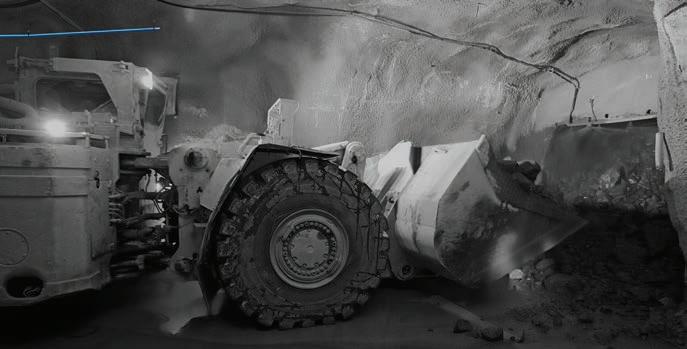
6 minute read
TECHNOLOGY
THE MISSING LINK IN MINING’S INDUSTRIAL NETWORKS
THIS SPECIALIST IN INDUSTRIAL NETWORKING AND CYBERSECURITY IS FAST BECOMING THE GO-TO PROVIDER FOR MINING NETWORK SOLUTIONS. WHERE PREVIOUS APPROACHES COULD BE FLAWED AND CONFUSING, VERNETZEN OFFERS A STRAIGHT LINE TO SUCCESS.
To effectively serve the mining market, it’s key to assess the current holes in traditional systems. Vernetzen does just that, as it brings together all the departments, solutions and ingredients for connectivity in a mining application.
With a background in consulting, Vernetzen has grown to understand the needs of its major mining clients, while providing the technical expertise required to find effective solutions to common or unique network pitfalls.
Vernetzen managing director Luke King exemplifies how his company turns technical topics into digestible results.
“We’ve been transitioning to a product-based business because we’ve seen that the current approach to network infrastructure in mining was just enterprise surface network techniques applied in these harsh environments,” King tells Australian Mining.
“Those traditional approaches require a lot of integration and a lot of trial and error to bring that solution together because you’ve got all these different departments and projects which aren’t talking to each other about a solution.
“Ours is a full turnkey solution which addresses everything from design through to operations support.”
Vernetzen serves some of the world’s largest resource companies with a focus on linear networks – the kind most suited to a haul road-like context.
This linear Wi-Fi network uses leaky feeder, Wi-Fi and a number of other network technologies to distribute the connection over a long distance, King explains.
“It’s a cable we run through tunnels or beside haul roads which leak the coverage out across a linear distance. Our cable is specified to support up to 500 metres of coverage – 250 metres in either direction of the appliance,” he says.
“Basically, the antenna on a truck is not far from the cable at any one point and that’s why we can achieve these large distances without worrying about the angulation or change in a mine or haul road.”
Vernetzen brings both data and electrical networking together to allow its customers to rely on one port-of-call.
Just as voice and data networks have merged in the enterprise space, King expects the industrial space to see a trend where data and electrical networks merge into one offering. Vernetzen has simply moved ahead of the curve.
“What this provides is visibility over utilisation of electrical networks – understanding what the loads are and what’s being attached – and data networking, to understand the connectivity of bandwidth and throughput,” King says.
“Over 80 per cent of outages are due to power so it’s important to have visibility of both of these systems.”
Without a concurrent understanding of both these networks, operations can leave themselves vulnerable to failure or longer wait times for technical support to assess the situation.
Vernetzen realises, however, that visibility and the ability to monitor operations is important to all levels of a mining company.
“In the underground environment, this could serve everyone from technicians that are being told where there’s coverage issues to be fixed,” King says.
“It serves remote operations who’ll have all the data to understand capacities and performance levels.
“And also, management will be given a high-level view over the general operations to understand what the availability is, what the up-time is, what the biggest problems are.”
These monitoring issues extend into cybersecurity and King addresses the rise in concern on the topic.
It takes more than just a hobbyist to tackle cyber security in a mining environment. When a range of other new technologies are at risk, any miner would want to know their lives and jobs are in safe hands.
“You can’t just have someone who broadly knows what they’re looking for, you need someone who understands the business, the threats, the type of bad actors that could potentially be involved in a mining situation,” King says.
“We’re building that capability and we see it as a high-growth area as mining starts to rely on more automation where you need cybersecurity and that domain expertise.”
The final piece of the puzzle is for operations to realise how integral effective industrial network solutions really are.
“It’s hard for a project team to justify the funds for a good network, but when you tie into it the criticality of all these systems like vehicle automation, ventilation and all these new technologies, networks are not just enabling them but they’re absolutely critical to the operations,” King says.
“This criticality is going to increase going forward and it’s really important that an adequate investment is put towards it.” AM
VERNETZEN’S LINEAR NETWORK SOLUTIONS ARE PLACED ALONG ROADS IN UNDERGROUND MINES. VERNETZEN’S TURNKEY SOLUTION BRINGS TOGETHER MULTIPLE DEPARTMENTS, STREAMLINING INSTALLATION AND MAINTENANCE.
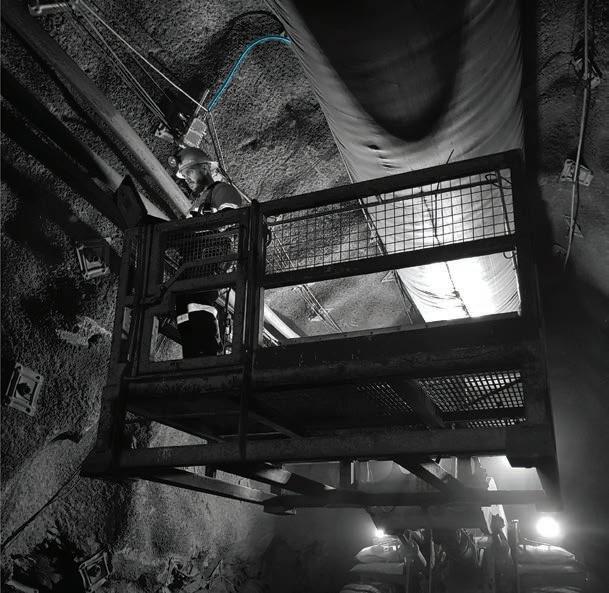
New oil-injected screw compressor for the mining industry - Now that’s something to smile about!
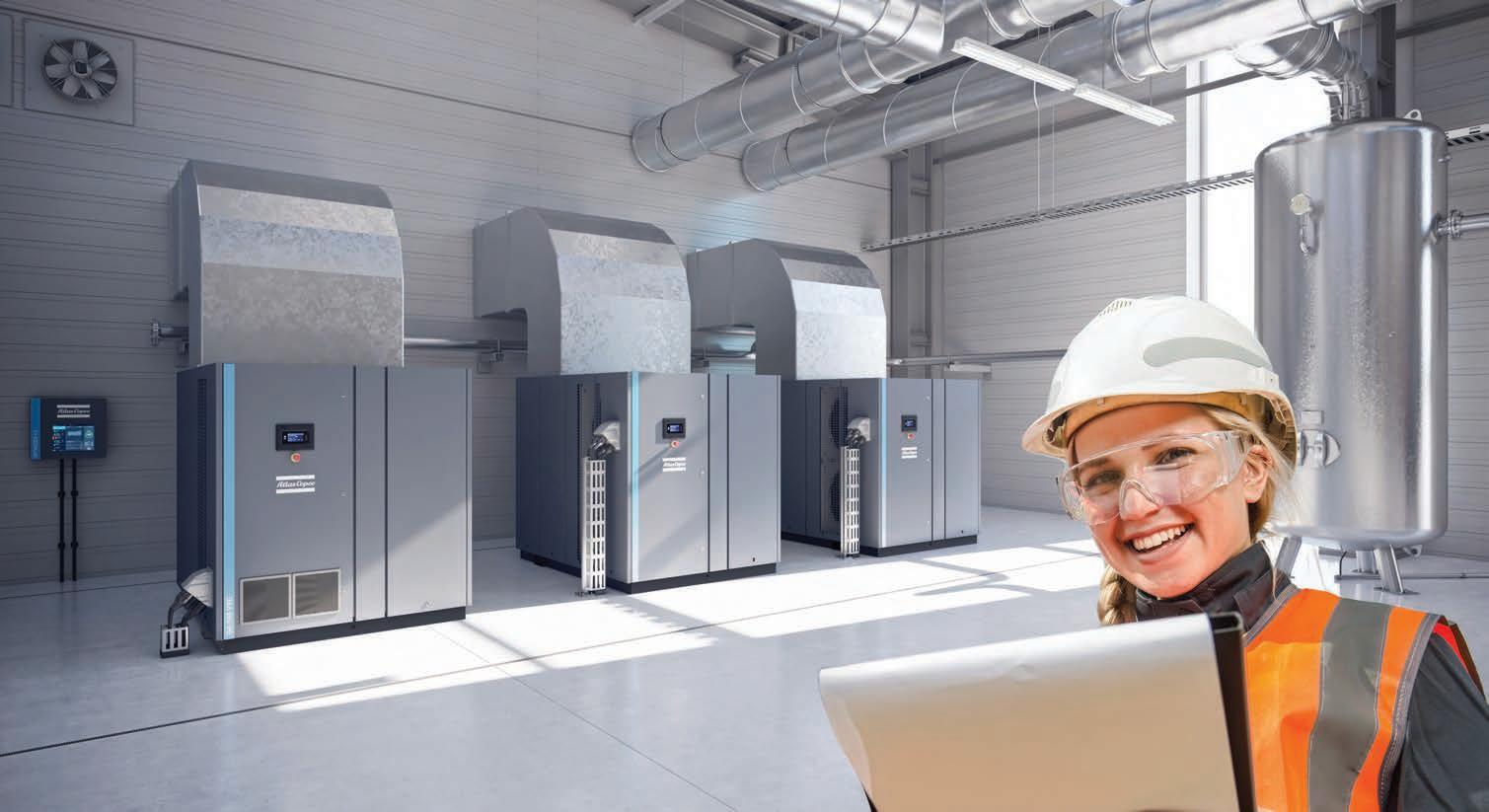
The most compact, efficient, reliable and serviceable oil-injected 90-160kW compressors in the market for our tough Australian mining conditions.
Innovation is in our DNA
The new design of the GA90 to 160 focuses on three key areas: Reliability, Efficiency and
Serviceability.
With innovations like the new superefficient screw element, sealed IP66 Oil Cooled motors with efficiency exceeding IE4 rating, oil forced lubricated bearings, split oil system, smart oil injection in the element and the latest generation Elektronikon MK5s Touch controller, Atlas Copco has created the ultimate compressor for mining
applications.
Reliability
The sealed oil cooled motors have no need for any service intervention. They also don’t need any external cooling air. The complete drive train is rated IP66 so there is no chance of any water or dust reaching internal components, enhancing the reliability of the compressor in extremely tough conditions.
The split oil system for the oil forced lubricated bearings guarantees oil at the best condition and temperature and increases the reliability of the bearings at the maximum. Another feature of the compressor is its reduced number of components, such as the new patented oil stop valve & unloader, which also serves to enhance the compressor’s overall reliability.
The latest generation Elektronikon MK5s Touch Controller, reflecting the latest in Atlas Copco know-how, monitors key parameters to ensure the compressor is operating reliably. If any issue is detected it is able to communicate with our service organisation and the final customer before any downtime occurs.
Efficiency
The compressor drive train, based in the new oil injected rotary screw element, is the most efficient in the market. The compressor’s oil cooled motors have efficiencies that meet or exceed IE4 requirements.
In addition to the super-efficient drive train, we have incorporated an oil smart injection system into the element. This ensures the right amount of oil inside the compression chamber, thereby avoiding excess oil use and improving the compressor efficiency.
Serviceability
Six key areas that influence the maintenance of the compressor were addressed during the design stage resulting in 50% reduction in time spent on servicing the compressor.
The modular oil separator registered under the Australian AS1210, a new minimum pressure valve, the integrated patented oil stop valve & unloader, the location of the thermostats and oil filters, the pressurised oil draining process, and the IP66 drive train make it possible to have this reduced service time against other traditional compressors in the market.
Atlas Copco New GA90 to 160 kW Oil Injected Screw Compressors, the most
efficient, reliable, and service friendly
compressor in the market!
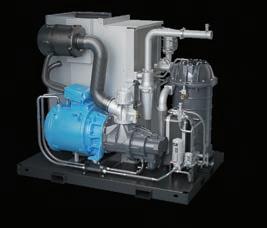