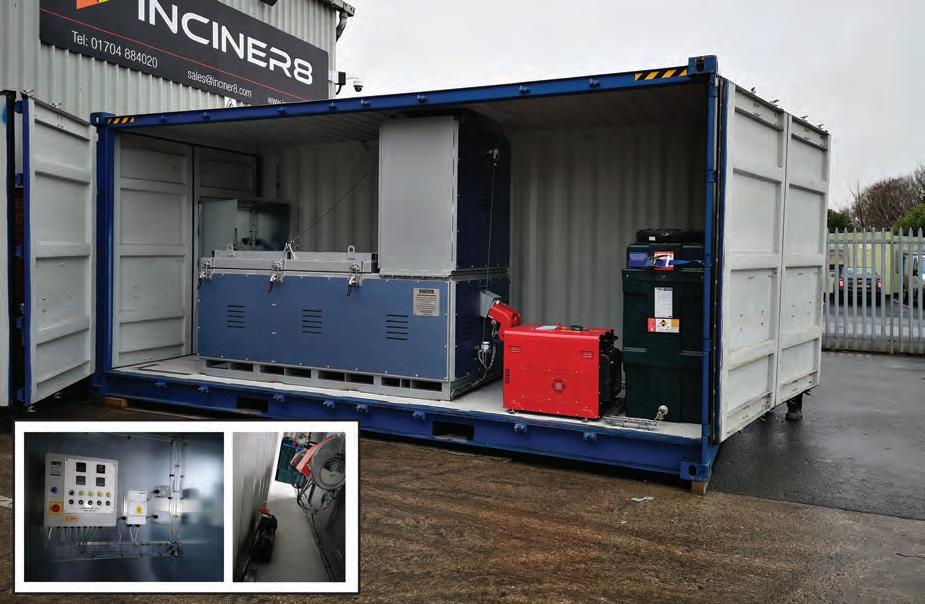
4 minute read
WASTE MANAGEMENT
DIGERO REDUCES MINING TO ASH WITH INCINER8
THIS NEW ZEALAND-BASED DISTRIBUTOR IS DIVING INTO THE WORLD OF AUSTRALIAN MINING WITH ITS FLAGSHIP LOWEMISSION INCINERATORS.
Digero has become a key distributor for Inciner8 products in the South Pacific region after experiencing success in waste management for a range of other industries.
The Inciner8 brand was developed in the United Kingdom to address the pollution caused by some current waste disposal practices like landfill.
The product’s main goal upon development in 2003 was ease of installation for remote operations, with minimal operator input and an affordable, environmentally friendly design.
As a growing family-owned business, Digero has been proud to take this on over the past three years and has achieved success in its distribution for Australia, New Zealand and Papua New Guinea.
Digero managing director Mark Courtney says the Inciner8 range is well-suited to Australia’s mining industry and he’s looking forward to growing the brand’s presence in the region.
“The mining industry has been of real interest to me because currently I believe they still bury a lot of their waste and that’s obviously not very good for the environment, so we’re looking to get our foot in there,” Courtney tells Australian Mining.
“As environmental regulation tightens around dumping rubbish in the ground, I believe mining companies are going to be looking for solutions and this is a great way to still dispose of rubbish on site in a responsible way.”
The Inciner8 range has a few environmental benefits compared to landfill, such as no water contamination, fewer greenhouse gases and a physical footprint only as wide as the incinerator itself.
Digero stocks several Inciner8 products to suit a number of applications throughout the mining industry, offering a range of burn rates from 100 to 1000 kilograms per hour.
Courtney envisions these incinerators to be ideal for mining villages where rubbish from potentially hundreds of miners is created every day.
“They can be especially helpful for mine villages because, if miners are living on site, not a heap may be getting recycled. So, anything they can’t recycle they can just incinerate with no worry about pollution either,” Courtney says.
Taking the i8-1000G as an example, the 21-tonne machine heats to 850 degrees Celsius and leaves an average ash residue of just 3 per cent the original weight of the rubbish.
Courtney says incineration can even add value for the operator, as ash residue can be used in other applications.
“After burning, the leftover ash has had all the harmful elements removed so it is essentially inert,” he says.
“Some larger operations have clients they can sell the ash to for use in road base and similar applications, providing a new life for otherwise disposable material.”
Once the material is burnt, the harmful gases are treated in a secondary chamber, using seven low nitrous oxide (NOx) burners.
These can either come as gas or oil-fired burners and take just two seconds to reduce the exhaust fumes to meet European air quality guidelines – some of the most stringent in the world.
“While a few gases are released by the end of this system, they are still well below the allowed amounts by law,” Courtney says.
“If customers require more assurance and pollution reduction, there are two types of filters we can offer as options.
“These are the ceramic and Venturi filtration systems.”
The 15-nozzle Venturi gas scrubber creates a high-pressure water mist to capture smaller particles for collection as a sludge in a container.
“The incinerator is already producing emission levels well below what’s allowed,” Courtney says.
“But it generally comes down to who is giving consent to a customer to operate, and if they’re asked to attach a filtration system for extra assurance, it’s available to them.”
“A lot of bigger operators do use them as they’re running the incinerators every day and they need as much help as possible to reduce waste and emissions.”
Courtney also explains how further costs can be saved using Inciner8 products in the form of energy and water.
“You can even recover and reuse the energy created by our machines if you want to go down that track, further reducing energy costs,” he says.
“This can be done by capturing the air and hot water created during incineration for use on site or around the village.”
A final optional extra is for remote monitoring and proactive analysis of the incineration unit and process.
A plug-and-play control panel comes as standard on several Inciner8 products for reliable use of the product.
This can be upgraded to connect with the Inciner8 headquarters for constant condition monitoring.
Inciner8’s team of engineers and technicians can advise of any faults or simply help to optimise the use of its incinerators, providing a clean service to an even cleaner product. AM
INCINER8 PRODUCTS COME IN ALL SHAPES AND SIZES.
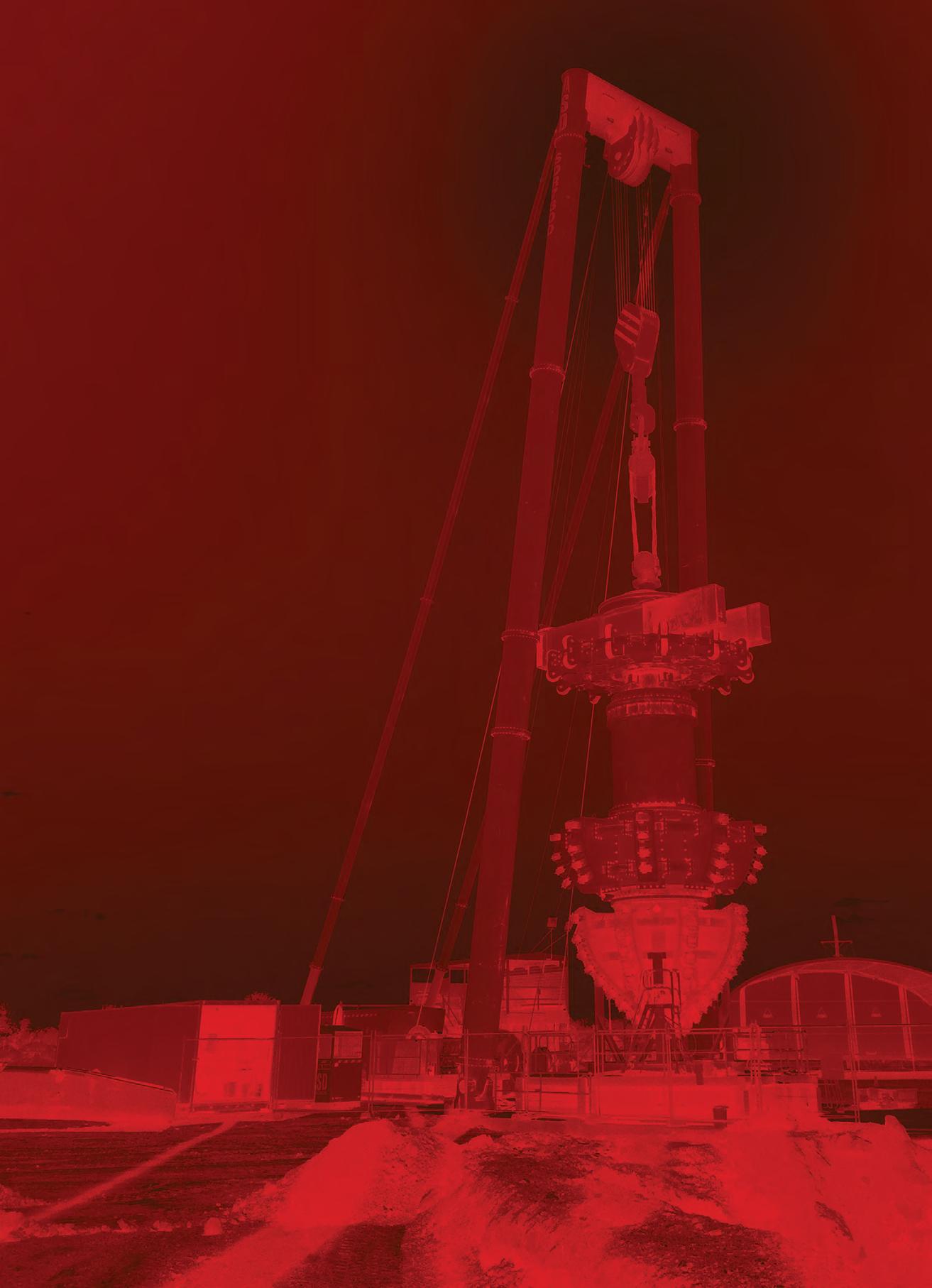