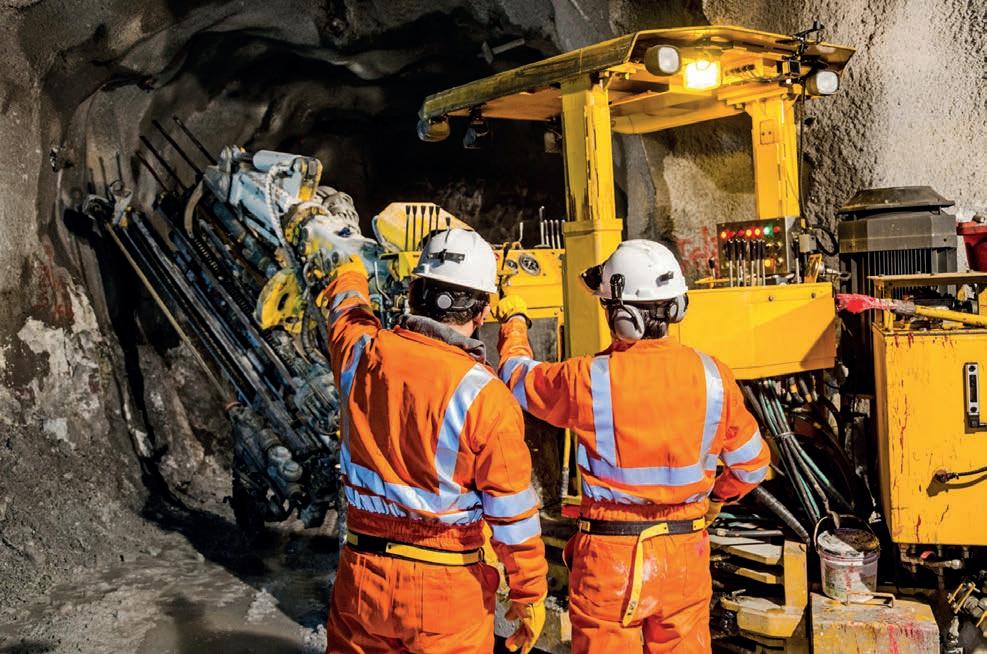
12 minute read
INDUSTRY OUTLOOK
THE ROAD TO BECOMING A REGISTERED ENGINEER
TO PROVIDE PROFESSIONAL ENGINEERING SERVICES IN QUEENSLAND, ENGINEERS NEED TO BE REGISTERED. WE SPEAK TO AUSIMM ASSESSOR PETER HILLS ABOUT THE PROCESS.
The Board of Professional Engineers of Queensland (BPEQ) is striving to improve the Queensland mining industry’s compliance with the Professional Engineers Act 2002.
In doing so, the independent statutory body is encouraging more mining engineers to register themselves as part of the registered professional engineer Queensland (RPEQ) system.
Despite engineers’ importance to mining, the industry does not have the same representation of RPEQs as other sectors and, given engineering misconduct can have major consequences to health and safety, as well as project integrity, registration is critical.
Becoming an RPEQ is a fourstage process. Once an engineer has graduated from a recognised tertiary institute with a four-year undergraduate degree in engineering (or equivalent), they will then need to gain 4–5 years’ experience working as an engineer and carrying out professional engineering services under supervision.
The application and assessment process can then commence; however, it is advised that engineers should start preparations long before they are ready to apply.
This starts with the continuing professional development (CPD) logbook where engineers must complete a minimum of 150 hours of structured CPD in a three-year period leading up to their application.
The logbook enables engineers to keep track of their experiences during their studies and early working life, whether it be attending workshops, conferences and events, preparing and presenting papers, or logging course units from university.
Engineers previously had an obligation to complete the CPD logbook, but it was not a requirement for the application process. That changed in 2015 when it was found a higher percentage of engineers weren’t passing their first audit and not keeping track of the required CPD and hours of work connected to this.
Peter Hills, Pitt & Sherry senior principal geotechnical engineer and Australasian Institute of Mining and Metallurgy (AusIMM) assessor for BPEQ, said engineers who can demonstrate their technical experience would be better positioned come the assessment.
“There are 10 categories for professional development that
RPEQ REGISTRATION IS CRITICAL TO PREVENT ENGINEERING MISCONDUCT IN THE QUEENSLAND MINING INDUSTRY. underpin the RPEQ, and the value of those various categories depends on the degree of technical involvement and activity from the person involved,” he told Australian Mining.
“So undertaking further university study, undertaking short courses, attending conferences, giving papers, and so forth are worth a lot more and you can do as much of those as you like.
“The easier activities such as private reading and on-the-job skill enhancement are limited in how many hours you can do, and we have tailored the scheme to weight towards the more active, getting-involved and learningnew-things-type activities.”
Once the engineer has satisfied the initial examination regarding their CPD logbook, a registered assessor will consider their sponsors.
“Engineers are required to have three sponsors who they nominate, and the assessors make contact with the sponsors and obtain feedback from them on the capability of the individual,” Hills said.
“If the sponsors are an RPEQ or a chartered professional, that rates a lot higher in the assessment than if it’s someone at a similar level.”
Once assessors are satisfied with an engineer’s sponsors they will then proceed to an interview where they will be asked about the documentation they’ve provided, that they understand what being an RPEQ entails and their responsibilities under the Professional Engineers Act 2002.
If the interview is successful, the assessor will recommend the engineer to the BPEQ, which will enable them the right to register as an RPEQ.
Hills said it was important for any budding mining engineer interested in becoming an RPEQ to be vigilant about their preparations.
“The important thing not only individuals should be aware of, but also companies with new graduates, is the requirement to work towards it (the RPEQ),” he said. “Because if you don’t have your three years of professional development logged when you apply, then you’re already three years away from a successful application.
“People need to be thinking about that … pretty much from day one and their mentors and managers should be pushing them in that direction to make sure they’re doing that.”
It’s also important engineers have clarity about the process of becoming an RPEQ and that their achievements recorded in the CPD logbook align with what’s required by the BPEQ. This is accessible via AusIMM.
“People need to look at the information on chartered professionals and registration on the AusIMM website as soon as they start thinking about becoming an RPEQ,” Hills said.
“They need to be quite clear on what they’re doing in terms of professional development so that from day one they’re doing relevant stuff.” AM
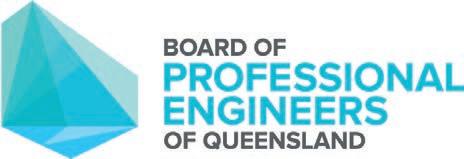
IRON ORE PLANT BENEFITS FROM ENGINEERED UPGRADES ON ROTARY SCRUBBERS
AN ESTABLISHED IRON ORE PROCESSING FACILITY IN WA HAS ADVANCED THE CAPABILITIES OF ITS ROTARY SCRUBBERS WITH MCLANAHAN’S NEW TRUNNION BASE ASSEMBLY.
These particular rotary scrubbers had been installed at the Western Australia site in 2009 and were beginning to show the wear of intensive use from over a decade of operation.
Due to its longstanding history as a trusted original equipment manufacturer (OEM), McLanahan was engaged to implement a design upgrade solution.
“We were also aiming to extend the wear life of the barrel, which was previously a large welded structure with a shrink-fitted ring all the way around,” McLanahan mechanical design manager Ben Freeburn said.
“It had begun to show some cracking, which was not all that surprising considering that these machines do in the order of two million cycles every six months. So we worked with the customer to implement a deep steel forging design that was a lot more durable.”
While the engineering team worked on retrofitting this new support frame, discussions with the customer resulted in the expansion of the project.
The process of manual precise alignment was time-consuming and presented some safety risks, so McLanahan proposed an upgrade to the trunnion base assembly that incorporated self-aligning features to remove risk and reduce maintenance downtime.
The washdown of crushed rock and ore in these suspended cylindrical barrels is a key step in the ore processing cycle but presents challenges relating to the barrel suspension technique.
“We were able to tackle a couple of issues in one go with this project,” Freeburn said. “With rotary equipment, there are two main support methods – hydrostatic bearings and trunnion rollers.
“While the hydrostatic solution has the benefits of high-capacity support and low friction, it does require complexities such as filtration, accumulator banks and complex hydraulics. In particular, it is important to have a robust sealing arrangement at the full barrel diameters to keep water and dust particles out of the main journal. This is nearly impossible to achieve in a mining environment.”
Conversely, trunnion rollers can support heavy loads on a much simpler apparatus, but the downside is that they are sensitive to misalignment, causing the barrel to thrust back and forth.
The mechanical design engineers at McLanahan sought to create a self-aligning system, rendering the trunnion base assembly as the superior option on various-sized rotary machines.
Freeburn likens this mechanism to “a swivelling shopping trolley wheel” that auto-corrects when misaligned due to a vertical axis offset.
He said this design was unique in its flexibility, as it had proven success operating on a broad weight and size range.
“It improves the reliability of the machines more than anything,” Freeburn said. “On customer sites where these changes have not been implemented yet, we are seeing reoccurring issues because a single component has shifted 2mm and it has ended up costing them in downtime for realignment.”
This project was not only successful in adjusting the trunnion rollers to skew on a horizontal axis, but also incorporated the ability to correct three-dimensionally in any plane of misalignment via a spherical seat.
“Our engineering team conducts frequent site visits, which helps to strengthen our relationship with each customer and deliver them more tailored support,” Freeburn said.
“Whether it is upgrading existing machinery or extending the equipment’s wear life, McLanahan has over 185 years of expertise to back our services. Through that experience, we have a very intimate knowledge on the capacity and design limits of these trunnion rollers.”
Other upgrades included a park brake, integrated jacking system and a cassette-style trunnion roller changeout frame co-developed with the site maintenance crew to ensure a holistic integration of this equipment upgrade into existing site operations.
“The park brake is an essential safety implementation, as it allows the operators to stop the machine via a hydraulic pump, support the full weight of the barrel, secure it from rotation, and work on it without causing back injuries or slipping,” Freeburn said.
“It is all about working with the customer to understand their plant layout and requirements.
“The key takeaway from this outcome is that if you prioritise a collaborative working relationship with the customer, it will benefit the outcome and solution.” AM

TRUNNION ROLLER ASSEMBLY.

MCLANAHAN’S EXPERIENCED TEAM HAS INTIMATE KNOWLEDGE OF THE CAPACITY AND DESIGN LIMITS OF THE TRUNNION ROLLERS.
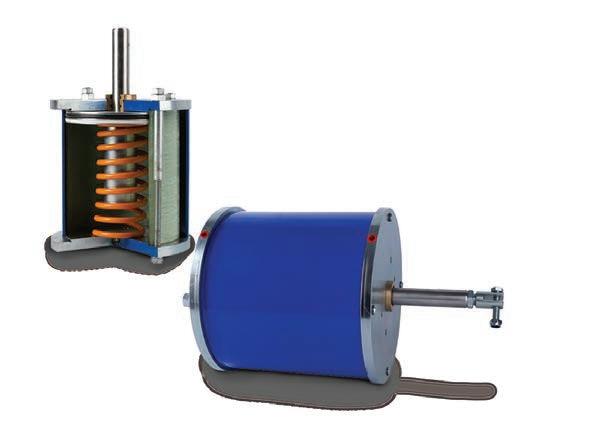
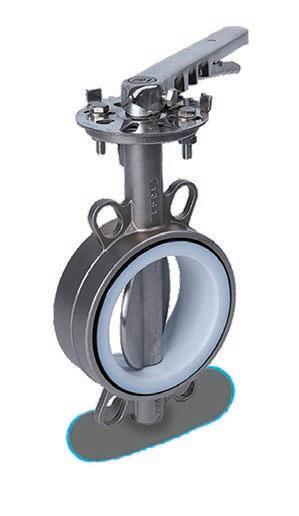
CONNECT, SCAN AND OPTIMISE
WHEN IT COMES TO COMPRESSED AIR INSTALLATIONS, ATLAS COPCO WANTS TO MAKE SURE ITS CUSTOMERS ARE ALWAYS CONNECTED AND INFORMED.
As Charles Darwin once said, “It is not the strongest of the species that survives, nor the most intelligent that survives. It is the one that is most adaptable to change”.
A compressed air system is one of a mine’s biggest energy consumers. Gaining energy efficiency can have a big impact on costs, while also helping to reduce CO2 footprint. Atlas Copco wants to make sure its customers are always connected and informed.
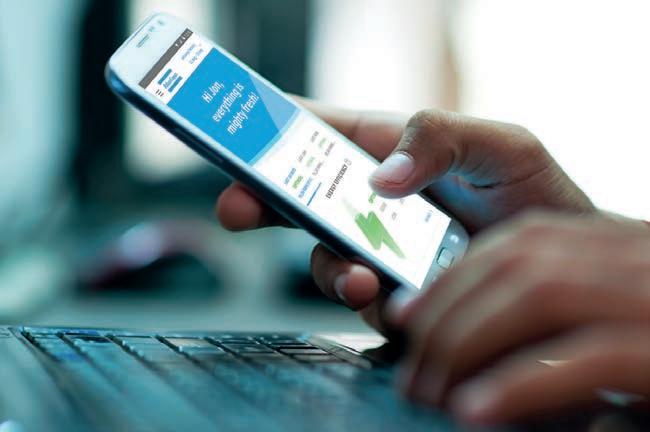
Connect In a world where smartphones have become so ubiquitous, there are already more connected devices than people in the world, so it makes sense that being connected has also become a normal part if modern industry.
Being connected means instant visibility, and the Atlas Copco SMARTLink range of monitors captures live data from compressed air equipment and translates that information into clear insights. Users can check uptime, energy efficiency and CO2 emissions at a glance.
SMARTLink offers easy followup of the energy consumption of compressed air installation. Users can get a quick overview on the dashboard or delve deeper into customised reports. Uniquely based on machines’ actual working conditions, recommendations present real opportunities to improve the efficiency of an air system.
Connecting via an SMARTLink Energy Plan means compressors’ data will be fed into the Atlas Copco Big Data Framework. This allows the company to activate diagnostic supervision of compressors, enabling it to spot and fix any deviations at an early stage. Based on algorithms and expert analysis, proactive troubleshooting keeps customers’ energy efficiency at its top level.
Scan Atlas Copco offers a compressed air auditing and leakage detection system so businesses can have a deeper understanding of their systems.
AIRScan is a compressed air auditing and leakage detection service. An AIRScan energy audit includes a full survey of the compressed air net parameters, including energy consumption of the equipment, flow rates and pressures, to get an accurate picture of the compressor room.
With measurements performed during operation, production does not need to stop during an audit. The logged information is used to simulate several energy-saving scenarios. The system’s unique and proprietary analysis software can simulate different configurations of a compressed air system, allowing insight into realistic savings figures.
The AIRscan report provides a clear summary for decision-makers, as well as an in-depth analysis of problems and solutions for technical staff to help to improve system performance.
It is estimated that after five years, 20–30 per cent of the energy used by a compressed air system is wasted on leaks. A leak as small as 3mm can be very expensive, with an energy loss equivalent to 16 tonnes of CO2 emissions.
During an AIRScan leak detection survey, a state-of-the-art acoustic camera detects 40 per cent more leaks than traditional tools, at twice the speed. The air leaks report includes the savings potential and a priority list for repairs.
Knowing the condition of compressed air equipment and being able to respond proactively is the surest way to achieve maximum availability and protect the investment. The AIRScan vibration analysis is a health check for the compressor element, gearbox, coupling, drive train and other rotating components – a powerful tool in preventing expensive breakdowns.
Air purity is also vital. Compressed air that contains unwanted substances like water, oil or solid particles may impact the quality of a mine’s final product, while companies may need to comply with quality standards.
The AIRScan analysis uses advanced tools to check the purity of compressed air. It comes with a clear report, including recommendations on achieving the air quality you need.
Optimise If a compressed air system has multiple compressors or blowers, they have to be started, stopped and regulated to meet fluctuations in air demand.
In a traditional system, output pressure often exceeds required pressure, resulting in a cost increase. The Atlas Copco Optimizer 4.0 and Equalizer 4.0 are designed to offer a much smarter solution. By automating compressor operation, these master controllers increase system stability, minimise wear and achieve optimal energy efficiency.
Additionally, Atlas Copco offers AIRNet piping systems for any compressor piping systems that have excessive leaks or are undersized or inadequately designed.
A high-end aluminium system designed to save the money that other piping systems spend, AIRNet is sized, planned and installed to support sustainable operational excellence in the production process. AIRNet piping systems can influence the total cost of ownership and the level of production efficiency by optimising the sizing, planning and installation of the piping.
Heat generated in air compression is diverted to the cooling system and released into the atmosphere.
The thermal energy that would otherwise be wasted from this can be put to good use with Atlas Copco’s Energy Recovery, which recovers the heat so it can be used for workspace heating, hot water or industrial processes.
Compressors of any age or type can benefit from the processing capability of the Elektronikon Mk5 Touch controller, which offers the most advanced control algorithms and connectivity via SMARTLink and results in improved machine control and energy savings.
Businesses seeking to unlock potential savings of their compressor rooms can discover how they can be better connected, informed and optimised. AM
ATLAS COPCO OFFERS A COMPRESSED AIR AUDITING AND LEAKAGE DETECTION SERVICE CALLED AIRSCAN. THE USE OF AIRNET PIPEWORK THROUGHOUT THE FACTORY WILL PROVIDE A LEAK-FREE ENVIRONMENT. THE ATLAS COPCO SMARTLINK PRODUCT IS DESIGNED TO CONNECT A MANUFACTURER TO AN EASIER LIFE.
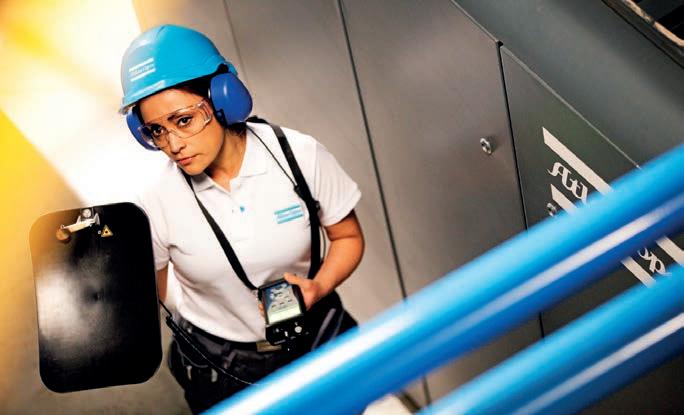
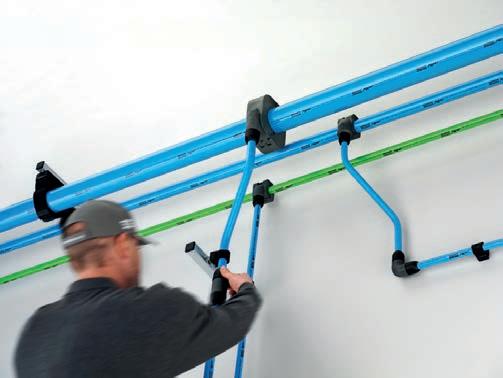