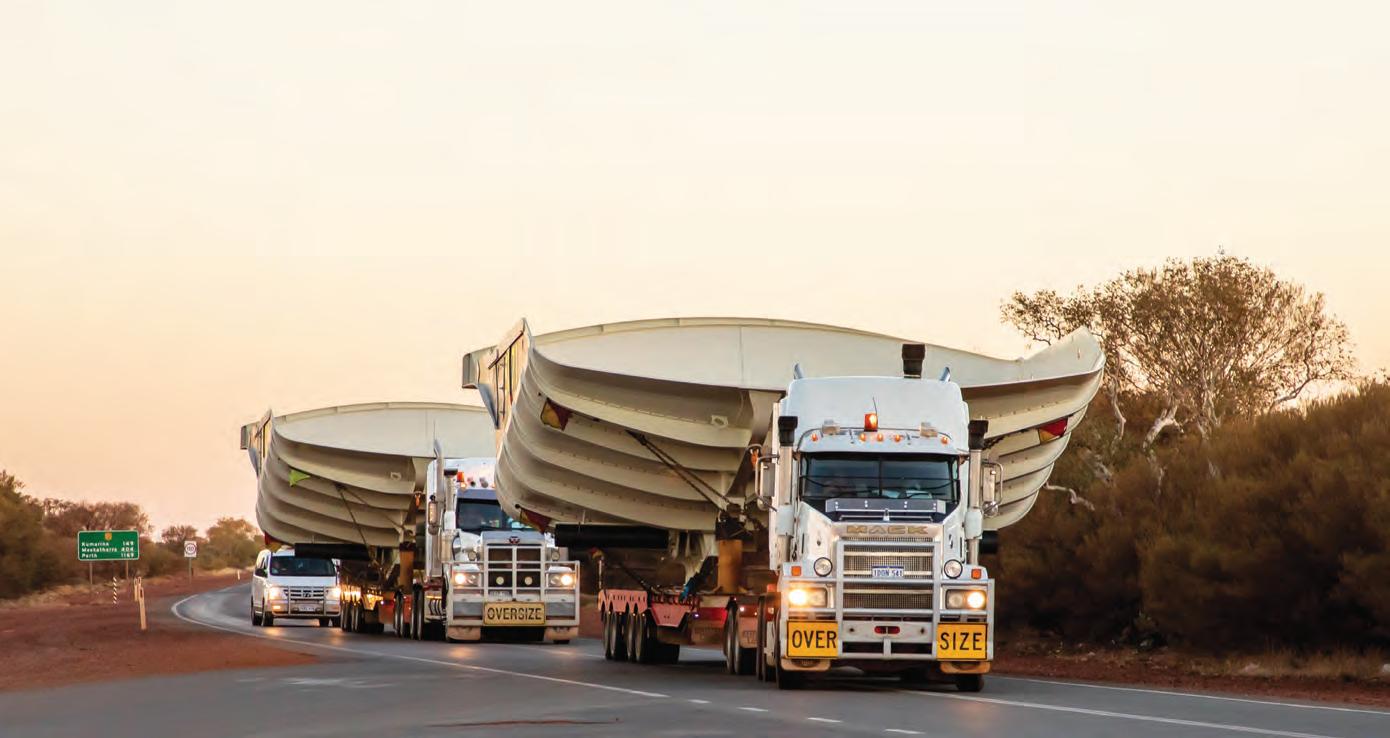
16 minute read
SURFACE MINING
MASTERING THE ART OF PAYLOAD
NEARLY 1500 HERCULES DUMP BODIES HAVE BEEN DEPLOYED ACROSS AUSTRALIA.
WITH MORE THAN 20 YEARS’ EXPERIENCE IN OPTIMISING PAYLOADS, SCHLAM HAS BECOME AN ESTEEMED PATRON OF THE AUSTRALIAN MINING INDUSTRY.
Schlam’s name keeps growing within the Australian mining industry as the company continues to unlock further productivity from its proven innovations.
The mining industry may be familiar with Schlam through its Hercules dump body – an ever-advancing product that heightens payload capability.
Nearly 1500 Hercules dump bodies have been designed and deployed across Australia, but don’t tell Schlam sales manager Tom Smith it’s a fixed product.
“To be honest, that perception does irk me – the perception that we’re not very innovative because our main product’s been leading the pack for so long. It couldn’t be further from the truth,” Smith says.
“We haven’t just been getting lucky for the past 20 or 30 years. The reason it’s (the Hercules dump body) remained the premium product in the market is because it’s continuously improving over time, even though the shape of the body has remained relatively consistent.”
Smith sees similarities in how the Hercules dump body has developed to the way the Apple iPhone has advanced with each model.
“The look of the phone hasn’t changed a whole lot over the years, but the technology and smarts that go into it have improved greatly,” Smith continues.
“You drop an iPhone five years ago; it shatters. You drop it now and it’s far more durable even though it looks the same. I think that applies really well to our dump bodies.”
The Hercules dump body has also developed in the same ilk that Schlam has evolved.
What is fundamentally known for its weightlessness has grown in its intricacy, paving the way for a stronger and more durable piece of equipment.
“The way that we’re able to achieve such low weights with our body, it’s a very unique design,” Smith says.
“It’s flexible, it absorbs a lot of impact, and what that flexibility allows us to do is, if you can take weight out of the structural components, because the stresses are reduced with that flexibility, we keep the weight in the areas where it’s actually needed, which could be the ore-facing surface that wears out over time.
“There has been a common misconception with our body, and this myth has been somewhat dispelled recently – ‘oh the Hercules body, because it’s lightweight, it doesn’t last as long as the others’ – and that couldn’t be further from the truth.
“In the critical areas, we’ve got the same materials, a lot of the time in greater thicknesses, so we actually have increased service life, increased time between needing to have wear plates installed or replace the components.”
Smith points to a Kalgoorlie case study to consolidate his point.
“We’ve got bodies out in the Kalgoorlie Super Pit that have been operating since 2010 that have got close to 60,000 hours,” he explains.
“If that’s a mine site strategy that we want these things to last forever, the bodies can be designed to do that.”
When a Hercules dump body left Schlam’s Forrestfield factory in August 2010, bound for a Kalgoorlie gold mine, it was just the ninth dump body of its kind.
Schlam has delivered up to 50 Hercules dump bodies to the same miner since that day, complementing the latter’s growing fleet of haul trucks.
With constant dialogue between Schlam and the miner, the dump body has continually evolved to meet the needs of the client’s hard rock mining environment.
As of August 2020, more than 1.1 million combined hours of operation had been achieved by this miner’s Hercules bodies.
Through Schlam’s engagement with the Australian mining industry, some prevailing trends have emerged regarding payload.
Many mining companies know their operation from the back of their hand and understand avenues to gain the upper hand.
“To be honest, I think the attitude’s been fantastic (towards payload). All major miners in Australia intricately understand the benefits of optimising payload and optimising load-andhaul strategies to maximise payload,” Smith says.
“The most important thing miners understand is the dollar value associated with improved payload.”
Schlam has payload down to a fine art, and that’s not just confined to the growing esteem of its Hercules dump body.
The company’s Bullant underground dump body is also turning heads, while its Barracuda mining bucket is known for speeding up load-and-haul operations.
Schlam also offer its Schlam Hex Tile wear plate, improving dump body durability, alongside its dedicated wear management program, an end-to-end initiative assisting mining companies as they monitor the condition of their assets. AM
SCHLAM HAS DECADES OF EXPERIENCE IN OPTIMISING PAYLOADS.
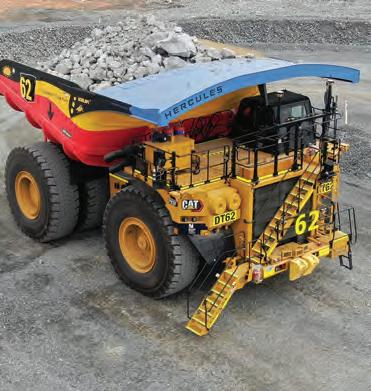
STAYING ONE STEP AHEAD WITH TECH TOOLS
MTG COMBINES DECADES OF EXPERIENCE MANUFACTURING GROUND ENGAGING TOOLS WITH ITS OWN FOUNDRY AND INNOVATION TEAM. THE COMBINATION OF IN-HOUSE DESIGN, MANUFACTURING AND TECHNOLOGICAL NOUS ALLOWS MTG TO MAKE A NAME FOR ITSELF IN THE AUSTRALIAN LANDSCAPE.
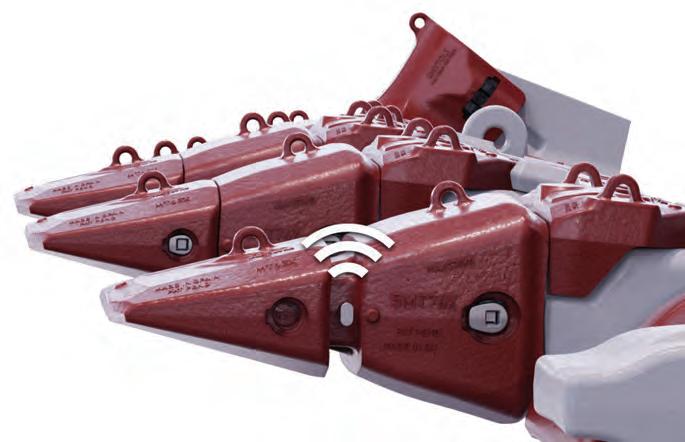
In its 60 years of existence, MTG has expanded into 60 countries thanks to a reliable distribution network.
In Australia, where the company staked its claim around the start of the millennium, MTG relies on 2MT Mining Products to distribute its products across the country, from the Pilbara in Western Australia to the Bowen Basin in Queensland.
But reliable distribution would be nothing without a quality product to deliver, so MTG proclaims that innovation without limits is its core value, and its ground engaging tools (GET) reflect this.
MTG chief executive officer Javier Triginer says the company is uniquely positioned to be creative with its products, unlocking a range of potential for the mining industry.
“You must be very brave to dare to innovate in your market with an expanded product that has functionalities you’ve never worked with before,” Triginer tells Australian Mining.
“Not all GET manufacturers have the capacity to innovate. Indeed, many do not have innovation departments and therefore are unable to create new products.”
This of course is not an issue at MTG, where a range of digitally enabled GET are on offer and in the works to satisfy an evolving industry.
MTG engages with industry specialists to understand how best to combine its current expertise in mining consumables with the technological solutions of the near future.
“We started the GET monitoring and detection project with an external electronic engineering company,” Triginer says.
“We later brought this project in-house. Being manufacturers of GET we have been able to combine this technology with our products to produce a new market category.”
One of MTG’s original GET products and one of the most popular in its line is TERRA – a cast lip solution which can be fitted to hydraulic mining shovels from 250- to 1000-tonne class machines.
To ensure the quality of these products, the manufacturer has invested in its own foundry for a complete overview of the process behind the product.
Triginer explains the benefits of owning and operating a foundry and the latest investment into MTG’s future.
“MTG’s 60 years of experience in running foundries has equipped us to design and build the most modern and GET specialised foundry in the world,” he says.
“MTG only manufactures GET within this foundry and we control the entire process from steel scrap selection to product packaging, to meet the highest standards.
“Last July, we announced an $18 million investment in the foundry that will enhance our production capacity while improving the recycling rates of our consumables. This is a great step towards more sustainable activity.”
By owning and operating its own foundry, MTG can send customer feedback straight to the designers, engineers and manufacturers for faster adaptation of suggestions.
Triginer says the company highly values the input of its Australian customer base, being the most technologically advanced mining sector in the world.
“The first step is to listen to customers: machine operators, GET crews, welders, maintenance and production engineers. Their inputs are key to understand how to improve products,” Triginer says.
“We are able to be very flexible in redesigning products to suit varying customer ground conditions and we are able to do this very quickly.”
One up-and-coming request of GET in Australia is for digital monitoring solutions which add value to an otherwise commonplace product.
MTG has pioneered the digitising of GET and is conducting trials in the Western Australian iron ore sector.
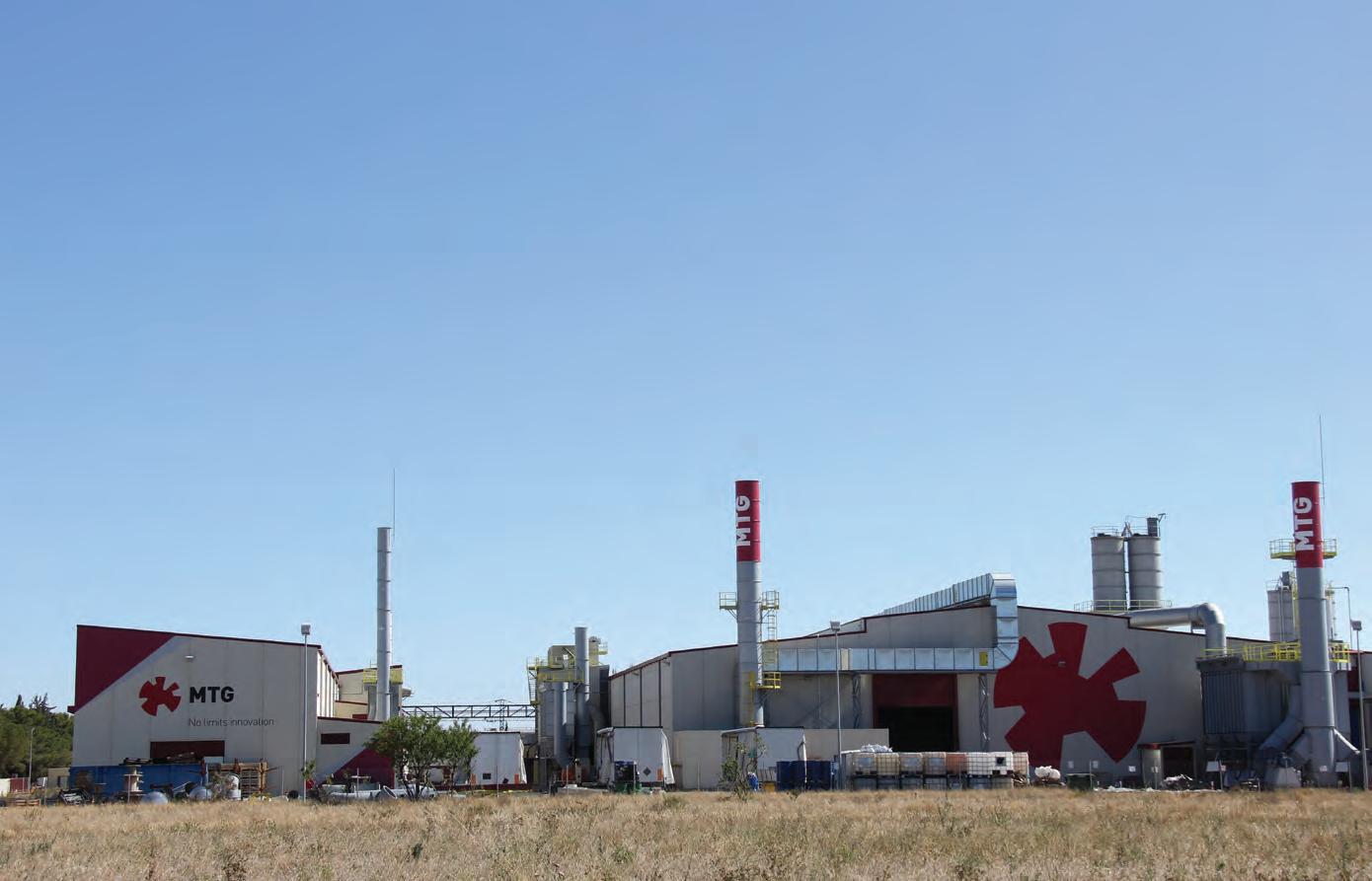
THE TERRA GET CAN BE DIGITALLY ENABLED TO IMPROVE SAFETY AND PRODUCTIVITY.
Triginer says the product type will only gain in popularity.
“Early indications are that this new GET detection solution is performing extremely well and we anticipate it being widely available in 2022,” he says.
“In a few years the sensorisation of the GET will be a must, but currently there are very few players who are in a position to face this challenge.”
MTG is also working on a brandnew cast lip design which will look to challenge traditional methods and bring significant improvement to operator efficiency.
Triginer says the company is always looking one step ahead to ensure it remains relevant in the Australian mining industry.
“Longer term, we think that we will play a critical role in sensing the stress GET is subject to when digging,” he says. “This would allow us to process such information and send the machine specific instructions to improve the digging efficiency, a critical step towards the autonomous excavator.” AM
MTG WILL INVEST $18 MILLION IN ITS SPANISH FOUNDRY.
BISALLOY PROTECTS INDUSTRY WITH AUSSIE-MADE STEEL PLATE
THIS MANUFACTURER LAYS CLAIM TO THE ONLY AUSTRALIAN-MADE QUENCHED AND TEMPERED STEEL ON THE MARKET, PROVIDING THE AUSTRALIAN MINING INDUSTRY WITH SOME OF THE MOST WELL-SUITED WEAR STEEL FOR ANY APPLICATION.
Bisalloy has developed a recipe for success with its national dealer network since it was established 40 years ago in Wollongong, New South Wales.
The company sources its raw materials from BlueScope just 10 minutes away, making it the only Australian manufacturer of its kind that does not require imports.
With the blessing of the National Association of Testing Australia (NATA), each plate of steel comes hot off the production line with a stamp of approval to withstand the most abrasive jobs mining can offer.
Bisalloy national sales and marketing manager Andrew Egan says the company uses these important partnerships to ensure its business is as trusted as its product.
“Reliable steel supply and consistent quality are the two obstacles to success,” Egan tells Australian Mining.
“We overcome this by working closely with our suppliers. One of which is BlueScope where we source 90 per cent our steel, and we’ve fostered a good relationship with them owing to our proximity.
“On consistent quality, we have a technical team dedicated to the monitoring and testing of quality to ensure we uphold our NATA-qualified standards.”
By partnering with BlueScope, Bisalloy combines the best of both worlds for a superior result.
“The green feed – the raw product – we get from BlueScope is made to our recipe and we then quench and temper it,” Egan says.

BISALLOY SOURCES ITS STEEL LOCALLY FROM BLUESCOPE.
BISALLOY WEAR STEEL IS SPECIFICALLY FORMULATED TO ENDURE HARSH MINING CONDITIONS.
“BlueScope steel is very highquality steel so bringing our two processes together makes for a very popular product.”
The reason to obsess over every step of the steel manufacturing process is that the Australian mining industry has grown a reputation for being one of the most abrasive in the world to operate in.
When iron ore comes tumbling down a chute or GET (ground engaging tools) are relied upon to withstand hours of relentless abrasion, mining operators need to be sure their equipment can handle these harsh conditions.
Egan says Bisalloy assures its products are up to the task, while saving time and money.
“The beauty of what we provide is it lasts longer so you don’t have to change it out as often,” Egan says.
“A mining company will spend less time and money on maintenance when using Bisalloy compared with a less wear-resistant brand, thanks to our recipe for quenched and tempered steel.”
This fact is no more apparent than with Bisalloy as it puts significant time into testing its solutions in realworld applications.
Egan says the size of the company allows Bisalloy to offer bespoke solutions to suit almost any calling by partners in the mining industry.
“We’ve conducted field tests with our end-users working through our dealers. The beauty of being a slightly smaller company is we can tweak chemistries in the steel to suit particular applications, if need be,” Egan says.
“If we work with a mine which has a unique requirement, we’ve got no problems discussing with them to provide a tailored solution.
“As a smaller company, relatively speaking, we are able to engage with customers on many different levels. We’re nothing if not nimble as these steel plates are all we do, and we do them well.”
Every corner of Australia can be reached by Bisalloy wear steel, with a reliable network of dealers providing the final polish to a reliable service.
While abrasive steel is one offering, it’s nothing without the accompanying support, according to Egan.
“We’re based here in an Australian time zone. We’ve got our own technical team available to travel and visit customer sites. We not only provide the product but the advice as to its application,” Egan concludes. AM
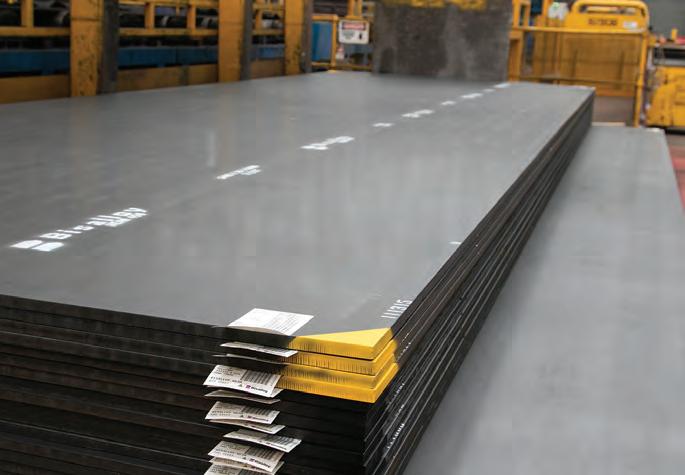
PLANT SIMULATION TOOLS OFFER A HIGH-LEVEL VIEW OF AN ENTIRE OPERATION’S EFFICIENCY.
DON’T COMPROMISE ON VIBRATING SCREEN HEALTH
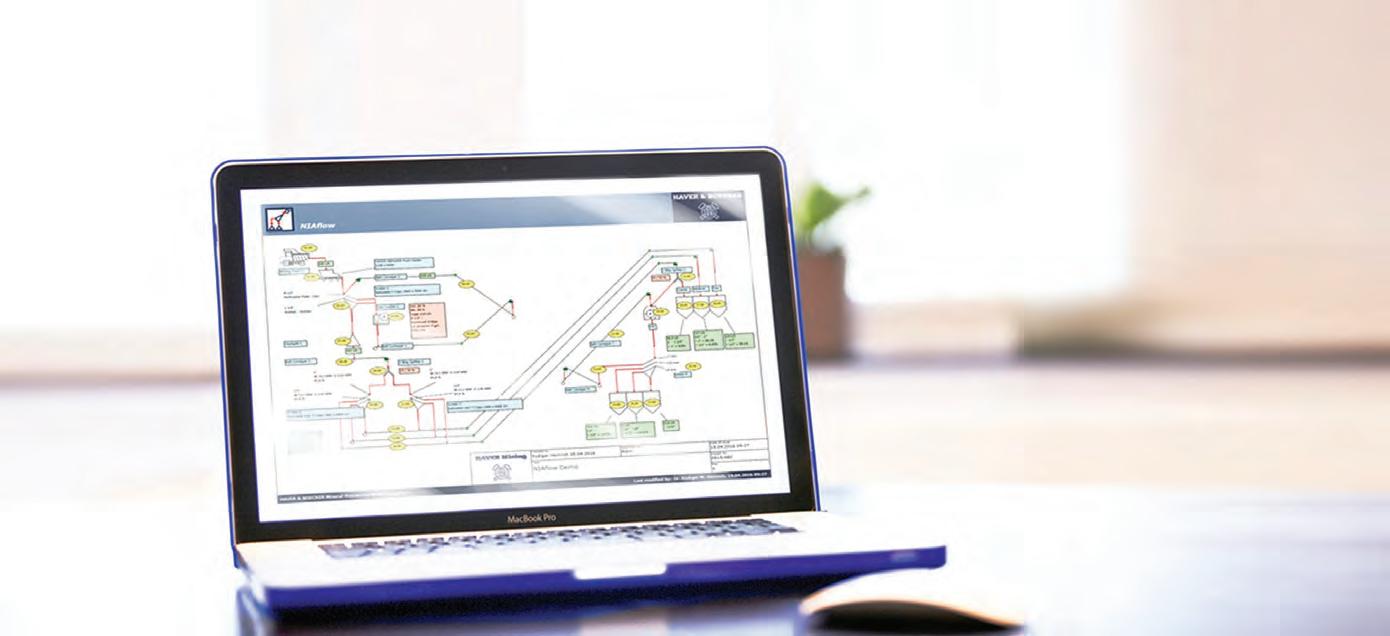
HAVER & BROECKER NIAGARA DISCUSSES HOW PARTNERING WITH A TECHNICAL ORIGINAL EQUIPMENT MANUFACTURER FOR MACHINERY MONITORING CAN HELP IMPROVE A MINE OPERATOR’S BOTTOM LINE.
Vibrating screens work at the heart of a processing operation.
Every tonne of material must be screened at least once before it is loaded into a truck for sale. And just like the human heart, they need to be kept strong and healthy to do their job well.
By partnering with a technical vibrating screen original equipment manufacturer (OEM) like Haver and Boecker, which also specialises in equipment monitoring, operations can rely on a team that not only manufactured the equipment, but offers comprehensive diagnostic tools, product-specific knowledge and years of engineering experience.
The result can be peace of mind, minimised downtime through faster problem solving and lower repair costs down the line.
There’s a wide range of OEMs to choose from. While many have engineered reputable screening equipment, it’s important to consider the services they offer to take care of that equipment for the long run.
Haver & Boecker Niagara is a leading provider in screening, pelletising and mineral processing plants and systems.
The company’s mission is to deliver the best of these technologies to customers in the mining and minerals industries.
With deep roots and years of experience in these industries, Haver & Boecker Niagara uses its innovative and shared technologies to effectively meet the needs of customers around the world.
Vibration analysis and monitoring Vibration analysis, for example, is dedicated to measuring the health of vibrating screens. These systems measure and transmit real-time vibration data such as acceleration, orbit, deviations and more.
The data is transmitted while the machine is in operation via sensors that are placed at dedicated locations on the screen body. The information is recorded to a cloud service where it can be viewed from multiple devices.
In addition to analysing current machine performance, some systems also store historical data to help predict the machine’s future performance so operators can

schedule maintenance accordingly.
All of this data is used to fine-tune equipment for optimal performance and maximum output, as well as to locate issues that could lead to larger repair costs or machine failure and unplanned downtime if not addressed.
An OEM should perform a vibration analysis on any new vibrating screen before it even leaves the factory.
This provides a baseline for how the machine should run. At each service visit, vibration analysis should be used to better understand the machine’s condition before any repairs are made.
Once technicians make necessary repairs, another vibration analysis should be completed to ensure the problem has been solved and to document that the machine is running at optimal condition once again.
The vibration analysis sensors themselves are something to consider. All vibration analysis systems require some sort of sensor to be placed on the vibrating screen.
Some are wired and require the user to stand within range while holding the connected device. Others are wireless, providing the safety benefit of allowing the user to stand farther away.
A vibration analysis setup may include one sensor that must be moved to multiple parts of a machine for a full reading.
Others save time by including multiple sensors, allowing for a comprehensive look at the entire machine at the same time.
Vibration analysis systems work similarly to a stethoscope – they analyse the machine at the moment in time at which it is being measured.
Conversely, condition monitoring systems work more like a heart monitor, or perhaps an EKG. These systems include permanently affixed sensors for 24/7 monitoring. Some condition monitoring systems include automated alerts if problems are detected, allowing for a quick shutdown before the problem becomes potentially catastrophic.
The accumulating data can be used to improve efficiency by illustrating trends, making predictions as to how long before an issue may arise and more.
Some around-the-clock monitoring systems allow OEM certified technicians to monitor results remotely, analyse the data and send expert recommendations to ensure equipment longevity.
In one example of an operation benefiting from these tools and services, a producer worked with an OEM to conduct a vibration analysis on a vibrating screen that appeared to be healthy.
The resulting data indicated a problem, however, and caused the operation to discover a broken spring which had led to damage to the vibrating screen’s foundation. Catching the problem early saved the producer money in downtime and repair costs.
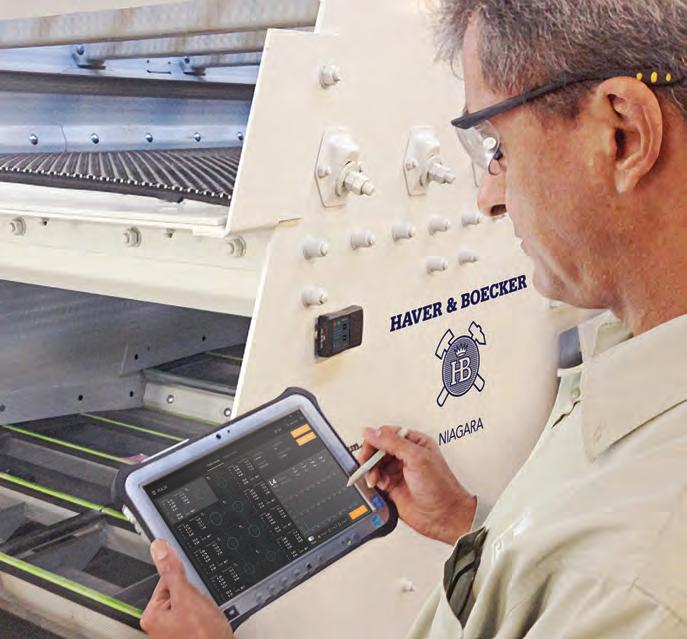
Plant simulation software Plant simulation tools offer a highlevel view of an entire operation’s efficiency. This helps optimise processes and look at opportunities for improvement in both existing sites and new mines or quarries for all mineral processing operations. The software also helps operations spot and fix bottlenecks.
Plant simulation programs take into account the equipment used throughout the plant, from material washers and conveyers to crushers and vibrating screens.
The operation’s existing setup, or a proposed setup, is entered into the program to understand and predict overall performance and plant flow.
The systems use scientific calculations to monitor input, output and waste piles, as well as to calculate mass and volumetric flow rates based on machine placement and machine-specific operating parameters.
The tool is also useful for insights into product specification or production rate changes — such as dry and wet crushing, screening and sorting — as the software can be used for pre-calculations.
A quick search will turn up a handful of brands of plant simulation software, but few are created by processing equipment OEMs.
Partnering with an OEM can allow for the most accurate simulations and enhanced features based on engineering expertise and application knowledge gained from actual site visits and understanding an operation’s challenges firsthand. AM
HAVER & BOECKER NIAGARA OFFERS DIAGNOSTIC TOOLS AND PRODUCT-SPECIFIC KNOWLEDGE.
1988
Industrial Flotation Specialists
Custom designed and manufactured to suit your requirements
SINCE 1988
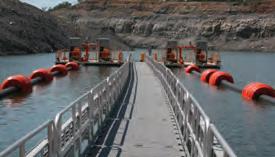
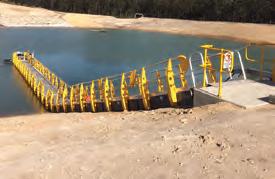
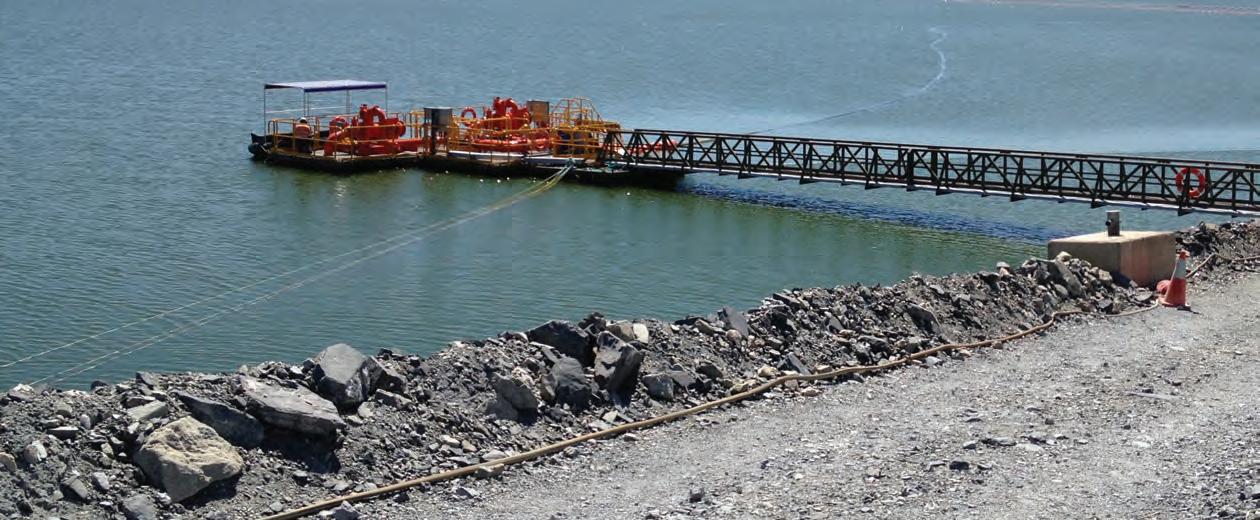
Pump Pontoons Pipe Floats Floating Walkways
All products manufactured in Australia Suppliers to the global major mining
companies & contractors
Aluminium gangway specialists Modular systems for easy installation 100% virgin PE materials used for
maximum UV protection and long life
Broad selection of products to suit all