RIO TINTO
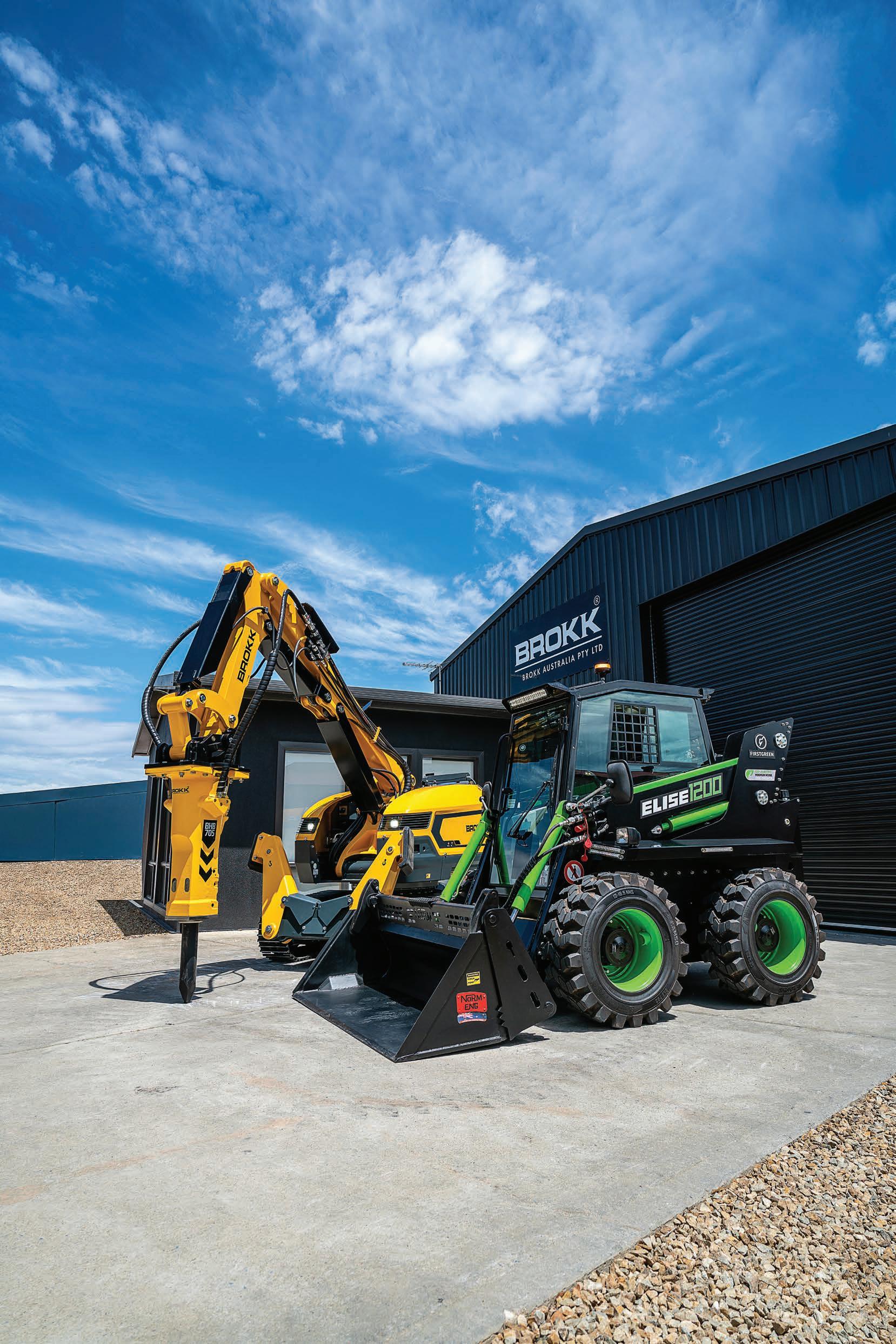
VOLUME 116/11 | DECEMBER 2024
COMMODITY SPOTLIGHT
INDUSTRY OUTLOOK
RIO TINTO
VOLUME 116/11 | DECEMBER 2024
COMMODITY SPOTLIGHT
INDUSTRY OUTLOOK
MINING EQUIPMENT CHARGES UP
United. Inspired.
Service agreements for underground and surface equipment designed to keep productivity levels up and costs down. With COP CARE, our technicians are scheduled to come to you for regular servicing following the factory service intervals, which reduces the risk of unexpected breakdowns. Speak to us today to find out what service agreement is available for your machine model!
AS
In order to look ahead, we have to know where we’ve come from. And the Australian mining industry’s legacy is one with a pulse.
Entire lives have been spent making mining what it is today, with Australians among the best and brightest in the world when it comes to cutting a new edge in what was previously thought impossible.
The advent of technologies once the stuff of science fiction has led the sector into new and ever safer and more efficient eras.
These technologies have been developed through partnerships both forged anew and over decades – between fledgling innovators and established industry giants alike.
Between them, the greatest minds in the country are looking towards a brighter and greener future, and Australian Mining looks eagerly with them.
In our December issue, we briefly press pause on an industry itching to advance and offer up a distillation of the excellence to come.
One company in pursuit of such excellence is Brokk Australia, a world-leading equipment supplier partnering with Firstgreen Industries to innovate emissions-free machinery.
Together, the companies’ electric equipment is helping to revolutionise mining operations, offering a cleaner and more cost-effective alternative to traditional diesel-powered machinery.
Elsewhere in this issue, SRK provides expert insights on what the mining industry can expect in 2025, examining the past year in the local and international sectors and assessing trends for the year ahead.
Looking at where the industry’s giants will tread in the coming year, we were on hand at the Melbourne Mining Club luncheon in October
CHIEF EXECUTIVE OFFICER
JOHN MURPHY
CHIEF OPERATING OFFICER CHRISTINE CLANCY
MANAGING EDITOR PAUL HAYES
EDITOR
TOM PARKER
Email: tom.parker@primecreative.com.au
ASSISTANT EDITOR
ALEXANDRA EASTWOOD
Email: alexandra.eastwood@primecreative.com.au
JOURNALISTS
OLIVIA THOMSON
Email: olivia.thomson@primecreative.com.au
KELSIE TIBBEN
where Rio Tinto Iron Ore chief executive officer Simon Trott divulged the company’s plans to revitalise its iron ore business.
The year ahead will also be defined by some of the Australian mining industry’s most vital events where premier original equipment manufacturers, mining companies and thought leaders will gather to share new innovations and drive the industry forward.
Known as Australia’s longest-running mining event, Asia Pacific’s International Mining Exhibition (AIMEX) is set to launch at a new home this year, with South Australia winning the bid to host.
We speak to AIMEX show runner Siobhan Rocks to discuss the move and what attendees can expect at the upcoming event.
The next iteration of the PNG Industrial and Mining Resources Exhibition and Conference is also gracing the stage in 2025, with Port Moresby preparing to glow, yet again, under the light of progress.
There’s much to look forward to in 2025 – a year that can be considered the next step in an industry preparing to push new frontiers for decades to come.
As this is the final issue of Australian Mining for 2024, I’d like to say thank you on behalf of the team for another great year and I invite you to join us in the next.
Happy reading.
Tom Parker Editor
Email: kelsie.tibben@primecreative.com.au
DYLAN BROWN
Email: dylan.brown@primecreative.com.au
CLIENT SUCCESS MANAGER
JANINE CLEMENTS
Tel: (02) 9439 7227
Email: janine.clements@primecreative.com.au
SALES MANAGER
JONATHAN DUCKETT
Tel: (02) 9439 7227 Mob: 0498 091 027
Email: jonathan.duckett@primecreative.com.au
ART DIRECTOR MICHELLE WESTON
michelle.weston@primecreative.com.au
SUBSCRIPTION
9690 8766
Brokk Australia is a world leading equipment supplier providing robotic, remote controlled machines to construction, tunnelling, mining and process customers.
As a fully-owned subsidiary of Brokk AB, this Australian company boasts a well-equipped workshop able to provide after-sales service, troubleshooting and operator training to ensure customer satisfaction that is reflected in production and profitability. Robust design in combination with an extensive range of attachments allow a single Brokk robot to perform various tasks such as oversize rock breaking, scaling, drilling, digging and shaft sinking. Brokk Australia is taking mining to a new level with improved safety, groundbreaking power and a wide range of unique attachments for the Australian mining industry.
Cover image: Brokk Australia
Melbourne Mining Club in October as Rio Tinto divulged plans to revitalise its iron
42 COMPANY PROFILE
Reaching golden heights
Australian Mining spoke with Westgold Resources managing director Wayne Bramwell about how the company plans to continue its success in 2025.
44 PROSPECT AWARDS
Innovation takes centre stage
s industries across the world push towards greater sustainability, Brokk Australia and Firstgreen Industries are helping to lead the charge within the mining sector.
36 INDUSTRY OUTLOOK
The next frontier in mine rehab
Dendra chief executive officer Susan Graham explains how digital technologies are changing the way ecosystem rehabilitation is being done in the Australian mining industry.
38 INDUSTRY OUTLOOK
E xpert insights for 2025
With the potential for declining interest rates and more geopolitical stability, SRK Consulting believes growth is on the horizon for the Australian mining industry.
Taking place as part of the WA Mining Conference and Exhibition for the first time, the 2024 Prospect Awards highlighted the resources sector’s best and brightest.
70 EFFICIENCY AND OPTIMISATION
Processing made efficient McLanahan’s recent partnership with a major miner has become a critical component in the expansion of a critical minerals project in Queensland.
72 EFFICIENCY AND OPTIMISATION
Engine overhaul slashes fuel consumption
Rapidly growing mining services firm National Group made a major investment in its fleet to support clients.
94 HAZARD AVOIDANCE
A new scope for stope Emesent’s Hovermap LHD has helped Byrnecut achieve near-real-time 3D stope hazard and volume assessments.
KEEP UP WITH THE LATEST EXECUTIVE MOVEMENTS ACROSS THE MINING SECTOR, FEATURING METSO, HASTINGS TECHNOLOGY METALS AND WESTGOLD.
Metso appointed Sami Takaluoma as the company’s new president and chief executive officer (CEO) in late October.
improved customer satisfaction, and its profitability has been clearly raised to a new level,” he said.
the quality of our Yangibana Project,” Hastings executive chairman Charles Lew said.
roles, most recently as general manager operational performance at Perenti.
Takaluoma commenced leadership duties on November 1, with thenpresident and CEO Pekka Vauramo continuing on until the end of the year to ensure a smooth transition.
Takaluoma has been with Metso since 1997 and has led Metso’s services business area since 2021. He has been a member of Metso’s leadership team since 2017.
Metso chair Kari Stadigh emphasised Takaluoma’s extensive experience with Metso’s businesses and customer industries in their selection.
“Sami has done an excellent job in leading the businesses and as a member of the leadership team over the past seven years,” Stadigh said.
“Under his leadership, Metso’s services and consumables businesses have grown and created significant value, especially after the merger of Metso and Outotec.
“The board is convinced that Sami is the right choice to lead Metso into its next phase.”
Stadigh, on behalf of the board, extended his thanks to Vauramo for his years of service to the company.
“Under Pekka’s leadership, Metso has evolved into an even stronger company, with a significantly enhanced culture and
“We wish Pekka all the best and success in his new phase of life.”
Takaluoma thanked the Metso board for the opportunity to lead the company.
“Having had the privilege of working for Metso for 27 years, I can confidently say that I know the company and understand our potential,” he said.
“With Metso’s long history and strong foundation in the aggregates and mining markets, we are excellently positioned to achieve industry leadership.
“I eagerly anticipate embarking on this journey to deliver even greater value to our customers and stakeholders, alongside my talented and dedicated colleagues.”
Hastings Technology Metals announced changes to its management and board structure as it advances the Yangibana rare earths and niobium project in Western Australia.
In a key appointment, Peter Phan has been named as Yangibana project director, bringing more than 30 years’ mining industry experience to the role.
He previously served as project director for Australian premium iron management (APIM), where he managed the $3 billion Ashburton channel iron deposits’ stage one development.
“Our ability to attract someone of Peter Phan’s calibre to the position of project director is a strong reflection on
“Peter brings considerable experience in mine project development and astute leadership capabilities.”
In addition to Phan’s appointment, Jean Claude Steinmetz was named chair of the project review committee, succeeding Bruce McFadzean, who has retired as a non-executive director.
“On behalf of the board, I would like to acknowledge Bruce’s contribution to Hastings over the last four years, we wish Bruce well in his future endeavours,” Lew said.
“It is pleasing to be able to appoint Jean Claude as chair of the project review committee, who has been on the Hastings’ board for over eight years.
“With more than 27 years’ experience in the plastic technical fibres and rare earth chemical industries, including as COO (chief operating officer) of Lynas Corporation, Jean Claude will bring both technical knowledge and experience to the project review committee.”
Westgold Resources announced two significant leadership appointments in October to support the company’s growth and optimisation strategy.
Aaron Rankine will take on the role of COO and will begin in the new year.
A mining engineer with over two decades of experience in Australia and overseas, Rankine has held various senior
Rankine also held general manager and operations manager positions at Barminco, which have equipped him with extensive expertise in underground operations across gold, copper, and nickel assets.
“I chose to join Westgold because of the amazing platform that has been built over many years by the dedicated people in the business, culminating in the recent acquisition of the Southern Goldfields assets,” Rankine said.
“This platform, and the team behind it, has created an opportunity to generate significant value,” he said.
Chalice Mining also announced changes to its board of directors, including a new member to the board.
Richard Hacker agreed to join the Chalice board, seeking election as a non-executive director in November. Hacker has been a member of the Chalice executive team for 17 years, taking on the role of chief financial officer and general manager – commercial and strategy.
Stephen McIntosh, an independent non-executive director at Chalice, has made the decision not to stand for reelection, stepping down from the board at the conclusion of the company’s annual general meeting on November 21. McIntosh has agreed to continue to advise Chalice, remaining on its technical committee AM
PROPRIETARY RUBBER AND COMPOSITE FORMULATIONS
OPTIMIZATION OF WEAR PARTS & PROCESS EFFICIENCY
TAILOR MADE PARTS
ASSET MANAGEMENT
INSTALLATION AND WEAR MONITORING PROGRAM
DESIGN SUPPORT
AUSTRALIAN MINING PRESENTS THE LATEST NEWS FROM THE BOARDROOM TO
RARE EARTHS ARE ESSENTIAL FOR CLEAN ENERGY TECHNOLOGIES SUCH AS ELECTRIC VEHICLES AND SOLAR PANELS.
Lynas Rare Earths has officially opened its state-of-the-art rare earths processing facility in Kalgoorlie, Western Australia.
First announced in 2019, the $800 million facility was delivered in less than two and a half years from the receipt of construction approvals.
The Kalgoorlie plant is expected to create around 115 direct jobs in the Goldfields region by processing ores from Lynas’ nearby Mt Weld mine to create a mixed rare earth carbonate.
elements are essential for clean energy technologies such as electric vehicles, solar panels and wind turbines, as well as advanced electronics, the defence industry and medical devices.
Minister for Resources and Northern Australia Madeleine King was on hand to open the facility, and said as the first rare earths processing facility in Australia and the largest
outside of China, the facility is globally significant.
“This opening is a big deal for Kalgoorlie, a huge deal for Western Australia and a massive step for Australia,” King said.
“Projects like the Lynas rare earths processing facility will deliver direct economic benefits to Australia while strengthening our sovereign capability.”
Lynas chief executive officer Amanda Lacaze said the project
AUSTRALIAN MINING GETS THE LATEST NEWS EVERY DAY, PROVIDING MINING PROFESSIONALS WITH UP-TO-THE-MINUTE INFORMATION ON SAFETY, NEWS AND TECHNOLOGY FOR THE AUSTRALIAN MINING AND RESOURCES INDUSTRY.
was ambitious, one that is foundational for the company’s future growth.
“To construct, commission and bring into production a facility of this scale in just over two and a half years is truly remarkable,” Lacaze said.
“I’m enormously proud of what we have achieved. The facility is fully commissioned and producing and we have a great production team in place.
“As the only significant ex-China producer of separated rare earths, Lynas plays an important role in the global rare earths supply chain.
NRW Holdings subsidiary NRW Civil & Mining has been awarded a development contract by BHP at the Jimblebar iron ore mine in Western Australia.
The contract, which is valued at around $109 million, includes various civil, building, mechanical, and electrical works aimed at supporting sustainable production at the mine.
The project scope includes bulk earthworks, the construction of permanent facilities, and the development of a new floodway.
Additionally, the contract involves the construction of a light vehicle access road, along with heavy and light vehicle standpipes and a washdown facility.
Further works include the realignment of a high-density polyethylene (HDPE) pipeline and the installation of a 33kV overhead powerline.
Completion is scheduled for the second quarter of 2026.
It will employ a workforce of up to 120 personnel and require the use of 55 pieces of plant and equipment.
This contract marks a continuation of NRW’s long-standing relationship with BHP, further expanding the company’s involvement in Pilbara mining infrastructure projects.
Jimblebar is one of BHP’s key operations in Western Australia, contributing significantly to the company’s iron ore output.
It has been in operation for just over 10 years and is located 40km east of Newman in the Pilbara region of WA. Jimblebar is an open-cut pit iron ore mine home to BHP’s first fully autonomous truck operation.
BHP has been using data and technology such as automation and artificial intelligence to further unlock growth opportunities and enhance their operating performance at Jimblebar.
The company is using autonomous trucks at some of its sites across Western Australia and Queensland and is extending this to the Spence and Escondida copper mines in Chile. At Jimblebar and Newman, truck automation has resulted in a 90 per cent reduction in heavy vehicle safety risks.
Horizon Minerals recently mined first ore at its Boorara gold project in WA.
Boorara contains over 1.5km of gold mineralisation striking northwest at 330° and is divided into three project areas, namely the southern Royal, central Crown Jewel and northern Regal deposits.
Horizon approved the development of Boorara in late July 2024 to mine a series of four open pits containing 1.24 million tonnes of ore.
Mining will continue over the next 14 months, with ore to be processed at Norton Gold Fields’ Paddington plant located 35km north of Kalgoorlie.
The processed ore is expected to generate up to $30 million in estimated free cashflow for Horizon at a $3600-per-ounce gold price.
“It is very pleasing that Boorara is on track for first ore delivery, with pouring of gold occurring in
Northern Star Resources reported a strong September quarter, with its gold sales reaching 393,890 ounces (oz) at an all-in sustaining cost (AISC) of $2082/oz.
“We continue to deliver consistently strong operational results across all three production centres during the September quarter,” Northern Star managing director Stuart Tonkin said.
“As a result of the positive start into FY25 (2024–25 financial year), we are confident we will achieve our full-year production and cost
guidance, providing shareholders the continued benefits of current higher gold prices.”
The company’s Kalgoorlie production centre saw the highest gold sales at 204,981oz, with an AISC of $1997/oz.
Yandal followed with 129,278oz sold at $2237/oz, while Pogo delivered 59,631oz at $1367/oz after completing major mill works.
“We generated net mine cash flow of $122 million while continuing our returns-focused capital investment program,” Tonkin said.
Australia’s first R 9400 E!
Liebherr-Australia
Scan here to watch now!
Step into the future of mining with Fortescue and Liebherr as they pioneer electrification in Australia's mining industry. Highlighting our groundbreaking partnership and the deployment of Australia’s first electric excavator, the Liebherr R 9400 E.
THE DUBBO PROJECT IS POISED TO PLAY AN IMPORTANT ROLE IN SUPPLYING CRITICAL MINERALS.
Australian Strategic Materials (ASM) has received a $5 million grant from the Federal Government for its Dubbo critical minerals project in New South
the Federal Government’s International Partnerships in Critical Minerals program, which provides critical minerals businesses up to $20 million in funding to grow end-to-end supply chains with international partners.
The grant funding will be matched by ASM and be used to find more efficient methods of refining rare earths at Dubbo and its processing plant.
earths is important for our sovereign capabilities and will help our trading partners meet their economic, national security and emission reduction commitments,” Federal Resources Minister Madeleine King said.
The rare earths options assessment and pilot program will the grant.
“This funding recognises the Dubbo project’s national and international strategic importance,” Smith said.
“With this funding, we will be able to undertake important and several rare earth elements. Dubbo is expected to deliver up to 1000 local jobs during the construction phase and about 270 jobs during the operational phase, with a final investment decision targeted for the first half of 2026.
Gippsland Critical Minerals (GCM) has confirmed the Victorian Government has greenlit its Fingerboards rare earths project in Glenaladale.
Retention and exploration licences have been granted for the project, which will have a revised scope and stronger community engagement since it was originally tabled in 2023.
The Victorian Government also indicated that several exploration license applications made by GCM would be included in additional mining exclusion zones around the retention license areas.
GCM has made a number of changes to rescope the new Fingerboards project, which will include:
• the establishment of a mining exclusion or ‘buffer’ zone of approximately 1.5km from any mining to the existing Lindenow Valley horticultural area to safeguard local agriculture
• the fencing off and establishing of conservation areas in gullies to substantially reduce impacts on native vegetation
• significantly increasing investment in community and First Nations engagement
• ensuring positive outcomes for the local community through benefit sharing, including economic and employment opportunities.
Recently-appointed GCM chief executive officer Michelle Wood said Fingerboards will be a ‘world class’ deposit.
“After working to develop the Fingerboards opportunity over the past decade, we knew we needed to do things differently to create a project that meets community expectations,” Wood said.
“The licences have been renewed for an improved project
that protects local agriculture and jobs in the Lindenow Valley, creates new employment opportunities through training and apprenticeships, and better protects the environment for future generations.
“There is still a great deal to do to determine the final shape of the project.
“This includes a genuine commitment to listen and engage with the community and to work with local people on community benefit sharing and a wide range of technical and environmental studies.”
AUSTRALIAN MINING WAS ON HAND AT THE MELBOURNE MINING CLUB WHEN SIMON TROTT LAID OUT RIO TINTO’S PLANS TO REVITALISE ITS IRON ORE BUSINESS.
As 2024 comes to a close, Rio Tinto is looking to the future, announcing multiple changes to its global portfolio.
Rio is set to finalise its $US6.7 billion ($10.3 billion) acquisition of Arcadium Lithium in mid-2025, in a move that will position the major as the world’s third largest lithium supplier, sitting behind Albemarle and Sociedad Química y Minera de Chile S.A. (SQM).
Another commodity at the forefront of Rio’s future plans is iron ore, a vital component for steel and stainlesssteel manufacturing.
In the September 2024 quarter, Rio delivered a one per cent uplift in iron ore production while the company’s production of its lower-grade ore – also known as SP10 – continued to rise.
The boost in production was a win in the face of pressure from China’s steel market dampening demand prospects.
However, Rio’s output of the highergrade Pilbara Blend – the global iron ore sector’s most recognisable product – decreased, with a 12 per cent decline
in Pilbara Blend lump production and an eight per cent drop in Pilbara Blend fines production.
Pilbara Blend is China’s preferred iron ore product, with its highergrade makeup contributing to lower greenhouse gas emissions in the steelmaking process. While SP10 comes from the same orebodies as the Pilbara Blend, it’s considered a lowergrade product.
Rio said SP10 production levels are expected to remain elevated as replacement projects are delivered, prompting the major to evaluate its iron ore business.
Rio Tinto iron ore chief executive officer Simon Trott shed light on the review at a Melbourne Mining Club luncheon held in October.
Trott described Rio’s iron ore review as an outline of what products the company will take to the market.
The strategy has three main drivers behind it: Rio’s Pilbara operations in WA, its Iron Ore Company of Canada, and the Simandou iron ore project in Guinea.
“We set up port-side trading in China where we were able to blend product from different countries, so from the Pilbara operations, the Iron Ore Company of Canada, and thirdparty ores,” Trott said.
“Obviously, Simandou coming on gives us another value in the portfolio.”
Rio’s future product strategy will consider the blending opportunities it will have in the next 12 to 18 months when the Simandou mine commences production, complementing Rio’s iron ore supplies out of WA and Canada.
The company also needs to consider the current economic landscape, which could pertain to the capital, operating or closure costs at a particular time.
“We need to ask the question, ‘Are we best utilising the orebodies for the current settings?’” Trott said.
“There’s probably two parts: what areas do you mine in terms of what products do you mine and how do you package those iron units for the market? We currently sell different products. Should some of those be joined together and sold as one product (or) should we disaggregate some of them because we already blend different ore sources?
“Pilbara Blend in some form will remain a mainstay of our product offering. It’s around how we best package the overall portfolio.”
Global competitiveness
Simandou is known as the world’s largest untapped high-grade iron ore deposit.
While concerns have been raised as to whether Simandou supply has a place in the global market, Trott pointed to the scale of the seaborne iron ore market.
“Seaborne iron ore sees 1.6 billion tonnes moved every year,” he said.
“Every day, we mine an equivalent amount of earth that would fill all
of Melbourne’s Marvel Stadium. We’re moving some 3500 people. We fly from Perth to the Pilbara and back each and every day, (and have) 2000km of rail (transportation). It’s an amazing business and it’s an industry of scale.
“I think the thing that has been missed is just the size of 1.6 billion tonnes every single year.
“As Simandou comes online at the end of next year and ramps up to a target of 120Mt, the world’s going to need those iron units.
“We’re going to need Simandou and more resources like it.”
To meet the growing iron ore demand, Rio is hard at work developing the Rhodes Ridge project – billed as one of the world’s best undeveloped iron ore deposits – and the Western Range project. Both are located in WA.
While Trott acknowledged Rio has faced challenges with costs, delays and regulatory approvals in the last year, the company remains on track to deliver one new iron ore mine per year for the rest of the decade.
“Some of our existing operations are closer to the end of their life rather than the beginning, so we need a new mine per year,” Trott said. “Then we bridge across to Rhodes Ridge at the end of this decade.
“It’s gotten harder in terms of developing new operations. I think that’s true in iron ore and all commodities. We’re on track in terms of Western Range, and the next tranche of mines are on track.
Rio hopes to complete a prefeasibility study into its Rhodes Ridge project by the end of 2025. This will analyse the production of up to 40 million tonnes annually, with the company planning to spend more than $400 million on exploration between 2024 and 2028 before first ore is expected by the end of the decade.
Rio has been developing Western Range in partnership with China Baowu Steel Group Co. Ltd. First ore from the project was achieved in June.
According to data from the Federal Government, Australia is ranked first
for iron ore production and resources, producing 35 per cent of the world’s iron ore and holding 31 per cent of the world’s iron ore resources.
On the demand side, Chinese consumption has been volatile, but Trott remains confident about the longterm prospects.
“There were headwinds to iron ore demand in the major steel-producing regions at the start of the quarter,” Rio said in its September 2024 quarterly report. “However, Chinese demand improved in September following completion of maintenance at steel mills.
“Iron ore inventories at Chinese ports were flat, while China’s steel exports
fell slightly during the quarter, but remained higher than a year ago.”
Trott elaborated further.
“China is at a structural peak in terms of steel demand,” he said.
“All economies go through an initial phase where they consume significant steel for new bridges, houses, roads, so China is at that level now. But the demand is really strong, so iron ore will remain a large and really profitable market for us.
“We’re not going to see the same growth rates out of China in terms of steel demand in the next decade as we have in this last decade, so that means we’ve got to really focus on our business settings and make sure we get those right.” AM
CLOSE TO 10,000 DELEGATES PACKED THE FLOOR OF THE ICC SYDNEY IN LATE OCTOBER AS IMARC 2024 FOSTERED MINING DEVELOPMENTS, INNOVATIONS AND PARTNERSHIPS.
The International Mining and Resources Conference and Expo (IMARC) 2024 was one for the books.
This year’s conference saw more than 9000 delegates, 600 speakers and 500 exhibitors on-site, positioning IMARC 2024 as the premier platform for the global mining and resources sector.
As always, there were some big names at the event.
Federal Minister for Resources
Madeleine King and NSW Minister for Finance and Natural Resources
Courtney Houssos addressed attendees on the opening day, unveiling policies aimed at fostering sustainable growth, reinforcing Australia’s critical mineral supply chains, and supporting the country’s path toward netzero emissions.
“The resources sector is crucial to Australia’s prosperity and our ability to meet net-zero targets,” King said.
Houssos echoed these sentiments, emphasising the NSW Government’s focus on energy opportunities and partnerships to attract investment in green industries.
“NSW is on the cusp of realising the opportunities in energy, but we know we’re not alone in the global race,” she said.
“We will need six times the amount of critical minerals currently mined to meet net-zero commitments – and we know all of this can be found in NSW.”
People on the ground also appreciated the fact the event also looked beyond Australia’s borders, allowing companies and their people to export their mining expertise and knowledge.
“(IMARC works for us because) we’re growing globally and this is an international show,” Terrain Tamer general manager Brent Hutchinson told Australian Mining on the expo floor.
“It’s Australia’s true international mining show.”
Elsewhere on the expo floor, Colterlec national general manager Shahwar Khan emphasised the need to provide delegates with “proof of concept”.
That’s why Colterlec’s stand featured a ute loaded with a full spectrum of Moxa products attendees could see up close.
Metso also had an active presence during IMARC, with two topical presentations on green iron and critical minerals.
WE WILL NEED SIX TIMES THE AMOUNT OF CRITICAL MINERALS CURRENTLY MINED TO MEET NET-ZERO COMMITMENTS – AND WE KNOW ALL OF THIS CAN BE FOUND IN NSW.”
Metso’s solutions attracted various visitors to the stand, including several customers and dignitaries. Metso experts Timo Haimi and Duncan Wyatt were also on various panels during the three-day event.
Day two of IMARC 2024 was marked by hearty deals, debates and discussions.
A new memorandum of understanding between Hexagon and PT Petronesia Benimel was one of the day’s many highlights, while hundreds of meetings between miners and investors took place at IMARC Connect throughout the afternoon.
“We are thrilled with the momentum and engagement we’re seeing at IMARC this year,” IMARC chief operating officer Anita Richards said.
“From insightful discussions to our strong sales performance for 2025, IMARC continues to cement its place as the go-to event for shaping the future of mining.”
This kind of collaboration was one of the key themes running through of the event.
FLSmidth Asia Pacific regional president, sales and services Jason Elks highlighted the need for partnerships when taking part in a panel discussion, ‘Have we got management buy-in yet?
CLOSE TO 10,000 DELEGATES PACKED THE
The value of proposition for innovation and modernisation’.
Elks discussed the notion of a disconnect between corporate and operational levels when it comes to innovation in the mining industry, outlining the dissonance between corporate understanding the need for innovation and operations being reluctant to pause for the time required to make those changes.
“Operations wants to extract the most material today using yesterday’s technology,” he said. “We have decision-makers that don’t understand the incremental change that 2–3 per cent improvements (to production) will bring.
“No one takes the time to do that maths, but it’s big maths.
“(Miners need to) allow your operation the time to consider these concepts.”
This kind of collaboration was echoed by Komatsu when discussing a project with a client, Glencore, that
“We are successful in this because we are fully embedded within that customer’s organisation,”
Komatsu national manager – mining optimisation Barry Pamenter told Australian Mining. “We get to that customer’s site … we become part of their team.”
Pamenter was clear that, for Komatsu, it’s not about just selling a product, it’s about a partnership.
“It’s not successful without that partnership,” he said.
The networking opportunities on offer at IMARC 2024 was a key
business development manager Roxanne Bekker.
“The networking is very valuable,” she said. “I always tend to catch up with the same clients coming to IMARC, touching base and really finding out what the new problems in the industry are.”
MASPRO national sales manager Peter Lowenhoff echoed Bekker’s enthusiasm.
“I’ve had some good conversations with a couple of different companies, getting an understanding of their whole fleet in areas and even different mines
As IMARC 2024 wrapped up on day three, Richards thanked all involved for their efforts.
“As we celebrate the remarkable success of another IMARC, I want to extend my heartfelt gratitude to our founding partners Austmine, AusIMM and Mines and Money, and our host partner the NSW Government, for their unwavering support,” she said.
The 2025 event has already sold around 70 per cent of exhibition space, with companies keen to get involved for another year.
IMARC 2025 returns to Sydney
FIRSTGREEN INDUSTRIES HAS PIONEERED A RANGE OF ELECTRIC MACHINERY SPECIFICALLY DESIGNED FOR MINING AND OTHER HEAVY INDUSTRIES.
AS INDUSTRIES ACROSS THE WORLD PUSH TOWARDS GREATER SUSTAINABILITY, BROKK AUSTRALIA AND FIRSTGREEN INDUSTRIES ARE HELPING TO LEAD THE CHARGE WITHIN THE MINING SECTOR.
In the mining industry’s ongoing quest for sustainability, Brokk Australia and its partner Firstgreen Industries are taking significant steps toward reducing emissions while improving safety and productivity.
Brokk Australia sales manager Stefan Mace and Firstgreen Industries regional head of sales Jan Otta spoke with Australian Mining about how their companies’ electric equipment is helping to revolutionise mining operations, offering a cleaner and more cost-effective alternative to traditional diesel-powered machinery.
A new era of electric machinery
Czech-based company Firstgreen Industries has pioneered a range of electric machinery specifically designed for mining and other heavy industries.
These machines are built around a unique battery system with three electric motors; two are dedicated to drive functions, while the other manages hydraulics.
“We designed the machine around the battery,” Otta told Australian Mining “It’s a patented system where you have three electric motors, and two of them
are responsible for drive and direct drive, and the third runs the hydraulics.
“We also have our state-of-the-art software which allows us to get the most battery life out of the machine.
“Not only did we bring this aspect of zero CO2 emissions to the market, but we also help to reduce the operation costs significantly while increasing the safety of the operators.”
The advanced software powering Firstgreen Industries machines enables operators to work for approximately six hours on a single charge, which can be fully restored for just $10, compared to the higher fuel costs associated with diesel equipment.
“You can work around six hours on a single charge for $10, or you can spend money on 60 litres on diesel,” Otta said.
“We save 90 per cent of the corporation cost in general, so even though we are slightly more expensive than our diesel competition, your return on investment is typically somewhere around 12 to 18 months.”
Safety in mining is paramount, and Firstgreen Industries’ equipment
incorporates remote-controlled operation to enhance worker protection.
Operators can control machines via radio or Bluetooth, keeping them at a safe distance from hazardous sites.
This feature also enables tasks to be performed continuously without the need for close supervision – such as cleaning under conveyor belts while they’re still in motion – further improving productivity.
“With remote operation, we not only keep people out of harm’s way, but we’re also able to achieve higher productivity levels,” Otta said.
Reducing machine downtime is another major focus. Battery changes are streamlined to take just five minutes, enabling 24–7 operation with minimal interruptions.
Firstgreen Industries’ electric machinery also has fewer moving parts than diesel-powered equipment, resulting in less maintenance and lower service costs.
Beyond operational efficiency, Firstgreen Industries’ technology aligns with the environmental, social, and governance (ESG) goals
that many mining companies are increasingly prioritising.
With each Firstgreen Industries machine capable of offsetting approximately 18 tonnes of CO2 annually, companies can make significant strides toward their sustainability targets.
“Not only are our customers saving money, they are also fulfilling their ESG goals, which are important for the big players on the market,” Otta said.
This approach represents a shift in the industry, where achieving ESG goals is no longer seen solely as a business cost but as a path to efficiency and reduced expenses.
Brokk Australia’s expanding portfolio
Brokk Australia, known for its remotecontrolled demolition equipment, only recently expanded its product offerings to include Firstgreen Industries’ electric machinery.
Mace said this partnership complements Brokk’s lineup, which also includes electric-powered Twinca dumpers and Sherpa mini loaders.
“We aim to meet our clients’ needs with an array of electric solutions that
OUR GOAL IS TO HELP CLIENTS MAKE SMART INVESTMENTS IN EQUIPMENT THAT NOT ONLY MEET THEIR OPERATIONAL NEEDS BUT ALSO ALIGN WITH THEIR LONG-TERM SUSTAINABILITY GOALS.”
provide flexibility and environmental benefits,” he said.
Brokk’s electric machines, used in mining, construction, and nuclear applications, offer both diesel and electric options, depending on the operational requirements.
With over 700 Firstgreen Industries units sold across 60 countries, the machinery has proven popular for its low vibration, easy handling, and comfortable operator experience.
“Customer feedback is typically very good,” Otta said. “Customers appreciate the low maintenance and cost reduction, and that it’s simply a nice machine to be in.
“When you have an operator who spends long hours in the machine, they really appreciate that there’s no vibration, and that it’s a very smooth operation.
“We’ve built these machines to be versatile, allowing operators to adjust the controls to their preferred settings. This adaptability is one reason we receive such positive feedback.”
Firstgreen Industries is headquartered in Velka Dobra near Prague in the Czech Republic where it is innovating new designs to prioritise safety, efficiency, sustainability and employee comfort.
The company’s facilities are equipped with state-of-the-art production lines, warehouses and a progressive research and development department.
“We’re a family-owned business that built our distribution network from the ground up,” Otta said. “All of our dealers hold recommended spare parts to be able to support our customers locally.
“Brokk Australia is our dedicated partner for Australia, so this way we prevent customers waiting for the shipping of the components from Czech Republic.”
“While electric solutions are ideal for most applications, diesel still has its role where charging isn’t feasible,” Otta said.
balancing components. This keeps the machines as lightweight and efficient as possible.
The growing trend toward electric and sustainable machinery in the mining sector is undeniable, yet diesel-powered equipment will still have its place in some remote locations without sufficient power infrastructure.
So Brokk Australia and Firstgreen Industries are pioneering electrification in areas where these solutions can thrive. For example, the skid steer batteries offer a unique advantage, acting as built-in counterweights, reducing the need for additional
Mace said Brokk Australia’s participation in events like the International Mining and Resources Conference isn’t just about showcasing technology; it’s about redefining how mining companies approach safety, sustainability, and efficiency.
“Our goal is to help clients make smart investments in equipment that not only meet their operational needs but also align with their long-term sustainability goals,” Mace said. With innovative electric solutions like those from Firstgreen Industries, Brokk Australia is positioned at the forefront of a more sustainable mining future. AM
IN DECEMBER 2023, FORTESCUE MOVED ONE STEP CLOSER TO ITS DECARBONISATION GOAL WITH THE DEPLOYMENT OF A LIEBHERR R 9400 E, AUSTRALIA’S FIRST OPERATIONAL ELECTRIC EXCAVATOR ON A MINE SITE.
Fortescue and Liebherr are no strangers to making history.
Such was the case in December 2023 when Fortescue deployed Australia’s first operational electric R 9400 excavator from Liebherr in backhoe configuration, a significant step for sustainable mining.
Since then, additional R 9400 E excavators have been commissioned across Fortescue sites in Western Australia.
Fortescue and Liebherr recently announced they will deploy 475 Liebherr battery-electric haul trucks,
electric excavators and battery-powered dozers across Fortescue’s Western Australian iron ore operations, creating an all-electric, zero-emission ecosystem of mining machinery to help eliminate fossil fuels.
The haul trucks and dozers will be powered by Fortescue’s batteryelectric power system developed inhouse by Fortescue Zero – Fortescue’s technology arm.
“Our collaboration is all about pushing the boundaries of mining innovation,” Liebherr Australia key account manager Olivier Laurent said.
“With the introduction of the electric R 9400, we’re entering a new era of
efficiency and sustainability, and this is just the beginning.”
Known for its long-standing success with Liebherr’s R 9400 excavators, which dates back to 2011, Fortescue is now transitioning to electric machinery, advancing both mining efficiency and environmental responsibility.
This trust underscores Fortescue’s commitment to highperformance equipment that meets – and exceeds – demanding operational requirements.
The R 9400 has been a standout in the mining sector for the past six years, with over 130 units operating globally across various commodities.
Its advanced design enables more material to be moved with less energy, making it one of the most energyefficient hydraulic excavators in Liebherr’s portfolio. In Australia, it’s a go-to for iron ore, gold and coal mining.
Equipped with a 24m³ backhoe bucket – the largest in its class – the R 9400 boosts productivity by moving extra tonnes of material per pass.
Fortescue’s ambitious plan to decarbonise its Australian iron ore operations and achieve ‘Real Zero’ terrestrial emissions by 2030 is making significant progress with the deployment of multiple R 9400 E excavators, and Fortescue’s wider investment in
SINCE INTRODUCING THE LIEBHERR R 9400 EXCAVATOR IN 2011, FORTESCUE HAS CONSISTENTLY RELIED ON ITS PERFORMANCE AND PRODUCTIVITY.
decarbonisation technologies and renewable energy infrastructure.
The R 9400 E is powered by a 6.6 kilovolt substation, utilising over 2km of high-voltage trailing cable.
The excavator also uses the automated, hydraulically driven Liebherr cable reel, an automated, hydraulically driven solution to manage the excavator’s electric cable during operation. Liebherr’s cable reel offers
approximately 300m of free cable for enhanced operational efficiency.
This move is not just a step-change but a transformative leap towards a sustainable mining model.
Fortescue has experienced a number of benefits since introducing the R 9400 E, including a reduction in diesel consumption, fewer component replacements, a longer lifespan and increased breakout force.
Project executive general manager Paul Murphy said. “It’s a bold step in ensuring that future generations will inherit a mining industry redefined by innovation and responsibility.
“The R 9400 E and this project with Fortescue exemplifies our commitment
will inherit a mining industry redefined by innovation and responsibility.”
Fortescue and Liebherr continue to lead the industry with their innovative solutions and are committed to having a large-scale zero-emission mining ecosystem operational by 2030. AM
• Robust with an impressive reach and fully automated functions
• Lowest feed height in the industry, providing maximum versatility
• With standard designs up to 1500 MTPH eliminate the need for additional conveying equipment
• Stockpile material in flat concentric rows to eliminate segregation with the Telescopic Luffing Technology. It can travel in a 270-degree arc to Stockpile 30% larger volumes of materials
EPIROC HAS THE ELECTRIFICATION OFFERINGS TO ENABLE THE MINING INDUSTRY’S DECARBONISATION.
When the Federal Government introduced the reformed Safeguard Mechanism in 2023, it accelerated the need for decarbonisation in heavy industries such as mining.
Under the Safeguard Mechanism, companies that emit more than 100,000 tonnes of CO2-equivalent (CO2-e) per financial year are required to buy Australian carbon credit units (ACCUs) to offset their carbon footprint.
In the 2023–24 financial year, ACCUs could be bought for $75 per tonne for every tonne a company goes above its 100,000-tonne CO2-e cap. This increases annually with the consumer price index (CPI), plus two per cent.
To insulate themselves from the Safeguard Mechanism now and into the future, mining companies are turning to environmentally-conscious machinery such as Epiroc’s range of electricpowered drills, loaders, trucks and associated infrastructure.
With innovation coursing through its veins, Epiroc is on a mission to support the decarbonisation of the Australian –
and global – mining industry, and the timing couldn’t be more perfect.
Electrification is gradually increasing in popularity in the underground mining sector as original equipment manufacturers (OEMs) prove the capability of electrified machinery, not just in limiting carbon emissions but by also boosting productivity and safety.
Epiroc’s electrification portfolio includes a range of drill rigs, including battery-electric jumbos (Epiroc Boomer range), bolting rigs (Epiroc Boltec range) and production drills (Epiroc Simba range).
These machines can be bought new or Epiroc can retrofit an existing diesel machine with battery capability. This can also coincide with a zero-hour rebuild.
To best facilitate an electric transition, Epiroc works closely with its mining customers to understand their barriers and how to best overcome them, before building out a roadmap that doesn’t compromise operational productivity.
“Customers have different strategies around their electrification journey, and it’s important for Epiroc to be able to come up with an agile solution that isn’t just about supplying a new machine,”
Epiroc Australia electrification support lead Karl Van Mourik said.
“A solution could involve scoping out a machine and considering what a battery conversion might look like at the midlife stage. Maybe their infrastructure isn’t quite ready but they can see an opportunity down the track, and they can tie that in with a new batteryelectric machine.
“There are many different avenues to implementing batteryelectric technologies.”
Van Mourik outlined the advantages of deploying a battery-electric truck to an underground mine.
“Battery-electric vehicles typically have a higher speed-on-grade because of the efficiency of electric motors and less loss incurred through the drive train,” he said. “So once the mine truck is integrated into the cycle times and patterns of the existing fleet, it has the potential to boost productivity.
“An electric truck provides a solution for any mine that has a problem with heat, diesel particulates, noise, vibration, or other environmental factors that are affecting their working group.
“As mines get deeper, maybe an operator needs to go electric because the environmental conditions in the mine dictate that.”
Epiroc has also expanded its electric drill range for surface mining, with the OEM recently launching new electric Pit Viper rotary blasthole drill rigs and SmartROC surface drill rigs.
The Pit Viper 271 E can drill singlepass holes up to 18m with diameters of up to 311mm, while the Pit Viper 275 E can handle multi-pass holes up to 76m with diameters reaching 270mm.
Both drills can be configured with Epiroc’s XC (Xtra Capacity) package to provide 85,000 pounds (38.5 tonnes) of bit load capacity, ensuring operators don’t experience decreased productivity.
The new models in the electric Pit Viper range are the PV231 E and PV235 E, which are suited to ‘one size smaller’ drilling operations.
These platform drills come fitted with Epiroc’s suite of automation features, as well as smart functionalities that enhance operational safety, accuracy and productivity, all the while eliminating live work.
Epiroc also showcased a demonstrator of its first ever down-the-hole SmartROC D65 battery-electric drill rig at MINExpo 2024 in Las Vegas, US.
The SmartROC D65 batteryelectric demonstrator was based on the well-proven SmartROC D65 surface drill rig, which has a 110–229mm hole diameter enabling it to drill entire drill patterns and high-quality blastholes with accuracy and precision.
The SmartROC D65 is controlled via an advanced rig control system displayed on a touch screen, with the interface providing users with information such as drilling parameters and real-time MWD (measure while drilling) data, increasing efficiency across the operation.
While the bespoke benefits of these electric machines speak for themselves, customers taking the electrification plunge for the first time may be unsure about where to start.
Luckily, Epiroc has support networks available to support these customers along their journey.
The OEM offers integrated solutions for an electric mine, incorporating infrastructure, chargers and other consulting services like electrical audits. Epiroc can also provide guidance through its Batteries as a Service (BaaS) offering, which removes some of the
obstacles that come with making the electric transition.
BaaS moves the upfront costs of batteries from capital expenditure (capex) to operational expenditure (opex), with Epiroc taking full responsibility for the batteries, from certification to maintenance and technology upgrades. BaaS is also available on gear from other OEMs that use Epiroc batteries.
Van Mourik said BaaS ensures batteries are maintained with the same vigilance and precision as Epiroc would maintain its machinery.
“The service is done by us,” he said. “We’ll ensure that you’ve always got the latest technology because as we own the battery, we’ll do all the updates for you as battery technologies improve.
“And when it comes to maintenance, once you reach a certain cut-off point for battery usage we’ll then install a new battery, guaranteeing battery usage and reducing unnecessary downtime associated with reactive battery changeouts.”
Epiroc also offers electric optionality, which can come in the form of a battery conversion and sees a diesel machine retrofitted with electric capability.
“Miners understand they need to get the full lifetime out of their assets,” Epiroc product manager –drilling solutions Hans Hilden told Australian Mining.
“And because Australian miners increasingly want to standardise their equipment, we expect more battery
EPIROC’S PORTFOLIO INCLUDES A RANGE OF ELECTRIC DRILL RIGS SUCH AS THE SMARTROC T35 E.
and electric conversions to occur as the mining sector decarbonises.”
While the Australian mining sector has been slower to the electrification party, Hilden believes it won’t take long to ignite an electric evolution.
“Once we get more proven customer cases, it can open the door for electric technologies to become more accepted in Australia and in mining as well,” he said. “I’ve seen that happen in the
automation field of mining equipment, and I expect it to be the same case with electrification.”
Epiroc understands electrification requires more than the supply of electric mining equipment and machinery.
Backed by more than a century of innovation, the OEM has the expertisto aid customers on their electrification journey, no matter what stage they’re at in the transition. AM
Parker Australia’s SMART electrification technology is helping mining companies grab the energy transition with both hands, with electricpowered systems capable of cutting carbon emissions, improving efficiencies and slashing operational costs.
Scott Addison and Andrew Rowley from Parker’s electrification team spoke to Australian Mining about how the company’s approach to electrification is revolutionising the sector.
“Parker’s SMART electrification revolves around three core pillars: integrated, connected and efficient systems,” Addison said.
“These pillars guide Parker’s product design and implementation of electrification solutions for various mining applications, from vehicles to drill rigs.”
Addison said the efficiencies and power density of Parker’s GVM PMAC liquid cooled motors are what truly sets the company’s solutions apart from traditional internal combustion engines.
“When you compare the efficiencies of our liquid-cooled Parker GVM motors, which typically operate at 94–96 per cent efficiency, and digital inverters, which are about 98 per cent efficient, it becomes clear why these systems are superior,” he said.
“In contrast, internal combustion engines typically experience losses
ranging from 20 per cent to 30 per cent, making them highly inefficient in conjunction with the continued diesel and ongoing maintenance costs.”
The key to maximising the benefits of mining electrification lies in optimising the entire system.
Parker’s designs integrate multiple layers of technology for electric power takeoff (ePTO) and traction applications, including hydraulic motion control, GVM PMAC electric motors and GVI inverters for motor control, which are all managed through Parker’s IQAN digital control platform.
This holistic approach ensures that every component of the system works seamlessly together, creating a more efficient, reliable and sustainable solution for mining operations.
A primary driver behind the adoption of Parker’s SMART electrification technology is the pressing need to reduce emissions.
But, like any nascent industry, electrification has faced its challenges.
“The rapid advancement of electrification technology has outpaced the Australian labour market’s ability to keep up,” Addison said. “Many companies and service providers lack the necessary skill sets to work with these advanced systems.”
The skills gap is a hurdle for the sector, as tradespeople and engineers need specialised knowledge to work on electrified equipment.
While technical institutes such as TAFE are starting to offer courses
on electrification, there remains a gap in licensing and formal training, particularly at the university level.
Addison expressed concern that the mining industry is “playing catchup” when it comes to understanding and implementing this cuttingedge technology.
Despite these challenges, Parker Australia has positioned itself ahead of the curve, acting as both a solutions provider and a consultant to mining companies about the future of electrification.
Addison explained that Parker’s team brings a wealth of real-world application knowledge, working closely with clients to guide them through the adoption of electrification.
“We’re very much seen as a consultant, but also as an engineering partner as well,” Addison said.
“We help clients define specifications, conduct engineering
calculations, and model outcomes to ensure a smooth and successful transition, providing customers with the confidence to move forward with Parker electrification solutions.”
Parker’s approach is highly collaborative, and the company encourages clients to provide essential data, such as duty cycles of operation, to ensure the electrification solution is perfectly tailored to their needs.
“We engage with customers to make sure they understand how the system functions and how they can achieve the highest levels of performance and efficiencies for their machines,” Addison said.
This partnership extends to providing training and resources, ensuring companies are well-equipped to maintain and operate their electrified systems.
While the initial capital expenditure for electrification technology may be higher than traditional diesel-powered systems, Rowley said there were many long-term benefits.
“Your ongoing maintenance costs are significantly lower with electrified systems, and companies eliminate the need for fuel, oils and other consumables, leading to significant savings over time,” Rowley said.
“Although the payback period may be longer – typically around three to five years – companies see substantial cost reductions in the long term.”
Beyond cost savings, the sustainability benefits of Parker’s smart electrification solutions are clear.
“With our solutions, operators can achieve zero emissions in underground applications, and by eliminating diesel usage, operators can mitigate noise pollution and diesel particulate emissions,” Rowley said.
“This improves the operating environment of a underground mine and helps miners meet stringent regulatory requirements.”
Despite the clear advantages, some companies remain hesitant to embrace electrification, citing cost concerns and uncertainty about the technology.
But Addison and Rowley are seeing the industry come around.
“The next generation of engineers are driving new conversations about our energy future,” Addison said.
“These engineers, trained in mechatronics and electrical engineering, are questioning the status quo and pushing for more efficient, sustainable solutions.”
Parker is committed to helping companies overcome their hesitations by providing real-world examples and proven case studies.
“We show them what we’ve done with similar applications, and it gives them the confidence to move forward,” Addison said.
“With more companies seeing the long-term benefits of electrification, we expect the industry to continue shifting towards cleaner, more efficient technologies.”
As the mining sector grapples with the need to reduce emissions and improve efficiency, Parker Australia’s
SMART electrification technology offers a clear path forward. By focusing on integrated, connected, and efficient systems, Parker is helping mining companies transition to electricpowered operations that are not only more sustainable but also more costeffective in the long run. AM
ABB’S ‘MINING’S MOMENT’ REPORT HIGHLIGHTS THE INDUSTRY’S PROGRESS IN MAKING OPERATIONS MORE SUSTAINABLE.
Thinking about decarbonising a mining operation and actually doing it are two very different things.
Conducted by an external and independent market research agency, ABB surveyed 412 mining executives from 18 countries across Asia, Europe, North America, South America, South Africa and Australia for its ‘Mining’s Moment’ report.
Of those surveyed in Australia, made up of 64 per cent male and 36 per cent female representatives, 82 per cent said they were excited by the opportunities presented by the increasing recognition of mining’s role in supplying resources for green technologies.
Perhaps more significantly, exactly half of those surveyed said they anticipate significant or complete transformation of their operations over the coming five years.
Pair that with 32 per cent reporting that their mining businesses are behind on their decarbonisation objectives and there is clear recognition that
decarbonisation is the path forward; it’s a matter of when, not if.
“People are saying the industry is going to change,” ABB Australia head of process industries Stuart Cowie told Australian Mining. “The decarbonisation transformation is happening, and our ‘Mining’s Moment’ report reflects this.”
Only 11 per cent of respondents are very confident they will achieve their 2030 decarbonisation goals. This rises to 37 per cent when it comes to achieving 2050 targets.
Cowie drilled down into the results more closely.
“Of the Australian respondents, 76 per cent agree that to achieve decarbonisation an integrated approach involving a combination of electrification, automation and digitalisation is necessary,” he said.
“And by 2026, 35 per cent of Australian respondents plan to invest in electrifying their haulage fleets, while 73 per cent are planning to electrify at least 25 per cent of their fleet by 2030.”
Australia is a front runner in this regard, with 79 per cent of
MOST RESPONDENTS SAID INTEGRATED ELECTRIFICATION, AUTOMATION AND DIGITALISATION ARE ESSENTIAL FOR THE TRANSFORMATION OF MINING.
Australian respondents considering vehicle electrification as being the most important lever to achieve decarbonisation goals. The global average for this question was 76 per cent.
But the Australian mining sector still faces its barriers.
“While 57 per cent cited capital investment as a barrier to decarbonisation, 53 per cent cited inadequate infrastructure,” Cowie said.
Just under 39 per cent of the Australian executives surveyed consider unproven technologies as a barrier, while 44 per cent are worried about the disruption to operations.
While a big-bang approach has proven a success for greenfield mines, an incremental approach to decarbonisation can be an effective way to navigate initial cost and trust concerns.
“The incremental approach is a miner’s way of trying to stay within budget but also make gains towards their goals,” Cowie said. “It could involve upgrading certain fleets of equipment and sub processes or changing to more efficient fuel or motors.
“Adding sustainable practices bit by bit also enables companies to trial technologies before they make a significant investment and adopt it across the whole plant.”
Cowie highlighted ABB’s partnership with Gold Fields and the company’s Granny Smith gold mine in Western Australia as an example
of where an incremental approach has proven fruitful.
“We’ve helped Gold Fields digitalise the Granny Smith underground mine, implementing and integrating an operations management system, with a fleet management system supporting the latest Industry 4.0 interoperability standards set to follow,” he said.
“We embedded some of our digital engineers into Gold Fields’ office at Granny Smith, and we also had our research and development (R&D) teams in Zurich and Sweden supporting the project.
“We have been able to surround the project with different pockets of excellence, whether it is fleet control, yield or operations management, and we have formed a team, which is really important for any digitalisation or decarbonisation project.”
ABB’s regional factsheet found 71 per cent of Australian respondents believe partnerships, like ABB’s collaboration with Gold Fields, are critical to meeting decarbonisation targets.
When asked what he expected decarbonisation in the Australian mining industry to look like in the next five years, Cowie lifted the lid on some pioneering technologies.
“We’re working with the mining industry to improve charging capabilities of diesel-electric haul trucks,” he said. “This involves a fastcharging, trolley-assist solution.”
Companies that implement ABB’s eMine trolley assist system can achieve up to a 90 per cent reduction in their carbon emissions when compared with a diesel machine. Trolley-assisted trucks can also achieve higher speed-on-grade, improving operational productivity and accelerating return on investment.
Cowie also highlighted ABB’s hoisting solutions, which can offer a zero-emission alternative to haul trucks, particularly as mines get deeper.
ABB hoists at BHP’s Prominent Hill copper mine in South Australia are helping the major miner meets its productivity and sustainability targets.
ABB’s ventilation on-demand solution is another way to drive down
emissions, with miners able to select when and at what intensity ventilation is used in underground mines.
Cowie said the regional factsheet highlights Australia’s changing sentiment towards the digitalisation, automation and electrification that will underpin future mines, with companies more enthusiastic about the opportunities to not only make their operations more environmentally friendly but also more productive.
“The opportunities we’re talking about are not just within mines,” Cowie said. “What we’re seeing is, through their innovations, miners are now excited about providing resources for green technology across all other industries.
“A lot of executives see this as a great opportunity to commercialise solutions for the whole green transition.
“And through their dealings with other sectors, mining is not just being seen as part of the problem anymore, but now it’s also being seen as a critical part of the solution to the world’s decarbonisation journey.” AM
AUSTRALIAN MINING SAT DOWN WITH CJD EQUIPMENT EXECUTIVE GENERAL MANAGER –SALES AND MARKETING GRAYDEN LEAVER TO LEARN ABOUT THE COMPANY’S PLANS FOR 2025.
In a year marked by a global focus on sustainability and the increased adoption of electric mining machinery, CJD Equipment and Volvo Construction Equipment are at the forefront of pioneering solutions.
Committed to catering for a greener future, CJD Equipment executive general manager – sales and marketing Grayden Leaver shared insights into the company’s strides in 2024, including the introduction of zero-emission electric machines, and an ongoing commitment to environmentally friendly innovation.
As CJD Equipment celebrates its 50th anniversary, the brand continues
What were some 2024 highlights for CJD and Volvo Construction Equipment?
Early this year we introduced Volvo Construction Equipment’s zero-emission electric machines to the market.
The first two models were the Electric ECR25 compact excavator and the Electric L25 wheel loader and both have been received very well.
These electric machines offer the same performance as their diesel counterparts but with zero emissions, near-silent operation as well as reduced vibrations, all of which provide a fantastic work environment.
These electric compacts can also fast-
CJD EQUIPMENT EXECUTIVE GENERAL MANAGER –SALES AND MARKETING GRAYDEN LEAVER.
Solutions, offering a comprehensive suite of technologies and services designed to enhance efficiency, safety and sustainability in construction and mining operations.
What were CJD Equipment’s goals for 2024? How is CJD faring on these?
The first major goal we celebrated this year was the 50th anniversary of CJD Equipment back in February.
We have had many events around the milestone, and it was a great opportunity to recognise the businesses’ many achievements over the years and celebrate with our founding partners Ron Rafferty and Rob Jowett, along
and Loader which we have now done, and it has created a lot in interest and discussions around the product.
It also targets many companies’ plans around sustainability, so it’s an exciting time.
What can we expect to see from CJD and Volvo in 2025?
As we look ahead into 2025, we are not standing still.
We will build on our electric product offering with the Electric L120 wheel loader and the Electric EC230 20-tonne excavator hitting our shores.
On top of this we will launch the new F series excavators along with the new J series articulated haulers, so it’s a busy time for product releases.
We will also continue to develop the Volvo Site Solutions offering, providing safer, more productive and sustainable eco-systems for customer sites.
What will we see more of in terms of equipment and machinery in 2025?
I think that technology solutions will continue to evolve in the mining space.
Data requirements are huge for any successful operation and the desire for information around performance improvements, safety advancements and operational sustainability can only come with high-powered technology solutions and machines that are integrated seamlessly and that dovetail
Clearly automation will continue to develop, as will the requirement for more electric and other sustainably-
What role do CJD and Volvo have to play as technologies evolve?
We’re sure we will play a part in requirements moving forward
The Volvo Site Solutions offerings will bring gains in productivity, efficiency and site safety as well as programs to work with our partners on measuring and reducing their carbon footprints.
Our release of larger electric loaders and excavators is already creating a significant amount of interest in the mining industry, so we look forward to the many conversations we will have with mining companies about these offerings next year and the other sustainable products heading our way in the short- to medium-term.
I also think the new range of articulated haulers will play a big part in our success in 2025. Volvo is seen as a world class articulated hauler and the continued development of an already industry leading product
Hardox® 500 Tuf is the latest grade of Hardox® wear plate. It combines the hardness of Hardox® 500 with the toughness of Hardox® 450. The wear resistance of Hardox® 500 Tuf makes it possible to increase the load capacity by using a thinner plate and still have the same outstanding service life. Or stay with the same thickness and increase service life by 30% or more.
Hardox® 500 Tuf can also double as a structural steel. Its high yield strength and toughness allow for lighter mining bodies that are resistant to dents and can take impact loads with less supporting structures.
Get the full story of Hardox® 500 Tuf at www.hardox.com
LIGHTER MINING TRUCK BODY
HIGHER LOAD CAPACITY
EXTENDED SERVICE LIFE
LESS FUEL ON EMPTY RUNS
AUSTRALIAN POWER EQUIPMENT IS BECOMING AS WELL KNOWN FOR ITS SUSTAINABLE PRACTICES AS IT IS FOR QUALITY HIGHVOLTAGE SOLUTIONS.
As the COVID-19 pandemic took hold in 2020, the world was forced to slow the pace of progress for the first time in living memory. For many, it was a time for
APE HAS SUPPORTED A NUMBER OF CONSERVATION CAUSES, INCLUDING THE TARONGA CONSERVATION SOCIETY AUSTRALIA’S PLATYPUS RESEARCH.
APE’s adherence to its core values have seen the company quickly expand.
“Since our inception, we have achieved rapid growth and made significant strides in environmental, social, and economic (ESG) impacts,” Crawford told Australian Mining
“In fact, Australian Power Equipment is listed in the Australian Financial Review Top 100 Fast Growers 2024.
“Our journey reflects a commitment to sustainable practices and innovation, underpinned by a strong adherence to the principles of a circular economy.”
APE aims to extend the lifecycle of equipment and reduce waste by refurbishing and repurposing stranded assets like electrical switchgear, transformers and relays.
“By investing in Australian service providers for refurbishing, reengineering, and testing equipment, we support local businesses and
“These relationships have transcended traditional supplier dynamics, evolving into partnerships based on shared values and mutual goals.”
In February, APE installed a solar system on its warehouse roof, which is expected to reduce on-site power usage by 96 per cent every year.
Crawford said installing such a large solar system was more strategic than simply saving energy.
“The decision to install a larger system than necessary reflects our commitment to contributing surplus energy back to the grid,” she said. “We have increased efficiency in our daily operations by reducing paper use, enhancing water catchment and recycling systems, and investing in battery-operated forklifts and equipment.”
APE is a corporate partner of Taronga Conservation Society Australia, as well as a conservation resource contributor towards platypus research.
APE’s funding allows Taronga to dedicate a platypus project lead to focus on developing operational, husbandry and scientific guidelines and operate a purpose-built refuge and research facility at Taronga Zoo Sydney.
Taronga Conservation Society Australia wildlife conservation officer Phoebe Meagher thanked APE for its continued engagement and support.
“Critical conservation programs, such as our platypus conservation recovery program, cannot happen without the support of our partners,” Meagher said. “The knowledge and expertise within our two sites, drives our tangible conservation outcomes, and has the power to make a legacy impact for threatened species.
“Supporting people and skills provides the necessary fire for change and is one of the most crucial factors in project success.”
Crawford said APE’s investment in critical initiatives such as these has grown significantly.
“We hope to be remembered as leaders in sustainable business practices, demonstrating that profitability and environmental responsibility can go hand in hand,” she said.
entire high-voltage power supply chain, the APE journey began in New South Wales with a singular focus on cable
In driving this focus, it was an easy decision for Crawford and Cockbain to engage with Cambria Association for the Blind and Handicapped’s
“We launched as a sideline business with CAB’s cable hangers, aiming to establish a foothold in the mining, tunnelling and solar sectors,” Crawford said. “We chose CAB because of its alignment with
“CAB not only manufactures superior cable management products but also supports vision rehabilitation and employment services for people with disabilities.
“This made our initial venture into the Australian mining sector not just a business opportunity but a chance to support a meaningful cause.”
A commitment to these kinds of initiatives, whether it be giving out-ofuse equipment a new life, supporting wildlife conservation, or investing in a future that values the work of people with disabilities, has been embedded in APE since its inception.
Crawford said her and Cockbain’s vision for the company is driven as much by a desire to leave the world better than how they found it as it is by a determination to supply quality high-voltage power solutions to the mining industry.
“We are dedicated to sustainability, community investment, and fostering a business culture that supports meaningful causes,” she said.
“As we grow, we remain committed to choosing partnerships that prioritise impact over profit and align with our vision for a more inclusive and sustainable world.” AM
Transform your underground mining operations with a Vocus private LTE (4G) mobile network. Enabling new digital applications even in the deepest recesses of the mine can drive significant improvements in safety, productivity and sustainability. It’s the secure, high-performance and reliable connectivity that’s enabling brilliant possibilities for Australia’s resources industry.
Welding operators often need to carry out repair and maintenance jobs remotely onsite using only the tools they have access to.
On any given day, a piece of machinery might need to be welded or cut on-site, a power tool might be required, or a welding operator might need access to air.
To combat common welding challenges, Miller has expanded its Big Blue range of engine-driven welding machines to include a model that has 600 amps of weld power, 18,000 watts of continuous generator power, 45 CFM (cubic feet per minute) of air output and heavy gouging capabilities for the most demanding jobs.
Suitable for mining applications such as pipe welding, emergency repair, scheduled maintenance, fixed plant and mobile plant repair, the Miller Big Blue 600X Duo Air Pak has been developed and manufactured based on industry feedback.
Most Miller 60-hertz (Hz) generators are manufactured in the US, and the Miller Big Blue 600X Duo Air Pak 50Hz developed for the Australian market is no exception.
“From an operational point of view, the industry really likes large, highoutput machines as they’re able to do the job quickly and can act fast enough to cut and weld things back together on-site,” Welding Industries of Australia (WIA) products and sales manager – Oceania Fuhai Liu told Australian Mining
“Based on those two pieces of primary feedback, we redeveloped our
Big Blue 800X Duo Air Pak with ArcReach) to meet the 50Hz output power compliance, creating the Miller Big Blue 600X Duo Air Pak.”
The Miller Big Blue 600X Duo Air Pak has one engine with two independent arcs boasting up to 300 amps each, meaning the machine can weld up to 300 amps per side when set up in dual-operator mode, or up to 600 amps when in single-operator mode.
This configuration makes it easier to switch from single-operator to dualoperator mode.
“One engine that provides multiple arcs equals a lower cost-per-arc when compared to multiple single-arc machines,” Liu said. “The amount of savings is calculated based on current expenses, and the use and the size of the equipment.
“For example, if typical use is 1000 hours per year, fuel and regular service expenses of one dual-operator machine versus two single-operator machines will result in 34 per cent in
“More hours of use mean more money saved.”
The Miller Big Blue 600X Duo Air Pak can be paired with an ArcReach wire feeder or accessory, making it easier for operators to adjust parameters and processes at the weld joint.
The machine also offers parameter control via Miller’s ArcReach Suitcase 12 wire feeder or stick/TIG remote, both of which can be used without the need of a control cable and their associated costs.
“Welding operators typically need to go back and forth from the machine
to the feeder or welding power sources to adjust or change the parameters or settings,” Liu said.
“But with ArcReach, you can change the settings right then and there, saving you time on-site and improving safety and productivity.”
ArcReach possesses cross-platform compatibilities allowing its accessories working on engine-driven machines such as the Miller Big Blue 600X Duo Air Pak to be fitted to select Miller plug-in power sources.
“You have the ArcReach technology not only for use on the engine drives but on ‘plug in’ or electric machines to complete welding on-site,” Liu said. “One of the unique features of ArcReach is you can pre-heat parts using the induction heating method instead of gas heating. This process becomes available when you pair the Big Blue 600X Duo Air Pak with Miller’s ArcReach Heater.
“Imagine a welding operator on site; they generally cut the piece, split it, and in some cases preheat it. ArcReach really gives you a complete package.”
WIA market development manager Mathew Hefferan described ArcReach as “game-changing technology”.
“With ArcReach, you can adjust the amperage and voltage at the weld joint, meaning you don’t have to climb in and out all the time,” Hefferan told
Australian Mining. “This increases site safety by reducing slips, trips and falls.”
The Miller Big Blue 600X Duo Air Pak meets current NEMA (National Emergency Management Agency) and IEC (International Electrotechnical Commission) compliance requirements.
To avoid electrical tool incompatibility at the mine site, the electrical system frequency of all engine drive welders/generators must provide 50Hz auxiliary power outputs.
Every version of the Miller Big Blue 600X Duo Air Pak also comes with a dual voltage reduction device, reducing the open-circuit voltage at the welding output studs.
“Mines are establishing new compliance rules all the time,” Hefferan said.
“We make a standard machine and then those who carry out compliance for the mine sites are able to adjust it to meet new regulations and suit sitespecific requirements.”
The Miller Big Blue 600X Duo Air Pak has undergone multiple field trials across Australia’s major mining regions, notably around Mackay in Queensland and Newcastle in New South Wales.
Supported by service and repair agents throughout Australia, WIA helps customers ensure their Miller machines are running smoothly.
“Our team is highly technical and very accessible,” Liu said.
“They work closely with our customers and can provide support if needed, even while operators are on
a job, even in remote locations.”
As we embark on 2025, the Miller Big Blue 600X Duo Air Pak is a perfect choice for mine sites looking for more power and increased efficiency. AM
FOR XCMG AUSTRALIA, BUILDING AND NURTURING NEW PARTNERSHIPS IS KEY TO DRIVING CONTINUED GROWTH AND SUCCESS IN A CHALLENGING YET LUCRATIVE ENVIRONMENT.
Australia’s mining sector stands as one of the most dynamic and influential industries on the global stage.
As Australia continues to be a leader in the export of essential commodities such as iron ore, coal and gold, the pressure to innovate and remain competitive is intensifying.
In this evolving landscape, the role of strategic partnerships has never been more critical for sustainable growth.
A localised focus on growth
XCMG Australia business development manager Jason Keays said the company recognises that no single entity can thrive in isolation, especially in a complex and multifaceted industry like mining.
“Our partnerships with Australian suppliers, service providers and contractors form the backbone of our success in providing cutting-edge machinery solutions tailored specifically for Australian conditions,” Keays told Australian Mining.
“These collaborations allow us to meet the unique demands of local operators while fostering innovation and enhancing productivity across various mining operations.”
Emphasising local expertise
Australian mining projects are defined by their scale, diversity, and complexity.
Each mine, from the iron ore pits in the Pilbara to the coal mines of Queensland, faces its own set of challenges from environmental considerations to logistical hurdles.
Understanding this, XCMG Australia prioritises working with local experts who bring invaluable on-theground knowledge.
“By integrating our global expertise in construction and mining machinery with the local know-how of Australian engineers, technicians, and operators, we can ensure our products and services are aligned with the needs of the industry,” Keays said.
“For example, XCMG Australia’s advanced heavy machinery, including the XE4000 excavator and the XDE260 mining haul truck, is designed and modified specifically to endure the harsh and rugged terrains of Australian mines.
“But it’s the close collaboration with local teams that enables us to fine-tune these machines for peak performance, ensuring they meet Australian safety and environmental standards.”
Partnerships go beyond supply chains and service networks; they also extend into the realm of innovation.
XCMG Australia is actively engaging in collaborative research and development projects with Australian mining companies, contractors and tech startups to drive innovation.
“One example of this is our work in autonomous mining technology, where we are joining forces to enhance the capabilities of our next-generation autonomous projects,” Keays said.
“This initiative not only promotes safety and efficiency on mining sites but also contributes to the Australian
XCMG AUSTRALIA IS COMMITTED TO DELIVERING SHARED VALUE THROUGH ITS PARTNERSHIPS.
COLLABORATION IS HELPING XCMG AUSTRALIA SHAPE THE FUTURE.
mining industry’s push towards greater sustainability.”
Keays is confident XCMG Australia’s ongoing collaborations with Australian technology firms are helping to integrate real-time monitoring systems into the company’s equipment, ensuring operations can be managed with greater precision.
“This emphasis on technologydriven solutions has cemented XCMG Australia as a forward-thinking partner for mines looking to adopt smart, datadriven mining practices,” he said.
XCMG Australia is not just focused on growth for its own sake; the company is committed to delivering shared value through its partnerships.
Collaboration with Australian businesses extends beyond the mine site to create economic opportunities in regional communities, where much of the country’s mining activity is concentrated.
“By sourcing locally and investing in regional businesses, we help generate jobs and stimulate economic development, ensuring that the benefits of Australia’s mining boom are felt across the nation,” Keays said.
“For instance, our partnerships with local contractors have led to the development of specialised training programs, helping to upskill the Australian workforce.
“This investment in local talent aligns with our long-term vision of creating a skilled labour pool that can support the growth of the sector.”
As Australia’s mining industry continues to evolve, so too does the
need for innovative solutions and strategic partnerships.
XCMG Australia remains committed to expanding its local partnerships to meet the demands of the future.
Whether collaborating with environmental consultants to ensure sustainable practices, working with logistics providers to streamline supply chains, or partnering with Indigenous businesses to create opportunities in remote areas, XCMG Australia’s focus remains firmly on fostering growth through collaboration.
“With new mines being developed and existing operations looking for ways to improve efficiency, the opportunities for partnership are vast,” Keays said.
“For XCMG Australia, establishing new partnerships is not just about expanding our reach; it’s about creating long-term, mutually beneficial relationships that drive growth for the entire Australian mining industry.”
The future of the Australian mining sector is bright as the energy transition boosts demand for the country’s minerals, but constant adaptation and innovation is required to seize the opportunities at hand.
Core to XCMG Australia, Keays said, is the belief that continued growth lies in building strong, strategic partnerships with local experts, businesses and communities.
“By working together, we can deliver the cutting-edge machinery, tailored solutions, and sustainable practices that the Australian mining sector needs to thrive in an increasingly competitive global market,” he said.
“Through collaboration, we are not only shaping the future of mining but also contributing to Australia’s economic prosperity.” AM
Intelligently designed, precision engineered and fit for purpose. MASPRO’s Bolting Series 2.0: A groundbreaking advancement in mining innovation. This revolutionary series enhances traditional drilling functions and introduces pioneering features for bolting applications. Focused on quality, durability, reliability, and performance, MASPRO sets a new industry standard for safety and efficiency in mining.
Given the vast and remote expanses of the Australian resources industry, keeping on top of mine rehabilitation processes is easier said than done.
This is why Dendra, a leading environmental technology company, has developed a platform to enable operators to visualise and analyse end-to-end terrestrial restoration in one place.
“Ecosystem restoration is complex and, in many cases, a mine’s environmental teams and consultants are very detail-oriented,” Dendra chief executive officer Susan Graham told Australian Mining
“But there are many different stakeholders when it comes to ecosystem restoration, so we’ve built a new platform to bring simplicity to the process while also enabling our clients to manage complex sites and gain valuable insights at very large scales.
“These insights can direct them to the highest priority issues and the biggest wins on-site, so our clients can engage everyone from consultants, contractors, regulators and community stakeholders.”
Graham said the new platform will be particularly beneficial for large mine sites, which need to simplify their understanding of their operations.
EROSION HEATMAP ON THE DENDRA PLATFORM, HIGHLIGHTING THE EXTENT AND SEVERITY OF EROSION ACROSS SEVERAL HUNDRED HECTARES.
“The platform addresses some serious pain points in the market, where the challenges begin the moment a seed hits the ground, whether it’s erosion weathering away at the soil, or invasive plant species competing with
the valuable native species you’ve just planted,” she said.
“Having a data platform to support managing these aspects helps to address each of these issues and avoid restoration or rehabilitation failures and
rework, while also providing proof and data to relinquish the mine site once it is fully rehabilitated.”
Dendra backs its platform with ultra high-resolution mapping and artificial intelligence (AI) insights, enabling miners to generate crystalclear visualisations of their sites to detect success and many ecosystem risks that present opportunities for improvement.
This enables environmental teams to be able to manage their ecosystems with more conviction and predictability, leading to better restoration over a longer, more sustained period, paving the way for improved mine rehabilitation outcomes and the ability to relinquish land sooner.
The development of Dendra’s platform is one of many successes achieved in 2024.
The company’s mapping capabilities continue to expand, with the ability to capture 2000 hectares of land in a day.
“This is transformational for mine sites, greatly reducing the need for boots on the ground,” Graham said.
“Because of this scale capacity, we’re now looking at much larger sites, moving from thousands to tens of thousands to hundreds of thousands of hectares at a time, which wasn’t possible 10 years ago.”
Dendra has worked closely with its mining partners to launch a new erosion solution that harnesses existing LiDAR (light detection and ranging) data sets that miners use daily.
“Customers are seeing real value from this solution because, from an existing operational asset, Dendra is able to repurpose LiDAR data to provide erosion insights, giving them extra value on something they’ve already purchased,” Graham said.
The erosion solution has come to the fore at the Jellinbah coal mine in Queensland. By pairing LiDAR data with Dendra’s high-powered platform, Jellinbah has successfully pinpointed the erosion features that impact rehabilitation, enabling the site to implement informed strategies to tackle environmental hazards.
Dendra also continues to expand its aerial seeding capability, which Graham calls the “critical instigator” at the beginning of the revegetation process.
Aerial seeding is becoming a popular solution in the Australian mining industry due to its speed, seed capabilities, safety and costeffectiveness, surpassing traditional methods carried out by light vehicles and dozers, which can present safety hazards and disturb the ground as they seed.
Dendra Australia general manager Guy Smith said the company has seen a 200 per cent year-on-year increase in the hectares seeded in 2024, fuelled by higher demand and increased capability.
“The Dendra team has done significant work to meet seeding demand,” Smith told Australian Mining. “We’ve completely redesigned the seeding unit that sits on top of the drone to specifically deal with the diverse nature of Australian native seeds.
“We’re seeing a lot more reliability and consistency with that product given such an increase in demand, and in terms of the analysis work, we’ve
been seeing significant reductions in site-wide weed analysis times given the developments we’ve made in the AI back-end.
“While sites we’re seeding are getting larger, analysis times are coming down, which is encouraging to see.”
As Dendra continues to shape a new era of ecosystem restoration and management, where technology is unlocking more capabilities than ever before, the company is attracting interest from new markets.
This has seen Dendra grow its international client base. This includes a significant presence in the United Arab Emirates, where the company is leading various projects including the restoration of 27.3 million mangroves.
Closer to home, Dendra is bringing environmental consultants into the fold.
“Our ecology-powered AI operating on ultra-high-res data is becoming
highly prized by consultants who are increasingly looking to new technology to augment their customer offerings,” Graham said.
“Consultants serve multiple verticals. They can work across mine rehabilitation, infrastructure projects and real estate developments, for example, with each of these applications facing the same fundamental environmental challenges.
“Dendra’s capabilities span each of these use cases, and as they work with their clients on new developments, environmental consultants face biodiversity and land management challenges that can be addressed with our technology.”
Graham said environmental consultants “understand the value of AI”.
“Because Dendra focuses specifically on environmental monitoring and management, consultants can see how
AI can help them, rather than just being another ChatGPT for fun,” she said.
“The momentum from the consultancy industry has really picked up in the last few months, so we’ll be putting increased resources into this area in 2025 to really empower environmental consultants to leverage data and AI tools to delight their customers.”
As Dendra continues to push the boundaries of what’s possible with ecosystem restoration, larger sections of the Australian mining industry are catching onto the company’s inspired approach.
Word of mouth is proliferating and Dendra is attracting more demand for its solutions than ever before.
And in the context of where the industry sits with technology and AI, this could be just the beginning of Dendra’s ascension. AM
WITH THE POTENTIAL FOR DECLINING INTEREST RATES AND MORE GEOPOLITICAL STABILITY, SRK CONSULTING BELIEVES GROWTH IS ON THE HORIZON FOR THE AUSTRALIAN MINING INDUSTRY.
While some commodities have endured a difficult 2024 amid cyclically low prices, others are experiencing renewed prosperity in the face of heightened demand.
Mining and exploration companies must steel themselves to the undulations that come with working in an industry that hinges so dominantly on supply and demand.
But while all miners are likely to face a bear market at one point or another, there are ways in which companies can insulate themselves from the ups and downs.
Australian Mining sat down with SRK Consulting to examine the past year in the local and international mining industry, and to assess some potential trends for 2025.
The year that was According to SRK’s principal geoscientist Carl D’Silva, the seeds of 2024 were laid when decarbonisation first became a global priority following the instalment of the Paris Agreement in 2015.
“The energy market is growing exponentially, and if you say you’re going to decarbonise an economy yet you’re not bringing in the battery minerals such as nickel, lithium, graphite, manganese and cobalt, you really aren’t making any dent into your decarbonisation goals,” D’Silva told Australian Mining.
“So when the decarbonisation push began, we needed a quantum change in how we mined commodities.”
Given the aspirations set out by the Paris Agreement in 2015, it was always going to be difficult to align the growth of the energy market with that of the battery minerals mining industry that feeds it. This created structural deficits, with prices increasing on misaligned supply–demand dynamics.
This balance is just as representative of lithium’s boom cycle in 2021–22 as it is of the commodity’s recent retreat.
“You cannot control energy growth, but if you do not mine enough minerals in a timely manner,” D’Silva said.
“This means that mining operations will not produce sufficient raw materials in an orderly timeframe, which will cause a lot more volatility in the market.”
While market volatility saw lithium prices soar during 2021–22 amid surging electric vehicle (EV) uptake, it also resulted in the declining cyclical prices seen in 2024; miners racing to bring projects online to capitalise on the boom in turn created a market surplus.
SRK senior geologist Stephen Johnson said 2024 has highlighted the sector’s resilient and lessresilient commodities.
“One piece of advice I was given by some seasoned explorers is that if you’re an exploration company, it’s best to play in the big markets,” Johnson told Australian Mining.
“And what we’ve seen this year is more mature minerals like copper have been reasonably resilient, because the copper market is so huge.”
Copper has been mined and consumed across the world for centuries, making the supply–demand dynamic more predictable. And because copper’s end market has significantly more scale than some other maturing commodities, a proportionally surging demand can make it hard for supply to keep pace.
“If the automotive sector suddenly said, for example, ‘We’re boosting EV production and we need copper for all of our electric cars’, the ability for the copper industry to all of a sudden produce 30 per cent more copper is more challenging than it is to do in other smaller-scale commodities,” Johnson said.
This can lead to the twin dreams for any mining or exploration company: surging commodity prices and an appreciating valuation.
Several significant deals have been announced or closed in the international mining industry in 2024.
BHP pushed to acquire Anglo American in a hostile back and forth, while Rio Tinto announced its acquisition of Arcadium Lithium in a more amenable fashion as it aims to bolster its lithium business.
In selling its Telfer and Havieron gold assets in Western Australia to UK company Greatland Gold, Newmont looked to refine its portfolio with a focus on Tier 1 gold and copper mines.
Johnson said mergers and acquisitions (M&A) will continue to pervade the mining landscape as long as there are opportunities to be had. And with many companies enduring suppressed valuations amid a turbulent capital market, there will no doubt be opportunities.
“It comes down to fundamentals,” Johnson said. “We’re seeing the cyclical nature of exploration funding being really challenging, and the market capitalisation of some development companies in stronger-performing commodities has been low.
“There is potential for value-creating M&A activity in that environment.”
Johnson said M&A activity can be the trigger for a commodity’s next boom cycle.
“Commodity prices get so low that people become optimistic enough that commodity prices will reverse that they have the conviction to make transactions,” he said.
Rio Tinto’s move to acquire Arcadium Lithium has been seen as a strategic play to capitalise on a commodity’s downturn where assets and share prices are more affordable. Long bullish about lithium’s future and facing some development hurdles at its existing lithium assets, the major has been keen to build a vertically integrated lithium business for some time.
Arcadium Lithium, with a host of downstream and upstream assets stationed across the world, was the opportunity on which to capitalise.
D’Silva shared some thoughts on M&A.
“The general rule is, if you’ve got a good balance sheet and you’ve got a large enough portfolio, you should be in the M&A space at the moment,” he said.
“I see the bigger mining companies doing more acquisitions in 2025.”
The year to come
The interest rate in Australia remained at 4.35 per cent for much of 2024; however, expectations that interest rates will retreat in 2025 will potentially open up more opportunity for investment in local mining and exploration.
“If you’re paying seven per cent on your mortgage, for instance, you’re
SEVERAL SIGNIFICANT DEALS WERE ANNOUNCED OR CLOSED IN 2024.
invest in a speculative mining stock,” Johnson said. “So a declining interest rate would seemingly make investing in capital raises in the exploration industry more appealing.”
One contributor to higher interest rates is the global unrest that has occurred in recent years. Economic instability that was accentuated with Russia’s invasion of Ukraine has been further exacerbated by war in the Middle East, as well as a number of major elections.
in 2025.
“We’ve had too many wars, too many people at election ballots and too many competing things occurring in 2024,” he said.
“When you have wars, people hold onto money because they don’t trust equity markets and financial institutions to serve their best interests in the timeframe.
“It’ll also be about five years since the beginning of COVID-19 and all of the monetary policies that supported that
the way out.”
D’Silva said economies have had to navigate legacy issues, with countries working their way back from significant debt amid the COVID-19 era. But with interest rates regressing in some countries across the world, there are signs of economic optimism.
“We’ll start to see some structural changes in 2025, and I believe we’ll go back to the thinking of, ‘These projects can survive on their own merit’,” D’Silva said. AM
AUSTRALIAN MINING SAT DOWN WITH AUSTMINE INTERNATIONAL BUSINESS
DIRECTOR
FROBERT TRZEBSKI
TO TAKE A DEEP DIVE INTO THE YEAR AHEAD.
or over 35 years, Austmine has been at the heart of Australia’s mining industry as a premier not-for-profit association for mining equipment, technology and services (METS) companies.
Austmine has worked diligently for decades to uplift the sector, advocating for its recognition as a world leader in mining innovation and technology.
Now representing over 750 METS companies nationally, Austmine is a true reflection of the sector’s impressive diversity.
A key part of Austmine’s advocacy is its involvement with international mining and resources events.
Australian Mining sat down with Austmine international business director Robert Trzebski to discuss Austmine’s outlook for the global mining industry, as well as the key events the company is looking forward to in 2025.
Austmine is in its third year of the Global Mining Challenge – India program, which is supported by the Federal Government’s Department
A KEY PART OF AUSTMINE’S ADVOCACY IS ITS INVOLVEMENT WITH INTERNATIONAL MINING AND RESOURCES EVENTS.
of Industry, Science and Resources to continue until 2026.
The program aims to foster greater collaboration between Indian and Australian mining and METS sectors and seeks to drive more efficient, safe and sustainable operations.
“India has proven to be a very interesting market for Australian METS,” Trzebski told Australian Mining. “There are huge players with massive scale and diversity creating major potential for partnerships with Australian companies.”
Trzebski said growing industries like electric vehicles will drive the need for commodities into the future.
“There’s a massive push for India to go electric, which is growing demand for lithium and other critical minerals,” he said.
From February to March 2025, Austmine will lead a Mining Mission delegation to India to provide an opportunity to understand industry needs and develop business relationships in one of the world’s most prospective mining markets.
The delegation will visit mine sites and meet with key players in the
industry, including mining companies, local suppliers, associations and government bodies.
Another Mining Mission delegation will head to Kazakhstan in September. Since 2010, Austmine, in collaboration with Austrade and Trade and Investment Queensland, has been organising Australian trade delegations to the Central Asian country.
The delegation will coincide with the 2025 Mining and Metals Central Asia exhibition in Almaty. Delegates will receive connections and access to primary decision-makers across mining organisations, in-market partners and other key stakeholders.
“Kazakhstan is the biggest copper producer in Central Asia and a huge producer of other key commodities like ferrochrome,” Trzebski said. “It’s a very open market and there are many Australian METS companies that have been successfully doing business in the Kazakhstan market.”
Austmine will lead the inaugural Zambia Mining Mission in March 2025, with the program focusing on exploring
opportunities and understanding market needs in Zambia’s rapidly developing copper sector.
“Zambia, the Democratic Republic of the Congo and to a degree Zimbabwe are located around a copper belt, making them important producers in the region,” Trzebski said.
“Austmine is aligning a delegation with the Zambia International Mining and Energy Conference, which takes place from March 19–20, 2025, in Kitwe, which will provide connections to leading mining organisations, government officials and potential business partners in the region.”
This event brings together key stakeholders to discuss current mining and energy challenges and opportunities and set a pathway for a prosperous industry future.
Austmine has a number of agreements in place with Canadian companies thanks to what Trzebski described as a “great openness and willingness to collaborate” between Australia and Canada.
“Quebec has been steadily growing as a mining powerhouse,” he said.
“This includes an aim to attract manufacturers, engineering firms and contractors to increase availability to local supply chains.”
Building on significant collaboration between the Australian and Canadian mining and METS industries, Austmine will return to Quebec for a Mining Mission in 2025.
Taking place the week before CIM CONNECT 2025 in Montreal, the Austmine mining mission will help Australian METS connect with local stakeholders, potential partners and mining operators involved in iron ore, gold, zinc, lithium and other critical minerals found in Quebec.
The agenda will include tours to major mine sites, meetings with key decisionmakers, business-to-business matching with potential partners, and networking events to connect across the mining value chain.
Trzebski said Austmine will also be leading a delegation to Arizona in conjunction with the Elko Mining Expo in Nevada, US, held from June 6–7.
This event serves as a platform for industry professionals of the US mining industry to come together and explore the latest technologies in mining.
“Arizona is one of, if not the biggest copper producer in the US,” Trzebski said. “There’s huge potential for Australian companies to engage with key players.”
South American countries are a growing hub of mining activity, with Brazil especially becoming an ever-more attractive target.
Trzebski said there’s a great level of interest between South American mining stakeholders in the Australian METS sector – and vice versa.
“It’s a huge market and while the push towards critical minerals is as yet underdeveloped, there’s a big agenda for growth in not just Brazil but Peru, Argentina, and Chile as well,” he said.
Austmine will support the Australian Pavillion, hosted by Austrade, at the Exposibram 2025 exhibition from October 28–30 in Salvador, Brazil.
“We will be working with Austrade to take the delegation to some site visits in the nearby iron ore region,” Trzebski said.
This global movement sets the stage for an interesting 2025, and Austmine will yet again be on the forefront of thought leadership through its partnerships with events as the industry turns to new technologies.
Trzebski offered Australian Mining a look at some of the key global mining industry events taking place in 2025.
Expomin 2025
April 22–25 2025
Santiago, Chile
COPPER
Expomin 2025 is set to live up to its mission to unlock global mining opportunities for the 70,000 industry professionals expected to be in attendance, as well as its 1300 exhibitors.
As one of South America’s largest and most prestigious mining exhibitions, Expomin serves as a critical platform for showcasing cutting-edge technologies that drive innovation in the global mining sector.
“Austmine has over 400m2 of space in which we are inviting 50 exhibitors to showcase their capabilities,” Trzebski said. “It’s truly a worldwide exhibition that presents Australian METS companies the perfect opportunity to strengthen market entry.”
Austmine will be hosting the Australian Pavillion, where Australia will have its own delegation present, in collaboration with the Federal and State Governments.
Together, the delegation will present a united front highlighting the best Australia has to offer to local miners.
May 4–7 2025
Montreal, Canada
The CIM CONNECT Convention and Exhibition is Canada’s premier mining trade show that includes a line-up of expertled short courses, three full days of technical presentations and great networking opportunities.
At the 2025 CIM event, Austmine will coordinate and manage the Australian Pavilion with the aim of promoting Australia’s role as the global hub for mining innovation.
“CIM will be a great opportunity to connect with mining leaders interested in discovering the latest innovations and technologies from Australia,” Trzebski said.
May 20–22 2025
Brisbane, Queensland
The Global Resources Innovation Expo is a ‘by industry, for industry’ international conference and exhibition proudly hosted by Austmine in partnership with AusIMM.
GRX25 will shine a spotlight on technologies, breakthroughs, and collaborations, providing a global platform for thought leaders and innovators to drive the change needed for a sustainable future.
PNG Expo
July 2–3 2025
Port Moresby, Papua New Guinea
The PNG Industrial and Mining Resources Exhibition and Conference is Papua New Guinea’s (PNG) premier mining event, bringing together all sectors of the industrial, mining and resources industries into one location.
In 2025, the event will again be held in Port Moresby.
Austmine will lead a Mining Mission to PNG in conjunction with the 2025 PNG Expo to build upon key relationships with stakeholders in the Pacific nation’s mining and resources industry.
Through developing a carefully curated program to ensure meetings with the right contacts take place, the PNG mission will aim to provide exceptional value to participants.
Copper to the World
August 26–27 2025
Adelaide, South Australia
Austmine is proud to once again partner with the South Australian Government to host Copper to the World 2025, an event for global industry leaders, innovators, and experts to engage in critical conversations about the future of copper mining.
Building on the success of past events, Copper to the World will provide a dynamic platform to explore the latest advancements, challenges, and opportunities in copper mining. The event will spotlight cutting-edge technologies, innovations in decarbonisation, and strategies to ensure a sustainable, efficient copper supply chain for the future.
September 22–26 2025
Arequipa, Peru
Though the Australian Trade and Investment Commission will be the primary host, Austmine will again be on hand to support the Australian Pavillion at PERUMIN 2025.
Set to take off from September 22–26, PERUMIN is expected to draw in over 65,000 participants with over 1100 stands for exhibitors.
The aim of the conference is to stress the need to promote mining investments in the country as it evolves on the global stage.
Following the event, from September 29–October 3, Austmine will lead a Mining Mission delegation of Australian METS companies to visit key mining operations, meet with mining management, network with local suppliers and gain firsthand market insights in Peru AM
AUSTRALIAN MINING SPOKE WITH WESTGOLD RESOURCES MANAGING DIRECTOR AND CEO WAYNE BRAMWELL ABOUT HOW THE COMPANY PLANS TO CONTINUE ITS SUCCESS IN THE NEW YEAR.
If there is a company that embodies the success that the Australian gold mining sector has seen in 2024, it’s Westgold Resources.
From finalising a multibillion-dollar merger with Karora Resources to delivering strong gold production across its operations, Westgold has had win after win.
Through Karora, Westgold has acquired the Beta Hunt and Higginsville gold mines in the southern Goldfields, allowing Westgold to expand its operational footprint beyond the Murchison region it has operated in for many years.
“We’re really excited and proud to put these two businesses together,” Westgold managing director and chief executive officer Wayne Bramwell told Australian Mining
“Through the merger, we have picked up 500–600 employees, two more processing plants, one large underground mine, one small underground mine, and a massive exploration package within Higginsville.
“Karora operated in a very similar manner to us, so putting two businesses
together that have a similar culture gives you a good basis to build from.”
Bramwell described the similarities and differences between the Murchison and southern Goldfields regions within a gold mining context.
“(When) talking about the southern Goldfields, and the Goldfields in particular, there are three main mineralising structures that control the bulk of the gold endowment,” Bramwell said.
“The Boulder Lefroy Fault, Zuleika Shear and Speedway Fault all run
through the Higginsville package, so that was a real attraction to us. The Murchison probably has an endowment of 30 to 40 million ounces (Moz) of gold and the southern Goldfields is a little smaller than that.
“Both are very fertile and are historic gold producing regions. The southern Goldfields and Murchison are very underexplored and we are confident that drilling can add more reserve ounces to both.”
the fleet and having people to operate the fleet means we can move equipment and people around very quickly as new opportunities emerge,” Bramwell said.
Westgold currently owns six underground mines: Big Bell, Bluebird,
“Mining is a dynamic environment. When using mining contractors, if you want to make a change to a plan, it will normally cost you more. A contractor will charge you a 20–30 per cent margin to use their capital which is understandable. Westgold owns that capital, so we don’t have to pay that additional margin.
“We’re a little unusual in that we do all our underground drilling. If we were doing that with a third party, it would cost us about 30 per cent more. Not having to pay that additional margin allows us to drill more metres underground, and we invest that additional expense back into the business.
“It gives us operational flexibility to do more with our own people and our own capital at a lower cost.”
Westgold produced 227,237oz of gold during the 2023–24 financial year (FY24), within the company’s FY24 production guidance of 220,000–230,000oz.
The company kept that momentum going in the first quarter of FY25, producing a record 77,369oz of gold from its newly expanded portfolio.
Additionally, Westgold ramped up its exploration activities across its operations, something the company will continue in FY25.
“We recommitted to drilling in 2022,” Bramwell said.
“Prior to that, the company didn’t drill enough to extend mine life or bring the next suite of assets on.
“We’ve drilled intensively at the Bluebird–South Junction project at Meekatharra. Within two years, it’s gone from a very small mine of 250,000 tonnes per annum to a run rate of 500,000 tonnes per annum.
“Through additional drilling, we’re stepping up the production rate to about 1.2 million tonnes per annum in the new year. The more you drill, the more you find. We’ve drilled that ore body intensively, and we’re not slowing down.”
Westgold hopes to unlock a third mining front at Bluebird–South Junction in order to lift its production run rate to above 1.5 million tonnes per annum.
The company is currently carrying out sub-level open stoping of the South Junction lode, with plans for Bluebird–South Junction to become the primary ore source for the nearby Bluebird processing plant, following the Triton–South Emu and Paddy’s Flat mines being paused.
“Within the Murchison, we have three processing plants: Fortnum near the Starlight mine, Tuckabianna which is largely fed by our Big Bell mine and our other Cue operations, and Bluebird at Meekatharra,” Bramwell said. “To keep the Bluebird mill fed, we’ve been trucking ore from our Cue operations.
“So how do we optimise the Murchison business? We make Bluebird–South Junction as big as we can so it’s matched with the Bluebird mill. That way, we don’t have to truck ore from Cue.
“(We’re) trying to replicate a simple model of having a mine and mill that are equally matched, which we’ve got with Starlight and Fortnum.”
The increased exploration in the Murchison led to Westgold delivering its first increase in ore reserves post depletion since FY17. As of June 30 2024, the company’s ore reserves sit at 50 million tonnes at 2.05 grams per tonne of gold for 3.3Moz of gold.
“Westgold has been effectively producing gold for many years, but it wasn’t replacing what it had depleted,” Bramwell said. “Seven years of shrinking your reserve is not something you can turn around overnight, so the last two years of drilling has finally shown that we can grow the reserve. We are now confident it will continue to grow.”
Westgold has also been growing its newly acquired Beta Hunt mine, with plans to continue exploration during FY25.
So far, the company has uncovered sediment-hosted coarse gold mineralisation within the Western
Flanks orebody and defined a new exploration target at the Fletcher zone.
“Karora’s predecessor found a very high-grade vein called Father’s Day in about 2019,” Bramwell said.
“It was always thought to only exist in one part of Beta Hunt, that being the A zone. However, this sediment vein isn’t a flash in the pan. It’s been found in the A zone (and) we’ve now found it in the Western Flank zone. We expect it also exists in the Fletcher zone.
“We’re starting to accelerate Fletcher because we see that as the third mining front we can expand Beta Hunt above current production levels.”
With targeted exploration scheduled across its operations and production at the Great Fingall mine expected to commence in the fourth quarter of FY25, Westgold is poised to continue its operational success in the new year, leveraging the strong gold price.
“Westgold is now a top five ASXlisted gold company,” Bramwell said.
“We’re also a top 10 TSX-listed (Toronto Stock Exchange) gold miner. Our focus is the Murchison and southern Goldfields regions, and that’s where our focus is going to remain.
“We’ve got a portfolio of assets which we are confident we can leverage more production out of at a lower cost, and that’s really going to be our focus for the next 12 months.” AM
TAKING PLACE AS PART OF THE WA MINING CONFERENCE AND EXHIBITION FOR THE FIRST TIME, THE 2024 PROSPECT AWARDS HIGHLIGHTED THE RESOURCES SECTOR’S BEST AND BRIGHTEST.
For more than a decade, the Australian Mining Prospect Awards has recognised those who go above and beyond while excelling in their field, highlighting achievements in everything from safety to technology and Indigenous engagement.
The 2024 event promised to be bigger and better than ever before; and it did just that, with 11 awards presented on the night, including Innovative Mining Solution, Discovery of the year, and Excellence in Environmental Management and Sustainability.
The Australia’s resources industry has a critical role to play in supporting global decarbonisation, with Federal Resources Minister Madeleine King describing the industry as the “heart” of building a ‘Future Made in Australia’.
“The road to net-zero runs through Australia’s resources sector,” King said.
“The (Federal) Government has put the resources industry at the heart of its policy-making because it knows a strong resources sector means a strong Australia.”
Through its abundance of critical minerals needed for the global energy transition, Australia has potential to become a renewable superpower.
However, critical minerals such as graphite, lithium and cobalt don’t spring from the ground fully formed – they need to be extracted.
It is through inspired individuals pushing the envelope for innovation and new ways of thinking that makes efficient mineral extraction and processing possible, leading to new critical minerals mines coming online to serve the needs of modern society.
With that in mind, keep reading as we spotlight all the winners of the 2024 Australian Mining
THE 2024 AUSTRALIAN MINING PROSPECT AWARDS TOOK PLACE ON OCTOBER 9 AS PART OF THE WA MINING CONFERENCE AND EXHIBITION.
FORWARD-THINKING ADVANCES ACROSS SAFETY AND SUSTAINABILITY WERE CELEBRATED AT THE 2024 AUSTRALIAN MINING PROSPECT AWARDS.
HIGH-GRADE POLYMETALLIC NICKEL-COPPER-COBALT SULPHIDE DEPOSITS ARE RARE AND DIFFICULT TO FIND. BUT NOT FOR IGO.
Amid the global energy transition, new critical minerals discoveries are always welcome.
And among the plethora of findings made in 2023 was high-grade nickelcopper-cobalt mineralisation at the Dogleg prospect in Western Australia.
The Dogleg prospect is situated within the Quick Shears group of tenements, where IGO and joint venture partner Buxton Resources are targeting ‘Nova-style’ magmatic nickel-copper sulphide mineralisation.
After being originally identified as an area of interest due to its magnetic features associated with the nearby Merlin nickel-copper-cobalt prospect, IGO’s exploration team drilled the first diamond hole at Dogleg in November 2023 by targeting the specific area identified with a ground electromagnetic survey.
The assay results showcased highgrade sulphides within a broader zone of low-to-moderate grade mineralisation.
The discovery was made by interpreting newly flown IGO-owned detailed aeromagnetic data. According to IGO, the drillhole’s deposit style is extremely rare in Australia, with the company’s Nova deposit being the best example.
The new discovery also proves the Kimberley region hosts significant and attractive polymetallic nickel sulphide deposits that could lead to greater exploration expenditure and potentially new critical minerals mines for Australia.
In recognising Dogleg’s significant contribution to the broader Australian mining industry, IGO was awarded the Discovery of the Year award at the 2024 Australian Mining Prospect Awards.
The award celebrates a significant discovery at either a greenfields or brownfields site.
The award is especially welcome amid the global nickel downturn, which was primarily caused by a supply surplus and an increase in nickel supplies from countries like Indonesia and China.
Despite having to weather faltering nickel prices, IGO has continued to see great success at Dogleg.
The company drilled the second diamond hole at the prospect in February 2024, which established a broader zone of high-grade semi-
massive mineralisation that ground electromagnetic surveys didn’t detect.
The drillhole – which was drilled 65m down-plunge from the November 2023 hole – returned 2.63m at 4.17 per cent nickel, 0.83 per cent copper, 0.14 per cent cobalt from 233.63m in assays.
IGO said the second drillhole supports the sulphide mineralisation species logged as being a combination of pyrrhotite, pentlandite and chalcopyrite.
Once Western Australia’s wet season ends, IGO plans to build off the second drillhole by continuing to drill the Dogleg system towards a maiden resource.
IGO specifically plans to explore the host geological belt along the strike to identify more nickel-copper-cobalt discoveries now that the miner believes it has uncovered a district or ‘camp’ of deposits.
The company believes continued exploration could lead to multiple new nickel mines producing Class 1 nickel – which contains a minimum of 99.8 per cent nickel – for IGO and the wider Australian community.
When hosting its 2024 strategy day in September 2024, IGO managing director and chief executive officer Ivan Vella said electrification is at the core of the global energy transition.
“To drive the transition, the world is going to need to discover and deliver a lot more battery materials,” Vella said. “This is where IGO has a significant role to play.” AM
ROY HILL TOOK HOME TWO PRIZES FROM THE 2024 AUSTRALIAN MINING PROSPECT AWARDS.
The Roy Hill iron ore mine has long been described as a jewel of Western Australia’s mining sector.
Located 1200km north of Perth in the Pilbara, Roy Hill is one of Australia’s largest iron ore mines, employing more than 3000 people across its Perth, Port Hedland, and Newman operations.
As the mine evolves, Roy Hill has had the opportunity to embed a range of technologies to optimise delivery across its supply and demand chain, leading to the site being dubbed a ‘smart mine’.
“Our use of technology and innovative thinking have become defining features of our iron ore operation,” Roy Hill said.
“We’re improving productivity and safety across operations through automation and integration; in particular
through our remote operations, all drill rigs are now fully automated.”
Roy Hill regularly produces around 60 million tonnes of iron ore per annum and ships this vital commodity around the world.
“At Roy Hill, our vision is to be a high performing iron ore business where people contribute, realise their full potential and help to build the best mining company in Australia,” the company said. “This vision is not only our aspirational statement of what we want to be, but also helps set the direction for our success.”
Roy Hill is also a safety-conscious mine, with operational safety, mental health and emotional wellbeing procedures continuously reviewed and updated.
“Roy Hill is committed to providing a safe, productive and
healthy work environment for all employees, contractors, family members and visitors to our sites,” the company said.
“From physical health and safety onsite, to feeling supported as part of the community, we all have a responsibility to take care of one another.
“We take the wellbeing of our people very seriously, with a number of initiatives and programs in place to support this.”
It was for its drive towards a sustainable, safe and profitable mine that Roy Hill was awarded the Australian Mine of the Year award at the 2024 Australian Mining Prospect Awards for the second year in a row.
The award celebrates a site that not only reached production goals, but also one that has implemented outstanding safety controls, environmental programs
and has shown its capacity to innovate to drive the industry forward.
“Roy Hill is humbled to have been recognised as Australian Mine of the Year for a second straight year,” the company said.
“Having earlier being named the winner of the Excellence in Mine Safety Award, the Australian Mine of the Year rounded out a wonderful evening, reinforcing the commitment and efforts of Roy Hill’s people, and the outstanding leadership of executive chairman Gina Rinehart.
“Under the leadership of Rinehart, Roy Hill has an unwavering commitment to its people and operational excellence which has again been recognised by its peers.” AM
The Australian Mine of the Year award was proudly sponsored by Bonfiglioli.
Bonfiglioli supports the mining sector, with an extensive range of gear motors, gearboxes, drive systems, planetary gearboxes and inverters that have resolved materials handling and mining challenges for more than 60 years.
www.bonfiglioli.com/new-zealand/en
www.bonfiglioli.com/australia/en
BURU REHAB, AN INDIGENOUS MINE REHABILITATION AND EARTHWORKS SERVICES PROVIDER, WAS THE WORTHY WINNER OF THE 2024 INDIGENOUS AND COMMUNITY ENGAGEMENT AWARD.
Nof kilometres and work needing to be done 24–7, it’s only natural that companies collaborate with each other when needed.
So when Mineral Resources (MinRes) needed help with road maintenance, dust mitigation, civil earthworks, load and haul rehabilitation and general site maintenance at its Wodgina lithium mine, it called on Buru Rehab to get the job done.
And it was this partnership that saw Buru Rehab take home the Indigenous and Community Engagement award at the 2024 Prospect Awards.
The award recognises collaboration between an Aboriginal-owned business or community organisation and mining and minerals processing companies operating within Australia.
Buru Rehab is a Kariyarra-majority Indigenous-owned business aiming to create sustainable and mutually beneficial partnerships between Indigenous communities and mining companies.
The company was awarded the MinRes contract in November 2023 and has hit the ground running at the Western Australian mine.
“Employing Indigenous people to work on mine sites and be proactively engaged in rehabilitation of Country enables quality outcomes for our people and our Country,” Buru Rehab owner George Todd said.
“Along with civil works, Buru Rehab will undertake rehabilitation for MinRes’ exploration and mining activities, restoring the land and supporting it for future uses.”
Buru Rehab and MinRes’ partnership has led to significant community benefits, including employing an additional 12 Indigenous employees and acquiring new equipment through MinRes’ finance facility. This has expanded Buru Rehab’s capabilities, allowing the company to undertake larger projects.
Todd and his team are active promoters of community engagement,
Indigenous people and businesses in each Buru Rehab project.
“We’re pleased that Buru Rehab is providing subcontracting opportunities for other Indigenous owned businesses, giving them security to invest in their own machinery and equipment,” MinRes general manager – communities and heritage Heath Nelson said.
“This contract will have positive flowon effects for years to come, offering ongoing employment opportunities for people living in the Pilbara.”
Commenting on the Prospect Awards win in a Facebook post, MinRes said the company was proud of its continued work with Buru Rehab.
Rehab for this award, which recognises collaboration between an Aboriginalowned business and mining companies,” the post said.
“George Todd was on hand to accept the award and acknowledged our partnership while emphasising the importance of rehabilitating Country once mining activities are complete.”
With discussions about expanding the contract scope continuing, the MinRes and Buru Rehab partnership is a testament to what companies can achieve when they put their minds together. AM
The Indigenous and Community Engagement Award was proudly sponsored by Sandvik.
EMPLOYING INDIGENOUS PEOPLE TO WORK ON MINE SITES AND BE PROACTIVELY ENGAGED IN REHABILITATION OF COUNTRY ENABLES QUALITY OUTCOMES FOR OUR PEOPLE AND OUR COUNTRY.”
We are now better equipped than ever to help you to optimise your comminution and material handling operations for maximum performance, safety and efficiency.
Combining the industry leading screening, feeding and loading expertise of Schenck Process Mining with our mastery of crushing and wear protection, allows us to bring you an unrivalled equipment line-up. We underpin this unique offering with our expert process knowledge, full range of digital tools, high quality OEM spare parts, consumables and life-cycle services.
Scan the QR code to discover why we are the industry’s partner in eco-efficient mineral processing.
BLASTIQ UNDERGROUND IS HELPING TO REVOLUTIONISE DRILL AND BLAST OPERATIONS IN THE MINING INDUSTRY.
The mining industry is increasingly reliant on the latest innovations surrounding Industrial Internet of Things (IIoT) to optimise operations, streamline workflows, and achieve greater productivity.
In recognition of this vital field, the 2024 Australian Mining Prospect Awards celebrated a key player in the industry through the Excellence in IIoT Application award.
Orica Digital Solutions was the
Through its integration of drilling data, digital blast design, and postblast performance analysis, the application empowers engineers to make data-driven decisions that improve operational efficiency.
The software also helps reduce environmental impacts by minimising ground vibrations and air overpressure during blasting activities, making it
GOOD BLAST DESIGN IS ABSOLUTELY CRITICAL (BECAUSE) WE BLAST THREE TO FOUR TIMES A WEEK, AND HAVING ACCESS TO INSTANT DATA MEANS THAT YOU ARE MAKING INFORMED DECISIONS.”
a crucial tool for mines that prioritise sustainable practices.
BlastIQ Underground not only improves blast execution by digitally sharing blast designs and providing precision recharging, but also offers third-party interoperability, allowing for integration with mine planning systems.
The volumetric analysis feature enhances ore recovery by capturing material volumes and analysing the effects of drilling and blasting on mineral extraction.
29Metals’ Golden Grove copper-
recording blasthole conditions became inefficient, leading to delays and reduced productivity.
Recognising the need for a more streamlined approach, Golden Grove partnered with Orica Digital Solutions to trial BlastIQ Underground.
Over a three-month period, the application proved to be an invaluable asset to the mine’s drill and blast teams.
Using the BlastIQ Underground desktop application, the BlastIQ mobile platform for underground operators, and BlastIQ Insights, those stationed at
ifm were extremely proud to have sponsored the award “Excellence In IIoT Application” which recognises the outstanding implementation of IIoT that enhances mining and mineral processing.
ifm are at the forefront of the new and emerging digital era of IIoT in advancing Australian businesses with improved efficiencies, productivity and competitiveness.
THE LAND ACCESS AND DISTURBANCE PERMIT SYSTEM HAS BEEN INSTRUMENTAL AT BHP’S WEST MUSGRAVE PROJECT, DELIVERING OUTSTANDING ENVIRONMENTAL OUTCOMES.
As we edge closer to 2030, ways to minimise emissions and rehabilitate land are at the forefront of all environmental discussions in the mining industry.
At the heart of these discussions is innovation, and that is exactly what the Excellence in Environmental Management and Sustainability award recognises.
The award recognises a mine, company or project that has developed or conducted a pioneering, environmentally-focused sustainable program to protect, preserve and/or rehabilitate the natural environment, and contributes to decarbonisation and waste and emissions reduction.
BHP’s West Musgrave project in Western Australia took out the category at the 2024 Australian Mining Prospect Awards, thanks to its land access and disturbance permit (LADP) system.
First implemented in October 2022,
of ground disturbance activities within West Musgrave while protecting known priority flora species and fauna species within the site and ensuring compliance with government and community commitments.
The system was developed to preserve heritage and minimise environmental and cultural impacts arising from West Musgrave’s development.
“The Ngaanyatjarra People have a deep and enduring connection to Country and as the first large-scale industrial development in the West Musgrave region, the West Musgrave project has an ethical obligation to minimise disturbance to the greatest extent practicable and operate in an environmentally and socially sustainable manner,” BHP manager – environment and secondary approvals Shoanne Labowitch said.
Since its implementation, the LADP system has delivered an array of benefits, including improving standard land access control methodologies and providing
management, including where Traditional Owner involvement is required.
The system also reduces risks of unintentionally impacting on significant heritage through the automatic removal of prohibited and restricted areas from proposed activity areas, increasing efficiency by using algorithms
Implementation of BlackSky provides automated assurance and reporting data verification, increasing operational efficiency and providing robust assurance by reducing human error.
BlackSky’s tasking system can also be fitted to the LADP system.
The LADP system is also supported by applications such as RightStep, ESRI ArcGIS Online, Amazon Web Services’ Lambda script, and MS Power Automate, making the LADP solution a one-stop shop for managing land access permitting and
To date, 47 LADPs have been issued and numerous contractors have worked and continue to work under these LADPs to deliver a diverse range
“During this time, no unauthorised ground disturbance or material or significant environmental events have occurred on the West Musgrave project, in part due to the project team’s strong sustainability focus underpinned by the LADP approval, assurance and verification processes,”
“The LADP system has been outstanding environmental and cultural heritage performance of the West Musgrave project and will remain an essential tool throughout the life of
The Excellence in Environmental award was proudly sponsored by Sefar
THE SAFER SUMMER CAMPAIGN SAW A 36 PER CENT REDUCTION IN RECORDABLE INJURIES.
Safer Summer program.
Geographe extends congratulations to Roy Hill for receiving the 2024 Excellence in Mine Safety and OH&S award, recognising their safety efforts through their Safer Summer program.
Roy Hill’s commitment to enhancing safety during the high-risk summer months and achieving a 36% reduction in recordable injuries serves as an inspiration, highlighting the significance of advancing safety practices within teams.
geographe.com.au
CLAUDE MOCELLIN WAS CELEBRATED AT THE 2024 PROSPECT AWARDS FOR HIS UNWAVERING DEDICATION TO SAFETY, SUSTAINABILITY AND EFFICIENCY.
Awarded to an individual who has led a project or mine site to a successful outcome, the Project Lead of the Year category at this year’s Prospect Awards celebrated Claude Mocellin for his leadership at South32’s Dendrobium Area 3C extension project in New South Wales.
As the program manager, Mocellin led a multi-year initiative that brought about significant improvements to safety, operational efficiency, and environmental sustainability.
The Area 3C program, which ran from September 2021 to June
One of the most significant achievements of the project was reducing greenhouse gas emissions through a facility designed to flare pre-drainage gases. This innovation allowed the mine to tap into metallurgical coal reserves more efficiently while also addressing environmental concerns.
Throughout the program, Mocellin placed a heavy emphasis on safety, initiating a cultural shift that improved the overall safety performance of the project.
Under his leadership, the team conducted mock emergency evacuations and rewarded strong safety behaviour, contributing to a program that
Mocellin’s approach to the project was notable not only for its operational success but also for the way he mentored his team as he pushed for the inclusion of graduates in project teams, fostering an environment of learning and collaboration.
Mocellin’s leadership style, described as ‘more of a coach than a manager’, empowered his team to take ownership of problem-solving and escalate issues when necessary. This resulted in a highperforming team that thrived under his guidance.
The program also had a positive impact on the surrounding community.
Mocellin oversaw multiple community projects that upgraded
the first Sunday in March at the Illawarra catchment, further strengthening ties with the local community.
One of the key elements of Mocellin’s success was his ability to navigate challenges mid-project, with his negotiation skills critical in resolving any delays, ensuring the project stayed on track while prioritising worker safety.
Mocellin’s leadership in the Dendrobium Area 3C expansion has left a lasting impact on both the project and the community, making him a deserving recipient of the Project Lead of the Year Award at the 2024 Prospect Awards.
His focus on safety, environmental sustainability, and mentorship has set a
• Integrated cooling DURAPLATETM
• Drop-in footprints via customisable mounting feet
• Local engineering expertise
• Australian stock and assembly
• Full rebuild facilities on east and west coasts
• Full load testing to 1mW
DURAPLATETM
Integrated gearbox cooling system
NO external coolers required
NO external power or water required
Highly durable and damage resistant compared to alternate methods
Fully self contained
It’s no secret that innovation is key to unlocking new opportunities and maintaining a competitive edge in the mining industry.
Understanding this, IPI Australia – a fixed plant performance improvement specialist – has created a shaft alignment system (SAS) to address common conveyor challenges. Existing shaft alignment practices require surveyors to repurpose standard survey equipment to approximate pulley alignment based on the construction of a virtual pulley shell, as it sits spatially to the centreline of the conveyor it’s mounted to.
However, confirmation of the alignment is almost never performed because it’s too time consuming. This is where IPI’s SAS can help. Intended to be a permanent fixture to pulley bearing housings, IPI’s SAS safeguards correct factory seal alignment, prevents seal displacement during transport and handling, allows for pulley alignment directly off the shaft axis, and eliminates the need for seal adjustment when a pulley is landed on a conveyor structure.
It doesn’t need belt pockets to be pulled to function, reducing pulley installation timeframes and complexity and eliminating bearing contamination risks associated with in-situ shaft and seal alignments.
IPI’s SAS also provides real-time alignment data directly from the axis of the pulley shaft, ensuring accuracy.
According to IPI, no other solution performs the wide range of functions that the IPI SAS does.
“No existing product can ensure correct factory seal alignment and then guarantee that alignment is maintained through to final installation,” IPI Australia general manager Bart Morris said.
“No existing product can prevent housing over-rotation (known to damage seals) during transport and handling. No other product can facilitate shaft and seal alignment of pulleys during installation.”
Other benefits of IPI’s SAS include eliminating the need for building pockets, leading to reduced risks of airborne contamination entering the housing and increasing worker safety, as well as time and cost savings since a SAS can be performed in less than 30 minutes
compared to existing seal alignment practices taking over six hours.
Backed by a plethora of benefits, it’s no wonder IPI Australia took out the Innovative Mining Solution award at the 2024 Australian Mining Prospect Awards.
The Innovative Mining Solution award recognises a mine, company, or project that has developed a unique mining solution – which the IPI SAS has done for multiple clients.
Since hitting the market in February 2024, IPI Australia’s SAS has caught the eye of multiple major miners operating in Australia, with one company successfully deploying five generation one SAS’ across its mine sites.
One client used the SAS to confirm the alignment of an overlander drive pulley and to align a bend pulley that was believed to be 9mm out of alignment. Installation of the IPI SAS resulted in the belt avoiding contact with the conveyor structure.
Another client mounted the IPI SAS to a tripper head pulley that was used to correct pulley misalignment responsible for belt edge damage.
Installing the IPI SAS lead to both clients saving money that would have ordinarily been spent on fixing the damage caused to the belt.
Despite seeing significant success with its SAS generation one, IPI Australia hasn’t stopped there. In response to issues faced by installers with non-compliant shaft ends, IPI has redesigned the SAS into a generation two tool, which doesn’t require housing fluid to be displaced, making it easier for customers to complete all parts of a pulley alignment.
SAS generation two also ensures that seals are set correctly and are protected from damage through to service and the correctly aligned pulleys are installed with minimum effort.
IPI Australia firmly believes innovative and efficient approaches to solving problems is key to improving common practices in the mining industry, and both generations of its SAS are an example of that. AM
The Innovative Mining Solution award was proudly sponsored by Austmine.
20–22
The Global Resources Innovation Expo (GRX) is an industry-led annual conference and exhibition, proudly hosted by Austmine in partnership with AusIMM.
GRX25 will shine a spotlight on the technologies, breakthroughs, and collaborations taking place in our industry, offering a global platform for thought leaders and innovators to drive the necessary changes.
Conference themes:
Harnessing the Power of Disruption
Pioneering Change Across the Globe
Trailblazing Technologies: Unlocking Growth, Sustainability and Profitability
Shattering the Boundaries: Collaborative Innovation
Paving the Way to Our Bold Future
By industry, for industry
MINRES TOOK HOME THE 2024 OUTSTANDING MINE PERFORMANCE AWARD FOR ITS WODGINA AND MT MARION LITHIUM MINES IN WESTERN AUSTRALIA.
This year, Mineral Resources (MinRes) has been recognised at the Australian Mining Prospect Awards for its achievements at the Wodgina and Mt Marion lithium mines in Western Australia.
These operations are key to Australia’s growing lithium sector and have set new benchmarks in performance and growth, earning MinRes the Outstanding Mine Performance award.
Both Wodgina and Mt Marion are situated in iconic Australian mining regions, with Wodgina located approximately 120km south of Port Hedland, and Mt Marion just 40km southwest of Kalgoorlie.
These two projects have significantly contributed to Australia’s global standing as a major player in the lithium market, essential for electric vehicle batteries and renewable energy technologies.
MinRes delivered exceptional results
both Wodgina and Mt Marion setting records for lithium shipments.
Wodgina achieved a 41 per cent increase in production, delivering 201,000 dry metric tonnes (dmt) of spodumene, while Mt Marion exceeded saw a 46 per cent increase, delivering 218,000dmt.
These figures reflect MinRes’ commitment to operational excellence and efficiency in a competitive and rapidly growing global lithium market.
The company’s ability to scale up operations at both mines has positioned it at the forefront of the lithium industry, supporting global demand for the mineral as the world transitions towards greener energy solutions.
In addition to its award-winning performance, MinRes is making significant strides at Mt Marion, transitioning the mine to both an open pit and underground operation.
This evolution signals a new era for the
importance in MinRes’ portfolio and its long-term contribution to lithium supply.
The shift to a dual-operation model at Mt Marion is a bold strategic move, designed to maximise resource extraction and improve operational flexibility.
This also ensures continues success for the mine as lithium demand is expected to rise in the coming years.
MinRes’ focus on innovation and efficiency extends beyond just extraction as the company’s investments in leading technologies and sustainable practices have also been crucial in enhancing the productivity of its lithium operations.
This approach not only boosts production but also ensures that MinRes remains a responsible and forwardthinking player in the mining industry.
The success at Wodgina and Mt Marion is a testament to MinRes’ strong operational capabilities and its ability to adapt and thrive in the evolving
As the company transitions Mt Marion into an open-pit and underground operation, it looks poised to continue its trajectory of growth.
Now, MinRes’ achievements have been recognised industry-wide, with the Outstanding Mine Performance award celebrating the company’s significant contributions to Australia’s mining sector.
The award not only acknowledges the high performance of the mines but also highlights MinRes’ leadership in advancing lithium production in Australia.
MinRes’ Wodgina and Mt Marion mines are well-positioned to play a critical role in the future of energy as the global demand for lithium continues to rise, driven by electric vehicles and renewable energy storage AM
The Outstanding Mine Performance award was proudly sponsored by SEW-
Proud Sponsor of the 2024 Prospect Awards
Unleash the power of heavy industrial gears with SEW-EURODRIVE. Local availability and support backed by a global network of expertise.
IG Industries
• Mining
• Bulk Materials Handling
• Steel Industry
• Agriculture
• Quarry
• Ports & Logistics
• Sugar Industry
IG Products & Services
• Helical gear units / Helical-bevel gear units
• FleXeDrive
• X.e Series
• Planetary Gear Units
• Segmented Girth Gear
• Drop in Solutions
• DriveRadar ® IoT Suite
THE MAXWELL UNDERGROUND COAL MINE IN NEW SOUTH WALES IS OFF TO A STRONG START THANKS TO WORK COMPLETED BY ROBSON CIVIL PROJECTS.
Robson Civil Projects knows what it takes to get the job done.
So, when Malabar Resources reached out to the company to complete works at its Maxwell underground coal project in New South Wales, there was no doubt the Robson team would be perfect for the job.
Robson’s scope at Maxwell involved underground mine entry works and a 10km access road and conveyer trace. The works also involved the installation of 10 dams and all surface drainage.
And the work was a resounding success.
“Over the course of the project, Robson moved over 1.5 million cubic metres of material and placed 40,000 cubic metres of pavement material,” Robson said.
“Consistent communication and collaboration were essential for the success of the project. Construction
methodologies were adapted to site and geotechnical conditions as they were discovered.
“The project’s success can be measured by all parties working together, achieving coal production on the mine in March 2023 and enabling it to meet its first coal train milestone.”
Located east of Denman and south of Muswellbrook in the NSW Upper Hunter Valley, the Maxwell site was previously home to Anglo American’s Drayton open cut coal mine.
Drayton was closed in September 2016 after 30 years of operation and the site was acquired by Malabar in February 2018. Robson commenced its work onsite in May 2022.
Maxwell, approved by the NSW Government in December 2020, followed comprehensive environmental and technical analysis and more than eight years of ongoing consultation with the local community, ensuring the mine can comfortably co-exist with other
industries and land use in the area.
The target underground mining area sits on the western side of the Muswellbrook anticline, a prominent regional geological feature. Malabar is seeking to maximise resource recovery within geological, environmental and tenement constraints.
Malabar has ensured the project includes ongoing rehabilitation and remediation activities within the Maxwell infrastructure, and rehabilitation of any remaining disturbance areas at mine closure.
Maxwell is set to produce high-quality coal over a period of 26 years, generating 430 full-time jobs and delivering $86 million into the local economy each year.
The mine will also generate $1–1.2 billion in mining royalties for the people of NSW over its 26-year life.
The project has been completed so far with zero lost time injuries.
“(This) is a testament to the project team’s attitude to safety,” Robson said.
“The project team conducted 433 inspections and audits, successfully addressing all 233 identified actions, which demonstrates our commitment to maintaining high safety standards.”
Further, all disturbed areas of the project have been revegetated, with all works completed in compliance with environmental criteria performance measures.
Robson said receiving the Mine Project Success of the Year award at the 2024 Australian Mining Prospect Awards further underscored the project’s success.
“Congratulations to everyone on the project team, the team at Malabar Resources and everyone else involved in the Maxwell underground project,” Robson said.
“We’re still over the moon about (the win). We’d like to thank the project team who worked so hard on this project. The new trophy makes a great addition to the Newcastle office foyer.” AM
FORTESCUE AND LIEBHERR JOINTLY DEVELOPED AN AUTONOMOUS BATTERY-ELECTRIC T 264 TRUCK WITH EFFICIENT FUEL CONSUMPTION IN MIND.
As the world continues to embrace renewables, the mining industry is set to play an important role in the global energy transition.
An Australian mining company that understands this and is ramping up its decarbonisation efforts is Fortescue.
Known globally as one of the largest iron ore producers, Fortescue is aware of the amount of carbon emissions it has created through its operations over the years.
Now, Fortescue has a plan to eliminate Scope 1 and 2 emissions at its Pilbara iron ore operations by 2030 without voluntary carbon offsets and carbon capture and storage, known as ‘real zero’.
“We have identified the solutions needed to eliminate approximately 90 per cent of terrestrial Scope 1 and 2 emissions from our Australian iron ore operations and are actively working to identify solutions for the final approximately 10 per cent,” Fortescue said in its 2023–24 financial year (FY24) sustainability report.
“We are also finalising our plan for how to eliminate Fortescue’s remaining Scope 1 and 2 emissions from across our operations, including Fortescue Energy.”
As 2024 comes to a close, Fortescue has spent the year accelerating its commercial decarbonisation on a rapid, profitable and global basis.
Australian Mining looks at some of the major miner’s most significant decarbonisation moves over the past 12 months.
Liebherr
In December 2023, Australia’s first newly-built electric excavator debuted at Fortescue’s Cloudbreak iron ore mine in Western Australia.
It was the first of three R 9400 E electric excavators commissioned by Liebherr at Fortescue operations during the FY24.
“The commissioning of this fully electric excavator is a massive achievement by the team and is the first of its kind in Australia for the mining industry,” Fortescue Metals chief executive officer (CEO) Dino Otranto said.
A second R 9400 excavator was successfully converted from diesel to electric in January 2024, with Fortescue commissioning the machine at its Christmas Creek iron ore mine in WA.
It was the first time Liebherr had repowered one of its excavators from diesel to electric configuration during the standard service life of the machine.
The three Liebherr R 9400 E electric excavators that became operational at Fortescue’s Cloudbreak and Solomon mines each moved over one million tonnes in the first four months of operations.
“(The machines) are powered by the grid via 6.6 kilovolt substations, switchgear and more than 2km of high voltage trailing cable,” Fortescue said in its climate transition plan.
“A prototype offboard power unit, which can power a Liebherr R 9400 electric excavator that Fortescue Zero retrofitted from a diesel unit using onboard hydrogen and batteries ... is undergoing commissioning and sitebased testing at Christmas Creek.”
And to top it off, Fortescue signed a $US2.8 billion electric equipment deal with Liebherr at MINExpo 2024 in September.
The agreement will see Liebherr deliver 455 zero-emission machines to Fortescue’s operations, including 360 autonomous battery-electric trucks, 55 electric excavators and 60 batterypowered dozers.
This amount is triple the 120 trucks announced as part of the initial partnership between the two companies in 2022.
The influx of zero-emission equipment will represent about twothirds of Fortescue’s current mining fleet.
“This is an important next step in our 2030 ‘real zero’ target – to eliminate emissions from our Australian iron ore operations by the end of the decade,” Fortescue founder and executive chair Andrew Forrest said at MINExpo.
“We can together be the trailblazers who forge the world’s move away from fossil fuels.”
MINExpo also saw Fortescue and Liebherr debut their jointly developed autonomous battery-electric T 264 truck, which has a fleet management system designed to ensure efficient fuel and energy consumption and reduced carbon emissions.
After operating on hydrogen for the first time in May, Fortescue’s hydrogenpowered haul truck prototype Europa touched down in the Pilbara for sitebased testing in August.
Europa contains a 1.6-megawatt battery developed in-house by Fortescue, and 500 kilowatts of fuel cells.
The prototype can store over 380kg of liquid hydrogen and is currently undergoing site-based commissioning at Christmas Creek.
It will be refuelled with liquid hydrogen from a gaseous and liquid hydrogen plant on-site and will join RoadRunner – its battery electric equivalent that underwent site-based testing at Christmas Creek – exceeding the performance expectations of the battery power system while carrying 231 tonnes of iron ore.
“Once we decarbonise our entire fleet, around 95 million litres of diesel will be removed from our operations every year, or more than a quarter of a million tonnes of carbon dioxide equivalent,” Otranto said in March.
Although its supply is vast, hydrogen is not commonly found in its purest form in nature.
Hydrogen can be manually produced through a process called electrolysis, which requires electricity. Electrolysis is achieved by running electricity through demineralised water to split the water into hydrogen and oxygen.
However, when electrolysis is achieved using renewable energy resources like solar and wind, green hydrogen can be extracted from the water.
Green hydrogen has many benefits: it’s non-toxic, contains zero carbon and is highly storable. Fortescue is looking to use green hydrogen to decarbonise its mining and shipping fleet.
To help achieve this goal, Fortescue is committed to scaling green hydrogen production.
FORTESCUE’S HYDROGEN-POWERED HAUL TRUCK IS UNDERTAKING SITE-BASED TESTING IN THE PILBARA.
An example of this is the company’s electrolyser manufacturing facility in Gladstone, Queensland, which opened in April 2024.
The 15,000km2 facility was constructed and fully commissioned over two years and can produce over two gigawatts of proton exchange membrane electrolyser stacks per year.
“The process of splitting hydrogen and oxygen isn’t new – but the innovative ways the world is looking to use green hydrogen to decarbonise are, and that means demand for green hydrogen and for the electrolysers to produce it is growing rapidly,” Fortescue Energy CEO Mark Hutchinson said.
The facility is the first stage of Fortescue’s Green Energy Manufacturing Centre, currently being developed on the 100-hectare site.
Outside of Australia, Fortescue is developing its first green hydrogen facility in Arizona.
Construction at the 150-acre site is slated to create over 2000 jobs, with a further 400 jobs set to be created during operation.
The project, dubbed Arizona Hydrogen, is expected to produce up to 11,000 tonnes of liquid green hydrogen annually.
Arizona Hydrogen is currently in the feasibility stage and is expected to involve construction of up to about 4.5 gigawatts of wind and solar renewable energy resources, which will power electrolysers with the potential to produce up to 200,000 tonnes of green hydrogen per year.
Fortescue also has the rights to develop, build, own and operate another green hydrogen project in Oman via a consortium.
Green hydrogen would be sold to local industrial offtakers and processed into derivatives such as green ammonia for exporting from the port of Salalah.
As part of its efforts of building a green metal supply chain, Fortescue commenced works at its Green Metal project in the Pilbara region in August.
The $50 million project, located at Christmas Creek, is expected to produce more than 1500 tonnes of green metal per annum, with first production anticipated in 2025.
“Locating the project at Christmas Creek will allow Fortescue to demonstrate a ‘green pit to product’ supply chain, with the company’s green mining fleet able to be paired with green metal making,” Fortescue said in its FY24 sustainability report.
The operation will use green hydrogen produced at Fortescue’s gaseous and liquid hydrogen facility, together with an electric smelting furnace, to produce high-purity green metal.
“Iron and steel are the backbone of our infrastructure, however traditional iron and steel production processes are among the largest sources of greenhouse gas emissions,” Forrest said.
“By rethinking the entire iron and steel value chain we can produce an entirely new, green industry here in Australia. Right now, we have a once
FORTESCUE IS COMMITTED TO SCALING GREEN HYDROGEN PRODUCTION.
WE CAN TOGETHER BE THE TRAILBLAZERS WHO FORGE THE WORLD’S MOVE AWAY FROM FOSSIL FUELS.”
in a generation opportunity to build a green supply chain, and Fortescue is wasting no time to seize it.”
If FY24 was a period of great change for Fortescue, FY25 looks to be even bigger.
The major miner has partnered with Downer Group to design and develop a battery-electric locomotive for heavy industry applications such as haul rail.
To decarbonise shipping, Fortescue
develop technologies to lower emissions and build a green fuel supply chain.
The company has also locked in a partnership with MacLean, which will see a fleet of GR8 motor graders become powered by the Fortescue zero emissions power system, expected to be delivered by 2026.
While the outcomes of many of its decarbonisation initiatives are yet to be seen, Fortescue has cemented its reputation as a mining company
FORTESCUE HAS SIGNED A $US2.8 BILLION PARTNERSHIP WITH LIEBHERR FOR THE DELIVERY OF CARBON-FREE MINING SOLUTIONS.
Understand more in minutes to avoid hazards and improve safety.
Featuring Emesent’s most advanced LiDAR scanner, Hovermap LHD ensures load–hall–dump (LHD) operations maximize output and maintain safety by enhancing visibility with detailed 3D imagery.
Connecting easily and securely to the LHD via a purpose-built mount, Hovermap provides a 360-degree scan, helping to identify obstacles and complex structural issues before they become a problem.
emesent.com/underground-mine-production
FENIXLIGHT’S PRODUCTS ARE MADE TO WITHSTAND EXTREME WEATHER CONDITIONS, HIGH LEVELS OF DUST, AND THE CORROSIVE NATURE OF MANY MINING ENVIRONMENTS.
FENIXLIGHT PROVIDES LED LIGHTING SOLUTIONS DESIGNED TO WITHSTAND THE EXTREME CONDITIONS MINERS FACE EVERY DAY.
Mining in Australia is known for its often harsh and demanding environments, with visibility sometimes being the difference between operational success and potential disaster.
Fenixlight, one of the leading providers in high-performance LED lighting solutions, has made a name for itself by offering products designed to withstand the extreme conditions miners face daily.
Established in 2001, the company’s expertise extends across industries such as mining, construction, law enforcement, and emergency services, providing innovative, durable and reliable lighting products that are trusted worldwide.
From product durability to energy efficiency, Fenixlight’s offerings are specifically designed for mining operations, which require highperformance lighting to enhance safety, productivity, and sustainability.
“We tailor our lighting solutions to withstand extreme weather conditions, high levels of dust, and the corrosive nature of many mining environments,” Fenixlight Australia director Marco Orlando told Australian Mining
“We also recognise the importance of energy efficiency, so we ensure our lights are not only robust but also reduce energy consumption, which is essential for mining operations with long operational hours.”
Mining environments demand lighting solutions that are not only tough but also capable of performing consistently over time.
Fenixlight products, many of which meet IP66 and IP68 ratings, are dusttight and water-resistant which is crucial for the conditions miners face every day.
The LED lights’ high lumen outputs guarantee maximum visibility,
particularly in underground and lowlight conditions, enhancing both safety and operational efficiency.
Research and development (R&D) is a major part of Fenixlight’s approach, with the company constantly evolving its product lines to meet the growing safety and efficiency demands of mining operations.
“We continuously invest in R&D to integrate new LED technologies,” Orlando said.
“Our focus is on enhancing safety through more efficient lighting, reducing power consumption, and extending product lifespans.”
The company’s design process is detailed, beginning with direct input from mining professionals and industry experts.
Once a product’s design is finalised, Fenixlight rigorously tests it in simulated environments to ensure it can handle the extreme conditions of mining.
“Our products meet several industry standards, including IP66, IP68, and ATEX for hazardous locations,” Orlando said.
This adherence to high standards ensures that Fenixlight products not only comply with but often exceed international safety certifications.
A key way Fenixlight contributes to greater mining efficiency is by reducing downtime caused by lighting failures.
Orlando said its products are designed with longevity and low energy consumption in mind, helping to decrease maintenance needs and keep operations running smoothly.
“With extended lifespans and low energy consumption, our products require fewer replacements and less maintenance, reducing downtime
associated with lighting failures,” he said. “Additionally, our lights deliver consistent performance in challenging environments, ensuring miners have clear visibility, which directly impacts productivity.”
One standout example of Fenixlight’s impact on the mining industry is the company’s partnership with a major Australian mining company, where the introduction of advanced LED flashlights and headlights have made a significant difference.
“The switch to our advanced LED flashlights and headlights have significantly improved the miner’s visibility, reducing the risk of accidents related to poor lighting,” Orlando said.
“The long-lasting nature of our lights and reduced need for maintenance has also helped increase operational uptime.”
This partnership highlights the critical role Fenixlight’s products play in not only improving safety but also in enhancing operational efficiency – a twofold emphasis that the company strives to maintain across its entire product line.
As mining companies increasingly decarbonise their operations, Fenixlight
“By using LED technology, we can reduce energy consumption by up to 70 per cent compared to traditional lighting, and we are constantly innovating to make our products even more energy-efficient,” Orlando said.
“The longevity of our products means less waste and fewer replacements, which aligns with the mining industry’s goals for more sustainable and environmentally friendly operations.”
Looking to the future, Fenixlight is focused on remaining at the forefront of lighting technology.
Orlando said the company is investing in cutting-edge technologies, such as hands-free lighting with gesture control, improved lumen output, and advanced thermal management systems.
“The future of mining lighting will likely focus on greater energy efficiency,” he said.
“Fenixlight is investing heavily in R&D to ensure we continue to lead the market with innovative solutions.”
Through innovation and a commitment to customer feedback, Fenixlight continues to illuminate the way forward for Australian miners, ensuring that their operations can thrive in even the most
CRUSADER HOSE DESIGNS DEWATERING SYSTEMS FOR SAFER HANDLING UP HIGH PIT WALLS.
CRUSADER HOSE HAS AN UNWAVERING COMMITMENT TO MANUFACTURING THE MOST ROBUST AND RELIABLE HOSE SYSTEMS FOR AUSTRALIAN INDUSTRY.
Dewatering is critical to any mining operation’s success and development.
Designed to control the inflows and lowering of groundwater levels, dewatering ensures the safety and efficiency of a mine site by removing water from underground and surface areas.
While dewatering is a vital process, operators are all too familiar with the challenges of safely running long overland pipelines and up high pit walls. To address these issues, Crusader Hose’s range of layflat hose and reel systems are designed and built to withstand harsh environmental conditions.
Based in Bayswater, Victoria, Crusader Hose manufactures worldleading layflat hose and handling systems locally for a variety of industrial applications.
And each layflat hose system is built with innovation at the forefront.
“We drive continuous improvement through our culture, from a whole of business perspective, not just in engineering or production,” Crusader
Hose Defence Business Manager Stuart Enright told Australian Mining
“We conduct surveys and get customer feedback on what works well for them and what products they would like to see. If there’s a gap in the market, we investigate it.”
Crusader Hose unveiled a variety of developments across its hose reel and winder systems range in 2024, including the Argyle layflat hose handling solution.
Designed for the rapid deployment and retrieval of a layflat hose, Argyle was fabricated to help alleviate manual labour challenges associated with handling layflat hose pipelines, ensuring ease of use and installation, safety, and efficiency.
“It can be towed by any four-wheel drive and deploys 200m of hose up to eight inches,” Enright said. “We’re seeing it be really useful in dealing with flood events or as an emergency stopgap.
“We had a customer that had their major ring lane damaged while conducting repair work. They were able to quickly roll out one of our hose
reel systems and deploy some hose as a stopgap.”
Crusader Hose has also revolutionised its larger Hamersley reel system, which has a strong reputation in the mining industry as a leading solution for rapid dewatering.
“We developed the latest generation of Hamersley based on customer feedback,” Enright said. “Hamersley is useful for laying down larger hose lengths of up to 12 inches in diameter.
“We’ve started to see customers choose layflat overland pipelines hoses rather than running polylines. The benefit there is the speed of deployment and redeployment.
“Sometimes overland pipelines might be positioned only for a year or two, so installation and decommissioning of a polyline taking up 10–15 per cent of the total use time is unpalatable.
“But layflat only requires a couple of days to roll it up and redeploy to another area of the mine or business.”
Other benefits of Crusader Hose’s product portfolio include abrasion resistance, flexibility and adaptability
to various terrain, mobility, and guaranteed long-term performance.
“There are plenty of benefits in the speed in which you can set up a layflat hose system,” Enright said. “For example, a 4km pipeline of poly pipe might take several weeks to a month to install, whereas our hose systems can be deployed in only a few days, getting your operation up and running in a shorter amount of time.
“At the end, it’s easy to roll it up and take for use elsewhere or disposal, rather than trying to deal with truckloads of poly pipe.
“What we see with several mines conducting ground dewatering is they’ll do it in one area of the mine for a particular period of time so they can excavate the area, and while that excavation is happening, they’ll try to dewater another area.
“With our layflat hose system, you can redeploy all the bore hoses and overland pipeline hoses straight to that other area. You don’t need to cut or reweld anything. It’s much simpler and safer.
“You also get the benefit of the hose being elastomeric, so it swells
to a greater size than its diameter at working pressure, allowing more fluid flow through the product. It’s better at conforming to undulations in terrain, so you don’t need to support it as it conforms to the contours naturally.”
If users need to traverse equipment or trucks across the layflat hose system, they can depressurise it so it can be driven over, removing the need for disassembling the line or building a bridge. Deploying the system from location to location is also made easier.
Crusader Hose also sells field-fittable hose couplings to provide flexibility to the user on the ground.
“If you damage the layflat hose system, you can cut that point and put two new couplings in to get the hose back to full operation without any welding,” Enright said.
Looking ahead to 2025, Crusader Hose has several projects in the works.
The company is working with a mining customer requiring several hose systems for its 450m vertical high pit wall.
Crusader Hose is developing a hose rugged enough for the customer to move around the mine and up and down the benches. It will also have enough pressure to deal with the 50 bar of head required for the pump and hose to work. The project is due for delivery in early 2025.
In the defence industry, Crusader Hose is using its decades of experience supplying the Australian Defence Force with layflat hose and reel systems for its
rapid refuelling projects to design and manufacture a ship-to-shore system for the South Korean Navy.
Enright described the relationship and project as collaborative.
“We did lots of research into their use case, looked at their requirements, and we negotiated where their requirements weren’t aligned with what their use case was, so we could essentially tailor a bespoke solution to them,” he said.
“I think they were very receptive to seeing our want to provide a solution and not just a system. It would have been easy for us just to say, ‘Yep, no worries. We’ll align with the requirements you’ve given’, but that wouldn’t be in anyone’s best interest.
“We’ve spent a lot of time ensuring the system will meet the end user’s needs. When (the South Korean Navy) came out to witness testing and precommissioning, they were blown away by the extra attention to detail we’d gone to in order to ensure the system we provide is world-class.”
If innovation is the brain power behind Crusader Hose, quality is at its heart.
“We put a lot of effort into making sure nothing leaves here that we aren’t proud of,” Enright said.
“We’re working on creating turn-key solutions with our customers, rather than them just calling us or sending a request for a quote … We can provide our expertise to ensure they’re able to get on with their core business.” AM
MCLANAHAN’S RECENT PARTNERSHIP WITH A MAJOR MINER HAS BECOME A CRITICAL COMPONENT IN THE EXPANSION OF A CRITICAL MINERALS PROJECT IN QUEENSLAND.
Mplayed a key role in increasing throughput at a major miner’s Queensland aluminium project to seven million tonnes per annum.
Pivotal to this achievement is McLanahan’s wobbler feeder and cross belt sampling system, each designed to address the unique challenges associated with bauxite processing.
Peter Bone, regional manager –wet processing at McLanahan, spoke to Australian Mining about how the partnership began.
“McLanahan worked collaboratively with the mining company and its engineering partner to investigate solutions to improve the scalping of saleable bauxite from their run of mine feed,” Bone said.
“Bauxite is very sticky and highly cohesive. It tended to agglomerate as it passed over the existing vibrating screen, leading to low screening efficiencies and loss of saleable product to oversized reject material.”
To address these issues, McLanahan recommended the use of a wobbler feeder, which can scalp -3.5 inches (89mm) of material from the feed with high efficiency. This not only allows for direct shipment of the product material, but it also reduces the material load sent for further processing.
such as vibrating screens and grizzly feeders often struggle with the wet, sticky texture of bauxite, an issue especially pronounced in Queensland’s tropical environment.
“Bauxite tends to build up on surfaces such as feed and discharge chutes and agglomerates into larger lumps under its own mass,” Bone said.
The wobbler feeder overcomes these limitations with its self-cleaning mechanism. Wobbler feeders feature elliptical bars that rotate at low revolutions per minute (RPM) oriented at 90 degrees to the adjoining bar, agitating the material and releasing fines while preventing clogging.
“Every second wobbler bar cleans the adjacent bar, physically preventing the sticky product from building up,” Bone said.
This helps maintain throughput and minimises downtime, which is especially crucial when operations restart after the wet season.
MCLANAHAN’S EQUIPMENT WAS CENTRAL TO THE PROJECT’S SUCCESS.
MCLANAHAN RECOMMENDED THE USE OF A WOBBLER FEEDER TO ADDRESS THE ISSUE OF STICKY BAUXITE.
In addition to the wobbler feeder, McLanahan has also supplied the miner with a cross belt sampling system to enable the company to more easily collect representative samples of the -3.5-inch material to ensure quality standards are met.
Bauxite is primarily used in the production of alumina and, ultimately, aluminium, but it contains multiple compounds that affect its suitability for alumina production.
“Accurate sampling of the bauxite is critical in determining the types and concentrations of the desirable aluminaproducing compounds so an accurate value can be determined for the ore,” Bone said.
The implementation of McLanahan’s wobbler feeder and cross belt sampling system at the Queensland mine represents a significant upgrade in the site’s processing capabilities.
“McLanahan equipment is fit for purpose with high-end components used,” Bone said. “The McLanahan customer service team supports our equipment with service centres across Australia and around the world to ensure ongoing performance.”
McLanahan’s partnership with the miner continues to prioritise operational efficiency, positioning the critical minerals mine for sustained success. AM
Australian Power Equipment is a leading provider of low, medium and high-voltage power equipment across the Power Generation, Infrastructure, Renewable Energy and Resources sectors.
As the agents for Üntel cables, B&D transformers, Leistung Energie switchgear, CAB cable systems and WE Walter substations, they can supply new equipment to specification.
With a strong commitment to sustainability, the company also provides repurposed and refurbished equipment including substations, transformers and switchrooms.
They can provide immediate solutions to unplanned outages with their in-stock equipment or their critical sourcing solutions.
Australian Power Equipment is dedicated to delivering exceptional customer service and electrical engineering support, ensuring businesses can make best-practice decisions for their operations.
AA successful collaboration between National Group, Komatsu Australia and Cummins South Pacific is delivering efficiency gains and environmental benefits for mining companies through advanced engine technology.
In early 2023, National Group, a leading privately-owned mining services firm, embarked on the largest engine upgrade in its history.
The goal: upgrading each engine in 16 Komatsu 830E haul trucks used at the Lake Lindsay and Curragh coal mines in the Bowen Basin in central Queensland.
National Group’s multi-milliondollar project involved converting the Cummins Tier 1 QSK60 engines in the haul trucks to its ‘Advantage’ solution. Cummins’ Advantage solution enables the QSK60 to be upgraded to the latest diesel technology at overhaul time with no major changes to the base 60-litre V16 design. The result is lower fuel consumption and greenhouse gas emissions, and a substantial extension to engine life in the haul trucks.
National Group founder and
providing one of the largest and most advanced equipment fleets in the Australian mining sector.
“National Group continues to invest heavily in its fleet,” Ackroyd said. “We are providing more equipment that utilises the latest technology to help our mining clients reduce their fuel consumption and carbon footprint.”
The engine upgrade is an important part of National Group’s broader environmental, social and governance (ESG) strategy. In 2023, National Group launched a sustainability strategy to build on its previous sustainability achievements and provide a roadmap to expand its ESG focus this decade.
“The engine upgrade is the largest initiative so far resulting from National Group’s new sustainability strategy,” Ackroyd said.
“We plan to further expand our ESG focus and are encouraged by the early success of the engine upgrade project. The feedback from project stakeholders has been very positive.”
To date, 12 of 16 engines have been upgraded on time and on budget, with no safety incidents or project setbacks. The remaining engines are
The project’s complexity is reflected in the amount of planning required, the number of people involved across three firms, and the scale of National Group’s investment to upgrade 16 engines.
Each engine, about 2.5m high and 3m wide, was removed on-site by Cummins engineers, then upgraded and resupplied as certified modular common-rail system (MCRS) engines.
For National Group, that meant getting back the engines it originally purchased and are familiar to its on-site maintenance teams.
The modularised engines were then sent to one of Komatsu’s Mackay workshops for engine overhaul and upgrades, then returned to site to be reinstalled into the next 830E.
Each overhaul and upgrade in Mackay took around 200 hours, including extensive testing.
The key technology upgrade was to the engine’s fuel injection system.
The early high-pressure unit injection system (HPI) was replaced with the high-pressure MCRS that now feature on all of Cummins’ latest-generation high-horsepower engines.
Cummins’ Advantage solution
most stringent off-highway emissions standards in the world, delivering a proven 63 per cent reduction in diesel particulate matter.
In addition, lower fuel consumption supports a reduction of Scope 1 carbon emissions aligned to the National Greenhouse and Energy Reporting (NGER) scheme.
Cummins’ Emerald branch manager Glen Evans said the engine upgrade required extensive collaboration.
“A lot of credit should go to the teams at National Group, Komatsu and Cummins on this project,” he said.
and Stage V emissions compliance – the
NATIONAL GROUP’S LARGEST ENGINE UPGRADE REQUIRED A TEAM EFFORT BETWEEN VARIOUS PARTNERS.
“Everyone worked together really well to understand each other’s needs, what was required and how to ensure the project achieved its goals. The project has been a good opportunity for Cummins to expand its relationship with National Group.”
At the ground level, Evans’ colleague and Cummins product support representative Fredy Cerdan liaised with National Group maintenance superintendent Damien Melville.
A larger group of stakeholders from National Group, Cummins and Komatsu was then formed and the group met before the project officially began.
Komatsu Australia’s Queensland regional service manager Gary Clarke said a unique feature of the Komatsu 830E truck is its modularisation.
“All the engine components are in one module that slides in and out of the 830E,” he said. “It’s a really great design and means we were able
to complete all of the upgrades and modifications off the truck which reduced downtime when we completed the installations on-site.
As Clarke explained, the task is made more sophisticated by the size of the engines.
“With the MCRS engine, we are installing a 60-litre engine into a very large haul truck,” he said. “For comparison, with a car, you’re typically talking about a 3-4-litre engine.
“But there have been no quality issues with the build or installation, everything has been delivered on time and there have been no safety incidents.
“The first upgraded 830E has been in operation for over a year and 11 others are in the field. From Komatsu’s perspective, the results so far have been as expected.”
Clarke said Komatsu welcomed the opportunity to work closer with National Group.
“It’s one of the biggest projects Komatsu has ever undertaken for National Group, so it’s great that the relationship between our organisations continues to grow,” Clarke said. “The National Group and Cummins teams have been great to work with.”
Equipment upgrades to achieve improved environmental outcomes are not mandatory, making National Group’s investment all the more impressive.
“Costly upgrades of equipment to deliver these benefits are not something mining contractors in Queensland are required to do,” Clarke said.
“The direct benefits of reduced fuel consumption and lower greenhouse gas
NATIONAL GROUP’S COMMITMENT IS TO HAVE ONE OF THE AUSTRALIAN MINING SECTOR’S LARGEST AND MOST ADVANCED EQUIPMENT FLEETS.
investment in this project for its clients, even though it receives indirect benefits from the engine upgrade.”
For Ackroyd, the main benefit is helping National Group clients achieve their goals.
“Our firm’s DNA has always been built on being customer-focused,” he said. “Our clients want to use mining equipment that reduces their carbon footprint through lower fuel consumption.
“ We are responding to our clients’ needs through this investment in engine upgrades.”
Cummins and our people have learnt more about collaboration on large projects,” he said.
“As we continue to expand and upgrade National Group’s fleet, in response to rising demand for our services, the ability to collaborate with other firms is increasingly valuable.”
Another benefit of the project is its alignment with National Group’s sustainability strategy.
“The risk with developing a sustainability strategy is that it looks great on paper, but ultimately sits on the shelf,” Ackroyd said.
investments that will benefit our clients, mining workers, communities and the environment for years to come.”
And when it comes to further expansion, Ackroyd said he expects National Group to further upgrade its fleet in the next few years.
“It’s something we are looking at,” he said. “Our business has a lot of momentum and capacity to invest.
“We see the quality of our fleet, and the maintenance skills behind it, as key competitive advantages that we continue to build on to support our clients as they grow.” AM
SCHLAM’S HERCULES OPEN-CUT DUMP BODY IS NOW A HOUSEHOLD NAME IN THE MINING INDUSTRY.
Hercules is a true testament to Schlam’s business, offering clients a range of proven benefits from increased payload capacity to extended asset longevity,
With a commitment to customer service and a foundation built on strong values, Schlam partners closely with its clients to tackle unique challenges to optimise payload productivity.
Tackling payload challenges together
Guided by a commitment to customer service and a core set of values, Schlam has a reputation for assisting its clients in overcoming any challenge.
Schlam’s success can also be attributed to its focus on innovation, demonstrated by the triumph of its Hercules open-cut dump bodies as they continue to deliver significant payload savings for miners across the globe.
According to Schlam Payload AsiaPacific managing director Hendrik Mueller, the success of Hercules has ensued from a culture of continuous product improvement.
“Our clients are our partners, and we collaborate to tackle the payload challenges they encounter,” Mueller said. “Their challenges drive us to push our limits, resulting in continuous improvements in our payload products.”
Characterised by its innovative curved shape, the Hercules open-cut dump body has become one of the most sought-after payload solutions among leading miners.
The Hercules dump body provides both a reduced body weight and a longer service life. This is achieved by targeting weight reduction in all nonwearing areas and optimising lighter yet stronger materials for structural components – all without sacrificing structural integrity.
“Traditionally, miners have faced a choice: a lightweight body that offers a greater payload but has a shorter lifespan, or a heavier body that lasts longer but reduces the payload capacity,” Mueller said.
“Hercules was developed as a product to offer both.”
Most mining operators plan for a long asset service life to maximise their asset investment. Hercules dump bodies are designed to experience less structural fatigue, prolonging the life of the asset and ensuring compatibility with any site production strategy.
Schlam clients can also further extend the service life of their Hercules body by designing the ideal wear package for installation during manufacturing and providing an optional product lifecycle support program.
The lighter Hercules body can accommodate a wear package without sacrificing payload performance. A Hercules body fitted with a bespoke wear package usually weighs less than a comparative OEM (original equipment manufacturer) dump body.
Schlam’s optional product lifecycle support program includes site visits and inspections where wear rates are measured, enabling corrective measures to be prescribed.
“Hercules bodies typically have a longer service life, which can be further extended with the right wear
mitigation strategy. For instance, one Hercules dump body was recently decommissioned after a long 12 years of operation,” Mueller said.
Schlam works closely with its clients to address site-specific variables, including wear, material flow, and asset lifecycle management, to design and engineer every Hercules body individually.
“Each mine site is unique,” Mueller said. “One site might struggle with abrasion, while another could be dealing with material hang-up.
“We invest significant effort in designing each Hercules for maximum performance at the site it will operate in.”
The demand for Hercules dump bodies is expanding across the global mining industry.
The first Hercules was manufactured in Australia in 2003. Today, Hercules dump bodies are actively engaged in mining operations at mine sites across the world.
Hercules dump bodies consistently deliver the payload advantages they
A HERCULES DUMP TRUCK BODY DESIGNED TO ACCOMMODATE AN AUTOMATED HAULAGE SYSTEM.
were individually designed for – from the deserts of Australia to the plains of Kazakhstan.
Schlam has formed partnerships with quality-driven manufacturers in China and Mexico, allowing the company to quickly respond to the demands of clients in key international markets.
In 2023, Schlam opened a dedicated Americas office situated in Tucson, Arizona, to better serve its clients within the region.
In the same year, Schlam supplied a leading miner in Kazakhstan with seven Hercules bodies.
“In a relatively short time, we’ve developed into a truly global company,” Mueller said. “We’ve achieved a lot, and celebrated many milestones along the way, including the recent 2000th Hercules body.”
As a category-leading manufacturing business, Schlam has invested significantly in technology and innovation. This includes investments in automation, robotics, and other advanced technologies, all combining to provide consistent product quality, enhanced manufacturing efficiencies, and more rewarding career opportunities.
Schlam also continues to research and address new challenges and opportunities presented in the mining industry, including autonomous haulage and decarbonisation.
“We continue to work with our clients throughout the evolution of autonomous fleets, especially in the iron ore mining centre of Western Australia,” Mueller said.
“We’ve even made modifications to Hercules designs to accommodate autonomous technologies and seen Hercules bodies adopted by major autonomous mining fleet operators.”
With a commitment to taking global sustainability seriously, Schlam is also
(per tonne produced), allowing miners to reduce carbon and other emissions.
Schlam also continues to work towards developing lower-carbon products.
“Decarbonisation has become a priority within the resources sector, and we are proud to be developing product
A HERCULES BODY DESIGNED FOR FORTESCUE’S HYDROGEN-POWERED HAUL TRUCK PROTOTYPE.
fuel sources, including hydrogen.” Schlam’s journey from a regional player to a global innovator is testament to the company’s dedication to excellence and client satisfaction.
With a widespread global reach, and with long-term supply contracts in place
SANDVIK’S DECKMAPP CAPTURES, STORES AND SHARES REAL-TIME DATA.
SANDVIK’S ATTENDANCE AT MINEXPO 2024 WAS DEFINED BY INNOVATION, QUALITY AND ENVIRONMENTAL STEWARDSHIP, WITH A RANGE OF NEW PRODUCTS UNVEILED.
eld in Las Vegas from September 24–26, MINExpo 2024 brought together the global mining industry to drive collaboration, innovation and gain valuable insights.
Sandvik Rock Processing Solutions was front and centre at this year’s event, ready to showcase its range of innovative and sustainable technology.
“Not only is our latest equipment easier to operate, manage, maintain and service, but it also contributes to our industry’s desire to reduce its environmental impact,” Sandvik Rock Processing Solutions president Richard
“Through our close partnerships with customers and our unwavering focus on innovation, we are shaping a future
where rock processing is eco-efficient, productive and sustainable.”
Innovative technology
Sandvik prides itself on being at the forefront of delivering solutions that not only meet but exceed industry expectations.
The company showcased its latest line-up of rock processing solutions at MINExpo 2024, including its 800i cone crusher series, featuring the new ACS-c 5 automation system.
The Sandvik 800i cone crusher series reflects the company’s commitment to the continuous evolution of design, materials and technology.
The latest models, integrated with the new ACS-c 5 automation system, combine robust mechanical design with powerful, user-friendly automation, supporting diverse operational needs.
And thanks to recent acquisitions, Sandvik now offers an expanded lineup of heavy-duty vibrating screens and feeders adapted to the world’s toughest mineral processing applications.
Sandvik’s newly launched solutions are engineered to reduce energy consumption, minimise waste and optimise operational efficiency.
These advancements are geared toward assisting companies seeking to improve their environmental footprint while delivering high performance.
Sandvik launched its groundbreaking digital platform for screen deck maintenance, DeckMapp, at MINExpo 2024.
Accessible via laptop, tablet or mobile phone, DeckMapp captures, stores and shares real-time data to present a reliable, single source of truth for all activities within the screen media lifecycle.
Sandvik digital solutions product manager Matt Cutbush was on the exhibition floor to show attendees how DeckMapp works.
“By guiding operators through maintenance updates and wear assessments, DeckMapp ensures consistent data entry across the board, resulting in robust, reliable historical wear data for every screen in your operation,” Cutbush said.
“DeckMapp enhances data quality and formalises maintenance processes, eliminating information inconsistencies that can adversely affect production and
profitability due to rework and extended task durations.
“DeckMapp delivers real-time updates to ensure all team members are aligned, further reducing the risk of miscommunication and operational inefficiencies.”
A key feature of DeckMapp is the optional add-on WearApp, an innovative wear assessment system powered by artificial intelligence (AI).
Using WearApp, users can capture images of worn screening media panels with a smartphone or a tablet. WearApp then applies AI to automatically assess each aperture, calculating the amount of wear, panel efficiency and remaining wear life.
The enhanced capabilities of DeckMapp and WearApp allow processing plant operators to make more informed decisions regarding their screening media maintenance strategies.
Sandvik’s commitment to driving innovation and sustainability is longstanding, with the company continuously pushing the latest solutions in ecoefficient rock processing.
“One of the main aspects of our approach to eco-efficient rock processing is focusing on extending the crushing process,” Harris said.
“This will decrease reliance on energy-intensive conventional grinding, which accounts for about 40 per cent of the energy used in the comminution process, while significantly reducing overall energy consumption and operating expenses. Our message is clear: crush more –grind less.”
By working closely with its customers to optimise comminution circuits and incorporate the latest technology, Sandvik can move the transfer size between crushing and milling down towards 6mm to enable much more efficient grinding processes.
Sandvik’s processing solutions can also achieve up to 50 per cent greater energy efficiency compared to conventional grinding.
“Sustainability is an essential component of modern mining operations,” Harris said.
“We are committed to leading the industry toward a future where eco-efficiency is standard and not the exception.” AM
EARLY FIELD TEST RESULTS FROM A HYBRID DIESEL-BATTERY MINING TRUCK DEPLOYED IN CHINA HAVE SHOWN MARKED IMPROVEMENTS IN FUEL EFFICIENCY.
According to Cummins executive director of strategy, digital and product planning Molly Puga, the global need to reduce mining emissions will be achieved with the support of ready-to-implement power solutions.
“Cummins anticipates that the mining industry will need multiple power technology solutions for the foreseeable future,” Puga said at MINExpo 2024 in Las Vegas during September.
“The mining energy transition will be driven by the availability of solutions that help achieve TCO (total cost of ownership) parity or improvement, combined with the ability to meet varied environmental sustainability goals in operation.”
And Cummins has seen first-hand how important it is to provide operations with ready-to-implement technologies.
Early field test results of a hybrid dieselbattery mining truck deployed in China have shown 15–20 per cent improvements in fuel efficiency after Cummins laid out
the bridge technologies it is pursuing to support the energy transition.
“While longer term zero-emission technologies – such as full batteryelectric solutions and hydrogen – have exciting potential, a lack of infrastructure availability, high upfront costs and performance of current equipment limits how effective this technology can be over the coming years,” Puga said.
“Based on conversations with our customers, there has been a noticeable shift in expectations from focusing solely on zero emissions to also considering bridge technologies, which can reduce carbon emissions and assist miners in making sustainability progress this decade.”
Bridge technologies
Cummins will continue to invest in its internal combustion engine range while advancing its Destination Zero strategy for mining, which includes further development of two bridge pathways: hybrid and clean fuel capabilities.
Both technologies provide fuel savings and emissions reductions from well to wheel.
As of 2023, all Cummins highhorsepower engines are approved for unblended use with 100 per cent HVO (hydrated vegetable oil), allowing miners to utilise renewable diesel and generate emissions savings while maintaining power output.
Cummins is also developing dualfuel technology to allow for the use of ethanol or methanol alongside diesel in mining applications.
Cummins, global mining company Vale and Komatsu recently signed an agreement to develop and test dual-fuel haul trucks, powered by a mixture of ethanol and diesel. They are set to be the world’s first dual-fuel powered trucks of their size, with payloads of 250–320 tonnes (t).
For hybrid power units, Cummins is taking a modular approach, with plans for first-fit and retrofit application capabilities.
Cummins’ hybrid solutions can be used in tandem with HVO-ready internal combustion engines to generate
additional emissions benefits, creating an affordable way to reduce emissions and fuel consumption costs compared to alternatives like trolley assist.
Cummins is performing field testing of a mining diesel-battery hybrid truck solution in China with North Hauler Joint Stock Co., Ltd. (NHL).
In the hybrid NTH260, a 220t payload mining truck, the hybrid system allows the truck engine to be downsized from the previous 2500 horsepower (hp) QSK60 engine to the current 2000hp twostage QSK50.
Early field test results show a 15–20 per cent average fuel saving compared to a non-hybrid system.
“Hybrid bridge technology makes economic and environmental sense, which is why it has so much potential to achieve change,” Puga said.
“Projected potential increases significantly when you consider further system optimisation, opportunity charging and use of low-carbon fuels.” AM A
The Schlam Hercules open-cut dump body continues to improve the payload capacity of all classes of haul trucks, across all commodities, the world over.
Engineered to meet the challenges of hard rock mining, the unique Hercules curved design offers a lighter body, with outstanding strength and durability.
Being lighter means your fleet can carry more payload every trip. With a payback period of as little as a few months, you’ll be rewarded with a solution that will keep delivering for longer.
Every Hercules is custom engineered to meet your unique site-specific requirements. We can also design and supply the right wear package, and even a wear maintenance program, to further extend the life of your Hercules body.
Maximise your payload productivity with the Schlam Hercules dump body.
schlam.com/hercules
THANKS TO A STRATEGIC PARTNERSHIP BETWEEN WARRIN MINING, CJD EQUIPMENT AND VOLVO CONSTRUCTION EQUIPMENT, HALLETT GROUP’S TRURO QUARRY HAS BEEN TRANSFORMED WITH VOLVO SITE SOLUTIONS.
In the mining and quarrying industries, partnerships are essential for productivity and profitability.
Hallett Group, a leading operator in concrete and quarrying across South Australia, recently benefitted from its own collaboration with CJD Equipment and Volve Site Solutions in transforming its Truro quarry.
This collaboration has enhanced efficiency and productivity and significantly improved safety at one of the region’s premier hard rock quarries.
“This Truro site was added to the quarry stable in 2018,” Hallett Group managing director Mark Pickard said. “This is, without doubt, one of the best hard rock and hardest rock quarries in South Australia.”
Since acquiring the Truro site in 2018, Hallett Group has quickly established itself as a leading operation.
However, the quarry’s remote location presented unique challenges that called for a more strategic approach to site
management. Hallett adopted Volvo Site Solutions to assist, a company known for its comprehensive, data-driven strategy to streamline their operations.
This decision allowed Hallett to tackle the complexities of quarry management by capturing and analysing operational data to develop customised solutions tailored to the specific needs of the Truro site.
Central to Volvo Site Solutions is the Connected Map platform – a datadriven solution tool offering real-time visualisation of all on-site activities. It is also brand agnostic.
This cutting-edge technology gives site managers a comprehensive overview of vehicles, equipment and personnel, enabling remote monitoring and quick adjustments to site guidelines.
The platform also facilitates the coordination of projects across multiple locations through a single interface, ensuring smooth communication and maximising resource utilisation.
The partnership with Volvo was a natural progression for Hallett Group, underpinned by a longstanding
relationship with CJD Equipment spanning over two decades.
Volvo’s reputation for durability and performance was established at the site, and a Volvo 460B excavator purchased at the outset is still in operation today. Beyond the reliability of its machinery, the opportunity to incorporate Volvo’s advanced excavators, front-end loaders, and digital solutions was a key factor in the decision.
The implementation of Connected Map technology has proved transformative for Truro. Managers now have the tools to monitor activities in real-time, adjust routes, and establish safety zones remotely.
This comprehensive approach to site management has led to increased productivity, lower operational costs, and a safer working environment.
Volvo’s data-driven approach to productivity services provides Hallett Group with a robust toolset for optimising operations.
The system continuously captures data on material movement, machine
usage and site activity, enabling detailed analysis to inform decision-making.
This information is displayed through performance indicators on a visual dashboard, allowing on-site managers and remote supervisors to track progress towards production targets and make informed adjustments.
“One of the main reasons why we chose Volvo for this semi-remote site was their connected map technology,” Pickard said.
Volvo Co-Pilot technology equips each machine at the quarry with the capability to set goals, monitor progress, and collaborate more effectively with the team.
The site solutions are brand agnostic, meaning they can be used across different types of machinery, regardless of the manufacturer. This integration ensures operators work towards shared objectives, fostering a culture of accountability and continuous improvement throughout their fleet.
Putting safety first Safety is paramount in quarry operations, and Volvo’s commitment is evident in several innovative features.
Its Connected Map technology allows for the creation of restricted zones anywhere on-site, providing real-time alerts for approaching traffic and managing one-way road access. A visitor app also works to enhance site security by ensuring that all personnel and visitors are accounted for. These measures reduce the risk of accidents and contribute to a more structured and controlled site environment.
“It has allowed us to be able to, in realtime, understand where that equipment is on-site, and what its performance and operating efficiencies have been,” Pickard said.
Hallett Group values Volvo’s responsiveness and commitment to understanding the specific needs of quarry operators.
The collaborative efforts with CJD Equipment has enabled continuous system refinement, ensuring that Truro quarry remains at the forefront of technological advancements in the industry.
The evolution of these solutions has been instrumental in maintaining high productivity and efficiency standards.
Committed to a sustainable future
In the future, the partnership
GROUP, CJD AND VOLVO ARE COMMITTED TO A SUSTAINABLE FUTURE.
promoting sustainable growth in the quarrying industry.
The collaboration focuses on reducing carbon emissions and improving operational efficiency, setting an example for using innovative technology to achieve sustainability goals.
The continuous development of datadriven solutions shows the potential for more intelligent, environmentally friendly operations in the sector.
The transformation at Hallett Group’s Truro quarry illustrates the profound impact that innovative technology and strategic partnerships can have on the quarrying industry.
By adopting Volvo’s advanced tools like Connected Map and Co-Pilot, Hallett Group has overcome the challenges of its remote location while significantly enhancing productivity, efficiency and safety.
The enduring partnership with CJD Equipment and Volvo has provided dependable machinery and practical solutions, fostering a culture of continuous improvement and sustainability.
“Volvo has listened to and understood our needs as a quarry operator in managing our plant and fleet on-site,” Pickard said.
“The backup support through CJD has allowed us to implement the system as efficiently and productively as possible on the site.
“What we do today will hopefully
have in Volvo in being able to listen to us and then implement these micro changes to be as efficient as possible.”
The experience of Hallett Group demonstrates that adopting datadriven and customised solutions can
This collaboration lays the foundation for a more intelligent, safer and sustainable approach to quarry management. It shows that with the appropriate tools and knowledge, even the most
The global mining industry understands that commodity markets will experience regular fluctuations.
However, it’s fair to say lithium has faced its challenges throughout 2024.
Cyclically low lithium prices were primarily triggered by a supply surplus caused by the increased production of cheaper lithium from countries like Indonesia and China, which have less stringent environmental, social and governance (ESG) standards.
A decrease in global electric vehicle (EV) sales also played a part in the decline, despite EV demand rising.
But despite the testing year, not all hope is lost.
With the Grattan Institute expecting lithium demand to grow by up to 41 times by 2040, many Australian exploration companies are investing in the critical mineral’s future.
Major miners are also joining the frenzy, with Rio Tinto set to acquire Arcadium Lithium for $US6.7 billion ($10 billion).
As 2024 comes to a close, Australian Mining takes a look at two lithiumfocused companies looking to make a splash in the new year.
Since debuting on the ASX in January 2024, Kali Metals – the lithium spin-out of Kalamazoo Resources – has wasted no time.
Backed by an exploration tenure of approximately 3854km2, Kali is exploring three lithium assets: the Higginsville project, the Pilbara project, and the Southern Lachlan Fold Belt project.
Kali managing director Paul Adams said Higginsville is the company’s flagship project, with Kali owning the lithium rights of ground now held by Westgold Resources via its merger with Karora Resources.
“The Higginsville lithium district in southern Western Australia is adjacent to well-known hard rock lithium mines such as Mineral Resources’ (MinRes) Bald Hill and Mt Marion mines,” Adams told Australian Mining
“We’ve got a very large land package right in the middle of that region within the lithium corridor, which presents us with tremendous opportunities.”
In August, preliminary findings into historic drilling at the Spargoville prospect within Higginsville demonstrated the presence of
spodumene in several shallow dipping pegmatite dykes.
“At Spargoville, we completed a maiden reverse circulation drilling program in April and the results included 10m intersections of around one per cent lithium oxide, with some high-grade over four to five metres,” Adams said.
“The reason we started with Spargoville is because we’d identified spodumene on the surface and mapped the pegmatites.
“There was an existing heritage survey over the area and the environmental survey was complete, so as a new ASX-listed company, we wanted to get drilling done as soon as possible. We had all the logistics and various parameters in place to initiate
As Kali embarks on 2025, the company is focused on developing new exploration targets across Higginsville and its Pilbara project, the latter of which comprises the DOM’s Hill and Marble Bar projects situated east of Pilbara Minerals’ Pilgangoora operation and MinRes’ Wodgina mine.
In October, Kali completed its first pass mapping and rock chip sampling over Marble Bar, which returned rock chip assays of up to 1.5 per cent lithium oxide and confirmed lithium–caesium–tantalum (LCT) pegmatites.
“(At the Panther prospect), we’ve got surface widths of circa 15–20m in outcrop,” Adams said. “We plan to go there in early November to get more samples, complete more mapping and
Kali will also target the DOM’s Hill and Pear Creek projects via its joint venture (JV) with Sociedad Química y Minera de Chile (SQM), which was recently expanded and will see SQM spend a minimum of $500,000 on exploration by December 2025 to retain its 30 per cent interest in the tenements.
Outside WA, Kali is focused on exploring the Southern Lachlan Fold Belt in NSW and Victoria, which Adams described as an “emerging lithium province” that hasn’t seen much modern lithium exploration.
“We’ve completed soil sampling (at the Sweetwater project),” Adams said. “We’ve got some kilometre-scale anomalies in pathfinder elements for lithium, but also for tin, tungsten and arsenic, so that’s exciting.”
Adams said Kali has worked hard to refine its strategy amid cyclically low lithium prices.
“It’s going to take a while for the demand side to catch up with the supply side,” Adams said.
“You’ve got a lot of M&A (mergers and acquisitions) happening in the market, including Rio and Arcadium. The cure for low prices is low prices and I think there’ll be several cashed-up lithium companies looking at M&A, asking, ‘What can we do to take advantage of lower share prices to increase our resource inventory?’”
Backed by major shareholders such as Westgold, Kalamazoo and MinRes, Kali is fully funded for exploration up until the end of 2025.
Once spodumene is mined, it can be converted into battery-grade lithium carbonate for use in EV batteries.
A company excelling in this space is IRIS Metals, an ASX-listed explorer and developer with several hard-rock projects across South Dakota, US, and a memorandum of understanding (MoU) in place with a downstream lithium player.
IRIS is specifically focused on developing the Beecher and Tin Mountain projects, both situated in the Black Hills region, one of the largest lithium pegmatite districts in North America.
“The Beecher project is already permitted for mining,” IRIS president – US operations Matt Hartmann told Australian Mining
“Part of that is because we are on private ground, eliminating the influence of the US Forest Service,
other federal entities that can lengthen the permitting process. South Dakota has a very favourable regulatory environment for permitting these types of deposits specifically.”
IRIS has made headway in drilling Beecher, having completed a diamond drilling program in September. A total of 56 diamond core holes were drilled in 2024, totalling 7925m.
“We’ll be moving that forward to a mineral resource estimate (MRE) in the first quarter of 2025,” Hartmann said.
“We are currently drilling Tin Mountain, which is famous for having some of the largest spodumene crystals in the world. They’re like tree logs in the wall rock and are rather impressive.”
Unlike other exploration companies, IRIS is advancing its processing work in parallel with its MRE to expedite the mining process from exploration all the way through to production.
production of six per cent spodumene concentrate from Beecher, which was very low in impurities,” Hartmann said.
“Off the back of that, we supplied that product to ReElement Technologies Inc., which converted our spodumene concentrate into a 99.5 per cent pure battery-grade lithium carbonate.”
Following the successful conversion, IRIS and ReElement signed a MoU for further bulk testing and development of a commercial-scale lithium supply solution for the US market.
“We’re looking at creating a complete US supply chain from the mine all the way to lithium carbonate,” Hartmann said. “Right now, no other US company has that capability.
“Even though we haven’t completed our MRE for the Beecher project, we’ve already demonstrated the potential viability of the project and our
development strategy through the ability to mine spodumene in the US, process that into spodumene concentrate, then convert it into lithium carbonate without the material leaving the US.”
In the US, if lithium exploration and development companies want to unlock funding from the Inflation Reduction Act 2022 (IRA), they must demonstrate their contribution to the entire lithium supply chain.
“We have the front end and ReElement has the back end,” Hartmann said.
“When combined, we can demonstrate the entire process.
Hopefully that will allow us to unlock IRA funding for our projects and ReElement’s process development activities.”
Like Adams, Hartmann believes M&A lithium plays will continue.
“Lithium has been a volatile commodity over the last 15 years as there are several different market dynamics in play,” Hartmann said.
“I think things will flush out over time and we will see rising prices. The fact we’re starting to see M&A discussions and transactions take place indicates that not only do I think the price is going to go up, but some of the other major miners out there think it’ll go up as well.
“This presents IRIS with an opportunity to rapidly advance our projects to the point where they’re ready for production, so when prices do rebound, we can take full advantage.”
According to the September 2024 ‘Resources and Energy Quarterly’ report, global lithium demand is forecast to rise by 17 per cent per year between now and 2026 due to rising EV adoption.
To meet the demand, Kali and IRIS are ramping up their projects, positioning themselves as future lithium suppliers. AM
THACO INDUSTRIES, VIETNAM’S LEADING OEM PARTNER FOR INDUSTRIAL EQUIPMENT, IS GROWING ITS REPUTATION IN THE AUSTRALIAN MINING INDUSTRY.
With large-scale production capabilities and professional services, THACO INDUSTRIES is a strategic partner of major enterprises in the mining industry, particularly in the Australian market.
THACO INDUSTRIES’ manufacturing facilities cover an area of 320 hectares and a total investment capital exceeding $US850 million, comprising a research and development (R&D) centre, mechanical centre, and automotive component manufacturing plants.
The corporation’s plants are equipped with cutting-edge technology lines meeting international standards such as a slitting line, 10 fiber laser cutting machines, a five-axis computer numerical control (CNC) milling
machine, CNC pressing machines, a precision mechanical processing line, 15 press machines (800–6300 tonnes), 100 welding robots, a shot blasting booth, and an electro deposition (ED) coating line.
THACO INDUSTRIES excels in manufacturing and processing large quantities of equipment and mechanical structures with high synchronisation. Its main products include underground mining equipment, conveyor systems, and mining equipment spare parts.
To deliver maximum benefits to customers, THACO INDUSTRIES offers comprehensive OEM services with “all-in-one” solutions, from product R&D, workpiece processing, welding, surface treatment and painting, to assembly, delivery, and installation.
By integrating modern technologies with professional processing capabilities, the corporation commits to delivering optimal solutions and automated extraction processes, enhancing operational efficiency and significantly reducing operating costs.
With a team of over 1000 R&D engineers working in specific teams across various sectors, THACO INDUSTRIES is capable of offering customised designs that meet customers’ unique requirements while adhering to technical standards.
Thus, the company successfully fulfills the specialised demands of projects, even in the Australian market’s challenging terrains.
Notably, THACO INDUSTRIES has extensive experience in processing oversized structures, including frame structures, block/tube/box structures, complex welded structures, and oversized products.
For complex welded structures, the corporation can handle dimensions up to 18 x 2.8 x 0.8m (length x width x height) and weights up to 33 tonnes.
By flexibly integrating advanced robotic welding technology with manual welding, performed by engineers certified at the 4G and 6G level, THACO INDUSTRIES meets stringent standards (AWS D1.1 and ISO 9606-1). This enables the corporation to precisely shape the products’ overall structure.
With a strong focus on rigorous quality control at every stage of production and adherence to international standards such as ISO 9001:2015, THACO INDUSTRIES has established itself as a reliable OEM partner, collaborating with many major mining companies both domestically and internationally.
THACO INDUSTRIES commits to absolute confidentiality regarding project information and is always willing to sign non-disclosure agreements (NDAs) to protect customer information throughout the collaboration.
THACO INDUSTRIES places significant emphasis on sustainable development throughout its manufacturing activities.
The corporation ensures compliance with the standard of environmental management system ISO 14001 and legal environmental regulations, including ISO 45001, BSCI/ESG, CBAM, ISO 14064, and ISO 14067 (European Union market export standards).
THACO INDUSTRIES proudly stands as a reputable and professional OEM partner, delivering comprehensive solutions and supporting mining enterprises throughout their projects. AM
MADE FOR THE
50Hz. Dual Operator. Air. Power. Weld.
Scan to register your interest today!
WHETHER ON THE GLOBAL STAGE OR FROM ITS DEDICATED AUSTRALIAN BUSINESS, THEJO ENGINEERING IS TAKING ITS COMMITMENT TO ITS CUSTOMERS TO A NEW LEVEL.
It was 50 years ago that two childhood friends in India had a vision to partner together and develop a specialised engineering business.
After years of hard work, K.J. Joseph and Thomas John brought their dream to life and launched their jointly owned company: Thejo Engineering. Today, their vision has moved beyond India and onto the global stage.
Thejo Engineering specialises in conveyor belt splicing through a cold vulcanising process, in-situ pulley lagging and in-situ recapping of conveyor belts. The company is also recognised as a leading industrial solutions provider for belt conveyorbased bulk material handling systems, mining and mineral processing and corrosion protection applications.
As Thejo Engineering chair, Joseph believes one of the company’s major strengths is that it has maintained a consistent set of clients from the beginning.
“We might be a small company compared to the global giants, but even though we are small, the unique feature we offer to clients is our sensitivity to their needs,” Joseph told Australian Mining. “One of the key areas where we have made a difference globally is by virtue of being a one-stop shop for services and manufacturing.”
Through the support of its clients, Thejo Engineering has taken the opportunity to grow, expanding its business across India, Australia, the Middle East and South America.
THEJO ENGINEERING HAS FIVE MANUFACTURING PLANTS AND AN R&D CENTRE HEADQUARTERED IN CHENNAI,
Committed to meeting the needs of its clients, Thejo Engineering works to innovate as new challenges arise.
The company’s chief operating officer Manoj Joseph Kallarackal is confident this approach has ensured a lower cost for its clients.
“We initially had a client who called us and said ‘I have a problem with this, can you make something to fix it’,” Kallarackal told Australian Mining. “As a result, Thejo Engineering now has eight product verticals.
“Every step Thejo has taken and every single product we have made, Thejo has developed the technology and manufactured it in-house.”
Headquartered in Chennai, India, the company has five manufacturing plants and a research and development (R&D) centre, which has been approved by the Department of Scientific and Industrial Research, Ministry of Science and Technology of India.
Thejo Engineering managing director V.A. George, who has more than four decades of experience in the industry, has been instrumental in transforming the company from a family-owned business to a global name.
When looking at ways to increase Thejo’s global presence, George found strong demand for its product offering in Australia’s mining industry.
“We are still expanding our presence, though Australia has become our prime focus,” George told Australian Mining
This focus has led to Thejo Engineering launching a subsidiary in
has quickly taken off, with branches in Kalgoorlie, Bunbury and the Pilbara joining the family and supporting the local mining industry.
Thejo Australia’s focus is on belt splicing and pulley lagging, rubber lining, the supply of belting, splicing machines, belt winders, tool kits, splice kits, adhesives, pulley lagging products, belt conveyor accessory products and the supply of belt maintenance equipment for the mining industry.
Following the success of Thejo Australia, Thejo Engineering established its own branch in Perth, offering abrasion and wear, filtration, screening and customised product related solutions for the mining, mineral processing and corrosion protection sectors.
Today, the companies work together to deliver a complete conveyor care and engineered manufactured parts and
Looking to the future, the Thejo group plans to triple or even quadruple its business, with Australian expansion a key part of these plans.
“All these years, it was about developing products and getting the team ready,” Kallarackal said.
“Now, we’re ready to launch into a new era.
“One of the biggest factors in our growth has been our people and we definitely want to expand that.
“The products, technology and services are all important, but without the people we wouldn’t be where we are today.”
With almost two decades of supply to various clients, ranging from mineral processing, aggregates, power, metal, cement, ports, chemical and fertilisers, the company’s focus is on the growing demand for specialised and customised solutions.
Thejo Engineering vice chair Thomas John said the company’s stateof-the-art manufacturing plants offer a wide range of engineered products, equipment and customised solutions to its clients, no matter where they are in the world.
John said he takes pride in knowing that the company’s range of machinery, technical competency and human resources allows it to deliver topquality products.
“It is also one of the main reasons why today many international original equipment manufacturers outsource their requirements to Thejo Engineering,” John said.
“By continuing to increase a global presence that is backed by highquality products and service, Thejo Engineering is dedicated to becoming a niche player for engineering and manufacturing solutions across a range of mining disciplines.” AM
WITH MINING OPERATIONS EXPANDING ACROSS THE COUNTRY, THERE IS A RISING DEMAND FOR DEPENDABLE TRANSPORT SOLUTIONS.
As the Australian mining industry enters a new era of productivity and sustainability, access to robust and reliable transport solutions has never been more important.
This is where AAA Trailers comes to the fore.
AAA’s trailers, designed for rugged terrain and heavy loads, play a critical role in ensuring the smooth and safe transportation of materials and equipment to and from mine sites.
Mining operations require specialised equipment that can not only handle the extreme conditions synonymous with remote parts of Australia but can also travel vast distances between mine sites and processing plants, and mine sites and ports.
These often-harsh environments can be difficult to traverse, so trailers need to be durable, high-capacity, and versatile.
AAA Trailers offers side-tippers, flatbed trailers, and low loaders which are engineered to carry heavy machinery, such as excavators, loaders, and drilling rigs, as well as raw materials like ore and coal.
The company’s robust designs minimise downtime caused by mechanical failures, a key concern for mining companies under constant pressure to meet production targets.
AAA Trailers prides itself on being customer-focused, meeting client needs with tailored solutions across any industry where cargo needs to be moved by road.
The company manufactures, distributes and services the most appropriate trailer type for the job, and has an extensive product line of trailers loaded with performance and safety features.
From initial consultation and concept design through to assembly and testing, AAA Trailers works alongside customers to achieve the safest and most cost-efficient outcome.
AAA is committed to quality, utilising high-grade materials like reinforced steel and advanced welding techniques in its manufacturing process.
This ensures trailers can handle the toughest jobs without compromising on safety or performance, with each trailer undergoing rigorous testing to
meet Australian safety and compliance standards, giving operators peace of mind when transporting valuable and often-hazardous cargo across challenging terrains.
Safety is paramount in the mining industry, and AAA Trailers incorporates advanced safety features into its designs.
These include load restraint systems, hydraulic ramps, and heavy-duty braking systems that allow for smooth and controlled movement, even on steep or uneven terrain.
Additionally, AAA’s trailers are designed with ease of use in mind, allowing for quick loading and unloading, which reduces operational downtime.
The company emphasises safety with the fitment of electronic braking systems (EBS) on each of its trailers.
EBS adds an extra level of safety, detecting if a vehicle will roll and slowing down engine speed when necessary.
The continued growth of Australia’s mining industry, driven by rising demand for resources like iron ore, lithium and copper, has boosted the need for efficient transport solutions.
As mining companies expand their operations, AAA Trailers is
well-positioned to respond to higher demand and more sophisticated logistics, offering customised, premium trailers that keep the wheels of the industry turning.
Whether it’s moving massive machinery or bulk materials,
AAA Trailers ensures that mining companies can keep operations running smoothly, efficiently and safely, reinforcing the company’s commitment to powering the mining industry’s future through innovative solutions. AM
As Australia’s longest running mining show, Asia-Pacific’s International Mining Exhibition (AIMEX) has a long, established history of showcasing and supporting the latest trends and developments in the industry.
AIMEX is relocating and will call South Australia home for the next 10 years, following market feedback and strong support from the local government and key mining players.
The move marks an exciting new chapter for the event and the region’s resource sector, with the state leading the way in future-focused mining.
AIMEX offers unparalleled opportunities to connect with Australia’s largest community of mining suppliers and professionals in an environment that stimulates innovation and collaboration.
WHAT CAN
ENERGY
The year 2024 might be drawing to a close, but the Australian mining industry isn’t slowing down.
Throughout December and January, the sector will be gearing up for another year of work – and the September ‘Resources and Energy Quarterly’ (REQ) is forecasting 2025 to be a bumper year for a handful of key commodities.
Iron ore
The Australian mining sector wouldn’t be where it is today without iron ore, and this isn’t looking to change anytime soon.
Still ranked the world’s number one for iron ore resources, exploration expenditure remains strong in the wake of lower iron ore prices, and export
AS A URANIUM AND COPPER HOTSPOT.
volumes are tipped to rise by 1.7 per cent annually over the next two years.
China remains Australia’s main iron ore export partner, with the country earning $115.6 billion from Chinese exports in 2023 alone.
Weakened steel production in Asia played a hand in the 0.6 per cent drop in Australian iron ore production in the seven months to July 2024.
Iron ore production is still sitting slightly above the average global range and Western steel demand is forecast to recover marginally in the second half of the 2024–25 financial year, with hopes this demand will translate to higher iron ore prices and production results.
Uranium
South Australia continues to be the unofficial home of uranium in the country, with Boss Energy’s newly opened Honeymoon mine driving export highs.
April, and production is expected to ramp up to 2.45 million pounds per year, eventually pushing Australia’s uranium export earnings to $1.3 billion in 2024–25.
projected in global markets in 2025 and 2026,” the REQ said.
“As the world’s largest exporter of key commodities required for steel production, Australia is well placed to benefit from the demand growth
This year saw a hive of activity in the gold sector, with several new gold projects coming online and major miners making merger and acquisition moves.
Higher prices and volumes are expected throughout 2025.
Global uranium needs are driven primarily by reactor fuel demand – and as Australia is yet to open a nuclear power plant, the majority of the country’s stockpiles are being shipped to countries that have embraced nuclear power.
“In addition to the 30 reactors currently under construction in China, India is building reactors in ‘fleet mode’,” the REQ said.
growing demand.
Supply from uranium mines is expected to lift from 64,000 tonnes in 2023 to 77,000 tonnes in 2026.
Miners are also willing to spend more on uranium exploration as the demand increases. Exploration expenditure rose to $15.2 million in the 2024 June quarter, up from the $3.4 million spent in the 2021 March quarter, demonstrating the sector’s enthusiasm for the energy material.
Gold prices are expected to remain at high levels through to the end of 2024, supported by global monetary easing and ongoing geopolitical uncertainty. Prices are expected to rise further in 2025.
“China’s desire for increased gold holdings is expected to be the main driver of gold demand over the outlook period,” the REQ said.
“The World Gold Council expects above-trend purchases from central banks to continue in the next 12 months.”
Australian gold production will continue to be supported by major project expansions in 2025 and beyond, with Pantoro’s Norseman project and Bellevue Gold’s namesake mine leading the charge.
Genesis Minerals’ Ulysses gold project is also expected to be a major contributor to export volumes in the coming years as production ramps up.
While gold production fell by five per cent in the first half of 2024 due to wet weather and lower gold grades, export earnings and volumes are forecasted to remain high.
“Exports to our main export destinations, Hong Kong and Singapore, rose by 197 per cent and 37 per cent to $11 billion and $1.7 billion, respectively,” the REQ said.
From higher prices to increased export earnings, there’s a lot to look forward to as the mining industry enters 2025.
While nothing is ever certain, it seems clear that the sector is in a good place to bounce back from any challenges, creating a stronger and more diversified industry in the years to come. AM
Address the urgency of modernisation in mining.
How the industry can make real progress without sacrificing business success.
50% of Australian mining businesses anticipate significant or complete transformation of their operations over the next five years.
https://new.abb.com/mining/campaigns/mining-moment
THE 2024 WA MINING CONFERENCE AND EXHIBITION SERVED AS ONE OF THE LARGEST PLATFORMS FOR INDUSTRY PLAYERS TO COME TOGETHER FOR INNOVATION.
KEY THEMES OF WA MINING 2024 INCLUDED ADVANCED TECHNOLOGY, INNOVATIVE SOLUTIONS AND DECARBONISATION.
The 2024 WA Mining Conference and Exhibition (WA Mining) served as a vibrant platform for industry players this year, bringing together established companies, newcomers, and future engineers.
This year’s theme underscored the mining sector’s shift towards safer, cleaner, and more efficient practices, with companies focusing on automation, electrification, and sustainable operations.
With companies bringing cuttingedge technologies and solutions to the forefront, the event highlighted the shift towards more efficient, safer, and environmentally responsible mining practices.
Keep reading to discover what companies focused on at this year’s event and how their contributions are shaping the future of mining.
Control Systems Technology
Control Systems Technology (CST) attracted considerable attention at this year’s event, especially among aspiring engineers and established professionals.
MOTION DEMONSTRATED ITS DIVERSE CAPABILITIES AND EXPANSIVE NETWORK OF COMPANIES.
and sustainability.”
provide ongoing maintenance.
Motion Australia WA state manager Bruce Skinner and national mining business developer Michael Greelish shared their enthusiasm for WA Mining, describing it as an ideal setting to demonstrate the diverse capabilities of Motion’s expansive network of companies.
With 23 integrated companies, Motion Australia is committed to presenting unified solutions to its clients. This motivated the company to have a visible presence at this year’s event.
“The event’s focus on innovation aligns perfectly with our goals and it’s a prime opportunity to showcase our products, network with potential clients, and introduce ourselves to industry partners we may not typically meet,” Greelish said.
Plans are already underway for a bigger and bolder presence at next year’s WA Mining, with Motion looking to expand its offering as it continues on its journey of integrating companies and refining a seamless service experience.
Epiroc came to WA Mining with a clear message of sustainability, safety, and inclusivity.
Hayly Lim, Epiroc regional sales manager for Western Australia, spoke proudly of the company’s commitment to fostering a supportive and diverse workplace.
“I’m five months pregnant and have just been appointed our new sales manager,” Lim said.
“We talk about diversity and inclusion, and I was really sceptical about sort of reception I would get by announcing my pregnancy, but the company is so supportive, which makes me proud to work for them the last three years.”
Epiroc’s product focus at WA Mining centred around electrification and emissions reduction, providing mining clients with hybrid and electric solutions tailored to meet their specific needs.
Lim said Epiroc’s dedication to agnostic solutions enables seamless integration with various mining equipment, whether manufactured by Epiroc or others, enhancing safety and productivity across mining sites.
“We are big on electrification, but also reducing emissions in general,” she said. “We can talk to people about improving fuel efficiencies or about our various products.
“Depending on the client, it could be an electric solution, a hybrid solution, or maybe they are still running diesel, so we look at different ways we can offset that.”
Epiroc also brought recruiters to the event, promoting opportunities for
apprenticeships, product managers, and other roles.
The company views WA Mining not only as a platform to showcase its technology but also to strengthen relationships within the mining sector.
“Our slogan is ‘dare to think new’, and that is what we are always doing,” Lim said.
Dredge Robotics introduced an innovative approach to dredging technology at WA Mining.
Barry Steed, Dredge Robotics commercial manager – West Coast, explained how the company’s robotic dredging machines can operate in challenging environments where traditional machinery is impractical.
“These robots are designed for unique applications, including the recovery of valuable materials from mining waste – a capability especially beneficial in sectors like gold mining,” Steed said.
Steed also highlighted the importance of brand visibility at WA Mining, emphasising that while Dredge Robotics has established a strong foothold in WA, there’s always an opportunity to meet new partners.
“These events offer us a concentrated timeframe to network, gain insights into industry trends, and connect with people who may have innovative ideas or collaborative opportunities for the future,” he said. “You come to these shows, and there’s always someone new and different to connect with.”
Dredge Robotics is pushing the boundaries of mining operations by providing solutions that are safe, efficient, and suited to environments where traditional methods fall short, positioning the company as an industry leader in specialised dredging technology.
The diversity of exhibitors, from CST’s precision weightometers to Epiroc’s emission-reducing equipment, reflects the multifaceted challenges the mining industry faces.
These solutions are not just about operational efficiency; they are about transforming the way the mining industry engages with environmental and social responsibilities.
The presence of students and early-
of engaging with the next generation of mining professionals, viewing these interactions as ways to inspire future leaders and ensure that sustainability and innovation remain at the forefront of the sector.
With the positive reception from this year’s exhibitors and the announcement of even larger commitments for next year’s event, WA Mining is solidifying its status as a key gathering for the mining community.
Exhibitors like Motion Australia are already planning expanded exhibits for 2025, showcasing more integrated solutions and innovative offerings as the company continues to grow.
As WA Mining continues to grow, it will play an essential role in shaping an
WA MINING SHOWCASED A WIDE RANGE OF EFFICIENT, SAFER, AND ENVIRONMENTALLY RESPONSIBLE MINING SOLUTIONS.
THE HOVERMAP LHD ENABLES REMOTE OPERATORS TO CONTINUOUSLY SCAN AND VISUALISE A 360° POINT CLOUD OF THE ENTIRE STOPE.
EMESENT’S HOVERMAP LHD HAS HELPED BYRNECUT ACHIEVE NEAR-REAL-TIME 3D STOPE HAZARD AND VOLUME ASSESSMENTS.
Load haul dump (LHD) machines, also known as scooptrams or boggers, are essential in underground mining operations, transporting ore and waste material from the mining face to designated dumping points.
While remote control and automation systems allow for safer operation, they also present challenges, particularly in low-visibility conditions common in underground mines.
Operators often rely on 2D cameras, which can provide a limited, poorly lit view, making it difficult to accurately assess the remaining material in a stope or detect geotechnical hazards like loose rocks and overhangs.
Limited visibility not only impacts productivity but also increases the risk of operational hazards, such as equipment damage or entrapment.
These risks can be particularly pronounced in cave-style mines, where LHDs are more likely to become trapped under falling rock.
The loss of equipment can halt ore extraction and lead to costly delays, with replacement machinery sometimes taking years to deliver.
Traditionally, cavity monitoring systems (CMS) have been used to measure stope volumes and assess hazards, but these systems require specialist training and are dependent on the availability of trained surveyors, typically only available during day shifts.
This can delay equipment planning decisions and potentially reduce productivity, especially when relocations need to occur outside of regular shift changes.
Recognising the potential for enhanced safety, productivity and cost savings, specialised underground mining contractor Byrnecut leveraged Emesent’s technology to implement an optimised bogging workflow in one of its sub-level caving operations.
The goal was to assess whether improved situational awareness through 3D data could help operators make faster, better decisions, ultimately enhancing both productivity and safety.
Emesent collaborated with global mining services provider Mining Plus to drive development of the solution, working with Byrnecut to understand its needs and test various options.
The result was Hovermap LHD,
offering a 300m range and a 360° field of view to capture and visualise surveygrade point clouds in the field.
The unit, which can be easily mounted onto the cab or bucket of an LHD using magnetic feet, connects to the mine’s network via the machine’s onboard Wi-Fi.
This setup enables remote operators to continuously scan and visualise a 360° point cloud of the entire stope, even in zero-light conditions, using a dedicated tablet.
This near-real-time data can enable the safe, fast and thorough identification of loose rocks, geotechnical hazards and hazardous rill angles that could potentially damage equipment.
Designed for simplicity, Hovermap LHD requires no specialist training,
of equipment allocation, which can significantly boost productivity.
Beyond LHD operations, Hovermap’s versatility sees it used in various configurations, including handheld, on a backpack, mounted on a drone, vehicle, ground robot, or CMS boom, or lowered into shafts in a cage.
This flexibility can expand Hovermap’s applications throughout a mine, potentially offering an even greater return on investment.
The data captured by Hovermap LHD was able to dramatically reduce the time needed to identify hazards such as steep rill angles, oversized material, and confirm the stability of brows, walls, and crowns during remote bogging operations.
Areas that once took up to two days to scan and process can now be captured and visualised in just 10 minutes.
In a hypothetical copper-gold mining operation, an LHD getting stuck can result in one or two shifts of lost production, or even several days.
With Hovermap LHD, crews can perform scans underground at any time, which can lead to accelerated decision-making and minimised risk of damaging or burying an LHD.
This capability has also increased stope turnover, as underground crews can quickly assess an area and make rapid decisions on equipment relocation when the stope is clean.
After realising these benefits, Byrnecut decided to roll out Hovermap LHD to additional mine sites, further advancing its commitment to safety and productivity. AM
As the world shifts from fossil-based energy sources to renewables, Australia is preparing to take centre stage as a leading critical minerals provider.
A state full of these critical resources is South Australia, which saw a 55 per cent increase in mineral exploration in 2022.
According to Geoscience Australia’s ‘Australia’s Identified Mineral Resources 2023’ report, South Australia contains 68 per cent of the country’s demonstrated resources of copper, making it one of the world’s premier copper jurisdictions.
The state is also emerging as a key supplier of green iron, uranium, graphite, zircon, zinc and green hydrogen.
For this reason and many more, South Australia has been chosen as the new home of Asia Pacific’s International Mining Exhibition (AIMEX) for the next 10 years, strengthening the state’s position as one of the fastest growing mining markets globally.
Known as Australia’s longest-running mining event, AIMEX has a deep history of supporting the latest industry trends, innovation and developments by bringing leading local and international mining suppliers and professionals under one roof.
Now under Prime Creative Media’s ownership, AIMEX is positioned to showcase the technology, equipment and services empowering the next generation of mining and exploration.
Prime Creative Media general manager of events Siobhan Rocks said AIMEX’s move to South Australia was decided based on exhibitor and partner feedback, with support from key mining players operating in the state.
“For the past 40 years, AIMEX has taken place in New South Wales, a heavy coal mining region,” Rocks told Australian Mining
“As the world decarbonises, we felt it was important to have AIMEX’s new location reflect this change in industry. South Australia has a progressive and forward-thinking mining sector, and the green resources needed to build critical infrastructure.”
The revitalised AIMEX is sponsored by the South Australian Government, with the event set to generate more than
$250 million for the state’s economy over the next decade.
“With our natural advantages and ingenuity, South Australia has the potential to lead the world in decarbonisation of critical minerals, including green steel and copper,” South Australian Premier Peter Malinauskas said.
“We have a compelling story to tell, and AIMEX being hosted in Adelaide for the next decade provides a strong platform to do just that.
“This exhibition will attract thousands of mining delegates from around Australia and the world to Adelaide every two years, delivering a significant boost to South Australia’s visitor economy.”
AIMEX will feature a free-to-attend conference full of industry insights, case studies and thought leaders speaking about mining developments.
Trends on the agenda include sustainability and electrification – both of which are illustrated by AIMEX’s decarbonisation showcase that will offer a special look at the latest technology and equipment designed to lower emissions and increase operational efficiency.
Businesses will have a chance to promote their emerging technologies
companies can showcase their achievements while promoting themselves as an employer of choice at the Mining Pavilion.
Recent technological advancements from universities will also be highlighted at AIMEX’s Research and Development Hub.
The ‘meet the buyer’ program is also set to return, connecting mining companies with suppliers and helping decision-makers find the best solutions for their needs.
“AIMEX will spotlight diversity in the mining and energy sectors,” Rocks said.
“The 2025 program will have a strong focus on women and First
status quo and generate new solutions for a more inclusive industry.”
Since its inception, AIMEX has been the go-to destination for the mining industry to foster connections and find practical solutions to industry challenges.
From welcome drinks to exhibitor functions, AIMEX 2025 will offer endless opportunities for visitors and exhibitors from around the world to connect with one another face-to-face.
“We’re maintaining AIMEX’s global reputation as a leading mining event in the Asia-Pacific region,” Rocks said. AM
AIMEX 2025 will take place at the Adelaide Showgrounds from September 23–25.
At Parker, our purpose is to make the world a better place – today and well into tomorrow. As we continue to develop electrification technologies to ensure less reliance on traditional fuels, we’re moving one step closer to reaching our goal.
AUSTRALIAN MINING SAT DOWN WITH TWO OF AUSIMM’S 2025 INTERNATIONAL WOMEN’S DAY SERIES AMBASSADORS TO DISCUSS WHAT DIVERSITY, EQUITY AND INCLUSION MEANS TO THEM.
Change will only come when people talk about it.
That message is the motivation behind AusIMM’s International Women’s Day (IWD) Event Series, which works to shape conversations and drive positive change in the resources sector through inspiring speeches.
And the message is driven home further by 2025 IWD Series Ambassadors Brooke Adamson, Lisa Baptista, Odette Patterson, Rowena Albones, and Sharon Lo.
Australian Mining sat down with Adamson and Lo to discuss the IWD Series’ role in championing diversity, equity and inclusion (DEI) and the women’s own contributions to this vital area.
Both Adamson and Lo, like the other Series Ambassadors, are seasoned professionals working in a traditionally male-dominated sector.
Adamson is an ore processing manager – final product at Newmont, while Lo is an area manager – New Zealand, New Caledonia and Fiji at Weir. Although they have vastly different jobs, championing DEI in their respective workplaces has seen them connect on common ground.
“DEI has always been a big passion of mine,” Adamson told Australian Mining. “I feel very honoured to be in this position because I’m among some phenomenal women.
AUSIMM’S 2025 INTERNATIONAL WOMEN’S DAY SERIES AMBASSADORS. BACK ROW: SHARON LO, BROOKE ADAMSON AND ODETTE PATTERSON. FRONT ROW: LISA BAPTISTA AND ROWENA ALBONES.
“I often speak with my team about how DEI isn’t something we can further by just putting policies and systems in place; every single person at every level has to pitch in, be allies, and advocate for change.”
Lo echoed this statement. She credits the allies on her team as some of the driving forces behind her success.
“When I moved out to Cobar in New South Wales for six months, I worked in a very male-dominated team,” she said.
“But it was their support that helped me figure out what I wanted to do with my career and helped me to believe in myself and my abilities.
“Being a Series Ambassador is important because I want to show other people that you can go into an industry like mining and succeed; that being a female in these roles isn’t a barrier.”
Both Adamson and Lo are heavily involved in DEI initiatives at their respective workplaces.
Lo is involved with the Weir Women’s Network – both its global and Australian
BEING A SERIES AMBASSADOR IS IMPORTANT BECAUSE I WANT TO SHOW OTHER PEOPLE THAT YOU CAN GO INTO AN INDUSTRY LIKE MINING AND SUCCEED; THAT BEING A FEMALE IN THESE ROLES ISN’T A BARRIER.”
chapters – an affinity group dedicated to the attraction, retention and continued development of women at Weir.
“We create events to promote women in the workplace and provide training to advance their careers,” Lo said. “I help to support our local chapters, who tailor those events to each area, because we know there are cultural differences within different parts of our global business.
“We recently had an event centred around storytelling, where our global business leaders shared their personal stories about how they came to be in their roles and the challenges they faced.”
Adamson is involved with similar initiatives at Newmont.
“We run women’s mentoring programs across the business,” she said. “But one of the most powerful things we do is create a safe space for everyone.
“There’s a lot of power in talking openly about conscious and unconscious biases and teaching people that diversity isn’t just split between male and female.
“At Newmont, we have pillars of diversity. We have LGBTQIA+, families and careers, family and domestic violence, gender, disability and cultural identity. Members of our senior leadership team drive particular initiatives under each pillar.”
Adamson and Lo both agree that conversations and speaking openly about DEI will lead to the most change in the industry – and it’s one of the reasons both women are looking forward to AusIMM’s 2025 IWD Event Series.
“The IWD Series creates awareness, which is one of the most important things about championing DEI,” Adamson said.
“Like last year, we have phenomenal ambassadors involved in the Series and I was blown away listening to their achievements when I met them.
“It’s important to understand that we all have a role to play. We need diversity advocates and sponsors from across the industry. The more allies we have, the better.”
Lo said events like AusIMM’s IWD Event Series lets people know that it’s okay to talk about DEI.
“The series gives us an open platform where there isn’t any judgment, and it gets men and our allies involved in conversations which they might not usually be comfortable to have,” she said.
“When I tell people I’m a Series Ambassador, it gives me a chance to explain what IWD and DEI is, and why it’s so important.”
Going forward, championing DEI and recruitment will be key focuses for both Adamson and Lo.
“Diversity shouldn’t be seen as a quota,” Lo said. “The thought process needs to change from ‘You were probably hired so the company can meet their diversity goal’ to ‘You were hired because you were the best person for job’.
“People shouldn’t have to feel as though they have to prove their worth.”
Adamson echoed Lo’s sentiments.
“It’s easy to just focus on the ‘female quota’,” she said. “But we don’t want to be just a number. We’re all exceptional, and that’s why we’re in the positions that we are.” AM
AusIMM’s 2025 IWD Event Series will be held across Brisbane, Adelaide, Perth, Kalgoorlie, Melbourne, Sydney and the Hunter Valley from February 27–March 14.
EVENT SUBMISSIONS CAN BE EMAILED TO TOM.PARKER@PRIMECREATIVE.COM.AU
Underground Operators Conference 2025
Adelaide | April 7–9
At Underground Operators 2025, the mining industry will address the demand for more intelligent and cost-effective ways to extract orebodies and explore new technologies that are making it possible to mine at greater depths.
Discussions will focus on health and safety, mine ventilation, social licencing, technology, automation, and the global journey toward net-zero.
Over 1500 mining engineers, operators, technical service managers and consultants from around the world will be in attendance, with a strong keynote speaker lineup scheduled throughout the two days.
Delegates can expect a unique showcase of new technologies, services and over 100 industry-leading organisations on the exhibition floor.
• ausimm.com/conferences-andevents/underground-operators
Mineral Resource Estimation Conference 2025
Perth | May 7–8
AusIMM’s Mineral Resources
Estimation Conference 2025 is expected to bring together over 500 geologists, geostatisticians, software solution providers and other resources professionals from across the globe to challenge the status quo of mineral
resource estimation and share leading best practice examples.
The conference aims to showcase leading best practice, case studies and research on mineral resource estimation and the software applications required, facilitating open exchange of information, boasting interactive sessions, panel discussions and keynote presentations alongside case studies and peerreview papers.
Session topics will showcase the latest advancements and leading examples in 3D geological and estimation domain modelling, geostatistical analysis, estimation, validation, risk analysis, and reporting.
• ausimm.com/conferences-andevents/mineral-resource-estimation
Global Resources Innovation Expo Brisbane | May 20–22
The Global Resources Innovation Expo (GRX) is an industry-led conference and exhibition hosted by Austmine in partnership with AusIMM. It represents an exciting evolution from past Austmine conferences, with GRX25 poised to become an annual global event for the international resources industry.
GRX25 connects attendees with global leaders, allowing them to discover cutting-edge solutions and engage in insightful discussions that drive progress.
GRX25 will feature some of the most influential voices in technology, emerging industries, mining and resources.
• grx.au
PNG Industrial & Mining Resources Exhibition and Conference 2025
Port Moresby, PNG | July 2–3
The 2025 PNG Industrial & Mining Resources Exhibition will showcase over 100 local, national and international manufacturers and suppliers with the latest innovations in the supply of services and equipment for the industrial, mining and oil & gas sectors.
The two-day exhibition is the premier meeting place to connect and network with thousands of industry decisionmakers across a broad industry reach, including senior management, procurement, government personnel, engineers and contractors. With extensive support from key stakeholders in government, associations and industry, PNG Expo is a premier meeting place for industry trade and a forum for establishing high-quality customer contacts and conducting business.
• pngexpo.com
APCOM Conference 2025
Perth | August 10–13
The Application of Computers and Operations Research in the Mining Industry (APCOM) Conference 2025 will
address digitisation across the mining supply chain.
APCOM 2025 will bring together people working in digitally focused roles from across the international mining sector, attracting innovators, mining leaders, planning engineers, mine managers, geoscientists, operators and ESG professionals to Perth in August.
The conference program will include pre-conference workshops, an exhibition, networking opportunities and presentations by leading experts from across the globe.
• ausimm.com/conferences-andevents/apcom-2025
AIMEX 2025
Adelaide | September 23–25
In 2025, Australia’s longest-running mining exhibition will make its South Australian debut in Adelaide to bring together the largest community of mining suppliers and professionals all under one roof to drive innovation and collaboration.
As the key event on the mining calendar, Asia-Pacific’s International Mining Exhibition (AIMEX) is an internationally renowned platform showcasing the latest mining technology, equipment and services, and offering a unique opportunity for leading suppliers and buyers to conduct face-to-face business, learn about the latest trends and network in an interactive forum.
• aimex.com.au
“We capture data of your site then analyse this data to implement a customised solution tailored to your site’s requirements.”
Ability to manage multiple sites and projects from one portal
Brand Agnostic
Ability to change guidelines on site for vehicles, routes & zones