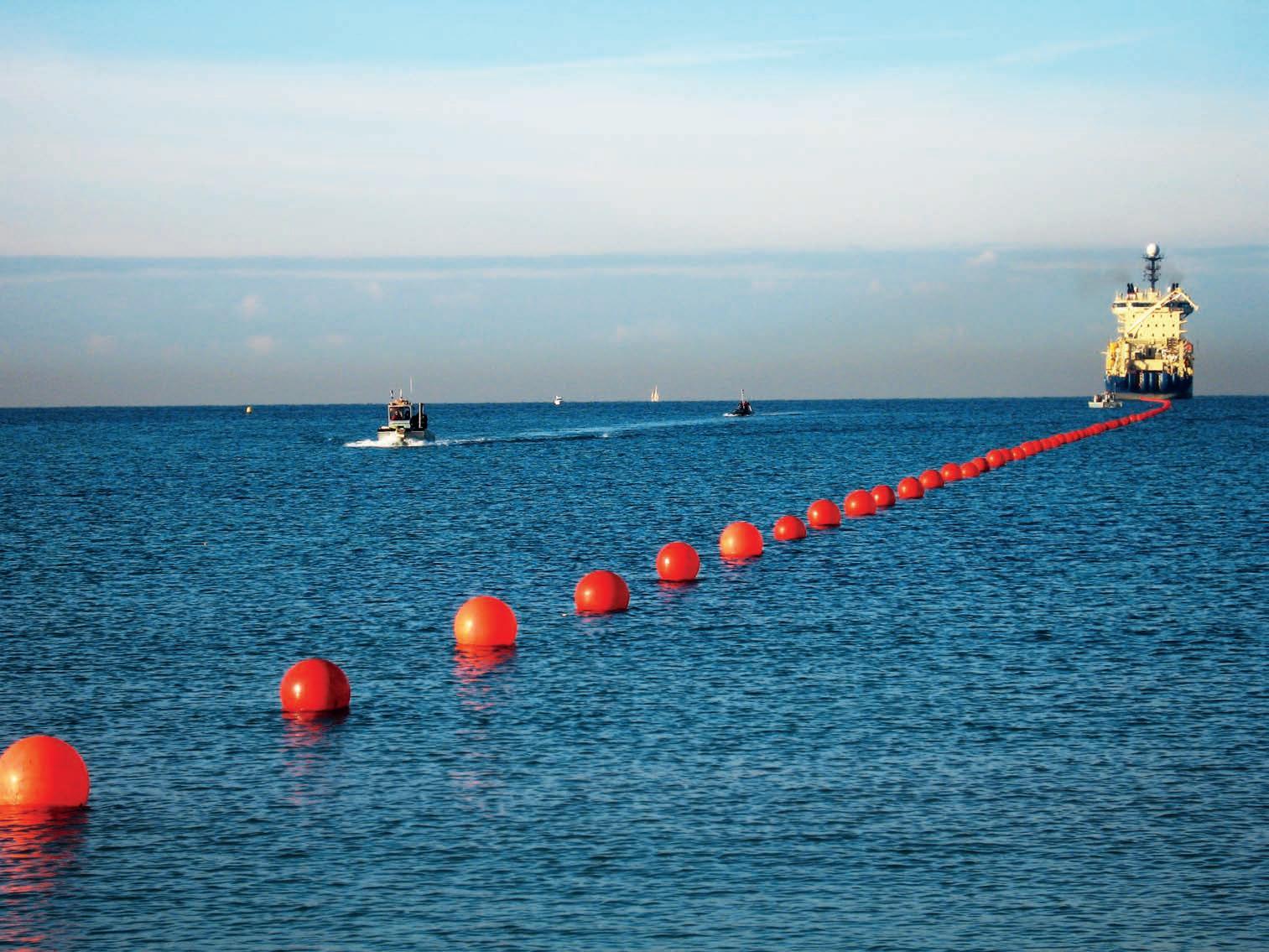
17 minute read
MINING SERVICES
VOCUS’ LEO SATELLITES WILL COMPLEMENT ITS FIBRE INFRASTRUCTURE.
CONNECTING THE DOTS
TO ENABLE THE MINING INDUSTRY’S TRANSITION TO CLOUD-BASED TECHNOLOGY, VOCUS GROUP IS DEVELOPING FIBRE NETWORK CABLES AND SATELLITE TECHNOLOGY TO IMPROVE CONNECTIONS IN REMOTE AREAS.
Australia is home to hundreds of mining leases that are being mined and explored across northern and western parts of the country.
But border closures and fly-in, fly-out (FIFO) travel bans due to COVID-19 restrictions have affected mining companies’ ability to source skilled workers.
This situation is shifting many companies further towards automated and virtual means of conducting mining and exploration activities.
However, these technologies require a fast and low-latency network connection, which is costly and often unavailable in remote mining areas.
Vocus is developing multiple solutions to get rural mining areas up to speed through capable fibre network connections and satellite internet technology.
“Smaller mining companies are going to want to be highly leveraged around their cloud infrastructure,” Vocus national general manager government and special projects Michael Ackland said.
“Rather than smaller miners buying their own servers, they adopt ‘pay as you use’ servers, which are currently based on Australia’s east coast.”
Vocus’ Darwin-Jakarta-Singapore Cable will allow mining companies to hook up their cloud infrastructure to Singapore rather than Melbourne or Sydney, which will improve latency and cost.
This will be the first international cable connection into Darwin and amps up the connectivity of much of northern Australia through stronger fibre infrastructure.
Vocus is also developing Project Horizon, which will deliver fibre infrastructure from Geraldton to Port Hedland, Western Australia, and then on to Singapore via the DarwinJakarta-Singapore Cable.
The company expects these projects to significantly strengthen the internet connection in remote regions of WA.
To complement its fibre services, Vocus is investing in LEO (low earth orbit) satellite-based telecommunications.
In 2021, Elon Musk’s company SpaceX launched its Starlink satellite internet in a beta phase to Australian customers. It has delivered higher download and upload speeds that outclass fixed wireless connections.
The technology was also hailed as a breakthrough for delivering internet to areas without fixed-line connections, a situation with which northern Australia has struggled.
Rather than relying on fixed cables, LEO technology will provide an internet connection anywhere the sky is visible. For mining companies, there is a strong value incentive to such a technology.
According to Ackland, mine sites have been deploying edge computing systems to enable more remote operational capabilities.
Edge computing is conducted on-site to deliver enough processing power to run remote operations across a mine operation.
The need for edge computing has grown during the COVID pandemic as more operations require remote access.
However, this can be costly, with Vocus’ “as a service” approach for satellite internet allowing mining companies to save costs and rely on the cloud rather than expensive edge technologies.
MINERAL EXPLORERS CONDUCTING DRILLING CAMPAIGNS CAN BENEFIT FROM STRONGER TELECOMMUNICATIONS CAPABILITIES.
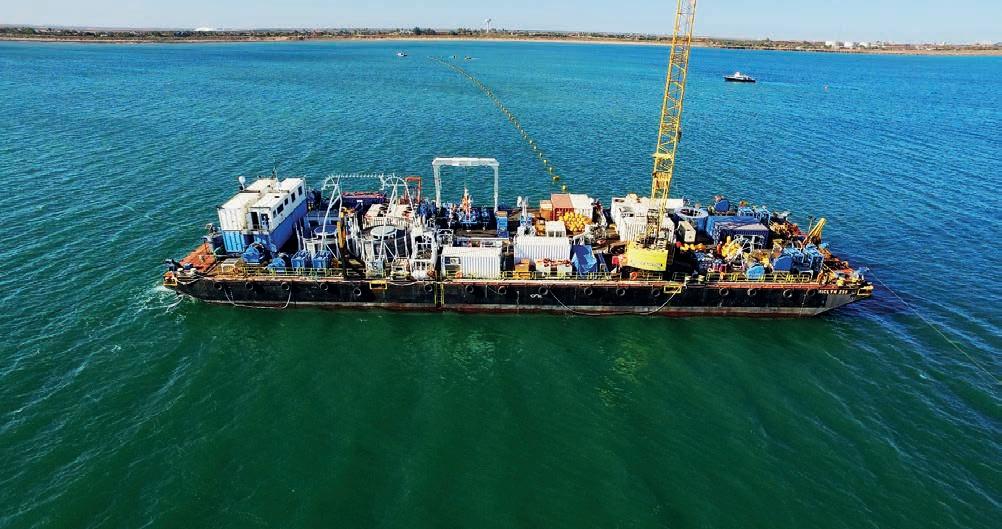
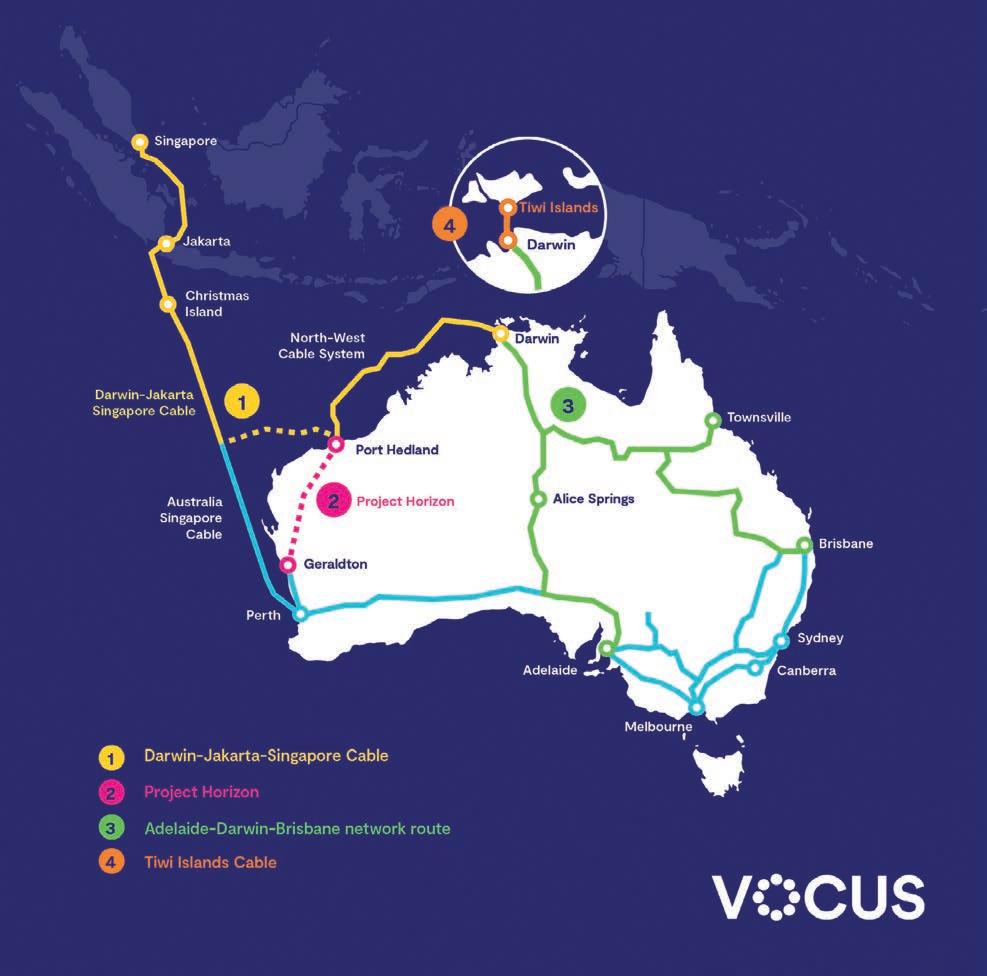
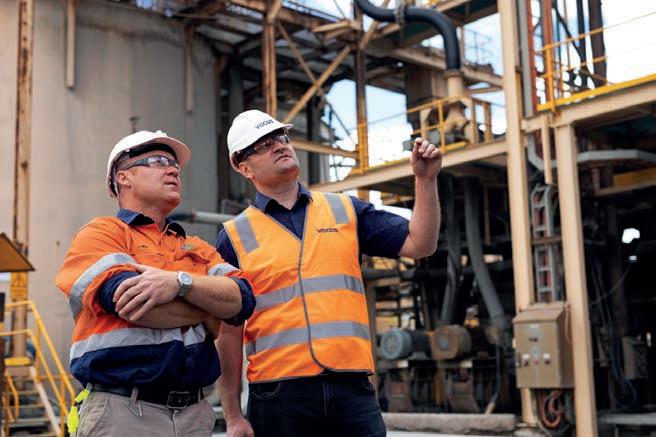
“We’ve seen a lot of emergency deployments of edge computing where people are putting server racks inside shipping containers and pumping energy into them to keep them cool,” Ackland said.
“From a mining perspective, you’ve got to have reliable low latency highspeed secure connectivity.
“Those are the keys to be able to move things away from the edge in terms of the amount of personnel you need to have in potentially high-risk situations – or indeed with COVID – moving people in and out has become more difficult, and the more it can be done remotely the more we can keep production running.”
Vocus’ vision for LEO satellites is for them to complement fibre infrastructure through satellite ground stations.
The company is a founding partner and shareholder in Australian-based and run Quasar Satellite Technologies, which will deliver the “ground stations as a service” offering.
“The fibre network that we’re deploying in WA is going to allow for the creation of satellite earth stations,” Ackland said.
“Those satellite earth stations are going to need to be within 500km of the point you’re trying to get communications.”
Ackland said the satellite ground stations need to be connected to fibre. For satellite providers, the industryfirst Quasar phased array antenna will allow multiple satellite companies to leverage the same ground station infrastructure.
By bringing Quasar’s technology together with Vocus’ fibre infrastructure projects, the company is preparing to provide mining companies with a reliable, stable and low-bandwidth connection. This will cut costs and deliver stable internet by preventing the need for bespoke ground infrastructure.
“What we’re seeing with LEO technology is improved connection to satellite services,” Ackland said.
“For mining companies, you could effectively pull this out of your truck, power it up and have the ability to feed data or have it analysed live through your connection to cloud.”
The next wave of mining operations will adopt more smart technology, including autonomous haulage and real-time analysis. Autonomous equipment relies on a strong internet connection to maintain full control over driverless vehicles at a mine site.
Even mineral explorers conducting drilling campaigns can benefit from stronger telecommunications capabilities.
Drilling campaigns usually rely on manually putting data on a hard drive for future analysis. But with border closures remaining a potential issue, LEO technology enables explorers to instead process drilling results in real-time.
The mining companies of the future also plan to take advantage of artificial intelligence (AI) and augmented reality (AR) technologies, which are becoming essential to more efficient maintenance practices along with off-site processing of drilling information.
“If you were conducting a drilling campaign with LEO technology you could have live feeds going back to data processing,” Ackland said.
“This allows for a far more real-time approach for where it is best to drill; that interactivity is going to lead to more accurate finds and more accurate campaigns.
“AI has the ability to compute vast amounts of information, such as analysing drilling data while you’re still out in the field, so you can imagine the benefits of doing that while mobilised, such as an improvement in the productivity of searching resources.”
Vocus is receiving strong backing from the mining industry for the installation of fibre networks and LEO technology. Companies are aware that this infrastructure will increase their ability to unlock more productivity and efficiency in some of Australia’s most significant mining regions.
Vocus’ network operations centres also feature a high level of security to ensure its services are safe, private and reliable.
“The bottom line here is that a lot of this operational technology that is being deployed, until now, has been almost exclusive to the bigger end of town,” Ackland said.
“A combination of LEO and fibre network competition is going to change the game for these junior miners.
“Things are about to get a lot cheaper in terms of their ability to access and leverage this technology and it is quite an exciting time in telecommunications development for mining sector.”
As the world evolves alongside technology, Vocus is working hard to connect remote areas of Australia to future opportunities through internet services that drive down costs and time. AM
VOCUS IS AIMING TO CONNECT PARTS OF WESTERN AUSTRALIA AND THE NORTHERN TERRITORY TO SINGAPORE WITH FIBRE CABLE. VOCUS IS IMPROVING CONNECTIVITY BY INSTALLING FIBRE NETWORKS.
ONE TECH PLATFORM CAN MAKE EACH BLAST SMARTER THAN THE LAST
AUSTMINE MEMBER HEXAGON MINING SHARES ITS INSIGHTS AND EXPERIENCE OF SMARTER DRILL AND BLAST PROCESSES.
MINEMEASURE PROVIDES ACCURATE BLAST INFORMATION THAT IS USED TO RECOVER ALL OF A MINE’S RESOURCES.
There are few certainties in mining, but reduced ore yield is all but guaranteed if errors are made at any stage of the complex, multi-layered, drill and blast (D&B) process. The potential for wasted energy, time, and opportunity costs business more now in an age of declining grades when miners are digging more earth for less ore.
In the mining cycle, D&B is arguably the first and most important step to get right.
D&B operations impact the entire mining process, from equipment efficiency through crushing and grinding circuit performance to recoveries and final-product quality. Costs and energy usage increase throughout the comminution process. Efforts targeted at optimising the blasting process can pay huge dividends downstream, reducing costs and energy consumption.
A correct blast not only optimises cost, but also improves the total cost profile of the entire mine. Correct fragmentation means easier digging, reduced shovel cycle times, reduced rework, less oversize causing downtime at the crusher, lower-cost crushing, and improved tonnes per hour (TPH) through the processing plant.
A continuous D&B feedback loop underpinned by technology not only increases the profit from every blast, but also increases a mine’s purchasing power over one of the most expensive parts of the process – explosives.
Hexagon’s MineMeasure is a tailored portfolio for D&B, improving yield, fragmentation, and dilution by combining blast design software, high-precision drills, blast movement monitoring, fragmentation analysis, and enterprise analytics.
From one platform, MineMeasure ensures data does its best work, empowering customers with a feedback loop, calibrated to increase profit from every blast. It’s a good example of Hexagon’s Power of One approach, a holistic, life-of-mine platform connecting sensors and software, infield apps and cloudware.
MineMeasure represents a scalable, platform-agnostic answer to challenges previously addressed by point solutions and multiple vendors. Here’s a closer look.
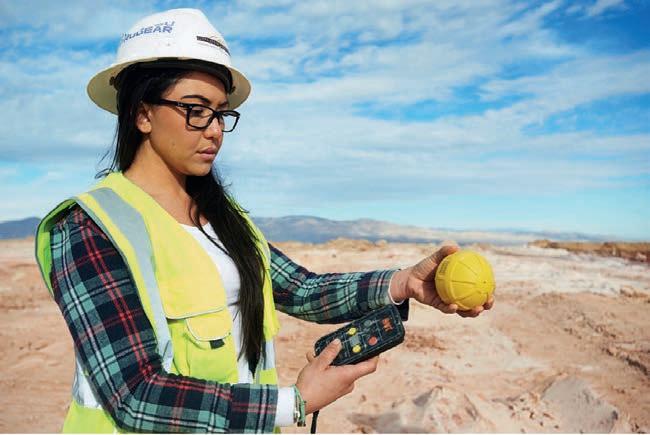
Blast design and high-precision drilling A well-designed blast pattern and the effective execution of the blast plan using high-precision drills are an important part of an effective D&B operation.
MineMeasure includes a comprehensive software utility for D&B and reconciliation. Rather than risking high-wall stability problems, uneven blasting, poor fragmentation, unnecessarily high energy costs, and dangerous working conditions, MineMeasure incorporates charge and blast design templates that are based on sound engineering principles and methods proven in mines worldwide.
The portfolio features machine guidance for drills (as well as dozers and loading equipment). This ensures that drilling is performed to the right position and elevation. It provides accuracy and instantaneous feedback, meaning improved loading times across the fleet, less mis-routed material, fewer hours of rework on ramps, roads, and benches, and fewer over- and under-drilled holes.
It is proven to improve both the quality of material produced and fragmentation with precise drillhole placement and depth.
Integration with Hexagon’s operational management hub means a single source of reporting and support.
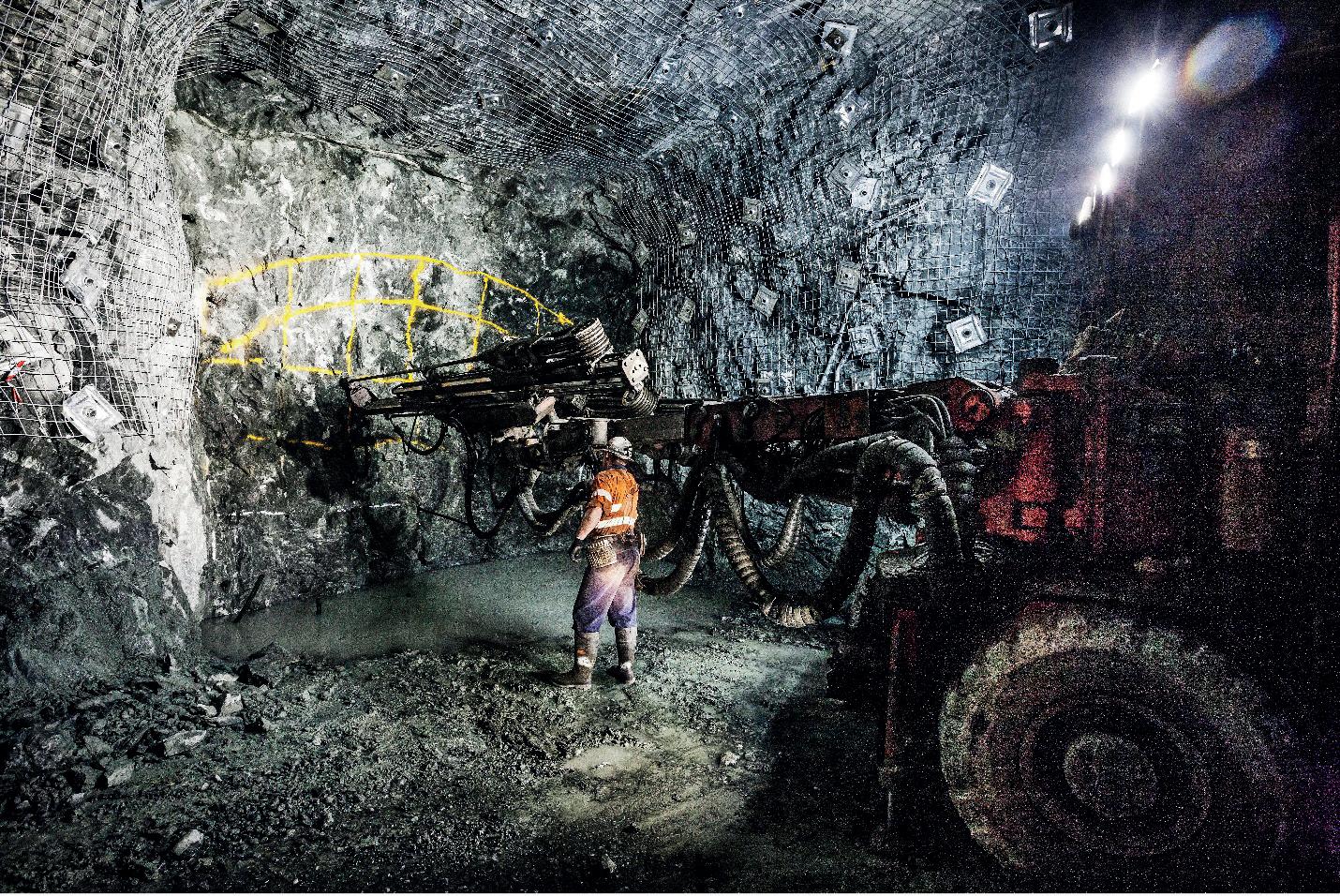
Blast movement monitoring, fragmentation analysis and blast optimisation Preparing for the D&B stage, mine operations have already spent significant amounts of money (running into the millions) to accurately locate the ore body and maximise the information known about the surrounding geology. Proven
fragmentation analysis and blast monitoring solutions minimise loss and dilution and deliver the data necessary for the next blast pattern design.
Acquired by Hexagon in 2020, Blast Movement Technologies (BMT) is an integral part of MineMeasure, providing accurate ore location information for open-pit mines. Via sensors and software, BMT provides accurate blast information that is used to recover all of a mine’s resources. It ensures that, post-blast, the mine retains a full vision of where its ore body moved to.
Hexagon’s Split Engineering systems are flexible and can monitor in different areas and process along with the operation automatically, such as in shovels, excavators, loaders, haul trucks, crushers, conveyor belts, mill feed and screen decks. The entire process can be connected from pit to plant for a unified approach to fragmentation management.
Monitoring trends in size at each point in the comminution circuit enables operational adjustments in real time. Alarms can be created for oversize events, reducing the downtime from inefficiencies caused by blockages and broken screen decks.
Precision drilling underground In January 2022, Hexagon acquired Minnovare, a leading provider of drilling technology that improves the speed, cost and accuracy of underground drilling.
Minnovare specialises in eliminating the manual, labour-intensive, and unproductive processes in underground mining that lead to blast-hole deviation, dilution, and downtime. Its advanced hardware and data-capture software combine to deliver drill-data faster and more accurately than ever before, improving the efficiency, productivity and overall profitability of underground drilling operations. Its solutions combine sensors, software and data analytics to address deficiencies in existing drilling processes across the resource definition, development and production phases.
The acquisition will enhance MineMeasure and accelerate Hexagon’s underground development roadmap.
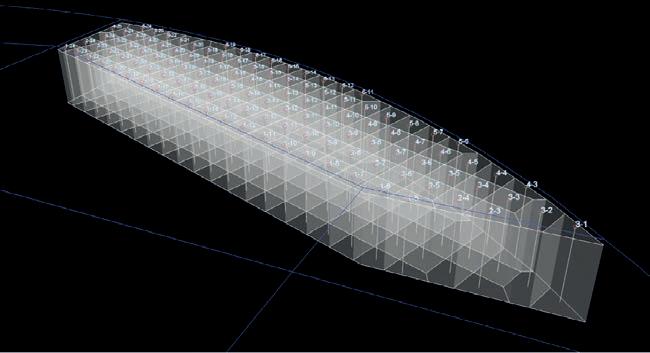
A uniquely holistic approach The ability to tailor fragmentation outcomes and to minimise ore loss and dilutions through blast movement monitoring are proving to be highly sought after. This uniquely holistic view of the operation combines key knowledge banks, such as geology behavior, effects on powder factor, blast design, planning and fleet management.
MineMeasure’s comprehensive D&B approach delivers the power to improve the most vital part of the mine, where everything starts with the drill and blast, without losing purchasing power over the bulk commodity blasting material.
All from a single technology vendor. That’s the Power of One. AM
“DRILL TO MILL” AND “PIT TO PLANT” ARE DECEPTIVELY SIMPLE DESCRIPTIONS FOR COMPLEX PROCESSES. MINEMEASURE INCORPORATES CHARGE AND BLAST DESIGN TEMPLATES.
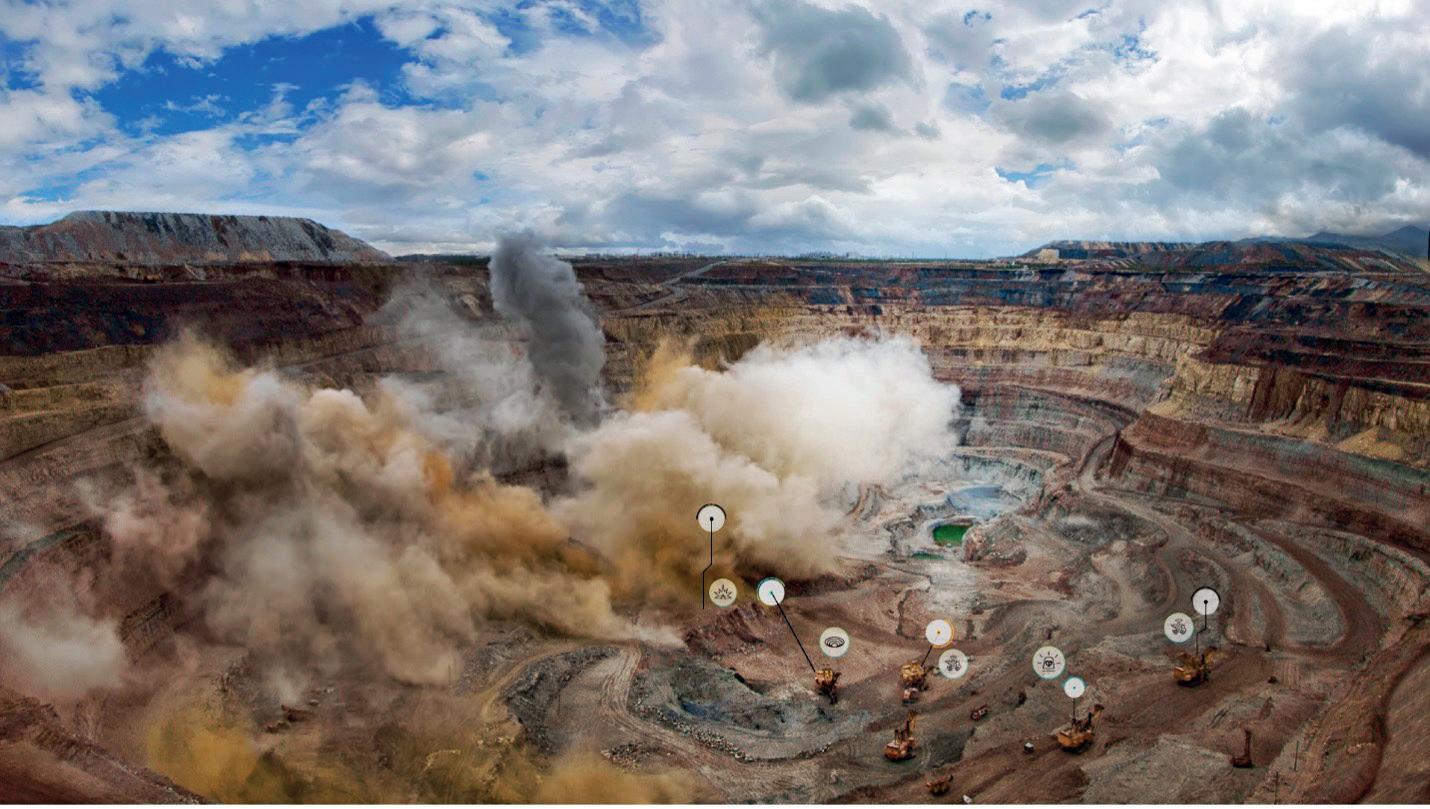
1988
Industrial Flotation Specialists
Custom designed and manufactured to suit your requirements
SINCE 1988
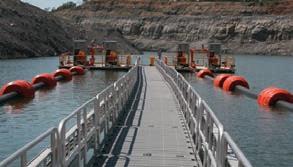
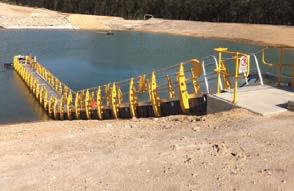
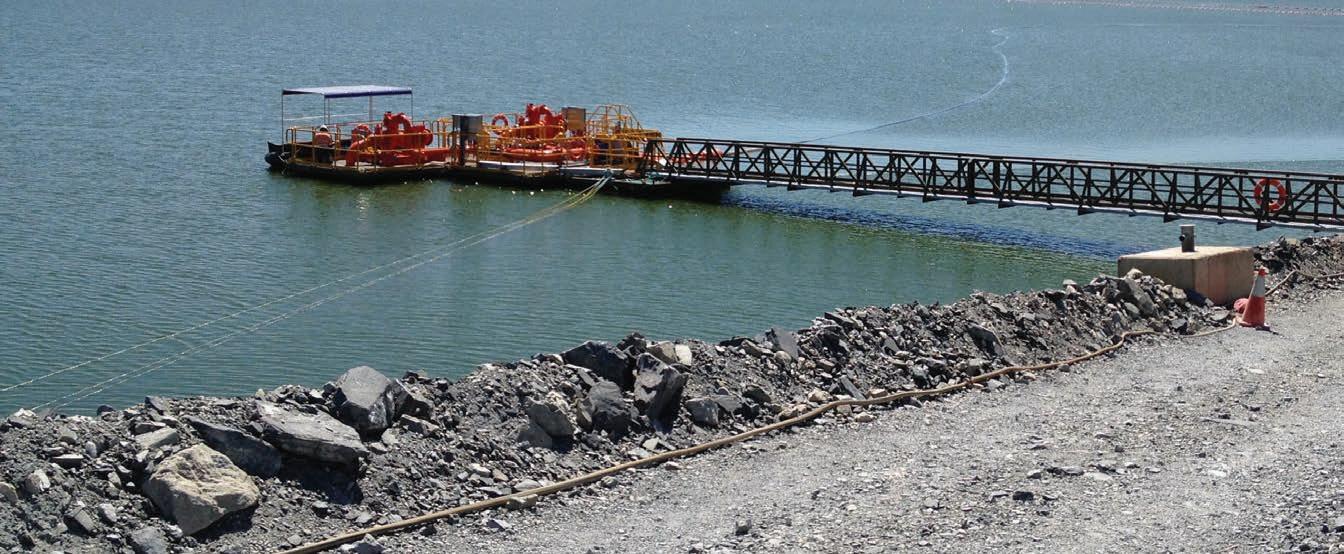
Pump Pontoons Pipe Floats Floating Walkways
All products manufactured in Australia Suppliers to the global major mining
companies & contractors
Aluminium gangway specialists Modular systems for easy installation 100% virgin PE materials used for
maximum UV protection and long life
Broad selection of products to suit all
mining applications
WORKING AS ONE ENTITY FOR ALL CUSTOMERS
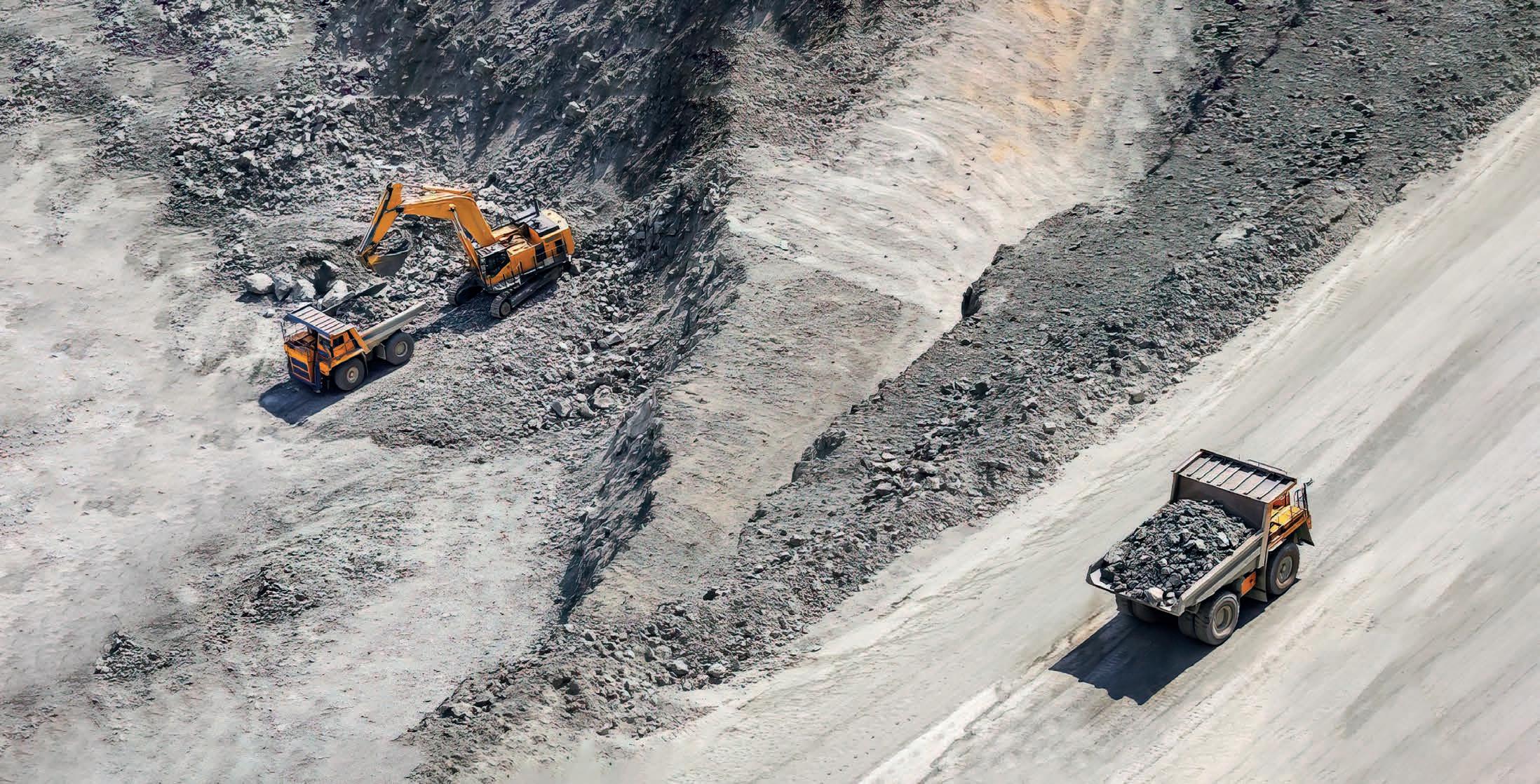
‘ONE MOTION’ AUSTRALIA HAS EXPANDED ITS SERVICE OFFERING FOR HEAVY INDUSTRY.
Mines, quarries, and other businesses in the heavy-industry sector are set to reap the benefits of Motion Australia consolidating all of its subsidiary businesses into a single entity.
According to national sales manager Grant Gray, the company arrived at this full-circle solution after engaging in important conversations with key suppliers and customers.
“Customers were saying to us, ‘We love dealing with you but is there any way we can deal with you as one entity?’” he said.
“This prompted us to begin exploring ways that we could mature our business and drive home our desire to streamline our services and foster an ease of doing business.
“This is a very exciting time for us as a business and for our customers; in fact, we are already having conversations about how this broader offering under the one business group will be of benefit to them.
“For example, if a customer is looking for bearings and transmission solutions at one of our BSC or CBC locations, they can now also enquire about more advanced industrial solutions such as fluid transfer, hose fittings and connections through our other businesses like Hardy Spicer, CRAM and AIP.”
These iconic brands have come together under Motion Australia to create a wholly-owned general parts company. Customers in Australian mining and quarrying sectors now have unmatched coverage of products and services, with access to over 600,000 unique parts from more than 2300 world-class suppliers around the globe.
“From a mining and quarrying perspective, we are often dealing with critical deadlines, expensive pieces of machinery and remote harsh conditions,” Gray said.
“Particularly on younger mining and quarrying operations, we are looking to understand what their critical parts are by looking at ways that we can extend the life of these components and support their needs surrounding stock, inventory, supply chain, and logistics in the current market climate.
“With the transition to One Motion, we want to harness our mechanical and hydraulic engineering expertise by ensuring we have accredited inhouse capabilities, which include rigging, hydraulic sealing, hose manufacturing, seal refurbishments and fully equipped workshops for manufacturing, repairs, welding, fabrication, and design,’ Gray said.
“We have a fantastic offering as a larger entity, and we back it up with a very strong workforce and we want to align ourselves with other businesses that have a fantastic footprint by focusing on three key criteria: maintaining the largest stock holding, the largest national footprint, and the largest technical workforce in the country.”
While Australian mining operations are considered highly efficient, the cost of production and variable commodity prices still present unique challenges to the market, according to Motion Australia technical manager of strategic partnerships Ross Lee.
“Mining applications present the most punishing operating conditions for products in Motion Australia’s scope such as bearings, shaft seals, power transmission drive units, fluid power systems, hydraulic
WITH THE MOVE TO ONE MOTION, THE COMPANY WANTS TO HARNESS ITS EXPERTISE ACROSS THE VARIOUS ASPECTS OR MINING AND OTHER HEAVY INDUSTRIES. cylinders seals, hoses, and driveshaft assemblies,” Lee said.
“As we continue to expand our capabilities in these products and services, we are also focusing on more advanced ways to avert downtime and maximise production continuity, crucial to our customers’ bottom-line results.”
A few of these ways, according to Lee, are an increased focus on predictive maintenance and remote condition-monitoring of machine health, application of best and safest practices for maintenance procedures, and utilising the latest in machinery component technologies.
“Beyond supporting the supply of quality industrial products, Motion Australia’s service scope looks to address the unsatisfactory service life of equipment components by employing countermeasures such as improved part capability, engineering design analysis, and best practices for mounting, installation and adjustment,” Lee said.
“This also encompasses optimising lubrication procedures and providing frontline sealing protection for machinery modules exposed to harsh operating environments. Plus rapid response services in the event of equipment breakdown.”
Motion Australia is consulted on a wide range of mining and quarrying equipment operating issues every year, which continuously adds to the company’s application-problem knowledge base for utilisation across their nationwide technical support network.
On- and off-site, maintenance support services represent a key aspect of the company’s expanding level of frontline support to the mining and quarrying industries.
“The challenges we are seeing now in these industries are uncertainty surrounding supply chain, transport and logistics, as well as demands around inventory,” Gray said.
“We are still currently seeing some shortages globally, so our aim is to help supply align with demands in production right now.
“We will achieve this by offering more comprehensive programs and increased efficiencies, ranging from cost savings to automated inventory management solutions to asset management. This will happen by leveraging our technology, expertise and the established processes we bring to the table as a larger organisation.
“If you look at the multitude of businesses out there, it’s all about ensuring that you have the bandwidth of offerings and we are pleased to be able to say that we do,” Gray said.
“These industries are not new to us, and our businesses are not new to our customers. Many of our businesses are long-term entrenched companies that have been doing what they do for more than 100 years.
“So, you know, this is not our first rodeo.”
Motion employs more 60 expertlevel engineers around Australia, each with their own specific skill set in their field.
“Our team has extensive practical experience and knowledge, and they truly excel talking directly with end users on-site to understand every individual application and how to achieve the best outcomes for each one,” Gray said.
The changes customers can expect to see as these internal industrial solutions businesses transition to a single entity are many and varied. But there is one key area of growth that is certain: customer relationships.
“Now we can approach the customers that we have built up a level of trust and transparency with over a long period of time and start to have a dialogue about what other offerings we have as a company,” Gray said.
“Already having these relationships established lays the groundwork for us and makes the job a little bit easier. But, above all else, we want our customers to feel comfortable to come and talk to us about what’s next.” AM
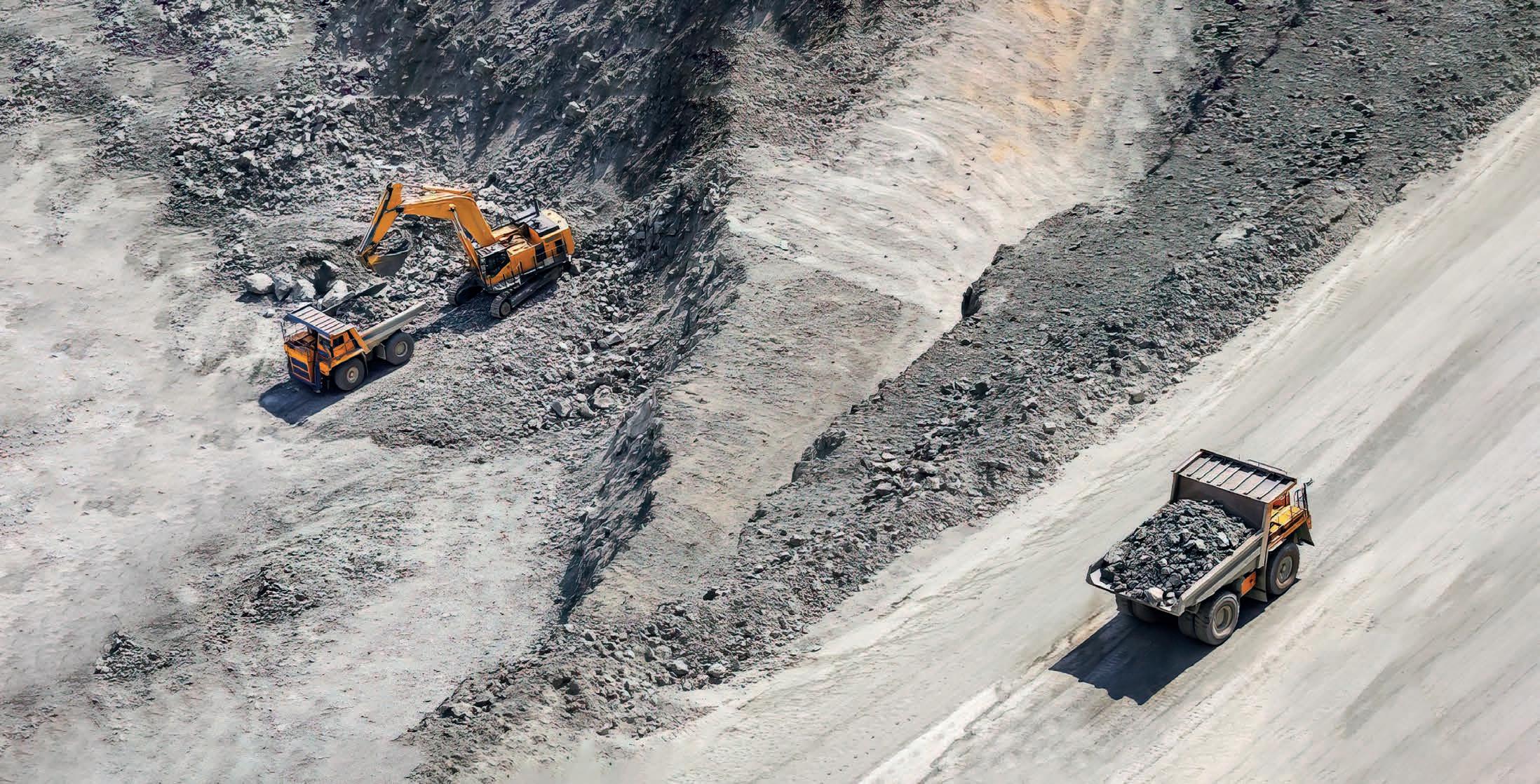
Experience the Power of Red
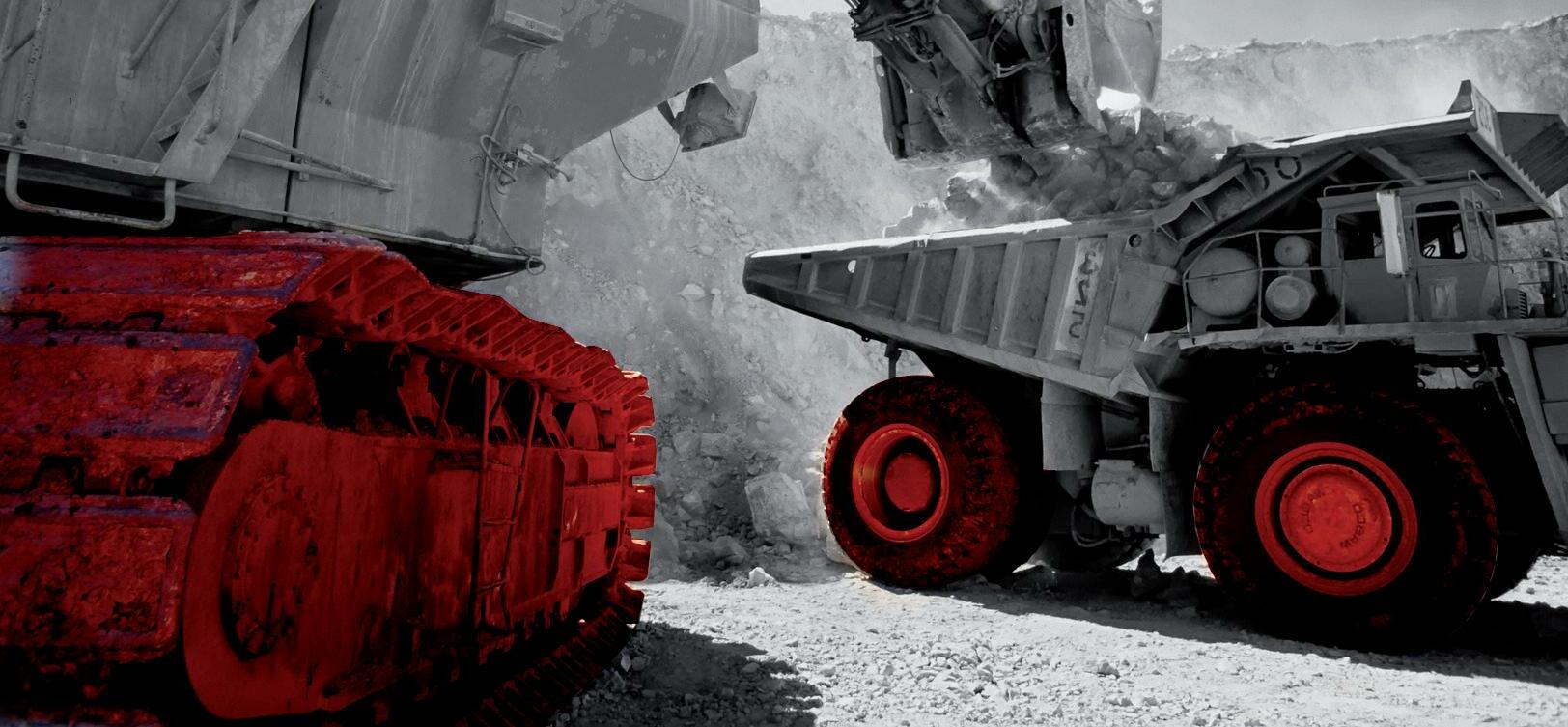
www.cpcompressors.com.au 1300 555 284 YouTube-LinkedIn-Facebook
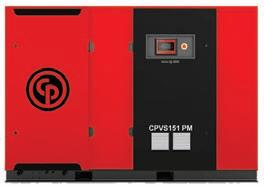