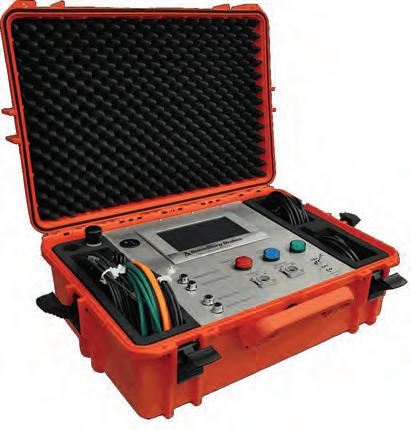
27 minute read
DIGITAL MINING
BACK IN CONTROL
SVENDBORG, AN ALTRA INDUSTRIAL MOTION BRAND, HAS DEVELOPED A CASE THAT ENABLES ITS EXPERTS TO COMMISSION CONVEYOR BRAKES FROM THEIR DESKS.
THE UCCASE CAN BE DEPLOYED GLOBALLY FOR USE BY ALTRA MOTION TECHNICIANS.
THE UCCASE IS COMPACT AND CAN SUPPORT HIGH-QUALITY BRAKE COMMISSIONING.
The COVID-19 pandemic has thrown a spanner into maintenance and installation plans across conveyor sites, as new safety restrictions limit who can attend a site.
This created a conundrum for Altra Motion, which would typically support its customers with face-toface commissioning.
The company’s Svendborg Brakes experts – often the same people who have written the SOBO (soft braking option) software – ensure the company provides the best service quality possible.
COVID-19 and mobility restrictions threatened this capability, which is why it developed the Universal Control Case (UCCase). The case is a smart technology service tool that enables the remote monitoring of product performance and can help provide insights for maintenance assessment.
Importantly, it allows remote support on standard and SOBO Svendborg Brakes during commissioning and service.
Svendborg Brakes UCCase project manager Christoffer Bjerremand says the case is simple to hook up, requires no training and can be done by following instructions in the manual.
“We can send the case to a customer; they connect it to the SOBO PLC and use their phone to connect it to the internet,” he says.
“From there, the sensor sends signals to the cloud, and our team of specialists can take over, using complex algorithms to troubleshoot any faults in the system.”
Altra Motion Australia’s experts, through the UCCase, can diagnose brake system behaviour with analytical models, which they can use to provide advice on which actions to take to prevent a malfunction.
It has already proved immensely useful. For example, in 2020, a customer in Belarus needed support for commissioning. However, due to COVID-19 restrictions and political instability, it wasn’t easy to arrange for a technician to visit the site.
Bjerremand says the project was extensive and couldn’t afford to wait, so Svendborg sent the UCCase.
“Instead of our technician being there, he was at his desk while the customer’s on-site technician used the case to give us remote access,” he says.
The technology has been designed to be backwards compatible and can even work with SOBO units that are decades old.
A drilling ship had a 20-yearold SOBO system that needed planned maintenance at a harbour in Italy. Unfortunately, the customer uninstalled the old system, and a technician was supposed to arrive on site to reinstall a new one.
Bjerremand says any drillship in downtime is a costly exercise and should be avoided.
“During COVID, we could not travel but it was only going to be in port for only so long. So, because we only had a short window of time to act, we hired out the UCCase for one of their service technicians to operate,” he says.
“Our engineer stayed in close connection with the customer’s local service technician and was able to remotely monitor the situation and guide him on site to reinstall the old SOBO.
“The data from the UCCase showed that the valves of the hydraulic unit were worn out and needed replacing.”
After the successful remote service check-up, the customer replaced its SOBO system with the latest IQ version. This version can be permanently connected to a Svendborg Brakes cloud, making it possible to constantly measure the behaviour of the brake system and avoid unexpected downtime.
Svendborg Brakes plans to continue developing the case and adding new functionalities, such as an integrated computer running a local cloud. This would allow the case to function independently from the internet in areas such as mine shafts with a poor internet connection.
Altra Industrial Motion’s UCCases are available and ready to support this remote IIoT (industrial internet of things) technology to Australian and Oceanic customers for commissioning, predictive and preventative maintenance. AM
SVENDBORG’S SOBO IQ SYSTEM
The SOBO IQ is a closed loopcontrolled system that gives operators constant stopping times and distances. It acts on the gear drives, applying a torque based on the stopping time irrespective of the loads on the conveyor to stop it in a controlled manner. Using a speed reference signal taken from the coupling bolts and a pressure feedback loop, the SOBO IQ can accurately predict what the braking system needs to stop the conveyor. Stopping too hard can cause the material to spill or damage to the belt itself, often one of the most expensive pieces of equipment. The SOBO avoids potential flowon effects, such as blocked chute overflows and gives operators greater control over how the equipment will work. The SOBO control system has a backup that will kick in even if there is a complete loss of power resulting in a safe controlled stop.
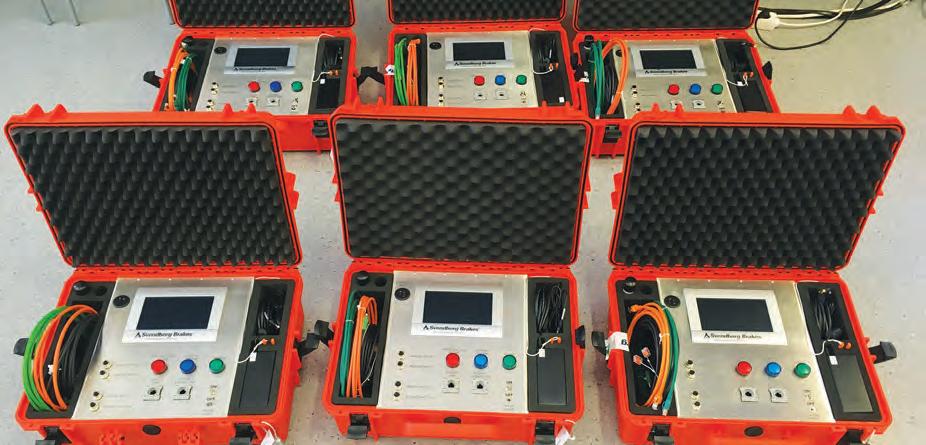
LAUNCHING MINING COMMUNICATIONS INTO ORBIT
VOCUS IS PIONEERING AN INNOVATIVE SATELLITE-BASED TELECOMMUNICATIONS SOLUTION THAT WILL ALLOW MORE MINING COMPANIES TO ACCESS DATA-DRIVEN TECHNOLOGIES.
Mining technology is advancing at a rapid pace and key drivers in this are high-capacity connectivity and the development of cloudbased services.
These can influence things from sensors on critical plant and equipment to full-fledged automated mines that are controlled from control centres thousands of kilometres away.
The engine room of these technologies depends on a reliable and fast data connection, which consumerbased internet cannot sustain.
While some form of connectivity might be available in remote regions, high latency and low speeds can disrupt real-time automation or monitoring capabilities.
For example, a poor data connection can cause automated machinery to not respond to command inputs.
Until now, the most effective means of mining companies improving their connection is developing costly telecommunications infrastructure, which can cause unwanted capital expenditure.
Yet the rise of satellite telecommunications has started to plant the seeds needed to revolutionise the mining sector’s connectivity.
“Latency makes a big difference in terms of what applications you can provide or use,” Vocus national general manager government and special projects Michael Ackland tells Australian Mining.
“We’re all familiar being with a low or high latency link just trying to make a phone call and understanding convenience with that.”
Vocus is eyeing the opportunity for miners to invest in LEO (low earth orbit) satellite-based telecommunications to gain low latency internet connections in regional areas.
LEO satellite technology consists of large constellations of small satellites that orbit the Earth, which in turn deliver a reliable internet connection in the remotest parts of the world.
“The big improvement from satellite access that comes from LEO is latency,” Ackland says. “By reducing 200- to 300-millisecond latency to 20- to 40-millisecond latency, a whole new range of applications are available.”
Elon Musk’s company, SpaceX, launched its Starlink internet service which uses LEO technology in Australia this year.
This has been particularly important for regions of Australia that lack robust internet access. It also cuts costs for users by offering a wireless alternative to a fixed-line connection.
“Starlink shows there is new and easy deployment coming with this technology in a much easier way than traditional technology,” Ackland says.
“It opens up a lot more possibilities for how satellites can be used for productivity. It can be more agile, and of course with lower latency people have previously not thought of using with geostational satellite technology.”
Vocus aims to adopt an ‘as a service’ approach to satellite internet to prevent the need for mining companies to empty their pockets on telecommunications infrastructure.
The telecommunications company has become a founding partner and shareholder of Quasar Satellite
Technologies, which is an Australian-based and run company that will provide ground station arrays as a service.
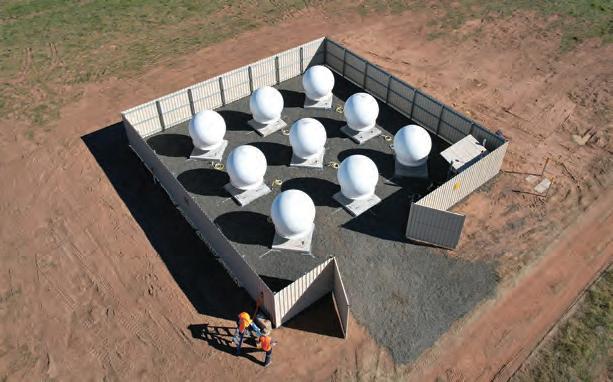
LEO GROUND STATION UNDER CONSTRUCTION WITH ANTENNAS.
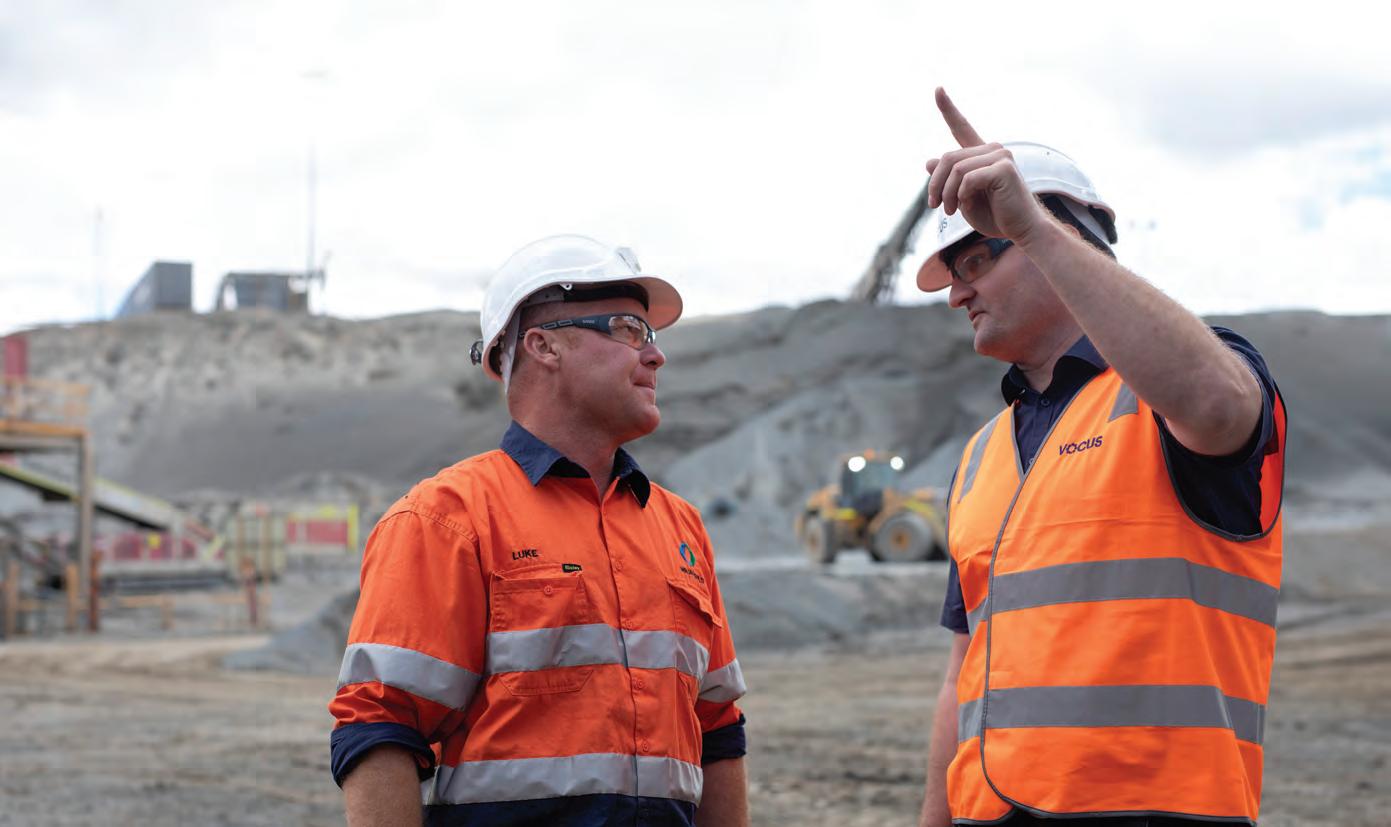
According to Ackland, the satellite ground stations will be connected to Vocus’ fibre network and will allow multiple satellite companies to leverage the service.
Northern Australia, which is home to some of Australia’s largest mining operations, lacks the fibre internet infrastructure enjoyed by the eastern side of the country.
To solve this issue, Vocus is developing its Darwin-JakartaSingapore Cable to enable mining companies a world-class fibre connection to connect their infrastructure to Singapore via a much more direct route.
This alone will improve latency and drive down costs, while also unlocking the capabilities of the satellite ground stations.
“The fibre network that we’re deploying in Western Australia is going to allow for the creation of satellite earth stations,” Ackland says. “Those satellite earth stations are going to need to be within 500 kilometres of the point you’re trying to get communications.
“The concept of a shared ground station is nothing new but the technology being used here, which is phased array antenna, is a first.
“This allows for a ground station to not have rotating dishes which you see traditionally. It instead is a flat panel that doesn’t move but can track moving satellites across the sky.”
With the next generation of mining operations expected to adopt more smart technology, a strong data connection will be needed to maintain control over large-scale autonomous haulage and real-time diagnostic solutions.
Mining companies are also gradually taking advantage of artificial intelligence (AI) and augmented reality (AR) technologies to gain an edge in productivity through more reliable maintenance and data access from off site.
LEO satellite technology will allow entire processes for mining companies to be revolutionised with more efficient and convenient alternatives.
“A drilling campaign previously took data and put it on a hard drive and put it back or trickle feed it back to a mobile satellite service,” Ackland says. “If you were conducting a drilling campaign with LEO technology, you could instead have live feeds going back to data processing, which is going to lead to more accurate finds and more accurate campaigns.
“AI has the ability to compute vast amounts of information, such as analysing drilling data while you’re still out in the field, so you can imagine the benefits of doing that while mobilised, such as an improvement in the productivity of searching resources.”
Through the implementation of satellite ground stations, Vocus can tap into markets that previously couldn’t access its services – particularly those in regional areas.
The company has also received strong support from the mining industry for the installation of these technologies, which will allow them to easily access and transfer data from remote areas.
“To get a low latency link even to a small mine at the moment is still quite a cost intensive prospect in many areas,” Ackland says.
“It’s more or less on industry to support communication services investments and this technology allows for that to be aggregated.”
By providing mines with more access to a reliable, stable and low-bandwidth connection, operations will be able to grasp the full capabilities of their digital transformation.
“Things are about to get a lot cheaper in terms of their ability to access and leverage this technology – it is quite an exciting time in telecommunications development for the mining sector,” Ackland concludes. AM
LEO GROUND STATION ANTENNA BEING DELIVERED.
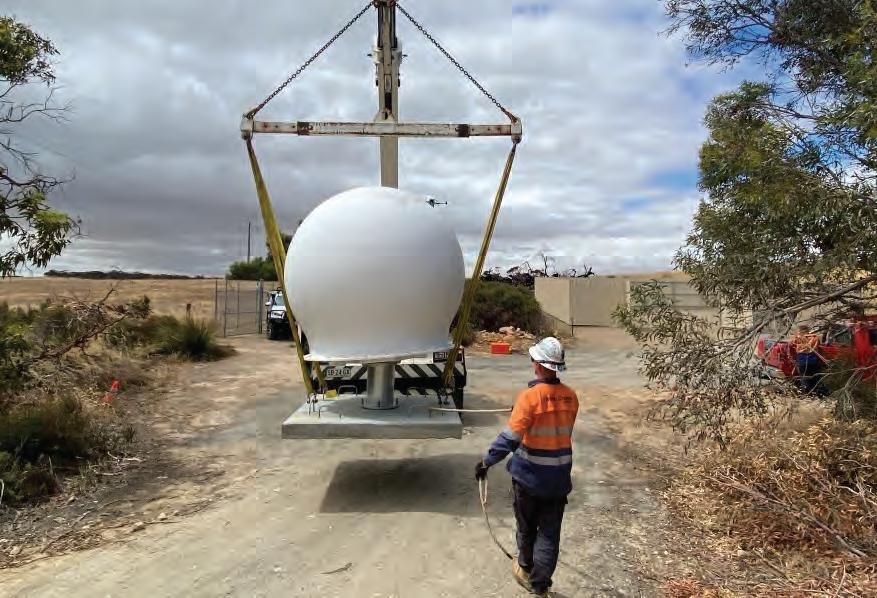
BELT CONVEYOR SERVICES...
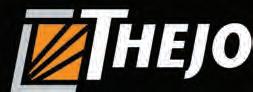
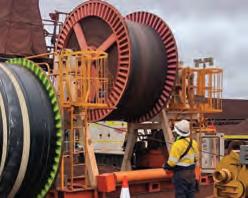
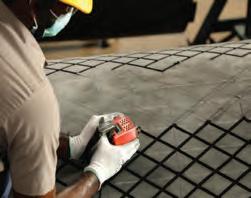
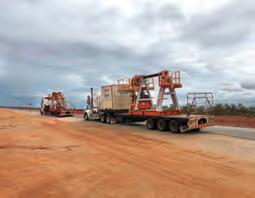
Conveyor Belt Repair Belt Replacement Pulley Lagging Project Execution
• Belt Splicing & Repair (Fabric Ply, Steel Cord) • Belt Splicing (By cold & hot Process) • Longitudinal Rip Repairs • Belt recapping • Replacement of damaged or old belt conveyors • Lagging insitu cold process • Autoclave hot process • Ceramic Lagging • Belt Changeover • Belt Laying • Belt Splicing • Belt training & commissioning
Corporate Office: 41, Cathedral Road, 3rd Floor, Chennai -600014, Email: marketing@thejo-engg.com Australia:240 Barrington Street, Bibra Lake, WA 6163, Email: thejo@thejoaustralia.com website: www.thejo-engg.com
THE FUTURE OF MINING IS DIGITISATION
AS THE MINING INDUSTRY EMBRACES NEW TECHNOLOGIES TO IMPROVE PRODUCTIVITY, THE SECTOR IS STARTING TO THINK DIFFERENTLY ABOUT ITS APPROACH TO DIGITISATION AND AUTOMATION. MICHAEL PHILIPPS WRITES.
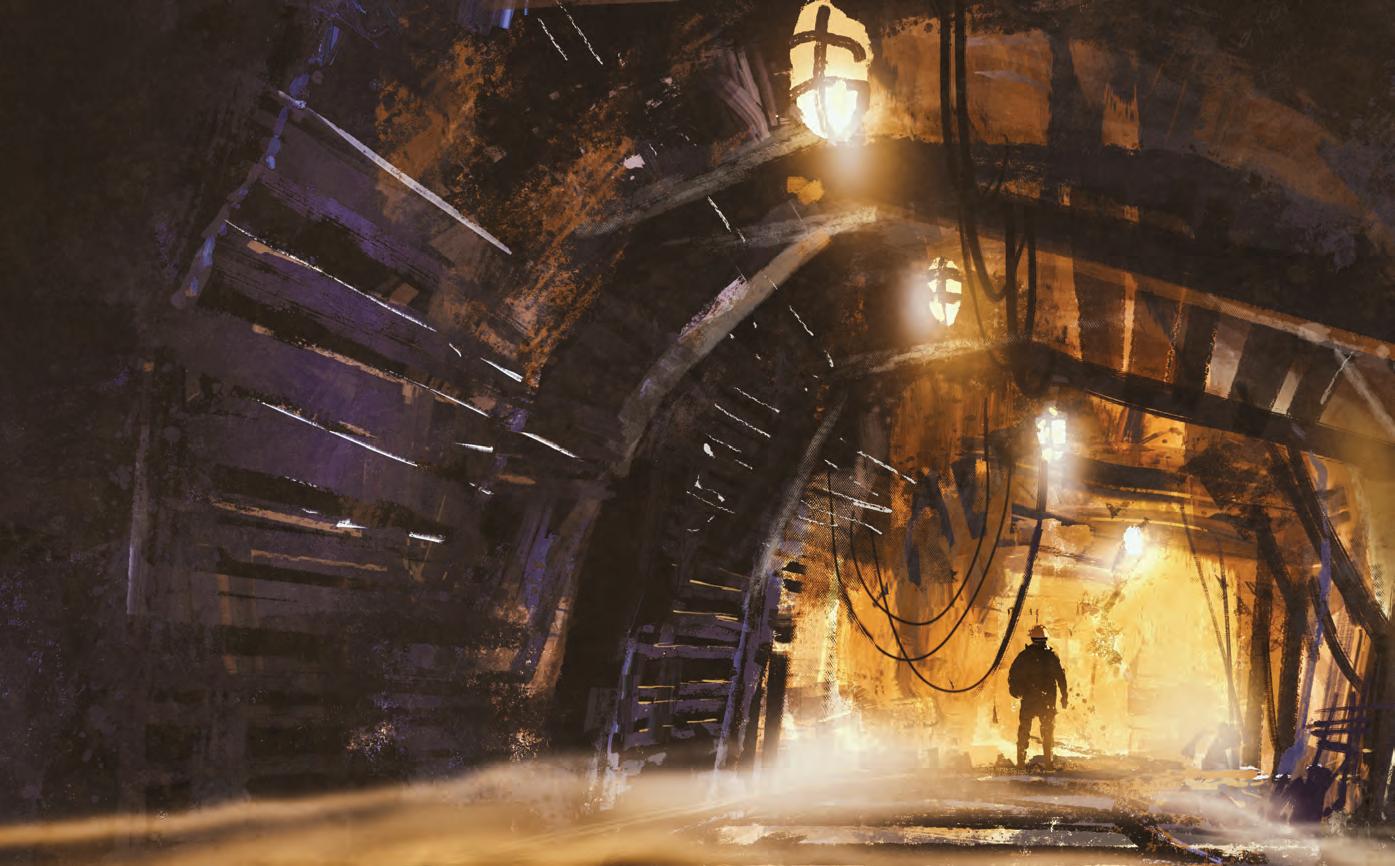
The development of new technology in the mining sector has been responsible for significant advancements in efficiency and productivity.
Automation is used more and more, not only due to its benefits to worker safety, but also in terms of using the technology to gather data which can be analysed to gain a greater insight into operational practices.
This data is also providing a wealth of information that allows mining companies to apply advanced analytical techniques to identify the causes of adverse outcomes, be they safety, productivity or quality
Chamber of Minerals and Energy Western Australia director of policy and advocacy Rob Carruthers says the Western Australian resources industry is at the forefront of automation and digitisation.
“We have seen a range of different technologies either developed or trialled in the mining sector first here in WA,” he says.
“In many ways the incremental benefit is gained from stitching all of the small initiatives together when you bring together new technology with the application of digitised planning and scenario software – data comes into that as well in terms of predictability for future opportunities and recovery.”
Rio Tinto will be the first to deploy Caterpillar’s 793 zeroemission autonomous haul trucks, once development is complete at the Gudai-Darri iron ore mine in Western Australia.
Newmont, meanwhile, has become Australia’s first gold miner to implement a fully operational autonomous haulage fleet at the Boddington gold mine, also in Western Australia.
Carruthers says there are three main drivers when it comes to adapting technology and digitisation – efficiency, predictability and safety.
“It is really across the value chain from assaying on site using technology and data; it is predictability around mine development and sequencing from a planning perspective, as well as the whole blasting and extraction process that goes with that,” he says.
“From an operational perspective, whether it is drill and blast or using a machine, when that is done with automated technology it takes human beings out of the line of fire and that can only be a good thing from a safety point of view.”
Carruthers says the advancement of technology has also led to a larger diversification of employment opportunities for those working in the resources industry.
Rio Tinto announced that more than 100 employees have completed Automated Haulage Systems (AHS) training at the WesTrac Technology Training Centre in Collie over the past six months in preparation for work at Gudai-Darri.
“The subset of that is the human element of more interesting and diverse jobs going into the future where it is not just about operating a piece of equipment, but being across a range of roles where you are a maintainer, a technical expert and potentially a data analyser all in one role,” Carruthers says.
“There were a few concerns early on, and there probably was concern going back to the industrial revolution, around new technology and what its application will mean to individuals.
“But we have seen across the board an increase in roles related to these sectors, and while there have been roles lost in operations, a lot of those roles have been welded into broader planning, automotive operations, analysis and recovery.”
Professor of practice in mining automation and data analysis at Curtin University’s Western Australian School of Mines (WASM) in Kalgoorlie, Dr Robert Solomon, says there are a number of social and environmental benefits of adapting digitisation in the resources sector.
For more than a century, Curtin University and WASM have been research leaders in the mining and resources sector
“The ongoing use and optimisation of digital technologies can provide the framework for optimising the recovery of scarce resources with minimal energy, this is a primary requisite for achieving a sustainable future,” Solomon says.
“Removing our employees from high risk or repetitive activities will continue to produce improvements in the safety of our employees.
“As with all technologies, however, it is important not just to focus on the advantages, but keep a close eye out for unintended negative consequences. Identification of these is not an argument to stop development, but an opportunity to enhance the value of the technology.”
This year’s MINExpo International, held in Las Vegas, showcased the
MINING’S OUTLOOK COULD BE DIFFERENT DEPENDING ON THE PACE OF DIGITAL ADOPTION.
latest exploration, mine development, open pit and underground mining, processing, safety and environmental improvement technologies.
It featured the latest offerings from original equipment manufacturing companies including Liebherr, Komatsu, Sandvik and Epiroc. It also included the latest in digital mining software technology
During the event, ABB launched its ABB Ability eMine, a new portfolio of electrification technologies set to fully facilitate all-electric mines from pit to port. The zero-carbon mine solution can electrify mining equipment across hauling, hoisting, grinding and material handling, and has been furnished with digital applications to monitor and optimise energy usage.
ABB Australia head of mining Nik Gresshoff says digitisation and sustainability go hand in hand.
“You hear a lot about digitisation, but I think decarbonisation is really the buzzword that you hear about a lot more right now,” Gresshoff says.
“I think it will really come down to what the original equipment manufacturers will bring out next and if they bring out a new electric vehicle which is capable of the same capabilities as the truck a company is replacing, then they will go with the newer vehicle.
“Battery technology will change and it is very simple to change a battery, so as we progress with battery technology we are finding ways that we can reduce the size and weight of these batteries while the charging systems stay the same.”
Gresshoff says ABB is looking forward to contributing and going on the journey towards electrification of mine sites and the advancement of digital technology.
“It is really about that journey, which is the electrification of the entire mine, and that includes sustainability and
digitisation,” he says.
“Every company is asking the question: how do we get to net zero emissions? We are committed to lead the sustainable decarbonisation within the Australian mining sector through the energy transition while leveraging the ABB Ability eMine solutions.”
Solomon says WASM has reviewed its curriculum for the new generation of mining engineers to ensure they are skilled and ready to enter the industry with a critical understanding of the impact of digital technology and automation in mining.
This includes working closely with industry, developing skills in advanced analytical techniques and an understanding of the impacts and opportunities from automation.
“We are only just starting down the road of extracting the benefit of the vast amounts of information available to the modern mining operation,” Solomon says.
“We are still wrestling with the tasks of data access and cleaning, although progress in this area is moving rapidly.
“Machine learning and artificial intelligence are rightly being utilised more and more in the industry, perhaps however, at the cost of more traditional physics-based modelling tools.”
Carruthers says one of the additional benefits of the advancements of technology in mining has been in softening the blow of the global COVID-19 pandemic, especially during the closure of the international and interstate borders.
These closures have led to a skills shortage in the sector with a number of companies forced to suspend operations due to a lack of workers.
However, advancements in remote operations and the increased use of autonomy in the sector have also helped the industry contribute to a record commodities trade period for the Australian economy.
“The proof is in the pudding in terms of the phenomenal year the WA sector has had and the contribution the sector has made to the state over the past 12 months,” Carruthers says.
“When we open up the technologies and the processes that are proving here will be exportable to the world, and that is not just the hardware and the software, but also the knowledge of how to extract the most value out of it.” AM

TECHNOLOGY ADVANCES HAVE LED TO A DIVERSITY OF OCCUPATIONS IN THE RESOURCES SECTOR.
BRADKEN’S NEW TECHNOLOGY SERVICES INCLUDE CONDITION MONITORING.
NEW-LOOK BRADKEN APPROACHES CENTENARY WITH A SPARK
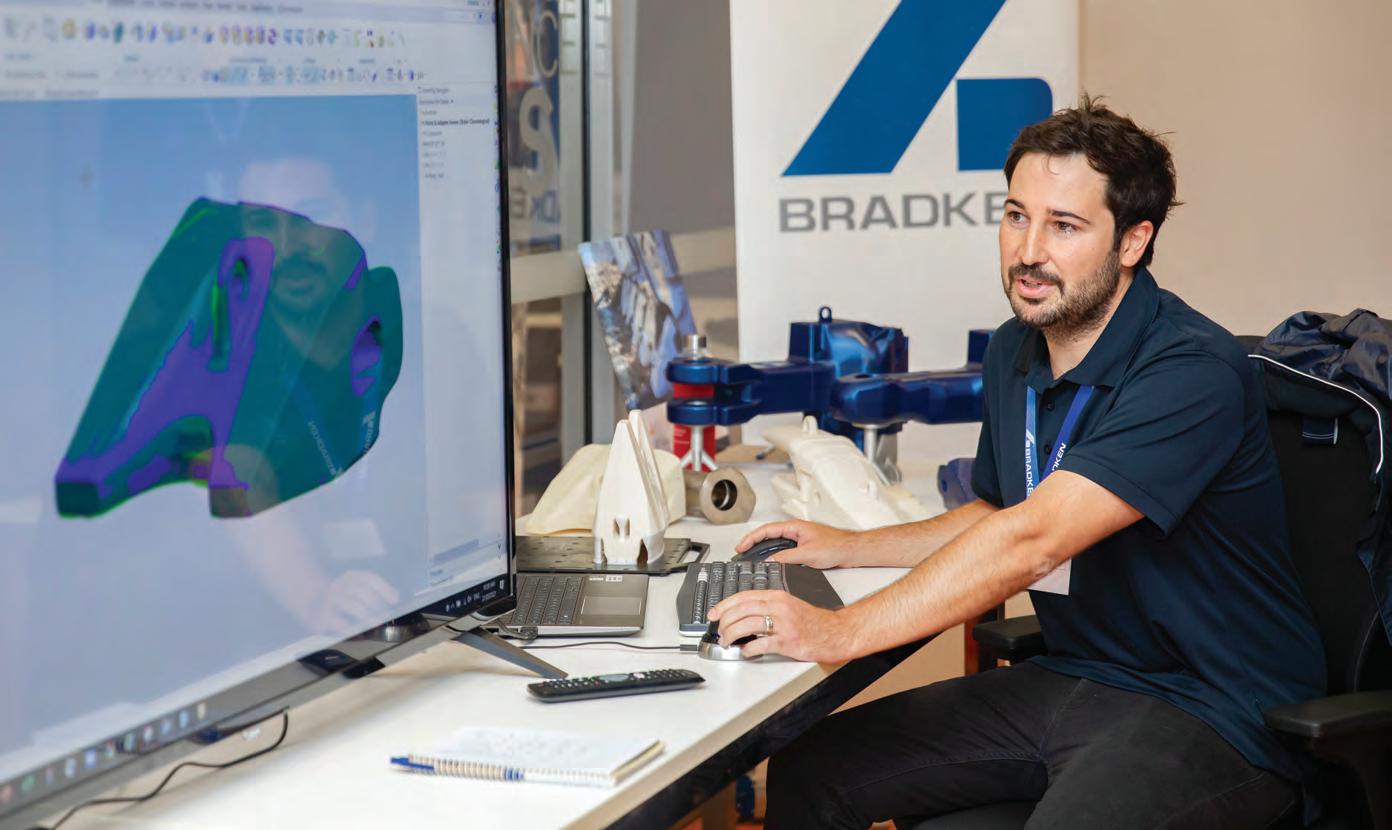
BUILDING ON 100 YEARS OF BESPOKE MANUFACTURING EXPERTISE, A NEW BRADKEN IS TAKING SHAPE AS THE COMPANY SUPPORTS ITS CUSTOMERS IN ADOPTING INNOVATIVE DIGITAL MINING SOLUTIONS. FROM A TRADITIONAL MANUFACTURER TO TODAY’S DIVERSIFIED BRAND, BRADKEN’S TRANSFORMATION CONTINUES TO SUPPORT MINING’S EVOLUTION.
Celebrating its centenary next year, Bradken has come a long way as a company since founders Leslie Bradford and Jim Kendall pledged some horse race winnings towards a new steel foundry in 1922.
Bradken built its name in the design, engineering and construction of a range of steel plant and rail equipment. Over time, Bradken found a calling in the mining industry for ground engaging tools, undercarriage systems, buckets, and mill and chute liners.
Under new ownership in 2017, Bradken started on a path to increase its focus on digital solutions, backed by consistent in-house manufacturing capabilities.
Bradken research and development manager Reece Attwood says this shift in perspective has changed the way the company operates.
“We now have sister companies like Wenco who are specialists in fleet management software – that’s really opened our eyes into the service space,” Attwood tells Australian Mining.
“Instead of only selling a range of similar products that we specialise in, we’ve been able to broaden our horizons and develop an innovative approach that has supported the development of technology services which support our products.”
These horizons now include the integral technologies of condition and performance monitoring for equipment in the field.
These solutions support Bradken’s future growth and transform the company from a niche manufacturer into a technology and service provider.
Attwood says the monitoring of product conditions presents a range of benefits for Bradken and the people it serves.
“Customers can remotely monitor the wear condition of their liners and predict the remaining life on the product,” he says.
“This helps with scheduling and getting the most out of each liner, but it also provides a valuable safety benefit because they don’t have to go near the equipment to monitor its condition.”
Bradken is developing its range of monitoring liners for grinding mills, crushers, ground engaging tools and also undercarriage components for hydraulic excavator crawler systems.
Further into the technology space, the company has developed an online dashboard and data reporting solution for all its monitoring products.
This encompasses a range of product specific widgets, as well as a cloudlevel software reporting suite.
Attwood says it’s the kind of thing no one expected of Bradken 10 years ago, but is becoming a reality as the company innovates to connect with the future of mining.
“Our software team is working hard to ensure the product is easy to manage and easy to consume,” Attwood says.
“Mine sites don’t necessarily want another portal, another dashboard and another set of login details, they just want to take their data and do what they need to do.”
Attwood adds that providing insights
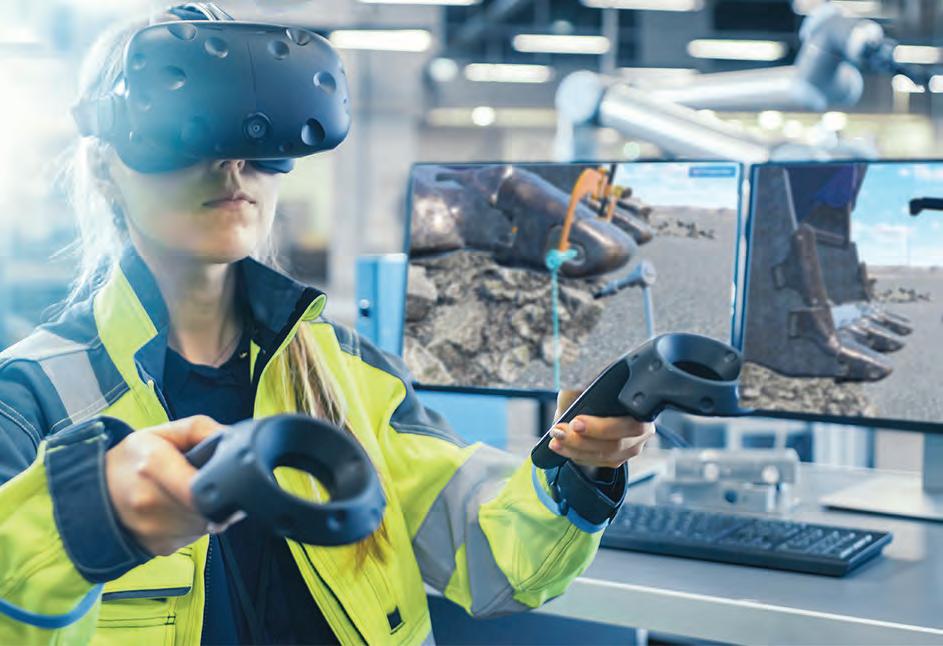
into the ideals of this tech-savvy market, while working with customers on the design is equally important.
“A key focus for us is the concept of interoperability, and open-architecture design on this monitoring software,” Attwood says.
“We’ve worked directly with a major customer in Western Australia to determine what would be acceptable from a cybersecurity, architecture and documentation perspective.
“We’ve really listened to their feedback and implemented it so the end product suits their operations and solves their problems, our technology solutions will also be ideal for future customers.”
But to transition from manufacturer to a broader service provider doesn’t happen overnight.
To ensure Bradken accommodates rapid technological adoption, the team has integrated new roles, skill sets and specialists.
“To be able to speak that digital language with our customers has become very important,” Attwood says.
“We’ve overcome this by investing in new people and training our existing staff. Instead of only hiring mechanical engineers, as in the past, we’re now hiring software engineers too.”
Of course, COVID-19 has accelerated this adoption for Bradken, as it has for the wider industry.
Remote monitoring is now a necessity rather than a bonus and realising this, Bradken is remaining connected with its clients around the globe, without the need to travel on site.
“Previously we would have preferred our own sales teams monitoring the products in person. But for now, our sales teams are interacting with our customers behind the scenes. The fewer hands on the equipment and fewer people on site, the safer and more manageable for the mine operators in current conditions,” Attwood says.
Reinforcing the digital solutions focus even further, the company recently announced the establishment of a new marketing and technology business unit, led by mechatronics engineer and Bradken stalwart Mark Hurley.
Since October 1 2021, the unit has included the dedicated research and development team, IT, as well as customer-focussed market analysts and marketing teams.
Hurley says supporting customers through Bradken’s own digital evolution is at the heart of his team’s vision and the company’s future.
“Bradken is proud of the 100 years of manufacturing history and of the customers we continue to serve,” Hurley says.
“Their needs are changing and
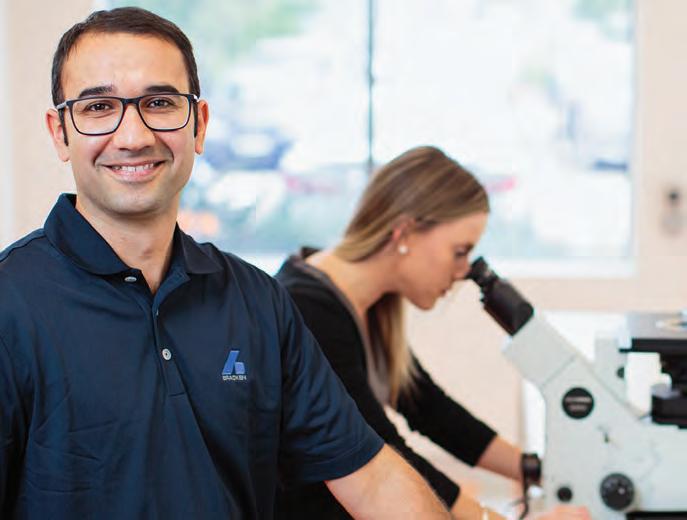
BRADKEN IS DEVELOPING ITS TECHNOLOGY SERVICES AS WELL AS ITS MANUFACTURING.
we are committed to joining them on that journey to deliver innovation through digital product and service solutions, which improve site safety and sustainability, while lowering total costs of ownership.”
This sentiment is supported by Bradken chief executive officer Sean Winstone.
“It goes without saying that the future is becoming more digitally orientated and Bradken will be able to offer customers a superior service and experience via digitised solutions at every touchpoint,” Winstone says.
“Matching our history of working with customers to understand what they need and value with these technology solutions is key to Bradken’s future.” AM
The KCA Carbon Converter
Recover Gold From Your Carbon Fines On Site
Kappes, Cassiday & Associates (KCA) now has three carbon converters successfully operating, at mines in Armenia, Argentina and Nevada. These units take carbon fines and dirty, wet waste carbon at gold leach plants, thoroughly ash it and remove all mercury. Recovery of gold and silver into bullion is typically 99%. For waste carbon loaded to 200 grams gold per tonne, operating cost is $6.00 per gram, or 11% of the value of the recovered gold. Often waste carbons are loaded much higher - the cost per gram drops accordingly. Mines with the Carbon Converter can recover their gold quickly without the Chain-of-Custody problems of shipping carbon to outside processors. Shipping mercury-contaminated wastes off-site incurs large risks of environmental contamination, and the Carbon Converter eliminates this risk. Having the Carbon Converter on site allows the operation to explore various process optimization techniques. For example, carbon fines below 30 mesh are usually lost to tailings in CIL plants, because such fines cannot be recovered cleanly. These losses can account for 1% of the gold fed to the plant. The Carbon Converter can process them. Another opportunity exists where process facilities periodically discard a portion of their coarse carbon in order to maintain optimum carbon activity. With the Carbon Converter, this carbon can be consumed on site and the contained gold recovered economically. The installed cost of the Carbon Converter is about US$1 million including site services, a building, and infrastructure. For mines which generate at least 50 tonnes/year of carbon wastes and fines, payback is typically less than one year. 775-972-7575 www.carbonconverter.com or www.kcareno.com
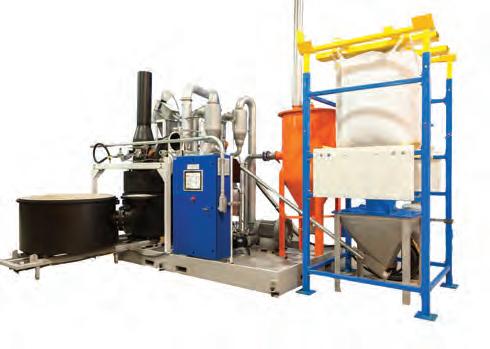
VERNETZEN CREATES VALUE FROM NETWORK VULNERABILITY
VERNETZEN HANDS DIGITAL CONTROL BACK TO THE NETWORK OPERATOR WITH ITS PRE-AUTHORISATION SYSTEM, VERNETZEN VETO. BOTH CYBER AND PHYSICAL SAFETY ARE ASSURED BY VETO WHILE MINE SITES GET ON WITH THE JOB.
The patent-pending Vernetzen Veto technology was borne out of an understanding of risk.
Vernetzen recognises how modern-day firewalls and VPNs (virtual private networks) present issues for valuable enterprises like mining companies – Veto is designed to mitigate these concerns.
The issue with firewalls lies in their static nature, where rule sets for network access are fixed, and temporary access for specific remote technicians or network vendors is made difficult.
VPNs can be similarly secure through a username and password set up. However, a lack of rule sets allows anyone with details to log in at any time.
Vernetzen founder and network architecture consultant Luke King
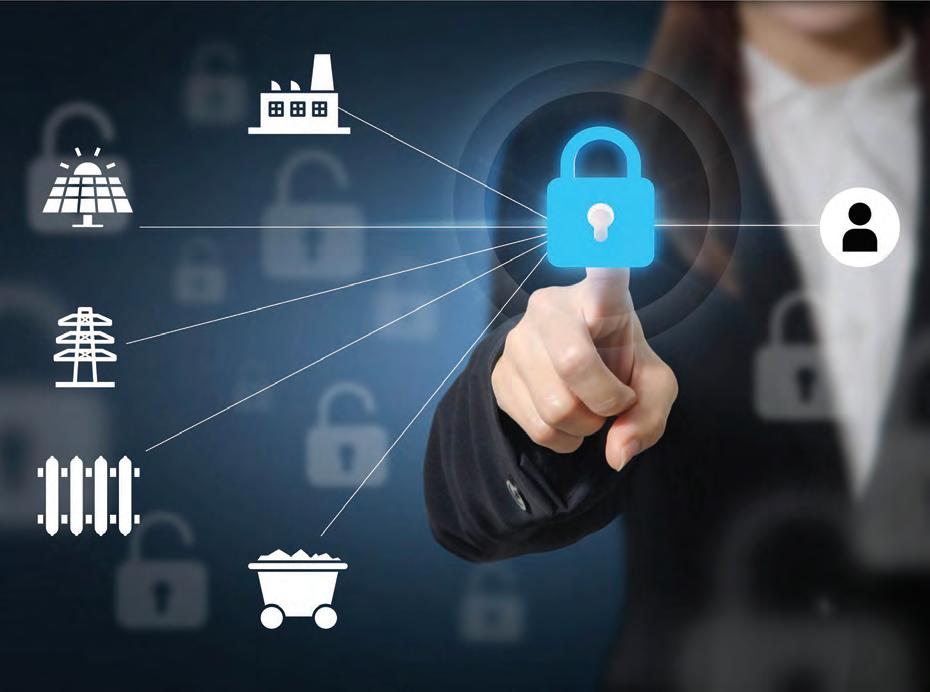
VERNETZEN VETO CONNECTS EXTERNAL PARTIES THROUGH ONE SECURE ACCESS POINT.
explains the problem with VPNs on an active mine site.
“This is an issue in a production environment because if you have someone working on site with live equipment and changes are made remotely without anyone on the ground being aware, this causes an obvious risk,” King tells Australian Mining.
“Also, if unplanned changes are made remotely, it can cause an interruption which can cause a loss of productivity.”
When the worst-case scenario is a safety incident and best is an unplanned stop in production, questions must be asked of the current system.
To address these issues, Vernetzen Veto requires those in charge on site to authorise remote access on a caseby-case basis where each session is scheduled, time limited and can be terminated at any time.
This way, network operators have full visibility of those accessing their mine’s network, while remaining secure against unauthorised actors. King says authorisation can take place in several ways.
“We have a pretty interesting authorisation process. It can be tailored to the requirements of the assets being accessed,” he says.
“So, you can nominate specific individuals or a preconfigured team to receive the authorisation requests.”
Veto can also specify the level of access for each individual visitor, limiting them to a brand of equipment or a section of the site.
“You might be a remote technician from a particular OEM so we’re only going to allow you to work with the equipment from your own company,” King says.
“This removes the need to create a bunch of micro rule sets within the firewall, which would otherwise cause issues of latency.”
High latency – or a slow connection – on a mine site’s network is essentially the opposite of productivity.
King provides an example of where low latency is crucial for the safety and productivity of those on site.
“Say there’s a system in a paste plant on the surface and a system underground. Then there’s some pressure sensors at the top of a pipe which is being filled with concrete to give structure to the mine,” King says.
“If those pressure sensors are delayed by even a second, due to a slow network with too many firewalls, this could result in the pump shutting off too late, pressure building and an incident occurring.”
Network operators can also keep remote visitors accountable using real-time monitoring.
While policies and procedures should be in place both on site and digitally to remove the risk of an accident, King says customers have required an extra level of reassurance.
“We can also do things like capturing video to monitor what support providers are clicking on,” King says.
“Our experience has been requests for playback of the session as there has been an incident at the same time. And Veto satisfies this request.”
As autonomy and remote control becomes crucial to the operation of Australian and global mines, securities like Veto are becoming even more important.
King says as the industry grows and evolves with technology, Vernetzen will continue to secure the industry.
“There’s been a push for remote access and a need for that assistance. Whether it’s the vendor or remote technician who needs to log in to a certain site,” King concludes.
“Particularly for mining where there are sites all over the world, easy remote access is even more necessary.” AM
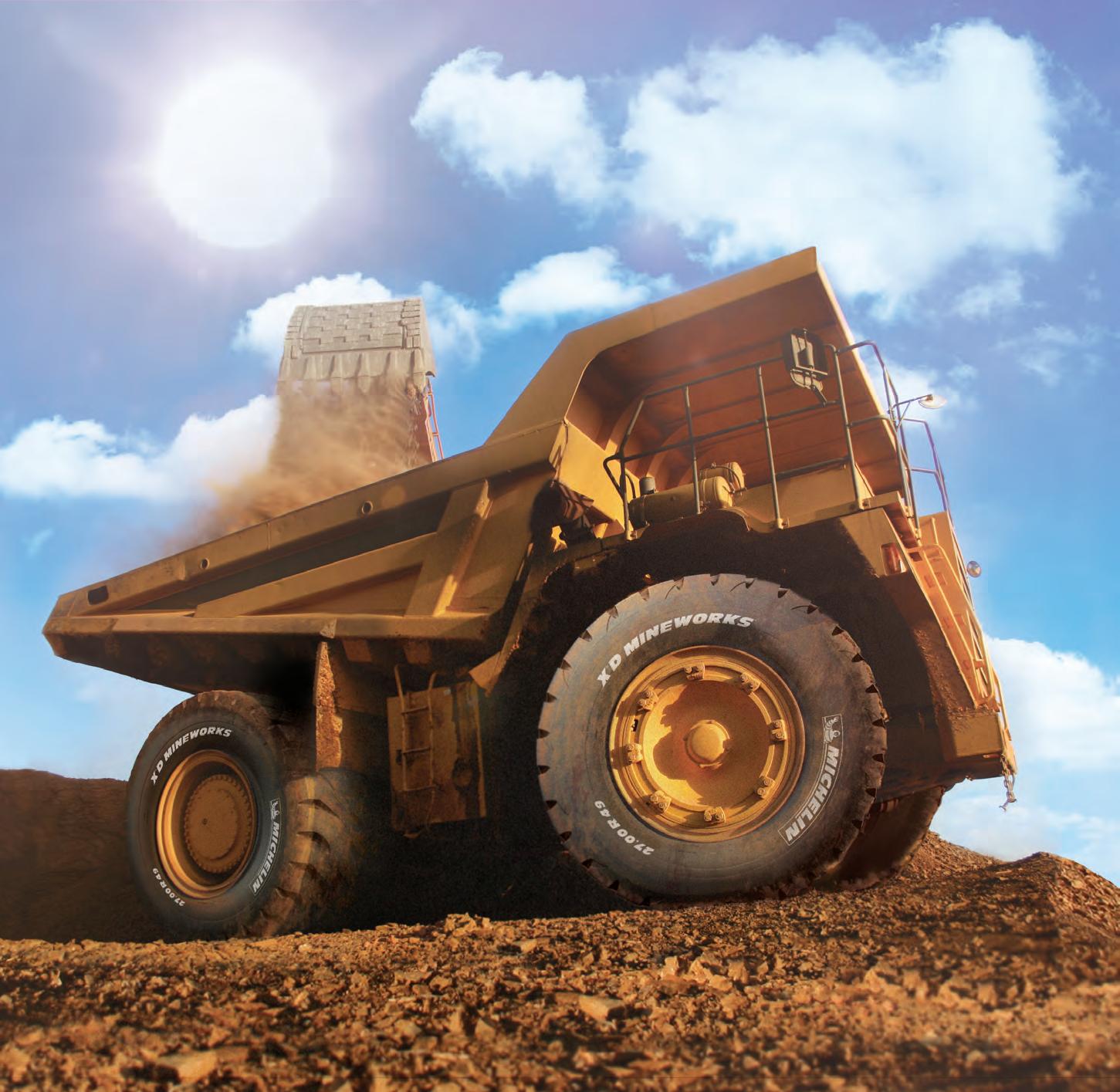