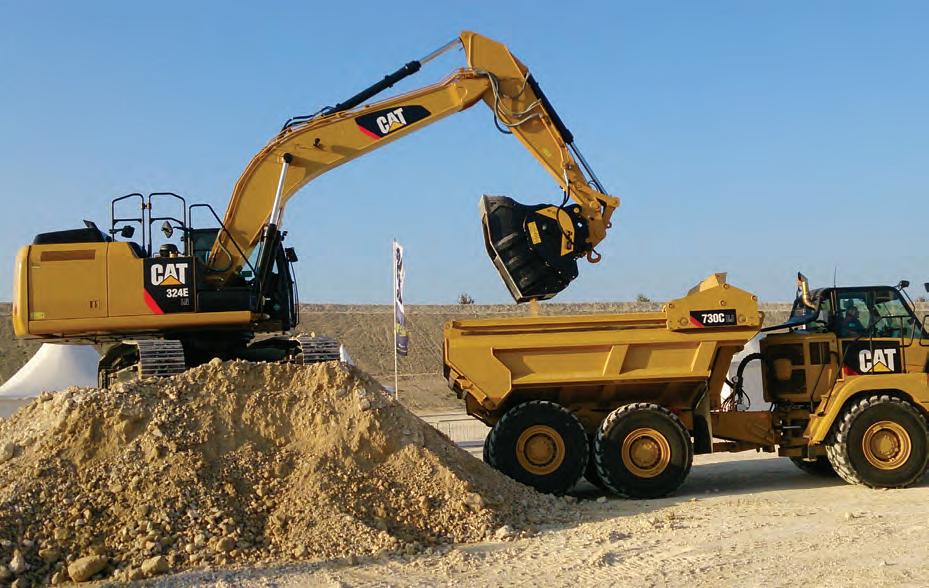
23 minute read
CRUSHING & SCREENING
A BUSINESS BUILT ON EXPERTISE AND ACCESSIBILITY
THROUGH ITS RELATIONSHIPS AND INDUSTRY REPUTATION, DM BREAKER HAS BECOME A MAINSTAY FOR MINING’S CRUSHING AND SCREENING ENTERPRISES.
Trading since 1997, DM Breaker Equipment has earned a reputation as a trusted supplier for a variety of sectors, including mining, construction, farming and civil engineering.
The company originally supplied rockbreakers for industry use, but the business has grown since then, becoming the sole Australian distributor of the reputed DNB attachments range, while also branching out to distribute attachments from the likes of MB Crusher, Remu and Movax.
DM Breaker’s work with MB and Remu has seen it provide solutions for crushing and screening – two critical steps in the ore reduction process.
The partnerships have been about more than just supplying a part; DM Breaker has assisted mining companies and contractors to achieve critical ambitions in the field.
“Five years ago, DM Breaker took on the MB Crusher dealership for Western Australia and Northern Territory, seeing an opportunity to assist companies and contractors in the mining industry to not only save them costs, but also to reduce the impact on the environment made by mining and earthmoving,” DM Breaker managing director Marion Marriott says.
With more than 60 years’ experience in the field, MB is at the forefront of research and technology in crushing and screening.
Over the years, the company has developed buckets that reduce the environmental footprint of operators and contractors alike, enabling the recovery of materials in situ.
“MB emphasises increased productivity in mining applications, such as increased production in gravity plants, MRP (materials requirement planning) applications and on-site processing,” Marriott says.
“The crusher buckets have the capability to add more value to mining operations and already existing tools at the job site.”
It’s no question crusher buckets play a vital role in the mining industry, and Marriott suggests the by-products created from crushing and screening processes hold untapped potential that some mining operators or contractors might not be aware of.
“Crusher buckets are very evolutionary for the mining industry and can change the way miners work. They create more versatility in handling a job, such as working in limited access areas where only an excavator can move in or crushing material immediately to optimise space and load factors on site,” Marriott says.
“Often it is just a matter of changing perspective; not only understanding that crushing and screening waste is not really waste, but realising that it is actually a huge resource, still to be exploited.”
After securing its MB dealership, DM Breaker established a relationship with Finnish crushing and screening manufacturer Remu.
Today, DM Breaker supplies Remu’s screening buckets for mining companies and contractors, another attachment that has proved its worth environmentally.
“Remu Screening Buckets are an ideal recycling solution – a multifunctional tool for padding, mixing, separating and crushing. The Remu buckets are being used for recycling landfill, composting, padding pipelines, backfill for underground mining and drying out tailings,” Marriott says.
“Each rotor has a direct drive radial piston motor to divide the power of the bucket equally. Interchangeable sized rotors enable various sized products to suit the required needs.”
Marriott says Remu and MB buckets are currently in operation across Australia, offering solutions for varying requirements.
The buckets are being used in the Tanami region of Northern Territory to dry out tailings, are working in nickel mines in the Goldfields region of Western Australia, processing gypsum in WA’s Mid West region, and completing remediation and utilising waste for road haul base in the Pilbara region of WA.
The current deployment showcases the versatility of the buckets, providing solutions for all manner of conditions and demands.
And such expansive commission couldn’t be made possible without the communication and collaboration between different parties in the supply chain.
DM Breaker believes cooperation is imperative in ensuring everyone is on the same page and that no work falls between the cracks.
The company is constantly engaged with Remu and MB at the original equipment manufacturer (OEM) level as the buckets are constantly finetuned to maintain their applicability in the field, while its exchange with contractors and mining companies is never stagnate.
And when DM Breaker isn’t maintaining liaison throughout the supply chain, the company is on the ground providing maintenance through its field service teams and dedicated workshops. A resolution is never far away.
A family-owned and operated institution, DM Breaker is underpinned by friendly and proficient customer support.
It’s a business built on approachability and accessibility – two traits never undervalued in the mining industry. AM
DM BREAKER DEPLOYS MB AND REMU BUCKETS ALL ACROSS AUSTRALIA.
THE POWER OF COLLABORATION
BOTH CRITICAL COGS IN THE MINING SUPPLY CHAIN, LINCOM AND DARACON HAVE FORGED A STRONG RAPPORT OVER THE YEARS. AS THE MINING INDUSTRY CONTINUES TO EVOLVE, THE RELATIONSHIP KEEPS BLOOMING.
Lincom has established a reputation for its work in the mining supply chain, delivering machinery from the likes of McLanahan, Thor Global and Powerscreen to mining companies and contractors.
The company recently distributed a fleet of Powerscreen crushers and screeners to New South Wales’ Daracon Group to supply road base, gravel and stemming materials at mines in the Hunter Valley.
Powerscreen’s Premiertrak 400X jaw crusher, Maxtrak 1300 cone crusher and Chieftain 2100X 3-deck screener have enabled mining operations to remain on track, exceeding expectations and highlighting the importance of relationships and cooperation along the way.
According to Daracon maintenance operations manager Mick Hingerty, the machines went through a judicious selection process before being selected for use, which included considering whole-of-life costs.
Powerscreen is a familiar original equipment manufacturer (OEM) to Daracon, and while a recognisable name always helps, the power of collaboration in the supply chain cannot be understated.
This is where Daracon’s strong connection with Lincom has proved vital.
“From our perspective, the Powerscreen product is well known to us. We’ve got a great depth of knowledge about the product and we’ve been on a bit of a journey over the last couple of years where Lincom have really partnered with us to provide direct feedback back to the factory,” Hingerty says.
“We’re really trying to create that continual improvement through Lincom to Powerscreen and we’re starting to see some of those initiatives flow back through some of the machines. There’s a lot of product improvements that we’d flagged with the manufacturer.
“We’re seeing some good payback in terms of the effort we’ve collectively put in.”
Hingerty believes that across the journey, Lincom has become more than just a supplier to Daracon. In an industry as scrupulous as mining, the importance of optimising productivity, safety and everything between has seen relations elevate beyond just a transactional connection.
“When you’ve got a big reliance on a supplier like Lincom like we do, you’ve got to treat them as more than a supplier; they definitely have to become a partner,” Hingerty says.
“They’re a part of our business. We have monthly supplier meetings – we’re very disciplined on that. We have actions out of every meeting and every person that participates in those meetings has one thing in mind and that’s to improve the Powerscreen products, and increase efficiency and uptime for Daracon.”
A key consideration in the continual improvement of Powerscreen’s machines is the need to ensure they are compliant with a constantly evolving and demanding mining industry.
Lincom’s equipment is mine spec compliant to Australian Standards, as well as MDG 15 compliant on all Hunter Valley mine sites.
This further consolidates the importance of collaboration and communication between more than one party.
“You cannot work on a mine site without meeting various regulations. Those three machines are probably among the first machines in the crushing industry at least that are fit-for-purpose, out of the box,” Hingerty says.
“Lincom has learned a lot over the last couple of years. The company is very proficient and knowledgeable about the mine site compliance requirements.
“A lot of the initiatives we are seeing Lincom present with its new machines now are all a result of us working together and us educating them on what we require.”
Daracon contract crushing manager Wayne Roberts says improving conveyor guarding is one part of this development process, again with mine spec compliance as the ultimate goal.
Each of Powerscreen’s Premiertrak 400X, Maxtrak 1300 and Chieftain 2100X 3-deck machines have conveyor guards which are installed to protect workers, whether it be from rogue material flying off the fast-paced machinery or to prevent employees from entering the danger zone.
“One of the big things about working with Lincom and Powerscreen is that we can have these guards put in place, but unless they’re in the correct place, most times they’re only going to be a hindrance to the actual operation,” Roberts says.
“So over time we’ve been able to work with Lincom and Powerscreen and have these guards designed so they’re fully compliant with safety.”
Roberts says that not only have the companies collaborated to redesign guards to ensure safety, but adjustments are being made end-toend, spanning components such as belt covers, skirting, dust suppression and beyond.
Both family-owned businesses, Daracon and Lincom share the humility and understanding to enable open communication and collaboration. It’s a relationship of constant improvement and development. Not always is an objective achieved first go.
But it’s only inevitable a likeminded partnership will achieve the desired outcome, and Daracon and Lincom have that down to a tee. AM
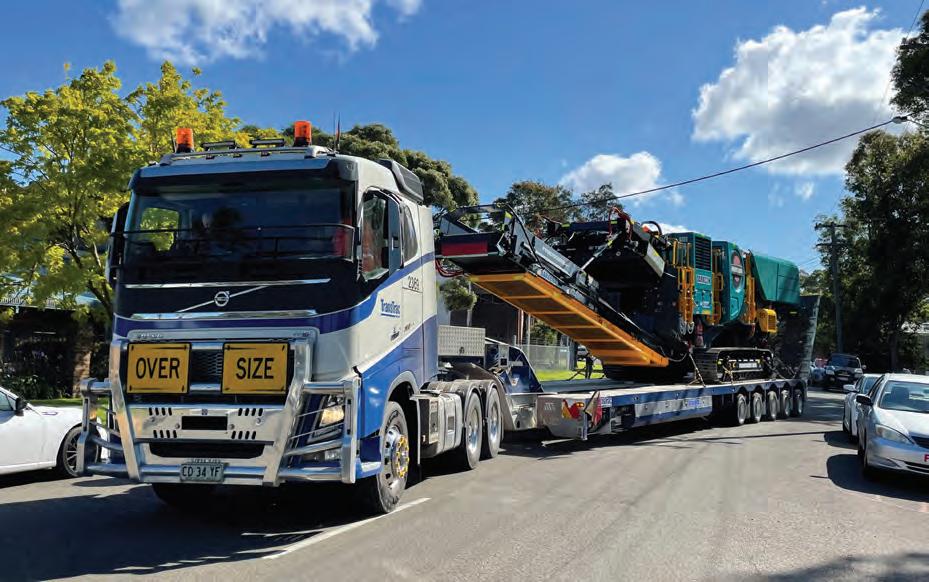
POWERSCREEN’S MACHINES HAVE BEEN A CRITICAL ASSET TO THE HUNTER VALLEY MINING INDUSTRY.
THE BACKBONE OF CRUSHING IS CUSTOMER-FOCUSSED
THYSSENKRUPP DESIGNS ITS CRUSHERS TO REMOVE ANY EXTRA STRESS FOR THE OPERATOR, WITH AN UNDERSTANDING OF THE SHEER NUMBER OF PROCESSES INVOLVED IN AN UNDERGROUND MINE.
Mineral processing is just one of Thyssenkrupp’s specialties in the mining space, with a range of equipment to cater to the vast array of environments and materials presented by the industry.
One of the most demanding applications these machines excel in is Australia’s iron ore industry where some of the most difficult conditions in global mining is found.
Thyssenkrupp product line manager for mining, Luke Bennett, tells Australian Mining the company’s vibrating grizzly feeder (VGF) is just one example of its crushing prowess, with a reputation to match.
“This machine has been the backbone of primary scalping for many years in the Australian iron ore industry,” Bennett says.
“With multiple installations, including the largest VGF installed in iron ore, and continual rotable machine demands, our clients request these machines because they know they will perform and last.”
Another example of the company’s crushing expertise is epitomised by its jaw gyratory crusher (JGC). Bennett says Thyssenkrupp sets itself apart by continuing to develop its existing portfolio of equipment while also introducing new technology as customers request it.
“The jaw gyratory crushers have been leading the way in block cave mining operations with the largest feed opening on the market,” he says.
“A client wanted a machine they could feed from both sides so Thyssenkrupp designed it for them.”
In response to the broader needs of its clients, Thyssenkrupp also designed the eccentric roll crusher (ERC).
The ERC is designed for greater efficiency and productivity using a roll mounted eccentrically between the crushing chamber and the integrated screening chamber. This optimises mining operations for better integration and automation.
Bennett also says the machine’s reduced size – up to 50 per cent – allows it to suit a wider range of mining scenarios.
“Our machines not only look at the process they are involved in, but the effect on our clients’ overall projects,” he says.
“The ERC not only delivers the product our clients require, which can be achieved from other machines, but also reduces the size of the underground cavity, or height of the crushing wall which has significant savings to the overall project.”
In all these crusher models and more, Thyssenkrupp ensures a formula for robust and simple operation.
Bennett says the less Thyssenkrupp customers must worry about the state of their machinery, the better.
“Robustness is one of the biggest considerations for our customers,” he says.
“This gives them peace of mind so that they can simply turn the machine on and all they need to worry about is replacing a liner in 12 months’ time, for example. They can rely on this happening year after year as the machine operates.”
This customer-centric consideration is a key pillar of Thyssenkrupp, supported by its number of service centres and approach to customer service.
Thyssenkrupp sales and service director Uwe Zulehner says all the aspects and disciplines of Thyssenkrupp’s customer’s operations are considered.
“In order for Thyssenkrupp to improve our products and services we need to understand the demands of our clients in a challenging and changing environment,” Zulehner says.
“The constant contact to our customers is fundamental for our business and the development of our support offerings.
“This goes for all different levels in their organisation, from the planning to the operational departments, as we listen to what clients have to say and where their challenges are.”
Thyssenkrupp operates multiple service centres near its customers’ sites, including in Port Hedland and Perth in Western Australia, and in Brisbane and Mackay in Queensland.
“These service centres provide continuous support to customer operations for shutdowns, maintenance and off-site repairs,” Zulehner concludes. “Having a strong and stable workforce helps us to deploy the same personnel to the same sites and machines.
“This increases their knowledge of specific sites which results in more effective on-site support and potentially reduces shut down times.” AM
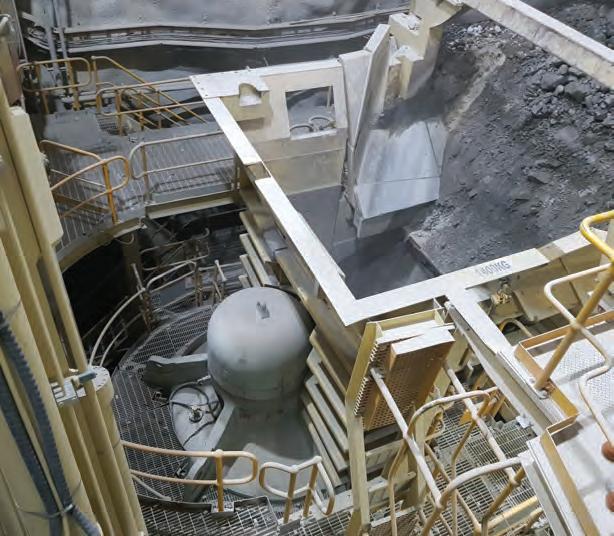
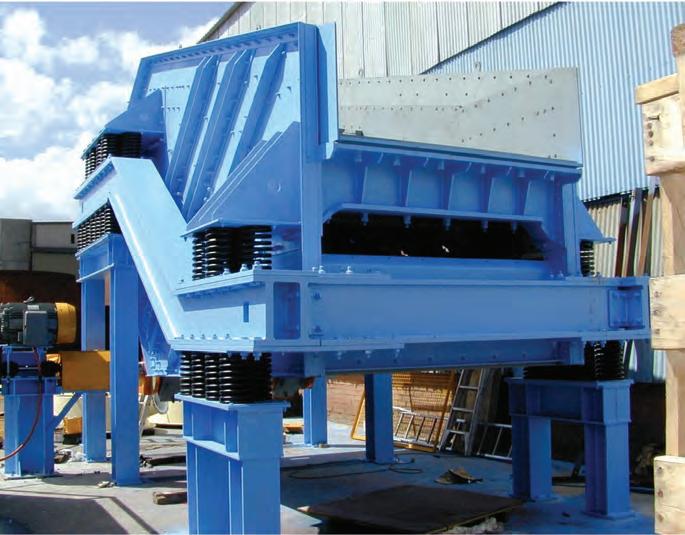
THYSSENKRUPP’S CRUSHERS CATER TO A WIDE RANGE OF MINED MATERIALS.
FLSMIDTH ZEROES IN ON SUSTAINABILITY
AS THE WORLD SCURRIES INTO ACTION TO REACH NET ZERO EMISSIONS BY 2050, FLSMIDTH IS TACKLING THE CEMENT AND MINING INDUSTRIES.
FLSmidth is bringing its A-game when it comes to reducing emissions, using unmatched technology and knowledge to enable mining and cement companies to be part of the solution, not the problem.
With sustainability at the forefront of FLSmidth’s ethos, its MissionZero ambition was born to reduce emissions in mining and cement to zero by 2030.
The fundamentals of MissionZero are FLSmidth’s goal to offer customers sustainable solutions that enable zero water waste, zero emissions and zero energy waste by 2030.
MissionZero utilises FLSmidth technology and products that allow miners to implement solutions that assist in reducing emissions across its flowsheet.
“You need mining for the clean energy revolution to go forward, so how we help our customers is absolutely critical to support mining in reaching net zero,” FLSmidth regional president Tamer Eid tells Australian Mining.
“The majority of Scope 3 emissions are from our customers, so the biggest impact we can have as a provider is helping our customers reduce their emissions, water and energy waste.”
There is no silver bullet to deliver MissionZero. Mining is complex and there are different solutions that need to be applied depending on the commodity and needs of the region.
Loading and hauling is one of the biggest sources of greenhouse gas emissions from a mine, and tailored solutions for in-pit crushing and conveying can significantly reduce those emissions.
“When you go to ship out the rock from the pit, in some places mines are so deep that the truck can take well over an hour to get to the top and the same to go back down,” Eid says.
“Think about that from an emissions perspective; that’s a huge amount of emissions just to get around the mine. But what about if you could crush it and ship it on a conveyor straight out of the pit where you’ve done the work?
“In-pit crushing and conveying means you can send it out ready to be used at the next stage of the process, which reduces the amount of trucks, thereby taking out one step of emissions creation.”
Grinding is another large source of greenhouse gas emissions, however, technology breakthroughs like coarse flotation and fast flotation machines can reduce the energy needed to grind ore by up to 30 per cent, improving recoveries and producing a cleaner product.
FLSmidth aims to put a sustainable package forward to customers which enhances productivity but reduces environmental impact at the same time.
In July 2021, FLSmidth agreed to acquire thyssenkrupp’s mining technologies business, thyssenkrupp Mining, with integration expected in the second half of 2022.
“The thyssenkrupp Mining acquisition is really important for us, it is a transformational deal that will set up FLSmidth as an even stronger mining sustainability innovator,” Eid says. “This creates a stronger value proposition for our customers, as we will become a true leader in global mining with a complete pit-to-plant range of technology, equipment and service expertise.
“We will also be able to offer bestin-class digital solutions, covering continuous mining, mineral processing and mining systems.”
The thyssenkrupp Mining acquisition will complement FLSmidth’s work with MissionZero as thyssenkrupp Mining has a strong in-pit crushing set up which will add to FLSmidth’s existing product range.
MissionZero is FLSmidth’s main focus of 2022 and beyond as the 2030 deadline looms.
“We’re confident knowing 2030 is a pretty short timeline, because we have these products available right here, right now. They’ve been used. They’ve been proven. It’s a particularly exciting time,” Eid says.
“For us it’s imperative that we help our customers achieve their goals with the products and technologies that are ready to go.”
As FLSmidth looks to the future, the company’s focus is to be the partner of choice for its customers, increasing productivity and profitability with sustainable solutions.
“It’s important to practice what we preach, so we are going full steam ahead down our MissionZero path as well, it’s not just about saying ‘this will work for our customers’, we also have to walk the talk,” Eid concludes. AM

What benefits could the MissionZero Mine deliver?
30% overall energy consumption reduction
Water in Reduce GHG emissions by more than 100,000 tonnes of CO₂e per year MISSIONZERO IS FLSMIDTH’S MAIN FOCUS OF 2022 AND BEYOND.
30% increase in plant throughput 45% reduction in grinding energy per kWh/t
35% reduction in grinding energy per kWh/t
Eliminating SAG mill grinding media saves up to 100,000 tonnes of CO₂e per year 80% reduction in water consumption 35% increase in revenue from metals recovered
We modelled what the impact would be if you replaced a traditional wet milling SABC circuit, standard flotation cells and cyclone sand tailings dam with the MissionZero Mine flowsheet for a 100,000 tpd plant.
THE VALUE OF THE CRUSHER OUTWEIGHS ITS COST
MINPROVISE GENERAL MANAGER OF ENGINEERING AND VALUE-ADDED SERVICE, JOHN MINNAAR, EXPLAINS WHY THE HIGH CAPACITY OF THE KAWASAKI ZI-2100 CONE CRUSHER’S CHAMBER RESULTS IN A REMARKABLE IMPROVEMENT IN CRUSHING CAPACITY.
The crusher is one of the most important pieces of machinery in mining.
It is responsible for breaking rocks and ore to produce a product that is suitable to be exported and sold or used in downstream processing.
The method used by some conventional crushers is to maximise crusher throughput. Their large eccentric settings result in a significant amount of material being recirculated through the circuit before it reaches the required size.
Improving on this method, Earthtechnica, a subsidiary of manufacturers Kobe and Kawasaki, has created the ZI-2100 cone crusher, which is distributed in Australia by Minprovise.
As Minprovise General Manager of Engineering and Value-Added Service, John Minnaar, explains, the ZI-2100 cone crusher stands apart from the competition by the way it processes material.
“It produces more material closer to the client’s desired size, per crusher pass,” he says.
“The ZI-2100 uses a smaller eccentric throw that means more precise crushing and less energy use. The rocks are more rounded through inter particle crushing, resulting in less recirculating load and reduced degradation when shipping the product.”
Degradation refers to the change in size of the product between the mine site and its final destination – normally overseas.
“When rocks break in the crushing chamber, they end up with jagged or splintered shapes that can be worn down during the transport and handling process,” Minnaar says.
“Degradation creates a significant difference between the weight of acceptable product on departure compared to its arrival at its destination. This can, and usually does, result in penalties for producers. Something the ZI-2100 crusher can reduce.”
Minnaar says crushers are generally selected in terms of throughput, but clients don’t make money with crusher throughput – they make money on the product produced, and that’s where the ZI2100 excels.
“Say, for example, a crusher processes 500 tonnes per hour. Of that 500 tonnes passing through the machine, maybe 150 tonnes per hour are not quite the client’s desired size, so it has to go back into recirculation,” he explains.
“Whereas with the ZI-2100, because of the slightly taller chamber, material stays in the chamber longer for more breakage, which means that of the 500 tonnes, less than 100 tonnes per hour are recirculated. This unlocks capacity potential in the circuit for more product to be produced and uses less energy.”
Minnaar says this increased efficiency has the potential to provide huge economic benefit, especially in the iron ore industry that has seen major price fluctuations over the past 12 to 18 months. More overall product can mean millions of dollars in additional revenue.
“As another example, say a plant produces 10 million tonnes per annum of product, common in the Pilbara, using ZI-Cone crushing technology could increase the plant output by approximately two per cent,” he says.
“That is more or less another 200,000 tonnes per year extra product. At $100 per tonne the two per cent adds an additional $20 million revenue to the bottom line. So, imagine what would happen if the increase was five per cent? This can be quantified through test work”.
Looking at another feature, the crushing liner nip angle on the ZI-2100 is optimised compared to conventional crushers.
“Because the ZI-2100’s crushing chamber is slightly longer, it can have a more gradual increase in angle and never exceed the material’s natural nip angle,” Minnaar says.
“If you have a very short crushing chamber, you need a large angle to go from the closed-side setting to the feed opening. This large angle is usually close or larger than the material natural nip angle causing the liner to wear very quickly, especially in localised areas resulting in liner belling.”
Minnaar says a longer chamber results in less downtime, less maintenance time and clients often gaining financially as liner changes are less frequent.
“With the ZI-2100 you can generally get a longer life out of a liner set,” he says. “We do see in our industry that focus is on the pricing of crushers and liners more than the value they can offer. Decisions on models are made by comparing crushers on throughput and seeing that one model costs less than the other.
“However, clients may be losing out on millions of dollars a year in additional revenue because selection of a specific crusher is not based on its value.
“For us it’s important to distinguish the difference between a crusher price and the value that a crusher adds to the process. Minprovise assist clients with data and information to evaluate and select based on value”. AM
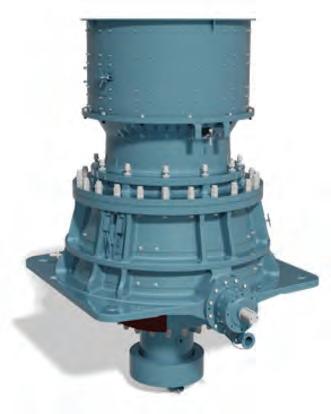
USING ZI-CONE CRUSHING TECHNOLOGY COULD INCREASE THE PLANT OUTPUT BY APPROXIMATELY TWO PER CENT. THE ZI-2100’S CRUSHING CHAMBER IS SLIGHTLY LONGER THAN OTHER MODELS.
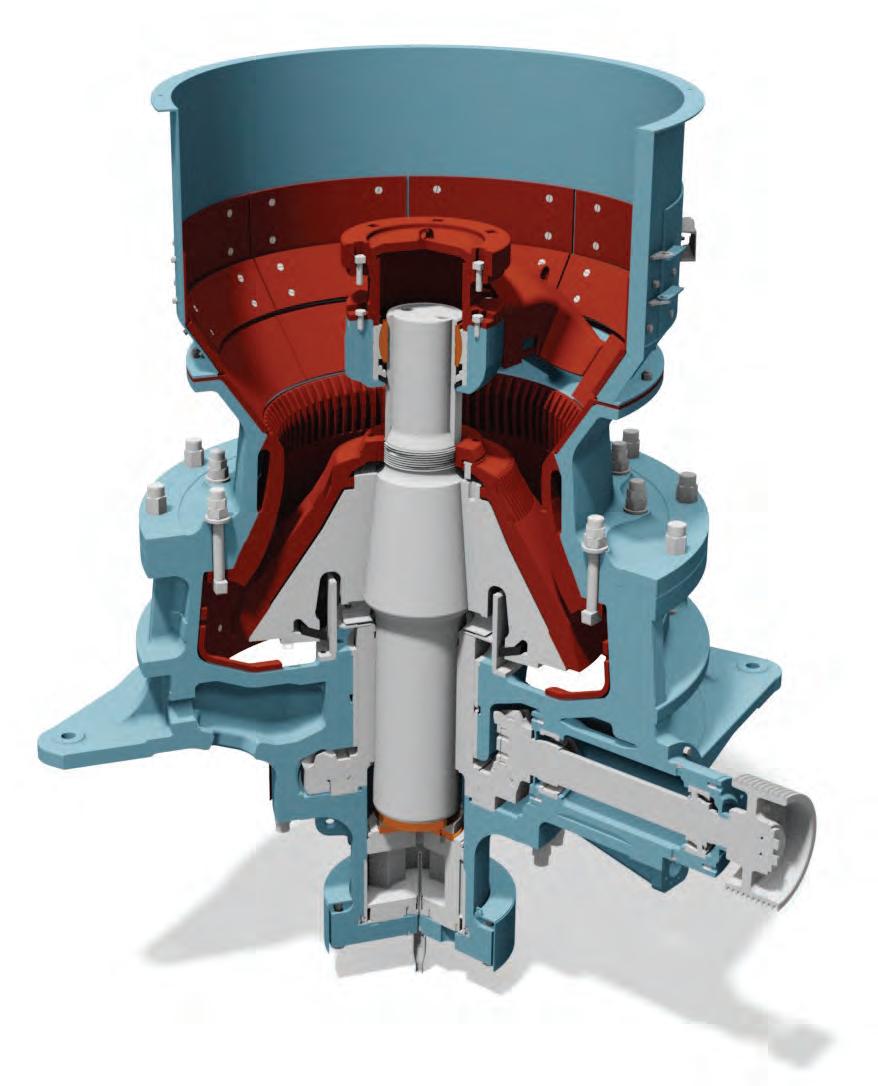
SEARCHING FOR SAFETY: BOOST SAFETY AND EFFICIENCY WITH DIAGNOSTIC TOOLS
HAVER & BOECKER NIAGARA PARTS AND SERVICE MANAGER WILM SCHULZ EXPLAINS HOW VIBRATING SCREENS AND THEIR PROPER MAINTENANCE CAN MAKE OR BREAK AN OPERATION.
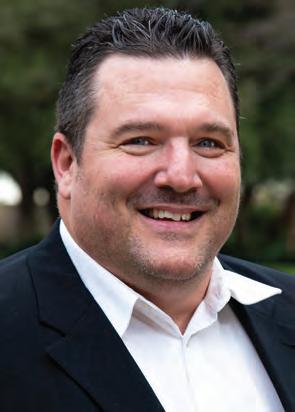
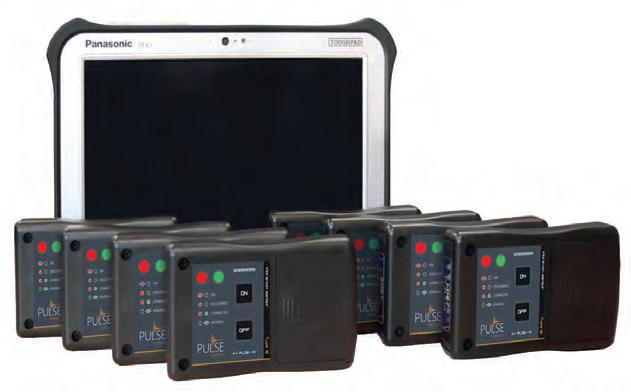
HAVER & BOECKER NIAGARA PARTS AND SERVICE MANAGER WILM SCHULZ.
Avibrating screen is the heart of steady operations, as the deciding factor in mined products meeting specifications. Deadlines and quotas might tempt producers to overload the screen while attempting to increase their bottom line. However, this contributes to downtime due to premature wear and might create safety hazards for workers near an unbalanced screen. And just as monitoring a heart rate is an essential for optimal health, the same idea applies to a mining operation.
Think of manufacturers as an operation’s cardiologist, there to diagnose and remedy operating issues before they become a safety hazard or halt production altogether. They provide producers with the necessities to streamline an operation and minimise downtime or injury. And, these days, that starts with diagnostics.
Like a house-call from a doctor, onsite diagnostics enhance aggregate operations through vibration analysis service programs without having to transport the equipment into a shop.
These programs offer producers insight on their screen’s performance to achieve optimum efficiency and ensure minor operating issues don’t become major hazards.
For the first time ever, manufacturers’ service programs provide producers the opportunity to monitor screening performance in real time. And recently, some manufacturers advanced these systems by using wireless technology.
These advancements offer a handsoff approach to analysing screening equipment by allowing operators to stand out of harm’s way — from a potentially off-balanced screen — when performing diagnostics.
In addition to safety, wireless technology offers operators remote, real-time monitoring, which ensures equipment is properly maintained and running optimally. This means less risk that strain is placed on the screen or other parts of the operation to maintain production quota. This increased efficiency and enhanced safety is the healthy choice for all areas of the operation.
Sound interesting? Here’s how it works:
It all begins with a close relationship with the original equipment manufacturer (OEM) and is enhanced by real-time equipment monitoring. Finding a key partnership where an OEM approaches the application as a solution provider rather than an equipment supplier is key to productivity and success. If your OEM isn’t providing consultative advice and real-time proactive monitoring, it might be time to seek another solution.
A key aspect to safety is having equipment that runs at peak performance and knowing when and how to maintain it. The more time spent fixing and maintaining the equipment heightens the risk of injury. That is where real-time monitoring comes in handy.
An advanced vibration analysis program specifically monitors the health of vibrating screens. That real-time feedback ensures optimised screen performance and equipment durability.
The hands-free system uses a wireless, industrial-grade tablet computer and eight tri-axial sensors to detect abnormalities the human eye cannot, such as a hairline crack in a side plate or an uneven or twisting motion. Even the slightest irregularities can result in diminished performance, decreased efficiency and safety risks for the operator.
The programs use wireless accelerometers to detect any irregularities, allowing operators to stand as far as 100 metres out of harm’s way. Each sensor attaches to key places on a machine to send 24 channels of data to the tablet via WiFi — illustrating the machine’s orbit, acceleration, deviations and more.
After the sensors record the data, trained and experienced engineers review, study and interpret the results through the system’s database. This provides the engineers and producer with a detailed report of any concerns.
If an irregularity is detected, the service team travels to complete onsite service, which keeps producers on top of preventative maintenance and ensures a safe operation that runs at maximum efficiency and lower risk. Some vibration analysis systems store each machine’s historical data, which allows for quick comparison over time and easy troubleshooting.
More and more often, producers rely on diagnostics for safer work environments and a streamlined operation. Its hands-off approach offers producers a healthy operation, running at peak performance, which helps them efficiently meets deadlines and produce quality product for their customers. AM
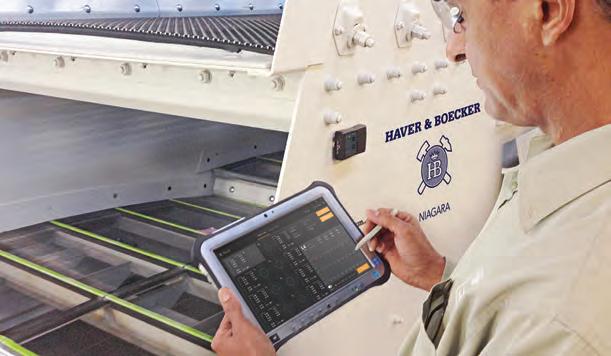
HAVER & BOECKER NIAGARA’S PULSE VIBRATION ANALYSIS PROGRAM MONITORS VIBRATING SCREENS.
AFTER THE SENSORS RECORD THE DATA, TRAINED AND EXPERIENCED ENGINEERS REVIEW, STUDY AND INTERPRET THE RESULTS THROUGH THE SYSTEM’S DATABASE.
CAPS AUSTRALIA HIRE, SALES & SERVICE BUILT FOR THE MINING INDUSTRY
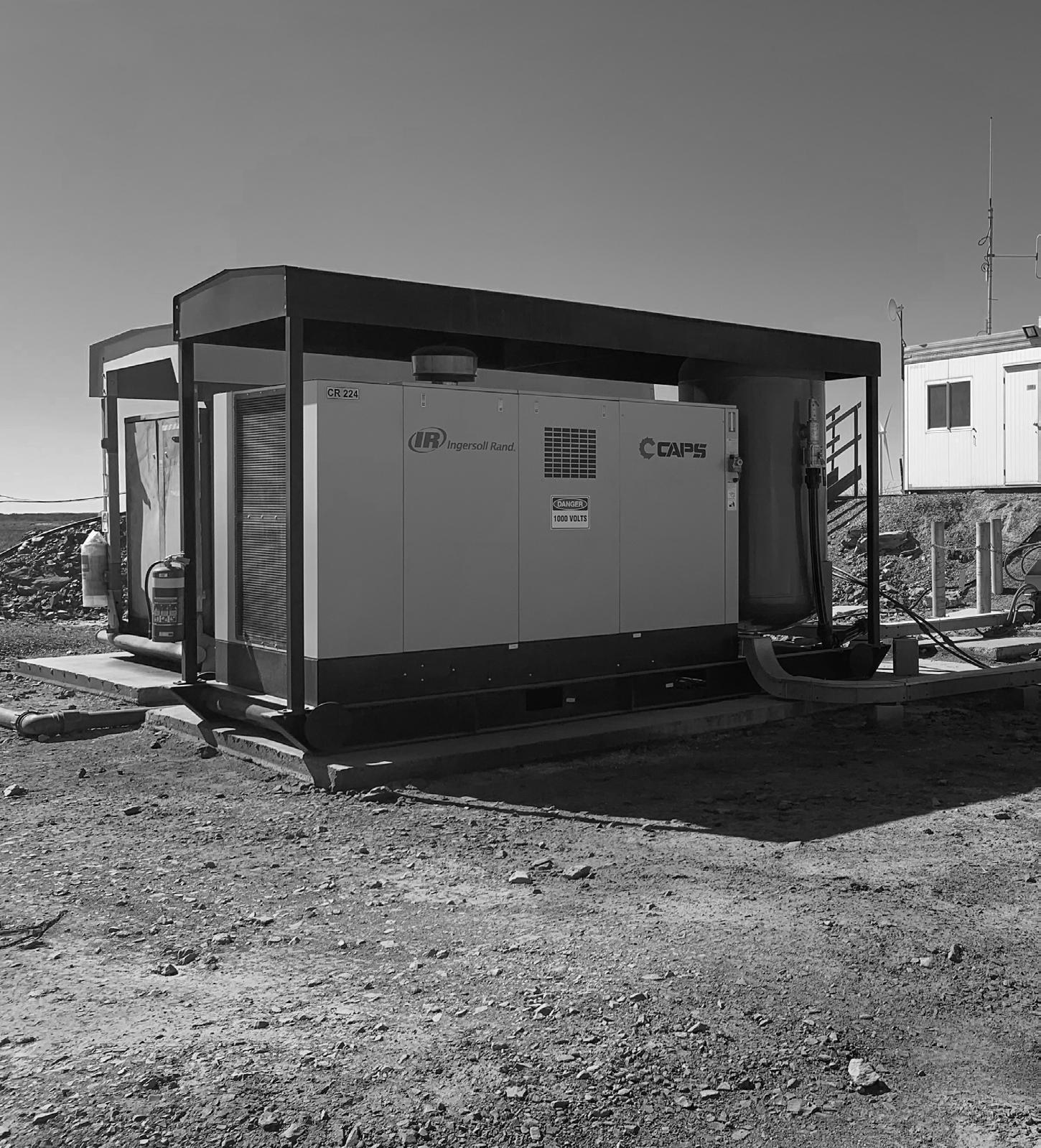