STEEL VALUE CHAIN.
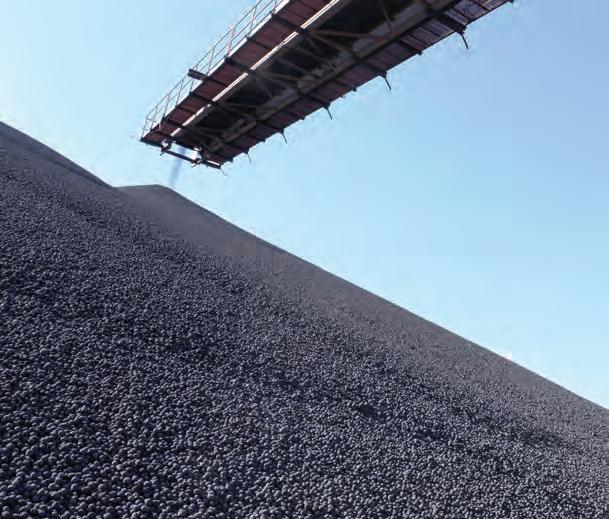
The KCA Carbon Converter
Recover Gold From Your Carbon Fines On Site
Kappes, Cassiday & Associates (KCA) now has three carbon converters successfully operating, at mines in Armenia, Argentina and Nevada. These units take carbon fines and dirty, wet waste carbon at gold leach plants, thoroughly ash it and remove all mercury. Recovery of gold and silver into bullion is typically 99%. For waste carbon loaded to 200 grams gold per tonne, operating cost is $6.00 per gram, or 11% of the value of the recovered gold. Often waste carbons are loaded much higher - the cost per gram drops accordingly. Mines with the Carbon Converter can recover their gold quickly without the Chain-of-Custody problems of shipping carbon to outside processors. Shipping mercury-contaminated wastes off-site incurs large risks of environmental contamination, and the Carbon Converter eliminates this risk. Having the Carbon Converter on site allows the operation to explore various process optimization techniques. For example, carbon fines below 30 mesh are usually lost to tailings in CIL plants, because such fines cannot be recovered cleanly. These losses can account for 1% of the gold fed to the plant. The Carbon Converter can process them. Another opportunity exists where process facilities periodically discard a portion of their coarse carbon in order to maintain optimum carbon activity. With the Carbon Converter, this carbon can be consumed on site and the contained gold recovered economically. The installed cost of the Carbon Converter is about US$1 million including site services, a building, and infrastructure. For mines which generate at least 50 tonnes/year of carbon wastes and fines, payback is typically less than one year. 775-972-7575 www.carbonconverter.com or www.kcareno.com
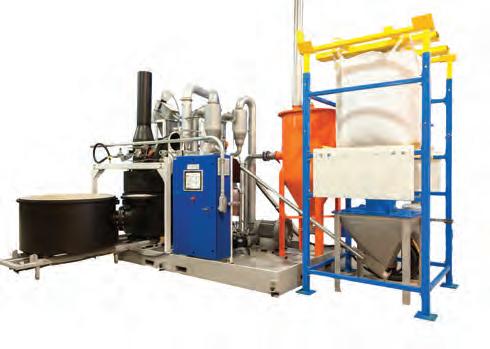