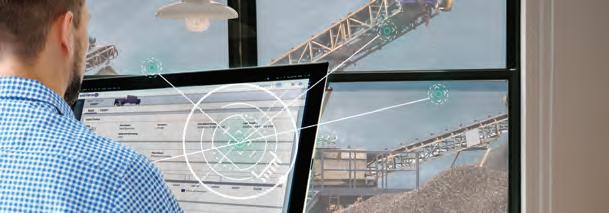
12 minute read
DIGITAL MINING
TAKING BELT CLEANER MAINTENANCE TO ANOTHER LEVEL
FLEXCO INDUSTRY MANAGER FRANKLIN MOORE HIGHLIGHTS THE FOUR KEY PAIN POINTS OF BELT CLEANER MAINTENANCE THAT CAN BE ALLEVIATED THROUGH THE COMPANY’S LATEST SOFTWARE OFFERING – FLEXCO ELEVATE.
Carryback is one of the main causes of conveyor issues at mining operations.
It can lead to faster belt wear and additional clean-up activities, with both translating to further downtime and a loss of production, which is critical in the resources sector.
Flexco industry manager Franklin Moore says carryback is often thought of as an unavoidable reality for belt conveyors at cement operations, but it doesn’t have to be.
“If not given the full attention it requires, carryback can threaten the productivity and safety of an operation,” Moore tells Australian Mining.
“When not addressed, it can reduce potential throughput, require frequent cleanup, pose slipping hazards for employees, and even cause premature belt wear.
“While it can be easy to overlook belt cleaners as just one small piece of a much larger puzzle, they play a critical role in minimising carryback and its negative effects on an operation.”
Moore says the best defense to the threat of carryback is an effective maintenance strategy for belt cleaners supported by remote belt cleaner monitoring technology.
Flexco has just released its latest technology, Elevate, a new software that allows customers to monitor their belt cleaners from anywhere.
Elevate’s predictive, data-driven engine lets customers move from traditional methods of monitoring cleaner performance to a new way that empowers operations for the future.
Moore says this technology employs devices attached to belt cleaners throughout an operation to monitor cleaner performance and transmit data to the cloud in real time.
“In a true remote belt cleaner monitoring system, this data is interpreted in the form of critical insights and predictive analysis that can help optimise productivity, streamline operations and heighten operational efficiencies,” Moore says.
He highlights four primary pain points of traditional belt cleaner maintenance that can be alleviated through using Elevate.
Keeping cleaners engaged and working properly For belt cleaners to work effectively, they need to be properly engaged with the belt and maintain proper tension levels.
“Because cleaners can become disengaged over the course of normal operations, it is essential that they be monitored and maintained regularly,” Moore says.
“If not, excessive carryback and buildup of debris on belts can lead to wear and tear, poor tracking, and seized idlers.”
Elevate can significantly improve an operation’s ability to track belt cleaner effectiveness and address maintenance needs in a timelier manner.
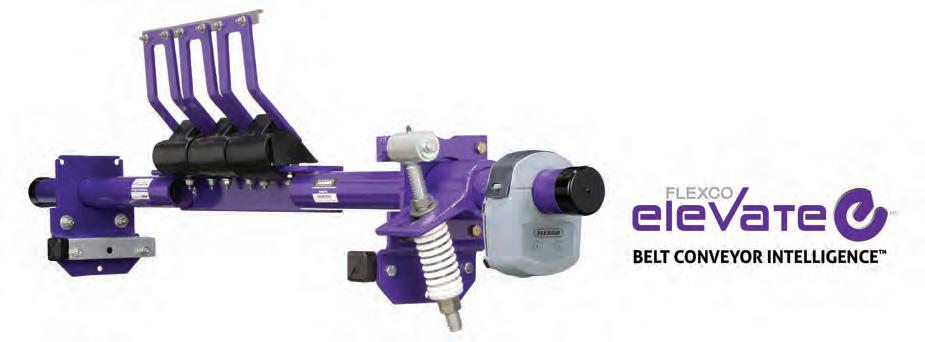
Manual maintenance and repairs compromise safety Moore says carryback is one of the greatest threats to employee safety on a belt conveyor.
“While there is a critical need for proper belt cleaner inspections and maintenance on conveyors, both of these tasks present safety challenges of their own by placing employees close to the moving belt and often in confined spaces to access the cleaners.
“A belt cleaner monitoring system lets operations remotely gather critical data and perform real-time analysis of belt cleaner performance.
“This can significantly reduce the reliance on manual inspections and the possibility for injury they present.”
Labor hours and wasted costs Manual inspections require a significant use of manpower for an operation.
This includes hours walking the belt or even driving to the site to conduct the inspections. Moore says once repairs are identified, additional time is required to coordinate with a purchasing department to secure any necessary parts.
“Allowing operations to better evaluate belt conveyor health anytime, anywhere, without dispatching a crew to the physical belt location is a significant advantage to remote belt cleaner monitoring,” he says.
Elevate can not only help reduce the need for belt cleaner monitoring, but it can provide insights to other areas of belt performance that can improve overall maintenance efficiency.
Accurately timing maintenance Scheduling belt cleaner maintenance on a belt conveyor can pose a number of challenges. If problems are not caught soon enough, what could have been solved with routine maintenance can lead to equipment failure, downtime and even potentially catastrophic events.
“In an ideal scenario, necessary maintenance work is identified in a timely manner and scheduled for upcoming planned downtime,” Moore says.
“However, even this situation can result in equipment being replaced prematurely, resulting in unnecessary costs for an operation.”
Elevate delivers valuable insights remotely and in real time.
These insights provide a detailed view of the belt cleaner performance and allow maintenance teams to better realise several factors such as cleaner engagement, belt and cleaner run times, tensioning reminders, and urethane and carbide blade wear.
Elevate can also detect abnormal events in overall belt performance that could indicate a more significant problem to come, including those that might not even be caught by the naked eye with a physical inspection. AM
THE FLEXCO ELEVATE I3 DEVICE SIMPLY ATTACHES TO FLEXCO BELT CLEANERS WITH A 42-BOLT CLAMP. THE FLEXCO ELEVATE I3 DASHBOARD PROVIDES OPERATORS INSIGHTS AT THEIR FINGERTIPS.
MACRO LEVEL ADVANCEMENTS FOR MICROMINE
TECHNOLOGY IS ADVANCING BEFORE OUR EYES, WITH BIGGER AND BETTER CAPABILITIES AND EACH SUPERIOR TO THE LAST.
Mining software is no different, and as technology progresses, there is no limit to what can be done on a mine site.
Micromine has taken the evolving industry in its stride and given itself a complete rebrand to increase its focus on new processes and opportunities unlocked by mining innovations.
The Micromine rebrand will give clients more clarity on which product is the right one for them and their particular mine.
“We have more offerings now, so the rebrand is about showing our clients what the product is, who it is for, the problem it is solving and where it fits in the value chain,” Micromine chief strategy and product officer Kiril Alampieski says.
Micromine revealed the rebrand at its industry event Micromine Momentum in November 2021, a virtual conference for geo-professionals and mining specialists, and the event also saw the release of Micromine Nexus.
Micromine Nexus will be released early this year, and is designed to connect and orchestrate workflow tools, while providing data security across the entire ecosystem.
“What we’re hoping with Micromine Nexus is to connect users and the data across the whole value chain so that everyone is singing from the same hymn sheet; working from the same set of data and collaborating around that to understand how they impact each other,” Alampieski says.
“By improving these decisions and outcomes, it will also have less of an impact on the environment and the community by getting it right the first time.”
After recently acquiring Alastri Software and Precision Mining’s mine scheduling software, Spry, Micromine is focussed on integration and making the companies mesh together as seamlessly as possible.
“With the acquisition of the two new businesses, it helps us clarify where our offerings fit in and what value they are delivering for our clients - that’s the key driver of the rebrand,” Alampieski says.
The two products created from the acquisitions are Micromine Spry and Micromine Alastri.
Both are mine scheduling software, however Micromine Alastri specialises in open pit metals and iron ore while Micromine Spry specialises in open pit coal.
The company has also revamped its namesake product, splitting it into two separate products - Micromine Origin and Micromine Beyond.
Micromine Beyond does everything around designing and simulating the mine, including long-term scheduling or strategic scheduling.
Micromine Origin is a comprehensive exploration and 3D modelling solution that allows you to integrate, validate and interpret critical exploration data.
“Micromine has a product covering almost every need of every user in the mining value chain,” Alampieski says.
The vision is clear for Micromine moving forward.
The company intends to work even closer with its clients to be able to give them the best mining solutions it possibly can.
“The focus is really listening to what our clients are saying and thinking about what the underlying issues are,” Alampieski tells Australian Mining.
“It’s not just solving the problem that’s right in front of our clients, but developing a technology solution that unlocks that next step – to the next generation technology for mining,”
Micromine is helping mines go digital across their whole operation as quickly as possible, utilising all the different parts of the value chain through the technology, which significantly scales up the client’s capabilities in their mining operation.
“This year is very much about facilitating collaboration between users by simply providing them with a technology platform that’s integrated,” Alampieski says.
With physical separation among mining and exploration teams becoming more commonplace, seamless transfers of knowledge and effortless data management is more critical than ever.
Micromine Nexus brings teams together through the latest cloud technology and direct integration into Micromine Origin.
Onsite exploration teams can utilise Micromine Nexus to collaborate with city-based resources or geographic information system teams, ensuring tighter version control of data and projects.
“We’re focussed on making sure that there is fluidity of data sharing and collaboration across the value chain so that it’s as seamless as possible to work with their colleagues, whether they’re in the same building, in the same team, or on the other side of the planet,” Alampieski says.
In the wake of the pandemic, many mining companies are enthusiastic about technology and how it, combined with better communication, can improve the future of mining, and with Micromine they have a one-stop-shop solution. AM
MICROMINE NEXUS WILL BE RELEASED EARLY THIS YEAR.
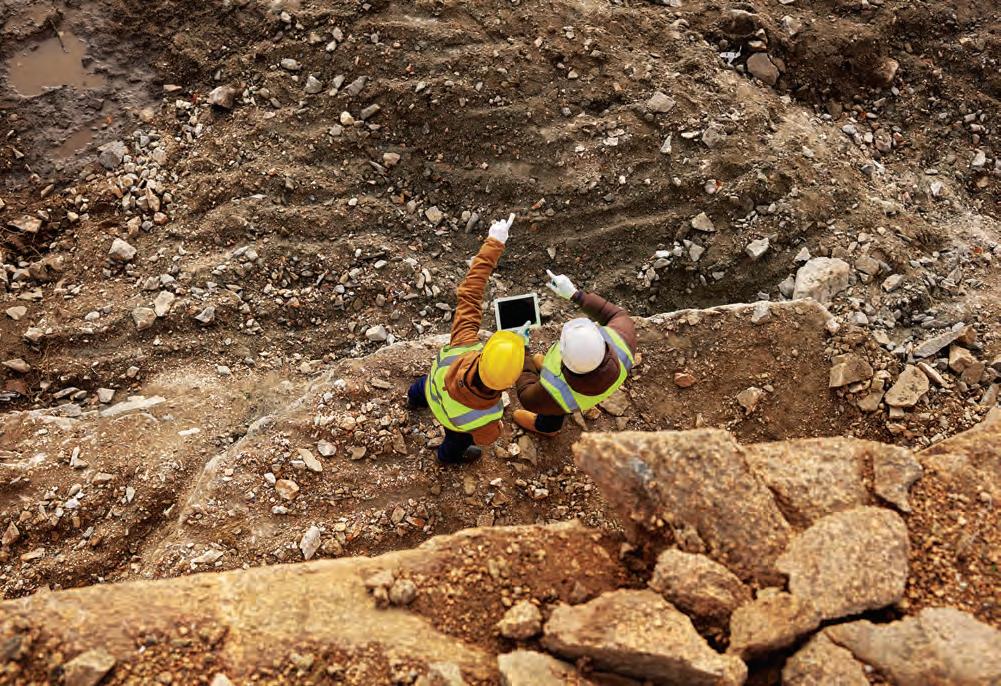
WIRELESS MONITORING IMPROVES SAFETY AND PRODUCTIVITY
EQUIPMENT IN THE MINING AND QUARRYING INDUSTRIES IS SUBJECT TO HEAVY USE, DIRTY ENVIRONMENTS AND HIGH TEMPERATURES. BSC LOOKS AT THE VALUE OF WIRELESS MONITORING IN THIS ENVIRONMENT.
ABB IS DELIVERING SMARTER OPERATIONS TO THE MINING INDUSTRY.
Wear and tear from these challenges and other pressures is unavoidable – but becomes crippling if it causes a machine’s rotating components to fail.
“The major pieces of equipment in a quarry or mining operation are rotatorbased,” BSC’s national engineering manager Anthony O’Keefe says.
“Think of crushers, combiners, rollers, pumps – these and others are the fundamental pieces of equipment needed to get the job done.”
The reliability of rotating components is paramount in ensuring facility output is maintained without disruption.
“Take a crusher, for instance. Big rocks need to be crushed down to size. If that crusher’s rotating component fails, then the crusher is out of action and the whole process comes to a halt. If you can’t crush rock, there’s no production,” he elaborates.
“So, we need to make sure such equipment lasts as long as possible – and to know where the machine is at in terms of maintenance and when it needs to be replaced. This might range from simple lubrication every now and then, to as much as a complete rebuild or equipment overhaul.
“How do you ensure reliability? By monitoring the condition of your equipment. This won’t come as a revelation to anyone.”
And essential to condition monitoring is vibration analysis – the process of monitoring levels and patterns of the various vibration signals in all types of components – so that abnormal vibration events are detected, and existing or oncoming problems identified and fixed before it’s too late.
“Vibration analysis is not a revelatory new discovery either,” he continues.
“Everybody does it. But not everyone conducts wireless vibration analysis. And this is key – because they should.
“Wireless vibration is not a new technology, but the mining and quarry industries have some catching up to do, which is completely understandable, because the pace of technological improvement and increasing cost-effectiveness has happened so fast – especially recently – that it’s just not on people’s radars yet.”
At the moment, the standard practice is for individuals to go to sites and manually conduct vibration analysis.
“Operations rely on individual data collectors to go to a site with their equipment, plug it into each asset, and do a series of data collections,” O’Keefe explains. “Then they will sit down and have to analyse that data.”
The whole process is very time consuming, with individuals – or even teams of individuals – walking through a whole plant, collecting data, analysing it, then returning to the main office to deliver reports on what has been found out and what actions might need to be taken.
“This is why we at BSC find ABB wireless monitoring devices so helpful – they make the case for mining operations to switch to wireless,” O’Keefe says.
“ABB remote wireless monitoring devices – the ABB Ability™ Smart Sensor is a great example – remove the need for individuals to walk around the plant.”
Using ABB’s remote wireless condition monitoring devices, companies can improve safety – as individual assessors are not exposed to risk; receive data in real time over the internet cloud – instead of receiving once-monthly reports from individual assessors; and access more and better data for greater reliability.
What goes along with these improvements and savings is greater capacity for analysis – and training in analytical trends – so that personnel can determine what equipment needs to be fixed, removed, or overhauled ahead of time.
O’Keefe sums it up as safer machines, safer workers, better data, better predictive ability, no surprises and no disruption.
“Customers can be confident in us as a supplier of wireless condition monitoring devices,” he concludes. “We have many supply options available, including ABB products; access to different technologies – and the competence to assist in choosing and implementing the right one.
“As part of Motion Australia, BSC is a big company with a great service offering. And that is matched by a big company like ABB, which has the resources to invest in R&D and produce the best devices – like the ABB Ability Smart Sensor.” AM
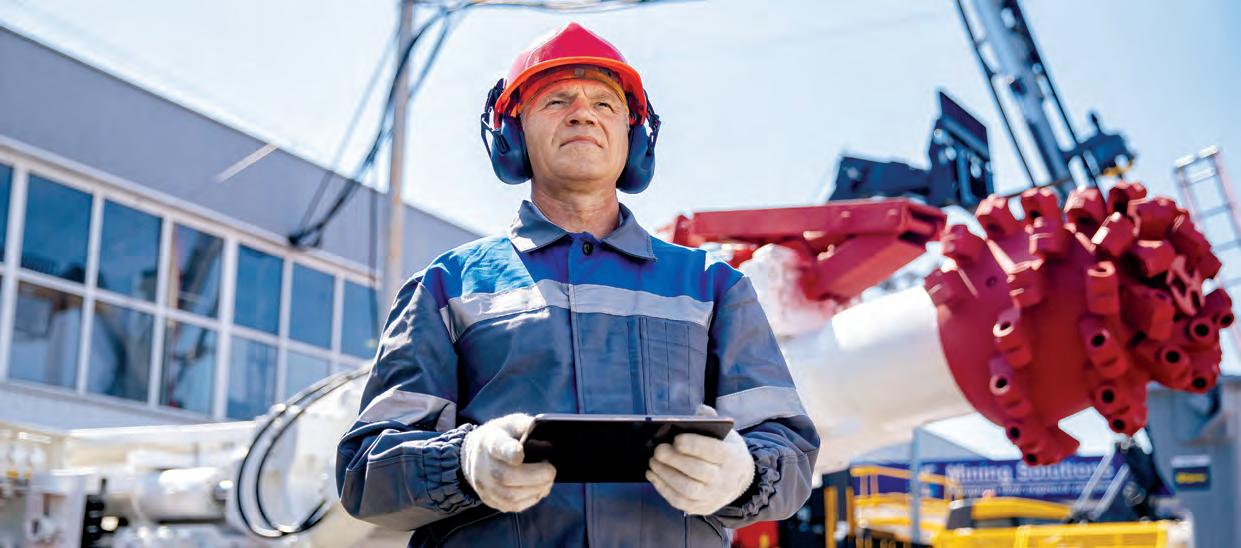
THE WORLD’S #1 WEAR STEEL
Hardness and toughness work together to make Hardox® wear plate a leading abrasion-resistant steel. It’s hard from the surface to the core, giving long service life and low maintenance even in the most extreme wear environments. It’s also tough, which makes it possible to use Hardox® as a structural steel. If you are looking for the best in wear steel, make sure you get genuine Hardox® .
www.hardox.com
Contact SSAB
Brisbane . Melbourne. Perth
G1, 28 Balacalva Street Woolloongabba, QLD 4102 Email: australia@ssab.com
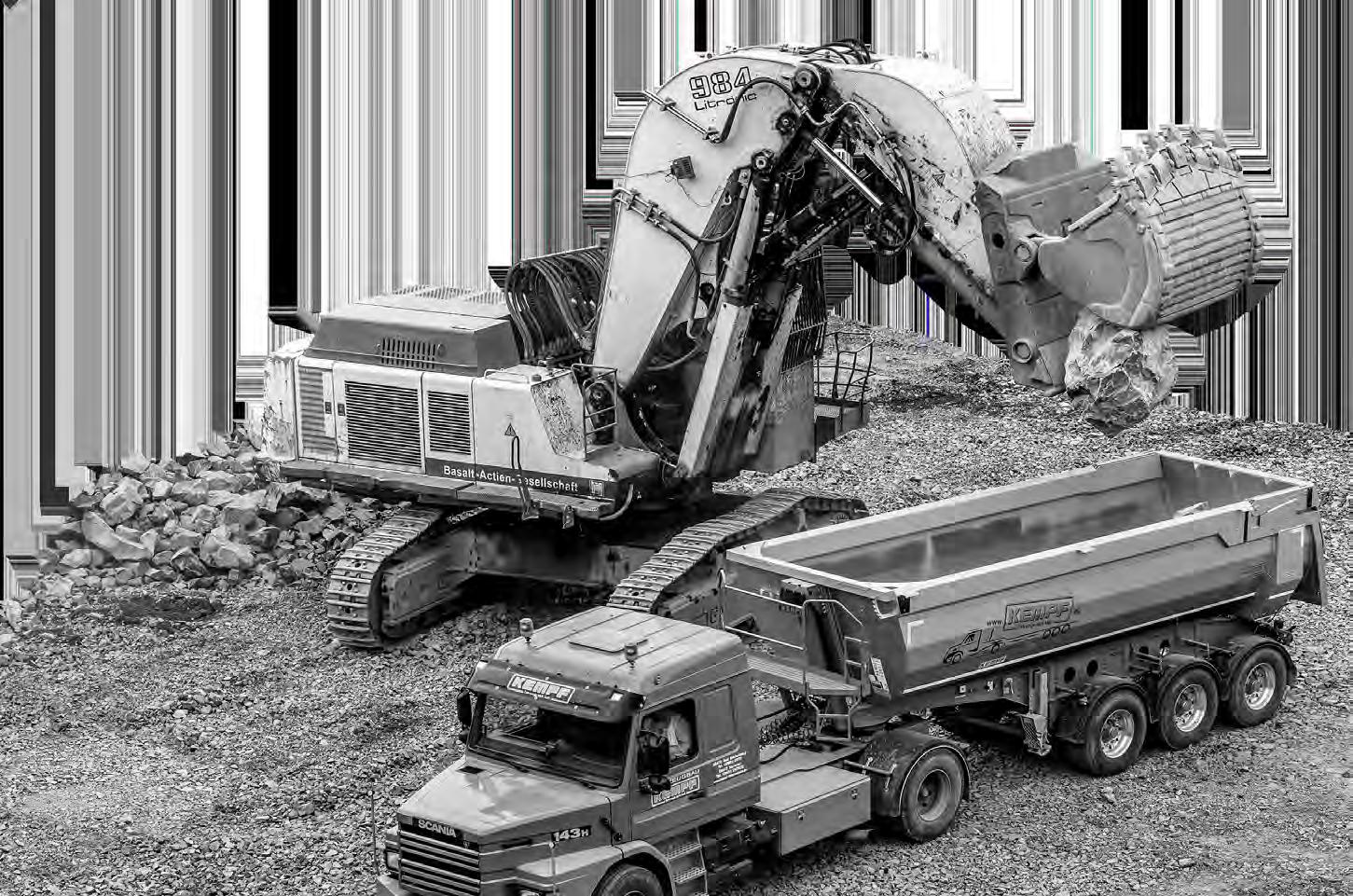